DOI:
10.1039/D3RA01597A
(Paper)
RSC Adv., 2023,
13, 12141-12152
Study on the quality and inkjet printing effect of the prepared washing-free disperse dye ink†
Received
11th March 2023
, Accepted 5th April 2023
First published on 19th April 2023
Abstract
With the rapid development of digital inkjet printing, it will inevitably lead to the uneven quality of inkjet printing ink products on the market. Therefore, making a more comprehensive and accurate quality evaluation of digital printing ink is particularly important. In this study, a short process and environment-friendly washing-free disperse dye ink was prepared based on the research on ink quality. The quality of printing ink is closely related to its physical properties, printing ink stability, inkjet performance, and inkjet printing effect. The microdistribution state of water for washing-free disperse dye ink was analyzed by LF-NMR, and the influence of the microstate of water on the macro physical properties of the ink was clarified. The physical properties (particle size, pH value, surface tension, viscosity, rheological properties, etc.) of the washing-free disperse dye ink were systematically tested and analyzed. At the same time, the stability (weatherability, the temperature sensitivity of viscosity, and shear stability) and inkjet performance (drive waveform A, B, and C) of washing-free disperse dye ink were systematically investigated. Finally, the inkjet printing effect of washing-free disperse dye ink was evaluated. This study systematically examined the quality and printing effect of the prepared washing-free disperse dye ink and provided quality evaluation reference for the development of high-quality washing-free disperse dye ink.
Introduction
The three elements of digital printing are software, inkjet printing machine, and printing ink.1–3 Among them, printing ink is the main consumable material in the production of digital printing. Its development has become an indispensable part of the development of digital inkjet printing technology and has become a research hotspot in the field of fine chemicals for textile.4–7 With the rapid development of digital printing technology, the number of digital printing ink manufacturers continues to expand, which will inevitably lead to uneven quality of printing ink products on the market. Thus, conducting a more comprehensive and accurate quality identification of digital printing ink is very important. Digital printing inks mainly include the following types: disperse dye inks, reactive dye inks, acid dye inks, and pigment inks.8–14 Inkjet printing inks are generally composed of colorant, organic solvent, surfactant, defoamer, dispersant, pH regulator, water, etc.12–17 Although different types of inkjet printing inks have certain differences in their components, inkjet printing ink products have many commonalities while having individual characteristics.
Therefore, the quality level of digital printing ink can be evaluated from the following aspects: (1) viscosity is the resistance of printing ink fluidity, and surface tension is the spreading ability of ink to the printing medium. The viscosity of printing ink is generally 2–10 mPa s. The surface tension of printing ink is generally 25–50 mN m−1.5,14–16 (2) To prevent the printing ink from corroding the nozzle, the pH value is generally 7–10.5,15,16 (3) In the printing ink, the value of conductivity is a measure of its salt content.5,15,16 The conductivity of printing ink is generally less than 10
000 μS cm−1. (4) The inkjet fluency is directly related to the effect and quality of digital printing. For disperse dye ink and pigment ink, the inkjet fluency is related to the particle size of the ink, and the ink particle size is generally less than 500 nm. At the same time, a certain amount of water-based polymer is added to the pigment ink, and the water-based polymer in the ink has a crucial influence on its inkjet fluency. The inkjet performance of printing ink is also related to the physical properties of printing ink and the driving waveform loaded on the piezoelectric nozzle.15,16,18 (5) The influence of the storage environment on printing ink. It has been reported that storage environments have little effect on the pH, conductivity, viscosity, and surface tension of the printing ink, and the above parameters of the ink mainly depend on the ink components. The storage stability of printing ink is usually evaluated for the particle size stability of disperse dye ink or pigment ink.5,19,20 (6) Color has three elements, namely, hue, saturation, and lightness. The hue refers to the texture and appearance of the color. The saturation of color refers to the brightness of color. The lightness of printing fabrics can also be characterized by color densitometer.19–21 The above color parameters are closely related to the quality of printing ink. (7) The color fastness of printing fabrics includes washing fastness, dry rubbing fastness, and wet rubbing fastness. The color fastness is also an important standard for measuring the printing effect of printing ink. For the printed fabric products printed with excellent printing ink, the color fastness of 4–5 or 6–8 is the best.19–21 In addition to the color fastness of printed fabrics, the sharpness of printed patterns is also closely related to the quality of printed ink.19,21
In the field of digital inkjet printing of textiles, disperse dye ink accounts for a large proportion, which is mainly based on conventional disperse dye ink. The conventional disperse dye ink printing process consists of five processes: printing, drying, color fixing, washing, and finishing. However, the production process of washing-free disperse dye ink printing includes printing and baking finishing.19,22–25 It can be seen that the biggest advantage of the washing-free disperse dye ink printing production process is that the process is short and the efficiency is high. However, there is a lack of systematic evaluation, induction, and research on the quality of washing-free disperse dye ink and its inkjet printing fabrics.
Therefore, based on the research background of green environmental protection, energy conservation, and emission reduction of textile printing and dyeing, this study prepared washing-free disperse dye ink. The physicochemical properties of washing-free disperse dye ink were systematically evaluated. At the same time, the stability and inkjet performance of washing-free disperse dye ink has also been tested and analyzed. Finally, the influence mechanism of color strength, color fastness, and pattern sharpness of polyester fabric inkjet printed with washing-free disperse dye ink was clarified. In conclusion, this study provides a theoretical and experimental basis for the preparation and quality research of washing-free disperse dye ink.
Experimental section
Materials
C. I. Disperse Blue 359 (press cake) was obtained from Shanghai Annoqi Group Co., Ltd. The dispersant MF (naphthalenesulfonic acid, polymer with formaldehyde, sodium salt, industrial grade) was provided by Anyang Shuanghuan Reagent Co., Ltd. Ethylene glycol (EG), butane-1,2-diol, and sodium dodecyl sulfate (SDS) were supplied by Sinopharm Chemical Reagent Co., Ltd. The foam-free powder (organosilicon defoamer) was purchased from Shanghai BBI Co., Ltd. Triethanolamine (TEOA) were provided by Shanghai Macklin Biochemical Co., Ltd. Polyacrylate emulsion (4008A, solid content, 51.2 wt%, industrial grade) was supplied by Guangzhou Fanhao Trading Co., Ltd (China). Deionized water (DI water) was prepared in laboratory. Polyester fabric (135 g m−2, plain weave) was supplied by Shanghai Textile Industry Institute.
Preparation of color paste and washing-free disperse dye ink
C. I. Disperse Blue 359 (10.00 wt%), dispersant MF (10.00 wt%), EG (10.00 wt%), silicone defoamer (0.05 wt%), and deionized water (69.95 wt%) were weighed and added to 100.00 g zirconia beads (0.40–0.60 mm, diameter). Grinding was performed using a planetary ball mill (Nanjing Chishun Science & Technology Co., Ltd., CN) operated at 600.0 rpm for 20.0 h. As a result, the color paste was successfully prepared.
The preparation of washing-free disperse dye ink (Table 1) is as follows: color paste (30.00 g), butane-1,2-diol (25.00 g), TEOA (0.50 g), SDS (0.50 g), silicone defoamer (0.05 g), polyacrylate emulsion (0.000 g, 0.586 g, 1.172 g, 1.758 g, 2.344 g, 2.929 g, and 3.906 g), and deionized water (44.400 g, 43.814 g, 43.228 g, 42.642 g, 42.056 g, 41.471 g, and 40.494 g) were accurately weighed. It was stirred evenly through the magnetic stirrer and finally filtered with a waterborne filter membrane (0.22 μm, 0.45 μm, and 0.80 μm) to obtain the required washing-free disperse dye ink (Ink a, b, c, d, e, f, and g), respectively.
Table 1 The formulation of washing-free disperse dye ink
Sample |
Color paste (wt%) |
SDS (wt%) |
TEOA (wt%) |
Butane-1,2-diol (wt%) |
Polyacrylate emulsion (wt%) |
Silicone defoamer (wt%) |
Deionized water (wt%) |
Ink a |
30.000 |
0.500 |
0.050 |
25.000 |
0.000 |
0.050 |
44.400 |
Ink b |
30.000 |
0.500 |
0.050 |
25.000 |
0.586 |
0.050 |
43.814 |
Ink c |
30.000 |
0.500 |
0.050 |
25.000 |
1.172 |
0.050 |
43.228 |
Ink d |
30.000 |
0.500 |
0.050 |
25.000 |
1.758 |
0.050 |
42.642 |
Ink e |
30.000 |
0.500 |
0.050 |
25.000 |
2.344 |
0.050 |
42.056 |
Ink f |
30.000 |
0.500 |
0.050 |
25.000 |
2.929 |
0.050 |
41.471 |
Ink g |
30.000 |
0.500 |
0.050 |
25.000 |
3.906 |
0.050 |
40.494 |
LF-NMR measurements
LF-NMR relaxation measurements were performed using Niumag Bench-top Pulsed NMR Analyzer PQ001 (Niumag Electric Corporation, Shanghai, China) operated at a proton resonance frequency of 22.7 MHz at 32 °C (±0.01 °C). For this purpose, accurately weighed 1.5 g sample (Ink components, washing-free disperse dye ink) was inserted in the LF-NMR probe. Spin–spin relaxation time, T2, was measured using the Carr-Purcell-Meiboom-Gill (CPMG) sequence. For the measured samples, the relaxation signal could also be expressed in the multiexponential form. The spin–spin relaxation time inversion was performed using eqn (1), where pi is the signal intensity of the ith component whose spin–spin relaxation time is T2i.20,26 |
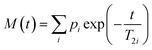 | (1) |
Characterization of washing-free disperse dye ink
The particle size and zeta potential of the washing-free disperse dye ink were characterized using a Zetasizer Nano-ZS90 from Malvern Instruments Co., Ltd., UK at 25.00 °C. The pH of the washing-free disperse dye ink was tested using the pH meter (PHS-3C, Shanghai Instrument Science Instrument Co., Ltd., CHN). The conductivity of the ink was determined using the conductivity meter (ST3100C, OHAUS Instrument Co., Ltd., CNH). The surface tension was measured with a BP100 bubble pressure tensiometer (Kruss, Hamburg, Germany) at 25.00 °C. The viscosity was determined using a rotational viscometer (Rhellab QC, Anton Paar Instruments Co., Ltd., CHN) at 20 °C or 32 °C with a speed of rotation of 60 rpm. The rheological properties of inks were characterized in the shear rate range of 150.00–1000.00 s−1 at 20.00 °C (shear increase rate 10.00 s−1). The washing-free disperse dye ink (the filter membrane with pore size of 0.22 μm) was diluted 10
000 times with DI water and analyzed by an ultraviolet spectrophotometer (TU-1900, Beijing General Instruments Co., Ltd.).
The stability of the washing-free disperse dye ink was mainly evaluated by its weatherability (Sampling after ink oscillation), such as thermal stability (60 °C, 7 days, RTS), and freeze-thaw stability (−18 °C, 7 days, RFT). The rate of change (R) for the particle size was calculated using eqn (2) (original washing-free disperse dye ink, P0 nm−1; measured washing-free disperse dye ink, P nm−1; particle size relative change, R/%). The higher is the R value, the poorer is the ink stability.19
|
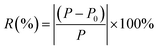 | (2) |
Observation of droplet formation and inkjet printing
The droplet formation process and driving waveform optimization were achieved using JetXpert analytical instrument at 20 °C (driving waveform (A, B, C), Fig. 1, Imagexpert Co., Ltd, America). The JetXpert analytical instrument consisted of a jetting driver (piezoelectric type; A, B, C waveform), print head (nozzle diameter 21 μm, Epson Dx5), and drop watcher stroboscope LED delay camera system (CCD). Three different trapezoidal driving waveforms (A, B, C) were used for the testing of washing-free disperse dye ink inkjet performance, and the driving waveforms matching the washing-free disperse dye ink was optimized.
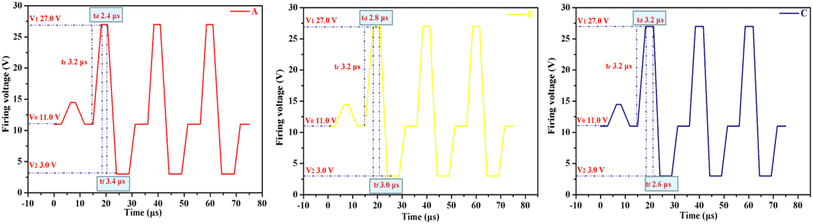 |
| Fig. 1 Driving waveform of the piezoelectric nozzle. | |
Characterization of printing fabric
The line width of the printed lines was specified as 352.00 μm. The size of inkjet printing block is 160 mm × 200 mm. Inkjet printing was carried out using an Epson R330 inkjet printer (Seiko Epson Corporation, Japan) at 20.00 °C (Warp direction inkjet printing). The printing patterns (lines and color blocks) were subsequently thermo-fixed by treatment in a hot air oven at 110.00 °C for 1.00 min and post-treatment at 175.00 °C for 1.00 min. The printing pattern (line width) was photographed by a 3D super depth digital microscope (VHX-1000, Keyence Instruments Company, Japan). The rate of change (W) of the line width was calculated using eqn (3) (Print Linewidth, D0 μm−1; measured linewidth, D μm−1; linewidth relative change, W/%). The larger the W value, the more serious the ink diffusion and the worse the pattern sharpness.19 |
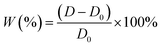 | (3) |
The color strength data (K/S) was obtained using an Ultra Scan Hunter Lab K/S (USA) with a D65 spectrophotometer. The printing fabrics were folded twice and four measurements were performed in each case. The K/S value was calculated using the Kubelka–Munk equation (eqn (4); K is the adsorption coefficient, S is the scattering coefficient, and R is reflectance of the printing fabrics). The colorfastness of the printing fabrics was analyzed according to GB/T3921-2008 (soaping fastness), GB250-2008, and GB251-2008 (dry/wet rubbing fastness).16,20
|
 | (4) |
Results and discussion
Analysis of main components of washing-free disperse dye ink
The information on molecular motions and intermolecular interaction was obtained by the relaxation time information of LF-NMR.15,16,19,20 It was employed to further reveal the mechanism of interaction between the main components of the ink and DI water.19,20 Fig. 2 is the T2 inversion spectrum of LF-NMR relaxation time of ink components. The characteristics of molecular motions are closely associated with the relaxation time. The larger the relaxation time, the stronger the molecular motions.15,16,19,20 It can be seen from Fig. 2 that there is only one peak at the inversion spectrum of DI water, and the relaxation time range is 1873.82–4922.02 ms.20 The inversion spectrum of the butane-1,2-diol molecule also exhibits only one peak, and the relaxation time range is 89.07–219.64 ms. This indicates that the fluidity of water molecules is much stronger than that of butane-1,2-diol. For 25 wt% butane-1,2-diol aqueous solution, there are three peaks T21 (7.84–10.35 ms), T22 (235.43–622.26 ms), and T23 (880.49–2866.07 ms), which are completely different from DI water and butane-1,2-diol. The reason is that butane-1,2-diol has a strong intermolecular force with DI water, which binds the fluidity of water molecules. It can be seen that there are three states of water in polyacrylate emulsion: intra-microstructure water (T21, T22) and extra-microstructure water (T23).19 The inversion spectrum of polyacrylate emulsion (1.758 wt%) (Fig. 3a and b) shows the three states of water, T21 (0.74–2.25 ms), T22 (2.25–5.54 ms), and T23 (1644.68–3072.11 ms), respectively. This indicates that the polyacrylate emulsion can increase the water content in the polyacrylate microstructure and enhances the bound intensity to DI water. The polyacrylate emulsion was dried into a film by thermal drying (Fig. 3c). From the freeze-drying SEM image of the polyacrylate emulsion (Fig. 3d), it is known that the polyacrylate emulsion exhibits a three-dimensional network structure in the emulsion dispersion system. The SEM image of freeze-drying polyacrylate emulsion can further confirm the existence of intra-microstructure water and extra-microstructure water in the washing-free disperse dye ink system.16,19
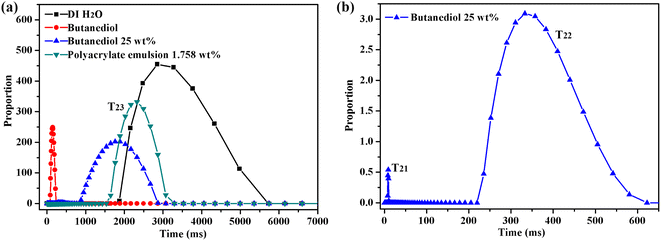 |
| Fig. 2 T2 relaxation time (T2 relaxation time range is 0–7000 ms) distribution of DI H2O, butanediol, butanediol 25 wt% and Polyacrylate emulsion 1.758 wt% (a), T2 relaxation time (T2 relaxation time range is 0–650 ms) distribution of butanediol 25 wt% (b). | |
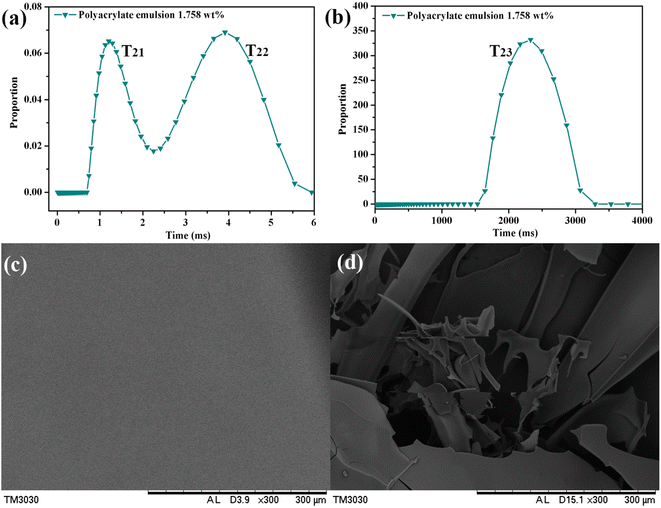 |
| Fig. 3 Polyacrylate emulsion T2 relaxation time distribution (a and b), polyurethane emulsion heating drying SEM diagram (c), and polyurethane emulsion freeze-drying SEM diagram (d). | |
Analysis of washing-free disperse dye ink
It is well known that washing-free disperse dye ink components (butane-1,2-diol, polyacrylate emulsion, H2O, Table 1) contain a hydroxyl or three-dimensional structure, which can form a strong binding effect on DI water and butane-1,2-diol. According to Fig. 4(a) and (b), the relaxation time of the washing-free disperse dye ink is divided into two parts or three parts. For example, the relaxation times of Ink a are T21 (4.20–12.75 ms) and T22 (382.75–1011.64 ms). The relaxation times of Ink g are T21 (2.97–7.32 ms), T21–1 (7.84–20.73 ms), and T22 (270.49–880.49 ms), which may be because the content of polyacrylate emulsion in Ink g is relatively high, the three-dimensional structure is more compact, and the binding to water is stronger. As shown in Fig. 4b, the relaxation times of washing-free disperse dye ink shows a trend of moving to the left with an increase in the content of polyacrylate emulsion in the ink, which indicates that the three-dimensional structure formed by polyacrylate emulsion has a strong binding effect on DI water and the fluidity of the ink is decreasing. Table 2 shows the relaxation time data of the washing-free disperse dye ink. For example, the relaxation times of Ink a, Ink c, and Ink g are T22 (382.75–1011.64 ms), T22 (357.09–1011.64 ms), and T22 (270.49–880.49 ms), respectively. According to the relaxation time data of washing-free disperse dye ink shown in Table 2, the relaxation time of washing-free disperse dye ink decreases with the increase in the polyacrylate emulsion content, which indicates that the fluidity of washing-free disperse dye ink decreases with the increase in the polyacrylate emulsion content. This phenomenon suggests that the addition of polyacrylate emulsion can reduce DI water fluidity and further restrict their degree of freedom.19 In particular, the presence of polyacrylate emulsion (three-dimensional structure) in the washing-free disperse dye ink is the most effective in entrapping the ink component in the washing-free disperse dye ink.15,16,19 Due to the different intermolecular forces (hydrogen bond, ion bond force, van der Waals force, etc.) between water molecules and various ink components and the existence of microstructure in washing-free disperse dye ink, the water molecules in washing-free disperse dye ink are in an uneven environment, showing multiexponential relaxation characteristics.19,21
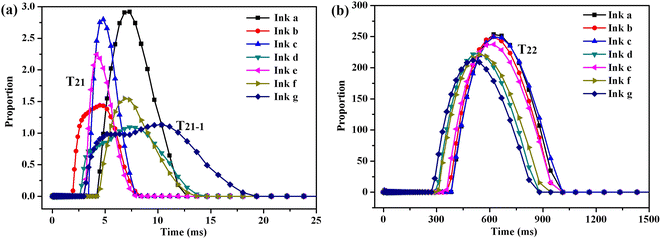 |
| Fig. 4 T2 relaxation time (T2 relaxation time range is 0–25 ms) distribution of washing-free disperse dye ink (a), T2 relaxation time (T2 relaxation time range is 0–1500 ms) distribution of washing-free disperse dye ink (b). | |
Table 2 Low field nuclear magnetic data of the washing-free disperse dye ink
Sample |
Peak |
Initial time of peak (ms) |
Peak maximum time (ms) |
Peak end time (ms) |
Peak area |
Ink a |
1 |
4.20 |
7.32 |
12.75 |
26.56 |
2 |
382.75 |
622.26 |
1011.64 |
2225.83 |
Ink b |
1 |
1.82 |
4.50 |
9.01 |
20.69 |
2 |
357.08 |
622.26 |
1011.64 |
2231.93 |
Ink c |
1 |
3.41 |
4.82 |
8.41 |
20.27 |
2 |
357.09 |
622.26 |
1011.64 |
2257.24 |
Ink d |
1 |
2.58 |
7.32 |
14.65 |
17.41 |
2 |
289.94 |
541.59 |
880.49 |
2205.44 |
Ink e |
1 |
2.97 |
4.20 |
8.41 |
16.86 |
2 |
333.13 |
622.26 |
1011.64 |
2232.47 |
Ink f |
1 |
4.20 |
6.83 |
14.65 |
14.05 |
2 |
289.94 |
541.59 |
943.79 |
2222.04 |
Ink g |
1 |
2.97 |
6.37 |
7.32 |
10.61 |
1–1 |
7.84 |
10.35 |
20.73 |
10.19 |
2 |
270.49 |
505.26 |
880.49 |
2207.96 |
Quality evaluation of the washing-free disperse dye ink
The physicochemical properties of washing-free disperse dye ink are important parameters of ink. The physicochemical properties of ink are mainly evaluated from the pH, conductivity, zeta potential, viscosity, rheological properties, particle size, and surface tension.5,11,13,15,20 The pH value of inkjet printing ink has an important influence on the ink characteristics and applicability. To prevent the ink from corroding the important parts of the inkjet system, such as the nozzle, the pH value range of the ink is about 7–10.5,21 In this study, the pH value of washing-free disperse dye ink was regulated by pH regulator (0.05 wt%, TEOA). In Table 3, the washing-free disperse dye ink pH is 7.4–7.9. The conductivity is another important index to evaluate the washing-free disperse dye ink properties, which can be used to reflect the salt content of ink. To prevent the clogging of the nozzle and the corrosion of the ink path system, the conductivity is preferably as small as possible.5,21 The conductivity of the washing-free disperse dye ink described in Table 3 is in the range of 2.9–3.2 mS cm−1, which is less than the required conductivity of the printing ink, which does not exceed 10.0 mS cm−1.
Table 3 Physicochemical properties of washing-free disperse dye ink
Sample |
pH |
Conductivity (mS cm−1) |
Zeta potential (mV) |
Viscosity (mPa s) |
Particle size (nm) |
Surface tension (mN m−1) |
Ink a |
7.6 ± 0.2 |
2.9 ± 0.1 |
−53.2 ± 0.1 |
4.1 ± 0.1 |
169.2 ± 2 |
38.8 ± 0.1 |
Ink b |
7.5 ± 0.1 |
2.9 ± 0.2 |
−51.4 ± 0.1 |
3.9 ± 0.1 |
169.0 ± 1 |
39.0 ± 0.1 |
Ink c |
7.6 ± 0.1 |
3.0 ± 0.2 |
−52.2 ± 0.2 |
3.8 ± 0.1 |
169.4 ± 2 |
38.8 ± 0.1 |
Ink d |
7.5 ± 0.2 |
3.0 ± 0.1 |
−49.9 ± 0.1 |
4.3 ± 0.1 |
170.5 ± 1 |
38.4 ± 0.1 |
Ink e |
7.6 ± 0.1 |
3.1 ± 0.2 |
−50.3 ± 0.2 |
3.8 ± 0.1 |
166.5 ± 1 |
38.3 ± 0.2 |
Ink f |
7.7 ± 0.2 |
3.1 ± 0.2 |
−52.7 ± 0.2 |
4.0 ± 0.1 |
167.0 ± 2 |
38.2 ± 0.1 |
Ink g |
7.7 ± 0.1 |
3.2 ± 0.2 |
−47.2 ± 0.2 |
4.3 ± 0.1 |
167.7 ± 1 |
37.8 ± 0.1 |
Zeta potential is an important indicator of the stability of the dispersion system.20 It is a measurement of strength of repulsion or attraction between disperse dye particles in washing-free disperse dye ink. The higher the absolute value of zeta potential (positive or negative), the more stable the system; then, disperse dyes can resist aggregation. The absolute value of the zeta potential for the washing-free disperse dye ink needs to be greater than 25 mV.20 The zeta potential of the washing-free disperse dye ink is between 47 and 53 mV (Table 3). The zeta potential of washing-free disperse dye ink is between 47 and 53 mV (Table 3), which indicates that the disperse dye in the prepared ink is not easy to agglomerate and has good stability. In general, the particle size of the disperse ink is less than 200.0 nm, which is due to the aperture of the piezoelectric nozzle of about 21.0 μm. The particle size of the washing-free disperse dye ink is too large, which will clog the nozzle. As illustrated in Table 3, the average particle size of washing-free disperse dye ink is 166.5–169.2 nm, indicating that the particle size of the ink meets the demands of the printing washing-free disperse dye ink.
The surface tension of printing ink is mainly regulated by the surfactant.27–29 In this study, the surfactant (SDS, 0.5 wt%) was used to regulate the surface tension of the washing-free disperse dye ink, which was about 38.0–39 mN m−1 (Table 3, Fig. 5), which indicated that the surface tension of the prepared ink was mainly determined by the surfactant SDS. The viscosity of printing ink is related to the interaction of ink components and its microstructure.19,20 Table 3 presents the viscosity of inks (Ink a–g), which are 4.1, 3.9, 3.8, 4.3, 3.8, 4.0, and 4.3 mPa s, respectively. The surface tension and viscosity of inks with different formulations are different,27–29 which may be caused by the different content of polyacrylate emulsion in the inks, leading to the different microstructure of the inks. Fig. 6 gives the rheological properties of the washing-free disperse dye ink, and the shear-rate increases almost linearly with the shear stress. Fig. 6 illustrates that the prepared washing-free disperse dye ink presents the characteristics of Newtonian fluid. Fig. 7 presents the change in viscosity of the washing-free disperse dye ink at different temperatures (20 °C, 32 °C). As shown in Fig. 7, there are some differences in the viscosity changes of different washing-free disperse dye inks at different temperatures. It can be seen from Fig. 7 that the viscosity of Ink a is less sensitive to temperature, and the viscosity of Ink b is more sensitive to temperature. The viscosity change rate of Ink a at different temperatures (20 °C, 32 °C) is 28.83%. The viscosity change rate of Ink e at different temperatures (20 °C, 32 °C) is 30.53%; the reason may be that the change in the ink temperature has a great influence on the microstructure of its internal three-dimensional network (polyurethane emulsion).30,31 Fig. 8 shows the shear stability of washing-free disperse dye Ink a and e. Fig. 8 indicates that the prepared washing-free disperse dye ink has good consistency in ink rheological properties under different shear conditions. The reason may be that the prepared disperse dye ink belongs to Newtonian fluid.
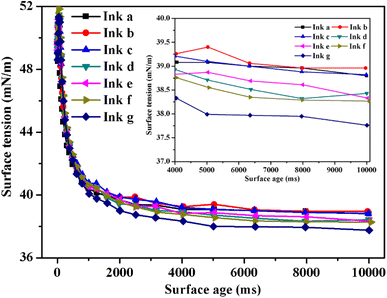 |
| Fig. 5 Surface tension of washing-free disperse dye ink. | |
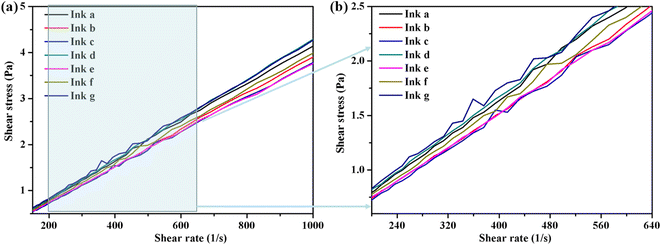 |
| Fig. 6 Relationship between shear stress and shear rate (the shear rate range is 150–1000 s−1) of washing-free disperse dye ink (a), relationship between shear stress and shear rate (the shear rate range is 200–640 s−1) of washing-free disperse dye ink (b). | |
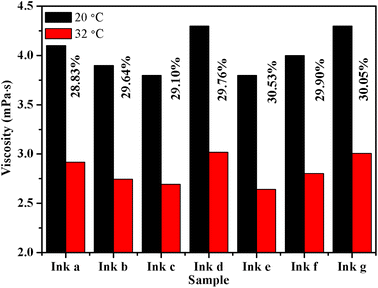 |
| Fig. 7 Effect of temperature on the viscosity of washing-free disperse dye ink. | |
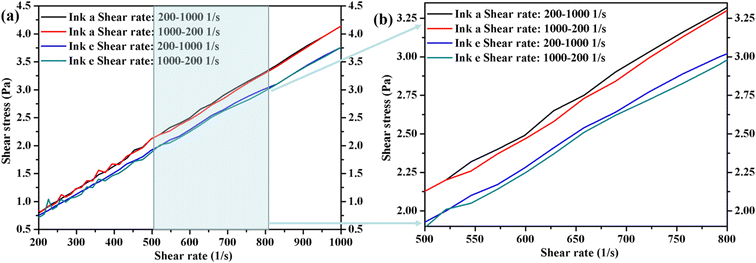 |
| Fig. 8 Shear stability (the shear rate range is 200–1000 s−1) of washing-free disperse dye ink a and e (a), shear stability (the shear rate range is 500–800 s−1) of washing-free disperse dye ink a and e (b). | |
The weatherability of washing-free disperse dye ink is critical, which is related to the service life of printing ink. The weatherability of printing ink is mainly evaluated by the thermal stability (60.0 °C) and freeze stability (−18.0 °C).19 It has been reported that temperature has little effect on the pH, conductivity, viscosity, and surface tension of printing ink, and the above parameters of ink mainly depend on the ink components.5,19 For washing-free disperse dye ink, the ink was left at a high temperature (60.0 °C) or low temperature (−18.0 °C) environment for two weeks without stratification phenomena and sedimentation. Table 4 shows the low temperature stability and high temperature stability of washing-free disperse dye ink (Ink a–g). As shown in Table 4, the particle size of washing-free disperse dye ink changes little under different temperature conditions, which shows that the components in the washing-free disperse dye ink prepared have good compatibility.
Table 4 Weatherability of washing-free disperse dye ink
Sample |
Original particle size (nm) |
Thermal stability |
Freeze stability |
Particle size (nm) |
RTS (%) |
Particle size (nm) |
RFT (%) |
Ink a |
169.2 |
170.6 |
0.83 |
165.1 |
2.42 |
Ink b |
169.0 |
172.1 |
1.83 |
172.4 |
2.01 |
Ink c |
169.4 |
158.8 |
6.26 |
174.8 |
3.19 |
Ink d |
170.5 |
175.4 |
2.87 |
173.7 |
1.88 |
Ink e |
166.5 |
165.3 |
0.72 |
173.7 |
4.32 |
Ink f |
167.0 |
161.3 |
3.41 |
170.9 |
2.33 |
Ink g |
167.7 |
166.5 |
0.71 |
174.9 |
4.29 |
The concentration of the colorant in the ink can be determined by UV absorption spectrum because the absorption value of the specific spectral wavelength is different for different concentrations.21 The UV absorption spectra of washing-free disperse dye ink is shown in Fig. 9. The ink component in washing-free disperse dye ink (C. I. Disperse Blue 359) had little effect on the UV spectral shift of the ink. The UV spectrum intensity of the washing-free disperse dye ink is different due to the difference in the polyacrylate emulsion content of the washing-free disperse dye ink. The color strength of the prepared washing-free disperse dye ink will affect the color strength of the printed fabric.
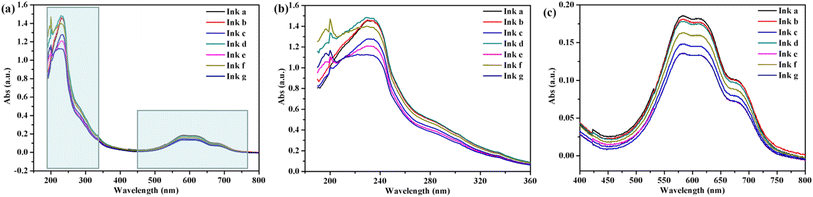 |
| Fig. 9 UV spectrum (the wavelength range is 190–800 nm) of washing-free disperse dye ink a–g (a), UV spectrum (the wavelength range is 190–360 nm) of washing-free disperse dye ink a–g (b), UV spectrum (the wavelength range is 400–800 nm) of washing-free disperse dye ink a–g (c). | |
Inkjet performance of washing-free disperse dye ink
The inkjet performance is the combined result of the nozzle parameters (nozzle aperture, nozzle interface material, etc.), driving waveform parameters (driving voltage, driving waveform, and pulse time), and physical properties of ink (viscosity, fluidity, surface tension, and density).26,29–31 The drop-on-demand pulse was controlled using a jetxpert analytical instrument with the trapezoidal waveform illustrated in Fig. 1 (A, B, C). The parameters of trapezoidal waveform include voltage initial value (V0), voltage maximum value (V1), voltage minimum value (V2), voltage rise time (Tr), voltage dwell time (Td), voltage fall time (Tf), and voltage echo time (Te).26 In this study, piezoelectric nozzle was used to observe the inkjet process of washing-free disperse dye ink. Due to the nozzle aperture (about 21.00 μm) and driving waveform (driving voltage 27.00 V) used in the inkjet observation, the inkjet performance depends on the physical properties of the washing-free disperse dye ink, voltage dwell time (Td), and voltage fall time (Tf). The voltage dwell time (Td) of driving waveform (A, B, C) are 2.4 μs, 2.8 μs, and 3.2 μs, respectively. The voltage fall time (Tf) of driving waveform (A, B, C) are 3.4 μs, 3.0 μs, and 2.6 μs, respectively.
As illustrated in Table SI,† the inkjet process of ink is noted to be different for different driving waveforms. When the washing-free disperse dye ink (Ink a–g) was observed under the condition of driving waveform A, the ink droplets could not merge and the phenomenon of satellite droplets was seen, which indicated that the prepared washing-free disperse dye ink was not suitable for inkjet printing under the condition of driving waveform A. The formation process of ink droplets was observed under the condition of driving waveform B. It was found that the washing-free disperse dye ink (Ink c, e, g) could not inkjet normally, while the Ink f showed inkjet instability, which may be due to the different physical properties (viscosity, 4.0 mPa s; surface tension, 38.2 mN m−1) of the ink. When observing the inkjet process under the condition of driving wave C, only Ink b has satellite droplets (viscosity, 3.9 mPa s; surface tension, 39.0 mN m−1), and other inks can be inkjet normally. The ink droplet formation process is observed under the condition of driving waveform C. The ink droplet formation process depends on the physical properties of the ink. For example, the ink droplet inkjet time and the primary and secondary ink droplet merging time of Ink a are 23 μs and 48 μs, respectively. The ink droplet inkjet time and the primary and secondary ink droplet merging time of ink g are 23 μs and 41 μs, respectively.
Analysis of pattern quality of polyester fabric inkjet printing
For the fabric inkjet printing pattern, the principal index to evaluate the quality of printing ink is the sharpness, color strength, and color fastness of the printing pattern.25,26,30–32 Table 5 lists the printing fabric parameters of washing-free disperse dye ink. It can be seen from Table 5 that the line width of the printing fabrics is related to the ink viscosity and fluidity (The fluidity of ink is closely related to its transverse relaxation time).19,21,31 The viscosity of Ink a, b, c, d, e, f, and g were observed to be 4.1 mPa s, 3.9 mPa s, 3.8 mPa s, 4.3 mPa s, 3.8 mPa s, 4.0 mPa s, and 4.3 mPa s, respectively. The shifts in the T23 main peak in the T2 relaxation time inversion spectra of the printing Ink a, b, c, d, e, f, and g are 382.75–1011.64 ms, 357.08–1011.64 ms, 357.09–1011.64 ms, 289.94–880.49 ms, 333.13–1011.64 ms, 289.94–943.79 ms, and 270.49–880.49 ms, respectively. The viscosity and fluidity of the ink can overcome the capillary force caused by the fabric structure and weaken the diffusion of the ink on the surface, which will help to improve the sharpness of the printing pattern.19,21,31 For example, the viscosity of ink c is 3.8 mPa s, the transverse relaxation time is 357.09–1011.64 ms, and the line width of the printed polyester fabric is 417.36 μm. The viscosity of ink g is 4.3 mPa s, the transverse relaxation time is 270.49–880.49 ms, and the line width of the printed polyester fabric is 372.50 μm.
Table 5 Printing fabric parameters (fixation temperature 175 °C)
Printing sample |
Weft linewidth (μm) |
Printing lines (warp direction inkjet printing) |
K/S |
Dry rubbing fastness |
Wet rubbing fastness |
Washing fastness |
Ink a |
401.19 |
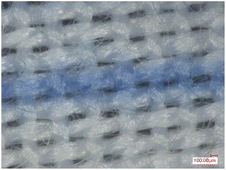 |
4.9 |
3–4 |
3 |
3–4 |
Ink b |
392.91 |
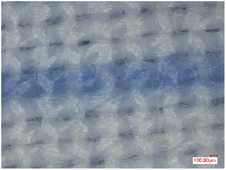 |
3.2 |
4 |
3–4 |
4 |
Ink c |
417.36 |
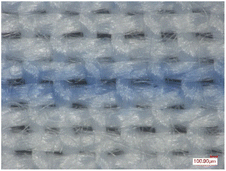 |
3.5 |
4 |
3–4 |
4 |
Ink d |
378.48 |
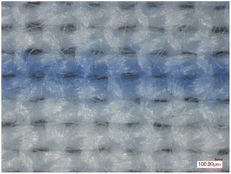 |
4.0 |
4 |
3–4 |
4 |
Ink e |
395.48 |
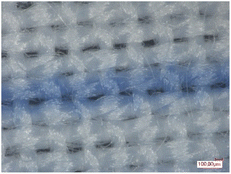 |
3.5 |
4 |
3–4 |
4 |
Ink f |
389.38 |
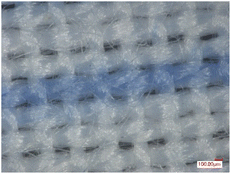 |
3.1 |
4 |
3–4 |
4 |
Ink g |
372.50 |
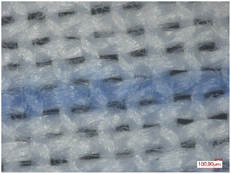 |
3.0 |
4 |
3–4 |
4 |
The K/S value of the printing pattern is directly related to the content of the disperse dye in the printing ink.21,31 The UV spectral absorption intensity (Fig. 5) of different washing-free disperse dye inks (Ink a, b, c, d, e, f, and g) are 1.454, 1.460, 1.275, 1.483, 1.210, 1.400, and 1.126, respectively. As shown in Table 5, the K/S values of the printing fabrics for Ink a, b, c, d, e, f, and g are 4.9, 3.2, 3.5, 4.0, 3.5, 3.1, and 3.0, respectively. It can be seen from the above data that the UV absorption strength of ink b, c, d, e, f, and g is consistent with the K/S value of printed polyester fabric, while Ink a is quite different because it is not filled with polyacrylate emulsion. As listed in Table 5, the dry/wet rubbing fastness and washing fastness (level 3) of printing fabrics generally meet the color fastness requirements. The dry rubbing fastness and washing fastness of the printed fabric with ink a are level 3–4, and the wet rubbing fastness is level 3. However, the dry rubbing fastness and washing fastness of other ink (Ink b–g) printing fabrics are level 4, and the wet rubbing fastness is level 3–4. The results show that there is almost no disperse dye in the soaping solution of printed fabric by UV spectral (Fig. 10a). The reason is that the washing-free disperse dye ink is added with polyacrylate emulsion. When the printing fabric was thermo-fixed at high temperature, the disperse dye is covered by polyacrylate, and a layer of polyurethane film is formed on the surface of the printed fabric (Fig. 10c). The existence of the polyurethane film helps to improve the color fastness of the printed fabric.31
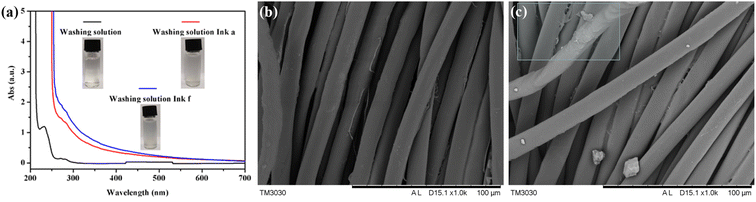 |
| Fig. 10 The UV spectrum of polyester fabric printing soaping (a), SEM image of polyester fabrics (b), and printed polyester fabrics (c). | |
Conclusion
The purpose of this study is to develop high-quality washing-free disperse dye ink and systematically study the quality of the prepared ink. The physical properties of the ink were tested and evaluated. The results showed that the ink's particle size (131.3–147.8 nm), pH value (7.5–7.7), conductivity value (2.9–3.2 mS cm−1), surface tension (38.0–39 mN m−1), viscosity (3.8–4.3 mPa s), and rheological properties (Newtonian fluid) were in line with the requirements of the printing ink. In terms of the evaluation of the stability of the prepared washing-free disperse dye ink, the prepared ink has good weatherability as a whole, without ink delamination, and only Ink c has poor thermal stability and freeze stability. The study on the sensitivity of the viscosity of the prepared ink to temperature shows that the change in the ink temperature has a greater impact on the microstructure of its internal three-dimensional network (polyurethane emulsion). The study on the shear stability of ink indicates that the prepared ink belongs to Newtonian fluid and has good shear stability. The research on the inkjet performance of the prepared ink demonstrated that the prepared ink has good inkjet performance under the condition of driving waveform c (driving voltage, 27.00 V; Td, 3.2 μs; Tf, 2.6 μs). Finally, the influence mechanism of color strength and color fastness of polyester fabrics printed with washing-free disperse dye ink was studied. The experimental data reported that the color strength of printing fabrics is related to the content of disperse dyes in the preparation of inks. The color fastness of the printing fabric is excellent. The reason is that the polyacrylate emulsion contained in the washing-free disperse dye ink can be served as the carrier of the disperse dye and help to fix the disperse dyes. In conclusion, this study provides a theoretical and experimental basis for the preparation and quality research of washing-free disperse dye ink.
Author contributions
Experiment, data analysis, manuscript writing (original draft), funding: Chengyong Gao; funding: Sheng Shi, Hong Guo; manuscript writing (review and editing): Shuhua Wang, Hua Wang, Huirong Zhao, Liangxin Fan.
Conflicts of interest
There are no conflicts to declare.
Acknowledgements
This work was supported by Shanxi Youth Science Research Program (202203021212285, 20210302124492), Science and Technology Innovation Program of Colleges and Universities in Shanxi Province (2022L042) and Fund Program of Taiyuan University of Technology (2022QN081).
References
- T. Carey, S. Cacovich, G. Divitini, J. S. Ren, A. Mansouri, J. M. Kim, C. X. Wang, C. Ducati, R. Sordan and F. Torrisi, Nat. Commun., 2017, 8, 1–11 CrossRef CAS PubMed.
- Z. X. Wang, T. Lowe and B. Derby, ACS Appl. Mater. Interfaces, 2020, 12, 45516–45524 CrossRef CAS PubMed.
- Y. Yang, M. Li and S. H. Fu, Cellulose, 2021, 28, 1843–1856 CrossRef CAS.
- C. Li, L. Fang, K. J. Fang, X. M. Liu, F. F. An, Y. C. Liang, H. Liu, S. Zhang and X. R. Qiao, Langmuir, 2021, 37, 683–692 CrossRef CAS PubMed.
- X. N. Hou, G. Q. Chen, T. L. Xing and Z. Z. Wei, J. Eng. Fibers Fabr., 2019, 14, 1–11 Search PubMed.
- Y. Zhao, M. Li, L. P Zhang, A. L. Tian, Y. Zhang and S. H. Fu, Text. Res. J., 2019, 89, 162–171 CrossRef CAS.
- H. Z. Yang, K. J. Fang, X. M. Liu and F. F. An, ACS Appl. Mater. Interfaces, 2019, 11, 29218–29230 CrossRef CAS PubMed.
- L. Wang, C. Y. Hu and K. L. Yan, Carbohydr. Polym., 2018, 197, 490–496 CrossRef CAS PubMed.
- Y. W. Song, K. J. Fang, M. N. Bukhari, K. Zhang and Z. Y. Tang, J. Mol. Liq., 2021, 324, 114702 CrossRef CAS.
- E. K. Karanikas, N. F. Nikolaidis and E. G. Tsatsaroni, J. Appl. Polym. Sci., 2012, 125, 3396–3403 CrossRef CAS.
- M. Li, L. P. Zhang, D. T. Wang, C. Agbo and S. H. Fu, Color. Technol., 2017, 133, 476–484 CAS.
- G. Yu, B. Tawiah, L. P. Zhang, C. S. Du and S. H. Fu, Colloids Surf., A, 2014, 462, 90–98 CrossRef.
- S. H. Fu, C. S. Du, M. J. Zhang, A. L. Tian and X. Zhang, Prog. Org. Coat., 2012, 73, 149–154 CrossRef CAS.
- S. H. Fu, G. F. Zhang, C. S. Du and A. L. Tian, J. Appl. Polym. Sci., 2011, 121, 1616–1621 CrossRef CAS.
- C. Y. Gao, Y. Zhang, S. Mia, T. L. Xing and G. Q. Chen, Colloids Surf., A, 2021, 609, 125676 CrossRef CAS.
- C. Y. Gao, Z. L. Zhang, T. L. Xing, X. N. Hou and G. Q. Chen, J. Mol. Liq., 2020, 297, 111783 CrossRef CAS.
- S. Magdassi, Ink requirements and formulations guidelines, in The chemistry of inkjet inks, ed. S. Magdassi, World Scientific Ltd, New Jersey, 2008, ch. 2, pp. 35–36 Search PubMed.
- D. Jang, D. Kim and J. Moon, Langmuir, 2009, 25, 2629–2635 CrossRef CAS PubMed.
- C. Y. Gao, T. L. Xing, X. N. Hou, Y. Zhang and G. Q. Chen, J. Cleaner Prod., 2021, 282, 124315 CrossRef CAS.
- C. Y. Gao, X. N. Hou, T. L. Xing and G. Q. Chen, Colloids Surf., A, 2020, 592, 124503 CrossRef CAS.
- C. Y. Gao, T. L. Xing, X. N. Hou and G. Q. Chen, Color. Technol., 2020, 136, 45–59 CAS.
- L. L. Wang, S. S. Cui, H. G. Ni, M. H. Wu and W. Wang, Prog. Org. Coat., 2018, 123, 75–81 CrossRef CAS.
- J. T. Jiang, Y. F. Shen, D. Y. Yu, M. H. Wu, L. Yang and S. Q. Li, Polym. Adv. Technol., 2021, 32, 641–650 CrossRef CAS.
- L. Zhang, Q. Q. Zhou, Q. P. Zhang and M. H. Wu, Fibers Polym., 2021, 22, 396–404 CrossRef CAS.
- L. L. Wang, S. S. Cui, H. G. Ni and M. H. Wu, Text. Res. J., 2019, 89, 2721–2728 CrossRef CAS.
- C. Y. Gao, T. L. Xing and G. Q. Chen, Colloids Surf., A, 2020, 606, 125237 CrossRef CAS.
- M. Yousaf and M. Lazzouni, Dyes Pigm., 1995, 27, 297–303 CrossRef CAS.
- B. Derby, Annu. Rev. Mater. Res., 2010, 40, 395–414 CrossRef CAS.
- J. Park, Y. Hirata and K. Hamada, Dyes Pigm., 2012, 95, 502–511 CrossRef CAS.
- C. Y. Gao, T. L. Xing, X. N. Hou and G. Q. Chen, RSC Adv., 2019, 9, 19791–19799 RSC.
- C. Y. Gao, T. L. Xing and G. Q. Chen, Langmuir, 2020, 36, 14130–14144 CrossRef CAS PubMed.
- K. Zhang, K. J. Fang, W. C. Chen, F. Y. Sun, Y. W. Song and L. Han, ACS Appl. Mater. Interfaces, 2021, 13, 60581–60589 CrossRef CAS PubMed.
|
This journal is © The Royal Society of Chemistry 2023 |
Click here to see how this site uses Cookies. View our privacy policy here.