DOI:
10.1039/D2RA01831D
(Review Article)
RSC Adv., 2022,
12, 17104-17137
Recent progress in treatment of dyes wastewater using microbial-electro-Fenton technology
Received
21st March 2022
, Accepted 2nd May 2022
First published on 9th June 2022
Abstract
Globally, textile dyeing and manufacturing are one of the largest industrial units releasing huge amount of wastewater (WW) with refractory compounds such as dyes and pigments. Currently, wastewater treatment has been viewed as an industrial opportunity for rejuvenating fresh water resources and it is highly required in water stressed countries. This comprehensive review highlights an overall concept and in-depth knowledge on integrated, cost-effective cross-disciplinary solutions for domestic and industrial (textile dyes) WW and for harnessing renewable energy. This basic concept entails parallel or sequential modes of treating two chemically different WW i.e., domestic and industrial in the same system. In this case, contemporary advancement in MFC/MEC (METs) based systems towards Microbial-Electro-Fenton Technology (MEFT) revealed a substantial emerging scope and opportunity. Principally the said technology is based upon previously established anaerobic digestion and electro-chemical (photo/UV/Fenton) processes in the disciplines of microbial biotechnology and electro-chemistry. It holds an added advantage to all previously establish technologies in terms of treatment and energy efficiency, minimal toxicity and sludge waste, and environmental sustainable. This review typically described different dyes and their ultimate fate in environment and recently developed hierarchy of MEFS. It revealed detail mechanisms and degradation rate of dyes typically in cathodic Fenton system under batch and continuous modes of different MEF reactors. Moreover, it described cost-effectiveness of the said technology in terms of energy budget (production and consumption), and the limitations related to reactor fabrication cost and design for future upgradation to large scale application.
1 Introduction
Textiles are included amongst the most pollution causing industrial sectors into air, water and terrestrial environments. Persistent organic pollutants (POPs) such as dyes and pigments are extensively manufactured and discharged (5–1500 mg L−1) in textile industry effluents. Other industries including leather, foods, beverages, pharmaceuticals, cosmetics, paper and pulp are also releasing significant amounts of such pollutants in their effluent.1,2
Developing countries are mostly devoid of any domestic or industrial wastewater treatment facilities, while those operating are often ineffective for refractory chemicals.3 Moreover, power shortages and cost of treatment facilities are one of the major drawbacks. Considering these facts the wastewater generally originating from industrial units is released in existing water channels (streams and rivers) after primary settlement tanks. The refractory contaminants stay in waster channels or settle in soil and sediments depending upon their half-lives, causing enormous issue to freshwater ecology.
Dyes are highly diverse (∼100
000 types)4 xenobiotic and stable under ambient conditions of light and oxygen in natural ecosystems and conventional treatment plants. Such pollutants, due to their strong structural integrity and reactive nature, impose a varying degree of toxicity and mutagenicity to living systems, and create long term environmental issues.5 Physically, color due to dyes is aesthetically objectionable in water and more specifically red and purple as being unnatural create more concerns compared to blue, green and brown that are normally natural colors.6 Moreover, color prevents sunlight penetration in water,7 thereby limits gross ecological productivity (photosynthesis) of aquatic environment. Under these conditions, the natural processes can no longer compensate the bacterial consumption or decomposition of such and other contaminants resulting a stagnant aquatic environment.8 Chemically, these compounds affect the water chemistry and associated quality due to increasing load of pollutants indicators such as TDS, COD and BOD. Depleting oxygenic levels causes oxygenic stress that limits a great deal of respiratory physiology in living organisms. Whereas high levels of TDS results creates electric conductivity level that may add further toxicity. Such factors ultimately lead toward death and decay of aquatic flora and fauna.9
Discharge of untreated dyes containing wastewater (WW) is highly objectionable and extensive treatments are required for environmental health and sustainability. Worldwide, various traditional and advance physico-chemical treatments10 methods including; adsorption,11 ozonation, photo-catalysis (UV + H2O2), coagulation, electrochemical oxidation, and filtration have been used for textile dyes and WW from industries. Coagulation and adsorption have been the simplest and commonly used methods.11 Irradiation is very efficient but unsuccessful against photo stable dyes.12,13 Membrane filtration is highly proficient though need sophisticated nano or ultrafiltration membranes.12 Chemical or electro-chemical methods including ozonation Fenton process or Electro-Fenton process (EF), and advance oxidation process (AOPs) showed great prospects for degradation of both soluble and insoluble dyes, however, these treatment are either costly or facing issues of sludge waste management12,14–18. Moreover, both chemical and physical methods have been reported for the removal of only 20–30% dyes from WW.19 Biological wastewater treatments include an array of living organisms (bacteria, fungi and plants) integrated into different suspended and attached growth reactors. They are considered ultimate due to diverse physiological capabilities of organisms to be operationalized both under aerobic and anaerobic conditions for complete decomposition of dyes. Still they are slow to evolve and functionalize until given additional technical or operational support.20,21 Smart application of biological process may also lead to re-innovating useful products from organic waste (renewable energy & industrial products). Moreover, they are environmental friendly, cost-effective and highly sustainable.
In the last two decades considerable advancements have been made on multifaceted microbial electrochemical technologies (METs). Typically, microbial fuel cell (MFC) and microbial electrochemical cell (MEC) have been mostly developed for treatment of variety of pollutants linked to domestic and industrial sectors.9,22,23 METs principally work on the anaerobic bio-catalysis of contaminants for harnessing renewable energy [electrical24 or gaseous energy (H2)].7 Recently, advancement on MXCs as Micro (Bio-)-electro-Fenton process (MEFP) is taking lead relying on the previously established WWT technologies typically including EFP, AOP, biological processes and MES.15,18 MEFS using MFC or MECs have gone through a series of innovations and advancements.25–27 In 2000, Lin and Chang, reported a combine sequential approach of treating landfill leachate and refractory compounds using EF and biological processes28 Later, in 2009, the 1st MEFS was developed for aerobically stable pollutant like dyes and it further expanded the scope of such innovative technologies.27,29–33 As compared to traditional EF technologies, the MEF technology is more efficiency and cost-effective (approx. 10 fold) for refractory compounds in WWT.21 Besides it creates almost negligible amount of sludge. This technology offer superior possibilities of treating persistent organic pollutants (POPs) of xenobiotic nature in WW34,35 including dyes,32,36,37 pesticides, dioxins, personal care products and pharmaceuticals24,38,39 lignin (paper and pulp), bagasse and molasses from different industries. Besides, it is equally effective for municipal and agriculture waste treatment under varying physicochemical loads.32,40
A basic MEFS include a similar METs set up21 for anaerobic degradation of biodegradable compounds in anodic chamber, however, it is also supplemented with a Fenton Process (FP) for simultaneous treatment of refractory compounds (dyes, pesticides or aromatic compounds) in a non-selective manner in cathodic chamber.34 Cathodic oxidation of contaminants involves oxygen species as hydroxyl radicals that are highly reactive and generated through catalysis of H2O2 by Fe2+.10,41,42 By Fenton's reagent, oxidation of organic compounds is rapid and exothermic process that helps almost complete mineralization of contaminants into inorganics i.e., carbon dioxide and water.29 Additionally reports have also suggested possibilities of coupling photo-catalytic (UV/light) oxidation along with typical FP to enhance the overall efficacy of MEFS.21 An added advantage of this innovative technology is treatment of two different wastewaters (pollutants) in the same reactor. In the last few years, further improvement in architecture and scope of MEFS helped development of new reactors that are yet to be operationalized at pilot and large scales.
2 Dyes and pigments; characteristics, source and environmental fate
2.1 Characteristics of dyes and pigments
Worldwide, an annual production of various dyes and pigments is about 700
000 tons.4 Generally dyes and pigments are made up aromatic backbone structure of benzene with alternating double C bonds (delocalized electrons pairs) that helps in transmission and reflectance of natural white light resulting in creation of different hues.1 From an industrial perspective, successful dyes have a strong structural integrity and high water solubility for possible sustainable application in different products.8 On the other hand, pigments are made hydrophobic with large molecular structures and intermolecular attractions due to hydrogen bonding (N–H and C
O groups).43 Globally, 40% of colorants used comprise chlorine that is organically-bound.6 With their widespread applications and complicated chemistry, the utilization of colorants in textile industry could also be a major cause of dioxins and their precursors that typically relates to POPs. Being the most toxic compound, dioxins are associated to halogens homologues. The recalcitrant nature of dyes and pigments is typically associated with their benzoic structure that makes them highly objectionable as they avoid natural process of mineralization under normal oxygenic environment44 thereby creating environmental issues of low biotic productivity. The reactive nature of such compounds due to presence (e.g.) chloro, nitro, and sulphonic groups make them toxic and mutagenic at varying degrees at different trophic levels.
The basic structure of dyes and related compounds comprises a chromophore group represented by “the azo group (–N
N), ethylene group (
C
C
), methine group (–CH
), carbonyl group (
C
O), carbon-nitrogen (
C
NH; –CH
N–), carbon-sulphur (
C
S;
CS–S–C
), nitro (–NO2; –NO–OH), nitrozo (–N
O;
N–OH) or chinoid groups. The auxochrome groups are ionizable groups that confer to the dyes the binding capacity onto the textile or any material. The usual auxochrome groups are: -NH2 (amino), –COOH (carboxyl), –SO3H (sulphonate) and –OH (hydroxyl)”.45 Overall, the major classes include; azo or anthraquinone accounting for 65–75% in textile dyes. An about 2/3 of them are azoic in nature. The precursor compounds or intermediates are anline, chloroanilines, naphthylamines, methylanilines, benzidines, phenylendiamines, and others.6 Azo dyes are characterized by the reactive groups that make covalent bonds with HO–, HN–, and HS– groups present in fibers e.g. cotton, silk, nylon, wool. These dyes are frequently utilized for the yellow, red and orange colors.
2.2 Classification of the dyes
Environmental positioning of dyes is related to; C atoms number and the aromatic structure, number and nature of substituents, and overall backbone molecular structure.6 Typically, classification of dyes and pigments is either based upon their chemical structure or their mode of applications to different substrate products. Structure based classification is related to the nature and chromophore groups that helps predicting dyeing and associated oxidation – reduction. There are 8 different categories of dyes based upon their chemical structures. Dyes based upon application depends on chromophore grouping that help dying based upon dye solubility in dye bath and its affinity with different fibers and nature of fixation. On solubility basis, dyes and pigments are broadly characterized as anionic, nonionic and cationic in nature.46 Among anionic dyes (direct, acid and reactive) reactive and acidic are most problematic due to their bright colors and water solubility in conventional wastewater treatments.6 Nonionic dyes such as disperse do not ionize in the aqueous system, while, cationic ones are anthraquinone, azoic, reactive and disperse dyes. Few disperse dyes are efficiently bioaccumulate and their azo and nitro groups are reductively cleaved (reduced) in soil sediments to toxic aromatic amines.6 On this basis, they are 9 different types partially distributed in the two categories of water soluble and insoluble. Some basic details on classification of dyes is mentioned in Table 1.
Table 1 Classification and properties of Dyes
Category (structure and mode of application) |
Sub-category (type/nature) |
Chromophore |
Auxochrome |
Properties/examples |
Discharge rate (%) |
Fabric type |
Structure and chemical formula |
References |
Chemical structure |
Azo |
–N N- |
NH2, OH, SO3, Cl |
70% of synthetic dyes, mon, di, tri azo. Yellow reactive 4, black reactive 5 |
5–10 |
Cellulose |
 |
47 |
Anthraquinone |
C O. and C C , forming an anthraquinone complex (quinone nucleus) |
NH2, OH, SO3 |
Most important after azo, derived from anthracene. e.g.; acid blue 62, reactive blue 19 |
2–10 |
|
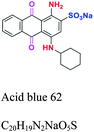 |
46 |
Indigo |
C O, NH2, C C, C–O, C N, C–C |
SO3, NH2, C O |
Derived from indigo. e.g.; blue acid 74, indigo blue |
|
|
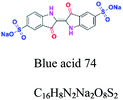 |
48 |
Xanthene |
Xanthylium or di-benzo-g-pyran nucleus |
Amino or hydroxyl, COOH |
Intense fluorescence, used as markers/tracers in maritime accidents or underground river. e.g.; fluorescein, eosin, erythrosine |
|
|
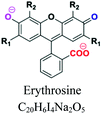 |
49 |
Phthalocyanine |
Phythalocyanine nucleus |
SO3 |
Metal complex (Cu, Ni, Co, Pt e.g.; copper phthalocyanine. e.g.; pigment blue 15/3, nickel(II) tetrasulfonic acid |
|
|
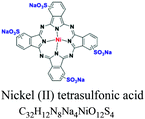 |
32 |
Nitrated & nitrosated |
O–NH O, O–NH O, phenol, nitro |
Nitro (–NO2), OH, NH2, CH3NH |
Limited number, older e.g.; picric acid (2, 4, 6-trinitrophenol), 2-nitrophenol, 2-amino-4-nitrophenol |
|
|
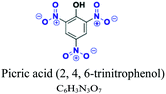 |
50 |
|
Diphenylmethane & triphenylmethane |
|
CH3, NH, SO3 |
Oldest, derivative of auramine and triphenylmethane e.g.; fuchsin and malachite green |
|
|
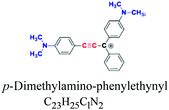 |
51 |
|
Polymethinic |
HC–HC CH–CH![[double bond, length as m-dash]](https://www.rsc.org/images/entities/char_e001.gif) |
OH, SO3−, CH3, HN–N–CH3 |
Also called cyanines, e.g.; basic yellow 28, polymethine dye 2630 |
|
|
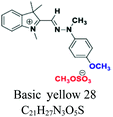 |
52 |
![[thin space (1/6-em)]](https://www.rsc.org/images/entities/char_2009.gif) |
Application |
H2O soluble |
Acid or anionic |
Azo, anthraquinone or triaryl |
SO3−, NH2, OH |
For wool, polyamide, silk and acrylic, e.g.; red acid 27, acid blue 90, acid blue 74 |
7–20 |
Wool & nylon |
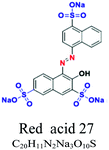 |
53 |
Basic or cationic |
Diaryl, triaryl, anthraquinone, azo, phthalocyanine |
NH2 |
e.g.; basic blue 9, basic yellow 37, blue nile |
2–3 |
Acrylic |
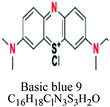 |
54 |
Metalliferous |
Azo, phthalocyanine |
|
Acidic dye with metals (Cr, Cu, Ni and Co) |
2–10 |
Leather, finishing, stationery, printing, inks, inks, coloring for metals, plastic |
|
32 |
|
Reactive |
Azo, anthraquinone, and phthalocyanine |
SO3, NH2 |
e.g.; reactive red 198 |
10–50 |
Wool and nylon |
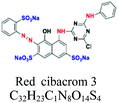 |
55 |
|
Direct or substantive |
Azo, phthalocyanin |
NH2, SO3, OH |
Large molecules with positive and negative charges, affinity to cellulose, wide variety, easy to apply and low cost, e.g.; direct blue 1 |
5–30 |
Cellulose |
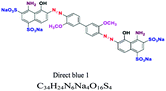 |
8 |
H2O insoluble |
Vat dyes |
Anthraquionone |
NH2, C O, CH3 |
Good resistant to degradation (soap and sunlight), good affinity to cotton, linen, wool, silk, rayon, use for dyeing jeans. e.g.; indigo (vat blue 1), blue indanthrene RS (vat blue 4, vat green 1 |
5–20 |
Cellulose |
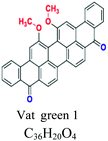 |
56 |
Sulfur |
Thiazoles, thiazone, thianthrene, and phenothiazonethioanthrone |
NH2, OH, SO3 |
Like vat dyes, complex high MW, used for cotton, dark shades, e.g.; sulfur black, sulfur blue 15 |
30–40 |
Cellulose |
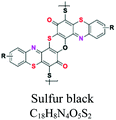 |
8 |
Disperse or dispersible |
Anthraquinone |
NH2, OH |
Plastosolubles, stable at high tempeture, used in polyester and polyamide, e.g.; blue disperse 7, red disperse 60 |
2–20 |
Synthetic |
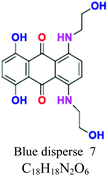 |
8 |
Pigments |
|
|
Organic (benzoic), inorganic (metals; Ti, Zn, Ba, Pb, Fe, Mo, antimony, zirconium Ca, Al, Mg, Cd, Cr), kept in suspension tanks to dispersants, film formation by heating, used in printing |
|
Paint, ink, plastic, fabric, cosmetics, food, and other materials |
|
43 |
2.3 Source and environmental fate of dyes and pigment
Industrial units including textile, pulp/paper, leather tanning, dyestuff manufacturing, pharmaceutical and kraft bleaching industries have been reported as major point sources contaminating dyestuffs in water sources.6 Typically dyes are released in water ways from dyebath (dyeing unit) and dyes manufacturing units of industries.57 The annual estimated load of pollutants in textile wastewater varies from 200
000–250
000 t salts. The exhaustion rate of dyes and pigments from dyebath unit is 10–60% comprising 10–50% reactive dyes, 5–20% vat dyes, 5–30% direct dyes and 10–40% sulphur dyes and that is 280
000 tons per year.1 Release of raw or partially treated effluents adds a huge load of TOC, nitrites, nitrates, phosphates and heavy metal ions (zinc, iron, mercury, lead, chromium, cobalt and copper) thereby also creating an issue of eutrophication. Typically, textile dyes are highly relevant in ecological perspective. Among them, azo are taken as model dyes due to their large production, consumption (60–70%) and discharge in the hydrosphere. Effluent of leather dyeing may contain greater than 250 ppm dyes causing an about 7000 ppm COD load. It is highly acidic (pH 4.5 approx)58 although alkaline in the case of the textile industry. Effluents from these industries are also source of dioxins because of the presence of dioxazin and anthraquinone dyes and pigments made from chloranil (tetrachloro benzoquinones) and pentachlorophenol. Dioxins are generally released during manufacturing and treatment of dyes by photolysis/UV.59
Long time persistence (i.e. half-life = several years/2 − 13 years) of dyes accumulate them in abiotic sediments or living or dead biomasses particularly in fish and other aquatic forms of life. Mostly they are soluble still they tend to biosorb or absorb and accumulation in suspended and settled abiotic and abiotic components of water bodies. With solubility greater than 2000 mg L−1 in water, bioaccumulation is not estimated for dyes. Adsorption is high in basic and direct dyes while range is from high to medium in disperse dyes, and it depends on degree of sulphonation or ease of hydrolysis. In group 1, ability to adsorb on the biomass and water solubility is increased due to higher levels of sulphonation. In Group 2, dyes are also greatly sulphonated but indorsed good adsorption performance on sludge moderately. Additional information in bio-elimination of different reactive dyes stated that disazos, anthraquinones, triphendioxazines and phthalocyanines are usually better adsorbed than monoazos. It is crucial to highlight that toxic compounds e.g. benzidine, aromatic amines and its derivatives can be produced in environment via transformation of textile dye precursors such as by reduction or hydrolysis of azo dyes. Moreover, sequential bioaccumulation in entire food chain60 and later biomagnified at higher trophic levels cause lethal effects.
As dyes are photo-chemically stable under ambient environmental temperature, so, they normal create problem in conventional industrial and residential treatments systems.61 Dyes are highly polar (log
Kow up to 3) and shows recalcitrance also depending on environmental variables such as redox milieu or pH. A compound like aniline (1st synthetic known dye) has been found easily degradable under aerobic condition; however, it is highly stable under anoxic condition.62 The recalcitrant and xenobiotic nature of dyes usually influence the structure and function of aquatic ecology.57 Additionally these compounds also inflict a negative effect on microbial communities of the soil and germination of plants. Typically, living species at the higher trophic levels of the food web are exposed to a thousand times higher concentration of toxicants than those at lower levels.8 Ecological and Toxicological Association of Dyes (ETAD) reported that 98% of dyes have LC50 value higher than 1 mg L−1 for fishes and 59% of dyes have LC50 greater than 100 mg L−1 and 28% higher than 500 mg L−1. LD50 reported for most of the azo dyes varies between 100–2000 mg kg−1 body weight.62 They affect physiological status of biotic community and in England, it was reported that inhibition of respiration rate in sewage bacteria is caused by 18% of 200 dyes.
Dyes generally composed of benzene moieties that makes them recalcitrant (xenobiotic nature) toxigenic and mutagenic.63 Additionally, certain functional groups such as halogens (chloride), amide, amino, sulphides and metals may add further toxicity and mutagenicity at different trophic levels.61,64 They may also carry precursors of toxic compounds like dioxins that as by-products produced during the synthesis of chlorobenzenes, chlorophenols, polyvinyl chloride, chlorobiphenyls, pigments, dyes, and printing inks. They can even be toxic at 1 mg L−1 concentration in effluents so that they are related to environmental deterioration and various diseases in living beings.61,65 Despite recalcitrance they are potentially degradable or transformable in anoxic environmental condition and soil sediments, releasing sometime toxic compounds. Acute toxicity to textile dyes relates to ingestion and inhalation,66 causing bladder cancer,67 dermatitis, nervous disorders65 impaired enzymatic activities,68 eliciting irritations to the eyes and skin.67 The personnel handling and producing reactive dyes may have contact rhinitis, allergic conjunctivitis, dermatitis, asthma or other allergic reactions.67,69
This persistence nature of dyes has also been closely related to their reactivity. It increases with the number and types of electron donating substituents typically halogens, nitro, sulphonic and alkyl groups.8 Besides, substituents in ortho and para position further upsurge the carcinogenic potential. Essentially, the toxicity lessened by the protonation of aminic groups.6 Highly reactive nature of dyes and aromatic products makes them potential candidates to transform biomolecules at very minor to major levels in the living bodies. Such changes in the living biomolecular structure impair the physiological status of living organism that becomes sever under hypoxic conditions in aquatic sediments or living biomass. Under extreme situations azo dyes may leads to DNA damage that can result in mutation and cancerous growth and sometime lethal effects like death. A substantial decline in tadpole survivorship was witnessed at 209 μg g−1 while a major upsurge in malformations at two peak concentrations was tested in sediment.70 Especially in the case of azo dyes, carcinogenicity can be produced by both the dye itself and its own metabolized compounds.67 Few well-known azo dyes i.e. azodisalicylate, precursor for 4-phenylenediamine; Direct Black 38, precursor for benzidine and their derivatives are benzidine and its derivatives, and also higher number of anilines i.e. 4-chloroaniline, 2-nitroaniline, 4-phenylenediamine, 4,4′-dimethylendianiline, dimethylamines, nitrosamines etc. causing cancer in humans and animals.
At genotoxicity level, large concentrations of dye (DY7) in sediment prompted cellular stress-related gene transcription and influenced the genes associated with chromosome condensation, necrotic cell death, and mRNA processing.70,71 Dyes may67 create chromosomal aberrations other times mutagenic.69 Dyes like Azure B found to be affecting helical structure of DNA67,72 and duplex RNA.73 Whereas at cytotoxic level, they inhibition enzymes (monoamine oxidase A) (MAO-A),74 involved in nervous system75 related to human behavior.76 Similarly, inhibition of glutathione reductase77 disturbed redox homeostasis cellular.78 Disperse red 1 dye has been reported exhibiting mutagenic potential79 on human lymphocyte and hepatoma (HepG2) cells, hepatocyte imitative cells,80 causing occurrence of micronuclei,81 indicated mutagenicity at chromosome level.82 Besides, it caused DNA adducts83 a key cancer causing event in Salmonella spp.84 Similarly, disperse orange 1 exhibited mutagenicity79 causing DNA damage-a base pair substitution and frameshift mutations in Salmonella spp. Moreover, it caused cytotoxicity with apoptosis in HepG2 cells. Another dye, Sudan I (solvent yellow 14),85 although illegal, used as a food supplement in paprika, has enzymatically transformed into carcinogenic aromatic amines by intestinal microbiota. In rats, the presence of Sudan I dye is confirmed by neoplastic liver nodules. Basic red 9 a commonly used dye in textile, leather, paper and ink industries86 indicated carcinogenic potential in human and environmental87 after partially degradation into carcinogenic aromatic amines in anaerobic conditions. Disposal of such compounds in water bodies showed potential for allergic reactions, skin irritation, mutations and cancer. Besides they comprise local sarcomas and tumors in the liver, bladder,88 mammary glands and hematopoietic system. Crystal violet, a cationic dye (triphenylmethane group),89 caused mitotic dysfunction and suspension at metaphases90 and inducing disruption of chromosomes in Chinese hamster ovules. Crystal violet has also been reported promoting fish tumors, and hepatocarcinoma, reticular cell sarcoma in vagina, uterus, ovary and bladder, hardened gland adenoma and ovarian atrophy in rats. Besides, it caused cystitis, irritation of the skin and digestive tract, respiratory and renal failure.90
3 Degradation mechanism of dyes and organic compounds in MEFS
MEFS is an integration of biological (microbial) degradation with that of electrochemical process i.e. Fenton process, for efficient removal of pollutants in less time. In a typical Microbial-electro-Fenton processes using a two chamber MFC, electrons originating from anaerobic bio-catalysis (oxidation) of organics and inorganics follows an anodic pathway reach the cathode to combine to reduce (2 electron) O2 to form H2O2 (79 to 196 mg L−1) with simultaneous electricity production in 1st stage. Then it follows the production of highly reactive (oxidative) OH radical through chemical catalysis (Fe) of H2O2 in the 2nd stage. The enhanced oxidation of the target compounds such as dyes through hydroxyl radical is the final 3rd stage. MEC, an extended version of MFCs, requires a minor input of electricity (0.2–0.8 V) in order to accelerate overall performance and H2O2 production (1300–1447 mg L−1). A part of free energy formed is taken by bacteria for catabolic activities and rest can be employed to produce electricity for maintainable operations of the system.91–94 Such systems can equally be good to treat two different dyes and their byproducts at 1st and 3rd operational stages simultaneously. Another good possibility can be sequential treatment (back and forth) of same refractory dyes in the two chambers of reactor in order to achieve complete mineralization as shown in Fig. 1. Beside these systems creates a workable electric potential to facilitate reactor performance and make them cost-effective and sustainable. A biological catalyst is either an enzyme or bacteria immobilized on the anodic reactions. Although the cathodic reactions may involve a biological or chemical catalyst in a typical MFC.40,95,96 For advanced oxidation of refractory compounds in cathodic chamber, a chemical catalyst like Fe2+ is utilized to generate OH radical from H2O2.
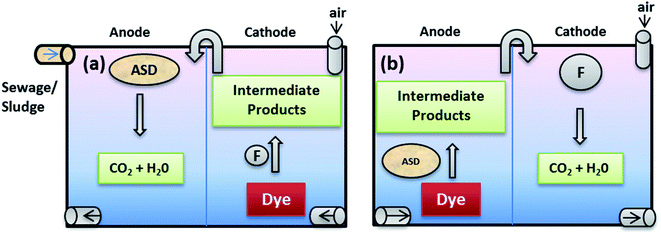 |
| Fig. 1 Model concept of MXCs based MEFS: sequential batch or continuous modes; (a) aerobic degradation of dyes in cathode through Fenton reaction (FR) followed by anaerobic mineralization of dyes products and sewage/sludge in anode, (b) anaerobic degradation of dyes and sewage/sludge in anode followed by aerobic mineralization of products of dyes and sewage/sludge in cathode through FR (ASD = anaerobic sewage sludge digestion; F = Fenton agent ˙OH). | |
Microbial electrochemical systems depend on diverse bacterial communities that encompasses electricigens or ARB. In the anode compartment, a mutualistic activities of several anaerobic microorganisms (fermentative, syntrophic, acetogenic, and methanogenic) consequent in the degradation of complicated organic substances into simple and stabilized compounds, primarily, methane and CO2. Initially such systems often operated with glucose and acetate as a fermentable substrate to upkeep the growth of electricigens. The fermenters and other syntrophic bacteria perform hydrolytic monomerization and fermentation of complicated substrates97,98 from food, beverages, pulp and paper, leather, pharmaceutical and residential wastewater. The enrichment and catalysis role of fermenters helps improved oxidation rates of monomers by electricigens in the secondary stage.99 It also work to ease the role of hydrogen scavengers.100 Generally, anaerobic digestion (AD) involves liquefaction or hydrolysis of insoluble compounds,101 followed by acidogenesis/acetogenesis and methanogenesis.102 Bacteria like Streptococcus and Enterobacterium release extracellular hydrolytic enzymes e.g. cellobiase, xylanase, cellulase, amylase, protease, and lipase to degrade biopolymers103 into simple monomers and dimers i.e. monosaccharides, fatty acids and amino acids.104–107 In the 2nd stage, monomeric products are then transformed into “short-chain organic acids (formic, acetic, propionic, butyric, and pentanoic) alcohols (methanol, ethanol), aldehydes, carbon dioxide, and hydrogen by acidifying bacteria including Pseudomonas, Bacillus, Clostridium, Micrococcus, or Flavobacterium”.105,108,109 In the 3rd stage, acetogens including Syntrophomonas and Syntro-phobacter transform the acid phase products into acetates and hydrogen that could be utilized by methanogens110 in syntrophic relation with acetogenic bacteria.110,111 Methanosarcina and Methanosaeta, acetogenic methanogens, generate methane that accounts an about 2/3 in AD in the 4rth stage.112,113 Methylated compounds and Carbon dioxide are the alternate substrates for production of methane by Methanosarcina, Methanothermobacter, and hydrogenotrophic methanogens. Whereas, methylated compounds are appropriate substrates for Methanosphaera, Methanosarcina and methylotrophic methanogens.113 Overall, biogas production during AD comprises 65–70% methane and 30–35% carbon dioxide.114
Typically MEFS based reactors demonstrated enrichment of diverse ABR bacterial community in anodic biofilms.115 Proteobacteria has been reported most abundant phylum under these setups due to its versatile abilities for aromatic compounds (azo dyes) biodegradation, electricity generation, and fermentation.116 Functionality based analysis showed chemo-heterotrophy the predominant followed by fermentation (6.6 ± 1.6%) and nitrate reduction (7.4 ± 2.3%). Two distinctive electricity producing bacteria i.e. Shewanella and Geobacter,117 were anticipated to be the key players in the improvement of iron respiration.118,119 Other bacteria with selective relevant function include Serratia, Stenotrophomonas for EET, Stenotrophomonas Dysgonomonas, Brevundimonas, and Achromobacter for reduction of azo-dye or degradation of aromatic compounds.120–122 The relative abundances of fermenters Acinetobacter, Cloacibacillus and methanogens Methanobacterium were lowered under MES systems.123–125
Compound like azo dyes from dyeing and production sectors of industries account for an about 60% of the total known dyes. Usually they are taken as model compounds to be treated in any biological, physical or chemical treatment. Azo dyes have shown partial to complete mineralization in most of the MEFS.20 Still, most of the previous studies have reported microbial-electro-Fenton process achieving complete degradation of azo dyes including amaranth, orange G, methylene blue, crystal violet, Lissamine green B, and orange II by integrating effective electro-Fenton reaction in the cathode chamber.126–128 Generally, for azo dyes removal two different types of MEFS such as MFC or MEC and their modified version have been used. Azo dyes due to their charged large structures are expected to be reduced either extracellularly or with membrane bounded enzymes. Under anaerobic condition azo dyes cleavage at N
N to produce colorless aromatic amines. Anodic catalysis in MFC using microbial consortia broadens the horizon of substrates utilization due to diverse microbial metabolic apparatus in terms of enzymes, coenzymes and cofactors this helps improves the energy efficiency and less toxicity in the system.129–131
During anodic biocatalysis of dyes the role of oxidoreductases (dehydrogenases (alcohol, formaldehyde, formate, fructose) oxidases, oxido-reductases), cofactors and coenzymes “(nicotinamide adenine dinucleotide (NAD+), nicotinamide adenine dinucleotide phosphate (NADP+), pyrroloquinoline quinine (PQQ), Flavin adenine dinucleotide (FAD) have always been vital (Fig. 3). In case of FAD cofactor dependent oxidoreductases, three FAD-dependent glucose dehydrogenase (FAD-GDH), cellobiose dehydrogenase (CDH) and fructose dehydrogenase (FDH) have been extensively studied”.132 Additionally, the role of natural and artificial mediators (methylene green, methylene blue, neutral red,133 phenazines, methylene blue, alizarin yellow, methyl violet, thionine, Prussian blue, azure A, toluidine blue and azure C) that reacts with reduced enzymes or coenzyme in order to transfer electrons to electrode is highly effective.134–137 Moreover, the degradation products of dye (AO7) such as naphthol have been reported as an alternative for electron mediation.138 On the other hand, the electrode can also reduce enzyme thereby enzymatic reduction of substrate i.e. dye (bioelectrocatalytic reduction). Direct enzymatic reduction of electrode proved to be more effective, however,139,140 if cofactors are involved then they should not be 20 Å (2 nm) away from electrode surface.141,142
Metals and their alloys have also been reported playing a major role as catalyst due to their different oxidation state in Microbial-electrochemical Fenton system. These metals include Pt, Au, Ni, Co143 Fe and Cr. Ti, V, Cr, Mg, Mo, and Re.144 However, they are sometime expansive,145 susceptible to adsorption by the impurities144,146 and show limited substrate specificities. “Commonly occurring metallocofactor motifs of metalloenzymes are: haem centres, Fe–S clusters ([Fe–S]), Fe centres, Cu centres, Mo centres (Mo-cofactors, Moco) and W, including various iterations and combinations. In many cases, only a single catalytic redox cofactor is found, although others can be found to be involved in internal ET (commonly the case of [4Fe–4S] containing proteins). Frequently, oxidoreductases that comprise non-metallocofactors (FAD) and PQQ-dependent enzymes also utilize metallocofactors to transfer electrons to and from their redox partners, or in other cases electrode surfaces. Additionally, metalloenzymes have been known to function as a transmembrane enzyme that functions on either side of a membrane or the enzyme contains a deeply hidden catalytic redox cofactor. One of the most fascinating examples of such an internal ET pathway can be found in prokaryotic nitrate reductase (Nar NR), such as that in Escherichia coli (NarGHI NR)”.147 Modern studies have reported that Mtr respiratory pathway in S. oneidensis MR1 involve OmcA/MtrC playing role of “azo reductase”.148,149 Where flavins have been reported to assist and improve the decolorization process.150 Besides, removal of dye (AO-7) was largely associated with bio-reduction due to dehydrogenase activity (DHA) rather than electrochemical reduction.119 Greater DHA activity reflected greater transfer activity of intracellular electron e.g., AO-7 reduction by anodic bacteria, but some of them showed EET capability.151
Different bioanodic degradation pathways and byproduct have been reported in case of dyes. Fig. 3 reveals a typical anaerobic degradation an azo dye methyl orange 7 (MO7) that possible occurs in anodic compartment generating by products including N,N dimethyl-benzene 1,4 diamine and sulfanilic acid. The reaction initiated through intra-cellular dehydrogenases producing NADH from oxidation of reduced C compounds. Azoreductase then reduced the azo bond using reduced mediator from NADH generating primary extra-cellular degradation product of dye. In a typical MFC anode using S. oneidensis, a symmetrically cleavage pathway of AO7 was predicted after reduction of the azo bond in the creation of aminobenzene sulfonic acid (sulfanilic acid), 1-amino-2-naphthalenol (1-A-2-N), and 2-amino-1-naphthalenol.152 Previously, the existence of aminobenzenes under anaerobic decolorization of AO7 was reported by.153 In case of mordant azo dyes salicylic acid derivatives were numerically predominant byproducts, whereas, N,N-dimethylaniline, sulfanilic acid and sodium sulfanilate in case of methyl orange.154 Likewise, microbial or electrochemical degradation of AO-7 produces 1-amino-2-naphthol (AN) and 4-aminobenzenesulfonic acid (AA) in anaerobic environments.20 However, mineralized of a Congo red indicated less toxic and more degradable organic byproducts such as maleic acid and malonic acid in MEF-COR system.35 Current density has been reported to increase with the higher concentration of azo dyes. It further helps in degradation of dyes.155 Beside higher current efficiency puts a low energy demand in the system, nonetheless, required extended time for achieving acceptable mineralization.17 Despite MFC being energy gaining rather consuming, it has CE loses due to dyes and their increasing concentrations of dyes (AO-7) and electron consumption.119 In some cases, degradation of azo-dyes displayed prompt electricity generation156,157 compared MFCs inoculated sludge. This has been linked with products of dye such as phenazine, aminophenol, and naphthol playing role as electron mediators in electricity generation.138,158 Mostly reports have indicated the production of toxic or mutagenic byproducts of partially degraded azo dyes in conventional anaerobic digestion (AD). Such compounds were preferred to be treated under aerobic conditions for complete mineralization. So, current approach of treating dyes in MEFS is considerably required. Sometimes, dyes or their products became toxic due to synergistic effects of several chemical or biological constituents in the effluents instead of one or certain contaminants.
Iron (F2+/Fe3+) is a key player in cathodic Fenton reaction. In a typical Fenton reaction ferrous salt (Fe2+ ions) in the catholytes catalyze the production of ˙OH from H2O2.10 Usually Fe2+ (Fenton) is preferred over Fe3+ (Fenton-like), however, a combine blend of both (e.g., magnetite and ilmenite) in pure homogenous or heterogeneous and in conjugation form with other cations59 and composite electrodes can be effectively utilized. In case a typical Fenton reaction, powerful ˙OH is generated (E° = 2.80 V) (k = 63 M−1 s−1). Whereas in Fenton like reaction, less powerful ˙OOH radical (E° = 1.65 V) is released and causing a rate limiting step in hydroxyl radical production. Moreover, Fe2+ is constantly renewed through cathodic reduction of Fe3+ and though chain of other Fenton reactions.159 Reports have clearly validated better performance of Fenton reaction rather than Fenton-like reaction in pollutants (dyes) degradation.23 For optimum MEFS, factors like type and concentration of Fe catalyst and pollutant, electrodes surface area and spacing, bio-electrochemical potential and water quality are vital. It is reported that rise in Fe2+ concentration improved the rate of degradation of pollutants (dyes), but the rate declines above a definite value because of acceleration of parasitic reactions between Fe2+ and hydroxyl radical thereby loss of the system efficiency.10,23 Beside efficiency of FR also depends upon the bio-anodic and cathodic potentials. Excess concentration of Fe2+ may result %OH loss and thereby gradual decline in degradation efficiency of the pollutant. Previously, the maximum degradation efficiency of azo dye was reported at 1.0 mM of Fe2+ in MEFS, however, further increase in Fe2+ concentration to 5 mM reduced degradation efficiency to 80.15% from 100%.92 Beside excessive Fe2+ addition may cause further operational costs160 due to great volume of sludge generation and its successive treatment. Some solid iron oxides such as α-FeOOH, FeO, Fe3O4, Fe2O3 have been considered as iron catalysts in Electro-Fenton process. The removal efficiency of POPs was related to release Fe2+ from its oxides into the solution for Fenton's reaction (Fig. 2C). Moreover, synthetic iron-containing nanoparticles (e.g., nano-Fe3O4, α-Fe2O3 and Pd/Fe3O4) have also been considered for the treatment of POPs based upon electro-Fenton process.59
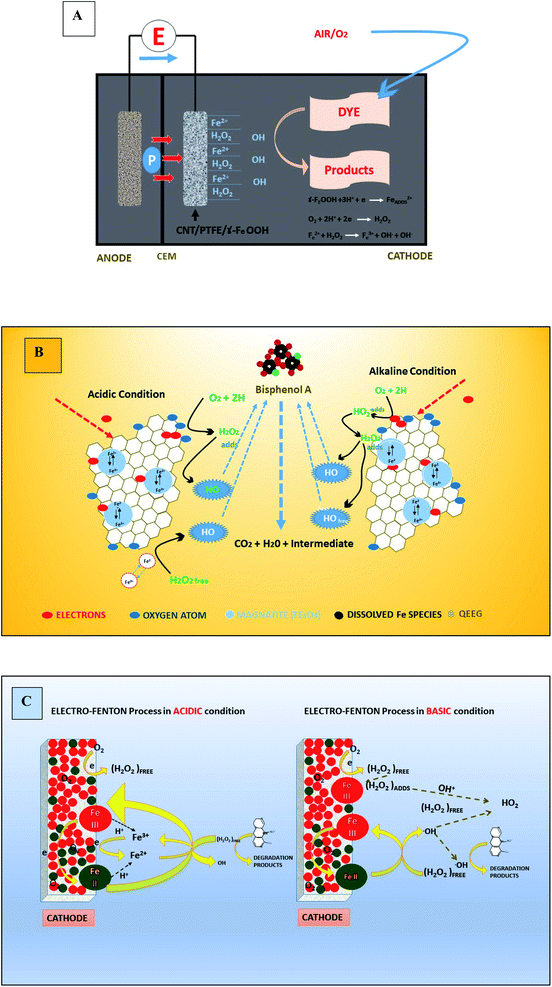 |
| Fig. 2 Cathodic electrochemical Fenton reaction: (A) a typical MFC; mechanisms of reactive oxygen species formation under acid and alkaline conditions (B) the graphene/Fe3O4 composite electrode (refabricated from ref. 161) (C) Fe3O4@Fe2O3/ACA cathode (refabricated from ref. 162). | |
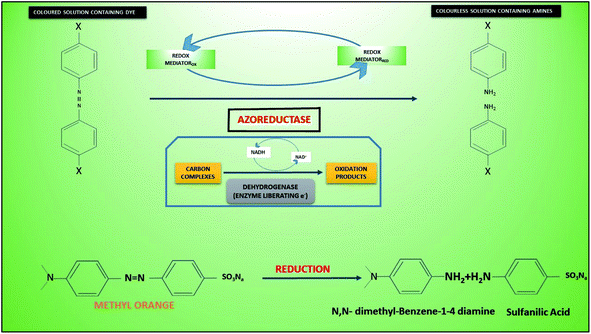 |
| Fig. 3 Proposed scheme of partial anaerobic degradation (decolorization) of methyl orange 7 (refabricated from ref. 169). | |
Degradation of methyl orange using hybrid advanced oxidation (Fig. 4) suggested involvement of hydroxyl radical with amputation at electron-rich site of N
N (azo bonding),163 creating intermediates like dimethylaniline (a) and sodium benzenesulfonate (b) which then converted to aniline (c) and benzenesulfonic acid (d) respectively. Further hydroxylation of resulted conversation of aniline into hydroxyaniline (e) and benzenesulfonic acid into 4-hydroxybenzenesulfonic acid (f), and both these intermediates decomposed into hydroquinone (g) and then p-benzoquinone (h). The final aromatic end product is transformed into an aliphatic acid (oxalic acid or carboxylic acid) for complete mineralization into CO2 and H2O.164 Another sequential (symmetrical and asymmetrical) degradation of dye MO using hydroxyl radical demonstrated aromatic products such as hydroquinone and p-benzoquinone. Whereas aliphatic byproducts like succinic acid, malic acid, acetic acid and isobutaric acid are easily assimilate into TCA and other respiratory pathways. To attain high degradation performance in MEFS, high H2O2 concentration and production rate are obligatory. In MXCs-integrated systems containing both biotic and abiotic phases, the relationship between current, ARB, and the electrode revealed123,165,166 voltage (Ohmic) losses in the electrodes due to resistance at the interface of biofilm, anolytes/catholytes and electrodes, CEM/PEM membrane, and the cathode over potential (for H2 production or O2 reduction).119 The process conversion efficiency can be lowered by 100% due to losses at the bio-anode. In cathode chamber, the reaction mechanism is comparable with classical electro-Fenton process. However, in both cases H2O2 reacts with Fe2+ to yield hydroxyl radical that could be used for oxidation of dyes.162 The cathode potential is one of the key players in H2O2 production and it varies with different types and composition of cathodes. For example, a maximum H2O2 concentration can be achieved at cathode potential of −0.4 V using graphite cathode.167 Though, the maximum H2O2 concentration of 711.2 mg L−1 was witnessed under cathode potential of −0.85 V with 0.5 V in MEC using 3D electrodes as cathode.168 Apart from cathodic potential, cathodic material should be resistant to corrosion and should have good electrical conductivity.
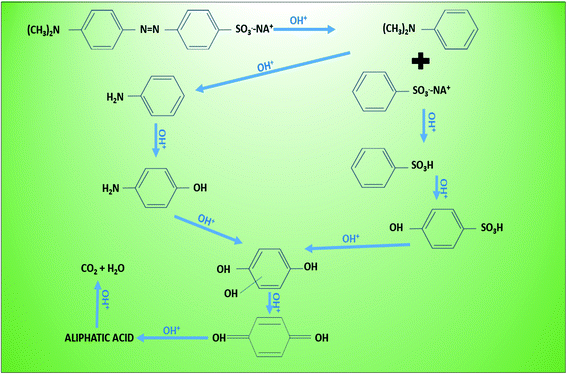 |
| Fig. 4 Degradation of methyl orange using hybrid advanced oxidation (refabricated from ref. 170). | |
4 Materials used in MEFS
4.1 Electrode material
Electrodes play an integral role on the efficiency of any electro-chemical or bio-electro-chemical cells. Electrodes types are characterized on the basis of their material, conductivity (electronic potential), reactivity, surface area, and their integration in the MEFS. Some of the electrodes have also been fabricated in laboratory.171 Typically in a MEFS, these electrodes are vital in terms of their compatibility with cellular organelles and exo-secretions (extra-polymeric substances = EPS) in order enrich biofilms of exo-electrogens on them.172 In many reactors, both electrodes i.e. cathode and anode were similar173 but in others cases they may be different.174 Carbon-based materials are preference in different MES including carbon paper, glassy carbon, carbon felt, carbon cloth, graphite plate, granule graphite, granule active carbon, graphite brush carbon mesh, carbon aerogels and reticulated vitrified carbon (Fig. 5). Most of the carbon materials, such as carbon paper, glassy carbon, carbon cloth, are composed of 2D structures that are plane with identical surface property and morphology. The electrochemical property of these pristine carbon materials can be improved effectively by proper surface treatment (acid, heat, amino gas, etc.) and modification with nanomaterials, conductive polymer, and immobilized electron shuttle that results insignificant improvement in performance of MES. Beside, these electrodes were modified with various types of materials like nanomaterials, activated carbon, metal (Pt catalyst) and etc. in order to improve their performance.175
3D anodes are grabbing substantial consideration for the improvement of profoundly efficient systems.176,177 These anodes have demonstrated 80–90% hydrogen recovery and COD removal efficiency.153 Additionally, layers of carbonized corrugated cardboard as anode material increased the current density by manifold.178 Furthermore, pre-treatment of anode with ammonia, phosphate, trace metals proved to be increasing; porosity (biocatalytic sites increases), conductivity, and particles capable of supporting biofilm growth.179–181 Whereas modification of C anode with polypyrole/anthraquinone-2,6-disulfonate cause the increased power density, redox properties and associated microbial-electo-catalysis of azo dye.174 Modification of carbon fibers with carbon nanotubes and polypyrole composite resulted in excellent biocompatibility and conductivity. Efficiency of modified anode in producing electricity is 2.63 times higher than that of unmodified ones, generating 1876.62 mW m−2 power density, and enhanced mineralization rate of orange II dye.182,183
4.2 Cathode and Fe forms and types
Cathode material should be porous and resistant to corrosion in order to support exchange of protons and electrons and interaction with oxidants. It is also usually carbon based due to less cost, good conductivity and stability.162,177,186 These include carbon brush, activated carbon, carbon fiber and modified CNT, carbon paper and cloth etc. that have been employed in MEFS.177,178,187,188 Production of H2O2 is vital in MEFS, and it then converted into highly responsive oxygen species such as ˙OH radicals to mineralize pollutants in cathode.153,162,177,186 Modified cathodes with C substrates with catalysts' layers and diffused (channeled) air supply proved to be highly effective in catalytic reduction of oxygen and H2O2 production.177,184,189 The iron source is one of the vital element to impact the performance of the MEFS. Usually, dissolve Fe2+ (Fenton) and sometimes Fe3+ (Fenton-like) salts have also been used in catholytes as catalysts for Fenton reaction in MEFS. Some researchers also have used iron alginate beads, scrap iron or iron plates as Fenton catalysts. Carbon-based modified cathodes with iron or transition metal oxides have also been preferred.184 Wang et al. reported the use of composite cathodes in MEFS for dye wastewater treatment. The cathode was fabricated by generating CNTs on SS316 stainless steel mesh with addition of iron phthalocyanine as catalyst, which resulted in enhanced current density and power of the system by 937 and 2594 times respectively along with 84.6% of dye decolorization in 12 h.171
Combination of both divalent iron and trivalent iron (e.g., magnetite and ilmenite) has found more effective for Fenton reactions. These catalysts of iron were also used in EF studies in pure forms, doped with other cations,59 or mostly as composite electrodes.190 The usage of self-designed electrodes like Fe@Fe2O3/CF,191 γ-FeOOH/CF,192 carbon nanotube (CNT)/γ-FeOOH/CF, PPy/AQDS/CF162 and FeVO4/CF191 are providing iron catalyst as heterogeneous or homogeneous reactions has expanded the scope. Study showed that degradation rates of rhodamine B were 38%, 63% and 79% (15.3–30.1 a cm−2) with non-catalyzed CF (NCF), NCF with Fe2+solution (Fe2+/NCF) and Fe@Fe2O2/NCF composite cathodes at closed circuit (1000 Ω), however, it improved to 49%, 64% and 95% (current density of 43.7–65.2 μA cm−2) at short circuit (0 Ω external resistor), respectively, in 12 h. Among homogenous form of iron(III) chloride hexahydrate (FeCl3·6H2O) and Iron(II) sulfate heptahydrate (FeSO4·7H2O) iron salts are mostly used and relatively cheaper than heterogeneous salts.40 But they may cause Fe sludge generation and require adjustment of low pH for Fenton reaction thereby making system more costly. Contrarily, Fenton reaction with heterogeneous iron salts35,162 such as goethite (α-FeOOH), magnetite (Fe3O4), maghemite (γ-Fe2O3), clino-pyrrhotite (Fe1−xS) or hematite (α-Fe2O3) can be highly efficient for FR and catalysis of pollutants in mesophilic soil and wastewater.193 Moreover, coating of C felt and graphite cathodes with γ-FeOOH composite,157 pyrrhotite,31 and Fe@Fe2O3 (ref. 194) proved to be slowly leaching out and discharging ferric or ferrous ions in cathodic solution. Carbon aerogel with iron and copper proved to be another effective modification of cathode Fenton reaction enhancing WWT containing dyes (MB).195 Such modification help control release of iron and decreases sludge generation and management cost.175
5 Types and operation models of microbial-electro-Fenton systems
In the last two decades, developments in MEFS have provided considerable scope for innovative efficient solutions for wastewater treatment. Such green multifaceted technology has shown great prospects7,22,23,196–198 though they are still under stages of research and development for large scale application. Studies have reported treatment of dyes and pigments through different MEFS that has been implemented in different configurations, with different membranes, mostly proton exchange membrane (PEM), cation exchange membrane (CEM), and through their integration with biological degradation of dyes. In most of the studies, most commonly treated dyes in MEF systems include; Congo red, orange G, orange II, rhodamine B, methyl orange, reactive black 5 Lissamine green B and crystal violet. Comparatively, orange II (Acid orange 7) is the most studied azo dye in the said systems.
MEF technology typically evolved as an extended version of MFCs and MECs, where apart from anodic (anaerobic) oxidation of organic compounds additional cathodic oxidative detoxification and decomposition of certain pollutants is carried out through highly reactive hydroxyl radicals generated in Fenton reaction. However, previous WWT processes including batch, sequential or continuous flow reactors also helped in innovating MEF technology. Extensive studies of MEFS are underway toward development of new designs for achieving ideal system performance. MFC-Fenton system is though less efficient but cost effective in terms of electrical and H2O2 outputs associated Fenton reaction for dyes treatment.30,154,199 Development of single chamber rather than double chamber considerably improved the energy out of the MFC system.200 MFC powered EFS has also gained advancement through integration of super-capacitor for bio-electricity storage for subsequent use in Fenton reaction.21,201 Considering treatment efficiency on priority compared to electrical energy outputs, MEC based Fenton process has shown greater prospects. Such system is highly efficient for treating high load of contaminates and is equally good to treat domestic and industrial wastewater at the same time. Still this system need an additional input of minor energy (0.2–0.8 V) although, it is about 100 times lower than conventional EFS.32 But the possibility that lies in usage of single chamber MFC to empower a two-chamber MEC-electro-Fenton system for treatment of persistent pollutants is another good option to avoid any external input electrical energy for self-sustainable.27 Before seeking industrial scale applications there are several other challenges that need to be addressed.
Microbial Reverse Electro-dialysis Cells (MRECs), Automated Microbial Fenton Cell (AMFC) are the most innovative in MEFS.32,183,202 The development of continuous or semi-continuous mode of reactors is highly required in order to further enhance these technologies at large commercial scales relying on previously developed anaerobic and MFC/MEC based reactors. MEFS technology have offered considerable opportunity of treating two different substrates (pollutants) or wastewater in two separate chambers of the same reactor.175 They have been studied for the removal of natural (biopolymers) and synthetic/recalcitrant compounds including azo dyes (Congo red,35 methylene blue,27 acid orange,173 orange II, rhodamine B), pesticides, heavy metals, phenol, trimethoprim, caffeine, sulfamethazine, and ranitidine.203,204 The efficiency of systems above varies with electrode material, microorganisms, pH, current density, cathode potential, and concentration of ferrous/ferric ions their homogenous and heterogeneous forms.
5.1 Classification of microbial-electro-Fenton reactors
MEFS can be classified based upon their configurations and mode of operations. There are operated as (i) single cell [e.g. MFC or MEC or MREC], (ii) double cell [MFC-AFT],29 and (iii) hybrid or sequential [EF and degradation of microbes].203 Most of them run under batch mode and only few under continuous modes.205,206 Besides, there are mostly laboratory scale reactors, and few pilot scale with none large scale.44 Considering MFC batch reactors as the bench mark, several modifications have been done in its configuration and fabricating material converting it into more efficient wastewater treatment and energy generating technology.207 For instance, Modification of C anode with polypyrole/anthraquinone-2,6-disulfonate cause the power density to increase, redox properties and associated bio-electo-catalysis of azo dye.174 Modification of carbon fibers with carbon nanotubes and polypyrole composite resulted in excellent biocompatibility and conductivity. Efficiency of modified anode in producing electricity is 2.63 times higher than that of unmodified ones, generating 1876.62 mW m−2 power density, and enhanced mineralization rate of orange II dye.183
5.1.1 Batch mode of operation. In batch mode, specified amount of waste liquors as anolytes and catholytes are treated for a stipulated period of time and then drawn out to revive the reactor.208 MFC or MEC reactors have been mostly used under batch mode reactors in various studies. Agitation is provided in the system using magnetic stirrer for the anolytes and catholytes.23 Aeration is maintained in a cathodic chamber by using commercial air pumps.209 Time span of treatment usually varies 2–10 days; however, it may exceed to 30 days. It purely depends upon the efficiency of the system with reference to specific waste type. For simple substrates generally it usually takes less time whereas for complex substrate longer time is required.207 However, major limitation of batch reactor is organic compound's mass transfer rate mass to microbes on anodic surface for biocatalysis and harnessing of electrons and protons to harvest cathodic H2O2 (ref. 50) for FR. However, depletion of nutrients in medium under batch mode may cause potential loses and inefficiencies in the systems.210 Table 2 shows details on different batch or sequential mode MEF reactors with their operational conditions and efficiencies for dyes wastewater treatments.
Table 2 Removal of dyes in different (batch or sequential) MEFS
Reactor configuration |
Anodic inoculum |
Cathode material |
Pollutants |
Concentration |
pH |
Amendments |
Power density |
Removal efficiency |
Operation time |
Reference |
MFC |
Shewanella decolorationis S12 |
CNT/PTEF/γ-FeOOH |
Orange II |
35 mg L−1 |
7 |
Synthesis of H2O2 in MFC using cathode as spectrographically pure graphite (SPG) |
25.13 mW m−2 |
100% |
43 h |
126 |
MFC |
Anaerobic sludge |
Graphite |
Acid blue 113 |
300 mg L−1 |
3 |
MEF was operated with effluents of constructed wetland |
3.5 A m−2 |
91.57% |
43 h |
94 |
Dual chamber MFC |
Shewanella decolorationis S12 |
Ppy/AQDS/carbon |
Orange II |
10 mg L−1 |
7 |
Modified electrodes used to enhance performance |
823 mW cm−2 |
97% |
7 h |
211 |
Dual chamber MFC |
Shewanella decolorationis S12 |
CNT/γ-FeOOH |
Orange II |
10 mg L−1 |
7 |
Modified electrodes used in dual chamber MFC |
230 W m−2 |
100% |
14 h |
92 |
MFC |
Glucose |
Spectrographic pure graphite (SPG) |
OrangeII, Amaranth |
75 mg L−1 |
7 |
Iron conc. Changes 1.14–3.43 mg L−1 & 0.1–1 mg L−1 |
25.13 mW m−2 |
82.59% |
1 h |
92 and 126 |
MFC |
Anaerobic sludge |
Graphite |
Amaranth |
75 mg L−1 |
3 |
Optimal cathode conditions were applied n cell for H2O2 production |
42.6 Am |
84.24% |
2 h |
167 |
MFC |
Brewery wastewater |
Fe@Fe2O3/NFC |
Rhodamine B |
15 mg L−1 |
3 |
The double chamber MFC was proposed by utilizing Fe@Fe2O3/carbon felt composite cathode |
307 mW m−2 |
95% |
12 h |
195 |
MFC (H-type) |
T.versicolor S.oneidensis |
Graphite rod |
Lissamine green B |
10 mg L−1 |
2 |
Combination of fungus and bacterium used |
1.2 W m−3 |
94% |
9 h |
212 |
MFC (H-type) |
T.versicolor S.oneidensis |
Graphite rod |
Crystal violet |
10 mg L−1 |
2 |
Combination of fungus and bacterium used |
1.2 W m−3 |
83% |
9 h |
212 |
Hybrid reactor of benthic MFC and EF |
Sewage sludge, marine sediments |
Graphite sheet |
Lissamine green B, reactive black 5, indigo carmine |
10 mg L−1, 20 mg L−1, 50 mg L−1 |
7 |
Marine sediment microbial fuel cell used to drive external electrochemical and electro-Fenton processes |
1033–1046 mV |
100% |
1 h |
36 |
MFC (hybrid cell) |
Sewage sludge |
Graphite sheet |
Reactive black 5 |
50 mg L−1 |
7.5 |
SMFC anode and electro-Fenton cathode connected with a salt bridge |
1033 mV |
88.2% |
15 min |
36 |
MFC (hybrid cell) |
Sewage sludge |
Graphite sheet |
Lissamine green B |
10 mg L−1 |
7.5 |
SMFC anode and electro-Fenton cathode connected with a salt bridge |
1034 mV |
98.2% |
15 min |
36 |
MFC (hybrid cell) |
Sewage sludge |
Graphite sheet |
Crystal violet |
5 mg L−1 |
7.5 |
SMFC anode and electro-Fenton cathode connected with a salt bridge |
1046 mV |
96.2% |
15 min |
36 |
MFC (hybrid cell) |
Sewage sludge |
Graphite sheet |
Indigo carmine |
20 mg L−1 |
7.5 |
SMFC anode and electro-Fenton cathode connected with a salt bridge |
1045 mV |
97.2% |
15 min |
36 |
MFC (hybrid cell) |
Sewage sludge |
Graphite sheet |
Poly R-478 |
80 mg L−1 |
7.5 |
SMFC anode and electro-Fenton cathode connected with a salt bridge |
1035 mV |
19.1% |
15 min |
36 |
MFC |
Shewanella decolorationis S12 |
Ppy/AQDS/carbon |
Orange II |
70 mg L−1 |
7 |
Modified electrodes used in dual chamber MFC |
823 mW cm−2 |
100% |
50 h |
174 |
MFC powered advanced FS |
Anaerobic sludge |
Carbon felt |
Acid orange 7 |
50 mg L−1 |
3 |
MFC was combined with Fenton-like technology to simultaneously generate electricity and degrade dye |
15.9 W m−3 |
89% |
60 h |
204 |
MFC |
Anaerobic sludge |
Fe2O3/ACF |
Methyl orange |
5 mg L−1 |
2 |
Composite Fe2O3/ACF electrode was used |
268.10 mW m−3 |
86.7% |
12 h |
213 |
MFC |
Anaerobic sludge |
Graphite rod |
Congo red |
100 mg L−1 |
7 |
MFC and a COR reactor were integrated together |
808.3 mW m−3 |
90% |
72 h |
35 |
MFC |
Domestic wastewater |
FePc/CNT/SS316 |
Reactive black 5 |
50 mg L−1 |
7 |
Composite cathode is used |
726.55 mW m−2 |
80% |
12 h |
171 |
MFC |
Anaerobic sludge |
Graphite rod |
Acid blue113 |
100 mg L−1 |
3 |
Graphite cathode was treated with nitric acid |
36.438 mW m−2 |
71.36% |
12 h |
17 |
MREC |
Domestic wastewater |
Graphite |
Orange G |
400 mg L−1 |
2 |
Salinity gradient energy drove the microbial-electro-Fenton process |
2 A m−2 |
100% |
10 h |
32 |
3D-EF-MFC |
Anaerobic sludge |
Activated carbon |
Methyl orange |
100 mg L−1 |
3 |
MFC coupled with 3D electro Fenton technique |
566 mW m−3 |
84% |
72 h |
183 |
MFC-MEC |
Domestic wastewater |
Graphite |
Methylene blue |
50 mg L−1 |
3 |
MFC as renewable power source used to power MEC-electro-Fenton process |
50.1 mW m−2 |
97% |
16 h |
27 |
MFC power |
Anaerobic sludge |
Graphite plate |
Acid orange 7 |
16 mg L−1 |
6 |
A novel heterogeneous EAFL system driven by MFC used |
54.02 mW m−2 |
96.4% |
2 h |
214 |
MEF-COR |
Glucose |
Graphite rod |
Congo red |
20 mg L−1 |
7 |
Integration of MEF with catalytic oxidation system |
808.3 mW m−3 |
90% |
72 h |
35 |
MFC-AFT |
Anaerobic sludge |
Iron plate with carbon paper |
Acid orange 7 |
400 mL (0.16 M NaCl) |
3 |
External addition of 2 mM H2O2 and 0.3 mW power output |
0.27 mW |
85% |
— |
173 |
Automatic MEFS |
Electroactive biofilm |
Carbon impregnated iron oxide |
Acid orange 7 |
50 mg L−1 |
7 |
Microchannel-structured carbon enlivened with iron oxides utilized as electro-Fenton cathode |
— |
93–96% |
24 h |
202 |
5.1.1.1 One step (in situ) integrated process. One step integrated process involves a single MFC/MEC or MREC reactor, generating electrical potential for cathodic Fenton process. It is classified into following types based upon their configurations or designs.
5.1.1.1.1 MFC based electro Fenton system (MFC-EFS).
MFC-EFS is basically a two chamber MEFS with in situ FR system in cathode. It can mineralize biodegradable organics in anodic chamber, and recalcitrant organic pollutants (dyes, pesticides) in cathodic chamber through Fenton reaction (FR) or electro-chemical Fenton (EF) treatment shown in Fig. 7A.174 MFC-EFS reactors are cost-effective than Electro Fenton (EF) processes because they are energy generating rather than consuming. Besides they also generate quantifiable amount of hydroxyl radical from FR for decomposing pollutants.17
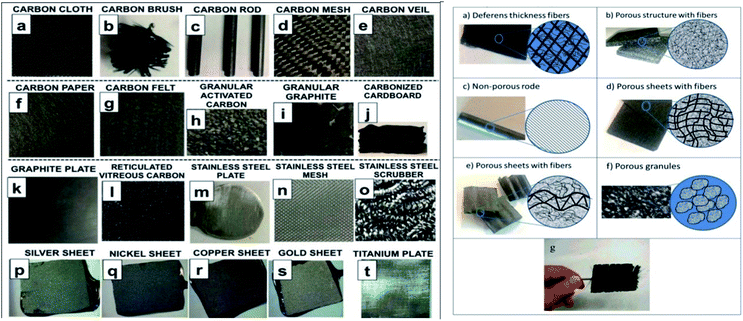 |
| Fig. 5 Different anode material used in MEFS (adopted from ref. 184 and 185). | |
5.1.1.1.2 Automatic microbial electro-Fenton system (AMEFS).
A three-dimensional micro and macro-porous geometrical electrode provides large ratio of surface area to volume for biofilm development and electrolyte or substrate diffusion for efficient MEFS shown in Fig. 6.215,216 AMEFS is highly innovative and workable development in MEFS for on situ remediation of dyes and other related pollutants in water, soil or sludge. It is fabricated with microchannel-structured carbon impregnated iron oxides cathode for EF reaction and with an additional but similar anode for biofilm bio-catalysis in a two-electrode configuration connected by an external circuit. The second configuration of AMEFS includes a similar but single-electrode configuration serving both as bioanode and cathode. AMEFS is a spontaneously driven system similar to natural transpiration system in plants. The highest degradation efficiency (93–96%) at 50 ppm is generated at the condition of short-circuit with two-electrodes and that was comparable to single-electrode configuration. Such a system can be easily installed for sludge and soil purification by directly inserting microchannel structured carbon electrodes in the contaminated site or reactor.202 Furthermore AMEF is equally good to operate under batch or continuous mode operations.
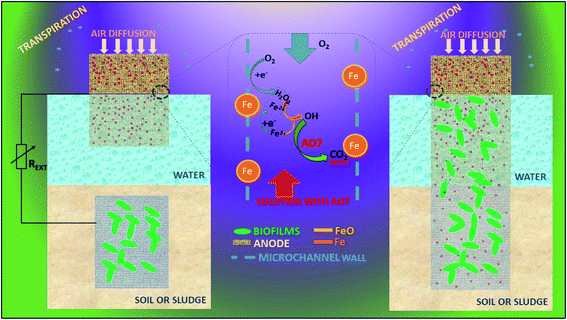 |
| Fig. 6 Automatic microbial electro-Fenton system (AMEFS) (refabricated from ref. 202). | |
5.1.1.1.3 Other novel designs.
MECs an extended version of MFC with small input of charge (0.2–0.8 V) (Fig. 7B) has proved to be yielding H2O2 several time higher than MFCs. Therefore, MEC electro Fenton reactor can be suitable for treating wastewater that contains comparatively excessive loads of pollutants in both anodic and cathodic chambers with remarkably lower energy consumption than classical electro Fenton process.217 This system was efficiently used for azo dye WWT.32 Besides, it uses (approx low cost 25.93 kW h kg−1-TOC) an average of 75% (17 fold) less energy as compared to the regular electro-Fenton process (45.8–865 kW h kg−1 TOC).218,219 The degradation efficiency of TOC was found to be 93.1%. The larger removal at the short circuit leads to larger current density of 43.7–65.2 μA cm−2.195
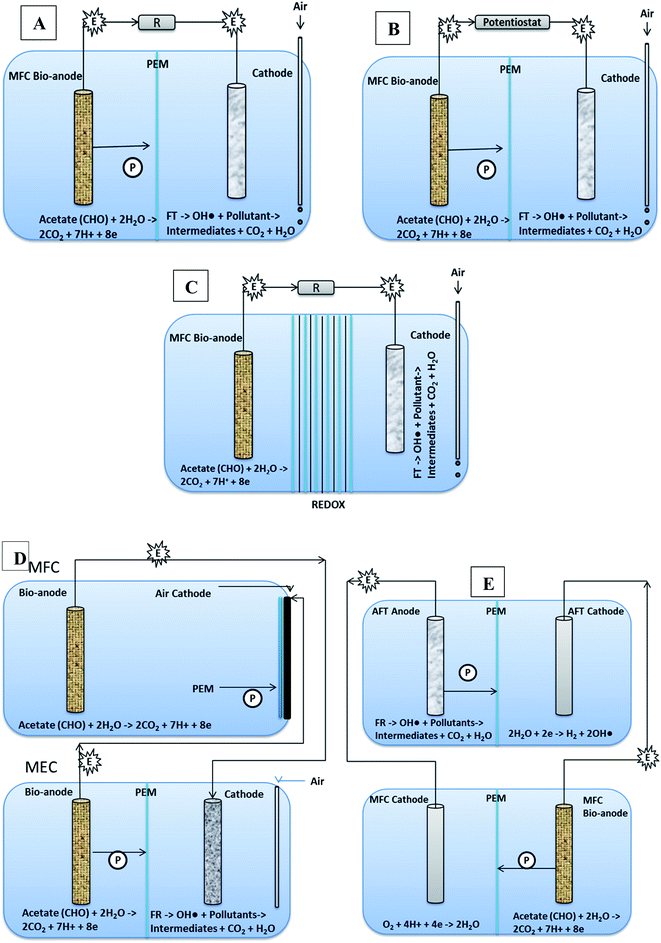 |
| Fig. 7 Removal of dyes in different batch MEFS (A) MFC-electro Fenton system (B) MEC-electro Fenton system (C) MREC-electro Fenton system (A–C single cells) (D) MFC-MEC-electro Fenton system (double cell) (E) MFC assisted AFT (double cell). | |
MFC-3D EF is originally an MFC reactor but filled with granular AC either in both anode and cathode chambers or in cathode chamber as electrodes. The bed electrodes played an arbiter job in cathode and anode chambers, elevating the output voltage and power density, and lost cause internal impedance to get lowered. Dye evacuation efficiency is observed to be 84%.183
Microbial reverse electro-dialysis cells (MREC) is a novel hybrid bio-electro-chemical system for efficient H2O2 production through in situ electric energy generation by the microbial oxidation of biodegradable matters and salinity-slope that is between different fresh and salt channels and does not require power input (Fig. 7C). The cathodic and anodic chambers are separated with RED stacks and the reaction of cathode is not affected by the continuous flow of wastewater in anode chamber.32 It proved to be highly efficient in comparison with MFC and MEC with dye removal efficiency up to 99%. Moreover, the cost of the treatment proved to be lower (25.93 kW h kg−1 TOC) by ≥ 45% than other Fenton processes (45.8–865 kW h kg −1 TOC).218,219
Using MFC as renewable energy source to power MEC Fenton process (Fig. 7D), electricity can be saved. But removal efficiency of pollutants and power density is found to be low as compared to traditional Fenton processes.27
MFC-AFT is a two cells system; where anodic Fenton reaction based treated of pollutants occurs in chemical cell supported by electronic energy harnessed from bio-anodic compartment of another MFC (Fig. 7E). Kinetic studies indicated that this system had higher pseudo-first order rate constant than other conventional Fenton processes and 87% of the dye was degraded in AFT system within 15 minutes. According to electrochemical analysis, the corrosion of iron was not hindered by dye. It was also revealed that MFC power density was improved by increasing dissolved oxygen in cathode compartment, which resulted in increased degradation of dye.173
5.1.1.2 Sequential or hybrid process. Sequential MEFS is a two-step sequential treatment of refractory compounds through pre or post EF oxidation with biological method in order to achieve a comprehensive efficiency shown in Fig. 8. The span of EF is minimized in order to keep the system cost effective. However, the type of effluent and its priority pollutant helps in deciding whether EF should be used as pre-treatment or post-treatment in conjugation with biological methods. EF as pre-treatment, involves hydroxyl radicals for oxidative mineralization of refractory compounds or into aliphatic by-products that may be sometimes toxic.220 Later biological process completely removes any remaining short chain compounds.159,221,222 EF-microbial oxidation proved to be effective treatment strategy for real textile wastewater. If EF is applied as post treatment then it helps complete decomposition of toxic and mutagenic aromatic by-products of compounds like azo dyes such as alpha-napthol or sulfanilic acid that are stable specifically under anaerobic biological condition.21,223 Selection of treatment strategy still greatly depends upon the nature of dyes. Previously, an EF-biological (aerobic) (yeast) process helped to degrade reactive black 5 dye 91%.224 EF and aerobic-microaerophilic process when combined removed almost 85% color and COD with 56% TOC of textile wastewater. Whereas, 52.7% color, 82.5% COD, and 41% TOC were observed when EF-aerobic microbial process was used. Moreover, dyes removal rates improved to >95% with 85% of TOC in a bubble column MFC reactor coupled ex situ EF process.36,153 The dyes wastewater usually contain many organic compounds beside of dyes. Some pretreatment e.g. coagulation, precipitation may be essential to improve dyes removal. Therefore, integrated process based on MEFT would be useful for dye wastewater treatment. Afanga et al. reported the sequential treatment of dye wastewater employing the integrated coagulation-electro Fenton process. The system achieved remarkable removal of organic matter along with dye degradation. The results revealed the removal of COD, TOC, and TSS up to 97%, 98% and 98% respectively.225
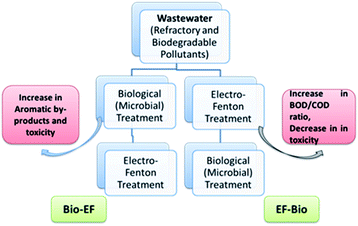 |
| Fig. 8 Sequential treatment of refractory compounds (dyes) through biological and EF/EAOP. | |
5.1.2 Continuous mode of operation. In continuous mode reactors, the substrate (anolytes or catholytes) is continuously charged along with discharge of products simultaneously during upstream and downstream processing. Such systems are more dynamic and overcome the issues of mass transfer rates (coefficient) and nutrients depletion226,227 through constant flow and agitation provided.23 Current density obtained by continuous MFC was 2 times more than that obtained from MFC operated under batch mode.207 Continuous mode has higher efficiency in mass transfer and heat transfer and are less spacious than batch mode.228 In addition, continuous operation allows the usage of extreme conditions that aids to improve yield, continuous can allow up to 300° and 30 bar of temperature and pressure. Moreover, continuous process is easier, flexible, and faster to scale up than that of batch process.Previously, different continuous flow reactors viz. Airlift229 Fluidized bed reactor, bubble reactor, Tubular,230 Plug flow,226,231 MFC, MDC and MEC [MFC-MEC, MFC-membrane232 were used based upon either microbial or electro-chemical processes for treatment of different pollutants (Table 3). Such reactors provided a solid platform for development of any continuous MEF reactors. Fig. 9 shows the various continuous flow reactors.
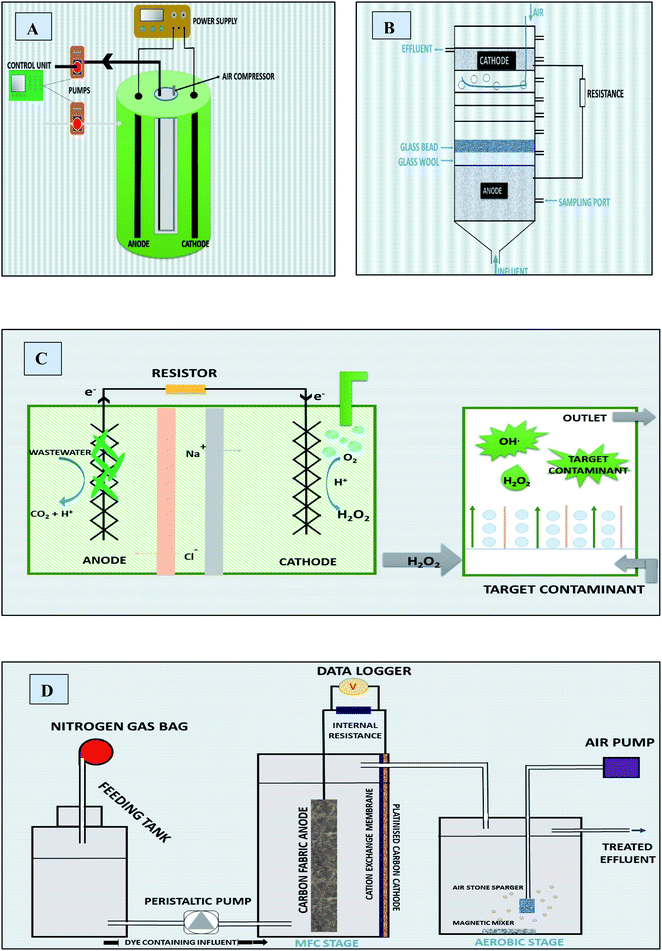 |
| Fig. 9 Continuous operated reactors (A) schematic diagram of Airlift continuous reactor with electro Fenton setup (refabricated from ref. 229) (B) schematics diagram of mediator-and membrane-less MFC column reactor (refabricated from ref. 240) (C) microbial desalination reactor (refabricated from ref. 175) (D) schematic of integrated MFC-aerobic system (refabricated from ref. 153). | |
5.1.2.1 MFC and MEC. Earlier MES studies reported both partial and almost complete azo dyes degradation (e.g. acid orange-7, etc.)233 in batch and continuous flow integrated MFC (-aerobic system) and MEC (-membrane).153 Single-chamber MFCs or membrane-less MFCs are favored over double chamber even for large scale WWT.234 Moreover, single chambered MFC tubular or inner circular electrodes proved to be superior for efficient treatment of azo dyes. Integration of Fenton process in MFC holds the greater potential of efficient degradation and detoxification of the dyes through maintaining maximum cathode half-cell potential for higher production of H2O2. Recently, a pilot scale (20 L) two chamber rectangular MEF reactor was developed to treat dyes WWT under continuous mode.44
5.1.2.2 Microbial desalination cell (MDC). A microbial desalination cell (MDC) is one of the most innovative modified version of MFC containing a desalination compartment sandwiched between CEM and AEM for separating it from cathode and anode chambers respectively. MDC is capable of simultaneous WWT and desalination with minor input of energy.173 Charge balance is maintained by salt ions migration from desalination chamber to cathode and anode by ion exchange membranes.117 MDC-MEF hybrid system, comparatively a novel approach, could be employed for the efficient removal of dyes from wastewater. Huang et al. reported application of MEF integrated MDC for increased degradation of methylene blue. The system reached maximum; power density of 566 mW m−3 and H2O2 of 24.07 g per m3 per day with degradation efficiency up to the 82.8% under the influence of Fenton reaction. Without which the system was capable to attain only 53% efficiency.183 Comparison in performance of a MEFS was investigated by switching MDC batch mode to continuous. System demonstrated a maximum power density of 15.9 W m−3 in continuous and 13.9 W m−3 in batch mode. Additionally, 83.7% of COD was eliminated in the continuously fed system at two days hydraulic retention time, and it was 13.8% more than that obtained under a two days batch system. It was demonstrated that enrichment of ARB and high mass transfer under continuous flow and feeding condition might have improved the system performance.207,228
Table 3 Characteristics of continuous mode reactors
Reactor configurations |
Inoculum |
Pollutants |
Operational parameters |
Hydraulic Retention time |
Applied-voltage/current |
Efficiency |
References |
Two chambers having 10 L each, anode: Carbon fiber brush, cathode: graphite plate |
Domestic waste water |
Methylene blue |
Aeration rate of 350 mL min−1, 20 mg L−1, pH 2, Fe2+ of 0.2 mM, applied voltage 0.4 V |
28 h |
0.2 V |
95% dye decolorization 89% TOC removal |
44 |
SMFC, electrodes: Graphite sheet |
Marine sediment |
Lissamine green |
Na2SO4 0.01 mol L−1, iron concentration 150 mg L−1 |
1 h |
— |
97–99% decolorization |
36 |
Cylindrical reactor containing two electrodes at the center, cathode: modified graphite with carbon nanotubes, anode: Graphite |
Dye solution |
C.I. acid red 14 (a), C.I. acid blue 92 (b) |
NaCl: 1 g L−1, 0.05 mM Fe3+, pH: 3, aeration 10 mg L−1 dye, effective volume 1 L, flow rate: 0.33 L h−1 |
— |
0.14 A |
86.78% COD removal in 60 min, pollutant degrading efficiency 91.22% (a) 93.45% (b) |
235 |
Microbial fuel cell MFC (H type) |
T. versicolor and S. oneidensis MR-1 |
Lissamine green B, crystal violet |
Graphite rod used as anode, dye conc. 10 mg L−1, pH 2, iron concentration 150 mgL−1 |
— |
— |
94% Lissamine green B, 83% crystal violet after 9 h treatment time |
212 |
Fluidized bed reactor, cathode: nickel foam layered with iron-chitosan, anode: graphite sheet |
Dye solution |
Lissamine green B |
pH 2, 0.15 L working volume, 0.01 M, Na2SO4, 100 mg L−1 dye, mixing by continuous air flow at 0.15 vvma |
45 min and 90 min |
5 V |
75% TOC removal, dye degradation efficiency 95% |
236 |
Cylindrical glass reactor, electrodes: graphite bar |
Dye solution |
Lissamine green B (a) reactive black 5 (b) |
pH = 2, 22 °C, catalyst 115 g Fe alginate gel beads made of sodium alginate, Bacl2, Fe2(SO4)3, air bubbling near cathode at 1.5 L min−1, working volume 1.5 L |
6 h (a), 12.5 h (b) |
3 V |
TOC removal 81% (a), % (a), 87% (b) |
229 |
Cylindrical glass reactor. Electrodes: graphite sheet |
Dye solution |
Lissamine green B (a) azure B (b) |
Catalyst: 8.69 g Fe alginate beads, air bubbling near the cathode at 1Lmin−1, working volume 0.15 L, pH=2 |
30 min |
14.19 V |
TOC removal 93% (a) 89% (b) |
237 |
Bubble reactor formed of cylindrical glass, electrode: graphite |
Dye solution |
Lissamine green B, methyl orange, reactive Black 5, Fuchsin acid |
0.04 M Na2SO4, 8.5 mg L−1 (LGB), 1.5 mg L−1 (MO), 70 mg L−1 (RB5), 15 mg L−1 (FA), pH=2, bubbling compressed air at L min−1, 0.675 L working volume |
21 hour |
15 V |
47% TOC removal, 43% dye removal |
238 |
Bubble glass column reactor, electrodes: graphite |
Textile wastewater |
Rhodamine B |
pH 3, catalyst: FeCl3 at 5 mg L−1, 3 L of electrolyte at 10 mL min−1 |
8 h |
3.5 V |
98% dye - removal |
239 |
5.1.2.3 Hybrid cell: sediment MFC (SMFC) or benthic MFC (BMFC). Benthic or Sediment MFC (BMFC or SMFC) assisted FR and BMFC-FR hybrid processes also highlights importance of continuous or semi-continuous cost effective wastewater treatments.
6 Feasibility of scaling up of MEFS and cost benefit analysis
Current developments on MEFS propose innovative energy efficient solutions for dyes and industrial WWT in near future.21 Most of the MEF studies that are conducted so far are at lab scale, relying upon MFC and MEC configurations.44 The greatest driver in up-scaling of MEFS would be MFC/MEC based multifaceted reactors that work on the principles of harnessing renewable energy from WWT to minimise the capital cost.59 Initial advancement in MFC or MEC at pilot scale integrating EF reactors by addressing previously reported drawbacks could be the benchmark for further developments. Nevertheless, some reports outlined the practicality of the said technology for direct/or indirect power generation from wastewater at volumes exceeding those in lab scales MEC241 and MFC.176,242–245 Comparatively, WWT capacity of MEC based MEF system proved to be much greater than that of MFC based system.27 A very recent study mentioned up-scaling of MEC (0.4 V) based MEFS of 20 L for the treatment of dye WW using C fibre brushes as anode and graphite plate and silver/silver chloride as cathode with Fe2+ 0.2 mM and Na2SO4 50 mM. Almost 100% removal of methylene blue dye was observed after 8 hours treatment. Likewise the dyes and TOC removal rates were 100%, 70–90% in case of Meldola's blue (MeB), Toluidine blue (TB), Orange G (OG) and Rhodamine 6G (Rh6G) and Rhodamine B (RhB) after 28 hours respectively44 Overall, complete mineralisation of dyes was significantly less compared to their decolorization and it has been related to their complex aromatic structure and high molecular weight. Other studies on lab scale MEFS reported that for MB removal, the Kapp was 0.43 h−1 and KTOC was 0.22 h−1, while compared to Orange II, Kapp was 0.212 h−1 and KTOC was 0.0827 h−1.174 Thus, the results explained that scaled-up MEFS has higher efficiency than that of MEFS operated at lab scale for the treatment of dyes containing wastewater.
Prior studies have revealed that MEF technology is a cost-effective substitute to traditional EF technology for the treatment of dye wastewater with energy consumption of only 25.93 kW h (kg TOC)−1.32,39 But for large scale application, cost benefit analysis of MEF systems is vital for its feasibility in dyes and industrial WWT.44 MFC based MEFS are facing technical and cost challenges for commercial viability at large scale. Moreover, improving the performance and reducing the capital costs of reactor and its operation need to be addressed. System scaling-up requires extensive studies on the reactors' designs and material and operational variables, typically related to continuous in situ regeneration of catalyst i.e. Fe2+, and H2O2 in order to prevent sludge formation.21 So, primarily, the design of bio-reactor is extremely important for optimum functioning and then up-scaling. Initial modeling through computer simulated program of MEFS is highly important as an effective tool for reactor configuration.246 The major cost based variables include electrodes and membranes (CEM/PEM). Specifically, the cost of the membranes sometimes cost an about 38% of the total cost of the reactor. For instant, Nafion membrane cost around 2500 $ per m2.247 And is 37 fold higher than sulfonated biochar (SBC)-600 with PVA membrane costing 77 $ per m2. Contrarily, per unit cost of SBC-600 membrane for proton conductivity was 0.42 S per cm per $ and that proved to be 32 times greater than Nafion membrane (1.31 × 10−2 S per cm per $). Likewise, the estimated standardized energy reclamation for SBC based MFC was much lower i.e., 0.014 kW h m−3 (6.356 kW h kg COD−1) than Nafion based MFC (0.024 kW h m−3 (9.59 kW h kg COD−1) system.248 Additionally, GORE-TEX membrane has been reported quite cheaper and costing an about 21 $ per m2 and besides, the PVA modified membranes has been reported equally cost-effective.247 The electrodes do a crucial job in electricity generation and a main factor in deciding the implementation of the MFC technology at a large level. Different materials ranging from non-corrosive stainless steel to versatile carbons have been investigated as anodes in different structures and shapes.249 The cost of C clothes varies from $ 100–1000/m−2, Still, cheap carbon mesh based electrodes costing an about $10–40/m−2 can also be another good alternative to of carbon cloth.250 Moreover, the cost of cathode increases when it is modified metal catalysts [e.g., FeSO4 cost = $13782/kg and FeOOH cost = $ 826/kg]251 to apply in MEFS. In this case possibility of using scrap iron waste and the wastewater originating from steel and mining industry could be a good source of iron in cathode for Fenton reaction.251,252 In the similar situation, usage of non-polished graphite over carbon might increase the microbial adhesion over anode and will be cost-effective for huge-scale operation. Recently cheaper such as activated carbon and metal mesh showed oxygen reduction performance.247 Usage of graphite coated with metal as cheaper electrode material and carbon felt results in better performance and electron transfer because of their low cost, good conductivity and huge surface area in contrast to other expensive materials.253–255 Bio-electricity production in system (e.g., MEC-MEF) through microbial bio-catalysis of organic compounds cut down energy budget by almost 40–50%.252 When the MEF process run without external energy than the normal electrical energy budget was 11
526.6 kW h (kg TOC−1) with respect to TOC removal costing US$ 2420.59. The higher cost relates to higher energy consumption and lower efficiency in MFC based MEF process requiring more reaction time and aeration costs. However, MEC based system requires a small input (0.2–0.8 V) of electricity in order to generate H2O2 in cathode at much high rate as compared to the MFCs. The production of H2O2 requires much lower energy i.e., 0.93 kW h kg-H2O−1 with a cost price of US$ 0.195 in MECs compared to traditional electrochemical process20,27 Still only small amount of electrical energy was directly applied i.e. 5.96 kW h (kg TOC)−1 with a cost of US$ 1.25,44 and it was considerably low in comparison to the traditional EF processes.256,257 Besides, the energy budget of MEC based MEF system is highly economical considering the in situ bioelectricity generation by microbes that reduces the electrical energy consumption [0.728 kW per h per kg for aniline) may be hundred times lower than conventional electro Fenton process (74 kW h kganiline−1).217 The approximate capital cost of MES (MFC and MEC) reactors were reported to be $100,000/ton COD × day and $1220/ma3.258,259 MREC-Fenton system has been reported to treat azo dyes (Orange G) containing wastewater with a cost of US$ 5.44 for 25.93 kW h (kg TOC)−1 which is very less as compared to traditional EF processes costing US$ 9.6–179.76 for 45.8–865 kW h (kg TOC)−1.21,218,219 The substitution of electrical energy from power grid to the renewable salinity gradient for direct driving of Fenton process is the main advantage of MREC-Fenton system.
Previously MEFS were mostly tested with artificial WW, so there is a need to operationalize the reactors with real wastewaters. At laboratory stage it was 0.25 kW h m−3 or 0.40 kW per h per kg of COD/0.18 kW h m−3 and 0.12 kW per h per kg of COD in terms of energy consumption for the reactors with pure substrates such as acetate and glucose respectively and was significantly higher compared to domestic [0.04 kW h m−3 or 0.17 kW per h per kg of COD] or industrial [0.01 kW h m−3 or 0.04 kW per h per kg of COD] wastewaters.243 But systems performance was still lower in power density that could be insufficient enough for large scale industrial plants.260 So there is a need to optimize the MEFS with real WW to apply it at large scale. Moreover, life cycle assessment of the most efficient microbial-electron-Fenton systems is vital to operationalize them at commercial level.261
7 Conclusions
Microbial electro Fenton technology for dye wastewater treatment have emerged as scientific inquisitiveness and are proved to be innovative, multidimensional approach that can be operated under batch and continuous mode where chances of treating domestic and dye wastewater can go side by side. Comparatively, the system is preferable to other methods due to its higher efficiency in terms of time and treatment. Characteristics, classification, environmental fate, toxicity and degradation mechanism of dyes have been assessed critically. Various types and operational models of MEFS for dyes wastewater treatment have also been reviewed. MFC being a platform technology has been greatly explored. In past, MFC based MEFS studies have shown to reduce the operational time from days to hours, even minutes, along with mineralization rate up to 90% and even above in case of dyes. Being an innovative technology, dual advantages of electricity production along with dye decolorization simultaneously have also been reported by in situ-designed MFC based Fenton process and generated electricity has been utilized to run ex situ Fenton process in continuous and batch operations. The scope of technology has broadened as it is heading toward bio-monitoring, paving way for upcoming competitive approaches. Despite promising, it still faces several challenges of reactor configuration, high electrode/membrane cost, iron toxicity and information on large scale application. Therefore, extensive research and investigation is indispensable for future exploration and upgradation.
In future studies, there could be an opportunity of replacing chemical catalyst by biological catalysts produced by microorganisms in cathode chamber to accelerate and improve the pollutant treatment. This can mitigate the predicament of iron toxicity along with the provision of other beneficial opportunities.
Conflicts of interest
There are no conflicts to declare.
References
- M. Berradi, R. Hsissou, M. Khudhair, M. Assouag, O. Cherkaoui and A. El Bachiri, et al., Textile finishing dyes and their impact on aquatic environs, Heliyon, 2019, 5(11), e02711 CrossRef PubMed.
- V. San, V. Spoann and J. Schmidt, Industrial pollution load assessment in Phnom Penh, Cambodia using an industrial pollution projection system, Sci. Total Environ., 2018, 615, 990–999 CrossRef CAS PubMed.
- P. Nidheesh, M. Zhou and M. A. Oturan, An overview on the removal of synthetic dyes from water by electrochemical advanced oxidation processes, Chemosphere, 2018, 197, 210–227 CrossRef CAS PubMed.
- P. R. Sahoo, K. Prakash and S. Kumar, Light controlled receptors for heavy metal ions, Coord. Chem. Rev., 2018, 357, 18–49 CrossRef CAS.
- B. Lellis, C. Z. Fávaro-Polonio, J. A. Pamphile and J. C. Polonio, Effects of textile dyes on health and the environment and bioremediation potential of living organisms, Biotechnol. Res. Int., 2019, 3(2), 275–290 Search PubMed.
- Z. Carmen and S. Daniela, Textile organic dyes-characteristics, polluting effects and separation/elimination procedures from industrial effluents-a critical overview, IntechOpen Rijeka, 2012 Search PubMed.
- M. Hassan, A. S. Fernandez, I. San Martin, B. Xie and A. Moran, Hydrogen evolution in microbial electrolysis cells treating landfill leachate: Dynamics of anodic biofilm, Int. J. Hydrogen Energy, 2018, 43(29), 13051–13063 CrossRef CAS.
- S.-L. Lim, W.-L. Chu and S.-M. Phang, Use of Chlorella vulgaris for bioremediation of textile wastewater, Bioresour. Technol., 2010, 101(19), 7314–7322 CrossRef CAS PubMed.
- M. Hassan, H. Wei, H. Qiu, Y. Su, S. W. H. Jaafry and L. Zhan, et al., Power generation and pollutants removal from landfill leachate in microbial fuel cell: variation and influence of anodic microbiomes, Bioresour. Technol., 2018, 247, 434–442 CrossRef CAS PubMed.
- E. Brillas, I. Sirés and M. A. Oturan, Electro-Fenton process and related electrochemical technologies based on Fenton's reaction chemistry, Chem. Rev., 2009, 109(12), 6570–6631 CrossRef CAS PubMed.
- N. Chaukura, W. Gwenzi, N. Tavengwa and M. M. Manyuchi, Biosorbents for the removal of synthetic organics and emerging pollutants: opportunities and challenges for developing countries, Environ. Dev., 2016, 19, 84–89 CrossRef.
- D. Bhatia, N. R. Sharma, J. Singh and R. S. Kanwar, Biological methods for textile dye removal from wastewater: A review, Crit. Rev. Environ. Sci. Technol., 2017, 47(19), 1836–1876 CrossRef CAS.
- S. N. Banu, Comparative Study Of Photocatalytic Degradation Of Methylene Blue And Methyl Orange In Presence Of Solar Light Using Green Synthesized Cuo nanocatalyst, International Journal of Engineering Applied Sciences and Technology, 2019, 4(8), 365–370 CrossRef.
- J. J. Pignatello, E. Oliveros and A. MacKay, Advanced oxidation processes for organic contaminant destruction based on the Fenton reaction and related chemistry, Crit. Rev. Environ. Sci. Technol., 2006, 36(1), 1–84 CrossRef CAS.
- F. Sun, H. Liu, B. Liang, R. Song, Q. Yan and A. Wang, Reductive degradation of chloramphenicol using bioelectrochemical system (BES): a comparative study of abiotic cathode and biocathode, Bioresour. Technol., 2013, 143, 699–702 CrossRef CAS PubMed.
- M. T. Yagub, T. K. Sen, S. Afroze and H. M. Ang, Dye and its removal from aqueous solution by adsorption: a review, Adv. Colloid Interface Sci., 2014, 209, 172–184 CrossRef CAS PubMed.
- A. Asghar, A. A. A. Raman and W. M. A. W. Daud, Challenges and recommendations for using membranes in wastewater-based microbial fuel cells for in situ Fenton oxidation for textile wastewater treatment, Rev. Chem. Eng., 2015, 31(1), 45–67 CAS.
- F. Yu, M. Zhou and X. Yu, Cost-effective electro-Fenton using modified graphite felt that dramatically enhanced on H2O2 electro-generation without external aeration, Electrochim. Acta, 2015, 163, 182–189 CrossRef CAS.
- S. Saroj, K. Kumar, N. Pareek, R. Prasad and R. P. Singh, Biodegradation of azo dyes Acid Red 183, Direct Blue 15 and Direct Red 75 by the isolate Penicillium oxalicum SAR-3, Chemosphere, 2014, 107, 240–248 CrossRef CAS PubMed.
- Y. Mu, K. Rabaey, R. A. Rozendal, Z. Yuan and J. Keller, Decolorization of azo dyes in bioelectrochemical systems, Environ. Sci. Technol., 2009, 43(13), 5137–5143 CrossRef CAS PubMed.
- X. Li, S. Chen, I. Angelidaki and Y. Zhang, Bio-electro-Fenton processes for wastewater treatment: Advances and prospects, Chem. Eng. J., 2018, 354, 492–506 CrossRef CAS.
- V. Kiran and B. Gaur, Microbial fuel cell: technology for harvesting energy from biomass, Rev. Chem. Eng., 2013, 29(4), 189–203 CAS.
- M. Hassan, N. Pous, B. Xie, J. Colprim, M. D. Balaguer and S. Puig, Employing Microbial Electrochemical Technology-driven electro-Fenton oxidation for the removal of recalcitrant organics from sanitary landfill leachate, Bioresour. Technol., 2017, 243, 949–956 CrossRef CAS PubMed.
- W. Wang, Y. Lu, H. Luo, G. Liu, R. Zhang and S. Jin, A microbial electro-Fenton cell for removing carbamazepine in wastewater with electricity output, Water Res., 2018, 139, 58–65 CrossRef CAS PubMed.
- H. Wang and Z. J. Ren, A comprehensive review of microbial electrochemical systems as a platform technology, Biotechnol. Adv., 2013, 31(8), 1796–1807 CrossRef CAS PubMed.
- B. E. Logan, M. J. Wallack, K.-Y. Kim, W. He, Y. Feng and P. E. Saikaly, Assessment of microbial fuel cell configurations and power densities, Environ. Sci. Technol. Lett., 2015, 2(8), 206–214 CrossRef CAS.
- Y. Zhang, Y. Wang and I. Angelidaki, Alternate switching between microbial fuel cell and microbial electrolysis cell operation as a new method to control H2O2 level in Bioelectro-Fenton system, J. Power Sources, 2015, 291, 108–116 CrossRef CAS.
- S. H. Lin and C. C. Chang, Treatment of landfill leachate by combined electro-Fenton oxidation and sequencing batch reactor method, Water Res., 2000, 34(17), 4243–4249 CrossRef CAS.
- X. Zhu and J. Ni, Simultaneous processes of electricity generation and p-nitrophenol degradation in a microbial fuel cell, Electrochem. Commun., 2009, 11(2), 274–277 CrossRef CAS.
- R. A. Rozendal, E. Leone, J. Keller and K. Rabaey, Efficient hydrogen peroxide generation from organic matter in a bioelectrochemical system, Electrochem. Commun., 2009, 11(9), 1752–1755 CrossRef CAS.
- X. Zhu and B. E. Logan, Using single-chamber microbial fuel cells as renewable power sources of electro-Fenton reactors for organic pollutant treatment, J. Hazard Mater., 2013, 252, 198–203 CrossRef PubMed.
- X. Li, X. Jin, N. Zhao, I. Angelidaki and Y. Zhang, Novel bio-electro-Fenton technology for azo dye wastewater treatment using microbial reverse-electrodialysis electrolysis cell, Bioresour. Technol., 2017, 228, 322–329 CrossRef CAS PubMed.
- X. Li, I. Angelidaki and Y. Zhang, Salinity-gradient energy driven microbial electrosynthesis of hydrogen peroxide, J. Power Sources, 2017, 341, 357–365 CrossRef CAS.
- A. Asghar, A. A. Abdul Raman and W. M. A. W. Daud, Recent advances, challenges and prospects of in situ production of hydrogen peroxide for textile wastewater treatment in microbial fuel cells, J. Chem. Technol. Biotechnol., 2014, 89(10), 1466–1480 CrossRef CAS.
- G.-E. Yuan, Y. Li, J. Lv, G. Zhang and F. Yang, Integration of microbial fuel cell and catalytic oxidation reactor with iron phthalocyanine catalyst for Congo red degradation, Biochem. Eng. J., 2017, 120, 118–124 CrossRef CAS.
- M. F. de Dios, O. Iglesias, E. Bocos, M. Pazos and M. Sanromán, Application of benthonic microbial fuel cells and electro-Fenton process to dye decolourisation, J. Ind. Eng. Chem., 2014, 20(5), 3754–3760 CrossRef.
- L. Zhang, X. Yin and S. F.
Y. Li, Bio-electrochemical degradation of paracetamol in a microbial fuel cell-Fenton system, Chem. Eng. J., 2015, 276, 185–192 CrossRef CAS.
- Y. Wang, C. Feng, Y. Li, J. Gao and C.-P. Yu, Enhancement of emerging contaminants removal using Fenton reaction driven by H2O2-producing microbial fuel cells, Chem. Eng. J., 2017, 307, 679–686 CrossRef CAS.
- H. Nadais, X. Li, N. Alves, C. Couras, H. R. Andersen and I. Angelidaki, et al., Bio-electro-Fenton process for the degradation of non-steroidal anti-inflammatory drugs in wastewater, Chem. Eng. J., 2018, 338, 401–410 CrossRef CAS.
- M. Hassan, X. Wang, F. Wang, D. Wu, A. Hussain and B. Xie, Coupling ARB-based biological and photochemical (UV/TiO2 and UV/S2O82−) techniques to deal with sanitary landfill leachate, Waste Manag., 2017, 63, 292–298 CrossRef CAS PubMed.
- N. Wang, T. Zheng, G. Zhang and P. Wang, A review on Fenton-like processes for organic wastewater treatment, J. Chem. Environ. Eng., 2016, 4(1), 762–787 CrossRef CAS.
- S. Gligorovski, R. Strekowski, S. Barbati and D. Vione, Environmental implications of hydroxyl radicals (˙OH), Chem. Rev., 2015, 115(24), 13051–13092 CrossRef CAS PubMed.
- T. A. Nguyen, C.-C. Fu and R.-S. Juang, Effective removal of sulfur dyes from water by biosorption and subsequent immobilized laccase degradation on crosslinked chitosan beads, Chem. Eng. J., 2016, 304, 313–324 CrossRef CAS.
- R. Zou, I. Angelidaki, B. Jin and Y. Zhang, Feasibility and applicability of the scaling-up of bio-electro-Fenton system for textile wastewater treatment, Environ. Int., 2020, 134, 105352 CrossRef CAS PubMed.
- D. Suteu, C. Zaharia and T. Malutan, Removal of orange 16 reactive dye from aqueous solutions by waste sunflower seed shells, J. Serb. Chem. Soc., 2011, 76(4), 607–624 CrossRef CAS.
- T. Robinson, G. McMullan, R. Marchant and P. Nigam, Remediation of dyes in textile effluent: a critical review on current treatment technologies with a proposed alternative, Bioresour. Technol., 2001, 77(3), 247–255 CrossRef CAS PubMed.
- C. R. Holkar, A. J. Jadhav, D. V. Pinjari, N. M. Mahamuni and A. B. Pandit, A critical review on textile wastewater treatments: possible approaches, J. Environ. Manag., 2016, 182, 351–366 CrossRef CAS PubMed.
- M. Alkan, S. Çelikçapa, Ö. Demirbaş and M. Doğan, Removal of reactive blue 221 and acid blue 62 anionic dyes from aqueous solutions by sepiolite, Dyes Pigm., 2005, 65(3), 251–259 CrossRef CAS.
- A. Paz, J. Carballo, M. J. Pérez and J. M. Domínguez, Biological treatment of model dyes and textile wastewaters, Chemosphere, 2017, 181, 168–177 CrossRef CAS PubMed.
- Z. Ahmad, S. M. Abdullah and K. Sulaiman, Temperature-sensitive chemical cell based on Nickel (II) phthalocyanine-tetrasulfonic acid tetrasodium salt, Sensor Actuator Phys., 2012, 179, 146–150 CrossRef CAS.
- X. Wang, H. Mao, W. Huang, W. Guan, X. Zou and J. Pan, et al., Preparation of magnetic imprinted polymer particles via microwave heating initiated polymerization for selective enrichment of 2-amino-4-nitrophenol from aqueous solution, Chem. Eng. J., 2011, 178, 85–92 CrossRef CAS.
- S. Akiyama, N. Si, K. Nakashima and S. Yamasaki, Diphenylmethane and triphenylmethane dye ethynovinylogues with absorption bands in the near-infrared, Dyes Pigments, 1988, 9(6), 459–466 CrossRef CAS.
- G. Moussavi and M. Mahmoudi, Removal of azo and anthraquinone reactive dyes from industrial wastewaters using MgO nanoparticles, J. Hazard Mater., 2009, 168(2–3), 806–812 CrossRef CAS PubMed.
- V. K. Puttaswamy and N. Gowda, Oxidation of CI Acid Red 27 by chloramine-T in perchloric acid medium: spectrophotometric, kinetic and mechanistic approaches, Dyes Pigm., 2008, 78(2), 131–138 CrossRef.
- D. Ž. Mijin, M. L. A. Ivić, A. E. Onjia and B. N. Grgur, Decolorization of textile dye CI Basic Yellow 28 with electrochemically generated active chlorine, Chem. Eng. J., 2012, 204, 151–157 CrossRef.
- M. A. Hassaan, A. El Nemr and F. F. Madkour, Testing the advanced oxidation processes on the degradation of Direct Blue 86 dye in wastewater, Egypt. J. Aquat. Res., 2017, 43(1), 11–19 CrossRef.
- D. Rawat, R. S. Sharma, S. Karmakar, L. S. Arora and V. Mishra, Ecotoxic potential of a presumably non-toxic azo dye, Ecotoxicol. Environ. Saf., 2018, 148, 528–537 CrossRef CAS PubMed.
- B. Mella, B. SdC. Barcellos, D. E. da Silva Costa and M. Gutterres, Treatment of leather dyeing wastewater with associated process of coagulation-flocculation/adsorption/ozonation, Ozone: Sci. Eng., 2018, 40(2), 133–140 CrossRef CAS.
- S. O. Ganiyu, C. A. Martinez-Huitle and M. A. Rodrigo, Renewable energies driven electrochemical wastewater/soil decontamination technologies: a critical review of fundamental concepts and applications, Appl. Catal., B, 2020, 270, 118857 CrossRef CAS.
- S. Sandhya. Biodegradation of azo dyes under anaerobic condition: role of azoreductase. Biodegradation of azo dyes. 2010:39–57 Search PubMed.
- C. Zaharia, D. Suteu and A. Muresan, Options and solutions for textile effluent decolorization using some specific physico-chemical treatment steps, Environ. Eng. Manage. J., 2012, 11(2), 493–509 CrossRef CAS.
- H. Börnick and T. C. Schmidt, Amines. Organic pollutants in the water cycle: properties, occurrence, analysis and environmental relevance of polar compounds. 2006, pp. 181–209 Search PubMed.
- J. Khatri, P. Nidheesh, T. A. Singh and M. S. Kumar, Advanced oxidation processes based on zero-valent aluminium for treating textile wastewater, Chem. Eng. J., 2018, 348, 67–73 CrossRef CAS.
- B. Sharma, A. K. Dangi and P. Shukla, Contemporary enzyme based technologies for bioremediation: a review, J. Environ. Manag., 2018, 210, 10–22 CrossRef CAS PubMed.
- S. Khan and A. Malik, Toxicity evaluation of textile effluents and role of native soil bacterium in biodegradation of a textile dye, Environ. Sci. Pollut. Res., 2018, 25(5), 4446–4458 CrossRef CAS PubMed.
- M. Clark, Handbook of textile and industrial dyeing: principles, processes and types of dyes, Elsevier, 2011 Search PubMed.
- R. Christie, Environmental aspects of textile dyeing, Elsevier, 2007 Search PubMed.
- F. Copaciu, O. Opriş, V. Coman, D. Ristoiu, Ü. Niinemets and L. Copolovici, Diffuse water pollution by anthraquinone and azo dyes in environment importantly alters foliage volatiles, carotenoids and physiology in wheat (Triticum aestivum), Water, Air, Soil Pollut., 2013, 224(3), 1–11 CrossRef CAS.
- K. Hunger, Industrial dyes: chemistry, properties, applications, John Wiley & Sons, 2007 Search PubMed.
- J. Mathieu-Denoncourt, C. J. Martyniuk, S. R. de Solla, V. K. Balakrishnan and L. VrS, Sediment contaminated with the azo dye disperse yellow 7 alters cellular stress-and androgen-related transcription in Silurana tropicalis larvae, Environ. Sci. Technol., 2014, 48(5), 2952–2961 CrossRef CAS PubMed.
- I. S. Thakur, Environmental biotechnology: basic concepts and applications, IK International, 2006 Search PubMed.
- I. Haq and A. Raj, Biodegradation of Azure-B dye by Serratia liquefaciens and its validation by phytotoxicity, genotoxicity and cytotoxicity studies, Chemosphere, 2018, 196, 58–68 CrossRef CAS PubMed.
- A. Y. Khan and G. S. Kumar, Spectroscopic studies on the binding interaction of phenothiazinium dyes, azure A and azure B to double stranded RNA polynucleotides, Spectrochim. Acta, Part A, 2016, 152, 417–425 CrossRef CAS PubMed.
- A. Petzer, B. H. Harvey, G. Wegener and J. P. Petzer, Azure B, a metabolite of methylene blue, is a high-potency, reversible inhibitor of monoamine oxidase, Toxicol. Appl. Pharmacol., 2012, 258(3), 403–409 CrossRef CAS PubMed.
- S. A. Factor and W. J. Weiner, Parkinson's disease: diagnosis and clinical management, 2007 Search PubMed.
- G. Di Giovanni, V. Di Matteo and E. Esposito, Serotonin-dopamine interaction: experimental evidence and therapeutic relevance, Elsevier, 2008 Search PubMed.
- P. Paul and G. S. Kumar, Thermodynamics of the DNA binding of phenothiazinium dyes toluidine blue O, azure A and azure B, J. Chem. Thermodyn., 2013, 64, 50–57 CrossRef CAS.
- N. Couto, J. Wood and J. Barber, The role of glutathione reductase and related enzymes on cellular redox homoeostasis network, Free Radicals Biol. Med., 2016, 95, 27–42 CrossRef CAS PubMed.
- F. M. D. Chequer, J. P. F. Angeli, E. R. A. Ferraz, M. S. Tsuboy, J. C. Marcarini and M. S. Mantovani, et al., The azo dyes Disperse Red 1 and Disperse Orange 1 increase the micronuclei frequencies in human lymphocytes and in HepG2 cells, Mutat. Res., Genet. Toxicol. Environ. Mutagen., 2009, 676(1–2), 83–86 CrossRef CAS PubMed.
- Y. Will, J. E. McDuffie, A. J. Olaharski and B. D. Jeffy, Drug discovery toxicology: From target assessment to translational biomarkers, John Wiley & Sons, 2016 Search PubMed.
- F. H. Fernandes, E. Bustos-Obregon and D. M. F. Salvadori, Disperse Red 1 (textile dye) induces cytotoxic and genotoxic effects in mouse germ cells, Reprod. Toxicol., 2015, 53, 75–81 CrossRef CAS PubMed.
- M. C. Duarte and M. Rai, Therapeutic medicinal plants: from lab to the market, CRC Press, 2015 Search PubMed.
- F. M. D. Chequer, T. M. Lizier, R. de Felício, M. V. B. Zanoni, H. M. Debonsi and N. P. Lopes, et al., Analyses of the genotoxic and mutagenic potential of the products formed after the biotransformation of the azo dye Disperse Red 1, Toxicol. in Vitro, 2011, 25(8), 2054–2063 CrossRef CAS PubMed.
- F. I. Vacchi, P. C. Von der Ohe, A. F. de Albuquerque, J. A. de Souza Vendemiatti, C. C. J. Azevedo and J. G. Honório, et al., Occurrence and risk assessment of an azo dye–The case of Disperse Red 1, Chemosphere, 2016, 156, 95–100 CrossRef CAS PubMed.
- E. A. Petrakis, L. R. Cagliani, P. A. Tarantilis, M. G. Polissiou and R. Consonni, Sudan dyes in adulterated saffron (Crocus sativus L.): Identification and quantification by 1H NMR, Food Chem., 2017, 217, 418–424 CrossRef CAS PubMed.
- O. Duman, S. Tunc and T. G. Polat, Adsorptive removal of triarylmethane dye (Basic Red 9) from aqueous solution by sepiolite as effective and low-cost adsorbent, Microporous Mesoporous Mater., 2015, 210, 176–184 CrossRef CAS.
- M. V. Foguel, X.-A. Ton, M. V. Zanoni, T. S. Maria Del Pilar, K. Haupt and B. T. S. Bui, A molecularly imprinted polymer-based evanescent wave fiber optic sensor for the detection of basic red 9 dye, Sens. Actuators, B, 2015, 218, 222–228 CrossRef CAS.
- R. P. Pohanish. Sittig's handbook of toxic and hazardous chemicals and carcinogens, William Andrew, 2017 Search PubMed.
- H. Ali, S. Shehata and K. Ramadan, Microbial decolorization and degradation of crystal violet dye by Aspergillus niger, Int. J. Environ. Sci. Technol., 2016, 13(12), 2917–2926 CrossRef CAS.
- S. Mani and R. N. Bharagava, Exposure to crystal violet, its toxic, genotoxic and carcinogenic effects on environment and its degradation and detoxification for environmental safety, Rev. Environ. Contam. Toxicol., 2016, 237, 71–104 CAS.
- R. A. Rozendal, H. V. Hamelers, K. Rabaey, J. Keller and C. J. Buisman, Towards practical implementation of bioelectrochemical wastewater treatment, Trends Biotechnol., 2008, 26(8), 450–459 CrossRef CAS PubMed.
- L. Fu, S.-J. You, G.-q Zhang, F.-L. Yang and X.-h Fang, Degradation of azo dyes using in situ Fenton reaction incorporated into H2O2-producing microbial fuel cell, Chem. Eng. J., 2010, 160(1), 164–169 CrossRef CAS.
- J.-y Chen, N. Li and L. Zhao, Three-dimensional electrode microbial fuel cell for hydrogen peroxide synthesis coupled to wastewater treatment, J. Power Sources, 2014, 254, 316–322 CrossRef CAS.
- J. B. Arends, S. Van Denhouwe, W. Verstraete, N. Boon and K. Rabaey, Enhanced disinfection of wastewater by combining wetland treatment with bioelectrochemical H(2)O(2) production, Bioresour. Technol., 2014, 155, 352–358 CrossRef CAS PubMed.
- D. E. Meeroff, F. Bloetscher, D. Reddy, F. Gasnier, S. Jain and A. McBarnette, et al., Application of photochemical technologies for treatment of landfill leachate, J. Hazard Mater., 2012, 209, 299–307 CrossRef PubMed.
- M. Hassan, Y. Zhao and B. Xie, Employing TiO2 photocatalysis to deal with landfill leachate: Current status and development, Chem. Eng. J., 2016, 285, 264–275 CrossRef CAS.
- S. Freguia, K. Rabaey, Z. Yuan and J. Keller, Syntrophic processes drive the conversion of glucose in microbial fuel cell anodes, Environ. Sci. Technol., 2008, 42(21), 7937–7943 CrossRef CAS PubMed.
- A. P. Borole and J. R. Mielenz, Estimating hydrogen production potential in biorefineries using microbial electrolysis cell technology, Int. J. Hydrogen Energy, 2011, 36(22), 14787–14795 CrossRef CAS.
- J. F. Miceli III, I. Garcia-Peña, P. Parameswaran, C. I. Torres and R. Krajmalnik-Brown, Combining microbial cultures for efficient production of electricity from butyrate in a microbial electrochemical cell, Bioresour. Technol., 2014, 169, 169–174 CrossRef PubMed.
- P. Parameswaran, H. Zhang, C. I. Torres, B. E. Rittmann and R. Krajmalnik-Brown, Microbial community structure in a biofilm anode fed with a fermentable substrate: the significance of hydrogen scavengers, Biotechnol. Bioeng., 2010, 105(1), 69–78 CrossRef CAS PubMed.
- G. Lyberatos and I. Skiadas, Modelling of anaerobic digestion–a review, Global NEST J., 1999, 1(2), 63–76 Search PubMed.
- G. Merlino, A. Rizzi, A. Schievano, A. Tenca, B. Scaglia and R. Oberti, et al., Microbial community structure and dynamics in two-stage vs. single-stage thermophilic anaerobic digestion of mixed swine slurry and market bio-waste, Water Res., 2013, 47(6), 1983–1995 CrossRef CAS PubMed.
- P. Weiland, Biogas production: current state and perspectives, Appl. Microbiol. Biotechnol., 2010, 85(4), 849–860 CrossRef CAS PubMed.
- W. Parawira, J. S. Read, B. Mattiasson and L. Björnsson, Energy production from agricultural residues: high methane yields in pilot-scale two-stage anaerobic digestion, Biomass Bioenergy, 2008, 32(1), 44–50 CrossRef CAS.
- R. Conrad, Contribution of hydrogen to methane production and control of hydrogen concentrations in methanogenic soils and sediments, FEMS Microbiol. Ecol., 1999, 28(3), 193–202 CrossRef CAS.
- M. Bryant, Microbial methane production—theoretical aspects, J. Anim. Sci., 1979, 48(1), 193–201 CrossRef CAS.
- P. Smith, The microbial ecology of sludge methanogenesis, Dev. Ind. Microbiol., 1966, 7, 156–161 Search PubMed.
- P. Claassen, J. Van Lier, A. Lopez Contreras, E. Van Niel, L. Sijtsma and A. Stams, et al., Utilisation of biomass for the supply of energy carriers, Appl. Microbiol. Biotechnol., 1999, 52(6), 741–755 CrossRef CAS.
- I. Lyberatos, G. Ntaikou and G. Antonopoulou, Biohydrogen Production from Biomass and Wastes via Dark Fermentation: A Review, Waste Biomass Valorization, 2010, 21–39 Search PubMed.
- B. Schink, Energetics of syntrophic cooperation in methanogenic degradation, Microbiol. Mol. Biol. Rev., 1997, 61(2), 262–280 CAS.
- F. A. De Bok, H. J. Harmsen, C. M. Plugge, M. C. de Vries, A. D. Akkermans and W. M. de Vos, et al., The first true obligately syntrophic propionate-oxidizing bacterium, Pelotomaculum schinkii sp. nov., co-cultured with Methanospirillum hungatei, and emended description of the genus Pelotomaculum, Int. J. Syst. Evol. Microbiol., 2005, 55(4), 1697–1703 CrossRef CAS PubMed.
- S. H. Zinder. Physiological ecology of methanogens, Springer. Methanogenesis, 1993. pp. 128–206 Search PubMed.
- Y. Liu and W. B. Whitman, Metabolic, phylogenetic, and ecological diversity of the methanogenic archaea, Ann. N. Y. Acad. Sci., 2008, 1125(1), 171–189 CrossRef CAS PubMed.
- L. Appels, J. Lauwers, J. Degrève, L. Helsen, B. Lievens and K. Willems, et al., Anaerobic digestion in global bio-energy production: potential and research challenges, Renewable Sustainable Energy Rev., 2011, 15(9), 4295–4301 CrossRef CAS.
- Y. Xiao, Y. Zheng, S. Wu, E.-H. Zhang, Z. Chen and P. Liang, et al., Pyrosequencing reveals a core community of anodic bacterial biofilms in bioelectrochemical systems from China, Front. Microbiol., 2015, 6, 1410 Search PubMed.
- S. Galai, Pérez De Los Ríos A, Hernández-Fernández FJ, Mateo Ramírez F, Haj Kacem S and Quesada-Medina J, Application of microbial fuel cell for azoic dye decolorization with simultaneous bioenergy production using single bacterial strain, Chem. Eng. Technol., 2015, 38, 1511–1518 CrossRef CAS.
- L. Shi, D. J. Richardson, Z. Wang, S. N. Kerisit, K. M. Rosso and J. M. Zachara, et al., The roles of outer membrane cytochromes of Shewanella and Geobacter in extracellular electron transfer, Environ. Microbiol. Rep., 2009, 1(4), 220–227 CrossRef CAS PubMed.
- Y. Yang, M. Xu, Z. He, J. Guo, G. Sun and J. Zhou, Microbial electricity generation enhances decabromodiphenyl ether (BDE-209) degradation, PLoS One, 2013, 8(8), e70686 CrossRef CAS PubMed.
- Y. Yang, O. Luo, G. Kong, B. Wang, X. Li and E. Li, et al., Deciphering the anode-enhanced azo dye degradation in anaerobic baffled reactors integrating with microbial fuel cells, Front. Microbiol., 2018, 9, 2117 CrossRef PubMed.
- D. Jin, X. Kong, Y. Li, Z. Bai, G. Zhuang and X. Zhuang, et al., Biodegradation of di-n-butyl phthalate by Achromobacter sp. isolated from rural domestic wastewater, Int. J. Environ. Res. Public Health, 2015, 12(10), 13510–13522 CrossRef CAS PubMed.
- D. Paul, S. K. Kazy, T. D. Banerjee, A. K. Gupta, T. Pal and P. Sar, Arsenic biotransformation and release by bacteria indigenous to arsenic contaminated groundwater, Bioresour. Technol., 2015, 188, 14–23 CrossRef CAS PubMed.
- L. Hao, B. Zhang, M. Cheng and C. Feng, Effects of various organic carbon sources on simultaneous V (V) reduction and bioelectricity generation in single chamber microbial fuel cells, Bioresour. Technol., 2016, 201, 105–110 CrossRef CAS.
- D. R. Lovley, The microbe electric: conversion of organic matter to electricity, Curr. Opin. Biotechnol., 2008, 19(6), 564–571 CrossRef CAS PubMed.
- K. V. Krivushin, V. A. Shcherbakova, L. E. Petrovskaya and E. M. Rivkina, Methanobacterium veterum sp. nov., from ancient Siberian permafrost, Int. J. Syst. Evol. Microbiol., 2010, 60(2), 455–459 CrossRef CAS PubMed.
- T. Looft, U. Levine and T. Stanton, Cloacibacillus porcorum sp. nov., a mucin-degrading bacterium from the swine intestinal tract and emended description of the genus Cloacibacillus, Int. J. Syst. Evol. Microbiol., 2013, 63(Pt 6), 1960 CrossRef CAS PubMed.
- L. Fu, S. J. You, Fl Yang, Mm Gao, Xh Fang and Gq Zhang, Synthesis of hydrogen peroxide in microbial fuel cell, J. Chem. Technol. Biotechnol., 2010, 85(5), 715–719 CrossRef CAS.
- K. Solanki, S. Subramanian and S. Basu, Microbial fuel cells for azo dye treatment with electricity generation: a review, Bioresour. Technol., 2013, 131, 564–571 CrossRef CAS PubMed.
- J. Svojitka, L. Dvořák, M. Studer, J. O. Straub, H. Frömelt and T. Wintgens, Performance of an anaerobic membrane bioreactor for pharmaceutical wastewater treatment, Bioresour. Technol., 2017, 229, 180–189 CrossRef CAS PubMed.
- M. Katz, T. Frejd, B. Hahn-Hägerdal and M. F. Gorwa-Grauslund, Efficient anaerobic whole cell stereoselective bioreduction with recombinant Saccharomyces cerevisiae, Biotechnol. Bioeng., 2003, 84(5), 573–582 CrossRef CAS.
- S. D. Minteer, B. Y. Liaw and M. J. Cooney, Enzyme-based biofuel cells, Curr. Opin. Biotechnol., 2007, 18(3), 228–234 CrossRef CAS PubMed.
- F. Davis and S. P. Higson, Biofuel cells—recent advances and applications, Biosens. Bioelectron., 2007, 22(7), 1224–1235 CrossRef CAS PubMed.
- N. Mano, F. Mao and A. Heller, A miniature biofuel cell operating in a physiological buffer, J. Am. Chem. Soc., 2002, 124(44), 12962–12963 CrossRef CAS PubMed.
- A. Chaubey and B. Malhotra, Mediated biosensors, Biosens. Bioelectron., 2002, 17(6–7), 441–456 CrossRef CAS.
- A. Dubinin, F. Li, Y. Li and J. Yu, A solid-state immobilized enzyme polymer membrane microelectrode for measuring lactate-ion concentration, J. Electroanal. Chem. Interfacial Electrochem., 1991, 320(1), 131–135 CrossRef.
- A. A. Karyakin, O. V. Gitelmacher and E. E. Karyakina, Prussian blue-based first-generation biosensor. A sensitive amperometric electrode for glucose, Anal. Chem., 1995, 67(14), 2419–2423 CrossRef CAS.
- T. Aoyagi, A. Nakamura, H. Ikeda, T. Ikeda, H. Mihara and A. Ueno, Alizarin yellow-modified β-cyclodextrin as a guest-responsive absorption change sensor, Anal. Chem., 1997, 69(4), 659–663 CrossRef CAS.
- B. Brunetti, P. Ugo, L. M. Moretto and C. R. Martin, Electrochemistry of phenothiazine and methylviologen biosensor electron-transfer mediators at nanoelectrode ensembles, J. Electroanal. Chem., 2000, 491(1–2), 166–174 CrossRef CAS.
- B.-Y. Chen, C.-C. Hsueh, S.-Q. Liu, I.-S. Ng and Y.-M. Wang, Deciphering mediating characteristics of decolorized intermediates for reductive decolorization and bioelectricity generation, Bioresour. Technol., 2013, 145, 321–325 CrossRef CAS PubMed.
- V. Razumas, J. Jasaitis and J. Kulys, Electrocatalysis on enzyme-modified carbon materials, Bioelectrochem. Bioenerg., 1984, 12(3–4), 297–322 CrossRef CAS.
- B. P. Tarasevich and E. V. Kuznetsov, Progress in the polymer chemistry of borates, Russ. Chem. Rev., 1987, 56(3), 203 CrossRef.
- J. Celis. 2-D Proteome analysis protocols, ed. A. J. Link, Humana Press, Totowa, New Jersey, 1999, p. 704, $89.50 (hardcover), Protein Science, 1999, 8, (10), 2218 Search PubMed.
- E. Kjeang, D. Sinton and D. Harrington, Strategic enzyme patterning for microfluidic biofuel cells, J. Power Sources, 2006, 158(1), 1–12 CrossRef CAS.
- V. R. Stamenkovic, B. S. Mun, M. Arenz, K. J. Mayrhofer, C. A. Lucas and G. Wang, et al., Trends in electrocatalysis on extended and nanoscale Pt-bimetallic alloy surfaces, Nat. Mater., 2007, 6(3), 241–247 CrossRef CAS PubMed.
- J. L. Anderson, E. F. Bowden and P. G. Pickup, Dynamic electrochemistry: methodology and application, Anal. Chem., 1996, 68(12), 379–444 CrossRef CAS.
- S. Perkins, Electrode enhancements: New materials may boost fuel cell performance, Sci. News, 2007, 171(2), 21–22 CrossRef.
- R. H. Petrucci, F. G. Herring and J. D. Madura. General chemistry: principles and modern applications, Pearson Prentice Hall, 2010 Search PubMed.
- L. Gorton, E. Csöregi, E. Dominguez, J. Emnéus, G. Jönsson-Pettersson and G. Marko-Varga, et al., Selective detection in flow analysis based on the combination of immobilized enzymes and chemically modified electrodes, Anal. Chim. Acta, 1991, 250, 203–248 CrossRef CAS.
- A. Brigé, B. Motte, J. Borloo, G. Buysschaert, B. Devreese and J. J. Van Beeumen, Bacterial decolorization of textile dyes is an extracellular process requiring a multicomponent electron transfer pathway, Microb. Biotechnol., 2008, 1(1), 40–52 CrossRef PubMed.
- Y.-G. Hong and J.-D. Gu, Physiology and biochemistry of reduction of azo compounds by Shewanella strains relevant to electron transport chain, Appl. Microbiol. Biotechnol., 2010, 88(3), 637–643 CrossRef CAS PubMed.
- P.-J. Cai, X. Xiao, Y.-R. He, W.-W. Li, J. Chu and C. Wu, et al., Anaerobic biodecolorization mechanism of methyl orange by Shewanella oneidensis MR-1, Appl. Microbiol. Biotechnol., 2012, 93(4), 1769–1776 CrossRef CAS PubMed.
- C. Koch and F. Harnisch, What is the essence of microbial electroactivity?, Front. Microbiol., 2016, 7, 1890 Search PubMed.
- P. Mani, V. Fidal, K. Bowman, M. Breheny, T. Chandra and T. Keshavarz, et al., Degradation of azo dye (acid orange 7) in a Microbial fuel cell: comparison between anodic microbial-mediated reduction and cathodic laccase-mediated oxidation, Front. Energy Res., 2019, 7, 101 CrossRef.
- E. Fernando, T. Keshavarz and G. Kyazze, Complete degradation of the azo dye Acid Orange-7 and bioelectricity generation in an integrated microbial fuel cell, aerobic two-stage bioreactor system in continuous flow mode at ambient temperature, Bioresour. Technol., 2014, 156, 155–162 CrossRef CAS PubMed.
- N. Li, J. An, L. Zhou, T. Li, J. Li and C. Feng, et al., A novel carbon black graphite hybrid air-cathode for efficient hydrogen peroxide production in bioelectrochemical systems, J. Power Sources, 2016, 306, 495–502 CrossRef CAS.
- S. Li, H. Zhang, R. Lu and A. Yu, Interaction between triethanolamine and singlet or triplet excited state of xanthene dyes in aqueous solution, Spectrochim. Acta, Part A, 2017, 184, 204–210 CrossRef CAS PubMed.
- H. Gao, Y. D. Scherson and G. F. Wells, Towards energy neutral wastewater treatment: methodology and state of the art, Environ. Sci.: Processes Impacts, 2014, 16(6), 1223–1246 RSC.
- D. Wang, H. Hou, J. Hu, J. Xu, L. Huang and S. Hu, et al., A bio-electro-Fenton system with a facile anti-biofouling air cathode for efficient degradation of landfill leachate, Chemosphere, 2019, 215, 173–181 CrossRef CAS PubMed.
- F. Van der Zee, G. Lettinga and J. Field, The role of (auto) catalysis in the mechanism of an anaerobic azo reduction, Water Sci. Technol., 2000, 42(5–6), 301–308 CrossRef CAS.
- M. A. Oturan, M. Pimentel, N. Oturan and I. Sirés, Reaction sequence for the mineralization of the short-chain carboxylic acids usually formed upon cleavage of aromatics during electrochemical Fenton treatment, Electrochim. Acta, 2008, 54(2), 173–182 CrossRef CAS.
- H.-C. Tao, X.-Y. Wei, L.-J. Zhang, T. Lei and N. Xu, Degradation of p-nitrophenol in a BES-Fenton system based on limonite, J. Hazard Mater., 2013, 254, 236–241 CrossRef PubMed.
- G. Divyapriya, I. M. Nambi and J. Senthilnathan, An innate quinone functionalized electrochemically exfoliated graphene/Fe3O4 composite electrode for the continuous generation of reactive oxygen species, Chem. Eng. J., 2017, 316, 964–977 CrossRef CAS.
- C. Feng, F. Li, H. Liu, X. Lang and S. Fan, A dual-chamber microbial fuel cell with conductive film-modified anode and cathode and its application for the neutral electro-Fenton process, Electrochim. Acta, 2010, 55(6), 2048–2054 CrossRef CAS.
- C. Galindo, P. Jacques and A. Kalt, Photodegradation of the aminoazobenzene acid orange 52 by three advanced oxidation processes: UV/H2O2, UV/TiO2 and VIS/TiO2: comparative mechanistic and kinetic investigations, J. Photochem. Photobiol., A, 2000, 130(1), 35–47 CrossRef CAS.
- I. K. Konstantinou and T. A. Albanis, TiO2-assisted photocatalytic degradation of azo dyes in aqueous solution: kinetic and mechanistic investigations: a review, Appl. Catal., B, 2004, 49(1), 1–14 CrossRef CAS.
- G. Reguera, K. D. McCarthy, T. Mehta, J. S. Nicoll, M. T. Tuominen and D. R. Lovley, Extracellular electron transfer via microbial nanowires, Nature, 2005, 435(7045), 1098–1101 CrossRef CAS PubMed.
- H. Richter, K. P. Nevin, H. Jia, D. A. Lowy, D. R. Lovley and L. M. Tender, Cyclic voltammetry of biofilms of wild type and mutant Geobacter sulfurreducens on fuel cell anodes indicates possible roles of OmcB, OmcZ, type IV pili, and protons in extracellular electron transfer, Energy Environ. Sci., 2009, 2(5), 506–516 RSC.
- J. Sim, J. An, E. Elbeshbishy, H. Ryu and H.-S. Lee, Characterization and optimization of cathodic conditions for H2O2 synthesis in microbial electrochemical cells, Bioresour. Technol., 2015, 195, 31–36 CrossRef CAS PubMed.
- J.-y Chen, L. Zhao, N. Li and H. Liu, A microbial fuel cell with the three-dimensional electrode applied an external voltage for synthesis of hydrogen peroxide from organic matter, J. Power Sources, 2015, 287, 291–296 CrossRef CAS.
- S. Batool, S. Akib, M. Ahmad, K. S. Balkhair and M. A. Ashraf, Study of modern nano enhanced techniques for removal of dyes and metals, J. Nanomaterial., 2014, 2014, 20 Search PubMed.
- H. Lee, Y.-K. Park, S.-J. Kim, B.-H. Kim, H.-S. Yoon and S.-C. Jung, Rapid degradation of methyl orange using hybrid advanced oxidation process and its synergistic effect, J. Ind. Eng. Chem., 2016, 35, 205–210 CrossRef CAS.
- Y.-T. Wang and R.-S. Wang, A bio-electro-Fenton system employing the composite fepc/cnt/ss316 cathode, Materials, 2017, 10(2), 169 CrossRef PubMed.
- B. E. Logan, B. Hamelers, R. Rozendal, U. Schröder, J. Keller and S. Freguia, et al., Microbial fuel cells: methodology and technology, Environ. Sci. Technol., 2006, 40(17), 5181–5192 CrossRef CAS PubMed.
- X.-W. Liu, X.-F. Sun, D.-B. Li, W.-W. Li, Y.-X. Huang and G.-P. Sheng, et al., Anodic Fenton process assisted by a microbial fuel cell for enhanced degradation of organic pollutants, Water Res., 2012, 46(14), 4371–4378 CrossRef CAS PubMed.
- C.-H. Feng, F.-B. Li, H.-J. Mai and X.-Z. Li, Bio-electro-Fenton process driven by microbial fuel cell for wastewater treatment, Environ. Sci. Technol., 2010, 44(5), 1875–1880 CrossRef CAS PubMed.
- S. Li, T. Hua, F. Li and Q. Zhou, Bio-electro-Fenton systems for sustainable wastewater treatment: mechanisms, novel configurations, recent advances, LCA and challenges. An updated review, J. Chem. Technol. Biotechnol., 2020, 95(8), 2083–2097 CrossRef CAS.
- D. Jiang, M. Curtis, E. Troop, K. Scheible, J. McGrath and B. Hu, et al., A pilot-scale study on utilizing multi-anode/cathode microbial fuel cells (MAC MFCs) to enhance the power production in wastewater treatment, Int. J. Hydrogen Energy, 2011, 36(1), 876–884 CrossRef CAS.
- Z. Lv, D. Xie, X. Yue, C. Feng and C. Wei, Ruthenium oxide-coated carbon felt electrode: a highly active anode for microbial fuel cell applications, J. Power Sources, 2012, 210, 26–31 CrossRef CAS.
- S. Chen, G. He, X. Hu, M. Xie, S. Wang and D. Zeng, et al., A three-dimensionally ordered macroporous carbon derived from a natural resource as anode for microbial bioelectrochemical systems, ChemSusChem, 2012, 5(6), 1059–1063 CrossRef CAS PubMed.
- S. Cheng and B. E. Logan, Ammonia treatment of carbon cloth anodes to enhance power generation of microbial fuel cells, Electrochem. Commun., 2007, 9(3), 492–496 CrossRef.
- N. G. Yasri and G. Nakhla, Electrochemical behavior of anode-respiring bacteria on doped carbon electrodes, ACS Appl. Mater. Interfaces, 2016, 8(51), 35150–35162 CrossRef CAS PubMed.
- D. Paul, M. Noori, P. Rajesh, M. Ghangrekar and A. Mitra, Modification of carbon felt anode with graphene oxide-zeolite composite for enhancing the performance of microbial fuel cell, Sustain. Energy Technol. Assessments, 2018, 26, 77–82 CrossRef.
- G. Huang, H. Wang, H. Zhao, P. Wu and Q. Yan, Application of polypyrrole modified cathode in bio-electro-Fenton coupled with microbial desalination cell (MDC) for enhanced degradation of methylene blue, J. Power Sources, 2018, 400, 350–359 CrossRef CAS.
- T. Huang, L. Liu, J. Tao, L. Zhou and S. Zhang, Microbial fuel cells coupling with the three-dimensional electro-Fenton technique enhances the degradation of methyl orange in the wastewater, Environ.
Sci. Pollut. Res., 2018, 25(18), 17989–18000 CrossRef CAS PubMed.
- C. Santoro, C. Arbizzani, B. Erable and I. Ieropoulos, Microbial fuel cells: From fundamentals to applications. A review, J. Power Sources, 2017, 356, 225–244 CrossRef CAS PubMed.
- N. Yasri, E. P. Roberts and S. Gunasekaran, The electrochemical perspective of bioelectrocatalytic activities in microbial electrolysis and microbial fuel cells, Energy Reports, 2019, 5, 1116–1136 CrossRef.
- E. Guerrini, M. Grattieri, S. P. Trasatti, M. Bestetti and P. Cristiani, Performance explorations of single chamber microbial fuel cells by using various microelectrodes applied to biocathodes, Int. J. Hydrogen Energy, 2014, 39(36), 21837–21846 CrossRef CAS.
- B. Logan, S. Cheng, V. Watson and G. Estadt, Graphite fiber brush anodes for increased power production in air-cathode microbial fuel cells, Environ. Sci. Technol., 2007, 41(9), 3341–3346 CrossRef CAS PubMed.
- L. Zhao, J. Li, F. Battaglia and Z. He, Computational investigation of the flow field contribution to improve electricity generation in granular activated carbon-assisted microbial fuel cells, J. Power Sources, 2016, 333, 83–87 CrossRef CAS.
- M. Grattieri, S. Babanova, C. Santoro, E. Guerrini, S. P. Trasatti and P. Cristiani, et al., Enzymatic oxygen microsensor based on bilirubin oxidase applied to microbial fuel cells analysis, Electroanalysis, 2015, 27(2), 327–335 CrossRef CAS.
- P. Nidheesh and R. Rajan, Removal of rhodamine B from a water medium using hydroxyl and sulphate radicals generated by iron loaded activated carbon, RSC advances, 2016, 6(7), 5330–5340 RSC.
- P. Xu, H. Xu and Z. Shi, A novel bio-electro-Fenton process with FeVO4/CF cathode on advanced treatment of coal gasification wastewater, Sep. Purif. Technol., 2018, 194, 457–461 CrossRef CAS.
- X.-Q. Wang, C.-P. Liu, Y. Yuan and F.-b Li, Arsenite oxidation and removal driven by a bio-electro-Fenton process under neutral pH conditions, J. Hazard Mater., 2014, 275, 200–209 CrossRef CAS PubMed.
- C. Li, L. Zhang, L. Ding, H. Ren and H. Cui, Effect of conductive polymers coated anode on the performance of microbial fuel cells (MFCs) and its biodiversity analysis, Biosensors and Bioelectronics, 2011, 26(10), 4169–4176 CrossRef CAS PubMed.
- S. Hidayat, Y.-H. Song and J.-Y. Park, Performance of a continuous flow microbial reverse-electrodialysis electrolysis cell using a non-buffered substrate and catholyte effluent addition, Bioresour. Technol., 2017, 240, 77–83 CrossRef CAS PubMed.
- L. Zhuang, S. Zhou, Y. Yuan, M. Liu and Y. Wang, A novel bioelectro-Fenton system for coupling anodic COD removal with cathodic dye degradation, Chem. Eng. J., 2010, 163(1–2), 160–163 CrossRef CAS.
- S. B. Velasquez-Orta, T. P. Curtis and B. E. Logan, Energy from algae using microbial fuel cells, Biotechnol. Bioeng., 2009, 103(6), 1068–1076 CrossRef CAS PubMed.
- J. M. Pisciotta, Z. Zaybak, D. F. Call, J.-Y. Nam and B. E. Logan, Enrichment of microbial electrolysis cell biocathodes from sediment microbial fuel cell bioanodes, Appl. Environ. Microbiol., 2012, 78(15), 5212–5219 CrossRef CAS PubMed.
- H. Liu, R. Ramnarayanan and B. E. Logan, Production of electricity during wastewater treatment using a single chamber microbial fuel cell, Environ. Sci. Technol., 2004, 38(7), 2281–2285 CrossRef CAS PubMed.
- W. Miran, M. Nawaz, J. Jang and D. S. Lee, Chlorinated phenol treatment and in situ hydrogen peroxide production in a sulfate-reducing bacteria enriched bioelectrochemical system, Water Res., 2017, 117, 198–206 CrossRef CAS PubMed.
- G. Hernández-Flores, H. Poggi-Varaldo, O. Solorza-Feria, M. Ponce-Noyola, T. Romero-Castañón and N. Rinderknecht-Seijas, et al., Characteristics of a single chamber microbial fuel cell equipped with a low cost membrane, Int. J. Hydrogen Energy, 2015, 40(48), 17380–17387 CrossRef.
- M. C. Hatzell, Y. Kim and B. E. Logan, Powering microbial electrolysis cells by capacitor circuits charged using microbial fuel cell, J. Power Sources, 2013, 229, 198–202 CrossRef CAS.
- X. Yu, W. Fu, M. Jiang, G. Liu, Y. Zou and S. Chen, Automatic microbial electro-Fenton system driven by transpiration for degradation of acid orange 7, Sci. Total Environ., 2020, 725, 138508 CrossRef CAS PubMed.
- H. Olvera-Vargas, C. Trellu, N. Oturan and M. A. Oturan, Bio-electro-Fenton: a new combined process–principles and applications, Electro-Fenton Process, 2017, pp. 29–56 Search PubMed.
- Y. Luo, R. Zhang, G. Liu, J. Li, B. Qin and M. Li, et al., Simultaneous degradation of refractory contaminants in both the anode and cathode chambers of the microbial fuel cell, Bioresour. Technol., 2011, 102(4), 3827–3832 CrossRef CAS PubMed.
- K. Zuo, L. Yuan, J. Wei, P. Liang and X. Huang, Competitive migration behaviors of multiple ions and their impacts on ion-exchange resin packed microbial desalination cell, Bioresour. Technol., 2013, 146, 637–642 CrossRef CAS PubMed.
- Y. Kim and B. E. Logan, Microbial desalination cells for energy production and desalination, Desalination, 2013, 308, 122–130 CrossRef CAS.
- A. Ebrahimi, G. Najafpour and D. Kebria, Effect of batch vs. continuous mode of operation on microbial desalination cell performance treating municipal wastewater, Iran. J. Hydrogen Fuel Cell, 2016, 3(4), 281–290 Search PubMed.
- H. Monteil, Y. Pechaud, N. Oturan and M. A. Oturan, A review on efficiency and cost effectiveness of electro-and bio-electro-Fenton processes: application to the treatment of pharmaceutical pollutants in water, Chem. Eng. J., 2019, 376, 119577 CrossRef CAS.
- P. Nidheesh and R. Gandhimathi, Textile wastewater treatment by electro-Fenton process in batch and continuous modes, J. Hazard., Toxic Radioact. Waste, 2015, 19(3), 04014038 CrossRef.
- M. Rahimnejad, G. Najafpour and A. A. Ghoreyshi. Effect of mass transfer on performance of microbial fuel cell, Intech. 2011, vol. 5, pp. 233–50 Search PubMed.
- M. Xu, J. Guo, X. Kong, X. Chen and G. Sun, Fe (III)-enhanced azo reduction by Shewanella decolorationis S12, Appl. Microbiol. Biotechnol., 2007, 74(6), 1342–1349 CrossRef CAS PubMed.
- M. Á. F. de Dios, A. G. del Campo, F. J. Fernández, M. Rodrigo, M. Pazos and M. Á. Sanromán, Bacterial–fungal interactions enhance power generation in microbial fuel cells and drive dye decolourisation by an ex situ and in situ electro-Fenton process, Bioresour. Technol., 2013, 148, 39–46 CrossRef PubMed.
- T. Ling, B. Huang, M. Zhao, Q. Yan and W. Shen, Repeated oxidative degradation of methyl orange through bio-electro-Fenton in bioelectrochemical system (BES), Bioresour. Technol., 2016, 203, 89–95 CrossRef CAS PubMed.
- S. Yan, J. Geng, R. Guo, Y. Du and H. Zhang, Hydronium jarosite activation of peroxymonosulfate for the oxidation of organic contaminant in an electrochemical reactor driven by microbial fuel cell, J. Hazard Mater., 2017, 333, 358–368 CrossRef CAS PubMed.
- K. Rabaey, N. Boon, M. Höfte and W. Verstraete, Microbial phenazine production enhances electron transfer in biofuel cells, Environ. Sci. Technol., 2005, 39(9), 3401–3408 CrossRef CAS PubMed.
- W. He, M. J. Wallack, K.-Y. Kim, X. Zhang, W. Yang and X. Zhu, et al., The effect of flow modes and electrode combinations on the performance of a multiple module microbial fuel cell installed at wastewater treatment plant, Water Res., 2016, 105, 351–360 CrossRef CAS PubMed.
- X. Li, X. Jin, N. Zhao, I. Angelidaki and Y. Zhang, Efficient treatment of aniline containing wastewater in bipolar membrane microbial electrolysis cell-Fenton system, Water Res., 2017, 119, 67–72 CrossRef CAS PubMed.
- G. Gao, Q. Zhang, Z. Hao and C. D. Vecitis, Carbon nanotube membrane stack for flow-through sequential regenerative electro-Fenton, Environ. Sci. Technol., 2015, 49(4), 2375–2383 CrossRef CAS PubMed.
- L. Xu, H. Zhao, S. Shi, G. Zhang and J. Ni, Electrolytic treatment of CI Acid Orange 7 in aqueous solution using a three-dimensional electrode reactor, Dyes Pigm., 2008, 77(1), 158–164 CrossRef CAS.
- A. Dirany, I. Sirés, N. Oturan, A. Özcan and M. A. Oturan, Electrochemical treatment of the antibiotic sulfachloropyridazine: kinetics, reaction pathways, and toxicity evolution, Environ. Sci. Technol., 2012, 46(7), 4074–4082 CrossRef CAS PubMed.
- I. Oller, S. Malato and J. Sánchez-Pérez, Combination of advanced oxidation processes and biological treatments for wastewater decontamination—a review, Sci. Total Environ., 2011, 409(20), 4141–4166 CrossRef CAS PubMed.
- C. Trellu, O. Ganzenko, S. Papirio, Y. Pechaud, N. Oturan and D. Huguenot, et al., Combination of anodic oxidation and biological treatment for the removal of phenanthrene and Tween 80 from soil washing solution, Chem. Eng. J., 2016, 306, 588–596 CrossRef CAS.
- J. Kang, S. Irmak and M. Wilkins, Conversion of lignin into renewable carboxylic acid compounds by advanced oxidation processes, Renewable Energy, 2019, 135, 951–962 CrossRef CAS.
- S. Li, Y. Liu, R. Ge, S. Yang, Y. Zhai and T. Hua, et al., Microbial electro-Fenton: A promising system for antibiotics resistance genes degradation and energy generation, Sci. Total Environ., 2020, 699, 134160 CrossRef CAS PubMed.
- H. Afanga, H. Zazou, F. E. Titchou, Y. Rakhila, R. A. Akbour and A. Elmchaouri, et al., Integrated electrochemical processes for textile industry wastewater treatment: system performances and sludge settling characteristics, Sustainable Environ. Res., 2020, 30(1), 1–11 CrossRef.
- Y. Ling, H. Xu and X. Chen, Continuous multi-cell electrochemical reactor for pollutant oxidation, Chem. Eng. Sci., 2015, 122, 630–636 CrossRef CAS.
- I. M. S. Pillai and A. K. Gupta, Performance analysis of a continuous serpentine flow reactor for electrochemical oxidation of synthetic and real textile wastewater: energy consumption, mass transfer coefficient and economic analysis, J. Environ. Manag., 2017, 193, 524–531 CrossRef CAS PubMed.
- V. Hessel, I. V. Guersel, Q. Wang, T. Noel and J. Lang, Potential analysis of smart flow processing and micro process technology for fastening process development–use of chemistry and process design as intensification fields, Chem. Ing. Tech., 2012, 84(5), 660–684 CrossRef CAS.
- O. Iglesias, E. Rosales, M. Pazos and M. Sanromán, Electro-Fenton decolourisation of dyes in an airlift continuous reactor using iron alginate beads, Environ. Sci. Pollut. Res., 2013, 20(4), 2252–2261 CrossRef CAS PubMed.
- B. K. Körbahti, Response surface optimization of electrochemical treatment of textile dye wastewater, J. Hazard Mater., 2007, 145(1–2), 277–286 CrossRef PubMed.
- R. Zhu, C. Yang, M. Zhou and J. Wang, Industrial park wastewater deeply treated and reused by a novel electrochemical oxidation reactor, Chem. Eng. J., 2015, 260, 427–433 CrossRef CAS.
- K. Pan and P. Zhou, Performance enhancement with a hydrophilic self-immobilized redox mediator modified anode in Chlorella vulgaris-based microbial solar cell, ACS Sustainable Chem. Eng., 2015, 3(9), 1974–1981 CrossRef CAS.
- E. Fernando, Treatment of azo dyes in industrial wastewater using microbial fuel cells, University of Westminster, 2014 Search PubMed.
- Z. He, S. D. Minteer and L. T. Angenent, Electricity generation from artificial wastewater using an upflow microbial fuel cell, Environ. Sci. Technol., 2005, 39(14), 5262–5267 CrossRef CAS PubMed.
- E. Pajootan, M. Arami and M. Rahimdokht, Discoloration of wastewater in a continuous electro-Fenton process using modified graphite electrode with multi-walled carbon nanotubes/surfactant, Sep. Purif. Technol., 2014, 130, 34–44 CrossRef CAS.
- E. Bocos, D. Pérez-Álvarez, M. Pazos, M. C. Rodríguez-Argüelles and M. Á. Sanromán, Coated nickel foam electrode for the implementation of continuous electro-Fenton treatment, J. Chem. Technol. Biotechnol., 2016, 91(3), 685–692 CrossRef CAS.
- E. Rosales, O. Iglesias, M. Pazos and M. Sanromán, Decolourisation of dyes under electro-Fenton process using Fe alginate gel beads, J. Hazard Mater., 2012, 213, 369–377 CrossRef PubMed.
- E. Rosales, M. Pazos, M. Longo and M. Sanromán, Electro-Fenton decoloration of dyes in a continuous reactor: a promising technology in colored wastewater treatment, Chem. Eng. J., 2009, 155(1–2), 62–67 CrossRef CAS.
- P. Nidheesh and R. Gandhimathi, Electro Fenton oxidation for the removal of Rhodamine B from aqueous solution in a bubble column reactor under continuous mode, Desalin. Water Treat., 2015, 55(1), 263–271 CrossRef CAS.
- J. K. Jang, T. H. Pham, I. S. Chang, K. H. Kang, H. Moon and K. S. Cho, et al., Construction and operation of a novel mediator-and membrane-less microbial fuel cell, Process Biochem., 2004, 39(8), 1007–1012 CrossRef CAS.
- B. E. Logan, Exoelectrogenic bacteria that power microbial fuel cells, Nat. Rev. Microbiol., 2009, 7(5), 375–381 CrossRef CAS PubMed.
- H. Zhang, X. Ran and X. Wu, Electro-Fenton treatment of mature landfill leachate in a continuous flow reactor, J. Hazard Mater., 2012, 241, 259–266 CrossRef PubMed.
- Z. Ge, J. Li, L. Xiao, Y. Tong and Z. He, Recovery of electrical energy in microbial fuel cells: brief review, Environ. Sci. Technol. Lett., 2014, 1(2), 137–141 CrossRef CAS.
- Y. Dong, Y. Qu, W. He, Y. Du, J. Liu and X. Han, et al., A 90-liter stackable baffled microbial fuel cell for brewery wastewater treatment based on energy self-sufficient mode, Bioresour. Technol., 2015, 195, 66–72 CrossRef CAS PubMed.
- Z. Ge and Z. He, Long-term performance of a 200 liter modularized microbial fuel cell system treating municipal wastewater: treatment, energy, and cost, Environ. Sci.: Water Res. Technol., 2016, 2(2), 274–281 RSC.
- M. Hassan, H. Olvera-Vargas, X. Zhu, B. Zhang and Y. He, Microbial electro-Fenton: an emerging and energy-efficient platform for environmental remediation, J. Power Sources, 2019, 424, 220–244 CrossRef CAS.
- B. Tiwari, M. T. Noori and M. Ghangrekar, A novel low cost polyvinyl alcohol-Nafion-borosilicate membrane separator for microbial fuel cell, Mater. Chem. Phys., 2016, 182, 86–93 CrossRef CAS.
- I. Chakraborty, S. Das, B. Dubey and M. Ghangrekar, Novel low cost proton exchange membrane made from sulphonated biochar for application in microbial fuel cells, Mater. Chem. Phys., 2020, 239, 122025 CrossRef CAS.
- B. Logan and M. Regan, Microbial challenges and fuel cell applications, Environ. Sci. Technol., 2006, 40(17), 5172–5180 CrossRef CAS PubMed.
- P. Choudhury, U. S. Prasad Uday, T. K. Bandyopadhyay, R. N. Ray and B. Bhunia, Performance improvement of microbial fuel cell (MFC) using suitable electrode and Bioengineered organisms: A review, Bioengineered, 2017, 8(5), 471–487 CrossRef CAS PubMed.
- A. Rubio-Clemente, E. Chica and G. A. Peñuela, Petrochemical wastewater treatment by photo-Fenton process, Water, Air, Soil Pollut., 2015, 226(3), 1–18 CrossRef CAS.
- M. Kahoush, N. Behary, A. Cayla and V. Nierstrasz, Bio-Fenton and Bio-electro-Fenton as sustainable methods for degrading organic pollutants in wastewater, Process Biochem., 2018, 64, 237–247 CrossRef CAS.
- C. Moreno-Castilla and F. Maldonado-Hódar, Carbon aerogels for catalysis applications: An overview, Carbon, 2005, 43(3), 455–465 CrossRef CAS.
- H. Zhao, Y. Wang, Y. Wang, T. Cao and G. Zhao, Electro-Fenton oxidation of pesticides with a novel Fe3O4@ Fe2O3/activated carbon aerogel cathode:
high activity, wide pH range and catalytic mechanism, Appl. Catal., B, 2012, 125, 120–127 CrossRef CAS.
- W. Chen, X. Yang, J. Huang, Y. Zhu, Y. Zhou and Y. Yao, et al., Iron oxide containing graphene/carbon nanotube based carbon aerogel as an efficient E-Fenton cathode for the degradation of methyl blue, Electrochim. Acta, 2016, 200, 75–83 CrossRef CAS.
- W. R. Barros, P. C. Franco, J. R. Steter, R. S. Rocha and M. R. Lanza, Electro-Fenton degradation of the food dye amaranth using a gas diffusion electrode modified with cobalt (II) phthalocyanine, J. Electroanal. Chem., 2014, 722, 46–53 CrossRef.
- A. Thiam, I. Sirés, J. A. Garrido, R. M. Rodríguez and E. Brillas, Effect of anions on electrochemical degradation of azo dye Carmoisine (Acid Red 14) using a BDD anode and air-diffusion cathode, Sep. Purif. Technol., 2015, 140, 43–52 CrossRef CAS.
- A. Escapa, X. Gómez, B. Tartakovsky and A. Morán, Estimating microbial electrolysis cell (MEC) investment costs in wastewater treatment plants: Case study, Int. J. Hydrogen Energy, 2012, 37(24), 18641–18653 CrossRef CAS.
- J. Beegle and A. Borole, Wastewater Energy Recovery Using Bioelectrochemical Systems and Anaerobic Digestion, Proc. Water Environ. Fed., 2016, 2016(11), 459–465 CrossRef.
- V. Chaturvedi and P. Verma, Microbial fuel cell: a green approach for the utilization of waste for the generation of bioelectricity, Bioresour. Bioprocess., 2016, 3(1), 1–14 CrossRef.
- M. Xu, C. Wu and Y. Zhou, Advancements in the Fenton process for wastewater treatment, Adv. Oxid. Processes, 2020, 61, 61–77 Search PubMed.
|
This journal is © The Royal Society of Chemistry 2022 |
Click here to see how this site uses Cookies. View our privacy policy here.