DOI:
10.1039/D2RA08302G
(Paper)
RSC Adv., 2023,
13, 4351-4360
Ruthenium ion catalytic oxidation depolymerization of lignite under ultra-low dosage of RuCl3 catalyst and separation of the organic products with inorganic salts
Received
29th December 2022
, Accepted 18th January 2023
First published on 1st February 2023
Abstract
Depolymerization of lignite into valuable chemicals via ruthenium ion catalytic oxidation (RICO) is a potential route for the non-energy utilization of lignite. However, the high cost of the Ru catalyst during depolymerization and the high content of inorganic salts in the product solution limit the development of this route. In this work, RICO depolymerization of lignite was conducted under an ultra-low dosage of RuCl3 catalyst to decrease the usage of the catalyst during the RICO process. Different approaches were attempted to fulfill the separation of benzene polycarboxylic acids (BPCAs) products with the inorganic salts derived from the oxidant NaIO4, including butanone extraction and desalting via crystallization under different temperatures. The results show that lignite can be efficiently depolymerized under the mass ratio of RuCl3/lignite as low as 1/1000 by prolonging the reaction time without decreasing the depolymerization degree and BPCAs yields compared to the commonly used mass ratio of 1/10. Butanone can extract ca. 91% of the total BPCAs in the product solution, and the inorganic salts content (mainly NaIO3) in the extraction solution was as low as 0.19 mg mL−1. A new strategy of first acidification of depolymerization aqueous solution by HCl and then extraction by butanone is proved to be efficient for the separation of BPCAs with inorganic salts. Salting out via crystallization under lower temperature can remove ca. half content of the salts, and the efficiency is inferior to butanone extraction. The low usage of RuCl3 can efficiently decrease the catalyst cost of the RICO process, and butanone extraction can fulfill the enrichment of BPCAs and the separation of BPCAs with inorganic salts. This work is meaningful for the potential application of RCIO depolymerization of lignite for the production of valuable chemicals.
Introduction
Coal is an important fossil resource and has played significant roles in the development of the Chinese industrial economy.1 Lignite accounts for about 41.2% of China's coal reserves,2 and its characteristics of high moisture and volatile matter make it unable to be widely used in traditional utilization modes such as combustion, pyrolysis, gasification, and liquefaction like middle–high rank coal.3–8 With the continuous consumption of high rank coal, the utilization of low rank coal with high H/C ratio and high oxygen-containing functional groups becomes more and more important.9 Therefore, how to use the low rank coal more efficiently and cleanly has become an important issue.
The typical representative of low-rank coal is lignite, which is abundant in aromatic ring structures, making lignite potential as raw materials for the production of high value-added benzene polycarboxylic acids (BPCAs).9 Thermal extraction by organic solvent and oxidative depolymerization are typical procedures for the transformation of lignite into valuable chemicals. Extraction of lignite with organic solvent CS2 shows that lignite is also rich in aliphatic hydrocarbon structure, which also provides the possibility of its degradation into small molecular fatty acids.10 There are many oxidation methods for the preparation of carboxyl chemicals by oxidation depolymerization, such as alkali-oxygen oxidation,11 sodium hypochlorite oxidation,13,14 nitric acid oxidation,15 catalytic O2 oxidation,16 H2O2 oxidation,17,18 ruthenium ion catalytic oxidation,22–25 etc. Alkali-oxygen oxidation method can obtain various small molecular fatty acids and BPCAs.12 However, the reaction conditions are relatively harsh, requiring high temperature, high pressure, and a large amount of acid and alkali, which is difficult to recover and unfriendly to the environment. In the sodium hypochlorite oxidation process, besides the water-soluble fatty acids and a large number of BPCAs, many chlorinated products are also produced, and the depolymerization of lignite is not complete.29 Liu et al.19 investigated that the pretreatment of Shengli lignite with H2O2 before sodium hypochlorite oxidation could significantly improve the yield of fatty acids and BPCAs, and the generation of chloro-substituted alkanoic acids was inhibited. However, the price of the oxidant was high and limited the application of this route. For nitric acid oxidation, the strongly oxidative and corrosive nitric acid is used, which limit its large scale application. For catalytic O2 oxidation, Yang et al.20,21 proposed the oxidation method using NaVO3, Fe2(SO4)3, and FeCl3 as co-catalyst and O2 as oxidant. Although the reaction avoids the use of a large number of inorganic acids and bases, the reaction conditions are not mild, still under high temperature and high pressure, and the carbon yield is low. For ruthenium ion catalytic oxidation (RICO), the reaction conditions are relatively mild typically under 35 °C. Lv et al.26 studied the aromatic species structure of Huolinguole lignite by RICO, and found that the soluble species mainly consist of alkanedioic acids while BPCAs mainly contain carboxylic acids with less than four carboxylic groups. Due to the mild reaction condition and high efficiency in the depolymerization, RICO exhibits high potential for the application in the depolymerization of lignite.
However, the high cost of the precious ruthenium catalyst limits the development and application of RICO. In our previous study, the efficient recycling procedure of the homogeneous ruthenium catalyst using CCl4 extraction was established.27 It was proved that the ruthenium catalyst could be reused for at least 5 times with no obvious decrease of the BPCAs yields. The dosage of the ruthenium catalyst in the reported work is often high, with mass ratio of RuCl3/lignite as high as 1
:
10, which makes it impossible to be adopted in real application. Together with the reuse of the ruthenium catalyst, decreasing the usage of the ruthenium catalyst is another route to cut the cost of the catalyst in RICO. Besides the high cost of the catalyst, another bottleneck for RICO is that the high usage of the oxidant NaIO4 leads to the formation of large amount of NaIO3, which causes troubles in the separation of the target products and the formation of salt-containing wastewater. Therefore, studies concerning RICO under low-dosage of the ruthenium catalyst and the separation of inorganic salt from organic products are highly desired.
In this work, the RICO depolymerization efficiency of lignite under ultra-low dosage of the ruthenium catalyst was studied. The depolymerization degree and BPCAs yields were analyzed under different dosage of the ruthenium catalyst. After depolymerization, the separation of organic products with the inorganic salt was studied using different routes, including salting out28 under different temperatures and butanone extraction. The results showed that lignite could be efficiently depolymerized even under ultra-low dosage of the ruthenium catalyst with the mass ratio of RuCl3/lignite 1/1000 compared to the commonly used 1/10, with depolymerization degree and total BPCAs yields up to 87% and 8.9%, respectively. Among the studied separation routes, butanone extraction is the most efficient in both removing the inorganic salt and enriching the BPCAs products. This work provides basic data for promoting the development of RICO depolymerization of lignite for the production of valuable organic acids.
Material and methods
Materials
Raw Shengli lignite (RSL), from Inner Mongolia Shengli Coalfield in China. Ruthenium(III) chloride (RuCl3, AR, 99.5%), sodium periodate (NaIO4, AR, 99.5%), sodium iodate (NaIO3, AR, 99.5%), acetonitrile (CH3CN, AR, 99.5%), carbon tetrachloride (CCl4, AR, 99.5%) were purchased from Innochem. Butanone was distilled before use. The distillation procedure is as followings: The purchased butanone is placed in a round-bottom flask and heated at 100 °C in an oil bath connected to a distillation device, and the system is sealed to prevent butanone volatilization out of the system. Other solvents (except butanone) used in the experiments are analytical grade reagents and directly used as received without further treatment.
RICO depolymerization reaction
As shown in Fig. 1, RSL (5 g), RuCl3 (0.5 g, 0.05 g, 0.005 g), NaIO4 (100 g), and CCl4
:
CH3CN
:
H2O with volume ratio of 2
:
2
:
3 (total volume, 700 mL) were put into a 1000 mL spherical flask. The mixture was allowed to react with magnetic stirring under the temperature (35 °C) and different reaction time (0–139 h). After the reaction, the reaction mixture was filtered to obtain filter cake and filtrate, and the filtrate was separated by phase separation to obtain organic phase and aqueous phase. The target small molecules such as BPCAs exist in the aqueous phase. The filter cake is washed with distilled water until it is clear. The purpose is to remove the sodium iodate salt and sodium periodate salt as well as humic acid. The residual solid phase is then placed in a 105 °C air drying oven for approximately 12 h. The mass ratio of RuCl3 to lignite was varied, i.e. 1
:
100 and 1
:
1000, respectively.
where the mass of organic matter in lignite = mass of lignite-mass of ash-mass of moisture.
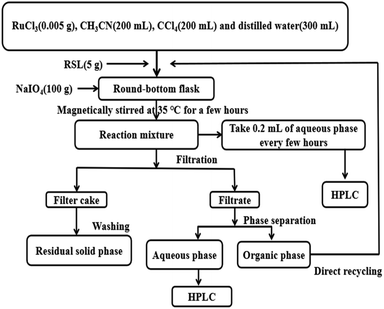 |
| Fig. 1 Procedure of the RICO reaction, subsequent sample treatment, and the recycling of the Ru-containing solvent. | |
Separation of BPCAs with inorganic acids
Butanone extraction was adopted to separate BPCAs from the mixture and fulfill the separation of organic products with the inorganic salt. The aqueous phase was extracted three times with equal volume of butanone. After extraction, butanone was removed via rotary evaporation under reduced pressure and 40 °C. Then the obtained depolymerized product powder was dried in a drying oven at 105 °C to prevent the presence of residual butanone. Finally, the depolymerized product powder was diluted with distilled water to the same volume as the water after depolymerization. The extraction phase was analyzed by HPLC to calculate the contents of BPCAs. The extracted phase was subjected to ICP-MS to determine the content of sodium ions.
Besides butanone extraction, crystallization under low temperatures was also attempted to fulfill the removal of the inorganic salt. As shown in Fig. 2, before crystallization, certain volume of the depolymerized aqueous solution was taken and condensed to different volume by rotary evaporator to improve the concentration of inorganic salts, and partial inorganic salts were crystallized and removed. Then the solution was stored under different temperatures, i.e. room temperature, 4 °C and −7 °C for 2–3 h. The precipitate was removed by centrifugation. The precipitated salts were dried, weighed, and characterized by XRD. The precipitated salts were also solubilized in water and analyzed by HPLC and TOC to test the residue of BPCAs and the total organic carbon.
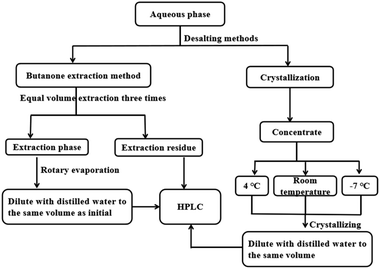 |
| Fig. 2 Different procedures of removing inorganic salts in the depolymerized solution. | |
Analysis and characterization method
The BPCAs in the depolymerized product was determined by HPLC(SHIMADZU LC-20AT).30 A binary gradient elution procedure was used for HPLC analysis. The mobile phase was acetonitrile and 0.1% (volume fraction) phosphoric acid aqueous solution, and the stationary phase was C18 bonded to silica gel (Shim-pack GIST C18, 5 mm). The BPCAs were quantified using a UV detector at 235 nm. The cylinder temperature was 45 °C, and the flow rate of the mobile phase was 0.8 mL min−1. The gradient elution procedure was as follows: at the beginning, the volume ratio of acetonitrile to aqueous solution was 5
:
95, the ratio linearly increased to 15
:
85 over 10 min and then remained unchanged for 20 min, and finally, the ratio was decreased to 5
:
95 over 2 min. The structures of typical BPCAs obtained from RICO reaction of lignite are shown in Scheme 1. The salts precipitated by the crystallization method were analyzed by XRD. XRD was performed on a Japan-Science SmartLab-9 kW diffractometer with a scanning range of 5–90° at a rate of 10° min−1. The total carbon (TC), total organic carbon (TOC), and total inorganic carbon (TIC) in the depolymerization solution and salt precipitated by crystallization were analyzed on Total Organic Carbon Analyzer (SHIMADZU TOC-L VCPN).
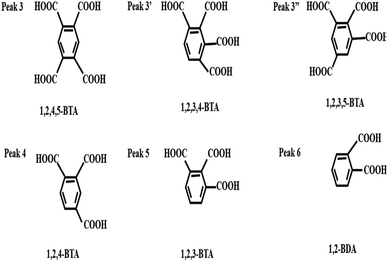 |
| Scheme 1 The typical structures of BPCAs obtained from the depolymerized products via RICO of lignite. | |
Results and discussion
Comparison of the raw and demineralized lignite
The RICO depolymerization efficiency of raw lignite and demineralized lignite were compared. The content of inherent minerals in lignite was analyzed in our previous work.27 For comparison, the raw lignite was demineralized before depolymerization according to our previous report to check the effect of minerals on the depolymerization and subsequent separation.31 The results were shown in Fig. 3. The differences in the yields of several typical BPCA products were not obvious for the raw and demineralized lignite (Fig. 3a). This result indicates that the inherent minerals in lignite have no significant effect on the yields of BPCAs during RICO depolymerization of lignite. Butanone extraction experiment shows that the extraction yields of different BPCAs have no obvious difference for the raw and demineralized lignite (Fig. 3b). These results show that the inherent minerals have no obvious effects on the depolymerization. Besides, the demineralization of the lignite requires a large amount of hydrochloric acid, leading to the formation of a large amount of wastewater containing acid and organic matter. Therefore, the raw lignite was directly used in the following studies.
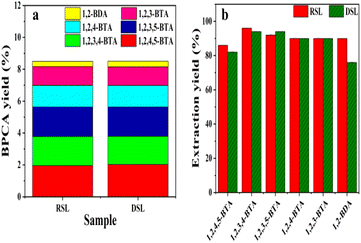 |
| Fig. 3 The BPCA yield (a) and extraction yield of each BPCA (b) in the RICO of the raw lignite (RSL) and demineralized lignite (DSL). Reaction conditions: lignite sample 0.4 g, CCl4 20 mL, CH3CN 20 mL, H2O 30 mL, RuCl3/lignite mass ratio 1/10.0, NaIO4/lignite mass ratio 20.0/1, 35 °C, 6 h (a); RICO depolymerized aqueous phase (30 mL), constant volume of butanone (30 mL), extract for 1 h each time, three times (b). | |
Depolymerization of lignite under different RuCl3 dosage
In order to decrease the usage of RuCl3 and study the dosage of RuCl3 on the depolymerization efficiency of lignite via RICO process, the mass ratio of RuCl3 to lignite was decreased from the commonly used 1
:
10 to 1
:
100 and 1
:
1000, respectively. The reaction time was prolonged under low RuCl3 dosage. Different from the common reports, the initial amount of lignite is scaled up ten times, which can increase the amount of BPCAs in the depolymerized products because large amount of the depolymerized products was required in the following separation. The results were shown in Fig. 4. The depolymerization degree increased to around 90% in a short reaction time, indicating the high efficiency of RICO in the depolymerization of lignite (Fig. 4a). The total yields of BPCAs came to 9.0% when the initial amount of demineralized Shengli lignite (DSL) was 0.4 mg. The yields of BPCAs can also reach more than 8% after the initial amount of RSL was amplified to 5.0 g (Fig. 4b). The total content of BPCAs changed little after 15 hours, and the highest yields of BPCAs occurred at the reaction time of 27 hours. When the mass ratio of RuCl3/lignite decreased to 1
:
100, both the depolymerization degree and the total yields of BPCAs increased gradually (Fig. 4c and d). Compared to the mass ratio of RuCl3/lignite 1
:
10, the increase of depolymerization degree and the total yield of BPCAs became slower, but similar level could be achieved by prolonging the reaction time. The depolymerization yield can reach to 89% at reaction time of 24 h, and the total yield of BPCAs comes to 8.8% at the reaction time of 56 h. Further decreasing the mass ratio of RuCl3/lignite to 1
:
1000, with the extension of time, the depolymerization degree can also reach to nearly 87% at the reaction time of 120 h, and the total yield of BPCAs gradually increased until 115 hours to the maximum 8.9%. Another interesting phenomenon is that the increasing of the depolymerization degree is fast, while the increasing of the BPCAs yields is relatively slow. This is due to that lignite was first converted to humic acid macromolecules and then BPCAs during RICO reaction.34 Lignite was first converted to humic acid macromolecules together with small amount of BPCAs, and this step was fast, leading to the fast increasing of the depolymerization degree. Humic acid macromolecules were further converted into BPCAs, but this step was slow, leading to the slow increasing of the BPCAs yields. In the Fig. 4a, c and e, the amount of catalyst RuCl3 has a great influence on the depolymerization degree of lignite. When other conditions are the same, the less the catalyst amount, the lower the depolymerization degree, and only by extending the reaction time can we achieve similar depolymerization levels. In the Fig. 4b, d and f, the yield of BPCAs under the condition of different dosage of RuCl3 and different time was studied. With the increasing of reaction time, the yield of BPCAs gradually increased and reached the maximum at a certain time. Subsequently, the acid yields tended to decrease, which is because the further increase of time may lead to the excessive oxidation of BPCAs, and the yields of BPCAs will decrease.32 These results show that decreasing the mass ratio of RuCl3/lignite has no obvious influence on the final depolymerization effect of lignite, only requiring a longer reaction time. Therefore, decreasing the mass ratio of RuCl3/lignite is an efficient and potential approach to cut the catalyst cost of RICO depolymerization of lignite.
 |
| Fig. 4 Effect of the reaction time on the depolymerization degree of lignite (a, c and e) and BPCA yields (b, d and f) under different dosage of RuCl3. Reaction conditions: RSL 5 g, CCl4 200 mL, CH3CN 200 mL, H2O 300 mL, NaIO4/lignite mass ratio 20.0/1, 35 °C, (a and b) RuCl3/lignite mass ratio 1/10, (c and d) RuCl3/lignite mass ratio 1/100, (e and f) RuCl3/lignite mass ratio 1/1000. | |
Comparison of desalting methods for the depolymerized supernatants
In the depolymerized supernatants, large amount of NaIO3 exists due to the reduction of NaIO4 as oxidant for RuCl3 during RICO reaction, and the residual NaIO4 also exists in the product solution. How to fulfill the removal of these inorganic salts and the separation of inorganic and organic components is a critical issue for the separation of target products. In this work, butanone extraction and desalting under different temperatures are used and compared to remove the inorganic salt and recycle the BPCAs products. As shown in Fig. 5, NaIO3 and NaIO4 indeed exist in the depolymerization solution with a total sodium concentration as high as 12.5 mg mL−1 (Table 1).
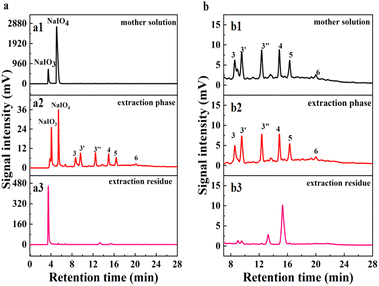 |
| Fig. 5 HPLC profile of the depolymerized products from RSL. Profiles (b) are the enlarged view of the corresponding profiles (a) with retention time from 7 to 28 minutes. Separation conditions: extract the supernatant three times with an equal volume of butanone reagent. | |
Table 1 Sodium content in desalting methodsa
Method of removing salt |
Sodium content after desalting (mg mL−1) |
Desalination efficiency (%) |
Conditions: the volume was condensed from 40 mL to 8 mL. Storing time under different temperature: 3 h. |
Mother solution |
12.5 mg mL−1 |
|
Room temperature |
8.5 mg mL−1 |
32.0 |
4 °C |
5.9 mg mL−1 |
52.8 |
−7 °C |
5.8 mg mL−1 |
53.6 |
Butanone extraction |
0.19 mg mL−1 |
98.5 |
The separation of BPCAs with the inorganic salt NaIO3 and NaIO4 is a critical step for the production of BPCAs from lignite by RICO. Therefore, how to separate BPCAs from the inorganic salts was studied. In the depolymerized solution (mother solution), there are high concentration of NaIO3 and NaIO4, which makes the signal intensity of BPCAs in HPLC profiles rather weak (Fig. 5a1). After extraction, no obvious NaIO4 was detected in the residual solution, but it was detected in the extraction phase (Fig. 5a2 and a3). This result shows that NaIO4 can be extracted by butanone together with BPCAs, which brings difficulties in the separation of BPCAs. The results also show that butanone can extract BPCAs efficiently (Fig. 5b1–b3). The total extraction yield of BPCAs can reach 91% after 3 subsequent extraction with equal volume butanone (Fig. 1b). The sodium residue in butanone phase was 0.19 mg mL−1 by ICP analysis (Table 1). In order to study the distribution behavior of NaIO3 and NaIO4 in the butanone and aqueous phase, the simulated solution of sodium iodate and sodium periodate with a molar ratio of 1
:
1 was prepared and extracted by butanone (Fig. 6a). It can be seen that butanone can indeed extract NaIO4 in the aqueous solution, while the extraction of NaIO3 was much less. Next, the simulated solution of sodium iodate and sodium periodate was acidified with 1 mol L−1 HCl solution to pH 1.5 (consistent with the conditions before butanone extraction of depolymerization supernatant). The acidified simulated salt solution was extracted three times with the same volume of butanone, the results was shown in Fig. 6b. It was found that no NaIO4 existed in both extraction phase and extraction residue, indicating NaIO4 was converted into NaIO3 under the presence of HCl. XRD analysis of the inorganic salts was conducted to prove the transformation of NaIO4 to NaIO3 (Fig. 7). After acidification, typical diffraction peaks of NaIO3 appear, indicating NaIO4 can be converted to NaIO3 by the addition of HCl. However, the diffraction peak of NaIO4 still exists, which may be due to that the amount of HCl was not enough to convert NaIO4. The peak for NaIO3 in the extraction phase is very weak, which further proved that butanone cannot extract NaIO3 from aqueous solution. These results give an efficient route for the separation of BPCAs from the aqueous solution containing inorganic salts. The depolymerization solution can be first acidified using HCl solution to convert the residual NaIO4 into NaIO3, and then butanone extraction can be used to extraction BPCAs from the solution. This route can fulfill the separation of BPCAs with the inorganic salts. Based on our previous report,33 the first two peaks in the HPLC diagram are the peak of benzene hexacarboxylic acid and benzene pentacarboxylic acid. These results provides an efficient route for the separation of BPCAs with the inorganic salts after RICO depolymerization of lignite.
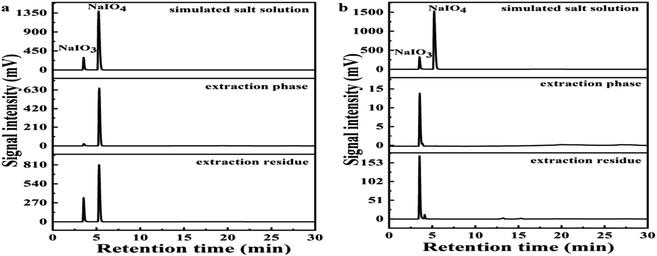 |
| Fig. 6 HPLC profile of the simulated salt solution of sodium iodate and sodium periodate (a) and the simulated salt solution of sodium iodate and sodium periodate acidified by HPLC (b). Reaction conditions: extract the solution three times with an equal volume of butanone reagent. Conditions for the acidification of the simulated solution: the simulated solution of sodium iodate and sodium periodate with a molar ratio of 1 : 1; pH < 1.5; extract the simulated solution three times with an equal volume of butanone. | |
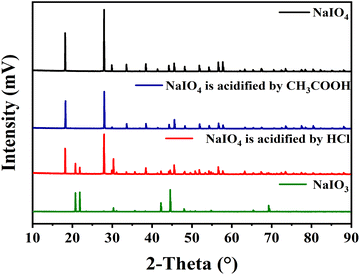 |
| Fig. 7 A comparison diagram of XRD patterns of NaIO4 after acidification by HCl or CH3COOH. | |
Besides butanone extraction, the desalting at different temperatures were attempted and compared to butanone extraction. The temperatures attempted for desalting are set at room temperature, 4 °C and −7 °C, respectively. The supernatant after concentration was stored under the above temperatures and white precipitate appeared after certain time. XRD analysis of the precipitate proves that the components of the precipitate are NaIO3 and NaIO4 (Fig. 8). NaIO4 was provided excessively and the residual NaIO4 was maintained in the solution after depolymerization, while NaIO3 was derived from the reduction of NaIO4 when oxidizing Ru3+ to RuO4. In order to investigate the effect of concentration volume on the efficiency of salt removal and the loss of BPCAs. As shown in Fig. 9a, when the depolymerization solution was concentrated to a smaller volume, the signal of the inorganic salts in the residual solution became weak, indicating higher efficiency of salt removal. However, a smaller concentrated volume also led to higher loss of BPCAs (Fig. 9b). Therefore, the volume of depolymerization supernatant was finally concentrated to around 1/5 of the original volume. The desalting efficiency under different temperatures with the prolonging of storing time is shown in Fig. 10. The desalting efficiency under −7 °C is better than that under room temperature and 4 °C. Before 80 min, the desalting efficiency under 4 °C is similar to that under room temperature, but further prolonging the storing time can promote the desalting efficiency, which is close to that under −7 °C. The residual salts after desalting and the desalting efficiency for different methods are summarized in Table 1. It can be seen that butanone extraction has the highest desalting efficiency. For the desalting via crystallization, the desalting efficiency under the temperature of 4 °C and −7 °C is similar. Considering the energy consumption, 4 °C seems to be the optimal temperature via crystallization.
 |
| Fig. 8 XRD of the salt precipitated from the depolymerized supernatant after concentration by rotary evaporation and stored under 4 °C for 3 h. | |
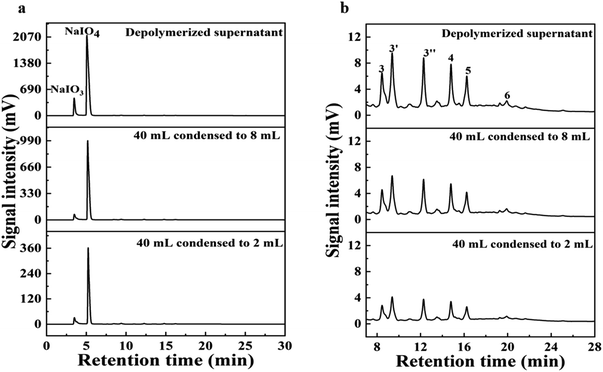 |
| Fig. 9 The HPLC profiles of the depolymerization aqueous solution concentrated to different final volumes. Separation conditions: −7 °C, 1 h. | |
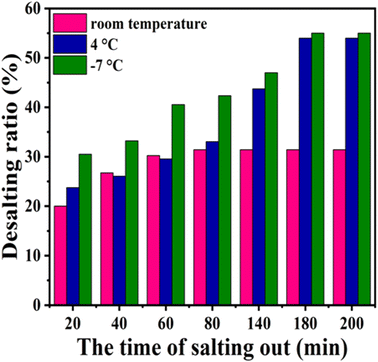 |
| Fig. 10 The desalting efficiency via crystallization under different temperature conditions, the change of desalting ratio with time. Conditions: the volume was condensed from 40 mL to 8 mL. | |
In order to analyze the BPCAs loss during crystallization, the precipitate was solubilized in water and analyzed by HPLC. HPLC profiles shows that there are weak peaks of BPCAs besides the strong peaks of NaIO3 and NaIO4 (Fig. 11). The contents of BPCAs in the precipitate were given in Table 2. These results show that there are small amount loss of BPCAs during the desalting via crystallization, which may be due to that BPCAs were entrained into the precipitate salt crystals during the formation of the precipitate. The content of total organic carbon(TOC) in the precipitated salt (4 °C) is about 2.25 mg g−1. This result indicates that the precipitated salt may contain other organic matter such as humic acid derived from lignite depolymerization besides the residual BPCAs. In our previous report,34 it was also found that lignite was first converted to humic acid macromolecules together with small amount of BPCAs, and the humic acid macromolecules were further converted to BPCAs. Some humic acid macromolecules cannot be depolymerized by RICO and maintained in the solution.
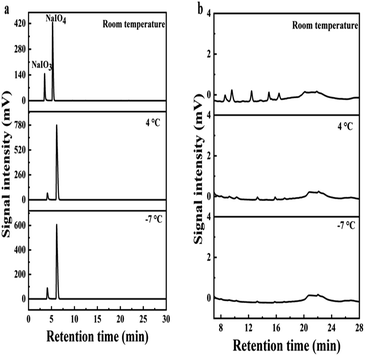 |
| Fig. 11 The HPLC profile of salts precipitated at room temperature, 4 °C and −7 °C. (b) is an enlarged view of (a) with retention time from 7 to 28 minutes. The salt precipitated was dissolved in 100 mL distilled water. | |
Table 2 The residual amounts of BPCAs in the precipitated inorganic saltsa
BPCA |
The content of BPCAs in the precipitated salt (mg g−1) |
The loss ratio of BPCAs (%) |
Conditions: 4 °C, 2.27 g salt was dissolved in 100 mL distilled water. |
1,2,4,5-BTA |
0.014 |
0.5 |
1,2,3,4-BTA |
0.007 |
0.3 |
1,2,3,5-BTA |
0.004 |
0.2 |
The recycling ratios of BPCAs during butanone extraction and crystallization under different temperatures are compared (Fig. 12). It can be seen that butanone extraction has the highest recycling ratio of BPCAs, and the total recycling ratio can reach to 91%. The total recycling ratio of BPCAs for desalting by crystallization under 4 °C can reach to 73%. The desalting by crystallization under different temperatures has the slight loss of BPCAs in the precipitate. As discussed above, the desalting efficiency of butanone extraction is much higher than that of crystallization. Though it has high recycling ratios of BPCAs and high desalting ratio, butanone extraction suffers the use of organic solvent butanone. Comparatively, the desalting by crystallization can avoid the use of organic solvent butanone. Therefore, the two routes have their unique characteristics in future potential applications.
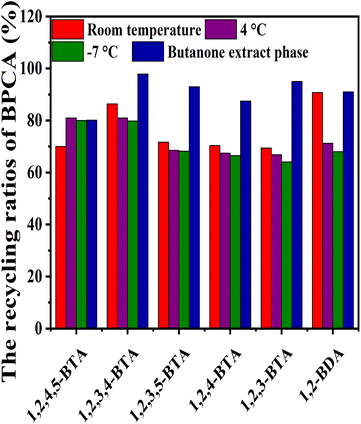 |
| Fig. 12 Comparison of the recycling ratios of BPCAs under different conditions. Separation conditions: RICO depolymerized aqueous phase (30 mL), constant volume of butanone (30 mL), extract for 1 h each time, three times; for the crystallization method, the volume was condensed from 30 mL to 6 mL, 3 h. | |
Conclusions
In summary, RICO depolymerization of lignite under a low dosage of RuCl3 catalyst was conducted, and the separation of BPCAs products with the inorganic salts using different approaches were compared. The results show that the mass ratio of RuCl3/lignite can be decreased to as low as 1/1000 without obvious decrease in depolymerization degree and BPCAs yields compared to the commonly used mass ratio of 1/10 just by prolonging the reaction time. Butanone extraction is an efficient way to enrich the BPCAs products with extraction ratio of total BPCAs as high as 91%. The residual NaIO4 can be transformed to NaIO3 under the presence of HCl. A new strategy of first acidification of depolymerization aqueous solution by HCl and then extraction by butanone is proved to be efficient for the separation of BPCAs with inorganic salts. Thus butanone extraction can also fulfill the separation of BPCAs with the inorganic salts. The shortcoming of butanone extraction is the use of organic solvent. Salting out via crystallization under lower temperature can remove ca. half content of the salts, and the efficiency is inferior to butanone extraction. The crystallization under low temperature can remove partial inorganic salts with slight loss of BPCAs in the salt precipitate. Besides, the concentration process of the depolymerization solution is required before crystallization to improve the desalting efficiency, indicating higher energy consumption during crystallization. Therefore, the two separation routes have their own advantages and disadvantages considering real application. From aspects of the recycling ratios of BPCAs and the desalting efficiency, butanone extraction is superior to the crystallization under low temperature. This work is meaningful to promote the separation of the valuable BPCAs from the depolymerization production solution during the potential application of RCIO depolymerization of lignite.
Conflicts of interest
There are no conflicts to declare.
Acknowledgements
This work was supported by the National Natural Science Foundation of China (21968021, 21868021), Science Fund for Distinguished Young Scholars of Inner Mongolia (2022JQ04), Program for Grassland Elite in Inner Mongolia, CAS “Light of West China” Program, Local Science and Technology Development Fund Projects Guided by the Central Government (2020ZY0010), Science and Technology Planning Project of Inner Mongolia Autonomous Region (2020GG0289), Major Science and Technology Projects of Inner Mongolia Autonomous Region (2021ZD0020), the Startup Fund for New Teachers of Inner Mongolia University of Technology (IMUT) (BS2021018), and the Science and Research Projects of IMUT (ZY202004).
Notes and references
- H. F. Shui, Z. Y. Cai and C. B. Xu, Recent advances in direct coal liquefaction, Energies, 2010, 3, 155–170 CrossRef.
- Z. H. Rao, Y. M. Zhao and C. L. Huang, et al., Recent developments in drying and dewatering for low rank coals, Prog. Energy Combust. Sci., 2015, 46, 1–11 CrossRef.
- Z. Y. Niu, G. J. Liu and H. Yin, et al., Devolatilization behaviour and pyrolysis kinetics of coking coal based on the evolution of functional groups, J. Anal. Appl. Pyrolysis, 2018, 134, 351–361 CrossRef CAS.
- Y. Man, S. Y. Yang, D. Xiang and X. X. Li, et al., Environmental impact and techno-economic analysis of the coal gasification process with/without CO2 capture, J. Cleaner Prod., 2014, 71, 59–66 CrossRef CAS.
- Z. Q. Ouyang, W. Liu and J. G. Zhu, et al., Flameless combustion behaviour of preheated pulverized coal, Can. J. Chem. Eng., 2018, 96, 1062–1070 CrossRef CAS.
- P. Jaramillo, W. M. Griffin and H. S. Matthews, Comparative life-cycle air emissions of coal, domestic natural gas, lng, and sng for electricity generation, Environ. Sci. Technol., 2007, 41, 6290–6296 CrossRef CAS PubMed.
- J. H. Wu, J. Z. Liu and X. Zhang, et al., Chemical and structural changes in XiMeng lignite and its carbon migration during hydrothermal dewatering, Fuel, 2015, 148, 139–144 CrossRef CAS.
- Z. K. Li, X. Y. Wei and H. L. Yan, et al., Advances in lignite extraction and conversion under mild conditions, Energy Fuel, 2015, 29, 6869–6886 CrossRef CAS.
- F. Yang, Y. C. Hou and W. Z. Wu, et al., The relationship between benzene carboxylic acids from coal via selective oxidation and coal rank, Fuel Process. Technol., 2017, 160, 207–215 CrossRef CAS.
- A. Tahmasebi, Y. Jiang and J. L. Yu, et al., Solvent extraction of Chinese lignite and chemical structure changes of the residue during H2O2 oxidation, Fuel Process. Technol., 2015, 129, 213–221 CrossRef CAS.
- T. Lu, G. Y. Li and W. Z. Wu, et al., Alkali-oxygen oxidation mechanism for producing benzene carboxylic acids from lignite: Experimental and molecular modelling studies, Fuel, 2020, 280, 118652 CrossRef CAS.
- W. H. Wang, Y. C. Hou and W. Z. Wu, et al., Simultaneous production of small-molecule fatty acids and benzene polycarboxylic acids from lignite by alkali-oxygen oxidation, Fuel Process. Technol., 2013, 112, 7–11 CrossRef CAS.
- G. Z. Gong, X. Y. Wei and Z. M. Zong, et al., Separation and analysis of the degradation products of two coals in aqueous NaOCl solution, J. Fuel Chem. Technol., 2012, 40, 1–7 CrossRef CAS.
- Z. H. Jing, S. Rodrigues and E. Strounina, et al., Use of FTIR, XPS, NMR to characterize oxidative effects of NaClO on coal molecular structures, Int. J. Coal Geol., 2019, 201, 1–13 CrossRef CAS.
- F. C. Liu, S. J. Xing and Z. Y. Du, Nitric acid oxidation for improvement of a Chinese lignite as soil conditioner, Commun. Soil Sci. Plant Anal., 2011, 42, 1782–1790 CrossRef CAS.
- F. Yang, J. Sun and R. Zheng, et al., Oxidation of toluenes to benzoic acids by oxygen in non-acidic solvents, Tetrahedron, 2004, 60, 1225–1228 CrossRef CAS.
- Y. K. Xiong, L. J. Jin and Y. Li, et al., Hydrogen peroxide oxidation degradation of a low-rank Naomaohu coal, Fuel Process. Technol., 2020, 207, 106484 CrossRef CAS.
- F. G. Liu, Z. M. Zong and J. Gui, et al., Selective production and characterization of aromatic carboxylic acids from Xianfeng lignite-derived residue by mild oxidation in aqueous H2O2 solution, Fuel Process. Technol., 2018, 181, 91–96 CrossRef CAS.
- F. J. Liu, X. Y. Wei and Y. Zhu, et al., Oxidation of Shengli lignite with aqueous sodium hypochlorite promoted by pretreatment with aqueous hydrogen peroxide, Fuel, 2013, 111, 211–215 CrossRef CAS.
- F. Yang, Y. C. Hou and M. G. Niu, et al., Catalytic oxidation of lignite to carboxylic acids in aqueous H5PV2Mo10O40/H2SO4 solution with molecular oxygen, Energy Fuels, 2017, 31, 3830–3837 CrossRef CAS.
- L. J. Gong, Y. C. Hou and W. Z. Wu, et al., Catalytic O2 oxidation of lignite to carboxylic acids with iron-based catalysts in acidic aqueous solutions, Fuel Process. Technol., 2019, 191, 54–59 CrossRef CAS.
- Z. K. Li, X. Y. Wei and H. L. Yan, et al., Effect of ethanolysis on the structure and pyrolytic reactivity of Zhaotong lignite, Energy Fuels, 2017, 31, 10768–10774 CrossRef CAS.
- F. J. Liu, X. Y. Wei and J. Gui, et al., Characterization of organonitrogen species in Xianfeng lignite by sequential extraction and ruthenium ion-catalyzed oxidation, Fuel Process. Technol., 2014, 126, 199–206 CrossRef CAS.
- J. X. Hao, L. M. Han and K. L. Yang, et al., A general route of using lignite depolymerized derivatives for catalyst construction: insights into the effects of the derivative structures and solvents, ACS Omega, 2021, 6, 14926–14937 CrossRef CAS PubMed.
- S. Murata, Y. Tani and M. Hiro, et al., Structural analysis of coal through RICO reaction: detailed analysis of heavy fractions, Fuel, 2001, 80, 2099–2109 CrossRef CAS.
- J. H. Lv, X. Y. Wei and Y. Qing, et al., Insight into the structural features of macromolecular aromatic species in Huolinguole lignite through ruthenium ion-catalyzed oxidation, Fuel, 2014, 128, 231–239 CrossRef CAS.
- X. F. Yao, X. L. Wang and Y. X. Chen, et al., Reusability investigation of a ruthenium catalyst during ruthenium ion-catalyzed oxidative depolymerization of lignite for the production of valuable organic acids, ACS Omega, 2021, 6, 26613–26622 CrossRef CAS PubMed.
- Y. Q. Sun, L. Yan and H. X. Fu, et al., Salting-out extraction and crystallization of succinic acid from fermentation broths, Process Biochem., 2014, 49, 506–511 CrossRef CAS.
- Y. G. Wang, X. Y. Wei and H. L. Yan, et al., Sequential oxidation of Jincheng No. 15 anthracite with aqueous sodium hypochlorite, Fuel Process. Technol., 2014, 125, 182–189 CrossRef CAS.
- J. X. Hao, H. C. Zhou and Q. S. Liu, et al., Metal ion-induced separation of valuable organic acids from a depolymerized mixture of lignite without using organic solvents, RSC Adv., 2020, 10, 3479 RSC.
- Y. M. Song, F. Wei and Q. S. Liu, et al., Effects of demineralization on the structure and combustion properties of Shengli lignite, Fuel, 2016, 183, 659–667 CrossRef CAS.
- F. Yang, Y. C. Hou and M. G. Niu, et al., Catalytic oxidation of lignite to carboxylic acids by molecular oxygen in an aqueous FeCl3 solution, Fuel, 2017, 202, 129–134 CrossRef CAS.
- Z. W. Ding, Q. Liu and H. C. Zhou, et al., Alkaline earth metal ions mediated coordination separation of valuable organic acids from depolymerization products of lignite, Fuel, 2022, 322, 124083 CrossRef CAS.
- Y. L. Zhang, H. C. Zhou and Q. S. Liu, et al., Structural evolution of lignite from heterogeneous particles to homogeneous products during ruthenium ion catalytic oxidation depolymerization, Fuel, 2023, 332, 126092 CrossRef CAS.
|
This journal is © The Royal Society of Chemistry 2023 |
Click here to see how this site uses Cookies. View our privacy policy here.