DOI:
10.1039/D1SC06751F
(Edge Article)
Chem. Sci., 2022,
13, 3281-3287
Photoluminescent coordination polymer bulk glasses and laser-induced crystallization†
Received
3rd December 2021
, Accepted 23rd February 2022
First published on 24th February 2022
Abstract
We synthesized luminescent coordination polymer glasses composed of d10 metal cyanides and triphenylphosphine through melt-quenching and mechanical milling protocols. Synchrotron X-ray total scattering measurements and solid-state NMR revealed their one-dimensional chain structures and high structural dynamics. Thermodynamic and photoluminescence properties were tunable by the combination of heterometallic ions (Ag+, Au+, and Cu+) in the structures. The glasses are moldable and thermally stable, and over centimeter-sized glass monoliths were fabricated by the hot-press technique. They showed high transparency over 80% from the visible to near-infrared region and strong green emission at room temperature. Furthermore, the glass-to-crystal transformation was demonstrated by laser irradiation through the photothermal effect of the glasses.
Introduction
Glassy coordination polymers (CPs) and metal–organic frameworks (MOFs) have been of interest as a new class of amorphous materials.1–4 Their structure and properties are distinct from conventional glasses and are controlled by the combination of metal ions and bridging molecular ligands. In addition, the non-crystalline, high processability, and adhesive characteristics have gained research interest in both fundamental behaviors as well as applications such as ion conductive solid electrolytes, gas separation membranes, and electrochemical catalysis.5–10
One of the most successful applications of glass, in general, is optics. The transparency and moldability of optically active glass materials have enabled many optical functionalities, including photoconductivity, photon up-conversion, and spectral concentration.11–13 However, studies on the optical properties and materials fabrication of CP/MOF glasses are still in their infancy. This is because limited compounds have been found which possess essential criteria for optical materials: (i) strong luminescence, (ii) moldability in bulk size (over a centimeter), and (iii) high transparency over 80%.14 The preparation of bulk ZIF-62 glass monoliths with a high transparency up to 90% in the visible and near-infrared region has been reported in a previous report.15 Mid-infrared luminescence was achieved through Co2+ doping into ZIF-62 glass.16,17 Au+ and thiophenolate CP only showed red luminescence at low-temperature (−180 °C) and a transparency of 26% at 850 nm.18 It is demanded to explore the new luminescent CP/MOF glasses to meet these criteria.
One ligand system to construct CP/MOFs with tunable compositions and dimensionalities is cyanide.19–21 CP/MOFs composed of cyanide and dicyanamide are reported to show melting and vitrification behaviors. The flexible coordination bond between cyanides and monovalent d10 metal ions is suitable for glass formation.22–25 Here we report three cyanide-based CP glasses with one-dimensional (1D) structures {[MN(PPh3)2][MC(CN)2]}n (MN, MC = Cu+, Ag+ or Au+).26 The glassy state was obtained from crystalline states through either the melt-quenching or ball milling process. The alternative monovalent metal centers adjust the thermodynamic and photoluminescence properties of glasses. The CP glasses formed a centimeter-scale transparent monolith by a simple vacuum hot-press technique and showed strong green emission at room temperature. Moreover, the laser triggered phase transition from glass to the crystal in the monolith was demonstrated.
Results and discussion
Crystal structures
Fig. 1A and B show the crystal structures of {[Ag(PPh3)2][Au(CN)2]}n (AgAu).27 Ag+ has a tetrahedral configuration with two phosphine atoms from triphenylphosphine (PPh3) and two nitrogen atoms from cyanides. These tetrahedra are linked to Au+ to give 1D zig-zag chains along the c-axis. Weak interactions including Au⋯H and C–H⋯π interactions exist between the 1D chains. Guest-containing {[Ag(PPh3)2][Cu(CN)2]}n·xH2O and {[Cu(PPh3)2][Au(CN)2]}n·xH2O were synthesized as microcrystalline powders following the reported procedures (see the ESI†).26–28 Their guest-free phases, {[Ag(PPh3)2][Cu(CN)2]}n (CuAg) and {[Cu(PPh3)2][Au(CN)2]}n (CuAu), were obtained by removing the guest water molecules upon heating. Powder X-ray diffraction (PXRD) patterns of AgCu and CuAu are similar to that of AgAu, indicating that they have the same 1D chain structures (Fig. S1A, S2A and S3A†). We conducted Rietveld refinement analysis of AgCu and CuAu using synchrotron PXRD data at 25 °C. These two crystal structures have the same space group as AgAu, and the structures are identical with slight differences of cell parameters (Fig. S4†). Elemental analyses and FT-IR spectra also confirmed the compositions and same structures for the three compounds. The compounds are hereafter denoted as MNMC, where MC is the metal center that links to the C atoms, and MN is the metal center that links to the N atoms (Scheme 1).
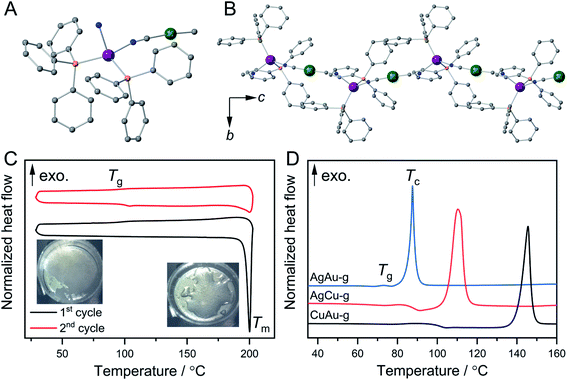 |
| Fig. 1 Crystal structures of AgAu (A) in the Ag+ coordination sphere and (B) 1D chains along the c-axis. Grey, blue, orange, violet, and green are C, N, P, Ag, and Au, respectively. (C) First (black) and second (red) DSC upscan/downscan cycles of CuAu. Melting temperature Tm and glass transition temperature Tg are shown. (D) First DSC upscan of MNMC-g from 35 to 160 °C. The heating rate is 10 °C min−1. | |
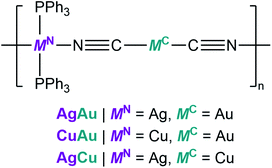 |
| Scheme 1 Illustration of the chemical structures of MNMC. | |
Crystal melting and formation of melt-quenched glass (MQG)
Thermogravimetric analysis (TGA) was carried out to check the thermal behaviors of MNMC. AgCu and CuAu showed no weight loss at 200 °C, while AgAu exhibited higher thermal stability and no weight loss at 220 °C. All MNMCs melt upon heating. Differential scanning calorimetry (DSC) clarified that the melting temperatures (Tm) of AgAu, AgCu, and CuAu are 218, 198, and 197 °C, respectively. The melt phases of CuAu and AgAu are colorless, and that of AgCu is yellow (Fig. S1B, S2B and S3B†). The enthalpy and entropy changes in phase transition (ΔHm and ΔSm) calculated from DSC are summarized in Table S1.†AgAu exhibits higher Tm and ΔHm (65 kJ mol−1) than CuAu and AgCu, suggesting the stronger coordination bonds and MC⋯H and C–H⋯π interactions. Glass transition (Tg) of CuAu was observed at 100 °C in the first cooling process, and the second heating–cooling cycle (Fig. 1C). We denote the glassy state of CuAu obtained by melt-quenching as CuAu-MQG hereafter. Glassy materials usually exhibit a Tg/Tm (K/K) value of 2/3, which is summarized as the empirical Kauzmann 2/3 rule.29,30CuAu-MQG has a Tg/Tm value of 0.79, which is higher than the commonly observed 2/3 ratio (=0.67), indicative of its high glass forming ability.31AgAu and AgCu did not form glass but crystallized upon cooling as confirmed by DSC and PXRD (Fig. S5†). Although these compounds have identical crystal structures, they show different Tm and ΔHm. Higher ΔHm in AgAu and AgCu than in CuAu suggests the stronger interactions (coordination bonds and other non-covalent interactions) in coordination polymers, which result in faster recrystallization kinetics than glass formation.32 Elemental analysis suggested that the composition of MNMCs does not change by the melt-quench process (Table S2†).
Formation of mechanically induced glasses (MIGs) and thermal properties
Ball milling of CP crystals is another procedure to obtain a glassy state.5,33 Ball milling of three MNMCs under an Ar atmosphere yielded the MIGs that are denoted as MNMC-g hereafter. MNMC-g exhibited broad PXRD patterns suggesting their amorphous nature. TGA confirmed that the decomposition temperatures of MNMC-g are the same as MNMC (Fig. S1–S3†). DSC confirmed that the onset Tg of MNMC-g are 73 °C, 84 °C, and 100 °C for AgAu-g, AgCu-g, and CuAu-g, respectively. Above Tg, we found the exothermal peaks which correspond to crystallization. The crystallization peak temperatures (Tc) are 88 °C, 116 °C, and 146 °C for AgAu-g, AgCu-g, and CuAu-g (Fig. 1D). PXRD confirmed that all MNMC-g crystallized back to the original crystal structures MNMC (Fig. S1A, S2A and S3A†). Different thermal behaviors were found between CuAu-MQG and CuAu-g in the heating process of the DSC profile, in which CuAu-MQG did not show Tc at 146 °C. This is due to their different particle sizes and surface areas. The larger surface area of CuAu-g induces higher probability for crystallization.23 We ground CuAu-MQG into a powder and then performed DSC. Tg and Tc at 100 and 146 °C were observed in the first heating process of the DSC profile, which is identical to CuAu-g. No exothermal peak was observed in the second heating process because of the formation of the bulk melt-quenched glass (Fig. S6†). CuAu-g exhibited the largest temperature window between Tg and Tc of 46 °C among MNMC-g (15 °C for AgAu-g and 32 °C for AgCu-g). The large operating window of CuAu-g provides an opportunity for glass engineering since crystallization hardly happens during the thermal treatment.34
Structural characterization of MIGs
FT-IR and Raman spectra were measured to study the local structural differences between MNMC and MNMC-g, as the –C
N bond (νCN) vibration is sensitive to its chemical environment.35 The four cyanide vibration peaks in CuAu are due to the coupling of stretching modes between cyanide bonds.23,36 In CuAu-g, these vibrational peaks were broader and red-shifted to 2158 and 2118 cm−1, indicating the elongation of the MN–N coordination bond (Fig. S7†).37,38 Only the broadness of the νCN bands is observed in AgCu-g and AgAu-g with a negligible shift (Fig. S8 and S9†). In the Raman spectra of CuAu, the peak at 128.9 cm−1 that is assigned to Cu–P vibration disappeared by vitrification.39,40 Same as CuAu-g, the peaks corresponding to Ag–P at 125.1 and 126.7 cm−1 in AgCu-g and AgAu-g disappeared (Fig. S10–S12†). The loss of crystallinity results in a broadening or disappearance of peaks in the Raman spectra.41–43
We performed X-ray absorption spectroscopy (XAS) for CuAu and CuAu-g to understand the local structure around Cu+. They showed identical X-ray absorption near-edge structure (XANES) spectra with the intense rising-edge 1s to 4p transition lies at 8980 eV, which is identical to Cu2O. This suggests that Cu in CuAu-g maintains the +1 oxidation state (Fig. S13†).44 The radial distribution functions (RDFs), obtained from the Fourier-transformed Cu K-edge extended X-ray absorption fine structure (EXAFS) spectra, showed a similar shape in the range of 1.2 to 2.3 Å corresponding to the first coordination sphere of Cu+. The lower peak intensity in CuAu-g than in CuAu is due to the structural disorder. The fitting results of k3 weighted RDFs indicate that the coordination number of Cu+ is 4.3 ± 0.6 and 4.2 ± 1.0 in CuAu and CuAu-g (Fig. S14†). The results suggest that the tetrahedral coordination geometry of Cu is preserved in the glassy state. X-ray total scattering measurements and corresponding pair distribution function (PDF) analyses were carried out to investigate the structural periodicity in MNMC-g. We compared the PDF profile of MNMC-g with the simulated profile of MNMC. The peaks at 5.0, 9.8 (peak 1), and 13.6 Å (peak 2) in Fig. 2A of CuAu-g correspond to Cu–NC–Au, Cu–Au(CN)2–Cu/Au–Cu(NC)2–Au, and Cu–Au(CN)2–Cu–NC–Au (Fig. 2A and B). This indicates the preservation of the periodic order along the 1D chain in the glassy state. PDF profiles of AgCu-g and AgAu-g showed the same periodic features as CuAu-g (Fig. S15†). We conclude that the 1D chain structures are mainly preserved in MNMC-g with disordered packing modes.
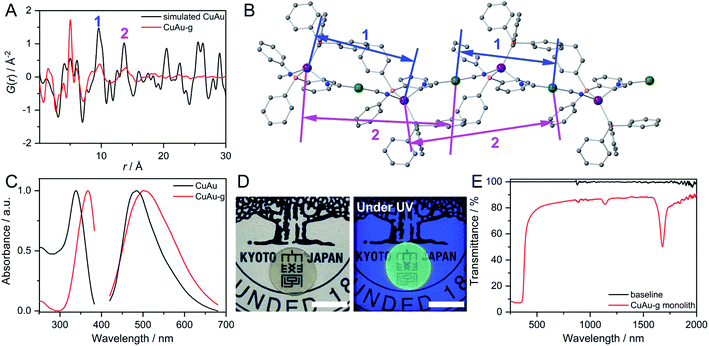 |
| Fig. 2 (A) PDF profiles of simulated CuAu and CuAu-g at 25 °C. (B) Atomic pairs corresponding to peak 1 and 2 in the PDF profile of CuAu. Grey, blue, orange, violet, and green are C, N, P, Cu, and Au, respectively. (C) Excitation and emission spectra of CuAu and CuAu-g at 25 °C. (D) Transparent monolith of CuAu-g made by hot-pressing with/without UV light. Scale bar is 1 cm. (E) Transmittance of the CuAu-g monolith from 250 nm to 2000 nm. | |
Solid-state NMR (SSNMR) at 25 °C was carried out to study the structural dynamics (Fig. S16†). 31P NMR spectra of CuAu exhibited peaks at 8.1, 3.2, −1.6, −6.6, and −12.4 ppm ascribed to Cu–P and P–P couplings. Broad peaks at −2.5 and 40 ppm were observed in CuAu-g due to the structural disorder. The peak at 40 ppm is ascribed to Cu(PPh3)2NC units.45 The 1H spin-lattice relaxation time (T1) of PPh3 in CuAu-g is 2.60 s, significantly shorter than that of CuAu (47.37 s). As a same trend, T1 values of 1H for AgCu-g and AgCu are 3.03 and 121.21 s, respectively. The shorter T1 in MNMC-g suggests the higher mobility of PPh3 ligands by the smaller MC⋯H and C–H⋯π interactions as a result of weakened inter-chain interaction.46
Photoluminescence properties of MIGs
The excitation and emission spectra of CuAu and CuAu-g are shown in Fig. 2C. CuAu showed the emission peak at 484 nm and excitation maximum at 338 nm. Previous studies have confirmed that the emission of MNMC is from metal-to-metal-to-ligand charge transfer (MMLCT).28 The LUMO of MNMC is composed of π*(C
N) and p*(MN) orbitals and HOMO is composed of the dxy2 orbital of the MNN2P2 chromophore with σ(MN–P) bonding, π-orbital from phenyl rings and π(C
N) bonding. The excitation and emission maxima red-shifted to 367 and 500 nm in CuAu-g. The emission and excitation spectra of CuAu-MQG show the same feature as CuAu-g (Fig. S17A†). The alteration of coordination bond lengths and molecular packing upon glass formation would affect the electronic structures and induce different photophysical properties. The changes contribute to the different energy levels of bonding orbitals and antibonding orbitals. This causes the smaller HOMO–LUMO bandgap and the bathochromic shift of the MMLCT emission band in CuAu-g.47,48 The full width at half maximum of the emission spectra of CuAu and CuAu-g is 96 and 140 nm. The larger FWHM is consistent with its disordered structure. AgCu, AgAu, and their glassy states exhibit weaker emissions than CuAu and CuAu-g. In AgCu and AgAu, the emission band did not significantly shift by amorphization because the HOMO–LUMO band gap is kept at a similar level (Fig. S17B and C†). MNMC exhibited two-component decay of the photoluminescence lifetime in the microsecond time scale, implying the phosphorescence mechanism. CuAu has 22.7 μs (61.7%) and 4.6 μs (38.3%) of photoluminescence lifetimes. CuAu-g exhibits 8.0 μs (36.2%) and 1.4 μs (63.8%). The average photoluminescence lifetime is 15.8 μs for CuAu and 3.8 μs for CuAu-g. The shorter lifetime in a glassy state than that of the crystal is due to the following reasons. (i) Increased energy trapping states by the formation of defects and (ii) enhanced molecular dynamics in glassy states as confirmed by the relaxation time of SSNMR.49,50 The other two glasses MNMC-g also showed a shorter photoluminescence lifetime than MNMC (Fig. S18†).
Preparation of a transparent bulk glass monolith from MIGs and laser-induced crystallization
One of most important advantages of glass is the processability of materials in a wide range of scales. We prepared a bulk glass monolith by the vacuum hot-press technique. We first preheated the pellet of CuAu-g at 105 °C which is higher than its Tg (100 °C). The pressure of 60 kN was then applied to the pellet and maintained for 30 min. A bulk glass monolith with a diameter of 1.273 cm and thickness of 0.438 mm was obtained after cooling to 25 °C. The prepared CuAu-g monolith maintains its amorphous state as confirmed by PXRD (Fig. S19A†). It exhibits high transparency and maintains green emission under UV light irradiation (365 nm, Fig. 2D). The transmittance is over 80% from 400 to 2000 nm, comparable to soda-lime glass which is used for windows.51–53 The absorption below 400 nm is ascribed to the MMLCT absorption band. Two absorption peaks observed at 1139 and 1680 nm are from the C–H stretching from the phenyl groups of PPh3, as these two peaks are observed at similar wavelengths from the reflectance diffusion spectra of PPh3 (Fig. 2E and S19B†).54 SEM and microscope images indicate that the monolith has a crack-free and smooth surface (Fig. S20A–C†). We prepared the crystalline CuAu pellet under the same hot-press conditions as the control experiment. The obtained crystalline pellet was opaque, and particles separated by grain-boundaries are observed during the SEM of its surface and cross section (Fig. S20D and E†).
A similar procedure was used to prepare the transparent monolith of AgCu-g, and the transmittance is 80% from 400 to 2000 nm (Fig. S21†). On the other hand, the transparent monolith of AgAu-g was not successfully prepared because crystallization occurred during hot-pressing due to its small Tg–Tc window of 15 °C.
The phase transition from amorphous to crystal by laser irradiation is a crucial phenomenon for the preparation of glass ceramics and phase memory devices.55–58 For instance, crystal and amorphous states of ternary alloy GeSbTe systems have different reflectance, and they are used in the Blu-ray disc. The phase transition from MNMC-g to MNMC has been confirmed by DSC and PXRD, which inspired us to demonstrate the glass-to-crystal transformation triggered by laser irradiation. AgCu-g was chosen because its lower Tc (116 °C) than CuAu-g (Tc = 146 °C), which means less thermal energy is required to induce crystallization. We first tried to induce crystallization of AgCu-g by direct irradiation of the monolith with a 730 nm laser . It was not successful due to the low absorption of the 730 nm laser in the glass. We then mixed anhydrous CuSO4 (particle sizes are ca. 2 μm) into the glasses as the laser absorber. It is known that Cu2+ in CuSO4 shows a photothermal effect from forbidden d–d transitions.59,60 Homogeneous distribution of the mixed CuSO4 particles would generate heat to induce the crystallization of local domains in the glasses. 20 mg of CuSO4 was mixed with 180 mg of AgCu-g by ball-milling under an Ar atmosphere. The PXRD pattern of the mixed powder AgCu-g-CuSO4 contains characteristic peaks of only CuSO4 (Fig. S22A†). Reflectance diffusion spectra of AgCu-g-CuSO4 showed an absorption band at 700 nm corresponding to the absorption of CuSO4 (Fig. S22B†). The bulk monolith of AgCu-g-CuSO4 obtained by the hot-press process maintains its transparency (>60%, Fig. S21C†). CuSO4 particles with a diameter of 2 μm are homogeneously distributed on the surface of the monolith, confirmed by SEM and energy-dispersive X-ray spectroscopy (EDS) mapping (Fig. S22D and E†). Fig. 3A shows the example of the surface of the monolith of AgCu-g-CuSO4 observed using the microscope. We irradiated some spots on the monolith for 60 min using a 730 nm laser of 47 μm size. The irradiated domain turned grey. Confocal Raman spectroscopy within the range of 300 nm was carried out to identify the phase of irradiated areas (Fig. 3B). The Raman spectra of grey areas 1 and 2 in Fig. 3A showed an identical pattern to AgCu. The Ag–P vibration peak at 125.1 cm−1 was found in the Raman spectra. The relative intensities of the two cyanide peaks at 2130.8 and 2153.6 cm−1 are the same as AgCu. These results suggest that the crystalline AgCu phase was generated in areas 1 and 2 upon laser irradiation. The change was not observed in areas without laser irradiation, as also shown in Fig. 3B. This observation further proves the occurrence of glass-to-crystal transition through laser irradiation. Laser-induced crystallization was also observed on the surface of AgCu-g-CuSO4 powder pellets (Fig. S23†).
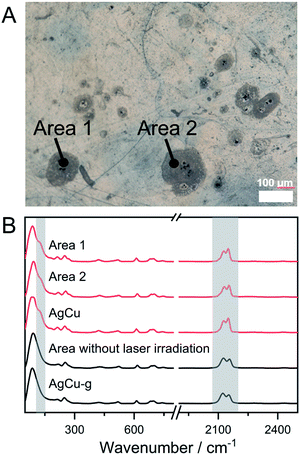 |
| Fig. 3 (A) Surface of the AgCu-g-CuSO4 monolith under the microscope. Areas 1 and 2 are irradiated using a 47 μm size laser. Other grey spots are also crystallized domains. (B) Confocal Raman spectra at areas 1 and 2, and the area without laser irradiation. Spectra of pure AgCu and AgCu-g are also shown. | |
Conclusions
We have explored three luminescent CP glasses MNMC-g composed of d10 metal cyanides and triphenylphosphine. Structural analyses revealed that the glasses are constructed from 1D chains which originate from their crystal structures. Higher structural dynamics in MNMC-g were confirmed by solid-state NMR. The disordered structures and enhanced molecular dynamics contributed to a shorter photoluminescence lifetime of MNMC-g than crystalline MNMC. Centimeter scale glass monoliths were prepared by the hot-press technique, and they exhibited both strong emission and high transparency over 80% from 400 to 2000 nm. Furthermore, the bulk transparent glass doped with a light absorber demonstrated the laser-induced crystallization at the target spot. The strong photoluminescence at room temperature and soft, moldable character of CP/MOF glasses in micro to macro scales will provide opportunities in lighting and photonic applications.
Data availability
All data needed to evaluate the conclusions in the paper are present in the paper and supporting information. The data that support the findings of this study are available from the corresponding author upon request.
Author contributions
S. H. designed the project. Z. F. and C. D. synthesized the compounds. Z. F. conducted and analyzed PXRD, TGA, DSC, SEM, FT-IR, Raman, diffusion reflectance, photoluminescence, EXAFS, XAS and laser irradiation experiments. A. D., R. Z. and S. T. conducted and analyzed photoluminescence lifetime. Y-S. W. conducted Rietveld analysis. S. H. and Z. F. wrote the paper.
Conflicts of interest
There are no conflicts to declare.
Acknowledgements
The work was supported by the Japan Society of Promotion of Science (JSPS) for a Grant-in-Aid for Scientific Research (B) (JP21H01950) and a Grant-in-Aid for Challenging Research (Exploratory, JP19K22200) from the Ministry of Education, Culture, Sports, Science and Technology, Japan. We acknowledge Drs Kazuo Kato and Hiroki Yamada for experimental support at Synchrotron SPring-8 BL01B1 and BL04B2 beamlines, and Dr Takahiro Fujiwara for his support in laser irradiation experiments.
References
- S. Horike, S. S. Nagarkar, T. Ogawa and S. Kitagawa, Angew. Chem., Int. Ed., 2020, 59, 6652–6664 CrossRef CAS PubMed.
- T. D. Bennett, F. X. Coudert, S. L. James and A. I. Cooper, Nat. Mater., 2021, 20, 1179–1187 CrossRef CAS PubMed.
- J. Fonseca, T. Gong, L. Jiao and H.-L. Jiang, J. Mater. Chem. A, 2021, 9, 10562–10611 RSC.
- S. Horike, N. Ma, Z. Fan, S. Kosasang and M. M. Smedskjaer, Nano Lett., 2021, 21, 6382–6390 CrossRef CAS PubMed.
- W. Chen, S. Horike, D. Umeyama, N. Ogiwara, T. Itakura, C. Tassel, Y. Goto, H. Kageyama and S. Kitagawa, Angew. Chem., Int. Ed., 2016, 55, 5195–5200 CrossRef CAS PubMed.
- T. Ogawa, K. Takahashi, S. S. Nagarkar, K. Ohara, Y. L. Hong, Y. Nishiyama and S. Horike, Chem. Sci., 2020, 11, 5175–5181 RSC.
- N. Ma, S. Kosasang, A. Yoshida and S. Horike, Chem. Sci., 2021, 12, 5818–5824 RSC.
- Y. Wang, H. Jin, Q. Ma, K. Mo, H. Mao, A. Feldhoff, X. Cao, Y. Li, F. Pan and Z. Jiang, Angew. Chem., Int. Ed., 2020, 59, 4365–4369 CrossRef CAS PubMed.
- J. Li, J. Wang, Q. Li, M. Zhang, J. Li, C. Sun, S. Yuan, X. Feng and B. Wang, Angew. Chem., Int. Ed., 2021, 60, 21304–21309 CrossRef CAS PubMed.
- R. Lin, X. Li, A. Krajnc, Z. Li, M. Li, W. Wang, L. Zhuang, S. Smart, Z. Zhu, D. Appadoo, J. R. Harmer, Z. Wang, A. G. Buzanich, S. Beyer, L. Wang, G. Mali, T. D. Bennett, V. Chen and J. Hou, Angew. Chem., Int. Ed., 2022, 61, e202112880 CAS.
- G. Yu, C. H. Lee, D. Mihailovic, A. J. Heeger, C. Fincher, N. Herron and E. M. McCarron, Phys. Rev. B Condens Matter., 1993, 48, 7545–7553 CrossRef CAS PubMed.
- J. Zhao, X. Zheng, E. P. Schartner, P. Ionescu, R. Zhang, T. L. Nguyen, D. Jin and H. Ebendorff-Heidepriem, Adv. Opt. Mater., 2016, 4, 1507–1517 CrossRef CAS.
- F. Meinardi, F. Bruni and S. Brovelli, Nat. Rev. Mater., 2017, 2, 17072 CrossRef CAS.
- F. Meinardi, S. Ehrenberg, L. Dhamo, F. Carulli, M. Mauri, F. Bruni, R. Simonutti, U. Kortshagen and S. Brovelli, Nat. Photonics, 2017, 11, 177–185 CrossRef CAS.
- A. Qiao, H. Tao, M. P. Carson, S. W. Aldrich, L. M. Thirion, T. D. Bennett, J. C. Mauro and Y. Yue, Opt. Lett., 2019, 44, 1623–1625 CrossRef CAS PubMed.
- L. Frentzel-Beyme, M. Kloß, R. Pallach, S. Salamon, H. Moldenhauer, J. Landers, H. Wende, J. Debus and S. Henke, J. Mater. Chem. A, 2019, 7, 985–990 RSC.
- M. A. Ali, J. Ren, T. Zhao, X. Liu, Y. Hua, Y. Yue and J. Qiu, ACS Omega, 2019, 4, 12081–12087 CrossRef CAS PubMed.
- S. Vaidya, O. Veselska, A. Zhadan, M. Diaz-Lopez, Y. Joly, P. Bordet, N. Guillou, C. Dujardin, G. Ledoux, F. Toche, R. Chiriac, A. Fateeva, S. Horike and A. Demessence, Chem. Sci., 2020, 11, 6815–6823 RSC.
- J. F. Keggin and F. D. Miles, Nature, 1936, 137, 577–578 CrossRef CAS.
- J. A. Hill, A. L. Thompson and A. L. Goodwin, J. Am. Chem. Soc., 2016, 138, 5886–5896 CrossRef CAS PubMed.
- M. J. Cliffe, E. N. Keyzer, M. T. Dunstan, S. Ahmad, M. F. L. De Volder, F. Deschler, A. J. Morris and C. P. Grey, Chem. Sci., 2019, 10, 793–801 RSC.
- D. Venkataraman, S. Lee, J. S. Moore, P. Zhang, K. A. Hirsch, G. B. Gardner, A. C. Covey and C. L. Prentice, Chem. Mater., 1996, 8, 2030–2040 CrossRef CAS.
- C. Das, T. Ogawa and S. Horike, Chem. Commun., 2020, 56, 8980–8983 RSC.
- C. Das and S. Horike, Faraday Discuss., 2021, 225, 403–413 RSC.
- B. K. Shaw, A. R. Hughes, M. Ducamp, S. Moss, A. Debnath, A. F. Sapnik, M. F. Thorne, L. N. McHugh, A. Pugliese, D. S. Keeble, P. Chater, J. M. Bermudez-Garcia, X. Moya, S. K. Saha, D. A. Keen, F. X. Coudert, F. Blanc and T. D. Bennett, Nat. Chem., 2021, 13, 778–785 CrossRef CAS PubMed.
- M. Ghazzali, M. H. Jaafar, S. Akerboom, A. Alsalme, K. Al-Farhan and J. Reedijk, Inorg. Chem. Commun., 2013, 36, 18–21 CrossRef CAS.
- M. Ghazzali, M. H. Jaafar, K. Al-Farhan, S. Akerboom and J. Reedijk, Inorg. Chem. Commun., 2012, 20, 188–190 CrossRef CAS.
- M. Jaafar, A. Pevec, S. Akerboom, A. Alsalme, K. Al-Farhan, M. Ghazzali and J. Reedijk, Inorg. Chim. Acta, 2014, 423, 233–237 CrossRef CAS.
- K. Ito, C. T. Moynihan and C. A. Angell, Nature, 1999, 398, 492–495 CrossRef CAS.
- G. N. Greaves and S. Sen, Adv. Phys., 2007, 56, 1–166 CrossRef CAS.
- A. Qiao, T. D. Bennett, H. Tao, A. Krajnc, G. Mali, C. M. Doherty, A. W. Thornton, J. C. Mauro, G. N. Greaves and Y. Yue, Sci. Adv., 2018, 4, eaao6827 CrossRef PubMed.
- M. Liu, R. D. McGillicuddy, H. Vuong, S. Tao, A. H. Slavney, M. I. Gonzalez, S. J. L. Billinge and J. A. Mason, J. Am. Chem. Soc., 2021, 143, 2801–2811 CrossRef CAS PubMed.
- Y. Ohara, A. Hinokimoto, W. Chen, T. Kitao, Y. Nishiyama, Y. L. Hong, S. Kitagawa and S. Horike, Chem. Commun., 2018, 54, 6859–6862 RSC.
- M. L. F. Nascimento, L. A. Souza, E. B. Ferreira and E. D. Zanotto, J. Non-Cryst. Solids, 2005, 351, 3296–3308 CrossRef CAS.
- K. I. Hadjiivanov, D. A. Panayotov, M. Y. Mihaylov, E. Z. Ivanova, K. K. Chakarova, S. M. Andonova and N. L. Drenchev, Chem. Rev., 2021, 121, 1286–1424 CrossRef CAS PubMed.
- A. A. Schilt, Inorg. Chem., 2002, 3, 1323–1325 CrossRef.
- M. Shao, M.-X. Li, Z.-X. Wang, X. He and H.-H. Zhang, Cryst. Growth Des., 2017, 17, 6281–6290 CrossRef CAS.
- H. Yoshino, K. Yamagami, H. Wadati, H. Yamagishi, H. Setoyama, S. Shimoda, A. Mishima, B. Le Ouay, R. Ohtani and M. Ohba, Inorg. Chem., 2021, 60, 3338–3344 CrossRef CAS PubMed.
- G. B. Deacon and J. H. S. Green, Spectrochim. Acta, Part A, 1968, 24, 845–852 CrossRef CAS.
- D. A. Edwards and R. Richards, Spectrochim. Acta, Part A, 1978, 34, 167–171 CrossRef.
- G. Wang, Y. Ling, H. Wang, X. Yang, C. Wang, J. Z. Zhang and Y. Li, Energy Environ. Sci., 2012, 5, 6180–6187 RSC.
- H. Cui, W. Zhao, C. Yang, H. Yin, T. Lin, Y. Shan, Y. Xie, H. Gu and F. Huang, J. Mater. Chem. A, 2014, 2, 8612–8616 RSC.
- Y. Li, P. Yan, C. Guo and Q. Xu, Chem. Commun., 2020, 56, 7805–7808 RSC.
- N. C. Tomson, K. D. Williams, X. Dai, S. Sproules, S. DeBeer, T. H. Warren and K. Wieghardt, Chem. Sci., 2015, 6, 2474–2487 RSC.
- G. A. Bowmaker, J. C. Dyason, P. C. Healy, L. M. Engelhardt, C. Pakawatchai and A. H. White, J. Chem. Soc., Dalton Trans., 1987, 1089–1097 RSC.
- S. S. Nagarkar, H. Kurasho, N. T. Duong, Y. Nishiyama, S. Kitagawa and S. Horike, Chem. Commun., 2019, 55, 5455–5458 RSC.
- H. Araki, K. Tsuge, Y. Sasaki, S. Ishizaka and N. Kitamura, Inorg. Chem., 2005, 44, 9667–9675 CrossRef CAS PubMed.
- E. Kwon, J. Kim, K. Y. Lee and T. H. Kim, Inorg. Chem., 2017, 56, 943–949 CrossRef CAS PubMed.
- C. L. Whittington, L. Wojtas and R. W. Larsen, Inorg. Chem., 2014, 53, 160–166 CrossRef CAS PubMed.
- M. A. Syzgantseva, N. F. Stepanov and O. A. Syzgantseva, J. Phys. Chem. Lett., 2019, 10, 5041–5046 CrossRef CAS PubMed.
- J. M. Florence, F. W. Glaze, C. H. Hahner and R. Stair, J. Am. Ceram. Soc., 1948, 31, 328–331 CrossRef CAS.
- M. Rubin, Sol. Energy Mater., 1985, 12, 275–288 CrossRef CAS.
- P. Němec, M. Olivier, E. Baudet, A. Kalendová, P. Benda and V. Nazabal, Mater. Res. Bull., 2014, 51, 176–179 CrossRef.
- L. Ma, Y. Peng, Y. Pei, J. Zeng, H. Shen, J. Cao, Y. Qiao and Z. Wu, Sci. Rep., 2019, 9, 9503 CrossRef PubMed.
- H. J. Stocker, Appl. Phys. Lett., 1969, 15, 55–57 CrossRef CAS.
- N. Yamada, E. Ohno, N. Akahira, K. i. Nishiuchi, K. i. Nagata and M. Takao, Jpn. J. Appl. Phys., 1987, 26, 61–66 CrossRef.
- H. S. P. Wong, S. Raoux, S. Kim, J. Liang, J. P. Reifenberg, B. Rajendran, M. Asheghi and K. E. Goodson, Proc. IEEE, 2010, 98, 2201–2227 Search PubMed.
- S. Raoux, W. Welnic and D. Ielmini, Chem. Rev., 2010, 110, 240–267 CrossRef CAS PubMed.
- T. Honma, Y. Benino, T. Fujiwara and T. Komatsu, Appl. Phys. Lett., 2006, 88, 231105 CrossRef.
- T. Komatsu, R. Ihara, T. Honma, Y. Benino, R. Sato, H. G. Kim and T. Fujiwara, J. Am. Ceram. Soc., 2007, 90, 699–705 CrossRef CAS.
Footnote |
† Electronic supplementary information (ESI) available: Experimental procedures and supplementary figures, table and schemes. See DOI: 10.1039/d1sc06751f |
|
This journal is © The Royal Society of Chemistry 2022 |
Click here to see how this site uses Cookies. View our privacy policy here.