Advances in the device design and printing technology for eco-friendly organic photovoltaics
Received
6th October 2022
, Accepted 30th November 2022
First published on 3rd December 2022
Abstract
Green solvent-treated organic solar cells (OSCs) have demonstrated significant potential in terms of commercialization in recent years. However, the low solubility and high boiling point of green solvents cause difficulties in morphology exploration and tuning, and are eventually detrimental to photovoltaic properties. In this perspective, the recent research advances in green solvent-treated OSCs are summarized, and solvent selection strategies along with the associated optimization strategies in green printing of OSCs are discussed. Furthermore, the optimization strategies of OSCs fabricated using a large-area printing process are discussed in-depth to provide theoretical guidance for the large-scale fabrication of organic photovoltaic (OPV) modules.
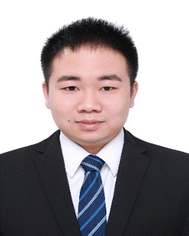
Xiaotian Hu
| Xiaotian Hu is a full professor at Nanchang University. He received his PhD from the Institute of Chemistry, Chinese Academy of Sciences (ICCAS) in 2019. He joined the Nanchang University in the same year. He has published more than 80 research papers in journals such as Nature Communication, Joule, Advanced Materials, Angewandte Chemie International Edition, Science Bulletin, Science China Chemistry, etc. His research interests are mainly focused on the printing fabrication and modular design of wearable perovskite/organic solar cells. |
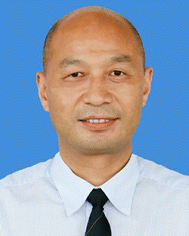
Yiwang Chen
| Yiwang Chen is a full professor of Chemistry at Nanchang University and Jiangxi Normal University. He was honored with the National Science Fund for Distinguished Young Scholars in 2014. His research interests include polymer/perovskite solar cells, supercapacitors, electrocatalysis for zinc-air batteries and fuel cells, and intelligent elastomers and fibers. He has published more than 500 research papers and 40 invention patents as well as 4 books. His research project has been awarded the “second class prize of science and technology in universities of China” in 2019 and a gold medal of The Geneva Salon International Des Inventions in 2022. |
Broader context
With the increased awareness of environmental protection, eco-friendly electronic devices are playing an increasingly important role in people's life with the advances in science and technology. Therefore, the research on eco-friendly power supply devices, as one of the core components, has scientific and practical application significance. In recent years, green solvent-treated organic solar cells (OSCs) have shown significant advantages in terms of large-area production. However, the rational choice of green processing solvents, optimization strategies of active layer film morphology, and the significant performance loss of large-scale printing processes are still the bottlenecks, limiting the commercialization of eco-friendly OSCs. In this perspective, the recent research advances in green solvent-treated OSCs are summarized, and solvent selection strategies along with associated optimization strategies in green printing of OSCs are discussed. In addition, the future development direction of environment-friendly OSC devices is prospected, providing a one-stop reference for printable large-scale organic semiconductor modules.
|
1. Introduction
The exploitation of innovative and sustainable energy alternatives to conventional fossil fuels is urgently needed to achieve carbon peaking and carbon neutrality targets.1,2 Organic solar cells (OSCs) have garnered widespread interest over the previous decades on account of their light weight, low cost, good printability and flexibility.3–22 With the continuous research on material synthesis, active layer morphology control and interface engineering, a power conversion efficiency (PCE) of 19.60% has been achieved for OSCs based on halogenated solvent treatment.23 However, the majority of these OSCs with high-PCE are treated with halogenated solvents such as chlorobenzene (CB) and chloroform (CF), which are extremely hazardous to humans and the environment.24–26 Furthermore, the use of virulent halogenated solvents during device fabrication undoubtedly raises environmental concerns and increases the cost of fabrication, and are some of the major impediments to the large-scale industrial fabrication of OPV modules.27,28 Consequently, OSCs treated with non-halogenated solvents (green solvents) have attracted a huge amount of investigative attention from researchers.
The term “green solvents” typically denotes non-halogenated solvents used in environmentally friendly OSC fields.29 The green solvents can be categorized into the following four types based on their molecular structure: water, alcohol solvents, non-halogenated non-aromatic solvents and non-halogenated aromatic solvents (Fig. 1). These green solvents are deemed to be less hazardous than halogenated solvents and thus are widely applied in the production of OPV devices (Table 1). However, the poor morphology of the active layer films treated with green solvents causes inferior photovoltaic properties of OSCs. Controlling the morphology of active layer films is essential for achieving high-performance OSCs. Historically, halogenated solvents are selected as the first choice for the processing of OSCs owing to their excellent film forming properties and the relatively small phase separation morphology of the active layer films.30–33 Additionally, the morphology achieved upon treating with non-halogenated solvents is not satisfactory, thanks to the lower solubility of the active layer materials when compared with that of halogenated solvents. In addition, non-halogenated solvents typically have high boiling points (B.P.); thus slowly evaporating the solvents during active layer film production leaves volatile organic impurities and solvent residues, which leads to the occurrence of large phase separation sizes.34,35 Meanwhile, the slow solvent evaporation process gives rise to prolonged drying times, which exacerbates the aggregation of donors and acceptors in films.36 Hence, several strategies have been utilized to optimize the morphology of active layer films treated with non-halogenated solvents to boost photovoltaic properties.
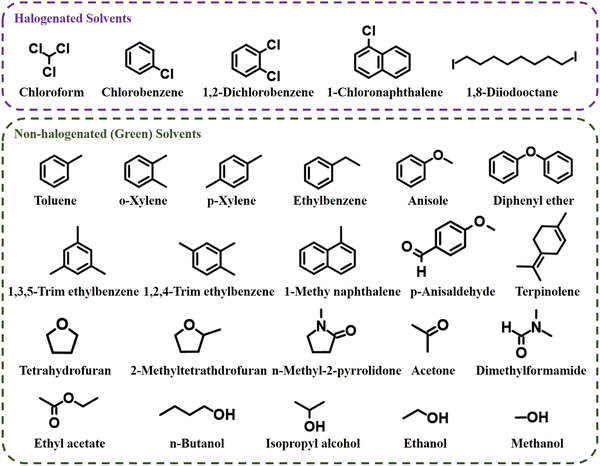 |
| Fig. 1 Chemical structure formulas of typical solvents used for the fabrication of OSCs. | |
Table 1 Photovoltaic parameters of green solvent-treated organic solar cells under simulated solar illumination (AM 1.5G, 100 mW cm−2)
Year |
Materials |
Solvent |
Fabrication methods |
V
OC (V) |
J
SC (mA cm−2) |
FF (%) |
PCEmax (%) |
Ref. |
2022 |
PM6:5BDTBDD:BTP-BO-4Cl |
o-XY (DIO) |
Spin-coating |
0.84 |
26.8 |
77.4 |
17.5 |
59
|
2022 |
PM6:5BDDBDT:BTP-BO-4Cl |
o-XY (DIO) |
Spin-coating |
0.84 |
26.7 |
77.4 |
17.3 |
59
|
2022 |
PM6:Y6 |
o-XY:CS2 |
Spin-coating |
0.84 |
25.6 |
76.8 |
16.5 |
75
|
2022 |
PM6:BO-4Cl |
o-XY |
Hot spin-coating |
0.84 |
26.7 |
79.0 |
17.7 |
87
|
2022 |
PM6:BO-4Cl:Y6-1O |
o-XY |
Hot spin-coating |
0.85 |
26.8 |
80.0 |
18.3 |
87
|
2022 |
PM6:BO-4Cl:Y6-1O |
p-XY |
Hot spin-coating |
0.84 |
27.1 |
80.0 |
18.2 |
87
|
2022 |
PM6:BO-4Cl:Y6-1O |
Tol |
Hot spin-coating |
0.85 |
27.2 |
79.0 |
18.1 |
87
|
2022 |
PM6:Y6 |
o-XY |
Spin-coating |
0.78 |
22.8 |
65.8 |
11.6 |
87
|
2022 |
PM6:Y6 |
o-XY |
Blade-coating |
0.80 |
25.0 |
74.8 |
15.1 |
93
|
2022 |
PM6:BTP-eC9 |
o-XY |
Blade-coating |
0.84 |
26.8 |
76.3 |
17.2 |
93
|
2022 |
PM6: PTer-N25 |
o-XY (2-MN) |
Spin-coating |
0.94 |
19.5 |
65.1 |
11.9 |
104
|
2022 |
PM6/BO-4F |
o-XY/THF (DIO) |
Spin-coating (PPHJ) |
0.82 |
26.2 |
47.3 |
16.0 |
105
|
2022 |
PBDB-T-b-PYT |
THF (CN) |
Spin-coating |
0.89 |
21.0 |
66.1 |
12.4 |
99
|
2022 |
PBDB-T-b-PYT |
Tol (CN) |
Spin-coating |
0.89 |
20.6 |
68.4 |
12.5 |
106
|
2022 |
PBDB-T-b-PYT |
o-XY (CN) |
Spin-coating |
0.90 |
20.6 |
68.5 |
12.6 |
106
|
2021 |
PTB7-Th:PC71BM |
o-XY (EHB) |
Spin-coating |
0.80 |
17.2 |
67.5 |
9.3 |
49
|
2021 |
PM6:Y6:BTO |
PX (CN) |
Spin-coating |
0.85 |
26.3 |
74.3 |
16.6 |
63
|
2021 |
PM6:Y6:BTO:PC71BM |
PX (CN) |
Spin-coating |
0.85 |
27.1 |
75.8 |
47.4 |
63
|
2021 |
PM6:A-2ThCl:A-4Cl:PC71BM |
Tol (DIO) |
Spin-coating |
0.86 |
26.3 |
77.0 |
17.4 |
65
|
2021 |
PTzBI-dF:CH1007:PC71BM |
o-XY:TMB |
Spin-coating |
0.82 |
28.2 |
77.8 |
18.0 |
74
|
2021 |
PM6:Y6 |
o-XY (DMN) |
Spin-coating |
0.81 |
23.7 |
68.3 |
13.2 |
96
|
2021 |
PM6:Y6 |
o-XY (DMN) |
Blade-coating |
0.83 |
25.0 |
74.6 |
15.5 |
96
|
2021 |
PPDT2FBT:PC61BM |
o-XY |
Spin-coating |
0.80 |
15.6 |
72.0 |
9.2 |
107
|
2021 |
PPDT2FBT:PC61BM |
o-XY (AA) |
Spin-coating |
0.80 |
15.6 |
72.0 |
9.2 |
107
|
2021 |
PPDT2FBT:PC61BM |
o-XY (DIO) |
Spin-coating |
0.80 |
11.8 |
66.0 |
6.6 |
107
|
2021 |
PM6:YSe-C6 |
o-XY |
Spin-coating |
0.85 |
25.9 |
73.0 |
16.1 |
108
|
2021 |
PM6:PYT |
o-XY (CN) |
Spin-coating |
0.96 |
10.7 |
53.0 |
5.4 |
109
|
2021 |
PM6:PY2F-T |
o-XY |
Spin-coating |
0.86 |
23.5 |
64.8 |
13.1 |
109
|
2020 |
PM6:BTP-BO-4Cl |
Tol (BV) |
Spin-coating |
0.85 |
26.10 |
77.7 |
17.33 |
72
|
2020 |
PM6:DTY6 |
o-XY |
Blade-coating |
0.86 |
24.94 |
75.5 |
16.1 |
95
|
2020 |
PM6:Y6 |
o-XY |
Hot slot-die coating |
0.81 |
26.6 |
70.3 |
15.6 |
98
|
2020 |
PM6:Y6 |
TMB |
Hot slot-die coating |
0.80 |
26.4 |
70.9 |
15.4 |
98
|
2020 |
TPD-1:IT-4F |
o-XY (DIO) |
Spin-coating |
0.81 |
19.4 |
74.7 |
11.7 |
110
|
2020 |
TPD-2:IT-4F |
o-XY (DIO) |
Spin-coating |
0.81 |
19.6 |
74.2 |
11.8 |
110
|
2020 |
TPD-3:IT-4F |
o-XY (DIO) |
Spin-coating |
0.80 |
20.1 |
75.3 |
12.1 |
110
|
2020 |
TPD-3F:IT-4F |
o-XY (DIO) |
Spin-coating |
0.91 |
20.5 |
73.8 |
13.8 |
110
|
2020 |
PM6:IT-4F |
o-XY (P2) |
Spin-coating |
0.83 |
19.2 |
73.9 |
11.8 |
111
|
2020 |
PM6:PC71BM |
o-XY (P2) |
Spin-coating |
0.81 |
20.3 |
67.0 |
11.0 |
111
|
2020 |
PTB7-Th:F10IC2 |
o-XY |
Spin-coating |
0.76 |
20.3 |
66.8 |
10.7 |
112
|
2020 |
PTB7-Th:F10IC2 |
o-XY |
Blade-coating |
0.75 |
22.3 |
65.0 |
11.4 |
112
|
2020 |
PM7:IT-4Cl |
CS2 |
Spin-coating |
0.89 |
19.1 |
74.8 |
12.5 |
113
|
2020 |
PM7:IT-4Cl |
o-XY |
Spin-coating |
0.88 |
20.6 |
62.4 |
10.8 |
113
|
2020 |
PM7:IT-4F |
CS2 |
Spin-coating |
0.93 |
17.1 |
73.4 |
11.7 |
113
|
2020 |
PMT50:Y6(BO) |
TMB (CN) |
Spin-coating |
0.84 |
26.8 |
67.7 |
15.3 |
114
|
In this perspective, the factors, including Hansen solubility parameters, B.P., viscosity and surface tension are discussed first for the selection of green processing solvents. Then, the strategies such as the additive strategy, ternary strategy, pre-aggregation strategy, co-solvent strategy and so on are further discussed, for optimizing the morphology of active layer films in green solvent-treated OSCs. In addition, the mechanics, advantages and disadvantages of each strategy are explained. Finally, the future development direction of environment-friendly OSC devices is prospected.
2. Strategies for the selection of processing non-halogenated solvents
To enable eco-friendly OSCs to maintain high performance, green solvents ought to have sufficient solubility and suitable Hansen solubility parameters (HSPs). Several groups have used HSPs to screen non-halogenated solvents for the preparation of high-performance OSCs.37–45 Yang et al.37 successfully fabricated ternary eco-friendly OSCs based on PTB7-Th:DR3TSBDT:PC71BM with a PCE of 12.3% by assaying the solubility of the active materials in different solvents and quantifying the solvent-active material interactions using HSPs. First, Yang et al. measured the solubility of each active material in green solvents and mapped Hansen spheres (Fig. 2a), which narrowed down the selection range of green solvents. On account of the excellent solubility, the authors chose mesitylene (MES), toluene (Tol) and o-xylene (o-XY) as alternative solvents. In addition, the relative energy differences (REDs) (Fig. 2b) and Flory–Huggins interaction parameters (χ) (Fig. 2c) between the solvents and components were calculated. The RED and χ values of Tol and o-XY solvents are smaller than those of MES, which indicates that they exhibit better affinity to the active layer materials. As predicted, the OSCs treated with o-XY and Tol showed superior photovoltaic properties (PCE of 12.3% and 11.8% respectively), while the photovoltaic performance of the devices treated with MES exhibited a PCE of 4.57%. Similarly, Vogt et al.38 successfully prepared P3HT:PCBM-based OSCs with a PCE of 3.51% by using green solvents [acetophenone (AP) and mesitylene (MS)] instead of halogenated solvents (dichlorobenzene and DCB) through calculating the HSP (Fig. 2d).
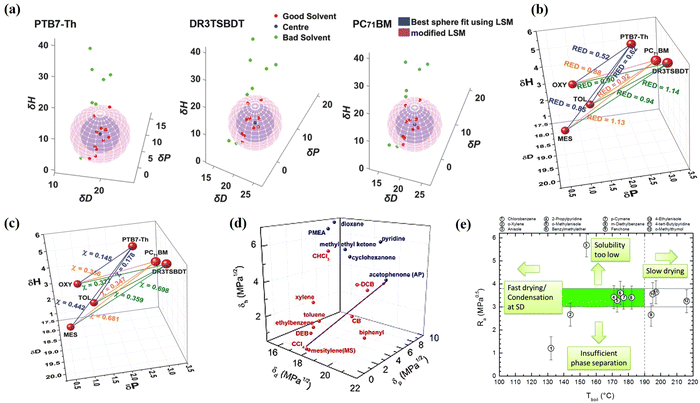 |
| Fig. 2 (a) Hansen spheres fitted for PTB7-Th, DR3TSBDT, and PC71BM and 3D plots of good and bad solvents for each material. (b)Relative energy difference (RED). (c) Chi parameters calculated using Hansen solubility parameters for PTB7-Th, DR3TSBDT, and PC71BM in Tol, o-XY, and MES. (Reproduced with permission from ref. 37, copyright 2018, John Wiley and Sons.) (d) HSP for selected solvents and solvent mixtures. Solvents in red are considered as good solvents for P3HT/PCBM blends and in blue are bad solvents. Reproduced with permission from ref. 38, copyright 2011, Elsevier B.V. (e) P3HT-solvent solubility distance as a function of the solvent boiling point. Reproduced with permission from ref. 39, copyright 2018, Royal Society of Chemistry. | |
Furthermore, other properties of a non-halogenated solvent such as B.P., polarity, viscosity, surface tension and solvent miscibility should also be considered. Strohm et al.39 set boundary conditions (Fig. 2e) for processing solvents in slot die coating methods, taking into account the intrinsic properties of the solvents (B.P., viscosity, etc.). Highly volatile (low B.P.) and high B.P. solvents are not recommended as processing solvents in slot-die coating methods on account of the relatively short or long drying times of the films, which lead to the fabrication of poor-quality films. Consequently, the solvent (o-methylanisole) that fulfilled the boundary conditions was selected to fabricate large-area OPV modules achieving a PCE of 4.7%.
3. Optimization strategies of active layer films
3.1 Additive strategy
The additive strategy is a critical approach toward favoring the morphology of the active layer films.46–54 The solution additives can control the films' formation kinetics, which enhances the photovoltaic performance of OSCs. Machui et al.46 categorized the additives used in the field of photovoltaics into the following four groups (Fig. 3a) based on the solubility and volatility: (a) low volatility–poor solubility for both components, (b) low volatility–selective solubility for one component, (c) high volatility–poor solubility for both components, and (d) high volatility–selective solubility for one component. The majority of solution additives used currently fall into the category of low volatility (high B.P.) and selective solubility. This type of additive can control the crystallinity, domain size and phase separation scale during the evolution of active layer films by selective solubilization of the donor or acceptor.47,48 Xia et al.49 successfully introduced a non-halogenated additive ethyl 2-hydroxybenzoate (EHB) into the PTB7-Th:PCBM system to enhance the crystallinity of the donors by modulating the film formation kinetic process (Fig. 3b and c). In addition, EHB selectively solubilizes more aggregation-prone fullerene acceptors, allowing polymer donors (PTB7-Th) to enter the conformational domain of PCBM, which accelerates molecular rearrangements and provides a larger contact area between donors and acceptors. The optimized active layer morphology of the interpenetrating network structure favors the photovoltaic performance, with its devices boosting the PCE from 5.21% to 9.41%. Likewise, Hou et al.50 successfully prepared OSCs based on T1:PTB-4F-12 by using a non-halogenated additive (diphenyl ether, DPE) instead of a halogenated additive (1,8-diiodooctance, DIO), which exhibited a PCE of 16.1%. However, the high B.P. solvent additives are extremely challenging to remove from the active layer films by additional procedures, and the residual additives can adversely affect the reproducibility and stability of OSCs.55,56 The introduction of solid additives is also often used as an effective method to enhance the performances of OSCs. Sun et al.57 added a volatile solid additive (2-methoxynaphthalene, 2-MN) to the PM6:PY-DT blend to prepare efficient and stable all-polymer OSCs. The introduction of 2-MN can help effectively control the aggregation of the active layer material in the film deposition process, forming an excellent phase separation morphology. In addition, 2-MN can be entirely removed from the active layer films by hot annealing and therefore exhibits better photostability. Consequently, the PCE of the all-polymer OSCs based on PM6:PY-DT prepared using green solvents (o-XY) reached 17.03%.
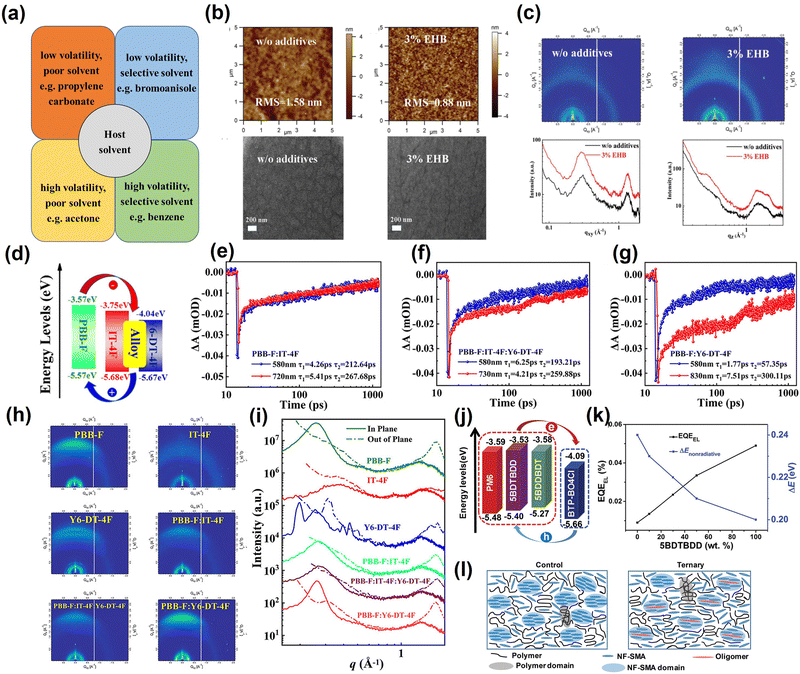 |
| Fig. 3 (a) Categorization of solvent additives based on volatility and solubility. Reproduced with permission from ref. 46, copyright 2015, John Wiley and Sons. (b) AFM, TEM and (c) GIWAXS plots under different conditions. Reproduced with permission from ref. 49, copyright 2021, John Wiley and Sons. (d) Energy level alignments of PBB-F, IT-4F and Y6-DT-4F. (e–g) Dynamics of the PBB-F:IT-4F, PBB-F:IT-4F:Y6-DT-4F, and PBB-F:Y6-DT-4F blend films. (h) 2D GIWAXS patterns under different conditions, and (i) the in-plane and out-of-plane line cuts from the GIWAXS patterns. Reproduced with permission from ref. 58, copyright 2022, American Chemical Society. (j) Energy levels of PM6, 5BDTBDD, 5BDDBDT, and BTP-BO-4Cl. (k) EQEEL and nonradiative recombination loss as a function of the 5BDTBDD contents. (l) Schematic diagrams of film morphology in binary and ternary devices. Reproduced with permission from ref. 59, copyright 2022, John Wiley and Sons. | |
3.2. Ternary strategy
The ternary strategy has been proven to be an effective approach for enhancing the photovoltaic performances of eco-friendly OSCs.58–66 The ternary materials in OSCs exhibit a complementary absorption spectral range or energy-level to enhance photon collection, which can boost photovoltaic properties. Moreover, the incorporation of a ternary component can help optimize the compatible morphology of the active layer films, suppressing the excessive phase separation and allowing the formation of excellent D/A interpenetrating network structures. Xia et al.58 added a highly crystalline non-fullerene acceptor (Y6-DT-4F) as a ternary component to the PBB-F:IT-4F based blend films. Y6-DT-4F exhibits excellent miscibility with IT-4F and forms an “alloy acceptor”. In ternary blended films, the electron transfer rate from the donor to the alloy acceptor is faster than that in the binary films, which facilitates the photovoltaic performances of the devices (Fig. 3d–g). Furthermore, the introduction of Y6-DT-4F as a ternary component enhances the crystalline properties of the blend films and aids the charge transfer (Fig. 3h and i). Consequently, this strategy contributes to the synergistic optimization of the photon capture, exciton dissociation, carrier transport capabilities of the ternary devices, with a PCE of 15.27% being achieved for the devices prepared with o-XY. Li et al.59 added oligomeric donors (5BDTBDD or 5BDDBDT) as a ternary component to the PM6:BTP-BO-4Cl based blend films to prepare ternary OSCs treated with o-XY. 5BDTBDD and 5BDDBDT have higher highest occupied molecular orbital (HOMO) levels than PM6, and exhibit relatively higher electroluminescence quantum efficiency (EQEEL), which favors VOC enhancement (Fig. 3j and k). In addition, the highly crystalline guest molecules have excellent miscibility with BTP-BO-4Cl and enable synergistic optimization of the active layer film morphology (Fig. 3l).
3.3. Pre-aggregation strategy
Appropriate pre-aggregation is recognized as a prerequisite for achieving high-quality active layer films.67–69 Cao et al.70 revealed that the polymer donor PTzBI and acceptor N2200 exhibited strong intrinsic pre-aggregation in 2-methyltetrahydrofuran (Me-THF) solvent. Such pre-aggregation contributes to the formation of interpenetrating network structures with small domains and high domain purity (Fig. 4a–c), which facilitates efficient charge transportation and exciton dissociation. Accordingly, the applicable pre-aggregation facilitates the enhancement of photovoltaic performances in OSCs. Similarly, Peng et al.71 observed that P3HT dissolves readily in the high-temperature TMB solvent and crystallizes gradually during long-term aging at room temperature; thus the degree of pre-aggregation was controlled by altering the aging time (Fig. 4d–g). After aging for 40 minutes, the prepared active layer films have suitable phase separation scales, which are in favor of the formation of interpenetrating network structures, allowing the devices to achieve a PCE of 8.25%. They further adapted this strategy for the PM6:BTP-BO-4Cl-based OSCs.72 The crystallization and aggregation of the active layer films are optimized by controlling the delay time to obtain excellent morphology with a PCE of 17.33%. (Fig. 4h) However, when pre-aggregation is achieved by adjusting the aging time, the reproducibility of the device is not only affected, but also the industrial production of large-scale areas is not favored. Therefore, the pre-aggregation of donors and acceptors in solvents through alternative strategies has become a focus of research.
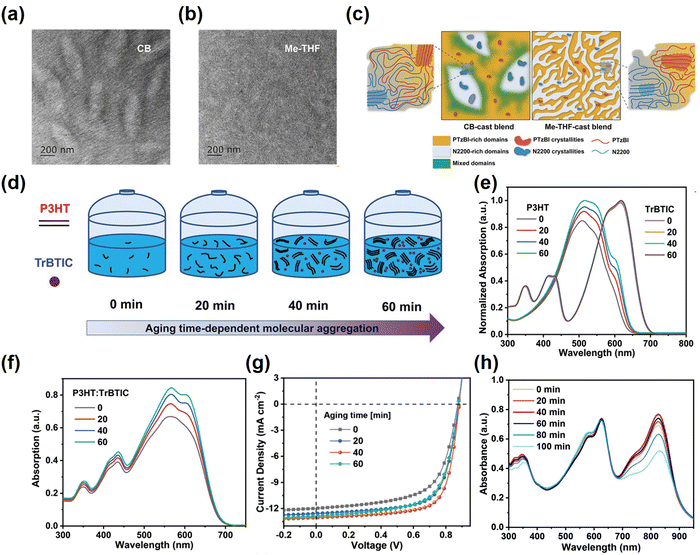 |
| Fig. 4 (a and b) TEM images of the films based on PTzBI:N2200 processed with different solvents. (c) Schematic illustration of the active layer film morphology treated with various solvents. Reproduced with permission from ref. 70, copyright 2019, John Wiley and Sons. (d) Diagramatic illustration of the pre-aggregation of the active layer material at various aging times in TMB. The UV-vis absorption of (e) pure and (f) blend films under different aging times. (g) J–V curves of the OSCs fabricated from different aging time solutions. Reproduced with permission from ref. 71, copyright 2019, John Wiley and Sons. (h) Delayed processing time-dependent UV-vis-NIR absorption of the PM6:BTP-BO-4Cl films cast from Tol solutions Reproduced with permission from ref. 72, copyright 2020, Royal Society of Chemistry. | |
3.4. Co-solvent strategy
The co-solvent strategy is regarded as one of the simple strategies to implement the pre-aggregation strategy.73–78 The BHJ blends prepared by using a single solvent failed to exhibit a suitable miscibility and aggregation degree simultaneously due to the different solubility of each material. The active layer films prepared with high B.P. solvents result in large phase separation sizes on account of the inferior solubility and degree of crystallinity. In contrast, solvents with good solubility lead to excessively small phase separation sizes, resulting in severe carrier recombination, which is detrimental to the photovoltaic performances. Hence, the co-solvent strategy can be effective in addressing these issues.73 Jen et al.74 achieved appropriate pre-aggregation of the polymer donor (PTzBI-dF) and acceptor (CH1007) in mixed non-halogenated o-XY
:
TMB (3.5
:
1, vol
:
vol) solvents, allowing the preparation of active layer films with high crystallinity and proper phase separation scales. Therefore, the OSCs based on PTzBI-dF:CH1007 reached a PCE of 18.0%. Likewise, Zhu et al.75 successfully produced OSCs based on PM6
:
Y6 and PM6
:
BTP-eC9 by using the co-solvent (CS2
:
o-XY, 3
:
7, vol
:
vol) strategy and demonstrated its universality in the fabrication process of devices. The improvements in the device performances resulted from the enhanced solubility of the donor (PM6) and acceptor (Y6 and BTP-eC9) in the guest solvent CS2, which helped in optimizing the miscibility between the acceptors and donors. And the highly volatile nature of the CS2 solvent shortens the drying time of the wet films to alleviate the aggregation-prone properties of PM6. Besides, the main solvent o-XY further extended the crystal growth kinetics of Y6 to enhance the photovoltaic performances of the OSCs with a PCE of 16.5%. In addition, the co-solvent strategy was further applied to PM6:BTP-eC9-based OSCs to demonstrate the universality of this strategy, which led to an increase in the PCE from 14.3% to 17.6%.
3.5. Process strategies
The OSCs with a quasi-planar heterojunction (PPHJ) structure between the planar heterojunction (PHJ) and bulk heterojunction (BHJ) structures, which are prepared by the layer-by-layer (LBL) method, have attracted widespread interest in recent years.79–82 The LBL strategy refers to the sequential deposition of an active layer material, typically with the donor material being deposited first followed by the acceptor material. Thus, the PPHJ structure can help precisely modulate the distribution of the vertical phase in the active layer films so that the acceptor and donor materials are enriched at the negative and positive poles, respectively, making enhanced exciton dissociation and reduced carrier recombination more favorable. Furthermore, the active layer material is deposited separately, making it easier to tune and optimize the morphology and reducing the dependence on processing conditions. In addition, the LBL strategy matches well with various preparation processes and therefore effectively facilitates the transition of OSCs from a laboratory scale to a commercial scale. Tao et al.83 combined the LBL strategy with the ternary strategy to co-optimize the active layer morphology and prepare PM6/BO-4Cl:L8-BO based devices (with o-XY as the solvent) with a PCE of 17.89%. The authors first compared the effects of the BHJ (PM6:BO-4Cl) and PPHJ (PM6/BO-4Cl) structures for OSC performance, and discovered that the PPHJ films have a superior vertical morphology than the BHJ films, which facilitates the carrier transport. For the further enhancement of the PCE of OSCs, the PPHJ OSCs based on the PM6/BO-4Cl: L8-BO system were fabricated by doping L8-BO into BO-4Cl and a PCE of up to 17.89% was achieved. The PCE enhancement is attributed to the introduction of L8-BO for increased light utilization and the formation of an alloyed structure in the PHJ structure, which optimizes the vertical gradient distribution of the active layer material. Similarly, Li et al.84 prepared OSCs based on PTQ10:HO-IDIC-2F by using the LBL strategy with THF as the solvent which reached a PCE of 12.03%.
A high-temperature stress is imposed on the active layer solution or substrate before the deposition of the active layer film, thus enabling the proper pre-aggregation of the active layer materials. Moreover, the hot-coating strategy suppresses the over-aggregation of molecules and the oversize phase separation scale by revising the film formation kinetic processes, which facilitates the photovoltaic performances of OSCs.85,86 Recently, Li et al.87 explored the influence of different substrate temperatures on the morphology of active layer films treated with non-halogenated solvents (Fig. 5a–c). When a mixed solution with a higher temperature was exposed to a substrate with lower temperature, the polymer donors (PM6) rapidly formed larger size aggregate domains, which allows the entangled polymer containing the small acceptors (Y6) to precipitate out from the solution. Premature precipitation of the polymer donors led to a reduction in the viscosity of wet films, which resulted in detachment of significant amounts of acceptors from the top of the films (leaving fewer acceptors at the top of the films). It ultimately led to the formation of relatively thin active layer films with large aggregation scales, which resulted in inferior photovoltaic properties. In the hot spin-coating procedure, the solution temperature was similar to the substrate temperature, which delayed the time for the evolution of the interpenetrating network structure. A longer film formation time maintains the high viscosity of the wet films, consequently forming active layer films with smaller phase separation scales and enriched acceptors on the surface. The optimized active layer morphology can enhance the photovoltaic performance of the device, and the OSCs based on PM6:Y6-1O:BO-4Cl treated with o-XY solvents ultimately achieved a PCE of 18.25%. Equally, Wang et al.88 prepared eco-friendly ternary OSCs based on PM6:PM7:M36 and PM6:M36:ITCC-M by using the hot spin-coating method, both of which exhibited a PCE of 15.8%.
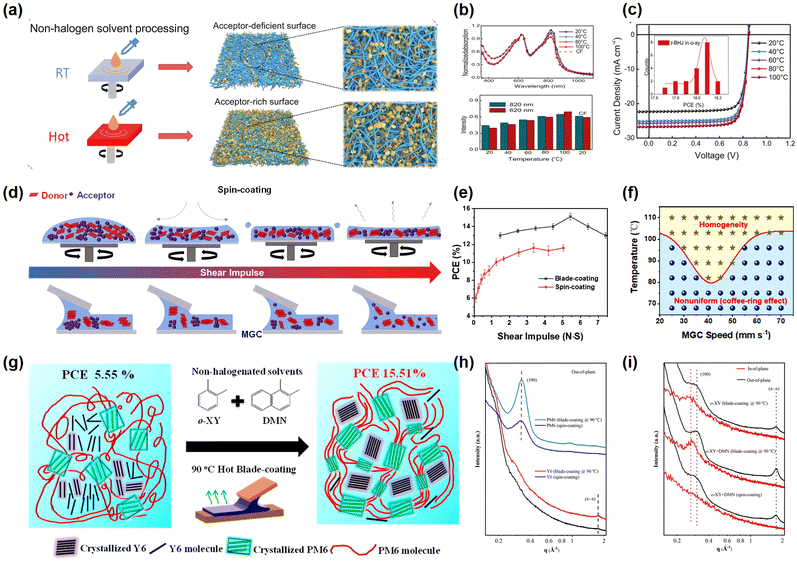 |
| Fig. 5 (a) Illustration of the distribution of donor and acceptor in the active layer films fabricated by spin-coating at various substrate temperatures. (b) Normalized absorbance and the relative ratio (620 and 820 nm absorbance) of blend films. (c) Photovoltaic performances at different substrate temperatures. Reproduced with permission from ref. 87, copyright 2022, John Wiley and Sons. (d) Illustration of donors and acceptors in the active layer with different shear impulses. (e) Photovoltaic performances with different shear impulses. (f) Homogenization conditions of active layer films prepared by blade-coating. Reproduced with permission from ref. 93, copyright 2022, Royal Society of Chemistry. (g) Schematic diagram of the morphology of the active layer films under different preparation conditions. (h–i) GIWAXS patterns of films prepared under different process conditions. Reproduced with permission from ref. 96, copyright 2021, American Chemical Society. | |
Although, the OSCs treated with non-halogenated solvents have made remarkable progress recently due to the application of morphology optimization strategies. However, the OSCs with high performances treated with non-halogenated solvents are mainly prepared by the spin-coating process, which is not suitable for future large-scale production due to the inherent limitations.89 During the preparation of the films by the spin-coating method, the active layer solution is thrown out from the substrate, leading to the wastage of material. Meanwhile, the thickness of the active layer films is uneven due to different forces at the edges and center of the substrate. Consequently, several potential printing methods, such as blade-coating, slot-die coating and roll-to-roll techniques, are applied due to their unique advantages. These meniscus-guided coating (MGC) methods have high material utilization and can be used to prepare large-area OSCs of uniform thickness with good reproducibility. A series of optimization strategies for active layer films adapted to the printing process have been explored, and have significant implications for small-area devices moving towards large-area modules.
The blade-coating method is currently a prevalent method of preparing large-area OSCs in laboratories. In this method a unidirectional shear force is applied to the solution through a gap between the substrate and the blade, where the capillary force is the primary driving force for film formation. The various blade-coating speeds (shear impulses) have different solution flow processes, which influence the quality of the films. When the shear impulse is relatively small, evaporation drives capillary flow and transports solutes to a three-phase line, causing stick-slip effects. In addition, the Couette flow of the solution at this point is analogous to the coffee ring effect. The stick-slip and coffee-ring effects can adversely influence the homogeneity of large-area films, resulting in poor photovoltaic performance. The solution flows rapidly out of the gap between the substrate and the blade due to the viscous forces when the shear impulse enhances. And the Couette flow of the solution is similar to laminar flow, which facilitates the alignment and extension of the polymer chains, contributing to improved photovoltaic properties.90,91 Based on our previous work, we discovered that the shear impulse exhibits an extremely important function in the preparation of high-quality films (Fig. 5d).92,93 Quantitative calculations of the shear impulse revealed that the wet films are subjected to a greater shear impulse in blade-coating than in the spin-coating method. In addition, the larger shear impulse inhibits the aggregation of the active layer materials in green solvents, facilitating the improvement of performances of large-area films. Thus, the relation between shear impulse, active layer film morphology and photovoltaic performances was discovered (Fig. 5e). Moreover, the basic requirements for the homogenization of large-area films are investigated by characterizing the shear impulses (Fig. 5f). Eventually, we successfully prepared the PM6:BTP-eC9 based-OSCs with a PCE of 17.15% and 11.29% for small-area (0.04 cm2) devices and large-area (25 cm2) flexible modules, respectively.
Furthermore, the blade-coating process can be combined with other strategies (additive strategy, ternary strategy, LBL strategy and so on) to synergistically optimize the morphology of blend films.94,95 Under the larger shear impulse conditions, a high-temperature stress is applied to modulate the degree of pre-aggregation of the donors and acceptors to enhance the crystallinity while inhibiting the aggregation in active layer films. Xie et al.96 investigated the change in morphology of o-XY solvent-treated PM6:Y6 blended films on addition of a non-halogen solution additive (1,2-dimethylnaphthalene, DMN) and by varying the substrate temperature. Under low temperature (30 °C) conditions, the high B.P. solvents (o-XY) led to prolonged film drying processes with large phase separation sizes and over-aggregation of Y6. A higher substrate temperature (90 °C) shortens the drying time of the wet films and suppresses the aggregation of Y6, allowing the formation of suitable phase separation sizes (Fig. 5g–i). Furthermore, the calculation of the interaction parameters revealed that the addition of DMN induced more nucleation sites and promoted the close packing of molecules and polymer chains by prolonging the drying time of the wet films. The eventual PCE achieved for the small-area (0.04 cm2) and large-area (1 cm2) OSCs was 15.51% and 13.87%, respectively. The blade-coating method is also frequently combined with LBL and ternary strategies to fabricate high-efficiency large-area OSCs. Xie et al.97 improved the vertical gradient distribution of the donor (PM6:IT-M)/acceptor (BTP-eC9) by using the LBL blade-coating strategy, thereby enhancing the PCE of the device. The addition of the third component (IT-M) facilitates the formation of a dense nanofibrous morphology and enhances the crystalline properties, with the PCE (17.16%) of the devices being higher than the PCE (15.34%) of the devices based on the PM6:BTP-eC9 BHJ structure.
The slot-die coating is the ultimate expression of the application of blade-coating for large-scale commercial preparation. The slot-die coating method is also frequently combined with other strategies such as the high-temperature stress, the additive strategy and layer-by-layer strategy.98–101 Like the blade-coating method, the slot-die coating procedure combined with the high-temperature stress can be used to optimize the active layer films by regulating the degree of pre-aggregation and reducing the time for molecules to aggregate in the wet films. Ma et al.98 investigated the morphological evolution of PM6:Y6 blends from solution to films and discovered that a similar film forming kinetic process could be achieved with different solvents through temperature control. In addition, the universality of the hot slot-die process in the fabrication of OSCs was demonstrated (Fig. 6a–h). Conclusively, the PCE of PM6:Y6-based OSCs treated with TMB and o-XY solvents was 15.4% and 15.6%, respectively. Furthermore, the slot-die coating strategy is frequently combined with the layer-by-layer strategy to optimize large-area active layer films treated with non-halogenated solvents. Ma et al.102 utilized the dual-slot-die sequential processing (DSDS) strategy to create a graded-BHJ morphology through the cross-diffusion and subsequent progressive aggregation between the donor and acceptor (Fig. 6i–k). The graded-BHJ structure favors charge transport, achieving a PCE of 17.07% for OSCs based on PM6:Y6 treated with non-halogenated solvents. Multiple optimization strategies are used in parallel to guide the commercialization of large-area organic photovoltaics. Similarly, Wei et al.103 used the LBL slot-die process to fabricate flexible devices based on PTB7-Th/p-DTS(FBTTH2)2:PCBM, obtaining a PCE of 7.32%. The LBL slot-die coating allows the polymer to form pre-aggregates to enhance the crystallinity and thus boost the performances of the OSCs.
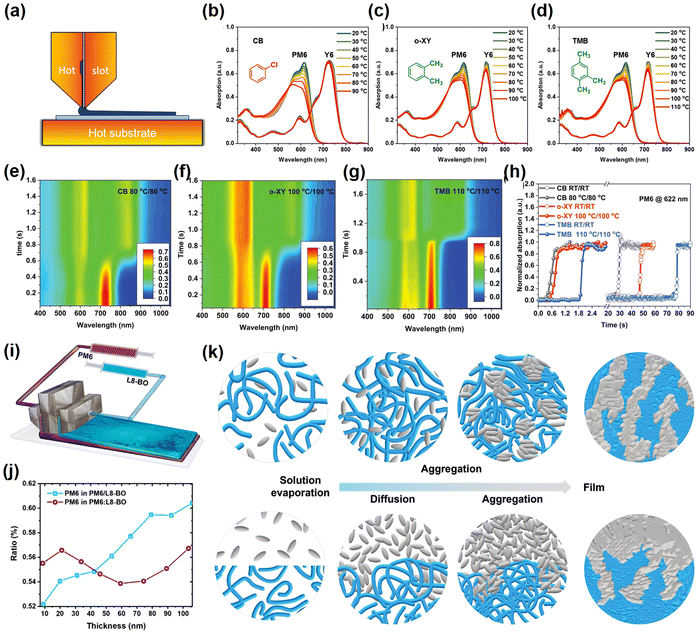 |
| Fig. 6 (a) Diagram of hot slot-die coating. (b–d) UV-vis absorption spectra in different solvents. (e–g) Time evolution of UV-vis absorption spectra during slot-die coating under different conditions. (h) Time evolution of normalized absorption at 622 nm (PM6) during slot-die coating under different conditions Reproduced with permission from ref. 98, copyright 2020, John Wiley and Sons. (i) Diagram of dual-slot-die coating. (j) Vertical distribution of PM6 in the active layer films. (k) Distribution of donor and acceptor molecules in the photoelectric conversion layer under different process conditions. Reproduced with permission from ref. 102, copyright 2022, John Wiley and Sons. | |
4. Perspective
Substituting highly toxic halogenated solvents with green solvents plays a crucial role in the evolution of OSCs. Currently, the green processing solvents suffer from two main disadvantages in the fabrication of OSCs. The relatively inferior solubility of active layer materials compared to that of halogenated solvents is an obvious disadvantage of non-halogenated solvents. The over-aggregation of the active layer materials in solution can lead to large phase separation scales in the active layer films or even to the inability to prepare homogenized films. Additionally, the green solvents typically have high B.P., which is another significant drawback in the process of producing OSCs. The slow evaporation of the active layer solution is the primary factor leading to a prolonged drying time of the films, exacerbating the aggregation of the donors and acceptors. Besides, the slow evaporation of the solvent can leave volatile organic impurities in the films, which facilitate the excessive phase separation scales, resulting in a decrease in the photovoltaic properties. Facing the above challenges, we have reviewed the research progress of green solvent treatment of OSCs in terms of solvent selection and printing process optimization strategies (Fig. 7). Selecting an appropriate treatment solvent by a solvent selection strategy is the primary requirement for the formation of a superior active layer film morphology. Furthermore, other optimization strategies are also necessary to further improve the active layer morphology of the donors and acceptors with poor solubility. Altogether, the synergy of multiple strategies can facilitate the enhancement of the photovoltaic performances of OSCs. We conjecture that the next research focus will be the transformation from the laboratory to industrial preparation. However, the enormous performance loss of the large-area films prepared by the printing process remains a considerable bottleneck in the commercialization of OSCs. As a result, various strategies are adopted to boost the quality of large-area active layer films, and are discussed in this perspective. The research strategy in this perspective will provide reasonable guidance for the design and development of high-performance and eco-friendly OSCs. We expect that the application of these strategies will bring us closer to eventual commercialization.
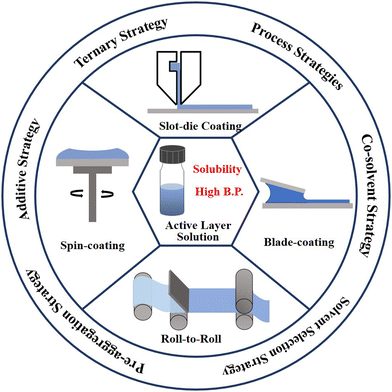 |
| Fig. 7 Summary of methods and optimization strategies for the preparation of OSCs. | |
Conflicts of interest
The authors declare no conflict of interest.
Acknowledgements
This research was funded by the National Natural Science Foundation of China (NSFC) (51833004, 22005131, 52173169 and 52222312), the “Double Thousand Plan” Science and Technology Innovation High-end Talent Project of Jiangxi Province (jxsq2019201049) and the Natural Science Foundation of Jiangxi Province (20212BAB214055).
Notes and references
- E. S. Beach, Z. Cui and P. T. Anastas, Energy Environ. Sci., 2009, 2, 1038–1049 RSC.
- S. Niu, X. Wang, F. Yi, Y. Zhou and Z. Wang, Nat. Commun., 2015, 6, 8975–8983 CrossRef CAS PubMed.
- G. Yu, J. Gao, J. Hummelen, F. Wudl and A. Heeger, Science, 1995, 270, 1789–1791 CrossRef CAS.
- H. Huang, Q. Guo, S. Feng, C. Zhang, Z. Bi, W. Xue, J. Yang, J. Song, C. Li, X. Xu, Z. Tang, W. Ma and Z. Bo, Nat. Commun., 2019, 10, 3038–3048 CrossRef PubMed.
- B. Fan, X. Du, F. Liu, W. Zhong, L. Ying, R. Xie, X. Tang, K. An, J. Xin, N. Li, W. Ma, C. J. Brabec, F. Huang and Y. Cao, Nat. Energy, 2018, 3, 1051–1058 CrossRef CAS.
- X. Dong, Y. Jiang, L. Sun, F. Qin, X. Zhou, X. Lu, W. Wang and Y. Zhou, Adv. Funct. Mater., 2022, 32, 2110209 CrossRef CAS.
- M. L. Ball, Q. Burlingame, H. L. Smith, T. Liu, S. R. Parkin, A. Kahn and Y. Loo, ACS Energy Lett., 2022, 7, 180–188 CrossRef CAS.
- W. Song, K. Yu, E. Zhou, L. Xie, L. Hong, J. Ge, J. Zhang, X. Zhang, R. Peng and Z. Ge, Adv. Funct. Mater., 2021, 31, 2102694 CrossRef CAS.
- F. Qin, L. Sun, H. Chen, Y. Liu, X. Lu, W. Wang, T. Liu, X. Dong, P. Jiang, Y. Jiang, L. Wang and Y. Zhou, Adv. Mater., 2021, 33, 2103017 CrossRef CAS PubMed.
- X. Meng, Z. Xing, X. Hu and Y. Chen, Chin. J. Polym. Sci., 2022, 40, 1522–1566 CrossRef CAS.
- G. Xu, X. Hu, X. Liao and Y. Chen, Chin. J. Polym. Sci., 2021, 39, 1441–1448 CrossRef CAS.
- D. Chen, S. Liu, X. Hu, F. Wu, J. Liu, K. Zhou, L. Ye, L. Chen and Y. Chen, Sci. China: Chem., 2022, 65, 182–189 CrossRef CAS.
- Y. Liu, B. Liu, C. Ma, F. Huang, G. Feng, H. Chen, J. Hou, L. Yan, Q. Wei, Q. Luo, Q. Bao, W. Ma, W. Liu, W. Li, X. Wan, X. Hu, Y. Han, Y. Li, Y. Zhou, Y. Zou, Y. Chen, Y. Li, Y. Chen, Z. Tang, Z. Hu, Z. Zhang and Z. Bo, Sci. China: Chem., 2022, 65, 224–268 CrossRef CAS.
- Z. Xing, X. Meng, R. Sun, T. Hu, Z. Huang, J. Min, X. Hu and Y. Chen, Adv. Funct. Mater., 2020, 30, 2000417 CrossRef CAS.
- L. Zhang, F. Yang, X. Meng, S. Yang, L. Ke, C. Zhou, H. Yan, X. Hu, S. Zhang, W. Ma and Y. Yuan, Org. Electron., 2021, 89, 106027 CrossRef CAS.
- H. Yao and J. Hou, Angew. Chem., Int. Ed., 2022, 134, e202209021 Search PubMed.
- P. Jiang, J. Chen, F. Qin, T. Liu, S. Xiong, W. Wang, C. Xie, X. Lu, Y. Jiang, H. Han and Y. Zhou, Angew. Chem., Int. Ed., 2022, e202208815, DOI:10.1002/ange.202208815.
- H. Chen, H. Liang, Z. Guo, Y. Zhu, Z. Zhang, Z. Li, X. Cao, H. Wang, W. Feng, Y. Zou, L. Meng, X. Xu, B. Kan, C. Li, Z. Yao, X. Wan, Z. Ma and Y. Chen, Angew. Chem., Int. Ed., 2022, e202209580, DOI:10.1002/ange.202209580.
- Y. Liu, B. Liu, C. Ma, F. Huang, G. Feng, H. Chen, J. Hou, L. Yan, Q. Wei, Q. Luo, Q. Bao, W. Ma, W. Liu, W. Li, X. Wan, X. Hu, Y. Han, Y. Li, Y. Zhou, Y. Zou, Y. Chen, Y. Liu, L. Meng, Y. Li, Y. Chen, Z. Tang, Z. Hu, Z. Zhang and Z. Bo, Sci. China: Chem., 2022, 65, 1457–1497 CrossRef CAS.
- J. Xu, F. Lin, L. Zhu, M. Zhang, T. Hao, G. Zhou, K. Gao, Y. Zou, G. Wei, Y. Yi, A. Jen, Y. Zhang and F. Liu, Adv. Funct. Mater., 2022, 2201338, DOI:10.1002/aenm.202201338.
- C. Li, X. Gu, Z. Chen, X. Han, N. Yu, Y. Wei, J. Gao, H. Chen, M. Zhang, A. Wang, J. Zhang, Z. Wei, Q. Peng, Z. Tang, X. Hao, X. Zhang and H. Huang, J. Am. Chem. Soc., 2022, 144, 14731–14739 CrossRef CAS PubMed.
- R. Ma, C. Yan, J. Yu, T. Liu, H. Liu, Y. Li, J. Chen, Z. Luo, B. Tang, X. Lu, G. Li and H. Yan, ACS Energy Lett., 2022, 7, 2547–2556 CrossRef CAS.
- L. Zhu, M. Zhang, J. Xu, C. Li, J. Yan, G. Zhou, W. Zhong, T. Hao, J. Song, X. Xue, Z. Zhou, R. Zeng, H. Zhu, C. Chen, R. MacKenzie, Y. Zou, J. Nelson, Y. Zhang, Y. Sun and F. Liu, Nat. Mater., 2022, 21, 656–663 CrossRef CAS PubMed.
- C. Sun, F. Pan, S. Chen, R. Wang, R. Sun, Z. Shang, B. Qiu, J. Min, M. Lv, L. Meng, C. Zhang, M. Xiao, C. Yang and Y. Li, Adv. Mater., 2019, 31, 1905480 CrossRef CAS PubMed.
- T. Yan, W. Song, J. Huang, R. Peng, L. Huang and Z. Ge, Adv. Mater., 2019, 31, 1902210 CrossRef PubMed.
- G. Chai, Y. Chang, J. Zhang, X. Xu, L. Yu, X. Zou, X. Li, Y. Chen, S. Luo, B. Liu, F. Bai, Z. Luo, H. Yu, J. Liang, T. Liu, K. Wong, H. Zhou, Q. Peng and H. Yan, Energy Environ. Sci., 2021, 14, 3469–3479 RSC.
- R. Sun, Q. Wu, J. Guo, T. Wang, Y. Wu, B. Qiu, Z. Luo, W. Yang, Z. Hu, J. Guo, M. Shi, C. Yang, F. Huang, Y. Li and J. Min, Joule, 2020, 4, 407–419 CrossRef CAS.
- R. K. Henderson, C. Jiménez-González, D. J. C. Constable, S. R. Alston, G. G. A. Inglis, G. Fisher, J. Sherwood, S. P. Binksa and A. D. Curzons, Green Chem., 2011, 13, 854–862 RSC.
- C. Capello, U. Fischer and K. Hungerbühler, Green Chem., 2007, 9, 927–934 RSC.
- S. Liu, D. Chen, X. Hu, Z. Xing, J. Wan, L. Zhang, L. Tan, W. Zhou and Y. Chen, Adv. Funct. Mater., 2020, 30, 2003223 CrossRef CAS.
- S. Liu, D. Chen, W. Zhou, Z. Yu, L. Chen, F. Liu and Y. Chen, Macromolecules, 2019, 52, 4359–4369 CrossRef CAS.
- S. Zhou, D. Xia, S. Liang, B. Liu, J. Wang, C. Xiao, Z. Tang and W. Li, ACS Appl. Mater. Interfaces, 2022, 14, 7093–7101 CrossRef CAS PubMed.
- Y. Wu, Q. Fan, B. Fan, F. Qi, Z. Wu, F. Lin, Y. Li, C. Lee, H. Y. Woo, H. Yip and A. Jen, ACS Energy Lett., 2022, 7, 2196–2202 CrossRef CAS.
- G. Li, R. Zhu and Y. Yang, Nat. Photon., 2012, 6, 153–161 CrossRef CAS.
- S. Li, H. Zhang, S. Yue, X. Yu and H. Zhou, Nanotechnology, 2021, 33, 072002 CrossRef PubMed.
- O. Wodo and B. Ganapathysubramanian, Comp. Mater. Sci., 2012, 55, 113–126 CrossRef CAS.
- T. Kumari, S. Lee and C. Yang, Adv. Funct. Mater., 2018, 28, 1707278 CrossRef.
- C. Park, T. Fleetham, J. Li and B. Vogt, Org. Electron., 2011, 12, 1465–1470 CrossRef CAS.
- S. Strohm, F. Machui, S. Langner, P. Kubis, N. Gasparini, M. Salvador, I. McCulloch, H.-J. Egelhaafa and C. J. Brabec, Energy Environ. Sci., 2018, 11, 2225–2234 RSC.
- J. Tait, T. Merckx, W. Li, C. Wong, R. Gehlhaar, D. Cheyns, M. Turbiez and P. Heremans, Adv. Funct. Mater., 2015, 25, 3393–3398 CrossRef CAS.
- I. Burgués-Ceballos, F. Machui, J. Min, T. Ameri, M. Voigt, Y. Luponosov, S. Ponomarenko, P. Lacharmoise, M. Campoy-Quiles and C. Brabec, Adv. Funct. Mater., 2014, 24, 1449–1457 CrossRef.
- B. Walker, A. Tamayo, D. Duong, X. Dang, C. Kim, J. Granstrom and T. Nguyen, Adv. Energy Mater., 2011, 1, 221–229 CrossRef CAS.
- N. Holmes, H. Munday, M. Barr, L. Thomsen, M. Marcus, A. Kilcoyne, A. Fahy, J. Stam, P. Dastoor and E. Moons, Green Chem., 2019, 21, 5090–5103 RSC.
- C. Liu, Y. Zhu, J. Chen, H. Wang, Y. Cao and J. Chen, Synth. Met., 2018, 242, 17–22 CrossRef CAS.
- C. Sprau, A. Cruz, L. Bautista, L. Molina, M. Wagner, C. Chochos, M. Pirriera and A. Colsmann, Adv. Energy Sustainability Res., 2021, 2, 2100043 CrossRef.
- F. Machui, P. Maisch, S. Langner, J. Krantz, T. Ameri and C. Brabec, Chem. Phys. Chem., 2015, 16, 1275–1280 CrossRef CAS PubMed.
- S. Park, I. Jin, H. Ahn and J. Jung, Org. Electron., 2020, 86, 105893 CrossRef CAS.
- C. McDowell, M. Abdelsamie, M. Toney and G. Bazan, Adv. Mater., 2018, 30, 1707114 CrossRef PubMed.
- Z. Fu, X. Liu, X. Niu, M. Ren, L. Xue, S. Du, J. Tong, J. Li, X. Bao and Y. Xia, Adv. Sustainable Syst., 2021, 5, 2100235 CrossRef CAS.
- L. Hong, H. Yao, Z. Wu, Y. Cui, T. Zhang, Y. Xu, R. Yu, Q. Liao, B. Gao, K. Xian, H. Woo, Z. Ge and J. Hou, Adv. Mater., 2019, 31, 1903441 CrossRef PubMed.
- G. Park, S. Choi, S. Park, D. Lee, M. Cho and D. Choi, Adv. Energy Mater., 2017, 7, 1700566 CrossRef.
- C. Sprau, F. Buss, M. Wagner, D. Landerer, M. Koppitz, A. Schulz, D. Bahro, W. Schabel, P. Scharfer and A. Colsmann, Energy Environ. Sci., 2015, 8, 2744–2752 RSC.
- S. Bao, H. Yang, H. Fan, J. Zhang, Z. Wei, C. Cui and Y. Li, Adv. Mater., 2021, 33, 2105301 CrossRef CAS PubMed.
- W. Zhao, L. Ye, S. Li, X. Liu, S. Zhang, Y. Zhang, M. Ghasemi, C. He, H. Ade and J. Hou, Sci. China Mater., 2017, 60, 697–706 CrossRef CAS.
- K. Park, Y. An, S. Jung, H. Park and C. Yang, Energy Environ. Sci., 2016, 9, 3464–3471 RSC.
- R. Yu, H. Yao, L. Hong, Y. Qin, J. Zhu, Y. Cui, S. Li and J. Hou, Nat. Commun., 2018, 9, 4645–4654 CrossRef PubMed.
- J. Song, Y. Li, Y. Cai, R. Zhang, S. Wang, J. Xin, L. Han, D. Wei, W. Ma, F. Gao and Y. Sun, Matter, 2022, 5, 4047–4059 CrossRef CAS.
- X. Liu, Z. Liang, S. Du, X. Niu, J. Tong, C. Yang, X. Lu, X. Bao, L. Yan, J. Li and Y. Xia, ACS Appl. Mater. Interfaces, 2022, 14, 9386–9397 CrossRef PubMed.
- H. Xia, Y. Zhang, W. Deng, K. Liu, X. Xia, C. Su, U. Jeng, M. Zhang, J. Huang, J. Huang, C. Yan, W. Wong, X. Lu, W. Zhu and G. Li, Adv. Mater., 2022, 34, 2107659 CrossRef CAS PubMed.
- K. Kranthiraja, U. Aryal, V. Sree, K. Gunasekar, C. Lee, M. Kim, B. Kim, M. Song and S. Jin, ACS Appl. Mater. Interfaces, 2018, 10, 13748–13756 CrossRef CAS PubMed.
- Z. Li, R. Xie, W. Zhong, B. Fan, J. Ali, L. Ying, F. Liu, N. Li, F. Huang and Y. Cao, Sol. RRL, 2018, 2, 1800196 CrossRef.
- C. Liao, M. Zhang, X. Xu, F. Liu, Y. Lia and Q. Peng, J. Mater. Chem. A, 2019, 7, 716–726 RSC.
- H. Chen, R. Zhang, X. Chen, G. Zeng, L. Kobera, S. Abbrent, B. Zhang, W. Chen, G. Xu, J. Oh, S. Kang, S. Chen, C. Yang, J. Brus, J. Hou, F. Gao, Y. Li and Y. Li, Nat. Energy, 2021, 6, 1045–1053 CrossRef CAS.
- P. Xia, M. Wu, S. Zhang, J. Hu, L. Chen, T. Bu, J. Yi, D. Wu and J. Xi, Org. Electron., 2019, 73, 205–211 CrossRef CAS.
- D. Wang, H. Liu, Y. Li, G. Zhou, L. Zhan, H. Zhu, X. Lu, H. Chen and C. Li, Joule, 2021, 5, 945–957 CrossRef CAS.
- Y. Wu, H. Yang, Y. Zou, Y. Dong, C. Cui and Y. Li, Sol. RRL, 2018, 2, 1800060 CrossRef.
- D. Li, C. Guo, X. Zhang, B. Du, C. Yu, P. Wang, S. Cheng, L. Wang, J. Cai, H. Wang, D. Liu, H. Yao, Y. Sun, J. Hou and T. Wang, Sci. China: Chem., 2022, 65, 373–381 CrossRef CAS.
- D. Yuan, G. Qin, L. Zhang, F. Pan, R. Qiu, S. Lei, S. Deng and J. Chen, ACS Appl. Mater. Interfaces, 2021, 13, 57654–57663 CrossRef CAS PubMed.
- J. Liu, Y. Yin, K. Wang, P. Wei, H. Lu, C. Song, Q. Liang and W. Huang, IScience, 2022, 25, 104090 CrossRef CAS PubMed.
- B. Xie, K. Zhang, Z. Hu, H. Fang, B. Lin, Q. Yin, B. He, S. Dong, L. Ying, W. Ma, F. Huang, H. Yan and Y. Cao, Sol. RRL, 2019, 4, 1900385 CrossRef.
- X. Xu, G. Zhang, L. Yu, R. Li and Q. Peng, Adv. Mater., 2019, 31, 1906045 CrossRef CAS PubMed.
- X. Xu, L. Yu, H. Yan, R. Li and Q. Peng, Energy Environ. Sci., 2020, 13, 4381–4388 RSC.
- J. Franeker, M. Turbiez, W. Li, M. Wienk and R. Janssen, Nat. Commun., 2015, 6, 6229–6237 CrossRef PubMed.
- B. Fan, F. Lin, J. Oh, H. Fu, W. Gao, Q. Fan, Z. Zhu, W. Li, N. Li, L. Ying, F. Huang, C. Yang and A. K.-Y. Jen, Adv. Energy Mater., 2021, 11, 2101768 CrossRef CAS.
- X. Song, P. Sun, D. Sun, Y. Xu, Y. Liu and W. Zhu, Nano Energy, 2022, 91, 106678 CrossRef CAS.
- W. Zhao, S. Zhang, Y. Zhang, S. Li, X. Liu, C. He, Z. Zheng and J. Hou, Adv. Mater., 2017, 30, 1704837 CrossRef PubMed.
- K. An, W. Zhong, L. Ying, P. Zhu, B. Fan, Z. Li, N. Li, F. Huang and Y. Cao, J. Mater. Chem. C, 2020, 8, 270–275 RSC.
- X. Zhou, T. Dai, X. Li, Y. Yan, W. Xiong, T. Lin, J. Zhou, D. Xu, Y. Zhu, J. Zhao and A. Geng, ACS Appl. Energy Mater., 2021, 4, 8175–8182 CrossRef CAS.
- X. Li, X. Du, J. Zhao, H. Lin, C. Zheng and S. Tao, Solar RRL, 2021, 5, 2000592 CrossRef CAS.
- H. Ning, Q. Jiang, P. Han, M. Lin, G. Zhang, J. Chen, H. Chen, S. Zeng, J. Gao, J. Liu, F. He and Q. Wu, Energy Environ. Sci., 2021, 14, 5919–5928 RSC.
- B. Zhang, F. Yang, S. Chen, H. Chen, G. Zeng, Y. Shen, Y. Li and Y. Li, Adv. Funct. Mater., 2022, 32, 2202011 CrossRef CAS.
- J. Deng, S. Huang, J. Liu, D. Zhou, L. Zhao, L. Liu, B. Huang, Y. Cheng, C. Yang, F. Wu and L. Chen, Chem. Eng. J., 2022, 443, 136515 CrossRef CAS.
- X. Li, H. Yang, X. Du, H. Lin, G. Yang, C. Zheng and S. Tao, Chem. Eng. J., 2023, 452, 139496 CrossRef CAS.
- H. Huang, X. Li, C. I. Sun, I. Angunawela, B. Qiu, J. Du, S. Qin, L. Meng, Z. Zhang, H. Ade and Y. Li, J. Mater. Chem. C, 2020, 8, 7718–7724 RSC.
- J. Hu, X. Liu, K. Wang, M. Wu, H. Huang, D. Wu and J. Xia, J. Mater. Chem. C, 2020, 8, 2135–2141 RSC.
- N. Al-Shekaili, S. Hashim, F. Muhammadsharif, K. Sulaiman and M. Al-Abri, J. Electron. Mater., 2021, 50, 6828–6835 CrossRef CAS.
- D. Wang, G. Zhou, Y. Li, K. Yan, L. Zhan, H. Zhu, X. Lu, H. Chen and C. Li, Adv. Funct. Mater., 2022, 32, 2107827 CrossRef CAS.
- B. Du, Y. Ma, C. Guo, J. Cai, D. Li, S. Cheng, D. Liu, Q. Zheng and T. Wang, Adv. Funct. Mater., 2021, 31, 2105794 CrossRef CAS.
- X. Gu, L. Shaw, K. Gu, M. Toney and Z. Bao, Nat. Commun., 2018, 9, 534–550 CrossRef PubMed.
- J. Yuan, D. Liu, H. Zhao, B. Lin, X. Zhou, H. Naveed, C. Zhao, K. Zhou, Z. Tang, F. Chen and W. Ma, Adv. Energy Mater., 2021, 11, 2100098 CrossRef CAS.
- M. Richard, A. Al-Ajaji, S. Ren, A. Foti, J. Tran, M. Frigoli, B. Gusarov, Y. Bonnassieux, E. G. Caurel, P. Bulkin, R. Ossikovski and A. Yassar, Adv. Colloid Interface Sci., 2020, 275, 102080 CrossRef CAS PubMed.
- X. Meng, L. Zhang, Y. Xie, X. Hu, Z. Xing, Z. Huang, C. Liu, L. Tan, W. Zhou, Y. Sun, W. Ma and Y. Chen, Adv. Mater., 2019, 31, 1903649 CrossRef CAS PubMed.
- H. Li, S. Liu, X. Wu, Q. Qi, H. Zhang, X. Meng, X. Hu, L. Ye and Y. Chen, Energy Environ. Sci., 2022, 15, 2130–2138 RSC.
- S. Liu, H. Li, X. Wu, D. Chen, L. Zhang, X. Meng, L. Tan, X. Hu and Y. Chen, Adv. Mater., 2022, 34, 2201604 CrossRef CAS PubMed.
- S. Dong, T. Jia, K. Zhang, J. Jing and F. Huang, Joule, 2020, 4, 2004–2016 CrossRef CAS.
- Y. Li, H. Liu, J. Wu, H. Tang, H. Wang, Q. Yang, Y. Fu and Z. Xie, ACS Appl. Mater. Interfaces, 2021, 13, 10239–10248 CrossRef CAS PubMed.
- Y. Li, J. Wu, H. Tang, X. Yi, Z. Liu, Q. Yang, Y. Fu, J. Liu and Z. Xie, ACS Appl. Mater. Interfaces, 2022, 14, 31054–31065 CrossRef CAS PubMed.
- H. Zhao, H. Naveed, B. Lin, X. Zhou, J. Yuan, K. Zhou, H. Wu, R. Guo, M. Scheel, A. Chumakov, S. Roth, Z. Tang, P. Müller-Buschbaum and W. Ma, Adv. Mater., 2020, 32, 2002302 CrossRef CAS PubMed.
- H. Zhao, B. Lin, J. Xue, H. Naveed, C. Zhao, X. Zhou, K. Zhou, H. Wu, Y. Cai, D. Yun, Z. Tang and W. Ma, Adv. Mater., 2021, 34, 2105114 CrossRef PubMed.
- L. Zhu, W. Zhong, C. Qiu, B. Lyu, Z. Zhou, M. Zhang, J. Song, J. Xu, J. Wang, J. Ali, W. Feng, Z. Shi, X. Gu, L. Ying, Y. Zhang and F. Liu, Adv. Mater., 2019, 31, 1902899 CrossRef CAS PubMed.
- N. Chaturvedi, N. Gasparini, D. Corzo, J. Bertrandie, N. Wehbe, J. Troughton and D. Baran, Adv. Funct. Mater., 2020, 31, 2009996 CrossRef.
- J. Xue, H. Zhao, B. Lin, Y. Wang, Q. Zhu, G. Lu, B. Wu, Z. Bi, X. Zhou, C. Zhao, G. Lu, K. Zhou and W. Ma, Adv. Mater., 2022, 34, 2202659 CrossRef CAS PubMed.
- Y. Zhao, G. Wang, Y. Wang, T. Xiao, M. Adil, G. Lu, J. Zhang and Z. Wei, Sol. RRL, 2019, 3, 1800333 CrossRef.
- H. Liu, L. Wang, H. Liu, M. Guan, C. Su, U. Jeng, B. Zhao, C. Weng, K. You and X. Lu, Chem. Eng. J., 2022, 429, 132407 CrossRef CAS.
- J. Wan, L. Zeng, X. Liao, Z. Chen, S. Liu, P. Zhu, H. Zhu and Y. Chen, Adv. Funct. Mater., 2022, 32, 2107567 CrossRef CAS.
- J. Guo, Y. Wu, W. Wang, T. Wang and J. Min, Sol. RRL, 2022, 6, 2101024 CrossRef CAS.
- Z. Du, M. Mainville, J. Vollbrecht, A. Dixon, N. Schopp, M. Schrock, Z. Peng, J. Huang, S. Chae, H. Ade, M. Leclerc, G. Reddy and T. Nguyen, Sol. RRL, 2021, 5, 2100213 CrossRef CAS.
- C. Kim, S. Chen, J. Park, G. Kim, H. Kang, S. Lee, T. Phan, S. Kwon, Y. Kim and B. Kim, J. Mater. Chem. A, 2021, 9, 24622–24630 RSC.
- H. Yu, S. Luo, R. Sun, I. Angunawela, Z. Qi, Z. Peng, W. Zhou, H. Han, R. Wei, M. Pan, A. Cheung, D. Zhao, J. Zhang, H. Ade, J. Min and H. Yan, Adv. Funct. Mater., 2021, 31, 2100791 CrossRef CAS.
- C. Liao, Y. Chen, C. Lee, G. Wang, N. Teng, C. Lee, W. Li, Y. Chen, C. Li, H. Ho, P. Tan, B. Wang, Y. Huang, R. Young, M. Wasielewski, T. Marks, Y. Chang and A. Facchetti, Joule, 2020, 4, 189–206 CrossRef CAS.
- T. Kumari, S. Jung, Y. Cho, H. Kim, J. Lee, J. Oh, J. Lee, S. Lee, M. Jeong, J. Baik, W. Jo and C. Yang, Nano Energy, 2020, 68, 104327 CrossRef CAS.
- X. Han, J. Zhu, Y. Xiao, H. Jiang, Z. Zhang, J. Wang, Z. Li, Y. Lin, X. Lu and X. Zhan, Sol. RRL, 2020, 4, 2000108 CrossRef CAS.
- J. Cheng, L. Zhang, H. Jiang, D. Yuan, Q. Wang, Y. Cao and J. Chen, Org. Electron., 2020, 85, 105871 CrossRef CAS.
- C. Zhang, F. Lin, W. Huang, J. Xin, J. Wang, Z. Lin, W. Ma, T. Yang, J. Xia and Y. Liang, J. Mater. Chem. C, 2020, 8, 11532–11539 RSC.
|
This journal is © The Royal Society of Chemistry 2023 |
Click here to see how this site uses Cookies. View our privacy policy here.