DOI:
10.1039/D2RA02071H
(Paper)
RSC Adv., 2022,
12, 17689-17700
Decolorization of dark-colored waste cotton fabric using redox decoloring agents†
Received
30th March 2022
, Accepted 3rd May 2022
First published on 15th June 2022
Abstract
A huge quantity of dark-colored waste cotton fabrics with a high content of dye powder is dumped in landfills and incinerated, which is a waste of resources and pollutes the land and atmosphere. Also, it is meaningful to effectively strip the color from these dark-colored waste cotton fabrics with minimal damage to the strength of the textiles. In this study, a dark-colored waste cotton fabric dyed with reactive dyes was subjected to chemical treatment with redox decoloring agents. The effects of various treatments on the coloration and mechanical properties of the fabric were compared. This work developed an effective Na2S2O4–H2O2 system for decolorizing waste cotton fabric, with numerous advantages over conventional physicochemical approaches including achieving a CIE whiteness index of 74.1, tensile strength loss of 24.0%, weight loss of 1.2%, decoloration rate of 97.8%, and a degree of polymerization of 735.3. Furthermore, a mechanism was proposed to explain the two-step synergistic decolorization process.
1. Introduction
The growth of the global population, elevated standards of living in many parts of the world, and fast fashion have led to both an increase in demand for textiles and a large accumulation of related surplus/wastes.1–3 The average lifetime of a garment is roughly three years, which generates a huge amount of waste.4,5 Specifically, 40 million tons of waste textiles are produced worldwide each year.6 The huge quantity of waste textiles that cannot be utilized as used garments is dumped in landfills and incinerated, which is a waste of resources and produces environmental pollution.7
Recycling is the preferred economic and environmental approach to dispose of these waste textiles.8 White or light-colored waste fabrics may be reused via a physical approach such as making mops and curtains. In contrast, dark-colored waste textiles with dye powder tend to be landfilled and incinerated for the generation of electricity. However, this treatment approach will eventually contribute to environmental pollution because the dye powder from dark-colored waste textiles seeps into land or flows into rivers during the degrading process of the textiles or in the incineration process, harmful gases are released. Also, dark-colored waste textiles seriously restrict the recycling of waste textiles. Hence, the development of appropriate decolorization approaches is necessary for improving the utilization of dark-colored waste textiles.
Cotton is the most common material used for textiles, and more than 50% of cotton textiles are dyed with reactive dyes.9,10 Importantly, reactive dyes have excellent colorfastness because they bond covalently with the active hydroxyl groups of the cellulose molecules in cotton fibers.11 Thus, reductants and oxidant undergo reduction or oxidation reactions on dyed fibers are generally used as decoloring agents to achieve the decolorization of colored textiles. Specifically, reductants such as sodium hydrosulfite and sodium formaldehyde sulfoxylate can reduce pigment molecules, destroying the double bond in the chromophore groups of dyes for decolorization. Chen used thiourea dioxide as a reducing agent to decolorize cotton fabrics dyed with reactive dyes. Compared with the traditional hydrosulfite decolorization process, the decolorization rate of the waste textiles improved, but their strength was also greatly reduced.12 Our group used sodium dithionite to fade waste textiles dyed with vat dyes, and the results showed that the peeling rate of sodium dithionite was higher than that of sodium hypochlorite.13 Reductants are also promising for decolorizing cotton fabrics while causing low material degradation.14–16 Unfortunately, the whiteness of the reduced fabric is not stable and it is easily oxidized and recolored by air after exposure to air for a long time.
Oxidants are used as bleaching agents in the bleaching process such as sodium hypochlorite and hydrogen peroxide. Hydrogen peroxide is an economically and environmentally friendly oxidant, which is often used as a bleaching agent to decolorize the impurities that mask the natural whiteness of fibers in preparation for the dyeing and printing process.17–20 In the traditional H2O2 bleaching process, harsh processing conditions such as the high temperature of 90 °C and high concentration of alkali can lead to extensive water and energy consumption and serious chemical damage to the textiles.21–24 As effective alternatives, low-temperature and low-alkali decolorizing methods have been proposed for decolorizing cotton.25,26 Zhang employed sodium hypochlorite and hydrogen peroxide to decolorize waste textiles, and then added 1 mol L−1 NaOH aqueous solution to adjust the pH of the decolorization bath to 10, indicating that alkaline conditions result in less damage to textiles.27 Zhang decolorized cotton fibers by alkali treatment via a two-bath method and one-bath method, respectively, and studied the effect of decolorization on the structure and properties of raw cotton and recycled cotton.28 Abdel-Halim bleached cotton fabric without severe loss in its mechanical properties using a sodium chloride/potassium permanganate bleaching system.29 Bigambo studied the reliability of a sequential acid/dithionite/peroxide treatment to strip reactive dyes from cotton.30 However, these methods did not completely remove the color, while cellulose treated with oxidation was also subject to depolymerization under alkaline conditions, and thus oxidative damage decreased the strength and changed other physical properties of the fibers.31,32
Simultaneously, due to the extensive decolorization process, dyes accumulate in industrialized waste, which are dangerous to the environment and human health. Numerous methods are used for wastewater management, allowing dyes in wastewater to be effectively degraded.33,34 Therefore, a crucial issue still to be resolved is how to effectively strip reactive dyes from cotton fabric, while minimizing unwanted effects on the cotton fibers and reducing the environmental impact.
In this study, we combined oxidants and reducing agents as decolorizing agents to treat post-consumer dark-colored waste cotton fabric dyed with vinyl sulfone reactive dyes. Na2S2O4, H2O2, KMnO4, and Na2S2O4–H2O2 were used as decolorizing agents, and their oxidation (reduction) effects on the stripping of color, strength, and degree of polymerization (DP) of the fabric were analyzed. The decolorizing mechanism was studied via scanning electron microscopy (SEM), X-ray diffraction (XRD), Fourier transform infrared (FT-IR) spectroscopy, and X-ray photoelectron spectroscopy (XPS). The optimum decolorizing process was identified based on the absorption coefficient/scattering coefficient ratio (K/S), CIE whiteness index, tensile strength, and fabric weight loss after treatment. This work developed a two-step decolorization method (Na2S2O4–H2O2) that efficiently removed dyes from fabrics with low physical damage to the fabrics. Compared with traditional decolorization methods, our proposed method has a short processing time and low environmental pollution, and the decolorized fabrics do not return to their original color in the air.
2. Experimental
2.1 Materials
Waste cotton fabric colored dark blue with vinyl sulfone reactive dyes (50 mm × 300 mm, weight: 120 g m−2, woven fabric) was obtained from a local market in China and the dye type was verified by the manufacturer. Hydrogen peroxide (H2O2, 30%), potassium permanganate (KMnO4, AR), sodium hydrosulphite (Na2S2O4, 85%), oxalic acid (H2C2O4, AR), sodium hydroxide (NaOH, 96%), sulfuric acid (H2SO4, 98%) and N,N,N′,N′-tetraacetylethylenediamine (TAED, 92%) were obtained from Sinopharm Chemical Reagent Co., Ltd. All reagents were of analytical grade and used without further purification.
2.2 Methods
The dark-colored waste cotton fabric was pre-cleaned to remove dirt, soluble soil, and finishing agents, and then dried for a later decolorization process. The four decoloring formulations are shown in Table 1. The decoloring formulations were prepared at room temperature and the bath ratio was 1
:
30 in all cases. Owf% is based on the weight of the fabric.
Table 1 Decoloring formulations: (A) Na2S2O4, (B) H2O2, (C) KMnO4, and (D) Na2S2O4–H2O2
Decoloring formulation A |
Decoloring formulation B |
Na2S2O4 |
25 g L−1 |
H2O2 |
40 g L−1 |
Temperature |
90 °C |
NaOH |
20 g L−1 |
pH |
9 |
TAED |
10 g L−1 |
|
|
Temperature |
70 °C |
|
|
pH |
10 |
Decoloring formulation C |
Decoloring formulation D |
Step 1 |
Step 1 |
KMnO4 |
5 owf% |
Na2S2O4 |
30 g L−1 |
H2SO4 |
5 owf% |
Temperature |
90 °C |
Temperature |
40 °C |
pH |
9 |
pH |
5 |
|
|
Step 2 |
Step 2 |
H2C2O4 |
8 g L−1 |
H2O2 |
40 g L−1 |
H2SO4 |
5 owf% |
NaOH |
20 g L−1 |
Temperature |
40 °C |
TAED |
10 g L−1 |
|
|
Temperature |
70 °C |
|
|
pH |
10 |
The dark-colored waste cotton fabric was pre-cleaned to remove soluble soil and dirt, and then dried for a later decolorization process. The decolorization process was carried out in a 100 mL Erlenmeyer flask, which was placed in a reciprocating shaker and heated for the designed treatment duration. During treatment, the fabric sample was immersed in the decoloring solution. Then, the sample was rinsed in hot and cold water until pH was 7 and finally dried at room temperature.
Decoloring formulations A and B each contained a single treatment step, while C and D contained two steps (formulation C followed by oxalic acid (H2C2O4), and formulation D followed by H2O2, respectively). The details of formulation D are depicted in Fig. 1. The waste cotton fabric was weighed and immersed in a decolorization bath containing 25 g L−1 Na2S2O4, and shaken vigorously at 90 °C. Six samples were prepared the same way, and one sample was withdrawn every 7.5 min. Immediately after washing to neutrality, the sample was placed in a two-stage decolorization bath composed of 40 g L−1 H2O2, 20 g L−1 NaOH, and 10 g L−1 TAED, and shaken vigorously at 70 °C. A sample was taken out every 7.5 min, first washed with hot water at 60 °C, then washed with cold water until neutral, and finally dried at 25 °C for 24 h to observe the decolorization effect. In the four decolorization processes, the decolorization time increased proportionally from 0–90 min.
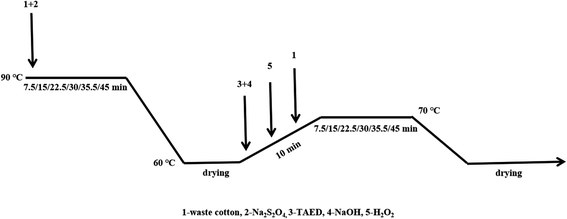 |
| Fig. 1 Diagram of the decolorization process for decoloring formulation D (Na2S2O4–H2O2). | |
2.3 Measurements
2.3.1 Surface analysis. The K/S values of the fabric sample before and after decolorization were measured using an X-ray Rite 8400 computer color matching instrument based on the λmax value. Each sample was folded twice to achieve opacity. The dye stripping percentage was calculated using the following equation: |
 | (1) |
The CIE whiteness index was measured on a WSB-V Intelligent digital whiteness meter according to the AATCC 110-2005 standard. Each sample was measured at four different positions, and the values were averaged for three identically treated samples.
The surface morphology was studied using SEM (Tescan Vega3 – SBU) at 20.00 kV after sputtering the samples with gold particles for 1 min.
2.3.2 Mechanical properties. The tensile strength of the fabric samples was determined on an HD026PC-500 multifunctional electronic fabric strength tester according to the ASTM D 5035-1995 strip test (ASTM test method). The fabric weight loss was calculated using the following formula: |
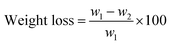 | (2) |
where w1 and w2 are the dry weights before and after decoloring treatment, respectively.
2.3.3 Chemical properties. The degree of polymerization (DP) of fabrics is an excellent factor to assess the molecular weight of the cotton fabric. Copper ethylene diamine solution was used to test the DP of cotton fabric according to the ISO 5351:2010. The fabric sample and 0.2 g copper ethylene diamine solution were added to a bottle and mixed with a shaker until complete dissolution. The time required to pass the diluted solution and pulp solution at a specified concentration through a capillary viscometer at 25 °C was recorded, which gives the corresponding viscosity ratio. Therefore, it was obtained in this study from the calculated limiting viscosity using the equations reported by Marx-Figini.35XRD measurement was carried out on a diffractometer (D8-Advance, Bruker) at the scan speed of 5° min−1 in the 2θ range of 10° to 80°. The crystallinity χC (%) of the cellulose fibers was calculated and estimated according to eqn (3),36 as follows:
|
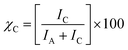 | (3) |
where
IC and
IA are the integrated intensities of the crystalline and amorphous phases, respectively.
For FT-IR measurement, the dried sample was analyzed using a Nicolet iS50 FT-IR spectrometer in the attenuated total reflection mode. The scanning range was from 400 to 4000 cm−1 with a resolution of 4 cm−1. XPS (Kratos Co.) was employed to study the vinyl sulfone dye before and after reduction under the conditions of 12 kV and 15 mA using Al Kα radiation (1486.6 eV).
3. Results and discussion
3.1 Effects of different decolorization agents
Four decolorizing processes using various oxidants and reducing agents were compared for decolorizing dark-colored waste cotton fabric with vinyl sulfone blue reactive dye. The CIE whiteness index, decolorization rate, tensile strength, and DP were compared.
3.1.1 Effect of reducing agent – Na2S2O4. Fig. 2 shows the effect of the Na2S2O4 decolorization treatment on the waste cotton fabrics at different decoloring durations from 0 to 90 min. As shown in Fig. 2a, when Na2S2O4 was used to decolorize the dark-colored waste cotton fabric, the whiteness of the waste textile decreased to 11.4 compared to that of the original sample of 33.8 in the first 15 min. Subsequently, the whiteness of waste textile increased from 11.4 to 21.2 with an increase in the decolorization duration from 15 to 90 min. As shown in Fig. 2b, the decoloration rate of the waste textile increased continuously with an increase in the decolorization duration, which was up to 90.9% after 90 min of decolorization. Moreover, the decolorized fabric was unstable. As shown in Fig. 2c, the treated samples exhibited a darker blue appearance after one week of storage at room temperature. This may be because Na2S2O4 quickly attached to the dye and reduced it to maroon without separating the dye from the cellulose macromolecules. The possible reason for this is that the reduced dye is unstable in the air and is easily oxidized by oxygen to restore its original color. As shown in Fig. 2d and e, the tensile strength and DP value of the fabric both decreased noticeably in the first 45 min, and then changed slightly afterward, respectively. Following 90 min treatment, the tensile strength decreased from 479.1 to 387.4 N. The Na2S2O4 treatment only slightly weakened the cotton fabric, which is consistent with previous reports.16
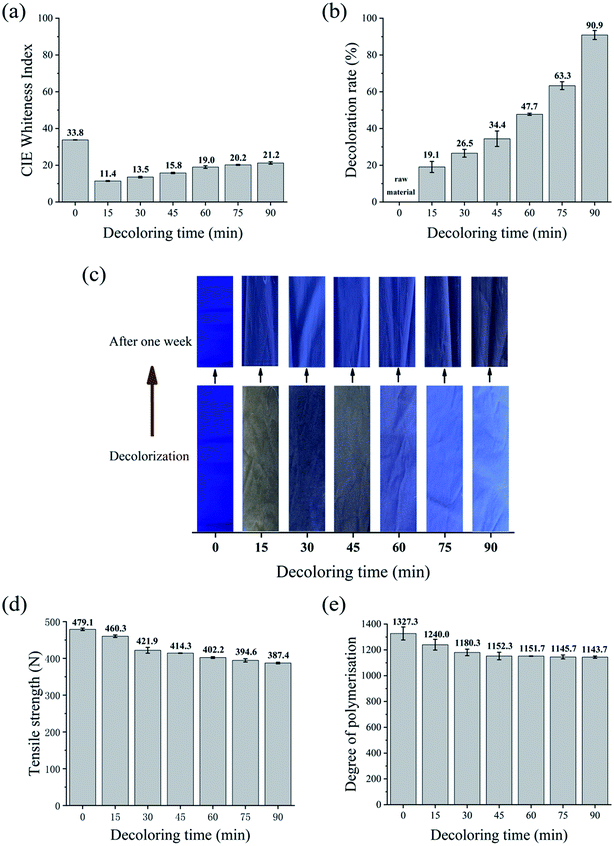 |
| Fig. 2 Effects of the decoloring duration of Na2S2O4 on cotton fabric: (a) CIE whiteness index, (b) decoloration rate, (c) digital photographs of fabric samples, (d) tensile strength, and (e) degree of polymerization. | |
3.1.2 Effect of oxidizing agent – H2O2. Fig. 3 shows the effect of the H2O2 decolorization treatment on the waste cotton fabrics at different decoloring durations from 0 to 90 min. As shown in Fig. 3a, the whiteness of the waste cotton fabrics increased from 33.8 to 65.9 when the decolorization duration with H2O2 increased from 0 to 90 min. As shown in Fig. 3b, the decoloration rate of the waste cotton fabrics sharply rose to 86.8% after 30 min of decolorization, and then the increasing trend slowly reached 96.4% when the treatment duration was 90 min. The photographs of the waste cotton fabrics without and with H2O2 decolorization, as shown in Fig. 3c, demonstrated that some residual pigment remained in the textile after 90 min, while the decolorized fabric still had a reddish color.
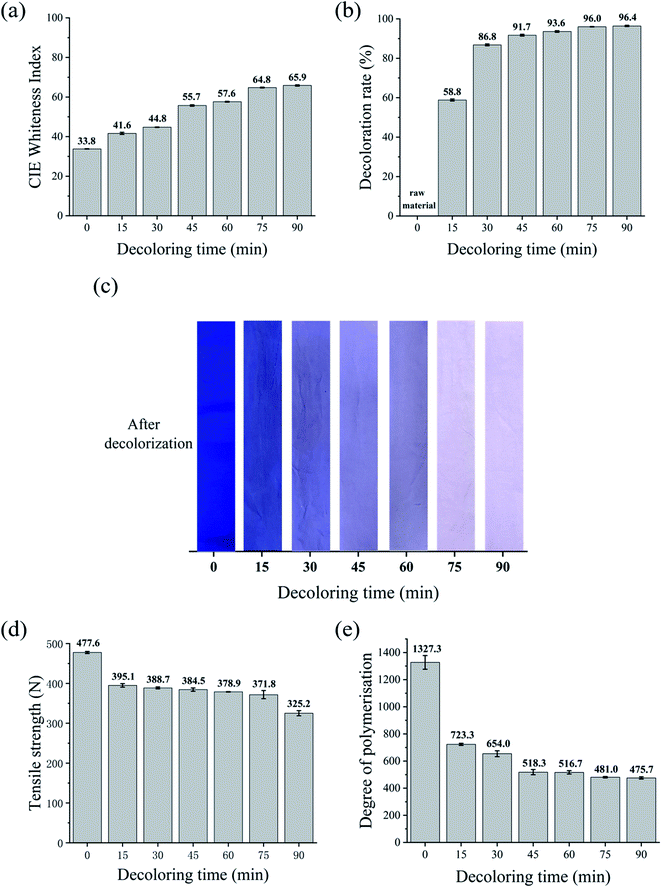 |
| Fig. 3 Effects of H2O2 treatment for different times on dyed cotton fabric: (a) CIE whiteness index, (b) decoloration rate, (c) digital photographs of fabric samples, (d) tensile strength, and (e) degree of polymerization. | |
Nevertheless, Fig. 3d reveals that the tensile strength of the waste cotton fabrics with H2O2 decolorization was 325.2 N with 90 min of decolorization, which was approximately reduced by 31%. Besides, the DP of the waste cotton fabrics decreased from 1327.3 to 723.3 when they were treated with H2O2 in the first 15 min, as shown in Fig. 3e. With an increase in the decolorization duration, the DP of the waste cotton fabrics decreased to 479.5, and subsequently the lowest DP was achieved.20,37 These phenomena can be explained by the fact that H2O2 can penetrate the crystalline regions in the fibers and change the crystal lattice to some extent.18 Consequently, some crystalline regions became amorphous, leading to a decrease in the fabric strength and DP.17
3.1.3 Effect of oxidizing agent – KMnO4. Fig. 4 shows the effect of KMnO4 decolorization treatment on the waste cotton fabrics at different decoloring durations from 0 to 90 min. As shown in Fig. 4a, the CIE whiteness index of the waste cotton fabrics significantly increased from 33.8 to 79.2 with an increase in the decolorization time from 0 to 90 min. As shown in Fig. 4b, the decoloration rate of the waste cotton fabric reached 90.8% in the first decoloration of 15 min, which finally reached 99.4% when the decoloration duration was 90 min. As shown in Fig. 4c, the surface of the waste cotton fabrics treated with KMnO4 presented a pastel creamy color, which was more pastel than that of the textiles treated with H2O2 and Na2S2O4. When the decolorization time was more than 45 min, the residual dyes on the fabric were almost removed. However, the whiteness could not be improved by further KMnO4 treatment, which is similar to that shown in Fig. 4a and b. Meanwhile, the waste cotton fabric treated with KMnO4 suffered from a major decrease in tensile strength and DP, which reached 50% and 55%, as shown in Fig. 4d and e respectively. Most of these changes occurred within the first 15 min of treatment due to the rapid initial reaction rate of KMnO4. Overall, decolorization by KMnO4 was fast and efficient but caused extensive fiber damage.
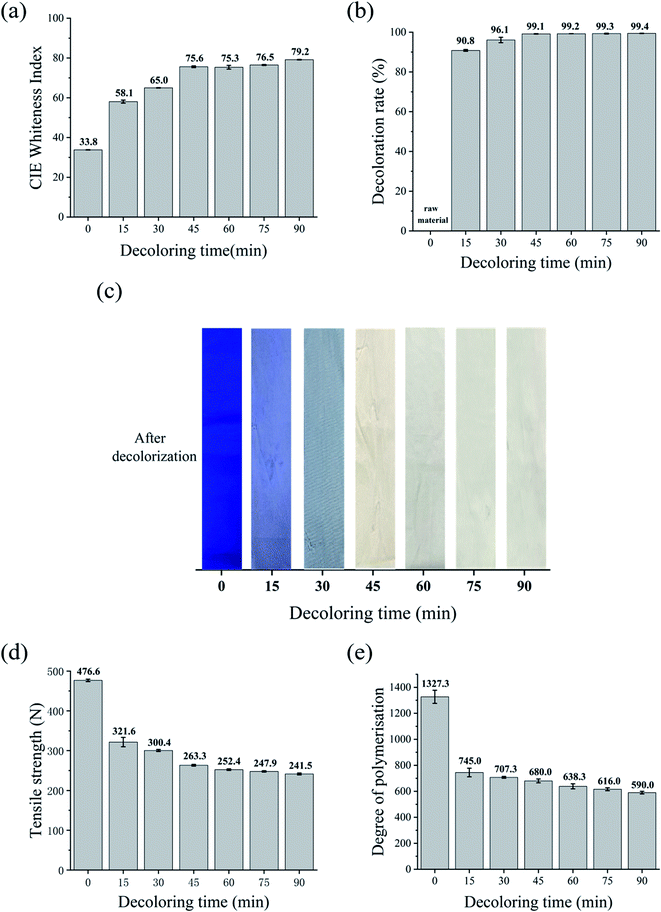 |
| Fig. 4 Effects of KMnO4 treatment for different times on dyed cotton fabric: (a) CIE whiteness index, (b) decoloration rate, (c) digital photographs of fabric samples, (d) tensile strength, and (e) degree of polymerization. | |
3.1.4 Two-step decolorization method Na2S2O4–H2O2. A two-step decolorization method combined with a reduction–oxidation decolorization system (Na2S2O4–H2O2) was used to treat the waste cotton fabric. The corresponding effects are shown in Fig. 5. As shown in Fig. 5a, the whiteness of the waste cotton fabric decreased to 74.1 after 90 min of decoloration treatment. As shown in Fig. 5b, the decolorization rate of the waste cotton fabrics reached 79.1% in the first 15 min, and then 97.8% when the decoloring time was 90 min. According to Fig. 5c, compared to the case of Na2S2O4, in the reaction with Na2S2O4–H2O2, the decolorization effect showed a dramatic increase. More importantly, there was no recovery of color, which was appropriate for the decolorized waste cotton.
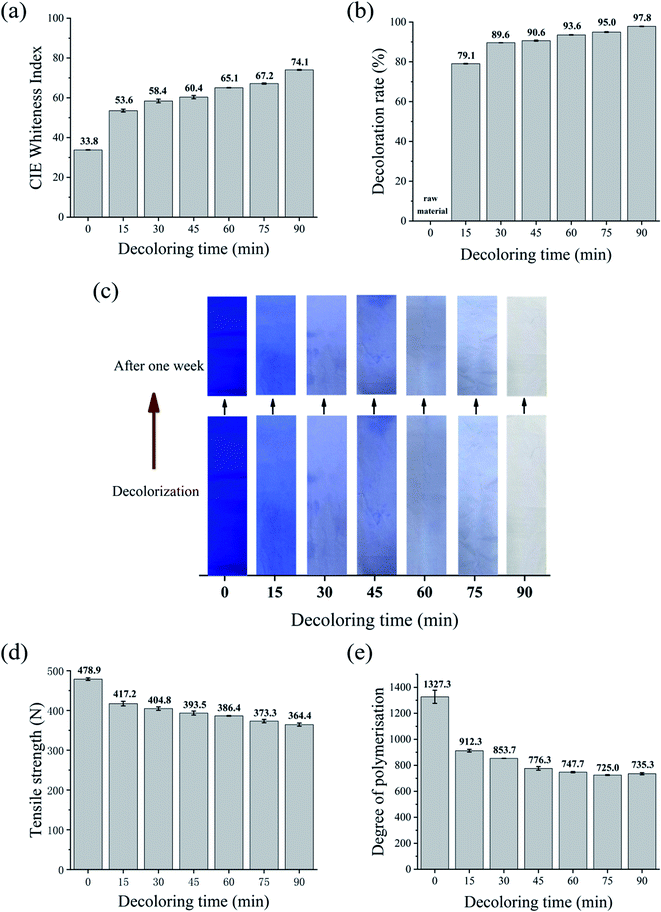 |
| Fig. 5 Effects of Na2S2O4–H2O2 treatment for different times on dyed cotton fabric: (a) CIE whiteness index, (b) decolorization rate, (c) digital photographs of fabric samples, (d) tensile strength, and (e) degree of polymerization. | |
Similarly, the relationship between the decolorization time and tensile strength is illustrated in Fig. 5d. Most of the strength loss already occurred within the first 15 min, and the tensile strength of the cotton fabric only decreased gently with prolonged treatment by 24% after 90 min. The strength retention rate of the fabric was higher when the decolorization time was 30 min. Meanwhile, the strength loss was only 15.5%. As shown in Fig. 5e, the DP value also declined from 1327.3 to 735.3 when the decolorization time increased to 90 min. Na2S2O4 is a reducing agent,38 and therefore its addition may mitigate the severe damage to the fiber from the subsequent oxidant treatment. This was due to the reduction reaction between Na2S2O4 and the chromophore in the attached dye molecules.38,39
In the subsequent step, H2O2 broke the covalent bond formed between the dye and the fiber for complete decolorization. Moreover, the reduction reaction promoted by Na2S2O4 was reversible. In this case, the added H2O2 broke the covalent bond between the dye and fiber, and the dye dissolved in the decolorizing bath without the chance to recolor the fabric. These results indicate that the Na2S2O4–H2O2 system adequately decolorized the dyed cotton fabric, while retaining its tensile strength and (to a lesser degree) polymer structure.
3.2 Comparison of different decolorization processes
To compare the decolorization effect of the four formulations more directly, the CIE whiteness index, tensile strength, decoloration rate, and DP value of the waste cotton fabrics treated using the different processes for 90 min are shown in Table 2. Information about the untreated fabric is also included as a reference.
Table 2 CIE whiteness index, tensile strength, decoloration rate, DP, and photographs after using four different processes to decolorize cotton fabric with reactive dye
Fabric |
CIE whiteness |
Tensile strength (N) |
Decoloration rate (%) |
DP |
Weight loss (%) |
Photograph |
Untreated cotton |
33.8 ± 0.2 |
478.9 ± 3.0 |
0 |
1327.3 ± 50 |
0 |
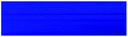 |
Na2S2O4 treated |
21.2 ± 0.4 |
387.4 ± 2.6 |
90.9 ± 1.2 |
1143.7 ± 21 |
0.9 ± 0.1 |
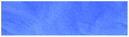 |
H2O2 treated |
65.9 ± 0.3 |
325.2 ± 3.2 |
96.4 ± 0.2 |
475.7 ± 20 |
2.0 ± 0.5 |
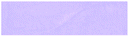 |
KMnO4 treated |
79.2 ± 0.3 |
241.5 ± 1.2 |
99.4 ± 0.1 |
590.0 ± 17 |
5.7 ± 1.1 |
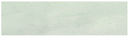 |
Na2S2O4–H2O2 |
74.1 ± 0.6 |
364.4 ± 4.0 |
97.8 ± 0.2 |
735.3 ± 10 |
1.2 ± 0.4 |
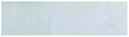 |
In terms of whiteness, the results followed the order of KMnO4 > Na2S2O4–H2O2 > H2O2 > Na2S2O4. The tensile strength followed the order of Na2S2O4 > Na2S2O4–H2O2 > H2O2 > KMnO4. KMnO4 achieved a high decolorization efficiency and satisfactory whiteness in a very short time, while Na2S2O4 had the lowest decoloration rate of 34.4%. The DP values of the treated fabrics followed the order of Na2S2O4 (1143) > Na2S2O4–H2O2 (735) > KMnO4 (590) > H2O2 (475). The combination of Na2S2O4 and H2O2 resulted in a reasonably white fabric (74.1) without major loss in tensile strength. When we considered the decolorizing effect, whiteness, and environmental impact, the Na2S2O4–H2O2 system emerged as the best choice for treating dyed cotton fabrics.
3.3 Surface and structure properties
Fig. 6 displays the scanning electron microscopy images of waste cotton textiles after various decolorization treatments. The sample treated with Na2S2O4 had a cleaner and smoother surface, which is probably due to the change in the dye chromophore attached to the surface of the cotton fibers and the removal of the finishing auxiliaries on the fiber (Fig. 6a). Na2S2O4 is a reducing agent that acts on the conjugated double bonds of the dye chromophore instead of the covalent bonds with cellulose. This explains the minimum fiber damage after Na2S2O4 treatment. Because the H2O2 treatment was carried out under relatively harsh conditions (high temperature and concentrated alkali), NaOH residue and easily broken fibers can be seen in Fig. 6b.40 According to Fig. 6d, the fabric decolorized by Na2S2O4–H2O2 had a smooth surface, fewer impurities, and tough fibers. These morphological changes discussed above are consistent with the measured mechanical properties. Again, Na2S2O4–H2O2 appears to be the best compromise between efficient decolorization and maintaining fabric integrity.
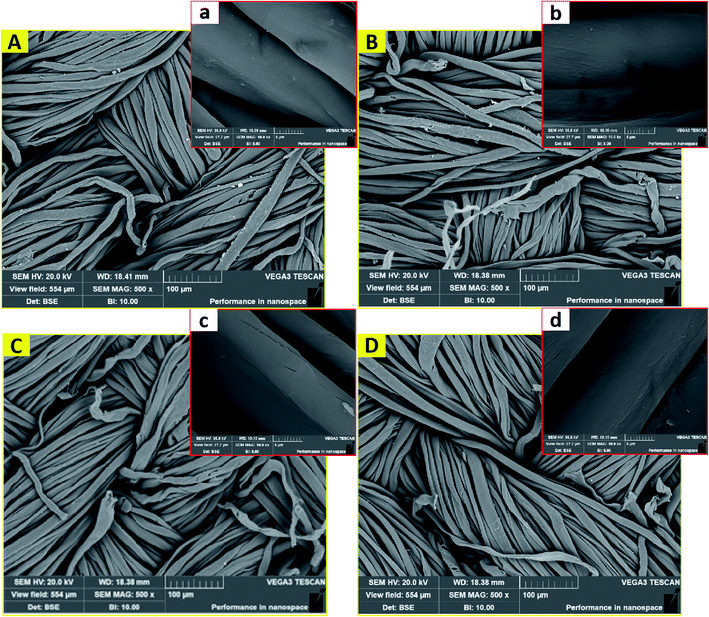 |
| Fig. 6 SEM images of fabric samples after decolorization treatment using (A) Na2S2O4, (B) H2O2, (C) KMnO4, and (D) Na2S2O4–H2O2. | |
The XRD patterns of the fabric samples subjected to the four decolorization processes are shown in Fig. 7, together with that of the untreated fabric. The samples displayed five peaks at 2θ = 14.7°, 16.4°, 20.5°, 22.7°, and 34.7°, which are assigned to the (1−10), (110), (012/102), (200) and (004) planes of cellulose I, respectively.41–44 For all the materials, the conventional 10–80° 2θ range, two-point background, and five crystalline peaks were used to fit their crystalline peaks. In this study, we subtracted the environmental background first, and then added a 2-point correction for inelastic scattering. Furthermore, according to the XRD calculations, the total crystallinity of the four treated fabrics was higher than that of the raw material. It is clear from Fig. 7 that the crystallinity of the cotton fabric samples treated with H2O2 (80.2%) is higher than that treated with Na2S2O4 (66.7%), KMnO4 (66.1%), and Na2S2O4–H2O2 (65.7%), and also higher than the crystallinity of raw cotton (62.8%). After the decolorization treatment, the position of the sharp peak did not change, which proves that the crystal structure did not change. The removal of non-cellulosic materials such as auxiliaries and dyes increased the degree of crystallinity.45 In contrast, the crystallinity and orientation of the cellulose increased slightly after treatment with Na2S2O4–H2O2, proving that this combination of oxidizer/reducing agent effectively minimizes damage to the fabric.
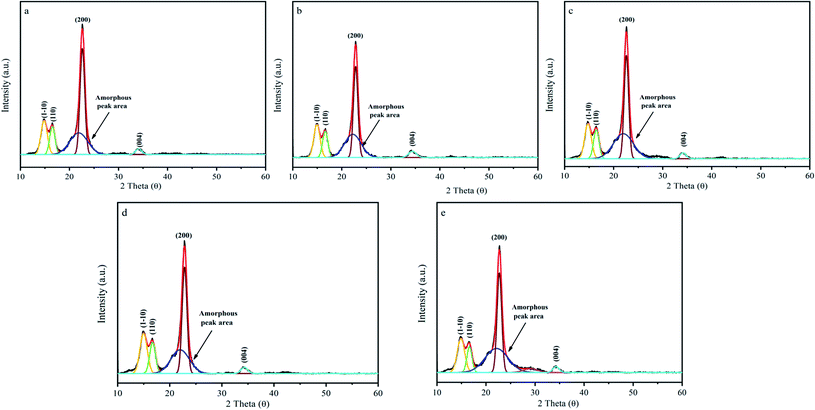 |
| Fig. 7 XRD pattern of original cotton fiber (a), treated with Na2S2O4 (b), treated with H2O2 (c), treated with KMnO4 (d), and treated with Na2S2O4–H2O2 (e). | |
Fig. 8 compares the FT-IR spectra of the fabric samples decolorized using the four processes. The different treatments produced almost no change in the absorption peak positions. The combined characteristic broad peak of the –OH and –NH2 groups was observed at around 3400–3500 cm−1.46 The absorption peak at 1403 cm−1 is assigned to the CH bending vibration on the benzene ring. The strong absorption peak at 1632 cm−1 is attributed to the C
O stretching vibration on the anthraquinone ring.47,48 The benzene and naphthalene ring structures (1632 cm−1) in the dye molecules were not destroyed. Nevertheless, the peak intensities were greatly reduced after the decolorization treatments, indicating the partial destruction of the anthraquinone structure. The FT-IR peak intensities after treatments may have been caused by the residual dyes on the fabric. Thus, subsequently, we further explored whether Na2S2O4 destroyed the chromophore in the dye or not.
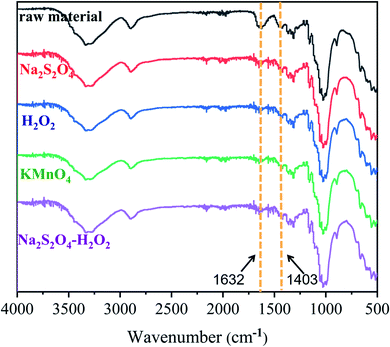 |
| Fig. 8 FT-IR spectra of the fabric samples before and after decolorization using four processes: Na2S2O4, H2O2, KMnO4, and Na2S2O4–H2O2. | |
3.4 Decolorization mechanism
To study the decolorization mechanism in the dark-colored waste cotton fabrics treated with reducing and oxidizing agents, in this study, we performed XPS measurements before and after fabric decolorization (shown in Fig. 9a and b, respectively). To further confirm whether the C
O conjugated color system in the anthraquinone structure was destroyed during the treatment and any possible changes in the macromolecular structure of the dye, the raw dye and a sample of the dye after Na2S2O4 treatment and purification (reactive blue KN-R) were tested by XPS. Fig. 10 reveals the presence of C and O elements in the fabric both before and after decolorization. In the sample before decolorization, the O 1s signal was deconvoluted into three characteristic peaks of C–O (531.92 eV), –SO3Na (533.25 eV), and C
O (536.4 eV), all of which were derived from the dye color system. After decolorization, the O 1s signal could also be deconvoluted into three peaks of C–O (531.71 eV), –SO3Na (533.04 eV), and C
O (536.13 eV).49,50 After decolorization, the content of C–O increased from 87.24 to 88.43 wt%, and that of C
O decreased from 12.76 to 11.57 wt%. In the dyed fabric, the anthraquinone structure in reactive blue KN-R had a higher decoloration rate during our proposed treatment, because Na2S2O4 reduced C
O in the dye color system to C–O, and then the oxidant (H2O2) destroyed the covalent bonding of the dye molecule to the fiber to allow its removal from the fabric.
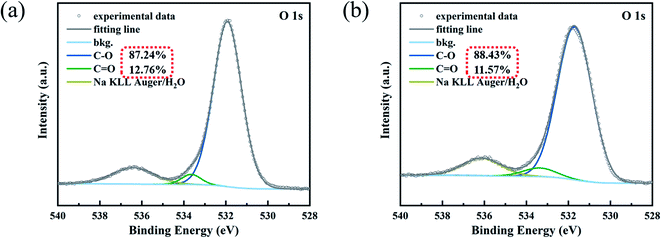 |
| Fig. 9 XPS spectra of the raw dye (a) and the dye after Na2S2O4 treatment (b). | |
Finally, we proposed a synergistic decolorization mechanism for Na2S2O4 and H2O2, which is shown in Fig. 10. In step 1, the waste cotton fabrics dyed with vinyl sulfone dyes were first subjected to pretreatment steps such as washing and crushing. During step 2, the hydrolysis of S2O42− generated a large amount of hydrogen atoms, and S3+ in S2O42− was oxidized to S4+. The HSO3− and SO32− generated in this reaction act on the cyclic conjugated double structure of the dye, and the reducibility was mainly used to improve the whiteness of the fabric. Decolorization mainly occurred through the reduction reaction with Na2S2O4, which destroyed the conjugated double bond in the dye molecule. In step 3, alkali helped degrade H2O2 to form the hydroxyl anion,37 which reacted with activator TAED to form peracetic acid (a stronger decolorizing chemical). Although H2O2 alone could produce a certain level of whiteness in the fabric, the treatment cost increased rapidly.51 Then, the strongly oxidizing properties of peracetic acid destroyed the covalent bonds between the dye and cotton fibers.
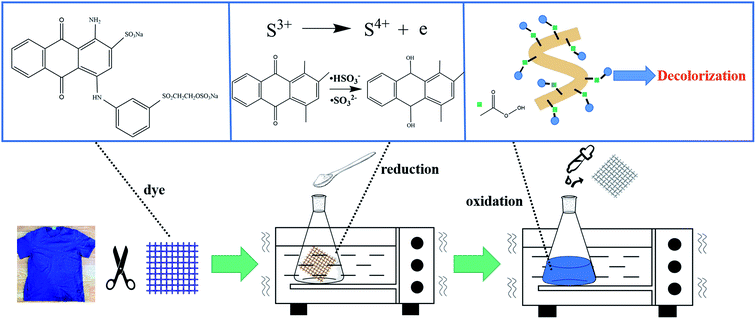 |
| Fig. 10 Proposed synergistic decolorization mechanism of Na2S2O4 and H2O2. | |
Our experiments showed that Na2S2O4 as a reductive decolorant was complementary to the oxidative decolorant H2O2, and their synergistic effects were conducive to decolorization. Compared with the use of Na2S2O4 alone, the two-stage treatment resulted in better decolorization of the blue cotton fabric with less loss in fabric strength. Most importantly, this decolorization method did not generate carcinogenic substances such as organic chloride produced during sodium hypochlorite bleaching. The treated fabric retained its whiteness for at least one week, in contrast to the recolorisation observed when using Na2S2O4 alone.
4. Conclusions
To facilitate the reuse and recycling of waste fabrics, this study compared different systems for decolorizing dark-colored waste cotton fabric with reactive dyes. The reducing agent Na2S2O4 effectively retained the mechanical strength of the fabric, but its whiteness was not ideal. Conversely, the oxidizing agents KMnO4 and H2O2 efficiently and rapidly stripped the dye from the fabric, while also causing reductions in the tensile strength and degree of polymerization. The optimum Na2S2O4–H2O2 two-step decolorizing process could achieve a CIE whiteness index of 74.1, low tensile strength loss of 24.0%, weight loss of 1.2%, decoloration rate of 97.8%, and degree of polymerization of 735.3. In the proposed mechanism of synergistic decolorization by Na2S2O4–H2O2, the chromophore in the dye was rapidly reduced by Na2S2O4, and then the covalent bonding between the dye molecule and the cotton fiber was cleaved by H2O2. In this work, a facile approach for removing reactive dyes from colored waste cotton with Na2S2O4–H2O2 was demonstrated. This method provided a simple and efficient process for treating colored waste cotton, which is suitable for the physical recovery of waste cotton fabrics and can be recycled for secondary processing.
Conflicts of interest
There are no conflicts to declare.
Acknowledgements
This work was financially supported by the National Natural Science Foundation of China (Grant No. 52005275); State Key Laboratory of Bio-Fibers and Eco-Textiles (Qingdao University), No. ZKT43.
References
- L. Barnes, L. Barnes and G. Lea-Greenwood, J. Fash. Mark. Manag., 2006, 10, 259–271 Search PubMed.
- M. Määttänen, M. Gunnarsson, H. Wedin, S. Stibing, C. Olsson, T. Köhnke, S. Asikainen, M. Vehviläinen and A. Harlin, Cellulose, 2021, 28, 3869–3886 CrossRef.
- L. Ding, Y. Jiang, B. Wang, Y. Li, Z. Mao, H. Xu, Y. Zhong, L. Zhang and X. Sui, Cellulose, 2018, 25, 7369–7379 CrossRef CAS.
- U. Ratanakamnuan, D. Atong and D. Aht-Ong, Carbohydr. Polym., 2012, 87, 84–94 CrossRef CAS PubMed.
- M. Wang, S. Shi, J. Dai, H. Guo, W. Hou, S. Wang, H. Jia, Z. Yan and C. Ge, Fibers Polym., 2021 DOI:10.1007/s12221-021-2194-0.
- L. Ayed, N. Ladhari, R. El Mzoughi and K. Chaieb, J. Microbiol. Methods, 2021, 181, 106129 CrossRef CAS PubMed.
- J. H. Jordan, M. W. Easson, B. Dien, S. Thompson and B. D. Condon, Cellulose, 2019, 26, 5959–5979 CrossRef CAS.
- W. Hou, C. Ling, S. Shi, Z. Yan, M. Zhang, B. Zhang and J. Dai, Fibers Polym., 2018, 19, 742–750 CrossRef CAS.
- A. Khatri, M. H. Peerzada, M. Mohsin and M. White, J. Clean. Prod., 2015, 87, 50–57 CrossRef CAS.
- A. Y. L. Tang, C. H. Lee, Y. M. Wang and C. W. Kan, Cellulose, 2019, 26, 4159–4173 CrossRef CAS.
- L. Hao, R. Wang, K. Fang, J. Liu, Y. Sun and Y. Men, Carbohydr. Polym., 2015, 125, 367–375 CrossRef CAS PubMed.
- X. Wang and Y. C. Ping, Printing and dyeing auxiliaries, 2019, 36, 41–44 Search PubMed.
- B. Li and H. Zhu, China Fiber Inspection, 2012, pp. 59–61, DOI:10.14162/j.cnki.11-4772/t.2012.02.020.
- N. Meksi, M. Kechida and F. Mhenni, Chem. Eng. J., 2007, 131, 187–193 CrossRef CAS.
- G. Schwedt and L. M. de Carvalho, J. Chromatogr. A, 2005, 1099, 185–190 CrossRef PubMed.
- Y. Luo, L. Pei and J. Wang, J. Clean. Prod., 2020, 251, 119728 CrossRef CAS.
- K. Liu, X. Zhang and K. Yan, Carbohydr. Polym., 2018, 188, 221–227 CrossRef CAS PubMed.
- P. Tang and G. Sun, Carbohydr. Polym., 2017, 160, 153–162 CrossRef CAS PubMed.
- K. M. Thompson, W. P. Griffith and M. Spiro, J. Chem. Soc., Faraday Trans., 1993, 89, 1203–1209 RSC.
- T. Topalovic, V. A. Nierstrasz and M. M. C. G. Warmoeskerken, Fibers Polym., 2010, 11, 72–78 CrossRef CAS.
- A. Farooq, S. Ali, N. Abbas, G. A. Fatima and M. A. Ashraf, J. Clean. Prod., 2013, 42, 167–171 CrossRef CAS.
- E. S. Abdel-Halim and S. S. Al-Deyab, Carbohydr. Polym., 2013, 92, 1844–1849 CrossRef CAS PubMed.
- L. Tian, C. Branford-White, W. Wang, H. Nie and L. Zhu, Int. J. Biol. Macromol., 2012, 50, 782–787 CrossRef CAS PubMed.
- H. Changhai and D. Hinks, et al., Carbohydr. Polym., 2015, 119, 71–77 CrossRef PubMed.
- K. R. Jegannathan and P. H. Nielsen, J. Clean. Prod., 2013, 42, 228–240 CrossRef CAS.
- H. A. Eren, O. Avinc, B. Erişmiş and S. Eren, Cellulose, 2014, 21, 4643–4658 CrossRef CAS.
- X. Zhang, Master of thesis, Beijing University of Chemical Technology, 2015.
- N. Zhang, Master of thesis, Donghua University, 2019.
- E. S. Abdel-Halim, Carbohydr. Polym., 2012, 90, 316–321 CrossRef CAS PubMed.
- P. Bigambo, C. M. Carr, M. Sumner and M. Rigout, J. Text. Inst., 2019, 111, 785–794 CrossRef.
- J. Y. Cai and D. J. Evans, Color. Technol., 2007, 123, 115–118 CAS.
- F. O. Howitt, J. Text. Inst., Proc., 1956, 47, P909–P933 CrossRef.
- K. V. Karthik, A. V. Raghu, K. R. Reddy, R. Ravishankar, M. Sangeeta, N. P. Shetti and C. V. Reddy, Chemosphere, 2022, 287, 132081 CrossRef CAS PubMed.
- U. Jinendra, J. Kumar, B. M. Nagabhushana, A. V. Raghu and D. Bilehal, Green Mater., 2019, 7, 137–142 CrossRef.
- M. Marx-Figini, Angew. Makromol. Chem., 1978, 72(1), 161–171 CrossRef CAS.
- Y. Liang, W. Zhu, C. Zhang, R. Navik, X. Ding, M. S. Mia, M. N. Pervez, M. I. H. Mondal, L. Lin and Y. Cai, Cellulose, 2021, 28, 7435–7453 CrossRef CAS.
- R. E. Brooks, Cellulose, 2000, 7, 263–286 CrossRef CAS.
- L. Saikhao, J. Setthayanond and T. Karpkird, et al., J. Clean. Prod., 2018, 197, 106–113 CrossRef CAS.
- S. Komboonchoo, A. Turcanu and T. Bechtold, Dyes Pigm., 2009, 83, 21–30 CrossRef CAS.
- M. O. Bulut, J. Clean. Prod., 2016, 137, 461–474 CrossRef CAS.
- S. Shang, X. Ye, X. Jiang, Q. You, Y. Zhong, X. Wu and S. Cui, J. Non-Cryst. Solids, 2021, 569, 120922 CrossRef CAS.
- M. E. El-Naggar, S. Shaarawy and A. A. Hebeish, Int. J. Biol. Macromol., 2018, 106, 1192–1202 CrossRef CAS PubMed.
- A. D. French, Cellulose, 2014, 21, 885–896 CrossRef CAS.
- A. D. French and M. S. Cintrón, Cellulose, 2013, 20, 583–588 CrossRef CAS.
- M. Kamali Moghaddam and E. Karimi, Cellulose, 2020, 27, 9383–9396 CrossRef CAS.
- D. P. Suhas, T. M. Aminabhavi, H. M. Jeong and A. V. Raghu, RSC Adv., 2015, 5, 100984–100995 RSC.
- J.-J. Long, B. Liu, G.-F. Wang and W. Shi, J. Clean. Prod., 2017, 165, 788–800 CrossRef CAS.
- D. P. Suhas, A. V. Raghu, H. M. Jeong and T. M. Aminabhavi, RSC Adv., 2013, 3(38), 17120–17130 RSC.
- W. M. E. M. M. Daniyal, Y. W. Fen, J. Abdullah, H. S. Hashim, N. I. M. Fauzi, N. Chanlek and M. A. Mahdi, Thin Solid Films, 2020, 713, 138340 CrossRef CAS.
- N. Tavker and M. Sharma, J. Clean. Prod., 2020, 271, 1–14 CrossRef.
- M. A. Imran, T. Hussain, M. H. Memon and M. M. A. Rehman, J. Clean. Prod., 2015, 108, 494–502 CrossRef CAS.
|
This journal is © The Royal Society of Chemistry 2022 |
Click here to see how this site uses Cookies. View our privacy policy here.