DOI:
10.1039/D3NR03797E
(Paper)
Nanoscale, 2023,
15, 15975-15981
Selective and controlled H2 generation upon additive-free HCOOH dehydrogenation over a Pd/NCS nanocatalyst†
Received
31st July 2023
, Accepted 6th September 2023
First published on 14th September 2023
Abstract
Although sodium formate is widely used as a conventional additive to enhance selective H2 evolution from HCOOH dehydrogenation, this leads to a waste of resources and an increase in the cost of H2 production. For this reason, N-doped carbon nanospheres with abundant graphitic C/N have been designed to enrich the electron cloud density of the Pd atom for improving its catalytic activity in H2 generation upon additive-free HCOOH dehydrogenation. Herein, we have synthesized N-doped carbon nanosphere-stabilized Pd nanoparticles (Pd/NCSs) as high-efficiency nano-catalysts, via fixation of Pd nanoparticles onto N-doped carbon nanospheres (NCSs), for selective and controlled H2 generation upon additive-free HCOOH dehydrogenation. Pd/NCS-800 (1640 h−1) provided a 12 times larger TOF than commercial Pd/C (134 h−1) in H2 generation upon additive-free HCOOH dehydrogenation. It seemed that graphitic N/C of NCS-800 enriched the electron cloud density of the Pd atom, which was favorable for the cleavage of C–H bonds in HCOOH dehydrogenation. In addition, the selective H2 evolution from additive-free HCOOH dehydrogenation over Pd/NCS-800 is successfully controlled by adjusting the pH.
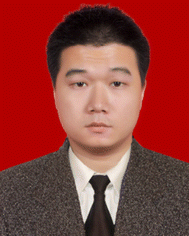 Xiang Liu | Xiang Liu received his Ph.D. degree at Université de Rennes 1 in 2017. He is now an associate professor and independent researcher at China Three Gorges University. His research interests are organic synthesis, photocatalysis and functionalization, and engineering of transition-metal nanoparticles or nanoclusters for applications in H2 evolution and water treatment. He has published more than 120 SCI papers in journals such as Adv. Mater., Nat. Commun., Appl. Catal. B. Environ., iScience, ACS Catal., J. Mater. Chem. A, Chem. Sci., Chem. Eng. J. and so on. |
Introduction
Humanity's high dependence on traditional fossil fuels has caused the growth of greenhouse gas emission (e.g. CO2 and CH4),1–3 which leads to ocean acidification, climatic anomaly, global warming and other environmental deterioration.4–7 To overcome this issue, it is of high significance to develop renewable energy sources, switching from fossil fuels, for a green future.8–10 Hydrogen (H2) is identified as the most promising renewable energy carrier because of its superior energy density and environmentally-friendly economy.11–15 However, physical storage of H2 gas suffers from low capacity, high costs and explosibility.16–20 In this regard, a good deal of hydrogen storage materials, for instance methanol,21–24 borohydrides,25,26 silicohydrides,27 ammonia borane,28 hydrazine hydrate29 and formic acid,30–32 are being intensively developed for H2 generation.
Since 1978,33 formic acid (HCOOH), which could be readily obtained from biomass, has been deemed as the most promising liquid hydrogen carrier due to its excellent hydrogen storage capacity (4.4 wt% and 53 g L−1), low toxicity, outstanding stability and safe transportation/storage.34–40 As a consequence, plenty of heterogeneous and homogeneous catalysts have been explored for selective H2 evolution from formic acid dehydrogenation (HCOOH → H2↑ + CO2↑) and preventing CO release from formic acid dehydration (HCOOH → H2O + CO↑).41–47 Among them, PdAg bimetal nanomaterials exhibited superior catalytic activities in H2 generation from formic acid dehydrogenation because the alloying of Ag could enrich the electron cloud density of the Pd atom in PdAg, which was in favor of C–H bond cleavage in HCOOH dehydrogenation.48 Although sodium formate is widely used as an additive to improve selective H2 evolution upon HCOOH dehydrogenation,49 this leads to a waste of resources and an increase in the cost of H2 production.
For this reason, we have designed and synthesized N-doped carbon nanospheres with abundant graphitic C/N for enriching the electron cloud density of the Pd atom in additive-free HCOOH dehydrogenation. Herein, we have synthesized N-doped carbon nanosphere-stabilized Pd nanoparticles (Pd/NCSs) as high-efficiency nano-catalysts, via fixation of Pd nanoparticles onto N-doped carbon nanospheres (NCSs), for selective and controlled H2 generation upon additive-free HCOOH dehydrogenation. Then the kinetic behavior and catalytic activity of Pd/NCSs, mechanistic insight using a tandem reaction, CO2 capture ability, and “on–off” control for selective and controlled H2 generation upon additive-free HCOOH dehydrogenation were investigated.
Results and discussion
As described in Scheme 1, NCS-700, NCS-800 and NCS-900 were synthesized by the calcination of melamine, α-D-glucose hydrochar and NaHCO3, with a mass ratio of 1.0
:
1.0
:
1.0, at 700 °C, 800 °C and 900 °C under a N2 atmosphere for 1 h, respectively.50 Then Pd/NCS-700, Pd/NCS-800 and Pd/NCS-900 were synthesized by using K2PdCl4 and NCSs, followed by NaBH4 reduction, respectively. For studying the structure and morphology of NCS and Pd/NCSs, their SEM images were obtained and are shown in Fig. 1. As illustrated in Fig. S1,† the SEM image shows that the NCS precursor has a uniform spherical structure with a mean size of 0.27 μm (Fig. S2†). After high temperature carbonization, the uniform spherical structure was retained in Pd/NCS-700 (0.23 μm, Fig. 1a, b & S3†), Pd/NCS-800 (0.22 μm, Fig. 1c, d & S4†) and Pd/NCS-900 (0.22 μm, Fig. 1e, f & S5†), and the size of the NCSs reduced as the calcination temperature increased. Then, XRD, FTIR, Raman spectrum and BET analyses were employed to measure the microstructure of Pd/NCS-700, Pd/NCS-800 and Pd/NCS-900. As shown in Fig. 2a, a broad diffraction peak of graphitic C (002) at 2θ = 24° appeared in all of the Pd/NCSs (JCPDS 75-1621).51 Pd (111) and Pd (200) were also found in Pd/NCSs (JCPDS 87-0638),52 showing that the PdNPs were immobilized on the surface of NCSs. In the FTIR spectra of Pd/NCSs (Fig. 2b), the absorption peaks at 3232, 2356, 1575 and 1228 cm−1 corresponded to the –OH, C–H, C
C and C–O–C groups, respectively,53 which were favorable for PdNP stabilization. As presented in Raman spectra (Fig. 2c), the three peaks at 1338, 1613 and 2756 cm−1 were assigned to the D-band, G-band and 2D-band, respectively.54 The values of ID/IG in Pd/NCS-700, Pd/NCS-800 and Pd/NCS-900 were 1.00, 1.08 and 1.13, respectively, suggesting that the content of disordered carbon increased as the calcination temperature increased. Moreover, the texture properties of Pd/NCSs were studied by BET analysis. As shown in Fig. S6† and Table 1, Pd/NCS-900 exhibited a larger surface area and pore volume (635.09 m2 g−1 & 0.37 m3 g−1) than Pd/NCS-700 and Pd/NCS-800.
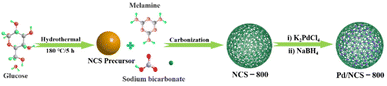 |
| Scheme 1 The synthesis of Pd/NCS-800 nanocomposites. | |
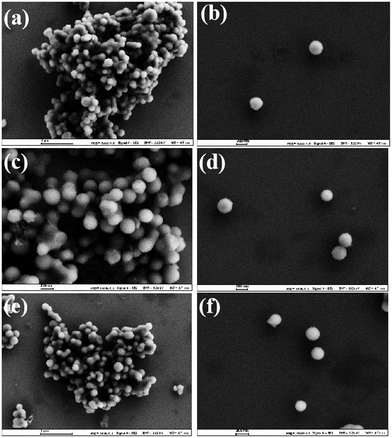 |
| Fig. 1 SEM images of (a and b) Pd/NCS-700, (c and d) Pd/NCS-800 and (e and f) Pd/NCS-900. | |
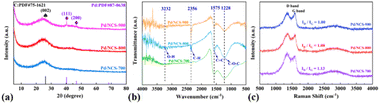 |
| Fig. 2 (a) XRD, (b) FT-IR, and (c) Raman spectra of Pd/NCS-700, Pd/NCS-800 and Pd/NCS-900. | |
Table 1 BET analysis of Pd/NCS-700, Pd/NCS-800 and Pd/NCS-900
Catalysts |
Surface area (m2 g−1) |
Pore volume (m3 g−1) |
Pore size (nm) |
Pd/NCS-700 |
458.43 |
0.27 |
2.34 |
Pd/NCS-800 |
572.74 |
0.33 |
2.33 |
Pd/NCS-900 |
635.09 |
0.37 |
2.33 |
First, the catalytic performances of Pd/NCSs in H2 generation upon additive-free HCOOH dehydrogenation were compared as shown in Fig. S7.† H2 production was carried out with HCOOH (1 mmol) and 2 mol% of Pd/NCSs in 5 mL of H2O at 60 °C. It is clear that Pd/NCS-800 exhibited a superior catalytic performance, with a TOF of 1640 h−1, compared to Pd/NCS-700 (1456 h−1) and Pd/NCS-900 (921 h−1) in additive-free HCOOH dehydrogenation. Hence, Pd/NCS-800 was chosen as the optimal catalyst because of its kinetic behavior, recyclability, CO2 capture ability, tandem reaction, and “on–off” switch of H2 generation upon additive-free HCOOH dehydrogenation.
For probing why Pd/NCS-800 was so super-efficient in H2 generation upon additive-free HCOOH dehydrogenation, TEM and HRTEM were employed to confirm the morphology of Pd/NCS-800. From Fig. 3a–e, it is clear that Pd/NCS-800 possessed a homogeneous nanospherical structure, and PdNPs (3.19 nm, Fig. S8†) were successfully stabilized onto the surface of N-doped carbon nanospheres. As shown in Fig. 3f, Pd (111), whose corresponding lattice space is 0.22 nm, was recorded in Pd/NCS-800, verifying the presence of PdNPs on NCSs. Then, the precise localization of Pd, N, O and C elements in Pd/NCS-800 was further investigated by EDX elemental mapping. As described in Fig. 4, the Pd/NCS-800 nanocomposite was made up of palladium, nitrogen, oxygen and carbon elements, verifying that N atoms were successfully doped into carbon nanospheres.
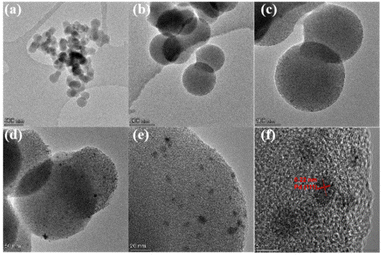 |
| Fig. 3 (a)–(e) TEM and (f) HRTEM images of Pd/NCS-800. | |
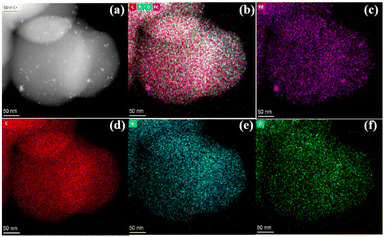 |
| Fig. 4 (a) STEM and (b) combined C, N, O and Pd, (c) Pd, (d) C, (e) N and (f) O EDX mapping of Pd/NCS-800. | |
In addition, XPS was employed to investigate the elemental composition and chemical valence of Pd/NCS-800. As displayed in Fig. 5a, the Pd 3d5/2 spectrum is deconvolved into two peaks of Pd0 (336.26 eV) and PdII (337.94 eV), demonstrating that Pd nanoparticles were partly oxidized by air into PdII.55 In Fig. 5b, the N 1s spectrum is fitted into four peaks of nitric oxide (405.1 eV, 19.9%), graphitic-N (401.4 eV, 18.5%), pyrrolic-N (399.9 eV, 26.2%) and pyridinic-N (398.2 eV, 35.4%). As displayed in Fig. 5c, the C 1s spectrum is fitted into five typical peaks at 290.3, 288.3, 286.3, 285.4 and 284.6 eV, which are assigned to π–π* (10.05%), C
O (12.49%), C–O (18.58%), C–N (23.28%) and C–C/C
C (35.60%), respectively. As illustrated in Fig. 5d, the O 1s spectrum is fitted into four typical peaks of C–O–C (534.17 eV), C–C
O (532.53 eV), C–OH (531.44 eV) and C
O (530.47 eV), respectively. These results exhibited the presence of N and O-containing functional groups at the Pd/NCS-800 surface. ICP-AES verified that Pd nanoparticles were stabilized onto the surface of NCSs (5.38 wt% Pd, which was slightly smaller than the theoretical value of 6.62 wt%).
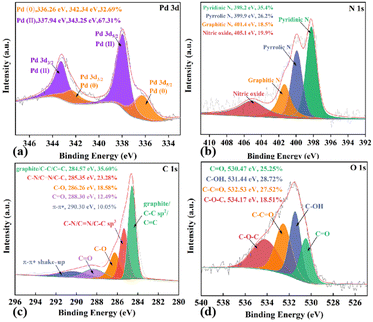 |
| Fig. 5 (a) Pd 3d, (b) N 1s, (c) C 1s and (d) O 1s XPS of Pd/NCS-800. | |
The kinetics of H2 generation upon additive-free HCOOH dehydrogenation (including different Pd/NCS-800 catalyst dosages, various initial HCOOH concentrations and reaction temperatures) was further studied for the potential industrial application. As described in Fig. 6a, the H2 generation upon additive-free HCOOH dehydrogenation was conducted with various dosages of the Pd/NCS-800 catalyst from 1.5 to 3.0 mol%. The H2 generation rate elevated as the Pd/NCS-800 catalyst dosage increased, with a slope of 1.4, illustrating that there was a linear positive relationship between them. As presented in Fig. 6b, the H2 production rate was independent of the initial HCOOH concentration, indicating that additive-free HCOOH dehydrogenation was a zero-order reaction with the initial HCOOH concentration. Then H2 generation upon additive-free HCOOH dehydrogenation over Pd/NCS-800 was measured at various reaction temperatures from 313 to 343 K (Fig. 6c). The Ea of H2 generation upon additive-free HCOOH dehydrogenation over Pd/NCS-800 was obtained to be 39.63 kJ mol−1. The comparison of Pd/NCS-800 and commercial Pd/C in H2 generation upon additive-free HCOOH dehydrogenation was recorded and is shown in Fig. 6d. The result shows that Pd/NCS-800 (1640 h−1) provided a 12 times larger TOF than commercial Pd/C (134 h−1) in H2 generation upon additive-free HCOOH dehydrogenation. In addition, the Pd/NCS-800 catalyst also showed excellent catalytic performance in H2 generation from NH3BH3 (NH3BH3 + 4H2O → NH4B(OH)4 + 3H2↑, TOF = 11
116.1 h−1, Fig. 7a), tetrahydroxydiboron (B2(OH)4 + 2H2O → 2B(OH)3 + H2↑, TOF = 10
111.6 h−1, Fig. 7b), dimethylaminoborane (Me2NHBH3 + 4H2O → Me2NH2B(OH)4 + 3H2↑, TOF = 2902 h−1, Fig. 7c) and tetramethyldisiloxane ([Me2SiH]2O + 2H2O → [Me2Si(OH)]2O + 2H2↑, TOF = 1955 h−1, Fig. 7d), confirming that the Pd/NCS-800 catalyst is a versatile and applicable catalyst.
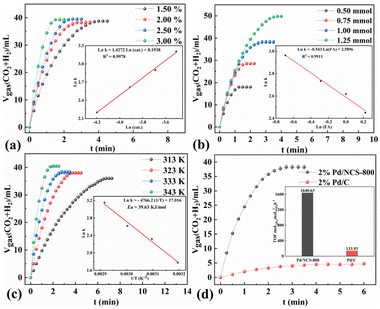 |
| Fig. 6 The volumes of generated CO2 and H2 gases vs. time for H2 generation upon additive-free HCOOH dehydrogenation (a) with various amounts of the catalyst, (b) with different amounts of HCOOH and (c) at different reaction temperatures; (d) comparison of additive-free HCOOH dehydrogenation catalyzed by Pd/NCS-800 and Pd/C. | |
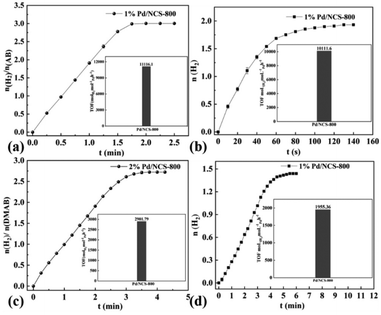 |
| Fig. 7 Pd/NCS-800 catalyzed H2 generation from (a) ammonia borane, (b) B2(OH)4, (c) dimethylaminoborane and (d) tetramethyldisiloxane at 30 °C. | |
The stability of the Pd/NCS-800 catalyst in H2 generation upon additive-free HCOOH dehydrogenation was investigated for further industrial application.56 When H2 generation was completed, the Pd/NCS-800 nanocatalyst was isolated and recycled by filtration. Next, another fresh HCOOH solution was injected into the medium for next recycling. As described in Fig. S9,† it is clear that the Pd/NCS-800 catalyst still maintained excellent catalytic activity at least for 5 cycles in H2 generation upon additive-free HCOOH dehydrogenation without any activity loss. Then, the 5 times reused Pd/NCS-800 catalyst was further analyzed by XRD, and Fig. S10† shows that its crystal structure remained almost the same as that of the fresh one, demonstrating that Pd/NCS-800 is a heterogeneous and recyclable nanocatalyst for H2 generation upon additive-free HCOOH dehydrogenation.
H2 generation upon additive-free HCOOH dehydrogenation is applied not only for safe and economical production, storage and transportation of hydrogen, but also for a tandem reaction.57 1,1-Diphenylethylene hydrogenation with the in situ released H2 from additive-free HCOOH dehydrogenation was carried out in a two-chamber reactor (Scheme 2). The left tube was applied for H2 generation upon additive-free HCOOH dehydrogenation, and the right one was applied for 1,1-diphenylethylene hydrogenation with the H2 from the left tube via a glass tube (Fig. S11†). The yield of the target product (1,1-diphenylethane) was 99% (Fig. S12†), illustrating selective H2 generation upon additive-free HCOOH dehydrogenation.
 |
| Scheme 2 The tandem reaction. | |
For verifying the selective H2 generation upon additive-free HCOOH dehydrogenation, a gas mixture was passed through a NaOH solution for CO2 absorption. As shown in Fig. 8a, the volume of the gas mixture was reduced by half with the sodium hydroxide trap, suggesting that the released gases were H2 and CO2, with a volumetric ratio of 1.0
:
1.0. Then the released gases were also confirmed by GC to be H2 and CO2, with a molar ratio of 1.0
:
1.0 (Fig. 8b). The CO2 capture test and GC analysis verified that the selective H2 generation upon additive-free formic acid dehydrogenation over the Pd/NCS-800 catalyst was successfully designed for fuel cells. Based on the CO2 capture test, GC analysis and relevant literature,58,59 a possible mechanism involved in HCOOH dehydrogenation is discussed in Fig. S13.† First, a HCOOH molecule was decomposed into Pd–H and HCOO–Pd on the surface of Pd/NCS-800. Then, CO2* and Pd–H were formed from HCOO–Pd via β-hydride elimination. Finally, H2 was obtained by the reductive elimination of two Pd–H molecules.
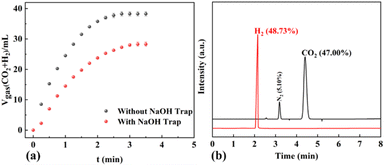 |
| Fig. 8 (a) HCOOH dehydrogenation over Pd/NCS-800 with and without a sodium hydroxide trap; (b) GC spectra of the gases released from additive-free HCOOH dehydrogenation at 60 °C. | |
The exploitation of the “on–off” switch for demand-based H2 production is highly desirable.60–62 As demonstrated in Fig. 9, selective H2 generation upon additive-free HCOOH dehydrogenation over Pd/NCS-800 was successfully controlled by adjusting the pH. Specifically, H2 generation upon additive-free HCOOH dehydrogenation stopped after the addition of NaOH solution because formic acid converted into formate. Then, H2 generation upon additive-free formic acid dehydrogenation restarted after the addition of H2SO4 solution due to the regeneration of formic acid. However, a slight decrease in the H2 generation rate was recorded after each “on–off” switch, which may be caused by the dilution effect.
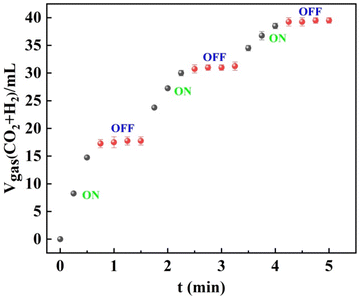 |
| Fig. 9 “On–off” switch of H2 generation upon additive-free formic acid dehydrogenation. Reaction conditions: 1 mmol of formic acid and 2 mol% of Pd/NCS-800 in water (5 mL) at 60 °C. | |
The catalytic performances of Pd/NCS-800 and other reported catalysts for H2 generation upon additive-free HCOOH dehydrogenation were compared and are shown in Table S1.†
63–72 The result shows that Pd/NCS-800 exhibited an excellent TOF of 1641 h−1, illustrating that Pd/NCS-800 is an excellent catalyst for selective and controlled H2 generation upon additive-free HCOOH dehydrogenation.
Conclusions
In summary, a battery of N-doped carbon nanosphere-stabilized Pd nanoparticles (Pd/NCSs) have been synthesized as high-efficiency nano-catalysts, via fixation of Pd nanoparticles onto N-doped carbon nanospheres (NCSs), for selective and controlled H2 generation upon additive-free HCOOH dehydrogenation. The characterization studies confirmed that Pd/NCS-800 has a homogeneous nanospherical structure, and PdNPs are stabilized onto the surface of N-doped carbon nanospheres. Pd/NCS-800 showed superior catalytic performance, with a TOF of 1640 h−1, compared to Pd/NCS-700 (1456 h−1) and Pd/NCS-900 (921 h−1) in H2 generation upon additive-free HCOOH dehydrogenation. The CO2 capture test, GC analysis and tandem reaction verified that selective H2 generation upon additive-free formic acid dehydrogenation over the Pd/NCS-800 catalyst was developed for fuel cells. Pd/NCS-800 (1640 h−1) provided a 12 times larger TOF than commercial Pd/C (134 h−1) in H2 generation upon additive-free HCOOH dehydrogenation. It seemed that graphitic N/C of NCS-800 enriched the electron cloud density of the Pd atom, which was favorable for the cleavage of C–H bonds in HCOOH dehydrogenation. In addition, the selective H2 production from additive-free HCOOH dehydrogenation over Pd/NCS-800 is successfully controlled by adjusting the pH. The strategy derived from glucose in this work might generate new ideas for the development of N-doped carbon nanospheres for selective and controlled H2 generation.
Author contributions
Q. Zhang: investigation and formal analysis. Y. Wang and X. Jin: formal analysis. X. Liu: project administration, supervision, resources, conceptualization, and writing – original draft, review & editing.
Conflicts of interest
The authors declare no competing financial interest.
Acknowledgements
Financial support from the NSFC (No. 21805166) is gratefully acknowledged and thanks eceshi (https://www.eceshi.com) for the ICP test and Yuan Zhou from Shiyanjia Lab (https://www.shiyanjia.com) for GC test.
References
- S. Kar, M. Rauch, G. Leitus, Y. Ben-David and D. Milstein, Nat. Catal., 2021, 4, 193–201 CrossRef CAS PubMed.
- X. Liu, W. Hou, Y. Huang, H. Zhao, Z. Song and Y. Huang, Chem. Eng. J., 2022, 433, 133822 CrossRef CAS.
- S. Xu, H. Zhao, T. Li, J. Liang, S. Lu, G. Chen, S. Gao, A. M. Asiri, Q. Wu and X. Sun, J. Mater. Chem. A, 2020, 8, 19729–19745 RSC.
- C. Peng, T. Li, Y. Zou, C. Xiang, F. Xu, J. Zhang and L. Sun, Int. J. Hydrogen Energy, 2021, 46, 666–675 CrossRef CAS.
- H. Song, M. Wu, Z. Tang, J. S. Tse, B. Yang and S. Lu, Angew. Chem., Int. Ed., 2021, 60, 7234–7244 CrossRef CAS PubMed.
- Y. Peng, Y. Zhang, A. Guo, M. Mao, Y. Wang, Y. Long and G. Fan, Chem. Eng. J., 2022, 433, 133648 CrossRef CAS.
- H. Liu, Q. Lei, R. Miao, M. Sun, C. Qin, L. Zhang, G. Ye, Y. Yao, B. Huang and Z. Ma, Adv. Funct. Mater., 2022, 32, 2207408 CrossRef CAS.
- N. Kang, X. Wei, R. Shen, B. Li, E. G. Cal, S. Moya, L. Salmon, C. Wang, E. Coy, M. Berlande, J.-L. Pozzo and D. Astruc, Appl. Catal., B, 2023, 320, 121957 CrossRef CAS.
- M. S. İzgi, O. Baytar, Ö. Şahin and H. Ç. Kazıcı, Int. J. Hydrogen Energy, 2020, 45, 34857–34866 CrossRef.
- H. N. Abdelhamid, Int. J. Hydrogen Energy, 2021, 46, 726–765 CrossRef CAS.
-
(a) X. Zou and Y. Zhang, Chem. Soc. Rev., 2015, 44, 5148–5180 RSC;
(b) L. Zhang, H. Zhao, S. Xu, Q. Liu, T. Li, Y. Luo, S. Gao, X. Shi, A. M. Asiri and X. Sun, Small Struct., 2021, 2, 2000048 CrossRef CAS;
(c) J. Chen, L. Zhang, J. Li, X. He, Y. Zheng, S. Sun, X. Fang, D. Zheng, Y. Luo, Y. Wang, J. Zhang, L. Xie, Z. Cai, Y. Sun, A. A. Alshehri, Q. Kong, C. Tang and X. Sun, J. Mater. Chem. A, 2023, 11, 1116–1122 RSC;
(d) Q. Liu, S. Sun, L. Zhang, Y. Luo, Q. Yang, K. Dong, X. Fang, D. Zheng, A. A. Alshehri and X. Sun, Nano Res., 2022, 15, 8922–8927 CrossRef CAS.
- T. Hisatomi, J. Kubota and K. Domen, Chem. Soc. Rev., 2014, 43, 7520–7535 RSC.
-
(a) C. C. L. McCrory, S. Jung, I. M. Ferrer, S. M. Chatman, J. C. Peters and T. F. Jaramillo, J. Am. Chem. Soc., 2015, 137, 4347–4357 CrossRef CAS PubMed;
(b) L. Ouyang, X. He, Y. Sun, L. Zhang, D. Zhao, S. Sun, Y. Luo, D. Zheng, A. M. Asiri, Q. Liu, J. Zhao and X. Sun, Inorg. Chem. Front., 2022, 9, 6602–6607 RSC.
- J. Wang, W. Cui, Q. Liu, Z. Xing, A. M. Asiri and X. Sun, Adv. Mater., 2016, 28, 215–230 CrossRef CAS PubMed.
- J. Ran, J. Zhang, J. Yu, M. Jaroniec and S. Z. Qiao, Chem. Soc. Rev., 2014, 43, 7787–7812 RSC.
- Y. Liu, F. Fu, L. Salmon, B. Espuche, S. Moya, M. Berlande, J.-L. Pozzo, J.-R. Hamon and D. Astruc, ACS Appl. Mater. Interfaces, 2023, 15, 23343–23352 CrossRef CAS PubMed.
- N. Gao, D. Han, T. Yang, Q. Meng, X. Wang, C. Liu, J. Ge and W. Xing, Appl. Catal., B, 2023, 336, 122913 CrossRef CAS.
- X. Sun, Y. Ding, G. Feng, Q. Yao, J. Zhu, J. Xia and Z.-H. Lu, J. Colloid Interface Sci., 2023, 645, 676–684 CrossRef CAS PubMed.
- Z. Yuan, T. Cao, M. Deng, J. Ma, S. Geng, C. Yang, Y. Ren, M. Yao, F. Liu and X. Wang, Fuel, 2023, 346, 128333 CrossRef CAS.
- J. Wang, Y. Yu, H. Yu, W. Wang, L.-L. Shen, G.-R. Zhang and D. Mei, ACS Catal., 2023, 13, 5135–5146 CrossRef CAS.
- A. Kumar, P. Daw and D. Milstein, Chem. Rev., 2022, 122, 385–441 CrossRef CAS PubMed.
- J. Hao, J. Liu, D. Wu, M. Chen, Y. Liang, Q. Wang, L. Wang, X.-Z. Fu and J.-L. Luo, Appl. Catal., B, 2021, 281, 119510 CrossRef CAS.
- L. Lin, Q. Yu, M. Peng, A. Li, S. Yao, S. Tian, X. Liu, A. Li, Z. Jiang, R. Gao, X. Han, Y.-w. Li, X.-d. Wen, W. Zhou and D. Ma, J. Am. Chem. Soc., 2021, 143, 309–317 CrossRef CAS PubMed.
- Z. Li, X. Tang, Y. Jiang, Y. Wang, M. Zuo, W. Chen, X. Zeng, Y. Sun and L. Lin, Chem. Commun., 2015, 51, 16320–16323 RSC.
- C. Wang and D. Astruc, Chem. Soc. Rev., 2021, 50, 3437–3484 RSC.
- C. Wang, Q. Wang, F. Fu and D. Astruc, Acc. Chem. Res., 2020, 53, 2483–2493 CrossRef CAS PubMed.
- X. Liu, X. Jin, J. Yan, S. Fan, Y. Wang and D. Astruc, Appl. Catal., B, 2023, 324, 122261 CrossRef CAS.
- S. Guan, Y. Liu, H. Zhang, R. Shen, H. Wen, N. Kang, J. Zhou, B. Liu, Y. Fan, J. Jiang and B. Li, Adv. Sci., 2023, 2300726 CrossRef CAS PubMed.
- J. Cao, W. Huang, Y. Wang, Q. Zhang and X. Liu, J. Mol. Liq., 2023, 369, 120917 CrossRef CAS.
- Z. Li and Q. Xu, Acc. Chem. Res., 2017, 50, 1449–1458 CrossRef CAS PubMed.
- Z. L. Wang, J. M. Yan, Y. Ping, H. L. Wang, W. T. Zheng and Q. Jiang, Angew. Chem., Int. Ed., 2013, 52, 4406–4409 CrossRef CAS PubMed.
- Y. Liu, J. Zhang, Y. Li, Q. Qian, Z. Li, Y. Zhu and G. Zhang, Nat. Commun., 2020, 11, 1853 CrossRef CAS PubMed.
- R. Williams, R. S. Crandall and A. Bloom, Appl. Phys. Lett., 2008, 33, 381–383 CrossRef.
- Z. Chen, C. A. M. Stein, R. Qu, N. Rockstroh, S. Bartling, J. Weiß, C. Kubis, K. Junge, H. Junge and M. Beller, ACS Catal., 2023, 13, 4835–4841 CrossRef CAS.
- M. Karatok, H. T. Ngan, X. Jia, C. R. O'Connor, J. A. Boscoboinik, D. J. Stacchiola, P. Sautet and R. J. Madix, J. Am. Chem. Soc., 2023, 145, 5114–5124 CrossRef CAS PubMed.
- W.-F. Peng, X. Sun, Y. Ding, P. Liu, Q. Yao and Z.-H. Lu, ACS Sustainable Chem. Eng., 2023, 11, 1898–1908 CrossRef CAS.
- L. Yaacoub, I. Dutta, B. Werghi, B. W. J. Chen, J. Zhang, E. A. Hamad, E. P. Ling Ang, E. Pump, A. B. Sedjerari, K.-W. Huang and J.-M. Basset, ACS Catal., 2022, 12, 14408–14417 CrossRef CAS.
- Y. Ding, W. Peng, L. Zhang, J. Xia, G. Feng and Z.-H. Lu, J. Colloid Interface Sci., 2023, 630, 879–887 CrossRef CAS PubMed.
- M. Deng, A. Yang, J. Ma, C. Yang, T. Cao, S. Yang, M. Yao, F. Liu, X. Wang and J. Cao, ACS Appl. Mater. Interfaces, 2022, 14, 18550–18560 CrossRef CAS PubMed.
- Q. Zhang, Q. Mao, Y. Zhou, L. Zou, D. Zhu, Y. Huang, H. Gao, X. Luo, Y. Mao and Z. Liang, ACS Sustainable Chem. Eng., 2022, 10, 4599–4609 CrossRef CAS.
- D.-X. Liu, Y.-T. Zhou, Y.-F. Zhu, Z.-Y. Chen, J.-M. Yan and Q. Jiang, Appl. Catal., B, 2022, 309, 121228 CrossRef CAS.
- D. H. Carrales-Alvarado, C. López-Olmos, A. B. Dongil, A. Kubacka, A. Guerrero-Ruiz and I. Rodríguez-Ramos, Appl. Catal., B, 2021, 298, 120604 CrossRef CAS.
- S. Prabu and K.-Y. Chiang, J. Colloid Interface Sci., 2021, 604, 584–595 CrossRef CAS PubMed.
- C. Martin, A. Quintanilla, G. Vega and J. A. Casas, Appl. Catal., B, 2022, 317, 121802 CrossRef CAS.
- S. Zhong, X. Yang, L. Chen, N. Tsumori, N. Taguchi and Q. Xu, ACS Appl. Mater. Interfaces, 2021, 13, 46749–46755 CrossRef CAS PubMed.
- C. Wan, L. Zhou, S. Xu, B. Jin, X. Ge, X. Qian, L. Xu, F. Chen, X. Zhan, Y. Yang and D.-g. Cheng, Chem. Eng. J., 2022, 429, 132388 CrossRef CAS.
- W. Peng, S. Liu, X. Li, G. Feng, J. Xia and Z.-H. Lu, Chin. Chem. Lett., 2022, 33, 1403–1406 CrossRef CAS.
- F. Xu and X. Liu, ACS Catal., 2021, 11, 13913–13920 CrossRef CAS.
- F. Xu, J. Yan, Y. Wang and X. Liu, iScience, 2023, 26, 106504 CrossRef CAS PubMed.
- Z. Pi, K. Hou, F. Yao, L. He, S. Chen, Y. Fu, X. Li and Q. Yang, Carbon, 2022, 196, 736–748 CrossRef CAS.
- Y. Qian, S. Jiang, Y. Li, Z. Yi, J. Zhou, J. Tian, N. Lin and Y. Qian, Angew. Chem., Int. Ed., 2019, 58, 18108–18115 CrossRef CAS PubMed.
- S. Hyok Ri, F. Bi, A. Guan and X. Zhang, J. Colloid Interface Sci., 2021, 586, 836–846 CrossRef CAS PubMed.
- W. Huang, F. Xu, D.-S. Li, D. Astruc and X. Liu, Carbon Energy, 2023, 5, e269 CrossRef CAS.
- D. B. Schuepfer, F. Badaczewski, J. M. Guerra-Castro, D. M. Hofmann, C. Heiliger, B. Smarsly and P. J. Klar, Carbon, 2020, 161, 359–372 CrossRef CAS.
- C. H. Wu, C. Liu, D. Su, H. L. Xin, H.-T. Fang, B. Eren, S. Zhang, C. B. Murray and M. B. Salmeron, Nat. Catal., 2019, 2, 78–85 CrossRef CAS.
- Y. Yan, B. Y. Xia, B. Zhao and X. Wang, J. Mater. Chem. A, 2016, 4, 17587–17603 RSC.
- F. Fu, C. Wang, Q. Wang, A. M. Martinez-Villacorta, A. Escobar, H. Chong, X. Wang, S. Moya, L. Salmon, E. Fouquet, J. Ruiz and D. Astruc, J. Am. Chem. Soc., 2018, 140, 10034–10042 CrossRef CAS PubMed.
- J. S. Yoo, Z.-J. Zhao, J. K. Nørskov and F. Studt, ACS Catal., 2015, 5, 6579–6586 CrossRef CAS.
- F.-Z. Song, Q.-L. Zhu, X. Yang, W.-W. Zhan, P. Pachfule, N. Tsumori and Q. Xu, Adv. Energy Mater., 2018, 8, 1701416 CrossRef.
- S. Santra, D. Das, N. S. Das and K. K. Nanda, Chem. Sci., 2017, 8, 2994–3001 RSC.
- C. Wang, J. Tuninetti, Z. Wang, C. Zhang, R. Ciganda, L. Salmon, S. Moya, J. Ruiz and D. Astruc, J. Am. Chem. Soc., 2017, 139, 11610–11615 CrossRef CAS PubMed.
- S. Santra, D. Das, N. S. Das and K. K. Nanda, ACS Appl. Energy Mater., 2019, 2, 260–268 CrossRef CAS.
- A. Bulut, M. Yurderi, Y. Karatas, M. Zahmakiran, H. Kivrak, M. Gulcan and M. Kaya, Appl. Catal., B, 2015, 164, 324–333 CrossRef CAS.
- Z. Wang, S. Liang, X. Meng, S. Mao, X. Lian and Y. Wang, Appl. Catal., B, 2021, 291, 120140 CrossRef CAS.
- I. Barlocco, S. Capelli, E. Zanella, X. Chen, J. J. Delgado, A. Roldan, N. Dimitratos and A. Villa, J. Energy Chem., 2021, 52, 301–309 CrossRef CAS.
- Y. Gao, E. Hu, G. Yin and Z. Huang, Fuel, 2021, 302, 121142 CrossRef CAS.
- Y. Karatas, A. Bulut, M. Yurderi, I. E. Ertas, O. Alal, M. Gulcan, M. Celebi, H. Kivrak, M. Kaya and M. Zahmakiran, Appl. Catal., B, 2016, 180, 586–595 CrossRef CAS.
- Z.-L. Wang, J.-M. Yan, Y.-F. Zhang, Y. Ping, H.-L. Wang and Q. Jiang, Nanoscale, 2014, 6, 3073–3077 RSC.
- X. Zhao, P. Dai, D. Xu, X. Tao, X. Liu and Q. Ge, J. Energy Chem., 2021, 59, 455–464 CrossRef CAS.
- Z.-L. Wang, H.-L. Wang, J.-M. Yan, Y. Ping, O. Song-Il, S.-J. Li and Q. Jiang, Chem. Commun., 2014, 50, 2732–2734 RSC.
- A. Zhang, J. Xia, Q. Yao and Z.-H. Lu, Appl. Catal., B, 2022, 309, 121278 CrossRef CAS.
- S. Zhang, Y. Qian and W.-S. Ahn, Chin. J. Catal., 2019, 40, 1704–1712 CrossRef.
|
This journal is © The Royal Society of Chemistry 2023 |
Click here to see how this site uses Cookies. View our privacy policy here.