DOI:
10.1039/D2RA01822E
(Review Article)
RSC Adv., 2022,
12, 14509-14520
Halogen-free instinct flame-retardant waterborne polyurethanes: composition, performance, and application
Received
21st March 2022
, Accepted 25th April 2022
First published on 13th May 2022
Abstract
Ideal halogen-free instinct flame-retardant waterborne polyurethanes have high flame-retardant efficiency, environmental friendliness, fine compatibility, and good thermostability. Phosphorus flame-retardants are currently widely used in halogen-free instinct flame-retardant waterborne polyurethanes (HIFWPU), especially those with phosphorous–nitrogen co-structures. Phosphorous–nitrogen HIFWPU have become a hotspot because their co-structures provide higher flame-retardance as compared to waterborne polyurethanes. This review introduces three main types of HIFWPU based on composition, performance and application. HIFWPU not only have improved flame-retardance but also satisfy the various requirements for functionality. HIFWPU have been widely developed in textile, furniture, automobile, and aerospace applications.
Introduction
Polyurethanes (PU) have been extensively studied since their discovery in the 1950s by DuPont.1,2 With the increasing global concern regarding environmental protection, the application of solvent-based polyurethanes (PU) has been strictly limited due to its emission of volatile organic chemicals (VOCs). Therefore, the development of environmentally friendly PU production has been largely promoted and rapidly accelerated since the 1970s.3–5 In 1972, Bayer first used a type of water-based PU in leather surface finishing, which drew research attention. This kind of water-based PU was named waterborne polyurethane (WPU), which saw breakthrough research in the 1980s and became widely applied in textile dyeing-finishing and processing all over the world. WPU is a type of emulsion that uses water as a dispersion medium and contains little or no solvent, affording it low toxicity and pollution with good energy conservation and workability.3,6 Meanwhile, its viscosity and rheological properties can be easily adjusted and controlled for textile, leather, furniture, and building applications7–9 by modifying the surface. For instance, fabric WPU coatings provide high wear- and water-resistance, while woody WPU coatings provide high strength, rigidity, and glossiness.10–13 Nevertheless, environmental protection and surface modifiability are not enough to meet the more demanding and wider requirements in textiles, leather and furniture. These applications need fireproofing treatments for personal and property safety. As pioneers in fireproofing studies, von Pidoll14 and Tang15 indicated that flame-retardance is a vital property of fabric and woody WPU coatings and makes textiles and wood products safer. Therefore, the development of flame-retardant WPU (FWPU) has great research significance and application prospects.16 To endow WPU with flame-retardance, two modifications are often utilized: the blending method and instinct method. Although the preparation of blending-FWPU is simple with good flame-retardance,17,18 the physical blending method largely influences the stability and grain size of the emulsion, as seen in the basic study by Yıldız19 and El-Fattah.20 Compared with blending-FWPU, instinct-FWPU (IFWPU) is synthesized via the incorporation of reactive flame-retardants into PU chains. Gelebi21 and Zhang22 found that the flame-retardant efficiency and durability of IFWPU are higher and longer, respectively, than those of blending-FWPU, despite the preparation requiring complex technology. IFWPU is composed of flame-retardant elements and PU chains combined using chemical reactions. The innovative IFWPU is modified at the molecular level, which overcomes interfacial incompatibility (e.g., volatilization, dissolution, migration, and exudation) and provides durable high flame-retardance.22–25
According to the differently modified PU molecular segments, the modifications of IFWPU are classified as soft-, hard-, and soft-co-hard segment modifications.26–33 Besides, the compositions of IFWPU are classified as one-component, two-component, and hyperbranched based on different components.34–37 Of these, one-component IFWPU consists of multiple soft and hard segments obtained through block formation. Halogen-free flame-retardants used as reactive monomers can participate in the synthesis of WPU by introduction into the main chain or branches to endow flame-retardance to polymer materials.38,39 The aim of these modifications is to enhance flame-retardance without influencing the WPU's mechanical and thermal properties. Although one-component IFWPU has many advantages, such as a variable structure and simple fabrication process, it also has many disadvantages, such as low tensile strength, thermostability, and toughness.40,41 Two-component IFWPU has gradually begun to replace one-component IFWPU with high transparency, good waterproofness, and stable storage characteristics. Two-component IFWPU consists of flame-retardant waterborne polyol dispersions and a hydrophilic curing agent.42–45 For water-dispersing polyols, their structures are easy to control and design. Waterborne polyol dispersions have small particle sizes and good stability.15,46 Reactive flame-retardant units can be incorporated into the backbones and branched chains of PU during the synthesis process.47,48 Hyperbranched polymers are macromolecules with highly branched structures, which have been applied in adhesives, printing inks, and coatings due to their external functional groups and internal cavity structure.49–52 They have attracted increasing attention for improving the mechanical properties and processability of IFWPU by combining hyperbranched polymers and flame-retardants with WPU.53–55 The whole development of IFWPU derived from PU in industrial application is shown in Fig. 1 for intuitionistic exhibition.
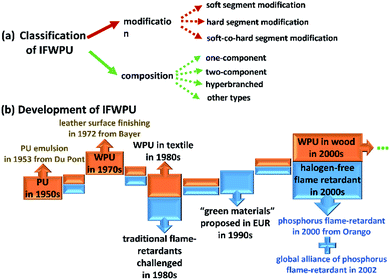 |
| Fig. 1 The (a) classification and (b) development of IFWPU derived from PU in industrial applications. | |
To satisfy the requirements of high flame-retardance and environmental protection, the type of flame-retardant is a crucial selection in designing the composition of IFWPU. Halogenated and toxic flame-retardants have gradually been replaced by low- or non-toxic flame-retardants such as organic phosphorous flame-retardants, nitrogen flame-retardants, and phosphorous–nitrogen flame-retardants.42,56–61 These kinds of flame-retardants are called halogen-free flame-retardants, which emit phosphoric acid, polymetaphosphoric acid or large nonflammable gases for isolating oxygen and heat during burning as the temperature increases.12,57,58 Therefore, the kind of IFWPU synthesized by halogen-free flame-retardants is always called halogen-free IFWPU (HIFWPU). HIFWPUs have lots of excellent properties such as flame-retardancy, environmental friendliness, fabricability and stability, which can largely make up for the shortcomings of phosphorus-containing IFWPUs. To satisfy the demands of applications, HIFWPUs are often designed with many species, which are classified as flame-retardant coatings, flame-retardant coating adhesives, and flame-retardant paint.62–67 This paper mainly summarizes the research on HIFWPU based on modifications, compositions, performances, and applications.
One-component HIFWPU
Soft segment modification
Soft segment modification occurs when flame retardants react with other agents to obtain macromolecule polyether polyol- or polyester polyol-containing flame-retardant elements.24,68–71 Then, they partially or completely replace the polyether polyol or polyester polyol to react with isocyanate and produce HIFWPU after emulsification. HIWPU modified via soft segment modification possesses good flame-retardance with little effect on film properties. Soft segment modification can endow HIWPU with a high content of flame-retardant elements and the high molecular weight of soft segments, which occupy the relatively high ratio of the PU molecular weight. Therefore, PU modified via the partial replacement of flame-retardant soft segments has a greater composition of flame-retardant and relatively unaffected film properties. Chen72,73 and Li,74 from our research group, successfully synthesized HIWPU modified by organophosphorus soft segments, which improved the limiting oxygen index (LOI) to 32.0%. Two kinds of soft segment flame retardants are usually used: halogen-free polyphosphate (OP550, Clariant AG) and hydroxy-terminated organophosphate oligomer (HFPO, Fyroltex HP). OP550 is a new reactive phosphorus flame retardant that has high flame-retardant effectiveness and little effect on physical and mechanical properties. Its structure is shown in Scheme 1. WPU modified through OP550 is named WPU-OP. Generally, the synthesis uses a common method, as shown in Scheme 2, based on their previous work.56,75–81 Commonly, the stoichiometric ratio of –NCO to –OH (R) is generally from 1.3 to 1.7 because of the preparation technology.82–84 A solid content of 20–30% provides good film properties.85–87
 |
| Scheme 1 Structure of OP550. | |
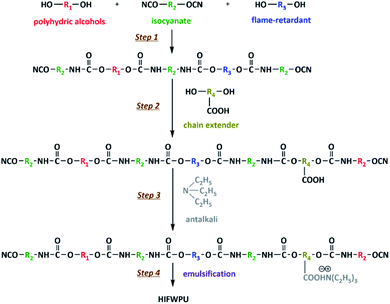 |
| Scheme 2 The modification process of HIFWPU. | |
Characterizations of the structure and performance of one-component HIFWPU have certain essential aspects. The details are listed in Table 1. Commonly, it is necessary to characterize the structure and the fundamental and functional properties of HIFWPU. In WPU-OP systems, although organophosphorus decreases the decomposition temperature (Td) value and thermostability of HIFWPU (Fig. 2), its carbon yield provides high flame-retardance. According to the carbonization theory of Park, organophosphorus will decrease Td and accelerate the formation of char after being added to PU chains at high temperatures, which can effectively reduce the flammability and heat release rate (HRR) of PU burning. The research by Chen88 indicated that the movement of hard segments dispersed in a soft segment phase has a remarkable effect on the microstructure of PU. Therefore, an ethyl side chain enlarged the free volume of the soft segment micro-area after WPU was added to organophosphorus, which aggregated in a more regular short-range ordered structure that needed more energy to be damaged.63,88 As a result, the hard segment decomposition temperature (Tgh) moved to high temperatures as more OP550 was added (Fig. 2). The OP550 soft segment modifier has soft and tough characteristics, which decrease tensile strength and increase flexibility with a large volume of organophosphorus molecular structure via crippling the molecular chain rotation. The high content of organophosphorus in PU always implies high flame-retardance, even to obtain non-combustible material level (the best LOI and UL-94 of WPU-OP were 33.1% and V-0, respectively).89
Table 1 Essential characterizations for one-component HIFWPU
Performance or structure |
Characterization |
Reference |
Structure |
FTIR, 1H NMR, GPC |
90–93 |
Particle size and emulsion stability |
Nanosizer |
94 and 95 |
Viscosity and rheological properties |
Viscometer |
94 and 96 |
Tensile strength and elongation at break |
Lectronic and mechanical testing machine |
97–99 |
Thermal properties |
DSC, DMA, TGA, TGA-FTIR |
80 and 100–103 |
Flame-retardance |
SEM, EDS, UL-94, LOI, FTIR, cone calorimeter |
104–107 |
Water resistance |
Water absorption, contact angle measurement |
108–110 |
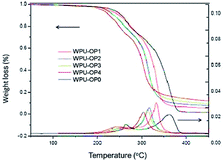 |
| Fig. 2 TG and DTG curves: WPU-OP0 (0 wt% OP550), WPU-OP1 (5 wt% OP550), WPU-OP2 (10 wt% OP550), WPU-OP3 (15 wt% OP550), and WPU-OP4 (20 wt% OP550).73 2008 Wiley Periodicals, Inc. | |
HFPO is another kind of soft segment modifier (Scheme 3). The synthesis is the same as for WPU-OP, except for the flame retardant. The Td moves to low temperature and its thermostability decreases, but the thermal decomposition rate is reduced to delay thermal decomposition (Fig. 3). In a soft modified system, the lower Tgs means higher microphase separation.111,112 There are two reasons why Tgs decreases with the increase in the HFPO content. One reason is that HFPO is a soft modifier, which reduces the content of hard segments in the PU system and lifts the restraint on the soft segments and enhances mobility at low temperatures.113 Another reason is that there is –O–CH3 in the sidechains, which provides strong chain flexibility. Details of the mechanical properties and flame-retardance are listed in Table 2.
 |
| Scheme 3 Structure of HFPO. | |
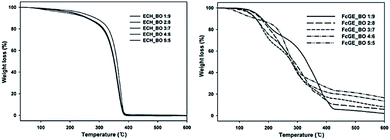 |
| Fig. 3 TGA thermograms for the poly(ECH-co-BO) series and poly(FcGE)-BO copolymer series.112 2014 Springer Science+Business Media, LLC. | |
Table 2 Tensile strength and flame-retardance of soft segment modification, hard segment modification, and soft-hard segment modification systems
Properties (content of flame retardant) |
WPU-OP |
WPU-HF |
WPU-F6 |
WPU-OD |
WPU-OPF6 |
WPU-HFF6 |
WPU-OPOD |
LOI (%) |
(15 wt%) |
33.1 |
34.2 |
30.2 |
30.6 |
30.4 |
36.6 |
31.4 |
(5 wt%) |
23.4 |
29.1 |
26.4 |
29.6 |
29.4 |
31.7 |
30.4 |
UL-94 |
(15 wt%) |
V-0 |
V-0 |
V-0 |
V-1 |
V-0 |
V-0 |
V-0 |
(5 wt%) |
V-0 |
V-0 |
V-1 |
V-1 |
V-0 |
V-0 |
V-1 |
Tensile strength |
(15 wt%) |
2.1 |
10.4 |
12.6 |
9.3 |
14.8 |
7.5 |
5.0 |
(5 wt%) |
12.6 |
17.8 |
8.2 |
2.1 |
16.1 |
12.0 |
9.3 |
Hard segment modification
Hard segment flame-retardant modification is like soft segment flame-retardant modification: WPU is incorporated with a modified hard segment flame-retardant, which means a flame-retardant unit is embedded into the hard segment of PU. Hard segment flame-retardant modification is also a simple method. The product not only has high flame-retardance but can also improve other properties like tensile strength. Common halogen-free phosphorus hard segment flame retardants include diethyl-N,N-bis(2-hydroxyethyl)aminomethylphosphonate (Fyrol-6) and 2,7-bis(N,N-dimethylamine)-1,6,3,8,2,7-octahydrodioxadiazole diphosphate (ODDP), which have reactive units that react with isocyanate. Fyrol-6 is a new reactive phosphorus flame retardant that has good anti-oxidation and water resistance properties because it can add phosphorus to the hard segments of PU chains via chemical reaction (Scheme 4a). The synthesis is like that in Scheme 2. Compared with soft segment modified systems, in WPU-F6 system, Td is reduced by Fyrol-6. However, the thermal decomposition rate (vd) and char yield of WPU-F6 decreased and increased, respectively, by adding Fyrol-6. Although Fyrol-6, as a hard segment modifier, has high rigidity and strength, elongation at break is reduced due to the large group volume.114 The LOI and UL-94 values can reach 30.1% and V-0, respectively. From the SEM images (Fig. 4), the char surface of an unmodified sample (WPU-F60, 0 wt% Fyrol-6) appears loose and porous. These cavities are beneficial for transferring oxygen and heat, which accelerates burning.115,116 After adding Fyrol-6 (WPU-F63, 3 wt% Fyrol-6), it forms dense, smooth and hole-free P-C layers that cover the material surface to isolate it from oxygen and heat, which is like a typical carbon layer in a flame-retardant mechanism.117 Fyrol-6 improves the flame-retardance of WPU. The WPU-F6 can reach V-0 and 30.1%, respectively, which makes it a nonflammable material.
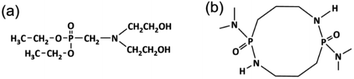 |
| Scheme 4 Structures of (a) Fyrol-6 and (b) ODDP.58 2014 Wiley Periodicals, Inc. | |
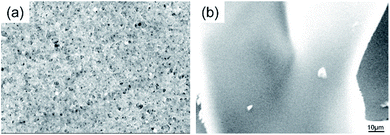 |
| Fig. 4 SEM of the carbon layers of (a) WPU-F60 and (b) WPU-F63 at 500 °C.58 2014 Wiley Periodicals, Inc. | |
OP550, HFPO and Fyrol-6 are all industrial products. ODDP (Scheme 4b) is a laboratory-made flame retardant, fabricated by Luo's group led by Gu.58 The synthesis is like those of the above three systems. In the WPU modified by the ODDP (WPU-OD) system, the viscosity and particle size were larger but were still <1.5 mPa s and 220 nm, respectively, and Td was reduced through ODDP. However, the vd and char yield of WPU-OD6 (6 wt% ODDP) were made lower and higher, respectively, by adding ODDP.100 Although ODDP, as a hard segment modifier, has high rigidity and strength that improve tensile strength, the elongation at break was reduced due to the large group volume, which is similar to the case for WPU-F6 modified via Fyrol-6.111 The best LOI and UL-94 can reach 30.6% and V-1, respectively. Details of the mechanical properties and flame-retardance are listed in Table 2.
Soft-co-hard segment modification
To further improve flame-retardance without affecting mechanical properties, soft and hard segment co-modification was developed. Three modified systems are introduced in this section: the OP550/Fyrol-6 system (WPU-OPF6), HFPO/Fyrol-6 system (WPU-HFF6), and OP550/ODDP system (WPU-OPOD).57,73,118 The synthesis of co-modification is different from that of single modification (Scheme 2). R generally ranges from 1.3 to 1.7 because of the preparation technology.82–84 The solid content is often 20–30% to obtain good film properties.85–87 As a result, the variation of the co-modification system is like that of the single system. Td decreased with the addition of OP550 but the char yield of modified samples was 2.3-times that of non-modified samples. This means that the soft and hard segment co-modification modifier plays a more obvious role in the material carbonization during high-temperature decomposition.105 Adding OP550 also decreased the tensile strength and elongation at break, which is like the case for WPU-OP. The LOI reached 30.4%, making it a nonflammable material, which is a little more than that of WPU-F6 but less than those of WPU-OP and WPU-HF.
The synthesis of WPU-HFF6 is like that of WPU-OPF6. The Tmax was reduced remarkably with the addition of HFPO. Meanwhile, HFPO delayed vd but reduced thermostability. The char yield increased sharply from 0.4% to 14.0% due to the addition of organophosphorus. Adding HFPO also decreased the tensile strength and elongation at break, which is like the case for WPU-HF. This was because of the large content and volume of soft segments. The best LOI was 37.1%, which is characteristic of a non-combustible material. This value is much higher than those of WPU-HF and WPU-F6, which means that the soft segment flame-retardant modifier plays an important role in improving flame-retardance. The synthesis of the final co-modification system is also like that of WPU-OPF6, and the variation in thermal properties is also like those of the above two systems. The char yield increased drastically from 4.84 to 14.03%. OP550 and ODDP also delayed vd in HIFWPU systems, as shown in Fig. 5. The LOI can reach 31.6%, which is 1.0% larger than that of WPU-OD. However, the modification efficiency of ODDP is a little lower than that of Fyrol-6. Fyrol-6 has more organophosphorus than ODDP at the same additive amount.
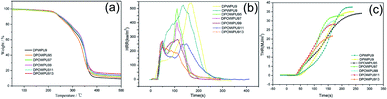 |
| Fig. 5 (a) TGA, (b) HRR and (c) THR curves of OWPU-OPOD systems.57 © 2015 American Chemical Society. | |
Summary
To clearly show the key values of each system, a list is provided in Table 2. Although the hard segment flame-retardant modifier can improve the tensile strength, the elongation at break also decreases. In terms of flame-retardance, the LOI of soft segment modified systems is commonly larger than that of hard segment modified systems. Meanwhile, the LOI of soft and hard segment co-modified systems are also higher than that of hard segment modified systems. These indicate that the soft segment flame-retardant modifier plays an important role in improving flame-retardance because it has more organophosphorus than the hard segment flame-retardant modifier. The P-C from the soft and hard segment flame-retardant modifiers produces stable polyphosphoric acid, which forms a thermal insulation layer that protects the internal material to reduce weight loss in PU at high temperatures. Usually, more organophosphorus is beneficial for forming P-C layers to obtain better flame-retardance.
Two-component HIFWPU
Lu (one of Luo's colleagues) and the authors used methoxypolyethylene glycols (MPEG) and hexamethylene diisocyanate (HDI) trimer to prepare hydrophilic curing agents containing ether bonds.119 Lu further used toluene diisocynate (TDI), DMPA, and dibromoneopentyl glycol (DBNPG) to synthesize waterborne flame-retardant hydroxyl prepolymers that were then reacted with a hydrophilic curing agent to obtain two-component HIFWPU. The hydrophilic curing agent improved the thermostability, tensile strength, and water resistance of the two-component WPU. Meanwhile, the LOI was over 28.0% with the addition of 10 wt% DBNPG. In our previous research, various kinds of two-component HIFWPU and hydrophilic curing agents have been investigated, which have been introduced in the review.34,119–122 The mixed emulsion was subjected to high-speed shear mixing or ultrasonic vibration to gain a two-component HIFWPU (Scheme 5).
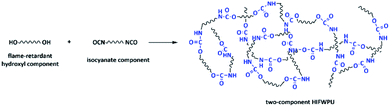 |
| Scheme 5 The reaction of the flame-retardant hydroxyl component and isocyanate component. | |
Both Fyrol-6 and OP550 promote the degradation of WPUs and increase the production of carbon residue. The compositions of HIFWPU modified by Fyrol-6 and OP550 have been displayed in ref. 34. For consistency with previous research, the results of 2K-WPU1 (without being modified by flame-retardant hydrophilic curing agent) and 2K-WPU2 (modified by flame-retardant hydrophilic curing agent) are compared in Table 3.123,124 The flame-retardance and thermostability also improved because the flame-retardant hydrophilic curing agent decomposes to emit SO2. TGA-FTIR analysis showed that the SO2 combines with phosphoric acid and polyphosphoric acid to play a concerted catalytic role that improves the flame-retardance of the two-component WPU during heating. Subsequently, a functional two-component HIFWPU was researched by adding nano-TiO2 to further improve flame retardance. Consequently, the LOI and UL-94 reached 30.5% and V-0, respectively. TGA and TGA-FTIR indicated that nano-TiO2 can restrain thermal decomposition to improve flame-retardance and combine with phosphoric acid and polyphosphoric acid to provide synergistic flame-retardance.125,126 Meanwhile, nano-TiO2 also provides ultraviolet radiation resistance and visible light-shielding effects because of its light-influencing characteristics.127–130
Table 3 LOI and UL-94 of various two-component HIFWPU
Properties |
OFWPU |
FFWPU |
2K-WPU2 |
FRWPU |
PNWPU |
PU3 |
LOI (%) |
29.2 |
28.2 |
29.4 |
27.7 |
27.2 |
28.1 |
UL-94 |
V-0 |
V-0 |
V-0 |
V-0 |
V-0 |
V-2 |
Aras, from Turkey, prepared two-component HIFWPU with various contents of phosphorous compound and N3300 curing agent.120 He found that the LOI could reach 29.0%. The Universitat Rovira i Virgili in Spain prepared two-component HIFWPU via Fyrol-6;23 researchers also synthesized an epoxy system IHPO-DGEBA via IHPO and DGEBA. Northwest Agricultural and Forestry University also prepared a two-component HIFWPU via Fyrol-6.68 A series of hydroxy-terminated PU dispersions were prepared through 4,4-diphenyl-methane-diisocyanate, polypropylene glycol, and hydrophilic-modified polyisocyanate curing agent. The LOI and UL-94 were 28.1% and V-2, respectively, with a 12.0% content of Fyrol-6 (PU3). The burning rate was restrained after adding Fyrol-6 with an increasing char yield of 19.9% (Fig. 6). Besides, the tensile strength, modulus, and impact strength were all improved due to the addition of Fyrol-6.
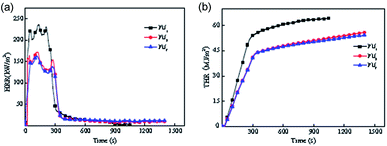 |
| Fig. 6 Conical calorimetry curve of flame-retardant two-component WPU. (a) Heat release rate (HRR) curve; (b) total heat release (THR) curve.68 2015 Elsevier B.V. | |
Zhang from Sichuan University prepared a flame-retardant chain extender and flame-retardant polyols,75,110 which were applied in a two-component HIFWPU. To balance the flame-retardance, thermostability, and mechanical properties, FRWPU was synthesized using the cyclic phosphoramidate lateral group bearing diol (PNMPD) and a silane coupling agent. He found that the tensile strength increased to 6.1 MPa with the addition of 12.0% PNMPD and 60% silane coupling agent. Meanwhile, the LOI and UL-94 were 27.7% and V-0, respectively. Furthermore, the thermal release rate peak (PHRR), total heat release (THR), smoke production rate (SPR), and total suspended particulates (TSP) decreased to 36.0%, 42.9%, 40.1%, and 35.4%, respectively. According to thermostability and flame-retardant mechanisms, the condensed phase flame-retardance obtained from phosphorus and silane chains could restrain the emissions of heat and inflammable gas and accelerate the formation of carbon layers containing –P(
O)–O–Si–. Zhang further used PNMPD to act as a chain extender to prepare PNWPU. He found that the thermostability and water resistance were improved but not the flame-retardance. The LOI and UL-94 were 27.2% and V-0, respectively, while the PHRR, THR, SPR, and TSP decreased to 44.7%, 39.0%, 42.9%, and 36.1%, respectively. Additionally, the surface of the condensed phase was covered with rugged and intumescent carbon layers containing abundant polyphosphoric acid, which could effectively impede the conduction of heat, oxygen gas, and volatile matter from the flame-retardant and shielding areas.
Hyperbranched HIFWPU
To further develop the HIFWPU, Luo's group synthesized hyperbranched HIFWPU and their blocking products via blending halogen-free flame-retardants and hyperbranched WPU. Tian synthesized acetic anhydride waterborne hyperbranched PU (WHBPU) via IPDI, DMPA, and diethanol amine (DEOA).131 Acetyl-terminated waterborne hyperbranched PU (AWHBPU) and WHBPU have been successfully synthesized after acetic anhydride and stearic acid-blocking, as proven via FTIR, 13C-NMR, GPC, and functional calculations.132 The viscosity and particle size of three kinds of hyperbranched WPU were all <7.0 mP s and 100 nm, respectively. The Td of WHBPU and AWHBPU was 185 °C, but that of stearic acid-terminated waterborne hyperbranched PU (SWHBPU) was 205.7 °C because the bond energy of stearic acid is lower.131 The Tg of AWHBPU and SWHBPU were lower than that of SWHBPU due to acetic anhydride and stearic acid-blocking WHBPU, which decreased the constraint of the hydrogen bonds from the hydroxyl groups. Thereafter, three kinds of hyperbranched HIFWPU were prepared through the blending of hyperbranched WPU with its blocking products. As a result, the LOI remained at over 30.0% and even the LOI of SWHBPU was 32.3%. AWHBPU and SWHBPU can promote phosphorus migration to the film surface to improve flame-retardance during the curing progress. Meanwhile, adding hyperbranched WPU can expand microphase separation to increase tensile strength, especially elongation at break in AWHBPU and SWHBPU.133
Tian prepared three kinds of hyperbranched WPU/organophosphorus hard segment HIFWPU (FWPU, FAPU, and FSPU). The variation in their viscosities was like that of non-mixed hyperbranched WPUs (Fig. 7). Although the thermostability was increased by adding hyperbranched WPU, the Td of soft segments was higher. Meanwhile, the decomposition was delayed by adding AWHBPU and SWHBPU. Besides, microphase separation and carbon yield were increased due to phosphorus enrichment by adding AWHBPU and SWHBPU. Their flame-retardance increased with the flame-retardant effectiveness. Additionally, Tian prepared three kinds of hyperbranched WPU/organophosphorus soft segment HIFWPU (OWPU, OAPU, and OSPU). The variation in their viscosities was like that of non-mixed hyperbranched WPU (Fig. 7). Although the thermostability was increased by adding hyperbranched WPU, the Td of soft segments was higher. Meanwhile, the decomposition was delayed by adding AWHBPU and SWHBPU. Besides, the crosslinking degree and carbon yield were higher due to the phosphorus enrichment of WHBPU and SWHBPU. For comparison with the six kinds of hyperbranched WPU/HIFWPU above, Tian synthesized hyperbranched WPU/compound HIFWPU (TWPU, TAPU, and TSPU). The variations in their viscosity, mechanical properties, and water resistance were like those in non-mixed hyperbranched WPU. The flame retardance was maintained at a high level, and WBHPU and SWHBPU can maintain flame retardance in different systems.
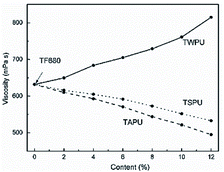 |
| Fig. 7 Viscosities of FWPU, FAPU, and FSPU.131 1994–2012 China Academic Journal Electronic Publishing House. | |
In summary, WBHPU and SWHBPU can maintain flame-retardance in various systems. The variations in viscosity, mechanical properties, and water resistance of coated systems were consistent with those of the non-coated polyester Oxford tent cloth. The flame-retardance and other properties of hyperbranched HIFWPU are largely dependent on the structure of hyperbranched WPU and the type of flame retardant used.
Other types of HIFWPU
Besides one-component HIFWPU, two-component HIFWPU, and hyperbranched HIFWPU, there are other types of HIFWPU prepared through special techniques. Feng from Luo's group prepared cross-linked prepolymers using polyether triols, polyether glycol, a hydrophilic chain extender, and diisocyanate. Then, Feng134 used OP550 and an oleophilic chain extender to modify the cross-linked prepolymer to obtain high-hydrostatic HIFWPU. The emulsion had a good appearance and stability after adding 12 wt% of OP550. Although the Td decreased, the carbon yield increased because the phosphate ester binds with low energy.58,105 The high hydrostatic HIFWPU had good compatibility, and a tensile strength and LOI of 26.5 MPa and 28.4%, respectively. Besides, the flame-retardant mechanism of high hydrostatic HIFWPU was similar to that of two-component HIFWPU.73 The particle size and zeta potential of the post-chain extension of HIFWPU were below 100 nm and ∼30 μm, respectively. Meanwhile, the thermostability decreased because brominated polyphenyl ether (BPPO) accelerated the decomposition of PU chains. BPPO was decomposed to produce phosphoric acid, which catalyzed the decomposition of soft and hard segments; BPPO also increased the carbon yield and compatibility. The tensile strength and LOI were improved to 26.0 MPa and 28.8%, respectively, by adding BPPO. PHRR and THR were reduced to 65% and 26.3%, respectively. The increasing magnesium hydroxide sulfate hydrate (MHSH) played the role of “diluent” in fire to enhance the fire performance index (FPI).135 The gas-phase and coagulation-phase flame-retardance of BPPO are key to promoting the formation of carbon and the release of nonflammable gases (Fig. 8).
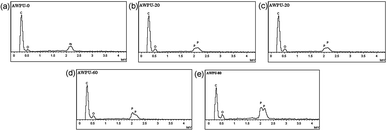 |
| Fig. 8 EDS of carbon yield after burning with various BPPO. (a) AWPU-0; (b) AWPU-20; (c) AWPU-40; (d) AWPU-60; (e) AWPU-80.135 2007 Springer Science+Business Media, LLC. | |
Chem-physical flame retardants are always reactive inorganic nanomaterials (such as nano-montmorillonite, nanometer silicon dioxide, and nanosilicate) modified by chemical reactive groups.136 Usually, reactive inorganic nanomaterials provide characteristics like rigidity, heat resistance, and chemical resistance to WPUs. Besides, some reactive inorganic nanomaterials also provide flame-retardance to WPU. So far, intumescent flame retardants have attracted more attention for use in high-transparency coatings because of the non-addition of another carbon source, which can reduce solid addition.137–140 Ammonium polyphosphate (APP-II) is a halogen-free inorganic flame retardant with N and P, which has a high polymerization degree, good thermostability, low hygroscopicity, and is green.67 However, APP-II has many disadvantages; for example, flame-retardant coated textiles prepared via APP-II show whitening, frosting, and low strength. Zhou added ethyl orthosilicate and methyltrimethoxysilane as precursors to cover an APP-II carrier to obtain synergistic flame-retardance through the sol–gel method. Consequently, the improved flame-retardant coated textile did not appear to have frosting and had good application prospects. Zeng et al. also used APP-II to prepare a flame-retardant coating adhesive.141 Besides phosphorus-containing polymers, antimony oxide and chlorocyclic triphosphoride are popular in the synthesis of intumescent HIFWPU. This kind of HIFWPU has many functional properties in addition to flame-retardance, like a matte appearance, water resistance, and zero formaldehyde release. The flame-retardant mechanism of intumescent HIFWPU is as follows. Tripolycyanamide and its salt belong to nitrogen or N–P flame retardants, which mainly consist of an air source and acid salt. Most current intumescent flame retardants contain N or P as a flame-retardant activity component.142 The advantages of intumescent flame retardants are low toxicity, corrosion, and smoke production. Most flame retardants containing tripolycyanamide and its salt have intumescent char formation and release CO2, N2, and NH3 without halogen hydride during heating. Meanwhile, the T0 of the flame retardant is >250 °C. Halogen-free intumescent HIFWPU has N–P synergy flame-retardance143 and a condensed-gas phase because phosphate is the main part of the intumescent flame retardant.
Applications
Currently, HIFWPU are mainly applied as coatings for textiles, leather, and furniture to provide flame-retardance and other functional properties. In this section, we introduce application examples for textiles and wood (most is research from Luo's group). Chen prepared a terylene textile coated with HIFWPU modified through HFPO. As a result, the flame-retardance of the textile coating was improved because the LOI increased and the UL-94 reached B1.73 Although the color change was reduced to 1.87, the color fastness was maintained at level-1. Stiffness slightly increased although the wrinkle recovery angle slightly decreased. The wash resistance of the coated terylene textile was good in soap testing. Li also prepared a terylene textile coated with HIFWPU modified with Fyrol-6. The flame-retardance of the textile coating maintained its primary color and soft hand-feel.144–146 The LOI increased from 14.6% to 20.3% and the UL-94 reached B1 (Fig. 9a). There was no dark smoke and little smoke production during heating. The carbon layer of the nonmodified textile had large amounts of fluffy cavities after heating (Fig. 9b).147–149 The carbon layer of the modified textile had no cavities after heating and formed a smooth and dense surface to isolate O2 and heat (Fig. 9c).
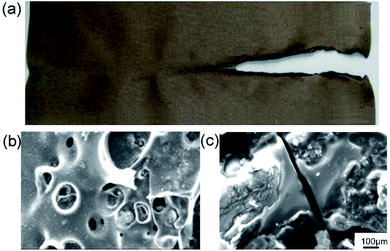 |
| Fig. 9 Images and SEM of flame-retardant Dacron after vertical burning: (a) textile after vertical burning; and SEM images of the surfaces of the (b) nonmodified Dacron and (c) modified Dacron.150,151 1994–2016 China Academic Journal Electronic Publishing House. | |
Gu found that polyester Oxford tent cloth modified with ODDP had a good adhesive force but a hard hand-feel.58 The LOI and UL-94 were 23.7% and B2, respectively. Further, Gu found that the LOI of polyester Oxford tent cloth modified with Fyrol-6 was 21.6%. Polyester Oxford tent cloth modified with OP550 and Fyrol-6 had outstanding flame-retardance, with LOI = 25.2% and UL-94 = B1.57 Furthermore, the polyester Oxford tent cloth modified with OP550 and Fyrol-6 had a good adhesive force and soft hand-feel, even though it had a C-level antistatic property.150,151 Zhu152 incorporated anthraquinone chromophore (DV26) and OP550 to synthesize flame-retardant and colorful WPU (DOWPU) coatings. He obtained a LOI of 29.7%. Meanwhile, the dry rubbing, wet rubbing and washing color-fastness of modified polyester fabrics were 4–5, 4–5 and 4, respectively (Fig. 10). Moreover, the LOI of polyester fabrics coated with DOWPU also reached 27.1%, which displayed excellent application properties of DOWPU. Ding modified montmorillonite (MMT) with OP550 to obtain high-quality and monolayered nanosheets.153 The high-quality and monolayered nanosheets were then added to the in situ polymerization to prepare environment-friendly WPU (OPWPU) coating154 and low gloss WPU (OWPU) coatings.155 The 60° gloss of coated polyvinyl chloride (PVC) leather was below 0.3 GU and 4.6 GU, respectively. Meanwhile, the LOI was over 18% after being coated. Feng used high hydrostatic HIFWPU to coat the Oxford cloth and then washed the Oxford cloth. Feng found that the LOI and UL-94 were 23.4% and V-1, respectively, after soaping.156 The water pressure resistance increased from 5.9 MPa to 9.7 MPa after soaping, which showed brilliant water pressure resistance in the textile. The stiffness, color change, and wrinkle recovery angle of the Oxford cloth were improved. A wood WPU varnish modified with BPPO was prepared by Wu. As a result, table-dry performance, water resistance, solvent resistance, abrasion resistance, and hardness were all improved.157 Then, Wu used wood WPU varnish modified with BPPO to coat the surface of polyester Oxford tent cloth. The LOI and UL-94 were 26.3% and B1, respectively. Smoke production and toxic pollutants decreased during heating. Color change, stiffness, and breaking strength were improved by adding BPPO.
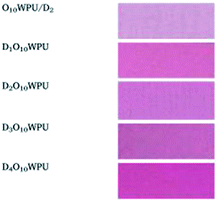 |
| Fig. 10 Images of coated polyester fabrics.152 2019 Elsevier B.V. | |
The author also prepared halogen-free two-component WPU varnishes by adding Fyrol-6 or OP550. The results are listed in Table 4, which shows that the pencil hardness was significantly improved. In particular, the pencil hardness reached 2H by adding Fyrol-6. Additionally, square impact, backswing, flexibility, adhesion, and solvent resistance were maintained at the highest level according to Chinese standards.158
Table 4 Coating application evaluation parameters
Samples |
Pencil hardness |
Shock resistance |
Flexibility |
Adhesive force |
Solvent resistance |
Square impact |
Back flushing |
FWPU |
HB |
>120 |
>120 |
7 |
No loss |
Pass |
FFWPU-15 |
2H |
>120 |
>120 |
7 |
No loss |
Pass |
OFWPU-15 |
H |
>120 |
>120 |
7 |
No loss |
Pass |
Hyperbranched HIFWPU can improve the hydrostatic pressure resistance, stiffness, tongue-tearing strength, and wrinkle-recovery angle of textiles.132 The after-flame time of the coated textile was still 0 s. The coating textile had good soap-to-wash resistance after adding hyperbranched HIFWPU. Tian prepared three kinds of hyperbranched WPU/organophosphorus hard segment HIFWPU (FWPU, FAPU, and FSPU), which were used to coat polyester Oxford tent cloth; the flame-retardance was slightly affected. WBHPU and SWHBPU can maintain flame-retardance in Oxford tent cloth. Additionally, Tian prepared three kinds of hyperbranched WPU/organophosphorus soft segment HIFWPU (OWPU, OAPU, and OSPU), which were also used to coat polyester Oxford tent cloth. The flame retardance was slightly affected, and WBHPU and SWHBPU maintained flame retardance in the systems. Finally, FWPU, FAPU, and FSPU were used to coat polyester Oxford tent cloth. The flame-retardance was affected slightly.
Xu used intumescent flame retardants to prepare flame-retardant coating adhesives. The flame-retardant coating adhesive was a novel, halogen-free, green, flame-retardant coating adhesive, which had low smoke and toxicity and did not form melting drops during heating. Pan synthesized an APP-II-coated siloxane flame-retardant coating agent. The LOI and after-flame time of the coated textile were 44.3% and 0 s, respectively, after baking at 180 °C. Jiang prepared a flame-retardant coating adhesive by adding a cationic phosphorus flame retardant, antimony trioxide, and melamine.159 The flame-retardant coating adhesive solved the problems of a non-durable flame-retardant effect, heavy losses, and easy color change during burning. Furthermore, the flame-retardant effect, smoke density, and smoke toxicity of the flame-retardant coating adhesive all reached the standard of non-combustibility, so it could be applied as seating fabric in aircraft and high-speed trains.
HIFWPU not only has good flame-retardancy and environmental protection but also has many functionalities such as luminescence, dyeing and so on. However, the versatility of HIFWPU urgently needs to be improved and its applications expanded in textile, wood, automotive and other fields. This is based on the in-depth discussion on HIFWPU, in order to better face the applications. The next step can use different physical or chemical methods to give HIFWPU more functionalities, which can balance mechanical properties, thermostability and flame-retardancy. Details are as follows: (1) to expand the synthesis method, the effective flame-retardancy of HIFWPU will be improved by designing and synthesizing flame retardants with different structure types. (2) HIFWPU can be endowed with properties such as anti-corrosion, super hydrophobicity, biological anti-bacterial and biodegradability, to meet the needs of broader application fields. (3) The thermostability and mechanical properties of HIFWPU can be improved by adding a matrix containing fluorine and a rigid large ring.
Conclusions
Different materials and applications have different requirements for HIFWPU, which means the matching demands for collecting halogen-free flame retardants. The ideal halogen-free flame-retardant waterborne PU has high flame-retardant efficiency, environmental friendliness, fine compatibility, and good thermostability and photostability. It also has a simple fabrication process, readily-available raw materials, and low cost. Hardly any HIFWPU can satisfy all the above conditions. Generally, the properties of WPU are reduced by adding too many nanometre-sized inorganic fillers. Although HIFWPU modified with P–N flame retardants are non-toxic, low smoke, and non-polluting, they are too expensive. Intumescent flame retardants can endow WPU with excellent properties but their surfaces need to be modified to prepare stable emulsions. Nowadays, HIFWPU not only have improved flame-retardance but also satisfy various requirements, which endow them with good potential for development. In the future, HIFWPU will occupy the main market in the surface finishing field and will be able to replace traditional products such as halogen-containing FWPU, solvent-based PU and blending-FWPU. Moreover, HIFWPU will be further developed due to their controllable molecular chain structure and excellent biocompatibility, which facilitate creative synthesis, novel modification and high-performance products.
Author contributions
X. Y.: visualization, conceptualization, writing-reviewing and editing. L. L. investigation. H. P.: writing-original draft preparation. Y. L.: project administration. B. Z.: supervision.
Conflicts of interest
There are no conflicts to declare.
Acknowledgements
This work is funded by the National Natural Science Foundation of China under Grant No. 51905295, Talent Introduction Program of BUCT under Grant No. buctrc202101 and the National Key Research and Development Program of China under Grant No. 2016YFC0204400.
Notes and references
- K. L. Noble, Prog. Org. Coat., 1997, 32, 131–136 CrossRef CAS.
- W. J. Macknight and M. Yang, J. Polym. Sci., Polym. Symp., 1973, 42, 817–832 CrossRef.
- D. E. Fiori, Prog. Org. Coat., 1997, 32, 65–71 CrossRef CAS.
- C. E. Tas, E. Berksun, D. Koken, S. Unal and H. Unal, ACS Appl. Polym. Mater., 2021, 3, 3929–3940 CrossRef CAS.
- N. Ballard, ACS Appl. Polym. Mater., 2020, 2, 4045–4053 CrossRef CAS.
- D. A. Ley, D. E. Fiori and R. J. Quinn, Prog. Org. Coat., 1999, 35, 109–116 CrossRef CAS.
- T. Hisakazu, S. Yasuyuki and Y. Fumio, Colloids Surf., A, 1999, 153, 597–601 CrossRef.
- R. Pires and H. J. Laas, Surf. Coat. Int., Part B, 2002, 85, 169–242 CrossRef.
- O. L. Figovsky, L. Shapovalov and O. Axenov, Surf. Coat. Int., Part B, 2004, 87, 71–148 CrossRef.
- C.-H. Yang, L.-W. Chong, L.-M. Huang, Y.-L. Lee and T.-C. Wen, Mater. Chem. Phys., 2005, 91, 154–160 CrossRef CAS.
- Y. Wang, J. Deng, J. Zhao and H. Shi, Prog. Org. Coat., 2020, 148, 105845 CrossRef CAS.
- Y. Wang, J. Deng, J. Zhao and H. Shi, Polym. Adv. Technol., 2020, 32, 153–164 CrossRef.
- S. Li, X. Wang, M. Xu, L. Liu, W. Wang, S. Gao and B. Li, Polym. Adv. Technol., 2021, 32, 4805–4814 CrossRef CAS.
- U. von Pidoll, IEEE Trans. Ind. Appl., 2008, 44, 15–19 CAS.
- Y. Tang, D.-Y. Wang, X.-K. Jing, X.-G. Ge, B. Yang and Y.-Z. Wang, J. Appl. Polym. Sci., 2008, 108, 1216–1222 CrossRef CAS.
- G. Malucelli, in Eco-friendly Waterborne Polyurethanes, CRC Press, 2022, ch. flame-retardant waterborne polyurethanes, p. 17 Search PubMed.
- S. Yin, X. Ren, P. Lian, Y. Zhu and Y. Mei, Polymers, 2020, 12, 32635235 Search PubMed.
- P. Zhang, P. Xu, H. Fan, Z. Sun and J. Wen, Appl. Surf. Sci., 2019, 471, 595–606 CrossRef CAS.
- B. Yıldız, M. Ö. Seydibeyoğlu and F. S. Güner, Polym. Degrad. Stab., 2009, 94, 1072–1075 CrossRef.
- M. A. El-Fattah, A. M. El Saeed, M. M. Dardir and M. A. El-Sockary, Prog. Org. Coat., 2015, 89, 212–219 CrossRef CAS.
- F. Gelebi, L. Aras, G. Gündüz and I. M. Akhmedov, J. Coat. Technol. Res., 2003, 75, 65–71 Search PubMed.
- P. Zhang, H. Fan, S. Tian, Y. Chen and J. Yan, RSC Adv., 2016, 6, 72409–72422 RSC.
- M. J. Alcón, G. Ribera, M. Galià and V. Cádiz, J. Polym. Sci., Part A: Polym. Chem., 2005, 43, 3510–3515 CrossRef.
- S. Wang, X. Du, X. Fu, Z. Du, H. Wang and X. Cheng, J. Appl. Polym. Sci., 2019, 137, 48444 CrossRef.
- Z. Zhao, D.-M. Guo, T. Fu, X.-L. Wang and Y.-Z. Wang, Polymer, 2020, 205, 122780 CrossRef CAS.
- Y.-C. Chung, J. W. Choi, S. J. Shin and B. C. Chun, Fibers Polym., 2012, 13, 815–822 CrossRef CAS.
- W. Zhou, D. Liu, T. Liu, L. Ni, H. Quan and Q. Sun, Mater. Res. Express, 2019, 6, 065303 CrossRef CAS.
- S. k. Gaddam and A. Palanisamy, Ind. Crops Prod., 2017, 96, 132–139 CrossRef CAS.
- F. Wu, Y. J. Li, R. J. Chen and S. Chen, Chin. Chem. Lett., 2009, 20, 115–118 CrossRef CAS.
- Y. H. Qi, Z. P. Zhang, Y. Zhang and M. Miao, Adv. Mater. Res., 2013, 634–638, 3033–3037 Search PubMed.
- K. S. Kang, C. Jee, J.-H. Bae, H. J. Jung, B. J. Kim and P. Huh, Prog. Org. Coat., 2018, 123, 238–241 CrossRef CAS.
- K. Petcharoen and A. Sirivat, Curr. Appl. Phys., 2013, 13, 1119–1127 CrossRef.
- Y.-L. Luo, B.-X. Wang and F. Xu, Sens. Actuators, B, 2011, 156, 12–22 CrossRef CAS.
- X. Yin, H. Pang, Y. Luo and B. Zhang, Polym. Chem., 2021, 12, 5400–5411 RSC.
- M. Faccini, L. Bautista, L. Soldi, A. M. Escobar, M. Altavilla, M. Calvet, A. Domènech and E. Domínguez, Appl. Sci., 2021, 11, 3446 CrossRef CAS.
- S. Tian, Polymers, 2020, 12, 1996 CrossRef CAS PubMed.
- S. Pradhan, P. Pandey, S. Mohanty and S. K. Nayak, Polym.-Plast. Technol. Eng., 2015, 55, 862–877 CrossRef.
- Y.-P. Song, D.-Y. Wang, X.-L. Wang, L. Lin and Y.-Z. Wang, Polym. Adv. Technol., 2011, 22, 2295–2301 CrossRef CAS.
- S.-M. Shau, R.-J. Jeng, J.-J. Lin, W.-C. Su and Y.-S. Chiu, Eur. Polym. J., 2002, 38, 683–693 CrossRef.
- L. Wang, F. Xu, H. Li, Y. Liu and Y. Liu, J. Coat. Technol. Res., 2016, 14, 215–223 CrossRef.
- G. M. Wu, J. Chen, S. P. Huo, G. F. Liu and Z. W. Kong, Carbohydr. Polym., 2014, 105, 207–213 CrossRef CAS PubMed.
- M. Akbarian, M. E. Olya, M. Ataeefard and M. Mahdavian, Prog. Org. Coat., 2012, 75, 344–348 CrossRef CAS.
- F. A. Zhang and C. L. Yu, J. Coat. Technol. Res., 2007, 4, 289–294 CrossRef CAS.
- P. Zhang, H. Fan, K. Hu, Y. Gu, Y. Chen, J. Yan, S. Tian and Y. He, Prog. Org. Coat., 2018, 120, 88–99 CrossRef CAS.
- D. Dave, S. Mestry and S. T. Mhaske, J. Coat. Technol. Res., 2021, 18, 1037–1049 CrossRef CAS.
- C. Wang, J. Zhang, J. Huang, H. Wang, M. He and L. Ding, Eur. J. Lipid Sci. Technol., 2021, 123, 2000248 CrossRef CAS.
- S. Yue, Z. Zhang, X. Fan, P. Liu and C. Xiao, Int. J. Polym. Anal. Charact., 2015, 20, 285–297 CrossRef CAS.
- P. J. A. Geurink, T. Scherer, R. Buter, A. Steenbergen and H. Henderiks, Prog. Org. Coat., 2006, 55, 119–127 CrossRef CAS.
- S. Zhu and W. Shi, Polym. Int., 2002, 51, 223–227 CrossRef CAS.
- S. S. Mahapatra and N. Karak, Polym. Degrad. Stab., 2007, 92, 947–955 CrossRef CAS.
- J. Borah, C.-s. Wang and N. Karak, Chin. J. Polym. Sci., 2009, 28, 107–118 CrossRef.
- R. H. Patel and K. S. Patel, Prog. Org. Coat., 2015, 88, 283–292 CrossRef CAS.
- P. K. Maji, N. K. Das and A. K. Bhowmick, Polymer, 2010, 51, 1100–1110 CrossRef CAS.
- S. Wang, X. Du, Y. Jiang, J. Xu, M. Zhou, H. Wang, X. Cheng and Z. Du, J. Colloid Interface Sci., 2019, 537, 197–205 CrossRef CAS PubMed.
- W. Du, Y. Jin, S. Lai, L. Shi, Y. Shen and J. Pan, Appl. Surf. Sci., 2019, 492, 298–308 CrossRef CAS.
- L. Wu, J. Guo and S. Zhao, Polym. Bull., 2016, 74, 2099–2116 CrossRef.
- L. Gu and Y. luo, Ind. Eng. Chem. Res., 2015, 54, 2431–2438 CrossRef CAS.
- L. Gu, Z. Ge, M. Huang and Y. Luo, J. Appl. Polym. Sci., 2015, 132, 41288 Search PubMed.
- X. Zhou, W. Tu and J. Hu, Chin. J. Chem. Eng., 2006, 14, 99–104 CrossRef CAS.
- S. Wang, Z. Du, X. Cheng, Y. Liu and H. Wang, J. Appl. Polym. Sci., 2018, 135, 46093 CrossRef.
- X. Ren, Y. Mei, P. Lian, D. Xie, W. Deng, Y. Wen and Y. Luo, Polymers, 2019, 11, 30960177 Search PubMed.
- M. Schellekens, D. Twene and A. van der Waals, Prog. Org. Coat., 2011, 72, 138–143 CrossRef CAS.
- K. S. Chen, T. L. Yu and Y. H. Tseng, J. Polym. Sci., Part A: Polym. Chem., 1999, 37, 2095–2104 CrossRef CAS.
- R. H. Patel and P. M. Kapatel, Int. J. Polym. Anal. Charact., 2018, 24, 1–9 Search PubMed.
- Y. Sun, C. Liu, Y. Hong, R. Liu and X. Zhou, Prog. Org. Coat., 2019, 137, 105323 CrossRef CAS.
- W. Meng, P. Li, Y. Lan, X. Shi, S. Peng, H. Qu and J. Xu, Sep. Purif. Technol., 2020, 233, 115988 CrossRef.
- Y. Wang, J. Deng, J. Zhao and H. Shi, Prog. Org. Coat., 2020, 147, 105758 CrossRef CAS.
- H. Si, H. Liu, S. Shang, J. Song, S. Liao, D. Wang and Z. Song, Prog. Org. Coat., 2016, 90, 309–316 CrossRef CAS.
- S. Hu, X. Luo and Y. Li, J. Appl. Polym. Sci., 2015, 132, 41425–41432 Search PubMed.
- J. Zhang, W. Tu and Z. Dai, Prog. Org. Coat., 2012, 75, 579–583 CrossRef CAS.
- P. Kardar, Prog. Org. Coat., 2015, 89, 271–276 CrossRef CAS.
- H. Chen, Y.-j. Luo, C.-p. Chai and Z. Ge, Polym. Mater. Sci. Eng., 2009, 25, 171–174 CAS.
- H. Chen, Y. Luo, C. Chai, J. Wang, J. Li and M. Xia, J. Appl. Polym. Sci., 2008, 110, 3107–3115 CrossRef CAS.
- F. Li, Y. Luo, X. Li and J. Li, CIESC J., 2012, 63, 653–657 CAS.
- P. Zhang, Y. He, S. Tian, H. Fan, Y. Chen and J. Yan, Polym. Compos., 2017, 38, 452–462 CrossRef CAS.
- S. M. Cakic, J. V. Stamenkovic, D. M. Djordjevic and I. S. Ristic, Polym. Degrad. Stab., 2009, 94, 2015–2022 CrossRef CAS.
- H. Mao, S. Qiang, Y. Xu and C. Wang, New J. Chem., 2017, 41, 619–627 RSC.
- M. Liao and D. Sun, J. Coat. Technol. Res., 2016, 13, 667–676 CrossRef CAS.
- A. Santamaria-Echart, I. Fernandes, A. Saralegi, M. R. Costa, F. Barreiro, M. A. Corcuera and A. Eceiza, J. Colloid Interface Sci., 2016, 476, 184–192 CrossRef CAS PubMed.
- X. Zhou, C. Fang, Q. Yu, R. Yang, L. Xie, Y. Cheng and Y. Li, Int. J. Adhes. Adhes., 2017, 74, 49–56 CrossRef CAS.
- H. Fu, Y. Wang, X. Li and W. Chen, Compos. Sci. Technol., 2016, 126, 86–93 CrossRef CAS.
- G. Wang, K. Li, W. Zou, A. Hu, C. Hu, Y. Zhu, C. Chen, G. Guo, A. Yang, R. Drumright and J. Argyropoulos, Prog. Org. Coat., 2015, 78, 225–233 CrossRef CAS.
- M. Li, X. Qiang, W. Xu and H. Zhang, Prog. Org. Coat., 2015, 84, 35–41 CrossRef CAS.
- S. M. Cakić, I. S. Ristić, M. M. Cincović, N. Č. Nikolić, L. B. Nikolić and M. J. Cvetinov, Prog. Org. Coat., 2017, 105, 111–122 CrossRef.
- L. Lei, Y. Zhang, C. Ou, Z. Xia and L. Zhong, Prog. Org. Coat., 2016, 92, 85–94 CrossRef CAS.
- Z. Ge, C. Huang, C. Zhou and Y. Luo, Prog. Org. Coat., 2016, 90, 304–308 CrossRef CAS.
- D. Gao, J. Feng, J. Ma, B. Lü, J. Lin and J. Zhang, Prog. Org. Coat., 2014, 77, 1834–1840 CrossRef CAS.
- T. K. Chen, T. S. Shieh and J. Y. Chui, Macromolecules, 1998, 31, 1312–1320 CrossRef CAS.
- L. Du, B. Qu and Z. Xu, Polym. Degrad. Stab., 2006, 91, 995–1001 CrossRef CAS.
- M. van der Schuur, B. Noordover and R. J. Gaymans, Polymer, 2006, 47, 1091–1100 CrossRef CAS.
- A. K. Mishra, D. K. Chattopadhyay, B. Sreedhar and K. V. S. N. Raju, J. Appl. Polym. Sci., 2006, 102, 3158–3167 CrossRef CAS.
- V. P. Ubale, A. D. Sagar, N. N. Maldar and M. V. Birajdar, J. Appl. Polym. Sci., 2001, 79, 566–571 CrossRef CAS.
- B. D. Kaushiva and G. L. Wilkes, Polymer, 2000, 41, 6981–6986 CrossRef CAS.
- V. García-Pacios, J. A. Jofre-Reche, V. Costa, M. Colera and J. M. Martín-Martínez, Prog. Org. Coat., 2013, 76, 1484–1493 CrossRef.
- X. Hu, X. Zhang, J. Liu and J. Dai, Polym. Int., 2014, 63, 453–458 CrossRef CAS.
- Y. Tao, A. Hasan, G. Deeb, C. Hu and H. Han, Polymers, 2016, 8, 94 CrossRef PubMed.
- B. Ghosh, S. Gogoi, S. Thakur and N. Karak, Prog. Org. Coat., 2016, 90, 324–330 CrossRef CAS.
- T. J. Lee, S. H. Kwon and B. K. Kim, Prog. Org. Coat., 2014, 77, 1111–1116 CrossRef CAS.
- J. A. Jofre-Reche, V. García-Pacios, V. Costa, M. Colera and J. M. Martín-Martínez, Prog. Org. Coat., 2015, 88, 199–211 CrossRef CAS.
- K. Mequanint, R. Sanderson and H. Pasch, Polym. Degrad. Stab., 2002, 77, 121–128 CrossRef CAS.
- R. Li and Z. Shan, Prog. Org. Coat., 2017, 104, 271–279 CrossRef CAS.
- H. J. Jin, Y. C. Han, J. H. Yang, D. S. Kwak and H. M. Jeong, Prog. Org. Coat., 2017, 103, 69–75 CrossRef.
- H. Nakatani, H. Ooike, T. Kishida and S. Motokucho, Prog. Org. Coat., 2016, 97, 269–276 CrossRef CAS.
- Q. Yong, F. Nian, B. Liao, Y. Guo, L. Huang, L. Wang and H. Pang, Polym. Bull., 2016, 74, 1061–1076 CrossRef.
- D. K. Chattopadhyay and D. C. Webster, Prog. Polym. Sci., 2009, 34, 1068–1133 CrossRef CAS.
- S. Zhu and W. Shi, Polym. Degrad. Stab., 2002, 75, 543–547 CrossRef CAS.
- J. Alongi, F. Carosio and P. Kiekens, Polymers, 2016, 8, 30974632 Search PubMed.
- Z. Ge and Y. Luo, Prog. Org. Coat., 2013, 76, 1522–1526 CrossRef CAS.
- L. Poussard, J. Lazko, J. Mariage, J. M. Raquez and P. Dubois, Prog. Org. Coat., 2016, 97, 175–183 CrossRef CAS.
- P. Zhang, Z. Zhang, H. Fan, S. Tian, Y. Chen and J. Yan, RSC Adv., 2016, 6, 56610–56622 RSC.
- S. L. Han and S. L. Hsu, Macromolecules, 1989, 22, 1100–1105 CrossRef.
- B.-S. Cho, J.-S. Kim, J.-M. Lee, J.-O. Kweon and S.-T. Noh, Macromol. Res., 2014, 22, 826–831 CrossRef CAS.
- L. Guo, L. Wang, S. Huang and J. Qu, J. Appl. Polym. Sci., 2017, 134, 44735 Search PubMed.
- K. Kojio, S. Nakashima and M. Furukawa, Polymer, 2007, 48, 997–1004 CrossRef CAS.
- M.-J. Chen, Z.-B. Shao, X.-L. Wang, L. Chen and Y.-Z. Wang, Ind. Eng. Chem. Res., 2012, 51, 9769–9776 CrossRef CAS.
- G. Malucelli, F. Carosio, J. Alongi, A. Fina, A. Frache and G. Camino, Mater. Sci. Eng., R, 2014, 84, 1–20 CrossRef.
- Y. Yuan, H. Yang, B. Yu, Y. Shi, W. Wang, L. Song, Y. Hu and Y. Zhang, Ind. Eng. Chem. Res., 2016, 55, 10813–10822 CrossRef CAS.
- F. Li, Y. Luo, X. Li and J. Li, Chin. J. Chem. Eng., 2012, 63, 653–657 CAS.
- X. Yin, Y. Luo and J. Zhang, Ind. Eng. Chem. Res., 2017, 56, 1791–1802 CrossRef CAS.
- L. Aras, F. Gelebi, G. L. Gondoz and I. M. Akhmedov, J. Coat. Technol., 2003, 75, 65–71 Search PubMed.
- D. B. Otts and M. W. Urban, Polymer, 2005, 46, 2699–2709 CrossRef CAS.
- W. J. Blank, Z. A. He and M. E. Picci, J. Coat. Technol., 2002, 74, 31–36 CrossRef.
- S. Hwang and P. P. Hsu, J. Ind. Eng. Chem., 2013, 19, 1377–1383 CrossRef CAS.
- S. C. Tjong, Mater. Sci. Eng., R, 2006, 53, 73–197 CrossRef.
- Z. Pala, E. Shaw, J. W. Murray, N. Senin and T. Hussain, J. Eur. Ceram. Soc., 2017, 37, 801–810 CrossRef CAS.
- P. Du, W. Hw and Z. Wang, Energ. Mater., 2005, 13, 99–102 Search PubMed.
- Y. Wen, S. Liu, Q. Zhang, Y. Zhang, Z. Yang and A. Zhu, Mater. Lett., 2016, 163, 262–265 CrossRef CAS.
- S. Monteiro, A. Dias, A. M. Mendes, J. P. Mendes, A. C. Serra, N. Rocha, J. F. J. Coelho and F. D. Magalhães, Prog. Org. Coat., 2014, 77, 1741–1749 CrossRef CAS.
- X. D. Chen, Z. Wang, Z. F. Liao, Y. L. Mai and M. Q. Zhang, Polym. Test., 2007, 26, 202–208 CrossRef CAS.
- K. Lee, K. Sato and A. R. Mohamed, Mater. Lett., 2016, 163, 240–243 CrossRef CAS.
- X. Tian, J. Li and Y. Luo, Trans. Beijing Inst. Technol., 2012, 32, 1195–1199 CAS.
- X. Tian, J. Li, Y. Luo and X. Li, Polym. Mater. Sci. Eng., 2013, 29, 19–22 CAS.
- F. Bao and W. Shi, Prog. Org. Coat., 2010, 68, 334–339 CrossRef CAS.
- J. Feng, Z. Ge, C. Chai, S. Wang, D. Yu, G. Wu and Y. Luo, Prog. Org. Coat., 2016, 97, 91–98 CrossRef CAS.
- S. Fang, Y. Hu, L. Song, J. Zhan and Q. He, J. Mater. Sci., 2007, 43, 1057–1062 CrossRef.
- J. W. Seo and B. K. Kim, Polym. Bull., 2005, 54, 123–128 CrossRef CAS.
- R. G. Puri and A. S. Khanna, J. Coat. Technol. Res., 2016, 14, 323–331 CrossRef.
- H. Li, Z. Hu, S. Zhang, X. Gu, H. Wang, P. Jiang and Q. Zhao, Prog. Org. Coat., 2015, 78, 318–324 CrossRef CAS.
- Z. Wang, E. Han and W. Ke, Can. Metall. Q., 2013, 46, 89–94 CrossRef.
- W. H. Awad and C. A. Wilkie, Polym. Adv. Technol., 2011, 22, 1297–1304 CrossRef CAS.
- J. Zeng, H. Chen, Y. Luo, J. Luo and S. Wang, Polym. Mater. Sci. Eng., 2010, 26, 121–124 CAS.
- J. Wang, S. Yang, G. Li and J. Jiang, J. Funct. Polym., 2003, 16, 238–242 CAS.
- G. Camino, L. Costa and E. Casorati, J. Appl. Polym. Sci., 1988, 35, 1863–1876 CrossRef CAS.
- F. Li, Y. Luo, X. Li and J. Li, Mater. Sci. Technol., 2011, 19, 36–40 CAS.
- F. Li, Y. Luo, X. Li, X. Li and J. Li, Dyeing Finish., 2013, 39, 13–15 CAS.
- F. Li, Y. Luo, X. Li and J. Li, J. Chem. Eng. Chin. Univ., 2018, 26, 716–720 Search PubMed.
- H. Yang and C. Q. Yang, Polym. Degrad. Stab., 2005, 88, 363–370 CrossRef CAS.
- S. Giraud, S. Bourbigot, M. Rochery, I. Vroman, L. Tighzert, R. Delobel and F. Poutch, Polym. Degrad. Stab., 2005, 88, 106–113 CrossRef CAS.
- E. D. Weil, R. H. Hansen and N. Patel, Prospective Approaches to More Efficient Flame-Retardant Systems, American Chemical Society, Washington, DC, 1990 Search PubMed.
- L. Gu and Y. Luo, Polym. Mater. Sci. Eng., 2015, 31, 1–5 CAS.
- L. Gu and Y. Luo, Trans. Beijing Inst. Technol., 2016, 36, 435–440 Search PubMed.
- J. Zhu, J. Li, W. Cai and Y. Luo, Prog. Org. Coat., 2020, 140, 105525 CrossRef CAS.
- Z. Ding, J. Li, B. Zhang and Y. Luo, Nanoscale, 2020, 12, 17083–17092 RSC.
- Z. Ding, J. Li, W. Xin and Y. Luo, Appl. Clay Sci., 2020, 198, 105798 CrossRef CAS.
- Z. Ding, J. Li, W. Xin, G. Zhang and Y. Luo, Prog. Org. Coat., 2019, 136, 105273 CrossRef CAS.
- J. Feng, Z. Ge, C. Chai, S. Wang, D. Yu, G. Wu and Y. Luo, Prog. Org. Coat., 2016, 97, 91–98 CrossRef CAS.
- G. Wu, J. Li, C. Chai, Z. Ge, J. Lin and Y. Luo, RSC Adv., 2015, 5, 97710–97719 RSC.
- D. A. Ley, D. E. Fiori and R. J. Quinn, J. Coat. Technol., 2000, 72, 63–69 Search PubMed.
- Z. Jiang, F. Ge, Z. Cai, L. Zeng, G. Chen and G. Chen, Dyeing Finish., 2008, 22, 6–9 Search PubMed.
|
This journal is © The Royal Society of Chemistry 2022 |
Click here to see how this site uses Cookies. View our privacy policy here.