DOI:
10.1039/D3RA01324C
(Paper)
RSC Adv., 2023,
13, 14097-14101
Synthesis of 2,5-dimethylhexene by isobutene dimerization with H2S co-feeding†
Received
27th February 2023
, Accepted 17th April 2023
First published on 10th May 2023
Abstract
This study investigates the effect of hydrogen sulfide (H2S) co-feeding on the synthesis of 2,5-dimethyl-1-hexene, 2,5-dimethyl-2-hexene, and 2,5-dimethylhexane (2,5-DMHs), useful compounds, using the dimerization of isobutene under mild pressure conditions. The dimerization of isobutene did not proceed in the absence of H2S, whereas the desired products of 2,5-DMHs were produced under H2S co-feeding conditions. The effect of reactor size on the dimerization reaction was then examined, and the optimal reactor was discussed. To enhance the yield of 2,5-DMHs, we changed the reaction conditions of the temperature, molar ratio of isobutene to H2S (iso-C4
/H2S) in the feed gas, and the total feed pressure. The optimum reaction condition was at 375 °C and 2/1 of iso-C4
/H2S. The product of 2,5-DMHs monotonously increased by an increment of total pressure from 1.0 to 3.0 atm with a fixed iso-C4
/H2S ratio at 2/1.
1. Introduction
Isobutene is an essential feedstock for methyl-tert-butyl ether (MTBE), ethyl-tert-butyl ether (ETBE), and isooctane in high-octane gasoline.1–5 However, the requirement for MTBE and ETBE would be decreased year by year owing to the significant decrease in gasoline demand caused by the widespread use of hybrid and electric vehicles and the improvement in fuel efficiency of cars. Therefore, a novel approach to utilize the surplus isobutene is required.
The dimerization of isobutene to produce 2,5-dimethylhexene (2,5-DMH) is an attractive reaction because 2,5-DMH can be selectively converted into aromatics.6–9 Several research studies on the dimerization of isobutene with 2,5-DMH have been reported. Behr et al. reported that a heterogeneous nickel complex catalyst promoted the dimerization of isobutene to produce linearly linked dimers of 2,5-DMH.10 However, the performance of the nickel complex catalyst declined during the reaction. Therefore, improving the stability of the catalyst is an issue for the continuous production of 2,5-DMH. Taubert et al. developed a Bi2O3 catalyst for the oxidative dimerization of isobutene in the presence of oxygen.11 The Bi2O3 catalyst provided a 13% yield of 2,5-DMH with 53% selectivity. Because the oxidation of isobutene produced carbon monoxide and carbon dioxide, the catalyst demonstrated less selective performance by increasing the isobutene conversion.
The activation of the terminal carbon atom in isobutene is necessary to synthesize 2,5-DMH via the dimerization of isobutene. Generally, the terminal activation of isobutene is not expected in conventional carbocation reactions because of the high stability of tertiary cations.2,11 In contrast, the radical reactions can activate the terminal carbon in isobutene because of the high chain reactivity between the radicals and the non-radical species.12–14 Conventionally, azo compounds and organic peroxides such as azo-bis isobutyronitrile (AIBN)15–17 and tert-butyl hydroperoxide,18–20 are used as radical initiators. AIBN decomposes by thermal or photoenergy to produce cyanoisopropyl radicals, which undergo dimerization, disproportionation, and chain reactions to produce various products.21–23 Hydrogen sulfide (H2S) could also be a potential radical initiator for alkyl coupling. Vitzthum et al. determined that the pyrolysis rate of n-butylbenzene accelerated under high-pressure conditions during the pyrolysis of H2S with n-butylbenzene.24 The apparent activation energy of the pyrolysis of n-butylbenzene decreased from 66.6 kcal mol−1 (pure n-butylbenzene) to 55.9 kcal mol−1 (n-butylbenzene in a mixture with H2S). Nguyen et al. reported on the pyrolysis properties of a mixture of n-octane and H2S. Many types of thiols and heavy hydrocarbons were formed in the presence of H2S, owing to the progress of the reaction between the hydrocarbon molecules and the radicals produced from H2S.25 Zeng et al. investigated the interaction of sulfanyl radicals (SH*) with aliphatic (C1–C4) hydrocarbons via calculations using CBS-QB3.26 Regarding hydrogen extraction by SH* from the C–H bond in hydrocarbons, the hydrogen extraction from isobutene was remarkably spontaneous (300–1200 K, ΔrG° < −20 kJ mol−1) owing to weak allylic hydrogen bonds. This study implies that the formation of terminal isobutene radicals may occur in the presence of H2S-derived SH*. Based on these results, we estimated that applying a radical reaction by the coexistence of H2S under high-pressure conditions could promote the formation of terminal radicals derived from isobutene and contribute to the production of 2,5-DMH. In petrochemical industries, hydrodesulfurization is performed to remove sulfur species from sulfur-containing compounds. A large quantity of hydrogen sulfide (H2S) gas is exhausted during this hydrodesulfurization process. The exhausted H2S is generally removed using the well-known Claus process (2H2S + O2 → 2S + 2H2O). However, global sulfur-supply could exceed demand by about several million tons, suggesting the need for a new application of H2S.27 If the expected reaction proceeds with the utilization of H2S, it could lead to new ways of using H2S.
Therefore, this study focused on the synthesis of 2,5-DMHs through the dimerization of isobutene via the activation of the terminal carbon of isobutene in the presence of H2S. The product yield and selectivity were evaluated by changing the reaction conditions, such as temperature, feedstock ratio, and reaction pressure.
2. Experimental
2.1. Reaction apparatus and synthesis conditions
The dimerization of isobutene (iso-C4
) was performed using a batch-type reactor composed of a stainless-steel tube (SUS316) with a total volume of 145 mL. After inert gas has been supplied to the reactor for a sufficient time before dimerization of iso-C4
, reactants were fed at room temperature by the specified feed rate until completely filling the reactor by the reaction gas. After that, the needle valve on the reactor outlet side was closed and the reaction gas was continuously fed until the desired initial pressure was reached and followed by closing the valve on the inlet side. The batch reactor filled with the feed gas was then installed in an electric furnace and the temperature was increased to start the reaction. Specific reaction conditions were the following: the reaction temperature was from 350 to 450 °C; the molar ratio of iso-C4
to H2S (iso-C4
/H2S) was from 1/5 to 5/1; and the total feed pressure was from 1.0 atm to 3.0 atm. The reaction was then performed for 3 h, 6 h and 12 h. The product gases were diluted with nitrogen and then placed in a polyvinyl fluoride gas bag to analyze the gas composition after the reaction. Subsequently, the diluted gas was collected using a micro-syringe and injected into an offline flame ionization detection (FID) gas chromatograph (GC-2014, Shimadzu Corporation, Japan). The iso-C4
conversion and yield of the product (YP) were calculated using the following equations: |
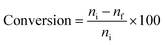 | (1) |
|
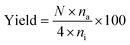 | (2) |
where, ni (mol) represents the material amount in the filled iso-C4
, nf (mol) represents the material amount in the iso-C4
remaining after the experiment, na (mol) represents the amount of product A with carbon number N.
3. Results and discussion
3.1. Effect of co-feeding of sulfur compound on isobutene dimerization
Fig. 1(a) and (b) show the yields and selectivity of product obtained in the dimerization of isobutene (iso-C4
) with and without H2S co-feeding. The reaction was performed at a temperature of 400 °C and iso-C4
/H2S = 1/1, with an initial total pressure of 2.5 atm. Under dimerization conditions without H2S co-feeding, 1,1,3-trimethylcyclopentane (1,1,3-TMCP), 2,2,4-trimethylpentane, and 2,4,4-trimethyl-1-pentene were produced. In contrast, the desired products of 2,5-dimethyl hexane, 2,5-dimethyl-2-hexene, and 2,5-dimethyl-1-hexene, denoted as 2,5-DMHs, were obtained with 4.1% yield and 27.8% selectivity in the dimerization with H2S; isobutane, isobutyl mercaptan (iso-C4SH) tert-butyl mercaptan were generated as byproducts. Nguyen et al. performed out the pyrolysis of n-octane/H2S mixtures and proposed free-radical reaction schemes, which were initiated by the decomposition of H2S into H* and SH* radicals.25 In the present study, the formed radical species H* and SH* could activate the terminal carbon of isobutene to promote dimerization, as expected. Because 1,1,3-TMCP was produced even in the absence of H2S, we followed the 1,1,3-TMCP formation pathway reported by McKinley,28 wherein iso-C4
was dimerized to 1,1,3,3-tetramethylcyclobutane, which was further isomerized to 1,1,3-TMCP under mild temperatures.
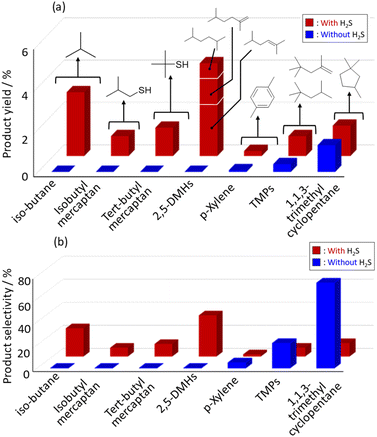 |
| Fig. 1 (a) Yield and (b) selectivity of products in isobutene dimerization with/without H2S (iso-C4 /H2S = 1/1, iso-C4 /N2 = 1/1) at 400 °C and 2.5 atm. | |
Fig. 2 shows the effect of reactor size (reactor #1, reactor #2) on the yield of the products in isobutene dimerization with H2S. Two types of reactors were used to study the dimerization of iso-C4
: reactor #1 has the high-volume and low-surface area (the ratio of surface area to volume of the reactor: 1.8), and reactor #2 has the low-volume and high-surface area (the ratio of surface area to volume of the reactor: 3.7); reactor #2 has approximately twice ratio of surface area/volume in reactor #1. As can be seen in Fig. 2, there is little difference in the 2,5-DMHs of the target product, and the major difference is the amount of isobutane produced. The isobutane is the result of hydrogenation of the raw material iso-C4
. The reactor contains iron component, which progress the following reaction of eqn (3).
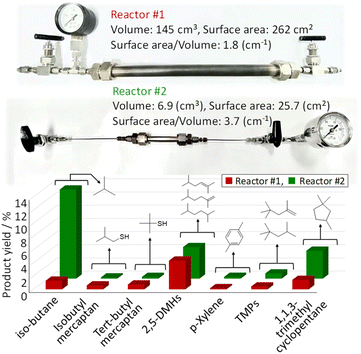 |
| Fig. 2 Effect of reactor size (reactor #1, reactor #2) on the yield of the products in isobutene dimerization with H2S (iso-C4 /H2S = 1/1) at 400 °C and 2.5 atm. | |
ESI data 1† shows XRD pattern of the iron component peeled off from the inner wall of the reactor after dimerization with H2S. The component of FeSx was found to be confirmed. Therefore, the reactor with high surface area/volume might produce high concentration of H2. It was inferred that the isobutane formation was promoted by the increase in H2 concentration via hydrogenation of iso-C4
. The result indicated the optimal reactors with small surface area per volume could reduce the formation of by-product such as isobutane.
The low bond dissociation energy of the R–SH bond of a thiol could allow the formation of radical species, such as alkyl radicals R and SH radicals,29 which could activate iso-C4
to produce 2,5-DMHs. Iso-C4
was dimerized with iso-C4SH to identify the effect of thiols on the production of 2,5-DMHs. Fig. 3 illustrates the yield of the product obtained from the reaction of iso-C4
with the co-feeding of iso-C4SH. The products are similar to those formed by the dimerization of iso-C4
with H2S. 2,5-DMHs were also produced, even in the presence of thiols, although the yield of 2,5-DMHs was lower than that in the presence of H2S. These results indicate that the SH radical species generated from iso-C4SH may activate the terminal carbon of iso-C4
, followed by the production of 2,5-DMHs. The energies of the C–S bonds in alkyl thiols probably be higher compared to those of the S–H bonds in H2S. Thus, the generation of SH radicals by alkyl thiols was expected to lead to a slow dimerization process. Conversely, the dimerization activity is higher in dimerization with the co-feeding of H2S, as shown in Fig. 3. Hydrogen sulfide is known to generate SH* radicals through decomposition of a single molecule and SH radicals through that of two molecules by reverse radical disproportionation (H2S + H2S → H3S* + SH*).25,30,31 It was speculated that the yield of 2,5-DMHs was higher in the dimerization with H2S because of the more efficient generation of radical species from H2S via a direct decomposition of H2S and/or a reverse radical disproportionation than that from iso-C4SH.
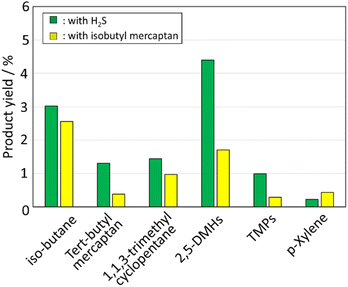 |
| Fig. 3 Product yield in dimerization of isobutene at 400 °C under the condition of 1/1 of iso-C4 (or iso-C4SH)/H2S and 2.5 atm. | |
3.2. Effect of reaction condition on isobutene dimerization
The reaction conditions were optimized to enhance the yield of 2,5-DMHs. Table 1 shows the effect of the iso-C4
/H2S ratios and reaction temperature on the isobutene dimerization. Based on Table 1, the maximum yield of 2,5-DMHs was ca. 4.6%, obtained at 375 °C and iso-C4
/H2S = 2/1. The higher and lower reaction temperatures decreased the yield of 2,5-DMHs. The yield of 2,5-DMHs was 0.7% at a high temperature of 450 °C with iso-C4
/H2S = 2/1; the product yield decreased, except isobutane and 1,1,3-TMCP, as shown in ESI data 2.† In addition, a liquid component was observed in the reactor after the reaction, which significantly decreased the carbon balance to approximately 50%. GC-MS spectrum of liquid product was shown in ESI data 3.† The compound from C5 and C7 compound was mostly included in the liquid product, which was considered to reduce the carbon balance. As for the lower reaction temperature of 350 °C, the product yield decreased under the condition of iso-C4
/H2S = 2/1; the yield of 2,5-DMHs was 1.8%, as shown in ESI data 4.† Therefore, a moderate temperature of approximately 375 °C was considered optimum for the production of 2.5-DMHs. When the molar ratio of iso-C4
/H2S was changed, the 2,5-DMH yield depended on the reaction conditions. Under the condition of iso-C4
/H2S = 1/5 at 375 °C, the yield of 2,5-DMHs was 0.3%, as shown in ESI data 5.† The generation of the low yield of 2,5-DMHs is attributed to the progress in the hydrogenation of iso-C4
to afford isobutane. Excess H2S was used as the H2 source. Such progress of side reaction reduce the effective utilization of iso-C4
for dimerization. Furthermore, the 2,5-DMHs yield increased when iso-C4
/H2S was increased at 375 °C. After reaching the maximum yield, the yield of 2,5-DMHs decreased by an excess feed of iso-C4
. Hence, the feed ratio of iso-C4
/H2S = 2/1 at 375 °C was determined to be the optimum reaction condition. Increasing the feed pressure might produce radical species of SH* by accelerating the reverse radical disproportionation.
Table 1 Effect of reaction conditions of iso-C4
/H2S ratio and reaction temperature on (a) the yield and (b) selectivity of the products in isobutene dimerization
(a) |
Reaction temperature/°C |
i-C4 /H2S ratio |
350 |
375 |
400 |
425 |
450 |
5/1 |
0.95% |
4.00% |
3.28% |
2.11% |
1.0% |
2/1 |
1.83% |
4.58% |
3.32% |
2.40% |
0.67% |
1/1 |
1.52% |
3.29% |
4.05% |
1.26% |
1.16% |
1/2 |
1.83% |
0.95% |
0.88% |
0.51% |
0.20% |
1/5 |
0.33% |
0.31% |
0% |
0% |
0% |
(b) |
Reaction temperature/°C |
i-C4 /H2S ratio |
350 |
375 |
400 |
425 |
450 |
5/1 |
20.6% |
43.6% |
26.7% |
12.6% |
6.0% |
2/1 |
24.3% |
49.0% |
16.7% |
11.8% |
2.7% |
1/1 |
17.7% |
31.5% |
27.8% |
3.3% |
3.5% |
1/2 |
32.0% |
3.9% |
3.7% |
1.1% |
0.4% |
1/5 |
5.1% |
1.3% |
0% |
0% |
0% |
To enhance the yield of desired product (2,5-dimethyl hexane, 2,5-dimethyl-2-hexene, 2,5-dimethyl-1-hexene, and p-xylene), we investigated the effect of reaction time and pressure on the isobutene dimerization. Fig. 4 shows the yield of 2,5-DMHs and p-xylene with reaction time. It could be seen that the yield of the desired product increased with reaction time and reached a steady state at 6 hours of reaction. Fig. 5 illustrates the effect of the initial total feed pressure on the dimerization reaction. The reaction condition was as follows: iso-C4
/H2S was 2/1, the reaction temperature was 375 °C, and the total pressure was from 1.0 atm to 3.0 atm. An increase in the initial total pressure produces higher yield of 2.5-DMHs. No evident relationship between the initial total pressure and product yield was observed for other products. The number of SH* radical species increased when the initial pressure was increased, forming terminal isobutene radicals, which contributed to the increase in 2,5-DMHs. It is not possible to determine whether H2S has catalytic function, based on the obtained results in this study. In future studies, it needs to be clarified whether H2S acts as a reactant or as a molecular catalyst.
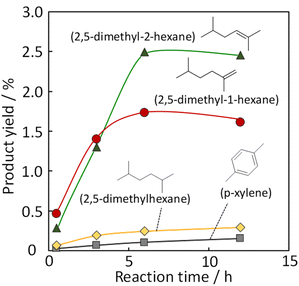 |
| Fig. 4 Product (2,5-dimethyl-2-hexene, 2,5-dimethyl-1-hexene, 2,5-dimethylhexane, p-xylene) yield with reaction time at 375 °C, 2.5 atm and iso-C4 /H2S of 2/1. | |
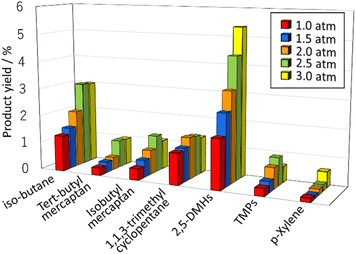 |
| Fig. 5 Effect of the total pressure (1.0–3.0 atm) of feed gas on the product yield under iso-C4 /H2S of 2/1, and 375 °C. | |
4. Conclusions
Isobutene dimerization was tested in a batch-type reactor under high-pressure conditions in the presence of H2S. Dimerization in the absence of H2S did not yield 2,5-DMHs, however, 2,5-DMHs were obtained in the presence of H2S. Then, the dimerization reaction in the presence of H2S was conducted in two reactors with different surface area to volume ratios (surface area/volume). The desired products of 2,5-DMHs were obtained with higher selectivity in the reactor with the smaller surface area/volume. This probably be because the H2 produced by the reaction of H2S with the Fe component in the tube wall largely reacts with isobutene to form the byproduct isobutane. By using the reactor with low surface area/volume, we investigated the effect of reaction conditions (iso-C4
/H2S ratio, temperature, pressure). We found that the yield of 2,5-DMHs was affected by changing the reaction conditions; in particular, the yield of 2,5-DMHs was improved by increasing the pressure. Whether H2S has a catalytic function or not cannot be determined from the results in this study, though, the decomposition of H2S might be accelerated at higher pressures, and generated SH radicals would activate terminal carbon of iso-C4
to promote dimerization.
Conflicts of interest
There are no conflicts to declare.
Acknowledgements
This work was supported by the Uncharted Territory Challenge 2050, New Energy and Industrial Technology Development Organization (NEDO), Japan. Also, this research was supported in part by JSPS KAKENHI (grant number 20K21107).
References
- A. Malaika, P. Rechnia-Gorący, M. Kot and M. Kozłowski, Catal. Today, 2018, 301, 266–273 CrossRef CAS.
- M. G. Yaocíhuatl, H. L. Martín and A. C. Jorge, Catal. Lett., 2006, 110(1), 107–113 CrossRef.
- F. Collignon and G. Poncelet, J. Catal., 2001, 202(1), 68–77 CrossRef CAS.
- L. M. Tau and B. H. Davis, Applied catalysis, 1989, 53(2–3), 263–271 CrossRef CAS.
- S. Talwalkar, M. Chauhan and P. Aghalayam, Ind. Eng. Chem. Res., 2006, 45(4), 1312–1323 CrossRef CAS.
- S. Wang and E. Iglesia, ACS Catal., 2016, 6(11), 7664–7684 CrossRef CAS.
- E. Iglesia and J. E. Baumgartner, Stud. Surf. Sci. Catal., 1993, 75, 993–1006 CrossRef CAS.
- B. H. Davis, Catal. Today, 1999, 53(3), 443–516 CrossRef CAS.
- D. A. Kondrat'ev, T. N. Bondarenko and A. A. Dergachev, Bull. Acad. Sci. USSR, Div. Chem. Sci., 1978, 27(3), 541–545 CrossRef.
- A. Behr, N. Rentmeister and T. Seidensticker, Chem.–Asian J., 2014, 9(2), 596–601 CrossRef CAS PubMed.
- T. Taubert, P. Scholz and B. Ondruschka, Chem. Eng. Technol., 2006, 29(4), 468–472 CrossRef CAS.
- M. Sawamoto and M. Kamigaito, Trends Polym. Sci., 1996, 11(4), 371–377 Search PubMed.
- R. R. Jenkins, Sports Med., 1988, 5(3), 156–170 CrossRef CAS PubMed.
- A. Studer and D. P. Curran, Angew. Chem., Int. Ed., 2016, 55(1), 58–102 CrossRef CAS PubMed.
- K. Murayama, S. Morimura and T. Yoshioka, Bull. Chem. Soc. Jpn., 1969, 42(6), 1640–1643 CrossRef CAS.
- M. Terazima, Y. Nogami and T. Tominaga, Chem. Phys. Lett., 2000, 332(5–6), 503–507 CrossRef CAS.
- J. Xia and K. Matyjaszewski, Macromolecules, 1997, 30(25), 7692–7696 CrossRef CAS.
- R. Edenharder and D. Grünhage, Mutat. Res., Genet. Toxicol. Environ. Mutagen., 2003, 540(1), 1–18 CrossRef CAS PubMed.
- E. C. McLaughlin, H. Choi and K. Wang, J. Org. Chem., 2009, 74(2), 730–738 CrossRef CAS PubMed.
- P. J. Thornalley, R. J. Trotta and A. Stern, Biochim. Biophys. Acta, Gen. Subj., 1983, 759(1–2), 16–22 CrossRef CAS PubMed.
- M. Chen, G. Moad and E. Rizzardo, J. Polym. Sci., Part A: Polym. Chem., 2009, 47(23), 6704–6714 CrossRef CAS.
- S. Li, B. Bruin, C. H. Peng, M. Fryd and B. B. Wayland, J. Am. Chem. Soc., 2008, 130(40), 13373–13381 CrossRef CAS PubMed.
- R. L. Guo, X. Q. Zhu, X. L. Zhang and Y. Q. Wang, Chem. Commun., 2020, 56(63), 8976–8979 RSC.
- V. Burklé-Vitzthum, N. C. L. Guerra and C. Lorgeoux, J. Anal. Appl. Pyrolysis, 2019, 140, 423–433 CrossRef.
- V. P. Nguyen, V. Burklé-Vitzthum, P. M. Marquaire and R. Michels, J. Anal. Appl. Pyrolysis, 2013, 103, 307–319 CrossRef CAS.
- Z. Zeng, M. Altarawneh and I. Oluwoye, J. Phys. Chem. A, 2016, 120(45), 8941–8948 CrossRef CAS.
- T. A. Rappold and K. S. Lackner, Energy, 2010, 35(3), 1368–1380 CrossRef CAS.
- J. B. McKinley and D. R. Stevens, J. Am. Chem. Soc., 1945, 67(9), 1455–1459 CrossRef CAS.
- B. Xing, L. Ye, J. Liu, X. Qin, W. Yu, J. Xie, L. Hou, H. Wang, Y. Ji, D. Lu, J. Zhao, H. Sun and H. Ling, Chem. Eng. J., 2021, 422, 129903 CrossRef CAS.
- V. Kaloidas and N. Papayannakos, Chem. Eng. Sci., 1989, 44(11), 2493–2500 CrossRef CAS.
- K. Karan, A. K. Mehrotra and L. A. Behie, AIChE J., 1999, 45(2), 383–389 CrossRef CAS.
|
This journal is © The Royal Society of Chemistry 2023 |
Click here to see how this site uses Cookies. View our privacy policy here.