DOI:
10.1039/D2RA06685H
(Paper)
RSC Adv., 2023,
13, 1106-1114
Urushiol modified epoxy acrylate as UV spray painting oriental lacquer ink
Received
22nd October 2022
, Accepted 23rd December 2022
First published on 4th January 2023
Abstract
As a natural “water-based” polymer composite material, oriental lacquer is often referred to as the “king of coatings” and is used as a coating in the defense industry, chemical industry, petroleum industry, metallurgy and mining industry, textile painting and dyeing industry, pharmaceutical industry, as well as the protection of ancient buildings and cultural relics. However, the development of modern industrialization is greatly hindered by the high viscosity of oriental lacquer, the difficulty of spraying, the long drying cycle, and the seriousness of allergenicity. Herein, based on the principle of oriental lacquer and the characteristics of prepolymer in ink, we developed a new prepolymer for modulating UV oriental lacquer ink and explored the feasibility of using it as a raw material for UV spray painting. In this study, lacquer phenol was extracted from oriental lacquer and modified with epoxy acrylate by a simple mechanical compounding method to obtain lacquer epoxy acrylate. Moreover, the UV spray painting oriental lacquer ink was also prepared by using it as the main film-forming substance. The orthogonal experiment method was used to optimize the best formulation of UV spray painting oriental lacquer ink by using nozzle passability, viscosity and curing time as test indexes. Meanwhile, the film properties of UV spray painting oriental lacquer inks were also evaluated. The test results show that the UV spray painting oriental lacquer ink prepared with urushiol epoxy acrylate has better dispersion, excellent paint film performance, and solves the problem that oriental lacquer cannot be printed. This present work shows that urushiol epoxy acrylate as a new type of prepolymer has broad application prospects in the actual preparation of UV inks.
1. Introduction
Oriental lacquer has been used for nearly 7000 years as a pure natural “water-based” polymer composite coating collected from green plants. It is a milky white liquid plucked from the bark layer of sumac, and it is the oldest industrial plastic known to mankind.1–3 The cured oriental lacquer has outstanding durability, corrosion resistance, antibacterial properties, stability, high decorative properties and environmental friendliness.4–6 Thus, it is widely used in textile, painting and dyeing, petroleum, chemical, handicraft and furniture industries.7,8 In terms of its performance, there is no artificial paint that can match it, and it is known as the “king of coatings”. However, the high cost of oriental lacquer, complicated finishing process and low efficiency make it difficult to meet the needs of modern industrial production.9,10 Therefore, the oriental lacquer is often modified to make up for its natural defects and improve its performance.11–13 At present, the modification of oriental lacquer is mainly to extract the lacquer phenols and modify the reaction with compounds to improve the physicochemical properties of the oriental lacquer film. The modification methods often used for oriental lacquer are lacquer phenol modified resin, hydrophilic modification, compound modification, nano-modification, UV curing, etc.14–17 Furthermore, most of the research on the application of oriental lacquer is focused on the traditional finishing process, but there is no research on the application of oriental lacquer combined with UV-curable ink for UV spray painting technology. Combined with the traditional process using UV spray painting technology and UV curing technology so that modified oriental lacquer through the equipment can be directly “printed” to the surface of the substrate. This not only can realize the transformation of lacquer painting from simple traditional manual production to the combination of traditional technology and digital production, but also effectively improve the production efficiency and capacity of products, reduce labor costs, and realize the integrated innovation of the paint industry and painting industry.2,8,12
Generally, the prepolymer in UV ink is the basic skeleton of UV ink components,18 generally with C
C double bond, epoxy groups and other curing groups, which can be further reacted under light conditions.19,20 Furthermore, epoxy acrylates have excellent comprehensive properties,21 which are the most studied and the largest amount of UV curing oligomers.22,23 Oriental lacquer is mainly composed of urushiol, laccase, polysaccharide, glycoprotein, water and metal ions. It is a kind of water-in-oil reactive bio-based composite system.24,25 Lacquer phenol is the main film-forming substance of oriental lacquer, which has a direct impact on the quality and film-forming properties. Lacquer phenols are polyphenolic compounds containing double bonds with multiple reactive centers. And the unsaturated side chains in the structure can undergo a series of reactions such as condensation and copolymerization during the curing reaction.26,27 In recent years, with the in-depth research on the composition and film-forming mechanism of oriental lacquer and the emergence of synthetic resins, the research on its modification has changed to diversification.28–30 Many polymer materials with excellent performance (such as efficient energy conversion, higher sensory sensitivities, stable, and degradable) have appeared,31,32 among which lacquer phenol formaldehyde resin and epoxy resin modified oriental lacquer are the most representative.33,34 Therefore, based on the principle of modified oriental lacquer and the characteristics of prepolymer in ink (such as high dispersion, low viscosity, low pollution, and environmental protection). A new film-forming resin with excellent properties of oriental lacquer can be synthesized as a component for the preparation of painting oriental lacquer ink.
In this study, we extracted lacquer phenol from oriental lacquer and modified the epoxy acrylate to obtain lacquer phenol epoxy resin. Using the similarity between UV ink prepolymer and urushiol epoxy resin, a new type of oriental lacquer-based painting ink was obtained by making it mutually soluble under the condition of auxiliary agent and grinding dispersion. Moreover, we also carried out experiments on different proportions of various components in order to obtain the best formulation of UV lacquer phenol-modified epoxy acrylate painting ink. It has the advantages of both oriental lacquer and UV spray painting oriental lacquer ink. Furthermore, by testing the film performance, the effect of different ratios of epoxy resin-modified oriental lacquer and UV ink on the film performance was explored. This work provides a new perspective for the research of coating process technology.
2. Materials and methods
2.1 Materials
Oriental lacquer (Pingli lacquer) was supplied by Xi'an Paint and Oriental Lacquer Research Institute (Xi'an, China). Formaldehyde and epoxy resin were obtained from Shenzhen Jitian Chemical Co., Ltd (Shenzhen, China). Xylene, acrylic monomer hexanediol diacrylate (HDDA), aqueous ammonia (NH3·H2O), butanol, neopentyl glycol diacrylate (NPGDA) and trimethylepropene triacrylate (TMPTA) were purchased from Tianjin Tianjiao Radiation Curing Material Co., Ltd (Tianjin, China). 2-Isopropylthioxanthone (ITX, light initiator), 1-hydroxycyclohexyl phenyl ketone (photoinitiator-184), 2,4,6-trimethylbenzoyldiphenyl phosphine oxide (TPO), 2-methyl-1-[4-(methylthio)phenyl]-2-morpholino-1-propanone (photoinitiator-907), and 2,4-diethyl-9H-thioxanthen-9-one (DETX) were procured from Shanghai Jinjin Trading Co., Ltd (Shanghai, China). Quinacridone magenta pigment, wetting dispersant, and polymerization inhibitor (ST-1) were purchased from Guangzhou Yuansu Chemical Technology Development Co., Ltd (Guangzhou, China). Moreover, other additives such as leveling agents, photosensitizing auxiliaries and defoaming agents were purchased from the commercial market. All materials were used without any further purification and the deionized water (DIW) was used in the whole experiment.
2.2 Extraction of lacquer phenol
Urushiol was extracted from oriental lacquer by xylene blending method. Briefly, the oriental lacquer and xylene were placed in a three-neck flask according to the mass ratio of 1
:
1, and the water divider, condensation tube, heating jacket, nitrogen tube, thermometer and stirring device were installed respectively. Subsequently, the three-neck flask was placed in a water bath and heated at 95 °C for 6 h. Finally, the lacquered phenol solution containing xylene was obtained by extracting the upper clear layer after standing the three-mouth flask for 60 min.
2.3 Preparation of urushiol modified epoxy acrylates
The lacquer phenol xylene solution was mixed with formaldehyde in the amount of 0.9
:
1 and aqueous ammonia was added, and then placed into the reaction kettle at 70 °C for 40 min. After the reaction, the temperature was raised to 136 °C for dehydration to obtain lacquer phenol formaldehyde polymer. The reaction process is shown in Fig. 1.
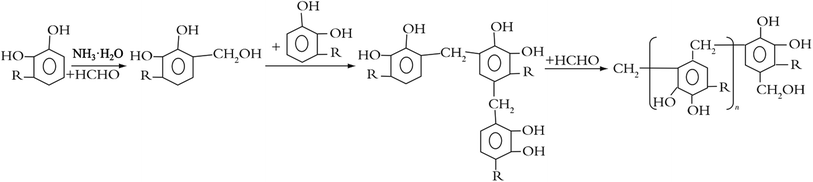 |
| Fig. 1 Synthesis mechanism of urushiol for formaldehyde polymer. | |
The as-prepared urushiol formaldehyde and epoxy resin were put into the reaction kettle in a 1
:
1 ratio and a small amount of polymerization inhibitor was added. The reaction was carried out at 70 °C for 30 min. Subsequently, the addition of butanol closes the residual hydroxymethyl groups on the benzene ring of the enamel phenol in the enamel phenol epoxy resin, which will prevent the resin molecules from continuing to grow or even gel. Then, the mixture was dehydrated at 136 °C to obtain urushiol epoxy resin. Immediately afterwards, a certain amount of lacquer phenol epoxy resin and polymerization inhibitor were added to the three-mouth flask and slowly heated to 65 °C, and then a mixture of acrylic acid and catalyst was slowly added dropwise and stirred at 90 °C for 50 min. The reaction should be stopped when the acid value dropped to 5, and the prepolymer lacquer epoxy acrylate was obtained. Moreover, the molecular weight and polydispersity index of the prepared urushiol epoxy acrylate prepolymer is 22
000 and 1.52, respectively. The reaction diagram for synthesis of urushiol epoxy resin reaction and its prepolymer lacquer epoxy acrylate counterpart is shown in Fig. 2.
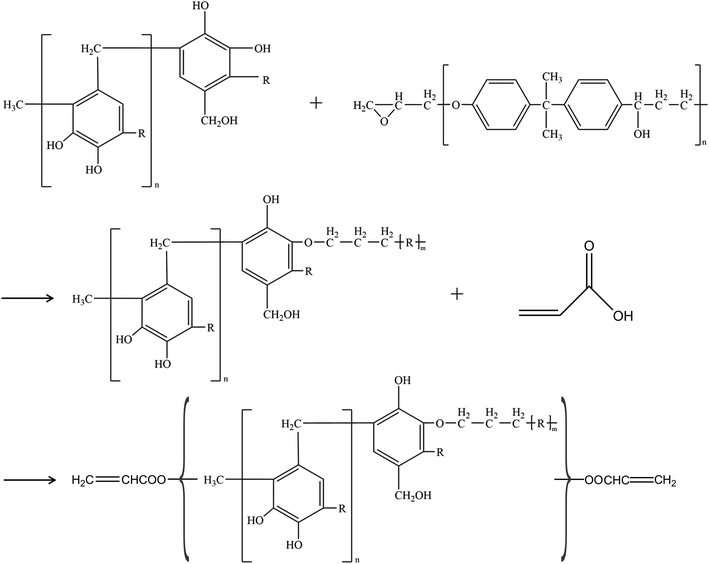 |
| Fig. 2 The reaction diagram for synthesis of urushiol epoxy resin reaction and its prepolymer lacquer epoxy acrylate counterpart. | |
2.4 Preparation of UV spray painting oriental lacquer ink
The illustration of urushiol-modified epoxy acrylate as UV spray painting oriental lacquer ink, as depicted in Fig. 3. Generally, UV spray painting oriental lacquer ink is mainly composed of pigment dispersion, film forming prepolymer, reactive monomer, photoinitiator and additives. Besides, the preparation process of pigment dispersion is completed by the method commonly used in the laboratory. In detail, mixed the prepolymer, part of the active monomer and the wetting dispersant into a beaker and placed on a magnetic stirrer until mixed evenly. Meanwhile, added the pigment and put it on the electric mixer for pre-dispersion for 60 min. Then put it into the high-speed grinder for grinding for 30–120 min, so that the pigment can be fully moistened and dispersed in the ink system. The fineness was measured every 20 min during the grinding process, and the grinding was stopped when the fineness of the system reached less than 10 μm. Finally, the grinding paste was ultrasonically dispersed for 30 min to get the pigment of UV painting ink. The viscosity of the prepared urushiol epoxy acrylate prepolymer before and after adding the reactive monomer is 55 s and 19.27 s, respectively.
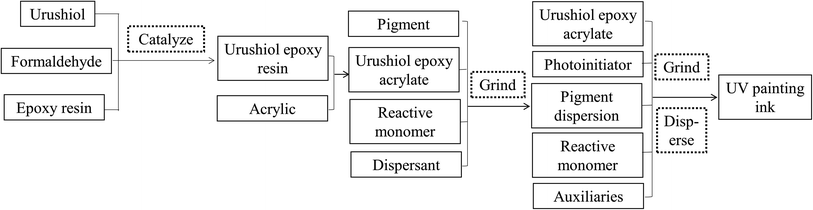 |
| Fig. 3 The illustration of urushiol-modified epoxy acrylate as UV spray painting oriental lacquer ink. | |
The pigment dispersion, lacquer phenol epoxy acrylate, reactive monomer, photoinitiator, and auxiliaries are mixed in the beaker according to the ratio in Table 1. Subsequently, the mixed solution was placed on a stirrer for 20 min and then ultrasonically dispersed for 30 min. Finally, UV spray painting oriental lacquer ink can be obtained, which can be used for UV ink spray painting after filtering.
Table 1 The basic formula of the UV spray painting oriental lacquer ink
Component |
Mass fraction (%) |
Pigment dispersion |
25–30 |
Lacquer phenol epoxy acrylate |
2–6 |
Reactive monomer |
65–75 |
Photoinitiators |
2–8 |
Auxiliaries |
0–2 |
Where the type of reactive monomer is oriental lacquer monomer and used alone; the type of photoinitiators is photoinitiator-907 and TPO, and used in combination.
2.5 UV spray painting oriental lacquer ink formulation design
In the experimental research and industrial production, the problem of formula selection is often encountered. It is necessary to verify different kinds of raw materials and different modulations through a large number of experiments to obtain formulas with excellent performance. In this experiment, the simplex center of gravity design test method is mainly used to complete the optimal formulation of urushiol modified epoxy acrylate UV spray painting oriental lacquer ink. The regression equation of the commonly used third-order centroid polynomial is as follows: |
 | (1) |
According to the formula, when n = 3, there are a total of 7 test points in the three-factor third-order simplex center of gravity test design, so the test is designed as shown in Table 2.
Table 2 Three-component simplex center of gravity experimental design
Test number |
X1 |
X2 |
X3 |
Test value |
Vertex |
1 |
1 |
0 |
0 |
y1 |
2 |
0 |
1 |
0 |
y2 |
3 |
0 |
0 |
1 |
y3 |
Two vertex center of gravity |
4 |
1/2 |
1/2 |
0 |
y4 |
5 |
1/2 |
0 |
1/2 |
y5 |
6 |
0 |
1/2 |
1/2 |
y6 |
Three vertex center of gravity |
7 |
1/3 |
1/3 |
1/3 |
y7 |
When n = 3, according to the regression analysis method, the regression equation between the variables in the three-factor third-order simplex center of gravity design specification and the test index can be obtained as follows:
|
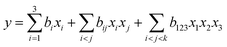 | (2) |
|
y = b1x1 + b2x2 + b3x3 − b12x1x2 − b13x1x3 − b23x2x3 + b123x1x2x3
| (3) |
where
y is the particle size parameter, he variables
x1,
x2, and
x3 represent the proportions of HDDA, NPGDA, and TMPTA in the mixed monomers, respectively. The calculation formula of each parameter in the formula is:
b1 =
y1;
b2 =
y2;
b3 =
y3;
b12 =
y12;
b13 =
y13;
b23 =
y23;
b123 = 27
y123 + 3(
y1 +
y2 +
y3) − 12(
y12 +
y13 +
y23).
2.6 Characterization
The microstructures of the UV spray painting ink were observed by using scanning electron microscopy (SEM, JEOL-7800F, JEOL Ltd, Tokyo, Japan). The characteristic functional groups were analyzed using a Fourier-transformed infrared spectrum (FT-IR, Cary630, Agilent Technologies Inc., USA). The FT-IR spectrum was investigated at 6 cm−1 spectral resolution in the range of 500–4000 cm−1. The particle size distribution of UV spray painting inks was carried out using a Laser Particle Size Analyzer (LS-609, Zhuhai OMEC Instrument Co., Ltd). Moreover, the paint film performance of UV spray painting ink was tested in accordance with corresponding Chinese standards. The viscosity of the sample was recorded at 20–25 °C by an ubbelohde viscometer (SBQ81834, Jaegda Precision Instrument Co., Ltd, Guangzhou, China), which meets Chinese Standards GB/T13217.4-2008. The glossiness of the coating film of UV spray painting ink before and after modification was tested by the gloss meter (BGD 512/S, Jaegda Precision Instrument (Guangzhou) Co., Ltd, Guangzhou, China) according to GB/T4893.6-2013. The pencil hardness method (GB/T6793-2006) was used to test the hardness of UV spray painting ink before and after modification. An abrasion tester (Taber 5750, Taber Company, Inc., USA) was carried out to investigate the abrasion resistance according to GB/T1768-2007. The adhesion was measured by BEVS 2202/1C (Guangzhou Shenghua Industrial Co., Ltd, Guangzhou, China) at 2 mm intervals according to GB/T4893.4-2013.
3. Results and discussion
3.1 FT-IR spectral analysis
The characteristic functional groups of UV spray painting oriental lacquer ink before and after urushiol epoxy acrylate modification were investigated using FT-IR, the corresponding FT-IR spectrum is shown in Fig. 4. It can be seen from the figure that the skeleton structure of the UV ink before and after modification with urushiol epoxy acrylate is similar. The broad characteristic absorption at 831 and 1628 cm−1 is the structural functional group of urushiol phenyl ring in the oriental lacquer ink configured with synthetic prepolymer, which is caused by the introduction of urushiol, formaldehyde and epoxy resin.35 However, the characteristic absorption peak of the epoxy group at 915 cm−1 disappeared, indicating that the epoxy group had a cross-linking reaction with the phenolic hydroxyl group and methylol group in the urushiol formaldehyde resin, respectively. This is reflected in the improvement of alkali resistance, flexibility and adhesion in the subsequent evaluation of oriental lacquer properties.36 Meanwhile, due to the introduction of epoxy resin, the crosslinking density of urushiol formaldehyde resin in the system is reduced, making it easier for the modified resin to pass through the nozzle.37 Furthermore, this will also greatly improve the flexibility and other properties of the modified UV spray painting oriental lacquer ink.
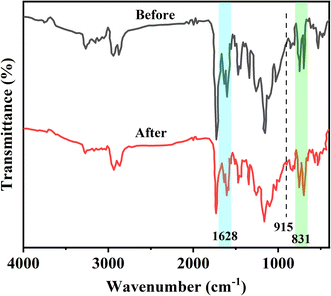 |
| Fig. 4 FT-IR spectra of UV spray painting oriental lacquer ink before and after urushiol epoxy acrylate modification. | |
3.2 Morphology analysis
The surface morphology of UV lacquer ink modified with phenol epoxy acrylate was characterized by SEM (Fig. 5). Fig. 5a and b are the morphologic images of urushiol modified epoxy acrylate UV paint ink amplified by 2000 and 5000 times under SEM, respectively. As shown in Fig. 5, the appearance of the paint film is relatively smooth and there is no molecular agglomeration phenomenon under the electron microscope, which further proves that the oriental lacquer ink prepared from urushiol epoxy acrylate has better dispersibility. Furthermore, this further indicates the practicality of the practical application of urushiol epoxy acrylate modified UV spray painting inks. Moreover, the field emission energy of the electron beam used in the field emission scanning electron microscope is too strong, which will cause some damage to the surface of the paint film. Therefore, the paint film is decomposed under the electron beam irradiation, resulting in the appearance of the white particles in Fig. 5b.
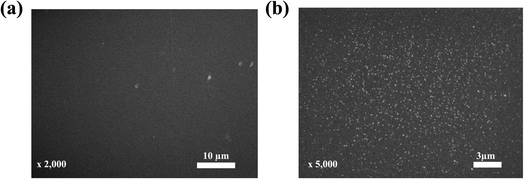 |
| Fig. 5 SEM images of UV lacquer ink modified with phenol epoxy acrylate at different magnifications. | |
3.3 Pigment dispersion formulation design of UV spray painting oriental lacquer ink
When formulating ink, molecular particle size and its dispersion stability are the key factors that determine whether the ink can be ejected smoothly. Moreover, the particle size has a certain influence on the stability of the ink system. When the particle size is smaller, the stability is higher, so the particle size of the system should be reduced as much as possible. The particle size of the ink system is tested by a laser particle size analyzer to test the dispersion degree of the ink paste. Due to the different types of monomers, their wetting and dispersing effects on pigments are also different. The activity and function of the monomer are key to determining the properties of the coating, such as curing speed, flexibility and hardness. When the selected monomers have low viscosity and are soluble, the prepolymer can become the dominant factor in the coating curing process. In order to investigate the effect of different monomers on the dispersion performance and dispersion stability of ink pastes, three-factor and three-order simple center-of-gravity experiments were designed. The pigment dispersion was prepared by changing the monomer type and the particle size was tested. The data are shown in Table 3. Substitute the particle size data in Table 3 into eqn (3) to calculate the regression coefficient. Then, the regression coefficient is substituted into the equation to obtain the regression equation between the particle size y and the variable x, as shown in eqn (4). |
y = 1.11x1 + 1.1x2 + 1.13x3 − 0.1x1x2 − 0.32x1x3 − 0.42x2x3 + 0.27x1x2x3
| (4) |
Table 3 Pigment dispersion formulation design and results
Experiment number |
X1 (HDDA) |
X2 (NPGDA) |
X3 (TMPTA) |
Particle size (μm) |
1 |
1 |
0 |
0 |
1.11 |
2 |
0 |
1 |
0 |
1.10 |
3 |
0 |
0 |
1 |
1.13 |
4 |
1/2 |
1/2 |
0 |
1.08 |
5 |
1/2 |
0 |
1/2 |
1.04 |
6 |
0 |
1/2 |
1/2 |
1.01 |
7 |
1/3 |
1/3 |
1/3 |
1.03 |
Generally, the smaller the value of the regression equation, the better the dispersibility of the colorant. When x1 = 0, x2 = 0.571, x3 = 0.429, the minimum value of particle size y is 1.01. Under the conditions of this experiment, it can be seen from the experiments and data analysis that the dispersibility prepared by the composite monomer is better than the color paste prepared by the single monomer. The optimal mass ratio of the composite monomer is m (NPGDA)
:
m (TMPTA) = 0.571
:
0.429. Using the optimized formula to prepare the color paste and test the particle size distribution, it can be seen that 97% of the particle size values are below 1.5 μm, which is consistent with the predicted value of the regression equation. This indicates that the dispersibility of the colorant is excellent at this time.
3.4 Pigment dispersion formula selection of UV spray painting oriental lacquer ink
In this study, a four-factor three-level orthogonal test scheme was selected, and the additions of colorants, epoxy acrylates, photoinitiators and additives were selected as influencing factors. Meanwhile, taking the viscosity of the ink, curing time, and whether it can pass the nozzle of the UV spray painting equipment as the evaluation indicators, the best matching scheme of the UV spray painting oriental lacquer ink is selected. The orthogonal test factor level table for formulating UV spray painting oriental lacquer ink is shown in Table 4.
Table 4 Factors and levels of the orthogonal experiment for formula of UV spray painting oriental lacquer ink
Level |
Factor |
A |
B |
C |
D |
Pigment dispersion/% |
Urushiol epoxy acrylate/% |
Photoinitiator/% |
Auxiliary/% |
1 |
25 |
2 |
2 |
0.6 |
2 |
27.5 |
4 |
5 |
1.3 |
3 |
30 |
6 |
8 |
2 |
According to the experimental conditions and the importance of various properties to the ink system, the weights of curing time, viscosity, and whether it can pass through the nozzle are taken as 0.2, 0.3, and 0.5, respectively. Table 5 shows the orthogonal test scheme of ink ratio and its performance test results. From the analysis in Table 5, it can be seen that the shorter the curing time, the smaller the viscosity value, the higher the nozzle passing rate, and the better the prepared sample performance. Meanwhile, according to the R value and the K value, the influencing factors of each index are in descending order: pigment dispersion > photoinitiator > urushiol epoxy acrylate > auxiliary. Moreover, the addition ratio of photoinitiator is the main factor affecting the curing performance of ink. The curing time decreases with the increase of the addition amount of photoinitiator, indicating that the photoinitiator has a catalytic effect on the photopolymerization of the system. The best scheme is A1B1C3D3, which is based on the nozzle passing rate, short curing time and low viscosity. Therefore, the optimum formulation of UV oriental lacquer ink is w (pigment dispersion)
:
w (urushiol epoxy acrylate)
:
w (photoinitiator)
:
w (auxiliary) = 25
:
2
:
8
:
2. According to the test results in Table 5, the particle size distribution diagram of the A1B1C3D3 formula verified by particle size test is shown in Fig. 6. It can be seen from Fig. 6 that the average particle size of the samples is less than 9 μm. Moreover, the particles smaller than 1 μm accounted for 7.6%, and 92.4% of the samples were concentrated around 6000 nm in particle size. The particle size of the UV spray painting oriental lacquer ink reaches nanometer level and the distribution is concentrated, indicating that the system dispersibility of the UV-cured urushiol modified epoxy acrylate spray painting ink under this formula is better. This also further illustrates that the optimal formula is A1B1C3D3.
Table 5 The orthogonal experiment of UV spray painting oriental lacquer ink matching programs and test results of performance
Experiment number |
A |
B |
C |
D |
Cure time membership |
Viscosity membership |
Nozzle pass rate membership |
1 |
1 |
1 |
1 |
1 |
0.34 |
1 |
1 |
2 |
1 |
2 |
2 |
2 |
0.62 |
0.98 |
1 |
3 |
1 |
3 |
3 |
3 |
1 |
0.92 |
1 |
4 |
2 |
1 |
2 |
3 |
0.54 |
0.99 |
1 |
5 |
2 |
2 |
3 |
1 |
0.58 |
0.78 |
1 |
6 |
2 |
3 |
1 |
2 |
0.17 |
0.51 |
0.33 |
7 |
3 |
1 |
3 |
2 |
0.65 |
0.85 |
1 |
8 |
3 |
2 |
1 |
3 |
0 |
0.57 |
0.67 |
9 |
3 |
3 |
2 |
1 |
0.55 |
0 |
0 |
K1 |
7.86 |
7.37 |
4.59 |
5.25 |
|
|
|
K2 |
5.90 |
6.20 |
5.68 |
6.11 |
|
|
|
K3 |
4.29 |
4.48 |
7.78 |
6.69 |
|
|
|
R |
3.57 |
2.89 |
3.19 |
1.44 |
|
|
|
Primary and secondary order |
A > C > B > D |
Priority order |
A1 |
B1 |
C3 |
D3 |
|
|
|
Excellent combination |
A1B1C3D3 |
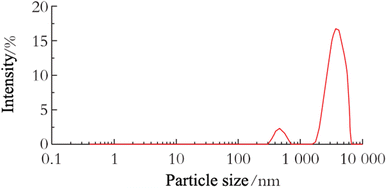 |
| Fig. 6 Particle size distribution of modified UV spray painting oriental lacquer ink. | |
3.5 Paint film performance test
In order to ensure the accuracy and validity of the test results, three boards A1, A2, and A3 for painting this kind of UV ink were produced in the test. When testing the performance of paint film, select multiple points at different positions on a sample for testing, and take the average value to make the test results more accurate. The relative properties of the UV-curable urushiol-modified epoxy acrylate spray painting ink prepared according to the optimal formulation are shown in Fig. 7. Moreover, the dry film thickness of the sample in all performance tests is 0.56 mm. It can be seen from the figure that the glossiness, hardness, adhesion, wear resistance, and roughness of the paint film can meet the requirements of national standards. Fig. 7a shows that the gloss of the sample is basically stable at 98.4, which indicates that the modified UV spray painting oriental lacquer ink coating has a stable gloss and exhibits high gloss characteristics. Fig. 7b displays the hardness of the modified UV spray painting ink coating at different positions, which shows the hardness is kept at 2H. Therefore, urushiol modified epoxy acrylate UV spray painting ink has a higher hardness. As illustrated in Fig. 7c, the adhesion of modified UV spray painting ink coating remained around level 1, which manifest the excellent adhesion of the coating. Moreover, as depicted in Fig. 7d, the weight loss value of paint film of modified UV spray painting ink remained basically at 0.033 g/50 r, which indicated that the paint film had excellent wear resistance. Furthermore, as shown in Fig. 7e, the roughness of the sample is basically stable at 0.782 μm, indicating that the coating of modified UV spray painting ink has an excellent smooth effect.
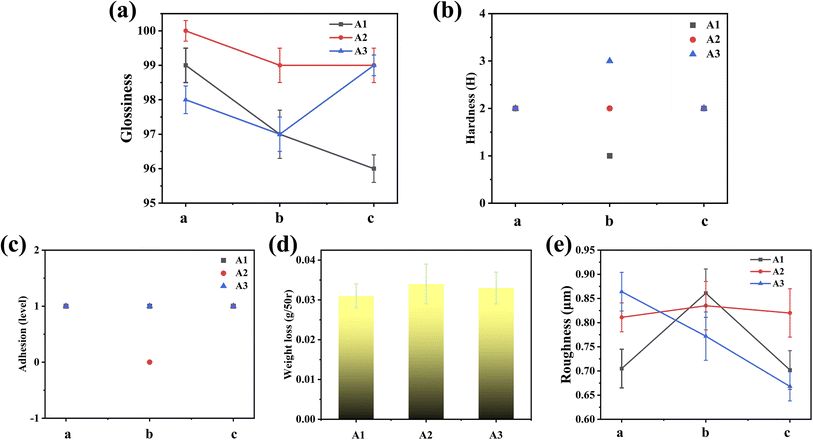 |
| Fig. 7 Paint film performance test of urushiol modified epoxy acrylate UV spray painting ink: (a) glossiness; (b) hardness; (c) adhesion; (d) wear resistance; (e) roughness. | |
3.6 Comprehensive performance evaluation of UV spray painting oriental lacquer ink
The performance parameters of the UV-curable urushiol modified epoxy acrylate spray painting ink prepared according to the optimal formulation are shown in Table 6. As shown in Table 6, the paint film of the modified UV spray painting ink is flat, smooth, without bubbles, and has a excellent appearance. The gloss of the corresponding paint film is above 90%, the adhesion to the substrate is outstanding, and the hardness reaches 2H. However, the hardness of UV spray painting oriental lacquer ink is slightly worse than that of oriental lacquer, which is mainly due to the lower content of its main film former. Furthermore, compared with the original ink, the performance of UV spray painting oriental lacquer ink is greatly improved in terms of hardness and adhesion. Moreover, it also has the advantages of oriental lacquer super durability, oxidation stability, corrosion resistance and so on. Compared with the original UV ink in hardness, adhesion and other properties have been greatly improved. This is due to the fact that the modified UV spray painting ink contains prepolymers synthesized from raw materials such as urushiol, epoxy resin, and acrylic acid, and introduces the components of oriental lacquer. Therefore, while having the advantages of oriental lacquer, UV-cured lacquer phenol-modified epoxy acrylate painting ink also solves the problem that oriental lacquer cannot be printed.
Table 6 Performance of the modified UV spray painting oriental lacquer ink
Test items |
Modified UV spray painting ink |
Oriental lacquer |
Original UV ink |
Testing method |
Performance index |
Appearance of paint film |
Smooth |
Smooth |
Smooth |
Visual inspection |
Smooth |
Solid content/% |
30 |
71 |
22 |
GB/T1725-2007 |
<100 |
Glossiness |
98 |
≥75 |
110 |
GB/T4893.6-2013 |
>50 |
Hardness |
2H |
3H–4H |
H |
GB/T6739-2006 |
6B–6H |
Adhesion |
1 |
0–1 |
3 |
GB/T4893.4-2013 |
0–5 |
4. Conclusions
In this study, a UV-curable urushiol-modified epoxy acrylate spray painting ink with excellent properties of both oriental lacquer and ink was prepared. The results suggest that the optimum formula of the painting oriental lacquer ink is w (pigment dispersion)
:
w (urushiol epoxy acrylate)
:
w (photoinitiator)
:
w (auxiliary agent) = 25
:
2
:
8
:
2. The FT-IR and SEM analysis of the samples showed that the painting oriental lacquer ink prepared from urushiol epoxy acrylate had better dispersibility. Furthermore, the urushiol epoxy acrylate can be used as a new type of prepolymer in the practical preparation of UV inks. This ink not only solves the problem that oriental lacquer cannot be sprayed, but also greatly improves the hardness, adhesion, stability and other properties of the UV spray painting ink film compared with the original ink. Moreover, the particle size analysis and performance test verified the excellent performance of the UV-curable urushiol modified epoxy acrylate painting ink developed with this formula. This UV spray painting oriental lacquer ink can be applied to actual production, and has great application value and broad market prospects in the coating industry and painting industry. It will be widely used in signage, textiles, ceramics, 3D printing, biomedicine, conductive circuits and other industries.
Author contributions
The design of this protocol was carried out by L. J. Wu and W. K. Zhu. The manuscript was written through the contributions of W. K. Zhu, M. L. Chen and S. Li. The main experiments including synthesis of the UV spray painting oriental lacquer ink were performed by L. J. Wu, W. K. Zhu, Z. Q. Li and H. M. Li. All the authors analyzed the results and experimental data. J. Xu, S. Li and M. L. Chen participated in the revise of the manuscript. All authors have given approval to the final version of the manuscript.
Conflicts of interest
There are no conflicts to declare.
Acknowledgements
This research was funded by the Research and Development Funding of Zhejiang A&F University (2022LFR076), the Project Funded by the Natural Science Foundation of Jiangsu Province of China (BK20201072), the National Natural Science Foundation of China (22078123, 32071687), the Natural Science Foundation of the Higher Education Institutions of Jiangsu Provience (19KJB22006), the 2021 project of the “fourteenth five year plan” of Education Science in Jiangsu Province “reform and innovation of professional art talent training mode” (T-c/2021/106), the 2019 Jiangsu University Philosophy and social sciences research project “analysis of typical characteristics of Republic of China home design and Its Enlightenment to contemporary” Republic of China style “design” (2019sja0482), and the achievements in the construction of national first-class undergraduate major in environmental design.
References
- H. H. Yu, J.-A. Lim, K.-B. Lee and Y. Lee, Polymers, 2021, 13, 1395 CrossRef CAS PubMed.
- B. Zheng, W. Bai, J. Chen, R. Jian, K. Yang, Q. Lin and Y. Xu, Prog. Org. Coat., 2021, 161, 106494 CrossRef CAS.
- R. Lu, T. Yoshida and T. Miyakoshi, Polym. Rev., 2013, 53, 153–191 CrossRef CAS.
- C.-W. Chang, J.-J. Lee and K.-T. Lu, Polymers, 2020, 12, 990 CrossRef CAS PubMed.
- J. Yang, J. Deng, Q. Zhang, Q. Shen, D. Li and Z. Xiao, Prog. Org. Coat., 2015, 78, 176–182 CrossRef CAS.
- M. Zhao and C. Hu, S. Afr. J. Bot., 2018, 116, 61–66 CrossRef.
- J. Lee, M. J. Kim, M. H. Kim, J. M. Doh, H. G. Hahn and Y. Lee, Surf. Interface Anal., 2015, 47, 1180–1186 CrossRef CAS.
- X.-M. Ma, R. Lu and T. Miyakoshi, Polymers, 2014, 6, 132–144 CrossRef.
- J. Honzicek, Ind. Eng. Chem. Res., 2019, 58, 12485–12505 CrossRef CAS.
- Q. Xiao, Y. Cao, H. Tan, Q. Feng, X. Gu, J. Lyu, H. Xiao, M. Chen and Y. Chen, J. Renewable Mater., 2023, 11, 1003–1016 Search PubMed.
- D. Tamburini, J. Anal. Appl. Pyrolysis, 2021, 157, 105202 CrossRef CAS.
- W. Bai, L. Cai, D. Zhuo, Y. Xu, H. Xue, Q. Chen and J. Lin, Prog. Org. Coat., 2014, 77, 431–438 CrossRef CAS.
- H. Szczepanowska and R. Ploeger, J. Cult. Herit., 2019, 40, 215–225 CrossRef.
- J.-W. Hong and H.-K. Kim, Macromol. Res., 2006, 14, 617–623 CrossRef CAS.
- C.-W. Chang, H.-L. Lee and K.-T. Lu, Coatings, 2018, 9, 11 CrossRef.
- R. Gao, L. Wang and Q. Lin, Prog. Org. Coat., 2019, 133, 169–173 CrossRef CAS.
- D. Zhang, J. Xia, H. Xue, Y. Zhang and Q. Lin, Polym. Eng. Sci., 2020, 60, 1177–1185 CrossRef CAS.
- R.-J. Sang and Z.-X. Fan, J. For. Eng., 2022, 7, 177–182 Search PubMed.
- F. Jiang, M. Zhou and D. Drummer, Polymers, 2022, 14, 3107 CrossRef CAS PubMed.
- R.-J. Sang, Z.-H. Wu, Z.-X. Fan and S.-Q. Yang, J. For. Eng., 2022, 7, 187–193 Search PubMed.
- L. Wu, M. Chen, J. Xu, F. Fang, S. Li and W. Zhu, Coatings, 2022, 12, 1453 CrossRef CAS.
- H. Karbalaei, A. Tarmian, D. Rasouli and S. Pourmahdian, Wood Mater. Sci. Eng., 2021, 1–10 Search PubMed.
- P. Bednarczyk, K. Mozelewska, M. Nowak and Z. Czech, Materials, 2021, 14, 4150 CrossRef CAS PubMed.
- H.-J. Oh, J. H. Hwang, M. Park, S. J. Kim, J. Lee, H. S. Lim, S.-S. Lee, J. A. Lim and E. Lee, Ultrason. Sonochem., 2021, 73, 105545 CrossRef CAS PubMed.
- K.-T. Lu and J.-J. Lee, Polymers, 2021, 13, 1110 CrossRef CAS PubMed.
- S.-C. Hu, J. Cheng, W.-P. Wang, Y.-H. Zhu, K. Kang, M.-Q. Zhu and X.-H. Huang, Energy, 2022, 239, 121918 CrossRef CAS.
- F. Fang, H.-Y. Guan, Z.-P. Lu and M.-Z. Li, J. For. Eng., 2021, 6, 191–197 Search PubMed.
- H. Lee, H. Han, D. Kim, B. Lee, J. H. Cho, Y. Lee, S.-S. Lee and J. A. Lim, Prog. Org. Coat., 2021, 154, 106195 CrossRef CAS.
- B.-C. Shiu, K. Wu, C.-W. Lou, Q. Lin and J.-H. Lin, Polymers, 2021, 13, 2858 CrossRef CAS PubMed.
- Y. Zhang, T.-T. Li, B.-C. Shiu, J.-H. Lin and C.-W. Lou, Appl. Surf. Sci., 2022, 584, 152573 CrossRef CAS.
- A. Chen, C. Zhang, G. Zhu and Z. L. Wang, Adv. Sci., 2020, 7, 2000186 CrossRef CAS PubMed.
- P. Song and H. Wang, Adv. Mater., 2020, 32, 1901244 CrossRef CAS PubMed.
- D. Li, K. Li and J. Fang, ChemistrySelect, 2022, 7, e202200943 CAS.
- Y. Chen, G. Zhang, G. Zhang and C. Ma, Chem. Eng. J., 2021, 421, 129755 CrossRef CAS.
- N. Niimura and T. Miyakoshi, Talanta, 2006, 70, 146–152 CrossRef CAS PubMed.
- J. Yang, Y. Du, R. Huang, Y. Wan and T. Li, Int. J. Biol. Macromol., 2002, 31, 55–62 CrossRef CAS PubMed.
- X.-R. Peng, Z.-K. Zhang and L.-R. Zhao, J. For. Eng., 2020, 5, 45–51 Search PubMed.
Footnote |
† These authors contributed equally to this work. |
|
This journal is © The Royal Society of Chemistry 2023 |
Click here to see how this site uses Cookies. View our privacy policy here.