DOI:
10.1039/D2RA07954B
(Paper)
RSC Adv., 2023,
13, 2418-2426
Ni loaded SnS2 hexagonal nanosheets for photocatalytic hydrogen generation via water splitting†
Received
13th December 2022
, Accepted 7th January 2023
First published on 16th January 2023
Abstract
Herein we have prepared the Ni-decorated SnS2 nanosheets with varying concentrations of Ni from 1 to 10 mol% (1, 2.5, 5, and 10 mol%) and studied their various physicochemical and photocatalytic properties. The chemical reduction technique was utilized to load the Ni nanoparticles on SnS2 nanosheets. The synthesized Ni decorated SnS2 (denoted as Ni-SnS2) was characterized using different spectroscopic techniques such as X-ray diffraction, diffuse reflectance UV-vis and photoluminescence spectroscopy, field emission scanning electron microscopy (FESEM), and field emission transmission electron microscopy (FETEM). XRD revealed the formation of the highly crystalline hexagonal phase of SnS2 but for nickel loading there is no additional peak observed. Further, the as-prepared Ni-SnS2 nano-photocatalyst shows absorption behaviour in the visible region, and photoluminescence spectra of the Ni-SnS2 nanostructures show band edge emission centred at 524 nm, and the peak intensity decreases with Ni loading. The FE-SEM and FE-TEM confirm the formation of hexagonal sheets having evenly distributed Ni nanoparticles of size ∼5–10 nm. BET surface area analysis was observed to be enhanced with Ni loading. The photocatalytic performance of the prepared Ni-SnS2 nanosheets was evaluated for hydrogen generation via water splitting under a 400 W mercury vapour lamp. Among the prepared Ni-SnS2 nanostructures, the Ni loaded with 2.5 mol% provided the highest hydrogen production i.e., 1429.2 μmol 0.1 g−1 (% AQE 2.32) in four hours, almost 1.6 times that of pristine SnS2 i.e., 846 μmol 0.1 g−1. Furthermore, the photocatalytic performance of the catalyst is also correlated with the photoconductivity by measuring the photocurrent. The photoconductivity of the samples is revealed to be stable and the conductivity of 2.5 mol% Ni-SnS2 is higher i.e. 20 times that of other Ni-SnS2 and pristine SnS2 catalysts.
1 Introduction
In the world of science and technology, the increasing energy demand and rapid depletion of fossil fuels are becoming major issues in the present scenario.1,2 So, the need for the development of alternate clean, renewable energy sources is an area that has received significant attention from the scientific community. Sunlight and water are abundantly available in nature and can be utilized to produce H2 via water splitting.3–6
Solar energy is one of the cleanest sources of energy. Many different technologies such as photovoltaic cells and photochemical water splitting can be used to harness solar energy. It is believed that the photo-assisted water-splitting reaction on the semiconductor surface is one of the most promising technologies for hydrogen production and provides direct conversion of sunlight into chemical fuels.7–10 In 1972 the pioneering report by Fujishima and Honda on photoelectrochemical (PEC) water splitting on a TiO2 photo-electrode attracted wide and continual research interest for the development of environmentally friendly, and stable photocatalysts.11–13 This photocatalytic water splitting using nanostructured semiconductor offers a low-cost eco-friendly approach for sustainable hydrogen production.
The nanostructured semiconductors' metal oxides and chalcogenides are playing a vital role in the photocatalysis technique. For having higher photocatalytic performance, the semiconductor catalyst must have an optimum bandgap, optimum energy positions, and chemical as well as biologically stable nature.14–20 Over the last two-three decades, the use of nanostructured semiconductor materials especially TiO2, ZnO, SnO2, ZnS, SnS2, MoS2, CdS, CeO2, Ta2O5, Nb2O5, SrTiO3, etc. has been used as a potential photocatalyst.21–45 However, the conversion efficiency of photon energy into H2 of the studied photocatalytic materials is limited by the factors such as poor absorption ability of the visible light, fast recombination of photoexcited charge carriers, low surface catalytic reaction efficiency, poor stability, etc. Since from a few decades, researchers have proposed many different strategies or routes to overcome these restrictions, including co-catalyst loading, crystal facet engineering, construction of different surface morphology with porous structure, band gap engineering, and construction of homo or hetero-junctions (binary, ternary), etc.46–60 To avoid the recombination of charge carriers, noble metal nanoparticles have been widely used as efficient co-catalysts decorated on semiconductor photocatalysts. Many researchers have reported that noble metal NPs, such as Au, Pt, Ag, Rh, Ni-Pt, Pd, Cu-Pd, and Au-Pd have been reported resulting in enhanced overall photocatalytic activity by enhancing the electron–hole charge separation.61–71
In this regard, SnS2 nanostructures were synthesized by hydrothermal method and were in situ decorated with Ni as a co-catalyst having different concentrations of Ni i.e., 1 mol%, 2.5 mol%, 5 mol%, and 10 mol% through a simple thermal reduction method. The detailed physico-chemical characterisation and influence of Ni loading on SnS2 towards its photocatalytic performance were investigated.
2 Experimental section
2.1 Materials
Stannic(IV) chloride (SnCl4·5H2O) was purchased from Otto Chemicals Pvt. Ltd, thiourea (CH4N2S) from Qualigens fine chemicals, ethylenediamine (EDA) (C2H8N2), nickel chloride from Fischer Scientific, ethylene glycol (EG) Merck Life Science Pvt Ltd, and hydrazine hydrate were purchased from Sisco Research Laboratories Pvt Ltd. All chemicals were used such as without further purification.
2.2 Synthesis of tin disulphide
The SnS2 hexagonal nanosheets were synthesized as per the previously reported method.33 In a typical experimental procedure, 10 mmol (3.5 g) of stannic chloride was dissolved in 30 ml of distilled water in a beaker, while 40 mmol (3.04 g) of thiourea were dissolved in 30 ml of distilled water in another beaker and stirred for 10–20 min at room temperature. Thiourea solution was then added dropwise into stannic chloride solution with constant stirring for 10 min. After that, 7.5 mmol (0.5 ml) of EDA was added to the solution with constant stirring for 5 minutes. Then the transparent reaction mass was transferred into a Teflon-lined stainless-steel autoclave, sealed, and heated at 200 °C for 24 h. Upon further completion of the reaction, the autoclave was naturally cooled down to room temperature, and a yellow product was obtained. The obtained sample was rinsed several times with distilled water followed by ethanol and collected by centrifugation and then dried at 60 °C in a vacuum oven and used for further characterizations.
2.3 Ni nanoparticles loading on SnS2 nanosheets
The Ni-loaded SnS2 nanosheets (Ni-SnS2) were prepared as follows: for 1 mol% loading firstly, 0.053 g of nickel chloride and hydrazine hydrate 0.53 ml was dissolved in 60 ml EG in a 250 ml beaker and stirred for 30 min. Second, as prepared SnS2 nanosheets were suspended into the suspension and stirred for 30 min to disperse the nanoparticles. Then 1 M aqueous NaOH solution was added dropwise into the suspension and stirred for 60 min at 60 °C. The obtained product was washed several times with distilled water followed by ethanol wash and collected by centrifugation and then dried at 60 °C in a vacuum oven for 24 hours. The same reaction was followed for loading of Ni with 2.5, 5 and 10 mol% respectively.
2.4 Materials characterization
Powder X-ray diffraction (XRD) analysis of the as-prepared samples was carried out using Bruker AXS D8 Advanced model equipped with a monochromator and Ni-filtered Cu Kα radiation (wavelength = 1.5418 Å) in the 2θ range of 10° to 70° with the scan rate of 1° min−1. Diffuse reflectance UV-visible absorbance spectra (DRS) were recorded at room temperature in the range of 200–800 nm using the Shimadzu UV-vis-NIR spectrophotometer (Model UV-3600). The morphology of the as-synthesized samples was observed using a field-emission scanning electron microscope (FESEM, HITACHI S-4800). The high-resolution TEM (HRTEM) and selected area electron diffraction (SAED) were also recorded using JEOL JEM-200FS FETEM. The BET surface area of the prepared SnS2 and Ni-SnS2 nanostructures were calculated from the N2 adsorption isotherms at liquid N2 temperature using the Quantachrome NOVATouch LX1 instrument. The sample was degassed in a vacuum at 120 °C for 2 h prior to the BET analysis.
2.5 Photocatalytic activity measurement
The photocatalytic activity of the prepared nanostructures was carried out by observing H2 generation via water splitting.
2.5.1 H2 generation. The photocatalytic hydrogen evolution via water splitting over prepared SnS2 and Ni-SnS2 nanostructures was performed as per the previously reported method.23 The cylindrical quartz vessel reactor (100 ml size) was used for photocatalytic H2 generation. The system was sealed with a septum arrangement to remove the evolved gas through a gas-tight syringe for quantifying the amount of gases evolved. The mercury vapour lamp (400 W) fitted in a quartz condenser having water circulation arrangement in order to absorb the iR radiation to minimize the heating effect was used as a light source. For photocatalytic activity measurements, 20 mg of the catalyst with 1 wt% preloaded platinum as a co-catalyst was dispersed into 25 ml distilled water and 5 ml methanol solution. Further, 0.1 M Na2S and 0.1 M Na2SO3 were added as a sacrificial agent in the above solution. In order to remove the dissolved gases, nitrogen gas was purged through this mixture for 30 min. After purging the nitrogen gas through the reaction vessel, it is kept under the mercury vapor lamp, and analyzed the evolved gases after an interval of one hour, using a gas chromatograph (Shimadzu: Model GC 2014) equipped with 5 Å molecular sieves column. The amount of hydrogen generation was calculated according to the fitted standard curve.
2.5.2 Photoconductivity measurement. Additionally, we have investigated the photoconductivity of synthesized SnS2 and Ni-SnS2 nanostructures. For photoconductivity measurement, SnS2 and Ni-SnS2 powder films were deposited on a pre-patterned silver inter-digited electrode printed on 96% alumina (substrate) with an inter-electrode spacing of 100 μm and a total path length of 25 mm. The deposited electrodes were directly used for I–V measurement. The measurements were performed using a Kelvin probe connected to spring-loaded pressure contacts at room temperature. The entire setup was maintained in the metallic chamber (shield) in order to reduce the electrical noise effect. I–V measurements were carried out using Keithley 4200 semiconductor characterization system (SCS) integrated with a photo-emission system (1000 W Xenon lamp and 1.5 AM (air-mass) ratio).
3 Results and discussion
3.1 X-ray diffraction analysis
In order to reveal the crystal structure of the as-synthesized SnS2 and Ni-SnS2 nanostructures, an X-ray diffraction analysis was conducted and depicted in Fig. 1.
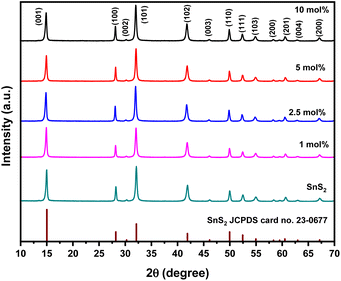 |
| Fig. 1 XRD pattern of pure SnS2, 1 mol% Ni-SnS2, 2.5 mol% Ni-SnS2, 5 mol% Ni-SnS2 and 10 mol% Ni-SnS2. | |
It can be seen that the XRD pattern exhibits diffraction peaks at 2θ = 15, 28.1, 30.2, 32.1, 41.8, 46.1, 49.9, 52.4, 54.9, 58.3, 60.6, 62.9, 67.1, 70.3 and 77.4° coincide with (001), (100), (002), (101), (102), (003), (110), (111), (103), (200), (201), (004), and (202) planes of pure SnS2 having a hexagonal crystal structure, respectively. The peaks in the XRD patterns shows the formation of the hexagonal phase of SnS2 (JCPDS card no. 23-0677). Because of the high crystallinity of SnS2 nanosheets, no distinct diffraction peaks of Ni can be found in the XRD patterns of the as-synthesized Ni-SnS2 composites. XRD pattern of pristine and recycled 2.5 mol% Ni-SnS2 is also appeared to be same indicating the stability of catalyst even after three recycles (Fig. S1 ESI†). However, the existence of metallic Ni in the as-synthesized Ni-SnS2 composites was confirmed by XPS analysis.
3.2 UV-visible diffuse reflectance spectroscopy (UV-DRS) analysis
UV-vis-DRS of the as-synthesized pristine SnS2 and Ni-SnS2 with different Ni concentrations (depicted in Fig. 2) were measured to evaluate their band gap as well as photo-absorption behaviour. The pristine SnS2 and different concentrations of Ni-SnS2 both show an absorbance edge around 550 nm corresponding to the optical band gap of 2.4 eV, also confirmed by the Tauc's plot (shown in Fig. 3). There was no noticeable change observed in the absorption edge with the increment in nickel content. This indicates that nickel was just deposited on the surface instead of being fused into the lattice structure of SnS2.
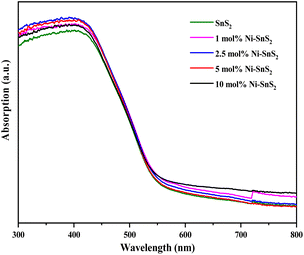 |
| Fig. 2 UV-DRS Spectra of pure SnS2, 1 mol% Ni-SnS2, 2.5 mol% Ni-SnS2, 5 mol% Ni-SnS2 and 10 mol% Ni-SnS2. | |
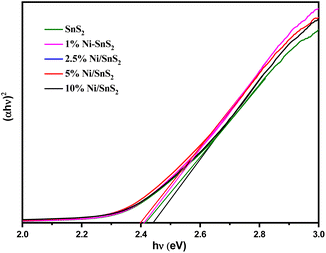 |
| Fig. 3 Tauc's spectra of pure SnS2, 1 mol% Ni-SnS2, 2.5 mol% Ni-SnS2, 5 mol% Ni-SnS2 and 10 mol% Ni-SnS2. | |
3.3 Photoluminescence study
The PL spectra of synthesized SnS2 and Ni-loaded SnS2 nanosheets having different Ni concentrations were obtained with an excitation wavelength of 350 nm and are shown in Fig. 4. The PL spectra of SnS2 as well as Ni-SnS2 nanosheets, show strong emission peaks centred at ∼525 nm. The band edge emission for SnS2 was observed to be around 525 nm and this peak shifts to 540 nm with increasing Ni loading. Additionally, as evident from the PL graph, the intensity of the emission peak of pristine SnS2 and Ni-SnS2 decreases with increment in Ni concentration and it is lowest for the sample with 10 mol% loading of Ni. This slaking might be due to the presence of Ni nanoparticles on the surface of SnS2 nanosheets and confirms the transfer of photogenerated electrons from the conduction band of SnS2 to Ni nanoparticles.
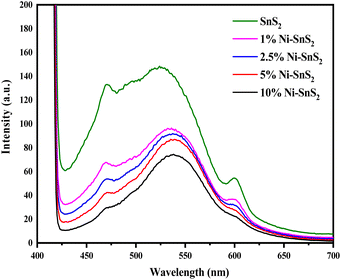 |
| Fig. 4 Photoluminescence spectra of pure SnS2, 1 mol% Ni-SnS2, 2.5 mol% Ni-SnS2, 5 mol% Ni-SnS2 and 10 mol% Ni-SnS2. | |
3.4 X-ray photoelectron study
The XPS survey spectrum depicts in Fig. 5a reveals that the as-synthesized 2.5 mol% Ni-SnS2 nanostructures consist of Sn, S and Ni. Fig. 5b–d represent the high-resolution deconvoluted XPS spectrum of Sn 3d, S 2p and Ni 2P for Ni-SnS2 nanostructures. Further the XPS of pristine SnS2 is also depicted in Fig. S2 (ESI†). The high-resolution Sn 3d core-level spectrum shows two prominent peaks at binding energies of 486.73 and 495.15 eV corresponding to the Sn 3d5/2 and Sn 3d3/2 levels respectively. The high-resolution spectrum of S depicts in Fig. 5c contains peaks at 161.59 and 162.80 eV binding energy that corresponds, respectively, to S 2p3/2 and S 2p1/2 levels. The binding energy values observed for Sn 3d and S 2p spectra are in good agreement with Sn4+ and S2− of SnS2. Additionally, the major peaks with binding energies of 856 and 854.28 eV are corresponding to Ni3+ as well as Ni2+ respectively (Fig. 5d). It has been observed that over the time metallic Ni get oxidized by losing electron and may easily generates high valence state Ni viz., +2 and +3. In the prepared nanostructures the presence of Ni along with Ni oxide on SnS2 were confirmed using XPS analysis.72
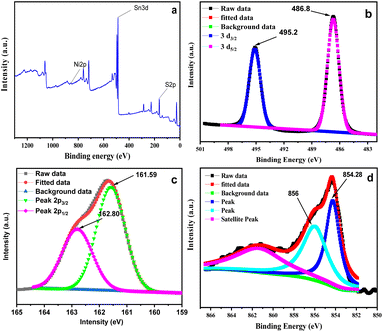 |
| Fig. 5 (a) Survey XPS spectrum of Ni-SnS2, (b) high-resolution XPS spectra of Sn 3d, (c) S 2p, (d) Ni 2p. | |
3.5 Morphological and nano-structural analysis
3.5.1 FE-SEM analysis of pure SnS2 and Ni-SnS2. FE-SEM micrographs of synthesized SnS2 and Ni-SnS2 nanostructures are shown in Fig. 6. The FE-SEM image indicates the formation of two-dimensional hexagonal nanosheets having size in the range of 400 to 600 nm with thickness of 20 to 30 nm. The EDA is used as the capping agent to form SnS2 nanostructure in such a way that, it results in the formation of plate-like structure and directing two-dimensional growths. The Ni loading with varying concentrations was deposited on SnS2 surface by the thermal reduction method. The FE-SEM of Ni-loaded SnS2 also shows the same morphology as pure SnS2 and some spherical particles were observed on the surface of SnS2 sheets that might be of Ni. As the mole percentage of Ni increases the small spherical nanoparticles of Ni are observed on SnS2 nanosheets. At the maximum loading of 10 mol% of Ni-loaded SnS2 nanosheets, a chunk of Ni nanoparticles is observed on the surface of SnS2. Overall, the Ni nanoparticles are uniformly distributed over the SnS2 surface.
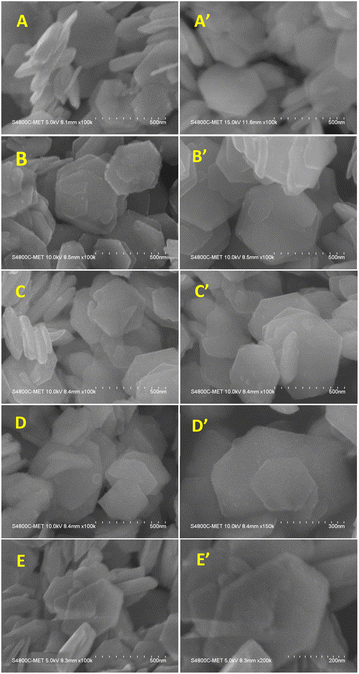 |
| Fig. 6 FESEM images of SnS2 and Ni-SnS2 nanosheets, (A and A′) pure SnS2 nanosheets, (B and B′) 1 mol% Ni-SnS2, (C and C′) 2.5 mol% Ni-SnS2, (D and D′) 5 mol% Ni-SnS2, (E and E′) 10 mol% Ni-SnS2. | |
3.5.2 FE-TEM analysis of pure SnS2 and Ni-SnS2. The orientation and distribution of Ni nanoparticles on the surface of SnS2 nanosheets were observed by FE-TEM analysis of a 2.5 mol% Ni-SnS2 sample shown in Fig. 7. The Fig. 7a and b shows the formation of uniformly distributed hexagonal shaped plates having the size in the range 300–500 nm along with homogeneous distribution of smaller Ni and NiO nanoparticles on the surface of SnS2 nanosheets. The HR-TEM image shown in Fig. 8c exhibits the interplanar spacing of d = 0.278 nm, 0.203 nm and 0.241 nm corresponds to (101), (111) and (111) hkl planes of SnS2, Ni and NiO nanostructures respectively. The size of Ni and NiO nanoparticles was observed as 5–10 nm. The HR-TEM analysis clearly indicates the presence of cubic Ni along with NiO nanoparticles uniformly distributed over hexagonal SnS2 surface. The Ni nanoparticles may get oxidised to form the NiO. The SEAD (selective area electron diffraction) with a hexagonal phase of SnS2. The diffraction spots can be indexed as (101) (111) and (100) planes confirming the main exposed facets of hexagonal SnS2. TEM associated elemental mapping analysis further confirmed the even distribution of Sn, and S within Ni-SnS2 (Fig. 7e–g). Further, the presence of Ni nanoparticles is displayed by the corresponding elemental mapping image as shown in Fig. 7h, while the overall distribution of Ni, Sn and S is substantiated in their overlap elemental mapping (Fig. 7i). Thus, FE-TEM analysis validates the XRD, and FESEM results and confirmed the formation of highly crystalline 2D SnS2 nanoplates with a homogeneous distribution of Ni and NiO nanoparticles on the surface of SnS2 nanosheets. Further the FETEM EDAX analysis for the 2.5 mol% Ni-SnS2 shows the loading of 2.18 wt% Ni over the SnS2 (Fig. S6†).
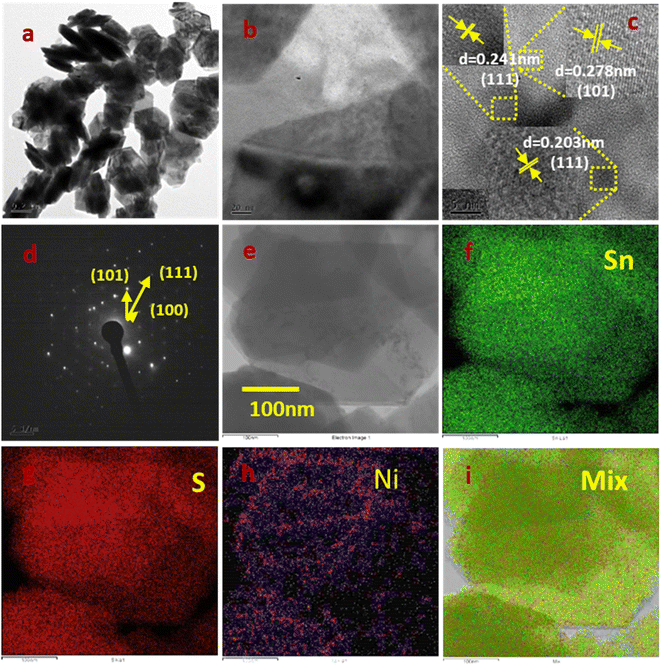 |
| Fig. 7 FETEM images of 2.5 mol% Ni-SnS2; (a, b and e) low magnification images, (c) HR-TEM image, (d) SAED pattern, (e–i) elemental mapping images of Ni-SnS2. | |
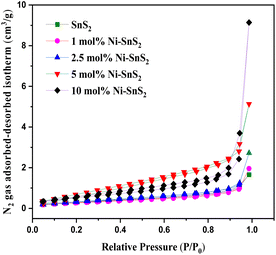 |
| Fig. 8 BET N2 gas adsorbed–desorbed isotherm curve of sample SnS2 and Ni-SnS2. | |
3.5.3 BET surface area analyser. The BET surface area and the porosity of the prepared SnS2 and Ni-SnS2 were investigated. Fig. 8 shows the nitrogen adsorption–desorption isotherm curves of pristine SnS2 and Ni-SnS2 nanostructures. The BET surface area of SnS2 and 1 mol% Ni-SnS2, 2.5 mol% Ni-SnS2, 5 mol% Ni-SnS2, 10 mol% Ni-SnS2 is observed as 7.8, 8.1, 10.2, 14.1, 18.4 m2 g−1 respectively. Therefore, as the Ni concentration on the surface of SnS2 nanosheets increases, the surface area of the photocatalyst also increases, this indicates that the loading of Ni nanoparticles is beneficial for the rise of the surface area of the catalyst. The pore size of the SnS2 and Ni-SnS2 nanostructure (Fig. 9) showed different levels of pores. The SnS2 and Ni-SnS2 nanostructures had a pore diameter less than 10 nm with a maximum diameter of ∼6 nm indicating that are mesoporous in nature.
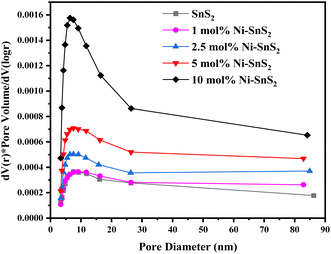 |
| Fig. 9 BJH pore size distribution curves of pristine SnS2, 1 mol% Ni-SnS2, 2.5 mol% Ni-SnS2, 5 mol% Ni-SnS2, 10 mol% Ni-SnS2. | |
3.6 Photocatalytic activity measurements
The investigation of photocatalytic H2 generation occurred by as-synthesized SnS2 and Ni-SnS2 nanosheets with different concentrations of Ni loading are depicted in Fig. 10. The 2.5 mol% Ni-SnS2 showed the highest H2 generation around 1429.2 μmol 0.1 g−1 within four hours of irradiation times. The Ni-SnS2 with Ni amounts of 1 mol%, 5 mol%, 10 mol%, and pristine SnS2 generates 850.09 μmol, 855.45 μmol, 848.67 μmol, and 843.75 μmol of hydrogen gas per 0.1 g of catalysts respectively shown in Table 1. The 2.5 mol% of Ni-SnS2 concentration showed almost 1.68 times higher photocatalytic activity as compared to pristine SnS2. Among the other concentrations of Ni-SnS2, the 2.5 mol% Ni-SnS2 shows the highest photocatalytic activity due to the generation of a large number of electron–hole pairs and its effective electron–hole pair separation. As nickel nanoparticles concentration increases more than 2.5 mol% loading, the Ni nanoparticles covers the effective surface of SnS2 nanosheets results in a shading effect and results in lowering the photocatalytic activity. For comparison of photocatalytic activity, the % apparent quantum efficiency (AQE) is also calculated (Table 1) and found to be around 2.32% for the 2.5 mol% Ni-SnS2. To support the effective charge generation, we have carried out the photoconductivity measurements of all the prepared catalysts.
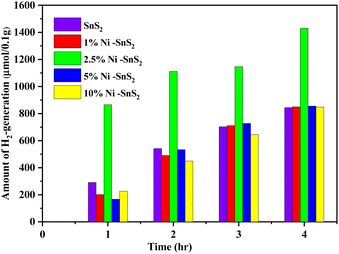 |
| Fig. 10 Photocatalytic H2 generation using pure SnS2, 1 mol% Ni-SnS2; 2.5 mol% Ni-SnS2, 5 mol% Ni-SnS2 and 10 mol% Ni-SnS2. | |
Table 1 Surface area, H2-generation, apparent quantum efficiency using prepared SnS2, Ni-SnS2 nanostructures
S. no. |
Sample code |
BET surface area (m2 g−1) |
H2 generation (μmol 0.1 g−1) in 4 h |
% [AQE]a |
The % AQE calculated using the H2 generation values for 0.1 g catalyst per h.75 |
1 |
SnS2 |
7.8 |
843.75 |
1.36 |
2 |
1 mol% Ni-SnS2 |
8.1 |
850.09 |
1.37 |
3 |
2.5 mol% Ni-SnS2 |
10.2 |
1429.2 |
2.32 |
4 |
5 mol% Ni-SnS2 |
14.1 |
855.45 |
1.38 |
5 |
10 mol% Ni-SnS2 |
18.4 |
848.67 |
1.37 |
The recycling study of the catalyst is an important parameter to find out the stability and reusability of the catalyst. For this purpose, the Ni-SnS2 that exhibits higher photocatalytic activity (2.5 mol% Ni-SnS2) was recycled three times for H2 generation. After each cycle, the catalyst was separated from the suspension by centrifugation, washed with deionized water and ethanol, dried and weighted for the next cycle. Fig. S5† shows the recycling performance for the 2.5 mol% Ni-SnS2 nanoplates in photocatalytic H2 generation. During the recycling study the catalyst shows some loss of catalytic performance for third cycle, this might be due to the loss of catalyst during the washing process. After third recycle, the amount of H2 generated is around 1160.12 μmol of H2, 0.1 g−1 in 4 h of irradiation of time. This was clearly indicating that the synthesized Ni-SnS2 have good photocatalytic stability. There is no change observed in surface morphology confirmed by the FESEM and FE-TEM analysis (Fig. S3 and S4†) of 2.5 mol% Ni-SnS2 nanoplates before and after water splitting reaction under 400 W mercury vapor lamp for three cycles respectively.
3.7 Mechanism of photocatalytic H2 generation of prepared Ni-SnS2 nanostructures
The schematic of the mechanism of photocatalytic H2 generation is shown in Fig. 11. Upon irradiation of the Ni-SnS2 nanostructures by light, electrons are excited from the valence band (VB) to the conduction band (CB), leaving holes in the valence band. The photoexcited electrons and holes are migrated to the surface of these semiconductors, further, the electrons in the conduction band initiate the reduction of H+ to generate hydrogen and the holes oxidizes water to generate oxygen.
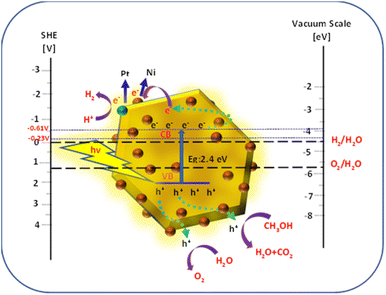 |
| Fig. 11 Schematic of band energy levels of Ni-SnS2 nanostructures for photocatalytic H2 generation/relative to the redox potential of water.73,74 | |
For H2 evolution, the CB potential of the catalyst must be more negative than the reduction potential of water. Providing an easy pathway for photogenerated electrons and holes for migrating towards reaction sites present on the surface. This decreases the recombination probability and enhances photocatalytic efficiency. In the present case of Ni-SnS2, improved activity with Ni loading may be due to the effective electron accepter property of Ni. The CB level of SnS2 is −0.61 V above the H2 evolution potentials. The photoexcited electrons from CB of SnS2 can migrate to Ni nanoparticles due to potential gradient and then react with H+ ions produced by oxidation of water to form H2. The Ni is having more electron affinity and its energy level is just −0.23 V more negative than the H2 evolution potential. Due to this, it easily captures the photogenerated electrons and is used further for H2O reduction. Further, Ni on SnS2 nanosheets can form the Schottky barrier and facilitates electron capture for H2 generation. Beyond the optimized loading, the activity was found to be decreased.
3.8 Photoconductivity measurement
Photoconductivity measurements of pure SnS2 and Ni-SnS2 nanosheets were performed in air at room temperature with a bias voltage from −5 V to +5 V under the illumination of solar simulator light to record the photo-induced effect. The I–V characteristics for pure SnS2 and Ni-SnS2 nanosheets under light are depicted in Fig. 12. Under the illumination of solar simulator light, linear changes in photocurrent are observed in pristine SnS2 and Ni-SnS2 samples.
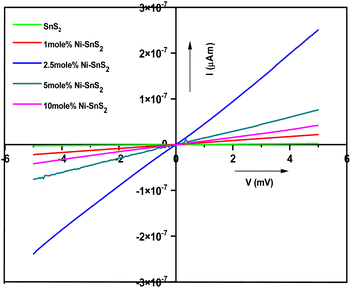 |
| Fig. 12 Current–voltage characteristics of pristine SnS2 and Ni-SnS2 nanosheets (1 mol% Ni-SnS2; 2.5 mol% Ni-SnS2, 5 mol% Ni-SnS2 and 10 mol% Ni-SnS2). | |
As the percentage of nickel loading increases the photocurrent also increases up to 2.5 mol% of nickel concentration and then it decreases. The 2.5 mol% Ni concentration of Ni-SnS2 shows the highest photocurrent almost 20 times enhanced than that of pristine SnS2. The result is clearly consistent with the enhancement in photocatalytic performance. Such behaviour can be attributed to the formation of Ni-SnS2 heterojunction, resulting in effective separation of electron–hole pairs, in-tern, allowing higher photoconductivity. Therefore, the enhanced photocatalytic activity is endorsed by the better photoconductivity of 2.5 mol% Ni loaded on SnS2 nanosheets. Overall, the study indicates that the Ni-SnS2 with 2.5 mol% concentration of nickel nanoparticles shows the highest photocurrent means that the generation of higher amounts of electron–hole pairs and its effective separation is due to Ni-SnS2 balance concentration upon illumination of light supporting higher photocatalytic performance. The surface area, H2 generation and the % apparent quantum efficiency (AQE) are tabulated in Table 1.
4 Conclusion
The Ni-SnS2 nanosheets with varying Ni concertation were synthesized. The formation of SnS2 hexagonal nanosheets was confirmed by FESEM analysis having a size of 300–500 nm diameter and decoration of nickel along with nickel oxide nanoparticles was confirmed by observation of FE-TEM. The photocatalytic activity of the resultant Ni-SnS2 catalyst was found to be higher than pure SnS2 nanosheets. The highest H2-evolution occurred when the usage of 2.5 mol% of Ni-SnS2 concentration. Thus, the presence of Ni on the surface of 2D SnS2 promotes the separation of electron–hole pairs and enhances photocatalytic activity. As the concentration of Ni increases more than 2.5 mol% on the surface of SnS2 the shading effect occurs and resulting the lowering of photocatalytic activity. In a nutshell, the improved photoconductivity due to Ni-loaded SnS2 resulting in efficient separation of electron–hole pair plays important role in governing the higher photocatalytic performance.
Conflicts of interest
There is no conflict of interest.
Acknowledgements
One of the authors Mr Niteen Jawale gratefully acknowledges to CSIR/UGC Government of India, New Delhi, for providing a Senior Research Fellowship.
References
- S. Banerjee, H. Sharma and S. Hazra, J. Bio-Clean Energy Technol., 2022, 2, 1–11 Search PubMed.
- S. G. Nnbuife, J. U. Johnson, N. E. Okeke and C. Ogbonnaya, Carbon Capture Sci. Technol., 2022, 3, 100042 CrossRef.
- Z. P. Ifkovits, J. M. Evans, M. C. Meier, K. M. Papadantonakis and N. S. Lewis, Energy Environ. Sci., 2021, 14, 4740–4759 RSC.
- F. Zhang and Q. Wang, ACS Mater. Lett., 2021, 3(5), 641–651 CrossRef CAS.
- A. R. Marlinda, N. Yusoff, S. Sagadevan and M. R. Johan, Int. J. Hydrogen Energy, 2020, 45(21), 11976–11994 CrossRef CAS.
- K. Ahmad, H. R. Ghatak and S. M. Ahuja, Environ. Technol. Innovation, 2020, 19, 100893 CrossRef.
- P. M. Rajaitha, S. Hajra, K. Mistewicz, S. Panda, M. Sahu, D. Dubal, Y. Yamauchi and H. J. Kim, J. Mater. Chem. A, 2022, 10, 15906–15931 RSC.
- C. S. Gopinath and N. Nalajala, J. Mater. Chem. A, 2021, 9, 1353–1371 RSC.
- T. Hisatomi and K. Domen, Nat. Catal., 2019, 2, 387–399 CrossRef CAS.
- W. Yang, R. R. Prabhakar, J. Tan, S. D. Tilley and J. Moon, Chem. Soc. Rev., 2019, 48, 4979–5015 RSC.
- I. R. Hamdani and A. N. Bhaskarwar, Renewable Sustainable Energy Rev., 2021, 138, 110503 CrossRef CAS.
- P. Chaudhary and P. P. Ingole, Green Chem. Sustainable Technol., 2021, 673–699 Search PubMed.
- D. Prusty, L. Paramanik and K. Parida, Energy Fuels, 2021, 35, 4670–4686 CrossRef CAS.
- B. Wang, J. Liu, S. Yao, F. Liu, Y. Li, J. He, Z. Lin, F. Huang, C. Liu and M. Wang, J. Mater. Chem. A, 2021, 9, 17143–17172 RSC.
- G. V. S. S. Sarma, M. Chavali, M. P. Nikolova, M. K. Enamala and C. Kuppan, Chalcogenide-Based Nanomaterials as Photocatalysts Micro and Nano Technologies, 2021, pp. 77–103 Search PubMed.
- A. Nawaz, S. Goudarzi, M. A. Asghari, S. Pichiah, G. S. Selopal, F. Rosei, Z. M. Wang and H. Zarrin, ACS Appl. Nano Mater., 2021, 4(11), 11323–11352 CrossRef CAS.
- S. Corby, R. R. Rao, L. Steier and J. R. Durrant, Nat. Rev. Mater., 2021, 6, 1136–1155 CrossRef CAS.
- A. Rahman and M. M. Khan, New J. Chem., 2021, 45, 19622–19635 RSC.
- F. Wen and W. Liu, J. Mater. Chem. A, 2021, 9, 18129–18147 RSC.
- S. N. F. Moridon, K. Arifin, R. M. Yunus, L. J. Minggu and M. B. Kassim, Ceram. Int., 2022, 48(5), 5892–5907 CrossRef CAS.
- Y. Quintero, E. Mosquera, J. Diosa and A. Garcia, J. Sol-Gel Sci. Technol., 2020, 94, 477–485 CrossRef CAS.
- M. Kowalkińska, S. Dudziak, J. Karczewski, J. Ryl, G. Trykowski and A. Z. Jurek, Chem. Eng. J., 2021, 404, 126493 CrossRef.
- N. S. Jawale, S. S. Arbuj, G. G. Umarji and S. B. Rane, ChemistrySelect, 2021, 6, 8861–8867 CrossRef CAS.
- S. R. Damkale, S. S. Arbuj, G. G. Umarji, S. B. Rane and B. B. Kale, RSC Adv., 2021, 11, 7587–7599 RSC.
- A. Saric, M. Vrankic, D. L. Hecht, I. Despotovic, Z. Petrovic, G. Drazic and F. Eckelt, Inorg. Chem., 2022, 61(6), 2962–2979 CrossRef CAS PubMed.
- N. J. Ridha, F. K. M. Alosfur, H. B. A. Kadhim, L. H. Aboud and N. Al-Dahan, J. Mater. Sci.: Mater. Electron., 2020, 31, 9835–9845 CrossRef CAS.
- P. Chhattise, S. Saleh, V. Pandit, S. Arbuj and V. Chabukswar, Adv. Mater., 2020, 1, 2339–2345 RSC.
- A. Tiwari and S. J. Dhoble, Cryst. Growth Des., 2017, 17(1), 381–407 CrossRef CAS.
- L. Song, J. Hu, X. Lu, Z. Lu, J. Xie, A. Hao and Y. Cao, Inorg. Chem., 2022, 61(21), 8217–8225 CrossRef CAS PubMed.
- T. Lange, S. Reichenberger, S. Ristig, M. Rohe, J. Strunk, S. Barcikowski and R. Schlogl, Prog. Mater. Sci., 2022, 124, 100865 CrossRef CAS.
- Y. Zhang, L. Hu, H. Zhou, H. Wang and Y. Zhang, ACS Appl. Nano Mater., 2022, 5(1), 391–400 CrossRef CAS.
- R. K. Mishra, G. J. Choi, H. J. Choi, J. Singh, S. H. Lee and J. S. Gwag, J. Alloys Compd., 2022, 921(15), 166018 CrossRef CAS.
- S. R. Damkale, S. S. Arbuj, G. G. Umarji, R. P. Panmand, S. K. Khore, R. S. Sonawane, S. B. Rane and B. B. Kale, Sustainable Energy Fuels, 2019, 3, 3406–3414 RSC.
- S. A. Patil, N. K. Shrestha, S. Hussain, J. Jung, S. W. Lee, C. Bathula, A. N. Kadam, H. Im and H. Kim, J. Hazard. Mater., 2021, 417, 126105 CrossRef CAS PubMed.
- Z. Liang, R. Shen, Y. Hau Ng, P. Zhang, Q. Xiang and X. Li, J. Mater. Sci. Technol., 2020, 56, 89–121 CrossRef CAS.
- R. Shen, D. Ren, Y. Ding, Y. Guan, Y. H. Ng, P. Zhang and X. Li, Sci. China Mater., 2020, 63, 2153–2188 CrossRef CAS.
- D. Wang, X. Li, L. L. Zheng, L. M. Qin, S. Li, P. Ye, Y. Li and J. P. Zou, Nanoscale, 2018, 10, 19509–19516 RSC.
- S. Shenoy, E. Jang, T. J. Park, C. S. Gopinath and K. Sridharan, Appl. Surf. Sci., 2019, 483, 696–705 CrossRef CAS.
- X. Li, Y. Deng, Z. Jiang, R. Shen, J. Xi, W. Liu and X. Chen, J. Chem. Educ., 2019, 96(6), 1224–1229 CrossRef CAS.
- S. Sultana, S. Mansingh and K. M. Parida, Adv. Mater., 2021, 2, 6942–6983 RSC.
- Z. Li, Z. He, H. Lai, Y. He, Z. Zhu, Y. Chen and T. Jin, Appl. Surf. Sci., 2021, 567, 150776 CrossRef CAS.
- K. Su, H. Liu, Z. Gao, P. Fornasiero and F. Wang, Adv. Sci., 2021, 8, 2003156 CrossRef CAS PubMed.
- H. Tan, Z. Zhao, W. Zhu, E. N. Coker, B. Li, M. Zheng, W. Yu, H. Fan and Z. Sun, ACS Appl. Mater. Interfaces, 2014, 6(21), 19184–19190 CrossRef CAS PubMed.
- M. Ganapathy, Y. Hsu, J. Thomas, C. T. Chang and V. Alagan, J. Mater. Sci., 2021, 56, 18976–18988 CrossRef CAS.
- A. Akhundi, A. Z. Moshfegh, A. H. Yangjeh and M. Sillanpaa, ACS ES&T Engg, 2022, 2(4), 564–585 Search PubMed.
- J. Kwon, K. Choi, M. Schrec, T. Liu, E. Tervoor and M. Niederberger, ACS Appl. Mater. Interfaces, 2021, 13(45), 53691–53701 CrossRef CAS.
- W. Li, D. Zhang, R. Wang, Z. Zhang and S. Qiu, ACS Appl. Mater. Interfaces, 2022, 14(28), 31782–31791 CrossRef.
- Y. Zhu, Q. Liang, M. Zhou, C. Yao, S. Xu and Z. Li, ACS Appl. Energy Mater., 2021, 4(11), 13239–13247 CrossRef CAS.
- S. Khanam and S. K. Rout, ACS Omega, 2022, 7(29), 25466–25475 CrossRef CAS PubMed.
- N. Nwaji, E. M. Akinoglu, B. Lin, X. Wang and M. Giersig, ACS Appl. Mater. Interfaces, 2021, 13(49), 58630–58639 CrossRef CAS PubMed.
- M. Tahir, A. Sherryna, R. Mansoor, A. A. Khan, S. Tasleem and B. Tahir, ACS Appl. Nano Mater., 2022, 5(1), 18–54 CrossRef CAS.
- P. Kumar, D. Laishram, R. K. Sharma, A. Vinu, J. Hu and M. G. Kibria, Chem. Mater., 2021, 33(23), 9012–9092 CrossRef CAS.
- M. Tahir, Energy Fuels, 2021, 35(17), 14197–14211 Search PubMed.
- P. Dhiman, G. Rana, A. Kumar, G. Sharma, D. N. Vo and M. Naushad, Environ. Chem. Lett., 2022, 20, 1047–1081 CrossRef CAS.
- M. Sher, M. Javed, S. Shahid, S. Iqbal, M. A. Qamar, A. Bahadur and M. A. Qayyum, RSC Adv., 2021, 11, 2025–2039 RSC.
- G. Kale, S. Arbuj, U. Chothe, S. Khore, L. Nikam and B. Kale, J. Compos. Sci., 2020, 4, 48 CrossRef CAS.
- D. B. Bankar, K. G. Kanade, R. R. Hawaldar, S. S. Arbuj, M. D. Shinde, S. P. Takle, D. P. Amalnerkar and S. T. Shinde, Arabian J. Chem., 2020, 13(12), 9005–9018 CrossRef CAS.
- S. P. Kunde, K. G. Kanade, B. K. Karale, H. N. Akolkar, S. S. Arbuj, P. V. Randhavane, S. T. Shinde, M. H. Shaikh and A. K. Kulkarni, RSC Adv., 2020, 10, 26997–27005 RSC.
- S. Megala, P. Ravi, P. Maadeswaran, M. Navaneethan, M. Sathish and R. Ramesh, Nanoscale Adv., 2021, 3, 2075–2088 RSC.
- R. Monsef, M.
G. Arani and M. S. Niasari, ACS Appl. Energy Mater., 2021, 4(1), 680–695 CrossRef CAS.
- Q. Cao, M. Guo, J. Cao, H. Lin and S. Chen, Catal. Commun., 2021, 149, 106197 CrossRef CAS.
- Z. Guo, F. Dai, H. Yin, M. Zhang, J. Xing and L. Wang, Colloid Interface Sci. Commun., 2022, 48, 100615 CrossRef CAS.
- F. Mu, X. Miao, J. Cao, W. Zhao, G. Yang, H. Zeng, S. Li and C. Sun, J. Cleaner Prod., 2022, 360, 131948 CrossRef CAS.
- Z. Liang, B. Ouyang, T. Wang, X. Liu, H. Huo, D. Liu, H. Feng, J. Ma, K. Deng, A. Li and E. Kan, Int. J. Hydrogen Energy, 2022, 47(20), 10868–10876 CrossRef CAS.
- S. Biswas, H. Y. Lee, M. Prasad, A. Sharma, J. S. Yu, S. Sengupta, D. D. Pathak and A. Sinhamahapatra, ACS Appl. Nano Mater., 2021, 4(5), 4441–4451 CrossRef CAS.
- M. Eder, C. Courtois, P. Petzoldt, S. Mackewicz, M. Tschurl and U. Heiz, ACS Catal., 2022, 12(15), 9579–9588 CrossRef CAS.
- S. Lu, B. Weng, A. Chen, X. Li, H. Huang, X. Sun, W. Feng, Y. Lei, Q. Aian and M. Q. Yang, ACS Appl. Mater. Interfaces, 2021, 13(11), 13044–13054 CrossRef CAS.
- F. Platero, A. L. Martin, A. Caballero, T. C. Rojas, M. Nolan and G. Colon, ACS Appl. Nano Mater., 2021, 4(3), 3204–3219 CrossRef CAS.
- S. Rohani, A. Ziarati, G. M. Ziarani, A. Badiei and T. Burgi, Catal. Sci. Technol., 2019, 9, 3820–3827 RSC.
- Y. Wei, M. Z. Shahid, S. Lyu, W. Sun and S. Lyu, RSC Adv., 2021, 11, 22618–22624 RSC.
- D. B. Bankar, R. R. Hawaldar, S. S. Arbuj, S. T. Shinde, J. R. Gadde, D. S. Rakshe, D. P. Amalnerkar and K. G. Kanade, Mater. Chem. Phys., 2020, 243, 122561 CrossRef CAS.
- Y. Gao, L. Bai, X. Zhang and F. Yang, ChemElectroChem, 2021, 8, 2087–2093 CrossRef CAS.
- Y. Xu and R. Xu, Appl. Surf. Sci., 2015, 351, 779–793 CrossRef CAS.
- R. Mangiri, K. S. kumar, K. Subramanyam, Y. C. Ratnakaram, A. Sudharani, D. A. Reddy and R. P. Vijayalakshmi, Colloids Interface Sci. Commun., 2021, 43, 100437 CrossRef CAS.
- T. Su, Z. D. Hood, M. Naguib, L. Bai, S. Luo, C. M. Rouleau, I. N. Ivanov, H. Ji, Z. Qin and Z. Wu, ACS Appl. Energy Mater., 2019, 2(7), 4640–4651 CrossRef CAS.
|
This journal is © The Royal Society of Chemistry 2023 |
Click here to see how this site uses Cookies. View our privacy policy here.