DOI:
10.1039/D1SM01540K
(Review Article)
Soft Matter, 2022,
18, 10-18
Pickering emulsions stabilized by metal–organic frameworks, graphitic carbon nitride and graphene oxide
Received
28th October 2021
, Accepted 8th November 2021
First published on 16th November 2021
Abstract
Pickering emulsion is a heterogeneous system consisting of at least two immiscible liquids, which are stabilized by solid particles, in which organic solvent or water is dispersed into other phase in form of micrometre-sized droplets. Compared to traditional emulsions stabilized by surfactant, solids are cheap and can be easily separated and recycled by centrifugation or filtration after use. Moreover, the properties of Pickering emulsions can be adjusted by using different types of solid particles. Up to now, Pickering emulsions have been applied in a wide range of areas such as material science and catalysis. Here we review recent studies on Pickering emulsions stabilized by metal–organic framework, graphitic carbon nitride and graphene oxide.
1 Introduction
Macro-emulsions are mixtures of two immiscible liquids (usually water and an organic solvent).1 Different from the thermodynamically stable micro-emulsions, of which the droplets are smaller than 100 nm, macro-emulsions are thermodynamically unstable and have larger droplets in the range of 0.1–10 μm. Generally, macro-emulsions are stabilized by amphiphilic materials like surfactants. Alternatively, colloid particles could be used to stabilize two immiscible fluids to form macro-emulsions, which are called Pickering emulsions (PEs).2,3 Compared with the traditional emulsions stabilized by a surfactant, PEs have many advantages, such as low cost, easy separation and recycling of solid, good stability and biocompatibility.4–6 Therefore, PEs have broad applications in the fields of food, cosmetics, petroleum, pharmacy, and biomedicine, interfacial catalysis, fabrication of superstructures,4,7,8etc. The inherent properties of solid particles can affect the preparation, characteristics and application of PEs.9–12 Generally, stabilization of solid particles at the interface is considered to be directed by particle wettability. Only particles with intermediate hydrophilicity can readily accumulate at the oil–water interface and stabilize emulsions. Oil-in-water emulsions are usually produced by solid particles with more hydrophilic surfaces, while particles with more hydrophobic surfaces are conducive to the formation of water-in-oil emulsions. In earlier work, silica (SiO2),13,14 polymers,15,16 metal oxides17 and carbon black18 are the mostly adopted emulsifiers to stabilize PEs. Recently, many efforts have been devoted to the construction of PEs stabilized by metal–organic frameworks (MOFs), graphitic carbon nitride (g-C3N4) and graphene oxide (GO). Owing to the functionalities and broad utilization of these materials in different fields, the PEs stabilized by them have unique properties and largely expanded applications. In this review, we discuss the recent progress on the PEs stabilized by MOFs, g-C3N4 and GO.
2 Pickering emulsions stabilized by MOFs
MOFs are composed of metal ions or metal clusters and organic ligands, which have regular and tunable porosity, a huge surface19 and wide applications in gas storage,20–22 catalysis,23 sensors24 and drug delivery.25 Furukawa and coworkers found that MOF crystallites could assemble at the air–liquid interface using the Langmuir–Blodgett technique.26 Granick et al. discovered that MOFs can form ordered supra-particle assemblies from colloidal solution.27 Due to the hybrid composition, mid-range zeta potential and facile surface functionalization, MOF particles are highly suitable for assembly at liquid–liquid interfaces to form PEs. The emulsions stabilized by MOFs can be divided into three kinds according to the liquids used, i.e., oil–water emulsions, ionic liquid (IL)–water emulsions and CO2–water emulsions.
2.1 Oil–water emulsions stabilized by MOFs
ZIF-8 is a tetrahedrally connected framework with the composition Zn(2-MeIm)2 (2-MeIm = 2-methylimidazole) and sodalite topology that displays high water stability and flexible sorption behaviour. The aqueous dispersion of ZIF-8 colloids has a zeta potential of 23.7 ± 0.8. Bradshaw and coworkers firstly used ZIF-8 to stabilize the dodecane-in-water emulsion, from which hollow ZIF-8/polystyrene microcapsules were obtained.28 In 2013, Williams and coworkers reported that Cu-BTC (BTC = 1,3,5-benzenetricarboxylate) particles, with a diameter of ∼291 nm, a polydispersity of 0.113 and a zeta potential of −0.3 mV, could stabilize both water-in-oil and oil-in-water emulsions by adjusting the ratio of oil to water.29
In 2016, Zhang and coworkers reported the utilization of Cu3(BTC)2 for emulsifying diethyl ether and water.30 The emulsion was formed by stirring a mixture of water, diethyl ether and Cu3(BTC)2 at room temperature. As the diethyl ether volume fraction is in the range of 0.29–0.57, the emulsion separates into a lower phase of excess water and an upper emulsion (Fig. 1a–c). Interestingly, the upper emulsion presents a gel-like or semi-solid appearance, which is a key character for the formation of high internal phase emulsions (HIPEs). The microstructures of the HIPEs were characterized by confocal laser scanning microscopy (CLSM). The droplets are polyhedral and squeeze among each other, which are bridged by Cu3(BTC)2 nanoparticles (Fig. 1d–f). This morphology is characteristic of HIPE formation, being the best geometric conformation to achieve the most dense and optimized close-packed structure. The CLSM images reveal that these HIPEs are diethyl ether-in-water type, that is, diethyl ether makes up the droplet, while water is the continuous phase. The average droplet sizes are 18 μm, 8 μm and 5 μm for the three HIPEs (Fig. 1d–f), i.e., the droplet size decreases with decreasing initial diethyl ether volume fraction of the emulsions. The HIPE stabilized by Cu3(BTC)2 is very stable and can keep stability for more than one month. From such a MOF-stabilized HIPE, the ultralight metal–organic aerogel was obtained after removing the two liquids, of which the density is as low as 0.01
g cm−3. The porosities and structures of the ultralight metal–organic aerogels could be easily tuned.
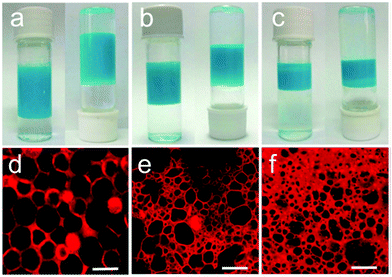 |
| Fig. 1 Characterization of Cu3(BTC)2-stabilized HIPEs. (a–c) Photographs of the emulsions stabilized by Cu3(BTC)2 with the initial diethyl ether volume fractions of 0.57, 0.43 and 0.29, respectively. (d–f) The corresponding CLSM images of the above HIPEs. Scale bars, 20 μm.30 Copyright 2016 Nature Publishing Group. | |
Zhu et al. studied the emulsification of UiO-66 particles, with a zeta potential of −30.34 ± 0.6 mV at room temperature in water, for water and oil (e.g., dodecane, hexane, toluene and cyclohexane).31 The oil-in-water HIPE was formed, which could serve as a template for the synthesis of 3D hierarchical porous MOF monoliths with an ultralow density (as low as 12 mg cm−3). The Jiang group utilized enzyme-conjugated ZIF-8 particles as an efficient and stable emulsifier for stabilizing the n-heptane-in-water emulsion.32 This MOF-stabilized PE was used for interfacial catalysis, which showed enhanced catalytic activity as a result of much lower external and internal diffusional resistances. After the reaction, the catalyst was simply recycled and positioned at the water–oil interface via relatively low-speed centrifugation. Thus, the substrate (in the oil phase), product (in the water phase) and catalyst (in the solid phase) could be easily separated.
In 2017, the Zhang group studied the emulsification of UiO-66-NH2 for cyclohexane and water.33 The cyclohexane-in-water emulsion was formed, of which the droplet size decreases with increasing UiO-66-NH2 concentration (2–25 μm). Interestingly, the amphiphilicity of UiO-66-NH2 can be changed from hydrophilic to hydrophobic by the cyclohexane–water interfacial assembling route. The modified UiO-66-NH2 particles have shown predominantly improved adsorption capacity for dyes in an organic solvent. The Zhang group also found that the UiO-67 particles could assemble at the water–oil interface as a stabilizer.34 They proposed the hydrolysis of the titanium precursor in the UiO-67-stabilized emulsion for the synthesis of the TiO2/UiO-67 composite. By such a route, the hollow capsules assembled by UiO-67 nanorods, which are decorated with highly dispersed ultra-small TiO2 nanoparticles, were produced. The as-synthesized TiO2/UiO-67 composite shows high catalytic activity for photocatalytic CO2 reduction. Up to now, different materials with the designed compositions and structures have been synthesized by utilizing MOF-stabilized PEs, including 3D hierarchical porous UiO-66 monoliths,35 ZIF-8/poly(hexadecyl acrylate),36 ZIF-8/polystyrene, UiO-66/polystyrene, MIL-101-Cr/polystyrene,37 and the meso–macroporous ZIF-8 platform.38
Moreover, the oil–water PEs stabilized by MOFs have found applications in the biological field. Jin and coworkers formed an emulsion stabilized by a nano-cyclodextrin MOF, based on less toxic alkaline earth metals and food-grade oligosaccharides.39 Luo and coworkers used Candida rugosa loaded ZIF-8 to stabilize the n-heptane-in-water emulsion for improved biocatalysis.40
2.2 IL–water emulsions stabilized by MOFs
ILs are organic salts with a wide liquid range, high thermal and chemical stability and high solubility,41,42 which have many applications in different areas, such as in material synthesis,43 catalysis,44 separation,45 and extraction.46 Using ILs as an alternative to organic solvents to form emulsions is very attractive due to the adjustable features and low volatility of ILs. The Zhang group firstly investigated the utilization of MOFs to emulsify two immiscible phases of water and an IL.47 Ni-BDC with nanoflake crystals and a size of 200–400 nm was used to stabilize the 1-butyl-3-methylimidazolium hexafluorophosphate ([BMIm]PF6)–water emulsion. With increasing [BMIm]PF6 content, the droplet size increases and the droplets are more crowded. For the emulsion with an IL volume fraction of 0.6, the droplets are polyhedral, corresponding to the formation of HIPE. The morphology of this emulsion was characterized to be [BMIm]PF6-in-water type, i.e., [BMIm]PF6 droplets are dispersed in the continuous water phase. This MOF-stabilized HIPE provides a novel way to synthesize kinds of composites by emulsion polymerization. The macroporous MOF/polyacrylamide network and MOF/polystyrene microspheres were obtained from HIPEs by using different kinds of monomers. Also, Cu-BTC and Zn-BTC could stabilize IL–water PEs.
2.3 CO2–water emulsions stabilized by MOFs
Supercritical CO2 or compressed CO2 has adjustable solvent power and excellent mass transfer characteristics, which offer many advantages to replace conventional organic solvents.48 The Zhang group firstly proposed the utilization of MOFs for emulsifying liquid CO2 and water.49 Mn3(BTC)2, a kind of hydrophilic MOF, was dispersed in water (Fig. 2a and b). Then CO2 was added to the above dispersion under stirring at 298.15 K. As the CO2 pressure is higher than 6.4 MPa, a uniform milky-white emulsion was formed (Fig. 2c). By electrical conductivity measurements, the morphology of the emulsion was determined to be CO2-in-water type (Fig. 2d). Such an emulsion is very stable and no phase separation was observed in at least 6 months after stopping stirring. The CO2–water emulsion provides a novel route for deriving MOF superstructures. To preserve the microstructure of the emulsion and avoid macropore collapse during the solvent removal process, the emulsion formed at 7.5 MPa was frozen in liquid nitrogen and then CO2 was released by depressurization. The obtained ice block preserved the morphology of the emulsion (Fig. 2e). Then water was removed by freeze drying and the solid of restructured Mn3(BTC)2 (r-Mn3(BTC)2) was prepared. Remarkably, the volume of r-Mn3(BTC)2 expands tremendously (Fig. 2f) compared with the pristine Mn3(BTC)2 (p-Mn3(BTC)2) and presents a three-dimensional network with macropores in the range of 4–30 μm (Fig. 2g). The network is assembled from nanofibers with a width of 50 nm and a length of 15 μm (Fig. 2h–j), much thinner than the p-Mn3(BTC)2 bars (Fig. 2b). This indicates that the Mn3(BTC)2-stabilized CO2-in-water emulsion has a dual effect on MOFs, that is, downsizing p-Mn3(BTC)2 to ultrafine nanofibers and conducting their assembly to a macroporous network. Moreover, the fluorogenic MOF (Mn(hfbba)(3-mepy)(H2O), H2hfbba: 4,4′-(hexafluoroisopropylidene) bis(benzoic acid), 3-mepy: 3-methyl pyridine) (Mn-HFMOF-W) was used to form a water-in-CO2 emulsion at 7.5 MPa and 298.15 K. By a similar route to remove CO2 and water in the emulsion, the r-Mn-HFMOF-W was obtained, which presents hollow micron-sized capsules assembled by nanoparticles.
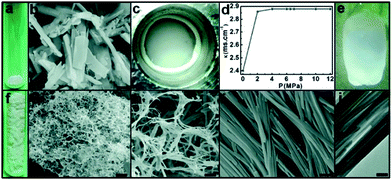 |
| Fig. 2 Water-continuous emulsion stabilized by Mn3(BTC)2 and derivation of the Mn3(BTC)2 network. (a and b) Photograph and SEM image of p-Mn3(BTC)2; (c) photograph of the emulsion at 7.5 MPa; (d) electrical conductivities of the CO2/H2O/Mn3(BTC)2 mixture at different pressures; (e) photograph of the frozen emulsion after releasing CO2; (f–j) photograph and SEM and TEM images of r-Mn3(BTC)2. Scale bars: 1 mm in (b), 50 mm in (g), 5 mm in (h), 200 nm in (i), and 50 nm in (j).49 Copyright 2016 Wiley-VCH. | |
Wang and coworkers studied the formation of MOF-stabilized HIPE in CO2 and water. UiO-66 can act as an efficient and stable emulsifier for stabilizing CO2-in-water HIPE, from which the UiO-66/polyacrylamide porous material was synthesized.50 They also used MOFs and polymers (e.g., Cu-BTC and polyvinyl alcohol,51 Cu-BDC and polyvinyl alcohol52) as emulsifiers for the preparation of CO2–water HIPEs. These emulsions were utilized to synthesize porous Cu-BTC/polyacrylamide51 and Cu-BDC/poly(N-methylol acrylamide) monoliths52 through emulsion polymerization.
The MOF stabilized CO2–water emulsion was also applied to chemical reactions. The Zhang group investigated the emulsification of NH2-MIL-125 (Ti) (Ti8O8(OH)4(BDCNH2)6 (BDC-NH2 = 2-amino-benzene-1,4-dicarboxylate)) for CO2 and water.53 When the pressure was higher than the vapor pressure of CO2 (6.89 MPa at 301.15 K), a milky yellow emulsion appeared under stirring for water, CO2 and NH2-MIL-125 (Ti), which was characterized to be CO2-in-water type. The NH2-MIL-125 (Ti)-stabilized CO2-in-water emulsion provides a novel route for photocatalytic CO2 conversion by utilizing NH2-MIL-125 (Ti) as both an emulsifier and a catalyst. As the pressure is higher than 6.89 MPa, the rate of HCOO− produced in the emulsion was improved significantly. It can be ascribed to the existence of a large number of interfaces in the emulsion system, which can enhance mass transfer across the interface and thus accelerate the reaction rate.
3 PEs stabilized by g-C3N4
g-C3N4 has wide applications in various areas such as catalysis, energy conversion and optoelectronics.54–62 Generally, g-C3N4 is in the form of 2D sheets consisting of tri-s-triazines interconnected via tertiary amines, made by polymerization of cyanamide, dicyandiamide or melamine.63–68 There are primary and secondary amine groups that result from incomplete condensation and hydroxyl groups due to the partial hydrolysis of terminal amine groups. The conjugated basal plane is hydrophobic, while the edge groups are hydrophilic, which endow g-C3N4 with an amphiphilic feature and the ability to stabilize PEs.69
3.1 Oil–water emulsions stabilized by g-C3N4
Antonietti observed the behavior of g-C3N4 at liquid–liquid, liquid–solid and liquid–air interfaces.69 A hexane-in-water emulsion can be generated by simple manual shaking of hexane in the presence of g-C3N4 aqueous dispersion. It is because g-C3N4 can tightly adsorb at the surface of the dispersed droplets and effectively stabilize them from coagulation and coalescence. The average diameter of the droplets declines as the g-C3N4 concentration increases. The emulsion remained stable against coalescence for at least months in ambient environment, regardless of the concentration of g-C3N4. It can be ascribed to its shape anisotropy down to a nanosheet-like texture creating locked, intertwined networks at the interface. Xu et al. found that g-C3N4 could emit blue light upon UV irradiation due to a sheet-like morphology with lateral sizes up to tens of micrometers of g-C3N4 and its conjugated framework.70 As a result, g-C3N4-stabilized PEs can act as an excellent platform for direct observation and mechanistic studies of Pickering-type systems.
Subsequently, styrene-in-water emulsions were formed by using g-C3N4 as the stabilizer, which were applied to the synthesis of polymer/g-C3N4 nanocomposites.71,72 Moreover, styrene-in-water, benzyl methacrylate-in-water and methyl methacrylate-in-water PEs stabilized by g-C3N4 were prepared for synthesizing polystyrene, poly-benzyl methacrylate and poly-methyl methacrylate latexes, respectively.73 C/g-C3N4 was obtained using the g-C3N4-stabilized styrene-in-water emulsion by a photocatalytic PE polymerization method and carbonization.74 This C/g-C3N4 catalyst exhibits high activity for degradation of methylene blue, with a photocurrent density about 68.3 times higher than that of the original g-C3N4.
PEs stabilized by g-C3N4 were also used for interfacial catalysis. In order to endow the material with specific catalytic activity while keeping the emulsifying capability, Xu and coworkers employed Pd/g-C3N4 to stabilize PEs for conducting an efficient alkene hydrogenation in the oil phase.75 The styrene-in-water emulsion stabilized by Pd/g-C3N4 presents numerous oil droplets in the range of 100–400 μm, of which the surfaces are densely covered by Pd/g-C3N4 particles (Fig. 3a). The hydrogen liberation–hydrogenation tandem reaction (alkene hydrogenation) using ammonia borane (AB) as the hydrogen source was conducted in the emulsion (Fig. 3b). The effect of Pd loading on the catalytic activity of the Pd/g-C3N4 nanocomposite was investigated (Fig. 3c). The results show that the activity is low for 0.5 wt% Pd loading and 0.31 mmol of ethylbenzene was obtained after 18 h reaction. For the nanocomposites with 2 and 5 wt% Pd loading, the reactions proceeded much more quickly, and 0.32 mmol of ethylbenzene was obtained in the first 8 h. A series of comparison studies were carried out to understand the underlying mechanism (Fig. 3d). When AB was replaced by 0.35 mmol of gaseous H2 (outside the emulsion system), a very low amount of ethylbenzene and hydrogen utilization efficiency (HUE) were observed due to limited mass transfer from the gas to the liquid phase (entry 2). Additionally, when AB was used but no emulsification was applied, 0.11 mmol of ethylbenzene and a HUE of 33% were obtained, resulting from the limited macro-interface between the two immiscible phases (entry 3). Applying stirring (500 rpm) led to an increased interface area and thus the catalytic performance was improved (entry 4). In another experiment, ethanol was added to generate a miscible and homogeneous solvent for this reaction. Only 0.15 mmol of ethylbenzene and a HUE of 45% were obtained (entry 5). These comparison studies confirmed the efficacy of combined dehydrogenation–hydrogenation in an emulsion microreactor. The droplets in emulsions can act as a hydrogen buffer for improving the HUE and ethylbenzene yield due to localized production, storage and consumption of hydrogen on Pd nanoparticles.
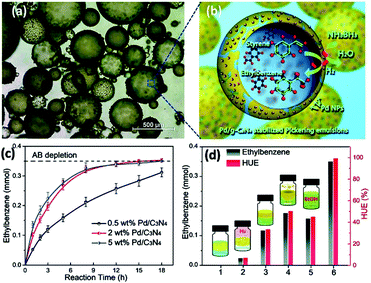 |
| Fig. 3 (a) Light microscopy image of Pickering emulsions made from 1 mL of styrene and 1 mL of 2 mg mL−1 2 wt% Pd/g-C3N4 dispersion. (b) Schematic illustration of AB hydrolysis combined with styrene hydrogenation in the Pickering emulsion system, catalyzed by Pd nanoparticles at the droplet interfaces. (c) Time-dependent ethylbenzene generation over 0.5, 2, and 5 wt% Pd/g-C3N4. (d) Control group experiments for hydrogenation: entry (1) g-C3N4 as the catalyst; (2) AB replaced by 0.35 mmol of gaseous H2; (3) without emulsification; (4) no emulsification but stirring at 500 rpm; (5) dissolving the whole emulsion system in ethanol; and (6) typical procedure. Note that all these experiments were conducted for 18 h.75 Copyright 2019 Wiley-VCH. | |
Xue and coworkers used pyrene-functionalized polymeric carbon nitride (PCN) for emulsifying water and cyclohexene PE for coupling reactions of photocatalytic CO2 reduction and oxidation of alkenes.76 Bicarbonate in aqueous solution served as the source of CO2, while alkene was in the organic phase of the PE. Such an aqueous–organic biphasic environment could efficiently improve both the photoreduction of bicarbonate in the aqueous phase and the simultaneous oxidation of alkenes in the organic phase.
3.2 CO2–water emulsions stabilized by g-C3N4
The Zhang group firstly used g-C3N4 to stabilize the CO2–water emulsion.77 For the formation of an emulsion, an aqueous dispersion of g-C3N4 was added into an autoclave. Then CO2 was charged into the autoclave under stirring. As the pressure was above the vapor pressure of CO2 (6.43 MPa at 298.15 K), a liquid CO2 upper phase formed. The g-C3N4/water/CO2 mixture was stirred vigorously at 298.15 K and 8.02 MPa for 0.5 h. The mixture became turbid, indicating the formation of the emulsion. The morphology of this emulsion was CO2-in-water type, i.e. water is the continuous phase and CO2 acts as the dispersed phase. The CO2 droplets stabilized by g-C3N4 were utilized as microreactors for in situ photocatalytic CO2 reduction, where g-C3N4 sheets assembling at the CO2–water interface can serve as both an emulsifier and a photocatalyst. A large amount of formic acid was produced from the CO2-in-water emulsion. It was found that the photocatalytic reaction efficiency can be improved with the increase of the water ratio in a certain range, which may be caused by the increased CO2–water interfaces stabilized by g-C3N4 nanosheets.
4 PEs stabilized by graphene oxide (GO)
GO is a type of water-dispersible material composed of planar, graphene-like aromatic patches of random size separated by sp3-bond carbons, which is decorated by hydroxyl, epoxy and carboxyl groups.78–81 The unique structural features endow GO with many intriguing surface chemical properties such as amphiphilicity, negatively charged nature and multi-oxygen containing groups on its sheets. Therefore, GO has the ability to adsorb on various interfaces and lower interfacial tension.82,83
4.1 Oil–water emulsions stabilized by GO
Generally, GO has been largely viewed as hydrophilic, presumably due to its excellent colloidal stability in water. Huang and coworkers confirm the amphiphilic nature and surface activity of GO sheets by the Brewster angle microscopy technique.83 The toluene-in-water emulsion stabilized by GO remained stable against coalescence for months (Fig. 4), which can be ascribed to the high surface area of GO that makes them kinetically trapped at the interface. The volume of the emulsion phase decreased with decreasing GO concentration (Fig. 4a–g), while the average sizes of toluene droplets increased (Fig. 4h). As the pH can affect the extent of ionization of –COOH, the amphiphilicity of GO depends on the pH of the media and GO can be reversibly shuttled between water and emulsion phases. Therefore, the formation and destruction of this emulsion can be achieved by adjusting pH, which has application potential for extraction or phase transfer.
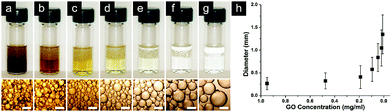 |
| Fig. 4 (a–g) Toluene droplets formed upon shaking a toluene/GO water mixture, where the concentration of GO was varied from (a) 0.95 mg mL−1 to (b) 0.47, (c) 0.19, (d) 0.095, (e) 0.047, (f) 0.019, and (g) 0.0095 mg mL−1, respectively. The bottom row shows the microscopy images of the toluene droplets. All scale bars are equal to 1 mm. (h) Dependence of the size of oil droplets on the concentration of GO.83 Copyright 2010 American Chemical Society. | |
The emulsions stabilized by GO provide a versatile route for fabricating different kinds of GO and GO-based materials, such as hollow GO spheres,84 Janus GO,85 3D graphene oxide frameworks,86 hollow ZIF-8/GO,87 hollow Cu3(BTC)2/GO,88 AgInZnS/GO,89 Ag/GO,90 SiO2/GO capsules,91,92 polymer/GO93–110 and ternary composites like Au nanoparticle/GO@polystyrene,111 GO–CoOx armored PS,112 and GO@polylactic acid@hydroxyapatite microcapsules.113 Further, the GO nanosheets can be peeled out after emulsion polymerization, thus producing a hollow molecularly imprinted polymer.114 Moreover, by GO reduction115 in a GO-stabilized PE, various graphene and reduced GO (rGO)-based materials were synthesized, including graphene hollow spheres,116 cellular graphene aerogels,117 3D graphene network encapsulating 1-hexadecanol,118 paraffin@graphene microcapsules119 and rGO-coated stearic acid.120
GO has good surface modification properties. The hydroxyl groups and delocalized electrons over sp2-hybridized carbon atom domains endow GO with the ability to form hydrogen bonds with other hydroxyl-rich molecules and introduce π–π interactions with other π-conjugated materials.121 The plentiful oxygen-containing groups on GO also provide active sites for chemical modification of the GO surface and many different functional groups can be introduced onto the sheets. Wang and coworkers used the GO modified by the cationic surfactant cetyltrimethylammonium bromide to emulsify water and styrene/divinylbenzene, forming a HIPE at a GO content as low as 0.2 mg mL−1 (relative to the volume of the oil phase).122 They also formed the cyclohexane-in-water HIPE by using cetyltrimethylammonium bromide-modified GO as the emulsifier, and interconnected macro-porous poly(acrylic acid) hydrogels were prepared from the HIPE.123 A series of water-in-oil and oil-in-water PEs were formed by using modified GO, such as sulfonated-GO,124 GO modified by the polycondensate of adipic acid and diethanolamine,125 GO decorated with nanoparticles,126 magnetically responsive reduced-GO,127 alkyl chain modified GO,128 amine functionalized GO129 and stearyltrimethylammonium bromide-grafted GO.130 Moreover, multiple emulsion droplets can be stabilized by GO; for example, the Gao group found that a water-in-oil-in-water multiple emulsion can be synthesized with low GO concentrations, low pH values, high oil–water ratios, high salt concentrations, or moderately reduced GO in the benzyl chloride–water system.131
4.2 IL–water emulsions stabilized by GO
Pentzer and coworkers utilized GO for the formation of the [BmimPF6]-in-water emulsion, which was used to template rGO–IL capsules by interfacial polymerization and thermal reduction of GO.132 The symmetric coin cells of the as-synthesized rGO–IL capsules exhibit high capacitance, with specific capacitances of 80 F g−1 at 18 °C and 127 F g−1 at 60 °C at a scan rate of 10 mV s−1. Later, the same group conducted a comprehensive study on the [BmimPF6]-in-water emulsion stabilized by GO nanosheets and the [BmimPF6]-in-octane emulsion stabilized by alkylated GO nanosheets (C18-GO).133 With increasing volume fraction of [BmimPF6], the droplet sizes of both [BmimPF6]-in-water and [BmimPF6]-in-octane emulsions increase. They also studied the effects of acids and bases on PE formation, which are related with protonation/deprotonation of different functional groups of GO and C18-GO. Pentzer and coworkers utilized GO and C18-GO stabilized PEs for the synthesis of capsules to encapsulate a variety of ILs for phenol removal.134 Furthermore, this group reported that C18-GO can stabilize the 1-ethyl-3-methylimidazolium bis(trifluoromethylsulfonyl)imide-in-water emulsion.135 This provides a new route for encapsulating ILs into GO/polymer capsules through polymerization in such PEs.
4.3 CO2–water emulsions stabilized by GO
Due to the strong hydrophilicity of GO, it cannot be used directly for the formation of the CO2–water emulsion under stirring. The surface wettability of GO can be easily modulated by the reduction degree of GO. The Zhang group demonstrated that rGO can act as a stabilizer for the formation of the CO2–water emulsion (Fig. 5) under stirring, without the aid of any additional emulsifier or surface modification for rGO.136 rGO was first dispersed in water (Fig. 5a). Then CO2 was charged into the above dispersion at 302.2 K. At pressure over 7.05 MPa and 302.2 K, an upper liquid CO2 phase formed (Fig. 5b). Then the above dispersion was stirred for 10 min at 7.30 MPa (Fig. 5c). The emulsion can remain stable for at least 12 h against coalescence. Interestingly, the formation and breakage of the emulsion could be tuned reversibly by pressurization and depressurization. The electrical conductivities of the CO2/water/rGO mixture manifest that the morphology of this emulsion is CO2-in-water type (Fig. 5d). The emulsion stabilized by rGO was utilized for constructing 3D rGO, Au/rGO and TiO2/rGO networks.136
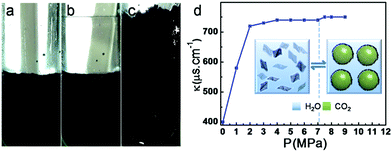 |
| Fig. 5 Photographs of (a) rGO dispersed aqueous solution, (b) rGO aqueous solution with an upper liquid CO2 phase at 7.30 MPa, and (c) the emulsion stabilized by rGO at 7.30 MPa. (d) Electrical conductivities of the CO2/H2O/rGO mixture at different pressures. The inset in (d) illustrates the reversible transition from the rGO dispersion to emulsion by pressurization and depressurization. The concentration of rGO in water is 5 mg mL−1, and the temperature is 302.2 K.136 Copyright 2017 American Chemical Society. | |
Gao and coworkers found that pristine GO can be used to emulsify the mixture of CO2 and an aqueous liquid to form the water-in-CO2 emulsion at a temperature of 305.15 ± 0.1 K and a pressure of 18 MPa, under ultrasonication with a power of 200 W and a frequency of 20 kHz.137 The addition of GO greatly increases the proportion of the dispersed phase (water) in the CO2 continuous phase. Under optimized conditions, GO emulsifies up to 23% water in CO2 with droplets around 0.5–3 μm. The stabilization time of these emulsions exceeded 10 h and increased with pressure and GO concentration.
5 Conclusions and outlook
MOF, GO and g-C3N4 have been used to emulsify two immiscible liquids, such as oil and water, an IL and water, and CO2 and water. The morphologies, structures and properties of PEs can be adjusted by modulating the amphiphilicity of the particles used. These PEs stabilized by these materials have found potential applications in materials synthesis, chemical reactions, separation, etc. Further fundamental and applied research studies need to be conducted into a deeper scale. Firstly, more novel functional materials should be explored for forming PEs so as to expand the PE applications. Secondly, some other solvents with environment-friendly and easily-adjustable features can be used as alternatives for the organic oil phase to produce PEs with unique structures and properties. Thirdly, it is of importance to form monodisperse PEs with controlled droplet size. The development of membrane emulsification and microfluidic methods has partly solved this problem, but it is still challenging for large-scale production. Without narrow size distributions, the utilization and evaluation of PEs would be difficult. We believe that the progress on these topics will contribute greatly to colloid and interface science and related areas such as materials synthesis, chemical reactions, separation and extraction, dug release, etc.
Conflicts of interest
There are no conflicts to declare.
Acknowledgements
This work was supported by the Ministry of Science and Technology of China (2017YFA0403003) and the National Natural Science Foundation of China (22033009).
Notes and references
- A. S. Utada, E. Lorenceau, D. R. Link, P. D. Kaplan, H. A. Stone and D. A. Weitz, Science, 2005, 308, 537 CrossRef CAS PubMed.
- W. Ramsden, Proc. R. Soc. London, 1903, 72, 156 CAS.
- S. U. Pickering, J. Chem. Soc., 1907, 91, 2001 RSC.
- J. Wu and G.-H. Ma, Small, 2016, 12, 4633 CrossRef CAS PubMed.
- M. Pera-Titus, L. Leclercq, J.-M. Clacens, F. De Campo and V. Nardello-Rataj, Angew. Chem., Int. Ed., 2015, 54, 2006 CrossRef CAS PubMed.
- D. E. Tambe and M. M. Sharma, Adv. Colloid Interface Sci., 1994, 52, 1 CrossRef CAS.
- Z. Chen, H. Ji, C. Zhao, E. Ju, J. Ren and X. Qu, Angew. Chem., Int. Ed., 2015, 54, 4904 CrossRef CAS PubMed.
- W.-J. Zhou, L. Fang, Z. Fan, B. Albela, L. Bonneviot, F. De Campo, M. Pera-Titus and J.-M. Clacens, J. Am. Chem. Soc., 2014, 136, 4869 CrossRef CAS PubMed.
- B. P. Binks and S. O. Lumsdon, Langmuir, 2000, 16, 8622 CrossRef CAS.
- B. P. Binks, Curr. Opin. Colloid Interface Sci., 2002, 7, 21 CrossRef CAS.
- B. P. Binks and S. O. Lumsdon, Langmuir, 2001, 17, 4540 CrossRef CAS.
- D. E. Tambe and M. M. Sharma, J. Colloid Interface Sci., 1994, 162, 1 CrossRef CAS.
- L. G. Torres, R. Iturbe, M. J. Snowden, B. Z. Chowdhry and S. A. Leharne, Colloids Surf., A, 2007, 302, 439 CrossRef CAS.
- S. Fujii, M. Okada and T. Furuzono, J. Colloid Interface Sci., 2007, 315, 287 CrossRef CAS PubMed.
- A. D. Dinsmore, M. F. Hsu, M. G. Nikolaides, M. Marquez, A. R. Bausch and D. A. Weitz, Science, 2002, 298, 1006 CrossRef CAS PubMed.
- B. P. Binks and J. A. Rodrigues, Angew. Chem., Int. Ed., 2005, 44, 441 CrossRef CAS PubMed.
- I. Akartuna, A. R. Studart, E. Tervoort, U. T. Gonzenbach and L. J. Gauckler, Langmuir, 2008, 24, 7161 CrossRef CAS PubMed.
- A. Saha, A. Nikova, P. Venkataraman, V. T. John and A. Bose, ACS Appl. Mater. Interfaces, 2013, 5, 3094 CrossRef CAS PubMed.
- O. M. Yaghi, M. O'Keeffe, N. W. Ockwig, H. K. Chae, M. Eddaoudi and J. Kim, Nature, 2003, 423, 705 CrossRef CAS PubMed.
- K. Xie, Q. Fu, C. Xu, H. Lu, Q. Zhao, R. Curtain, D. Gu, P. A. Webley and G. G. Qiao, Energy Environ. Sci., 2018, 11, 544 RSC.
- G.-Y. Jeong, A. K. Singh, M.-G. Kim, K.-W. Gyak, U. Ryu, K. M. Choi and D.-P. Kim, Nat. Commun., 2018, 9, 3968 CrossRef PubMed.
- Y.-P. Li, Y. Wang, Y.-Y. Xue, H.-P. Li, Q.-G. Zhai, S.-N. Li, Y.-C. Jiang, M.-C. Hu and X. Bu, Angew. Chem., Int. Ed., 2019, 58, 13590 CrossRef CAS PubMed.
- Q. Wang and D. Astruc, Chem. Rev., 2020, 120, 1438 CrossRef CAS PubMed.
- E. A. Dolgopolova, A. M. Rice, C. R. Martin and N. B. Shustova, Chem. Soc. Rev., 2018, 47, 4710 RSC.
- Y. Bai, Y. Dou, L.-H. Xie, W. Rutledge, J.-R. Li and H.-C. Zhou, Chem. Soc. Rev., 2016, 45, 2327 RSC.
- M. Tsotsalas, A. Umemura, F. Kim, Y. Sakata, J. Reboul, S. Kitagawa and S. Furukawa, J. Mater. Chem., 2012, 22, 10159 RSC.
- N. Yanai and S. Granick, Angew. Chem., Int. Ed., 2012, 51, 5638 CrossRef CAS PubMed.
- J. Huo, M. Marcello, A. Garai and D. Bradshaw, Adv. Mater., 2013, 25, 2717 CrossRef CAS PubMed.
- B. Xiao, Q. Yuan and R. A. Williams, Chem. Commun., 2013, 49, 8208 RSC.
- B. Zhang, J. Zhang, C. Liu, L. Peng, X. Sang, B. Han, X. Ma, T. Luo, X. Tan and G. Yang, Sci. Rep., 2016, 6, 21401 CrossRef CAS PubMed.
- H. Zhu, Q. Zhang and S. Zhu, Chem. – Eur. J., 2016, 22, 8751 CrossRef CAS PubMed.
- J. Shi, X. Wang, S. Zhang, L. Tang and Z. Jiang, J. Mater. Chem. B, 2016, 4, 2654 RSC.
- F. Zhang, X. Sang, X. Tan, C. Liu, J. Zhang, T. Luo, L. Liu, B. Han, G. Yang and B. P. Binks, Langmuir, 2017, 33, 12427 CrossRef CAS PubMed.
- L. Liu, F. Zhang, J. Zhang, X. Tan, B. Zhang, J. Shi, D. Shao, D. Tan, B. Han and G. Yang, Soft Matter, 2017, 13, 9174 RSC.
- J. Wang, H. Zhu, B.-G. Li and S. Zhu, Chem. – Eur. J., 2018, 24, 16426 CrossRef CAS PubMed.
- X. Chen, Y. Zhang, Y. Zhao, Y. Wu, S. Wang, W. Xu, J. Zhang, S. Yang, L. Liu and Y. Liu, Mater. Lett., 2018, 218, 67 CrossRef CAS.
- P. Jin, W. Tan, J. Huo, T. Liu, Y. Liang, S. Wang and D. Bradshaw, J. Mater. Chem. A, 2018, 6, 20473 RSC.
- C. Tan, M. Lee, M. Arshadi, M. Azizi and A. Abbaspourrad, Angew. Chem., Int. Ed., 2020, 59, 9506 CrossRef CAS PubMed.
- C. Qiu, J. Wang, Y. Qin, X. Xu and Z. Jin, J. Agric. Food Chem., 2019, 67, 391 CrossRef CAS PubMed.
- L. Qi, Z. Luo and X. Lu, ACS Sustainable Chem. Eng., 2019, 7, 7127 CrossRef CAS.
- J. Le Bideau, L. Viau and A. Vioux, Chem. Soc. Rev., 2011, 40, 907 RSC.
- H. Wang, G. Gurau and R. D. Rogers, Chem. Soc. Rev., 2012, 41, 1519 RSC.
- L. Peng, J. Zhang, J. Li, B. Han, Z. Xue and G. Yang, Angew. Chem., Int. Ed., 2013, 52, 1792 CrossRef CAS PubMed.
- A. Zhu, W. Feng, L. Li, Q. Li and J. Wang, Catal. Lett., 2017, 147, 261 CrossRef CAS.
- X. Han and D. W. Armstrong, Acc. Chem. Res., 2007, 40, 1079 CrossRef CAS PubMed.
- X. Sun, H. Luo and S. Dai, Chem. Rev., 2012, 112, 2100 CrossRef CAS PubMed.
- Z. Li, J. Zhang, T. Luo, X. Tan, C. Liu, X. Sang, X. Ma, B. Han and G. Yang, Soft Matter, 2016, 12, 8841 RSC.
- J. Zhang and B. Han, Acc. Chem. Res., 2013, 46, 425 CrossRef CAS PubMed.
- C. Liu, J. Zhang, L. Zheng, J. Zhang, X. Sang, X. Kang, B. Zhang, T. Luo, X. Tan and B. Han, Angew. Chem., Int. Ed., 2016, 55, 11372 CrossRef CAS PubMed.
- Y. Dong, L. Cao, J. Li, Y. Yang and J. Wang, RSC Adv., 2018, 8, 32358 RSC.
- Y. Yang, L. Cao, J. Li, Y. Dong and J. Wang, Macromol. Mater. Eng., 2018, 303, 1800426 CrossRef.
- Z. Yang, L. Cao, J. Li, J. Lin and J. Wang, Polymer, 2018, 153, 17 CrossRef CAS.
- T. Luo, J. Zhang, W. Li, Z. He, X. Sun, J. Shi, D. Shao, B. Zhang, X. Tan and B. Han, ACS Appl. Mater. Interfaces, 2017, 9, 41594 CrossRef CAS PubMed.
- J. Barrio, C. Gibaja, J. Tzadikov, M. Shalom and F. Zamora, Adv. Sustainable Syst., 2019, 3, 1800138 CrossRef.
- G. Liu, P. Niu, C. Sun, S. C. Smith, Z. Chen, G. Q. Lu and H.-M. Cheng, J. Am. Chem. Soc., 2010, 132, 11642 CrossRef CAS PubMed.
- J. Liu, Y. Liu, N. Liu, Y. Han, X. Zhang, H. Huang, Y. Lifshitz, S.-T. Lee, J. Zhong and Z. Kang, Science, 2015, 347, 970 CrossRef CAS PubMed.
- P. Niu, L. Zhang, G. Liu and H.-M. Cheng, Adv. Funct. Mater., 2012, 22, 4763 CrossRef CAS.
- A. Thomas, A. Fischer, F. Goettmann, M. Antonietti, J.-O. Mueller, R. Schloegl and J. M. Carlsson, J. Mater. Chem., 2008, 18, 4893 RSC.
- Y. Wang, R. Shi, J. Lin and Y. Zhu, Energy Environ. Sci., 2011, 4, 2922 RSC.
- Y. Wang, X. Wang and M. Antonietti, Angew. Chem., Int. Ed., 2012, 51, 68 CrossRef CAS PubMed.
- Y. X. Wang, N. N. Zhang, R. Hubner, D. M. Tan, M. Loffler, S. Facsko, E. Zhang, Y. Ge, Z. H. Qi and C. Z. Wu, Adv. Mater. Interfaces, 2019, 6, 1801664 CrossRef.
- X. Zhang, X. Xie, H. Wang, J. Zhang, B. Pan and Y. Xie, J. Am. Chem. Soc., 2013, 135, 18 CrossRef CAS PubMed.
- S. Cao, J. Low, J. Yu and M. Jaroniec, Adv. Mater., 2015, 27, 2150 CrossRef CAS PubMed.
- B. Kumru, M. Antonietti and B. Schmidt, Langmuir, 2017, 33, 9897 CrossRef CAS PubMed.
- W.-J. Ong, L.-L. Tan, Y. H. Ng, S.-T. Yong and S.-P. Chai, Chem. Rev., 2016, 116, 7159 CrossRef CAS PubMed.
- S. Yang, Y. Gong, J. Zhang, L. Zhan, L. Ma, Z. Fang, R. Vajtai, X. Wang and P. M. Ajayan, Adv. Mater., 2013, 25, 2452 CrossRef CAS PubMed.
- Z. Zhao, Y. Sun and F. Dong, Nanoscale, 2015, 7, 15 RSC.
- Y. Zheng, J. Liu, J. Liang, M. Jaroniec and S. Z. Qiao, Energy Environ. Sci., 2012, 5, 6717 RSC.
- J. Xu and M. Antonietti, J. Am. Chem. Soc., 2017, 139, 6026 CrossRef CAS PubMed.
- C. Han, Q. Cui, P. Meng, E. R. Waclawik, H. Yang and J. Xu, Langmuir, 2018, 34, 10135 CrossRef CAS PubMed.
- Q. Cao, Q. Cui, Y. Yang, J. Xu, C. Han and L. Li, Chem. – Eur. J., 2018, 24, 2286 CrossRef CAS PubMed.
- Q. Yu, S. Fang and X. Wang, J. Nano Res., 2017, 49, 215 CAS.
- Q. Cao, T. Heil, B. Kumru, M. Antonietti and B. Schmidt, Polym. Chem., 2019, 10, 5315 RSC.
- J. Min and Q.-B. Yu, J. Nanosci. Nanotechnol., 2019, 19, 7729 CrossRef CAS PubMed.
- C. Han, P. Meng, E. R. Waclawik, C. Zhang, X.-H. Li, H. Yang, M. Antonietti and J. Xu, Angew. Chem., Int. Ed., 2018, 57, 14857 CrossRef CAS PubMed.
- X. Z. Gong, S. J. Yu, M. L. Guan, X. L. Zhu and C. Xue, J. Mater. Chem. A, 2019, 7, 7373 RSC.
- L. Liu, J. Zhang, B. Zhang, J. Shi, X. Tan, B. Han, T. Luo, D. Shao, D. Tan and F. Zhang, Green Chem., 2018, 20, 4206 RSC.
- J. W. Burress, S. Gadipelli, J. Ford, J. M. Simmons, W. Zhou and T. Yildirim, Angew. Chem., Int. Ed., 2010, 49, 8902 CrossRef CAS PubMed.
- T. H. Han, Y.-K. Huang, A. T. L. Tan, V. P. Dravid and J. Huang, J. Am. Chem. Soc., 2011, 133, 15264 CrossRef CAS PubMed.
- K. P. Loh, Q. Bao, G. Eda and M. Chhowalla, Nat. Chem., 2010, 2, 1015 CrossRef CAS PubMed.
- L. J. Cote, F. Kim and J. Huang, J. Am. Chem. Soc., 2009, 131, 1043 CrossRef CAS PubMed.
- J. J. Shao, W. Lv and Q. H. Yang, Adv. Mater., 2014, 26, 5586 CrossRef CAS PubMed.
- J. Kim, L. J. Cote, F. Kim, W. Yuan, K. R. Shull and J. Huang, J. Am. Chem. Soc., 2010, 132, 8180 CrossRef CAS PubMed.
- P. Guo, H. Song and X. Chen, J. Mater. Chem., 2010, 20, 4867 RSC.
- A. Ma, G. Wang, Z. Yang, L. Bai, H. Chen, W. Wang, H. Yang, D. Wei and L. Yang, Chem. Eng. J., 2020, 385, 123962 CrossRef CAS.
- L. Imperiali, C. Clasen, J. Fransaer, C. W. Macosko and J. Vermant, Mater. Horiz., 2014, 1, 139 RSC.
- Z. Bian, S. Zhang, X. Zhu, Y. Li, H. Liu and J. Hu, RSC Adv., 2015, 5, 31502 RSC.
- Z. Bian, J. Xu, S. Zhang, X. Zhu, H. Liu and J. Hu, Langmuir, 2015, 31, 7410 CrossRef CAS PubMed.
- Z. Zang, X. Zeng, M. Wang, W. Hu, C. Liu and X. Tang, Sens. Actuators, B, 2017, 252, 1179 CrossRef CAS.
- T. Mingyi, W. Tao, Z. Lei and W. Fei, Mater. Res. Bull., 2014, 60, 118 CrossRef.
- M. Ali, S. P. Meaney, M. J. Abedin, P. Holt, M. Majumder and R. F. Tabor, J. Colloid Interface Sci., 2019, 552, 528 CrossRef CAS PubMed.
- M. Ali, S. P. Meaney, P. Holt, M. Majumder and R. F. Tabor, Environ. Sci. Technol., 2020, 54, 3549 CrossRef CAS PubMed.
- L.-C. Chen, S. Lei, M.-Z. Wang, J. Yang and X.-W. Ge, Chin. Chem. Lett., 2016, 27, 511 CrossRef CAS.
- H. Hu, X. Wang, J. Wang, L. Wan, F. Liu, H. Zheng, R. Chen and C. Xu, Chem. Phys. Lett., 2010, 484, 247 CrossRef CAS.
- S. I. Kattimuttathu, C. Krishnappan, V. Vellorathekkaepadil, R. Nutenki, V. R. Mandapati and M. Cernik, Polym. Adv. Technol., 2015, 26, 214 CrossRef CAS.
- S. D. Kim, W. L. Zhang and H. J. Choi, J. Mater. Chem. C, 2014, 2, 7541 RSC.
- Y. Chen, Y. Wang, X. Shi, M. Jin, W. Cheng, L. Ren and Y. Wang, Carbon, 2017, 111, 38 CrossRef CAS.
- S. Daradmare, M. Pradhan, V. S. Raja and S. Parida, J. Mater. Sci., 2016, 51, 10262 CrossRef CAS.
- Y. Huang, X. Wang, X. Jin and T. Wang, J. Therm. Anal. Calorim., 2014, 117, 755 CrossRef CAS.
- H. Jahandideh, P. Ganjeh-Anzabi, S. L. Bryant and M. Trifkovic, Langmuir, 2018, 34, 12870 CrossRef CAS PubMed.
- C. J. Lee and H. J. Choi, Colloids Surf., A, 2018, 550, 56 CrossRef CAS.
- Y. Liu, Y. Zhang, L. Duan, W. Zhang, M. Su, Z. Sun and P. He, Prog. Org. Coat., 2016, 99, 23 CrossRef CAS.
- T. H. Min and H. J. Choi, Macromol. Res., 2017, 25, 565 CrossRef CAS.
- T. H. Min, C. J. Lee and H. J. Choi, Polym. Test., 2018, 66, 195 CrossRef CAS.
- X. Song, Y. Yang, J. Liu and H. Zhao, Langmuir, 2011, 27, 1186 CrossRef CAS PubMed.
- J. Sun and H. Bi, Mater. Lett., 2012, 81, 48 CrossRef CAS.
- S. C. Thickett, N. Wood, Y. H. Ng and P. B. Zetterlund, Nanoscale, 2014, 6, 8590 RSC.
- B. Wang, S. Dou, Y. Gao and W. Li, J. Appl. Polym. Sci., 2020, e49017 CrossRef.
- P. Xie, X. Ge, B. Fang, Z. Li, Y. Liang and C. Yang, Colloid Polym. Sci., 2013, 291, 1631 CrossRef CAS.
- G. Yin, Z. Zheng, H. Wang, Q. Du and H. Zhang, J. Colloid Interface Sci., 2013, 394, 192 CrossRef CAS PubMed.
- M. Tang, X. Wang, F. Wu, Y. Liu, S. Zhang, X. Pang, X. Li and H. Qiu, Carbon, 2014, 71, 238 CrossRef CAS.
- K. Edgehouse, M. Escamilla, L. Wang, R. Dent, K. Pachuta, L. Kendall, P. Wei, A. Sehirliolgu and E. Pentzer, J. Colloid Interface Sci., 2019, 541, 269 CrossRef CAS PubMed.
- H. Guo, Y. Wang, Y. Huang, F. Huang, S. Li, Y. Shen, M. Zhu and A. Xie, Eur. J. Inorg. Chem., 2017, 3312 CrossRef CAS.
- Y. Li, Y. Sun, J. Chen, X. Zhu, H. Li, S. Huang, Y. Hu, Q. Chen and S. Zhong, RSC Adv., 2016, 6, 74654 RSC.
- M. Wojtoniszak, X. Chen, R. J. Kalenczuk, A. Wajda, J. Lapczuk, M. Kurzawski, M. Drozdzik, P. K. Chu and E. Borowiak-Palen, Colloids Surf., B, 2012, 89, 79 CrossRef CAS PubMed.
- X. Chen, P. K. Eggers, A. D. Slattery, S. G. Ogden and C. L. Raston, J. Colloid Interface Sci., 2014, 430, 174 CrossRef CAS PubMed.
- B. X. Zhang, J. L. Zhang, X. X. Sang, C. C. Liu, T. Luo, L. Peng, B. X. Han, X. N. Tan, X. Ma, D. Wang and N. Zhao, Sci. Rep., 2016, 6, 10 Search PubMed.
- Y. Shang and D. Zhang, Appl. Therm. Eng., 2017, 111, 353 CrossRef CAS.
- W. Yang, L. Zhang, Y. Guo, Z. Jiang, F. He, C. Xie, J. Fan, J. Wu and K. Zhang, J. Mater. Sci., 2018, 53, 2566 CrossRef CAS.
- P. A. Advincula, A. C. de Leon, B. J. Rodier, J. Kwon, R. C. Advincula and E. B. Pentzer, J. Mater. Chem. A, 2018, 6, 2461 RSC.
- R. Li, Z. Li, G. Wang and Z. Gu, Sens. Actuators, B, 2018, 276, 404 CrossRef CAS.
- Z. Zheng, X. Zheng, H. Wang and Q. Du, ACS Appl. Mater. Interfaces, 2013, 5, 7974 CrossRef CAS PubMed.
- W. Yi, H. Wu, H. Wang and Q. Du, Langmuir, 2016, 32, 982 CrossRef CAS PubMed.
- L. Zhang, T. Shi, S. Wu and H. Zhou, Colloid Polym. Sci., 2013, 291, 2061 CrossRef CAS.
- Y. Zhang, X. Zheng, H. Wang and Q. Du, J. Mater. Chem. A, 2014, 2, 5304 RSC.
- Y. Hu, J. Huang, Q. Zhang, Y. Yang, S. Ma and C. Wang, RSC Adv., 2015, 5, 103394 RSC.
- K.-Y. A. Lin, H. Yang, C. Petit and W. D. Lee, J. Colloid Interface Sci., 2015, 438, 296 CrossRef CAS PubMed.
- X. Fei, L. Xia, M. Chen, W. Wei, J. Luo and X. Liu, Materials, 2016, 9, 731 CrossRef PubMed.
- J. Zhu, F. Wang, D. Li, J. Zhai, P. Liu, W. Zhang and Y. Li, Catal. Lett., 2020, 150, 1909 CrossRef CAS.
- S. Yang, H. Wu, C. Li, Y. Xiong and S. Guo, ACS Appl. Mater. Interfaces, 2020, 12, 3976 CrossRef CAS PubMed.
- Y. Q. He, F. Wu, X. Y. Sun, R. Q. Li, Y. Q. Guo, C. B. Li, L. Zhang, F. B. Xing, W. Wang and J. P. Gao, ACS Appl. Mater. Interfaces, 2013, 5, 4843 CrossRef CAS PubMed.
- Q. M. Luo, P. Q. Wei, Q. W. Huang, B. Gurkan and E. B. Pentzer, ACS Appl. Mater. Interfaces, 2018, 10, 16707 CrossRef CAS PubMed.
- Q. Luo, Y. Wang, E. Yoo, P. Wei and E. Pentzer, Langmuir, 2018, 34, 10114 CrossRef CAS PubMed.
- Q. Luo, Y. Wang, Z. Chen, P. Wei, E. Yoo and E. Pentzer, ACS Appl. Mater. Interfaces, 2019, 11, 9612 CrossRef CAS PubMed.
- Q. Huang, Q. Luo, Y. Wang, E. Pentzer and B. Gurkan, Ind. Eng. Chem. Res., 2019, 58, 10503 CrossRef CAS PubMed.
- C. Liu, J. Zhang, X. Sang, X. Kang, B. Zhang, T. Luo, X. Tan, B. Han, L. Zheng and J. Zhang, ACS Appl. Mater. Interfaces, 2017, 9, 17614 Search PubMed.
- H. Gao, G. Hu and K. Liu, J. Supercrit. Fluids, 2020, 155, 104654 CrossRef CAS.
|
This journal is © The Royal Society of Chemistry 2022 |
Click here to see how this site uses Cookies. View our privacy policy here.