DOI:
10.1039/D2RA03066G
(Review Article)
RSC Adv., 2022,
12, 17959-17983
Strategies to improve electrocatalytic performance of MoS2-based catalysts for hydrogen evolution reactions
Received
16th May 2022
, Accepted 13th June 2022
First published on 17th June 2022
Abstract
Electrocatalytic hydrogen evolution reactions (HERs) are a key process for hydrogen production for clean energy applications. HERs have unique advantages in terms of energy efficiency and product separation compared to other methods. Molybdenum disulfide (MoS2) has attracted extensive attention as a potential HER catalyst because of its high electrocatalytic activity. However, the HER performance of MoS2 needs to be improved to make it competitive with conventional Pt-based catalysts. Herein, we summarize three typical strategies for promoting the HER performance, i.e., defect engineering, heterostructure formation, and heteroatom doping. We also summarize the computational density functional theory (DFT) methods used to obtain insight that can guide the construction of MoS2-based materials. Additionally, the challenges and prospects of MoS2-based catalysts for the HER have also been discussed.
1. Introduction
With the rapid growth of the economy, the traditional, polluting sources of energy are being consumed heavily, resulting in environmental degradation;1–3 thus, developing sustainable and clean energy has become urgent. Among all the alternative energies, hydrogen has significant advantages due to its high energy density and environmental friendliness.4 Currently, mass H2 production mainly comes from steam reforming of hydrocarbons, which is highly energy-consuming and relies on the polluting petroleum industry.5–7 To promote the adoption of the H2 economy, in the past several decades, new H2 production technologies, like photocatalytic and electrocatalytic water splitting, have been developed.8–12 Compared with photocatalytic water splitting, the electrochemical approach has more advantages in terms of energy efficiency and achieving effective product separation. Electrochemical water splitting consists of two half-reactions, which are named as the hydrogen evolution reaction (HER) and oxygen evolution reaction (OER).13 The OER is hard to occur, because it involves four-electron transfer.14 The reaction mechanism is as follows:
Total reaction:
|
 | (1) |
In acidic solution:
|
Cathode: 2H+(aq) + 2e− → H2(g)
| (2) |
|
 | (3) |
In neutral and alkaline solution:
|
Cathode: 2H2O(l) + 2e− → H2(g) + 2OH−(aq)
| (4) |
|
 | (5) |
Generally, the HER consists of the three following steps:
|
Volmer step: H+ + e− → H*
| (6) |
|
Heyrovsky step: H* + H+ + e− → H2
| (7) |
|
Tafel step: 2H* → H2 + 2*
| (8) |
In acidic electrolytes, the HER occurs when protons are adsorbed at the surface of the MoS2 and consequently, step (6) takes place, which is then followed by step (7) or (8). The overall reaction rate relies on the Gibbs free energy of H2 adsorption (ΔGH*). In theory, the closer this value is to zero, the greater is the HER activity. The reactions (7) or (8) are inhibited when the binding of H to the catalyst surface is weak. Therefore, catalysts with excellent HER performance tend to exhibit good adsorption of H atoms, which is conducive to charge transfer and bond breakage, resulting in the formation of H2.9,15–18
Under standard conditions, initiating HER requires a dynamic overpotential, which essentially involves additional energy consumption; thus, electrocatalysts are integral to abate the overpotential. As of today, Pt-based materials are the most widely used electrocatalysts; however, Pt is scarce and costly, making it essential to develop cost-effective electrocatalysts. Currently, a wide range of materials, including transition metal alloys,19–27 transition metal carbides,28–36 transition metal dichalcogenides,37–45 transition metal phosphides,46–50 and so on, are being studied as possible alternative HER electrocatalysts. Among them, MoS2 has attracted wide attention due to its unique two-dimensional layered structure and adjustable band gap width, which makes MoS2 has a property of ease incorporation into the lattice (heteroatoms and vacancies) and adjustability of electron transport. However, experimental and theoretical studies reveal that the HER activity of MoS2 remains unsatisfactory due to three main issues. First, the HER activity of MoS2 correlates with the active edge sites rather than basal planes, but the edge sites just account for a small part of the surface area of MoS2. Second, the semiconducting basal plane of MoS2 has a low intrinsic electronic conductivity, which leads to poor charge transfer. Third, the aggregation and restacking of MoS2 hinders the availability of edge sites. Herein, we discuss three important approaches that have been demonstrated to improve the intrinsic catalytic activity and HER performance of MoS2 effectively, i.e., defect engineering, formation of the heterostructure, and heteroatom doping (Fig. 1).
 |
| Fig. 1 Structural polytypes of MoS2:1T, 2H, and 3R. Reproduced with permission from ref. 51. Copyright 2020, Elsevier. | |
2. Properties of MoS2
MoS2 is a typical layered transition metal dichalcogenides composed of stacking S–Mo–S layers by van der Waals interactions, leading to a sandwich-like layered structure.51,52 The basal plane of MoS2 is generally believed to be inert toward HER, while the edge sites of MoS2 layers possess much higher chemical reactivity than the basal plane.13 Based on the arrangement of the S atoms, three phases of MoS2 can be obtained, i.e., 1T, 2H and 3R.53 The 2H phase MoS2 is thermodynamically stable, but the conductivity of 2H phase MoS2 is poor.54,55 Compared to 2H MoS2, 1T MoS2 is metallic and is 107 times more conductive than 2H MoS2.56 Nevertheless, 1T MoS2 is thermodynamically unstable and does not exist in nature57 (Fig. 2). Under some specific conditions,1T MoS2 can also exist and phase transformation is one of the most effective methods to improve the catalytic performance of MoS2.58,59 Zhao et al.60 investigated the HER dynamics in the MoS2 basal plane of the 1T and 2H phases. They calculated the absorbed H free energies on the 2H/1T structural interfaces and their work offered a new way to increase the number of MoS2 active sites on the basal plane. DFT calculations demonstrated that MoS2 had a similar H binding energy as that of Pt.61 In theory, MoS2 should exhibit outstanding HER performance; however, bulk MoS2 displays poor performance due to the following reasons. (i) The active sites of bulk MoS2 cannot be fully exposed.62 (ii) The superimposition of the van der Waals force in the interior of the bulk MoS2 leads to an incongruous effect of the active sites.63 (iii) The covalently bonded atoms in the layers lead to poor HER performance.64 (iv) The electronic conductivity of bulk MoS2 is low.65 Thus, many efforts have been devoted to designing a reasonable MoS2 nanostructure and modulating the MoS2 electronic structure.66–68 Furthermore, many engineering methods such as phase transformation engineering, vacancy engineering, and stretching have been developed to overcome the disadvantages of bulk MoS2.69–73 Cao et al.74 demonstrated that S vacancies could provide another type of active site for the HER besides the Mo and S active edge sites. They also found that the HER activity of grain boundaries was much lower than that of the S vacancy and S edge sites. Based on the structure determining properties, many efforts have been devoted to constructing specific MoS2 nanostructures, including nanoparticles, nanoflakes, nanowires, nanoflowers and nanosheets.75–79 These nanostructures can maximally expose active edge sites of MoS2 and shorten the electron transfer distance.80
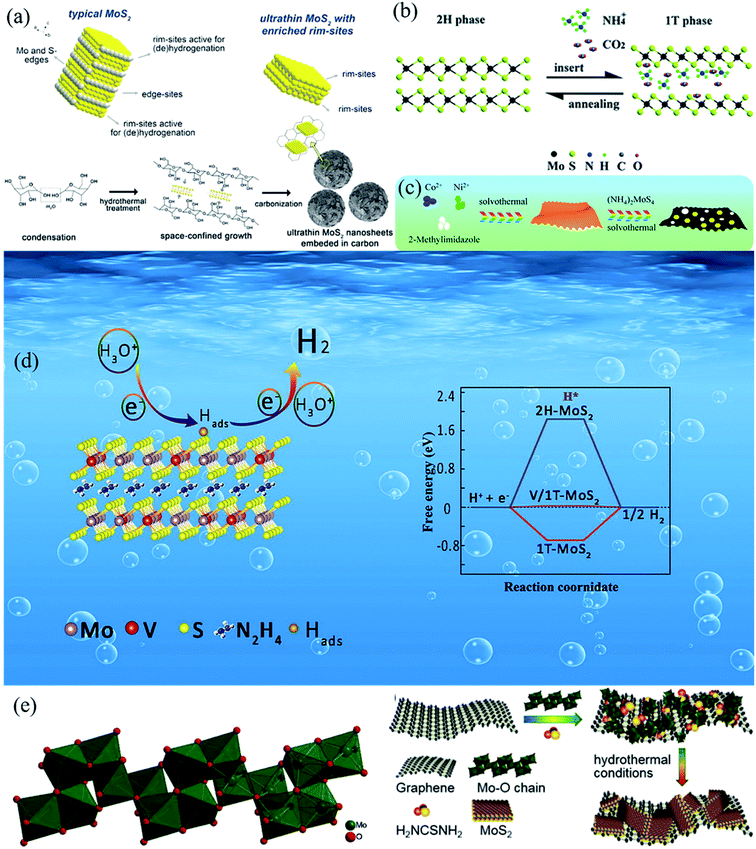 |
| Fig. 2 (a) Schematic illustration for synthesis of MoS2/C. Reproduced with permission from ref. 116, Copyright 2014 Elsevier. (b) Schematic illustration of 1T/2H MoS2 phase transition. Reproduced with permission from ref. 117, Copyright 2017 Royal Society of Chemistry. (c) Schematic of the synthesis process for MoS2/NiCoS heterostructures. Reproduced with permission from ref. 118, Copyright 2019 Royal Society of Chemistry. (d) Schematic illustration of HER process and DFT calculation results. Reproduced with permission from ref. 119, Copyright 2021 Elsevier. (e) Molybdenum oxide chain in (H2en)Mo3O10 and the proposed formation mechanism of 1T/2H-MoS2/RGO. Reproduced with permission from ref. 120, Copyright 2021 Elsevier. | |
3. Synthetic methods for MoS2
In order to synthesize MoS2, many strategies have been developed, including mechanical exfoliation,81–83 solution exfoliation,84–86 chemical vapor deposition87–89 (CVD), hydrothermal synthesis,90–92 electrodeposition methods,93–95 metal–organic chemical vapor deposition (MOCVD),96–98 and molecular beam epitaxy (MBE).99–101 These methods can be classified as top-down methods (including mechanical exfoliation and solution exfoliation) and bottom-up methods (including hydrothermal synthesis, CVD, MOCVD and MBE). In the top-down methods, the morphology of MoS2 can be well controlled since the structure of the final product is inherited from the original materials.102 However, top-down methods have intrinsic shortcomings; for instance, the nanoscale morphology of the final product is hard to adjust since it is difficult to change the distance between ions and atoms in top-down methods.103 In bottom-up methods, a large and complicated system are formed by atoms, molecules and nanoparticles through self-assembly or weak interactions, and the usage of materials is more efficient.104 The specific surface area and thickness of MoS2 can be better controlled than in top-down methods. For example, in hydrothermal method, the thickness and size of MoS2 can be modulated by simply tuning the hydrothermal time, temperature and growth parameters of solution concentration.105 The main disadvantage of bottom-up methods is the difficulty of large-scale synthesis.106,107 In the rest of this section, we try to list out the general methods of synthesizing MoS2 for the electrochemical HER (Table 1).
Table 1 Comparison of synthetic methods of MoS2-based catalysts
Synthetic method |
Advantages |
Disadvantages |
Reference |
Hydrothermal synthesis |
Easy to operate, high purity, good dispersibility, complete crystal form, uniform particle size |
Easy to agglomerate, unclear reaction mechanisms, unsuitable for water sensitive materials, poor repeatability |
90–92 |
Chemical vapor deposition |
Simple film-forming device, easy to control the product composition, good repeatability, good uniformity |
May produce corrosive, toxic or explosive reaction gas, low film forming rate, easy to introduce impurities |
87–89 |
Mechanical exfoliation |
Few defects, smooth surface, high mobility |
Difficult to control the thickness, random position on substrate, small output |
81–83 |
Solution exfoliation |
Low cost, high controllability, easy to realize large-scale preparation |
Small product size, low yield |
84–86 |
Electrodeposition methods |
Adjustable grain size, easy to operate, low cost, high efficiency |
Difficult to control growth rate, low crystallinity of product |
93–95 |
Metal–organic chemical vapor deposition |
Low reaction temperature, wide application range, suitable for mass production |
May produce toxic and flammable vapor, difficult to in situ monitor the growth process |
96–98 |
Molecular beam epitaxy |
Atomic-level controlled film thickness, composition and dopants |
High requirements for equipment conditions |
99–101 |
3.1. Hydrothermal synthesis
Hydrothermal method is to seal the reactants in the reactor, and the reaction process is completed through chemical transmission. Liquid or gaseous water is the pressure transmission medium under high temperature and high pressure, and most of the reactants can be dissolved in water, so that the reaction can be carried out in the critical state of gas phase and liquid phase solvent. Compared with other powder preparation methods, the powder prepared by hydrothermal methods has the advantages of complete grain development, small particle size, uniform distribution, light particle agglomeration, cheaper raw materials, and appropriate stoichiometry and crystal shape are easily obtained.108–111 Typically, the ceramic powder prepared by hydrothermal methods does not need high-temperature calcination treatment, which prevents grain growth, defect formation and introduction of impurities in the calcination process, so the prepared powder has high sintering activity.112–115
Liu et al.116 prepared ultrathin MoS2 nanosheets grown on an in situ-formed polysaccharide matrix derived from glucose condensation via a hydrothermal method. 0.80 g of glucose with a varied amount of ammonium heptamolybdate tetrahydrate ((NH4)6Mo7O24·4H2O) and thiourea (CS(NH2)2) was dissolved in 15.0 mL of distilled water, and then the solution was turned to a Teflon-lined stainless-steel autoclave, with a hydrothermal treatment at 240 °C for 48 h. After centrifugation, washing and annealing, the MoS2/C nanospheres was successfully synthesized. Wang et al.117 prepared 1T/2H MoS2 via a facile hydrothermal method with the addition of ammonium bicarbonate. During the hydrothermal process, ammonium bicarbonate was decomposed into small molecules and ions as guests, including NH4+, H2O and CO2, which were inserted into the lamellar structures of MoS2, inducing the formation of multiphasic 1T/2H MoS2. Zhang et al.118 used the hydrothermal method to construct MoS2/NiCoS nanosheets with ultrathin NiCo bi-metal–organic framework (NiCo-MOF) nanosheets and (NH4)2MoS4 as precursors. The hydrothermal process was controlled at 200 °C for 24 h. In this reaction, (NH4)2MoS4 not only acts as a precursor for the synthesis of MoS2, but also provides a source of sulfur for in situ conversion of NiCo-MOF nanosheets to NiCoS. Li et al.119 prepared V-doped 1T MoS2 nanosheets as a highly efficient HER electrocatalyst in both acidic and alkaline solutions through a hydrothermal method. Typically, 0.2 g sulfur was put into 4 beakers with different molar quantity of ammonium heptamolybdate ((NH4)6Mo7O24·4H2O). Then, 4 mL of hydrazine monohydrate (N2H4·H2O) was dissolved in each beaker. Then, 36 mL of DI water was added into the beakers to make the mixture 80% of autoclave volume, and different molar quantity of ammonium metavanadate (NH4VO3) were added into the beakers as the V source. Then the precursors were transferred to 50 mL stainless steel autoclaves. The whole set was sealed and put into the oven at 200 °C for 48 h. Xiao et al.120 synthesized 1T/2H MoS2@graphene via a hydrothermal method. The introduction of metallic 1T-MoS2 endues the as-prepared materials with remarkably electrocatalytic activity and favorable kinetics, highly efficient and stable HER performance.
3.2. Chemical vapor deposition
Chemical vapor deposition (CVD) is a method of synthesizing coatings and nanomaterials deposited on a substrate surface by chemical gas or vapor reaction. It is the most widely used technology for depositing a variety of materials in the semiconductor industry, including a wide range of insulating materials, most metal materials and metal alloy materials.121–123 Theoretically, the CVD process is very simple: two or more gaseous raw materials are introduced into a reaction chamber, which then react with each other to form a new material that is deposited on the wafer surface. However, experimentally, the reaction that takes place in the reaction chamber is very complex, and there are many factors that must be considered. The deposition parameters, which can vary over a wide range, include the pressure in the reaction chamber, the temperature of the wafer, the flow rate of the gas, the distance of the gas through the wafer, the chemical composition of the gas, the ratio of one gas to another, the role of the intermediate product of the reaction, and whether other reactions are needed.124–128
Pumera et al.129 synthesized MoS2 films via powderless gas deposition. The CVD fabrication method they used is suitable for industry because this powderless and one-step process eliminates the deviations of MoS2 growth which are likely to arise from the usage of a powder precursor. Yu et al.130 hybridized MoS2 micro-flowers on VS2 by a one-pot CVD method and their catalyst exhibited excellent HER performance. Atomic layer deposition (ALD) is a method in which substances can be deposited on the surface of the substrate, layer by layer, in the form of a monoatomic film.131 ALD has similarities with ordinary chemical deposition, except that the chemical reaction of the new layer of atomic film is directly dependent on the previous layer. In this way, only one layer of atoms is deposited per reaction. Due to its highly controllable deposition parameters (thickness, composition, and structure), atomic layer deposition technology, excellent deposition uniformity and consistency, it has wide application potential in the field of micro-nanoelectronics and nanomaterials. Tan et al.132 successfully synthesized layered MoS2 via the ALD method. Typically, MoS2 films were prepared by alternating exposure to molybdenum chloride (MoCl5) and hydrogen disulfide (H2S) vapors. Due to the self-limiting reactions of the vapors, the number of MoS2 film layers can be precisely controlled by the number of deposition cycles.
3.3. Exfoliation method
At present, the most effective preparation methods of single- or few-layer MoS2 are exfoliation methods, which can be divided into mechanical exfoliation, lithium-ion intercalation exfoliation and liquid phase ultrasonic exfoliation. In the mechanical exfoliation method, MoS2 powder is directly stripped to form a thin layer of MoS2 nanoflakes with a special gummed tape. This is the most original and traditional preparation method. The thickness of MoS2 that was first peeled off in 1965 ranged from a few layers to dozens of layers.133 After the improvement of this stripping process, monolayer MoS2 was successfully obtained.134 The most obvious advantage of the mechanical exfoliation method is that the process is simple, can be obtained manually, and the stripping efficiency is high. Since this is direct exfoliation, the monolayer MoS2 can maintain a good single crystal structure and offer high carrier mobility. However, this method has obvious disadvantages, such as low yield and poor repeatability. The lithium-ion intercalation-based exfoliation method can be used, for instance the LixMoS2 (x ≥ 1) intercalation compound is obtained by the reaction of the lithium-ion intercalation agent (such as n-butyl lithium) and MoS2 powder (intercalation process). Then the intercalation compound reacts violently in water and other protonic solvents, and the stripping process occurs. Thus, multilayer and monolayer MoS2 can be obtained by ultrasonic extraction. In 1986, Morrison et al.135 prepared monolayer MoS2 by this method. The efficiency of the Li ion intercalation stripping was found to be very high, with a yield close to 100%. The quality of the prepared nanosheets was very good, making it suitable for mass-production, and the method could be used to peel many other inorganic layered compounds. However, this preparation method is complex, the intercalation agent is sensitive to the environment, leading to a high production cost, and long preparation time. Moreover, it is difficult to control the degree of intercalation, which makes the post-treatment difficult. For this reason, Zeng et al.136 used an electrochemical lithium battery device to control the lithium ion insertion and stripping process, so as to prepare a variety of monolayer materials such as MoS2. This electrochemical lithium-ion intercalation exfoliation method can effectively avoid many of the abovementioned problems and obtain high yield monolayer MoS2. The basic principle of the liquid-phase ultrasonic exfoliation method is to put MoS2 and other layered materials into a suitable solvent, use the ultrasonic wave to vibrate and peel off the lower layer of materials from the block, and then centrifuge to obtain thin MoS2 nanosheets. In 2011, Coleman et al.137 prepared monolayer and multilayer nanosheets such as MoS2, BN and WS2. The solvent selected by the liquid phase ultrasonic exfoliation method is generally a polar solvent with good dispersity and solubility for layered materials and similar surface energy. Coleman et al.138 prepared thin MoS2 material by adding a sodium cholate surfactant and stripping it in an aqueous phase. However, Zhou et al.139 used ethanol/water mixed low-boiling solvents to successfully peel off nanosheets such as MoS2, making the peeling method cheaper and environmentally friendly, and peeling MoS2 under water phase conditions has become a new choice for people. The liquid-phase ultrasonic peeling method is simple and fast, and can be suitable for large-scale production, but generally the peeling degree is not high, the concentration of the obtained nanosheet solution is small, and the dependence on the ultrasonic conditions is high, and the ultrasonic power is too large or too small, which is not conducive to the formation of nanosheets.
3.4. Electrodeposition method
Electrodeposition method is an attractive way to synthesize MoS2 thin film in large scale because it uses cheap equipment, enables the deposition in large area and easy control of growth parameters through applied potential, current, pH and temperature of the bath.140 Many researchers have studied the mechanism of an electrochemical deposition of MoS2 from aqueous and little from non-aqueous solutions. A variety of electrodeposition techniques have been reported for the preparation of MoS2 films using anodic oxidation or cathodic reduction.
Ping et al.141 developed an edge-guided electrodeposition approach for the construction of high quality edge contacted metal-2D MoS2 and further demonstrated the potential of this approach in the fabrication of high performance electrocatalyst. Hwang et al.142 developed a novel MoS2 electrode with a nanocarbon (NC) coating as a catalytic cathode for hydrogen production in a microbial electrolysis cells (MEC), while treating simulated urine. The MEC performance of HER using the MoS2-NC cathode was characterized and evaluated under different applied voltages and various dilution factors for adjusting conductivity. Lyndi et al.143 prepared MoS2 films via an electrodeposition method. Electrodeposition of molybdenum disulfide films was carried out with a 10 mM (NH4)2MoS4 (ammonium tetrathiomolybdate) with 0.1 M LiClO4 adjusted to pH 10 with NH4OH using chronoamperometric deposition. Jiang et al.144 prepared the MoS2–Co3S4/NF heterostructure layer by Co-MOF vulcanization and cyclic voltammetry (CV) method, which showed better electrochemical performance than the single-layer Co3S4/NF. The as-prepared MoS2–Co3S4 heterostructure layer was decorated by ZnCo-LDH, the hydrogen evolution performance was further improved.
Though the above synthetic methods have been demonstrated to be an effective way to synthesize bulk MoS2, the HER performance of bulk MoS2 is still not satisfactory. In the following part, we summarize three main strategies to promote the HER performance of MoS2 (Fig. 3).
 |
| Fig. 3 (a) Schematic diagram of preparing MoS2/VS2 hybrid by a one-pot CVD process. The SEM images of MoS2/VS2 hybrid observed at different magnifications. (b) Low magnification; (c) middle magnification; and (d) high magnification. The morphological evolutions of MoS2/VS2 hybrid intercepted at different temperatures; (e) formation of pristine interfaced flake-like VS2 crystals at 300 °C, with an inset shows the high-magnification of VS2 crystals; (f) initial nucleation of flower-like MoS2 on the existing VS2 crystals at 730 °C; and (g) further growth of flower-like MoS2 on underlying flake-like VS2 crystals at 750 °C. (h) The EDX mapping of MoS2/VS2 hybrid, in which the elemental distributions of vanadium, molybdenum, and sulfur are illustrated in red, green, and yellow, respectively. Reproduced with permission from ref. 130, Copyright 2021 Elsevier. (i) Schematic illustration for a one-step powderless deposition growth process of 2H-MoS2. Reproduced with permission from ref. 129, Copyright 2021 Elsevier. | |
4. Main strategies to promote the HER performance of MoS2
4.1. Defect engineering
Many physical and chemical properties of materials are closely related to the existence of defects.145–147 Generally, defects can be classified as vacancies, grain boundaries and disorders.148–150 Furthermore, vacancies can consist of, for instance, Mo vacancies, S vacancies, O vacancies, N vacancies and C vacancies.151–155 Thermodynamically, it's unavoidable to introduce vacancies in the process of synthesizing MoS2.156 Many studies have examined the impact of vacancies on the HER performance of MoS2.157–167 Theoretically, the rational design of defects on the basal plane of MoS2 can enhance the HER performance of MoS2 because the basal plane of MoS2 is inert while the edge sites are significantly more active.
Li et al.168 designed vertically aligned MoS2 with a selectively cleaved Mo–S bond. Their work showed a new way to synthesize MoS2 with a vacancy and their synthesis route is shown in Fig. 4(a). Fig. 4(b) shows that the scanning electron microscopy (SEM) and transmission electron microscopy (TEM) images confirm the existence of micro-cubic c-MoS2–C morphology. Aberration-corrected high-angle annular dark-field scanning transmission electron microscopy (AC HAADF-STEM) images show the existence of the vacancy. This unique defect is beneficial to a thermoneutral H-adsorption energy, which leads to accelerate HER kinetics. The energy-dispersive X-ray spectroscopy (EDS) elemental mapping results further confirm the formation of MoS2 nanosheets with Mo and S defects. The electrocatalytic performance of the defect-rich MoS2 is shown in Fig. 5. Further DFT calculations reveal that the newly generated interior edge sites break the periodic electronic structure of the MoS2 basal plane, leading to an optimized surface charge configuration for H adsorption and desorption.
 |
| Fig. 4 (a) Schematic representation of the formation of c-MoS2−C; (b) SEM images of HZIF-Zn/Mo and c-MoS2−C. TEM image, HRTEM images, FFT-generated image of c-MoS2−C. Atomic-resolution HAADF-STEM images of c-MoS2−C with multiple MoxSy vacancies. EDS elemental mapping for c-MoS2−C. Reproduced with permission from ref. 168, Copyright 2021 American Chemical Society. | |
 |
| Fig. 5 The HER performance of c-MoS2−C and the reference samples. Reproduced with permission from ref. 168, Copyright 2021 American Chemical Society. | |
Li et al.74 conducted a study of the catalytic activities of all potential reaction sites, such as edge sites, S vacancies and grain boundaries. For the first time, they demonstrated that S vacancies provide another active site for HER in addition to the well-known active edge sites (Fig. 6(a)). In order to identify the influence of S vacancy states and concentration on catalysis, Wang et al.169 synthesized MoS2 with homo-vacancies, with an H2O2 chemical etching strategy (Fig. 6(b)). They performed DFT calculations of ΔGH* to explore the effect of S vacancy concentration and distribution on the HER performance. The results showed that 12.50% of the single S-vacancies yielded the optimal HER performance. They synthesized a vertically aligned MoS2 nanosheet guided by these theoretical DFT calculations. The X-ray diffraction (XRD) results in Fig. 7(a) demonstrate that the sample phase was firm and did not change after H2O2 etching. To determine the S-vacancy concentration as a function of the etching process, three X-ray photoelectron spectroscopy (XPS) spectra of P-MoS2 and MoS2−x are shown in Fig. 7(a). The S
:
Mo ratio in each spectrum was calculated and it was converted to the corresponding S-vacancy concentration. The electrochemical results are shown in Fig. 7(b) indicate that MoS2 with 12.11% S-vacancy exhibited the best HER performance and the ratio of S-vacancy was very close to the theoretically predicted optimal value of 12.50%. Furthermore, the superiority of single S-vacancies over agglomerate S-vacancies was found to originate from more effective engineering of the surface electronic structure. The synergistic modulation of catalytic performance from both vacancy concentration and distribution broadens the vacancy design field and can be further extended to other types of TMDs and for other catalytic reactions.
 |
| Fig. 6 (a) Schematic illustration for HER activity of MoS2 with an S vacancy. Reproduced with permission from ref. 74, Copyright 2016 American Chemical Society. (b) Schematic of the chemical etching process to introduce single S-vacancies. | |
 |
| Fig. 7 (a) XRD patterns with magnified regions and Raman spectra with magnified regions of P-MoS2 and MoS2−x. High-resolution Mo 3d XPS spectrum, high-resolution S 2p XPS spectrum, and S L-edge XANES spectra of P-MoS2 and MoS2-60s. (b) Electrochemical HER performance of P-MoS2 and MoS2−x. Reproduced with permission from ref. 169, Copyright 2020 American Chemical Society. | |
Forming pits on MoS2 monolayers has been found to be desirable for promoting HER performance. Park et al.170 investigated the effect of adventitious C on the pit formation in the MoS2 layers. They used an aperture type in situ ETEM to study the reaction between MoS2 monolayers and O2. The HER activity of MoS2 was enhanced in the presence of pits, which can be ascribed to the increase of active edge sites (Fig. 8(b)). They also conducted DFT calculations and found that the presence of C nanoparticles on monolayer MoS2 was favorable for progressive oxidation (Fig. 8(a)).
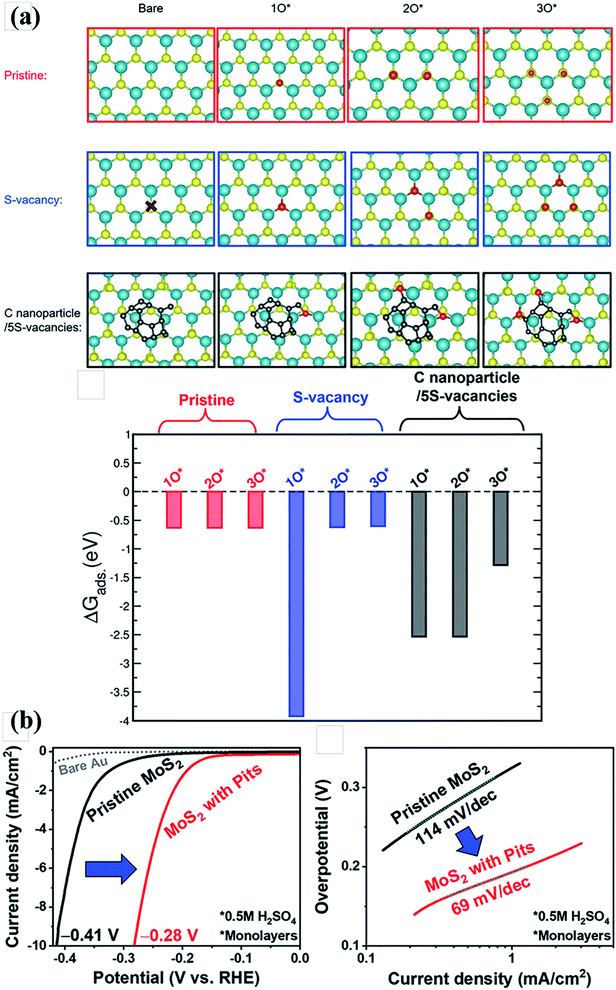 |
| Fig. 8 (a) DFT calculation of adsorption energies of three sequential O atoms, for three different model structures. (b) Comparisons of HER activity between the pristine monolayer MoS2 and monolayer MoS2 with pits. Reproduced from ref. 170, Copyright 2020 John Wiley and Sons. | |
Although the existence of defects can significantly improve the HER performance of MoS2, the key is the ability to detect the existence of defects. Thus, we need to study the relationship between defect types and electronic modes. Up till now, the existence of defects was observed indirectly because the concentration of defects is typically very low. One of the detecting methods is Raman spectroscopy, which can effectively detect edge defects and show distinct electronic structure. The vital task of defect engineering is to enhance the electrochemical activity of the MoS2 basal plane.
4.2. Formation of heterostructure
The construction of heterostructured composites is an effective way to enhance the activity of MoS2.171–181 Wei et al.182 synthesized core–shell structured CoS2@MoS2 by a hydrothermal method. As shown in Fig. 9(a), the CoS2@MoS2 nanoparticles had a uniform size distribution, ranging from 20–30 nm. The HER performance of CoS2@MoS2 in Fig. 9(b) shows that the overpotential of HER was only 276 mV and the Tafel slope was 60 mV dec−1. Mei et al.183 constructed a PCN@MoS2@C sandwich-like heterostructure by a facile hydrothermal method. The PCN@MoS2@C exhibited excellent HER performance within a wide pH range (Fig. 9(c)).
 |
| Fig. 9 (a) SEM images of bulk MoS2 and CoS2@MoS2 nanoparticles. (b) HER performance of CoS2@MoS2. Reproduced with permission from ref. 182, Copyright 2020 Elsevier B.V. (c) The HER performance of PCN, PCN@MoS2, PCN@MoS2@C and Pt/C. Reproduced with permission from ref. 183, Copyright 2020 the Royal Society of Chemistry. | |
Constructing heterostructures with multiple electrocatalytically active components simultaneously to improve HER performance is regarded as an effective strategy. He et al.184 synthesized CoS2/SnO2@MoS2 (denoted as CSM) nanotubes by a fast template-engaged hydrothermal treatment. The SEM and TEM images of the obtained CSM are shown in Fig. 10(a) and (b). These images revealed a porous structure, which enlarged the surface area of the material and boosted the mass transport process, leading to excellent HER performance (Fig. 10(c)). Huang et al.185 designed an exfoliated few-layer FePS3 decorated with vertical MoS2 nanosheets through a facile hydrothermal reaction. The synergistic effect between the FePS3 and MoS2 led to excellent HER performance. This effect can regulate the electronic structure and improve the electron conductivity. As shown in Fig. 10(d). The overpotentials of FeS3@MoS2 were 175 mV and 168 mV in alkaline and acidic media, respectively. Furthermore, the heterostructure could prevent agglomeration during electrocatalytic cycling, which led to high stability.
 |
| Fig. 10 (a) FESEM images of CSM1 nanocubes, CSM2 nanocubes and CSM3 nanocubes (b) TEM image, HRTEM image, the corresponding SAED pattern and TEM-EDX elemental mapping images of CSM1 nanocubes, respectively. (c) HER performance of CSMy (y = 0.5, 1, 2, 3), MoS2 and Pt/C. Reproduced with permission from ref. 184, Copyright 2020 the Partner Organisations. (d) HER performance of FePS3, MoS2 MoS2@FePS3 and 20 wt% Pt/C. Reproduced with permission from ref. 185, Copyright 2020 Elsevier B.V. | |
Tahira et al.186 reported a stable electrocatalyst composed of TiO2 nanorods decorated with MoS2 nanosheets by a two-step hydrothermal method. This electrocatalyst showed an enhanced HER performance compared with bulk MoS2 (Fig. 11(a)). Cao et al.187 prepared cobalt molybdenum nitride with a nanoscale morphology using a two-step solid-state reaction. This compound did not belong to any layered structural family prepared for HER; however, it exhibited HER activity comparable to MoS2 (Fig. 11(b)).
 |
| Fig. 11 (a) HER performance of TiO2/MoS2, TiO2, MoS2, Pt/C. Reproduced with permission from ref. 188, Copyright 2019 American Chemical Society. (b) HER performance of Co0.6Mo1.4N2. Reproduced with permission from ref. 187, Copyright 2013 American Chemical Society. | |
Theoretically, heterostructure engineering of MoS2 with graphene is an effective and facile method and the enhanced catalytic performance can be attributed to two factors. First, the induced graphene substrate prevents the agglomeration of MoS2 nanosheets; thus, creating sufficient edge sites for HER. Second, the excellent electronic conductivity of graphene encourages rapid electron transfer, which is beneficial for the absorption of the H atom and reduces the Gibbs free energy. Furthermore, the heterojunction of the MoS2@graphene hybrid provides new chemical properties and may be beneficial for an enhanced HER performance. Wang et al.189 constructed a MoS2@rGO hybrid catalyst by growing MoS2 arrays on the rGO surface via a one-step hydrothermal method. The MoS2@rGO presented a three-dimensional flower-like morphology, with plentiful active edge sites exposed, which contributed to good HER performance. Yan et al.190 reported a bottom-up method for the large-scale synthesis of 3D hybrid architectures constructed from graphene, MoS2 and graphitic carbon nitride nanosheets by self-assembly. Due to the distinct architectural features such as 3D interconnected porous networks and low charge-transfer resistance, the MoS2-CN/G exhibited superior HER performance with low overpotential, small Tafel slope and long-term durability. Wu et al.191 designed MoS2/MoN heterostructures with tuned components and the catalyst showed excellent HER performance in acid and alkaline electrocatalyst. DFT calculations suggested that the MoS2/MoN interface could optimize the H atom adsorption kinetic energy, accelerating the HER process. Liu et al.192 reported a hierarchical ZnS@C@MoS2 core–shell nanostructure in a bottom-up strategy combined with a selective etching method. The co-existence of ZnS and porous carbon shell not only improved the electrical conductivity but also separated and loaded the MoS2 nanosheets, which effectively exposed active edge sites. This catalyst showed an excellent HER performance with an overpotential of 118 mV and a Tafel slope of 55.4 mV dec−1. Li et al.193 reported a 1T-MoS2/CoS2 heterostructure via a self-sacrificing template method. In this work, they compared the cohesive energy of in-plane heterostructure and out-plane heterostructure by DFT calculation and revealed that the cohesive energy of in-plane heterostructure (−5.1 eV) is much lower than that of out-plane (−4.5 eV), which demonstrated that the in-plane heterostructure is thermodynamically more stable.
4.3. Heteroatom-doping method
4.3.1. Metal-doping method. Metal doping is an effective method to promote the HER activity of MoS2. Transition metals (Fe, Co, Ni, etc.) can significantly enhance the conductivity of MoS2, and modulate the electronic structure of MoS2. Co doping can enhance the conductivity of MoS2, which can decrease the H atom adsorption energy of MoS2 for HER, and also add new active catalytic sites for HER.Xiong et al.194 reported Co-doped MoS2 nanosheets via a facile one-step hydrothermal method. As shown in Fig. 12(a), the obtained Co-MoS2 exhibited superior HER activity with an overpotential of 60 mV/90 mV at a current density of 10mA cm−2 for HER in 0.5 M H2SO4 and 1.0 M KOH, respectively. They conducted DFT calculations (Fig. 12(b)) and revealed that the ΔGH* value of pristine MoS2 was about ∼2.06 eV while the ΔGH* value decreased to −0.20 eV after Co doping, demonstrating that Co doping is an effective method for enhancing HER activity of MoS2. They also studied the OER activity origin of Co-doped MoS2 by recording the ex situ Co and Mo K-edge EXAFS spectra of Co-MoS2.
 |
| Fig. 12 (a) HER performance of Co-doped MoS2, MoS2 and Pt/C. (b) The H2 adsorption free energy (ΔGH*) of MoS2 and Co-doped MoS2 and the cell voltage of different electrode couples in a two-electrode system in both acidic and alkaline media. Reproduced from ref. 194, Copyright 2018 The Royal Society of Chemistry. (c) HER performance of Fe-MoS2, MoS2 and Pt/C. (d) XPS spectra of Fe-MoS2. Reproduced from ref. 197, Copyright 2019 American Chemical Society. (e) HER performance of Ni-MoS2, MoS2 and Pt/C. Reproduced from ref. 198, Copyright 2019 The Authors. | |
Iron is a typical nonprecious and earth-abundant element, and Fe-containing materials are more effective in adsorbing hydroxyl, which leads to its unique conductivity to water splitting.13 Previous studies195,196 have verified these observations through XPS characterizations. Xue et al.197 synthesized a series of Fe-doped MoS2 nanomaterials via a facile one-pot solvothermal method. The Fe-MoS2 displayed high cycling stability and high HER activity with a small overpotential of 173 mV at a current density of 10 mA cm−2 (Fig. 12(c)). As shown in Fig. 12(d), the XPS full spectrum confirmed the existence of Fe, S, Mo and O.
Ni doping has a significant impact on surface topography and valence state of Mo in MoS2, which can accelerate the HER reaction kinetics. Wang et al.198 prepared Ni-doped MoS2 via a hydrothermal method. The layer number of MoS2 can be estimated by the difference in frequency between two characteristic Raman peaks. The results indicate that Ni doping decreases the vibration frequency of MoS2 and increases the number of layers of MoS2. Fig. 12(e) shows that the Ni-MoS2 displayed enhanced HER performance with an overpotential of 164 mV to reach a current density of 10 mA cm−2 in acidic media and a small charge transfer resistance (Rct) of 89 Ω.
In addition to Co, Fe, Ni doping,198–201 some other transition metals can also promote the HER activity of MoS2. Huang et al.202 prepared a self-supporting electrode composed of Cu mesh-supported graphene and MoS2 by electroplating zinc, followed by a hydrothermal reaction. The self-supporting catalytic electrode has the advantages of avoiding complex pre-treatment of the active substance and the usage of binders. As shown in Fig. 13(b), the MoS2–rGO–Cu exhibited excellent HER performance with a low Tafel slope of 54 mV dec−1 and a small overpotential of −300 mV at a current density of 400 mA cm−2. The excellent HER performance can be ascribed to the good electron transport capability of the Cu mesh, and specifically, the self-supporting electrode can be fabricated into any desired shape, which is well maintained while the HER takes place. Luo et al.203 designed Pd-doped MoS2 via a spontaneous interfacial redox technique. The Pd doping converted 2H phase MoS2 into a stabilized 1T structure. Furthermore, Pd atoms occurred at the Mo site, which simultaneously introduced an S vacancy. As shown in Fig. 13(a), the Pd-doped MoS2 exhibited good cycling stability and excellent HER activity with an overpotential of 78 mV at a current density of 10 mA cm−2. The DFT calculations demonstrated that the S atom next to the Pd sites had a low H atom adsorption energy of −0.02 eV. Sun et al.204 designed a novel intralayer V-doping method to synthesize semi-metallic V-doped MoS2 nanosheets. The introduction of V atoms regulated the intrinsic electrical properties of MoS2, leading to an enhanced in-plane conductivity and shortened electron transfer paths. The V-doped MoS2 showed excellent catalytic activity with an overpotential of 130 mV and a small Tafel slope (Fig. 13(c)). Zhang et al.205 reported a single Ru atom-doped MoS2 electrocatalyst for HER. As shown in Fig. 14(b) and (c), the DFT calculations revealed that the synergistic effects of the single Ru atom doping, S vacancies and phase transition of MoS2 modulated the electronic structure of MoS2 and significantly reduced the energy barrier of the Volmer step, leading to enhanced HER performance of Ru-MoS2 (Fig. 14(a)). Multi-doping methods are also a promising way to enhance the HER activity of MoS2. Yu et al.206 reported a typical MOF-engaged synthetic method to prepare Ni and Co incorporated MoS2 nano-boxes. The ultrathin nanosheets obtained exhibited enhanced electrochemical activity for HER (Fig. 13(d)). In recent years, materials with single-atom structure have been recognized as promising HER catalysts due to the maximized atom efficiency and tunable electronic properties. Ni et al.207 reported that Ru-based single-atom catalysts are promising HER catalysts due to its excellent HER performance, which is comparable to commercial Pt/C catalysts. However, Ru-based single atom catalysts have problems such as large amount of Ru and unsatisfactory stability. Ge et al.208 synthesized dual-metallic Ru and Ni atoms decorated MoS2, which resolve the above problems well. The introduction of Ni has two key roles. On the one hand, the introduction of highly electronegative heteroatom Ni could regulate the electronic structure of Ru and optimize the H* adsorption during the water splitting process, thus vastly enhancing the HER property. On the other hand, the incorporation of highly electronegative heteroatom Ni in the substrate exposes abundant active sites and improves electron transfer of the catalyst, and further anchors the single atom Ru and reduces the consumption of precious metal Ru atoms.
 |
| Fig. 13 (a) HER performance of Pd-MoS2/CP and its comparison. Reproduced with permission from ref. 203, Copyright 2020 Elsevier Ltd. (b) HER performance of MoS2–rGO–Cu and its comparison. Reproduced with permission from ref. 202, Copyright 2020 Elsevier. (c) HER performance of V-MoS2 and its comparison. Reproduced with permission from ref. 204, Copyright 2014 The Royal Society of Chemistry. (d) HER performance of Ni–Co–MoS2 and its comparison. Reproduced with permission from ref. 206, Copyright 2016 WILEY. | |
 |
| Fig. 14 (a) HER performance of Ru–MoS2 and its comparison. (b) Free energy diagrams of the different MoS2 model catalysts under alkaline solution. (c) Contour maps of the electron localization function (ELF) in 2H/1T-Ru-MoS2-Sv. Reproduced with permission from ref. 205, Copyright 2019 WILEY. | |
4.3.2. Nonmetal-doping method. Nonmetal doping can enhance the electrocatalytic activity of MoS2. Wang et al.209 synthesized amorphous P-doped MoS2 nanoparticles hydrothermally. The P-doping promoted the amorphization of MoS2; thus, affecting the HER performance of MoS2. Deng et al.210 prepared O-doped MoS2 via an electrochemical anodic activation method. The HER activity of O-doped MoS2 significantly improved at an overpotential of 50 mV, at a current density of 1 mA cm−2 (Fig. 15(a)). As shown in Fig. 15(b), the XPS images confirmed the strong electron interactions after O doping, which indicated the existence of Mo–O bonds and demonstrated that the O doping was successful. Liu et al.211 reported O and P dual-doped MoS2 nanosheets, which have a porous structure and conductive network via a one-pot hydrothermal approach. As shown in Fig. 15(c), the O, P multi-doped MoS2 showed superior electrocatalytic performances compared with O-doped MoS2 nanosheets. Wang et al.212 prepared MoS2 decorated Ni–Fe–N-doped carbon nanotubes via a hydrothermal method. According to the SEM results shown in Fig. 15(d), the catalysts were hierarchically structured. Due to the synergistic effect of the NiFe alloy and N-doped carbon nanotubes, the catalysts exhibited excellent HER performance with a cell voltage of 1.6 V at a current density of 10 mA cm−2. Tian et al.213 synthesized N, P dual-doped MoS2 on hollow carbon spheres by a template and hydrothermal process. The synergistic effect of N, P dual-doped carbon and MoS2 led to the enhanced electrocatalytic performance of MoS2 with an overpotential of 147 mV, at a current density of 10 mA cm−2 and Tafel slope of 72 mV dec−1. As shown in Fig. 15(e), the XPS spectra confirmed the co-existence of N and P atoms.
 |
| Fig. 15 (a) HER performance of O-doped MoS2. (b) Mo 3d XPS spectra of O, P-MoS2 (R = 10%) and O-MoS2. Reproduced with permission from ref. 210, Copyright Elsevier Ltd. (c) HER performance of O, P dual-doped MoS2 and its comparison. Reproduced with permission from ref. 211, Copyright 2019 WILEY. (d) SEM images and elemental mapping of NiFe–NCNT–MoS2. Reproduced with permission from ref. 212, Copyright 2019 The Royal Society of Chemistry. (e) XPS survey spectra and high-resolution scans of B, C 1s, C, N 1s, D, P 2p, E, S 2p, and F, Mo 3d electrons of the P-MoS2@NCs-2. Reproduced with permission from ref. 213, Copyright 2021 John Wiley& Sons Ltd. | |
Metal-doping and nonmental-doping can be synergistically used to improve the HER performance of MoS2. Meng et al.214 reported a 3D mesoporous hybrid structure of Co-doped MoS2 and graphene. The Co-doping enhanced the intrinsic electrocatalytic activity of the in-plane S sites. The graphene network was found to be electronically conductive and robust, which improved the conductivity of electrons and enhanced the stability of the hybrid structure. The catalysts showed good cycling stability and an excellent HER performance, with an overpotential of 143 mV at a current density of 10 mA cm−2. Wu et al.215 designed Co, Se dual-doped electrocatalysts via a solvothermal and post-low-temperature selenylation process. Due to the abundance of interfaces, the electrocatalysts exhibited excellent HER performance, with a low overpotential of 58 mV at a current density of 10 mA cm−2 and a small Tafel slope of 84 mV dec−1. Sun et al.216 reported plasma-induced N, Pt-doping and phase modulation of MoS2 nanosheets. The synergetic doping of N and Pt heteroatoms regulates the electronic and coordinated structures of MoS2 and further facilitates water adsorption and dissociation during the HER. Notably, this plasma bombardment method is highly feasible for the large-area fabrication of MoS2-derived HER active electrodes.
4.4. Theoretical study of the HER
The studies of electronic structures of MoS2 offer theoretical guidance for designing efficient catalysts. For MoS2, a typical 2D material, the theoretical calculation of the basal plane positions, Mo edge and S edge is quite significant. Furthermore, it is also beneficial to investigate the adsorption energy of intermediates. Jacob et al.217 proposed an H-binding mechanism for S atoms in the basal plane of MoS2. This model was tested and verified by DFT calculations; herein, the energy barrier can be tuned by introducing metal dopants and defects. Their study revealed the electronic structure mechanism which tends to influence the basal plane S atoms activation (Fig. 16(a) and (b)). Xian et al.218 synthesized the monodispersed single-crystal Pt nanoparticles decorated on 2H phase MoS2 nanosheets via a wet chemical method. They construct the atomic model of Pt truncated octahedron loaded on MoS2, and choose four Pt sites (Fig. 16(c)). The charge-density difference is showed in Fig. 16(d), indicating the variations of the charge distributions for Pt and S at the interface of Pt-MoS2 atomic model from those for pure Pt and S. The results reveal that the Pt–S bonds are formed. Then, they calculate the free energy of adsorbed atomic hydrogen (ΔGH*), including MoS2 (001), Pt (100), Pt (100) interface, Pt (1–11) and Pt (1–11) interface (Fig. 16(e)). The results indicate that the Pt (100) interface owns the smallest ΔGH* as well as the best HER activity. Further, they found that with the studied Pt atoms changing to the interface, the D-band center move away from the Fermi level (Fig. 14(f)), indicating the decrease of ΔGH*, which confirms the superiority for Pt (100) interface in HER performance. In published DFT studies, the electronic structures of MoS2-based materials are usually computed by VASP and the electron–ion interactions are described by the projector-augmented wave method. All calculations are typically implemented with PBE exchange–correlation functional on periodically repeated slabs. The details of the molecular model-building, HER mechanism and free-energy calculations are provided in the relevant ref. 219–222.
 |
| Fig. 16 (a) Left: ball model of a Mo/WS2 particle exposing both S-edge and Mo/W-edge. Right: differential free energies of H atom adsorption. (b) The charge of the irreversible oxidation peak as a function of the amount of Mo used during the synthesis of MoS2 Reproduced with permission from ref. 217, Copyright 2008 The Royal Society of Chemistry. (c) The side views of the atomic model of Pt truncated octahedron loaded on MoS2. (d) Charge-density difference for Pt-MoS2. The decrease of electron density is shown in yellow, and increase is shown in blue. (e) The adsorption Gibbs free energy of hydrogen on the above Pt positions and the surface for MoS2. (f) The partial density of states (PDOS) of Pt atoms on the above positions. Reproduced with permission from ref. 218, Copyright 2022 Elsevier. | |
5. Conclusions and outlook
With the depletion of traditional fossil energy, the development of green energy such as hydrogen energy has become urgent. Electrocatalytic water splitting to produce hydrogen offers a means to develop new energy sources. Up to now, significant progress has been made in achieving effecting hydrogen evolution reactions (HERs) using promising electrocatalysts such as transition metal sulfides (TMDs), transition metal carbides (TMCs), transition metal phosphides (TMPs) and transition metal nitrides (TMNs). As a typical electrocatalyst, MoS2 has been widely studied and much progress has been made. In this review, we summarize the synthetic methods of MoS2 and the effective strategies adopted to optimize the HER performance of MoS2. The introduction of defects significantly enhanced the HER activity of the MoS2-based materials, which was also verified theoretically. The formation of heterostructures is another effective way to enhance the HER activity of MoS2, which can modulate the electronic structure. Furthermore, doping metal atoms (Fe, Co, Ni, Cu, Mn, V, Ru etc.) or nonmetal atoms (C, N, F, P, S, Se etc.) into MoS2 can also improve its electrocatalytic HER performance.
However, there are still some challenges for the commercial application of MoS2-based materials. Firstly, even though ultrathin MoS2-based materials can be synthesized by CVD and hydrothermal methods, the large-scale production of MoS2 is still a challenge. Secondly, the standards for evaluating electrocatalytic stability have not yet been developed. Thirdly, while DFT calculations can provide a detailed theoretical insight into the reaction mechanism of a single active center, research involving the existence of multiple active centers is still lacking. Fourthly, the catalytic influence of H2O on the MoS2 surface and interlayers is still not completely understood because of the difficulty to develop bifunctional electrocatalysts for all electrolytes. Lastly, vacancies, doping atoms, and heterojunctions usually have a positive effect on the electrocatalytic process. However, the reaction mechanism needs to be further explored.
While there is still a long way to go for the development of MoS2-based electrocatalytic materials, the research interest in this area is increasing. Moreover, with the rapid development of computational tools, it is possible to make advances in many experimental areas, including MoS2-based materials. From this point of view, we can foresee that MoS2-based materials will be very promising for hydrogen production applications.
Conflicts of interest
The authors declare no competing financial interest.
Acknowledgements
This research was supported by National Science and Technology Major Project (Grant No. 2020YFB1506001) and Department of Science and Technology of Sichuan Province (Grant No. 2021YFG0231).
References
- M. A. Shannon, P. W. Bohn, M. Elimelech, J. G. Georgiadis, B. J. Marinas and A. M. Mayes, Nature, 2008, 452, 301–310 CrossRef CAS PubMed.
- D. Larcher and J. M. Tarascon, Nat. Chem., 2015, 7, 19–29 CrossRef CAS PubMed.
- A. Fiaz, D. Zhu and J. Sun, Environ. Sci. Eur., 2021, 33, 64–80 CrossRef CAS.
- L. Han, S. Dong and E. Wang, Adv. Mater., 2016, 28, 9266–9291 CrossRef CAS PubMed.
- I. K. Kapdan and F. Kargi, Enzyme Microb. Technol., 2006, 38, 569–582 CrossRef CAS.
- S. H. Mousavi-Avval, S. Rafiee, A. Jafari and A. Mohammadi, J. Clean. Prod., 2011, 19, 1464–1470 CrossRef.
- P. Nugent, Y. Belmabkhout, S. D. Burd, A. J. Cairns, R. Luebke, K. Forrest, T. Pham, S. Ma, B. Space, L. Wojtas, M. Eddaoudi and M. J. Zaworotko, Nature, 2013, 495, 80–84 CrossRef CAS PubMed.
- A. Kudo and Y. Miseki, Chem. Soc. Rev., 2009, 38, 253–278 RSC.
- Y. Li, H. Wang, L. Xie, Y. Liang, G. Hong and H. Dai, J. Am. Chem. Soc., 2011, 133, 7296–7299 CrossRef CAS PubMed.
- Y. Liang, Y. Li, H. Wang, J. Zhou, J. Wang, T. Regier and H. Dai, Nat. Mater., 2011, 10, 780–786 CrossRef CAS PubMed.
- C. C. McCrory, S. Jung, J. C. Peters and T. F. Jaramillo, J. Am. Chem. Soc., 2013, 135, 16977–16987 CrossRef CAS PubMed.
- S. Zhao, Y. Wang, J. Dong, C.-T. He, H. Yin, P. An, K. Zhao, X. Zhang, C. Gao, L. Zhang, J. Lv, J. Wang, J. Zhang, A. M. Khattak, N. A. Khan, Z. Wei, J. Zhang, S. Liu, H. Zhao and Z. Tang, Nat. Energy, 2016, 1, 184–193 Search PubMed.
- S. Li, J. Sun and J. Guan, Chin. J. Catal., 2021, 42, 511–556 CrossRef CAS.
- Y. Chen, Q. Zhou, G. Zhao, Z. Yu, X. Wang, S. X. Dou and W. Sun, Adv. Funct. Mater., 2017, 28, 170–176 Search PubMed.
- C. Liu, G. Zhang, L. Yu, J. Qu and H. Liu, Small, 2018, 14, 180–188 Search PubMed.
- J. Deng, H. Li, J. Xiao, Y. Tu, D. Deng, H. Yang, H. Tian, J. Li, P. Ren and X. Bao, Energy Environ. Sci., 2015, 8, 1594–1601 RSC.
- D. Y. Wang, M. Gong, H. L. Chou, C. J. Pan, H. A. Chen, Y. Wu, M. C. Lin, M. Guan, J. Yang, C. W. Chen, Y. L. Wang, B. J. Hwang, C. C. Chen and H. Dai, J. Am. Chem. Soc., 2015, 137, 1587–1592 CrossRef CAS PubMed.
- J. Deng, P. Ren, D. Deng, L. Yu, F. Yang and X. Bao, Energy Environ. Sci., 2014, 7, 1919–1923 RSC.
- M. S. Faber, M. A. Lukowski, Q. Ding, N. S. Kaiser and S. Jin, J. Phys. Chem. C Nanomater. Interfaces, 2014, 118, 21347–21356 CrossRef CAS PubMed.
- Q. Gong, L. Cheng, C. Liu, M. Zhang, Q. Feng, H. Ye, M. Zeng, L. Xie, Z. Liu and Y. Li, ACS Catal., 2015, 5, 2213–2219 CrossRef CAS.
- J. Kibsgaard, C. Tsai, K. Chan, J. D. Benck, J. K. Nørskov, F. Abild-Pedersen and T. F. Jaramillo, Energy Environ. Sci., 2015, 8, 3022–3029 RSC.
- M. Zeng and Y. Li, J. Mater. Chem. A, 2015, 3, 14942–14962 RSC.
- Y. Tan, H. Wang, P. Liu, Y. Shen, C. Cheng, A. Hirata, T. Fujita, Z. Tang and M. Chen, Energy Environ. Sci., 2016, 9, 2257–2261 RSC.
- A. Eftekhari, Int. J. Hydrogen Energy, 2017, 42, 11053–11077 CrossRef CAS.
- Y. Jia, L. Zhang, G. Gao, H. Chen, B. Wang, J. Zhou, M. T. Soo, M. Hong, X. Yan, G. Qian, J. Zou, A. Du and X. Yao, Adv. Mater., 2017, 29, 798–805 Search PubMed.
- H. Sun, Z. Yan, F. Liu, W. Xu, F. Cheng and J. Chen, Adv. Mater., 2020, 32, 326–334 Search PubMed.
- J. Feng, F. Lv, W. Zhang, P. Li, K. Wang, C. Yang, B. Wang, Y. Yang, J. Zhou, F. Lin, G. C. Wang and S. Guo, Adv. Mater., 2017, 29, 288–296 Search PubMed.
- M. S. Faber and S. Jin, Energy Environ. Sci., 2014, 7, 3519–3542 RSC.
- H. Vrubel and X. Hu, Angew. Chem., Int. Ed., 2012, 51, 12703–12706 CrossRef CAS PubMed.
- W. F. Chen, J. T. Muckerman and E. Fujita, Chem. Commun., 2013, 49, 8896–8909 RSC.
- Z. W. Seh, K. D. Fredrickson, B. Anasori, J. Kibsgaard, A. L. Strickler, M. R. Lukatskaya, Y. Gogotsi, T. F. Jaramillo and A. Vojvodic, ACS Energy Lett., 2016, 1, 589–594 CrossRef CAS.
- X. Wang, Y. V. Kolen'ko, X. Q. Bao, K. Kovnir and L. Liu, Angew. Chem., Int. Ed., 2015, 54, 8188–8192 CrossRef CAS PubMed.
- C. Liu, L. Sun, L. Luo, W. Wang, H. Dong and Z. Chen, ACS Appl. Mater. Interfaces, 2021, 13, 22646–22654 CrossRef CAS PubMed.
- X. Zhang, Z. Zhu, X. Liang, F.-X. Ma, J. Zhang, Y. Tan, Z. Pan, Y. Bo and C.-M. Lawrence Wu, Chem. Eng. J., 2021, 408, 1910–1916 Search PubMed.
- A. A. Koverga, E. Flórez, C. Jimenez-Orozco and J. A. Rodriguez, Electrochim. Acta, 2021, 368, 351–359 CrossRef.
- B. Zhang, H. Qin, Y. Pan, W. Lin, S. Xu, Q. Sun, E. Liu, F. He, L. Diao, C. He and L. Ma, ACS Appl. Nano Mater., 2020, 4, 372–380 CrossRef.
- D. Kong, J. J. Cha, H. Wang, H. R. Lee and Y. Cui, Energy Environ. Sci., 2013, 6, 3553–3558 RSC.
- J. Xie, J. Zhang, S. Li, F. Grote, X. Zhang, H. Zhang, R. Wang, Y. Lei, B. Pan and Y. Xie, J. Am. Chem. Soc., 2013, 135, 17881–17888 CrossRef CAS PubMed.
- J. Chen, X. J. Wu, L. Yin, B. Li, X. Hong, Z. Fan, B. Chen, C. Xue and H. Zhang, Angew. Chem., Int. Ed., 2015, 54, 1210–1214 CrossRef CAS PubMed.
- R. Lv, J. A. Robinson, R. E. Schaak, D. Sun, Y. Sun, T. E. Mallouk and M. Terrones, Acc. Chem. Res., 2015, 48, 56–64 CrossRef CAS PubMed.
- S. Xu, D. Li and P. Wu, Adv. Funct. Mater., 2015, 25, 1127–1136 CrossRef CAS.
- Y. Jiao, Y. Zheng, K. Davey and S.-Z. Qiao, Nat. Energy, 2016, 1, 160–169 Search PubMed.
- Q. Lu, Y. Yu, Q. Ma, B. Chen and H. Zhang, Adv. Mater., 2016, 28, 1917–1933 CrossRef CAS PubMed.
- D. Voiry, J. Yang and M. Chhowalla, Adv. Mater., 2016, 28, 6197–6206 CrossRef CAS PubMed.
- S. P. Kaur and T. J. Dhilip Kumar, Appl. Surf. Sci., 2021, 552, 3002–3012 CrossRef.
- P. Jiang, Q. Liu, Y. Liang, J. Tian, A. M. Asiri and X. Sun, Angew. Chem., Int. Ed., 2014, 53, 12855–12859 CrossRef CAS PubMed.
- Y. Shi and B. Zhang, Chem. Soc. Rev., 2016, 45, 1529–1541 RSC.
- S. M. El-Refaei, P. A. Russo and N. Pinna, ACS Appl. Mater. Interfaces, 2021, 13, 22077–22097 CrossRef CAS PubMed.
- W. Pei, X. Wang, C. Liu, D. Zhao, C. Wu, K. Wang and Q. Wang, Electrochim. Acta, 2021, 381, 286–296 CrossRef.
- Y. Jeung, H. Jung, D. Kim, H. Roh, C. Lim, J. W. Han and K. Yong, J. Mater. Chem. A, 2021, 9, 12203–12213 RSC.
- R. Zhang, Y. Dong, M. A. Al-Tahan, Y. Zhang, R. Wei, Y. Ma, C. Yang and J. Zhang, J. Energy Chem., 2021, 60, 85–94 CrossRef.
- W. J. Yu, Z. Li, H. Zhou, Y. Chen, Y. Wang, Y. Huang and X. Duan, Nat. Mater., 2013, 12, 246–252 CrossRef CAS PubMed.
- A. S. Sethulekshmi, J. S. Jayan, S. Appukuttan and K. Joseph, Phys. E Low-dimens. Syst. Nanostruct., 2021, 132, 89–96 Search PubMed.
- S. Park, C. Kim, S. O. Park, N. K. Oh, U. Kim, J. Lee, J. Seo, Y. Yang, H. Y. Lim, S. K. Kwak, G. Kim and H. Park, Adv. Mater., 2020, 32, 18–29 Search PubMed.
- W. Chen, Z. Wang, K. V. Bets, D. X. Luong, M. Ren, M. G. Stanford, E. A. McHugh, W. A. Algozeeb, H. Guo, G. Gao, B. Deng, J. Chen, J. T. Li, W. T. Carsten, B. I. Yakobson and J. M. Tour, ACS Nano, 2021, 15, 1282–1290 CrossRef CAS PubMed.
- J. Huang, X. Pan, X. Liao, M. Yan, B. Dunn, W. Luo and L. Mai, Nanoscale, 2020, 12, 9246–9254 RSC.
- H. He, X. Li, D. Huang, J. Luan, S. Liu, W. K. Pang, D. Sun, Y. Tang, W. Zhou, L. He, C. Zhang, H. Wang and Z. Guo, ACS Nano, 2021, 15, 8896–8906 CrossRef CAS PubMed.
- J. Dong, X. Zhang, J. Huang, J. Hu, Z. Chen and Y. Lai, Chem. Eng. J., 2021, 412, 556–576 Search PubMed.
- B. Gao, Y. Zhao, X. Du, Y. Chen, B. Guan, Y. Li, Y. Li, S. Ding, H. Zhao, C. Xiao and Z. Song, J. Mater. Chem. A, 2021, 9, 8394–8400 RSC.
- N. Zhao, L. Wang, Z. Zhang and Y. Li, ACS Appl. Mater. Interfaces, 2019, 11, 42014–42020 CrossRef CAS PubMed.
- X. Wang, C. Wang, S. Ci, Y. Ma, T. Liu, L. Gao, P. Qian, C. Ji and Y. Su, J. Mater. Chem. A, 2020, 8, 23488–23497 RSC.
- Y. Chen, J. Rong, Q. Tao, C. Xing, M. Lian, J. Cheng, X. Liu, J. Cao, M. Wei, S. Lv, P. Zhu, L. Yang and J. Yang, Electrochim. Acta, 2020, 357, 1307–1315 Search PubMed.
- A. Q. Mugheri, S. Ali, G. S. Narejo, A. A. Otho, R. Lal, M. A. Abro, S. H. Memon and F. Abbasi, Int. J. Hydrogen Energy, 2020, 45, 21502–21511 CrossRef CAS.
- X. Xin, Y. Song, S. Guo, Y. Zhang, B. Wang, J. Yu and X. Li, Appl. Catal. B Environ., 2020, 269, 773–780 CrossRef.
- A. Jalil, Z. Zhuo, Z. Sun, F. Wu, C. Wang and X. Wu, J. Mater. Chem. A, 2020, 8, 1307–1314 RSC.
- J. Zhang, T. Wang, P. Liu, S. Liu, R. Dong, X. Zhuang, M. Chen and X. Feng, Energy Environ. Sci., 2016, 9, 2789–2793 RSC.
- Y. Li, H. Li, K. Cao, T. Jin, X. Wang, H. Sun, J. Ning, Y. Wang and L. Jiao, Energy Storage Mater., 2018, 12, 44–53 CrossRef.
- M. S. Faber, R. Dziedzic, M. A. Lukowski, N. S. Kaiser, Q. Ding and S. Jin, J. Am. Chem. Soc., 2014, 136, 10053–10061 CrossRef CAS PubMed.
- D. Voiry, R. Fullon, J. Yang, E. S. C. de Carvalho Castro, R. Kappera, I. Bozkurt, D. Kaplan, M. J. Lagos, P. E. Batson, G. Gupta, A. D. Mohite, L. Dong, D. Er, V. B. Shenoy, T. Asefa and M. Chhowalla, Nat. Mater., 2016, 15, 1003–1009 CrossRef CAS PubMed.
- T. Zhang, M.-Y. Wu, D.-Y. Yan, J. Mao, H. Liu, W.-B. Hu, X.-W. Du, T. Ling and S.-Z. Qiao, Nano Energy, 2018, 43, 103–109 CrossRef CAS.
- Y. Li, J. Yin, L. An, M. Lu, K. Sun, Y. Q. Zhao, D. Gao, F. Cheng and P. Xi, Small, 2018, 14, 70–78 Search PubMed.
- S. Peng, F. Gong, L. Li, D. Yu, D. Ji, T. Zhang, Z. Hu, Z. Zhang, S. Chou, Y. Du and S. Ramakrishna, J. Am. Chem. Soc., 2018, 140, 13644–13653 CrossRef CAS PubMed.
- Y. Da, J. Liu, L. Zhou, X. Zhu, X. Chen and L. Fu, Adv. Mater., 2019, 31, 93–99 CrossRef.
- G. Li, D. Zhang, Q. Qiao, Y. Yu, D. Peterson, A. Zafar, R. Kumar, S. Curtarolo, F. Hunte, S. Shannon, Y. Zhu, W. Yang and L. Cao, J. Am. Chem. Soc., 2016, 138, 16632–16638 CrossRef CAS.
- X. J. Chua, S. M. Tan, X. Chia, Z. Sofer, J. Luxa and M. Pumera, Chemistry, 2017, 23, 3169–3177 CrossRef CAS PubMed.
- T. F. Jaramillo, K. P. Jorgensen, J. Bonde, J. H. Nielsen, S. Horch and I. Chorkendorff, Science, 2007, 317, 100–102 CrossRef CAS PubMed.
- M. Zheng, K. Guo, W.-J. Jiang, T. Tang, X. Wang, P. Zhou, J. Du, Y. Zhao, C. Xu and J.-S. Hu, Appl. Catal. B Environ., 2019, 244, 1004–1012 CrossRef CAS.
- A. Wang, K. Hu, Y. Liu, R. Li, C. Ye, Z. Yi and K. Yan, Int. J. Hydrogen Energy, 2019, 44, 6573–6581 CrossRef CAS.
- H. Wang, X. Xiao, S. Liu, C. L. Chiang, X. Kuai, C. K. Peng, Y. C. Lin, X. Meng, J. Zhao, J. Choi, Y. G. Lin, J. M. Lee and L. Gao, J. Am. Chem. Soc., 2019, 141, 18578–18584 CrossRef CAS PubMed.
- L. Song, M. Zhao, X. Li, Z. Zhang and L. Qu, RSC Adv., 2016, 6, 70740–70746 RSC.
- L. Zhang, J. Dong and F. Ding, Chem. Rev., 2021, 10, 191–199 Search PubMed.
- K. C. Kwon, T. H. Lee, S. Choi, K. S. Choi, S. O. Gim, S.-R. Bae, J.-L. Lee, H. W. Jang and S. Y. Kim, Appl. Surf. Sci., 2021, 541, 354–363 CrossRef.
- K. H. Choi, S. Oh, S. Chae, B. J. Jeong, B. J. Kim, J. Jeon, S. H. Lee, S. O. Yoon, C. Woo, X. Dong, A. Ghulam, C. Lim, Z. Liu, C. Wang, A. Junaid, J.-H. Lee, H. K. Yu and J.-Y. Choi, J. Alloys Compd., 2021, 853, 576–585 CrossRef.
- S. Dolai, P. Maiti, A. Ghorai, R. Bhunia, P. K. Paul and D. Ghosh, ACS Appl. Mater. Interfaces, 2021, 13, 438–448 CrossRef CAS PubMed.
- F. Yang, Z. Cao, J. Wang, S. Wang and H. Zhong, J. Alloys Compd., 2020, 817, 678–691 Search PubMed.
- Y. Qiao, T. Hirtz, F. Wu, G. Deng, X. Li, Y. Zhi, H. Tian, Y. Yang and T.-L. Ren, ACS Appl. Electron. Mater., 2019, 2, 346–370 CrossRef.
- Y. Yu, G. S. Jung, C. Liu, Y. C. Lin, C. M. Rouleau, M. Yoon, G. Eres, G. Duscher, K. Xiao, S. Irle, A. A. Puretzky and D. B. Geohegan, ACS Nano, 2021, 15, 4504–4517 CrossRef CAS PubMed.
- X. Lin, F. Wang, X. Shan, Y. Miao, X. Chen, M. Yan, L. Zhang, K. Liu, J. Luo and K. Zhang, Appl. Surf. Sci., 2021, 546, 45–55 Search PubMed.
- S. Li, S. Tian, Y. Yao, M. He, L. Chen, Y. Zhang and J. Zhai, Nanomaterials, 2021, 11, 98–108 CrossRef PubMed.
- H. Sun, H. Liu, M. Nie, Z. Zhao, Z. Xue, J. Liao, F. Xue, S. Zhang, M. Wu and T. Gao, Ceram. Int., 2021, 47, 13994–14000 CrossRef CAS.
- Z. Zhang, W. Li, R. Wang, H. Li, J. Yan, Q. Jin, P. Feng, K. Wang and K. Jiang, J. Alloys Compd., 2021, 872, 389–399 Search PubMed.
- Z. Guo, W. Li, Y. He, G. Li, K. Zheng and C. Xu, Appl. Surf. Sci., 2020, 512, 576–587 CrossRef.
- Y. Cai, H. Kang, F. Jiang, L. Xu, Y. He, J. Xu, X. Duan, W. Zhou, X. Lu and Q. Xu, Appl. Surf. Sci., 2021, 546, 1303–1314 CrossRef.
- S. Jana, S. Kumar Bhar, N. Mukherjee and A. Mondal, Mater. Lett., 2013, 109, 51–54 CrossRef CAS.
- Y. Zhou, L. Jia, T. Wang, Y. Du and C. Wang, Int. J. Hydrogen Energy, 2018, 43, 7356–7365 CrossRef CAS.
- K. Hernandez Ruiz, M. Ciprian, R. Tu, F. Verpoort, M. Li, S. Zhang, J. R. Vargas Garcia, H. Li, T. Goto, Y. Fan, W. Jiang and L. Zhang, J. Alloys Compd., 2019, 806, 1276–1284 CrossRef CAS.
- S. Kang, J.-J. Koo, H. Seo, Q. T. Truong, J. B. Park, S. C. Park, Y. Jung, S.-P. Cho, K. T. Nam, Z. H. Kim and B. H. Hong, J. Mater. Chem. C, 2019, 7, 10173–10178 RSC.
- I. Yang, S. Kim, M. Niihori, A. Alabadla, Z. Li, L. Li, M. N. Lockrey, D.-Y. Choi, I. Aharonovich, J. Wong-Leung, H. H. Tan, C. Jagadish and L. Fu, Nano Energy, 2020, 71, 235–245 Search PubMed.
- Y. Feng, X. Wu, L. Hu and G. Gao, J. Mater. Chem. C, 2020, 8, 14353–14359 RSC.
- W. Wan, L. Zhan, B. Xu, F. Zhao, Z. Zhu, Y. Zhou, Z. Yang, T. Shih and W. Cai, Small, 2017, 13, 465–475 Search PubMed.
- W. Wan, X. Li, X. Li, B. Xu, L. Zhan, Z. Zhao, P. Zhang, S. Q. Wu, Z.-z. Zhu, H. Huang, Y. Zhou and W. Cai, RSC Adv., 2016, 6, 323–330 RSC.
- L. Li, X. Wang, J. Li, Y. Guo, X. Li and Y. Lu, J. Alloys Compd., 2021, 872, 892–902 Search PubMed.
- S. Y. Ding, M. Dong, Y. W. Wang, Y. T. Chen, H. Z. Wang, C. Y. Su and W. Wang, J. Am. Chem. Soc., 2016, 138, 3031–3037 CrossRef CAS PubMed.
- Z. Yuan, H.-J. Peng, J.-Q. Huang, X.-Y. Liu, D.-W. Wang, X.-B. Cheng and Q. Zhang, Adv. Funct. Mater., 2014, 24, 6105–6112 CrossRef CAS.
- X. Zhuang, Y. Mai, D. Wu, F. Zhang and X. Feng, Adv. Mater., 2015, 27, 403–427 CrossRef CAS PubMed.
- X. Wu, F. Tian, W. Wang, J. Chen, M. Wu and J. X. Zhao, J. Mater. Chem. C, 2013, 1, 4676–4684 RSC.
- J. Hicks, A. Tejeda, A. Taleb-Ibrahimi, M. S. Nevius, F. Wang, K. Shepperd, J. Palmer, F. Bertran, P. Le Fèvre, J. Kunc, W. A. de Heer, C. Berger and E. H. Conrad, Nat. Phys., 2012, 9, 49–54 Search PubMed.
- I. Bilecka and M. Niederberger, Nanoscale, 2010, 2, 1358–1374 RSC.
- L. Mai, L. Xu, C. Han, X. Xu, Y. Luo, S. Zhao and Y. Zhao, Nano Lett., 2010, 10, 4750–4755 CrossRef CAS PubMed.
- M. Yoshimura and K. Byrappa, J. Mater. Sci., 2007, 43, 2085–2103 CrossRef.
- J. Jiang, Y. Li, J. Liu and X. Huang, Nanoscale, 2011, 3, 45–58 RSC.
- Y. Yang, H. Meng, S. Yan, H. Zhu, W. Ma, C. Wang, F. Ma and Z. Hu, J. Alloys Compd., 2021, 874, 677–687 Search PubMed.
- C. Ayappan, B. Palanivel, V. Jayaraman and A. Mani, J. Alloys Compd., 2021, 871, 1254–1264 CrossRef.
- D. Lee, H. W. Lee, S. Mathur and K. H. Kim, J. Alloys Compd., 2021, 868, 1365–1375 Search PubMed.
- Y. Qiu, X. Zhang, H. Han, Z. Liu, J. Liu and X. Ji, J. Power Sources, 2021, 499, 566–576 CrossRef.
- N. Liu, L. Yang, S. Wang, Z. Zhong, S. He, X. Yang, Q. Gao and Y. Tang, J. Power Sources, 2015, 275, 588–594 CrossRef CAS.
- D. Wang, X. Zhang, S. Bao, Z. Zhang, H. Fei and Z. Wu, J. Mater. Chem. A, 2017, 5, 2681–2688 RSC.
- C. Qin, A. Fan, X. Zhang, S. Wang, X. Yuan and X. Dai, J. Mater. Chem. A, 2019, 7, 27594–27602 RSC.
- M. Li, B. Cai, R. Tian, X. Yu, M. B. H. Breese, X. Chu, Z. Han, S. Li, R. Joshi, A. Vinu, T. Wan, Z. Ao, J. Yi and D. Chu, Chem. Eng. J., 2021, 409, 465–476 Search PubMed.
- Y. Xiao, M. Tan, Z. Li, L. He, B. Gao, Y. Chen, Y. Zheng and B. Lin, Int. J. Hydrogen Energy, 2021, 46, 11688–11700 CrossRef CAS.
- W. Ding and X. Meng, J. Alloys Compd., 2021, 866, 2307–2317 CrossRef.
- M. Kang, H. J. Chai, H. B. Jeong, C. Park, I. Y. Jung, E. Park, M. M. Cicek, I. Lee, B. S. Bae, E. Durgun, J. Y. Kwak, S. Song, S. Y. Choi, H. Y. Jeong and K. Kang, ACS Nano, 2021, 15, 8715–8723 CrossRef CAS PubMed.
- Y. Liu, J. He, N. Zhang, W. Zhang, Y. Zhou and K. Huang, J. Mater. Sci., 2021, 56, 12559–12583 CrossRef CAS.
- W. T. Kang, T. L. Phan, K. J. Ahn, I. Lee, Y. R. Kim, U. Y. Won, J. E. Kim, Y. H. Lee and W. J. Yu, ACS Appl. Mater. Interfaces, 2021, 13, 18056–18064 CrossRef CAS PubMed.
- Y.-H. Ting, M.-C. Wu, Y. Aoyama, K.-C. Lu and W.-W. Wu, Appl. Surf. Sci., 2021, 544, 809–819 CrossRef.
- S. D. Thammaiah, X. Liu, T. Knežević, K. M. Batenburg, A. A. I. Aarnink and L. K. Nanver, Solid-State Electron., 2021, 177, 763–773 CrossRef.
- J. Wen, Y. Wan, Y. Dong, H. Zhan, Y. Luo, F. Tang, G. D. West, F. Pang, G. Peng and T. Wang, J. Lumin., 2021, 231, 689–699 CrossRef.
- B. Shi, D. Zhou, R. Qiu, M. Bahri, X. Kong, H. Zhao, C. Tlili and D. Wang, Appl. Surf. Sci., 2020, 533, 1567–1577 CrossRef.
- M. P. Browne, F. Novotný, C. L. Manzanares Palenzuela, J. Šturala, Z. Sofer and M. Pumera, ACS Sustainable Chem. Eng., 2019, 7, 16440–16449 CrossRef CAS.
- S. H. Yu, Z. Tang, Y. Shao, H. Dai, H. Y. Wang, J. Yan, H. Pan and D. H. C. Chua, ACS Appl. Energy Mater., 2019, 2, 5799–5808 CrossRef CAS.
- G. Fiori, F. Bonaccorso, G. Iannaccone, T. Palacios, D. Neumaier, A. Seabaugh, S. K. Banerjee and L. Colombo, Nat. Nanotechnol., 2014, 9, 768–779 CrossRef CAS PubMed.
- L. K. Tan, B. Liu, J. H. Teng, S. Guo, H. Y. Low and K. P. Loh, Nanoscale, 2014, 6, 14002–14012 RSC.
- R. F. Frindt, J. Appl. Phys., 1966, 37, 1928–1929 CrossRef CAS.
- X. Wu, M. Yu, J. Liu, Y. Ma and S. Li, Chem. Eng. J., 2020, 381, 189–201 Search PubMed.
- L. Zhang and X. W. Lou, Chemistry, 2014, 20, 5219–5223 CrossRef CAS PubMed.
- Z. Zeng, Z. Yin, X. Huang, H. Li, Q. He, G. Lu, F. Boey and H. Zhang, Angew. Chem., Int. Ed., 2011, 50, 11093–11097 CrossRef CAS PubMed.
- J. N. Coleman, M. Lotya, A. O'Neill, S. D. Bergin, P. J. King, U. Khan, K. Young, A. Gaucher, S. De, R. J. Smith, I. V. Shvets, S. K. Arora, G. Stanton, H. Y. Kim, K. Lee, G. T. Kim, G. S. Duesberg, T. Hallam, J. J. Boland, J. J. Wang, J. F. Donegan, J. C. Grunlan, G. Moriarty, A. Shmeliov, R. J. Nicholls, J. M. Perkins, E. M. Grieveson, K. Theuwissen, D. W. McComb, P. D. Nellist and V. Nicolosi, Science, 2011, 331, 568–571 CrossRef CAS PubMed.
- R. A. Frampton, C. Taylor, A. V. Holguin Moreno, S. B. Visnovsky, N. K. Petty, A. R. Pitman and P. C. Fineran, Appl. Environ. Microbiol., 2014, 80, 2216–2228 CrossRef PubMed.
- K. G. Zhou, N. N. Mao, H. X. Wang, Y. Peng and H. L. Zhang, Angew. Chem., Int. Ed., 2011, 50, 10839–10842 CrossRef CAS PubMed.
- A. S. Aliyev, M. Elrouby and S. F. Cafarova, Mater. Sci. Semicond. Process., 2015, 32, 31–39 CrossRef CAS.
- X. Ping, W. Liu, Y. Wu, G. Xu, F. Chen, G. Li and L. Jiao, Adv. Mater., 2022, 2, 484–494 Search PubMed.
- J. H. Hwang, S. Fahad, H. Ryu, K. L. Rodriguez, J. S. Domingo, A. Kushima and W. H. Lee, J. Power Sources, 2022, 527, 1–11 CrossRef PubMed.
- L. E. Strange, S. Garg, P. Kung, M. Ashaduzzaman, G. Szulczewski and S. Pan, J. Electrochem. Soc., 2022, 169, 574–584 CrossRef.
- J. Jiang, H. Cong, X. Huang, R. Sun, Y. Li, W. Xu, H. Wang and S. Han, Int. J. Hydrogen Energy, 2022, 47, 2947–2957 CrossRef CAS.
- D. G. Li, D. R. Chen and P. Liang, J. Alloys Compd., 2021, 873, 901–911 Search PubMed.
- D. Chen, X. Zhan, T. Liu, Y. Zhao, N. Qi and L. Sun, Opt Laser. Technol., 2021, 140, 809–819 Search PubMed.
- Q. Wang, X. Kong, Y. Yu, H. Han, G. Sang, G. Zhang, Y. Yi and T. Gao, J. Nucl. Mater., 2021, 551, 532–542 CrossRef.
- X. Wang, J. Wang, B. Wei, N. Zhang, J. Xu, H. Miao, L. Liu, C. Su, Y. Li and Z. Wang, J. Mater. Sci. Technol., 2021, 78, 170–175 CrossRef.
- E. P. C. Higgins, A. A. Papaderakis, C. Byrne, A. S. Walton, D. J. Lewis and R. A. W. Dryfe, Electrochim. Acta, 2021, 382, 570–581 CrossRef.
- J. Li, C. Zhang, H. Ma, T. Wang, Z. Guo, Y. Yang, Y. Wang and H. Ma, Chem. Eng. J., 2021, 414, 1265–1275 Search PubMed.
- Y. Du, H. Zhao, W. Wang, X. Jiang, Y. Yang, Y. Liu, S. Li and L. Wang, J. Solid State Chem., 2021, 296, 3045–3055 Search PubMed.
- G. Liu, J. Li, C. Dong, L. Wu, D. Liang, H. Cao and P. Lu, Int. J. Hydrogen Energy, 2021, 46, 18294–18304 CrossRef CAS.
- W. Zhou, L. Dong, L. Tan and Q. Tang, Nanotechnology, 2021, 32, 145718 CrossRef CAS PubMed.
- J. Tang, Y. Chu, K. Wang, B. Deng, Y. Li and X. Tan, ACS Appl. Energy Mater., 2021, 4, 2300–2306 CrossRef CAS.
- N. Ran, B. Sun, W. Qiu, E. Song, T. Chen and J. Liu, J. Phys. Chem. Lett., 2021, 12, 2102–2111 CrossRef CAS PubMed.
- W. Dong, H. Liu, X. Liu, H. Wang, X. Li and L. Tian, Int. J. Hydrogen Energy, 2021, 46, 9360–9370 CrossRef CAS.
- Y. Dai, X. Wang, P. Wang, Y. Sun, R. Han and C. Luo, Int. J. Hydrogen Energy, 2021, 46, 6419–6426 CrossRef CAS.
- Y. Kang, Surf. Sci., 2021, 704, 468–478 CrossRef.
- Y. Li, Z. Yin, M. Cui, X. Liu, J. Xiong, S. Chen and T. Ma, J. Mater. Chem. A, 2021, 9, 2070–2092 RSC.
- S. Bolar, S. Shit, N. C. Murmu, P. Samanta and T. Kuila, ACS Appl. Mater. Interfaces, 2021, 13, 765–780 CrossRef CAS PubMed.
- J. Wu, B. Sun, H. Wang, Y. Li, Y. Zuo, W. Wang, H. Lin, S. Li and L. Wang, J. Mater. Chem. A, 2021, 9, 482–491 RSC.
- M. Wang, R. Song, X. Zhang, G. Liu, S. Xu, Z. Xu, J. Liu and G. Qiao, Int. J. Hydrogen Energy, 2021, 46, 1913–1922 CrossRef CAS.
- J. Lee, J. Heo, H. Y. Lim, J. Seo, Y. Kim, J. Kim, U. Kim, Y. Choi, S. H. Kim, Y. J. Yoon, T. J. Shin, J. Kang, S. K. Kwak, J. Y. Kim and H. Park, ACS Nano, 2020, 14(12), 17114–17124 CrossRef CAS PubMed.
- Y. Du, W. Wang, H. Zhao, Y. Liu, S. Li and L. Wang, J. Mater. Chem. A, 2020, 8, 25165–25172 RSC.
- L. Zeng, X. Li, S. Fan, Z. Yin, J. Mu, M. Qin and A. Chen, J. Power Sources, 2020, 478, 564–578 CrossRef.
- F. Sun, A. Hong, W. Zhou, C. Yuan and W. Zhang, Mater. Today Commun., 2020, 25, 3092–3103 Search PubMed.
- I. Matanovic, K. Leung, S. J. Percival, J. E. Park, P. Lu, P. Atanassov and S. S. Chou, Appl. Mater. Today, 2020, 21, 328–332 Search PubMed.
- Y. Li, S. Zuo, Q. H. Li, X. Wu, J. Zhang, H. Zhang and J. Zhang, Nano Lett., 2021, 21, 1848–1855 CrossRef CAS PubMed.
- X. Wang, Y. Zhang, H. Si, Q. Zhang, J. Wu, L. Gao, X. Wei, Y. Sun, Q. Liao, Z. Zhang, K. Ammarah, L. Gu, Z. Kang and Y. Zhang, J. Am. Chem. Soc., 2020, 142, 4298–4308 CrossRef CAS PubMed.
- S. Park, S. Siahrostami, J. Park, A. H. B. Mostaghimi, T. R. Kim, L. Vallez, T. M. Gill, W. Park, K. E. Goodson, R. Sinclair and X. Zheng, Adv. Mater., 2020, 32, 3020–3031 Search PubMed.
- Z. Zhang, H. Zhu, J. Hao, S. Lu, F. Duan, F. Xu and M. Du, J. Colloid Interface Sci., 2021, 595, 88–97 CrossRef CAS PubMed.
- Q. Wu, A. Dong, C. Yang, L. Ye, L. Zhao and Q. Jiang, Chem. Eng. J., 2021, 413, 3001–3012 CrossRef.
- J. Wu, X. Wang, J. Jiang, W. Lin, S. Zhu, J. Sha, L. Ma and N. Zhao, Mater. Lett., 2021, 292, 309–324 Search PubMed.
- M. Wang, J. Yang, X. You, C. Liao, J. Yan, J. Ruan and S. Dong, J. Mater. Sci. Technol., 2021, 71, 23–30 CrossRef CAS.
- Y. Huang, J. Lv, J. Huang, K. Xu and L. Liu, Nanotechnology, 2021, 32, 5602–5615 Search PubMed.
- H. R. Inta, S. Ghosh, A. Mondal, G. Tudu, H. V. S. R. M. Koppisetti and V. Mahalingam, ACS Appl. Energy Mater., 2021, 4, 2828–2837 CrossRef CAS.
- X. Song, B. Li, W. Peng, C. Wang, K. Li, Y. Zhu and Y. Mei, Nanoscale, 2021, 13, 5892–5900 RSC.
- B. Zhang, K. Xu, X. Fu, S. Guan, X. Li and Z. Peng, J. Alloys Compd., 2021, 856, 3002–3015 Search PubMed.
- B. Zhang, J. Li, Q. Song, X. Xu, W. Hou and H. Liu, Inorg. Chem., 2021, 60, 2604–2613 CrossRef CAS PubMed.
- R. Narasimman, M. Waldiya, K. Jalaja, S. K. Vemuri, I. Mukhopadhyay and A. Ray, Int. J. Hydrogen Energy, 2021, 46, 7759–7771 CrossRef CAS.
- Z. Chen, X. Liu, P. Xin, H. Wang, Y. Wu, C. Gao, Q. He, Y. Jiang, Z. Hu and S. Huang, J. Alloys Compd., 2021, 853, 4651–4663 Search PubMed.
- Q. Wei, Z. Ye, X. Ren, X. Li, M. Yin, L. Zan and F. Fu, J. Alloys Compd., 2020, 835, 5890–5903 CrossRef.
- Y. Mei, T. T. Li, J. Qian, H. Li, M. Wu and Y. Q. Zheng, Chem. Commun., 2020, 56, 13393–13396 RSC.
- Q. He, S. Huang, M. Liu, P. Li, W. Sun and L. Hou, Inorg. Chem. Front., 2020, 7, 2660–2668 RSC.
- H. Huang, J. Song, D. Yu, Y. Hao, Y. Wang and S. Peng, Appl. Surf. Sci., 2020, 525, 4309–4313 Search PubMed.
- A. Tahira, Z. H. Ibupoto, R. Mazzaro, S. You, V. Morandi, M. M. Natile, M. Vagin and A. Vomiero, ACS Appl. Energy Mater., 2019, 2, 2053–2062 CrossRef CAS.
- B. Cao, G. M. Veith, J. C. Neuefeind, R. R. Adzic and P. G. Khalifah, J. Am. Chem. Soc., 2013, 135, 19186–19192 CrossRef CAS PubMed.
- A. Tahira, Z. H. Ibupoto, R. Mazzaro, S. You, V. Morandi, M. M. Natile, M. Vagin and A. Vomiero, ACS Appl. Energy Mater., 2019, 2, 2053–2062 CrossRef CAS.
- Y. Wang, F. Lu, K. Su, N. Zhang, Y. Zhang, M. Wang and X. Wang, Chem. Eng. J., 2020, 399, 5901–5915 Search PubMed.
- M. Yan, Q. Jiang, L. Yang, H. He and H. Huang, ACS Appl. Energy Mater., 2020, 3, 6880–6888 CrossRef CAS.
- A. Wu, Y. Gu, Y. Xie, H. Yan, Y. Jiao, D. Wang and C. Tian, J. Alloys Compd., 2021, 867, 3907–3917 Search PubMed.
- S. Liu, S. Li, K. Sekar, R. Li, Y. Zhu, R. Xing, K. Nakata and A. Fujishima, Int. J. Hydrogen Energy, 2019, 44, 25310–25318 CrossRef CAS.
- Z. Liu, K. Wang, Y. Li, S. Yuan, G. Huang, X. Li and N. Li, Appl. Catal. B Environ., 2022, 300, 4821–4834 CrossRef.
- Q. Xiong, X. Zhang, H. Wang, G. Liu, G. Wang, H. Zhang and H. Zhao, Chem. Commun., 2018, 54, 3859–3862 RSC.
- Y. Zhao, K. Kamiya, K. Hashimoto and S. Nakanishi, J. Am. Chem. Soc., 2015, 137, 110–113 CrossRef CAS PubMed.
- G.-F. Chen, Y. Luo, L.-X. Ding and H. Wang, ACS Catal., 2017, 8, 526–530 CrossRef.
- J. Y. Xue, F. L. Li, Z. Y. Zhao, C. Li, C. Y. Ni, H. W. Gu, D. J. Young and J. P. Lang, Inorg. Chem., 2019, 58, 11202–11209 CrossRef CAS PubMed.
- C. Wang, Int. J. Electrochem. Sci., 2019, 66, 11607–11615 CrossRef.
- T. H. M. Lau, X. Lu, J. Kulhavy, S. Wu, L. Lu, T. S. Wu, R. Kato, J. S. Foord, Y. L. Soo, K. Suenaga and S. C. E. Tsang, Chem. Sci., 2018, 9, 4769–4776 RSC.
- Q. Xiong, Y. Wang, P. F. Liu, L. R. Zheng, G. Wang, H. G. Yang, P. K. Wong, H. Zhang and H. Zhao, Adv. Mater., 2018, 1450–1461, DOI:10.1002/adma.201801450.
- B. Gao, X. Du, Y. Ma, Y. Li, Y. Li, S. Ding, Z. Song and C. Xiao, Appl. Catal. B Environ., 2020, 263, 3769–3779 CrossRef.
- J. Huang, M. Chen, T. Tang, W. Liu and Y. Liu, Electrochim. Acta, 2020, 355, 6751–6764 CrossRef.
- Z. Luo, Y. Ouyang, H. Zhang, M. Xiao, J. Ge, Z. Jiang, J. Wang, D. Tang, X. Cao, C. Liu and W. Xing, Nat. Commun., 2018, 9, 2120–2130 CrossRef PubMed.
- X. Sun, J. Dai, Y. Guo, C. Wu, F. Hu, J. Zhao, X. Zeng and Y. Xie, Nanoscale, 2014, 6, 8359–8367 RSC.
- J. Zhang, X. Xu, L. Yang, D. Cheng and D. Cao, Small Methods, 2019, 3, 932–942 Search PubMed.
- X. Y. Yu, Y. Feng, Y. Jeon, B. Guan, X. W. Lou and U. Paik, Adv. Mater., 2016, 28, 9006–9011 CrossRef CAS PubMed.
- J. Yu, Q. He, G. Yang, W. Zhou, Z. Shao and M. Ni, ACS Catal., 2019, 9, 9973–10011 CrossRef CAS.
- J. Ge, D. Zhang, Y. Qin, T. Dou, M. Jiang, F. Zhang and X. Lei, Appl. Catal. B Environ., 2021, 298, 8012–8024 CrossRef.
- D. Wang, Y. Xie and Z. Wu, Nanotechnology, 2019, 30, 401–413 Search PubMed.
- Y. Deng, Z. Liu, A. Wang, D. Sun, Y. Chen, L. Yang, J. Pang, H. Li, H. Li, H. Liu and W. Zhou, Nano Energy, 2019, 62, 338–347 CrossRef CAS.
- J. Liu, Z. Wang, J. Li, L. Cao, Z. Lu and D. Zhu, Small, 2020, 16, 738–748 Search PubMed.
- T. Wang, X. Zhang, P. Yang and S. P. Jiang, Inorg. Chem. Front., 2020, 7, 3578–3587 RSC.
- J. Tian, N. N. Xia and C. Lin, Int. J. Energy Res., 2021, 45, 8639–8647 CrossRef CAS.
- X. Meng, L. Yu, C. Ma, B. Nan, R. Si, Y. Tu, J. Deng, D. Deng and X. Bao, Nano Energy, 2019, 61, 611–616 CrossRef CAS.
- Z. Wu, X. Guo, Z. Zhang, M. Song, T. Jiao, Y. Zhu, J. Wang and X. Liu, ACS Sustainable Chem. Eng., 2019, 7, 16577–16584 CrossRef CAS.
- Y. Sun, Y. Zang, W. Tian, X. Yu, J. Qi, L. Chen, X. Liu and H. Qiu, Energy Environ. Sci., 2022, 3, 825–836 Search PubMed.
- A. E. Russell, Faraday Discuss., 2008, 140, 9–10 RSC.
- A. Shan, X. Teng, Y. Zhang, P. Zhang, Y. Xu, C. Liu, H. Li, H. Ye and R. Wang, Nano Energy, 2022, 94 Search PubMed.
- J. Zhang, T. Wang, D. Pohl, B. Rellinghaus, R. Dong, S. Liu, X. Zhuang and X. Feng, Angew. Chem., Int. Ed., 2016, 55, 6702–6707 CrossRef CAS PubMed.
- C. Tsai, F. Abild-Pedersen and J. K. Norskov, Nano Lett., 2014, 14, 1381–1387 CrossRef CAS PubMed.
- I. S. Amiinu, Z. Pu, X. Liu, K. A. Owusu, H. G. R. Monestel, F. O. Boakye, H. Zhang and S. Mu, Adv. Funct. Mater., 2017, 27, 553–564 CrossRef.
- G. Zhang, H. Liu, J. Qu and J. Li, Energy Environ. Sci., 2016, 9, 1190–1209 RSC.
|
This journal is © The Royal Society of Chemistry 2022 |
Click here to see how this site uses Cookies. View our privacy policy here.