DOI:
10.1039/D2RA05679H
(Paper)
RSC Adv., 2022,
12, 29170-29176
3D hierarchical cobalt vanadate nanosheet arrays on Ni foam coupled with redox additive for enhanced supercapacitor performance†
Received
9th September 2022
, Accepted 4th October 2022
First published on 12th October 2022
Abstract
Room-temperature synthesized 3D hierarchical cobalt vanadate (Co3V2O8) nanosheet arrays on Ni foam for use as supercapacitor electrode is presented. In a 3 M KOH electrolyte, the electrode exhibits a capacitance of 109.9 mA h g−1 (878.9 F g−1) at a current density of 1 A g−1. The capacitance is enhanced to 198.1 mA h g−1 (1584.5 F g−1) at 1 A g−1 through the addition of 0.05 M redox-additive K3[Fe(CN)6] into the KOH electrolyte. Furthermore, the Co3V2O8/activated carbon asymmetric supercapacitor cell with the advanced electrolyte outperforms most reported Co3V2O8-based electrodes with a remarkable energy density of 55.5 W h kg−1 at an 800 W kg−1 power density. Combining a facile synthetic strategy and excellent electrochemical performance, the obtained Co3V2O8 exhibits potential for practical application.
1. Introduction
Exploration of renewable energy has been a continuous effort for reaching a green and sustainable world.1,2 One of the keys is related to an advanced energy storage device, namely, asymmetric supercapacitors (ASCs). ASC is composed of a positive electrode made from a faradaic, battery-like material and a negative electrode made from a non-faradaic, electric double-layer material.2–4 To date, the most effective negative electrodes are carbon-based materials.5–7 Thus, recent research interest in ASCs focuses on positive electrode materials.8–11 One of the battery-like electrode materials, i.e., metal vanadate, holds great potential owing to its layered structure and rich valence states. Common metal vanadates include Ni1−xVxO2, Zn2V2O7, BiVO4, Ni3V2O8, and Co3V2O8.12–15 Among them, cobalt vanadate (Co3V2O8) has drawn significant attention owing to its excellent stability, outstanding capacitance, low-toxicity, and simplicity of preparation.
Hydrothermally synthesized Co3V2O8 has a specific capacitance (Csp) of 505 F g−1 at 0.625 A g−1 and an energy density (Ed) of 28 W h kg−1 at a power density (Pd) of 1400 W kg−1.16 One-pot solvothermal Co3V2O8/graphene composite showed a Csp of 528.2 F g−1 at 0.5 A g−1, and 80% capacitance remaining after 5000 cycles.13 Hydrothermally synthesized Co3V2O8 nanoplate electrode shows a remarkable Csp of 739 F g−1 at 0.5 A g−1 and 2000 cycles retention of 95.3%.17 Electrode based on 3D porous Co3V2O8 microflowers synthesized using a co-precipitation method exhibits a Csp of 351 F g−1 at 1 A g−1 with 103% capacitance retention after 30
000 cycles.18 An Ed of 19 W h kg−1 at Pd of 375.8 W kg−1 was also reported. NiO–Co3(VO4)2 grown on nickel foam shows a Csp of 1166 F g−1 at 0.5 A g−1 and cycle stability of 99.4% after 5000 cycles.19 The Ed is 38.8 W h kg−1 at a Pd of 397.9 W kg−1. Heterostructure of Co3V2O8–Ni3V2O8/carbon composite exhibits Csp of 1731 F g−1 at 1 A g−1 and an Ed of 59.7 W h kg−1 at high Pd of 1970 W kg−1.20 The excellent SC performance is obtained due to the rich redox activities of the cobalt vanadate, and high active surface areas. On the other hand, the use of redox additive (RA) electrolyte has also been demonstrated to enhance the Csp.21–25
Herein, we present a room-temperature process to synthesize Co3V2O8 nanowalls on Ni foam (NF) using a template-assisted growth. Also, K3[Fe(CN)6] RA electrolyte is used to enhance ionic conductivity of electrolyte and provide additional redox reactions, targeting in the further capacitance improvements. With the use of the RA electrolyte, a capacitance of 198.1 mA h g−1 (1584.5 F g−1) at 1 A g−1 is demonstrated. Furthermore, we show that an ASC having an activated carbon (AC) negative electrode, Co3V2O8 positive electrode, and the RA electrolyte provides an excellent Ed of 55.5 W h kg−1 at a Pd of 800 W kg−1 and 82% capacitance remaining after 10
000 cycles.
2. Experimental
2.1 Chemicals
All chemicals were used as received. 2-methylimidazole (2-MIM, 99%, Sigma Aldrich), cobalt nitrate hexahydrate (Co(NO3)2·6H2O, 98%, Baker Analyzed Reagent), and sodium orthovanadate (Na3VO4, ≥90%, Sigma Aldrich), and potassium hydroxide (KOH, ≥85%, Honeywell Fluka).
2.2 Synthesis of ZIF-67
ZIF-67 was synthesized by a precipitation method.26 A piece of 2 × 3 cm NF was first cleaned with 10 mL HCl 37% for 5 minutes, followed by deionized (DI) water and ethanol in sequence washing. The NF is used as the substrate for the growth of ZIF-67. To grow ZIF-67, a 20 mL solution A consisting of 2 mmol Co(NO3)2·6H2O was first made under stirring for 30 minutes to form solution A. Meanwhile, 20 mL solution B containing 16 mmol of 2-MIM was also prepared. After that, the two prepared solutions were quickly mixed. After 5 minutes of stirring, the washed NF was then deep into the prepared solution at room temperature for 3 hours. The final product was achieved after washing with DI water and ethanol, followed by drying with flowing nitrogen gas.
2.3 Synthesis of Co3V2O8
To convert the ZIF-67 into Co3V2O8, the ZIF-67@NF was immersed in 20 mL of 0.1 M Na3VO4 aqueous solution. After a three hours' ion exchange process at room temperature, the resulting NF was soaked in ethanol and DI water, then dried under a nitrogen flow. The active material on the NF was calculated to be 1.6 mg cm−2.
2.4 Material characterizations
The morphology and structure were examined utilizing transmission electron microscopy (TEM, JEOL-2100F CS STEM) and scanning electron microscopy (SEM, JSM-6701F). X-ray photoelectron spectroscopy (XPS, PHI 5000) was used to analyze the surface chemistry. Crystalline structure was examined using X-ray diffraction (XRD, Rigaku X-ray Diffractometer) with a CuKα radiation source.
2.5 Electrochemical characterizations
Electrochemical characterization of the electrode was conducted using a three-electrode cell having 3 M KOH or RA electrolyte. The Co3V2O8 nanowalls on NF (1 cm × 1 cm) was used as the working electrode. The reference was a saturated calomel electrode (SCE) with saturated 3 M KCl aqueous solution, and a Pt rod was the counter electrode. All of the electrochemical tests were done using an Autolab NOVA system. Electrochemical impedance spectroscopy (EIS) analysis was performed with 5 mV amplitude and 100 kHz to 0.01 Hz frequency range.
2.6 Fabrication of ASC
The ASC consists of Co3V2O8 and AC (demoted as Co3V2O8//AC) was assembled. As-synthesized Co3V2O8 on NF was used as the positive electrode. For the AC negative electrode, 8 mg of AC, 1 mg of polyvinylidene fluoride, 1 mg of carbon black, and 1 mL of N-methyl-2-pyrrolidone were first prepared. After 12 h of stirring, the obtained slurry was dropped cast on an NF substrate, then dried at 60 °C for 12 h. The Co3V2O8 positive electrode was directly used after the synthesis. The negative electrode's active mass was decided following the charge balance relationship, as shown in eqn (1): |
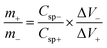 | (1) |
where m, ΔV, and Csp are the mass, potential window, and specific capacitance, respectively; while “−” and “+” represent the negative and positive electrodes, respectively.
The Csp was determined using eqn (2):
|
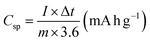 | (2) |
where
t is the discharge period (s),
V is the potential window (V),
m represents the active material's weight (g), and
I the discharge current (A).
Ed and
Pd were determined using
eqn (3) and
(4), respectively:
|
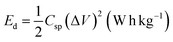 | (3) |
|
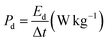 | (4) |
3. Results and discussion
Co3V2O8 were grown on ZIF-67@NF where the ZIF-67 homogenously distributes on the NF (Fig. S1A†) with a uniform thickness of 2.2 μm (Fig. S1B†) and a plate-like morphology (Fig. S1C†). After the ion exchange process, uniform coverage of the material on the NF surface remains, as shown in Fig. 1A. The nanoplate ZIF-67 turns into nanowall morphology (Fig. 1B). The average thickness of the nanowalls is about 30 nm (Fig. 1C), much less than that of the nanoplates. The nanowall is further examined using TEM, as illustrated in Fig. 1D. A high-resolution TEM image (Fig. 1E) shows d-spacings of 0.208 and 0.254 nm, corresponding to the (042) and (112) planes of Co3V2O8 (JCPDS no. 74-1487). Various diffraction rings in the selected area electron diffraction (SAED) pattern (Fig. 1F) are indexed to the polycrystalline Co3V2O8, confirming the formation of Co3V2O8 nanowalls. XRD analysis also indicates the formation of low-crystallinity Co3V2O8 (Fig. S2†). EDS elemental distribution and mappings are shown in Fig. 1H and G, respectively. The Co, V, and O uniformly distribute throughout the nanowalls. The Co and V both exhibit multi-valence states of Co2+/Co3+ and V4+/V5+, respectively, as shown by XPS analysis (Fig. S3†).
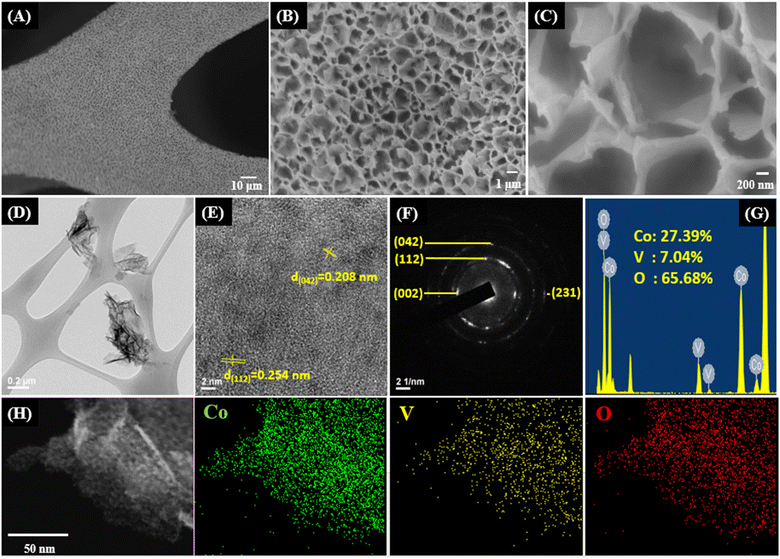 |
| Fig. 1 (A–C) SEM images, (D–E) TEM images, (F) SAED pattern, (G) EDS elemental distribution, and (H) EDS mappings of O, V, and Co elements. | |
CV curves of the Co3V2O8 electrode evaluated using the 3 M KOH and RA electrolytes are displayed in Fig.s S4A† and 2A, respectively. Fig. 2B shows the comparison of the CV curves acquired at 5 mV s−1. With the use of the KOH electrolyte, there are two redox peaks couple, which are ascribed to the reversible redox reactions of Co(II) ↔ Co(III) (at ∼0.03 and ∼0.13 V) and Co(III) ↔ Co(IV) (at ∼0.25 and 0.43 V) reactions, respectively.27 The existence of the redox peaks indicates that the Co3V2O8 electrode is pseudocapacitive. In the case of the RA electrolyte, two redox peaks couple shifting to the positive side are seen. The couple redox peak for Co(II) ↔ Co(III) is also seen. The second redox peaks at the right are attributed to the addition of Fe(CN)63−/Fe(CN)64− (0.5 and 0.27 V vs. SCE) redox peaks.22,28 The Faraday reaction of K3Fe(CN)6 in RA electrolyte provides additional capacitance,14 as shown in eqn (5) below.
|
Fe(CN)4−6 ↔ Fe(CN)3−6 + e−
| (5) |
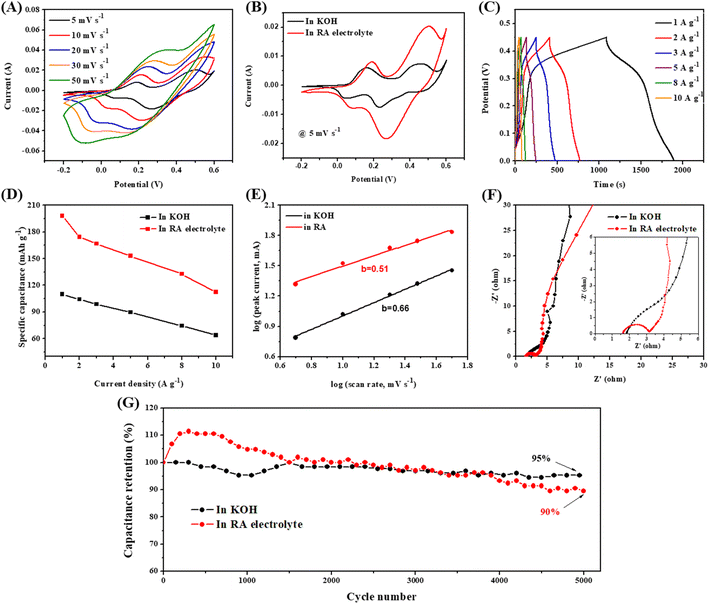 |
| Fig. 2 (A) CV curves obtained using RA electrolyte. (B) Comparative CV curve of the sample tested in KOH and without RA electrolytes at 5 mV s−1. (C) GCD curves collected using RA electrolyte at different current densities. (D) Csp calculated based on the GCD curves. (E) Relationship between cathodic peak current with scan rates on KOH and RA electrolytes. (F) Nyquist plots and (G) Cycle performances obtained using the two different electrolytes. | |
It is also seen that the RA electrolyte gives enhanced current densities, as seen in both of the redox pairs in Fig. 2B. In the first (left-hand side) redox peaks, the Co(II) ↔ Co(III) reaction is enhanced. This is attributed to the improvement of electrolyte conductivity by adding RA, which will be shown later.28,29 For the second redox peaks, the enhancement is primarily due to the redox reactions of K3Fe(CN)6. This then leads to enhanced Csp. The redox reaction occurring in the RA electrolyte is explained as followed.23,30 During the charging process, the oxidation of Co occurs: Co2+ to Co3+ and Co3+ to Co4+, leading to the loss of electrons. The electrons then transfer to Fe(CN)63− which then reduces to Fe(CN)64−. The reversed process takes place during the discharge process. GCD curves obtained at various current densities using the KOH and RA electrolytes are shown in Fig.s S4B† and 2C, respectively. Longer discharge time is seen in the GCD curves obtained using the RA electrolyte, indicating improved Csp. Both KOH and RA electrolytes exhibit pseudocapacitive behaviors. The GCD curves obtained using the KOH show a plateau at about 0.05 V for Co(II) ↔ Co(III) and 0.29 V for Co(III) ↔ Co(IV).18,31 In the case of the RA electrolyte, the lower plateau is insignificance. However the upper plateau is raised to a high V near 0.35 V, indicating the contribution of the redox-active K3[Fe(CN)6].28,29 The Csp measured in different electrolytes was calculated using the GCD results (Fig. 2D). Csp value of 109.9 mA h g−1 (878.9 F g−1) at 1 A g−1 and rate retention of 58% (63.9 mA h g−1 (511 F g−1) at 10 A g−1) were obtained in the KOH electrolyte. Nearly two-fold improvement of the Csp is seen when the RA electrolyte is used, giving a Csp of 198.1 mA h g−1 (1584.5 F g−1) at 1 A g−1 and the remaining 57% at 10 A g−1.
The charge storage mechanism for Co3V2O8 in KOH and RA electrolytes was analyzed using the following power law equation.32,33
where
a, and
b are constants,
ν is the scan rate from CV measurement, and
i is the current. The value of
b is used to determine if the charge storage is diffusion-controlled or surface-controlled as follows. For surface-controlled and diffusion-controlled charge storages, the values of
b are 1 and 0.5, respectively.
34 As shown in
Fig. 2E, the calculated values of
b are 0.66 and 0.51 for the electrode measured in KOH and RA electrolytes, respectively. This indicates that the RA provides more diffusion-controlled charge storage, representing more Faradaic redox reactions occurring due to the use of RA electrolyte. The additional redox reactions are ascribed to the Fe(CN)
63−/Fe(CN)
64− oxidation/reduction reactions, which are shown in the CV (
Fig. 2B) and GCD (
Fig. 2C) curves. Thus, the significant improvement in capacitance is obtained.
EIS investigation was done and is presented in Fig. 2F. The intercept between the curve and the x-axis represents the solution/electrolyte resistance (Rs), which is associated with the electrolyte ionic conductivity. Charge transfer resistance (Rct) is depicted by the semicircle at high frequencies. The slope at the high-frequency region represents the electrolyte diffusion resistance (Rd).23 The Nyquist plots exhibit that the Rs of RA electrolyte (1.6 Ω) is slightly lower than the value in KOH electrolyte (1.8 Ω). This indicates the better ionic conductivity in the RA electrolyte, which facilitates the ion movement to diffuse to the pores of the electrode. Furthermore, the Rct value of Co3V2O8 measured using the RA electrolyte is 1.5 Ω, which is lower than that of measured using 3 M KOH (3.2 Ω). The result indicates the faster electron transfer at the electrode/electrolyte interface in RA electrolyte and among the particle in the bulk electrode, which is beneficial for fast redox reactions. For the Rd, it is seen that the RA electrolyte smaller slope, indicating better ions diffusion into the pores of Co3V2O8. These reduced resistances contribute to the improvement of the electrochemical performance. Cycling performances were examined via GCD measurement at a current density of 5 A g−1 for 5000 cycles in the KOH and 0.05 M K3[Fe(CN)6] RA electrolytes, as shown in Fig. 2G. SEM images of the material after the cyclic testis in both electrolytes are presented in Fig. S5.† The Co3V2O8 shows excellent cycle stability in both the KOH and RA electrolytes. However, the use of RA electrolyte shows lower stability than the use of KOH electrolyte. This is attributed to the crystallization of K3[Fe(CN)6] and the aggregation of free ions during the prolonged Fe(CN)63−/Fe(CN)64− redox process.35,36 In addition, the redox additive involves intensive redox reactions at the interface of active electrode material and electrolyte, which promotes the rate of dissolution of active electrode material, leading to the cyclic retention degradation.36
To evaluate the material for practical application, ASC was assembled and tested. The CV curves of the AC negative electrode are displayed in Fig. S6A,† which shows no redox peak. The GCD curves show typical electrical double layer capacitor behavior of carbon (Fig. S6B†). The Csp is 38.8 mA h g−1 (139 F g−1) at 1 A g−1 (Fig. S6C†). Fig. S7A† shows the CV curves of the positive and negative electrodes at 5 mV s−1 in 3 M KOH. Fig. S7B† shows that the optimized cell voltage is 1.6 V. The CV curves of the ASC in KOH electrolyte with a cell voltage of 1.6 V is shown in Fig. S8A.† The CV curves of ASC obtained using the RA electrolyte are presented in Fig. 3A. All CV curves exhibit pseudocapacitive behavior. A higher current response is seen in the CV curves of the ASC having RA electrolyte, demonstrating the superior electrochemical performance. Fig. 3B and S8B† presented the GCD curves of the ASCs in the RA and KOH electrolytes, respectively. The discharge time of the ASC using the RA electrolyte is longer than that of the ASC using the KOH electrolyte, indicating higher capacitance in the former. Fig. 3C shows the Csp derived from the GCD curves of the two ASCs. In comparison, the Csp of the ASC utilizing RA electrolyte is 69.3 mA h g−1 (156 F g−1), more than two times higher than the ASC using KOH electrolyte (27.8 mA h g−1 (63 F g−1)). Fig. 3D show the Nyquist plots of the two ASCs. In comparison to the ASC using the 3 M KOH electrolyte (Rct = 1.52 Ω), the ASC using the RA electrolyte exhibits a reduced Rct of 0.32 Ω. This indicates better charge transfer in the RA electrolyte, contributing to the improvement of the Csp.37 Also, the ASC with the RA electrolyte gives a high Ed of 55.5 W h kg−1 at a high Pd of 800 W kg−1, as shown in Fig. 4A. For comparison, the ASC using the 3 M KOH delivers an Ed of 22.2 W h kg−1 at the same Pd. It is noted that the obtained Ed in this work outperforms most previously reported cobalt vanadate-based materials, such as Co1.5Ni1.5V2O8//AC (51.6 W h kg−1 at 850 W kg−1),38 Co2V2O7//rGO (19 W h kg−1 at 375.8 W kg−1),18 Ni2P–Co3V2O8//AC (40.2 W h kg−1 at 353 W kg−1),39 Co3O4–Co3V2O8//AC (38 W h kg−1 at 275 W kg−1),17 Ni3V2O8/Co3V2O8//AC (28 W h kg−1 at 1400 W kg−1),16 and NiO–Co3V2O8//AC (38.8 W h kg−1 at 379.7 W kg−1).19 The cycle stability of the ASC in 0.05 M K3[Fe(CN)6] RA electrolyte was determined via GCD measurement at a current density of 5 A g−1. As shown in Fig. 4B, the ASC exhibits 82.1% capacitance retention after 10
000 cycles. The reduction of capacitance is due to the occurrence side-reactions and the decreased activity of the redox additive during the long GCD measurement time.35,40,41
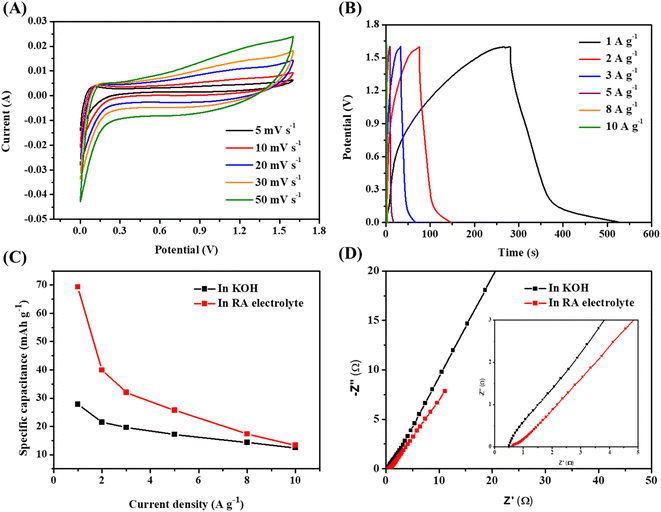 |
| Fig. 3 (A) CV curves at various scan rates, (B) GCD curves at various current densities of Co3V2O8//AC ASC in RA electrolyte. (C) Csp of the two ASC calculated from GCD curves. (D) Nyquist plots of the ASCs obtained using KOH and RA electrolytes. | |
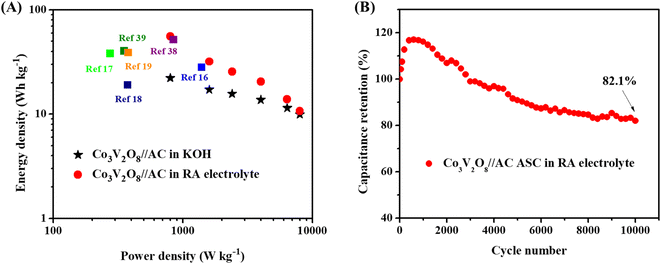 |
| Fig. 4 (A) Ragone plot correlating Ed and Pd and (B) Cyclic stability of Co3V2O8//AC ASC devices using KOH and RA electrolytes. | |
4. Conclusion
We report cobalt vanadate nanowalls grown on nickel foam for use as an electrode of supercapacitors. The nanostructured Co3V2O8 demonstrates a high specific capacitance of 109.9 mA h g−1 (878.9 F g−1) at 1 A g−1 in KOH. The use of K3Fe(CN)6 redox additive further improves the electrochemical performance, giving nearly two-time enhancement of the capacitance (198.9 mA h g−1 (1584.5 F g−1)). ASC consisting of Co3V2O8 positive electrode, AC negative electrode, and redox additive electrolyte delivers a high energy density of 55.5 W h kg−1 at a power density of 800 W kg−1 and good cyclic stability. The excellent electrochemical performance shows that the Co3V2O8 is an excellent electrode material for the next-generation supercapacitor.
Conflicts of interest
The authors declare that there is no competing financial interest that could have appeared to influence the work reported in this paper.
Acknowledgements
The study was supported by the Ministry of Science and Technology, Taiwan through grant no. MOST 110-2221-E-006-115 and the Hierarchical Green-Energy Materials (Hi-GEM) Research Center, from The Featured Areas Research Center Program within the framework of the Higher Education Sprout Project by the Ministry of Education and the Ministry of Science and Technology (MOST 111-2634-F-006-008) in Taiwan.
References
- R. Chen, P. Shi, Y. Gong, C. Yu, L. Hua, L. Li, J. Zhou, T. Xu, Y. Zhang and G. Sun, Energy Technol., 2018, 6, 2326–2332 CrossRef CAS.
- R. Chen, J. Xue, X. Gao, C. Yu, Q. Chen, J. Zhou, G. Sun and W. Huang, Nanoscale, 2020, 12, 22075–22081 RSC.
- H. Xu, X. Zhao, C. Yu, Y. Sun, Z. Hui, R. Zhou, J. Xue, H. Dai, Y. Zhao and L. Wang, Nanoscale, 2020, 12, 11112–11118 RSC.
- G. R. Wang, Z. L. Jin and W. X. Zhang, Dalton Trans., 2019, 48, 14853–14863 RSC.
- S. Sheng, W. Liu, K. Zhu, K. Cheng, K. Ye, G. L. Wang, D. X. Cao and J. Yan, J. Colloid Interface Sci., 2019, 536, 235–244 CrossRef CAS PubMed.
- M. Khalid, P. Bhardwaj and H. Varela, in Science, Technology and Advanced Application of Supercapacitors, IntechOpen, 2018 Search PubMed.
- L. Hua, P. Shi, L. Li, C. Yu, R. Chen, Y. Gong, Z. Du, J. Zhou, H. Zhang and X. Tang, ACS Appl. Mater. Interfaces, 2017, 9, 37022–37030 CrossRef CAS PubMed.
- X. Lv, W. Huang, Q. Shi, L. Tang and J. Tang, J. Power Sources, 2021, 492, 229623 CrossRef CAS.
- J. Acharya, T. H. Ko, M.-K. Seo, M.-S. Khil, H.-Y. Kim and B.-S. Kim, ACS Appl. Energy Mater., 2020, 3, 7383–7396 CrossRef CAS.
- L. Li, R. Chen, Y. Gong, C. Yu, Z. Hui, H. Xu, X. Zhao, Y. Sun, W. Zhao and G. Sun, J. Mater. Chem. A, 2019, 7, 107–111 RSC.
- Y. Gong, J. An, H. Dai, R. Chen, C. Yu, Q. Chen, J. Zhou, G. Sun and W. Huang, Electrochim. Acta, 2020, 356, 136843 CrossRef CAS.
- Y. Teng, Y. Li, D. Yu, Y. n. Meng, Y. Wu, X. Zhao and X. Liu, ChemistrySelect, 2019, 4, 956–962 CrossRef CAS.
- W. H. Low, C. W. Siong, C. H. Chia, S. S. Lim and P. S. Khiew, J. Sci.: Adv. Mater. Devices, 2019, 4, 515–523 Search PubMed.
- Z. Khan, B. Senthilkumar, S. Lim, R. Shanker, Y. Kim and H. Ko, Adv. Mater. Interfaces, 2017, 4, 1700059 CrossRef.
- H. Hosseini and S. Shahrokhian, Chem. Eng. J., 2018, 341, 10–26 CrossRef CAS.
- M.-C. Liu, L.-B. Kong, L. Kang, X. Li, F. C. Walsh, M. Xing, C. Lu, X.-J. Ma and Y.-C. Luo, J. Mater. Chem. A, 2014, 2, 4919–4926 RSC.
- W.-B. Zhang, L.-B. Kong, X.-J. Ma, Y.-C. Luo and L. Kang, J. Power Sources, 2014, 269, 61–68 CrossRef CAS.
- H. Sun, X. Chen, H. Chai, Y. Wang, D. Jia, Y. Cao and A. Liu, Appl. Surf. Sci., 2019, 469, 118–124 CrossRef CAS.
- W.-B. Zhang, L.-B. Kong, X.-J. Ma, Y.-C. Luo and L. Kang, J. Alloys Compd., 2015, 627, 313–319 CrossRef CAS.
- H. Hosseini and S. Shahrokhian, Chem. Eng. J., 2018, 341, 10–26 CrossRef CAS.
- A. Akram, M. A. Liaqat, S. Javed, M. Hamid, U. Ali, F. Javed, M. Wei and M. A. Akram, J. Alloys Compd., 2022, 891, 161961 CrossRef CAS.
- P. Samanta, S. Ghosh, N. C. Murmu and T. Kuila, Composites, Part B, 2021, 215, 108755 CrossRef CAS.
- Y. Zhao, J. Zheng, M. Yuan, Y. Wang, W. Liu, S. Yang, G. Li, J. Lian and Y. Bu, J. Alloys Compd., 2021, 885, 160886 CrossRef CAS.
- G. Dhakal, D. Mohapatra, T. L. Tamang, M. Lee, Y. R. Lee and J.-J. Shim, Energy, 2020, 119436 Search PubMed.
- D. B. Bailmare, P. Tripathi, A. D. Deshmukh and B. K. Gupta, Sci. Rep., 2022, 12, 1–10 CrossRef PubMed.
- Y. Li, L. Kong, M. Liu, W. Zhang and L. Kang, J. Energy Chem., 2017, 26, 494–500 CrossRef.
- T. Zhai, L. Wan, S. Sun, Q. Chen, J. Sun, Q. Xia and H. Xia, Adv. Mater., 2017, 29, 1604167 CrossRef PubMed.
- Y. Chen, J. Huang, X. Zhang and H. Xu, J. Electroanal. Chem., 2021, 884, 115069 CrossRef CAS.
- C. Zhao, W. Zheng, X. Wang, H. Zhang, X. Cui and H. Wang, Sci. Rep., 2013, 3, 2986 CrossRef PubMed.
- L.-H. Su, X.-G. Zhang, C.-H. Mi, B. Gao and Y. Liu, Phys. Chem. Chem. Phys., 2009, 11, 2195–2202 RSC.
- M. Amiri, S. S. H. Davarani, S. K. Kaverlavani, S. E. Moosavifard and M. Shamsipur, Appl. Surf. Sci., 2020, 527, 146855 CrossRef CAS.
- J. Pokharel, A. Gurung, A. Baniya, W. He, K. Chen, R. Pathak, B. S. Lamsal, N. Ghimire and Y. Zhou, Electrochim. Acta, 2021, 394, 139058 CrossRef CAS.
- R. Mohanty, G. Swain, K. Parida and K. Parida, J. Alloys Compd., 2022, 165753 CrossRef CAS.
- V. T. Nguyen and J.-M. Ting, ACS Sustainable Chem. Eng., 2020, 8, 18023–18033 CrossRef CAS.
- P. Samanta, S. Ghosh, N. C. Murmu and T. Kuila, Composites, Part B, 2021, 215, 108755 CrossRef CAS.
- N. R. Chodankar, D. P. Dubal, A. C. Lokhande, A. M. Patil, J. H. Kim and C. D. Lokhande, Sci. Rep., 2016, 6, 1–14 CrossRef PubMed.
- J. Fu, L. Li, D. Lee, J. M. Yun, B. K. Ryu and K. H. Kim, Appl. Surf. Sci., 2020, 504, 144250 CrossRef CAS.
- B. Huang, W. Wang, T. Pu, J. Li, C. Zhao, L. Xie and L. Chen, Chem. Eng. J., 2019, 375, 121969 CrossRef CAS.
- Y.-M. Hu, M.-C. Liu, Y.-X. Hu, Q.-Q. Yang, L.-B. Kong, W. Han, J.-J. Li and L. Kang, Electrochim. Acta, 2016, 190, 1041–1049 CrossRef CAS.
- M. He, K. Fic, E. Fra, P. Novák and E. J. Berg, Energy Environ. Sci., 2016, 9, 623–633 RSC.
- X. Liu, Z. Lu, H. Pan, J. Cheng, J. Dou, X. Huang and X. Chen, Electrochim. Acta, 2022, 429, 141056 CrossRef CAS.
|
This journal is © The Royal Society of Chemistry 2022 |
Click here to see how this site uses Cookies. View our privacy policy here.