Facile synthesis of alkyl- and arylboronate esters enabled by a carbon nanotube supported copper catalyst†
Received
7th October 2022
, Accepted 15th November 2022
First published on 15th November 2022
Abstract
An efficient synthesis of alkylboronate esters via alkyl halide borylation catalysed by copper nanoparticles stabilised on nitrogen-doped carbon nanotubes (N-CNT) is reported. This nanocatalyst provides practical access to alkylboronate esters at room temperature in 1 h, with good functional group tolerance. The procedure is also applicable to the borylation of benzyl chlorides and bromides. Radical clock experiments suggest that the reaction involves a radical pathway. The catalyst can be recycled up to ten runs without appreciable loss in the activity. In addition, we demonstrated the use of this supported copper catalyst for the anti-Markovnikov-selective hydroboration of vinylarenes and borylation of aryl halides with B2pin2, providing alkyl- and arylboronate esters, respectively, in good to excellent yields.
Introduction
Alkylboronic acids and esters represent highly valuable nucleophilic partners in transition-metal-catalysed cross-coupling reactions due to their stability and wide functional group tolerance.1,2 Additionally, these motifs are extensively used as key building blocks in chemosensoring,3 medicinal chemistry4 and in the field of materials science.5 Conventionally, these derivatives are synthesised by the reaction of reactive organometallic reagents (alkyl lithium or alkyl magnesium) with trialkoxyboranes via the transmetalation process. Advanced synthetic approaches include catalytic hydroboration of olefin,6 alkane C–H borylation,7 and β-borylation of α,β-unsaturated carbonyl compounds.8 In recent decades, homogeneous transition-metal-catalysed borylation of alkyl halides,9 based on Cu,10 Ni,11 Pd,12 Fe,13 Zn,14 Rh,15 Mn,16 Ag,17 Ti,18etc., has emerged as a potent synthetic tool to obtain such derivatives. Among the nonprecious metals explored, copper is quite attractive due to its low toxicity, low environmental impact, high abundance, and low cost.19 In 2012, Marder's10a and Ito's10b groups independently reported the first borylation of alkyl halides with diboron reagents using a Cu(I)-catalyst (Scheme 1a). Subsequently, Ito et al. reported a Cu(I)-catalysed borylative exo-cyclization and boryl substitution of alkyl halides bearing a terminal C
C double bond.10c,f,20 A Cu(II)-NHC-catalyst system for alkyl halides, including chlorides, was reported by Marder et al.10h The Cu(I)-catalysed borylation using B2neop2 (bis(neopentyl glycolato)diboron)21a and unsymmetrical diboron [(pin)B–B(dan)] (pin = pinacol; dan = 1,8-diaminonaphthalene) was also explored.21b
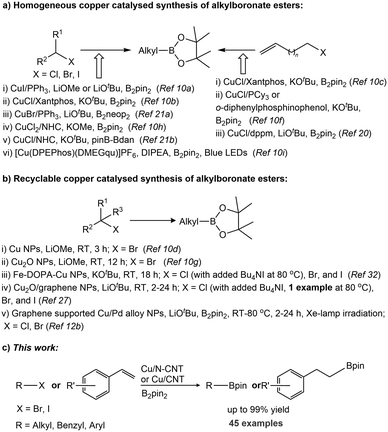 |
| Scheme 1 Synthesis of alkylboronate esters via copper-catalysed borylation: a) homogeneous catalyst systems, b) heterogeneous catalyst systems, and c) this work. | |
The stereoselective borylative cyclization of alkyl halides was developed by Ito et al.22 Recently, metal-free protocols were developed by Melchiorre et al. via photochemical borylation of benzyl halides, using dithiocarbonyl anion as an organocatalyst,23a and base-assisted alkyl iodide borylation was reported by Mo et al.23b In addition, a series of photoinduced transition metal-free radical-type borylation reactions were developed to yield alkylboronate esters.24
Whilst excellent homogeneous catalytic borylations of alkyl halides have been reported in recent years, these catalyst systems are associated with disadvantages, such as an inability of reusing the catalyst, a necessity to use ligands, and metal contamination in the products, limiting their use in industrial applications. Therefore, the use of recyclable nanoparticles (NPs) as heterogeneous catalysts has attracted attention recently, from a standpoint of environmental and sustainable chemistry (Scheme 1b).25 In 2012, Sarkar and co-workers developed a Pd NP-catalysed borylation of benzyl halides with bis(pinacolato)diboron (B2pin2), affording benzyl boronate esters in the presence of weak base KOAc.26 In 2014, Chung et al. reported the borylation of primary and secondary alkyl bromides with B2pin2, catalysed by commercially available copper nanoparticles (Cu NPs) in the presence of 2 equiv. of LiOMe as a base and DMF as a solvent.10d Huang, Xu and co-workers described the borylation reaction of activated and unactivated alkyl bromides catalysed by recyclable Cu2O nanoparticles supported on carbon black (Cu2O NPs/CB).10g Recently, Tortosa and Cid et al. described the borylation of aliphatic halides catalysed by recyclable Cu2O nanoparticles supported on graphite nanoplatelets at room temperature for 2–24 h (only one substrate, (2-bromopropyl)benzene, at rt for 30 min).27 Guo et al. reported a photocatalytic process based on graphene supported Cu/Pd alloy nanoparticles for the borylation of alkyl bromides and chlorides.12b
For the synthesis of heterogeneous nanoparticle catalysts, the metals/metal salts were coated, doped or immobilized on different suitable supports, for instance, carbon materials, silicon dioxide or titanium dioxide, to prevent aggregation. This may sometimes also have synergetic influence towards catalytic activity.28 In this context, carbon based materials, such as carbon nanotubes, carbon spheres, and carbon fibers, are primarily used as a support, because of their nano size, large specific surface area, mechanical strength, high electrical conductivity, and high chemical stability.29 Among all of these, N-doped carbon nanotubes (NCNTs) are an ideal choice, in which nitrogen configurations can be pyridine or pyrrole in/on carbon nanoparticles surface.30 The metal nanoparticles supported on N-doped nanocarbon were found to be advantageous for catalytic activity, selectivity, and stability, with respect to the N-free counterpart. Therefore, this material is the preferred choice in the field of catalysis.
Efforts in our laboratory have been directed towards developing heterogeneous catalyst systems for the synthesis of organoborane derivatives.31 Recently, we have reported an easy recyclable catalytic system based on a nano-ferrite-supported Cu catalyst (Fe-DOPA-Cu NPs; DOPA = dopamine) for the borylation of alkyl halides with alkoxy diboron reagents.32 The development of a new heterogeneous material for the synthesis of alkylboronate esters via both alkyl halide borylation and alkene hydroboration under mild reaction conditions with good recyclability would be of great advantage. In this study, we report an efficient catalytic system based on nitrogen-doped carbon nanotube-supported Cu nanoparticles (Cu/N-CNT NPs) for the borylation of alkyl halides, including benzyl chlorides and bromides, with alkoxy diboron reagents in 1 h under mild reaction conditions. In addition, supported copper NPs catalyse the hydroboration/protoboration of vinylarenes and the borylation of aryl halides with B2pin2 with good functional group tolerance.
Results and discussion
The copper nanoparticle-stabilised nitrogen-doped carbon nanotubes (Cu/N-CNT) were prepared using a wet chemical method.33 Cu/N-CNT NPs were characterised using field emission scanning electron microscopy (FESEM), transmission electron microscopy (TEM), energy-dispersive X-ray spectroscopy (EDS), Brunauer–Emmett–Teller (BET) analysis, powder XRD (X-ray diffraction), X-ray photoelectron spectroscopy (XPS), thermal gravimetric analysis (TGA), and atomic absorption spectroscopy (AAS; see ESI† for details). The TEM analysis of Cu/N-CNTs shows that the nanoparticles had a particle size in the range of 5–35 nm and an average particle size of ∼19 nm. XRD and XPS techniques provide important information about the oxidation state of the metal in the material. Both CuO and Cu2O species are detected by X-ray powder diffraction. In X-ray photoelectron spectroscopy (XPS), the peak of Cu 2p3/2 at 934.03 eV was accompanied by two satellite peaks at about 941.16 eV and 943.84 eV, suggesting the existence of Cu(II). The peak of Cu 2p1/2 at 953.98 eV and its satellite peak at 962.28 eV also confirm the presence of Cu(II).32 Cu(II) is detected on the surface (using XPS), whereas both Cu(I) and Cu(II) are present in the bulk material (using XRD). Due to the higher tendency of Cu to undergo oxidation upon exposure to oxygen, the copper on the surface present as Cu(II) species. Copper anchored between layers would possibly be prevented from undergoing oxidation. Further XPS analysis confirms nitrogen doping into the carbon nanotubes. Atomic absorption spectroscopy (AAS) showed that the Cu loading is 54.5 wt%.
Alkyl halide borylation
We initiate our study by investigating the borylation of commercially available (3-bromopropyl)benzene (1a) as the model substrate (Table 1). In the presence of Cu/N-CNT NPs as the catalyst (5 mg; 17 mol%, based on Cu), 1.2 equiv. of B2pin2 and KOtBu in DMF (dimethylformamide) solvent at 80 °C in 24 h gave a 96% yield of 1-Bpin-3-phenylpropane (1b; entry 1). In the absence of catalyst, only a 9% yield of 1b was obtained (entry 2). Using CNT (carbon nanotubes) as a catalyst, a trace of 1b was observed (entry 3). Further, to evaluate the influence of nitrogen doping of carbon nanotubes, we examined the activity of nano Cu/CNT (copper nanoparticles stabilised on carbon nanotubes) as a catalyst and the result shows the formation of 1b in 88% yield (entry 4).
Table 1 Optimisation results for the nanoparticle-catalysed borylation of (3-bromopropyl)benzene (1a)a
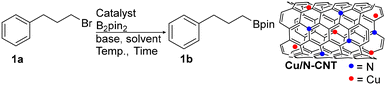
|
Entry |
Catalyst (NPs) |
Solvent |
Base |
Time (h) |
Temp (°C) |
Yieldb (%) |
Reaction conditions: 1a (0.25 mmol, 1 equiv.), NPs (5 mg), base (1.2 equiv.), B2pin2 (1.2 equiv.), solvent (1 mL), at 80 °C unless otherwise stated.
Yields were determined by 1H NMR using nitromethane as an internal standard.
Isolated yield after chromatographic workup.
CuO (2 mg, 10 mol%) was used.
CuO (2 mg; 10 mol%) and N-CNT (5 mg) were used.
Reaction was performed in air. RT = room temperature.
|
1 |
Cu/N-CNT |
DMF |
KOtBu |
24 |
80 |
96 |
2 |
— |
DMF |
KOtBu |
24 |
80 |
9 |
3 |
CNT |
DMF |
KOtBu |
24 |
80 |
Trace |
4 |
Cu/CNT |
DMF |
KOtBu |
24 |
80 |
88 |
5 |
Cu/N-CNT |
CH3CN |
KOtBu |
24 |
80 |
47 |
6 |
Cu/N-CNT |
Toluene |
KOtBu |
24 |
80 |
0 |
7 |
Cu/N-CNT |
DMF |
NaOtBu |
24 |
80 |
85 |
8 |
Cu/N-CNT |
DMF |
NaOMe |
24 |
80 |
98 |
9 |
Cu/N-CNT |
DMF |
KOMe |
24 |
80 |
99 |
10 |
Cu/N-CNT |
DMF |
— |
24 |
80 |
0 |
11 |
Cu/N-CNT |
DMF |
KOMe |
18 |
80 |
99 |
12 |
Cu/N-CNT |
DMF |
KOMe |
8 |
80 |
99 |
13 |
Cu/N-CNT |
DMF |
KOMe |
2 |
80 |
99 |
14 |
Cu/N-CNT |
DMF |
KOMe |
1 |
80 |
99 |
15 |
Cu/N-CNT |
DMF |
KOMe |
1 |
50 |
99 |
16 |
Cu/N-CNT |
DMF |
KOMe |
1 |
RT |
99 (84)c |
17 |
CuOd |
DMF |
KOMe |
1 |
RT |
59 |
18 |
CuO + N-CNTe |
DMF |
KOMe |
1 |
RT |
19 |
19f |
Cu/N-CNT |
DMF |
KOMe |
1 |
RT |
73 |
We next explored the solvent effect. The reaction in acetonitrile gave a lower yield of 1b (entry 5), whereas, in toluene solvent, it was completely inhibited (entry 6). Reactions using different bases, such as NaOtBu (entry 7), NaOMe (entry 8) and KOMe (entry 9), gave 1b in 85%, 98% and 99% yields, respectively. A control experiment established that the base is essential for the reaction to proceed (entry 10). Gratifyingly, the reaction proceeded very rapidly, requiring only 60 min to reach completion at room temperature (entries 11–16; at 50 °C require only 30 min; see Table S5†), while comparable transition-metal catalysed alkyl halide borylation reactions require several hours at RT-80 °C.10d,g,12b,25–27 When unsupported CuO NPs were used as a catalyst, only 59% of 1b was obtained (entry 17). Further, using CuO NPs and N-CNT together as catalyst, without previous anchoring, resulted in a significant decrease in the product yield (entry 18). The difference between the catalytic activity of alkyl halide borylation with and without N-CNT support (entries 16–18) revealed a synergetic effect of copper when anchored to nitrogen-doped carbon nanotubes. Interestingly, the reaction is somewhat tolerant of air (entry 19), an important aspect for practical application.
Implementing the best conditions described in entry 16 in Table 1, we focused on the generality of this heterogeneous Cu/N-CNT NP-catalysed borylation protocol. As for the scope of the process (Table 2), a range of substrates including primary and secondary alkyl halides can be efficiently borylated. Unactivated primary alkyl halides bearing a variety of functional groups, including ethers (5a–7a), ester (8a) and ketal (9a) are tolerated, and the corresponding alkylboronate esters were produced in excellent yields. The reaction of 1,4-dibromobutane with 2.4 equiv. of B2pin2 proceeded smoothly to give the 1,4-diborylated product (10b). 1-Bromo-6-chlorohexane (11a) exclusively gave monoborylation at the primary bromide center under the optimised reaction conditions. This reactivity difference can be used for the selective borylation of the C–Br bond of 11a.
Table 2 Screening of alkyl halides for the Cu/N-CNT-catalysed borylation reactiona
Reaction conditions: alkyl halide (1.0 mmol, 1 equiv.), Cu/N-CNT NPs (20 mg), B2pin2 (1.2 equiv.), KOMe (1.2 equiv.), DMF, 1 h at room temperature unless otherwise stated. Yields were determined by 1H NMR using nitromethane as an internal standard. Isolated yields are given in parentheses.
Reaction was performed using Cu/CNT as the catalyst.
Using 2.4 equiv. of B2pin2 and KOMe.
Reaction was performed at 80 °C for 24 h.
exo-2-Bromonorbornane was used, resulting in an exo : endo product ratio of ca. 74 : 26.
Reaction performed in the presence of 1.0 equiv. of (Bu4N)I at 80 °C for 30 h.
|
|
Next, we turned our attention to secondary alkyl bromides, such as acyclic, cyclic and bicyclic (12a–15a), which were efficiently converted into the corresponding secondary alkylboronate esters (12b–15b) in excellent yields (Table 2). The effects of the halides (Cl, Br and I) were investigated with cyclohexyl substrates (14); cyclohexyl iodide is readily converted into 14b (yield = 96%), while cyclohexyl chloride is not effectively borylated, the conversion being very low, even at a higher temperature and longer reaction time. exo-2-Bromonorbornane produced predominantly the exo product (15b; exo
:
endo ratio of 74
:
26). Alkyl halide with a protected amine (16a) was also readily borylated. Importantly, no reactivity difference was observed when Cu/CNT was used as the catalyst at room temperature for the borylation of some selected alkyl halides (Table 2; note b).
Borylation of 1-bromoadamantane (17a) gave a trace amount of product; even the addition of (Bu4N)I did not induce the transformation. This method is amenable to a gram scale (5 mmol) with the same efficiency. The borylation of 1a gave the desired product 1b in 79% yield (0.972 g).
Readily available unactivated alkyl chloride borylation is challenging and elusive.10h,13,16,18,23a,24u,v,27,32 Therefore, we intend to extend our approach to alkyl chloride borylation. Unactivated alkyl chloride borylation was unsuccessful under the optimised reaction conditions (vide supra); however, the addition of 1 equiv. of tetrabutylammonium iodide (Bu4NI) gave the desired alkylboronate esters in moderate to good yields (1b, 4b, 18b–21b; Table 3). This heterogeneous-catalyst protocol is also applicable for the borylation of a variety of heterocyclic substrates, such as thiophen (19a) and indole (20a) systems, giving borylated products in moderate to good yields. Notably, dichloromethane (21a) gave diborylmethane (21b) in 70% isolated yield, a valuable synthetic building block in organic synthesis.34,35 Cyclohexyl chloride substrate gave a low yield of desire product, even after prolonged heating. The reaction of benzylic halides (X = Cl and Br) gave the desired alkylboronate esters in good yields (22b). Furthermore, this protocol allows us to replace B2pin2 with B2neop2,36 giving the corresponding 3-phenylpropyl-Bneop compound (23b) in an excellent yield (82%; Scheme 2). A complete list of unsuccessful alkyl halide substrates for this heterogeneous borylation strategy is shown in Table S7, in the ESI.†
Table 3 Scope of the Cu/N-CNTs nanoparticle-catalysed borylation of alkyl chloridesa
Reaction conditions: alkyl chloride (1.0 mmol, 1 equiv.), Cu/N-CNT NPs (20 mg), B2pin2 (1.2 equiv.), KOMe (1.2 equiv.), 1.0 equiv. of (Bu4N)I in DMF at 80 °C for 24 h unless otherwise stated. Yields were determined by 1H NMR using nitromethane as an internal standard. Isolated yields are given in parentheses.
Reaction was performed using 2.4 equiv. of B2pin2 and KOMe, and 2.0 equiv. of (Bu4N)I.
Reaction was performed using KOtBu at 80 °C for 30 h.
Reaction was performed in the absence of (Bu4N)I.
|
|
 |
| Scheme 2 Borylation of (3-bromopropyl)benzene (1a) using B2neop2. | |
To check the heterogeneous nature of the Cu/N-CNT NP catalyst system, we performed a mercury poisoning experiment. Experimental results confirmed the heterogeneity of the catalyst (see ESI†). Further, a filtration experiment was performed using 1a as a substrate. After the reaction was left to proceed for 10 min (1b yield = 46%), the catalyst was filtered off and the filtrate was stirred for another 50 min under the standard reaction conditions. GC-MS analysis showed no enhancement of the yield of 1b after the removal of the catalyst. The removed catalyst was added to the filtrate and stirred for another 1 h, leading to the complete conversion of 1a, indicating negligible leaching and heterogeneity of the catalyst. To demonstrate the utility of this heterogeneous catalyst system, recycling experiments were carried out. Using 1a as a model substrate, Cu/N-CNT NPs were filtered out from the reaction mixture after the completion of the first cycle and were reused up to 10 times with no significant loss of catalytic activity (Fig. 1). These results demonstrated the excellent recyclability and stability of the NP catalyst system.
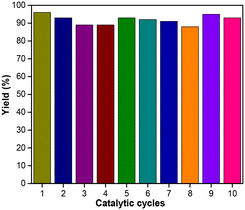 |
| Fig. 1 Cu/N-CNT nanoparticle catalyst recovery and recyclability experiments for the borylation of (3-bromopropyl)benzene (1a). | |
Next, the mechanism of this nanoparticle catalysed borylation of alkyl halides was investigated. We first explored the possibility of a radical-mediated mechanism by performing the reaction on cyclopropylmethyl bromide (24a, Scheme 3). The reaction of 24a at room temperature for 1 h yielded exclusively the ring-opened product 3-butenylboronate ester (24c). The borylation on 6-bromohex-1-ene (25a) afforded the cyclized alkylboronate ester 25c as the major product. The formation of ring-opened product 24c, as well as the cyclized product 25c, suggests the possibility of a radical mechanism. However, the addition of a Cu boryl bond to a terminal alkene followed by intramolecular cyclization cannot be excluded.10c
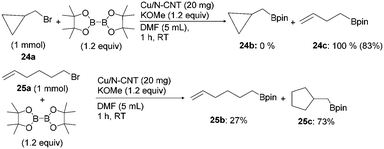 |
| Scheme 3 Borylation of cyclopropylmethyl bromide (24a) and 6-bromohex-1-ene (25a). | |
To validate the radical-mediated process, the reaction of 1a was performed in the presence of a radical scavenger TEMPO (2,2,6,6-tetramethyl-1-piperidinyloxy; 1 equiv.), and the desired product 1b was obtained in only 18% yield (Scheme 4). Analysis of the crude reaction mixture revealed the formation of the covalently bonded scavenger product 3-phenyl-1-(2′,2′,6′,6′-tetramethyl-1′-piperidinyloxy)-propane (1c)10h,37 in a 41% yield. Furthermore, the addition of 9,10-dihydroanthracene (7 equiv.) shuts down the reaction completely (0% of 1b). Therefore, this catalyst system seems to proceed via a radical mechanism.
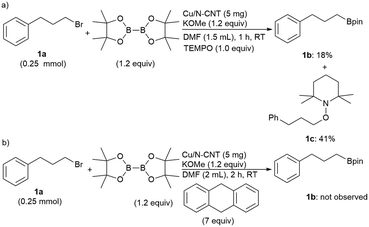 |
| Scheme 4 Radical scavenging experiments using: a) TEMPO and b) 9,10-dihydroanthracene as the reagent. | |
Computational studies
Density functional theory (DFT) calculations were carried out to demonstrate the step-by-step formation of alkylboronate esters by copper oxide stabilised on a nitrogen-doped carbon nanotube (CuO@N-CNT) catalyst. To support the involvement of radical species and the formation of alkylboronate ester (alkyl-Bpin), a free energy profile for the borylation reaction was calculated using the equation ΔG = ΔE − TΔS + ZPE,38,39 where ΔE denotes the change in total energy (calculated from DFT), ΔS represents the change in entropy and ZPE is the zero-point energy. Details of the entropy and zero-point energy are given in the ESI.†
DFT studies were performed using CuO cluster as a model (Fig. S11†), as well as a single Cu atom as a model (Fig. S12†). For the formation of the alkyl-Bpin product on copper nanoparticles, we considered CNT (5,5) as the host surface. We observed that the CuO cluster followed the chemisorption process and adsorbed strongly on the N-CNT surface with a free energy change of −0.19 eV and is named CuO@N-CNT. Overall, the reaction energy for the borylation is exothermic. The free energy profiles and a detailed mechanism of the reaction steps which were followed in plotting the free energy profiles are shown in ESI.†
Hydroboration of alkenes
The hydroboration/protoboration of alkenes using borane derivatives and diboron reagents is an attractive approach for the synthesis of alkylboronate esters. To date, several precious40 and non-precious 3d-transition metal-based catalyst systems41 have been developed for the protoboration of alkenes. In addition, a handful of examples of heterogeneous catalytic systems for the hydroboration of unsaturated hydrocarbons have also been reported.25a,42,43 To our knowledge, heterogeneous catalysts suitable for both alkyl halide and alkene protoboration are rare.32,44 We recently reported the protoboration of terminal alkene substrates with Fe-DOPA-Cu NPs.44 The Cu/N-CNT NPs catalyse the protoboration of styrene at room temperature (Table 4). The anti-Markovnikov-selective protoboration product 2b was obtained in >99% yield in the presence of 1.2 equiv. of B2pin2 and KOMe, and 5 equiv. of MeOH as an additive in DMF (entry 1). In the absence of a catalyst, a trace amount of 2b was detected (entry 2). When no base was used, no alkylboronate ester was formed (entry 3). A comparable yield was obtained when the MeOH additive was reduced to 2 equiv. (entry 4).
Table 4 Conditions for the nanoparticle-catalysed protoboration of styrenea

|
Entry |
Catalyst (NPs) |
Base |
MeOH (equiv.) |
Temp (°C) |
Time (h) |
Yieldb (%) |
Reaction conditions: styrene (0.25 mmol, 1 equiv.), NPs (5 mg), KOMe (1.2 equiv.), B2pin2 (1.2 equiv.), DMF (1 mL), MeOH for 1 h unless otherwise stated.
Yields were determined by 1H NMR spectroscopy using nitromethane as an internal standard.
|
1 |
Cu/N-CNT |
KOMe |
5 |
RT |
1 |
>99 |
2 |
— |
KOMe |
5 |
RT |
1 |
Trace |
3 |
Cu/N-CNT |
— |
5 |
RT |
1 |
0 |
4 |
Cu/N-CNT |
KOMe |
2 |
RT |
1 |
>99 |
With the optimised conditions in hand, the scope of the anti-Markovnikov-selective protoboration reaction was investigated using differently substituted styrene derivatives, as depicted in Table 5. Neutral (2b and 26b), electron-donating substituents, such as p-Me (28b), p-tBu (29b) and m-OMe (30b) groups, were well tolerated, affording the desired primary alkylboronate esters in excellent yields. Phenyl-substituted styrene gave a high yield of 27b. The styrene derivatives bearing the electron-withdrawing halide groups also showed good reactivity and selectivity (31a–33b).
Table 5 Substrate scope of Cu/N-CNT NP-catalysed protoboration of vinylarenesa
Further, the recyclability of the Cu/N-CNT NP-catalysed protoboration of styrene with B2pin2 was examined under standard reaction conditions. To our delight, the catalyst is recyclable and reusable up to five consecutive cycles without the loss of activity (see ESI†).
Aryl halides borylation
To expand the catalytic activity of this carbon nanotube-supported Cu nanoparticles material, we examined the borylation of aryl halides. Arylboronate esters are of great importance in organic synthesis, particularly in transition-metal-catalysed C–C, C–O and C–N bond-forming reactions, as exemplified by the Suzuki–Miyaura cross-coupling reaction.1,45 While Cu/N-CNT NPs worked in the reaction (see ESI†), Cu/CNT NPs offered the optimal combination of reactivity. Aryl halides with different electronic properties, as well as different halogen substituents, were investigated (Table 6). Aryl iodides with electron donating and withdrawing groups were converted into the corresponding ArBpin compounds in satisfactory to good yields. Furthermore, aryl bromides were borylated in moderate yields.
Table 6 Substrate scope of Cu/CNT NP-catalysed borylation of aryl halidesa
Conclusions
In summary, we have developed an efficient heterogeneous nitrogen-doped carbon nanotube-supported Cu nanoparticle-catalysed borylation of alkyl halides and protoboration of vinylarenes with diboron reagents at room temperature. The material is easily recyclable, and the catalytic reactions are scalable, proceeding under mild reaction conditions. This reaction offers good functional group compatibility, providing easy-to-access synthetically useful alkylboronate esters in good to excellent yields. Control experiments show some synergetic effect when CuO is anchored to N-CNT support. Preliminary mechanistic investigations suggest a possible radical pathway. DFT studies show that dissociation to form alkylboronate esters on CuO@N-CNT catalyst follow an exothermic reaction. Further efforts will be directed toward the development of relevant processes using nanoparticles as a catalyst and understanding the reaction mechanism in detail.
Conflicts of interest
There are no conflicts to declare.
Acknowledgements
S. K. B. thanks SERB (CRG/2022/002013), CSIR (01/3067/21/EMR-II) and JAIN (Deemed-to-be University) start-up research grant for funding. R. T. thanks SERB (CRG/2021/000620) and National Supercomputer Mission (NSM), India for financial support (Ref No: DST/NSM/R&D HPC Applications/2021/19). The authors also thank AllyChem Co. Ltd. for generously gifting B2pin2 and B2neop2, the Nanomission (SR/NM/NS-20/2014) for providing FESEM, EDX and PXRD analysis, IISc for NMR, XPS and 200 kV FETEM facilities, and the High-Performance Computing Center, SRM Institute of Science and Technology for providing computational facilities.
Notes and references
-
(a) A. Suzuki, Acc. Chem. Res., 1982, 15, 178–184 CrossRef CAS;
(b) N. Miyaura and A. Suzuki, Chem. Rev., 1995, 95, 2457–2483 CrossRef CAS;
(c)
D. G. Hall, in Boronic Acids: Preparation, Applications in Organic Synthesis and Medicine, ed. D. G. Hall, Wiley-VCH, Weinheim, Germany, 2011 CrossRef;
(d)
A. D. Meijere, Metal-Catalyzed Cross-Coupling Reactions, 2nd edn, Wiley-VCH, Weinheim, 2004 CrossRef;
(e) A. C. Frisch and M. Beller, Angew. Chem., Int. Ed., 2005, 44, 674–688 CrossRef CAS;
(f) S. K. Bose, L. Mao, L. Kuehn, U. Radius, J. Nekvinda, W. L. Santos, S. A. Westcott, P. G. Steel and T. B. Marder, Chem. Rev., 2021, 121, 13238–13341 CrossRef CAS.
-
(a) H. C. Brown and S. Krishnamurthy, Tetrahedron, 1979, 33, 567–607 CrossRef;
(b) R. Jana, T. P. Pathak and M. S. Sigman, Chem. Rev., 2011, 111, 1417–1492 CrossRef CAS PubMed;
(c) A. J. J. Lennox and G. C. Lloyd-Jones, Chem. Soc. Rev., 2014, 43, 412–443 RSC;
(d) L. Xu, G. Wang, S. Zhang, H. Wang, L. Wang, L. Liu, J. Jiao and P. Li, Tetrahedron, 2017, 73, 7123–7157 CrossRef CAS;
(e) J. W. B. Fyfe and A. J. B. Watson, Chem, 2017, 3, 31–55 CrossRef CAS;
(f) C. Sandford and V. K. Aggarwal, Chem. Commun., 2017, 53, 5481–5494 RSC;
(g) E. C. Neeve, S. J. Geier, I. A. I. Mkhalid, S. A. Westcott and T. B. Marder, Chem. Rev., 2016, 116, 9091–9161 CrossRef CAS.
- S. D. Bull, M. G. Davidson, J. M. H. Van den Elsen, J. S. Fossey, A. T. A. Jenkins, Y.-B. Jiang, Y. Kubo, F. Marken, K. Sakurai, J. Zhao and T. D. James, Acc. Chem. Res., 2013, 46, 312–326 CrossRef CAS PubMed.
-
(a) P. C. Trippier and C. McGuigan, Med. Chem. Commun., 2010, 1, 183–198 RSC;
(b) R. Smoum, A. Rubinstein, V. M. Dembitsky and M. Srebnik, Chem. Rev., 2012, 112, 4156–4220 CrossRef CAS.
-
(a) Y. Shirota, M. Kinoshita, T. Noda, K. Okumoto and T. Ohara, J. Am. Chem. Soc., 2000, 122, 11021–11022 CrossRef CAS;
(b) C. D. Entwistle and T. B. Marder, Angew. Chem., Int. Ed., 2002, 41, 2927–2931 CrossRef CAS;
(c) H. Doi, M. Kinoshita, K. Okumoto and Y. Shirota, Chem. Mater., 2003, 15, 1080–1089 CrossRef CAS;
(d) C. D. Entwistle and T. B. Marder, Chem. Mater., 2004, 16, 4574–4585 CrossRef CAS;
(e) S. Yamaguchi and A. Wakamiya, Pure Appl. Chem., 2006, 78, 1413–1424 CrossRef CAS;
(f) M. Elbing and G. C. Bazan, Angew. Chem., Int. Ed., 2008, 47, 834–838 CrossRef CAS PubMed;
(g) A. Fukazawa and S. Yamaguchi, Chem. – Asian J., 2009, 4, 1386–1400 CrossRef CAS PubMed;
(h) F. Jäkle, Chem. Rev., 2010, 110, 3985–4022 CrossRef PubMed;
(i) Y. L. Rao, H. Amarne and S. Wang, Coord. Chem. Rev., 2012, 256, 759–770 CrossRef CAS;
(j) A. Lorbach, A. Hübner and M. Wagner, Dalton Trans., 2012, 41, 6048–6063 RSC;
(k) A. Wakamiya and S. Yamaguchi, Bull. Chem. Soc. Jpn., 2015, 88, 1357–1377 CrossRef CAS;
(l) S. Mukherjee and P. Thilagar, J. Mater. Chem. C, 2016, 4, 2647–2662 RSC;
(m) H. Helten, Chem. – Eur. J., 2016, 22, 12972–12982 CrossRef CAS PubMed;
(n) Y. Ren and F. Jäkle, Dalton Trans., 2016, 45, 13996–14007 RSC;
(o) L. Ji, S. Griesbeck and T. B. Marder, Chem. Sci., 2017, 8, 846–863 RSC;
(p) W. L. A. Brooks and B. S. Sumerlin, Chem. Rev., 2016, 116, 1375–1397 CrossRef CAS.
-
(a) D. Männig and H. Nöth, Angew. Chem., Int. Ed. Engl., 1985, 24, 878–879 CrossRef;
(b) K. Burgess, W. A. van der Donk, S. A. Westcott, T. B. Marder, R. T. Baker and J. C. Calabrese, J. Am. Chem. Soc., 1992, 114, 9350–9359 CrossRef CAS;
(c) D. A. Evans, G. C. Fu and A. H. Hoveyda, J. Am. Chem. Soc., 1992, 114, 6671–6679 CrossRef CAS;
(d) D. R. Edwards, C. M. Crudden and K. Yam, Adv. Synth. Catal., 2005, 347, 50–54 CrossRef CAS;
(e)
G. C. Fu, in Transition Metal-Catalyzed Hydroboration of Olefins, Transition Metals for Organic Synthesis: Building Blocks and Fine Chemicals, ed. M. Beller and C. Bolm, Wiley-VCH, Weinheim, 2nd edn, 2008, pp. 193–198 Search PubMed;
(f) A. Whiting and J.-B. Chen, Synthesis, 2018, 50, 3843–3861 CrossRef;
(g) J. D. Hewes, C. W. Kreimendahl, T. B. Marder and M. F. Hawthorne, J. Am. Chem. Soc., 1984, 106, 5757–5759 CrossRef CAS;
(h) A. D. Bage, K. Nicholson, T. A. Hunt, T. Langer and S. P. Thomas, ACS Catal., 2020, 10, 13479–13486 CrossRef CAS.
-
(a) I. A. Mkhalid, J. H. Barnard, T. B. Marder, J. M. Murphy and J. F. Hartwig, Chem. Rev., 2010, 110, 890–931 CrossRef CAS;
(b) J. F. Hartwig, Acc. Chem. Res., 2012, 45, 864–873 CrossRef CAS;
(c) J. F. Hartwig, Chem. Soc. Rev., 2011, 40, 1992–2002 RSC;
(d) J. F. Hartwig, J. Am. Chem. Soc., 2016, 138, 2–24 CrossRef CAS;
(e) T. Ishiyama and N. Miyaura, J. Organomet. Chem., 2003, 680, 3–11 CrossRef CAS;
(f) J. Kalepu, Molecules, 2019, 24, 830 CrossRef;
(g) A. Ros, R. Fernandez and J. M. Lassaletta, Chem. Soc. Rev., 2014, 43, 3229–3243 RSC;
(h) H. Chen, S. Schlecht, T. C. Semple and J. F. Hartwig, Science, 2000, 287, 1995–1997 CrossRef CAS PubMed;
(i) H. Y. Chen and J. F. Hartwig, Angew. Chem., Int. Ed., 1999, 38, 3391–3393 CrossRef CAS.
-
(a) Y. G. Lawson, M. J. G. Lesley, N. C. Norman, C. R. Rice and T. B. Marder, Chem. Commun., 1997, 2051–2052 RSC;
(b) K. Takahashi, T. Ishiyama and N. Miyaura, Chem. Lett., 2000, 29, 982–983 CrossRef;
(c) H. Ito, H. Yamanaka, J. Tateiwa and A. Hosomi, Tetrahedron Lett., 2000, 41, 6821–6825 CrossRef CAS;
(d) N. J. Bell, A. J. Cox, N. R. Cameron, J. S. O. Evans, T. B. Marder, M. A. Duin, C. J. Elsevier, X. Baucherel, A. A. D. Tulloch and R. P. Tooze, Chem. Commun., 2004, 1854–1855 RSC;
(e) L. Dang, Z. Lin and T. B. Marder, Organometallics, 2008, 27, 4443–4454 CrossRef CAS;
(f) H. Wu, S. Radomkit, J. M. O'Brien and A. H. Hoveyda, J. Am. Chem. Soc., 2012, 134, 8277–8285 CrossRef CAS;
(g) E. Hartmann, D. J. Vyas and M. Oestreich, Chem. Commun., 2011, 47, 7917–7932 RSC;
(h) Y. Sasaki, Y. Horita, C. Zhong, M. Sawamura and H. Ito, Angew. Chem., Int. Ed., 2011, 50, 2778–2782 CrossRef CAS;
(i) B. Liu, M. Gao, L. Dang, H. Zhao, T. B. Marder and Z. Lin, Organometallics, 2012, 31, 3410–3425 CrossRef CAS;
(j) J. Cid, H. Gulyás, J. J. Carbó and E. Fernández, Chem. Soc. Rev., 2012, 41, 3558–3570 RSC;
(k) V. Lillo, A. Bonet and E. Fernández, Dalton Trans., 2009, 2899–2908 RSC;
(l) B. S. L. Collins, C. M. Wilson, E. L. Myers and V. K. Aggarwal, Angew. Chem., Int. Ed., 2017, 56, 11700–11733 CrossRef CAS PubMed;
(m) F. Beltran, E. Bergamaschi, I. Funes-Ardoiz and C. J. Teskey, Angew. Chem., Int. Ed., 2020, 59, 21176–21182 CrossRef CAS;
(n) C. C. Chong and R. Kinjo, ACS Catal., 2015, 5(6), 3238–3259 CrossRef CAS;
(o) J.-B. Xie, S. Lin, J. Luo, J. Wu, T. R. Winna and G. Li, Org. Chem. Front., 2015, 2, 42–46 RSC;
(p) Y. Yamamoto, T. Nishikata and N. Miyaura, Pure Appl. Chem., 2008, 80, 807–817 CrossRef CAS.
- K. Kubota, H. Iwamoto and H. Ito, Org. Biomol. Chem., 2017, 15, 285–300 RSC.
-
(a) C.-T. Yang, Z.-Q. Zhang, H. Tajuddin, C.-C. Wu, J. Liang, J.-H. Liu, Y. Fu, P. G. Steel, T. B. Marder and L. Liu, Angew. Chem., Int. Ed., 2012, 51, 528–532 CrossRef CAS;
(b) H. Ito and K. Kubota, Org. Lett., 2012, 14, 890–893 CrossRef CAS PubMed;
(c) K. Kubota, E. Yamamoto and H. Ito, J. Am. Chem. Soc., 2013, 135, 2635–2640 CrossRef CAS PubMed;
(d) J. H. Kim and Y. K. Chung, RSC Adv., 2014, 4, 39755–39758 RSC;
(e) Z.-Q. Zhang, C.-T. Yang, L.-J. Liang, B. Xiao, X. Lu, J.-H. Liu, Y.-Y. Sun, T. B. Marder and Y. Fu, Org. Lett., 2014, 16, 6342–6345 CrossRef CAS;
(f) H. Iwamoto, K. Kubota, E. Yamamoto and H. Ito, Chem. Commun., 2015, 51, 9655–9658 RSC;
(g) X.-F. Zhou, Y.-D. Wu, J.-J. Dai, Y.-J. Li, Y. Huang and H.-J. Xu, RSC Adv., 2015, 5, 46672–46676 RSC;
(h) S. K. Bose, S. Brand, H. O. Omoregie, M. Haehnel, J. Maier, G. Bringmann and T. B. Marder, ACS Catal., 2016, 6, 8332–8335 CrossRef CAS;
(i) A. Nitelet, D. Thevenet, B. Schiavi, C. Hardouin, J. Fournier, R. Tamion, X. Pannecoucke, P. Jubault and T. Poisson, Chem. – Eur. J., 2019, 25, 3262–3266 CAS.
-
(a) A. S. Dudnik and G. C. Fu, J. Am. Chem. Soc., 2012, 134, 10693–10697 CrossRef CAS;
(b) M. S. Cheung, F. K. Sheong, T. B. Marder and Z. Lin, Chem. – Eur. J., 2015, 21, 7480–7488 CrossRef CAS;
(c) J. Yi, J. H. Liu, J. Liang, J. J. Dai, C. T. Yang, Y. Fu and L. Liu, Adv. Synth. Catal., 2012, 354, 1685–1691 CrossRef CAS.
-
(a) A. Joshi-Pangu, X. Ma, M. Diane, S. Iqbal, R. J. Kribs, R. Huang, C.-Y. Wang and M. R. Biscoe, J. Org. Chem., 2012, 77, 6629–6633 CrossRef CAS;
(b) Z.-F. Jiao, Y.-M. Tian, X.-N. Guo, U. Radius, H. Braunschweig, T. B. Marder and X.-Y. Guo, J. Catal., 2021, 395, 258–265 CrossRef CAS.
-
(a) R. B. Bedford, P. B. Brenner, E. Carter, T. Gallagher, D. M. Murphy and D. R. Pye, Organometallics, 2014, 33, 5940–5943 CrossRef CAS;
(b) T. C. Atack, R. M. Lecker and S. P. Cook, J. Am. Chem. Soc., 2014, 136, 9521–9523 CrossRef CAS;
(c) S. Siddiqui, R. Bhawar and K. Geetharani, J. Org. Chem., 2021, 86, 1948–1954 CrossRef CAS.
- S. K. Bose, K. Fucke, L. Liu, P. G. Steel and T. B. Marder, Angew. Chem., Int. Ed., 2014, 53, 1799–1803 CrossRef CAS PubMed.
- T.-J. Gong, Y.-Y. Jiang and Y. Fu, Chin. Chem. Lett., 2014, 25, 397–400 CrossRef CAS.
- T. C. Atack and S. P. Cook, J. Am. Chem. Soc., 2016, 138, 6139–6142 CrossRef CAS PubMed.
- X. Lu, Z.-Q. Zhang, L. Yu, B. Zhang, B. Wang, T.-J. Gong, C.-L. Tian, B. Xiao and Y. Fu, Chin. J. Chem., 2019, 37, 11–18 CrossRef CAS.
- X. Wang, P. Cui, C. Xia and L. Wu, Angew. Chem., Int. Ed., 2021, 60, 12298–12303 CrossRef CAS.
-
(a) G. Stavber and Z. Casar, ChemCatChem, 2014, 6, 2162–2174 CrossRef CAS;
(b) D. Hemming, R. Fritzemeier, S. A. Westcott, W. L. Santos and P. G. Steel, Chem. Soc. Rev., 2018, 47, 7477–7494 RSC;
(c) J. Yun, Asian J. Org. Chem., 2013, 2, 1016–1025 CrossRef CAS;
(d) T. Fujihara, K. Semba, J. Terao and Y. Tsuji, Catal. Sci. Technol., 2014, 4, 1699–1709 RSC.
- J. Cui, H. Wang, J. Song, X. Chi, L. Meng, Q. Liu, D. Zhang, Y. Donga and H. Liu, Org. Biomol. Chem., 2017, 15, 8508–8512 RSC.
-
(a) X. Lou, Z. Q. Zhang, J. H. Liu and X. Y. Lu, Chem. Lett., 2016, 45, 200–202 CrossRef CAS;
(b) H. Yoshida, Y. Takemoto, S. Kamio, I. Osaka and K. Takaki, Org. Chem. Front., 2017, 4, 1215–1219 RSC.
- H. Iwamoto, S. Akiyama, K. Hayama and H. Ito, Org. Lett., 2017, 19, 2614–2617 CrossRef CAS PubMed.
-
(a) D. Mazzarella, G. Magagnano, B. S. Chaput and P. Melchiorre, ACS Catal., 2019, 9, 5876–5880 CrossRef CAS;
(b) Q. Liu, J. Hong, B. Sun, G. Bai, F. Li, G. Liu, Y. Yang and F. Mo, Org. Lett., 2019, 21, 6597–6602 CrossRef CAS PubMed.
-
(a) H. Y. Chen and J. F. Hartwig, Angew. Chem., Int. Ed., 1999, 38, 3391–3393 CrossRef CAS;
(b) J. F. Hartwig, K. S. Cook, M. Hapke, C. D. Incarvito, Y. Fan, C. E. Webster and M. B. Hall, J. Am. Chem. Soc., 2005, 127, 2538–2552 CrossRef CAS;
(c) A. Yoshimura, Y. Takamachi, L. B. Han and A. Ogawa, Chem. – Eur. J., 2015, 21, 13930–13933 CrossRef CAS;
(d) K. Chen, S. Zhang, P. He and P. F. Li, Chem. Sci., 2016, 7, 3676–3680 RSC;
(e) A. M. Mfuh, V. T. Nguyen, B. Chhetri, J. E. Burch, J. D. Doyle, V. N. Nesterov, H. D. Arman and O. V. Larionov, J. Am. Chem. Soc., 2016, 138, 8408–8411 CrossRef CAS PubMed;
(f) A. M. Mfuh, B. D. Schneider, W. Cruces and O. V. Larionov, Nat. Protoc., 2017, 12, 604–610 CrossRef CAS;
(g) D. W. Hu, L. H. Wang and P. F. Li, Org. Lett., 2017, 19, 2770–2773 CrossRef CAS;
(h) S. F. Jin and O. V. Larionov, Chem, 2018, 4, 1205–1207 CrossRef CAS;
(i) H. Cao, H. Jiang, H. Feng, J. M. C. Kwan, X. Liu and J. Wu, J. Am. Chem. Soc., 2018, 140, 16360–16367 CrossRef CAS PubMed;
(j) Y. M. Tian, X. N. Guo, M. W. Kuntze-Fechner, I. Krummenacher, H. Braunschweig, U. Radius, A. Steffen and T. B. Marder, J. Am. Chem. Soc., 2018, 140, 17612–17623 CrossRef CAS PubMed;
(k) V. D. Nguyen, V. T. Nguyen, S. Jin, H. T. Dang and O. V. Larionov, Tetrahedron, 2019, 75, 584–602 CrossRef CAS PubMed;
(l) Z. F. Jiao, J. X. Zhao, X. N. Guo and X. Y. Guo, Chin. J. Catal., 2020, 41, 357–363 CrossRef CAS;
(m) A. Fawcett, J. Pradeilles, Y. Wang, T. Mutsuga, E. L. Myers and V. K. Aggarwal, Science, 2017, 357, 283–286 CrossRef CAS PubMed;
(n) J. Wu, L. He, A. Noble and V. K. Aggarwal, J. Am. Chem. Soc., 2018, 140, 10700–10704 CrossRef CAS PubMed;
(o) Y. Cheng, C. Mgck-Lichtenfeld and A. Studer, J. Am. Chem. Soc., 2018, 140, 6221–6225 CrossRef CAS;
(p) Y. Cheng, C. Mück-Lichtenfeld and A. Studer, Angew. Chem., Int. Ed., 2018, 57, 16832–16836 CrossRef CAS;
(q) F. W. Friese and A. Studer, Angew. Chem., Int. Ed., 2019, 58, 9561–9564 CrossRef CAS;
(r) J. Hu, G. Wang, S. Li and Z. Shi, Angew. Chem., Int. Ed., 2018, 57, 15227–15231 CrossRef CAS PubMed;
(s) F. Sandfort, F. Strieth-Kalthoff, F. Klauck, M. James and F. Glorius, Chem. – Eur. J., 2018, 24, 17210–17214 CrossRef CAS PubMed;
(t) L. Zhang, Z. Q. Wu and L. Jiao, Angew. Chem., Int. Ed., 2020, 59, 2095–2099 CrossRef CAS;
(u) C. Wang, L. Zhou, K. Yang, F. Zhang and Q. Song, Chin. J. Chem., 2021, 39, 1825–1830 CrossRef CAS;
(v) B. Wang, P. Peng, W. Ma, Z. Liu, C. Huang, Y. Cao, P. Hu, X. Xi and Q. Lu, J. Am. Chem. Soc., 2021, 143, 12985–12991 CrossRef CAS PubMed.
-
(a) P. K. Verma, M. L. Shegavi, S. K. Bose and K. Geetharani, Org. Biomol. Chem., 2018, 16, 857–873 RSC;
(b)
K. Geetharani and S. K. Bose, in Science of Synthesis: Advances in Organoboron Chemistry towards Organic Synthesis, ed. E. Fernández, Thieme, Stuttgart, 2019, pp. 335–354 Search PubMed.
- A. Bej, D. Srimani and A. Sarkar, Green Chem., 2012, 1, 661–667 RSC.
- M. Franco, R. Sainz, A. M. Lamsabhi, C. Díaz, M. Tortosa and M. B. Cid, Catal. Sci. Technol., 2021, 11, 3501–3513 RSC.
-
(a) S. Martínez-Méndez, Y. Henríquez, O. Domínguez, L. D'Ornelas and H. Krentzien, J. Mol. Catal. A: Chem., 2006, 252, 226–234 CrossRef;
(b) S. Bhandari, A. Roy, M. S. Ali, T. K. Mallick and S. Sundaram, Sci. Rep., 2021, 11, 23388 CrossRef CAS;
(c)
O. A. Ferretti and M. L. Casella, Controlled preparation of heterogeneous catalysts for chemo- and enantioselective hydrogenation reaction, Modern Surface Organometallic Chemistry, Wiley-VCH Verlag GmbH & Co. KGaA, 2020, pp. 239–291 Search PubMed.
-
(a) L. F. Mabena, S. S. Ray, S. D. Mhlanga and N. J. Coville, Appl. Nanosci., 2011, 1, 67–77 CrossRef CAS;
(b)
P. Serp and J. L. Figueiredo, Carbon Materials for Catalysis, John Wiley & Sons, 2009 Search PubMed.
- R. Arrigo, M. E. Schuster, Z. Xie, Y. Yi, G. Wowsnick, L. L. Sun, K. E. Hermann, M. Friedrich, P. Kast, M. Havecker, A. K. Gericke and R. Schlogl, ACS Catal., 2015, 5, 2740–2753 CrossRef CAS.
-
(a) M. L. Shegavi, A. Baishya, K. Geetharani and S. K. Bose, Org. Chem. Front., 2018, 5, 3520–3525 RSC;
(b) R. Bhawar, K. S. Patil and S. K. Bose, New J. Chem., 2021, 45, 15028–15034 RSC.
- M. L. Shegavi, A. Agarwal and S. K. Bose, Green Chem., 2020, 22, 2799–2803 RSC.
- Z. Zhuang, S. A. Giles, J. Zheng, G. R. Jenness, S. Caratzoulas, D. G. Vlachos and Y. Yan, Nat. Commun., 2016, 7, 10141 CrossRef CAS.
-
(a) K. Endo, M. Hirokami and T. Shibata, Synlett, 2009, 8, 1331–1335 CrossRef;
(b) S. Xu, X. Shangguan, H. Li, Y. Zhang and J. Wang, J. Org. Chem., 2015, 80, 7779–7784 CrossRef CAS;
(c) W. N. Palmer, J. V. Obligacion, I. Pappas and P. J. Chirik, J. Am. Chem. Soc., 2016, 138, 766–769 CrossRef CAS;
(d) L. Zhang and Z. Huang, J. Am. Chem. Soc., 2015, 137, 15600–15603 CrossRef CAS.
-
(a) Y. Shi and A. H. Hoveyda, Angew. Chem., Int. Ed., 2016, 55, 3455–3458 CrossRef CAS PubMed;
(b) J. Kim, S. Park, J. Park and S. H. Cho, Angew. Chem., Int. Ed., 2016, 55, 1498–1501 CrossRef CAS PubMed;
(c) M. V. Joannou, B. S. Moyer and S. J. Meek, J. Am. Chem. Soc., 2015, 137, 6176–6179 CrossRef CAS;
(d) D. S. Matteson and R. J. Moody, Organometallics, 1982, 1, 20–28 CrossRef CAS;
(e) A. S. Batsanov, J. A. Cabeza, M. G. Crestani, M. R. Fructos, P. García-Álvarez, M. Gille, Z. Lin and T. B. Marder, Angew. Chem., Int. Ed., 2016, 55, 4707–4710 CrossRef CAS PubMed;
(f) A. K. Cook, S. D. Schimler, A. J. Matzger and M. S. Sanford, Science, 2016, 351, 1421–1424 CrossRef CAS;
(g) K. T. Smith, S. Berritt, M. González-Moreiras, S. Ahn, M. R. Smith III, M.-H. Baik and D. J. Mindiola, Science, 2016, 351, 1424–1427 CrossRef CAS PubMed;
(h) X. Liu, W. Ming, Y. Zhang, A. Friedrich and T. B. Marder, Angew. Chem., Int. Ed., 2020, 59, 304–309 CrossRef CAS;
(i) X. Liu, W. Ming, Y. Zhang, A. Friedrich and T. B. Marder, Angew. Chem., Int. Ed., 2019, 58, 18923–18927 CrossRef CAS PubMed.
-
(a) P. Nguyen, G. Lesley, N. J. Taylor, T. B. Marder, N. L. Picket, W. Clegg, M. R. J. Elsegood and N. C. Norman, Inorg. Chem., 1994, 33, 4623–4624 CrossRef CAS;
(b) F. J. Lawlor, N. C. Norman, N. L. Pickett, E. G. Robins, P. Nguyen, G. Lesley, T. B. Marder, J. A. Ashmore and J. C. Green, Inorg. Chem., 1998, 37, 5282–5288 CrossRef CAS.
- C. J. Hawker, G. G. Barclay, A. Orellana, J. Dao and W. Devonport, Macromolecules, 1996, 29, 5245–5254 CrossRef CAS.
-
(a) S. Kapse, S. Janwari, U. V. Waghmare and R. Thapa, Appl. Catal., B, 2021, 286, 119866 CrossRef CAS;
(b) S. Sinthika, U. V. Waghmare and R. Thapa, Small, 2018, 14, 1703609 CrossRef.
- S. Sinthika, S. M. Pushpa, E. R. Nimma, D. S. Gavali and R. Thapa, Int. J. Energy Res., 2022, 46, 4405–4416 CrossRef.
- For reviews on precious-metal-catalyzed hydroboration reactions, see:
(a) K. Burgess and M. J. Ohlmeyer, Chem. Rev., 1991, 91, 1179–1191 CrossRef CAS;
(b) I. Beletskaya and A. Pelter, Tetrahedron, 1997, 53, 4957–5026 CrossRef CAS;
(c) C. M. Crudden and D. Edwards, Eur. J. Org. Chem., 2003, 4695–4712 CrossRef CAS;
(d) A.-M. Carroll, T. P. O'Sullivan and P. J. Guiry, Adv. Synth. Catal., 2005, 347, 609–631 CrossRef CAS;
(e) C. M. Vogels and S. A. Westcott, Curr. Org. Chem., 2005, 9, 687–699 CrossRef CAS.
- For reviews on first-row-transition-metal-catalyzed hydroboration reactions, see:
(a) J. A. Schiffner, K. Müther and M. Oestreich, Angew. Chem., Int. Ed., 2010, 49, 1194–1196 (
Angew. Chem.
, 2010
, 122
, 1214–1216
) CrossRef CAS;
(b) J. A. Bull, Angew. Chem., Int. Ed., 2012, 51, 8930–8932 (
Angew. Chem.
, 2012
, 124
, 9060–9062
) CrossRef CAS PubMed;
(c) W. Fan, L. Li and G. Zhang, J. Org. Chem., 2019, 84, 5987–5996 CrossRef CAS;
(d) J. V. Obligacion and P. J. Chirik, Nat. Rev. Chem., 2018, 2, 15–34 CrossRef CAS PubMed.
-
(a) S. Furukawa, M. Ieda and K.-I. Shimizu, ACS Catal., 2019, 9, 5096–5103 CrossRef CAS;
(b) R. Cano, D. J. Ramón and M. Yus, J. Org. Chem., 2010, 75, 3458–3460 CrossRef CAS;
(c) G. Zhang, J. Wu, S. Li, S. Cass and S. Zheng, Org. Lett., 2018, 20, 7893–7897 CrossRef CAS PubMed;
(d) Y. Zhu, S. H. Agnes Jang, Y. H. Tham, O. B. Algin, J. A. Maguire and N. S. Hosmane, Organometallics, 2012, 31, 2589–2596 CrossRef CAS;
(e) S. Hong, M. Liu, W. Zhang, Q. Zeng and W. Deng, Tetrahedron Lett., 2015, 56, 2297–2301 CrossRef CAS.
-
(a) B. Mohan and K. H. Park, Appl. Catal., A, 2016, 519, 78–84 CrossRef CAS;
(b) S. Thoka, M. Madasu, C.-F. Hsia, S.-Y. Liu and M. H. Huang, Chem. – Asian J., 2017, 12, 2318–2322 CrossRef CAS;
(c) J. Zhao, Z. Niu, H. Fu and Y. Li, Chem. Commun., 2014, 50, 2058–2060 RSC;
(d) A. Grirrane, A. Corma and H. Garcia, Chem. – Eur. J., 2011, 17, 2467–2478 CrossRef CAS PubMed;
(e) C. Zhanga, M. Zhoub, S. Liub, B. Wanga, Z. Maoa, H. Xua, Y. Zhonga, L. Zhanga, B. Xub and X. Sui, Carbohydr. Polym., 2018, 191, 17–24 CrossRef;
(f) X. Zeng, C. Gong, H. Guo, H. Xu, J. Zhanga and J. Xie, New J. Chem., 2018, 42, 17346–17350 RSC.
- M. L. Shegavi, S. Saini, R. Bhawar, M. D. Vishwantha and S. K. Bose, Adv. Synth. Catal., 2021, 363, 2408–2416 CrossRef CAS.
-
(a) M. A. Beenen, C. An and J. A. Ellman, J. Am. Chem. Soc., 2008, 130, 6910–6911 CrossRef CAS;
(b) C. Kleeberg, L. Dang, Z. Lin and T. B. Marder, Angew. Chem., Int. Ed., 2009, 48, 5350–5354 CrossRef CAS PubMed;
(c) R. D. Grigg, R. Van Hoveln and J. M. Schomaker, J. Am. Chem. Soc., 2012, 134, 16131–16134 CrossRef CAS PubMed;
(d) F. Labre, Y. Gimbert, P. Bannwarth, S. Olivero, E. Duñach and P. Y. Chavant, Org. Lett., 2014, 16, 2366–2369 CrossRef CAS;
(e) S. Ando, H. Matsunaga and T. Ishizuka, J. Org. Chem., 2015, 80, 9671–9681 CrossRef CAS PubMed;
(f) L. Amenós, L. Trulli, L. Nóvoa, A. Parra and M. Tortosa, Angew. Chem., 2019, 131, 3220–3224 CrossRef.
|
This journal is © The Royal Society of Chemistry 2023 |
Click here to see how this site uses Cookies. View our privacy policy here.