Highly sensitive g-C3N4 nanosheets as a potential candidate for the effective detection of NO2 gas via langasite-based surface acoustic wave gas sensor†
Received
13th October 2021
, Accepted 17th November 2021
First published on 22nd November 2021
Abstract
In view of the fact, the poor stability and inadequate chemical properties of conductive polymers inhibit their use in gas sensor applications. Moreover, the elegant two-dimensional (2D) polymeric graphitic carbon nitride (g-C3N4) has attracted great attention for room-temperature (RT) gas sensing applications due to its intrinsic porous structure and lone pair electrons on nitrogen atoms. Herein, we report surface acoustic wave (SAW) NO2 gas sensors using 2D g-C3N4 nanosheets deposited on langasite (LGS) SAW device. Furthermore, the thickness effect on gas sensing performances was manifested and it was noticed that 220 nm thickness of g-C3N4-coated LGS SAW sensors showed better sensing performances. The g-C3N4/LGS SAW sensor showed a significant negative differential frequency shift (Δf) of ∼3.1 kHz at room temperature (RT ∼ 27 °C) for 100 ppm of NO2 gas with a quick response/recovery time (42/22 s). Furthermore, our experimental results indicated that the effect of temperature remarkably influences NO2 sensing responses, which escalated from ∼3.1 kHz to ∼23.3 kHz in the temperature range of 27 °C to 200 °C for 100 ppm of NO2. Moreover, the device showed immense sensitivity towards NO2 (100 ppm) under various relative humidity (RH) conditions (20–80%) at RT. Besides, the g-C3N4/LGS SAW sensor showed low detection limit (∼158 ppb), excellent long-term stability, high sensitivity and selectivity to NO2 gas, which could be ascribed to the enhancement in mass loading effect resulting from the absorption of NO2 gas molecules. Finally, using resistive gas sensor, we deliberately discuss the underlying gas sensing mechanism associated with the 2D g-C3N4 nanosheet–deposited LGS SAW device.
1. Introduction
In recent years, the development of smart gas sensors with low cost and high accuracy towards the detection of toxic gas analytes has become much important for environmental protection and human safety.1 A broad class of various conventional gas sensing technologies such as chemiresistive type, optical sensors and bio sensors etc., have been widely used in different gas sensing applications.2 Nevertheless, there are some impediments such as high cost of fabrication, reproducibility and high thermal energy requirements associated with the conventional gas sensing technologies, which are the bottlenecks for their practical applicability.1,2 In order to overcome these ongoing challenges, recently, the research community has probed to the surface acoustic wave (SAW) sensor technology, which has been found as promising gas sensing application due to the ease of fabrication, wireless and portable nature, small size, low detection limit, etc., as compared to the other gas sensing technologies.1–3 The fundamental principle of the SAW gas sensor is mainly based on the attenuation of the acoustic wave propagation caused by the sorption of gas molecules via a sorbent, i.e., a chemical interface coating on a piezoelectric device.3–5 Notorious piezoelectric crystals such as, quartz, lithium niobate, zinc oxide and langasite are well documented for SAW device applications.6–8 Among them, langasite (LGS, La3Ga5SiO14) is a new class of piezoelectric material and has gained great interest because of its stable frequency, high temperature stability (above 1400 °C) and high Q behaviour.9,10 In addition, the excellent electromechanical coupling factors of the LGS material make it a suitable candidate for the SAW device applications.11 However, the poor stability, low selectivity and inadequate sensitivity of the pristine LGS SAW devices are the current ongoing challenges, which are usually found in gas sensor applications, especially while operating at room temperature (RT).12–14 With this in mind, the integration of active sensing materials over the cavity area of the SAW device is an essential component, which makes it more selective to chemical interactions (adsorption/desorption) with analyte gas molecules for high-performance gas sensing. It is well known that polymers, especially conductive polymeric thin films, are the finest chemical interfaces to detect gas molecules, owing to their fast diffusion, reversibility and high sensitivity.15,16 Moreover, the chemical interface is particularly sensitive to the gas to be identified, and the gas molecules adsorbed onto the chemical interface led to a change in the electrical and mechanical coupling factors such as mass loading, elastic and conductivity, which can alter the wave velocity of the designed SAW device.17,18
In this globalized world, over usage of fossil fuels and automobiles results in the emission of highly toxic and harmful gases such as carbon monoxide, sulphur dioxide, ammonia, hydrogen sulphide, and nitrogen dioxide.19,20 The detection of these harmful gases at the early stage has received widespread attention in various fields such as environmental remediation, pollution monitoring, industrial manufacturing, and medical diagnostics.21,22 Nitrogen dioxide (NO2) is one of the notorious pungent toxic air pollutants, which is usually emitted from the exhaust of manufacturing industries and motor vehicles, causing deterioration of the environment, photochemical smog and acid rains.23,24 Besides environmental pollution, a few parts per million concentration of the NO2 gas shows adverse effects on human, animal and plant life. In fact, according to the Occupational Safety and Health Organization (OSHA) air quality standards, prolonged exposure to the NO2 gas (3 ppm) can cause detrimental health problems such as respiratory infections, asthma, nausea, and pulmonary diseases.25,26 Considering the above-mentioned facts, it is very essential to monitor and accurate detection of NO2 gas with great response, immense selectivity and the lowest possible detection limits (DL).25,27 One among the broad class of carbon materials, two-dimensional (2D) polymer-based graphitic carbon nitride (g-C3N4) is an emerging frontrunner material, which has been widely reported in various applications due to its peculiar properties such as ordered units of tri-s-triazine structural rings bonded together with the nitrogen atom in the layered structure that would provide high surface area.28,29 In addition, the excellent physiochemical properties of 2D g-C3N4 such as good biocompatibility, low density, and high thermal and chemical stability have made it a motivated research hotspot in diverse fields such as gas sensing, energy storage, catalysis and optoelectronics.30,31 More importantly, the electrical, chemical and structural (nano-ribbons, nanosheets, quantum dots, etc.) properties of g-C3N4 can be easily tuned by ultrasonic dispersion.32–34 In particular, due to its lone pair electrons on nitrogen sites including electron delocalization, π–π* conjugation, amine functional groups and inherent porous structure, 2D g-C3N4 can indisputably provide a large surface area and abundant active sites that would effectively improve the absorption of gas molecules.33,34 Due to its low cost and aforementioned merits, the research community pay much attention to the 2D g-C3N4 nanostructures, which have been extensively employed for the detection of various toxic gases at room temperature and elevated temperatures.35 However, to the best of our knowledge, utilizing 2D g-C3N4 nanosheets as chemical interfaces on piezoelectric LGS SAW sensors for NO2 gas detection is still rare and limited.
In this scenario, we extensively demonstrated the tuning of the physicochemical and structural properties of 2D g-C3N4 nanosheets using different spectroscopic studies by varying sonication time for the first time to the SAW-based gas sensing applications. Next, the high response NO2 gas sensing performances of the optimized g-C3N4 nanosheets using langasite SAW technology has been manifested comprehensively. We also investigated the effect of g-C3N4 nanosheet thickness on NO2 gas sensing properties. The g-C3N4/LGS SAW NO2 gas sensing characteristics were demonstrated at RT and elevated temperatures under different NO2 gas concentrations (5–100 ppm). Further, humidity and selectivity tests were carried out at RT to study their effects. The test results indicated that the proposed g-C3N4/LGS SAW sensor exhibits excellent sensitivity, selectivity, repeatability, and response/recovery times towards NO2 gas, which were mainly ascribed to the high mass loading effect. The gas sensing characteristics and mechanism of the as-prepared g-C3N4/LGS SAW are discussed and correlated with the g-C3N4 nanosheets thin-film resistive-based sensor.
2. Experimental details
2.1 Device fabrication and experimental setup
The SAW sensor device was designed and fabricated using a LGS substrate. Using the AutoCAD software, a two-port SAW resonator pattern was designed with specifications of input and output interdigital transducers (IDTs) with 100 electrode pairs followed by the 150 electrodes of reflector grating on either side of the IDTs. The electrodes spacing (d), aperture height and the active resonating cavity (sensing area) between the input and output IDTs were set to be 4 μm, 800 μm and 3 mm. Prior to the fabrication of the LGS SAW sensor, LGS substrates were cleaned with acetone, methanol, and isopropyl alcohol for 10 min at each stage under room temperature and finally rinsed in water. Then, the LGS substrates were dried under the flow of N2 gas. Conventional photolithography was employed to make the IDT patterns on the LGS substrate. A negative photoresist (PR) (DNR-L300-30) was spin-coated on the LGS substrate at a speed of 5000 rpm for 30 s, thereafter a PR-coated substrate was subjected to soft baking at 90 °C for 7 min and then exposed to the UV light (200 W) for 5 s under the designed photomask. Right after this process, the sample was moved to hard baking maintained at 110 °C for 90 s. Then, the SAW IDT patterns were developed by rinsing the LGS sample in an AZ-300 MIF developer for 40 s. Afterwards, the metal electrodes Au/Ti (50/10 nm) were deposited on the developed IDT patterns of the SAW sample using an e-beam lithography technique, and finally, dipped into acetone to lift-off the unwanted coating.
2.2 Gas sensing measurement set up
The NO2 gas sensing system includes a network analyser (HP, 8752C) and a Keithely-2400, which were connected to a LabVIEW program, as displayed in Fig. S1 (ESI†). The g-C3N4/LGS SAW device was placed on a sample holder, internally connected to a thermostat inside the metallic chamber. The temperature of the SAW device can be increased using a temperature controller. The gas concentration was determined using the well-noted equation C (ppm) = Cstd (ppm) × f/(f + F), where the terms Cstd (ppm), f and F represent the concentration of the analyte gas inside the gas cylinder (1000 ppm), which was balanced with nitrogen, flow rates of the target and carrier gases respectively. Humidity was created intentionally by mixing the dry air with DI water contained in a glass bubbler jar, and the humidity inside the chamber was monitored using a hydrograph. For the room-temperature gas sensing measurement, temperature and humidity inside the test gas chamber were maintained at 27 ± 2 °C and ∼3.2% respectively.
2.3 g-C3N4 synthesis and thin film deposition on LGS substrates
The two-dimensional g-C3N4 nanosheets were prepared using the following procedure: the bulk g-C3N4 powder was synthesized by a one-step thermal polymerization reaction of melamine (Sigma Aldrich, South Korea).25 In brief, 25 g of melamine was heated at 600 °C for 2 hours in a muffle furnace with a ramping rate of 3 °C per min in a semi-closed alumina crucible. After cooling down the furnace to RT, the yellowish solid product (bulk g-C3N4) was collected from the alumina crucible. The obtained solid g-C3N4 was grinded using a mortar to make a fine powder. The detailed description of the g-C3N4 nanosheet synthesis is illustrated in Fig. 1(a–c). Further, the g-C3N4 nanosheets were exfoliated from the bulk g-C3N4 powder (0.5 g), which was dispersed in 100 mL of deionized water in a glass beaker, and then the solution was subjected to ultrasonication for 3, 6, 12 and 18 hours each in different beakers at RT. Each sample of g-C3N4 nanosheets was drop-casted onto the cavity sensing area of the LGS SAW device. Finally, the devices were annealed at 60 °C for 20 min to obtain the g-C3N4 film. Among all, a 12 hours ultrasonicated mixture of g-C3N4 nanosheets showed magnificent sensing response towards NO2 gas (100 ppm) as compared to the other samples sonicated at 3, 6 and 18 h, as shown in Fig. S2 (ESI†). Moreover, for a detailed and comprehensive explanation about the better gas sensing performances of 12 hours sonicated g-C3N4 nanosheets among other samples (3, 6 and 12 h), FTIR, BET and XPS analyses were performed, which can be available in the ESI† (Fig. S3–S5). Our experimental analysis divulged that the 12 h sonicated sample showed excellent physiochemical and structural properties with a high surface area. Therefore, based on these experimental analyses, the 12 hours sonicated g-C3N4 nanosheet sample was considered and utilized as an optimized condition for the entire gas sensing conditions and the sample was named g-C3N4 nanosheets, which were simply denoted as g-C3N4/LGS SAW in the whole manuscript. Further, the 12 hours sonicated g-C3N4 sample's optimized thickness was estimated to be 220 nm, and it was utilized for the entire gas sensing experiment.
 |
| Fig. 1 Detailed schematic representation of the synthesis of g-C3N4 nanosheets (NS) and their use for gas sensing: (a) melamine, (b) g-C3N4 powder after calcination, (c) g-C3N4 NS using ultrasonication, (d) fabricated LGS SAW device deposited with g-C3N4 NS, (e) network analyser connected to the gas sensing chamber, and (f) LabVIEW programmed PC to monitor the gas sensing properties. | |
2.4 Characterization
X-Ray diffraction (XRD) patterns of the as-synthesized material were acquired using a X-ray diffractometer (HR-XRD: Bruker-D8 Advance). The structural morphology of the product was studied using a scanning electron microscope (SEM-TOPCON DS-130) and a high-resolution transmission electron microscope (HITACHI H-7650 and JEOL JEM-2010). The optical properties of the sample were studied using a UV-visible spectrometer (UV-Vis-LAMDA-265, PerkinElmer). The functional groups, surface chemistry and the surface area of the sample were investigated using a Fourier-transform infrared (FTIR) spectrometer (NICOLET is20), an X-ray photoelectron spectrometer (XPS, AXIS-NOVA, Kratos), Brunauer–Emmett–Teller (BET) analyser, and N2 adsorption/desorption isotherms (Micromeritics: ASAD2420).
3. Results and discussion
Fig. 2(a) depicts the XRD spectrum of the g-C3N4 nanosheets. The spectrum shows the two obvious characteristic diffraction peaks positioned at around 13.1° and 27.5° without any other impurity phases respectively.28,36 The diffraction peak at 13.1° corresponds to the (100) crystal plane, which could ascribed to the void-to-void distance of in-planar tri-s-triazine structural units of g-C3N4, and the other peak at 27.5° was divulged to the typical inter-layer stacking structure of the conjugated aromatic system that can be indexed to the (002) crystal plane.37 The typical surface and structure morphology of the as-prepared g-C3N4 sensor film was investigated using SEM and TEM analysis, and the resulting images of the g-C3N4 film are displayed in Fig. 2(b and c). Fig. 2(b) displays the top view of the SEM micrograph of the g-C3N4 film, exhibiting a sheet-like 2D lamellar structure, which was due to the ultrasonic treatment.38 The inset picture illustrates the thickness of the g-C3N4 layer, which was found to be around 220 nm. The TEM micrograph (Fig. 2(c)), revealing that the g-C3N4 nanostructure possessed a thin planar sheet-like lamellar morphology with an irregular curly silk-like texture that indicates the formation of g-C3N4 nanosheets consisting of graphitic layers, which is in consistent with the SEM micrograph. Such a nanostructured sheet-like structure of g-C3N4 was obtained due to the successful ultrasonic exfoliation that would further provide a large surface area and more active surface sites for the absorption of gas molecules.38–40
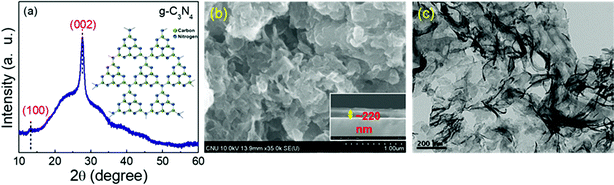 |
| Fig. 2 (a) XRD patterns of the g-C3N4 nanosheet sample, (b) SEM image of g-C3N4 nanosheets (inset picture indicates the cross-sectional image of the g-C3N4 nanosheet sample), and (c) TEM image of the g-C3N4 nanosheet sample. | |
Fig. 3(a) displays the UV-visible absorption spectrum of g-C3N4 nanosheets. The spectrum showed two distinguished characteristic peaks between 300 and 400 nm, that confirms the existence of g-C3N4 nanosheets as similarly observed in the published literature.40,41 The absorption peak at 330 nm is ascribed to the π–π* transitions of the conjugated network of g-C3N4, while the other peak appearing at 394 nm corresponds to the n–π* transition rising from the nitrogen non-bonding orbital to the aromatic π conjugated non-bonding orbital.41,42 The optical band gap value of the g-C3N4 nanosheets was estimated using the Tauc plot and the bandgap was found to be 2.78 eV, which is in consistent with a band gap value of g-C3N4 as reported earlier.31,32 Further to explore the chemical functionalizing groups present in g-C3N4 nanosheets, the FTIR analysis was employed, as shown in Fig. 3(b). The broad absorption band in the range of around 2900 to 3350 cm−1 region corresponds to the stretching vibrational modes of the –NH2/
N–H (primary/secondary amines) components, which are associated with the uncondensed amino groups on the broken aromatic ring of g-C3N4 edge and O–H vibrations from the absorbed water (H2O) molecules on its surface.41,43 The peak at 1634 cm−1 could be attributed to the stretching band of C–N, and the peaks located at 1543, 1457, and 1339 cm−1 are ascribed to the typical stretching vibrational modes of C
N heterocycle rings,32,40,43 while the absorption bands around 1315 and 1232 cm−1 are assigned to the out-of-plane bending vibration of heptazine rings in the basic structural unit of carbon nitride.43 The sharp absorption peaks observed at 891 and 807 cm−1 were assigned to the deformation mode of N–H bonds and the typical characteristic breathing mode of the tri-s-triazine ring system.32,43 To further characterize the surface chemical states of g-C3N4, the XPS analysis was carried out.33,40,41,43 Oxygen appears in the survey scan most probably due to the OH or water molecules on the g-C3N4 surface. Fig. 3(c) displays the high-resolution C 1s core-level XPS spectra of g-C3N4, which was de-convoluted into three distinct peaks located at binding energies of 284.3, 285.7, and 287.6 eV.43 The peak at 284.3 eV is attributed to the C–C coordination of the amorphous graphitic carbon atom. The other two peaks located at 285.7 and 287.6 eV are allocated to the C–NH2 bond and the nitrogen bond-containing aromatic ring in the Sp2 hybridized carbon atom N
C–N, respectively.40,41Fig. 3(d) represents the de-convoluted fitting characteristic peaks of N 1s spectra appearing at 398.1, 398.4, 400.5 and 403.9 eV, respectively. The peaks positioned at 398.1 and 398.4 eV are attributed to the C–N–C sp2 hybridized nitrogen atom present in the triazine structural unit and the tertiary nitrogen linking structure N–(C)3 in g-C3N4, while the other two characteristic peaks located at 400.5 and 403.9 eV were allocated to the nitrogen atom in the terminal amino group C–N–H and π-excitation, which is in accordance with the UV-visible spectra.41,43
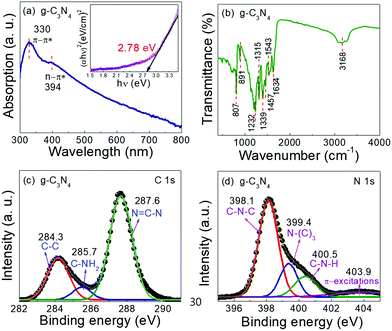 |
| Fig. 3 (a) UV-visible absorption spectra (inset image refers to the optical bandgap of g-C3N4 nanosheets), (b) FTIR spectra, and (c) and (d) deconvoluted XPS core level spectra of C 1s and N 1s of g-C3N4 nanosheets. | |
The device characteristic parameters such as insertion loss and centre frequency (CF) of bare LGS SAW and g-C3N4 coated LGS SAW sensors are shown in Fig. 4(a), and (b) depicts the enlarged view of the CF peak position. The bare LGS SAW device exhibited CF and insertion loss of about 19.1 ± 0.2 dB and 130.285 MHz, whereas the g-C3N4-coated SAW sensor showed the insertion loss and centre frequency at 24.5 ± 0.2 dB and 130.125 MHz. It was noticed that the g-C3N4-coated LGS SAW device exhibited an increment in the insertion loss and the centre frequency was decreased to a lower frequency as compared to the bare LGS SAW sensor, which was likely due to the mass loading effect further resulting in the wave diffraction (attenuation) caused by the addition of g-C3N4 films.2,8,14
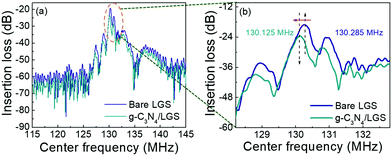 |
| Fig. 4 (a) Frequency response curves (centre frequency V/S insertion loss) of the pristine LGS and g-C3N4/LGS SAW sensor and (b) enlarged view of (a). | |
Fig. 5(a and b) elucidates the dynamic differential frequency response properties of the pristine LGS and various thicknesses of a 2D g-C3N4-coated LGS SAW sensor for 100 ppm of NO2 gas at RT. As displayed in Fig. 5a, the pristine LGS SAW sensor showed a frequency shift (Δf) of about ∼15 Hz with more noise, which was very negligible as compared to the sensitive interface material (g-C3N4)-coated LGS (Fig. 5b), and this phenomenon was mainly due to the lack of adequate sensitivity, poor selectivity and absorption capability of pristine LGS SAW sensors towards the target gas molecules. We have further examined the effect of the g-C3N4 thickness on NO2 gas sensing performances since it is one of the significant factor that influences the SAW device gas sensing performances.44,45 Meanwhile, g-C3N4 of various thicknesses such as 90, 160, 220, 300 and 380 nm with an error of ±15 nm was deposited on the LGS SAW resonator and the gas sensing performance was tested by exposing 100 ppm of NO2 gas at RT, as displayed in Fig. 5(b). It can be noticed that all the SAW devices coated with different thickness exhibited a negative Δf value towards NO2 gas, which was found to increase with the increase in the g-C3N4 thickness from 90 to 300 nm and then decrease with the further increase in the g-C3N4 film thickness (380 nm).50 This results indicate that, at a higher thickness of g-C3N4, the density of the nanosheets becomes larger and it would hamper the deep diffusion of NO2 gas molecules into the material surface and also the gas molecules need to travel longer distances to reach the g-C3N4/LGS SAW interface, which further affects the wave propagation, resulting in low Δf.49,50 In addition, the variation in the response/recovery times was observed with different thickness of g-C3N4. It can be seen that g-C3N4 of 300 nm thickness showed a high Δf value, which was higher than the 220 nm thickness of g-C3N4, despite the high Δf value, the fast response/recovery times and low noise level were also a vital parameter for the practical applications, also as similarly found in the reported literature.45,49 However, at a higher thickness (300 nm), the recovery time of the sensor drastically increases to a much larger value (∼168 s) as compared to the other samples, which was ascribed to the thicker film surface that requires longer time to release the absorbed gas molecules.45,49 Apart from the Δf value, the response/recovery time and low noise level of the 220 nm g-C3N4-coated SAW sensor were less in comparison with the other film thickness, as given in Table S1 (ESI†), which is more beneficial for real-time practical applications. Thus, for the LGS SAW resonator, 220 nm of g-C3N4 was considered as the optimal thickness for better NO2 gas sensing performances. Fig. 5(c) demonstrates the typical frequency response curves of the LGS SAW device coated with g-C3N4 of 220 nm optimal thickness towards various concentrations of NO2 gas at RT. Upon exposure to different NO2 gas concentrations ranging from 5 to 100 ppm, the frequency shift of the sensor was escalated from ∼0.9 kHz to ∼3.1 kHz. It can be seen that the Δf value of the sensor increases as the concentration of NO2 gas increases, which was ascribed to the absorption of more gas molecules on the surface of the active material. Besides, the repeatability (cycling stability) and long-term stability are the other key factors for the SAW-based practical gas sensing applications.14,40 In order to this, the g-C3N4/LGS SAW sensor was continuously exposed to 100 ppm of NO2 gas at RT for five consecutive cycles (Fig. 5(d)). During the 5 consecutive cycles, the shift in frequency remains almost unchanged (Fig. S6(a), ESI†), which indicates that the sensor has excellent repeatability and stability for NO2 monitoring. In addition to the cycling stability, long-term stability test of our device was also performed for every one month interval up to four months towards 5, 20, and 100 ppm of NO2 as given in Fig. S6(b) (ESI†) and the test results manifest that even after 4 months the SAW device showed excellent frequency shift with an overall diminution of ∼3.5% loss in Δf. As displayed in Fig. 5(e) the frequency shifts of the SAW sensor exhibited almost a linear trend to the different concentrations of the NO2 gas, which signifies its advantage in the detection of low concentration of NO2 gas.41 Due to the experimental limitations, we are unable to test the SAW sensor below 5 ppm (NO2). Hence, we estimated the theoretical values of the detection limit (DL) of the g-C3N4-coated LGS device, using the fitting of least-squares method in the linear regime.46,47 It is to be noted that DL is one of the significant indexes reflecting the sensitivity and represents the lowest possible amount of NO2 gas under ambient conditions that it can be detected. The fitting quality and the slope of the sensor frequency shift were found to be R2 = 0.988 and 1680 ppm−1.47 We further calculated the noise of the sensor using root-mean-square deviation with fifth-order polynomial fits for the experimental data points, as shown in Fig. 5f. In detail, 10 data points (N) of the initial frequency from the baseline of the sensor before the exposure of NO2 gas were taken and then averaged; the standard deviation was also acquired using eqn (1). Using these two parameters the noise of the sensor (RMSnoise) was estimated to be 88.9. According to given eqn (2) reported in the published journals,46–48 the theoretical DL limit of the g-C3N4/LGS sensor was found to be ∼158 ppb. The low DL in ppb level for NO2 gas indicates the potential usage of our device, the g-C3N4 nanosheet–coated LGS SAW sensor, in the applications of gas sensing as a part in the revolution of environmental protection. Table 1 lists the comparison of the NO2 gas sensing performances of our device with those previously reported in the literature.
| 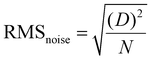 | (1) |
|  | (2) |
 |
| Fig. 5 (a) Pristine LGS SAW sensor NO2 gas (100 ppm) sensing response at RT, (b) thickness dependent g-C3N4/LGS SAW sensor frequency towards 100 ppm of NO2 gas at RT, (c) dynamic frequency shifts of the optimized (220 nm) thickness of the g-C3N4-coated LGS SAW sensor towards 5–100 ppm of NO2 gas at room temperature, (d) cycling stability test of the g-C3N4/LGS SAW sensor towards 100 ppm of NO2 measured at day 1 and after 4 months, (e) limit of detection of g-C3N4/LGS SAW sensor and (f) 5th-order polynomial fitting curve of the baseline data point of the g-C3N4/LGS SAW sensor. | |
Table 1 Comparison of g-C3N4/LGS SAW sensor NO2 gas sensing performances with the previously reported NO2 SAW gas sensors
Sensing material |
Working-temperature (°C) |
Target gas |
Sensitivity (kHz)/ppm |
Response/recovery time (s) |
Ref. |
GO-PEDOT:PSS |
RT |
NO2 |
5.8/100 |
∼35/10 |
14
|
SnS QD |
RT |
NO2 |
1.8/10 |
∼135/112 |
48
|
ZnS mucosal |
RT |
NO2 |
0.08/100 |
∼110/160 |
49
|
Fe3O4 NRs |
RT |
NO2 |
0.003/100 |
— |
59
|
SiO2-SnO2 |
RT |
NO2 |
0.04/100 |
∼158/590 |
60
|
BC-PEI |
RT |
NO2 |
0.95/100 |
— |
61
|
PPy/TiO2 |
RT |
NO2 |
0.09/100 |
∼30/145 |
62
|
SnO2 NFs@PDA |
RT |
NO2 |
0.01/30 |
— |
63
|
SiO2-TiO2 |
RT |
NO2 |
0.2/10 |
— |
64
|
Polypyrrole |
RT |
NO2 |
2.5/100 |
∼143/250 |
65
|
CuO-Al2O3 |
RT |
NO2 |
0.1/50 |
|
66
|
Bi2S3 |
RT |
NO2 |
2/10 |
∼48/110 |
67
|
GO |
RT |
NO2 |
0.32/50 |
∼225/321 |
68
|
g-C3N4 nanosheets |
RT |
NO2 |
3.1/100 |
∼42/22 |
This work |
Fig. 6 presents the temperature-dependent NO2 gas sensing characteristics of the g-C3N4/LGS SAW sensor. The centre frequency shift and the insertion loss of the g-C3N4/LGS SAW sensor were estimated as a function of temperature, as displayed in Fig. 6(a). One can be observed that the centre frequency and the insertion loss of the g-C3N4/LGS SAW sensor at RT were found to be 130.125 MHz and −24.5 ± 0.2 dB. However, with the increase in temperature, the centre frequency of the sensor was shifted to lower frequencies, i.e. from 130.125 MHz to 129.575 MHz, and the insertion loss of the device was increased from −24.5 dB to −36.01 dB (from RT to 200 °C), which was mainly due to the increase in mass loading effects on the sensing layer. Moreover, the higher the insertion loss (increases in negative term), the lower the noise level in sensing measurements, as similarly observed in the reports in the literature.49 Prior to the gas sensing measurement, the ambient temperature of test chamber was kept stable for half an hour at each temperature. Fig. 6(b–e) displays the NO2 gas sensing performances of the g-C3N4/LGS SAW sensor measured at different temperatures from 50 to 200 °C with an interval of 50 °C by varying the gas concentrations from 5 to 100 ppm. The experimental results manifested that the frequency shift was significantly enhanced, as the temperature raised from 50 to 200 °C. The maximum frequency shift was obtained at 200 °C, which was about 23.26 kHz to 100 ppm of NO2 gas concentration. The large frequency shifts obtained at higher temperatures were attributed to the increase in mass loading effects of the sensing film, which resulted from the more number of gas molecules absorbed over the film surface owing to the extraordinary adsorptive capability of g-C3N4 nanosheets. Fig. 6(f) depicts the summary of the frequency responses of the g-C3N4/LGS SAW sensor at each temperature condition (50 to 200 °C) with respective to the various NO2 gas concentrations.
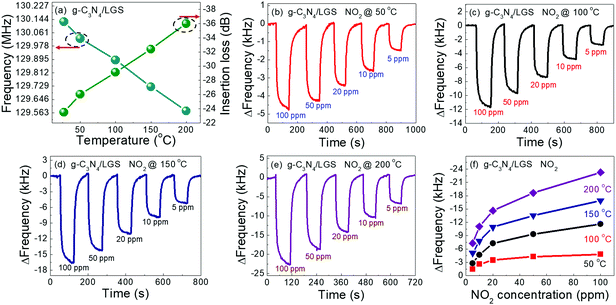 |
| Fig. 6 (a) Temperature-dependent resonant frequency and insertion loss of optimized thickness (220 nm) of the g-C3N4/LGS SAW sensor, (b–e) concentration-dependent NO2 gas sensing performances of the g-C3N4/LGS SAW sensor operating in the range of 50–200 °C, (f) summary of the temperature-dependent frequency shifts versus gas concentration (ppm) of the g-C3N4/LGS SAW sensor. | |
Fig. 7(a) displays the response/recovery times of the g-C3N4/LGS SAW device towards 100 ppm of NO2 gas measured at RT using an exponential fitting equation, as reported elsewhere.14,46 The estimated response and recovery times of the sensor measured at RT were found to be 42 and 22 s, respectively. Similarly, we measured the response and recovery times of the sensor for the 100 ppm of NO2 gas measured at different temperatures (RT to 200 °C) as given in Fig. 7(b). It can be observed that the response and recovery times of the g-C3N4/LGS SAW sensor were decreases as temperature increases from RT to 200 °C, which was due to the fast gas kinetics (absorption/desorption rate) mainly endorsed by high activation energy at evaluated temperature.1,51 The short response/recovery times at a higher temperature were induced by the chemisorption between the gas molecules and the sensing layer. Next, the selectivity is one among the vital characteristics of commercialized sensors, and it can be defined as the capacity of the device that how effectively it could differentiate the response of one particular gas from the other input gases. The selectivity test was examined with NO2, NO, CO, NH3 and H2S and the frequency shifts of each gas of 100 ppm were recorded at RT, as shown in Fig. 7(c). It was clearly observed that the proposed g-C3N4/LGS SAW sensor has a superior selectivity towards NO2 gas when compared to the other test gases. Thus, we inferred that the as-prepared sensor has a high potential to detect the NO2 gas molecules.
 |
| Fig. 7 (a) Response and recovery curves of the g-C3N4/LGS SAW sensor under 100 ppm of NO2 gas at room temperature, (b) response/recovery times of the g-C3N4/LGS SAW device towards NO2 gas (100 ppm) under various operating temperatures ranging from RT to 200 °C and (c) frequency response of the g-C3N4/LGS SAW sensor towards 100 ppm of various gases such as NO2, NO, CO, NH3 and H2S. | |
Furthermore, the improved NO2 gas sensing performances of g-C3N4/LGS SAW sensor and its superior selectivity can be better understood by estimating the activating energies (Ea) as shown in Fig. 8. According to the basics of gas kinetic theory, selectivity and response/recovery times of the respective sensor depend on Ea.1,46 Thus, Ea of the g-C3N4/LGS SAW sensor towards the various gases were calculated using Arrhenius plots by extrapolating from the linear fittings of ln(Δf) vs. 1000/T, reported elsewhere, and the graphs were plotted, as shown in Fig. 8(a–e). It is to be noted that the sensor with low Ea to a particular gas should exhibit a better sensing performance, in which the smaller Ea of the sensor would provide more active surface sites for the huge gas molecule absorption, which further leads to enhanced gas sensing responses. The estimated Ea value of the g-C3N4/LGS SAW sensor was found to be 13.82 kJ mol−1, 19.11 kJ mol−1, 20.51 kJ mol−1, 20.92 kJ mol−1, and 28.46 kJ mol−1 to NO2, NO, CO, NH3, and H2S, respectively. As displayed in Fig. 8(f), it can be clearly observed that the proposed senor showed low Ea to NO2 gas among the other existing gases. It is to be understood that the lowest Ea value of the selective gas would exhibit the highest selectivity.1 Hence, our proposed g-C3N4/LGS SAW sensor has exhibited enhanced gas sensing responses and excellent selectivity to NO2 gas as compared to other interfering gases.
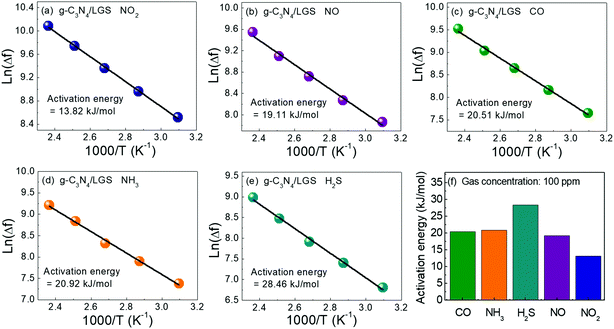 |
| Fig. 8 Arrhenius plots of the g-C3N4/LGS SAW sensor that describes the activation energies towards different test gases using (a) NO2, (b) NO, (c) CO, (d) NH3, (e) H2S and (f) comparison of activation energies. | |
Furthermore, the effect of humidity on the gas sensing performance of the SAW device especially operating at RT is another significant issue that needs to be addressed.5,52 So that it is of keen interest to examine the humidity effect for real-time practical applicability. We investigated the NO2 gas (100 ppm) sensing performances at RT under relative humidity (RH) conditions varying from 20 to 80% RH, as displayed in Fig. 9(a). The results indicated that the RH greatly affected the gas sensing performances, the frequency response value of the SAW sensor towards 100 ppm of NO2, obviously increased as the RH (%) value increases (from 20 to 80% RH) and exhibited a linear relationship, as shown in Fig. 9(b). The significant improvement in the gas sensing performance under different RH conditions was mainly attributed to the high mass loading effect endorsed by the huge NO2 gas molecule absorption, which was further explained using Grotthuss chain reaction (eqn (4)) in the mechanism section.53,56 The experimental test result of the g-C3N4/LGS SAW sensor has proved that the as-prepared sensor could meet the standard sensitivity requirements under the general environmental RH conditions.
 |
| Fig. 9 (a) Dynamic frequency responses of 100 ppm of NO2 of gas g-C3N4/LGS SAW sensor switching under various relative humidity levels (20 to 80% RH) at RT and (b) summary of frequency shift as a function of different RH values of the g-C3N4/LGS SAW sensor. | |
3.1 Sensing mechanism
The mechanism behind the significant gas sensing performances of g-C3N4 nanosheet-coated LGS was demonstrated using a typical SAW device sensing principle. It is important to understand the major contribution towards the sensing mechanism (frequency response behaviour) of the g-C3N4/LGS SAW device such as mass loading, conductivity change (acousto–electric interaction), and elastic loading effects. The following equation represents the contributions of each parameter towards the SAW frequency response given as follows:2,7,14 |  | (3) |
where v0 and Δv are the unperturbed SAW wave velocity and the change in wave velocity. fo is the operating resonant frequency of the SAW sensor, and Cm and Ce are the sensitivity coefficients of the mass and elasticity respectively. ρs is the surface mass density per unit area, σs, Cs and h are the sheet conductivity, capacitance and thickness of the sensing film, K2 is the electromechanical coupling coefficient, whereas μ and λ are the bulk and shear moduli of the film. According to eqn (3), the first and second factors indicate the mass loading and acousto–electrical loading effect, the last term describes the elastic effect. Here, we ruled out the elastic contributions since the elastic effect leads to the positive frequency response (shift).2,14,54 However, in our experimental study, it was noticed that the SAW device exhibits negative differential frequency shift for NO2 gas, which was mainly due to mass loading or/and conductivity effects of the sensing film.7,45 In order to find the contribution of acousto–electric interactions (conductivity effect), we further carried out the resistive-type measurement of g-C3N4 nanosheet thin films deposited on an n-Si substrate, as shown in Fig. 10. It was noticed that the resistance of the film increases with the exposure of NO2 gas (100 ppm) at RT, attains a maximum value and then reaches to its original base line position after turning off the gas. Typically, the SAW velocity of the device depends on the conductivity of the sensitive interface material coated on the SAW resonating cavity area. Meanwhile, under the NO2 gas ambient, the conductivity of g-C3N4 film decreased, which was ascribed to its intrinsic n-type semiconducting behaviour. Thus, in the presence of the oxidizing gas (NO2), the electrons on the conduction band of the sensing film were attracted by the NO2 gas molecules, thereby the conductivity of the sensor film decreased, as shown in Fig. 10. The decrease in the film conductivity results in a positive frequency shift, which is contradictory to the negative frequency shifts obtained in our present study. Moreover, we noticed that the response and recovery times of the g-C3N4/LGS SAW sensor were short as compared to the resistive-type sensor (Fig. 10). From the above-mentioned facts, it was realized that the role of acousto–electric interaction is also insignificant in gas sensing mechanism.2,14,45 Henceforth, it can be concluded that the Δf (negative frequency shift) value of the g-C3N4/LGS SAW sensor towards the NO2 gas was mainly ascribed to the mass loading effect.14,54,56
 |
| Fig. 10 Resistive-based g-C3N4 nanosheet gas sensor towards 100 ppm of NO2 gas at RT. | |
To acknowledge the superior performances of g-C3N4 coated LGS SAW device, a possible explanation is shown in Fig. 11. It was well noticed from the FTIR and XPS analysis that g-C3N4 nanosheets consist of a large number of active functional groups including, hydroxyl, epoxy and amino groups, which were benefited by its tri-s-triazine structure layers. More importantly, the intrinsic porosity and π–π* conjugation structure of g-C3N4 nanosheets with a plenty of free electrons on nitrogen atoms, and large surface area, would eventually promote the abundant adsorption of NO2 gas molecules, thereby it leads to an increase in the film mass. Generally, the absorption of gas molecules on the g-C3N4 surface involves two ways, namely, physisorption and chemisorption.31,47,55 It has been well documented that, in physisorption, the analyte gas molecules were adsorbed on the film surface via weak physical bonds such as dipole–dipole interaction and van der Waals forces, which occurs at low temperatures (≤100 °C). However, the chemisorption involves the electron transfer between the film surface and target gas molecules, which would be the dominant mechanism at higher temperatures (≥100 °C).1,31,55 In addition, the detailed possible gas reaction process at different operating temperatures were described using the following equations, given as below (eqn (5), (6), (7), (8) and (9)).1,2,55 It should be noted that under higher temperature conditions, the conductivity of the sample is enhanced, thus more number of electrons would be available on the g-C3N4 surface. Thus, the generated electrons attract more number of NO2 molecules that further lead to high sensitivity. Furthermore, the thermal energy enhances the rate of reaction of gas kinetics (fast absorption/desorption rate) between the NO2 molecules and the active surface of the g-C3N4 film, which results in the short response/recovery times of the sensor.1,2,30,46 The huge absorption of NO2 molecules over the sensitive film surface resulting in a drastic increase in film mass at higher temperatures, which further cause a large frequency shift via decrease in the resonant frequency of the SAW sensor.30,43 Furthermore, the effect of RH on NO2 gas sensing is one of the crucial factor for RT gas sensing application and the plausible mechanism can be explained as follows.56 It has been perceived that in the sensor film in a higher RH environment, H2O molecules were physically adsorbed on the film surface due to the presence of amine, nitrogen defects, hydrophilic property and OH functional groups. At the same time, the adsorbed water molecules would penetrate into the g-C3N4 surface layers, and it again turns into the multilayer absorption with the increase in the RH value. As per the Grotthuss chain reaction mechanism given in eqn (4), these absorbed water molecules would form strong hydrogen bonding networks with the functional groups of sensing materials that further ionize and generate the hydronium ions (H3O+) as charge carriers.43,56,57 Thus, the generated hydronium ions attract a large amount of NO2 gas molecules on the film surface, thereby the sensitivity and the mass of the film increases effectively.43,57,58 With the addition of H2O and NO2 molecules on the film surface, the mass of the film increases gradually as the RH value increases; as a result, a large frequency shift can be observed. Subsequently, the increased mass can further decline the SAW velocity, which results in large negative differential frequency shifts.
| (H2O + H3O+ → H3O+ + H2O) | (4) |
| O2(ads) + e− → O2(ads)−; T < 100 °C | (6) |
| O2(ads)− + e− → 2O(ads)−; T < 100–100 °C | (7) |
| NO2(gas) + e− → NO2(ads)− | (8) |
| NO2(gas) + O2(ads)− + 2e− → NO2(ads)− + 2O(ads)− | (9) |
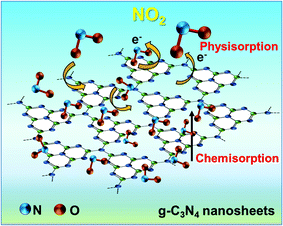 |
| Fig. 11 NO2 gas sensing mechanism of optimized thickness (220 nm) of the g-C3N4 nanosheet-coated LGS SAW sensor. | |
4. Conclusions
In summary, g-C3N4 nanosheets have been successfully synthesized and practically applied as a chemical interface for selective RT NO2 SAW gas sensor applications. The LGS SAW resonator coated with 220 nm thickness of g-C3N4 exhibited a large frequency shift of ∼3.1 kHz to 100 ppm of NO2 at RT. Also, the as-prepared device features good stability and repeatability with a fast response/recovery time (42/22 s) at RT. The potentiality of the device is further boosted by increasing operating temperatures from RT to 200 °C, which was endorsed by the chemisorption of NO2 gas molecules at high temperatures. Further, the magnificent NO2 gas sensing performances of g-C3N4/LGS SAW were observed under different RH conditions (20–80% RH). The significant gas sensing performances of our device were ascribed to the enhancement in the mass loading effect. Moreover, the high surface-to-volume ratio, abundant function groups and π–π* conjugation structure of g-C3N4 nanosheets would provide a plenty of active surface sites, which further enhances the diffusion ability of NO2 gas molecules; consequently, the mass of the sample would enhanced effectively. Our experimental studies clearly emphasize that the g-C3N4/LGS SAW device is an excellent NO2 gas sensor, which can be operated at both RT and high elevated temperatures, indicating that it is a promising candidate for futuristic high-performance RT-based SAW gas sensor applications.
Author contributions
Kedhareswara Sairam Pasupuleti: conceptualization, methodology, investigation, experiments, data curation, validation, writing – original draft. Dong-Jin Nam: formal analysis. Na-Hyun Bak: formal analysis. Maddaka Reddeppa: formal data analysis. Song-Gang Kim: formal analysis. Jae-Eung Oh: formal analysis. Hak Dong Cho: formal analysis. Moon-Deock Kim: conceptualization, visualization, validation, writing – review & editing, resources, supervision.
Conflicts of interest
The authors declare no conflicts of interest.
Acknowledgements
This research was supported by Basic Science Research Program through the National Research Foundation of Korea (NRF) funded by the Ministry of Science, ICT, and Future Planning (Grant No. 2017R1E1A1A01073076, 2020R1A2C2013385) and the Ministry of Education (NRF-2020R1A6A1A03047771) and was supported by Korea Institute for Advancement of Technology (KIAT) grant funded by the Korea Government (MOTIE). (P0008458, The Competency Development Program for Industry Specialist).
References
- J. Jaiswal, P. Singh and R. Chandra, Sens. Actuators, B, 2021, 327, 128862 CrossRef CAS.
- A. Ghosh, C. Zhang, S. Shi and H. Zhang, Sens. Actuators, B, 2019, 301, 126958 CrossRef CAS.
-
J. Devkota, E. Mao, J. Baltrus, P. R. Ohodnicki and B. Chorpening, Surface Acoustic Wave H2 and O2 Sensors Based on Conducting Metal Oxides/Langasite for Elevated Temperature Applications, 2020 Search PubMed.
- L. Rana, R. Gupta, M. Tomar and V. Gupta, Sens. Actuators, B, 2017, 252, 840–845 CrossRef CAS.
- K. Sonowal, A. V. Kalameitsev, V. M. Kovalev and I. G. Savenko, Phys. Rev. B, 2020, 102, 235405 CrossRef CAS.
- L. Yang, C. Yin, Z. Zhang, J. Zhou and H. Xu, Mater. Sci. Semicond. Process., 2017, 60, 16–28 CrossRef CAS.
- M. Li, H. Kan, S. Chen, X. Feng, H. Li, C. Li, C. Fu, A. Quan, H. Sun and J. Luo, Sens. Actuators, B, 2019, 287, 241–249 CrossRef CAS.
- C. Zhang, A. Ghosh, H. Zhang and S. Q. Shi, Smart Mater. Struct., 2019, 29, 015039 CrossRef.
- J. Thiele and M. P. Da Cunha, Sens. Actuators, B, 2006, 113, 816–822 CrossRef CAS.
- H. Xu, H. Jin, S. Dong, J. Chen, X. Song, W. Xuan, L. Shi, S. Huang, P. Zhang and J. Luo, AIP Adv., 2021, 11, 015143 CrossRef.
- S. Yenuganti, H. Zhang and C. Zhang, Sens. Actuators, A, 2018, 281, 108–116 CrossRef CAS.
- A. Leong, S. Seeneevassen, T. Saha, V. Swamy and N. Ramakrishnan, Surf. Interfaces, 2021, 23, 100964 CrossRef CAS.
- A. Leong, T. Saha, V. Swamy and N. Ramakrishnan, Sensors, 2020, 20, 334 CrossRef CAS.
- K. S. Pasupuleti, M. Reddeppa, D.-J. Nam, N.-H. Bak, K. R. Peta, H. D. Cho, S.-G. Kim and M.-D. Kim, Sens. Actuators, B, 2021, 130267 CrossRef CAS.
- T. Julian, S. N. Hidayat, A. Rianjanu, A. B. Dharmawan, H. S. Wasisto and K. Triyana, ACS Omega, 2020, 5, 29492–29503 CrossRef CAS PubMed.
- Y. Wang, A. Liu, Y. Han and T. Li, Polym. Int., 2020, 69, 7–17 CrossRef CAS.
- S. Xu, R. Zhang, J. Cui, T. Liu, X. Sui, M. Han, F. Zheng and X. Hu, Micromachines, 2021, 12, 552 CrossRef PubMed.
- T.-T. Hung, M.-H. Chung, J.-J. Chiu, M.-W. Yang, T.-N. Tien and C.-Y. Shen, Org. Electron., 2021, 88, 106006 CrossRef CAS.
- R. Kumar, N. Goel and M. Kumar, ACS Sens., 2017, 2, 1744–1752 CrossRef CAS PubMed.
- R. Kumar, O. Al-Dossary, G. Kumar and A. Umar, Nano-Micro Lett., 2015, 7, 97–120 CrossRef.
- Y. Niu, J. Zeng, X. Liu, J. Li, Q. Wang, H. Li, N. F. D. Rooij, Y. Wang and G. Zhou, Adv. Sci., 2021, 2100472 CrossRef CAS.
- Y. Wang, L. Yao, L. Xu, W. Wu, W. Lin, C. Zheng, Y. Feng and X. Gao, Sens. Actuators, B, 2021, 332, 129497 CrossRef CAS.
- N. Goel and M. Kumar, J. Mater. Chem. C, 2021, 9, 1537–1549 RSC.
- D. Liu, X. Ren, Y. Li, Z. Tang and Z. Zhang, J. Adv. Ceram., 2020, 9, 17–26 CrossRef CAS.
- M. Reddeppa, N. T. KimPhung, G. Murali, K. S. Pasupuleti, B. G. Park, I. In and M. D. Kim, Sens. Actuators, B, 2021, 329, 129175–129185 CrossRef CAS.
- S. Jain, A. Paliwal, V. Gupta and M. Tomar, Sens. Actuators, B, 2020, 311, 127897 CrossRef CAS.
- T.-Y. Su, Y.-Z. Chen, Y.-C. Wang, S.-Y. Tang, Y.-C. Shih, F. Cheng, Z. M. Wang, H.-N. Lin and Y.-L. Chueh, J. Mater. Chem. C, 2020, 8, 4851–4858 RSC.
- X. Chen, W. Zhang, L. Zhang, L. Feng, C. Zhang, J. Jiang and H. Wang, ACS Appl. Mater. Interfaces, 2020, 13, 2052–2061 CrossRef PubMed.
- B. B. Gicha, L. T. Tufa, S. Kang, M. Goddati, E. T. Bekele and J. Lee, Nanomaterials, 2021, 11, 1388 CrossRef CAS.
- P. Srinivasan, S. Samanta, A. Krishnakumar, J. B. B. Rayappan and K. Kailasam, J. Mater. Chem. A, 2021, 9, 10612–10651 RSC.
- K. Bai, Z. Cui, E. Li, Y. Ding, J. Zheng, C. Liu and Y. Zheng, Vacuum, 2020, 175, 109293 CrossRef CAS.
- Z. Liu, X. Zhang, Z. Jiang, H.-S. Chen and P. Yang, Int. J. Hydrogen Energy, 2019, 44, 20042–20055 CrossRef CAS.
- N. Prakash, G. Kumar, M. Singh, A. Barvat, P. Pal, S. P. Singh, H. Singh and S. P. Khanna, Adv. Opt. Mater., 2018, 6, 1800191 CrossRef.
- J. N. Coleman, M. Lotya, A. O’Neill, S. D. Bergin, P. J. King, U. Khan, K. Young, A. Gaucher, S. De and R. J. Smith, Science, 2011, 331, 568–571 CrossRef CAS PubMed.
- R. Zhang, Y. Wang, Z. Zhang and J. Cao, Sensors, 2018, 18, 2211 CrossRef.
- J. Liu, W. Fang, Z. Wei, Z. Qin, Z. Jiang and W. Shangguan, Appl. Catal., B, 2018, 238, 465–470 CrossRef CAS.
- H. Lei, Q. He, M. Wu, Y. Xu, P. Sun and X. Dong, J. Hazard. Mater., 2022, 421, 126696 CrossRef CAS.
- X. Zhang, P. Wang and P. Yang, Int. J. Hydrogen Energy, 2020, 45, 21523–21531 CrossRef CAS.
- K. Sun, J. Shen, Q. Liu, H. Tang, M. Zhang, S. Zulfiqar and C. Lei, Chin. J. Catal., 2020, 41, 72–81 CrossRef CAS.
- X. Wu, F. Chen, X. Wang and H. Yu, Appl. Surf. Sci., 2018, 427, 645–653 CrossRef CAS.
- Z. Lu, W. Song, C. Ouyang, H. Wang, D. Zeng and C. Xie, RSC Adv., 2017, 7, 33552–33557 RSC.
- P. Kumar, E. Vahidzadeh, U. K. Thakur, P. Kar, K. M. Alam, A. Goswami, N. Mahdi, K. Cui, G. M. Bernard and V. K. Michaelis, J. Am. Chem. Soc., 2019, 141, 5415–5436 CrossRef CAS PubMed.
- W. Meng, S. Wu, X. Wang and D. Zhang, Sens. Actuators, B, 2020, 315, 128058 CrossRef CAS.
- W. Wang, X. Liu, S. Mei, M. Liu, C. Lu and M. Lu, Sensors, 2019, 19, 3560 CrossRef CAS.
- V. B. Raj, A. Nimal, M. Tomar, M. Sharma and V. Gupta, Sens. Actuators, B, 2015, 220, 154–161 CrossRef CAS.
- B. Paschke, A. Wixforth, D. Denysenko and D. Volkmer, ACS Sens., 2017, 2, 740–747 CrossRef CAS PubMed.
- M. Šetka, F. Bahos, O. Chmela, D. Matatagui, I. Gràcia, J. Drbohlavová and S. Vallejos, Sens. Actuators, B, 2020, 321, 128573 CrossRef.
- H. Li, M. Li, H. Kan, C. Li, A. Quan, C. Fu, J. Luo, X. Liu, W. Wang and Z. Yang, Surf. Coat. Technol., 2019, 362, 78–83 CrossRef CAS.
- G. Long, Y. Guo, W. Li, Q. Tang, X. Zu, J. Ma, B. Du and Y. Fu, Microelectron. Eng., 2020, 222, 111201 CrossRef CAS.
- N. Van Toan, C. M. Hung, N. D. Hoa, N. Van Duy, D. Thi Thanh Le, N. Thi Thu Hoa, N. N. Viet, P. H. Phuoc and N. Van Hieu, J. Hazard. Mater., 2021, 412, 125181 CrossRef CAS.
- M. Asad and M. H. Sheikhi, Sens. Actuators, B, 2014, 198, 134–141 CrossRef CAS.
- D. Li, X. Zu, D. Ao, Q. Tang, Y. Fu, Y. Guo, K. Bilawal, M. B. Faheem, L. Li and S. Li, Sens. Actuators, B, 2019, 294, 55–61 CrossRef CAS.
- Y. Tang, D. Li, D. Ao, Y. Guo, M. B. Faheem, B. Khan, X. Zu and S. Li, Mater. Chem. Phys., 2020, 239, 122026 CrossRef CAS.
- Y.-L. Tang, Z.-J. Li, J.-Y. Ma, Y.-J. Guo, Y.-Q. Fu and X.-T. Zu, Sens. Actuators, B, 2014, 201, 114–121 CrossRef CAS.
- O. Alev, N. Sarıca, O. Özdemir, L. C. Arslan, S. Büyükköse and Z. Z. Öztürk, J. Alloys Compd., 2020, 826, 154177 CrossRef CAS.
- D. Zhang, J. Tong and B. Xia, Sens. Actuators, B, 2014, 197, 66–72 CrossRef CAS.
- R. Malik, V. K. Tomer, V. Chaudhary, M. S. Dahiya, A. Sharma, S. Nehra, S. Duhan and K. Kailasam, J. Mater. Chem. A, 2017, 5, 14134–14143 RSC.
- Y. Su, C. Li, M. Li, H. Li, S. Xu, L. Qian and B. Yang, Sens. Actuators, B, 2020, 308, 127693 CrossRef CAS.
- T. V. Nguyen, N. A. Luong, V. T. Nguyen, A. T. Pham, A. T. Le and T. L. To, Mater. Res. Bull., 2021, 134, 111087 CrossRef CAS.
- Y. Guo, G. Long, Y. Tang, J. Wang, Q. Tang, X. Zu, J. Ma, B. Du, H. Torun and Y. Fu, Smart Mater. Struct., 2020, 29, 095003 CrossRef CAS.
- J. Wang, Y. Guo, G. Long, Y. L. Tang, Q. Tang, X.-T. Zu, J. Ma, B. Du, H. Torun and Y. Fu, J. Hazard. Mater., 2020, 388, 121743 CrossRef CAS.
- X. Yan, D. Li, C. Hou, X. Wang, W. Zhou, M. Liu and T. Ye, Sens. Actuators, B, 2012, 161, 329–333 CrossRef CAS.
- Z. Kang, D. Zhang, T. Li, X. Liu and X. Song, Sens. Actuators, B, 2021, 130299 CrossRef CAS.
- Y. Tang, D. Ao, W. Li, X. Zu, S. Li and Y. Q. Fu, Sens. Actuators, B, 2018, 254, 1165–1173 CrossRef CAS.
- L. Al-Mashat, H. D. Tran, W. Wlodarski, R. B. Kaner and K. Kalantar-Zadeh, Sens. Actuators, B, 2008, 134, 826–831 CrossRef CAS.
- Y. Tang, W. Wu, B. Wang, X. Dai, W. Xie, Y. Yang, R. Zhang, X. Shi, H. Zhu and J. Luo, Sens. Actuators, B, 2020, 325, 128742 CrossRef CAS.
- J. Luo, X. Feng, H. Kan, H. Li and C. Fu, IEEE Sens. J., 2020, 21, 1404–1408 Search PubMed.
- Q. Tang, Y. Guo, Y. L. Tang, G. Long, J. Wang, D. Li, X.-T. Zu, J. Ma, L. Wang and H. Torun, J. Mater. Sci., 2019, 54, 11925–11935 CrossRef CAS.
Footnote |
† Electronic supplementary information (ESI) available. See DOI: 10.1039/d1tc04904f |
|
This journal is © The Royal Society of Chemistry 2022 |
Click here to see how this site uses Cookies. View our privacy policy here.