A dual-biomimetic knitted fabric with a manipulable structure and wettability for highly efficient fog harvesting†
Received
26th September 2021
, Accepted 24th November 2021
First published on 25th November 2021
Abstract
The shortage of freshwater severely constrains economic development and social security worldwide. Bio-inspired functional fog-harvesting devices (FHDs) have been broadly exploited to tackle this global challenge. Despite the great advances achieved in FHDs, efficient and large-scale water harvesting is still hindered by some inherent limitations: (1) a rational structure should be designed to maximize the function of the separated hydrophilic and hydrophobic regions, (2) simple, low-cost and mature manufacturing technology can better realize the large-scale production of FHDs. Here, inspired by the unique wettability of Namib desert beetles and the wedge-shaped structure of leaf veins, we prepared a dual-biomimetic tuck fabric with a manipulable structure and wettability using knitting technology, which greatly enhanced the fog capture velocity and directional water transportation. The influences of different structures and wettability on fog capture and droplet transportation efficiency have been systematically investigated. Moreover, massive theoretical models were proposed to reveal the fog harvesting mechanism. The optimized FHD exhibited rapid and highly efficient fog harvesting capacity (5424 mg h−1 cm−2). In addition, the prepared FHD showed excellent mechanical strength and durability, enabling low-cost and large-scale production. Thus, this work reinforces the understanding of the fundamental research and significantly promotes the practical applications of functional fog-harvesting devices.
1. Introduction
Freshwater is the foremost resource for the survival and development of natural organisms. However, with the rapid population growth, global warming, and water pollution, the absence of freshwater has become a severe problem in most of the semi-arid regions and land-scarce regions.1,2 At present, various advanced nanomaterials and functional devices have been exploited to achieve water supply and management from water collection (rainwater, moist air or water vapor) to water purification (seawater desalination,3–5 filtration6–9 or adsorption10,11). Among them, fog droplets, which consist of abundant moisture in air and were estimated to be around 13
000 trillion liters, are a promising water resource to alleviate water shortage.12,13 With the development of bionics, researchers have discovered that a myriad of creatures in arid regions survive on the water collected from the fog moisture, including the Namib desert beetle (hydrophilic area for fog capture and hydrophobic area for fog transport),14 cactus (conical spines create the Laplace pressure force for directional fog transport),15 spider silk (spindle-knots, same as cactus conical spines),16–18etc. Inspired by these creatures, various artificial fog-harvesting devices (FHDs) have been designed and fabricated by adjusting the surficial chemistry or physical structure, which can supply water resources in the coastal regions (South America or Western Africa) with massive amounts of water vapor.19–31
In all of the previously developed FHDs, it is well known that rapid and efficient fog harvesting processes highly rely on the two key criteria: (1) droplet condensation and nucleation and (2) directional and spontaneous departure of the condensed water. The most common FHDs are focused on selective modification of surface wettability to mimic the hydrophilic–hydrophobic surface of Namib desert beetles.32,33 The hydrophilic area of FHDs can enhance the droplet condensation and nucleation processes while the hydrophobic area can accelerate the spontaneous departure of the condensed water. However, the separation of these two aspects reduces the advantages offered by textures. The high adhesive force of droplets in the hydrophilic area and the wettability gradient from the hydrophilic area to the hydrophobic area make it harder to depart from the hydrophilic area. Furthermore, the captured droplets condense to form a water film, which prevents the further capture process.34 To enhance the directional and spontaneous departure process of the condensed water, micro-/nano structures were integrated onto the FHD, because micro-/nanostructures enable the FHD to transport droplets efficiently under the difference of the Laplace pressure and surface free energy gradient. Inspired by cactus spines, Guo et al. used the electrochemical deposition method to fabricate cactus-like conical copper needles, which exhibited a higher fog harvesting rate.35 However, the preparation of copper needles requires sophisticated equipment, and fine copper needles are relatively fragile and difficult to apply in harsh environments.
Leaf veins with directional water transport capacity have also brought great inspiration to researchers.36,37 The wedge-shaped tracks of leaf veins can form a Laplace pressure force difference from bottom to tip, which accelerates the transport speed of droplets. Based on this, Liao's group reported wedge-shaped tracks on flexible substrates prepared by a magnetron sputtering coating method to mimic leaf veins, and the droplets presented a spontaneous transport behavior.37 Although the methods mentioned above had allowed successful preparation of the structure of leaf veins, it is far from enough to rely on this structure to harvest fog; the wettability of FHDs also plays an important role in the process of fog harvesting.
In contrast, as a mature and intelligent technology, the textile weaving method has evolved as a tool for manufacturing high-performance FHDs.38–40 In a recent report, Lai et al. adopted a weaving method to combine superhydrophilic (SHL) and superhydrophobic (SHB) yarns into a patterned fabric to mimic Namib desert beetles.41 However, this report only studied the effect of wettability on fog transport, while ignoring the fog transport ability of the physical structure. Besides, the resistance to the fog flow generated by the impermeable structure caused the fog flow to deviate, and reduced fog capture efficiency. Overall, it is still a challenge to coordinate the relationship between the wettability and structure of FHDs accurately.
In this work, the patterned wettability of Namib desert beetles has been proved to be effective for fog harvesting. In addition, a large number of small veins are distributed on the surface of leaves, and these veins can be divided into lateral veins and main veins. Lateral veins are cross-linked with the main vein in the middle to form a large number of wedge-shaped channels. The curvature gradient of wedge-shaped tracks, which leads to a Laplace pressure difference between the two opposite sides of the captured fog droplet, will drive the directional movement of captured droplets. Inspired by the wettability of Namib desert beetles and the wedge-shaped structure of leaf veins, a dual-biomimetic SHL–SHB tuck fabric (SHL–SHB@TF) was prepared, and its ability to capture and transport fog droplets was entirely replicated. SHL–SHB@TF was made of two kinds of yarns with completely opposite wettability (SHL yarns and SHB yarns) by using a fully automatic knitting machine. SHL yarns could capture fog droplets while SHB yarns could transport the captured droplets. In order to coordinate the work of the SHL and SHB areas, the yarns are arranged in a wedge-shaped structure similar to leaf veins. The droplets captured by the SHL yarn (at the lateral vein position) could move towards the SHB yarn (at the main vein position) under the Laplace pressure generated by the wedge-shaped tracks and then rolled down along the SHB yarn. We systematically investigated the influence of different structures and wettabilities on fog capture and droplet transportation efficiency. Compared with the widely used Raschel mesh, SHL–SHB@TF exhibited a relatively fast transport process (it takes only 7 min for the first droplet to fall from the surface) and an extremely excellent water harvesting rate (WHR: ∼5424 mg h−1 cm−2). Relying on the widely available textile materials and mature manufacturing technology, SHL–SHB@TF can realize large-scale production and application. It enables people in undeveloped regions to carry out low-cost, high-efficiency and large-scale fog harvesting.
2. Experimental
2.1 Materials
Polyester yarns (300 D) were commercially available from Shanghai Textile Industry. ZnO nanoparticles (≥99.0%), n-hexane (analytical reagent grade) and methyl orange (analytical reagent grade) were acquired from Aladdin Industrial Corporation. PDMS (Dow Corning 184A) and the curing agent (Dow Corning 184B) were purchased from Dow Corning.
2.2 Fabrication of tuck fabric
(1) Pre-treatment of polyester yarns.
Pristine polyester yarns were first cleaned with ethanol solution and deionized water. After cleaning, the yarns were put in an oven at 60 °C for 1 h to dry. The polyester yarns exhibit superhydrophilicity with a water contact angle (WCA) around 0° and thus are denoted as SHL yarns hereafter.
(2) Preparation of superhydrophobic polyester yarns.
The SHB modifier was prepared as follows: 20 g of PDMS (mpre-polymer
:
mcuring agent = 10
:
1) was added in 600 mL n-hexane. After PDMS was completely dissolved, 2 g of ZnO nanoparticles were dispersed in the above solution. The superhydrophobic polyester yarns were obtained by dipping the dried polyester yarns into the prepared modifier at a bath ratio of 1
:
10 for 20 min and dried at 60 °C for 1 h.41
(3) Preparation of patterned tuck fabric.
To mimic the structure of leaf veins, patterned tuck fabric was prepared by using an intelligent molding knitting technology with a Computerized Flat Knitting Machine (KSC-132D 14G). By inputting the drawing plan to the knitting machine, the position of different wettable yarns can be precisely adjusted and the desired SHL–SHB patterns can be formed on the surface of the tuck fabric. The spacing between knitting needles is 1.8 mm. For comparison, weft plain fabric without the leaf vein structure was designed. In this work, 7 different fabric samples were prepared by changing the wettability and structure of yarns (Fig. 1c), including SHL@WPF (weft plain fabric with a superhydrophilic arrangement), SHB@WPF (weft plain fabric with a superhydrophobic arrangement), SHB–SHL@WPF (weft plain fabric with an alternate superhydrophilic and superhydrophobic arrangement), SHL@TF (tuck fabric with a superhydrophobic arrangement), SHB@TF (tuck fabric with a superhydrophilic arrangement), SHB–SHL@TF (superhydrophilic tuck fabric with a superhydrophobic elongated loop) and SHL–SHB@TF (superhydrophobic tuck fabric with a superhydrophilic elongated loop).
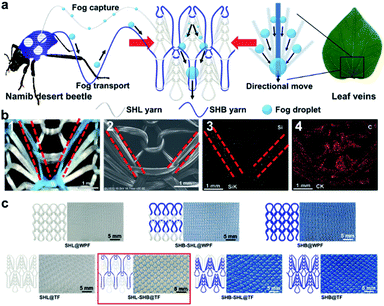 |
| Fig. 1 Design and characterization of SHL–SHB@TF. (a) A dual-biomimetic knitted fabric with similar wettability to Namib desert beetles and the structure to leaf veins. (b) Digital photo (1) and SEM image (2), distribution maps of Si (3) and C (4) of SHL–SHB@TF. (c) The schematic diagrams and optical images of the 7 prepared samples, including SHL@WPF, SHB–SHL@WPF, SHB@WPF, SHL–SHB@TF, SHL@TF, SHB–SHL@TF and SHB@TF. | |
2.3 Fog collecting measurement
The lab-made FHD (size: 60 × 60 × 60 cm3) was used to measure the water harvesting rate (WHR) of the as-prepared knitted fabric. In order to eliminate the influence of the external environment as much as possible, the entire device was placed in a large and sealed glass box. The diameter of the fog droplets generated by the humidifier is about 2–15 μm, which is similar to the fog droplets in the real world.42 The continuous fog flow is generated by the humidifier at a flow rate of ∼300 mL h−1 and a speed of 50 cm s−1. The deionized water was replaced with saturated salt water to test the salt fog harvesting ability of the sample. The samples were clamped by two iron stands and placed vertically 5 cm away from the humidifier. The efficiency of the FHD is characterized through the WHR according to eqn (1): |  | (1) |
where wt and w0 represent the weight of the collected water with and without the sample, respectively. S and t represent the effective area of the samples and testing time, respectively. To accurately evaluate the WHR of these samples, the amount of collected water in the container was weighed at one-hour intervals. Five measurements were carried out for each sample and the average value was taken as the final result.
2.4 Antibacterial adhesion test
Escherichia coli was adopted to evaluate the antibacterial ability of SHL–SHB@TF. The E. coli density of the bacterial solution was 1 × 105 CFU mL−1. The sample was placed in a 24-well TCPS plate and 1 mL of bacterial suspension was added. After shaking at 37 °C for 2 hours, the sample was gently rinsed with physiological saline three times to remove insufficiently adhered bacteria. Normal saline (1 mL) was added to the sample, followed by intermittent ultrasonic treatment for 50 s to peel off the adherent bacteria. The LB agar plate was coated with the solution (100 μL) which was obtained after ultrasonic treatment of the sample and incubated at 37 °C for 12 hours, and the number of bacterial colonies was counted.
2.5 Characterization
The morphology of the samples was examined by using a field emission scanning electron microscope (FESEM, Hitachi S-4800). Before the observation, the fibers were coated with a thin layer of Au to ensure the electrical conductivity of the samples. An energy-dispersive X-ray spectrometer (EDS) was used to analyse the surface elemental composition and distribution. The water contact angle (WCA) of the prepared samples was tested by winding the yarns on a glass slide. Then, using an optical contact angle meter system (Krüss DSA 100, Germany), the water droplet volumes were found to be 6 μL and 10 μL, respectively. The tensile mechanical properties of the fabric were tested on an YG026A electronic fabric strength meter (Changzhou Second Textile Machinery Co., Ltd, Changzhou, China). A Labsphere UV-1000F ultraviolet irradiation instrument was used to evaluate the UV resistance in the wavelength range of 250 nm to 450 nm. The detailed process of fog harvesting was recorded with an iPhone. A flowmeter (Testo 450-V1, Germany) was employed to measure the fog flow rate.
3. Results and discussion
3.1 Preparation and characterization of the dual-biomimetic knitted fabric
The dual-biomimetic knitted fabric was prepared by smart weaving technology. As shown in Fig. 1a, the unique design strategy was to combine patterned wettability of Namib desert beetles with wedge-shaped tracks of leaf veins together into a knitted fabric. In order to obtain and synergistically optimize the role of wettability and structure, SHL and SHB yarns were used during the knitting process and a novel SHL–SHB pattern was designed to mimic the wettability of Namib desert beetles and the leaf vein structure. Among these, the SHL yarns were distributed on both sides of the wedge-shaped tracks to capture fog droplets quickly, while the SHB yarns in the middle were used for droplet transportation. The unique structure (wedge-shaped tracks) could induce the droplets captured in the SHL area to flow to the SHB area. The original polyester yarn was composed of multiple fibers with a smooth surface, while the surface was superhydrophilic with a WCA = 0° (Fig. S1a and Movie S1†). After being soaked into the ZnO–PDMS solution, the as-prepared SHB yarn showed great superhydrophobicity and the WCA is as high as 153.0° (Fig. S1b†). Compared with the SEM image of the original SHL yarns, it could be observed that the surface of SHB yarns was rough and covered with plenty of nanoparticles (Fig. S1a and b†). Besides, the XPS spectra indicated that the original SHL yarns exhibited two peaks at 284.4 and 531.9 eV, ascribed to C 1s and O 1s, respectively (Fig. S1c†). As for the PDMS modified yarns, two new peaks at 101.6 and 1051.9 eV appeared, which correspond to Si 2p and Zn 2p, respectively. Taking advantage of mature textile technology, the tuck knitted fabric with patterned wettability and wedge-shaped tracks could be fabricated with ease, and the functions of the two mimicked creatures had also been successfully replicated (Fig. 1a). Through a traditional knitting method, the sample was prepared by interweaving SHL and SHB yarns on a fully automatic loom. Fig. S2† shows the drawing plan of SHL–SHB@TF. After inputting the drawing plan into the smart panel of the knitting machine, the knitting machine can automatically produce the sample. Movie S2† shows the rapid knitting process, and the as-prepared knitted fabric exhibited excellent stretching ability.
Fig. 1b presents the digital photos (1) and SEM images (2) of the as-prepared SHL–SHB@TF. The componential elements of SHL–SHB@TF were measured by EDS. Fig. 1b (3 and 4) show the distribution mapping images of elements Si and C; Si is one of the main elements of PDMS, and the distribution of Si is consistent with the distribution of SHB yarns in the optical photos (Fig. 1b (1)), which indicated that the sample had patterned wettability. The main element C was distributed on the entire yarn surface, and the morphology was similar to the wedge-shaped structure of leaf veins. Fig. S3† presents the quantitative analysis spectroscopy images of elements in the basic structure of SHL–SHB@TF by EDS, where the mass fractions of C, O, Si and Zn were 63.73%, 33.94%, 1.32% and 1.01%, respectively.
3.2 Fog capture and micro-droplet coalescence of different samples
The contact efficiency of the fog flow with the sample directly affects the fog capture ability of the sample. The contact efficiency is dependent on the shade coefficient (SC: the ratio of the projected area of the grid sample to the total area). In theory, the increase of SC of an FHD helps to improve the contact efficiency of the fog flow and FHD and enhance the fog capture ability of the FHD. However, the sample will have resistance to the fog flow, causing the fog flow starting to deviate, i.e. aerodynamic deviation (Fig. S4†).43 Therefore, in order to improve the fog capture ability of the FHD, it must have a suitable SC. The aerodynamic deviation of the fog flow is related to aerodynamic efficiency of the fog flow (ηa) and the deposition efficiency of fog droplets on mesh wires (ηd). The fog capture capacity of the sample can be calculated using η = ηa × ηd,28,44,45 where ηa can be expressed by eqn (2): | 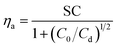 | (2) |
where C0 is the pressure drop coefficient of the sample, and Cd is the drag coefficient of an equivalently non-permeable screen. For WPF and TF with the same height and width, Cd remains the same.45 For yarns: | 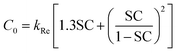 | (3) |
where kRe is an empirical correction factor, which is related to the diameter of the yarn. Because the WPF and TF were fabricated by using the same yarn, the kRe can be considered the same. Thus, C0 is only relevant to SC. The deposition efficiency (ηd) is directly related to the Stokes number (St): |  | (4) |
St is determined by the parameters including the density of water (ρwater), the radius of wires and fog droplets (rfog) and the flow rate (v0). Therefore, the WPF and TF have the same ηd values. | 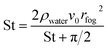 | (5) |
By theoretical calculations and analysis, the maximum capture efficiency of the sample can be obtained when the SC is nearly 0.55.45 The SC of TF and WPF was obtained by using ImageJ software to calculate the ratio of the non-blank area to the overall area. As shown in Fig. 2a, the SC of TF is 59.8%, which was higher than that of WPF (SC = 42.6%). Besides, the fog capture capacities of the seven prepared samples during 5 min were tested as demonstrated in Fig. 2b. As shown in Fig. 2b, SHL–SHB@WPF captured a small amount of droplets with a mass of 144 mg cm−2 after 5 min. For comparison, SHL–SHB@TF captured a larger amount of droplets with a mass of 290 mg cm−2. The results above indicated that tuck fabric exhibited a superior fog capture ability to WPF fabric due to its higher SC.
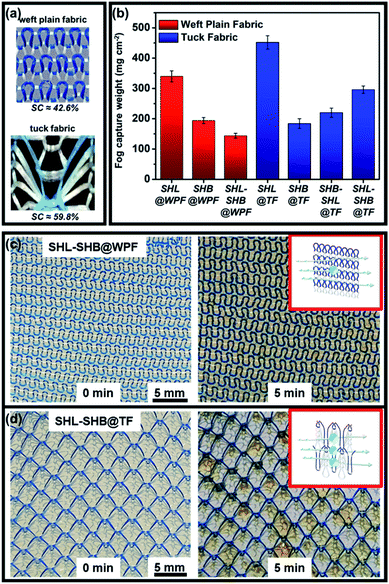 |
| Fig. 2 (a) Digital photo and the shade coefficient of SHL–SHB@WPF ((a) 43.6%) and SHL–SHB@TF ((b) 59.8%). (b) Fog capture weight of the 7 samples during 5 min. (c and d) Fog capturing photos during 5 min and the corresponding illustrations (insets) of SHL–SHB@WPF and SHL–SHB@TF. The water in the sprayer was dyed with methyl orange. | |
Moreover, the influences of the wettability of the samples on their fog capture ability and micro-droplet coalescence were characterized (Fig. S5†). Fig. S5a and b† show the fog capturing ability of SHL@TF and SHB@TF during 5 min. As expected, the surfaces with opposite wettability showed completely different fog capture effects. Obviously, all the droplets were captured by the SHL fabric which can be attributed to the capillary force of the SHL yarns. Therefore, the weight of the droplets captured on SHL@TF is as high as 452 mg cm−2. However, due to its superhydrophobicity, it was difficult for SHB@TF to capture droplets from the fog flow, so the fog capture ability was only 184 mg cm−2. Similarly, SHL@WPF and SHB–WPF showed similar behaviour, and the fog capture ability of the SHL@WPF and SHB@WPF was 342 mg cm−2 and 133 mg cm−2, respectively.
The results above indicated that the tuck fabric structure is more advantageous than weft plain fabric in terms of fog capturing. Besides, fog droplet capture ability on superhydrophilic surfaces was superior to that on the other surfaces, but such a surface wasn't beneficial for fog transportation. Moreover, the superhydrophilic/superhydrophobic anisotropic surface showed excellent fog capturing and transporting properties. More details will be discussed below.
3.3 Acceleration of droplet directional transportation
As mentioned in 3.2, the SHL area was conducive to increasing fog capture sites of the sample. However, in the fog harvesting process including fog capture and fog transport, the fog droplets captured by the SHL area always appear in the form of a water film, which inhibits the transportation of water droplets. Therefore, in order to achieve highly efficient fog harvesting performance, additional chemical modification and structural design of the FHD are required to enhance its capacity of directional transport of droplets. Here, inspired by the unique wettability of Namib desert beetles and wedge-shaped leaf veins, SHL–SHB@TF was fabricated. By applying the knitting technology, the wettability and structure of the sample had been systematically optimized, which greatly enhances its ability to directionally transport droplets. As shown in Fig. S6,† the prepared SHL–SHB@TF successfully imitated the characteristics of Namib desert beetle's wettability and leaf veins' wedge-shaped tracks. Lateral veins on both sides were composed of SHL yarns, and the main veins in the middle were composed of SHB yarns. This ingenious combination ensures a larger SHL area for fog capturing. A large number of wedge-shaped channels formed by SHL yarns on both sides ensure that the captured droplets will directionally move to the middle SHB area under the Laplace pressure gradient generated by wedge-shaped tracks. Then, the captured droplets will slide down along the SHB yarns. This novel strategy of integrating the SHL yarns and SHB yarns into a plane by knitting technology resulted in achieving a leaf vein-like wedge shape. The combination of wettability and structure significantly accelerates the coalescence, directional movement and slide down process of droplets.
A large number of wedge-shaped tracks were distributed on SHL–SHB@TF, enabling it to transport captured droplets directionally. To explore the relationship between the wedge-shaped tracks and droplet transportation process, potential mechanisms and theoretical models were proposed. As shown in Fig. 3, the curvature gradient of the wedge-shaped tracks resulted in a Laplace pressure difference on the two ends of the droplet. The Laplace pressure gradient combined with the difference between the liquid–gas interfacial tensions on the two ends of the droplet drives the droplet to move directionally toward the tip of wedge-shaped tracks.46,47 The relationship between the Laplace pressure gradient and the radius of curvature can be expressed by using the Laplace Young equation:48
| 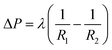 | (6) |
where Δ
P is the pressure difference acting on both sides of the droplet,
λ is the interfacial tension of droplet, and
R1 and
R2 are transverse radii at the two opposite menisci, respectively. The difference value of the radius of curvature between
R2 and
R1 can form the positive pressure difference, which contributes to the directional transportation of the droplets among the wedge-shaped tracks. Meanwhile, Movie S3
† further proves that the droplets moved toward the tip of wedge-shaped tracks.
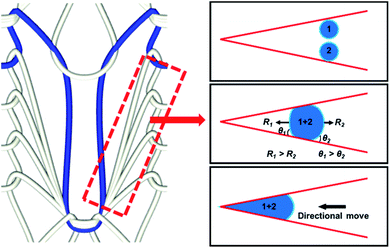 |
| Fig. 3 Schematic diagram of SHL–SHB@TF and force analysis of fog droplets on two adjacent fibers. | |
However, the Laplace pressure generated by the wedge-shaped track in different directions is also different. We have systematically studied the ability to transport fog droplets on multiple tracks in different directions, including downward (Fig. 4a), upward (Fig. 4b) and rightward (Fig. 4c). Since the droplet transport behavior of the leftward sample was similar to that of the rightward, there was no additional discussion on the leftward sample. As can be seen from Fig. 4a, SHL–SHB@TF with downward wedge-shaped tracks creates the top-down Laplace pressure force combined with gravity which could simultaneously drive water droplets to roll down along the yarns. However, with respect to SHL–SHB@TF placed upward or rightward, the direction of the Laplace pressure generated by the wedge-shaped tracks was different from the direction of gravity, causing slower transportation velocities of the condensed droplets. For the upward SHL–SHB@TF, wedge-shaped tracks generate the bottom-up Laplace pressure force that is opposite to the gravity action, which severely slowed down the rate of droplet falling (Fig. 4b); while for SHL–SHB@TF placed rightward, half of the wedge-shaped tracks face upwards and half face downwards. The downwardly facing wedge-shaped tracks produced the same Laplace pressure as the direction of gravity, while for the upwardly facing ones it was the opposite. The droplets converge on wedge-shaped tracks that are consistent with the direction of gravity, while no droplet was collected on the surface of the wedge-shaped tracks opposite to it (Fig. 4c).
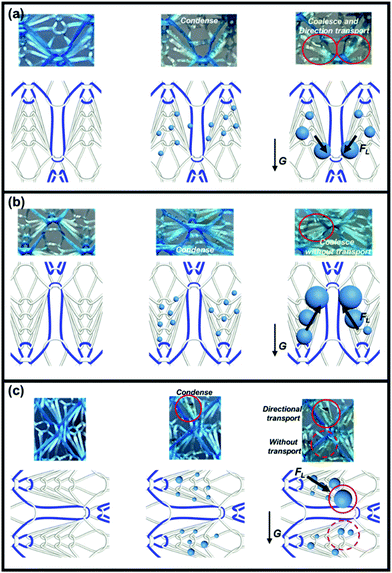 |
| Fig. 4 The fog harvesting process and corresponding mechanism diagrams of wedge-shaped tracks placed at different positions, including downward (a), upward (b), and rightward (c). The black arrow is the droplet moving direction. The solid circle is the area where the droplets converge, and the dashed circle is the opposite. The water was stained with methyl orange. | |
3.4 Fog harvesting measurements
The dynamic fog harvesting process of these 7 samples was recorded with digital photography, which can help to further understand the influence of different wettabilities and wedge-shaped tracks on fog harvesting (Fig. 5). As shown in Fig. 5, during the fog harvesting process, the surfaces of SHL@WPF (Fig. 5a) and SHL@TF (Fig. 5d) were covered with a water film, which was caused by their water affinity. In contrast, there were few water droplets on the surface of SHB@WPF (Fig. 5b) and SHB@TF (Fig. 5e) because it was difficult to capture the droplets from the air due to their intrinsic hydrophobicity. The above two phenomena were not conducive to continuous fog harvesting. As shown in Fig. 5c and g, a large number of droplets were distributed on the surface of SHL–SHB@WPF and SHL–SHB@TF. Owing to the SHB yarn, these droplets do not form a larger water film, which was the ideal harvesting state. For SHL–SHB@WPF and SHL–SHB@TF, the SC difference resulted in more fog droplets being captured on SHL–SHB@TF.
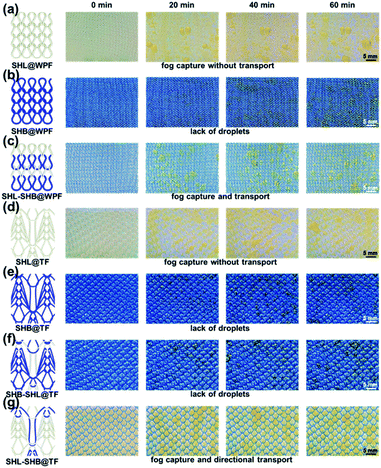 |
| Fig. 5 Scheme and fog harvesting dynamics process of SHL@WPF, SHB@WPF, SHL–SHB@WPF, SHL@TF, SHB@TF, SHB–SHL@TF and SHL–SHB@TF from 0 min to 60 min (a–g). The water was stained with methyl orange. | |
Fig. 6a displays a lab-made FHD, including a humidifier, a container and an iron support stand, and the as-prepared sample is fixed on the iron support stand; the fog harvesting process includes fog capturing and fog transportation. After fog harvesting, the droplets will be collected in the container below.
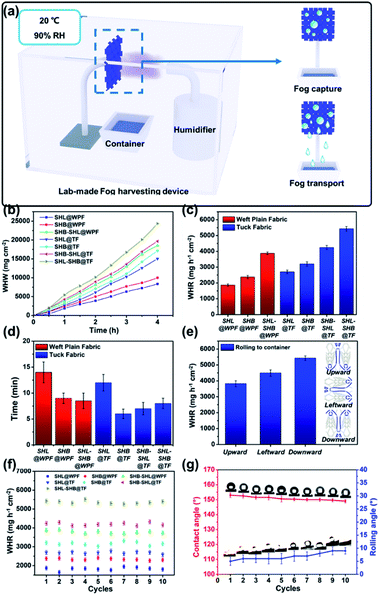 |
| Fig. 6 (a) The lab-made fog harvesting device including a humidifier, a container and an iron support stand with a sample. (b) Water harvesting weight tests of the 7 samples during a period of 4 h. (c) Water harvesting rate of the 7 samples. Insets are optical images of samples. (d) The time when the first drop captured by different samples rolls off. (e) Water harvesting rate of SHL–SHB@TF in different tilt positions. (f) Water harvesting rate of the 7 samples for 10 cycles of the fog-harvesting process. (g) Contact angle and rolling angle of the SHB area for 10 cycles of the fog-harvesting process. The sizes of all samples are 5 cm × 5 cm. | |
To further clarify the impact of various wettabilities and structures on fog capture and droplet transportation, all of the as-prepared samples were used for the fog harvesting process for 60 min. As depicted in Fig. 6b, it was obvious that the fog harvesting weight of SHL–SHB@TF was significantly higher than that of the other samples. After 4 h of the fog harvesting process, the WHR value of SHL–SHB@TF was as high as 24
347 mg cm−2. As shown in Fig. 6c, samples with a similar wettability and different structures showed a prominent difference in fog harvesting. The WPF samples (blue column, SHL@WPF: 1866 mg h−1 cm−2, SHB@WPF: 2374 mg h−1 cm−2 and SHL–SHB@WPF: 3874 mg h−1 cm−2) showed a lower WHR level than TF samples (red column, SHL@TF: 2700 mg h−1 cm−2, SHB@TF: 3200 mg h−1 cm−2 and SHL–SHB@TF: 5424 mg h−1 cm−2). Such a significant difference between WPF samples and TF samples could be attributed to TF samples with a proper SC compared to WPF samples (mentioned in 3.2). In addition, for TF samples with the same SC, wettability was the key factor affecting the WHR. The behaviors of droplet harvesting on samples with different wettabilities are demonstrated in Movie S4.† Among the various wettabilities of TF samples, SHL@TF and SHB@TF exhibited lower WHR values of approximately 2700 mg h−1 cm−2 and 3200 mg h−1 cm−2. As a comparison, the hybrid SHL and SHB surfaces have completely higher WHR values (SHB–SHL@TF: 4240 mg h−1 cm−2 and SHL–SHB@TF: 5424 mg h−1 cm−2). The SHL@TF and SHB@TF samples could not achieve excellent fog harvesting properties because the completely superhydrophilic surface exhibited prominent fog droplet capturing ability but failed to transport the droplets actively, while for the SHB sample the situation was opposite. The superhydrophilic/superhydrophobic anisotropic surfaces (SHL–SHB@TF and SHB–SHL@TF) exhibited better properties due to the synergistic effect of fog droplet capturing and transportation. However, the difference in WHR values for SHL–SHB@TF and SHB–SHL@TF is ascribed to the ratio and distribution of the SHL area and the SHB area on both surfaces. SHL–SHB@TF had larger SHL areas that could help it capture more fog droplets, and there was an elongated SHB channel (blue yarns) in the middle of the sample to ensure that the droplet transportation occurs rapidly. Besides, the fog harvesting process of SHL–SHB@TF is provided in Movie S5.†
The time when the first droplet rolls off from the samples is shown in Fig. 6d. Due to the lack of active transportation and directional Laplace pressure difference, it takes 14 min and 12 min for SHL@WPF and SHL@TF to collect the first droplet, respectively. In contrast, SHL–SHB@TF with SHL–SHB patterned wettability and wedge-shaped tracks only takes 8 min, which indicates that such a unique structure with anisotropic wettability was more favorable for fog harvesting. Fig. 6e shows the WHR of SHL–SHB@TF in three different tilt positions, which had proved that SHL–SHB@TF in the downward position achieved a better WHR. Obviously, SHL–SHB@TF in the downward position meant that the tip of the wedge-shaped tracks faces downward, which created a downward Laplace pressure difference to accelerate the transport process. A brief report of the WHR of the 7 mentioned samples is presented in Table S1.† In addition, the long-term stability of the as-prepared samples was characterized for a 10 cycle fog harvesting test and each cycle test time was 1 h, and between two cycles, the samples were dried in a 100 °C oven. After a long period of continuous harvesting and multiple cycles of testing, the WHR of SHL–SHB@TF decreased slightly (from 5424 mg h−1 cm−2 to 5264 mg cm−2), but still remained almost constant and significantly higher than that of other samples (Fig. 6f). Besides, the wettability of the SHB area was also tested during 10 cycles (Fig. 6g). When exposed to fog for a long time, its hydrophobic properties will inevitably decrease. The contact angle of the hydrophobic area decreased from the initial 153.0° to about 149.5°, and the rolling angle increased from 5° to 9°, but it still maintained good hydrophobic properties. The above results indicated that under the dual effects of wettability and the wedge-shaped structure, SHL–SHB@TF presents an excellent WHR (≈5424 mg h−1 cm−2). In addition, after a long period of continuous collection and multiple cycles of testing, the WHR and wettability of SHL–SHB@TF remained at the highest level, showing the potential for long-term application.
3.5 Mechanical properties and production cost of SHL–SHB@TF
The tensile mechanical property of the FHD is another important parameter for effective fog harvesting. Some literature studies claimed that FHDs lack rational mechanical design and would be damaged frequently during the fog harvesting process because they cannot withstand the strong wind.49 As shown in Fig. S8,† a simple tensile test was performed on WPF (Raschel mesh: traditionally used for fog harvesting) and TF. The two knitted fabrics (WPF and TF) were composed of many curved loops. Once stretched, the loops were first stretched into a straight status, so their stretched lengths could be longer than that of normal woven fabric. In this work, each loop on WPF was composed of only 2 wires, while 5 wires were for TF. The maximum breaking strengths of TF and WPF were 624.42 N m−1 and 276.54 N m−1 when the elongation was 50%, respectively. Such excellent mechanical properties undoubtedly met the requirement of durable FHDs in real-world application.
Moreover, the production cost of the fog harvesting device is a vital factor for practical large-scale application in the arid area. After evaluating the cost of SHL–SHB@TF, we concluded that the total cost was less than 1 $ for SHL–SHB@TF with 1 m2 area (the exchange rate was based on the value on May 16, 2021). A brief introduction and comparison of some advanced FHDs, as well as their fog harvesting rate and preparation cost are shown in Table S2.† Compared with the expensive 3D printing method (about 50 $ per m2, the price was based on https://Taobao.com), SHL–SHB@TF prepared based on the mature textile manufacturing technology, showed more potential practical applications.
3.6 Anti-aging and antibacterial ability of SHL–SHB@TF
The working environment of SHL–SHB@TF is harsh and moist, resulting in the possibility of aging and bacterial reproduction. Fig. S8† shows the long-time continuous fog harvesting test (12 h) of original SHL–SHB@TF, SHL–SHB@TF after 12 h UV irradiation, and salt fog harvesting test of SHL–SHB@TF. Based on the stability of the PDMS coating, the fog harvesting efficiency of the samples under these three conditions was almost the same in 12 hours of continuous fog harvesting test, more than 72
000 mg cm−2 (Fig. S8a†). Meanwhile, the surface morphology, chemical composition and contact angle of the samples after fog harvesting test were characterized. Compared with the original SHB yarn, the morphology, chemical composition and the contact angle of the SHB yarn after 12 h of continuous fog harvesting test, 12 h UV irradiation and salt fog harvesting test hardly changed (Fig. S8b–e†).
Additionally, the wettability changes of the yarns during the fog harvesting process were tested. Since the tiny fog droplets can infix into the space between those micro-fibers, the hydrophobicity of the SHB yarn decreased with time. As shown in Fig. S9,† the contact angle and the rolling angle of the SHB yarn changed from 153.6° and 5° (0 min) to 135.2° and 19° (90 min), respectively. However, the yarn remained hydrophobic, and since the sample was placed vertically, captured fog droplets can still slide off the surface, which proved the possibility of long-time continuous fog harvesting.
In a high-humidity environment, there is a possibility of bacterial proliferation. Cotton fabric and SHL–SHB@TF were employed to evaluate the ability to resist the adhesion of E. coli (Fig. S10†). Upon overnight co-incubation, plenty of E. coli colonies grown on the cotton fabric, corresponding to approximately 542 bacteria, adhered in a 10 cm2 area on the LB agar plate. In contrast, only a small number of E. coli colonies adhered on the SHL–SHB@TF group, about 289 bacteria. The results showed that SHB–SHL@TF exhibited good antibacterial properties. The capacity of SHL–SHB@TF to inhibit bacterial adhesion can be related to its weak hygroscopicity, the droplets would not adhere to the fiber for a long time, which reduces the possibility of bacterial proliferation.
4. Conclusions
Inspired by the unique fog harvesting strategy of Namib Desert beetles and leaf veins, a knitted fabric (SHL–SHB@TF) with hybrid wettability and wedge-shaped tracks was prepared via a mature textile manufacturing technology, which showed huge prospects in lab and practical applications. Due to the advantages of the mature manufacturing technology, the anisotropic wettability and structure can be controlled and designed by using superhydrophilic and superhydrophobic yarns. Owing to the reasonable distribution of SHL and SHB areas and well-designed wedge-shaped tracks, SHL–SHB@TF exhibited superior fog harvesting properties. SHL–SHB@TF showed the highest WHR value of 5424 mg h−1 cm−2, and the wettability (static WCA and dynamic SA) and fog harvesting properties almost did not change after multiple cycles. The fog harvesting mechanism was deeply discussed. In addition, knitted SHL–SHB@TF exhibited excellent mechanical stretching ability (F = 624.42 N m−1) and durability. The efficiency was stable even after 10 cycles and 12 h continuous fog harvesting. Thus, this high-efficiency, low-cost fog harvesting device based on the mature textile manufacturing technology has great application prospects for large-scale fog harvesting, especially in arid and undeveloped regions.
Conflicts of interest
There are no conflicts to declare.
Acknowledgements
This work was supported by the Natural Science Foundation of Jiangsu Province (BK20200607), Fundamental Research Funds for the Central Universities (JUSRP11916, JUSRP52007A and JUSRP22040). We also thank the International Joint Research Laboratory for Eco-Textile Technology (IJRLETT) at Jiangnan University for supporting in the course of research.
Notes and references
- M. M. Mekonnen and A. Y. Hoekstra, Sci. Adv., 2016, 2, e1500323 CrossRef PubMed.
- M. S. Mauter, I. Zucker, F. Perreault, J. R. Werber, J.-H. Kim and M. Elimelech, Nat. Sustain., 2018, 1, 166–175 CrossRef.
- S. Gao, X. Dong, J. Huang, J. Dong, F. D. Maggio, S. Wang, F. Guo, T. Zhu, Z. Chen and Y. Lai, Glob. Chall., 2019, 3, 1800117 CrossRef PubMed.
- R. Zhu, M. Liu, Y. Hou, D. Wang, L. Zhang, D. Wang and S. Fu, Chem. Eng. J., 2021, 423, 129099 CrossRef CAS.
- T. M. Subrahmanya, P. T. Lin, Y.-H. Chiao, J. Widakdo, C.-H. Chuang, S. F. Rahmadhanty, S. Yoshikawa and W.-S. Hung, J. Mater. Chem. A, 2021, 9, 7868–7880 RSC.
- K. N. Heck, S. Garcia-Segura, P. Westerhoff and M. S. Wong, Acc. Chem. Res., 2019, 52, 906–915 CrossRef CAS PubMed.
- X. Dong, S. Gao, J. Huang, S. Li, T. Zhu, Y. Cheng, Y. Zhao, Z. Chen and Y. Lai, J. Mater. Chem. A, 2019, 7, 2122–2128 RSC.
- J. Zhang, J. Song, L. Liu, P. Zhang, Y. Si, S. Zhang, J. Yu and B. Ding, J. Mater. Chem. A, 2021, 9, 15310–15320 RSC.
- J. Zhang, F. Zhang, J. Song, L. Liu, Y. Si, J. Yu and B. Ding, J. Mater. Chem. A, 2019, 7, 20075–20102 RSC.
- X. Zhou, P. Zhang, F. Zhao and G. Yu, ACS Mater. Lett., 2020, 2, 1419–1422 CrossRef CAS.
- Y. Shi, O. Ilic, H. A. Atwater and J. R. Greer, Nat. Commun., 2021, 12, 2797 CrossRef CAS.
- D. J. Jacob, R. F. T. Wang and R. C. Flagan, Environ. Sci. Technol., 1984, 18, 827–833 CrossRef CAS.
- Q. Schiermeier, Nature, 2014, 510, 326–328 CrossRef CAS PubMed.
- A. R. Parker and C. R. Lawrence, Nature, 2001, 414, 33–34 CrossRef CAS PubMed.
- J. Ju, H. Bai, Y. Zheng, T. Zhao, R. Fang and L. Jiang, Nat. Commun., 2012, 3, 1247 CrossRef PubMed.
- L. Xiao, G. Q. Li, Y. Cai, Z. H. Cui, J. H. Fang, H. Cheng, Y. B. Zhang, T. Duan, H. B. Zang, H. W. Liu, S. M. Li, Z. S. Ni and Y. L. Hu, Chem. Eng. J., 2020, 399, 125139 CrossRef CAS.
- Y. Zheng, H. Bai, Z. Huang, X. Tian, F. Q. Nie, Y. Zhao, J. Zhai and L. Jiang, Nature, 2010, 463, 640–643 CrossRef CAS.
- H. Dong, N. Wang, L. Wang, H. Bai, J. Wu, Y. Zheng, Y. Zhao and L. Jiang, ChemPhysChem, 2012, 13, 1153–1156 CrossRef CAS PubMed.
- H. Fan and Z. Guo, J. Colloid Interface Sci., 2021, 591, 418–428 CrossRef CAS PubMed.
- X. Tang, H. Liu, L. Xiao, M. Zhou, H. Bai, J. Fang, Z. Cui, H. Cheng, G. Li, Y. Zhang and M. Cao, J. Mater. Chem. A, 2021, 9, 5630–5638 RSC.
- M. Zhou, X. He, X. Wu, L. Xiao, Z. Cui, X. Tang, L. Guo, S. Liu, H. Liu, Y. Zhu, Y. Zhang, G. Li and J. Zhu, Appl. Mater. Today, 2020, 21, 100851 CrossRef.
- M. Wu, R. Li, Y. Shi, M. Altunkaya, S. Aleid, C. Zhang, W. Wang and P. Wang, Mater. Horiz., 2021, 8, 1518–1527 RSC.
- J. Li, C. Gao, W. Pei, Z. Guo, L. Zhong, Y. Liu, S. Wang, Y. Hou and Y. Zheng, ACS Appl. Mater. Interfaces, 2020, 12, 48049–48056 CrossRef CAS.
- C. Li, Y. Liu, C. Gao, X. Li, Y. Xing and Y. Zheng, ACS Appl. Mater. Interfaces, 2019, 11, 4507–4513 CrossRef CAS PubMed.
- R. Feng, F. Song, C. Xu, X.-L. Wang and Y.-Z. Wang, Chem. Eng. J., 2021, 422, 130119 CrossRef CAS.
- M. Yu, M. Liu, D. Zhang and S. Fu, Chem. Eng. J., 2021, 422, 130113 CrossRef CAS.
- T. Zhu, Y. Cheng, J. Huang, J. Xiong, M. Ge, J. Mao, Z. Liu, X. Dong, Z. Chen and Y. Lai, Chem. Eng. J., 2020, 399, 125746 CrossRef CAS.
- W. Shi, M. J. Anderson, J. B. Tulkoff, B. S. Kennedy and J. B. Boreyko, ACS Appl. Mater. Interfaces, 2018, 10, 11979–11986 CrossRef CAS PubMed.
- Y. Su, L. Chen, Y. Jiao, J. Zhang, C. Li, Y. Zhang and Y. Zhang, ACS Appl. Mater. Interfaces, 2021, 13, 26542–26550 CrossRef CAS PubMed.
- Y. Yamada, E. Sakata, K. Isobe and A. Horibe, ACS Appl. Mater. Interfaces, 2021, 13, 35079–35085 CrossRef CAS PubMed.
- R. Hu, N. Wang, L. Hou, Z. Cui, J. Liu, D. Li, Q. Li, H. Zhang and Y. Zhao, J. Mater. Chem. A, 2019, 7, 124–132 RSC.
- H. Liu, W.-Y. Xie, F. Song, X.-L. Wang and Y.-Z. Wang, Chem. Eng. J., 2019, 369, 1040–1048 CrossRef CAS.
- W. Huang, X. Tang, Z. Qiu, W. Zhu, Y. Wang, Y. L. Zhu, Z. Xiao, H. Wang, D. Liang, J. Li and Y. Xie, ACS Appl. Mater. Interfaces, 2020, 12, 40968–40978 CrossRef CAS PubMed.
- J. Feng, L. Zhong and Z. Guo, Chem. Eng. J., 2020, 388, 124283 CrossRef CAS.
- H. Zhou, X. Jing and Z. Guo, Langmuir, 2020, 36, 6801–6810 CrossRef CAS PubMed.
- H. G. Andrews, E. A. Eccles, W. C. Schofield and J. P. Badyal, Langmuir, 2011, 27, 3798–3802 CrossRef CAS.
- J. Lin, X. Tan, T. Shi, Z. Tang and G. Liao, ACS Appl. Mater. Interfaces, 2018, 10, 44815–44824 CrossRef CAS.
- P. Zhu, R. Chen, C. Zhou, Y. Tian and L. Wang, Chem. Eng. J., 2021, 415, 128944 CrossRef CAS.
- J. Knapczyk-Korczak, P. K. Szewczyk, D. P. Ura, R. J. Bailey, E. Bilotti and U. Stachewicz, Sustainable Mater. Technol., 2020, 25, e00191 CrossRef CAS.
- X. Li, Y. Liu, H. Zhou, C. Gao, D. Li, Y. Hou and Y. Zheng, ACS Appl. Mater. Interfaces, 2020, 12, 5065–5072 CrossRef CAS PubMed.
- Z. Yu, H. Zhang, J. Huang, S. Li, S. Zhang, Y. Cheng, J. Mao, X. Dong, S. Gao, S. Wang, Z. Chen, Y. Jiang and Y. Lai, J. Mater. Sci. Technol., 2021, 61, 85–92 CrossRef.
- H. Di, Z. Wang and D. Hua, Opt. Express, 2019, 27, A890–A908 CrossRef CAS PubMed.
- J. Park, C. Lee, S. Lee, H. Cho, M.-W. Moon and S. J. Kim, Soft Matter, 2021, 17, 136–144 RSC.
- M. Damak and K. K. Varanasi, Sci. Adv., 2018, 4, eaao5323 CrossRef.
- J. d. D. Rivera, Atmos. Res., 2011, 102, 335–342 CrossRef.
- X. Ma, M. Cao, C. Teng, H. Li, J. Xiao, K. Liu and L. Jiang, J. Mater. Chem. A, 2015, 3, 15540–15545 RSC.
- H. Dong, Y. Zheng, N. Wang, H. Bai, L. Wang, J. Wu, Y. Zhao and L. Jiang, Adv. Mater. Interfaces, 2016, 3, 1500831 CrossRef.
- E. Lorenceau and D. Quéré, J. Fluid Mech., 2004, 510, 29–45 CrossRef.
- J. d. D. Rivera and D. Lopez-Garcia, Atmos. Res., 2015, 151, 250–258 CrossRef.
Footnote |
† Electronic supplementary information (ESI) available. See DOI: 10.1039/d1ta08295g |
|
This journal is © The Royal Society of Chemistry 2022 |
Click here to see how this site uses Cookies. View our privacy policy here.