DOI:
10.1039/D2MA00072E
(Paper)
Mater. Adv., 2022,
3, 4851-4860
Fused filament fabrication of PVDF films for piezoelectric sensing and energy harvesting applications†
Received
23rd January 2022
, Accepted 29th April 2022
First published on 2nd May 2022
Abstract
Fused filament fabrication (FFF) of piezoelectric polymer polyvinylidene fluoride (PVDF) provides a simple manufacturing technique for the fabrication of lead-free piezoelectric devices compared to the traditional manufacturing methods, such as large-scale film extrusion and solution casting. Here, we investigate the effects of the stretching and poling parameters on the enhancement of piezoelectric performance of the printed PVDF films. The stretched and polarized PVDF films with dimensions of 40 × 20 × 0.06 mm (length × width × thickness) possess a piezoelectric charge coefficient (d33) of 7.29 pC N−1 and a fraction of β phase (Fβ) of 65% at a stretching ratio (R) of 4 after being polarized under an electric field of 30 V μm−1. The resulting d33 of the fabricated PVDF films has been substantially enhanced by ∼10–100 times higher than the related reported values of the FFF printed PVDF films. The fabricated PVDF films are capable of detecting compression (d33) and vibration (d31). By blowing four piezoelectric films connected in parallel for 3 min, the energy stored in the capacitor can make a LED blink. Our fabricated piezoelectric PVDF films could be used in the field of pressure sensing, vibration sensing and energy harvesting applications.
1. Introduction
Piezoelectric materials are used in various applications such as in pressure sensing,1,2 strain sensing,3,4 actuation5,6 and energy harvesting7,8 because of their capabilities of converting mechanical energy to electrical energy and vice versa.9,10 Compared to high piezoelectric ceramics such as lead zirconate titanate (PZT) and barium titanate (BaTiO3), piezoelectric polymer polyvinylidene fluoride (PVDF) has been increasingly used owing to its lightness, high flexibility, durability and biocompatibility.11,12 PVDF is a semicrystalline polymer with a repeating unit of the CH2–CF2 monomer.13 It has two main phases: a non-polar α phase and a polar β phase.14,15 The dipole moments in PVDF originate from the high electronegativity of fluorine atoms and smaller electronegativity of hydrogen atoms.16,17 The α phase with a trans–gauche–trans–gauche’ (TGTG’) conformation is not piezoelectric as a result of the cancellation of the dipole moments, while the β phase with an all trans (TTTT) conformation possesses the largest polarization due to the alignment of the dipole moments in the same direction.18 However, PVDF usually crystallizes into the thermally stable α phase.19,20 Several methods have been used to induce the conversion from the α phase to the β phase such as mechanical stretching21–23 and hot-pressing.24,25 In addition to the requirement of the high content of the β phase (Fβ) in PVDF, an electrical poling treatment is often essential to align the randomly dispersed β phase in order to obtain a net polarization.26–29 Poling parameters (e.g. time, temperature and poling voltage) have to be appropriately adjusted in order to maximize the efficiency of the poling process.30,31 A high Fβ is a prerequisite for achieving a high piezoelectric coefficient of the polarized PVDF elements. The piezoelectric strain coefficient (d31 and d33) with double subscripts is used to illustrate the piezoelectric performance: the first subscript indicates the direction of the charge generation and the second subscript indicates the direction of the applied mechanical strain.
Over the past decade, additive manufacturing technology (or 3D printing) has increasingly been utilized to fabricate smart materials including piezoelectric materials.1,2,32–39 The traditional manufacturing methods for the preparation of PVDF films such as solution casting40–42 and electrospinning43–45 require toxic solvents, while extrusion molding19,42 requires careful control of the melt temperature and the material feeding rate. Thus, fused filament fabrication (FFF) offers a maneuverable and eco-friendly approach for the fabrication of piezoelectric PVDF devices, i.e., recyclable and without the requirement of a toxic solvent. Several studies demonstrated FFF 3D printing of piezoelectric PVDF films. Lee et al.35 and Kim et al.33 integrated FFF 3D printing and electrical poling steps to achieve one-step fabrication of piezoelectric PVDF films. Porter et al.32 investigated the effects of printing parameters on the piezoelectric performance of the PVDF films. However, the reported piezoelectric coefficients in these studies (Kim et al.:33d33 = 0.048 pC N−1; Porter et al.:32d31 = 1.19 pC N−1) are much lower than those of the commercial hot-pressed piezoelectric PVDF films, which are in the range of 28–32 pC N−1.46 In addition, some researchers incorporated fillers to induce the generation of β phases in the FFF 3D printed PVDF films. Pei et al.47 added 5 wt% tetraphenylphosphonium chloride (TPPC) nanoparticles to obtain 83.8% β phases, while 28.9% of the β phase content for pure PVDF. Liu et al.48 enhanced the β phase content of the PVDF filament to 93% by adding 15 wt% ionic liquid as compared to only 13.5% of the β phase in pure PVDF.
Our novel strategy in this work is to fabricate piezoelectric PVDF films with highly enhanced d33 compared to the related reported values33 using the facile FFF 3D printing technique and two tailored post-treatments: mechanical stretching and electrical poling. Four different stretching ratios (R = final length/original length, R = 1, 2, 3 and 4) are investigated to achieve the highly polar β phase content. We then used the polarized printed piezoelectric PVDF films in three applications: a frequency detector, a pressure sensor and energy harvesters to convert wind energy to electricity. We believe that FFF 3D printing technology with appropriate post-treatments investigated herein is promising for the construction of flexible PVDF piezoelectric sensors and energy harvesters for more advanced applications in areas ranging from medical to aerospace and beyond.
2. Experimental section
Materials
PVDF filaments (1.75 mm in diameter, Fluorinar-H™ Kynar®) were purchased from Nile Polymers, Inc (USA). Commercially available unpolarized (R = 5) and polarized (R = 5) hot-pressed PVDF films with a thickness of ∼120 μm were purchased from PolyK Technologies, LLC (USA).
FFF printing of PVDF films
PVDF films were fabricated using a commercially available 1.75 mm diameter PVDF filament. An FFF 3D printer (Raised3D Pro 2) was used to print a one-layer film with dimensions of 60 × 40 × 0.15 mm. Table 1 lists the main printing parameters.
Table 1 FFF 3D printing parameters for preparing the PVDF films
Parameters |
Values |
Nozzle size |
0.4 mm |
Bed temperature |
100 °C |
Extrusion temperature |
250 °C |
Printing speed |
30 mm s−1 |
Infill percentage |
100% |
Layer height |
0.15 mm |
Stretching process
The stretching process was carried out on the printed PVDF films using a tensile test machine (eXpert 2600, ADMET). The dimensions of the PVDF film between the upper and lower grips were 40 × 40 × 0.15 mm. The stretching conditions were 100 °C in an environmental chamber (F-280DT, ADMET) and a stretching rate of 0.2 mm s−1. When other temperatures (80 to 120 °C) and speed (0.1 to 1 mm s−1) settings were used, the PVDF films cracked during the stretching process. The stretching ratios were varied from 1 to 4. The PVDF films have a great tendency to crack during the stretching process if we stretch them with R > 4.
Poling process
We built a contact poling setup to align the dipole moments of PVDF films, which consisted of three parts: an in-house-designed poling chamber, a high voltage power supply (ES60kV negative, 10 Watt, Gamma High Voltage Research, Inc.) and a hot plate (Thermo Scientific™ SuperNuova + ™, Fisher Scientific). (see Fig. S1, ESI†) The commercially available hot-pressed PVDF films were polarized to confirm the functionality of the in-house built poling setup.
Before the poling process, both the 3D printed and commercial PVDF films were cut into the same size of 40 × 20 mm and attached with conductive aluminum tape (3M, USA) to both surfaces as poling electrodes. During the poling process, the specimen was clamped between the copper rod and the bottom aluminum plate. Then, the specimen was cooled down to room temperature before removing the electric field to reduce the misalignment of dipole moments. After the poling process, the aluminum tapes were removed, and the films were washed with soap to remove the residue of silicone oil and dried at room temperature before painting the electrodes on their top and bottom surfaces.
To evaluate the poling performance of the contact poling setup, unpolarized commercially stretched hot-pressed PVDF films are polarized using four poling voltages (2, 4, 6 and 8 kV) at 80 °C for 60 min, four poling times (30, 60, 90 and 120 min) at 80 °C under 6 kV and five poling temperatures (room temperature, 50, 80, 110 and 140 °C) under 6 kV for 60 min, respectively. To investigate the optimal poling conditions for the printed PVDF films stretched at R = 4 (highest Fβ), we further polarized them using three poling voltages (1, 2 and 3 kV) at 80 °C for 60 min, four poling times (30, 60, 90 and 120 min) at 80 °C under 2 kV and five poling temperatures (room temperature, 50, 80, 110 and 140 °C) under 2 kV for 60 min, respectively. In addition, the printed PVDF films stretched at R = 1, 2 and 3 are also polarized with an electric field of 30 V μm−1 at 80 °C for 60 min.
Electrode fabrication and electrical connection process
A bristle paintbrush was used to paint a thin layer of silver conductive paste (MG Chemicals 842AR, ABRA Electronics Corp.) on the top and bottom surfaces of the printed piezoelectric PVDF films as electrodes for the electromechanical measurement. We left a gap (∼2 mm) between the edge of the silver electrodes and the edge of the PVDF films in order to avoid contact between the two electrodes. Then, two pieces of aluminum tapes (5 × 10 mm) were used to electrically connect the silver electrodes and the wires.
Piezoelectric property characterization
A d33 meter (YE2730, Sinocera Piezotronics, Inc.) was used to characterize the piezoelectric coefficient d33. The specimens were tested approximately one day after the poling process because the d33 value measured immediately after the poling process is higher than the real value. In the cantilever bending and compression tests, open-circuit voltages were collected using a charge amplifier (Piezo Lab Amplifier, MEAS Specialties) in the voltage mode. The data were acquired with an NI-9239 data acquisition system attached to a USB carrier NI-9162 (National Instruments) and recorded using a custom LabVIEW interface.
Piezoelectric β phase characterization
A Fourier-transform infrared (FTIR) spectrometer (Nicolet 6700, Thermo Scientific) was used to obtain the absorption spectra of different types of PVDF films at 8 cm−1 resolution from 550 to 1250 cm−1. 128 scans were conducted on each sample and the average values were used to assess the content of different phases.
Optical characterization
A Canon EOS Rebel T4i camera was used for the photography of the samples in this paper. Optical images of the cross-section of the sensors (Fig. 1f) were taken using an optical microscope (BX-61, Olympus). A high-speed camera (MotionBLITZ Cube4, Mikrotron) captured the cantilever bending test at a frame rate of 200 Hz.
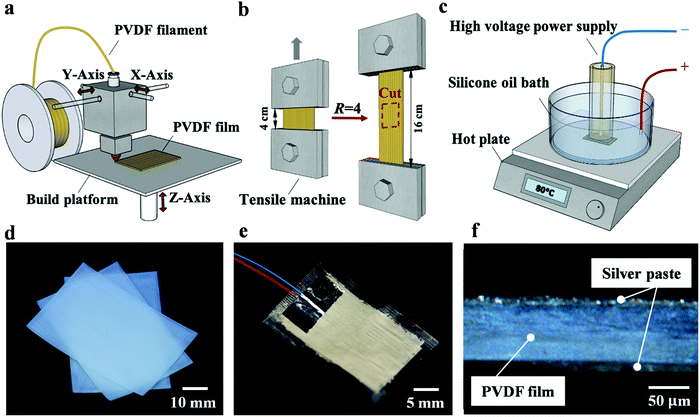 |
| Fig. 1 Fabrication of the piezoelectric PVDF films. Schematic of the (a) FFF printing process of the PVDF films (60 × 40 × 0.15 mm). (b) Stretching process of the printed PVDF films (R = 4). (c) Contact poling process of the stretched PVDF films (40 × 20 × 0.06 mm). Photos of (d) FFF printed PVDF films. (e) A piezoelectric PVDF film with electrical connections. (f) Optical image of the cross-section of the piezoelectric PVDF film. | |
Cantilever bending test
An aluminum beam with dimensions of 120 × 40 × 0.5 mm was fixed on a steel support and bent dynamically by a shaker (K2004E01, Mode Shop Inc.). The span length is ∼8 cm. The printed piezoelectric PVDF films were attached near the clamped end of the aluminum beam in order to exhibit maximum strain and detect the vibration frequency. During the cantilever bending test, the shaker was excited by a function generator (Model 19, Wavetek Corp.) in a sine wave format at eight different frequencies: 0.1, 0.5, 1, 5, 10, 20, 30 and 40 Hz.
Compression test
Compression tests of the printed piezoelectric PVDF films were carried out on an MTS Insight machine with a 1000 N load cell in the compression mode (MTS 569332-01). The crosshead speed was 1 mm s−1. An acrylic disc with a diameter of 10 mm was glued on top of the PVDF film to obtain the same contact area under compression. The compression head moved down 0.033, 0.056, 0.079, 0.101, 0.129, 0.159, 0.206 and 0.234 mm until the maximum compressive force of 100, 200, 300, 400, 500, 600, 700 and 800 N was reached, respectively. The average voltage output is calculated from three measurements.
Energy harvester
Four FFF printed PVDF films were connected in parallel and glued on a 3D printed PLA tree as the energy harvesting “leaves” and blown using a tabletop air circulation fan (PFT30T2ABB-V, PELONIS) at 1500 rpm. A circuit was built in order to light a red LED using the energy generated by the “piezo leaves”. In this circuit, a bridge-rectifier consisting of four diodes converted the AC generated by these four “piezo leaves” to DC, while a 2.2 μF capacitor stored the converted energy. The stored voltage in the capacitor was displayed on a digital multimeter (HHM11, Omega Engineering, Inc.).
3. Results and discussion
Fig. 1a–c schematically shows the fabrication process of a piezoelectric PVDF film based on FFF printing, stretching (R = 4) and poling processes. The FFF printed one-layer PVDF films are stretched along with the printing direction at R = 4 (i.e., from 4 cm to 16 cm) to induce the generation of the β phase (Fig. 1a and b). Then, the stretched PVDF films are cut to 40 × 20 mm and polarized along the thickness direction by a contact poling setup to align the randomly oriented dipole moment (Fig. 1c). Fig. 1d shows the photo of the printed PVDF films (60 × 40 × 0.15 mm). For efficient performance, the FFF printed PVDF films have to be free of porosities or impurities, otherwise a premature breakage during the mechanical stretching process or a permanent electrical breakdown during the poling process could happen. In case of an electrical breakdown, the piezoelectric element could not be further polarized and the piezoelectricity will remain very low. Undesired porosities or impurities can be created during the filament preparation and/or the FFF printing process. First, the as-received printing filament should have the least content of bubbles and impurities. Second, the PVDF filaments were dried in the oven to minimize their moisture content and the pores in the printed parts. Meanwhile, we slightly increase the extrusion width to make sure there is no gap between the printed lines (Fig. S2, ESI†). A fabricated PVDF film with electrical connections is shown in Fig. 1e. The optical image of the cross-section of the piezoelectric PVDF film with electrodes shown in Fig. 1f illustrates that the average thickness of the piezoelectric PVDF film after being stretched at R = 4 is ∼60 μm and the average thickness of the painted silver electrodes on each side is ∼15 μm. The photo and the thickness of the PVDF films stretched at R = 1, 2 and 3 are shown in Fig. S3 and listed in Table S1 in the ESI.†
Poling voltage, time and temperature are the three main poling parameters that influence the piezoelectric properties of polarized PVDF films. Poling voltage should be sufficiently high to align the dipole moments, while poling time should be optimized to ensure complete polarization in the shortest time. An elevated poling temperature is used to increase the mobility of the PVDF molecules. Fig. 2a–c show the d33 of the printed PVDF films (R = 4) and the commercial unpolarized PVDF films with respect to poling voltage, time and temperature, respectively. In Fig. 2a, d33 values of both printed (R = 4) and commercial PVDF films increase rapidly and then reach a plateau value with the enhancement of the poling voltage (poling temperature = 80 °C and poling time = 60 min). For the commercial stretched PVDF films, under the highest poling voltage value of 6 kV, which is approximately 50 V μm−1 electric field, the maximum d33 value of 32.41 pC N−1 is reached, consistent with the reported d33 value (32 pC N−1) of the commercial polarized PVDF film measured using a d33 meter.46 Electrical breakdown occurs at ∼7 kV as marked in blue. The printed PVDF films (R = 4) can hold a maximum poling voltage of 2 kV, which is approximately 30 V μm−1 electric field and leads to a maximum d33 value of 7.29 pC N−1. Electrical breakdown of the PVDF film occurs at 3 kV as marked in red. The maximum poling electric field of the printed PVDF films (R = 4) is less than those of commercial PVDF films due to the fact that the thinner section is present between the extruded lines in the printed PVDF films (Fig. S2, ESI†). In Fig. 2b, d33 of both printed (R = 4) and commercial PVDF films increase rapidly and then reach a plateau value with the poling time (poling temperature = 80 °C, poling voltage = 50 V μm−1 (commercial PVDF) and 30 V μm−1 (printed PVDF)). For both commercial and printed PVDF films, the d33 value increases with poling time until 60 min. The d33 is almost constant for a poling time beyond 60 min probably due to the completion of the alignment of the dipole moments in that period. In Fig. 2c, d33 of both printed (R = 4) and commercial PVDF films increase until 80 °C and then drop down with the increase of poling temperature (poling time = 60 min, poling voltage = 50 V μm−1 (commercial PVDF) and 30 V μm−1 (printed PVDF)). We observe that the highest d33 value is achieved at 80 °C. Below 80 °C, the PVDF molecules are inactive, so it could not be reoriented efficiently along with the electric field.49 However, when the poling temperature is above 80 °C, we observed that the PVDF films significantly warp and detach from the bottom poling plate, so the poling electric field cannot be uniformly applied on the PVDF films. The investigation of the poling parameters for the commercial PVDF films suggests that the optimal poling settings are 80 °C, 50 V μm−1 and 60 min. However, the printed PVDF films could not sustain more than 30 V μm−1 because of the thinner area between printed lines. Thus, the tailored poling settings for the printed PVDF films are 80 °C, 30 V μm−1 and 60 min. In the d33 measurement, three specimens are tested and each specimen is measured at three different locations. We found that the error bar of the specimens polarized under the same conditions is too small to be detected, which indicates the PVDF films have been uniformly polarized.
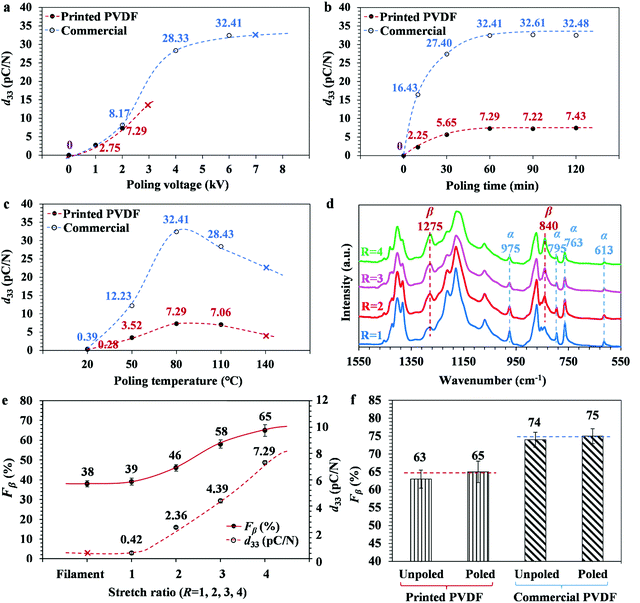 |
| Fig. 2 Investigation of the optimal poling and stretching parameters by characterizing and comparing the piezoelectric behaviors of printed PVDF films fabricated in this work and stretched commercial hot-pressed PVDF films. (a) d33 of commercial and printed (R = 4) PVDF films polarized under different poling voltages: 2, 4, 6 and 7 kV (for commercial PVDF); 1, 2 and 3 kV (for printed PVDF) (red and blue markers represent electrical breakdown). (b) d33 of commercial and printed (R = 4) PVDF films polarized for different poling times: 30, 60, 90 and 120 min. (c) d33 of commercial and printed (R = 4) PVDF films polarized at different poling temperatures: room temperature, 50, 80, 110 and 140 °C (red and blue markers represent electrical breakdown). (d) FTIR spectrum, (e) Fβ (%) and d33 of the unprinted PVDF filament and polarized printed PVDF films stretched at R = 1, 2, 3 and 4. (poling parameters: 80 °C, 30 V μm−1 and 60 min) (f) Comparison of Fβ (%) of printed PVDF films fabricated in this work (R = 4) and commercial PVDF films before and after the poling process. | |
We investigate the effect of R on the generation of piezoelectric β phases in the printed PVDF films. The photos and the dimensions of the printed PVDF films stretched at R = 1, 2, 3 and 4 are shown in Fig. S3, ESI.† The FTIR spectra of the polarized printed PVDF films stretched at R = 1 to 4 are shown in Fig. 2d. Herein, 840 cm−1 is the characteristic peak of the piezoelectric β phase, while 613, 713, 795 and 975 cm−1 are the representative peaks of the piezoelectric α phase. With the increase of R, the peaks of the α phase decrease, while the peak of the β phase increases, meaning that the printed PVDF films transform from the α phase into the β phase. For a system containing α and β phases, the modified Beer–Lambert law is used to calculate Fβ (%):
| 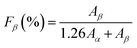 | (1) |
where
Aα and
Aβ are the absorbance of
α and
β phases at 763 and 840 cm
−1, respectively, and 1.26 is the ratio of the absorption coefficient at the corresponding wavenumber of 6.1 × 10
4 and 7.7 × 10
4 cm
2 mol
−1 for
α and
β phases, respectively.
19,50 Three specimens are prepared for each stretching condition and
Fβ (%) and
d33 of each specimen is measured at three different locations. As shown in
Fig. 2e,
Fβ (%) and
d33 increase with the value of
R. The unprinted PVDF filament and the printed PVDF films stretched at
R = 1 have a similar low
Fβ (%) and
d33, indicating that the 3D printing process cannot efficiently convert the
α phase to
β phase in PVDF. Both
Fβ (%) and
d33 increase with
R, which means that the stretching process is necessary for achieving higher piezoelectric performance. The polarized printed PVDF films possess an
Fβ (%) of 65% and a
d33 of 7.29 pC N
−1, which is ∼10–100 times higher compared to the previously reported FFF 3D printed PVDF films (Kim
et al.:
33d33 = 0.048 pC N
−1; Porter
et al.:
32d31 = 1.19 pC N
−1). The commercial hot-pressed PVDF film has a
Fβ of 74% and a
d33 of 28 pC N
−1. The lower
d33 of the FFF printed PVDF film compared to the commercial one is due to the lower poling electric field they can reach before the electrical breakdown occurs. The interface between the printed lines, and the surface roughness have an adverse effect during the poling phase. Further optimization of the FFF process parameters (
e.g., chamber temperature, nozzle size) might lead to an optimal poling electrical field to reach the performance of commercial dense films. Also, the lower
Fβ arises from the stretching process, when
R > 4, our printed PVDF films rupture, while the commercial films had already been stretched at
R = 5. The utilization of a lower
R value is due to the relatively weak interface between the printed lines that makes the printed films fail prematurely. In addition, we compare
Fβ (%) of the printed PVDF films and the commercial PVDF films before and after the poling process with their respective optimal poling parameters (
Fig. 2f). For both PVDF films,
Fβ (%) has not been much enhanced by the poling step. The commercial PVDF films have a slightly higher
Fβ (%) than the printed PVDF films owing to the hot-pressing process and the higher
R (
R = 5) during the stretching process. In conclusion, the stretching process creates higher
Fβ (%) and poling process aligns
β PVDF molecules to achieve a non-zero net polarization. In addition, we heat the polarized printed PVDF films at 30, 40, 50, 60, 70, 80, 90 until 100 °C. Below 60 °C,
d33 is stable. Above 60 °C,
d33 decreases with increasing temperature due to the misalignment of the PVDF molecules,
i.e., losing their net polarization. Thus, the maximum allowable operating temperature for the FFF printed piezoelectric PVDF films developed in this work is 60 °C as shown in Fig. S4, ESI.
†
We chose 40 × 20 × 0.06 mm polarized printed piezoelectric PVDF films (R = 4; polarized at 80 °C, 30 V μm−1 for 60 min) for the demonstration of two sensing (cantilever bending – d31 mode and compression tests – d33 mode) and one energy harvesting applications:
Application #1: cantilever for bending frequency sensing application
A cantilever bending test setup (Fig. 3a) is designed to evaluate the frequency detection behavior of the printed piezoelectric PVDF sensor. The shaker and the aluminum beam are fixed on a steel support and connected to a rod. The screwed rod moves back and forth in the x direction and bends the aluminum beam. The printed piezoelectric PVDF sensor is attached near the clamped end of the aluminum beam. The cantilever bending test was also recorded by the high-speed camera as shown in the ESI.† Movie S1. The shaker is excited by a function generator (in sine wave format) at eight frequencies (i.e., 0.1, 0.5, 1, 5, 10, 20, 30 and 40 Hz) and the deflection of the free end of the aluminum beam is held constant at +5/0 mm. To validate the durability of the printed piezoelectric sensor, we performed the cyclic test at 5 Hz for around 8 h and captured the voltage at the beginning and at the end of the cyclic test for 1200 s, respectively. The printed piezoelectric PVDF sensor still shows good sensitivity and favorable stability for more than 140
000 cycles (Fig. 3b). Fig. 3c shows the voltage generated from the printed piezoelectric film sensor in a period of 1 s between 0.1 and 40 Hz. The measured peak-to-peak voltage is ∼0, 9, 39, 35, 29, 6, 2 and 0 mV. The highest peak-to-peak voltage output of ∼39 mV is observed at 1 Hz. The peak-to-peak voltage increases from 9 to 39 mV as the frequency increases from 0.5 to 10 Hz and then decreases to 2 mV as the frequency increases from 10 to 30 Hz. The detected frequency by the printed piezoelectric sensor is consistent with the related actuating frequency between 0.5 to 30 Hz. The output voltage signal is close to zero below 0.5 Hz and above 30 Hz. Below 0.5 Hz, the movement is too slow to be detected. The reason is that the piezoelectric sensors are good at dynamic force measurement instead of static force measurement due to the fact that the surface charges are easily neutralized under static force.51 Above 30 Hz (i.e., frequency = 40 Hz), the piezoelectric PVDF sensor does not have enough time to transmit the charges generated from the bending movement in the positive x direction (forward); these charges are reversed by the recovery movement in the negative x direction (backward).
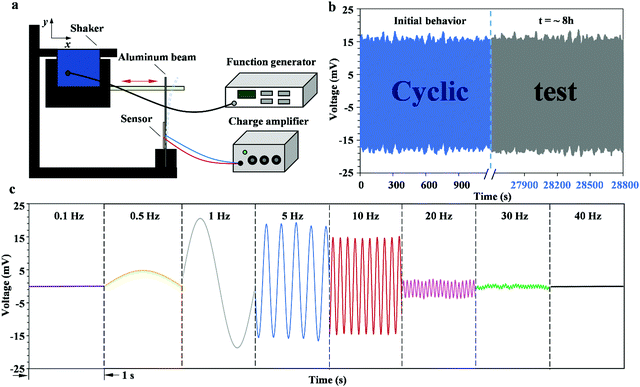 |
| Fig. 3 Cantilever bending test at different frequencies actuated by a shaker. (a) Schematic of the cantilever bending test setup. (b) Durability test for a polarized printed PVDF film sensor (R = 4) by continuous bending at 5 Hz for 1 44 000 cycles. The voltage generated in 1200 s intervals at the beginning and after 8 h. (c) Voltage generated by a polarized printed piezoelectric PVDF sensor (R = 4) at different actuating frequencies of 0.1, 0.5, 1, 5, 10, 20, 30 and 40 Hz. | |
Application #2: compression sensing application
The schematic of the compression test setup is shown in Fig. 4a. During the test, the compression head goes down by 0.033, 0.056, 0.079, 0.101, 0.129, 0.159, 0.206 and 0.234 mm to reach the maximum compressive force of 100, 200, 300, 400, 500, 600, 700 and 800 N, respectively. The voltage curves of the printed piezoelectric PVDF sensor under the compressive force between 0 to 700 N during a 1 s interval are shown in Fig. 4b. The PVDF films rupture when the load is equal to or greater than 800 N. As the compressive force increases, it takes a longer time for the voltage signal to go back to zero. Fig. 4c depicts a linear response of the PVDF film sensor voltage output for the force range between 0 and ∼700 N. The sensitivity of the sensor is ∼9.717 mV N−1. Then, we reversed the direction of the connection by switching the positive and negative wires on the piezoelectric sensor, and compressed the piezoelectric sensor with a load of 500 N. We observe that the direction of the voltage peak has been reversed, but the amplitude of two peaks is very close with a 0.8% difference, which confirms that the voltage comes from the piezoelectric sensor and not from the movement of the wires due to the change of the capacitance (Fig. 4d).
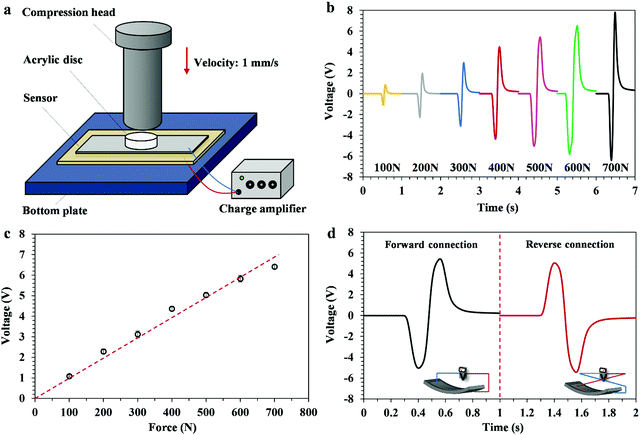 |
| Fig. 4 Compression test. (a) Schematic of the compression test setup. (b) Voltage curves during a 1 s period. (c) Maximum voltage generated by a 40 × 20 mm printed piezoelectric PVDF sensor (R = 4) under the maximum compressive forces of 100, 200, 300, 400, 500, 600 and 700 N. Error bars indicate the standard deviations obtained from three measurements. (d) Switching-polarity test: voltage generated during a 1 s period under the compression of 500 N using forward and reverse connections. | |
Application #3: “piezo leaves” for energy harvesting application
As shown in Fig. 5a, Four 40 × 20 × 0.06 mm printed polarized piezoelectric PVDF sensors (R = 4) are connected in parallel and glued on an FFF 3D printed PLA tree as energy harvesting “piezo leaves”. Fig. 5b shows a bridge-rectifier circuit used to convert the AC to DC to charge a 2.2 μF capacitor.52 In the energy harvesting test, we use a table fan to blow the “piezo leaves” (Fig. 5c). The distance between the fan and the PLA tree is 10 cm. As we turn on the table fan to the highest speed (motor speed = 1500 rpm), the “piezo leaves” are bent, thus generating electric current. We record the voltage reading of the capacitor on the multimeter every 30 sec. During a 3 min period of fan blowing, the “piezo leaves” are able to charge the capacitor from 0 to ∼2 V at a charging rate of ∼667 mV min−1. After we turn off the fan, the voltage drops gradually due to the intrinsic current leakage behavior of the capacitor (Fig. 5d). A 2.2 μF capacitor is selected in order to balance the current leakage rate and the charging rate. Larger capacitors have a higher charging rate but larger current leakage. The charges stored in the capacitor are further used to make a red LED bulb blink (ESI:† Movie S2). The number of “piezo leaves” and the amplitude of wind power have a significant effect on the charging rate. By calculation, ∼720 pieces of “piezo leaves” are required to light a LED continuously.
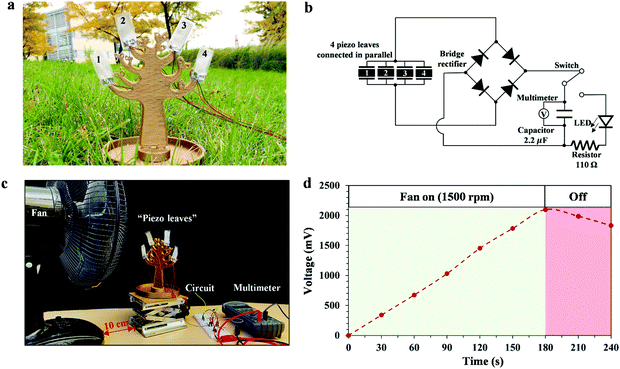 |
| Fig. 5 “Piezo leaves” energy harvester – Four PVDF films connected in parallel blown by a fan. (a) Photo of the four 40 × 20 mm printed piezoelectric PVDF sensors (R = 4) glued on an FFF 3D printed PLA tree. (b) Circuit diagram of the energy harvester: four “piezo leaves” connected in parallel generate AC, which is converted to DC by a bridge rectifier and stored in a capacitor to light a LED bulb. (c) Photo of the experimental setup: the wind energy from the fan is converted to electrical energy by four “piezo leaves” and the stored voltage in an energy harvesting circuit is read by a multimeter. (d) Voltage of a 2.2 μF capacitor charged by the “piezo leaves” after the fan is turned on (1500 rpm) for 3 min and then turned off. | |
As shown in Fig. S5 (ESI†), the calculated power density of the four “piezo leaves” is ∼9.38 μW cm−3 at a resistance of 1 MΩ (although there is a small deformation under the wind), which is comparable to the power density of the PVDF related energy harvesters from other works.53–55
4. Conclusion
In summary, we have successfully optimized the stretching–poling post-treatment parameters to fabricate FFF printed piezoelectric PVDF films and tested them for frequency sensing, pressure sensing and energy harvesting applications. By tailoring the stretching and poling parameters, a piezoelectric coefficient of 7.29 pC N−1 and a fraction of β phase of 65% were obtained. We find that the stretching step is necessary for the generation of the piezoelectric β phase, while the poling step is required to align the randomly dispersed dipole moments. The d33 of the polarized printed PVDF films (R = 4; polarized at 80 °C, 30 V μm−1 for 60 min) fabricated in this work is ∼10–100 times higher than the reported values.32,33 We have successfully demonstrated that the fabricated PVDF films could be directly used in both d31 and d33 mode sensing applications, including frequency (0.5 to 30 Hz) and compression detection (0 to 700N). Moreover, the 2 V voltage generated and stored in a 2.2 μF capacitor through a 3 min fan blowing of four printed PVDF films connected in parallel could make a LED bulb blink. In future work, to further enhance the piezoelectric charge coefficient of the 3D printed piezoelectric films, high piezoelectric ceramic fillers can be incorporated into the pure PVDF filament as a piezoelectric composite filament. The obtained piezoelectric coefficient will be the sum of the PVDF polymer matrix and the ceramic fillers. In addition, the stretching step is essential to enhance the β phase content in PVDF to achieve better piezoelectric performance, however, it limits the complexity of the manufacturable structures. In our future work, we will show the use of the FFF 3D printing technique to fabricate geometrically optimized true 3D piezoelectric composite devices. The present work is the foundation of our future work with the goal of showing the upper limit of piezoelectric performance that we can achieve in the FFF 3D printed PVDF films. Also, we plan to utilize a multi-material FFF 3D printing technique for the fabrication of piezoelectric sensors with electrodes in a single step. This multi-material 3D printing technique will offer a facile way to create piezoelectric devices without the need for post-metallization. We believe that FFF 3D printed piezoelectric devices would find enormous applications in sensing and energy harvesting fields.
Author contributions
This manuscript was written through contributions from all authors. All authors have given approval to the final version of the manuscript.
Conflicts of interest
There are no conflicts to declare.
Acknowledgements
The authors acknowledge support from the National Science and Engineering Research Council (NSERC), the Discovery program (#RGPIN-4566-2018) and the Department of National Defence (DND) (Grant#: DGDND-2018-00011). Ms Rui Tao and Mr Jiahao Shi acknowledge the financial support received from the China Scholarship Council (CSC). The authors are thankful for the instrument and the lab access kindly provided by Prof. Frédérick Gosselin, Prof. Stéphane Étienne, Prof. Annie Ross, and Prof. Abdellah Ajji at Polytechnique Montreal. The authors would like to especially thank technicians Mr Yanik Landry-Ducharme, Mr Bénédict Besner, Mr Nour Aimene, Mr Robert Delisle, and research associates Mr Matthieu Gauthier and Mr Richard Silverwood for the technical support, as well as Dr Rouhollah Farahani, Dr Kambiz Chizari and Dr Shibo Zou for technical advice.
References
- Z. Wang, X. Yuan, J. Yang, Y. Huan, X. Gao, Z. Li, H. Wang and S. Dong, 3D-Printed Flexible, Ag-Coated PNN-PZT Ceramic-Polymer Grid-Composite for Electromechanical Energy Conversion, Nano Energy, 2020, 73(March), 104737 CrossRef CAS.
- S. Bodkhe, G. Turcot, F. P. Gosselin and D. Therriault, One-Step Solvent Evaporation-Assisted 3D Printing of Piezoelectric PVDF Nanocomposite Structures, ACS Appl. Mater. Interfaces, 2017, 9(24), 20833–20842 CrossRef CAS PubMed.
- X. Lu, H. Qu and M. Skorobogatiy, Piezoelectric Micro- and Nanostructured Fibers Fabricated from Thermoplastic Nanocomposites Using a Fiber Drawing Technique: Comparative Study and Potential Applications, ACS Nano, 2017, 11(2), 2103–2114 CrossRef CAS PubMed.
- Z. Huo, X. Wang, Y. Zhang, B. Wan, W. Wu, J. Xi, Z. Yang, G. Hu, X. Li and C. Pan, High-Performance Sb-Doped p-ZnO NW Films for Self-Powered Piezoelectric Strain Sensors, Nano Energy, 2020, 73(February), 104744 CrossRef CAS.
- X. Wang, X. He, H. Zhu, L. Sun, W. Fu, X. Wang, L. C. Hoong, H. Wang, Q. Zeng, W. Zhao, J. Wei, Z. Jin, Z. Shen, J. Liu, T. Zhang and Z. Liu, Subatomic Deformation Driven by Vertical Piezoelectricity from CdS Ultrathin Films, Sci. Adv., 2016, 2(7), 1–10 Search PubMed.
- Y. Wu, J. K. Yim, J. Liang, Z. Shao, M. Qi, J. Zhong, Z. Luo, X. Yan, M. Zhang, X. Wang, R. S. Fearing, R. J. Full and L. Lin, Insect-Scale Fast Moving and Ultrarobust Soft Robot, Sci. Rob., 2019, 4(32), 1594–1603 CrossRef PubMed.
- N. Li, Z. Yi, Y. Ma, F. Xie, Y. Huang, Y. Tian, X. Dong, Y. Liu, X. Shao, Y. Li, L. Jin, J. Liu, Z. Xu, B. Yang and H. Zhang, Direct Powering a Real Cardiac Pacemaker by Natural Energy of a Heartbeat, ACS Nano, 2019, 13(3), 2822–2830 CrossRef CAS PubMed.
- Y. Zhang, C. R. Bowen, S. K. Ghosh, D. Mandal, H. Khanbareh, M. Arafa and C. Wan, Ferroelectret Materials and Devices for Energy Harvesting Applications, Nano Energy, 2019, 57, 118–140 CrossRef CAS.
- J. Shi and A. H. Akbarzadeh, Architected Cellular Piezoelectric Metamaterials: Thermo-Electro-Mechanical Properties, Acta Mater., 2019, 163, 91–121 CrossRef CAS.
- J. Shi and A. H. Akbarzadeh, 3D Hierarchical Lattice Ferroelectric Metamaterials, Int. J. Eng. Sci., 2020, 149, 103247 CrossRef CAS.
- W. Kim, S. Pyo, M. O. Kim, Y. Oh, D. S. Kwon and J. Kim, Humidity-Resistant Triboelectric Energy Harvester Using Electrospun PVDF/PU Nanofibers for Flexibility and Air Permeability, Nanotechnology, 2019, 30(27), 275401 CrossRef CAS PubMed.
- A. S. Fiorillo, S. A. Pullano, M. G. Bianco, C. D. Critello and U. S. Bioinspired, Sensor for Broadband Applications, Sens. Actuators, A, 2019, 294, 148–153 CrossRef CAS.
- E. Ghafari, X. Jiang and N. Lu, Surface Morphology and Beta-Phase Formation of Single Polyvinylidene Fluoride (PVDF) Composite Nanofibers, Adv. Compos. Hybrid Mater., 2018, 1(2), 332–340 CrossRef CAS.
- S. Sarkar, S. Garain, D. Mandal and K. K. Chattopadhyay, Electro-Active Phase Formation in PVDF-BiVO4 Flexible Nanocomposite Films for High Energy Density Storage Application, RSC Adv., 2014, 4(89), 48220–48227 RSC.
- G. H. Kim, S. M. Hong and Y. Seo, Piezoelectric Properties of Poly(Vinylidene Fluoride) and Carbon Nanotube Blends: β-Phase Development, Phys. Chem. Chem. Phys., 2009, 11(44), 10506–10512 RSC.
- M. El Achaby, F. Z. Arrakhiz, S. Vaudreuil, E. M. Essassi and A. Qaiss, Piezoelectric β-Polymorph Formation and Properties Enhancement in Graphene Oxide - PVDF Nanocomposite Films, Appl. Surf. Sci., 2012, 258(19), 7668–7677 CrossRef CAS.
- N. Soin, P. Zhao, K. Prashanthi, J. Chen, P. Ding, E. Zhou, T. Shah, S. C. Ray, C. Tsonos, T. Thundat, E. Siores and J. Luo, High Performance Triboelectric Nanogenerators Based on Phase-Inversion Piezoelectric Membranes of Poly(Vinylidene Fluoride)-Zinc Stannate (PVDF-ZnSnO3) and Polyamide-6 (PA6), Nano Energy, 2016, 30(August), 470–480 CrossRef CAS.
- A. N. Arshad, M. H.-M. Wahid, M. Rusop, W. H.-A. Majid, R. H.-Y. Subban and M. D. Rozana, Dielectric and Structural Properties of Poly(Vinylidene Fluoride) (PVDF) and Poly(Vinylidene Fluoride-Trifluoroethylene) (PVDF-TrFE) Filled with Magnesium Oxide Nanofillers, J. Nanomater., 2019, 2019, 5961563 Search PubMed.
- A. Salimi and A. A. Yousefi, FTIR Studies of β-Phase Crystal Formation in Stretched PVDF Films, Polym. Test., 2003, 22(6), 699–704 CrossRef CAS.
- H. Luo, Y. Huang and D. Wang, The Crystallization and Crystal Transition of PVDF in PAN Nano-Tube, Polymer, 2013, 54(17), 4710–4718 CrossRef CAS.
- R. Gregorio and E. M. Ueno, Effect of Crystalline Phase, Orientation and Temperature on the Dielectric Properties of Poly (Vinylidene Fluoride) (PVDF), J. Mater. Sci., 1999, 34(18), 4489–4500 CrossRef CAS.
- V. Sencadas, V. M. Moreira, S. Lanceros-Mendéz, A. S. Pouzada and R. Gregório, α - To - β Transformation on PVDF Films Obtained by Uniaxial Stretch, Mater. Sci. Forum, 2006, 514–516(PART 2), 872–876 CAS.
- N. Jahan, F. Mighri, D. Rodrigue and A. Ajji, Effect of the Inflation Strategy on the Piezoelectric Response of Cellular Poly(Vinylidene Fluoride) Ferroelectret, J. Appl. Polym. Sci., 2019, 136(20), 47540 CrossRef.
- X. Ren, N. Meng, H. Zhang, J. Wu, I. Abrahams, H. Yan, E. Bilotti and M. J. Reece, Giant Energy Storage Density in PVDF with Internal Stress Engineered Polar Nanostructures, Nano Energy, 2020, 72(February), 104662 CrossRef CAS.
- Z. X. Huang, M. M. Wang, Y. H. Feng and J. P. Qu, β-Phase Formation of Polyvinylidene Fluoride via Hot Pressing under Cyclic Pulsating Pressure, Macromolecules, 2020, 53(19), 8494–8501 CrossRef CAS.
- H. Tao and J. Wu, New Poling Method for Piezoelectric Ceramics, J. Mater. Chem. C, 2017, 5(7), 1601–1606 RSC.
- H. Guo, C. Ma, X. Liu and X. Tan, Electrical Poling below Coercive Field for Large Piezoelectricity, Appl. Phys. Lett., 2013, 102(9), 6–10 Search PubMed.
- T. Granzow, A. B. Kounga, E. Aulbach and J. Rödel, Electromechanical Poling of Piezoelectrics, Appl. Phys. Lett., 2006, 88(25), 252907 CrossRef.
- C. Ribeiro, D. M. Correia, S. Ribeiro, V. Sencadas, G. Botelho and S. Lanceros-Méndez, Piezoelectric Poly(Vinylidene Fluoride) Microstructure and Poling State in Active Tissue Engineering, Eng. Life Sci., 2015, 15(4), 351–356 CrossRef CAS.
- A. Kumar, V. V. Bhanu Prasad, K. C. James Raju and A. R. James, Optimization of Poling Parameters of Mechanically Processed PLZT 8/60/40 Ceramics Based on Dielectric and Piezoelectric Studies, Eur. Phys. J. B, 2015, 88(11), 287–296 CrossRef.
- E. Nilsson, A. Lund, C. Jonasson, C. Johansson and B. Hagström, Poling and Characterization of Piezoelectric Polymer Fibers for Use in Textile Sensors, Sens. Actuators, A, 2013, 201, 477–486 CrossRef CAS.
- D. A. Porter, T. V.-T. Hoang and T. A. Berfield, Effects of In-Situ Poling and Process Parameters on Fused Filament Fabrication Printed PVDF Sheet Mechanical and Electrical Properties, Addit. Manuf., 2017, 13, 81–92 CAS.
- H. Kim, F. Torres, Y. Wu, D. Villagran, Y. Lin and T.-L. Tseng, Integrated 3D Printing and Corona Poling Process of PVDF Piezoelectric Films for Pressure Sensor Application, Smart Mater. Struct., 2017, 26(8), 085027 CrossRef.
- H. Cui, R. Hensleigh, D. Yao, D. Maurya, P. Kumar, M. G. Kang, S. Priya and X. Zheng, Three-Dimensional Printing of Piezoelectric Materials with Designed Anisotropy and Directional Response, Nat. Mater., 2019, 18(3), 234–241 CrossRef CAS PubMed.
- H. Kim, T. Fernando, M. Li, Y. Lin and T. L.-B. Tseng, Fabrication and Characterization of 3D Printed BaTiO3/PVDF Nanocomposites, J. Compos. Mater., 2018, 52(2), 197–206 CrossRef CAS.
- C. Lee and J. A. Tarbutton, Electric Poling-Assisted Additive Manufacturing Process for Lead-Free Piezoelectric Device Fabrication, Procedia Manuf., 2015, 1, 320–326 Search PubMed.
- H. Wei, X. Cauchy, I. O. Navas, Y. Abderrafai, K. Chizari, U. Sundararaj, Y. Liu, J. Leng and D. Therriault, Direct 3D Printing of Hybrid Nanofiber-Based Nanocomposites for Highly Conductive and Shape Memory Applications, ACS Appl. Mater. Interfaces, 2019, 11(27), 24523–24532 CAS.
- Q. Wu, S. Zou, F. P. Gosselin, D. Therriault and M. C. Heuzey, 3D Printing of a Self-Healing Nanocomposite for Stretchable Sensors, J. Mater. Chem. C, 2018, 6(45), 12180–12186 RSC.
- S. Zou, D. Therriault and F. P. Gosselin, Spiderweb-Inspired, Transparent, Impact-Absorbing Composite, Cell Rep. Phys. Sci., 2020, 1(11), 100240 CrossRef.
- M. Ataur Rahman, B. C. Lee, D. T. Phan and G. S. Chung, Fabrication and Characterization of Highly Efficient Flexible Energy Harvesters Using PVDF-Graphene Nanocomposites, Smart Mater. Struct., 2013, 22(8), 085017 CrossRef.
- A. Salimi and A. A. Yousefi, Conformational Changes and Phase Transformation Mechanisms in PVDF Solution-Cast Films, J. Polym. Sci., Part B: Polym. Phys., 2004, 42(18), 3487–3495 CrossRef CAS.
- E. Brunengo, M. Castellano, L. Conzatti, G. Canu, V. Buscaglia and P. Stagnaro, PVDF-Based Composites Containing PZT Particles: How Processing Affects the Final Properties, J. Appl. Polym. Sci., 2020, 137(20), 1–8 CrossRef.
- J. Y. Lyu, S. Chen, W. He, X. X. Zhang, D. Y. Tang, P. J. Liu and Q. L. Yan, Fabrication of High-Performance Graphene Oxide Doped PVDF/CuO/Al Nanocomposites via Electrospinning, Chem. Eng. J., 2019, 368(November 2018), 129–137 CrossRef CAS.
- M. S. Sorayani Bafqi, R. Bagherzadeh and M. Latifi, Fabrication of Composite PVDF-ZnO Nanofiber Mats by Electrospinning for Energy Scavenging Application with Enhanced Efficiency, J. Polym. Res., 2015, 22(7), 1–9 CAS.
- B. S. Lalia, E. Guillen-Burrieza, H. A. Arafat and R. Hashaikeh, Fabrication and Characterization of Polyvinylidenefluoride-Co-Hexafluoropropylene (PVDF-HFP) Electrospun Membranes for Direct Contact Membrane Distillation, J. Membr. Sci., 2013, 428, 104–115 CrossRef CAS.
- Commercial piezoelectric PVDF film. https://piezopvdf.com/piezoelectric-poled-pvdf-film-d31/.
- H. Pei, Y. Xie, Y. Xiong, Q. Lv and Y. Chen, A Novel Polarization-Free 3D Printing Strategy for Fabrication of Poly (Vinylidene Fluoride) Based Nanocomposite Piezoelectric Energy Harvester, Composites, Part B, 2021, 225(July), 109312 CrossRef CAS.
- X. Liu, Y. Shang, J. Zhang and C. Zhang, Ionic Liquid-Assisted 3D Printing of Self-Polarized β-PVDF for Flexible Piezoelectric Energy Harvesting, ACS Appl. Mater. Interfaces, 2021, 13(12), 14334–14341 CrossRef CAS PubMed.
- P. H. Ducrot, I. Dufour and C. Ayela, Optimization of PVDF-TrFE Processing Conditions for the Fabrication of Organic MEMS Resonators, Sci. Rep., 2016, 6(January), 1–7 Search PubMed.
- B. Jaleh and A. Jabbari, Evaluation of Reduced Graphene Oxide/ZnO Effect on Properties of PVDF Nanocomposite Films, Appl. Surf. Sci., 2014, 320, 339–347 CrossRef CAS.
-
J. X.-J. Zhang and K. Hosshino. Molecular Sensors and Nanodevices, 2014 Search PubMed.
- Building a Piezoelectric Generator. https://www.Teachengineering.Org/Activities/View/Uoh_piezo_lesson01_activity1.
- J. Fu, Y. Hou, X. Gao, M. Zheng and M. Zhu, Highly Durable Piezoelectric Energy Harvester Based on a PVDF Flexible Nanocomposite Filled with Oriented BaTi2O5 Nanorods with High Power Density, Nano Energy, 2018, 52(August), 391–401 CrossRef CAS.
- S. K. Karan, R. Bera, S. Paria, A. K. Das, S. Maiti, A. Maitra and B. B. Khatua, An Approach to Design Highly Durable Piezoelectric Nanogenerator Based on Self-Poled PVDF/AlO-RGO Flexible Nanocomposite with High Power Density and Energy Conversion Efficiency, Adv. Energy Mater., 2016, 6(20), 1–12 Search PubMed.
- B. Sun, X. Li, R. Zhao, H. Ji, J. Qiu, N. Zhang, D. He and C. Wang, Electrospun Poly(Vinylidene Fluoride)-Zinc Oxide Hierarchical Composite Fiber Membrane as Piezoelectric Acoustoelectric Nanogenerator, J. Mater. Sci., 2019, 54(3), 2754–2762 CrossRef CAS.
|
This journal is © The Royal Society of Chemistry 2022 |
Click here to see how this site uses Cookies. View our privacy policy here.