DOI:
10.1039/D2RA01341J
(Review Article)
RSC Adv., 2022,
12, 10289-10305
Review on the preparation of fuels and chemicals based on lignin
Received
28th February 2022
, Accepted 29th March 2022
First published on 1st April 2022
Abstract
Lignin is by far the most abundant natural renewable aromatic polymer in nature, and its reserves are second only to cellulose. In addition to the rich carbon content, the structure of lignin contains functional groups such as benzene rings, methoxyl groups, and phenolic hydroxyl groups. Lignin degradation has become one of the high value, high quality and high efficiency methods to convert lignin, which is of great significance to alleviating the current energy shortage and environmental crisis. This article introduces the hydrolysis methods of lignin in acidic, alkaline, ionic liquids and supercritical fluids, reviews the heating rate, the source of lignin species and the effects of heating rate on the pyrolysis of lignin, and briefly describes the metal catalysis, oxidation methods such as electrochemical degradation and photocatalytic oxidation, and degradation reduction methods using hydrogen and hydrogen supply reagents. The lignin degradation methods for the preparation of fuels and chemicals are systematically summarized. The advantages and disadvantages of different methods, the selectivity under different conditions and the degradation efficiency of different catalytic combination systems are compared. In this paper, a new approach to improve the degradation efficiency is envisioned in order to contribute to the efficient utilization and high value conversion of lignin.
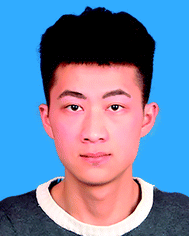 Peng-Hui Li | Peng-Hui Li received his B. E. degree in chemical engineering and technology from Liaoning Petrochemical University in 2016. He is currently pursuing his master postgraduates at the College of Light Industry and Food Science, Nanjing Forestry University under the supervision of Prof. Wenjuan Wu. His research has focused on modification and application of natural polymer. |
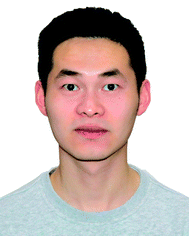 Jian-Peng Ren | Jian-Peng Ren received his B. E. degree in Bioengineering from Jiangsu University of Science and Technology in 2016. He is currently pursuing his master postgraduates at the College of Light Industry and Food Science, Nanjing Forestry University under the supervision of Prof. WenjuanWu. His project mainly focuses on modification and application of natural polymer. |
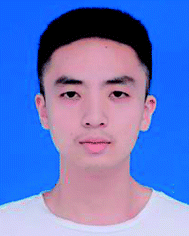 Zheng-Wei Jiang | Zheng-Wei Jiang is an undergraduate studying in College of Light Industry and Food Engineering, Nanjing Forestry University. During his participation of innovation and entrepreneurship training program for college students, a SCI article and a SCD article have been accepted/published. At present, he is under the leadership of Prof. Wenjuan Wu, engaging in the research of lignin modification and application. |
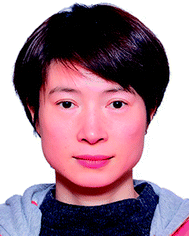 Wen-Juan Wu | Wen-Juan Wu received her Dr Ing. degree in pulp and paper from Nanjing Forestry University in 2015. She went to the University of Tokyo to study abroad during her PhD. Her research interests are biomass resources chemistry and engineering, including modification and application of natural polymer materials, clean separation and molecular structure of lignocellulose cell wall components, and interaction of biological macromolecules and their influence on biomass conversion. |
Introduction
With the depletion of non-renewable energy in nature and the excessive emission of greenhouse gases from petroleum materials, energetic and environmental problems are becoming increasingly acute. There is an urgent need for biomass with strong regeneration, clean, pollution-free and rich reserves in nature to be used as a substitute in the field of consumable fuel and petrochemical industry. China is a country with the largest energy consumption in the world, but the utilization rate of bioenergy is not high. In the same period, bioenergy accounts for only 0.1% of China's total energy consumption.1 As we all know, lignocellulose widely exists in the waste of agricultural and forestry production, and it has great utilization value. Among them, the degradation and transformation of lignin has attracted much attention. Lignin is a natural renewable resource, second only to cellulose (see Fig. 1), also it has an aromatic structure that is rich in benzene rings, methoxy groups, phenolic groups, hydroxyl groups, carboxyl groups and other groups. It can expand the network and modify chemical sites of lignin to create higher value chemical products.2 High value products such as bio-oil, chemical fuel, biochar and chemical monomers can also be obtained by pyrolysis and other degradation methods,3 especially alkylated phenols after degradation, such as guaiacol, which are mainly used in industries such as antioxidants, spices, drugs or pesticides.4 Therefore, the development and utilization of renewable lignocellulose resources to produce liquid fuels and bulk chemicals is of great significance to solve the resource and environmental crisis faced by human development, and alleviate people's excessive dependence on fossil resources.5 The degradation of lignin is one of the effective methods to realize the high value transformation of lignin.
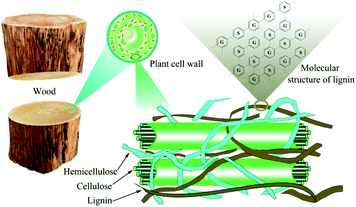 |
| Fig. 1 Lignin structure of lignocellulosic biomass in wood. | |
The main mode of bond breaking during lignin degradation is ether bond breaking (see Fig. 2).
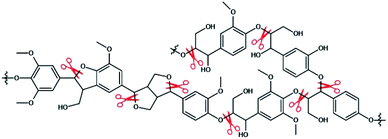 |
| Fig. 2 Degradation mechanism of lignin macromolecules. | |
According to the depolymerization mechanism, it can be divided into hydrolysis reaction, pyrolysis reaction, oxidation reaction, reductive hydrogenolysis reaction and biodegradation reaction. This paper reviews the latest research progress of lignin degradation methods in recent years from the aspects of hydrolysis, pyrolysis, oxidation, reduction and biodegradation (see Fig. 3).
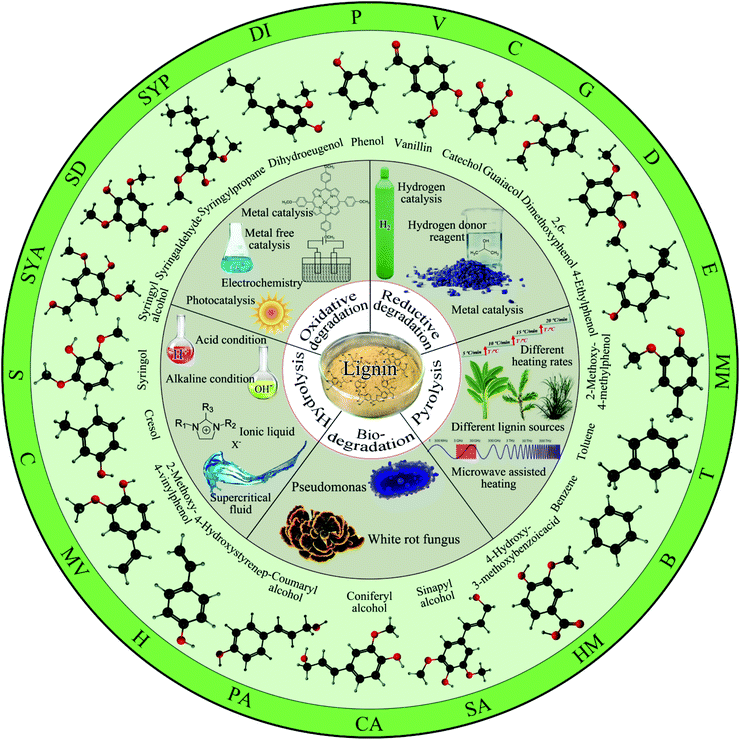 |
| Fig. 3 Lignin degradation method and its monomer. (The abbreviations corresponding to each monomer small molecule in the figure will appear in several tables below). | |
Industrial lignin is actually lignin separated from the original biomass raw materials in the process of extraction, pretreatment or other chemical activities. Here, it can be divided according to different treatment methods, mainly including sulfonated lignin, sulfated lignin, alkali lignin, organic solvent lignin, ammonia lignin, acid hydrolyzed lignin and ionic liquid lignin. On the other hand, for the division of natural lignin existing in biomass in its original form, it mainly includes milled wood lignin, enzymatic lignin and so on (see Fig. 4).
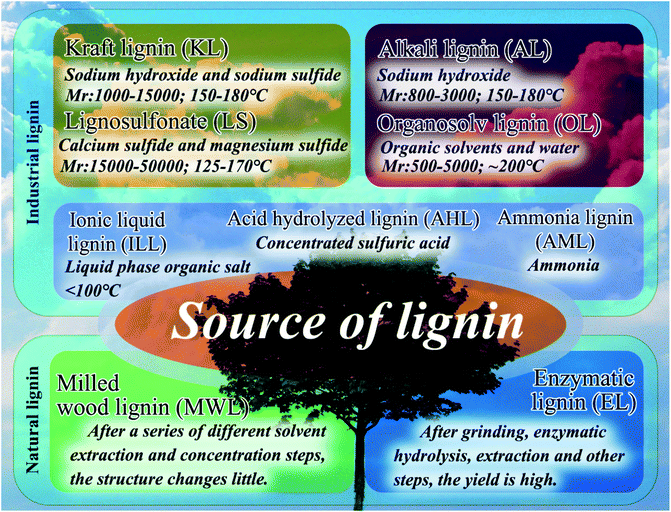 |
| Fig. 4 Sources of lignin. (The abbreviations corresponding to each lignin source in the figure will appear in several tables below). | |
Hydrolysis
Among the lignin degradation methods, hydrolysis is a practical method with relatively mild reaction conditions. In the hydrolysis process, the catalyst is easy to disperse and the active sites of the catalyst are easy to contact β–O–4 bond. Compared with combustion and pyrolysis, lignin has high product selectivity in liquid phase environment. The main product is high-value small molecular phenolic products, which is a promising means of lignin depolymerization.6
Hydrolysis of lignin under acid condition
Under the catalysis of acidic conditions, lignin may break the C–O bond. Ito et al.7 studied the acidic liquid catalytic reaction with lignin dimer as a model compound, and proposed a possible C–O bond breaking mechanism. The results showed that strong acidic liquid conditions were required for the breakage of β–O–4.
Rahimi et al.8 proposed a method for depolymerizing oxidized lignin under mild conditions of formic acid aqueous solution. This simple carbon oxygen cracking method can be used for depolymerization of poplar lignin to obtain low molecular weight aromatic compounds with a more than 60 wt% yield. Then Wang et al.9 carried out the polymerization experiment of black liquor lignin under formic acid environment and microwave conditions. After 30 minutes of reaction at 160 °C, the highest yield of aromatics was 9.7%, which was more moderate and efficient than the electric heating method. Yang et al.10 used an acidic catalyst (low acid amount) with a binary solvent to form a synergistic system to react the organic solvent lignin at a temperature of 200 °C for 60 min. The best yields of liquid product and phenolic monomer were 67.4% and 27.7% respectively, showing the combination had good compatibility and recovery rate. The inorganic strong acid with high acidity can break the ether bond very well. Generally, the degradation activity of strong acid is from high to low: HI, HCI or H2SO4. Although these strong acids have high activity, they have disadvantages such as high cost and great harm.
Hydrolysis of lignin under alkaline condition
In alkaline medium, the ether bond in lignin macromolecules is easy to break, which promotes the degradation of lignin. Thring et al.11 carried out experiments on lignin and its model compounds in alkaline solution, discovering that lignin was easy to degrade into guaiacol and purple eugenol under the condition of low reaction temperature; at high temperature, the main degradation product is catechol. In different alkaline solution systems, the solubility of sulfate lignin decreased in the following order, LiOH > NaOH > KOH > CuAOH > TPAOH > TBAOH.12 Therefore, the size of cation plays an important role in its solubility, and there are more simple aromatic compounds in the soluble part.13 Under the existence of alkali metal carbonate, hydroxyl ions promote the activation of Cβ–H bond. A single alkali metal ion interacts strongly with oxygen in the substrate, which is conducive to the polarization of ether bond. In AlCl3 solution, water can form hydrogen bonds with oxygen atoms in phenethoxybenzene. This process is beneficial to Cβ–O bonds' breaking, resulting in the production of phenol and 2-phenylethanol. AlCl3 and Na2CO3 aqueous solution promoted proton assisted C–O bond breaking.
Hydrolysis of lignin under in ionic liquid
Ionic liquids can be regarded as the “green medium” for biomass conversion. In recent years, they have been used in the development and research of agricultural waste efficient utilization technology and new energy technology.14 Ionic liquid is a kind of salt composed of cation and anion ions, existing in the form of melting at normal temperature and pressure. Ionic liquids have superior physical and chemical properties, such as low vapor pressure, high ignition point, difficult volatilization, excellent electrochemical performance and excellent solubility of organic and inorganic compounds.15 Jia et al.16 studied two lignin model compounds with acidic ionic liquid 1-methylimidazole chloride as solvent and catalyst. The hydrolysis of β–O–4 bond showed that the alkyl aryl ether bond was broken in the depolymerization process, and the main product was guaiacol at 150 °C, with a yield of more than 70.0%. Xue et al.17 used 1-methyl-3-benzylimidazole chloride and 1-methyl-3-benzylimidazole trichloroacetate to degrade and liquefy lignin. The liquefaction efficiency was up to 75.5%, and 60.0% of the low molecular products were phenols, reflecting the good selectivity of ionic liquid as a medium for the products. Cui et al.18 prepared an imidazole cationic double salt ionic liquid in diethyl phosphate medium with catalyst hydrogen sulfate. Lignin was hydrolyzed under mild conditions to obtain value-added aromatics such as 2-methoxyphenol and vanillin.
Hydrolysis of lignin in supercritical fluid
Here, the supercritical fluid for hydrolyzing lignin mainly refers to supercritical ethanol or water and its combination of metal substances such as copper and ruthenium, or non-metallic substances such as carbon. In recent years, the degradation of lignin macromolecules in supercritical fluid has also become an effective way to produce lignin value-added products. Under supercritical conditions, water is similar to compressing dense gas to “dissolve” organic compounds and achieve the purpose of rapid degradation. Under supercritical conditions, inorganic substances such as salt are almost insoluble in water. Changing the temperature and pressure of water will change its physical properties. Some organic reactions will be derived through supercritical reaction, such as oxidation reaction and hydrolysis reaction, then different ionic products will be generated. Organic substances can be completely transformed into carbon dioxide, water, etc.19 Jiang et al.20 hydrolyzed alkali lignin, xylitol residue lignin and ethanol residue lignin in supercritical water at 375 °C. The total phenol yield of corncob xylitol residue lignin was the highest, 140.0 mg g−1, including phenol 28.9 mg g−1 and 4-ethylphenol 36.2 mg g−1, with high selectivity. Kristianto et al.21 degraded the lignin separated by concentrated acid hydrolysis of empty fruit string in supercritical ethanol, supplemented by formic acid medium and ruthenium/carbon as catalyst. The yield of bio-oil was 66.3 wt% and the content of aromatic monomer was 6.1 wt%.
Overall, lignin in acidic solutions, alkaline solutions, ionic liquids, low eutectic solvents, supercritical solvents, etc. generally require high temperature conditions with possible accompanying catalysts, but the reaction products of general acid–base systems have low yields and poor selectivity. Ionic liquids, low eutectic solvents are efficient depolymerization solvents, they have good solubility for lignin, so the reaction efficiency is high. Ionic liquids are expensive and their performance is easily affected by impurities, while low eutectic solvents can be a good substitute for ionic liquids with cheap cost, stable performance and friendly to the environment. Finally, efficient solvent systems such as supercritical solvents are used to avoid the use of strong acids and bases so that the degradation reactions can be carried out under mild conditions and the product selectivity is not low. Industrial quality hydrolysis research progress as shown in Table 1 below.
Table 1 Progress in hydrolysis of industrial lignin from 2015 to 2021a
Raw materials |
Lignin type |
Solvent/catalyst |
Reaction temperature (°C) |
Productivity (wt%) |
Main products after degradation |
Ref. |
DL: dioxane lignin; BLL: black liquor lignin; XRL: xylitol residue lignin. |
Birch |
OL |
Water/Ru&Nb2O5 |
250 |
35.5 |
C7–C9 hydrocarbons |
22 |
— |
EL |
Water/Ru&Nb2O5 |
250 |
99.6 (mol%) |
C7–C9 hydrocarbons |
23 |
Birch |
OL |
Water/Pd1Ni4/MIL-100 (Fe) |
130–180 |
17.0 |
P, acetophenone |
24 |
— |
KL |
Water–ethanol (1 : 1 v/v) |
300 |
7.2 (Arene) |
MM, C, G, etc. |
25 |
Corn straw |
— |
Water–methanol (4 : 1 v/v) |
260 |
14.77 |
E |
26 |
— |
AL |
Ethanol/Ni–Co/activated carbon |
280 |
18.2 |
Phenolic compounds (V, etc.) |
27 |
Poplar wood |
DL |
Alkaline water/NiAl alloy |
220 |
18.9 |
Aromatic monomers |
28 |
— |
BLL |
Formic acid/microwave assisted |
160 |
9.69 (Arene) |
Apocynin, acetosyringone |
9 |
Pubescens |
OL |
H2O/ethane/formic acid/Pd/NbOPO4 |
160 |
22.4 |
Aromatic monomers |
29 |
Corncob residue |
— |
H2O/tetrahydrofuran |
300 |
24.3 |
Monophenols |
30 |
— |
KL |
[DMEA][HSO4] |
160 |
59.18 |
V |
31 |
— |
OL |
Propylene glycol ionic liquid |
160 |
7.2 (Arene) |
G, D, V, etc. |
18 |
Imidazole cationic double salt ionic liquid |
160 |
10.6 (Arene) |
G, D, 3,4,5-trimethoxybenzaldehyde, etc. |
Cassava |
OL |
BSbimHSO4, N-butanol, water, N-hexane; water/oil emulsion reactor |
250 |
1.74 |
P, E, D, 4-ethylguaiacol |
32 |
Straw |
2.34 |
Bagasse |
2.96 |
Corn straw |
4.21 |
Corn cob |
4.75 |
— |
AL |
[PrSO3Hmim]2[2HSO4] |
100 |
27.23 |
G |
33 |
Corn cob |
XRL |
Supercritical water |
375 |
2.89 |
P |
34 |
3.62 |
E |
Poplar |
AL |
1.43 |
G |
1.57 |
D |
Empty fruit bunches |
AHL |
Supercritical ethanol, formic acid, Ru/C |
350 |
6.1 (Arene) |
P, methylphenol, ethylphenol, methoxyphenol, etc. |
20 |
Oak |
AHL |
Supercritical ethanol |
350 |
85 (Bio-oil) |
Phenols, esters, furan, alcohols, etc. |
21 |
Indulin AT™ |
KL |
Supercritical ethanol/W–Ni–Mo/SEP trimetallic catalyst |
280 |
41.41 |
Lignin oil (G and ethoxyphenol) |
35 |
— |
AL |
Choline chloride and p-toluenesulfonic acid |
130 |
52.14 |
DI |
36 |
8.83 |
4-Hydroxy-3-methoxy phenylacetone |
6.73 |
4-Methoxy-3-hydroxyphenyl acetone |
Pyrolysis
Pyrolysis of lignin at high temperature will obtain hydrocarbons.37 It is one of the main thermochemical methods to directly produce bio-oil from lignocellulose. Its mechanism is mainly that the phenylpropane structure of lignin is cracked into phenols, the side chain carboxyl group is cracked into CO2, and the aromatic structure is carbonized into biochar.38 Lignin pyrolysis bio-oil contains many useful chemicals, especially components with aromatic structure, which can be catalytically upgraded to many high value-added products.39 The pyrolysis parameters and pyrolysis mechanism of lignin determine the distribution and properties of pyrolysis products. Heating degradation of lignin is conducive to further interpreting the original structure information of lignin and developing and producing energy sources such as sustainable bio-oil. In addition, the pyrolysis products of lignin are different due to the differences of heating rate, lignin type and other pyrolysis auxiliary conditions.
Effect of heating rate
Li et al.40 studied the pyrolysis of lignin at different heating rates. At higher heating rates, the deoxidation reaction was inhibited with a short residence time, so that biochar had lower calorific value and energy yield. The heating rate would also affect the yield and distribution of pyrolysis oil. Li et al.41 used moso bamboo as raw material, at the rate of 15 °C per minute, the total yield of small molecular products produced by carbohydrate degradation is 9.5 wt%, and the total yield of monophenol is 3.6 wt%. Galano et al.42 explained from the perspective of kinetics and thermodynamics that the pyrolysis mechanism and kinetic parameters of lignin in the range of 200–350 °C are independent of temperature and conversion. The yield of aromatic and aliphatic products is affected by heat and mass transferring (e.g. heat transfer rate and residence time) in the gas phase; when the heating process is fast and the residence time is short, the relative amount of aromatic fragments is favorable. Yu et al.43 pyrolyzed alkali lignin soluble and insoluble lignin separated from tetrahydrofuran (THF) at different temperatures and heating rates respectively. Heating rates and temperatures play an important role in the pyrolysis of lignin and biomass. In the temperature range of 450–525 °C, the amount of phenol is the highest in liquid products, while lower and higher temperatures promote the formation of dimers in liquid products.
Effect of lignin source
The pyrolysis technology of lignin has laid a foundation for expanding the application of lignin, but there are still many problems in practical application. For example, the structure of lignin, types of raw materials, processing and pretreatment have a direct impact on it. Lin et al.44 conducted rapid pyrolysis research on milled wood lignin (MWL), enzymatic lignin (EL), alkali lignin (AL) and lignosulfonate (LS), the results showed that the pyrolysis behaviors of the four types lignin were very different. Phenols are the most abundant pyrolysis products of MWL, EL and AL. Sulfonate lignin will produce a large number of furan compounds and sulfur compounds. At 350 °C, the pyrolysis of EL produces mainly phenols, acids and alcohols. Research shows that the pyrolysis time does not affect the product distribution of EL. Júnior et al.45 analyzed the pyrolysis of one commercial lignin and two lignin derived from papermaking process. The main pyrolysis products are phenolic compounds. At 650 °C, commercial lignin mainly produces hydrocarbons and phenols; industrial alkaline lignin mainly decomposes into hydrocarbons and acidic compounds; industrial lignin with stronger acidity generates phenolic compounds at heating rate. Naron et al.46 studied the catalytic pyrolysis of bagasse alkali lignin, eucalyptus sulfate lignin and pine sulfate lignin. At 250 °C and 350 °C, the catalyst impregnated with hydroxide will have different effects on the production and distribution of phenols depending on the type of lignin. The catalytic effect on pine is limited, but it can increase the phenolic yield of bagasse lignin by 26.0%, the phenol yield of Eucalyptus lignin can be increased by 40.0%, and the catalytic effect varies with the types of lignin. Zhang et al.47 conducted rapid pyrolysis experiments with grass lignin, poplar lignin and sulfate lignin. Grass lignin can release more alkyl groups and produce the least amount of coke. Poplar lignin produces more kinds of pyrolysis products than grass lignin and has higher bio-oil production.
Due to the different conditions of lignin separation and extraction, it contains different bonds. The pyrolysis products and yields of different sources of lignin are different because they have different ratios of S, G, H units and different carbon–carbon and ether bond contents. The chemical reaction of lignin pyrolysis is very complex, and the breakage of carbon–carbon bonds is more tenacious than that of ether bonds, and methoxy is also more resistant. Therefore, high temperatures are required for carbon–carbon bond breaking and relatively low temperatures for ether bond breaking. In the whole depolymerization process, the reaction temperature range is wide, and the general trend of lignin degradation is similar for different species, but there are still obvious differences.
Influence of heating method
Compared with general heating degradation, the advantages of microwave pyrolysis include rapid and selective heating, improving energy efficiency and reducing cost. Microwave assisted pyrolysis can also specifically control pyrolysis parameters to maximize gas or oil production.48 Bu et al.49 used activated carbon as catalyst and microwave conditions to obtain the main chemical components of bio-oil, including phenols, guaiacol, hydrocarbons and esters (accounting for 71–87% of bio-oil). Bio-oil with high concentration of phenol (45.0% in bio-oil) can be obtained. The maximum calorific value of biochar obtained by lignin pyrolysis is about 24.0% higher than that of raw lignin. Xie et al.50 used ZSM-5 supported cobalt catalyst to microwave pyrolysis bio-oil of lignin to obtain gases with main compounds of ketones, furans, phenols and guaiacols, as well as hydrogen and carbon monoxide. Bartoli et al.51 studied the vacuum pyrolysis of sulfate lignin under microwave-assisted pyrolysis. Carbon was used as microwave absorber to obtain 37.0 wt% of bio-oil, mostly composed of high concentration of polysubstituted aromatic rings and light linear or cyclic compounds. Li et al.52 used bagasse lignin and oxalic acid as catalysts to rapidly degrade lignin by microwave heating, and the liquefaction yield reached 78.7%. The microwave-assisted conditions can maximize the yield. The main chemical components of liquefied products include monosubstituted and disubstituted phenol, which can partially replace petroleum phenol to produce phenolic resin adhesive.
Microwave conditions can be well applied to the depolymerization of lignin, which mainly plays an auxiliary role and acts as a “catalyst” to improve the degradation and conversion rate of lignin. The microwave magnetic field promotes the breaking of carbon–carbon bonds or ether bonds by generating thermal effect and non-thermal effect oscillation, so that the pyrolysis temperature does not need to be too high. Please see Table 2 below for the progress of industrial lignin pyrolysis research.
Table 2 Progress in (catalytic) pyrolysis of industrial lignin from 2015 to 2021a
Raw material |
Lignin type |
Reactor type |
Reaction temperature (°C) |
Yield (wt%) |
Main products after degradation |
Ref. |
HL: hydrolyzed lignin. |
Corncob residue |
OL |
Fixed bed reactor |
350 |
16.2 (Monomer) |
H, MV |
53 |
Cork |
AL |
Fixed bed reactor |
650 |
54 (Bio-oil) |
Aromatics |
54 |
Douglas fir, radial pine |
AL |
Vertical pyrolysis furnace |
600 |
5.02 (Monomer) |
P, C |
55 |
Corn cob |
HL |
20.48 (Monomer) |
— |
AL |
Microwave reactor |
— |
3.36 (±0.40) |
P |
56 |
0.51 |
C |
1.84 |
Methoxyphenol |
0.50 (±0.04) |
BTEXS |
— |
AL |
Pyrolysis gas chromatography/mass spectrometry |
800 |
51.39 (Monomer) |
P, C, dimethylphenol |
57 |
20.83 (Monomer) |
18.01 (Monomer) |
Corn straw |
AL |
Fixed bed reactor |
450 |
29 (Bio-oil) |
H, MV |
58 |
Radial pine |
AL |
Fluidized bed reactor |
475 |
4.3 (Monomer) |
G, eugenol |
59 |
525 |
6.8 (Monomer) |
Alkylphenol, C |
575 |
12.0 (Monomer) |
Aromatics |
Maple |
AHL |
Pyrolysis gas chromatography/mass spectrometry |
550 |
17.87 |
D |
60 |
650 |
14.47 |
550 |
13.05 |
Isoeugenol |
650 |
14.14 |
Straw |
800 |
8.87 |
T |
900 |
8.55 |
Rice husk |
800 |
7.73 |
T |
900 |
9.47 |
— |
KL |
Fixed bed reactor |
500 |
∼32 (Bio-oil) |
Alkylphenol, aromatics, BTEX |
61 |
600 |
Selectivity 14.56 |
BTEX |
Selectivity 13.35 |
Other aromatics, etc. |
Birch and poplar mixed |
— |
Fixed bed reactor |
500 |
15.29 (Monomer) |
Phenolic aromatic hydrocarbon |
62 |
Eucalyptus |
12.57 (Monomer) |
Black liquor |
AL |
Fixed bed reactor |
600 |
20.34 (Bio-oil) |
Monomer aromatics, polycyclic aromatic hydrocarbons, phenols |
63 |
Corn cob |
AHL |
Fixed bed reactor |
550 |
28.30 |
B, T, xylene |
64 |
Oxidation
Compared with the above methods, the advantage of oxidative depolymerization of lignin is the high selectivity and high efficiency of lignin depolymerization products.65 The products of lignin oxidative degradation are mainly low molecular weight phenolic compounds, which are mostly used to produce fine chemicals. In fact, oxidation method was used to study the macromolecular structure of lignin and the relationship between precursors as early as the 1970s.66 In recent decades, various oxidation methods have been mature, including metal based catalysis, metal free catalysis, electrochemical catalysis and photocatalytic oxidation.
Metal catalysis
Kumar et al.67 used copper and manganese bimetallic catalysts to study the effect of metal oxides on the yield of products. In the case of 50/50 (wt/wt) ethanol water co-solvent mixture, the maximum yield of bio-oil was 74.3 wt%. Among the catalysts used, Cu/γ-Al2O3 catalyst combined with 25/75 (wt/wt) ethanol water solvent can produce the largest amount of phenolic compounds (84.2%), showing that it is an excellent catalyst.
Metalloporphyrins, such as Mn, Ru, Co and other transition metal porphyrins, can catalyze the oxidation of hydrocarbons. The use of metalloporphyrins as selective oxidation catalysts can further promote the degradation of lignin to high-value chemical monomers. Xie et al.68 degraded lignin in H2O2 menstruum with metalloporphyrin compound catalysis and microwave radiation. The results showed that cobalt porphyrin was helpful to improve the yield of aromatic monomers. Under the optimized conditions, with cobalt chloride as catalyst, the yield of aromatic monomers increased from 5.6% to 20.1%.
Co(salen), as a cobalt complex and dimeric peroxy compound containing oxygen molecules, has excellent oxygen carrying properties and can effectively oxidize lignin.69 Zhou70 further oxidized the lignin model with Co(salen) to benzaldehyde. On this basis, Zhou et al.71 loaded Co(salen) on graphene oxide, showing the high breaking in lignin model compounds β–O–4 bond activity. The combined biomimetic catalyst Cu([H-4]salen)/Co([H-4]salen) can effectively oxidize organic solvent lignin, finding there is a high percentage of carbonyl compounds (84.6%) in the total degradation products. With the enhancement of Cu([H-4]salen)/Co([H-4]salen) catalysis, the degree of ether bond breaking increases.72
Xu et al.73 designed a series of multiphase polyoxometalates with cesium exchange and transition metal substitution for the study of efficient catalysts for lignin depolymerization. 9.6% of monomer products can be produced in 3 hours under oxygen atmosphere of 150 °C. Under mild hydrothermal conditions, Tian et al.74 synthesized a mixed valence copper polyvanadate based on copper organic skeleton with high catalytic activity and selectivity. Using NENU-MV-5 as heterogeneous catalyst and oxygen atmosphere, β–O–4 bond of lignin was oxidized and cracked into phenol and aromatic acid in one step.
Metal free catalysis
Metal free catalytic oxidation is a method of depolymerization of lignin. It can degrade lignin with oxygen molecules, hydrogen peroxide, ozone and some peroxy acids to produce chemical monomer products, such as aldehydes (vanillin, p-hydroxybenzaldehyde and syringaldehyde) or acids (vanillic acid and syringic acid). Aromatic compounds and aliphatic compounds with carboxylic acids can be prepared according to its oxidation degree.75
Kong et al.76 used oxygen to catalyze oxidation, and the lignin in bagasse, poplar, bamboo and mango grass powder was degraded in the microemulsion reactor composed of octane, water and propyl alcohol. The yield of phenolic monomers was increasing significantly while the yield of p-coumarin was 6.1%. Li et al.77 cracked in formic acid with H2O2 but not metal catalyst. After reacting at room temperature for 6 h, the yield of β–O–4 lignin model compound was more than 90.0%, and the catalytic effect was higher than that of oxygen. It was found that the in situ formed peracid could be used as the main oxidant. Musl et al.78 treated sulfate lignin in alkaline solution with ozone. During the oxidation process, small molecular organic compounds were produced, resulting in the transfer of main active substances. The results showed that the carboxyl group in lignin polymer increased and the methoxy group decreased. Figueiredo et al.79 depolymerized various residual lignin in the micro reactor device with ozone and without catalyst. The generated products include carboxylic acid, methyl ester and acetal, and the depolymerization of organic solvent lignin is up to 70.0%, with ideal degradation effect. Bu et al.80 pretreated bagasse with peroxyformic acid. Under the optimized pretreatment conditions, the lignin degradation rate reached 59.0% and the its effect was good.
The reaction conditions for oxidative degradation of lignin are generally mild, and good degradation can be achieved without the use of high temperatures. Non-metallic oxidative degradation has low efficiency, low product selectivity and complex composition. Metal oxidation can improve the product yield and selectivity, but the metal catalyst preparation is more complicated as well as the loading of precious metals, which may cause high cost.
Electrochemical degradation
Electrochemical degradation is a green catalytic oxidation method. It is one of the most promising methods for efficient and sustainable conversion because of the availability of electron gain/loss transfer instead of redox reagents.81 Electrons can catalyze redox reactions by replacing expensive and complex redox reagents with current. The catalytic effect of electrochemistry has little relationship with concentration and temperature. The energy of electrons can be determined by external electric field. Most electrocatalytic oxidation reactions are carried out at room temperature without additional heating. The electrode plays the role of “catalyst” in redox and can act as homogeneous and heterogeneous catalysts.82
Ghahremani et al.83 designed a nickel cobalt bimetallic electrocatalyst for electrochemical oxidation of lignin. The research shows that the catalyst has a high electrochemical oxidation rate of lignin, and its degradation products mainly include vanillin, vanillin acetophenone and 3-methylbenzaldehyde. Chang et al.84 prepared an electrochemically treated titanium dioxide nanotube electrode to study the effect of tube length on lignin electrooxidation efficiency. After the treatment, a significant increase in lignin oxidation efficiency was observed. Zirbes et al.85 degraded sulfate lignin by electro-oxidation in a high temperature electrolytic cell at 160 °C. The results showed that the selectivity of vanillin was 67.0% higher than that of nitrobenzene oxidation.
Photocatalytic oxidation
Photochemical process, especially heterogeneous photocatalytic processes involving semiconductors and UV radiation, such as titanium dioxide/UV, Fe2O3 titanium dioxide/UV, zinc oxide/UV, zinc oxide/O2/UV and titanium dioxide/H2O2/UV,86,87 have also been widely used in the field of lignin degradation.
Gong et al.88 carried out the experiment of Bi and Pt promoting the oxidation of LS on the surface of titanium dioxide under certain conditions. Bi/Pt–TiO2 photocatalyst showed excellent reactivity in producing high-value compounds and CO2 in the process of oxidizing lignosulfonate. About 85.0% of lignosulfonate was converted to guaiacol, vanillic acid and vanillin. Kärkäs et al.89 developed a catalytic scheme to oxidize lignin model system by combining photooxidation and palladium catalysis, which can effectively oxidize lignin model substrate at room temperature and obtain high yield of oxidation products. Chu et al.90 prepared a metal derived photocatalyst that interacted with visible electromagnetic spectrum light to oxidize commercial lignin. The obtained oxidation products contain vanillic acid, ferulic acid, benzoic acid and p-coumaric acid, accounting for about 85.0% of the detectable lignin oxidation products, and the pretreatment effect is excellent. Research progress of oxidative degradation of industrial color quality as shown in Table 3 below.
Table 3 Progress in oxidation of industrial lignin from 2015 to 2021
Raw material |
Lignin type |
Oxidant |
Reaction temperature (°C) |
Solution |
Catalyst |
Productivity (wt%) |
Main products after degradation |
Ref. |
Cork |
AL |
H2O2 |
80–120 |
1-Ethyl-3-methylimidazole acetate solution |
Nb2O5 |
0.26–0.99 |
G, SYA, V, acetovanillone, homovanillic acid |
91 |
CoCl2 |
0.41–0.90 |
— |
Dealkylated lignin |
O2 |
160 |
NaOH |
LaFe0.2·Cu0.8O3 |
10.0 |
SD |
92 |
— |
KL |
O2 |
120 |
Phenol |
ReOx/γ-Al2O3 |
7.3 |
V |
93 |
Black liquor |
AL/KL |
TEMPO/Cu(OAc)2 |
110 |
Ionic liquid (ammonium 2-hydroxyethyl formate)/formic acid and sodium formate |
75 |
Ethyl acetate soluble product |
94 |
— |
Supercritical hydrolysis of lignin |
TEMPO, HNO3/HCl, O2 |
150 |
Methanol |
Polyoxometalates |
19.4 |
Aromatic monomer |
95 |
Bagasse, poplar, bamboo or Miscanthus powder |
OL |
O2 |
160 |
Water, n-octane, n-propanol |
CuSO4 |
6.09 ± 0.38 |
PA |
96 |
2.37 ± 0.25 |
CA |
0.56 ± 0.08 |
SA |
Poplar |
— |
O2 |
190 |
Buffer and NaOH |
CuSO4 |
7.8 |
V |
97a and 97b |
23.4 |
SD |
Pine |
KL |
Nitrobenzene |
180 |
NaOH |
— |
10.9 |
V |
98 |
Cryptomeria japonica |
Soda anthraquinone lignin |
Nitrobenzene |
180 |
NaOH |
— |
8–11.2 |
V |
Cryptomeria japonica |
Extraction of lignin with neutral solvent |
Bu4NOH aqueous solution |
120 |
NaBr, NaCl, NaOH, Na2SO4 |
Bu4NCl |
21.0 |
V |
99 |
1.7 |
HM |
Straw |
AL |
Battery anode stainless steel |
25 |
NaOH |
Current density: 50 mA cm−2 |
6 (Vanillin) |
V, acetosyringone, phthalic acid |
100 |
Black liquor |
KL |
Battery anode nickel base material |
80 |
NaOH |
Current density: 1.9 mA cm−2 |
0.34 mg ml−1 (Vanillin) |
V, HM, acetovanillone |
101 |
— |
KL |
Battery anode nickel base material |
80 |
Strong alkaline electrolyte, desorption of ethyl acetate and acetic acid |
Current density: 38 mA cm−2 |
1.3 |
V |
102 |
— |
KL |
— |
— |
Acetonitrile and deionized water |
TiO2 : lignin = 1 : 0.5 |
1.68 |
V |
103 |
— |
AL |
H2O2 |
27 |
H2O |
UV-vis radiation |
— |
About 64% reduction in COD values |
104 |
Reduction
Reductive depolymerization of lignin is usually carried out in the presence of various carriers, reducing agents and solvents.105 The aromatic structures of lignin contain very complex bonds, different phenolic units pass through C–O–C bonds (β–O–4/4′, α–O–4/4′, α/γ–O–γ, 4–O–5/5′, etc.) and C–C bond (5–5/5′, β–β, β–1, β–5) isosemirandom crosslinking.106 Reductive degradation is a degradation method in which the ether bond in lignin breaks under the action of hydrogen source and catalyst. The degradation products are mainly phenolic compounds and lignin oligomers.
Hydrogen reduction
When hydrogen is supplied as a gas, the process is usually called hydrotreating. Wang et al.107 prepared carbon modified nickel catalyst by carbothermal reduction method, studying its catalytic oxidation and hydrogenolysis of lignosulfonate. The reaction was carried out at 200 °C, 1 MPa H2, finding the total yield of aromatics could reach 22.0%. Qi et al.108 also adopted the method of combining oxidation and hydrogenolysis. After hydrogen peroxide destroyed the hydrogen bond of sulfate lignin, gaseous hydrogen was used as hydrogen donor for catalytic hydrogenolysis in the presence of nickel catalyst supported on ZSM-5 zeolite. The conversion of sulfate lignin to monomer exceeded 83.0 wt%, and the conversion of charcoal decreased to 8.0 wt%. Konnerth et al.109 studied the promotion of alkali in the metal catalyzed hydrogenolysis of lignin model compounds and organic solvent lignin. Using gaseous hydrogen as hydrogen donor, it was found that the presence of alkali had a positive selective response to monomer compounds, and the yield of monomer aromatic compounds obtained from lignin also increased significantly. The total conversion of Rh/Nb2O was 99.3%, of which the aromatic products were about 98.9%. Rh particles are responsible for the dissociation of H2 and NbOx to activate the C–O single bond. The conversion of lignin into valuable aromatic compounds under low hydrogen pressure provides a broad prospect.110
Reductive catalytic fractionation (RCF) of lignocellulose over heterogeneous catalysts can effectively recover high-yield phenolic monomers. Wang et al.133 conducted reduction experiments on birch on N-doped carbon-supported catalysts. At 250 °C, 3.0 MPa, under the initial H2 pressure, the yield of lignin-derived phenolic monomeric carbon is 52.7C%.
Hydrogen donor reduction
In addition, hydrogen has poor solubility in most solvents, and high-pressure molecular hydrogen needs to be directly used in the hydrogenolysis process, bringing disadvantages including purchase, transportation, expensive infrastructure and potential safety hazards. Catalytic transfer hydrogenation is a green alternative method, which is based on hydrogen supply solvents, such as methanol, ethanol, isopropanol, formic acid, tetrahydronaphthalene, etc. The advantage of this method is to avoid the use of high-pressure hydrogen and other explosive gases.
Wang et al.111 revolutionized the technique of lignin depolymerization and removal of oxygen-containing functional groups by applying the catalyst RANEY® Ni to the hydrogen transfer reaction of lignin model molecules, using isopropyl alcohol as the hydrogen transfer initiator and hydrogen transfer propagator. This reaction exhibited good hydrogenolysis and regenerative stability at 80–120 °C, which transformed lignin into low boiling point aromatics. Cheng et al.112 reductively degraded lignin in ethanol and isopropanol solvents. At 270 °C, the highest yield of phenol monomer obtained on Ni10Cu5/C catalyst is 63.4 wt%, with remarkable selectivity. The lignin dimers may include diphenylethane type, phenylcoumarin and terpineol. Shimanskaya et al.113 synthesized palladium containing catalysts in the presence of isopropanol. Lignin degradation produced aromatic compounds, mainly benzene and toluene. When supercritical isopropanol was used, the maximum conversion of lignin reached 50.0%, and the maximum selectivity of the catalyst to aromatics was more than 70.0% when supported on super crosslinked polystyrene.
Other catalytic reduction methods
Ouyang et al.114 studied the three-step method to obtain monomer alkylmethoxyphenol from pine wood rich in guaiacol lignin by platinum/carbon catalyzed reductive depolymerization. In the second step, the methoxy groups in these lignin monomers were selectively removed by using the optimized mop/silica catalyst to generate 4-alkylphenol, and the alkyl groups catalyzed by zeolite were transferred to the benzene stream for dealkylation. Based on the initial lignin content in pine wood, the total yield of phenol can reach 9.6 mol%. Verziu et al.115 explored the catalytic performance of nickel and ruthenium catalysts for the reductive depolymerization of Miscanthus lignin. The presence and oxidation state of ruthenium, and the content of nickel have an impact on the depolymerization performance of lignin. Ruthenium loaded on alumina will lead to lignin degradation rate of up to 89.0%. In addition, due to the synergistic effect of bimetallic, the best selectivity is obtained in the production of dimer. Zeng et al.116 prepared highly dispersed iron palladium bimetallic catalyst by impregnation method. Under the optimal reaction conditions in ethanol water solvent, the hydrogenolysis conversion of lignin is as high as 98.2%, the yield of aromatic monomer is 27.9%, and the hydrogenolysis effect is good. Research progress on reduction and degradation of industrial dyes, see Table 4.
Table 4 Progress in reduction of industrial lignin in 2015–2021
Raw material |
Lignin type |
Solvent |
Catalyst/additive |
Temperature (°C) |
Time (h) |
Gas pressure (bar) |
Monomer yield (wt%) |
Main products after degradation |
Ref. |
Beech |
OL |
Water |
RANEY® Ni |
360 |
3 |
70 (H2) |
10.1 |
P, 4-propylphenol |
117 |
Birch |
OL |
Methanol |
Ni1–Fe1/AC |
200 |
6 |
20 (H2) |
20.3 |
DI, SYP |
118 |
Oak |
OL |
Methanol |
Pd/C |
180 |
2 |
30 (H2) |
25.0 |
DI, SYP |
119 |
Corn cob |
OL |
Methanol |
ZnMoO4/MCM-41 |
220 |
4 |
30 (H2) |
14.3 |
Methyl ferulate, methyl coumarate |
120 |
Poplar |
AML |
Water/methanol (1 : 1, v/v) |
Pt/Al2O3 |
300 |
2 |
30 (H2) |
18.9 |
D, SYP, 2,6-dimethoxy-4-[(1E)-1-propen-1-yl]phenol, 4-(3-hydroxypropyl)-2,6-dimethoxyphenol |
121 |
Empty fruit bunches |
OL |
Water/ethanol (7 : 13, v/v) |
Ru/Hβ |
225 |
6 |
40 (H2) |
16.5 |
DI, isoeugenol |
122 |
Moso bamboo |
OL |
Water/ethanol (6 : 4, v/v) |
Pd/NbOPO4 |
100 |
20 |
20 (H2) |
22.4 |
D, E |
74 |
Bagasse |
OL |
Isopropyl alcohol |
Ni/ZrP |
260 |
4 |
20 (H2) |
15.1 |
E |
123 |
Bagasse |
OL |
Isopropyl alcohol |
Ni/MgO |
270 |
4 |
30 (H2) |
15.0 |
E |
124 |
Corncob residue |
OL |
Water/N-butanol (4 : 6, v/v) |
Ni/HZSM-5 |
300 |
4 |
20 (H2) |
19.5 |
E, 4-ethylguaiacol |
125 |
Bagasse |
OL |
Methyl isobutyl ketone |
H-USY |
350 |
1 |
20 (H2) |
19.4 |
P, G, E |
126 |
Cork |
KL |
Water |
NiMoS2/C |
300 |
5 |
30 mL min−1 (H2) Ar : H2 (1 : 2) |
— |
Organic acid |
127 |
Birch |
LS |
Methanol |
Ni/MgAlO–C |
200 |
6 |
10 (H2) |
22 |
Aromatic mixture |
128 |
— |
Indulin AT™ |
Water |
S2O82−/ZrO2–TiO2–SiO2/Pt/C |
270 |
1 |
20 (H2) |
6.81 |
Aromatic compounds |
129 |
— |
OL |
Ethanol |
Pd/C |
400 |
— |
50 (H2) |
13.5 |
2-Propylresorcinol and 2-ethylcatechol or 3-methoxycatechol, 4-methylcatechol (without the catalyst) |
130 |
Sorghum straw |
AHL |
Ethanol |
Ni/Al-SBA-15(20) |
280 |
4 |
10 (H2) |
17.83 |
G, phenolic monomer |
131 |
Poplar |
AHL |
Water/methanol (3 : 7, v/v) |
Pd/C |
200 |
3 |
20 (H2) |
35.5 |
4-(3-Hydroxypropyl)-2,6-dimethoxyphenol |
132 |
Castor seeds |
C-lignin |
Methanol |
Ru/ZnO/C |
200 |
4 |
30 (H2) |
51 |
Propenylcatechol |
133 |
Birch |
— |
Methanol |
Pd0.25/CNx |
250 |
3 |
30 (H2) |
52.7C% |
Phenolic monomers |
134 |
Birch |
OL |
Water/ethanol |
Ru@NCM-800 |
300 |
2 |
10 (H2) |
30.5 |
Aromatic monomers |
135 |
Switchgrass |
ILL |
Isopropyl alcohol |
5% Ru/C |
300 |
3 |
20 (N2) |
27 |
4-Ethylguaiacol, 2,6-dimethoxy-4-[(1E)-1-propen-1-yl]phenol, isoeugenol |
136 |
Sorghum |
DES lignin |
Isopropyl alcohol |
5 wt% Ru/C |
270 |
1 |
N2 |
27.39 |
P, E, 4-ethylguaiacol, DI |
137 |
— |
KL |
Isopropyl alcohol/water |
Rh/La2O3/CeO2–ZrO2 + Fe |
373 |
2 |
— |
26.4 |
— |
138 |
— |
LS |
Water/n-butanol/isopropyl alcohol (1 : 1 : 3, v/v/v) |
RANEY® Ni |
200 |
2 |
10 (N2) |
11.6 |
4-Ethylguaiacol |
139 |
Corn straw |
EL |
Isopropyl alcohol/water (2 : 1, v/v) |
Ni50Pd50/SBA-15 |
220 |
8 |
5 (N2) |
8.14 |
E, 4-ethyl-2,6-dimethoxyphenol, SYP |
140 |
Birch |
AHL |
245 |
8 |
18.52 |
SYP |
Beech |
OL |
Isopropyl alcohol |
Ni/Al2O3 |
170 |
12 |
10 (N2) |
13.4 |
2,6-Dimethoxy-4-[(1E)-1-propen-1-yl]phenol, SA, CA |
141 |
— |
KL |
Ethanol |
Ru/C + MgO/ZrO2 |
350 |
1 |
10 (N2) |
7.32 |
Butyl hydroxyanisole, 2-methoxy-2-phenylethanol |
142 |
Straw |
AL |
Supercritical ethanol |
Cu/ZSM-5(30) |
440 |
5 |
10 (N2) |
98.2 |
Monoaromatic compound |
143 |
Poplar |
OL |
Acetone/isopropyl alcohol |
ZnIn2S photocatalyst |
42 |
24 |
Ar |
10 |
p-Hydroxyacetophenone derivatives |
144 |
Birch |
AHL |
Methanol/water (1 : 2, mol mol−1) |
Pt/γ-Al2O3 |
230 |
3 |
30 (N2) |
46.1 |
4-Propyl-syringol |
145 |
Birch |
Untreated |
Water/ethanol (1 : 1, v/v) |
Co o-phenanthroline/C |
200 |
4 |
Ar |
15 |
4-Propyl-syringol |
146 |
11 |
4-Propenyl-syringol |
Poplar |
OL |
Ethanol/isopropyl alcohol |
Ni10Cu5/C |
270 |
4 |
10 (N2) |
63.4 |
DI, SYP |
147 |
Biodegradation
The biodegradation of lignin is mainly completed by the synergistic action of bacteria and fungi, in which fungi are considered to be more effective in the decomposition of lignin.148 For example, white rot fungi can decompose lignin with the help of extracellular peroxidase and laccase, and can preferentially degrade lignin rather than cellulose.149 Su et al.150 degraded corn straw under the action of fungus granula verrucosa. After two weeks, it was found that 49.9% of lignin had been depolymerized. Similarly, Tišma et al.151 used silage corn as raw material to explore the degradation effect of white rot fungus Chaetomium versicolor on lignin. Co-digestion and incubation with cattle manure at 27 °C for 7 days, the degradation rate was up to 70.0% with excellent results.
The fungal degradation of lignin has been fully studied, but the catabolic pathway of lignin degraded by microorganisms is still incomplete, mainly because lignin contains complex mixture of components and is difficult to decompose. In the catabolic pathway of lignin component degradation, bacteria and fungi also have diversity. It seems that there are more possible interactions between enzymes and metabolic pathways and microorganisms to be studied.152 The whole lignin catabolism system is redundant and complex, but the correct interpretation of the system will be important for the development of lignocellulose biorefinery. Research progress of industrial quality biodegradation see Table 5.
Table 5 Progress in biodegradation of industrial lignin in 2015–2021
Raw material |
Lignin type |
Microorganism |
Strain |
Degradation time (d) |
Degradation (%) |
Ref. |
Broad-leaved trees |
Sodium sulfite treatment |
Bacteria |
Brevibacillus thermoruber |
7 |
82.0 |
153 |
— |
AL |
Bacteria |
Pseudocitrobacter anthropi MP-4 |
7 |
52.1 |
154 |
Switchgrass |
— |
Bacteria |
A novel multi-copper polyphenol oxidoreductase (OhLac) |
3 |
6.2 |
155 |
Corn stalk |
5.2 |
Wheat straw |
4.3 |
Corn straw |
— |
Bacteria |
Enterobacter hormaechei KA3 |
7 |
32.1 |
156 |
Pulp and paper effluent |
— |
Bacteria |
Brevibacillus parabrevis MTCC 12105 |
6 |
53.8 |
157 |
Wheat straw |
— |
Fungi |
Pleurotus ostreatus |
15 |
16.8 |
158 |
Trametes versicolor |
6.1 |
Pleurotus eryngii |
7.6 |
Corn stover |
— |
Fungi |
Myrothecium verrucaria |
14 |
49.9 |
159 |
Radiata pine |
— |
Fungi |
Trametes versicolor |
21 |
16.0 |
160 |
Stereum hirsutum |
21 |
16.0 |
Corn silage |
— |
Fungi |
Trametes versicolor & cow manure |
7 |
70.0 |
151 |
— |
KL |
Fungi |
Phanerochaete chrysosporium & Irpex lacteus |
21 |
26.4 |
161 |
Black liquor |
— |
Fungi |
Daldania eschscholtzii SA2 146 |
7 |
15.0 |
162 |
— |
Dealkaline lignin |
Fungi & electro-fenton reaction |
L. Edodes & optimal voltage (4 V) |
4 |
89.0 |
163 |
Applications of depolymerization monomers
Lignin can be used as a high value fuel after degradation and the density of some of the fuels is very close to petroleum based high density jet fuel. Preparation of high density and low freezing point biomass-based jet fuels from lignin is still to be developed.164
Dai et al.165 applied Foucault alkylation reaction by utilizing lignin phenolic monomers, aldehydes and ketones intermediate small molecules (guaiacol and propionaldehyde) as raw materials, finally obtained long-chain alkane fuels. Nie et al.166 performed acid-catalyzed alkylation of lignin-derived phenols (phenol, anisole, guaiacol) with benzyl ether or benzyl alcohol. The alkylation products were hydrogenated in the presence of Pd/C and HZSM-5 to obtain biofuels with densities up to 0.93 g mL−1 and freezing points as low as −40.0 °C, comparable to the widely used JP-10 fuel, they had good low-temperature properties. Deng et al.167 used catalytic hydroxyalkylation/alkylation of lignin-derived cyclohexanone with hemicellulose-derived 2-methylfuran to produce high-density biofuel precursors. The amberlyst-15 catalyst, low FC/cyclohexanone ratio and the presence of aqueous solvent were used. After hydrodeoxygenation, high density biofuels with a density of 0.825 g mL−1 were obtained. Xu et al.168 extracted methylbenzaldehyde and cyclohexanone from lignocellulose to develop jet fuel, the obtained 1-methyldodecahydro-1H-fluorene and 3-methyldodecahydro-1H-fluorene had high density (0.99 g mL−1 and 0.96 g mL−1, respectively). Nie et al.169 used a hydrophobic acidic resin (Rx) to catalyze a lignocellulose-derived mixture and obtained a product yield of 75.4% in the co-conversion of lignocellulosic derivatives. After hydrodeoxygenation, a jet fuel blend with higher density and excellent freezing point than JP-7 was obtained.
As previously described, phenol, anisole, guaiacol, cyclohexanone, and methylbenzaldehyde are small molecule products of lignin degradation, the hydroxyl and methoxy groups of lignin-derived small molecules can provide electrons to the benzene ring, which will later be activated to undergo alkylation with alkanes, alkenes, alcohols, ethers, and ketones.166,170 Therefore, lignin degradation products can be used as feedstock for the economic synthesis of high-density biofuel precursors.
Conclusions
Hydrothermal degradation is common in the pretreatment of lignin. Generally, it should be degraded together with oxidation–reduction or completely degraded under microwave and other auxiliary conditions. The yield of hydrolysis is low and it is difficult to degrade into monomers in one step; in the process of pyrolysis, the product surface is easy to coke, resulting in poor product selectivity, so the requirements for equipment are high. Besides, the pyrolysis oil is highly oxidized and unstable. Redox degradation law is based on the molecular bond of lignin macromolecules, which is directional and efficient. However, there are still many shackles in industrial application, such as secondary polymerization and difficult separation of products. The cost of noble metal catalysis in oxidative degradation, efficiency of photocatalysis, the complexity of electrochemical catalysis and the safety of hydrogen in reductive degradation are also the defects of such methods. The advantage of biodegradation is green and it does not consume reagent materials, nevertheless, it needs bacteria selection, culture and other links in the process. Biodegradation has a long cycle and slow effect, it means that it is not suitable for large-scale production and is not conducive to practical application. Therefore, if lignin needs pretreatment, it can be considered to reduce the degree of polymerization, which is conducive to the next step of catalysis. In the aspect of lignin hydrolysis, reaction media such as green solvent ionic liquid, low eutectic solvent and supercritical fluid can be introduced to design ionic liquid with specific physical and chemical properties and binary solvent synergistic reaction; in terms of pyrolysis, microwave heating and other auxiliary conditions can be used to reduce energy consumption, or green alcohol based solvents can be added to inhibit the repolymerization reaction; when hydrogen donor reagent are used as hydrogen donors or lignin derived alcohols or acids are utilized instead of hydrogen as hydrogen donors to realize green “self-produced” reduction, the design of efficient catalysts in place of precious metals not only focuses on carbon–oxygen bonds, but also the fracture of carbon–carbon bonds.
In conclusion, the degradation of lignin is one of the ways to realize the high-value utilization of lignin, it is also a hot and difficult point in the research of renewable resources for petrochemical alternative products. It is believed that the degradation system of lignin and the application expansion of its degradation products will be continuously enriched and improved in the near future.
Conflicts of interest
There are no conflicts to declare.
Acknowledgements
This work was financially supported by the Natural Science Foundation of China (31730106), the Natural Science Foundation of China (21704045). In addition, Penghui Li wants to thank, in particular, the patience, care and support from Hui Zhou over the passed years.
Notes and references
- P. Yan, C. W. Xiao, L. Xu, G. R. Yu, A. Li, S. L. Piao and N. P. He, Renewable Sustainable Energy Rev., 2020, 127, 109857 CrossRef.
- M. P. Pandey and S. K. Chang, Chem. Eng. Technol., 2011, 34, 29–41 CrossRef CAS.
- Y. P. Wulandari, S. S. Chen, G. C. Hermosa, M. S. A. Hossain, Y. Yamauchi, T. Ahamad, S. M. Alshehri, K. C. W. Wu and H. S. Wu, Environ. Res., 2020, 190, 109976 CrossRef CAS PubMed.
- S. Van den Bosch, S.-F. Koelewijn, T. Renders, G. Van den Bossche, T. Vangeel, W. Schutyser and B. F. Sels, Top. Curr. Chem., 2018, 376, 36 CrossRef CAS PubMed.
- Y. X. Jing, L. Dong, Y. Guo, X. H. Liu and Y. Q. Wang, ChemSusChem, 2020, 13, 4181–4198 CrossRef CAS PubMed.
- Y. N. Sazanov, T. A. Kostereva, E. M. Kulikova, G. N. Fedorova, S. M. Krutov and E. V. Ipatova, Russ. Chem. Bull., 2014, 63, 2051–2055 CrossRef CAS.
- H. Ito, T. Imai, K. Lundquist, T. Yokoyama and Y. Matsumoto, J. Wood Chem. Technol., 2011, 31, 172–182 CrossRef CAS.
- A. Rahimi, A. Ulbrich, J. J. Coon and S. S. Stahl, Nature, 2014, 515, 249–252 CrossRef CAS.
- Q. Wang, S. P. Guan and D. K. Shen, Int. J. Mol. Sci., 2017, 18, 2082 CrossRef PubMed.
- Z. Z. Yang, J. F. Feng, H. W. Cheng, Y. X. Liu and J. C. Jiang, Bioresour. Technol., 2020, 321, 124440 CrossRef PubMed.
- R. W. Thring, Biomass Bioenergy, 1994, 7, 125–130 CrossRef CAS.
- E. Melro, A. Filipe, D. Sousa, A. J. M. Valente, A. Romano, F. E. Antunes and B. Medronho, Int. J. Biol. Macromol., 2020, 148, 688–695 CrossRef CAS PubMed.
- W. Song, M. Song, X. Jiang, X. Yi and W. Lai, React. Kinet., Mech. Catal., 2021, 133, 371–382 CrossRef CAS.
- S. M. Zakaria, A. Idris, K. Chandrasekaram and Y. Alias, Ind. Crops Prod., 2020, 157, 112885 CrossRef CAS.
- T. Zhang, T. Doert, H. Wang, S. J. Zhang and M. Ruck, Angew. Chem., Int. Ed., 2021, 60, 22148–22165 CrossRef CAS PubMed.
- S. Y. Jia, B. J. Cox, X. W. Guo, Z. C. Zhang and J. G. Ekerdt, ChemSusChem, 2010, 3, 1078–1084 CrossRef CAS.
- L. Y. Xue, L. C. Yan, Y. H. Cui, M. Jiang, X. L. Xu, S. L. Zhang, J. H. Gou and Z. W. Zhou, Environ. Prog. Sustainable Energy, 2016, 35, 809–814 CrossRef CAS.
- X. B. Cui, K. Li, H. Choudhary, J. L. Shamshina and R. D. Rogers, ECS Trans., 2018, 86, 215–229 CrossRef CAS.
- Wahyudiono, M. Sasaki and M. Goto, Chem. Eng. Process., 2008, 47, 1609–1619 CrossRef CAS.
- W. K. Jiang, G. J. Lyu, S. B. Wu, L. A. Lucia, G. H. Yang and Y. Liu, BioResources, 2016, 11, 5660–5675 CAS.
- I. Kristianto, S. O. Limarta, H. Lee, J. M. Ha, D. J. Suh and J. Jae, Bioresour. Technol., 2017, 234, 424–431 CrossRef CAS PubMed.
- Y. Shao, Q. Xia, L. Dong, X. Liu, X. Han, S. F. Parker, Y. Cheng, L. L. Daemen, A. J. Ramirez-Cuesta, S. Yang and Y. Wang, Nat. Commun., 2017, 8, 16104 CrossRef.
- Y. Xin, L. Dong, Y. Guo, X. Liu, Y. Hu and Y. Wang, J. Catal., 2019, 375, 202–212 CrossRef CAS.
- J. W. Zhang, G. P. Lu and C. Cai, Green Chem., 2017, 19, 4538–4543 RSC.
- H. S. Lee, J. Jae, J. M. Ha and D. J. Suh, Bioresour. Technol., 2016, 203, 142–149 CrossRef CAS PubMed.
- B. C. Yan, X. Y. Lin, Z. H. Chen, Q. J. Cai and S. P. Zhang, Bioresour. Technol., 2021, 321, 124503 CrossRef CAS PubMed.
- B. Biswas, A. Kumar, R. Kaur, B. B. Krishna and T. Bhaskar, Bioresour. Technol., 2021, 337, 125439 CrossRef CAS.
- D. Wang, Y. Y. Wang, X. Y. Li, L. Chen, G. C. Li and X. B. Li, Energy Fuels, 2018, 32, 7643–7651 CrossRef CAS.
- Q. Y. Fang, Z. C. Jiang, K. Guo, X. D. Liu, Z. Li, G. Y. Li and C. W. Hu, Appl. Catal., B, 2020, 263, 118325 CrossRef CAS.
- Z. C. Jiang, T. He, J. M. Li and C. W. Hu, Green Chem., 2014, 16, 4257–4265 RSC.
- A. Wufuer, Y. Wang and L. Dai, Biomass Convers. Biorefin., 2021 DOI:10.1007/s13399-021-01846-7.
- Z. P. Cai, Y. W. Li, H. Y. He, Q. Zeng, J. X. Long, L. F. Wang and X. H. Li, Ind. Eng. Chem. Res., 2015, 54, 11501–11510 CrossRef CAS.
- J. Fang, Y. Zhang, Y. Wang, Y. Li, H. Li and C. Li, J. Mol. Liq., 2020, 308, 113128 CrossRef CAS.
- A. Riaz, C. S. Kim, Y. Kim and J. Kim, Fuel, 2016, 172, 238–247 CrossRef CAS.
- M. Q. Chen, J. J. Shi, Y. S. Wang, Z. Y. Tang, Z. L. Yang, J. Wang and H. Zhang, Fuel, 2021, 303, 121332 CrossRef CAS.
- L. F. Li, Z. G. Wu, X. D. Xi, B. Y. Liu, Y. Cao, H. L. Xu and Y. C. Hu, J. Renewable Mater., 2021, 9, 219–235 CAS.
- W. Mu, H. Ben, A. Ragauskas and Y. Deng, Bioenergy Res., 2013, 6, 1183–1204 CrossRef CAS.
- C. X. Zhao, A. H. Chen, E. C. Jiang and L. Y. Qin, Energy Sources, Part A, 2017, 39, 458–464 CrossRef CAS.
- H. Y. Zhang, J. Hu, J. Zheng and R. Xiao, J. Anal. Appl. Pyrolysis, 2017, 128, 217–223 CrossRef CAS.
- C. Li, J. I. Hayashi, Y. Sun, L. Zhang, S. Zhang, S. Wang and X. Hu, J. Anal. Appl. Pyrolysis, 2021, 155, 105031 CrossRef CAS.
- Q. X. Li, X. Fu, J. D. Li, Y. Wang, X. Y. Lv and C. W. Hu, Energy Technol., 2018, 6, 366–378 CrossRef CAS.
- A. Galano, J. Aburto, J. Sadhukhan and E. Torres-García, J. Anal. Appl. Pyrolysis, 2017, 128, 208–216 CrossRef CAS.
- J. Yu, D. Wang and L. Sun, Fuel, 2021, 290, 120078 CrossRef CAS.
- X. Lin, S. Sui, S. Tan, C. U. Pittman Jr, J. Sun and Z. Zhang, Energies, 2015, 8, 5107–5121 CrossRef CAS.
- J. A. Santana Jr, W. S. Carvalho, T. J. P. de Oliveira and C. H. Ataíde, Mater. Sci. Forum, 2017, 899, 113–118 Search PubMed.
- D. R. Naron, F. X. Collard, L. Tyhoda and J. F. Görgens, Ind. Crops Prod., 2019, 131, 348–356 CrossRef CAS.
- M. Zhang, F. L. P. Resende, A. Moutsoglou and D. E. Raynie, J. Anal. Appl. Pyrolysis, 2012, 98, 65–71 CrossRef CAS.
- R. Luque, J. A. Menendez, A. Arenillas and J. Cot, Energy Environ. Sci., 2012, 5, 5481–5488 RSC.
- Q. Bu, H. Lei, L. Wang, Y. Wei, L. Zhu, X. Zhang, Y. Liu, G. Yadavalli and J. Tang, Bioresour. Technol., 2014, 162, 142–147 CrossRef CAS PubMed.
- X. Wei, J. Liang, H. M. Morgan, X. Zhang and B. Quan, J. Anal. Appl. Pyrolysis, 2018, 132, 163–170 CrossRef.
- M. Bartoli, L. Rosi, P. Frediani and M. Frediani, Fuel, 2020, 278, 118175 CrossRef CAS.
- Y. Li, B. Li, F. Du, Y. Wang and L. Pan, J. Appl. Polym. Sci., 2016, 134, 44510 Search PubMed.
- X. Y. Lv, Q. X. Li, Z. C. Jiang, Y. Wang, J. D. Li and C. W. Hu, J. Anal. Appl. Pyrolysis, 2018, 136, 115–124 CrossRef CAS.
- V. B. F. Custodis, S. A. Karakoulia, K. S. Triantafyllidis and J. A. van Bokhoven, ChemSusChem, 2016, 9, 1134–1145 CrossRef CAS PubMed.
- X. Zhang, W. Jiang, H. Ma and S. Wu, Fuel, 2020, 276, 118048 CrossRef CAS.
- P. C. Tarves, C. A. Mullen, G. D. Strahan and A. A. Boateng, ACS Sustainable Chem. Eng., 2016, 5, 988–994 CrossRef.
- A. Kumar, A. Kumar, J. Kumar and T. Bhaskar, Bioresour. Technol., 2019, 291, 121822 CrossRef PubMed.
- Z. Dong, H. Yang, P. Chen, Z. Liu and H. Chen, Energy Fuels, 2019, 33, 9934–9941 CrossRef CAS.
- Y. M. Kim, J. Jae, S. Myung, B. H. Sung, J. I. Dong and Y. K. Park, Bioresour. Technol., 2016, 219, 371–377 CrossRef CAS PubMed.
- D. Shen, G. Liu, Z. Jing, J. Xue, S. Guan and X. Rui, J. Anal. Appl. Pyrolysis, 2015, 112, 56–65 CrossRef CAS.
- H. W. Lee, Y. M. Kim, J. Jae, B. H. Sung, S. C. Jung, S. C. Kim, J. K. Jeon and Y. K. Park, J. Anal. Appl.
Pyrolysis, 2016, 122, 282–288 CrossRef CAS.
- J. Milovanović, R. Luque, R. Tschentscher, A. A. Romero, H. Li, K. Shih and N. Rajić, Biomass Bioenergy, 2017, 103, 29–34 CrossRef.
- J. Wu, G. Chang, X. Li, J. Li and Q. Guo, J. Anal. Appl. Pyrolysis, 2020, 146, 104775 CrossRef CAS.
- S. Wang, Z. Li, W. Yi, P. Fu, A. Zhang and X. Bai, Renewable Energy, 2021, 163, 1673–1681 CrossRef CAS.
- M. I. F. Mota, P. C. R. Pinto, J. M. Loureiro and A. E. Rodrigues, Sep. Purif. Rev., 2016, 45, 227–259 CrossRef CAS.
- Z. Jiang and C. Hu, J. Energy Chem., 2016, 25, 947–956 CrossRef.
- A. Kumar, B. Biswas, K. Saini, A. Kumar and T. Bhaskar, Biomass Convers. Biorefin., 2022, 12, 115–128 CrossRef CAS.
- J. Xie, G. Ma, X. Ouyang, L. Zhao and X. Qiu, Waste Biomass Valorization, 2020, 11, 4481–4489 CrossRef CAS.
- X. F. Zhou and J. Liu, Hem. Ind., 2012, 66, 685–692 CrossRef.
- X. F. Zhou, Pol. J. Chem. Technol., 2014, 16, 91–96 CrossRef CAS.
- X. F. Zhou and X. J. Lu, J. Appl. Polym. Sci., 2016, 133, 44133 Search PubMed.
- X. F. Zhou, Chiang Mai J. Sci., 2020, 47, 1230–1240 CAS.
- W. Xu, X. Li and J. Shi, Int. J. Biol. Macromol., 2019, 135, 171–179 CrossRef CAS PubMed.
- H. R. Tian, Y. W. Liu, Z. Zhang, S. M. Liu, T. Y. Dang, X. H. Li, X. W. Sun, Y. Lu and S. X. Liu, Green Chem., 2020, 22, 248–255 RSC.
- Z. Ahmad, W. W. A. Dajani, M. Paleologou and C. C. Xu, Molecules, 2020, 25, 2329 CrossRef CAS PubMed.
- J. H. Kong, L. X. Li, Q. Zeng, Z. P. Cai and X. H. Li, Bioresour. Technol., 2021, 321, 124466 CrossRef CAS PubMed.
- X. K. Li and Y. G. Zhang, ChemSusChem, 2020, 13, 1740–1745 CrossRef CAS PubMed.
- O. Musl, M. Holzlechner, S. Winklehner, G. M. Guebitz and S. Bhmdorfer, ACS Sustainable Chem. Eng., 2019, 7, 15163–15172 CrossRef CAS.
- M. B. Figueiredo, F. Keij, A. Hommes, P. J. Deuss and H. J. Heeres, ACS Sustainable Chem. Eng., 2019, 7, 18384–18394 CrossRef CAS.
- J. Bu, Y. T. Wang, M. C. Deng and M. J. Zhu, Bioresour. Technol., 2021, 326, 124751 CrossRef CAS PubMed.
- B. Elsler, D. Schollmeyer, K. M. Dyballa, R. Franke and S. R. Waldvogel, Angew. Chem., Int. Ed., 2014, 53, 5210–5213 CrossRef CAS PubMed.
- B. A. Frontana-Uribe, R. D. Little, J. G. Ibanez, A. Palma and R. Vasquez-Medrano, Green Chem., 2010, 42, 2099–2119 RSC.
- G. Raziyeh and J. A. Staser, Holzforschung, 2018, 72, 951–960 CrossRef.
- X. Chang, J. V. D. Zalm, S. S. Thind and A. Chen, J. Electroanal. Chem., 2020, 863, 114049 CrossRef CAS.
- M. Zirbes, L. L. Quadri, M. Breiner, A. Stenglein, A. Bomm, W. Schade and S. R. Waldvogel, ACS Sustainable Chem. Eng., 2020, 8, 7300–7307 CrossRef CAS.
- W. Subramonian, T. Y. Wu and S. P. Chai, J. Environ. Manage., 2017, 187, 298–310 CrossRef CAS PubMed.
- H. Biglari, M. Afsharnia, V. Alipour, R. Khosravi, K. Sharafi and A. H. Mahvi, Environ. Sci. Pollut. Res., 2017, 24, 4105–4116 CrossRef CAS PubMed.
- J. Y. Gong, A. Imbault and R. Farnood, Appl. Catal., B, 2017, 204, 296–303 CrossRef CAS.
- M. D. Kärkäs, I. Bosque, B. S. Matsuura and C. R. J. Stephenson, Org. Lett., 2016, 18, 5166–5169 CrossRef PubMed.
- Y. M. Chu, H. M. A. Javed, M. Awais, M. I. Khan, S. Shafqat, F. S. Khan, M. S. Mustafa, D. Ahmed, S. U. Khan and R. M. A. Khalil, Catalysts, 2021, 11, 54 CrossRef CAS.
- L. Das, S. Xu and J. Shi, Front. Energy Res., 2017, 5, 21 CrossRef.
- Y. X. Li, J. P. Zhu, Z. J. Zhang and Y. S. Qu, ACS Omega, 2020, 5, 2107–2113 CrossRef CAS PubMed.
- J. Luo, P. Melissa, W. Zhao, Z. Wang and Y. Zhu, ChemistrySelect, 2016, 1, 4596–4601 CrossRef CAS.
- J. Dai, A. F. Patti, L. Longé, G. Garnier and K. Saito, ChemCatChem, 2017, 9, 2684–2690 CrossRef CAS.
- W. Yang, X. Du, W. Liu, A. W. Tricker and Y. Deng, Energy Fuels, 2019, 33, 6483–6490 CrossRef CAS.
- J. Kong, L. Li, Q. Zeng, Z. Cai and X. Li, Bioresour. Technol., 2021, 321, 124466 CrossRef CAS PubMed.
-
(a) V. E. Tarabanko and N. Tarabanko, Int. J. Mol. Sci., 2017, 18, 2421 CrossRef PubMed;
(b) V. E. Tarabanko, E. P. Pervishina, N. V. Tarabanko, M. Y. Chernyak, K. L. Kaygorodov, Y. V. Chelbina and D. V. Boyarchuk, Khim. Rastit. Syr'ya, 2016, 4, 57–63 Search PubMed.
- T. Ikeda and K. Magara, J. Wood Chem. Technol., 2015, 35, 167–177 CrossRef CAS.
- M. Maeda, T. Hosoya, K. Yoshioka, H. Miyafuji, H. Ohno and T. Yamada, J. Wood Sci., 2018, 64, 810–815 CrossRef CAS.
- S. Singh and H. R. Ghatak, J. Wood Chem. Technol., 2017, 37, 407–422 CrossRef CAS.
- D. Schmitt, C. Regenbrecht, M. Schubert, D. Schollmeyer and S. R. Waldvogel, Holzforschung, 2017, 71, 35–41 CAS.
- D. Schmitt, C. Regenbrecht, M. Hartmer, F. Stecker and S. R. Waldvogel, Beilstein J. Org. Chem., 2015, 11, 473–480 CrossRef CAS PubMed.
- N. Srisasiwimon, S. Chuangchote, N. Laosiripojana and T. Sagawa, ACS Sustainable Chem. Eng., 2018, 6, 13968–13976 CrossRef CAS.
- K. Asha and S. K. Badamali, Mol. Catal., 2020, 497, 111236 CrossRef CAS.
- A. Dufour, E. Bartolomei, Y. L. Brech, V. Carre, F. Aubriet, E. Terrell, M. Garcia-Perez and P. Arnoux, ChemSusChem, 2020, 13, 4633–4648 CrossRef PubMed.
- H. L. Wang, Y. Q. Pu, A. Ragauskas and B. Yang, Bioresour. Technol., 2019, 271, 449–461 CrossRef CAS PubMed.
- M. Wang, X. C. Zhang, H. J. Li, J. M. Lu, M. J. Liu and F. Wang, ACS Catal., 2018, 8, 1614–1620 CrossRef CAS.
- S. C. Qi, J. I. Hayashi, S. Kudo and L. Zhang, Green Chem., 2017, 19, 2636–2645 RSC.
- H. Konnerth, J. Zhang, D. Ma, M. H. G. Prechtl and N. Yan, Chem. Eng. Sci., 2015, 123, 155–163 CrossRef CAS.
- W. Guan, X. Chen, H. Hu, C. W. Tsang, J. Zhang, C. S. K. Lin and C. Liang, Fuel Process. Technol., 2020, 203, 106392 CrossRef CAS.
- X. Wang and R. Rinaldi, Angew. Chem., Int. Ed., 2013, 52, 11499–11503 CrossRef CAS PubMed.
- C. Cheng, P. F. Li, W. Yu, D. Shen and S. Gu, Bioresour. Technol., 2020, 319, 124238 CrossRef PubMed.
- E. I. Shimanskaya, E. M. Sulman, M. G. Sulman and I. Y. Tiamina, Catal. Sustainable Energy, 2020, 7, 1–7 CAS.
- X. Ouyang, X. Huang, M. D. Boot and E. J. M. Hensen, ChemSusChem, 2020, 13, 1705–1709 CrossRef CAS PubMed.
- M. Verziu, A. Tirsoaga, B. Cojocaru, C. Bucur, B. Tudora, A. Richel, M. Aguedo, A. Samikannu and J. P. Mikkola, Mol. Catal., 2018, 450, 65–76 CrossRef CAS.
- Z. Zeng, J. Xie, Y. Guo, R. Rao and X. Ouyang, Fuel Process. Technol., 2021, 213, 106713 CrossRef CAS.
- J. O. Strüven and D. Meier, ACS Sustainable Chem. Eng., 2016, 4, 3712–3721 CrossRef.
- Y. Zhai, C. Li, G. Xu, Y. Ma, X. Liu and Y. Zhang, Green Chem., 2017, 19, 1895–1903 RSC.
- X. Ouyang, X. Huang, B. M. S. Hendriks, M. D. Boot and E. J. M. Hensen, Green Chem., 2018, 20, 2308–2319 RSC.
- S. Wang, W. Gao, H. Li, L. P. Xiao, R. C. Sun and G. Song, ChemSusChem, 2018, 11, 2114–2123 CrossRef CAS PubMed.
- A. McVeigh, F. P. Bouxin, M. C. Jarvis and S. D. Jackson, Catal. Sci. Technol., 2016, 6, 4142–4150 RSC.
- M. Kim, D. Son, J. W. Choi, J. Jae, J. S. Dong, J. M. Ha and K. Y. Lee, Chem. Eng. J., 2017, 309, 187–196 CrossRef CAS.
- Q. Fang, Z. Jiang, K. Guo, X. Liu and C. Hu, Appl. Catal., B, 2019, 263, 118325 CrossRef.
- H. Ma, H. Li, W. Zhao, L. Li, S. Liu, J. Long and X. Li, Green Chem., 2019, 21, 658–668 RSC.
- W. Zhao, X. Li, H. Li, X. Zheng and X. Li, ACS Sustainable Chem. Eng., 2019, 7, 19750–19760 CrossRef CAS.
- X. Liu, Z. Jiang, S. Feng, H. Zhang, J. Li and C. Hu, Fuel, 2019, 244, 247–257 CrossRef CAS.
- W. Wanmolee, N. Laosiripojana, P. Daorattanachai, L. Moghaddam, J. Rencoret, J. C. del Río and W. O. S. Doherty, ACS Sustainable Chem. Eng., 2018, 6, 3010–3018 CrossRef CAS.
- S. Mukundan, D. Boffito, A. Shrotri, L. Atanda and G. S. Patience, ACS Sustainable Chem. Eng., 2020, 8, 13195–13205 CrossRef CAS.
- W. Min, X. Zhang, H. Li, J. Lu and W. Feng, ACS Catal., 2018, 8, 1614–1620 CrossRef.
- H. Wang, W. Li, J. Wang, H. M. Chang and L. Jin, RSC Adv., 2017, 7, 50027–50034 RSC.
- K. J. Hakonen, J. L. G. Escobedo, H. M. Talvio, S. F. Hashmi, R. S. Karinen and J. Lehtonen, ChemistrySelect, 2018, 3, 1761–1771 CrossRef CAS.
- P. Chen, Q. Zhang, R. Shu, Y. Xu, L. Ma and T. Wang, Bioresour. Technol., 2017, 226, 125–131 CrossRef CAS PubMed.
- S. Wang, K. Zhang, H. Li, L. P. Xiao and G. Song, Nat. Commun., 2021, 12, 416 CrossRef CAS PubMed.
- J. Park, H. S. Cahyadi, U. Mushtaq, D. Verma, D. Han, K. W. Nam, S. K. Kwak and J. Kim, ACS Catal., 2020, 10, 12487–12506 CrossRef CAS.
- T. Li, H. Lin, X. Ouyang, X. Qiu and Z. Wan, ACS Catal., 2019, 9, 5828–5836 CrossRef CAS.
- T. Renders, S. V. D. Bosch, T. Vangeel, T. Ennaert and B. F. Sels, ACS Sustainable Chem. Eng., 2016, 4, 6894–6904 CrossRef CAS.
- K. H. Kim, B. Simmons and S. Singh, Green Chem., 2017, 19, 215–224 RSC.
- L. Das, M. Li, J. Stevens, W. Li, Y. Pu, A. J. Ragauskas and J. Shi, ACS Sustainable Chem. Eng., 2018, 6, 10408–10420 CrossRef CAS.
- L. Luo, J. Yang, G. Yao and F. Jin, Bioresour. Technol., 2018, 264, 1–6 CrossRef CAS PubMed.
- S. Liu, Z. Lin, Z. Cai, J. Long, Z. Li and X. Li, Bioresour. Technol., 2018, 264, 382–386 CrossRef CAS PubMed.
- B. Jiang, J. Hu, Y. Qiao, X. Jiang and P. Lu, Energy Fuels, 2019, 33, 8786–8793 CrossRef CAS.
- L. Jiang, H. Guo, C. Li, P. Zhou and Z. Zhang, Chem. Sci., 2019, 10, 4458–4468 RSC.
- S. O. Limarta, J. M. Ha, Y. K. Park, H. Lee, D. J. Suh and J. Jae, J. Ind. Eng. Chem., 2018, 57, 45–54 CrossRef CAS.
- S. Jeong, S. Yang and D. H. Kim, Mol. Catal., 2017, 442, 140–146 CrossRef CAS.
- N. Luo, M. Wang, H. Li, J. Zhang, T. Hou, H. Chen, X. Zhang, J. Lu and F. Wang, ACS Catal., 2017, 7, 4571–4580 CrossRef CAS.
- X. Ouyang, X. Huang, J. Zhu, M. D. Boot and E. J. M. Hensen, ACS Sustainable Chem. Eng., 2019, 7, 13764–13773 CrossRef CAS.
- S. Rautiainen, D. D. Francesco, S. N. Katea, G. Westin, D. N. Tungasmita and J. S. M. Samec, ChemSusChem, 2019, 12, 404–408 CrossRef CAS PubMed.
- J. C. Sigoillot, J. G. Berrin, M. Bey, L. L. Meessen, A. Levasseur, A. Lomascolo, E. Record and E. U. Boukhris, Adv. Bot. Res., 2012, 61, 263–308 CAS.
- E. Bari, K. Ohno, N. Yilgor, A. P. Singh, J. J. Morrell, A. Pizzi, M. A. T. Ghanbary and J. Ribera, Microorganisms, 2021, 9, 247 CrossRef CAS PubMed.
- Y. J. Su, X. X. Yu, Y. Sun, G. Wang, H. Chen and G. Chen, Ind. Crops Prod., 2018, 121, 396–404 CrossRef CAS.
- M. Tišma, M. Planinić, A. Bucić-Kojić, M. Panjičko, G. D. Zupančič and B. Zelić, Bioresour. Technol., 2018, 253, 220–226 CrossRef PubMed.
- C. Li, C. Chen, X. Wu, C. W. Tsang and C. S. K. Lin, Bioresour. Technol., 2019, 291, 121898 CrossRef CAS PubMed.
- J. Niu, X. Li, X. Qi and Y. Ren, Bioresour. Technol., 2021, 341, 125875 CrossRef CAS PubMed.
- F. Li, R. Xie, N. Liang, J. Sun and D. Zhu, BioResources, 2019, 14, 1992–2012 CAS.
- C. Yang, L. Ma, X. Wang, Y. Xing and X. Lü, Front. Microbiol., 2021, 12, 694166 CrossRef PubMed.
- Q. Zhang, J. Zhang, S. Zhao, P. Song, Y. Chen, P. Liu, C. Mao and X. Li, Energies, 2021, 14, 1–13 Search PubMed.
- R. Hooda, N. K. Bhardwaj and P. Singh, World J. Microbiol. Biotechnol., 2018, 34, 31 CrossRef PubMed.
- A. Sandra, W. Valentina, P. Carolyn and C. Andrea, Biochem. Eng. J., 2018, 140, 140–147 CrossRef.
- Y. Su, X. Yu, Y. Sun, G. Wang, H. Chen and G. Chen, Ind. Crops Prod., 2018, 121, 396–404 CrossRef CAS.
- E. Shirkavand, S. Baroutian, D. J. Gapes and B. R. Young, Energy Convers. Manag., 2017, 142, 13–19 CrossRef CAS.
- R. Luo, Q. Liao, A. Xia, Z. Deng, Y. Huang, X. Zhu and X. Zhu, Front. Energy Res., 2020, 8, 575371 CrossRef.
- Idris, I. Ramadhani, A. Kanti and I. M. Sudiana, IOP Conf. Ser. Earth Environ. Sci., 2019, 308, 012014 CrossRef.
- L. Hou, D. Ji, W. Dong, L. Yuan, F. Zhang, Y. Li and L. Zang, Front. Bioeng. Biotechnol., 2020, 8, 99 CrossRef PubMed.
- J. Xie, X. Zhang, J. Xie, G. Nie, L. Pan and J. Zou, Prog. Chem., 2018, 9, 1424–1433 Search PubMed.
- N. Dai, Z. Yang, Y. Huang and Y. Fu, J. Fuel Chem. Technol., 2015, 43, 48–53 CAS.
- G. Nie, X. Zhang, P. Han, J. Xie, L. Pan, L. Wang and J. J. Zou, Chem. Eng. Sci., 2017, 158, 64–69 CrossRef CAS.
- Q. Deng, P. Han, J. Xu, J. J. Zou, L. Wang and X. Zhang, Chem. Eng. Sci., 2015, 138, 239–243 CrossRef CAS.
- J. Xu, N. Li, G. Li, F. Han, A. Wang, Y. Cong, X. Wang and T. Zhang, Green Chem., 2018, 20, 3753–3760 RSC.
- G. Nie, H. Wang, Q. Li, L. Pan, Y. Liu, Z. Song, X. Zhang, J. J. Zou and S. Yu, Appl. Catal., B, 2021, 292, 120181 CrossRef CAS.
- C. R. Kumar, N. Rambabu, N. Lingaiah, P. S. S. Prasad and A. K. Dalai, Appl. Catal., A, 2014, 471, 1–11 CrossRef CAS.
|
This journal is © The Royal Society of Chemistry 2022 |
Click here to see how this site uses Cookies. View our privacy policy here.