DOI:
10.1039/D2RA01330D
(Paper)
RSC Adv., 2022,
12, 14268-14277
Impact of sp2 carbon material species on Pt nanoparticle-based electrocatalysts produced by one-pot pyrolysis methods with ionic liquids†
Received
28th February 2022
, Accepted 2nd May 2022
First published on 11th May 2022
Abstract
Pt-nanoparticle-supported graphene nanoplatelets (Pt/GNPs) and multiwalled carbon nanotube composite (Pt/MWCNTs) electrocatalysts for the oxygen reduction reaction (ORR) can be prepared using a one-pot method through the pyrolytic decomposition of the platinum precursor, platinum(II) bis(acetylacetonate) (Pt(acac)2) in 1-butyl-3-methylimidazolium bis(trifluoromethylsulfonyl)amide ([C4mim][Tf2N]) or N,N,N-trimethyl-N-propylammonium bis(trifluoromethanesulfonyl)amide ([N1,1,1,3][Tf2N]) ionic liquids (ILs) with the target sp2 carbon support. In this one-pot pyrolysis method, which does not require any reagents to reduce Pt metal precursors or stabilize Pt nanoparticles, Pt nanoparticles are readily immobilized onto the sp2 surface by a thin IL layer formed at the interface, which can work as a binder. We used three types of sp2 carbon materials with different geometric shapes (graphene nanoplatelets with <3 (GNPs-3) and 18–24 layers (GNPs-20) and multiwalled carbon nanotubes (MWCNTs)) to investigate Pt nanoparticle formation and anchoring. All the electrocatalysts, especially Pt/MWCNTs, showed higher durability than the commercial catalyst owing to the combined effect of the IL binder and sp2 carbon materials. Our findings strongly suggest that the original carbon surface properties are also an important factor for creating high-performance ORR electrocatalysts.
1. Introduction
Rationally designed Pt-nanoparticle-supported carbon (Pt/C) electrocatalysts have been used to expedite the sluggish oxygen reduction reaction (ORR) on the cathode for polymer membrane electrolyte fuel cells (PEMFCs), which are clean and high-power density solutions for powering vehicles.1,2 However, such Pt/C catalysts are required to further reduce the overpotential for the ORR and increase the durability. The latter is regarded as an unavoidable issue owing to the dissolution3 and Ostwald ripening4 of Pt nanoparticles under harsh operating conditions. In addition, catalyst degradation is induced by carbon support corrosion. The most commonly used carbon support is carbon black (e.g., Vulcan® X72), which has a high specific surface area and many functional groups that can easily anchor Pt nanoparticles. Unfortunately, carbon black is gradually oxidized and deformed during PEMFC operation, especially during start-up and shut-down.5–8 This aggravates Pt detachment and aggregation. sp2-hybridized carbon materials composed of two-dimensional hexagonal carbon planes such as carbon nanotubes (CNTs) and graphene analogs, e.g., graphene nanoplatelets (GNPs), have emerged as promising candidates to replace the widely used carbon black in PEMFC catalysts. These materials have attracted considerable attention in recent years owing to their unique physicochemical properties, including excellent electrical and thermal conductivities, high corrosion resistance, and large specific surface area.9,10 The application of corrosion-resistant carbon materials substantially reduces Pt nanoparticle-related carbon oxidation and degradation.5,11–13 However, anchoring Pt nanoparticles onto the smooth and chemically inert surface of sp2 carbon materials is difficult. In most cases, the honeycomb sp2 structure is destroyed by the addition of functional groups when immobilizing Pt nanoparticles onto carbon materials14,15 and heteroatoms are embedded into the sp2 structure.16,17 These approaches are accompanied by a high risk of lowering the expected stability of CNTs and GNPs. Wrapping a carbon surface with a polymer, which is categorized as a physical conjunction method, is another approach to fixing Pt nanoparticles onto the surface.18,19 We have previously reported a similar concept, but using an ionic liquid (IL) as the binder.20–22 In this manner, highly durable Pt/C electrocatalysts for the ORR are easily produced by heating and/or agitating the Pt-nanoparticle-dispersed IL with the carbon support.23–25 In electrocatalysts, small quantities of the IL, which can remain even after electrochemical cleaning, impede direct contact between Pt nanoparticles and the carbon surface, thereby inhibiting carbon support corrosion.
Inspired by this approach, we recently established a simple and mass-producible one-pot pyrolysis method with IL (IL one-pot pyrolysis method) for preparing composite Pt and PtNi alloy-nanoparticle-supported multiwalled carbon nanotube composite (MWCNT) electrocatalysts for the ORR.26 Unlike commonly used colloid methods, wherein the size and shape of nanoparticles are directly controlled by capping, stabilizing, and reducing agents,27–29 no additional agents are needed for the IL one-pot pyrolysis method. In this study, to investigate the impact of sp2 carbon material species on the ORR performance of electrocatalysts, we applied this IL one-pot pyrolysis method to graphene-based carbon materials, graphene nanoplatelets with <3 (GNPs-3) and 18–24 layers (GNPs-20) and MWCNTs. Using two types of ILs, 1-butyl-3-methylimidazolium bis(trifluoromethylsulfonyl)amide ([C4mim][Tf2N]) and N,N,N-trimethyl-N-propylammonium bis(trifluoromethanesulfonyl)amide ([N1,1,1,3][Tf2N]), we revealed the key factors responsible for controlling and maintaining the Pt nanoparticle size, which are directly related to the electrocatalytic performance.
2. Experimental
2.1 Preparation of the specimens
We prepared all specimens by a one-pot pyrolytic process under an N2 atmosphere. The reaction medium for the one-pot process was composed of 2 mL IL ([C4mim][Tf2N] (Kanto Chemical Co., Inc.) or [N1,1,1,3][Tf2N] (Kanto Chemical Co., Inc.), Fig. S1 (ESI†)), 5 mmol L−1 platinum(II) bis(acetylacetonate) (Pt(acac)2 (Mitsuwa Chemicals Co., Ltd.)), and 1.25 g L−1 of sp2 carbon materials. The carbon materials were graphene powder (Sigma-Aldrich Co., LLC., thickness: <3 graphene layers; lateral size: 0.5–5 μm (GNPs-3)), graphene nanoplatelets (Strem Chemical Co., Inc., thickness: 6–8 nm (18–24 graphene layers); lateral size: 5 μm (GNPs-20)), and multiwalled carbon nanotubes (Sigma-Aldrich Co., LLC., outer diameter × length: 6–13 nm × 2.5–20 μm (MWCNTs)). Prior to the pyrolytic process, we agitated the prepared reaction media at room temperature overnight to uniformly disperse the Pt (acac)2 and sp2 carbon materials. Subsequently, we heated the mixture at 573 K for 4 h and washed the resulting samples (Pt/GNPs-3, Pt/GNPs-20, and Pt/MWCNT) several times with anhydrous acetonitrile and dried them overnight in vacuum. We prepared specimens 1–6 under the six conditions described in Table 1. We used a commercially available Pt/C electrocatalyst (Pt–C, TEC10V30E, Tanaka Kikinzoku Kogyo Co., Ltd.) as the reference.
Table 1 Preparation conditions and characterization data for specimens 1–6 and Pt–C
Specimens |
Ionic liquidsa |
Carbon materials |
Mean particle size/nm |
Pt loading amount/wt% |
5 mmol L−1 Pt(acac)2 was added as a Pt metal precursor. Values in parentheses are standard deviations. |
1 |
[C4mim][Tf2N] |
GNPs-3 |
2.1 (0.3)b |
25.4 |
2 |
[C4mim][Tf2N] |
GNPs-20 |
2.5 (0.5)b |
25.0 |
3 |
[C4mim][Tf2N] |
MWCNTs |
2.7 (0.5)b |
26.5 |
4 |
[N1,1,1,3][Tf2N] |
GNPs-3 |
3.3 (0.5)b |
25.5 |
5 |
[N1,1,1,3][Tf2N] |
GNPs-20 |
3.8 (0.5)b |
24.5 |
6 |
[N1,1,1,3][Tf2N] |
MWCNTs |
4.3 (0.7)b |
25.3 |
Pt–C |
— |
— |
2.6 (0.7)26 |
23.7 (ref. 26) |
2.2 Characterization
We observed the morphologies of specimens 1–6 using a Hitachi H-7650 transmission electron microscope (TEM). We analyzed the amount of Pt nanoparticles loaded on the sp2 carbon materials using inductively coupled plasma atomic emission spectroscopy (ICP-AES) (Shimadzu ICPS-7510). We evaluated the Brunauer–Emmett–Teller (BET) surface area using nitrogen adsorption–desorption analysis (Quantachrome Instruments). We characterized the original carbon materials and specimens 1–6 using a Nanophoton RAMANview Raman spectrometer.
2.3 Electrochemical measurements
We examined the electrocatalytic activities of specimens 1–6 using a computer-controlled Hokuto Denko HZ-7000 potentiostat/galvanostat. We obtained electrochemical measurements using a three-electrode cell with a 0.1 M HClO4 aqueous solution. We used a glassy carbon rotating disk electrode (GC-RDE, surface area = 0.196 cm2), Pt mesh electrode, and reversible hydrogen electrode (RHE) as the working, counter, and reference electrodes, respectively. We ionically connected the RHE to the electrolyte in the main cell compartment via a Luggin capillary tip positioned close to the working electrode (WE). Each sample prepared in this study was dispersed in an i-propanol solution with a weight concentration of 1.48 g L−1. We added a 10 μL solution onto the GC-RDE (5 mm diameter) and allowed it to dry naturally. Finally, we covered the GC disk with 10 μL Nafion® i-propanolic solution (0.1 wt%) to fix the samples using a thin Nafion® layer. We conducted voltammetric experiments at 10 mV s−1 between 0.050 and 1.20 V (vs. RHE) at ∼298 K. Prior to the experiments, we electrochemically cleaned the working electrode with 40–100 potential sweeps between 0.050 and 1.20 V at a scan rate of 50 mV s−1 under a N2 atmosphere until the cyclic voltammograms (CVs) stabilized. Depending on the experimental purpose, we deaerated the electrolyte by bubbling with N2 or O2 for at least 30 min.
We determined the electrochemical surface area (ECSA) of the Pt nanoparticles by hydrogen adsorption or desorption coulombic charge in the cyclic voltammogram under N2 atmosphere after subtracting the double-layer charge current. We calculated the ECSA (m2 g−1) using the following equation:
|
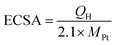 | (1) |
where
QH (C) is the charge of the hydrogen adsorption/desorption. An average value for the charge associated with a hydrogen adsorption/desorption monolayer formed on smooth polycrystalline Pt is 2.1 C m
−2.
30 MPt (g) is the Pt mass on the GC working electrode.
We investigated the ORR performance of the samples using rotating disk electrode linear sweep voltammetry (RDE-LSV) in the anodic direction at a sweep rate of 10 mV s−1 under five different RDE revolution speeds (200, 400, 800, 1200, and 1600 rpm) in an O2 atmosphere. The resultant voltammograms were examined using the Koutecký–Levich equation.
|
 | (2) |
|
B = 0.62nFAC*D2/3v−1/6ω1/2
| (3) |
where
I is the experimentally measured current at 0.85 V,
Ik is the kinetically limited current,
ω is the angular frequency of rotation (s
−1),
n is the electron transfer number,
F is the Faraday constant,
A is the electrode surface area,
C* is the O
2 concentration in the electrolyte,
D is the diffusion coefficient of O
2 in the electrolyte, and
v is the kinematic viscosity of the electrolyte. We estimated
Ik from the intercept of the Koutecký–Levich plot (
I−1 vs. ω−1/2). For each catalyst, we normalized
Ik to the Pt loading to obtain the mass activities.
We conducted the durability tests for the samples using the standard evaluation method recommended by the Fuel Cell Commercialization Conference of Japan.31 This test overloads the cathode for a proton-exchange membrane (PEM) fuel-cell system by potential sweeps between 1.00 and 1.50 V (vs. RHE) at 500 mV s−1, which easily causes the carbon support materials to corrode. Therefore, this electrochemical approach enables a quick durability evaluation of the cathode catalyst. To obtain further insight into the deterioration behavior, we estimated the catalytic activity retention rates for the ECSA and mass activities using the following equations:
|
 | (4) |
|
 | (5) |
3. Results and discussion
Fig. 1 shows the TEM images and Pt nanoparticle size distribution of specimens 1–6 that we prepared using the IL one-pot pyrolysis method under the conditions listed in Table 1. The ILs we used were [C4mim][Tf2N] with an unsaturated five-membered ring cation with two heteroatoms and [N1,1,1,3][Tf2N] with a saturated alkylammonium cation. The loading amounts of Pt and mean particle sizes of the nanoparticles deposited on the samples are summarized in Table 1. Regardless of the preparation conditions, the loading amounts were nearly the same (∼25 wt%), but this was not the case for the mean particle size. For the graphene-nanoplatelets-based carbon supports, when we used the same IL, the Pt nanoparticles modified on GNPs-3 were smaller (2.1 nm for [C4mim][Tf2N] and 3.3 nm for [N1,1,1,3][Tf2N]) than those on GNPs-20 (2.5 nm for [C4mim][Tf2N] and 3.8 nm for [N1,1,1,3][Tf2N]). According to the product information, the specific surface area of GNPs-20 is 120–150 m2 g−1.32 A similar, flat, sheet-like, and ultrathin carbon material, GNPs-3, has a much larger specific surface area of 1243 m2 g−1, which is calculated from the typical H3-type nitrogen adsorption–desorption isotherm curve of GNPs-3 (Fig. S2a (ESI†)). This higher specific surface area is extremely likely to result in smaller Pt nanoparticles, because GNPs-3 can provide more anchor points for Pt nucleation in the Pt(II) reduction process. However, the impact of specific surface area on Pt particle size seems to be limited, because the size variation is less than 0.5 nm even though the surface area is nearly 10 times larger. A schematic illustration of this plausible Pt nanoparticle formation mechanism is depicted in Fig. 2a and b. In addition, the geometric shape can affect the size of the nanoparticles. MWCNTs have completely different shapes but are sp2 carbon materials, as are GNPs-3 and GNPs-20. Although the MWCNTs we used in this study had a higher surface area, i.e., 210 m2 g−1 (Fig. S2b (ESI†)), than GNPs-20, the Pt nanoparticles on the MWCNTs were slightly larger (2.7 nm for [C4mim][Tf2N] and 4.3 nm for [N1,1,1,3][Tf2N]) than those on the GNPs-20. This result suggests that MWCNTs have fewer anchor points suitable for Pt nucleation. This may be associated with the curved surface shape of MWCNTs.
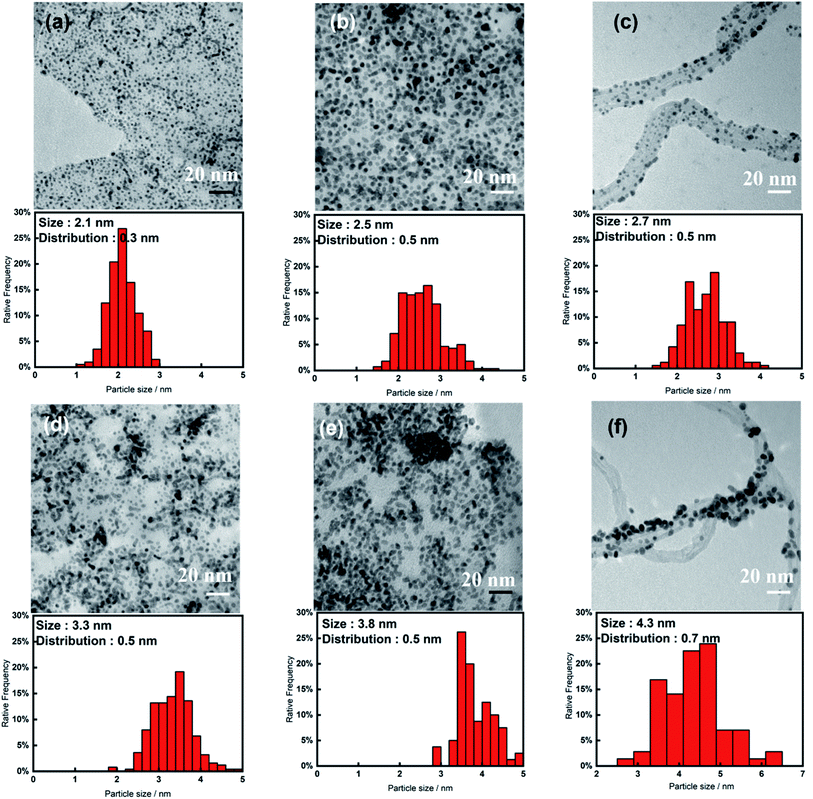 |
| Fig. 1 TEM images and Pt nanoparticle size distribution of specimens (a–f) 1–6, respectively, prepared under the experimental conditions described in Table 1. | |
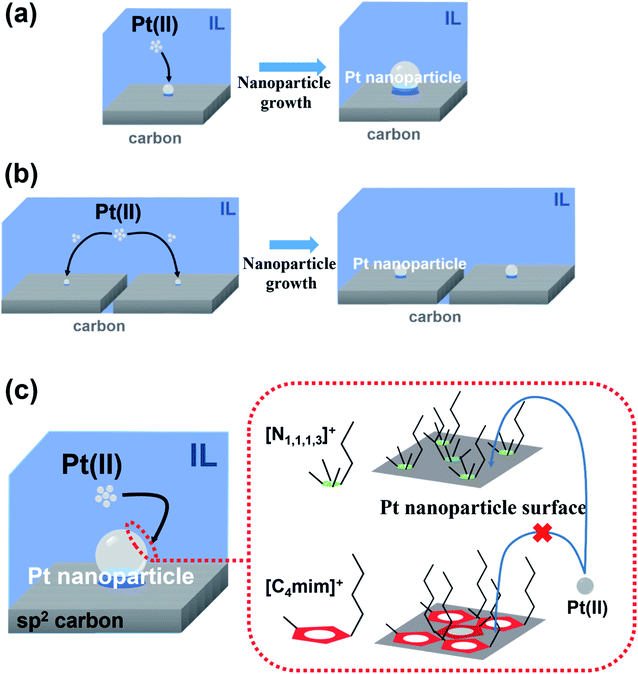 |
| Fig. 2 Schematic illustration of the plausible impact of carbon materials with (a) smaller and (b) larger surfaces and (c) the organic cationic species in [N1,1,1,3][Tf2N] and [C4mim][Tf2N] on Pt nanoparticle size in the process of the IL one-pot pyrolysis method. | |
The difference in the IL species had a more noticeable effect on the Pt particle size in specimens 1–6. As summarized in Table 1, the nanoparticles deposited became larger by changing the IL from [C4mim][Tf2N] (specimens 1–3) to [N1,1,1,3][Tf2N] (specimens 4–6). Nanoparticle growth in [C4mim][Tf2N] was hampered. Similar behavior was also confirmed by Pt nanoparticle preparation using the same IL one-pot pyrolysis method but without carbon supports (Fig. S3 (ESI†)). The mean particle sizes of the Pt nanoparticles we obtained for [C4mim][Tf2N] and [N1,1,1,3][Tf2N] were 3.5 and 6.9 nm, respectively. Because the surface of the Pt nanoparticles prepared in ILs is positively charged, the Pt nanoparticles are considered to be stabilized by anionic supramolecular aggregates, for example, [(organic cation)x(Tf2N)1+x]−.33 In the present case, the accessibility of Pt metal precursors and/or atoms to the nanoparticle surface was directly controlled by the cationic steric effect.34 Thus, a larger volume cation, [C4mim]+, could effectively block further Pt deposition on the nanoparticles. As a result, Pt nucleation was stimulated at other anchor points on the carbon supports, leading to less nanoparticle growth. A plausible process of Pt nanoparticle growth during the IL one-pot pyrolysis method is schematically summarized in Fig. 2c.
We collected further information on the carbon structure using Raman spectroscopy for specimens 1–6, and the as-prepared samples are shown in Fig. S4 (ESI†). Two characteristic peaks, the D band at 1350 cm−1 and G band at 1580 cm−1, are associated with defects or disorders and sp2-bonded carbons, respectively.35 We noted little difference between the Raman spectra before and after the Pt nanoparticle modification, indicating that the IL one-pot pyrolysis method employed in this research had no effect on the surface structure of the sp2 carbon materials.
As expected from the characterization of the specimens, their electrochemical performance differed significantly. Fig. 3 shows the cyclic voltammograms before and after 15
000 potential cycle durability tests recorded at the GC electrodes with specimens 1–6 prepared by the one-pot pyrolysis method in a N2-saturated 0.1 M HClO4 aqueous solution. The several commonly observed redox waves concerning the hydrogen and oxygen electrochemical reactions are recognized at potentials ranging from 0.10 to 0.35 V and 0.60 to 1.00 V, respectively. The ECSAs for specimens 1–6 estimated from the voltammograms for hydrogen adsorption–desorption are shown in Table 2. These values are lower than those of commercial Pt–C catalysts. The H2 adsorption was highly likely hampered by the IL remaining on the Pt nanoparticle surface.36–38 After the durability test, we found that the ECSA retention rates for the graphene nanoplatelet-based samples, 1 (51.2%), 2 (47.6%), 4 (26.9%) and 5 (65.2%), were inferior to that of Pt–C (71.1%). Conversely, specimens 3 (75.1%) and 6 (92.8%), prepared using MWCNTs, showed higher retention rates than Pt–C. Considering the larger number of defects or disorders on the MWCNTs, corroborated by the Raman spectra derived from the G-band (Fig. S4 (ESI†)), we deduced that their presence triggered slower nanoparticle aggregation during the durability test, that is, a higher retention rate of ECSA by Pt/MWCNTs.
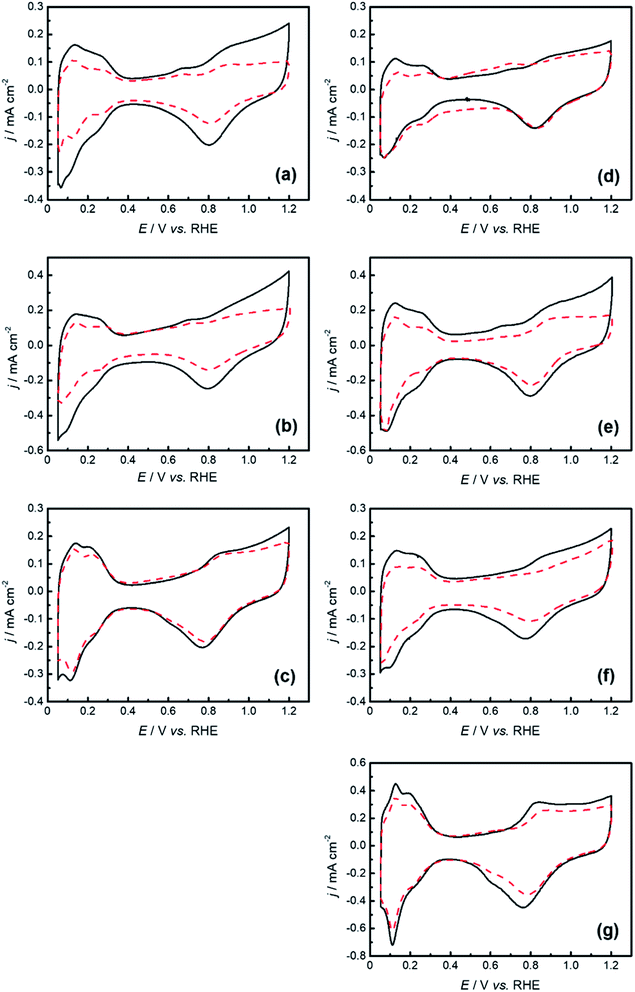 |
| Fig. 3 Cyclic voltammograms recorded at glassy carbon electrodes with the specimens (a) 1, (b) 2, (c) 3, (d) 4, (e) 5, and (f) 6 and (g) Pt–C in a N2-saturated 0.1 M HClO4 aqueous solution (—) before and ( ) after the durability test. Scan rate was 10 mV s−1. | |
Table 2 Summary of ECSA and mass activity data for specimens 1–6 and Pt–C
Specimens |
ECSA (original)/m2 g−1 |
ECSA (after)/m2 g−1 |
Retention rate of ECSA/% |
MAa @ 0.85 V (original)/A g−1 |
MAa @ 0.85 V (after)/A g−1 |
Retention rate of MAa @ 0.85 V/% |
MA: mass activity. |
1 |
31.1 |
15.9 |
51.2 |
329.9 |
243.4 |
73.79 |
2 |
26.1 |
12.4 |
47.6 |
221.7 |
137.4 |
61.99 |
3 |
35.4 |
26.6 |
75.1 |
177.5 |
173.1 |
97.52 |
4 |
16.7 |
4.49 |
26.9 |
205.3 |
172.9 |
84.20 |
5 |
45.1 |
29.4 |
65.2 |
202.5 |
189.4 |
93.52 |
6 |
33.7 |
31.3 |
92.8 |
190.9 |
265.4 |
139.02 |
Pt–C |
72.7 |
51.7 |
71.1 |
561.2 |
283.8 |
49.64 |
To evaluate the catalytic ability of specimens 1–6 toward the ORR, we measured the RDE-LSVs at the GC-RDEs with each specimen in an O2-saturated 0.1 M HClO4 aqueous solution before and after 15
000 potential cycle durability tests (Fig. S5 (ESI†)). Before the durability test, the increase in current flow for O2 reduction initiated at ca. 1.05–1.10 V, as observed for commonly used electrocatalysts for the ORR. Koutecký–Levich plots at 0.85 V were constructed using the RDE-LSVs obtained at speeds of 200–1600 rpm. The mass activities of the specimens that we calculated from the Koutecký–Levich plots and the mean Pt particle sizes before the durability tests are summarized in Table 2 and Fig. 4. The mass activity decreased with increasing nanoparticle size. We obtained the highest mass activity, 329.9 A g−1, for specimen 1, which had the smallest mean nanoparticle size of 2.1 nm, corresponding to the size that can obtain more Pt (111) facets.39 As focusing on Pt/GNPs-3 and Pt/GNPs-20, which are flat, sheet-like carbon supports, would provide an opportunity to discuss the effect of Pt nanoparticle density on catalytic ability, we prepared two extra GNPs-20-based specimens by the same procedure using [N1,1,1,3][Tf2N] but with different Pt precursor concentrations of 1 and 2.5 mmol L−1. TEM observation of the GNPs-20 prepared with 1, 2.5, and 5 mmol L−1 Pt(acac)2 revealed that the mean particle sizes were 3.8 ± 0.6 nm, 3.6 ± 0.7 nm and 3.8 ± 0.5 nm, respectively (Fig. 5). In other words, size does not depend on the precursor concentration. However, the Pt loading varied with precursor concentration. From these findings, we concluded that the number density of Pt nanoparticles on GNPs-20 increases with increasing precursor concentration. The mass activities of these three specimens are shown in Fig. 6a as a function of Pt loading. The mass activities increase with increasing Pt loading, but are nonlinear. Because their particle sizes are almost the same, the differences in their mass activities are not dependent on size. This nonlinear behavior should be linked to the number density of the Pt nanoparticles on the GNPs-20. Watanabe et al. reported that the active area territory on the Pt surface is an important factor in attaining higher mass activity.40 As illustrated in Fig. 6b, oxygen accessibility reduced when the Pt nanoparticle number density was too high.
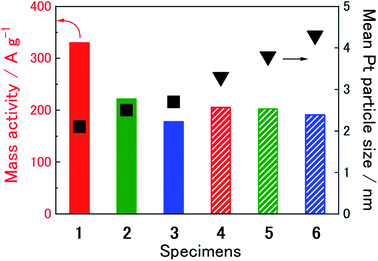 |
| Fig. 4 Comparison of mass activity and mean Pt nanoparticle size of specimens 1–6. | |
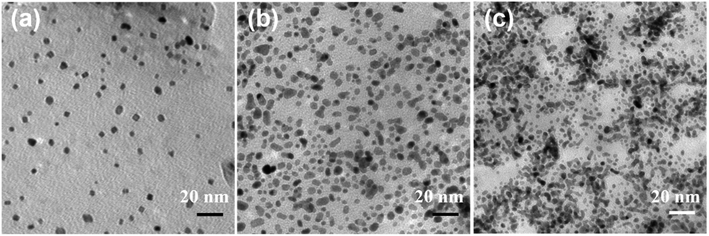 |
| Fig. 5 TEM images of the Pt/GNPs-20s prepared in [N1,1,1,3][Tf2N] with different Pt metal precursor (Pt(acac)2) concentrations: (a) 1, (b) 2.5, and (c) 5 mmol L−1. | |
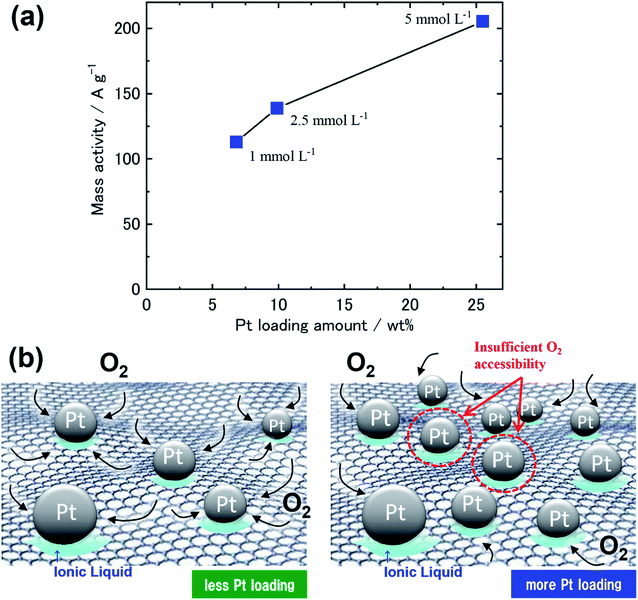 |
| Fig. 6 (a) Comparison of mass activities with different Pt loading amounts on Pt/GNPs-20s prepared in [N1,1,1,3][Tf2N] with different Pt metal precursor (Pt(acac)2) concentrations: 1, 2.5, and 5 mmol L−1. Pt particle size remained almost the same. (b) Schematic illustration of the effect of Pt nanoparticle number density deposited on GNPs-20s on mass transfer of oxygen during ORR. | |
Based on the RDE-LSVs after the 15
000-cycle tests (Fig. S5 and S6 (ESI†)), the mass activity data estimated at 0.85 V for specimens 1–6 and Pt–C are provided in Table 2. A comparison of all the mass activity data obtained in this study, with the catalytic activity retention rates, is presented in Fig. 7. All the specimens prepared showed a higher mass activity retention rate than Pt–C (49.6%). In particular, specimens 3 and 6, resulting from the MWCNTs, showed a much higher durability. The results of Raman spectroscopy indicated that, as more functional groups exist on MWCNTs than on the other two sp2 carbon materials, MWCNTs would suppress the displacement and aggregation of the Pt nanoparticles. Although the catalyst durability is improved by the IL binding between the Pt nanoparticles and the carbon material surface, the results here provide evidence that the original carbon surface properties also affect durability.
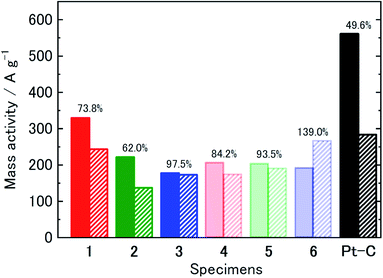 |
| Fig. 7 Comparison of mass activity and mean Pt nanoparticle size of specimens 1–6 and Pt–C: (filled bar) before and (diagonal bar) after 15 000-cycle test. | |
4. Conclusions
In this study, we successfully synthesized Pt-nanoparticle-modified sp2 carbon materials by the IL one-pot pyrolysis method using three different sp2 carbon supports, GNPs-3, GNPs-20, and MWCNTs, without any pretreatment. The higher surface area of the carbon supports led to the formation of smaller Pt nanoparticles. The cation size in the IL also significantly affected the Pt nanoparticle size. We obtained the highest mass activity when the Pt nanoparticle size was ∼2 nm. All the resulting specimens showed higher durability in terms of mass activity than the commercial catalyst. The samples prepared from MWCNTs had a much higher retention rate. More defects on the MWCNTs resulted in a stronger ability to fix the nanoparticles and prevent nanoparticle aggregation. This study provides useful information on the IL one-pot pyrolysis method for the synthesis of ORR electrocatalysts with high activity and durability.
Author contributions
T. T. conceived the idea of the one-pot process used in this research. S. K. gave the suggestions on experimental plan. Y. Y., Q. X. M. K. and H. Y. prepared and evaluated the specimens. Y. Y. and T. T. wrote the manuscript. All the authors participated in discussions of the results and in preparing the manuscript.
Conflicts of interest
The authors have no conflicts to declare.
Acknowledgements
This research was supported by JSPS KAKENHI (grant number JP19H02814).
References
- M. Blal, A. Benatiallah, A. NeÇaibia, S. Lachtar, N. Sahouane and A. Belasri, Contribution and investigation to compare models parameters of (PEMFC), comprehensives review of fuel cell models and their degradation, Energy, 2019, 168, 182–199 CrossRef.
- A. Kulkarni, S. Siahrostami, A. Patel and J. K. Norskov, Understanding Catalytic Activity Trends in the Oxygen Reduction Reaction, Chem. Rev., 2018, 118, 2302–2312 CrossRef CAS PubMed.
- R. M. Darling and J. P. Meyers, Kinetic Model of Platinum Dissolution in PEMFCs, J. Electrochem. Soc., 2003, 150, A1523–A1527 CrossRef CAS.
- P. J. Ferreira, G. J. la O', Y. Shao-Horn, D. Morgan, R. Makharia, S. Kocha and H. A. Gasteiger, Instability of Pt/C Electrocatalysts in Proton Exchange Membrane Fuel Cells, J. Electrochem. Soc., 2005, 152, A2256–A2271 CrossRef.
- X. Wang, W. Z. Li, Z. W. Chen, M. Waje and Y. S. Yan, Durability investigation of carbon nanotube as catalyst support for proton exchange membrane fuel cell, J. Power Sources, 2006, 158, 154–159 CrossRef CAS.
- J. J. Wang, G. P. Yin, Y. Y. Shao, S. Zhang, Z. B. Wang and Y. Z. Gao, Effect of carbon black support corrosion on the durability of Pt/C catalyst, J. Power Sources, 2007, 171, 331–339 CrossRef CAS.
- R. Borup, J. Meyers, B. Pivovar, Y. S. Kim, R. Mukundan, N. Garland, D. Myers, M. Wilson, F. Garzon, D. Wood, P. Zelenay, K. More, K. Stroh, T. Zawodzinski, J. Boncella, J. E. McGrath, M. Inaba, K. Miyatake, M. Hori, K. Ota, Z. Ogumi, S. Miyata, A. Nishikata, Z. Siroma, Y. Uchimoto, K. Yasuda, K. Kimijima and N. Iwashita, Scientific aspects of polymer electrolyte fuel cell durability and degradation, Chem. Rev., 2007, 107, 3904–3951 CrossRef CAS PubMed.
- S.-M. Jung, S.-W. Yun, J.-H. Kim, S.-H. You, J. Park, S. Lee, S. H. Chang, S. C. Chae, S. H. Joo, Y. Jung, J. Lee, J. Son, J. Snyder, V. Stamenkovic, N. M. Markovic and Y.-T. Kim, Selective electrocatalysis imparted by metal–insulator transition for durability enhancement of automotive fuel cells, Nat. Catal., 2020, 3, 639–648 CrossRef CAS.
- S. Sui, X. Y. Wang, X. T. Zhou, Y. H. Su, S. Riffatc and C. J. Liu, A comprehensive review of Pt electrocatalysts for the oxygen reduction reaction: Nanostructure, activity, mechanism and carbon support in PEM fuel cells, J. Mater. Chem. A, 2017, 5, 1808–1825 RSC.
- X. J. Zhou, J. L. Qiao, L. Yang and J. J. Zhang, A Review of Graphene-Based Nanostructural Materials for Both Catalyst Supports and Metal-Free Catalysts in PEM Fuel Cell Oxygen Reduction Reactions, Adv. Energy Mater., 2014, 4, 1301523 CrossRef.
- Y. J. Li, Y. J. Li, E. B. Zhu, T. McLouth, C. Y. Chiu, X. Q. Huang and Y. Huang, Stabilization of High-Performance Oxygen Reduction Reaction Pt Electrocatalyst Supported on Reduced Graphene Oxide/Carbon Black Composite, J. Am. Chem. Soc., 2012, 134, 12326–12329 CrossRef CAS PubMed.
- J. H. Kim, J. Y. Cheon, T. J. Shin, J. Y. Park and S. H. Joo, Effect of surface oxygen functionalization of carbon support on the activity and durability of Pt/C catalysts for the oxygen reduction reaction, Carbon, 2016, 101, 449–457 CrossRef CAS.
- D. Higgins, P. Zamani, A. P. Yu and Z. W. Chen, The application of graphene and its composites in oxygen reduction electrocatalysis: a perspective
and review of recent progress, Energy Environ. Sci., 2016, 9, 357–390 RSC.
- R. Kou, Y. Y. Shao, D. H. Mei, Z. M. Nie, D. H. Wang, C. M. Wang, V. V. Viswanathan, S. Park, I. A. Aksay, Y. H. Lin, Y. Wang and J. Liu, Stabilization of Electrocatalytic Metal Nanoparticles at Metal-Metal Oxide-Graphene Triple Junction Points, J. Am. Chem. Soc., 2011, 133, 2541–2547 CrossRef CAS PubMed.
- S. Liu, J. Wang, J. Zeng, J. Ou, Z. Li, X. Liu and S. Yang, “Green” electrochemical synthesis of Pt/graphene sheet nanocomposite film and its electrocatalytic property, J. Power Sources, 2010, 195, 4628–4633 CrossRef CAS.
- L. Guo, W. J. Jiang, Y. Zhang, J. S. Hu, Z. D. Wei and L. J. Wan, Embedding Pt Nanocrystals in N-Doped Porous Carbon/Carbon Nanotubes toward Highly Stable Electrocatalysts for the Oxygen Reduction Reaction, ACS Catal., 2015, 5, 2903–2909 CrossRef CAS.
- D. Higgins, M. A. Hoque, M. H. Seo, R. Y. Wang, F. Hassan, J. Y. Choi, M. Pritzker, A. P. Yu, J. J. Zhang and Z. W. Chen, Development and Simulation of Sulfur-doped Graphene Supported Platinum with Exemplary Stability and Activity Towards Oxygen Reduction, Adv. Funct. Mater., 2014, 24, 4325–4336 CrossRef CAS.
- D. P. He, C. Zeng, C. Xu, N. C. Cheng, H. G. Li, S. C. Mu and M. Pan, Polyaniline-Functionalized Carbon Nanotube Supported Platinum Catalysts, Langmuir, 2011, 27, 5582–5588 CrossRef CAS PubMed.
- T. Fujigaya and N. Nakashima, Fuel Cell Electrocatalyst Using Polybenzimidazole-Modified Carbon Nanotubes As Support Materials, Adv. Mater., 2013, 25, 1666–1681 CrossRef CAS PubMed.
- T. Tsuda, T. Kurihara, Y. Hoshino, T. Kiyama, K. Okazaki, T. Torimoto and S. Kuwabata, Electrocatalytic Activity of Platinum Nanoparticles Synthesized by Room-Temperature Ionic Liquid-Sputtering Method, Electrochemistry, 2009, 77, 693–695 CrossRef CAS.
- T. Tsuda, K. Yoshii, T. Torimoto and S. Kuwabata, Oxygen reduction catalytic ability of platinum nanoparticles prepared by room-temperature ionic liquid-sputtering method, J. Power Sources, 2010, 195, 5980–5985 CrossRef CAS.
- T. Fujigaya, S. Hirata and N. Nakashima, A highly durable fuel cell electrocatalyst based on polybenzimidazole-coated stacked graphene, J. Mater. Chem. A, 2014, 2, 3888–3893 RSC.
- K. Yoshii, T. Tsuda, T. Arimura, A. Imanishi, T. Torimoto and S. Kuwabata, Platinum nanoparticle immobilization onto carbon nanotubes using Pt-sputtered room-temperature ionic liquid, RSC Adv., 2012, 2, 8262–8264 RSC.
- R. Izumi, Y. Yao, T. Tsuda, T. Torimoto and S. Kuwabata, Oxygen reduction electrocatalysts sophisticated by using Pt nanoparticle-dispersed ionic liquids with electropolymerizable additives, J. Mater. Chem. A, 2018, 6, 11853–11862 RSC.
- T. Sasaki, R. Izumi, T. Tsuda and S. Kuwabata, Innovative Approach for Preparing a CNT-Supported Pt Nanoparticle Functional Electrocatalyst Using Protic Ionic Liquids, ACS Appl. Energy Mater., 2021, 4, 7298–7308 CrossRef CAS.
- Y. Yao, R. Izumi, T. Tsuda, Y. Oshima, A. Imanishi, N. Oda and S. Kuwabata, Pt and PtNi nanoparticle-supported multi-walled carbon nanotube electrocatalysts prepared by one-pot pyrolytic synthesis with an ionic liquid, ACS Appl. Energy Mater., 2019, 2, 4865–4872 CrossRef CAS.
- T. S. Ahmadi, Z. L. Wang, T. C. Green, A. Henglein and M. A. ElSayed, Shape-controlled synthesis of colloidal platinum nanoparticles, Science, 1996, 272, 1924–1926 CrossRef CAS PubMed.
- B. R. Cuenya, Synthesis and catalytic properties of metal nanoparticles: Size, shape, support, composition, and oxidation state effects, Thin Solid Films, 2010, 518, 3127–3150 CrossRef CAS.
- Y. N. Xia, X. H. Xia and H. C. Peng, Shape-Controlled Synthesis of Colloidal Metal Nanocrystals: Thermodynamic versus Kinetic Products, J. Am. Chem. Soc., 2015, 137, 7947–7966 CrossRef CAS PubMed.
- K. Yamamoto, D. M. Kolb, R. Kotz and G. Lehmpfuhl, Hydrogen Adsorption and Oxide Formation on Platinum Single-Crystal Electrodes, J. Electroanal. Chem., 1979, 96, 233–239 CrossRef.
- M. Asano, R. Kawamura, R. Sasakawa, N. Todoroki and T. Wadayama, Oxygen Reduction Reaction Activity for Strain-Controlled Pt-Based Model Alloy Catalysts: Surface Strains and Direct Electronic Effects Induced by Alloying Elements, ACS Catal., 2016, 6, 5285–5289 CrossRef CAS.
- https://www.strem.com/catalog/v/06-0210/12/carbon_1034343-98-0.
- C. W. Scheeren, G. Machado, S. R. Teixeira, J. Morais, J. B. Domingos and J. Dupont, Synthesis and Characterization of Pt(0) Nanoparticles in Imidazolium Ionic Liquids, J. Phys. Chem. B, 2006, 110, 13011–13020 CrossRef CAS PubMed.
- G. R. Zhang, T. Wolker, D. J. S. Sandbeck, M. Munoz, K. J. J. Mayrhofer, S. Cherevko and B. J. M. Etzold, Tuning the Electrocatalytic Performance of Ionic Liquid Modified Pt Catalysts for the Oxygen Reduction Reaction via Cationic Chain Engineering, ACS Catal., 2018, 8, 8244–8254 CrossRef CAS PubMed.
- P. Lespade, R. Al-Jishi and M. S. Dresselhaus, Model for Raman Scatterig From Incompletely Graphitized Carbons, Carbon, 1982, 20, 427–431 CrossRef CAS.
- L. Johnson, A. Ejigu, P. Licence and D. A. Walsh, Hydrogen Oxidation and Oxygen Reduction at Platinum in Protic Ionic Liquids, J. Phys. Chem. C, 2012, 116, 18048–18056 CrossRef CAS.
- G. R. Zhang, M. Munoz and B. J. M. Etzold, Boosting Performance of Low Temperature Fuel Cell Catalysts by Subtle Ionic Liquid Modification, ACS Appl. Mater. Interfaces, 2015, 7, 3562–3570 CrossRef CAS PubMed.
- K. Huang, T. Song, O. Morales-Collazo, H. Jia and J. F. Brennecke, Enhancing Pt/C Catalysts for the Oxygen Reduction Reaction with Protic Ionic Liquids: The Effect of Anion Structure, J. Electrochem. Soc., 2017, 164, F1448–F1459 CrossRef CAS.
- M. Shao, A. Peles and K. Shoemaker, Electrocatalysis on Platinum Nanoparticles: Particle Size Effect on Oxygen Reduction Reaction Activity, Nano Lett., 2011, 11, 3714–3719 CrossRef CAS PubMed.
- M. Watanabe, H. Sei and P. Stonehart, The Influence of Platinum Crystallite Size on the Electroreduction of Oxygen, J. Electroanal. Chem. Interfacial Electrochem., 1989, 261, 375–387 CrossRef CAS.
|
This journal is © The Royal Society of Chemistry 2022 |
Click here to see how this site uses Cookies. View our privacy policy here.