DOI:
10.1039/D3RA01939J
(Paper)
RSC Adv., 2023,
13, 13472-13476
Conversion of cellulose into aromatic compounds using supported metal catalysts in high-temperature water†
Received
24th March 2023
, Accepted 24th April 2023
First published on 2nd May 2023
Abstract
Production of aromatic compounds from lignocellulosic biomass has recently been one goal of efforts to establish a sustainable society. We studied cellulose conversion into aromatic compounds over charcoal-supported metal catalysts (Pt/C, Pd/C, Rh/C, and Ru/C) in water at temperatures of 473–673 K. We found that charcoal-supported metal catalysts enhanced conversion of cellulose to aromatic compounds such as benzene, toluene, phenol, and cresol. The total yields of aromatic compounds produced from cellulose decreased in the order: Pt/C > Pd/C > Rh/C > no catalyst > Ru/C. This conversion could proceed even at 523 K. The total yield of aromatic compounds reached 5.8% with Pt/C at 673 K. The charcoal-supported metal catalysts also enhanced conversion of hemicellulose to aromatic compounds.
1. Introduction
At present, large amounts of aromatic compounds derived from fossil resources are used as feedstocks for plastics and polymers such as phenolic resins and polyesters.1 Demands for plastics and polyesters are growing constantly, and renewable feedstocks of aromatic compounds are therefore needed to achieve the reduction of fossil resource dependence required for establishing a sustainable society.
Lignocellulosic biomass is one of the candidate feedstocks for production of aromatic compounds. Lignocellulose consists of cellulose, hemicellulose, and lignin. Cellulose is a polymer of glucose and hemicellulose consists of several pentoses and hexoses. These saccharides do not have aromatic rings, whereas lignin contains aromatic rings. Depolymerization of lignin to aromatic monomers has been thoroughly studied with various metal catalysts2–7 or porous oxide catalysts.8,9 Efficient use of biomass requires that all components of lignocellulose, cellulose, hemicellulose, and lignin be used to produce aromatic compounds. Fast pyrolysis of lignocellulose using catalysts such as zeolite,10–14 mesoporous silica,13 and porous metal oxides10,13 can produce aromatic compounds from cellulose, hemicellulose, and lignin. However, high temperature (above 873 K) is required to produce aromatic compounds from cellulose, hemicellulose, and lignin. In addition, a large amount of char is formed at the same time. High reaction temperatures and char formation lead to deactivation of catalysts.10,15–17 There is hence a need for a new method of lignocellulose conversion to aromatic compounds at lower temperatures and without char formation.
In our previous study, we found that aromatic compounds were obtained from organosolv lignin and Japanese cedar using charcoal-supported metal catalysts (Pt/C, Rh/C, Pd/C, and Ru/C) in supercritical water at 673 K.18,19 The yields of aromatic products based on the number of aromatic rings in the reactant were 6.4% for organosolv lignin18 and 17.4% for Japanese cedar19 over Pt/C for 1 h at 673 K. The indication was that conversion of lignocellulose could produce more aromatic compounds than conversion of lignin under the same reaction conditions. These results suggested that aromatic compounds might be obtained from not only lignin but also from cellulose and/or hemicellulose. However, the formation of aromatic compounds from cellulose and hemicellulose over supported metal catalysts in high-temperature water has not been reported. We therefore studied conversion of cellulose and hemicellulose into aromatic compounds under the same reaction conditions used to convert lignin in our previous study.18
2. Experimental
2.1. Materials
Cellulose was purchased from Merck & Co., Inc. Charcoal-supported Pd, Pt, Rh, and Ru (5 wt% metal loading; denoted as Pd/C, Pt/C, Rh/C, and Ru/C, respectively), D-glucose, D-xylose, tetrahydrofuran (THF), 1-propanol, and 1-butanol were purchased from FUJIFILM Wako Pure Chemical Corporation. Xylan (from Maple) was purchased from Tokyo Chemical Industry Co., Ltd.
2.2. Reaction procedure
Conversion of cellulose was performed in a batch reactor (316 stainless steel tube: volume, 6.0 cm3). Cellulose used without pretreatment. Supported metal catalyst (0.15 g), cellulose (0.20 g), and water (3.0 g) were loaded into the reactor. The inside of the reactor was purged with argon to remove air, and the reactor was heated for 1 h at temperatures of 473–673 K using a molten salt bath. After the reaction, the reactor was cooled rapidly using a water bath. Gaseous products were collected with a glass syringe and then analyzed on a gas chromatograph (Shimadzu, GC-8A) equipped with a Shincarbon
ST column and a thermal conductivity detector. The reaction slurry was recovered by rinsing the reactor with THF, and solid residue was separated by filtration of the slurry. The liquid products in the filtrate were quantitatively analyzed on another gas chromatograph (Agilent, HP-6890) equipped with a flame ionization detector (GC-FID) and a DB-WAX capillary column using 1-propanol or 1-butanol as an internal standard. The yield of products was defined on the basis of the number of moles of carbon as follows:
|
Yield of aromatic products (%) = (moles of carbon atoms in aromatic products)/(moles of carbon atoms in initial cellulose) × 100
| (1) |
|
Yield of gaseous products (%) = (moles of carbon atoms in gaseous products) / (moles of carbon atoms in initial cellulose) × 100
| (2) |
|
Gas composition (%) = (moles of individual gaseous products)/(sum of moles of total gas products) × 100
| (3) |
The amount of solid residue was estimated by the difference between the initial catalyst mass and the mass of the solid residue after drying as follows:
|
Amount of solid residue (wt%) = {(weight of solid residue) – (weight of supported metal catalyst)}/(weight of initial cellulose) × 100
| (4) |
We also converted glucose, xylan, and xylose to aromatic compounds under the same reaction conditions, and the products were analyzed by the same process. Glucose, xylan, and xylose were used without pretreatment.
3. Results and discussion
3.1. Cellulose conversion using Pt/C in water
Cellulose was converted to aromatic compounds over Pt/C for 1 h at 673 K (Table 1). We found that aromatic compounds were formed from cellulose. The identified aromatics included benzene, toluene, ethylbenzene, propylbenzene, naphthalene, methylnaphthalene, bibenzyl, phenol, cresol, ethylphenol, and propylphenol. The total yield of identified aromatic products was 5.8%. Gaseous products such as H2, CH4, CO2, and C2H6 were also formed. The total carbon yield of gaseous products was 46%. The composition of gaseous products was as follows: H2, 13%; CH4, 12%; CO2, 71%; and C2H6, 4.5%. No solid residue was observed after the reaction. Cellulose was also converted without a catalyst; however, the yields of aromatic products and gaseous products were smaller without catalysts than with a Pt/C catalyst, and some solid residue remained after the reaction. The results indicated that Pt/C could catalyze the conversion of cellulose into aromatic compounds at 673 K.
Table 1 Results of cellulose conversion into aromatic compounds at 673 K. Gas composition (%) is shown in parentheses
|
None |
5% Pt/C |
Aromatic compounds yield (C%) |
1.7 ± 0.3 |
5.8 ± 0.3 |
Benzene |
0.3 |
2.4 |
Toluene |
0.1 |
0.5 |
Ethylbenzene |
0.1 |
0.1 |
n-Propylbenzene |
0.2 |
0.2 |
Phenol |
0.3 |
0.7 |
m-Crezol |
0.1 |
0.2 |
p-Crezol |
0.2 |
0.1 |
4-Ethylphenol |
0.0 |
0.1 |
4-Propylphenol |
0.0 |
0.1 |
Indane |
0.5 |
0.2 |
Naphthalene |
0.0 |
0.4 |
2-Methylnaphthalene |
0.0 |
0.4 |
Bibenzyl |
0.0 |
0.2 |
Gas yield (C%) |
17 ± 1.1 |
46 ± 1.8 |
H2 |
— |
(11) |
— |
(13) |
CO |
5.3 |
(27) |
0.0 |
(0.0) |
CH4 |
1.1 |
(5.5) |
6.3 |
(12) |
CO2 |
11 |
(55) |
37 |
(71) |
C2H6 |
0.5 |
(1.3) |
4.8 |
(4.5) |
Solid residue (wt%) |
13 ± 0.6 |
0.0 |
Fig. 1 shows the yields of aromatic products obtained from cellulose at various temperatures with and without Pt/C. Table S1† summarizes the yields of gaseous products and the amount of solid residue. The total yields of aromatic products at 473 K were very low with Pt/C (0.19%) and without catalysts (0.07%). At 523 K, the total yield with Pt/C increased dramatically to 4.7%, which was higher than the yield of 0.23% with no catalyst. The total yield with Pt/C was about 5% in the temperature range 523–673 K, whereas the total yield without catalysts was at most 1.8%. We found that Pt/C catalyzed conversion of cellulose to aromatic compounds in the temperature range 523–673 K.
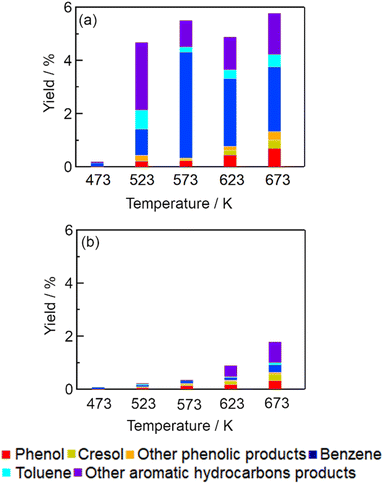 |
| Fig. 1 Yields of aromatic products obtained by conversion of cellulose (a) with Pt/C (b) with no catalyst (catalyst, 0.15 g; cellulose, 0.20 g; water, 3.0 g; reaction time, 1 h). | |
Formation of aromatic compounds from cellulose by fast pyrolysis has been studied under an inert atmosphere in the temperature range 573–973 K.10–15,20,21 Formation of monocyclic aromatic hydrocarbons like benzene and toluene can proceed at temperatures over 873 K;21 however, small amounts of aromatic products (e.g., 0.1% yield of phenols) have been observed in the fast pyrolysis of cellulose at 573 K.20 The results shown in Fig. 1 and Table 1 are therefore the first report of a conversion of cellulose to aromatic hydrocarbons, especially benzene and toluene, achieved at such a low temperature (523 K). Table 2 shows the comparison of this study and fast pyrolysis. The major benzenoid aromatic product is phenol by fast pyrolysis of cellulose at 973 K without catalyst.20 On the other hand, cellulose conversion with Pt/C in supercritical water at 673 K produces benzene as a main product without solid residue.
Table 2 The comparison of aromatic compounds formation by fast pyrolysis of cellulose and catalytic conversion of cellulose in water
|
This study |
Fast pyrolysis20 |
Temperature (K) |
673 |
973 |
Atmosphere |
Water |
Inert gas |
Catalyst |
Pt/C |
None |
Gas yield (wt%) |
67 |
40 |
Solid residue (wt%) |
0.0 |
15 |
Benzenoid aromatic compounds yield (C%) |
5.8 |
2.0 |
Major benzenoid aromatic product |
Benzene |
Phenol |
3.2. Conversion of cellulose using various supported metal catalysts
Conversion of cellulose over charcoal-supported metal catalysts (Pt/C, Pd/C, Rh/C, and Ru/C) at 673 K for 1 h was carried out. Fig. 2 shows the yields. Table S1† summarizes the yields of gaseous products and the amount of solid residue. The total yields of aromatic products decreased in the order Pt/C (5.8%) > Pd/C (4.2%) > Rh/C (3.4%) > no catalyst (1.8%) > Ru/C (1.7%). We found that Pd/C and Rh/C also catalyzed conversion of cellulose to aromatic compounds. The yield of benzene over Pt/C (2.4%) was higher than over Pd/C (0.76%) and Rh/C (0.82%). It has been reported that Pt catalyzes the dehydroxylation of phenolic compounds.22,23 We previously carried out phenol conversion instead of cellulose with Pt/C, Pd/C, Rh/C, and Ru/C under the same conditions in this study (reaction temperature: 673 K, reaction time: 1 h, water density: 0.5 g cm−3).23 Pt/C, Pd/C, and Rh/C catalyzed dehydroxylation of phenol to benzene with the yield of benzene in the order Rh/C (13.8%) > Pt/C (13.7%) > Pd/C (4.4%).23 Conversely, Ru/C catalyzed the phenol conversion to gas products such as methane and carbon dioxide with 88% yield and the Rh/C catalyst also show the activity for the phenol gasification (yield 37%).23 The Pt/C catalyst showed the activity for the phenol to benzene but did not show the gasification of phenol, resulting in the high yield of aromatic products in the case of the Pt/C catalyst. The total yield of aromatic products over Ru/C was lowest; however, Ru/C gave the highest yield of gaseous products (Table S1†). In our previous studies, Ru catalysts have been active for gasification of lignin and cellulose in supercritical water.24–27 The results with Ru/C in this study are consistent with those previous studies.
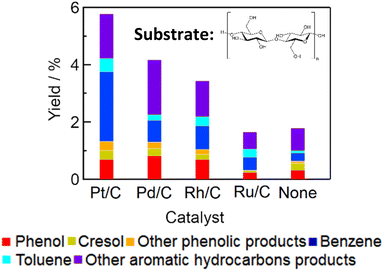 |
| Fig. 2 Yields of aromatic products obtained by conversion of cellulose with various catalysts (catalyst, 0.15 g; cellulose, 0.20 g; water, 3.0 g; reaction temperature, 673 K; reaction time, 1 h). The yield with Pt/C is the same as shown in Fig. 1. | |
3.3. Conversion of glucose using Pt/C and Pd/C in water at 673 K
Conversion of glucose with Pt/C and Pd/C was also performed to understand the mechanism of cellulose conversion. We found that glucose was also converted to aromatic compounds. Fig. 3 shows the yields of aromatic products converted from glucose. Table S2† summarizes the yields of gaseous products and the amount of solid residue. The total yields of aromatic products were comparable for glucose conversion and cellulose conversion with either Pt/C or Pd/C. This result indicates that cellulose conversion to aromatic compounds proceeds via hydrolysis of cellulose to glucose in water. Glucose might be dehydrated to furanic compounds,28,29 and furanic compounds might subsequently be converted into monocyclic aromatic hydrocarbons.30–33
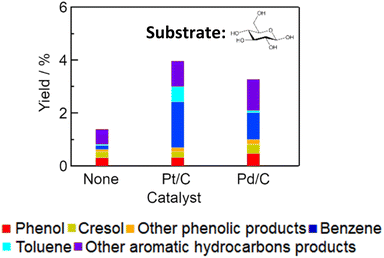 |
| Fig. 3 Yields of aromatic products obtained by conversion of glucose with various catalysts (catalyst, 0.15 g; glucose, 0.20 g; water, 3.0 g; reaction temperature, 673 K; reaction time, 1 h). | |
3.4. Conversion of xylan and xylose using Pt/C and Pd/C in water at 673 K
We carried out the conversion of xylan, which is the main component of hemicellulose, to evaluate the possibility of converting the hemicellulose in lignocellulose to aromatic compounds. We found that aromatic compounds could be obtained from xylan (Fig. 4). In addition, xylose, which is the monomer of xylan, could also be converted to aromatic compounds. Tables S3 and S4† summarize the yields of gaseous products from xylan and xylose, respectively, and the amounts of solid residue. The total yields of aromatic products from xylan with Pt/C and Pd/C were 3.4% and 3.9%, respectively, which were higher than the yields without catalysts (1.7%). We thus found that aromatic compounds could be obtained from xylan with Pt/C and Pd/C. However, the total yield was less from xylan conversion than from cellulose conversion with Pt/C (5.8%) and Pd/C (4.2%). Pt/C and Pd/C also catalyzed xylose conversion, and the total yields of aromatic products with Pt/C and Pd/C were 4.2% and 3.3%, respectively. These results indicated that charcoal-supported metal also catalyzed conversion of hemicellulose to aromatic compounds in water at 673 K. We considered that hemicellulose was converted into xylose by hydrolysis at first. The xylose might be dehydrated to furanic compounds like furfural, and then furanic compounds could be converted into aromatic hydrocarbons.
 |
| Fig. 4 Yields of aromatic products obtained by conversion of (a) xylan and (b) xylose (catalyst, 0.15 g; xylan or xylose, 0.20 g; water, 3.0 g; reaction temperature, 673 K; reaction time, 1 h). | |
Previous studies have indicated that production of phenols and monocyclic aromatic hydrocarbons by fast pyrolysis of hemicellulose requires temperatures over 673 K and 873 K, therefore be converted from hemicellulose at a lower temperature than the temperature required for fast pyrolysis of hemicellulose. This study showed that all components of lignocellulose—cellulose, hemicellulose, and lignin—can be converted to aromatic compounds with charcoal-supported metal catalysts in high-temperature water.
4. Conclusions
We found that charcoal-supported metal catalysts enhanced conversion of cellulose to aromatic compounds in high-temperature water. The conversion could proceed even at 523 K, which is lower than the temperature required for pyrolysis of cellulose.10–15,20,21 Charcoal-supported metal catalysts also enhanced conversion of hemicellulose to aromatic compounds. This study demonstrated that cellulose and hemicellulose could be converted with charcoal-supported metal catalysts in high-temperature water under the same conditions used to convert lignin to aromatic compounds.17 We thus found that all components of lignocellulose—cellulose, hemicellulose, and lignin—could be converted to aromatic compounds with charcoal-supported metal catalysts in high-temperature water. The fact that solid byproducts of the conversion were not observed at temperatures over 623 K indicated that this process precluded char formation in high-temperature water. In the future, we will consider effects of the support on the catalytic performance and optimize reaction conditions to increase the yields of aromatic compounds from lignocellulosic biomass.
Conflicts of interest
There are no conflicts to declare.
Acknowledgements
This work was supported by Japan Society for the Promotion of Science KAKENHI grant no. JP22H00578.
Notes and references
- BP statistical review of world energy, 2021 June, Available online: https://www.bp.com/en/global/corporate/energy-economics/statistical-review-of-world-energy.html, accessed 22 December 2022 Search PubMed.
- J. G. Zhang, J. Teo, X. Chen, H. Asakura, T. Tanaka, K. Teramura and N. Yan, ACS Catal., 2014, 4, 1574–1583 CrossRef CAS.
- C. Z. Li, X. C. Zhao, A. Q. Wang, G. W. Huber and T. Zhang, Chem. Rev., 2015, 115, 11559–11624 CrossRef CAS PubMed.
- S. Van den Bosch, W. Schutyser, S. F. Koelewijn, T. Renders, C. M. Courtin and B. F. Sels, Chem. Commun., 2015, 51, 13158–13161 RSC.
- R. Y. Shu, Y. Xu, L. L. Ma, Q. Zhang, C. Wang and Y. Chen, Chem. Eng. J., 2018, 338, 457–464 CrossRef CAS.
- J. Hu, S. H. Zhang, R. Xiao, X. X. Jiang, Y. J. Wang, Y. H. Sun and P. Lu, Bioresour. Technol., 2019, 279, 228–233 CrossRef CAS PubMed.
- K. Yan, Y. Q. Liu, Y. R. Lu, J. J. Chai and L. P. Sun, Catal. Sci. Technol., 2017, 7, 1622–1645 RSC.
- P. R. Chen, Q. Zhang, R. Y. Shu, Y. Xu, L. L. Ma and T. J. Wang, Bioresour. Technol., 2017, 226, 125–131 CrossRef CAS PubMed.
- K. Barta, G. R. Warner, E. S. Beach and P. T. Anastas, Green Chem., 2014, 16, 191–196 RSC.
- A. V. Bridgwater, Biomass Bioenergy, 2012, 38, 68–94 CrossRef CAS.
- T. R. Carlson, G. A. Tompsett, W. C. Conner and G. W. Huber, Top. Catal., 2009, 52, 241–252 CrossRef CAS.
- W. L. Wang, Y. J. Shi, Y. Cui and X. P. Li, J. Anal. Appl. Pyrolysis, 2018, 131, 93–100 CrossRef CAS.
- M. F. Yang, J. A. Shao, H. P. Yang, K. Zeng, Z. S. Wu, Y. Q. Chen, X. W. Bai and H. P. Chen, Bioresour. Technol., 2019, 273, 77–85 CrossRef CAS PubMed.
- S. N. Liu, J. P. Cao, X. Y. Zhao, J. X. Wang, X. Y. Ren, Z. S. Yuan, Z. X. Guo, W. Z. Shen, J. Bai and X. Y. Wei, J. Energy Inst., 2019, 92, 1567–1576 CrossRef CAS.
- L. Devi, K. J. Ptasinski and F. Janssen, Biomass Bioenergy, 2003, 24, 125–140 CrossRef CAS.
- D. Mohan, C. U. Pittman and P. H. Steele, Energy Fuels, 2006, 20, 848–889 CrossRef CAS.
- C. G. Wang, X. H. Zhang, Q. Liu, Q. Zhang, L. G. Chen and L. L. Ma, Fuel Process. Technol., 2020, 208, 24 CrossRef.
- A. Yamaguchi, N. Mimura, A. Segawa, H. Mazaki and O. Sato, J. Jpn. Pet. Inst., 2020, 63, 221–227 CrossRef CAS.
- A. Yamaguchi, T. Watanabe, K. Saito, S. Kuwano, Y. Murakami, N. Mimura and O. Sato, Mol. Catal., 2019, 477, 6 Search PubMed.
- C. X. Zhao, E. C. Jiang and A. H. Chen, J. Energy Inst., 2017, 90, 902–913 CrossRef CAS.
- F.
X. Collard and J. Blin, Renew. Sustain. Energy Rev., 2014, 38, 594–608 CrossRef CAS.
- M. B. Griffin, G. A. Ferguson, D. A. Ruddy, M. J. Biddy, G. T. Beckham and J. A. Schaidle, ACS Catal., 2016, 6, 2715–2727 CrossRef CAS.
- A. Yamaguchi, N. Mimura, M. Shirai and O. Sato, Sci. Rep., 2017, 7, 7 CrossRef PubMed.
- A. Yamaguchi, N. Hiyoshi, O. Sato, M. Osada and M. Shirai, Energy Fuels, 2008, 22, 1485–1492 CrossRef CAS.
- A. Yamaguchi, N. Hiyoshi, O. Sato, K. K. Bando, M. Osada and M. Shirai, Catal. Today, 2009, 146, 192–195 CrossRef CAS.
- M. Osada, A. Yamaguchi, N. Hiyoshi, O. Sato and M. Shirai, Energy Fuels, 2012, 26, 3179–3186 CrossRef CAS.
- A. Yamaguchi, N. Hiyoshi, O. Sato, K. K. Bando and M. Shirai, Chemsuschem, 2010, 3, 737–741 CrossRef CAS PubMed.
- M. T. Reza, B. Wirth, U. Luder and M. Werner, Bioresour. Technol., 2014, 169, 352–361 CrossRef CAS PubMed.
- J. R. Yin, Z. N. Cheng, L. J. Guo, S. Li and H. Jin, Int. J. Hydrogen Energy, 2017, 42, 4642–4650 CrossRef CAS.
- Y. Zhao, T. Pan, Y. Zuo, Q. X. Guo and Y. Fu, Bioresour. Technol., 2013, 147, 37–42 CrossRef CAS PubMed.
- A. G. Wang, D. Austin, H. Qian, H. B. Zeng and H. Song, ACS Sustainable Chem. Eng., 2018, 6, 8891–8903 CrossRef CAS.
- L. J. Zhu, M. H. Fan, Y. L. Wang, S. F. Wang, Y. T. He and Q. X. Li, J. Chem. Technol. Biotechnol., 2019, 94, 2876–2887 CrossRef CAS.
- Z. J. Lin, M. Ierapetritou and V. Nikolakis, AIChE J., 2013, 59, 2079–2087 CrossRef CAS.
|
This journal is © The Royal Society of Chemistry 2023 |
Click here to see how this site uses Cookies. View our privacy policy here.