DOI:
10.1039/D2GC02185D
(Communication)
Green Chem., 2022,
24, 7874-7882
Sustainability and efficiency assessment of vanillin allylation: in solution versus ball-milling†
Received
9th June 2022
, Accepted 27th September 2022
First published on 29th September 2022
Abstract
Allylation of phenols, a widely used reaction in multistep synthetic pathways, was herein investigated using mechanochemistry. This synthesis was first optimized on vanillin by varying key parameters including both chemical (e.g., stoichiometry, reaction time) and mechanical (e.g., rotational speed, material, size and number of beads, liquid additive) conditions, leading to the isolation of allylated vanillin at the gram scale in excellent yield (95%). The optimized procedure was also successfully implemented to another bio-based phenol of interest, ethyl ferulate (92% isolated yield). The environmental impact of these procedures was compared with more classical in-solution protocols by calculating E factors. When work-up solvents were not taken into account, E factor (sEF) clearly indicated the superiority of the ball-milling approach over the solution-based procedure, underscoring the capacity of ball-mills to drastically reduce the need for “reaction” solvents. On the other hand, when work-up solvents were taken into consideration, E factors (cEF) were in favor of the solvent-based approach, which could be explained by the solvent quantities required to recover the reaction mixture from the ball-mill reactor. Overall, these results highlight (i) the great potential of mechanochemistry to enable the development of both efficient and waste-less allylation of lignin-derived phenolic synthons, and (ii) the need to study higher-scale and continuous mechanochemical processes, such as by using extruders, to further improve efficiency and sustainability of such mechanochemical processes.
Introduction
Composed of p-hydroxyphenylpropanoids units, lignins are a natural and abundant polyphenolic resource that is gaining more and more interest and value in the chemical industry. Indeed, lignins can be used as macromolecular polyols1 or (bio)-catalytically depolymerized to prepare monophenolics such as vanillin, syringaldehyde, or 4-hydroxyphenyl ethanol.2 Among the various phenolics that can be readily obtained from lignins, vanillin is probably the most promising, by being mainly produced from the hydrolysis–oxidation of lignosulfonate coming from paper industries. In order to meet the world demand for vanillin, 15% of the general production comes from this lignosulfonate revalorization which would have been burned otherwise.3–5 These renewable phenolics constitute a great source of valuable synthons for the production of bio-based alternatives to petroleum-based phenolic/aromatic bioactive compounds – such as antioxidants,6 UV filters,7–13 monomers and corresponding polymers.3
In the literature, many groups – including URD ABI – have reported several works on the use of vanillin14 and p-hydroxycinnamate esters (e.g., ethyl ferulate15,16 and ethyl sinapate17,18) as bio-based synthons for the synthesis of poly-epoxidized phenolics as a sustainable and non-toxic alternative to endocrine disruptive bisphenol A (BPA). So far, the epoxidation process used to access these BPA substitutes involved epichlorohydrin. To circumvent the use of this chlorinated reagent, pioneer work on the use of a two-step allylation/lipase-catalyzed epoxidation demonstrated that one could replace epichlorohydrin-based glycidylation to synthesize epoxides from phenols such as vanillin.19 Building on this finding, we decided to green up this strategy further through the use of mechanochemical allylation.
Allylation is an easy and quick reaction to functionalize hydroxylic group with a reactive and versatile double bound, which is widely used in multistep synthetic pathways. The first group that applied allylation on vanillin was Ayer et al. in 1991 (Scheme 1, first step), to synthesize a molecule inhibiting the growth of pathogens.20 Then, Detterbeck et al. used it to create hydroxylated aryldihydrobenzofuran systems as key structures to obtain natural compounds.21 Later on, Breloy et al., who aimed to develop a green vanillin-based photoinitiator for free-radical polymerization of an acrylate monomer, performed vanillin allylation to avoid radical side reactions on phenols during polymerization.22 Still in the polymer field, Han et al. carried out the allylation of vanillin to ease the curing of a phtalonitrile resin.23 Willing to enhance the bioactivity of vanillin-based chalcones, Sharma et al. also implemented this allylation step.24 It is noteworthy to mention that some researchers, such as Yu et al., took advantage of the resulting allyloxy group to perform Claisen rearrangement (Scheme 1, second step).25
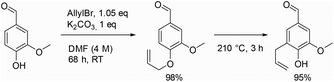 |
| Scheme 1 Allylation in solution20 followed by Claisen rearrangement.25 | |
Generally, allylation of vanillin is carried out in solution in organic solvents, such as DMF, acetone or ethanol, in the presence of potassium carbonate as a base. Although these reaction conditions allow the isolation of allylated vanillin in high yields, they also present some drawbacks such as the toxicity and the quantities of the solvent used,26 long reaction times or the need to perform the reaction at relatively high temperature (such as in refluxing EtOH or acetone). Due to the critical importance of vanillin and other renewable phenolic compounds (e.g., ethyl ferulate) as well as their allylated counterpart, the development of efficient and sustainable allylation conditions is of high interest.
Based on previous successes in the field,27–29 we therefore envisaged using mechanochemistry to produce allylated phenols. Mechanochemistry can be defined as the field of science that studies chemical transformations facilitated by mechanical energy.30 It has been demonstrated in many cases that mechanochemistry allows the development of more efficient and sustainable alternatives to the processes classically performed in solution.31 Mechanochemical allylation of vanillin was therefore attempted by milling vanillin with K2CO3 and allyl bromide.
Results and discussion
Mechanochemical allylation of vanillin
Optimization of reaction conditions by planetary ball-milling.
At first, 143.7 mg of vanillin were reacted with 130.6 mg of K2CO3 (1.0 eq.) in a 20 mL reactor made of zirconium oxide (noted ZrO2) containing 80 beads of the same material (5 mm diameter). After 5 min milling at 850 rpm in a planetary ball-mill, 90.4 μL of allyl bromide (1.1 eq.) were added to the reactor and the reaction mixture was agitated at 850 rpm. After 1 h of milling, an HPLC analysis of the crude revealed that ∼37% of vanillin was allylated (Table 1, entry 1). Here, the number of parameters that could be optimized being quite large (mechanical parameters adding to the chemical ones), performing a Design of Experiments (DoE) and Response Surface Methodology (RSM) was not adopted.32 It was thus decided to implement classic One Variable At a Time (OVAT) approach to optimize the mechanochemical allylation of vanillin. Before studying and optimizing the mechanical parameters, it was decided to first investigate the chemical parameters and more specifically, the reaction time and the excess of allyl bromide, which is a liquid at ambient temperature (Table 1). Indeed, it is widely known in mechanochemistry that adding small amounts of a liquid can dramatically influence the course of the reaction. This technique, called Liquid-Assisted Grinding (LAG), is often used to increase the homogeneity of the reaction mixture but also to accelerate and control the selectivity of a reaction.33–35 To quantify LAG solvent added in the bulk, the η value was defined in the literature as the liquid volume added per total mass of reagents.36 In this work, η will be calculated based on the total mass of the following reagents: phenol, potassium carbonate and allyl bromide.
Table 1 Optimization of the chemical parameters for the allylation of vanillin
In our case, it was expected that allyl bromide could both play the role of a reactant and of a beneficial liquid additive. Therefore, the quantity of allyl bromide was increased to 1.5 and 4.0 equivalents (Table 1, entries 2 and 3). Counterintuitively, increasing the equivalents of allyl bromide did not favor the conversion of vanillin towards allylated vanillin. On the opposite, the yield dropped down to ∼28% when using 4.0 equivalents of allyl bromide, while no other side products could be detected (Table 1, entry 3). Similar tendency was observed when the reaction time was increased to 3 hours (Table 1, entries 4–6). This confirmed that the deleterious effect of allyl bromide as a liquid additive was stronger than the positive effect that would have been expected from increasing the excess of this reactant. It was hypothesized here that the excess of allyl bromide led to a less homogeneous distribution of the reactants, which is essential in solvent-free synthesis and could explain the lower yields. Additionally, increasing the reaction time did not significantly improve the yield, neither led to the formation of side products, whatever the excess of allyl bromide used (Table 1, entries 4–6). Finding a suitable liquid additive was thus the next step of this study. Ten polar aprotic solvents and EtOH, which is a commonly used solvent for allylation, were then tested as liquid additives: acetone, EtOAc, anisole, dimethyl carbonate, DMF, DMSO, diethyl malonate, acetonitrile, Cyrene® and γ-valerolactone (Table 2). Vanillin and K2CO3 were first milled for 5 min before allyl bromide and the liquid additive were added and milled.
Table 2 Liquid additive screening for the mechanical allylation of vanillin
Among the different liquid additives tested, DMF allowed for the highest yield (79%, Table 2, entry 6) while the use of diethyl malonate and DMSO provided the lowest (12% and 14%, respectively, Table 2, entries 7 & 8). DMF is a widespread and efficient solvent for many chemical processes, yet its toxicity is an incentive for the development of safer and more sustainable alternatives.37–39 Among the solvents commonly recognized as more sustainable (i.e., ethanol, acetone, EtOAc, anisole, dimethyl carbonate),40 yields unfortunately did not exceed 40% (Table 2, entries 1 to 5). Yields obtained with other alternative solvents (acetonitrile, Cyrene® and γ-valerolactone) did not provide better results (Table 2, entries 9 to 11). Of note, the low yield in the case of Cyrene® could be explained by its capacity to undergo K2CO3-mediated deprotonation and subsequent homo-oligomerization through Michael-addition, aldol condensation or allylation.41 Well-aware that DMF is not the ideal liquid additive because of its reproductive toxicity, reducing its concentration from 0.2 μL mg−1 to 0.1 μL mg−1 was attempted (Table 2, entry 12). Unfortunately, this resulted in a decrease in yield from 79% to 48% (Table 2, entries 6 vs. 12). By combining the aforementioned optimized parameters (i.e., 1.5 eq. of allyl bromide and 0.2 μL of DMF as LAG), while increasing the milling time to 3 hours, the yield reached 98% (Table 2, entry 13).
In parallel with the optimization of the chemical parameters, the influence of the mechanical parameters on the yield was studied: quantity, diameter and material of beads (Table 3), as well as rotational speed (Table 4). Indeed, such parameters will influence on the energy transferred to the reaction mixture, and hence on the course of the reaction. For instance, under otherwise equal conditions, beads made of a dense material, such as stainless steel (ρstainless
steel = 7.8 g cm−3), will provide more energy to the system on every impact than a less dense material, such as ZrO2 (ρzirconium
oxide = 5.9 g cm−3). In total, three diameters and two materials were tested (i.e., 3, 5 or 10 mm diameter beads made of ZrO2 or stainless steel) (Table 3). As a reminder, using 5 mm ZrO2 beads without any liquid additive provided allylated vanillin with a yield of ∼37% after 1 h of milling (Table 1, entry 1). Changing the material of the beads and reactor to stainless steel, while keeping other parameters constant, slightly reduced the yield to 32% (Table 3, entry 1). Using larger stainless steel beads (10 mm diameter) also reduced the yield to 20% (Table 3, entry 2), yet smaller 3 mm beads increased the yield to 40% (Table 3, entry 3). The same tendency was observed with ZrO2 beads: yield decreased to 23% with 10 mm diameter beads (Table 3, entry 4 vs.Table 1, entry 1) and increased to 42% with 3 mm diameter beads (Table 3, entry 5 vs.Table 1, entry 1).
Table 3 Influence of size and number of beads for the mechanical allylation of vanillin
Table 4 Influence of the rotational speed on the allylation of vanillin by planetary ball-milling
Entrya |
LAG |
Allyl bromide equivalents |
Speed (rpm) |
Yieldb (%) |
Vanillin: K2CO3 1 : 1, reaction time: 1 h, 20 mL ZrO2 reactor, 80 ZrO2 beads (32 g, d = 5 mm).
Estimated based on the surface areas of the peaks visible on the HPLC chromatograms. No side products could be detected in any of the experiments performed. Yields are presented as an average of three samples taken at three different spots of the reaction mixture. The standard deviation therefore represents the homogeneity of the distribution of the reactants and products in the reaction mixture.
η is defined as the volume of liquid additive over the total mass of reactants.36 It is expressed in μL mg−1.
|
1 |
No LAG |
1.1 |
600 |
19 ± 2 |
2 |
DMF η = 0.2c |
1.5 |
600 |
55 ± 5 |
3 |
DMF η = 0.2c |
1.5 |
850 |
93 ± 2 |
Another parameter allowing to easily modulate the induced mechanical energy is the rotational speed. Without any liquid additive, lowering the frequency to 600 rpm decreased the yield down to 19% (Table 4, entry 1 vs. ∼37% in Table 1 entry 1). Adding DMF as a liquid additive (η = 0.2 μL mg−1) and increasing the excess of allyl bromide to 1.5 equivalents led to a better yield of 55% (Table 4, entry 2). Yet, the highest yield (93%) was obtained when running the reaction with a rotational speed of 850 rpm, the maximal acceptable rotational speed for our equipment (Table 4, entry 3). The latter results showed that lowering this parameter did not improve the yield, suggesting that higher-energy reaction conditions were needed here.
After having varied the different parameters of the reaction individually from each other (stoichiometry, reaction time, material of reactors, quantity, material and size of beads, as well as rotational speed), the allylation was performed using the optimal conditions (i.e., 1.5 eq. of allyl bromide, DMF η = 0.2 μL mg−1, 20 mL ZrO2 reactor, 32 g of 3 mm ZrO2 beads, 3 h, 850 rpm) leading to a quantitative conversion of vanillin. After recovery of the reaction mixture from the reactor with EtOAc, water and 1 M NaOH aqueous solution, the aqueous phase was extracted with EtOAc. Combined organic layers were dried, filtered and concentrated to furnish pure allylated vanillin in 87% isolated yield.
Comparison with reaction in solution.
To evaluate the advantages brought by the aforementioned mechanochemical conditions compared to those in solution, an allylation reaction was performed in solution under classical stirring by using DMF as a solvent.22 The reaction was conducted at 50 °C with the minimal volume of DMF required to obtain a homogeneous solution under stirring, which corresponded to a η ratio of 0.84 μL mg−1 in these conditions. The temperature of the reaction was set at 50 °C to be as close as possible to the milling conditions (50 °C was the temperature of the reaction medium in the ball-mill right after milling was stopped in the best conditions described in the previous paragraph). Like in ball-milling conditions, a complete conversion was attained after 3 h of reaction and the allylated vanillin was isolated in 86% yield (87% isolated yield for ball-milling conditions). Yet, one can highlight that, under these solution-based conditions, the amount of DMF reached more than 4 times the amount required under ball-milling (η = 0.84 μL mg−1 in solution vs. η = 0.2 μL mg−1 for ball-milling).
Mechanochemical allylation of ethyl ferulate
The allylation of vanillin being successful by using ball-milling, it was decided to apply these conditions to ethyl ferulate, a naturally occurring synthon of interest that has been used for the synthesis of renewable compounds such as non-toxic alternatives to endocrine disruptive bisphenol A.6,16 At first, 180 mg of ethyl ferulate was reacted with 112 mg of K2CO3 (1.0 eq.) in a 20 mL ZrO2 reactor containing 80 beads of the same material (5 mm diameter). As for vanillin, after 5 min milling at 850 rpm, 77.6 μL of allyl bromide (1.1 eq.) were added to the reactor and the reaction mixture was agitated at 850 rpm. After 3 h of milling, an HPLC analysis of the crude revealed that 49% of ethyl ferulate was allylated (Table 6, entry 1).
In the same conditions, only ∼37% of vanillin was allylated (Table 1, entry 1), thus demonstrating a better reactivity of ethyl ferulate compared to vanillin in these conditions. As for vanillin in the same conditions (Table 1, entry 5), increasing the excess of allyl bromide to 1.5 equivalents and the milling time to 3 hours did not significantly improve the yield (50%, Table 5, entry 2). Yet when DMF was used as a liquid additive (η = 0.2 μL mg−1), ethyl ferulate was converted almost quantitatively (97% yield, Table 5, entry 3). After work-up, allylated ethyl ferulate was isolated with 82% yield. Of note, allylated vanillin is a liquid in our reaction conditions. On the opposite, allylated ethyl ferulate is a solid. Gratifyingly, in these reaction conditions, yield does not seem to be influenced by the physical states of the reactants and products. Although it is known that “hot spots” can be generated during milling, it is worth mentioning that, in our reaction conditions, no trace of the thermally-favored Claisen rearrangement product (Scheme 1, second step) was detected neither for vanillin nor for ethyl ferulate.
Table 5 Mechanochemical allylation of ethyl ferulate
Scale-up and benchmarking
This mechanochemical allylation reaction was further studied at a higher scale. For this, a Retsch PM100 planetary ball-mill equipped with a 250 mL stainless steel reactor containing ∼2080 stainless steel beads (3 mm diameter) was utilized (instead of the Fritsch P7 and 20 mL ZrO2 reactor). Thus, 1.61 g of vanillin produced 1.94 g of allylated vanillin (95% isolated yield, Scheme 2) after having been milled for 3 h at 400 rpm in the 250 mL reactor. Following a similar procedure, 2.05 g of ethyl ferulate furnished 2.24 g of allylated ethyl ferulate (92% isolated yield, Scheme 2).
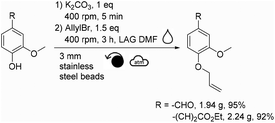 |
| Scheme 2 Mechanochemical allylation of vanillin and ethyl ferulate at the gram scale (for meaning of symbols please see ref. 30). | |
The efficiency and the environmental impact of the allylation of vanillin under mechanochemical and solution conditions were then compared (Table 6). As one cannot compare the sustainability of processes based only on their yields, the E factor was calculated for all selected procedures. E factor, which represents how many kg's of waste are produced for a kg of product, is nowadays largely accepted as a useful and simple measure to rapidly give an idea of the sustainability of a chemical reaction.3,42–44 Although many conditions describing the allylation of vanillin with K2CO3 and allyl bromide were reported in the literature, only the reaction conditions with the best yield and E factor are detailed in Table 6. As quantities of “work-up solvents” (such as those used for extraction, washing, crystallization or column chromatography) are not always indicated in publications, E factors were first calculated without taking them into account (corresponding E factor being identified as “simple E factor” and abbreviated “sEF”).42 Thus, here sEF will account for all reagents, products and “reaction” solvents, as opposed to “work-up” solvents. While DMF was the best liquid additive for the allylation of vanillin in a ball-mill (furnishing allylated vanillin in 95% isolated yield), less problematic solvents such as acetone and ethanol provided better yields when used under classical stirring conditions (100% and 98%, Table 6, entries 1 and 2, respectively).45,46 Yet these procedures presented sEF above 3, indicating that they produced more than 3 times the amount of waste than the amount of allylated vanillin. A lower sEF of only 2.47 could be obtained by Ayer et al. when using DMF as a solvent, albeit the reaction lasted 68 hours.20 Other research groups obtained allylated vanillin in shorter reaction times by using DMF, yet by running the reaction at higher temperatures (65 and 70 °C, Table 6, entries 4 and 5, respectively), and with higher sEF (5.46 and 5.51, entries 4 and 5, respectively).47,48 These differences led us to perform the vanillin allylation reaction with DMF as a solvent under classical stirring conditions while (i) trying to minimize as much as possible the amount of DMF, and (ii) keeping the same excesses of K2CO3 and allyl bromide as for the ball-milling conditions. In such conditions, allylated vanillin could be obtained in 86% yield after 3 hours of reaction at 50 °C in DMF, with a sEF of 4.09. When performing the allylation in a ball-mill by using DMF as a liquid additive, allylated vanillin was isolated in yields comparable to the previously described procedures in solution (87% and 95% isolated yields for ball-milling conditions, Table 6, entries 7 and 8, respectively; 86–100% yield range for reactions performed in solution). Yet, the ball-milling conditions enabled to reach the lowest sEF of 2.33 and 2.06, for the mg-scale and the gram-scale synthesis, respectively (Table 6, entries 7 and 8). Similar trend was also obtained for the allylation of ethyl ferulate, with sEF of 1.98 and 1.66, for the mg-scale and gram-scale respectively. Such results clearly highlight the capacity of ball-milling to drastically reduce the need for “reaction” solvent, while keeping overall efficiency (in terms of yield and reaction time). Although many publications do not mention the quantities of solvent used during work-up steps, the E factor taking into account these solvents (defined as “complete E factor” and abbreviated “cEF”) was calculated when possible.42 Thus, the procedure developed by Kevwitch et al. presented a cEF of 14 (Table 6, entry 5). In our hands, performing the allylation in solution in DMF at 50 °C resulted in a higher cEF of 91 (Table 6, entry 6). This significative difference can be explained by the difference in scale at which the reactions were performed. In our hands, 6.6 mmol of vanillin were engaged in the allylation reaction while 670.4 mmol were used in the procedure described by Kevwitch et al. Performing the reaction at such scale (more than 100 grams of vanillin were allylated) enabled to drastically minimize the work-up solvent quantities, which was not possible in our small scale reaction conditions. The same “scale effect” is visible when looking at the cEF values for the allylation reactions performed in the ball-mill: the mg-scale ball-mill procedure requires more work-up solvents (cEF = 268, Table 6, entry 7) than the one performed at the gram-scale (cEF = 124, Table 6, entry 8). Yet, our results show that, when performed at a similar scale, the ball-mill procedure uses more work-up solvents than the procedure in solution (Table 6, entry 8 vs. entry 6). A detailed analysis of these differences in cEF indicates that a large portion of the work-up solvents used in the ball-mill process corresponds to the amount of solvent required to recover the reaction mixture from the ball-mill reactor. Of note, such excess in work-up solvents could be easily avoided by using continuous mechanochemical equipment such as extruders.38,49
Table 6 Comparison of reaction conditions, yields and simple and complete E factors for the allylation of vanillin
Entry |
Author, year |
Solvent |
Reaction time (h) |
Temperature (°C) |
Scalea (mmol) |
Isolated yield (%) |
Simple E factor (sEF)b |
Complete E factor (cEF)c |
Number of mmol of vanillin involved in the reaction.
Work-up solvents were not taken into account in the calculation of the E factor.
Work-up solvents were taken into account in the calculation of the E factor.
n.a.: not applicable (information not available in the original publication, e.g. volume of solvent used for column chromatography purification).
Reaction run under ultrasonication.
370 ZrO2 beads (32 g, d = 3 mm) in a 20 mL ZrO2 reactor.
Temperature reached a maximum of ∼50 °C right after milling was stopped.
2080 stainless steel beads (180 g, d = 3 mm) in a 250 mL stainless steel reactor.
|
1 |
Srikrishna et al., 2007 45 |
Acetone |
5 |
Reflux |
16.4 |
100 |
3.61 |
n.a.d |
2 |
Hoffmann et al., 2014 46 |
Ethanol |
6 |
Reflux |
99.9 |
98 |
3.34 |
n.a.d |
3 |
Ayer et al., 1991 20 |
DMF |
68 |
RT |
80.2 |
99 |
2.47 |
n.a.d |
4e |
Chate et al., 2012 47 |
DMF |
1 |
65 |
6.6 |
92 |
5.46 |
n.a.d |
5 |
Kevwitch et al., 2012 48 |
DMF |
24 |
70 |
670.4 |
96 |
5.51 |
14 |
6 |
This work, in solution |
DMF |
3 |
50 |
6.6 |
86 |
4.09 |
91 |
7f |
This work, ball-milling at mg-scale |
DMF |
3 |
Self-heatingg |
0.8 |
87 |
2.33 |
268 |
8h |
This work, ball-milling at g-scale |
DMF |
3 |
Self-heating |
10.6 |
95 |
2.06 |
124 |
Conclusions
The present work demonstrates that mechanochemistry is a versatile and efficient method for the allylation of biobased phenols such as vanillin and ethyl ferulate. It is shown that mechanical parameters (i.e. rotational speed, material, size and number of beads, liquid additive) are as important as the chemical parameters (i.e. stoichiometry, reaction time). Both of them were examined for the allylation of vanillin and their effects on the yield were reported. For example the bead choice enabled to double the yield. Allylated products were isolated in high yields (vanillin: 87%, ethyl ferulate: 82%). Better results were obtained when the method was scaled-up to the gram scale furnishing allylated vanillin and allylated ethyl ferulate with 95% and 92% isolated yield, respectively. Finally, E factors were calculated and compared to results obtained in solution, taking into account the work-up solvents (cEF) or not (sEF). Thus, sEF values clearly highlighted the capacity of ball-milling to drastically reduce the need for “reaction” solvent. On the opposite, the solution strategy revealed better E factors values (cEF) when the work-up solvents were taken into account. A detailed analysis of these differences in cEF indicated that a large portion of the work-up solvents used in the ball-mill process corresponded to the amount of solvent required to recover the reaction mixture from the ball-mill reactor, which could be avoided by using continuous mechanochemical equipment such as extruders. Overall, these results highlight (i) the great potential of mechanochemistry to enable the development of both efficient and waste-less allylation of lignin-derived phenolic synthons and (ii) the need to study higher-scale and continuous mechanochemical processes, such as by using extruders, to further improve efficiency and sustainability of such mechanochemical processes.
Experimental section
Chemicals
Vanillin (99%), allyl bromide (99%) and potassium carbonate (99%) were all purchased from Sigma Aldrich. Ethyl ferulate was synthesized following the already reported procedure.2 Sodium hydroxide was purchased from Fischer Scientific. Cyrene® was graciously provided by Circa Group. All other solvents were obtained from VWR, Sigma Aldrich, Fischer Scientific and Alfa Aesar.
Materials
Small scale mechanochemical reactions were performed in a Fritsch Pulverisette 7 premium line planetary ball-mill with 20 mL inner-volume reactors containing 3, 5, or 10 mm diameter beads. Reactors and beads were made of zirconium oxide (noted ZrO2) or stainless steel. Gram scale mechanochemical reactions were performed in a Retsch PM100 planetary ball-mill with a 250 mL inner-volume reactor and 3 mm diameter beads, both made of stainless steel. Reactions were performed at room temperature, without control of the temperature by external heating or cooling. A slight increase in reactor temperature was observed, due at least in part to bead frictions during grinding.
Chemical analysis
UHPLC.
UHPLC analyses were performed on an Agilent technologies 1220 Infinity LC using a Chromolith high resolution RP-18e 50-4.6 mm column and a linear gradient of 0 to 100% CH3CN/0.1% TFA in H2O/0.1% TFA over 3 min, detection at 214 nm. Flow rate: 3 mL min−1.
LCMS.
Mass spectra were obtained using a LCMS with ESI using a Water Alliance 2695 as LC, coupled to a Waters ZQ spectrometer with electrospray source, a simple quadrupole analyzer and a UV Waters 2489 detector. Analyses were carried out using a linear gradient of 0 to 100% CH3CN/0.1% TFA in H2O/0.1% TFA over 2.5 min, detection at 214 nm. Flow rate: 3 mL min−1.
NMR.
NMR analyses were performed at the “Plateforme d'Analyse et de Caractérisation” of the Pôle Chimie Balard, Université de Montpellier. 1H NMR spectra were recorded on a Bruker Avance III HD 400 MHz spectrometer and chemical shifts are reported in ppm using DMSO-d6 peak as an internal standard (2.50 ppm). Peaks are reported as s = singlet, d = doublet, t = triplet, q = quadruplet, m = multiplet; coupling constant are reported in Hz. 13C NMR spectra were recorded on a Bruker Avance III HD 101 MHz spectrometer and are reported in ppm using DMSO-d6 peak as an internal standard (39.52 ppm).
FTIR.
IR spectra were recorded on an Agilent Cary 630 FTIR Spectrometer and are reported in cm−1.
Methods and procedure
General procedure for the mechanochemical allylation of vanillin at small scale.
The total mass of reagents (vanillin, potassium carbonate and allyl bromide) was fixed at 400 mg for all small scale assays. Vanillin (1.0 eq.) and potassium carbonate (1.0 eq.) were added in the reactor. Beads were then added. The reactor was closed and agitated at the chosen rotational speed for 5 min to obtain a homogeneous mixture. If any, LAG solvent (80 μL, 0.2 μL mg−1) was added followed by the addition of allyl bromide (1.1–1.5 eq.). The reactor was closed and agitated for 1 to 3 cycles of 1 h separated by 30 min breaks. The reactor was opened and three reaction samples were collected at different locations in the reactor and solubilized in a mixture of aqueous 1 M HCl and acetonitrile (50/50 v/v) for further analysis by HPLC. The reaction mixture inside the reactor was then solubilized with 5 mL of EtOAc, 5 mL of H2O, and finally 10 mL of an aqueous solution of sodium hydroxide 1 M was added. The crude solution was then transferred into a separatory funnel and the organic layer was recovered. The aqueous layer was extracted twice with 10 mL of EtOAc. The combined organic layers were then dried over anhydrous magnesium sulfate, filtered and concentrated under vacuum to afford allylated vanillin as a pale yellow liquid.
Optimized conditions for the mechanochemical allylation at small scale.
3-Methoxy-4-(2-propen-1-yloxy)benzaldehyde (allylated vanillin), CAS: 22280-95-1.
Vanillin (129 mg, 0.85 mmol) and potassium carbonate (117.2 mg, 0.85 mmol, 1.0 eq.) were added in the reactor. 370 ZrO2 beads of 3 mm diameter (32 g) were then added. The reactor was closed and agitated at 850 rpm for 5 min to obtain a homogeneous mixture. DMF (80 μL, 0.2 μL mg−1) and allyl bromide (110 μL, 1.27 mmol, 1.5 eq.) were then added. The reactor was closed and agitated at 850 rpm following 3 cycles of 1 h separated by intervals of 30 min. Three samples were collected at different locations in the reactor and solubilized in a mixture of aqueous 1 M HCl and acetonitrile (50/50 v/v) for further analysis by HPLC where no trace of vanillin was detected. The reaction mixture inside the reactor was then solubilized with 5 mL of EtOAc, 5 mL of H2O, and finally 10 mL of an aqueous solution of sodium hydroxide 1 M was added. The crude solution was then transferred into a separatory funnel and the organic layer was recovered. The aqueous layer was then extracted twice with 10 mL of EtOAc. The combined organic layers were then dried over anhydrous magnesium sulfate, filtered and concentrated under vacuum to afford allylated vanillin as a pale yellow liquid (143 mg, 87% isolated yield).
1H NMR (ppm, 600 MHz, DMSO-d6) δ (ppm): 9.84 (s, 1H), 7.53 (d, J = 8.2, 1H), 7.40 (s, 1H), 7.17 (d, J = 8.3, 1H), 6.17–5.92 (m, 1H), 5.42 (d, J = 17.3, 1H), 5.29 (d, J = 10.5, 1H), 4.68 (d, J = 5.4, 2H), 3.84 (s, 3H).
13C NMR (ppm, 101 MHz, DMSO-d6) δ (ppm): 191.3 (s), 153.0 (s), 149.3 (s), 133.0 (s), 129.8 (s), 125.9 (s), 118.2 (s), 112.4 (s), 109.7 (s), 69.0 (s), 55.5 (s).
3-[3-Methoxy-4-(2-propen-1-yloxy)phenyl]-2-propenoic acid ethyl ester (allylated ethyl ferulate), CAS: 54744-76-2.
Ethyl ferulate (164 mg, 0.74 mmol) and potassium carbonate (102 mg, 0.74 mmol, 1.0 eq.) were added in the reactor. 370 ZrO2 beads of 3 mm diameter (32 g) were then added. The reactor was closed and agitated at 850 rpm for 5 min to obtain a homogeneous mixture. DMF (80 μL, 0.2 μL mg−1) and allyl bromide (96.4 μL, 1.11 mmol, 1.5 eq.) were then added. The reactor was closed and agitated at 850 rpm following 3 cycles of 1 h separated by intervals of 30 min. Three samples were collected at different locations in the reactor and solubilized in a mixture of aqueous 1 M HCl and acetonitrile (50/50 v/v) for further analysis by HPLC where no trace of vanillin was detected. The reaction mixture inside the reactor was then solubilized with 5 mL of EtOAc, 5 mL of H2O, and finally 10 mL of an aqueous solution of sodium hydroxide 1 M was added. The crude solution was then transferred into a separatory funnel and the organic layer was recovered. The aqueous layer was then extracted twice with 10 mL of EtOAc. The combined organic layers were then dried over anhydrous magnesium sulfate, filtered and concentrated under vacuum to afford allylated ethyl ferulate as a pale orange powder (160 mg, 82% isolated yield).
M.p.: 70–74 °C.
1H NMR (ppm, 600 MHz, DMSO-d6) δ (ppm): 7.58 (d, J = 16.0 Hz, 1H), 7.37 (s, 1H), 7.21 (d, J = 8.4, 1H), 6.97 (d, J = 8.4, 1H), 6.56 (d, J = 15.9, 1H), 6.12–5.94 (m, 1H), 5.39 (d, J = 17.3, 1H), 5.26 (d, J = 10.5, 1H), 4.59 (d, J = 5.3, 2H), 4.17 (q, J = 7.1, 2H), 3.81 (s, 3H), 1.25 (t, J = 7.1 Hz, 3H).
13C NMR (ppm, 101 MHz, DMSO-d6) δ (ppm): 166.7 (s), 149.9 (s), 149.3 (s), 144.7 (s), 133.6 (s), 127.2 (s), 122.9 (s), 118.0 (s), 115.9 (s), 113.0 (s), 110.7 (s), 68.9 (s), 60.0 (s), 55.8 (s), 14.4 (s).
Reaction in a 250 mL stainless steel reactor in the PM100 planetary ball-mill (scale-up assay).
3-Methoxy-4-(2-propen-1-yloxy)benzaldehyde (allylated vanillin), CAS: 22280-95-1.
The total mass of reagents (vanillin, potassium carbonate and allyl bromide) was fixed at 5 g for all scale-up assays. Vanillin (1.61 g, 10.58 mmol) and potassium carbonate (1.46 g, 10.56 mmol, 1.0 eq.) were added in the reactor. 2080 stainless steel beads of 3 mm diameter (180 g) were then added. The reactor was closed and agitated at 400 rpm for 5 min to obtain a homogeneous mixture. DMF (1.0 mL, 0.2 μL mg−1) and allyl bromide (1.38 mL, 15.90 mmol, 1.5 eq.) were then added. The whole reactor was agitated at 400 rpm following 3 cycles of 1 h separated by 1 h breaks. Three samples were collected at different locations in the reactor and solubilized in a mixture of aqueous 1 M HCl and acetonitrile (50/50 v/v) for further analysis by HPLC. The reaction mixture inside the reactor was then solubilized with 50 mL of EtOAc, 50 mL of H2O, and finally 50 mL of an aqueous solution of sodium hydroxide 1 M was added. The crude solution was then transferred into a separatory funnel and the organic layer was recovered. The aqueous layer was then extracted twice with 50 mL of EtOAc. The combined organic layers were then dried over anhydrous magnesium sulfate, filtered and concentrated under vacuum to afford allylated vanillin as a pale yellow liquid (1.94 g, 95% isolated yield).
3-[3-Methoxy-4-(2-propen-1-yloxy)phenyl]-2-propenoic acid ethyl ester (allylated ethyl ferulate), CAS: 54744-76-2.
The total mass of reagents (ethyl ferulate, potassium carbonate and allyl bromide) was fixed at 5 g for all scale-up assays. Ethyl ferulate (2.05 g, 9.23 mmol) and potassium carbonate (1.28 g, 9.26 mmol, 1.0 eq.) were added in the reactor. 2080 stainless steel beads of 3 mm diameter (180 g) were then added. The reactor was closed and agitated at 400 rpm for 5 min to obtain a homogeneous mixture. DMF (1.0 mL, 0.2 μL mg−1) and allyl bromide (1.2 mL, 13.84 mmol, 1.5 eq.) were then added. The whole reactor was agitated at 400 rpm following 3 cycles of 1 h separated by 1 h breaks. Three samples were collected at different locations in the reactor and solubilized in a mixture of aqueous 1 M HCl and acetonitrile (50/50 v/v) for further analysis by HPLC. The reaction mixture inside the reactor was then solubilized with 50 mL of EtOAc, 50 mL of H2O, and finally 50 mL of an aqueous solution of sodium hydroxide 1 M was added. The crude solution was then transferred into a separatory funnel and the organic layer was recovered. The aqueous layer was then extracted twice with 50 mL of EtOAc. The combined organic layers were then dried over anhydrous magnesium sulfate, filtered and concentrated under vacuum to afford allylated ethyl ferulate as a pale orange powder (2.24 g, 92% isolated yield).
Allylation reaction in solution.
Vanillin (1 g, 6.57 mmol) and potassium carbonate (0.908 g, 6.57 mmol, 1.0 eq.) were added in a 10 mL round-bottom flask. A minimum quantity of DMF (2.6 mL) and allyl bromide (0.85 mL, 9.82 mmol, 1.5 eq.) were added. The reaction was stirred for 3 h at 50 °C and then concentrated under vacuum. The crude was analyzed by 1H NMR to determine the conversion. The reaction mixture inside the reactor was then solubilized with 20 mL of EtOAc, 20 mL of H2O, and finally 20 mL of an aqueous solution of sodium hydroxide 1 M was added. The crude solution was then transferred into a separatory funnel and the organic layer was recovered. The aqueous layer was then extracted twice with 20 mL of EtOAc. The combined organic layers were then dried over anhydrous magnesium sulfate, filtered and concentrated under vacuum to afford allylated vanillin as a pale yellow liquid (1.09 g, 86% isolated yield).
Author contributions
Conceptualisation and visualization: TXM and FA; methodology: TXM; data curation: DB; investigation: DB and TXM; formal analysis: TXM, DB, FA and SF; validation: TXM, FL, FA, SF and VF; supervision: TXM; project administration: TXM and FA; resources: FL, FA, TXM and VF; funding acquisition: FA; writing – original draft: DB, SF and TXM; writing – review & editing: TXM, FA, SF, FL and VF.
Conflicts of interest
There are no conflicts to declare.
Acknowledgements
The authors are grateful to CHRYSO Saint-Gobain, Grand Reims, Département de la Marne, Grand Est Region, Université de Montpellier and Centre National de la Recherche Scientifique (CNRS) for their financial support.
Notes and references
- S. Laurichesse, C. Huillet and L. Avérous, Green Chem., 2014, 16, 3958–3970 RSC.
- M. M. Abu-Omar, K. Barta, G. T. Beckham, J. S. Luterbacher, J. Ralph, R. Rinaldi, Y. Román-Leshkov, J. S. M. Samec, B. F. Sels and F. Wang, Energy Environ. Sci., 2021, 14, 262–292 RSC.
- S. Fadlallah, P. Sinha Roy, G. Garnier, K. Saito and F. Allais, Green Chem., 2021, 23, 1495–1535 RSC.
- F. G. Calvo-Flores and J. A. Dobado, ChemSusChem, 2010, 3, 1227–1235 CrossRef CAS.
- M. Fache, B. Boutevin and S. Caillol, ACS Sustainable Chem. Eng., 2016, 4, 35–46 CrossRef CAS.
- A. F. Reano, F. Pion, S. Domenek, P.-H. Ducrot and F. Allais, Green Chem., 2016, 18, 3334–3345 RSC.
- M. D. Horbury, A. L. Flourat, S. E. Greenough, F. Allais and V. G. Stavros, Chem. Commun., 2018, 54, 936–939 RSC.
- M. D. Horbury, E. L. Holt, L. M. M. Mouterde, P. Balaguer, J. Cebrián, L. Blasco, F. Allais and V. G. Stavros, Nat. Commun., 2019, 10, 4748 CrossRef.
- M. D. Horbury, M. A. P. Turner, J. S. Peters, M. Mention, A. L. Flourat, N. D. M. Hine, F. Allais and V. G. Stavros, Front. Chem., 2020, 8, 633 CrossRef CAS PubMed.
- C. Peyrot, M. M. Mention, F. Brunissen, P. Balaguer and F. Allais, Molecules, 2020, 25, 2178 CrossRef CAS.
- C. Peyrot, M. Mention, R. Fournier, F. Brunissen, J. Couvreur, P. Balaguer and F. Allais, Green Chem., 2020, 22, 6510–6518 RSC.
- B. Rioux, C. Peyrot, M. M. Mention, F. Brunissen and F. Allais, Antioxidants, 2020, 9, 331 CrossRef CAS.
- J. M. Toldo, M. T. do Casal and M. Barbatti, J. Phys. Chem. A, 2021, 125, 5499–5508 CrossRef CAS.
- E. Savonnet, E. Grau, S. Grelier, B. Defoort and H. Cramail, ACS Sustainable Chem. Eng., 2018, 6, 11008–11017 CrossRef CAS.
- F. Pion, A. F. Reano, P.-H. Ducrot and F. Allais, RSC Adv., 2013, 3, 8988 RSC.
- A. Maiorana, A. F. Reano, R. Centore, M. Grimaldi, P. Balaguer, F. Allais and R. A. Gross, Green Chem., 2016, 18, 4961–4973 RSC.
- A. S. Jaufurally, A. R. S. Teixeira, L. Hollande, F. Allais and P.-H. Ducrot, ChemistrySelect, 2016, 1, 5165–5171 CrossRef CAS.
- M. Janvier, L. Hollande, A. S. Jaufurally, M. Pernes, R. Ménard, M. Grimaldi, J. Beaugrand, P. Balaguer, P.-H. Ducrot and F. Allais, ChemSusChem, 2017, 10, 738–746 CrossRef CAS.
- C. Aouf, J. Lecomte, P. Villeneuve, E. Dubreucq and H. Fulcrand, Green Chem., 2012, 14, 2328–2336 RSC.
- W. A. Ayer and P. A. Craw, Can. J. Chem., 1991, 69, 1909–1916 CrossRef CAS.
- R. Detterbeck and M. Hesse, Helv. Chim. Acta, 2003, 86, 343–360 CrossRef CAS.
- L. Breloy, C. Negrell, A.-S. Mora, W. S. J. Li, V. Brezová, S. Caillol and D.-L. Versace, Eur. Polym. J., 2020, 132, 109727 CrossRef CAS.
- Y. Han, D.-H. Tang, G.-X. Wang, Y.-N. Sun, Y. Guo, H. Zhou, W.-F. Qiu and T. Zhao, Chin. J. Polym. Sci., 2020, 72–83 CrossRef CAS.
- N. Sharma, D. Mohanakrishnan, R. Kumar, Richa, A. K. Sinha, U. K. Sharma and D. Sahal, Eur. J. Med. Chem., 2014, 79, 350–368 CrossRef CAS.
- A. Yu, E. M. Serum, A. C. Renner, J. M. Sahouani, M. P. Sibi and D. C. Webster, ACS Sustainable Chem. Eng., 2018, 12586–12592 CrossRef CAS.
- Preventing adverse health effects from exposure to dimethylformamide (DMF), 2020. DOI:10.26616/NIOSHPUB90105.
- T. Friščić, C. Mottillo and H. M. Titi, Angew. Chem., Int. Ed., 2020, 59, 1018–1029 CrossRef PubMed.
- J. L. Howard, Q. Cao and D. L. Browne, Chem. Sci., 2018, 9, 3080–3094 RSC.
- S. L. James, C. J. Adams, C. Bolm, D. Braga, P. Collier, T. Friščić, F. Grepioni, K. D. M. Harris, G. Hyett, W. Jones, A. Krebs, J. Mack, L. Maini, A. G. Orpen, I. P. Parkin, W. C. Shearouse, J. W. Steed and D. C. Waddell, Chem. Soc. Rev., 2012, 41, 413–447 RSC.
- A. A. L. Michalchuk, E. V. Boldyreva, A. M. Belenguer, F. Emmerling and V. V. Boldyrev, Front. Chem., 2021, 9, 359 Search PubMed.
- K. J. Ardila-Fierro and J. G. Hernández, ChemSusChem, 2021, 14, 2145–2162 CrossRef CAS PubMed.
-
M. Uy and J. K. Telford, in 2009 IEEE aerospace conference, 2009, pp. 1–10.
- K. L. Denlinger, L. Ortiz-Trankina, P. Carr, K. Benson, D. C. Waddell and J. Mack, Beilstein J. Org. Chem., 2018, 14, 688–696 CrossRef CAS PubMed.
- A. M. Belenguer, G. I. Lampronti and J. K. M. Sanders, J. Visualized Exp., 2018, e56824 Search PubMed.
- D. Hasa, E. Miniussi and W. Jones, Cryst. Growth Des., 2016, 16, 4582–4588 CrossRef CAS.
- T. Friščić, S. L. Childs, S. A. A. Rizvi and W. Jones, CrystEngComm, 2009, 418–426 RSC.
- J. E. Camp, ChemSusChem, 2018, 11, 3048–3055 CrossRef CAS PubMed.
- Y. Yeboue, B. Gallard, N. Le Moigne, M. Jean, F. Lamaty, J. Martinez and T.-X. Métro, ACS Sustainable Chem. Eng., 2018, 6, 16001–16004 CrossRef CAS.
- According to Regulation (EC) No. 1272/2008, DMF is classified as presenting reproductive toxicity.
- D. Prat, A. Wells, J. Hayler, H. Sneddon, C. R. McElroy, S. Abou-Shehada and P. J. Dunn, Green Chem., 2016, 18, 288–296 RSC.
- F. Diot-Néant, L. Mouterde, S. Fadlallah, S. A. Miller and F. Allais, ChemSusChem, 2020, 13, 2613–2620 CrossRef PubMed.
- sEF and cEF definitions adapted from reference: F. Roschangar, R. A. Sheldon and C. H. Senanayake, Green Chem., 2015, 17, 752–768 RSC.
-
S. Fadlallah, L. M. M. Mouterde, G. Garnier, K. Saito and F. Allais, in ACS Symposium Series, ed. H. N. Cheng and R. A. Gross, American Chemical Society, Washington, DC, 2020, vol. 1373, pp. 77–97 Search PubMed.
- R. A. Sheldon, Green Chem., 2007, 9, 1273 RSC.
- A. Srikrishna, S. Ratna Kumar and P. C. Ravikumar, Synth. Commun., 2007, 37, 4123–4140 CrossRef CAS.
- J. Hoffmann and U. Kazmaier, Angew. Chem., Int. Ed., 2014, 53, 11356–11360 CrossRef CAS PubMed.
- A. V. Chate, M. D. Nikam, P. S. Mahajan and C. H. Gill, Org. Commun., 2012, 5, 83–98 CAS.
- R. M. Kevwitch, C. S. Shanahan and D. V. McGrath, New J. Chem., 2012, 36, 492–505 RSC.
- V. Isoni, K. Mendoza, E. Lim and S. K. Teoh, Org. Process Res. Dev., 2017, 21, 992–1002 CrossRef CAS.
Footnotes |
† Electronic supplementary information (ESI) available: IR, 1H & 13C NMR spectra and chromatograms of all synthesized compounds, details of the calculations of the E factors. See DOI: https://doi.org/10.1039/d2gc02185d |
‡ Current address: ICGM, Univ. Montpellier, CNRS, ENSCM, Montpellier, France. |
|
This journal is © The Royal Society of Chemistry 2022 |
Click here to see how this site uses Cookies. View our privacy policy here.