DOI:
10.1039/D1RA08255H
(Paper)
RSC Adv., 2022,
12, 9917-9922
Toward layered MoS2 anode for harvesting superior lithium storage†
Received
10th November 2021
, Accepted 7th March 2022
First published on 30th March 2022
Abstract
As a typical transition metal dichalcogenide (TMD), molybdenum disulphide (MoS2) has become one of the most promising anode materials for lithium-ion batteries (LIBs) due to its desirable electrochemical properties. But the development of commercial MoS2 is limited by the problem of agglomeration. Thus, the production of MoS2 nanosheets with few (<10) layers is highly desired but remains a great challenge. In this work, a facile and scalable approach is developed to prepare large-flake, few-layer (4–8) MoS2 nanosheets with the assistance of ultrasonics. Simultaneously, the as-prepared MoS2 nanosheets and commercial bulk MoS2 were analysed under multiple spectroscopic techniques and a series of electrochemical tests to understand the dependence of electrochemical performance on structural properties. When used as anode materials for LIBs, the obtained MoS2 nanosheets provide a reversible capacity of 716 mA h g−1 at 100 mA g−1 after 285 cycles, and demonstrated an excellent capacity retention rate of up to 80%. Compared with that of commercial MoS2 (14.8%), the capacity retention rate of our MoS2 nanosheets has a significant improvement. This work explored the ability of few-layered MoS2 nanosheets in the field of LIBs while suggesting the commercialization of the MoS2 by an ultrasonicated ball milling exfoliation technique.
Introduction
Lithium-ion batteries (LIBs) have become the most indispensable item of supreme energy storage that is prospering in electronic devices and automobile industries. Accompanying the people's continuing demand for high energy and power densities and a keen motive to lower the environmental impact, the components and commercialization of LIBs have turned out to be a topic of extensive scientific research for a couple of decades.1–3 Of late, numerous LIB anode materials, ranging from carbonaceous material like graphite to transition metal-based two-dimensional materials (TMDs) like molybdenum disulphide (MoS2), molybdenum selenide (MoSe2), molybdenum trioxide (MoO3) and tungsten disulphide (WS2), are being investigated due to their exceptional crystal structures that contribute to remarkable electrochemical, electrical and optical properties.4–7 As conventional graphite anodes produced a considerably lower theoretical capacity of 372 mA h g−1, the latest TMDs have portrayed a higher capacity of over 500 mA h g−1 exceeding those of the bulk equivalents.7–9
MoS2 has been verified as one of the most assuring anode materials by exhibiting a theoretical capacity of over 669 mA h g−1 with a low reaction potential.10 These unique properties could potentially be applicable in fields such as capacitors, lubricants, catalysts and even as an extraordinary anode material for LIBs.11–16 The morphology of MoS2 nanosheets comprises covalently bonded sulphur–molybdenum–sulphur atoms which are weakly stacked by van der Waals forces in order to form layers of two dimensions.9,17–21 The interaction of these layers enables the lithium ions to diffuse between the layers through intercalation without an obvious expansion in volume.16,22,23 These reported insights of MoS2 have aided us to understand the influence of morphology on electrochemical properties, the intercalation capacity of lithium, and the lithiation and delithiation cycle of LIB.24,25
Furthermore, a minimal layering of MoS2 nanosheets has demonstrated an extended reversibility capacity while supporting a faster Li ion intercalation process compared with that of bulk MoS2. This excellent storage response with a negligible Li ion diffusion limit is due to the surface area offered by nanosheets of fewer than 10 layers with adequate interlayer and interplanar spacing.26 Nevertheless, agglomeration of the nanosheets has been shown to compromise the electrochemical performance of the cell in numerous cases.27–33 Thus, an effective synthesis is essential for fabricating high performance MoS2 anodes.
There are various bottom-up34 and top-down35 approaches to produce MoS2 but attaining a few layers of nanosheets continued to be a massive challenge through the years.26 Generally, the bottom-up approach requires an extreme energy intensive post-treatment under stringent conditions, making it a least preferred process.36,37 In spite of low yields, the top-down approach is commonly preferred on account of the bulk material abundance.38 Liquid phase exfoliation (LPH), mechanical exfoliation (ME), ball milling (BM) and alkali-ion intercalation (AII) are a few processes chosen to create desirable layers, but there are advantages and disadvantages associated with these techniques in terms of process conditions and quality of nanosheets.39–49 Of all the mentioned techniques, ball milling was recognized as the most scalable and commercialized method of nanosheet production.49,50 However, the pure ball milling method cannot give full play to the advantages of the layered structure of MoS2.51 Additionally, ball milling has the ease of coupling with numerous auxiliary methods to obtain nanostructure-like sheets and flakes of the desired dimensions and composition by altering the process conditions.2,26,50,52,53 Therefore, we proposed ultrasonic-assisted ball milling. The preparation method reduces the size of MoS2 by ball milling on the one hand, and obtains few-layer MoS2 by ultrasonic peeling on the other hand. The corresponding discussion is later in the paper.
Therefore, this paper aims to report the potential of minimal-layered MoS2 nanosheets, fabricated from a simple ultrasonicated ball milling exfoliation method, over commercial bulk MoS2. The as-prepared MoS2 material was demonstrated to be composed of only 4–8 layers and investigated under multiple spectroscopic techniques to understand the structural and morphological properties in comparison with those of commercial bulk MoS2. Benefiting from the non-agglomerated lamella structure, the electrochemical performance of the MoS2 anode is significantly improved by the controllable exfoliation of MoS2 compared with that of commercial MoS2. Besides, the mechanism involved in the synthesis of MoS2 nanosheets is illustrated to show the impact of the selected approach on structural properties and the ease of fabrication. Collectively, this provides an effective strategy for the exfoliation of other bulk materials, which has great significance for future material design and applications in energy conversion and storage devices.
Experimental
Exfoliation of MoS2
Firstly, 500 mg of commercial bulk MoS2 with a 325 mesh was dispersed in 5 mL of anhydrous ethanol solvent. The mixture was ball-milled continuously for 12 h at a speed of 450 rpm on a planetary mill with zirconia grinding balls and vials. The obtained dispersion was then ultrasonicated at ambient temperature for 5 h to produce a colloidal suspension of MoS2 nanosheets. The suspension was subjected to centrifugation at 5000 rpm for 15 min to remove any large particles, including partially exfoliated bulk MoS2 and unexfoliated residual bulk MoS2.
Fabrication of MoS2 anode electrode
According to previous reports,27 a vacuum filtration method was employed to obtain the MoS2 nanosheet anode on Celgard 2400 as a LIB polypropylene separator. Following the mentioned procedure, the as-prepared suspension was filtered through a porous filter paper, Celgard 2400 polypropylene separator, forming the MoS2 film. Subsequently, the film was dried in a vacuum chamber at 80 °C for 72 h, and the MoS2 anode electrode was obtained. In parallel, for comparison, the commercial MoS2 anode electrode was prepared by slurry-casting on Cu foils that served as current collectors. The slurry contained 80 wt% bulk MoS2, 10 wt% carbon black (CB) and 10 wt% poly(vinylidene) fluoride (PVDF) binder in a N-methylpyrrolidinone (NMP) solvent. The obtained electrode was dried in a vacuum at 90 °C overnight. The electrodes were then subjected to material characterization techniques.
Material characterization
The morphology of the bulk and prepared MoS2 was analysed in a field emission scanning electron microscope (FE-SEM, Hitachi S-4800), transmission electron microscope (TEM, Hitachi H-7000), and high-resolution transmission electron microscope (HRTEM, JEOL 2010F). The powder X-ray diffraction (XRD) pattern was recorded by a Rigaku RU-200BVH diffractometer using a Co-Kα source (λ = 1.7892 Å).
Electrochemical measurements
Coin-type electrochemical half-cells were used; the working electrode was the prepared anode electrode and the counter electrode was a lithium foil. The electrolyte for the system consisted of 1 M LiPF6 salt dissolved in ethylene carbonate (EC)
:
diethyl carbonate (DEC)
:
ethyl methyl carbonate (EMC) with a volume ratio of 1
:
1
:
1. The CR-2032 button battery was assembled in a dry glove box filled with argon (moisture and oxygen concentration < 1 ppm). A Princeton ParSTAT MC 2000A was utilized to perform cyclic voltammetry (CV) at a potential of 0.01 to 3.0 V (vs. Li/Li+) at a scan rate of 0.1 mV s−1. The charging and discharging characteristics were tested using a Neware CT-4000 battery tester at room temperature and constant current between 0.01 and 3.0 V (vs. Li/Li+).
Results and discussion
Fig. 1a shows the XRD patterns of bulk and as-prepared MoS2 as black and blue lines, respectively. The typical diffraction peaks of the bulk MoS2 finely matched the standard peaks of the hexagonal phase (JCPDS 37-1492). The as-prepared MoS2 sample represented five peaks corresponding to the (002), (004), (103), (006) and (008) planes in which a sharp peak is clear for (002) and confirms the well-stacked layered structure formation.21,54–56 Additionally, the larger peak widths clearly convey that the obtained MoS2 has a smaller particle size compared with that of bulk MoS2.57
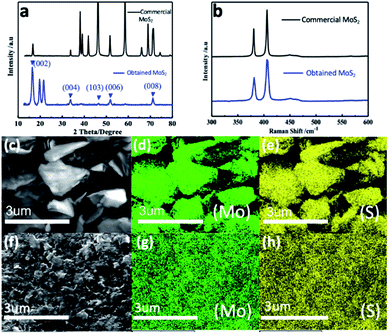 |
| Fig. 1 (a) XRD patterns and (b) Raman spectra of commercial MoS2 (black line) and obtained MoS2 (blue line) nanosheets; SEM element mappings of (c–e) commercial MoS2 and (f–h) MoS2 nanosheets: (d and g) are of Mo and (e and h) are of S. | |
Raman spectra of the bulk and as-prepared MoS2 are compared in Fig. 1b, in which the spectra show the same set of peaks. The two typical Raman active modes located at 380 cm−1 and 406 cm−1 can be attributed to E12g and A1g, resulting from the inlayer vibration of molybdenum and sulphur atoms along with the vibration of sulphides in the out-of-plane direction.58–61 Furthermore, Fig. 1c–h depict the elemental mappings of the bulk and as-prepared MoS2, where Fig. 1c and f are the overall images of the bulk and as-prepared MoS2. In the following images, it is worth noting that the atoms of Mo and S are evenly distributed in the two samples. The energy dispersive X-ray spectroscopy (EDX) associated with the functioning of HRTEM (Fig. S1†) shows that the as-prepared MoS2 consists only of Mo and S, which further confirms the Mo
:
S atomic ratio of 1
:
2; as agreed with the elemental composition of MoS2.
Moreover, SEM was employed to observe the morphology of the bulk MoS2 (shown in Fig. S2†). The random-shaped MoS2 displayed a sheet-like morphology with a thickness of ca. 1 μm. The as-prepared MoS2, as shown in Fig. 2a, exhibits a different morphology from that of the bulk one (Fig. S2†) signifying the essence of ball milling that decreased the size of MoS2 nanosheets dramatically. Similarly, the TEM image of the as-prepared MoS2 in Fig. 2b confirms the presence of thin MoS2 nanosheets. HRTEM (Fig. 2c) showcases the lateral view of a few lamellar structures with visible lattice fringes. Evidently, each film is composed of 4–8 MoS2 layers, that is, significantly reduced compared with those in the bulk MoS2 structure or any MoS2 nanosheet structures reported earlier. A characteristic peak that belongs to the [002] direction of the MoS2 nanosheets is demonstrated in Fig. 2d. The interlayer spacing is measured to be ∼0.66 nm and is consistent with the (002) plane of a layered hexagonal MoS2. This result reveals that each molybdenum atom layer is sandwiched between two sulphur atom layers. In addition to the interlayer spacing, the HRTEM image in Fig. 2e clearly illustrates the lattice fringes of MoS2 nanosheets with an elaborative crystal structure, in which the interplanar distances were measured to be 0.27 nm, corresponding to the (100) plane of MoS2.47,62 The several bright rings in Fig. 2f, as shown by Selected Area Electron Diffraction (SAED), coincide with the hexagonal MoS2 structure's diffraction pattern by further indicating the good stacking of MoS2 nanosheets with different crystallographic orientations.63,64 Additionally, the diffraction dots within the diffraction rings were identified as (002), (100), (103), (105), and (110) planes, which confirms the high crystallinity of the MoS2 nanosheets.65
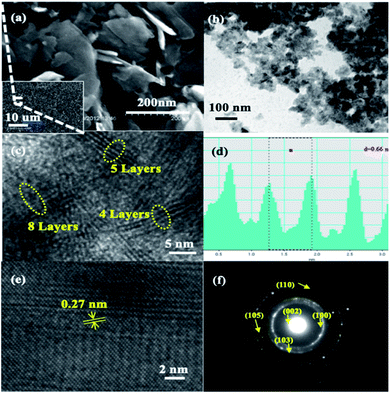 |
| Fig. 2 MoS2 nanosheets: (a) SEM and (b) TEM images; (c) lateral view of the MoS2 layers measured by HRTEM; (d) intensity profile along the MoS2 layers in (c) with nm units for the x-axis; (e) HRTEM image of a MoS2 nanosheet for interplanar spacing; (f) SAED pattern of a MoS2 nanosheet. | |
Through the above material characterization techniques and analysis, it can be deduced that the observations that emerged from the exfoliated MoS2 nanosheets via ultrasonic assisted ball milling process are admirable and satisfactory for commercial usage in LIBs. The desirable structural characteristics are possible due to the approach proposed and employed in this study to synthesize MoS2 nanosheets (as displayed in Fig. 3). After stage I, the layered MoS2 was dispersed into ethanol and ball-milled for 12 h. That the shear force from ball milling is superior to that of the weak van der Waals interactions between the MoS2 layers resulted in the easy exfoliation of some MoS2 layers during the process of ball milling.66 In the case of un-exfoliated MoS2, the ethanol solvent intercalated between the MoS2 layers, resulting in an increased layer distance. The exfoliation of MoS2 inevitably occurred when ultrasonics was employed (stage II). However, commercial MoS2 layers were stacked together via relatively weak van der Waals interactions, as represented in stage III.
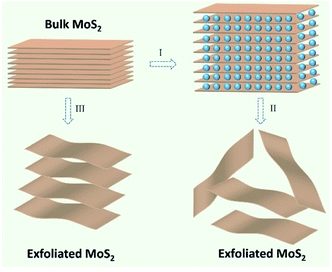 |
| Fig. 3 Schematic illustration for MoS2 nanosheet synthesis: (I) ball milling; (II) ultrasonic exfoliation; (III) untreated. | |
Lithium storage properties of bulk and as-prepared MoS2 were studied by a series of electrochemical tests, such as cyclic voltammetry (CV) and galvanostatic charge–discharge (GCD) testing. Fig. 4 shows the voltage range from 0.01 V to 3.00 V. First, the CV of bulk MoS2 and the prepared MoS2 under a scan rate of 0.1 mV s−1 were evaluated. The CV curves of the two samples were performed and evaluated as for the first scan. Firstly, in the first cathodic scan,67–70 the two peaks at 0.89 and 1.08 V correspond to the insertion of Li+ with the formation of LixMoS2 (MoS2 + xLi+ + xe− = LixMoS2) for the bulk and as-prepared MoS2, respectively. Inclusively, another obvious reduction peak (positioned at 0.35 and 0.52 V for bulk and as-prepared MoS2, respectively) indicates the existence of an electrochemical reduction that originates from a conversion reaction (LixMoS2 + 4Li+ + 4e− = 2Li2S + Mo/Liy), in which the formation of Mo metal along with the Li2S from LixMoS2 occurs. In the opposite process (anodic scan), one obvious oxidation peak due to the oxidation of Li2S into sulphur shows a similar reaction potential at ∼2.30 V for two anodes.70,71 If a comparative analysis is carried out of the second and third CV curves of bulk MoS2, a big difference can be observed, which reveals a poor cyclic performance. In the case of the as-prepared MoS2, these two CV curves nearly overlap, verifying superior cyclic performances.
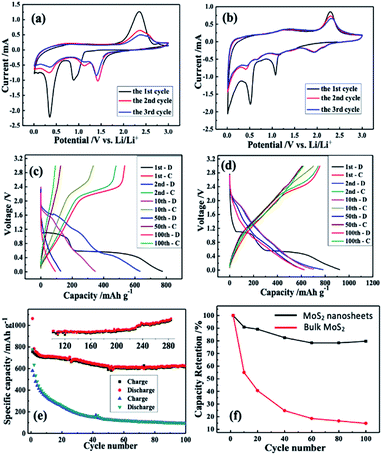 |
| Fig. 4 Cyclic voltammograms of (a) bulk MoS2 and (b) MoS2 nanosheets; typical charge and discharge curves at selected cycles of (c) bulk MoS2 and (d) MoS2 nanosheets; (e) a comparison of the cyclic performance of bulk MoS2 (to 100 cycles) and MoS2 nanosheets (over 280 cycles) and (f) capacity retention versus cycle numbers of (i) bulk MoS2 and (ii) MoS2 nanosheets. | |
For good measure, the lithium storage behaviour of the MoS2 anode was further measured by GCD testing via a CR-2032 coin. Fig. 4c and d illustrate the bulk and as-prepared charge–discharge curves of MoS2, respectively. The first discharge curves reveal two insertion plateaus, which shift in the subsequent cycles. In the subsequent charging curve, an obvious plateau due to delithiation was noticed, which corresponds to the CV curve.
Although the charge/discharge profiles of the as-prepared MoS2 have not considerably changed through cycling (as depicted in Fig. 4e), those of the bulk MoS2 anode were altered after 10 cycles. In the first cycle, the bulk MoS2 anode reported charge and discharge capacities of 581 mA h g−1 and 777 mA h g−1, respectively, while those values of the as-prepared MoS2 were 925 mA h g−1 and 657 mA h g−1. It is noteworthy that the irreversible capacity in the first cycle is high, which may arise from two aspects: (1) a solid electrolyte intermediate phase (SEI) is formed on the anode surface due to the electrolyte's decomposition; (2) during the lithium insertion in MoS2 nanosheets, lithium ions trapped in the nanoclusters or defect sites/intratubal sites cause the irreversible capacity.23,72
According to Fig. 4e, at a current density of 100 mA g−1, the cycle performances of the bulk and the as-prepared MoS2 are different. Noticeably, the as-prepared MoS2 still delivers a remarkable specific energy capacity after 100 cycles, while the bulk MoS2 anode shows an obvious capacity decay over 100 cycles. Fig. 4f displays the capacity retention of the two anodes. It is evident that the bulk MoS2 shows a much lower capacity retention (14.8%) than the as-prepared MoS2 (80.0%). The as-prepared MoS2 still maintained a high capacity of 716 mA h g−1 in the 285th cycle (see the inset of Fig. 4e) with an average of 0.030% capacity loss per cycle, suggesting its excellent cycling performance compared with those of other MoS2 based anode materials (Table S1†). Inclusively, the excellent cycle performance of the as-prepared MoS2 composed of 4–8 layers is attributed to the more facilitated diffusion in the liquid electrolyte and an increase in the electrolyte–electrode contact area compared with that of the bulk one.73–75 Moreover, the presence of only a few layers decreases the solid-state transport length of the lithium diffusion.70,76,77 Considering the results shown in Fig. 4, the as-prepared MoS2 as a LIB anode can effectively enhance the battery performance to a great extent.
Conclusions
The MoS2 nanosheets we obtained through a simple ball milling approach are only a few (4–8) layers. As an anode of LIBs, the as-prepared MoS2 achieves an outstanding reversible capacity of 716 mA h g−1 after 285 cycles, which reveals an improved cyclic performance and higher energy capacity compared with those of the bulk material with a measured specific capacity of only 94 mA h g−1 after observation for 100 cycles. This lead to an understanding of the effect of the synthesis method on MoS2 nanosheets for both the structural properties and the electrochemical performance. The proposed simple exfoliation process in this study can be potentially used for other layered materials, such as WS2, SnS2, MoSe2, etc. Moreover, this research can be of great importance to create cost-effective ultra-thin layered anodes with a promising performance for LIB application.
Conflicts of interest
There are no conflicts to declare.
Acknowledgements
The authors gratefully acknowledge the financial support from the Natural Science Foundation of Qinghai Province of China (2020-ZJ-910), the National Natural Science Foundation of China (52072298 and 51802261), and the Natural Science Foundation of Shaanxi Province (2020JC-41).
References
- V. Etacheri, R. Marom, R. Elazari, G. Salitra and D. Aurbach, Energy Environ. Sci., 2011, 4, 3243–3262 RSC.
- C. Wang, C. Zhan, X. Ren, R. Lv, W. Shen, F. Kang and Z.-H. Huang, RSC Adv., 2019, 9, 42316–42323 RSC.
- Y. Li, X. Yin, X. Huang, X. Liu and W. Wu, Int. J. Hydrogen Energy, 2020, 45, 16489–16499 CrossRef CAS.
- Q. H. Wang, K. Kalantar-Zadeh, A. Kis, J. N. Coleman and M. S. Strano, Nat. Nanotechnol., 2012, 7, 699–712 CrossRef CAS.
- K.-A. N. Duerloo, Y. Li and E. J. Reed, Nat. Commun., 2014, 5, 1–9 Search PubMed.
- W. Zhao, J. Pan, Y. Fang, X. Che, D. Wang, K. Bu and F. Huang, Chem.–Eur. J., 2018, 24, 15942–15954 CrossRef CAS PubMed.
- L. Jiang, B. Lin, X. Li, X. Song, H. Xia, L. Li and H. Zeng, ACS Appl. Mater. Interfaces, 2016, 8, 2680–2687 CrossRef CAS PubMed.
- J. R. Dahn, T. Zheng, Y. Liu and J. Xue, Science, 1995, 270, 590–593 CrossRef CAS.
- T. Stephenson, Z. Li, B. Olsen and D. Mitlin, Energy Environ. Sci., 2014, 7, 209–231 RSC.
- H. Zhao, H. Zeng, Y. Wu, S. Zhang, B. Li and Y. Huang, J. Mater. Chem. A, 2015, 3, 10466–10470 RSC.
- G. Fiori, F. Bonaccorso, G. Iannaccone, T. Palacios, D. Neumaier, A. Seabaugh, S. K. Banerjee and L. Colombo, Nat. Nanotechnol., 2014, 9, 768–779 CrossRef CAS PubMed.
- F. Xia, H. Wang, D. Xiao, M. Dubey and A. Ramasubramaniam, Nat. Photonics, 2014, 8, 899–907 CrossRef CAS.
- O. V. Yazyev, Rep. Prog. Phys., 2010, 73, 056501 CrossRef.
- D. Deng, K. Novoselov, Q. Fu, N. Zheng, Z. Tian and X. Bao, Nat. Nanotechnol., 2016, 11, 218–230 CrossRef CAS PubMed.
- F. Bonaccorso, L. Colombo, G. Yu, M. Stoller, V. Tozzini, A. C. Ferrari, R. S. Ruoff and V. Pellegrini, Science, 2015, 347, 1246501 CrossRef PubMed.
- J. Xiao, D. Choi, L. Cosimbescu, P. Koech, J. Liu and J. P. Lemmon, Chem. Mater., 2010, 22, 4522–4524 CrossRef CAS.
- J. Yuan, J. Zhu, R. Wang, Y. Deng, S. Zhang, C. Yao, Y. Li, X. Li and C. Xu, Chem. Eng. J., 2020, 125592 CrossRef CAS.
- H. Tan, Y. Feng, X. Rui, Y. Yu and S. Huang, Small Methods, 2020, 4, 1900563 CrossRef CAS.
- X. Man, P. Liang, H. Shu, L. Zhang, D. Wang, D. Chao, Z. Liu, X. Du, H. Wan and H. Wang, J. Phys. Chem. C, 2018, 122, 24600–24608 CrossRef CAS.
- M. Remskar, A. Mrzel, Z. Skraba, A. Jesih, M. Ceh, J. Demšar, P. Stadelmann, F. Lévy and D. Mihailovic, Science, 2001, 292, 479–481 CrossRef CAS PubMed.
- M. Chhowalla and G. A. Amaratunga, Nature, 2000, 407, 164–167 CrossRef CAS.
- E. Pomerantseva and Y. Gogotsi, Nat. Energy, 2017, 2, 1–6 Search PubMed.
- C. Feng, J. Ma, H. Li, R. Zeng, Z. Guo and H. Liu, Mater. Res. Bull., 2009, 44, 1811–1815 CrossRef CAS.
- Q. Su, S. Wang, M. Feng, G. Du and B. Xu, Sci. Rep., 2017, 7, 1–10 CrossRef PubMed.
- J. Kong, C. Zhao, Y. Wei and X. Lu, ACS Appl. Mater. Interfaces, 2015, 7, 24279–24287 CrossRef CAS.
- C. Liang, X. Sui, A. Wang, J. Chang, W. Wang, Z. Chen, W. Jiang, Y. Ma, J. Zhang and X. Liu, Adv. Mater. Interfaces, 2020, 7, 2001130 CrossRef CAS.
- X. Li, J. Yang, Y. Hu, J. Wang, Y. Li, M. Cai, R. Li and X. Sun, J. Mater. Chem., 2012, 22, 18847–18853 RSC.
- G. Cunningham, M. Lotya, C. S. Cucinotta, S. Sanvito, S. D. Bergin, R. Menzel, M. S. Shaffer and J. N. Coleman, ACS Nano, 2012, 6, 3468–3480 CrossRef CAS PubMed.
- J. N. Coleman, M. Lotya, A. O'Neill, S. D. Bergin, P. J. King, U. Khan, K. Young, A. Gaucher, S. De and R. J. Smith, Science, 2011, 331, 568–571 CrossRef CAS PubMed.
- H. Ramakrishna Matte, A. Gomathi, A. K. Manna, D. J. Late, R. Datta, S. K. Pati and C. Rao, Angew. Chem., Int. Ed., 2010, 49, 4059–4062 CrossRef.
- Z. Zeng, Z. Yin, X. Huang, H. Li, Q. He, G. Lu, F. Boey and H. Zhang, Angew. Chem., 2011, 123, 11289–11293 CrossRef.
- B. Radisavljevic, A. Radenovic, J. Brivio, V. Giacometti and A. Kis, Nat. Nanotechnol., 2011, 6, 147–150 CrossRef CAS.
- C. Lee, H. Yan, L. E. Brus, T. F. Heinz, J. Hone and S. Ryu, ACS Nano, 2010, 4, 2695–2700 CrossRef CAS PubMed.
- R. Liu, D. Wu, X. Feng and K. Müllen, J. Am. Chem. Soc., 2011, 133, 15221–15223 CrossRef CAS PubMed.
- A. Ciesielski and P. Samori, Chem. Soc. Rev., 2014, 43, 381–398 RSC.
- X. Duan, C. Wang, J. C. Shaw, R. Cheng, Y. Chen, H. Li, X. Wu, Y. Tang, Q. Zhang and A. Pan, Nat. Nanotechnol., 2014, 9, 1024–1030 CrossRef CAS PubMed.
- M.-Y. Li, Y. Shi, C.-C. Cheng, L.-S. Lu, Y.-C. Lin, H.-L. Tang, M.-L. Tsai, C.-W. Chu, K.-H. Wei and J.-H. He, Science, 2015, 349, 524–528 CrossRef CAS PubMed.
- V. Nicolosi, M. Chhowalla, M. G. Kanatzidis, M. S. Strano and J. N. Coleman, Science, 2013, 340, 1226419 CrossRef.
- H. Liu, L. Liu, M. Yi, Z. Shen, S. Liang, X. Zhang and S. Ma, Chem. Eng. J., 2017, 311, 293–301 CrossRef CAS.
- H. Li, J. Wu, Z. Yin and H. Zhang, Acc. Chem. Res., 2014, 47, 1067–1075 CrossRef CAS PubMed.
- G. S. Bang, K. W. Nam, J. Y. Kim, J. Shin, J. W. Choi and S.-Y. Choi, ACS Appl. Mater. Interfaces, 2014, 6, 7084–7089 CrossRef CAS PubMed.
- A. Jawaid, D. Nepal, K. Park, M. Jespersen, A. Qualley, P. Mirau, L. F. Drummy and R. A. Vaia, Chem. Mater., 2016, 28, 337–348 CrossRef CAS.
- A. Gupta, V. Arunachalam and S. Vasudevan, J. Phys. Chem. Lett., 2016, 7, 4884–4890 CrossRef CAS PubMed.
- X. Zhang, Z. Lai, C. Tan and H. Zhang, Angew. Chem., Int. Ed., 2016, 55, 8816–8838 CrossRef CAS PubMed.
- G. Eda, H. Yamaguchi, D. Voiry, T. Fujita, M. Chen and M. Chhowalla, Nano Lett., 2011, 11, 5111–5116 CrossRef CAS PubMed.
- D. Voiry, M. Salehi, R. Silva, T. Fujita, M. Chen, T. Asefa, V. B. Shenoy, G. Eda and M. Chhowalla, Nano Lett., 2013, 13, 6222–6227 CrossRef CAS PubMed.
- Y. H. Lee, X. Q. Zhang, W. Zhang, M. T. Chang, C. T. Lin, K. D. Chang, Y. C. Yu, J. T. W. Wang, C. S. Chang and L. J. Li, Adv. Mater., 2012, 24, 2320–2325 CrossRef CAS PubMed.
- J. Zhou, J. Lin, X. Huang, Y. Zhou, Y. Chen, J. Xia, H. Wang, Y. Xie, H. Yu and J. Lei, Nature, 2018, 556, 355–359 CrossRef CAS PubMed.
- C. Han, Y. Zhang, P. Gao, S. Chen, X. Liu, Y. Mi, J. Zhang, Y. Ma, W. Jiang and J. Chang, Nano Lett., 2017, 17, 7767–7772 CrossRef CAS PubMed.
- S. Mateti, M. M. Rahman, P. Cizek and Y. Chen, RSC Adv., 2020, 10, 12754–12758 RSC.
- F. Yang, X. Feng, P.-A. Glans and J. Guo, APL Mater., 2021, 9, 050903 CrossRef CAS.
- S. Kim, W. Park, D. Kim, J. Kang, J. Lee, H. Y. Jang, S. H. Song, B. Cho and D. Lee, Nanomaterials, 2020, 10, 1045 CrossRef CAS.
- A. Tayyebi, N. Ogino, T. Hayashi and N. Komatsu, Nanotechnology, 2019, 31, 075704 CrossRef PubMed.
- D. He, Y. Yang, Z. Liu, J. Shao, J. Wu, S. Wang, L. Shen and N. Bao, Nano Res., 2020, 13, 1029–1034 CrossRef CAS.
- Y. Teng, H. Zhao, Z. Zhang, Z. Li, Q. Xia, Y. Zhang, L. Zhao, X. Du, Z. Du and P. Lv, ACS Nano, 2016, 10, 8526–8535 CrossRef CAS PubMed.
- X. L. Li, J. P. Ge and Y. D. Li, Chem.–Eur. J., 2004, 10, 6163–6171 CrossRef CAS PubMed.
- J. I. Langford and A. Wilson, J. Appl. Crystallogr., 1978, 11, 102–113 CrossRef CAS.
- J. Wang, Z. Shen and M. Yi, New J. Chem., 2020, 44, 15887–15894 RSC.
- G. Ke, H. Chen, J. He, X. Wu, Y. Gao, Y. Li, H. Mi, Q. Zhang, C. He and X. Ren, Chem. Eng. J., 2021, 403, 126251 CrossRef CAS.
- Y. Zhan, Z. Liu, S. Najmaei, P. M. Ajayan and J. Lou, Small, 2012, 8, 966–971 CrossRef CAS PubMed.
- V. Koroteev, L. Bulusheva, A. Okotrub, N. Yudanov and D. Vyalikh, Phys. Status Solidi B, 2011, 248, 2740–2743 CrossRef CAS.
- F. Chen, D. Shi, M. Yang, H. Jiang, Y. Shao, S. Wang, B. Zhang, J. Shen, Y. Wu and X. Hao, Adv. Funct. Mater., 2020, 2007132 Search PubMed.
- Z. Deng, H. Jiang, Y. Hu, Y. Liu, L. Zhang, H. Liu and C. Li, Adv. Mater., 2017, 29, 1603020 CrossRef PubMed.
- A. Zak, Y. Feldman, V. Lyakhovitskaya, G. Leitus, R. Popovitz-Biro, E. Wachtel, H. Cohen, S. Reich and R. Tenne, J. Am. Chem. Soc., 2002, 124, 4747–4758 CrossRef CAS PubMed.
- C. M. Zelenski and P. K. Dorhout, J. Am. Chem. Soc., 1998, 120, 734–742 CrossRef CAS.
- W. Zhao, M. Fang, F. Wu, H. Wu, L. Wang and G. Chen, J. Mater. Chem., 2010, 20, 5817–5819 RSC.
- J. B. Cook, H. S. Kim, Y. Yan, J. S. Ko, S. Robbennolt, B. Dunn and S. H. Tolbert, Adv. Energy Mater., 2016, 6, 1501937 CrossRef.
- R. Zhao, Y. Han, W. Li, J. Li, M. Chen and L. Chen, Chem. Commun., 2020, 56, 3007–3010 RSC.
- Q. Wang and J. Li, J. Phys. Chem. C, 2007, 111, 1675–1682 CrossRef CAS.
- X. Fang, X. Yu, S. Liao, Y. Shi, Y.-S. Hu, Z. Wang, G. D. Stucky and L. Chen, Microporous Mesoporous Mater., 2012, 151, 418–423 CrossRef CAS.
- C. Chen, X. Xie, B. Anasori, A. Sarycheva, T. Makaryan, M. Zhao, P. Urbankowski, L. Miao, J. Jiang and Y. Gogotsi, Angew. Chem., Int. Ed., 2018, 57, 1846–1850 CrossRef CAS PubMed.
- J. Li, S. Du, H. Tao and X. Yang, Ionics, 2020, 1–10 Search PubMed.
- X. Cao, C. Tan, X. Zhang, W. Zhao and H. Zhang, Adv. Mater., 2016, 28, 6167–6196 CrossRef CAS PubMed.
- Z. Li, N. Liu, X. Wang, C. Wang, Y. Qi and L. Yin, J. Mater. Chem., 2012, 22, 16640–16648 RSC.
- C. Yuan, L. Yang, L. Hou, L. Shen, X. Zhang and X. W. D. Lou, Energy Environ. Sci., 2012, 5, 7883–7887 RSC.
- A. Pan, J.-G. Zhang, G. Cao, S. Liang, C. Wang, Z. Nie, B. W. Arey, W. Xu, D. Liu and J. Xiao, J. Mater. Chem., 2011, 21, 10077–10084 RSC.
- L. Li, X. Yin, S. Liu, Y. Wang, L. Chen and T. Wang, Electrochem. Commun., 2010, 12, 1383–1386 CrossRef CAS.
Footnote |
† Electronic supplementary information (ESI) available. See DOI: 10.1039/d1ra08255h |
|
This journal is © The Royal Society of Chemistry 2022 |
Click here to see how this site uses Cookies. View our privacy policy here.