DOI:
10.1039/D2MA01036D
(Paper)
Mater. Adv., 2023,
4, 995-1004
An electrochemically stable Ag@Au–Co core–shell nanowire network-based transparent conductor for flexible self-powered Zn-based electrochromic smart devices†
Received
15th November 2022
, Accepted 17th December 2022
First published on 21st December 2022
Abstract
Silver nanowires (AgNWs) are important materials used to fabricate flexible transparent conductors (FTCs) for next-generation wearable electronics. However, the electrochemical instability still limits their practical application in electrochemical devices. Herein, highly stable FTCs are demonstrated via coating an Au–Co alloy shell around an AgNW core by electrodeposition. The AgNW@Au–Co core–shell network exhibited excellent resistance against chemical (in H2O2 solution for 200 s) and electrochemical corrosion (electrochemical anodic corrosion in 1 M H2SO4 solution for 100 s). Meanwhile, the modified FTC also possessed good optoelectrical performance and high mechanical stability (2000 bending cycles) owing to the firm metallic bonding between the stacked NWs during the electrodeposition process. To evaluate the improvement in electrochemical stability, a prototype of a self-powered polyaniline electrochromic smart system based on the versatile AgNW@Au–Co network FTC was fabricated, and it exhibited a high optical modulation range (41.22%) and good energy-storage performance (4 mF cm−2). Our strategy of introducing a protective alloy shell onto AgNW by electrodeposition opens a new door for realizing high-performance FTCs by a facile method to broaden their application in flexible electrochemical devices.
1. Introduction
Transparent conductors (TCs) serve a critical function in a variety of applications in optoelectronics, including light-emitting diodes (LEDs),1 solar cells,2 flexible displays,3,4 and electrochromic devices.5–9 Indium tin oxide (ITO), which has high optical transmittance and low sheet resistance, is the most commonly used commercial transparent conductive material to fabricate TCs for these applications.10–12 However, being a kind of ceramic material, the intrinsic brittleness of ITO is still a deterrent.13–15 The recent interest in the revolution of optoelectronic devices from rigid to flexible has created an urgent need to seek an alternative material.16–19 Compared with ITO-based TCs, silver nanowire (AgNW) networks possess significant advantages, such as excellent electrical conductivity, mechanical flexibility, transmittance, solution compatibility, and scalability.20–23 The applications of AgNW networks have been expanding to various flexible devices. For instance, Chang et al. fabricated a bendable polymer fuel cell based on an AgNW FTC.24–26 Moon et al. obtained an Ag/Au/Polypyrrole(PPy) core–shell NW network for flexible supercapacitors.27 Lee fabricated a highly stretchable transparent supercapacitor using an Ag–Au core–shell NW network.28 Hu et al. successfully fabricated a transparent capacitive sensor using an AgNWs/polyurethane conductive film.29 A stretchable and transparent Kirigami conductor was successfully obtained by Won et al. for use in e-skin.30 Park et al. realized the fabrication of an AgNW-coated fibrous air filter medium.31 Jeong obtained an active PM2.5 filter based on an AgNW network.32 Ko et al. fabricated color-changing soft robots with AgNWs.33–36
However, the electrochemical instability problem of AgNW networks is still the major obstacle that prevents their application in electrochemical devices, such as supercapacitors, and electrochromic devices (ECDs).37–39 The critical failure mode is when AgNWs easily dissolve in the electrolyte, resulting in disconnection and loss of conductivity. Previous works have made many attempts to prevent this phenomenon by encapsulating the AgNW network with protective materials, including PEDOT:PSS,40 graphene,41 and metal oxides.33 For example, Shinde et al. wrapped the AgNWs with benzotriazole and a TiO2:Cs layer to fabricate a flexible WO3-ECD, which remained stable after 100 electrochemical redox cycles.42 Aghazadehchors et al. fabricated a ZnO/Al2O3-coated AgNW network, which exhibited improved thermal stability with minimal transparency loss.43 A thermal and electrically stable AgNW network was realized by depositing ZnO coatings.44 Chang et al. fabricated a thermally stable Ag@ZrO2 core–shell nanowire network by atomic layer deposition. A flexible supercapacitor was successfully achieved using the AgNWs/PEDOT:PSS hybrid electrode because the PEDOT:PSS layer provided significantly improved resistance against the electrochemical corrosion of the AgNW network.45 However, the poor intrinsic conductivity of these materials usually has a negative effect on their optoelectrical performance. Moreover, these materials are usually spin-coated onto the whole electrode without selectivity, which would block the blank area in the network and reduce the transmittance.46
Besides coating a protective layer onto the AgNW network, Other structures have been explored to improve the AgNW stability. For example, Kumar et al.47 fabricated a graphene/AgNWs/graphene conductor with good resistance to oxidation and mechanical flexibility. An aluminum-doped zinc oxide (AZO)/AgNWs/AZO FTC was obtained by Xu et al. with enhanced thermal stability.48 Liu et al. successfully embedded octadecanethiol-decorated AgNWs into an epoxy resin, which exhibited excellent resistance against high temperatures and chemical corrosion of Na2S.49 In another work, a thermally stable ZnO–Ag NW-Polyimide FTC was fabricated, and a white polymer light-emitting diode was obtained.50 However, these works have not paid enough attention to electrochemical stability.
To improve electrical conductivity, many methods have been developed to weld the NWs together. For example, Joule heating has proved to be an effective method to join AgNWs.51 Tukuno et al. welded stacked NWs by mechanical pressing.52 Celano et al. realized capillarity-driven welding of semiconductor NWs to form Ohmic junctions.53 Lee et al. soldered AgNWs using a conductive polymer to improve electrical conductivity, and a flexible touch panel was obtained.54 Laser nano-welding is also an effective method to weld the AgNWs network and enhance conductivity.55–57 Lee et al. joined AgNWs via carbon nanotubes (CNTs) to achieve a stretchable transparent conductor, which exhibited excellent conductivity. Although these methods achieved firm welding of NWs and reduced contact resistance, they could not improve the electrical stability at the same time.
Electrochromic smart windows can present different color responses when different voltages are applied and are attracting increasing interest in reducing energy consumption.58–62 In contrast to rigid ECDs, flexible ECDs can be installed onto pristine glass windows without replacing them.63 Moreover, they can be adapted to non-planar-shaped windows because of their intrinsic conforming ability. Conductive polymers with low cost, excellent mechanical flexibility and processability are attracting increasing interest in electrochemical devices.64–67 Recently, some important advances have been made in the fabrication of flexible electrochemical devices based on conductive polymers. For instance, Guo et al. successfully fabricated an electrochromic energy-storage device using polyaniline (PANI)-stabilized tungsten oxide, which exhibited a coloration efficiency of 98.4 cm2 C−1 and an areal capacitance of 0.025 F cm−2.68 Zhou et al. fabricated a multicolour PANI electrochromic film with a reversible color-changing ability from yellow to purple.63 Yuksel fabricated a supercapacitor based on coaxial AgNW/PPy nanocomposite with a long cycle life.69 However, these flexible ECDs still need an external power supply, which would involve extra energy consumption.70 Self-powered ECDs with metal Zn as the counter electrode have become a hot research area71 as they can realize zero energy consumption and simplify the installation, while reports on self-powered flexible PANI ECDs are still pretty scarce.
Constructing core–shell structures has been considered an effective method to fabricate highly stable NW-based FTCs.72 For example, Stewart et al. synthesized Cu@Ag, Cu@Au and Cu@Pt core–shell NWs with anti-oxidation performance for use in FTCs.73 Due to the excellent electrical conductivity and chemical stability, the Au–Co alloy is widely used in the electronic industry as the gold finger material on printed circuit boards,74 which inspired us to use the Au–Co alloy as an inhibitor to prevent AgNWs from electrochemical corrosion. Therefore, in this work, a passive Au–Co alloy shell was conformally and selectively coated around the AgNW shell by using a facile and simple electrodeposition method, which could provide good protection and avoid the extensive decrease in transmittance. Moreover, the stacked AgNWs were welded together during the electrodeposition process. Thus, the sheet resistance was also significantly decreased due to the reduction in contact resistance between the stacked NWs. Based on these modifications, we successfully fabricated a self-powered flexible ECD prototype using polyaniline (PANI) as the electrochromic material and metal Zn as the counter electrode, which demonstrated great potential for application in energy-efficient flexible electronics.
2. Experimental methods
2.1. Fabrication of the transparent AgNW@Au–Co network conductor
The AgNW ink with an average diameter of 20–25 nm and length of 20–40 μm (purchased from Zhejiang Kechuang Advanced Materials Technology Co., Ltd.) was washed 3 times with isopropanol and deionized water in sequence. Polyvinyl pyrrolidone (Mw = 800
000) was used in the synthesis process of AgNWs. After washing, the obtained AgNW ink was adjusted to a concentration of 0.05 mg mL−1. For fabricating the flexible TC (FTC), the AgNWs were coated onto a flexible polyethylene terephthalate (PET) polymer substrate with a thickness of 100 μm and transmittance of 90.6% (at 550 nm, Fig. S1, ESI†) using the vacuum filtration method to form a conductive network. The AgNW ink was first filtered using a 45 μm microporous filtration membrane to form the network. Then, the AgNW network was transferred onto the flexible PET substrate by mechanical pressing. The vacuum filtration installation is shown in Fig. S2 (ESI†). The PET substrate was washed using acetone and absolute ethyl alcohol. Then, the Au–Co shell was electrodeposited around the AgNW core using a two-electrode electrodeposition system. The AgNW FTC was connected as the cathode, and the graphite sheet was connected as the anode. The electrolyte was prepared according to previous reports;75 it contained CoSO4·7H2O (16.8 g L−1), citric acid (140 g L−1), KOH (120 g L−1), and KAu(CN)2 (3.2 g L−1). The electrodeposition process was performed under a constant current density (1 mA cm−2) for 10 s.
2.2. Fabrication of the self-powered electrochromic device
The PANI layer was deposited onto the AgNW@Au–Co FTC using the electropolymerization method in an electrochemical workstation (CHI660E, CHENGHUA, China) with a three-electrode system. The AgNW@Au–Co FTC was connected as the green working electrode, a Pt sheet was connected as the red counter electrode, and Ag/AgCl was connected as the white reference electrode. The electropolymerization process was carried out under a current density of 0.1 mA cm−2 for 700 s. The electrolyte used for depositing PANI contained 0.5 mol L−1 H2SO4 and 0.25 mol L−1 aniline in absolute ethyl alcohol. After the PANI electrode was obtained, double sticky tape with a thickness of 125 μm was fixed around the PANI electrode as a supporting frame. Then, the metal Zn strip was placed on the double sticky tape. Subsequently, 1 mol L−1 ZnCl2 solution was dropped into the frame. Then, another piece of PET without AgNWs was placed on top. At last, the device was sealed using UV curing adhesive.
2.4. Characterization
We observed the morphologies of the AgNW and AgNW@Au–Co networks by scanning electron microscopy (SEM, MIRA3XMH, TESCAN, Czech). The crystal structure was characterized by transmission electron microscopy (TEM, Tecnai G2 F30, FEI, America). The surface chemical state was characterized using an X-ray photoelectron spectrometer (XPS, PHI 5400, ULVAC-PHI, Japan) equipped with an Al Kα X-ray (1486.6 eV) source. The transmittance was measured using an ultraviolet spectrophotometer (Lambda 650S, PerkinElmer, America). The transmittance of FTC was measured relative to that of PET (The transmittance of PET was set as 100%). The transmittance of ECD was measured relative to that of the air (The transmittance of air is set as 100%). The sheet resistance of FTC was measured using a surface resistivity meter (MCP-T370, Mitsubishi, Japan).
The electrochemical test was performed in an electrochemical station (CHI660E, CHENGHUA, China). The cyclic voltammetry (CV) curves were collected to measure the electrochemical redox behaviours of different samples. Galvanostatic charge–discharge (GCD) tests were performed to obtain the areal capacitance. The areal capacitance was calculated using the following formula:76
where
I, Δ
t, and Δ
U represent the areal current density, discharge time and voltage window, respectively.
3. Results and discussion
3.1. Fabrication of the Ag@Au–Co nanowire network
Fig. 1a schematically shows the experimental process. Firstly, the AgNW ink was uniformly distributed on the surface of a flexible PET polymer substrate to obtain the AgNW network. Then, the conductive AgNW network was set as the cathode. After the power was turned on, Au and Co ions in the electrolyte were reduced to atoms and deposited onto the AgNW network FTC under the driving force of the current. Because only the NW network was conductive, the Au–Co layer was selectively deposited around the AgNWs, and the core–shell structure could be formed. The passive Au–Co alloy layer could significantly improve the electrochemical stability of the pristine AgNW network. As a result, the PANI electrochromic layer was anodically electropolymerized onto the modified FTC. Fig. 1b–d exhibit the optical images of the AgNW network FTC, the AgNW@Au–Co FTC and the PANI electrochromic film, respectively. The rose flower under the AgNW network FTC was clearly visible, suggesting excellent light transmittance (Fig. 1b). No apparent change was observed after the Au–Co layer was coated, which proved that the selective coating of the Au–Co shell had a negligible effect on transmittance (Fig. 1c). Moreover, the film changed color to green, indicating that the PANI layer was successfully deposited, as shown in Fig. 1d.
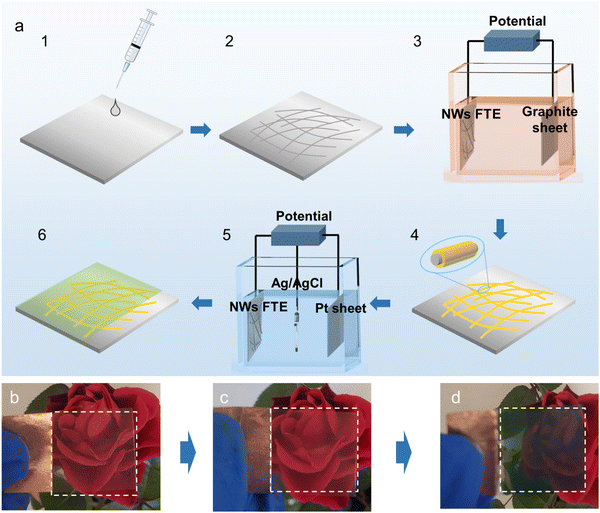 |
| Fig. 1 (a) Schematic illustration of electrodeposition toward fabricating the AgNW@Au–Co network FTC and the PANI electrochromic film. The optical image of (b) the AgNW network FTC, (c) the AgNW@Au–Co network FTC and (d) the PANI electrochromic film. | |
We collected the SEM images of the AgNW network before and after electrodeposition, as shown in Fig. 2a and b. In the pristine AgNW network, the upper NWs loosely overlapped the bottom ones, suggesting only physical contact between each other. Hence, it would be difficult for the electrons to pass the junction, and the electrical resistance is higher. By contrast, after electrodeposition, the gaps between stacked AgNWs were filled with Au and Co atoms, and firm joints between them were obtained at the junction region, as depicted in Fig. 2b. The upper NWs were obviously embedded into the bottom NWs, which would significantly facilitate the transfer of electrons. We further used TEM to characterize the morphologies of the AgNWs and Ag@Au–Co alloy NWs. As shown in Fig. 2c, before electrodeposition, the edges of the stacked NWs were clear and distinct. However, when the Au–Co alloy was deposited, the edges of the bottom and top NWs were merged together, suggesting firm metallurgical bonding (Fig. 2d). To prove the formation of the core–shell structure, EDS mapping was used to obtain the elemental distribution. Fig. 2e shows the morphology of an Ag@Au–Co alloy NW. The corresponding silver, gold, and cobalt elemental distributions are shown in Fig. 2f–i, respectively. The XPS spectra of silver, gold and cobalt are depicted in Fig. 2j–l, respectively. These characteristic peaks also confirm the formation of the alloy structure. We further measured the composition of the Au–Co alloy layer using EDS, as shown in Table. 1. The proportions of Co and Au elements were 1.41 at% and 98.59 at%, respectively. We further measured the thickness of the Au–Co alloy layer. As shown in Fig. S3 (ESI†), before the electrodeposition of the Au–Co alloy layer, the diameter of a pristine Ag NW was 20.12 nm. In contrast, the diameter increased to 31.25 nm later. Hence, the thickness of the Ag–Co layer was 5.57 nm.
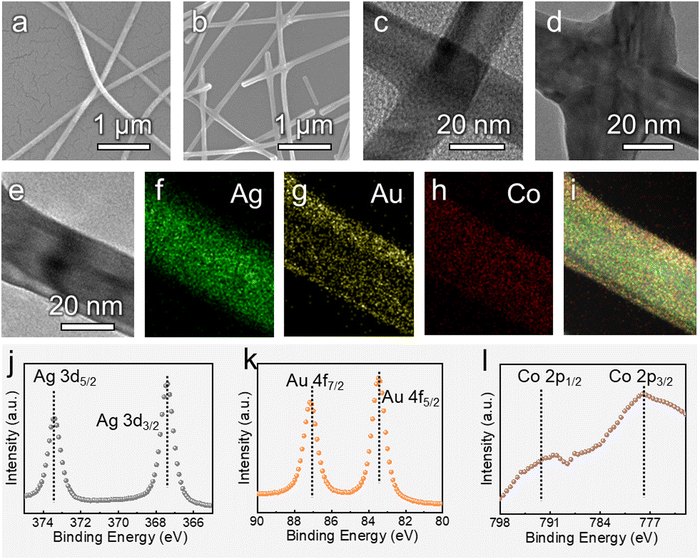 |
| Fig. 2 The SEM images of the (a) AgNW network and (b) AgNW@Au–Co alloy network. The TEM images of (c) a loose junction before and (d) a tight junction after electrodeposition. (e–i) The TEM images and the corresponding Ag, Co and Au elemental distributions of the AgNW@Au–Co alloy. The XPS survey spectra:(j) Ag 3d; (k) Au 4f and (l) Co 2p. | |
Table 1 The elemental composition of Ag@Au–Co NWs
Element |
Weight % |
Atomic % |
Co(K) |
0.15 |
0.32 |
Ag(L) |
65.23 |
77.22 |
Au(L) |
34.62 |
22.45 |
3.2. Opto-electrical performance of the Ag@Au–Co nanowire network
Because of the metallic joints between stacked NWs, the electrical conductivity of the FTC was improved. Fig. 3a plots the changes in sheet resistance and transmittance with the electrodeposition time. Initially, the pristine AgNW network showed a sheet resistance of 180 Ohm per sq at a transmittance of 94.1%. After electrodeposition for 6 s, the sheet resistance decreased to 20 Ohm per sq at a transmittance of 85.2%, suggesting that the Au and Co atoms filling the gaps are beneficial for the transfer of electrons. With a further increase in electrodeposition time, sheet resistance exhibited a slight decrease, which indicated that the metallic bonding had formed in the first 6 s. We compared the optoelectrical performance of AgNW@Au–Co with AgNW and ITO FTC,77 as shown in Fig. 3b. It was obvious that the FTC based on the AgNW@Au–Co network processed higher transmittance at similar sheet resistance, implying its excellent comprehensive optoelectrical performance. We further calculated the value of the figure of merit (FoM) at different electrodeposition times according to the following formula:78
where Rs and T are sheet resistance and transmittance, respectively. The FoM value of the original AgNW FTC was 32.39. Surprisingly, the FoM value reached 131.82 after electrodeposition for 6 s, proving the significant improvement in optoelectrical performance (Fig. 3c). Stability against mechanical deformation is of great importance for the actual usage of FTCs. We measured the mechanical stability of the AgNW and AgNW@Au–Co FTCs using the cyclic outward bending test with a radius of 6 mm, as shown in Fig. 3d. The resistance of the pristine AgNW FTC exhibited an obvious decline after 2000 bending cycles. In contrast, the modified AgNW@Au–Co FTC remained stable under the same condition. We also measured the change in relative resistance during cyclic inward bending. Similar to outward bending, the modified AgNW@Au–Co FTC again exhibited better stability, as shown in Fig. S4 (ESI†). This advance can be attributed to the firm joints between the stacked NWs, which strengthen the conductive network.
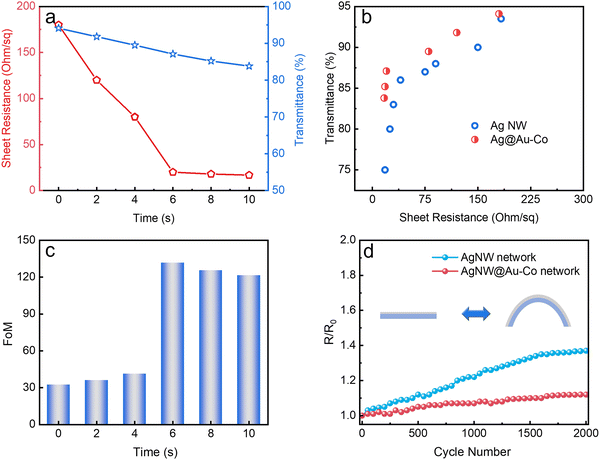 |
| Fig. 3 (a) The sheet resistance and transmittance of the AgNW@Au–Co network FTC vs. electrodeposition time. (b) The transmittance of the AgNW and AgNW@Au–Co network FTCs as a function of sheet resistance. (c) The FoM of the AgNW@Au–Co network FTC vs. electrodeposition time. (d) Relative resistance variation of the AgNW FTC and the AgNW@Au–Co FTC during cyclic outward bending. | |
3.3. The stability of the Ag@Au–Co nanowire network
Stability against chemical corrosion is also an important index for FTCs. We measured the change in relative resistance after dropping them in a 15 wt% H2O2 solution, as schematically shown in the inset of Fig. 4a. The pristine AgNW network rapidly lost conductivity when dropped in the H2O2 solution. By contrast, the relative resistance of the modified AgNW@Au–Co network showed negligible change, indicating that the coated alloy layer significantly improved the chemical stability. The CV cures of the AgNW and AgNW@Au–Co networks are depicted in Fig. 4b. The pristine AgNW network showed a high oxidation peak, but no corresponding reduction peak was observed, suggesting that it had lost conductivity and failed. However, when the Au–Co alloy shell was coated around the AgNW core, a pair of redox peaks were observed, indicating its high resistance against electrochromic anodic corrosion. We further measured the electrochemical stability of the AgNW network and AgNW@Au–Co network when an anodic current density of 10 mA cm−2 was applied. As depicted in Fig. 4c, the potential response of the pristine AgNW network rapidly increased beyond the measurement limit (10 V) within 10 s, while the AgNW@Au–Co alloy network remained stable after 100 s. These results also proved that the Au–Co alloy formed an effective layer against electrochemical corrosion. The morphologies of the AgNW and AgNW@Au–Co alloy networks after immersion in the H2O2 solution were characterized using SEM. The pristine AgNW network was seriously destroyed (Fig. 4d), and the FTC had lost conductivity. However, although some broken NWs could be observed in the AgNW@Au–Co alloy network, the NWs were still welded together and conductive, as shown in Fig. 4e. Similar to the results observed after chemical corrosion, many particles were observed in the AgNW network after electrochemical corrosion (Fig. 4f), while the AgNW@Au–Co network only showed slight changes (Fig. 4g). These results are also consistent with the aforementioned change in relative resistance.
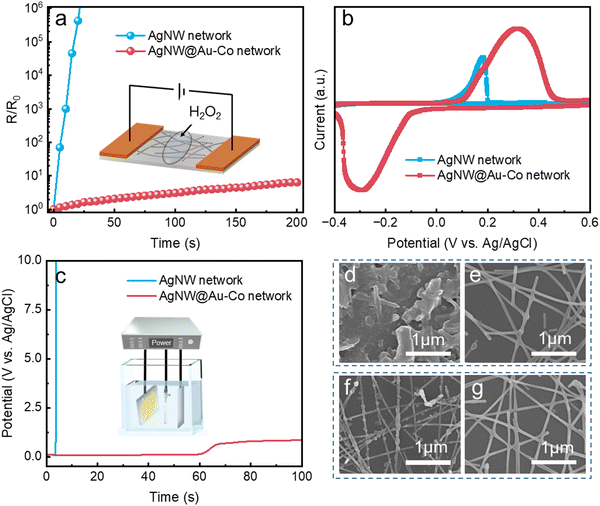 |
| Fig. 4 (a) The relative resistance variation of the AgNW FTC and AgNW@Au–Co FTC after H2O2 corrosion. (b) The CV curves of the AgNW FTC and AgNW@Au–Co FTC. (c) The response potential (vs. Ag/AgCl) of the AgNW FTC and AgNW@Au–Co FTC against anode oxidation in 1 mol L−1 H2SO4 solution. The SEM images of the (d) AgNW FTC and (e) AgNW@Au–Co FTC after H2O2 corrosion. The SEM images of the (f) AgNW FTC and (g) AgNW@Au–Co FTC after anode oxidation in 1 mol L−1 H2SO4 solution. | |
3.4. Fabrication of the prototype of flexible self-powered ECD
Based on these improvements, we electropolymerized a PANI layer onto the FTC to fabricate an electrochromic device. During the electropolymerization process, the FTC was set as the anode. Hence, it was difficult to deposit the PANI layer onto the pristine AgNW FTE due to anodic electrochemical corrosion. As shown in Fig. 5a, the pristine AgNWs were severely destroyed. By contrast, a uniform PANI layer was electrodeposited onto the Ag@Au–Co NW FTE (Fig. 5b). Then, we assembled an ECD using metal Zn as the counter electrode, as shown in Fig. 5c. Surprisingly, this ECD also exhibited energy-storage properties. When we connected the two devices, the stored energy in the ECD successfully powered a red LED. Fig. 5d shows the CV curves of the ECD at different scanning rates. When the scanning rate was increased from 2 mV s−1 to 10 mV s−1, the shape of the CV curves showed negligible change, suggesting excellent rate performance. Fig. 5e exhibits the GCD curves of the ECD at different current densities. With increasing discharge current densities, the discharge time gradually decreased. Furthermore, we calculated the areal capacitance of the electrochromic device at different current densities. For example, when the discharge current density was 0.1 mA cm−2, the areal capacitance was 4 mF cm−2. We measured the CV curves (Scanning Rate: 100 mV s−1) of the ECD in the flat and bent states (with a bent radius of 25 mm), as shown in Fig. S5 (ESI†). The CV curves showed a similar shape at the different states, suggesting the good flexibility of the ECDs.
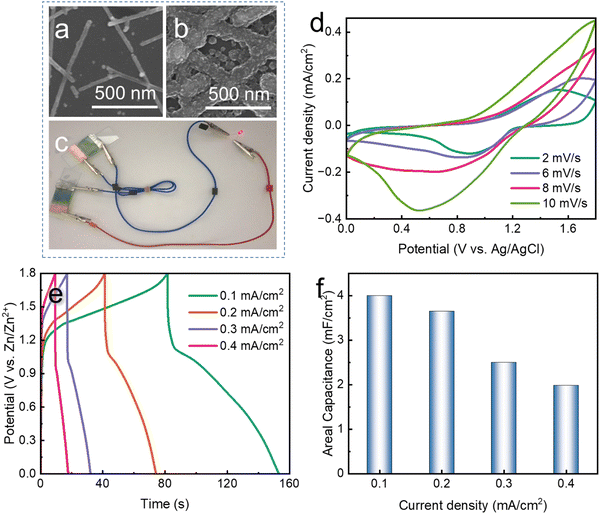 |
| Fig. 5 The SEM images of the (a) AgNW FTC and (b) AgNW@Au–Co FTC after electropolymerization of PANI on the surface. (c) A red LED was powered by the ECD. (d) The CV and (e) GCD curves of the ECD. (f) The areal capacitances of the ECD at different discharge current densities. | |
Fig. 6a schematically exhibits the configuration of the ECD prototype based on the AgNW@Au–Co network FTC. In the daytime, when a solar cell was connected to the ECD, the potential caused by sunlight could drive the ECD to change to a deep blue color (Fig. 6b), which avoided excessive light intake indoors. In the night, when we want more light come to indoor, we short-circuited the two electrodes of the ECD. The ECD turned back to light green under the driving force of the internal potential (Fig. 6c). These results suggested the unique self-driving property of the ECD containing a metal as counter material. The conventional ECD can also be colored when driven by solar cells, but it cannot spontaneously bleach. In other words, the bleaching process needs an external energy supply. Fig. 6d shows the UV-visible absorption spectrum of the ECD in a wavelength range of 400–800 nm in the colored and bleached states. In the colored state, an obvious peak was observed at 633 nm, indicating low light transmittance. We measured the in situ change in transmittance in a sweeping voltage window from 0 V to 1.8 V, as depicted in Fig. 6e. When the input voltage was 1.8 V, the transmittance decreased to 26.15%. However, the transmittance increased to 67.37 when 0 V voltage was applied. Moreover, the ECD exhibited an optical modulation range of 41.22%. After 100 cycles of the coloring and bleaching process, the ECD still presented stable transmittance adjustment performance, as illustrated in Fig. 6e (green line). Fig. 6f demonstrates the optical images of the ECD at different voltages. With increasing voltage, the color gradually changed from light green into a deep blue, and the logo of Harbin Institute of Technology gradually became dim. We further measured the chromaticity values using the CIE system, as depicted in Table. 2. In the table, L*, a* and b* are the parameters that describe the lightness, green–red and blue–yellow, respectively. The higher L* value in the bleached state indicated higher transmittance. The negative a* value suggested that the ECD showed a high degree of green at both colored and bleached states. The b* value gradually decreased from the bleached to colored state, demonstrating that the ECD had become bluer. It is obvious that the point had moved from the green region to the blue region in Fig. 6g with increasing voltage, which is also consistent with the optical images in Fig. 6f.
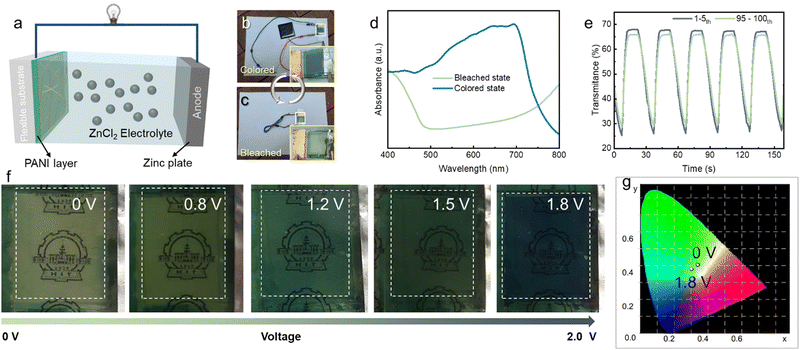 |
| Fig. 6 (a) Schematic illustration of the configuration of the ECD based on the AgNW@Au–Co FTC using metal Zn as the counter electrode. (b) The colored state of the ECD when connected with a solar cell. (c) The bleached state of the ECD when short-circuited. (d) The UV-vis absorption spectra of the ECD in the colored and bleached states. (e) The in situ change in transmittance in the sweeping voltage window of 0–1.8 V. (f) The optical images of the ECD at different voltages. (g) Colorimetry of the ECD in the colored and bleached states. | |
Table 2 The CIE parameters of the ECD under different voltages
Voltage |
0 V |
1.8 V |
L* |
51.58 |
39.5 |
a* |
−12.50 |
−14 |
b* |
17.30 |
7.96 |
Conclusions
In summary, we successfully fabricated a highly stable FTC by electrodepositing a protective Au–Co shell around the AgNW network. The resistance against chemical (remaining stable under corrosion by H2O2 for 200 s), and electrochemical corrosion (remaining stable as the electrochemical anode for 100s) was significantly improved. Moreover, because the Au and Co atoms could fill the gap between stacked NWs and weld them together, the modified electrode exhibited good optoelectrical performance (20 Ohm per sq at a high optical transparency of 87.1%) and high mechanical stability (2000 bending cycles). Besides, PANI was electropolymerized onto the AgNW@Au–Co network FTC, and a prototype flexible dual-functional electrochromic and energy-storage device was assembled using metal Zn as the counter electrode, which showed a high optical modulation range (41.22%) and good energy-storage performance (4 mF cm−2). More importantly, the device exhibited a unique self-powering property. Our work exhibits great potential for application in next-generation multifunctional and energy-efficient flexible electronics.
Author contributions
He Zhang: conceptualization, data curation, investigation, methodology, writing – original draft; Jiayun Feng: methodology; Fangyuan Sun: data curation, investigation; Dongyan Zhou: data curation; Ge Cao: methodology; Zhuohuan Wu: data curation, Shang Wang: conceptualization, Fengyu Su: Writing – review & editing, funding acquisition; Yanqing Tian: funding acquisition, supervision; Yanhong Tian: funding acquisition, supervision.
Conflicts of interest
There are no conflicts of interest to declare.
Acknowledgements
This work was supported by the National Natural Science Foundation of China (Grant No. 52175300), Heilongjiang Touyan Innovation Team Program (HITTY-20190013), Shenzhen Fundamental Research Programs (JCYJ20200925160843002) and the Start-up fund of SUSTech (Y01256114).
References
- H. Lee, D. Lee, Y. Ahn, E.-W. Lee, L. S. Park and Y. Lee, Nanoscale, 2014, 6, 8565–8570 RSC.
- H. Tang, H. Feng, H. Wang, X. Wan, J. Liang and Y. Chen, ACS Appl. Mater. Interfaces, 2019, 11, 25330–25337 CrossRef CAS.
- N. M. Nair, I. Khanra, D. Ray and P. Swaminathan, ACS Appl. Mater. Interfaces, 2021, 13, 34550–34560 CrossRef CAS PubMed.
- J. L. Sun, Y. Chang, J. Liao, S. L. Chang, S. G. Dai, Y. Y. Shang, C. X. Shan and L. Dong, Nano Energy, 2022, 99, 107392 CrossRef CAS.
- J. L. Wang, S. Z. Sheng, Z. He, R. Wang, Z. Pan, H. Y. Zhao, J. W. Liu and S. H. Yu, Nano Lett., 2021, 21, 9976–9982 CrossRef CAS.
- W. J. Ye, X. Guo, X. J. Zhang and P. Liu, Synth. Met., 2022, 287, 117076 CrossRef CAS.
- W. Zhang, H. Z. Li and A. Y. Elezzabi, Adv. Funct. Mater., 2022, 32, 2108341 CrossRef CAS.
- G. Cai, R. Zhu, S. Liu, J. Wang, C. Wei, K. J. Griffith, Y. Jia and P. S. Lee, Adv. Energy Mater., 2022, 12, 2270015 CrossRef.
- S. Zeb, G. Sun, Y. Nie, H. Xu, Y. Cui and X. Jiang, Mater. Adv., 2021, 2, 6839–6884 RSC.
- H. L. Wang, S. Y. Liao, X. P. Bai, Z. L. Liu, M. H. Fang, T. Liu, N. Wang and H. Wu, ACS Appl. Mater. Interfaces, 2016, 8, 32661–32666 CrossRef CAS PubMed.
- B. Bob, A. Machness, T. B. Song, H. P. Zhou, C. H. Chung and Y. Yang, Nano Res., 2016, 9, 392–400 CrossRef CAS.
- K. Qian, X. Han, H. K. Li, T. P. Chen and P. S. Lee, ACS Appl. Mater. Interfaces, 2020, 12, 4579–4585 CrossRef CAS.
- Y. Qin, L. Yao, F. Zhang, R. Li, Y. Chen, Y. Chen, T. Cheng, W. Lai, B. Mi, X. Zhang and W. Huang, ACS Appl. Mater. Interfaces, 2022, 14, 38021–38030 CrossRef CAS.
- S. H. Pham, A. Ferri, A. Da Costa, M. M. S. Mohan, V. D. Tran, D. C. Nguyen, P. Viville, R. Lazzaroni, R. Desfeux and P. Leclere, Adv. Mater. Interfaces, 2022, 9, 2200019 CrossRef CAS.
- H. Zhang, Y. Tian, S. Wang, Y. Huang, J. Wen, C. Hang, Z. Zheng and C. Wang, Chem. Eng. J., 2020, 399, 125075 CrossRef CAS.
- W. He and C. Ye, J. Mater. Sci. Technol., 2015, 31, 581–588 CrossRef CAS.
- D. Li, T. Han, L. Zhang, H. Zhang and H. Chen, R. Soc. Open Sci., 2017, 4, 170756 CrossRef PubMed.
- H. Zhang, Y. Tian, S. Wang, J. Feng, C. Hang, C. Wang, J. Ma, X. Hu, Z. Zheng and H. Dong, Chem. Eng. J., 2021, 426, 131438 CrossRef CAS.
- Y. Jin, Y. Sun, K. Wang, Y. Chen, Z. Liang, Y. Xu and F. Xiao, Nano Res., 2018, 11, 1998–2011 CrossRef CAS.
- B. Zheng, Q. Zhu and Y. Zhao, J. Mater. Sci. Technol., 2021, 71, 221–227 CrossRef CAS.
- C. Yang, Y. Tang, Z. Su, Z. Zhang and C. Fang, J. Mater. Sci. Technol., 2015, 31, 16–22 CrossRef CAS.
- A. R. Madaria, A. Kumar, F. N. Ishikawa and C. Zhou, Nano Res., 2010, 3, 564–573 CrossRef CAS.
- K. Huang, J. Liu, S. Lin, Y. Wu, E. Chen, Z. He and M. Lei, Adv. Compos. Hybrid Mater., 2022, 5, 220–228 CrossRef CAS.
- I. Chang, T. Park, J. Lee, M. H. Lee, S. H. Ko and S. W. Cha, J. Mater. Chem. A, 2013, 1, 8541–8546 RSC.
- I. Chang, T. Park, J. Lee, H. B. Lee, S. Ji, M. H. Lee, S. H. Ko and S. W. Cha, Int. J. Hydrogen Energy, 2014, 39, 7422–7427 CrossRef CAS.
- T. Park, I. Chang, H. B. Lee, S. H. Ko and S. W. Cha, Int. J. Hydrogen Energy, 2017, 42, 1884–1890 CrossRef CAS.
- H. Moon, H. Lee, J. Kwon, Y. D. Suh, D. K. Kim, I. Ha, J. Yeo, S. Hong and S. H. Ko, Sci. Rep., 2017, 7, 41981 CrossRef CAS PubMed.
- H. Lee, S. Hong, J. Lee, Y. D. Suh, J. Kwon, H. Moon, H. Kim, J. Yeo and S. H. Ko, ACS Appl. Mater. Interfaces, 2016, 8, 15449–15458 CrossRef CAS.
- W. Hu, X. Niu, R. Zhao and Q. Pei, Appl. Phys. Lett., 2013, 102, 083303 CrossRef.
- P. Won, J. J. Park, T. Lee, I. Ha, S. Han, M. Choi, J. Lee, S. Hong, K.-J. Cho and S. H. Ko, Nano Lett., 2019, 19, 6087–6096 CrossRef CAS PubMed.
- K. Park, S. Kang, J.-W. Park and J. Hwang, J. Hazard. Mater., 2021, 411, 125043 CrossRef CAS.
- S. Jeong, H. Cho, S. Han, P. Won, H. Lee, S. Hong, J. Yeo, J. Kwon and S. H. Ko, Nano Lett., 2017, 17, 4339–4346 CrossRef CAS.
- H. Kim, H. Lee, I. Ha, J. Jung, P. Won, H. Cho, J. Yeo, S. Hong, S. Han, J. Kwon, K.-J. Cho and S. H. Ko, Adv. Funct. Mater., 2018, 28, 1801847 CrossRef.
- H. Kim, J. Choi, K. K. Kim, P. Won, S. Hong and S. H. Ko, Nat. Commun., 2021, 12, 4658 CrossRef CAS PubMed.
- P. Won, K. K. Kim, H. Kim, J. J. Park, I. Ha, J. Shin, J. Jung, H. Cho, J. Kwon, H. Lee and S. H. Ko, Adv. Mater., 2021, 33, 2002397 CrossRef CAS.
- H. Kim, S.-k Ahn, D. M. Mackie, J. Kwon, S. H. Kim, C. Choi, Y. H. Moon, H. B. Lee and S. H. Ko, Mater. Today, 2020, 41, 243–269 CrossRef CAS.
- K. L. Zhou, C. B. Han, C. F. Li, J. Jiu, Y. Yang, L. Li, H. Wang, J. B. Liu, Z. Q. Liu, H. Yan and K. Suganuma, ACS Appl. Mater. Interfaces, 2018, 10, 36128–36135 CrossRef CAS.
- J. Jung, H. Cho, R. Yuksel, D. Kim, H. Lee, J. Kwon, P. Lee, J. Yeo, S. Hong, H. E. Unalan, S. Han and S. H. Ko, Nanoscale, 2019, 11, 20356–20378 RSC.
- H. Kim, K. R. Pyun, M.-T. Lee, H. B. Lee and S. H. Ko, Adv. Funct. Mater., 2022, 32, 2110535 CrossRef CAS.
- G. Cai, P. Darmawan, M. Cui, J. Wang, J. Chen, S. Magdassi and P. S. Lee, Adv. Energy Mater., 2016, 6, 1501882 CrossRef.
- I. N. Kholmanov, S. H. Domingues, H. Chou, X. Wang, C. Tan, J.-Y. Kim, H. Li, R. Piner, A. J. G. Zarbin and R. S. Ruoff, ACS Nano, 2013, 7, 1811–1816 CrossRef CAS PubMed.
- M. A. Shinde and H. Kim, Mater. Today Commun., 2021, 26, 102147 CrossRef CAS.
- S. Aghazadehchors, V. H. Nguyen, D. Muñoz-Rojas, C. Jiménez, L. Rapenne, N. D. Nguyen and D. Bellet, Nanoscale, 2019, 11, 19969–19979 RSC.
- A. Khan, V. H. Nguyen, D. Muñoz-Rojas, S. Aghazadehchors, C. Jiménez, N. D. Nguyen and D. Bellet, ACS Appl. Mater. Interfaces, 2018, 10, 19208–19217 CrossRef CAS.
- X. Liu, D. Li, X. Chen, W. Y. Lai and W. Huang, ACS Appl. Mater. Interfaces, 2018, 10, 32536–32542 CrossRef CAS.
- H. Zhang, S. Wang, Y. Tian, Y. Liu, J. Wen, Y. Huang, C. Hang, Z. Zheng and C. Wang, Chem. Eng. J., 2020, 390, 124495 CrossRef CAS.
- P. Kumar, F. Shahzad, S. M. Hong and C. M. Koo, RSC Adv., 2016, 6, 101283–101287 RSC.
- Q. Xu, W. Shen, Q. Huang, Y. Yang, R. Tan, K. Zhu, N. Dai and W. Song, J. Mater. Chem. C, 2014, 2, 3750–3755 RSC.
- G.-S. Liu, J.-S. Qiu, D.-H. Xu, X. Zhou, D. Zhong, H.-P. D. Shieh and B.-R. Yang, ACS Appl. Mater. Interfaces, 2017, 9, 15130–15138 CrossRef CAS.
- D. Chen, J. Liang, C. Liu, G. Saldanha, F. Zhao, K. Tong, J. Liu and Q. Pei, Adv. Funct. Mater., 2015, 25, 7512–7520 CrossRef.
- T.-B. Song, Y. Chen, C.-H. Chung, Y. Yang, B. Bob, H.-S. Duan, G. Li, K.-N. Tu, Y. Huang and Y. Yang, ACS Nano, 2014, 8, 2804–2811 CrossRef CAS.
- T. Tokuno, M. Nogi, M. Karakawa, J. Jiu, T. T. Nge, Y. Aso and K. Suganuma, Nano Res., 2011, 4, 1215–1222 CrossRef CAS.
- T. A. Celano, D. J. Hill, X. Zhang, C. W. Pinion, J. D. Christesen, C. J. Flynn, J. R. McBride and J. F. Cahoon, Nano Lett., 2016, 16, 5241–5246 CrossRef CAS.
- J. Lee, P. Lee, H. B. Lee, S. Hong, I. Lee, J. Yeo, S. S. Lee, T.-S. Kim, D. Lee and S. H. Ko, Adv. Funct. Mater., 2013, 23, 4171–4176 CrossRef CAS.
- J. Lee, P. Lee, H. Lee, D. Lee, S. S. Lee and S. H. Ko, Nanoscale, 2012, 4, 6408–6414 RSC.
- P. Lee, J. Lee, H. Lee, J. Yeo, S. Hong, K. H. Nam, D. Lee, S. S. Lee and S. H. Ko, Adv. Mater., 2012, 24, 3326–3332 CrossRef CAS PubMed.
- S. Hong, H. Lee, J. Yeo and S. H. Ko, Nano Today, 2016, 11, 547–564 CrossRef CAS.
- D. Ma, A. Lee-Sie Eh, S. Cao, P. S. Lee and J. Wang, ACS Applied Materials & Interfaces, 2022, 14, 1443–1451 Search PubMed.
- C. Kortz, A. Hein, M. Ciobanu, L. Walder and E. Oesterschulze, Nat. Commun., 2019, 10, 4874 CrossRef PubMed.
- H. Wang, C. J. Yao, H. J. Nie, L. Yang, S. L. Mei and Q. C. Zhang, J. Mater. Chem. C, 2020, 8, 15507–15525 RSC.
- Z. Q. Tong, Y. L. Tian, H. M. Zhang, X. G. Li, J. Y. Ji, H. Y. Qu, N. Li, J. P. Zhao and Y. Li, Sci. China: Chem., 2017, 60, 13–37 CrossRef CAS.
- X. Tao, Y. Zhang, J. Cai, H. H. Tan, J. Cui, Y. Wang, X. Shu, Z. Dai, Y. Qin, J. Liu and Y. Wu, Mater. Adv., 2022, 3, 7881–7893 RSC.
- K. Zhou, H. Wang, J. Jiu, J. Liu, H. Yan and K. Suganuma, Chem. Eng. J., 2018, 345, 290–299 CrossRef CAS.
- J. Guo, X. Li, H. Liu, D. P. Young, G. Song, K. Song, J. Zhu, J. Kong and Z. Guo, Adv. Compos. Hybrid Mater., 2021, 4, 51–64 CrossRef CAS.
- H. Wei, J. Zhu, S. Wu, S. Wei and Z. Guo, Polymer, 2013, 54, 1820–1831 CrossRef CAS.
- T. V. Nguyen, H. H. Do, T. Q. Trung, Q. V. Le, T. P. Nguyen, S. H. Hong, H. W. Jang, S. H. Ahn and S. Y. Kim, J. Alloys Compd., 2021, 882, 160718 CrossRef CAS.
- N. Zohrevand, T. Madrakian, A. Ghoorchian and A. Afkhami, Electrochim. Acta, 2022, 427, 140856 CrossRef CAS.
- H. Wei, X. Yan, S. Wu, Z. Luo, S. Wei and Z. Guo, J. Phys. Chem. C, 2012, 116, 25052–25064 CrossRef CAS.
- R. Yuksel, E. Alpugan and H. E. Unalan, Org. Electron., 2018, 52, 272–280 CrossRef CAS.
- W. Zhang, H. Li, W. W. Yu and A. Y. Elezzabi, Small Sci., 2021, 1, 2100040 CrossRef CAS.
- H. Li, W. Zhang and A. Y. Elezzabi, Adv. Mater., 2020, 32, 2003574 CrossRef CAS.
- J. Bang, S. Coskun, K. R. Pyun, D. Doganay, S. Tunca, S. Koylan, D. Kim, H. E. Unalan and S. H. Ko, Appl. Mater. Today, 2021, 22, 100909 CrossRef.
- I. E. Stewart, S. Ye, Z. Chen, P. F. Flowers and B. J. Wiley, Chem. Mater., 2015, 27, 7788–7794 CrossRef CAS.
- G. Luo, D. Li, G. Yuan and N. Li, J. Electrochem. Soc., 2018, 165, D107–D109 CrossRef CAS.
- M. Monev, A. Pfund, G. Beck, K. Petrov, R. Bretzler, U. Heuberger and A. Zielonka, Trans. IMF, 2012, 90, 305–310 CrossRef CAS.
- T. G. Yun, M. Park, D. H. Kim, D. Kim, J. Y. Cheong, J. G. Bae, S. M. Han and I. D. Kim, ACS Nano, 2019, 13, 3141–3150 CrossRef CAS.
- J.-H. Kim, H.-J. Seok, H.-J. Seo, T.-Y. Seong, J. H. Heo, S.-H. Lim, K.-J. Ahn and H.-K. Kim, Nanoscale, 2018, 10, 20587–20598 RSC.
- Y. Huang, Y. Tian, C. Hang, Y. Liu, S. Wang, M. Qi, H. Zhang and J. Zhao, ACS Appl. Mater. Interfaces, 2019, 11, 21850–21858 CrossRef CAS.
|
This journal is © The Royal Society of Chemistry 2023 |
Click here to see how this site uses Cookies. View our privacy policy here.