Process optimization and kinetics of microwave assisted transesterification of crude glycerol for the production of glycerol carbonate†
Received
15th September 2020
, Accepted 17th November 2020
First published on 19th November 2020
Abstract
The production of glycerol carbonate (GC) from industrial grade crude glycerol was catalyzed by calcium oxide (CaO) via microwave assisted transesterification (MAT). Influencing process parameters including reaction temperature, time and molar ratio of dimethyl carbonate/glycerol (DMC/Gly) were examined and optimized by applying Box Behnken Design (BBD). The reaction was modelled into a reduced cubic model with good predictive accuracy. A high GC yield of 99.5% was achieved with 1 wt% CaO at optimized conditions such as reaction temperature of 65 °C, reaction time of 3 min and DMC/Gly molar ratio of 2.5. The study performed on the reaction kinetics suggests that the reaction follows an irreversible second order rate equation. A relatively low activation energy of 4.53 kJ mol−1 was determined for the microwave assisted transesterification of crude glycerol for the production of GC. The values of rate constants between 45 °C to 65 °C were in the range of 0.023–0.026 L mol−1 min−1, which are of one magnitude order higher than that of the conventional heating.
1. Introduction
In view of the supply glut of crude glycerol slated to cross 14 billion gallons by 2020,1 exploring new applications for crude glycerol is essential to reduce the foreseeable oversupply. Consequently, numerous outlets for disposal and utilization of the crude glycerol have been attempted. In particular, large-scale biodiesel producer upgraded crude glycerol to pure glycerol via costly purification processes.2 However, new alternatives of using crude glycerol as chief feedstock to produce value-added products via chemical conversion and thermochemical/biological conversion hold promise for affordable production. Catalytic chemical conversions outshine other processes as it is faster and more economically viable.3 For instance, catalytic transformation of glycerol to useful chemicals such as glycerol carbonate (GC) involving direct utilization of crude glycerol from biodiesel plant and oleochemical industries.4–6
Glycerol carbonate (GC) or 4-hydroxymethyl-2-oxo-1,3-dioxolane is a small molecule with molar weight of 118.09 g mol−1 which contains a hydroxyl group and a 2-oxo-1,3-dioxolane group (ODO). Its unique functional group allows GC to have wide reactivity and therefore it has various industrial applications.7 Due to its biodegradability, low toxicity and good water miscibility, GC has been considered as an eco-friendly polar solvent.8 For instance, it can potentially be used as a curing agent for pozzolanic matrix in the construction industry.
Glycerol carbonate can be synthesized from glycerol via various direct or indirect routes.9 Carboxylation of glycerol with CO2 and oxidative carboxylation with CO/O2 are direct synthesis routes of GC. The indirect process routes include phosgenation, transesterification and glycerolysis of glycerol with carbonate derivatives to produce GC. Among the synthesis routes, transesterification of glycerol with dimethyl carbonate (DMC) is a greener, direct and industrial feasible route to produce high GC yield.9,10
Considering energy is an essential economic factor in large-scale production, heating methods have been vastly researched to intensify chemical processes. Among various heating methods, microwave technique has shown efficient high-speed synthesis of materials attributing to its association with dielectric heating. The microwave processing technology has been known to be an effective route in chemical synthesis with shorter reaction time and lower operating temperature.11–18 In the formation of GC, the feedstock glycerol exhibiting strong absorber characteristic towards microwave radiations.12 Moreover, heterogeneous catalyst has also been reported to be efficient in microwave-assisted transesterification.13,17,19,20 The present study incorporated a metal oxide heterogeneous catalyst with microwave irradiation in converting both pure and crude glycerol to GC via a transesterification process.
In process intensification, optimization has directly influenced the yield and production economics. The key process parameters for optimizing the microwave-assisted transesterification yield and the effects of parameters on crude glycerol were determined by using Box Behnken Design (BBD) of response surface methodology (RSM). The present study also includes reaction kinetics which is useful in designing suitable reactors for the catalytic transesterification process considering the kinetics in GC synthesis has been rarely reported. The kinetic study on MAT of crude glycerol was intended to evaluate the kinetic model and activation energy of the reaction.
2. Materials and methods
2.1 Materials
Industrial grade crude glycerol with 70% purity was obtained from a local biodiesel plant in Malaysia. The main impurities of crude glycerol include Matter Organic Non-Glycerol (MONG) (27.74 wt%) which is composed of sodium methylate (1 wt%), methanol (15 wt%), soap, fatty acid esters and water (0.34 wt%). Pure GC and catalyst calcium oxide (CaO) were supplied by Sigma Aldrich (USA). Dimethyl carbonate (DMC) was purchased from Merck (Germany).
2.2 Microwave-assisted transesterification
Microwave-assisted transesterification was performed in a microwave reactor (Milestones, 1200 W, 2450 MHz) in which is equipped with an infrared temperature sensor, a temperature probe, a three-neck round-bottomed flask, an electromagnetic stirrer and a condenser. 0.125 mol glycerol was placed into a 100 mL three-neck reaction flask and mixed with CaO and DMC in the predetermined ratio. The prepared samples were heated to the desired temperature at maximum microwave power of 500 W. The temperature was measured by in situ temperature probes. Upon completion of the reaction, the sample was collected and cooled to room temperature and centrifuged at 3500 rpm for 5 minutes to filter off the catalyst. The sample was then analysed for its GC content and the unreacted glycerol using Waters High Pressure Liquid Chromatograph (HPLC) apparatus equipped with a PL aquagel-OH column (Agilent) and a RI detector (Waters 410). The mobile phase used was water and its flow rate was set at 1 mL min−1. In the catalyst screening study, experiments were replicated three times to examine the reproducibility of GC production. The yields of GC and conversions of glycerol (GLY) were determined using eqn (1) and (2) in terms of mole, respectively. | 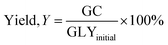 | (1) |
|  | (2) |
2.3 Experimental design and optimization
The microwave assisted transesterification of industrial grade crude glycerol was performed according to BBD design matrix generated with the aid of Design Expert 12 software (STAT-EASE Inc., Minneapolis, USA). The effect of three independent variables namely temperature, time and DMC/Gly molar ratio were investigated. The studied ranges of these independent variables were listed in Table 1. The range of reaction parameters selected are based on the individual factor effect studied in previous work.13 The transesterification performance was evaluated based on the yield of GC. The experimental response, Y (yield of GC) was fitted into a second order polynomial regression model as shown in eqn (3): |  | (3) |
where Xi and Xj are the independent variables studied, β0 is the constant coefficient, βi is the ith linear coefficient, βii is the quadratic coefficient and βij is the ijth interaction coefficient. The significance of the model developed was evaluated by performing analysis of variance (ANOVA). Three-dimensional response surface plots and contour plots generated by the program were used to provide some graphical illustration of the interaction between the operational variables. To evaluate and verify the predicted optimum GC yield, three experiments were conducted at the suggested optimum conditions.
Table 1 Independent variables used in the Box–Behnken design for microwave assisted transesterification of crude glycerol
Variables |
Coding |
Unit |
Uncoded levels |
Temperature |
A
|
°C |
45 |
55 |
65 |
Reaction time |
B
|
min |
1 |
5 |
9 |
DMC/glycerol molar ratio |
C
|
— |
1 |
2 |
3 |
3. Results and discussion
Biphasic existed during the initial stages of the reaction when crude glycerol was used as feedstock. The reaction mixture changed into single phase after a brief of less than 30 seconds during the microwave heating. A synergistic effect might have occurred whereby the polar solvent methanol resolved the immiscibility between reactants dimethyl carbonate (DMC) and glycerol21 together with the aid of microwave heating, the biphasic system changed to a single-phase reaction mixture which has in turn enhanced the interaction between the catalyst and the reactants. Consequently, the transesterification reaction was accelerated, resulting in high yield between 1–9 min. The detailed explanation is presented in the following section.
3.1 Statistical analysis
The experimental design for MAT of crude glycerol is tabulated in Table 2. The data of BBD was fitted well into the cubic and quadratic polynomial equations after elimination of the insignificant terms (P > 0.05) to predict the responses of yield and conversion, respectively. The models are expressed in terms of coded factors for yield and conversion of MAT of crude glycerol as shown in eqn (4) and (5), respectively. A, B and C represent temperature (°C), reaction time (min) and DMC/Gly molar ratio respectively. | Yield (Y) = 94.29 + 2.42A + 2.87B + 12.81C − 0.78AB − 0.53AC + 5.03BC − 5.30B2 − 10.10C2 − 2.69AC2 − 6.77B2C + 5.18BC2 | (4) |
| Conversion (x) = 73.93 + 4.98A + 4.95B + 15.21C+ 1.46A2 − 6.13B2 − 9.03C2 − 2.96AB − 2.53AC + 6.46BC | (5) |
Table 2 Experimental design layout with their corresponding responses for MAT of crude glycerol
Run |
Experimental variables |
Response |
Temperature, A (°C) |
Reaction time, B (min) |
DMC/glycerol molar ratio, C |
Yield of GC (%) |
Conversion (%) |
1 |
55 |
5 |
2 |
95.65 |
72.13 |
2 |
45 |
1 |
2 |
82.45 |
56.49 |
3 |
65 |
1 |
2 |
88.86 |
73.54 |
4 |
45 |
5 |
1 |
70.65 |
44.57 |
5 |
55 |
1 |
3 |
72.31 |
62.21 |
6 |
55 |
5 |
2 |
95.91 |
74.30 |
7 |
45 |
5 |
3 |
97.33 |
79.36 |
8 |
65 |
5 |
3 |
95.75 |
83.08 |
9 |
45 |
9 |
2 |
89.75 |
70.90 |
10 |
55 |
5 |
2 |
92.66 |
73.40 |
11 |
55 |
9 |
1 |
76.33 |
42.42 |
12 |
55 |
5 |
2 |
94.38 |
75.69 |
13 |
55 |
5 |
2 |
94.73 |
74.12 |
14 |
55 |
9 |
3 |
98.48 |
86.43 |
15 |
65 |
5 |
1 |
71.18 |
58.41 |
16 |
65 |
9 |
2 |
93.03 |
76.11 |
17 |
55 |
1 |
1 |
70.30 |
44.02 |
The models for yield and conversion of MAT of crude glycerol in terms of actual factors are shown in eqn (6) and (7), respectively, in which the parameters of temperature, time and DMC/Gly molar ratio are denoted by T, t and M respectively.
| Yield (Y) = 33.46182 − 0.34694T + 5.22441t + 0.65968M + 0.31009t2 + 2.57582M2 − 0.065062Tt + 1.34925TM − 2.76094tM − 0.40050TM2 − 0.29828t2M + 1.75062tM2 | (6) |
| Conversion (x) = −23.67228 − 0.23060T + 5.90906t + 57.17975M + 0.014585T2 − 0.38291t2 − 9.03150M2 − 0.074000Tt − 0.25300TM + 1.61375tM | (7) |
The results of GC yield and conversion are shown in Table 2. A large discrepancy between the yield and the conversion is due to high GC yield that was achieved in a short time even though conversion was not yet completed. This might be attributed to the effect of impurities that present in the crude glycerol. The impurities such as methanol, residual catalyst sodium methylate (NaOMe) and fatty acid esters exerted positive effect that had enhanced the yield of GC.13 As presented in our previous work,13 the mentioned impurities had greatly enhanced the GC yield. The presence of methanol in crude glycerol had resolved the immiscibility between reactants and promoted the interaction between catalyst and reactants. This is because, being a good microwave radiation absorption solvent with loss factor, tan
<delta> = 0.659, methanol dominates microwave spectrum and would lead to localized superheating.22 Furthermore, the transesterification reaction could have also been catalyzed by NaOMe in addition to the CaO catalyst. The other impurity in crude glycerol was sodium methylate which is very soluble in MeOH.23 The two stated impurities and the reaction mixture together produced up to 4 fold of increment in GC yield.13 Apart from that, the other impurity fatty acid esters also contributed to high GC yield from its reaction with DMC that produced GC.13 In the present study, excess DMC which is up to 3 times of the stoichiometric proportion was used in the transesterification of glycerol reaction to facilitate the forward reaction. Some of the excessive DMC might have reacted with fatty acid esters to produce GC. The similar observations were reported in the transesterification reaction using DMC as acyl acceptor and reactant for the simultaneous synthesis of biodiesel and GC.24–28 The findings collectively have proven that the three stated impurities in the crude glycerol had affected GC synthesis positively via microwave-assisted transesterification of crude glycerol to produce high GC yield.
The significance of the developed models that derived from the ANOVA is presented in Table 3. The p-value that is less than 0.0001, both calculated from the model and obtained for the MAT reactions imply that the models are significant. The insignificant lack of fit further emphasizes the fitness of the models in representing the reactions. In addition, the consistency between the experimental data and the model predicted values was confirmed by the high R-squared values >0.99 for both yield and conversion as presented in Table 3. Moreover, the MAT of crude glycerol has adequate precision values and this suggested that the model can be used within the design space defined by the BBD.
Table 3 Fitness of the model for microwave assisted transesterification of crude glycerol
|
p-Value, prob. > F |
Yield |
Conversion |
Model |
<0.0001 (significant) |
0.0001 (significant) |
Lack of fit |
0.6842 (insignificant) |
0.3414 (insignificant) |
R-squared |
0.9959 |
0.9952 |
Adjusted R-squared |
0.9870 |
0.9890 |
Predicted R-squared |
0.9606 |
0.9557 |
Adequate precision |
23.463 |
39.293 |
3.2 Process analysis
The effects of the process variables on the production of GC were examined using RSM. The interactions between any two of the variables were illustrated by three-dimensional response surface plots and contour plots as shown in Fig. 1(a)–(c).
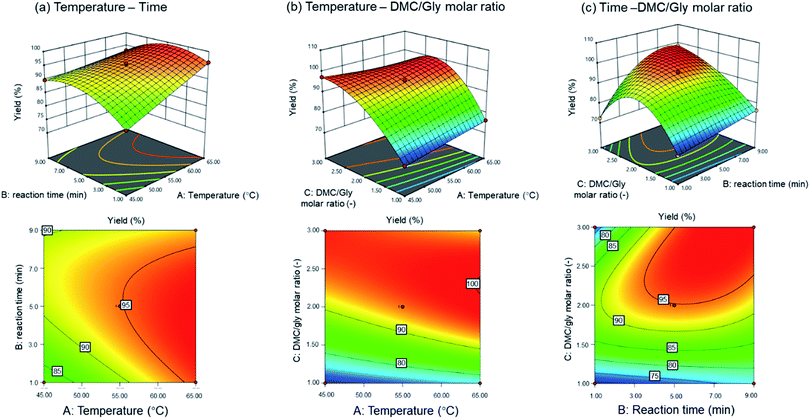 |
| Fig. 1 Three dimensional (3D) contour and response surface plot of the MAT of crude glycerol (a) temperature–time; (b) temperature–DMC/glycerol molar ratio; and (c) time–DMC/glycerol molar ratio for the predicted yields of GC. | |
Fig. 1(a) depicts the interaction between the reaction time and the temperature. In the temperature range of 45 to 55 °C, an increase in reaction time improves the yield. However, for a temperature range between 55 to 65 °C, there is no significant increase in the yield. Approaching 65 °C, yield as high as 95% can be achieved within a reaction time of between 1 to 8 minutes.
The effect of temperature and molar ratio of DMC/Gly is illustrated in Fig. 1(b). The figure shows that in the temperature range of 45 to 65 °C, DMC/Gly molar ratio has a positive effect on the yield. Following the trend, yield as high as 100% could be achieved at 65 °C within a molar ratio range of 2 to 2.5.
Fig. 1(c) shows that in between the reaction time of 1 to 4 minutes with increased DMC/Gly molar ratio up to 2.0, it improves the yield while an increase of molar ratio above 2.5 for the same reaction time range leads to a decrease in yield attainment. On the other hand, within the reaction time range of 4 to 9 minutes, an increase in DMC/Gly molar ratio improves the yield. Generally, 95% yield can be achieved with DMC/Gly molar ratio of greater than 2.0.
As shown in Table 2 (Run 4, 7, 8 and 15), the GC yield was increased from 70% to >95% when the molar ratio of DMC/Gly increased from 1 to 3, in 5 min reaction time and temperature of 45 °C and 65 °C, respectively. The overlay plots for various yield attainments above 95% are presented in Fig. 2. In Fig. 2(a), the overlay plot for minimum 95% of yield was achieved at DMC/Gly molar ratio of 2.5. The plot indicates that a minimum yield of 95% is achievable over a wide range of reaction parameters. Fig. 2 reveals that the range of reaction parameters is narrower for desirable higher yields. The findings thus far suggested that the molar ratio of DMC/Gly is the most significant parameter affecting the yield and conversion rate in MAT of crude glycerol. As previously discussed, this could be attributed to the excess DMC in the reaction solution which reacted with fatty acid esters in the crude glycerol to produce GC within a short time under the microwave heating. In Table 2, Run 5, 7, 8 and 14 show that the discrepancy between yield and conversion is among the lowest obtained at high DMC/Gly molar ratio of 3 compared to other runs. It can also be observed that the discrepancy between yield and conversion decreased with the increase of molar ratio as shown in the ESI of Table (a).† This suggests that high concentration of DMC has promoted high GC yield. However, the interactive effects exerted by the factors of the reaction conditions had also impacted the GC production yield. Therefore, the interaction of DMC/Gly molar ratio and temperature as well as the reaction time cannot be excluded. For instance, higher temperature and longer reaction time are required to compensate lower DMC/Gly molar ratio in achieving desirable GC yield.
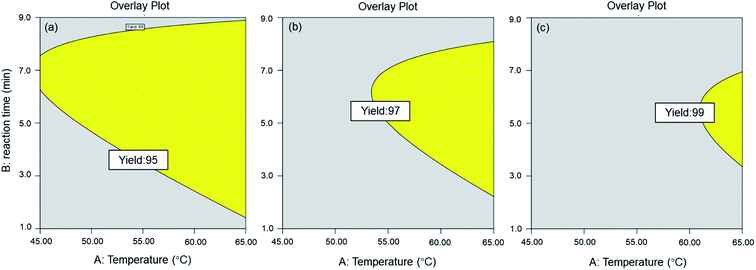 |
| Fig. 2 Overlay plot for (a) 95% yield attainment, (b) 97% yield attainment and (c) 99% yield attainment. | |
From the point prediction feature shown in the Design Expert software, MAT reaction with conditions of DMC/Gly molar ratio of 2.5, 3 min and 65 °C are the most favourable as it yields the highest GC at 99.5%.
3.3 Optimization and kinetic study
3.3.1 Process optimization and model validation.
In the microwave-assisted transesterification reaction of crude glycerol, an optimum yield of 99.5% of GC was predicted using the quadratic model at condition of 65 °C, 3 min, DMC/Gly molar ratio of 2.5 and 1 wt% CaO. The model validation results are shown in Table 4. An average yield of GC at 97.1% was obtained, which is consistent with the predicted yield. This confirms the model for MAT reaction of crude glycerol is well fitted to the experimental data.
Table 4 Verification of optimum conditions for microwave assisted transesterification of crude glycerol
Experimental value |
Response (yield of GC), % |
First replicate |
96.6 |
Second replicate |
99.2 |
Third replicate |
95.5 |
Average |
97.1 |
Predicted value by statistical model |
99.5 |
Error |
2.4 |
Fig. 3 shows the microwave heating effect and catalytic effect on transesterification reaction of crude glycerol. The comparisons are based on addition of 1 wt% CaO for catalytic reaction. It can be observed that the combination of CaO and microwave heating gave the best yield performance. As achieved in our previous work,13 with the same reaction conditions applied (65 °C, DMC/Gly molar ratio of 2, 5 min of reaction time), no GC could be produced in non-catalyzed conventional transesterification whereas 57% GC yield was achieved with addition of CaO. However, it is obvious that microwave heating provides efficient heating that could lead to GC yield above 80% within this short reaction time even with the absence of CaO. It could be due to the catalytic effect of the residual catalyst (NaOMe) in crude glycerol as discussed previously in Section 3.1. Through the process optimization done in this work, MAT reaction gave the highest yield of 97.1% in 3 min whereas 84.3% of GC yield could be achieved in 2 h of conventional heating. This suggests that microwave assisted transesterification of crude glycerol catalyzed by CaO is efficient for GC production (Table 5).
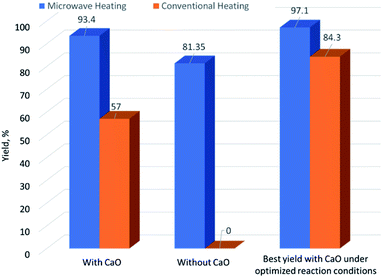 |
| Fig. 3 Comparison of yield performance between microwave heating and conventional heating with and without CaO on transesterification of crude glycerol. | |
Table 5 MAT conversion (%) at different times and temperature
Time |
Conversion (%) |
s |
min |
45 °C |
55 °C |
65 °C |
5 |
0.08 |
53.60 |
58.20 |
65.55 |
10 |
0.17 |
54.13 |
58.56 |
65.85 |
15 |
0.25 |
54.59 |
58.96 |
66.21 |
20 |
0.33 |
55.03 |
59.32 |
66.5 |
25 |
0.42 |
55.45 |
59.68 |
66.8 |
30 |
0.50 |
55.87 |
60.11 |
67.1 |
40 |
0.67 |
56.66 |
60.71 |
67.7 |
50 |
0.83 |
57.50 |
61.58 |
68.56 |
60 |
1.00 |
58.62 |
62.57 |
69.44 |
120 |
2.00 |
64.90 |
68.10 |
74.23 |
180 |
3.00 |
70.40 |
72.86 |
78.26 |
240 |
4.00 |
75.14 |
76.87 |
81.25 |
300 |
5.00 |
77.40 |
80.10 |
84.01 |
360 |
6.00 |
79.70 |
82.57 |
85.73 |
420 |
7.00 |
80.20 |
83.51 |
86.43 |
480 |
8.00 |
79.90 |
83.51 |
86.43 |
540 |
9.00 |
80.00 |
85.23 |
86.33 |
600 |
10.00 |
80.50 |
84.79 |
85.00 |
660 |
11.00 |
80.70 |
83.42 |
82.89 |
900 |
15.00 |
81.10 |
|
|
1200 |
20.00 |
81.40 |
|
|
3.3.2 Kinetic model development.
In the synthesis of GC, the kinetic model was developed and presented based on the rate of conversion of glycerol. Therefore, the side reaction of DMC and fatty acid esters could be neglected and only the transesterification of glycerol via MAT was considered in the kinetic study. Therefore, the kinetic model for transesterification of glycerol with MAT can be simplified into an overall reaction as shown in eqn (8). |  | (8) |
Since there were no intermediates detected, assumption of the fast disappearance of the reaction intermediates being transformed into GC is made, the kinetic model of the reaction (8) can be simplified to eqn (9), where A and B represent glycerol and DMC. This equation can be further expressed in the form of eqn (10) which is integrated to eqn (11), in which xA is conversion of glycerol, M = CB0/CA0, CA0 and CB0 are the initial molar concentrations of glycerol and DMC, respectively.
| 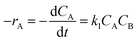 | (9) |
| 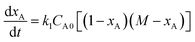 | (10) |
| 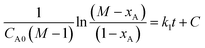 | (11) |
Conformity of the reaction kinetics with irreversible second order kinetic model can be tested through plotting the above equation in the form as shown below.
3.3.3 Conversion of glycerol to GC.
Kinetic study on transesterification of glycerol was conducted at a temperature range of 45 to 65 °C and at optimized reaction conditions (DMC/Gly molar ratio of 2.5 and 1 wt% CaO) which were obtained from process optimization at Section 3.3.1. Results of the reaction conversion at different time intervals and temperatures are summarized in Table 5 and Fig. 4. The conversion of glycerol reached a maximum of 84.0 ± 2.5% at the equilibrium point for all reaction temperatures. As the reaction temperature increased, the time for the conversion to reach equilibrium point reduced. The conversion at 45, 55 and 65 °C reached the equilibrium point with reaction times of 20 min, 9 min and 7 min, respectively.
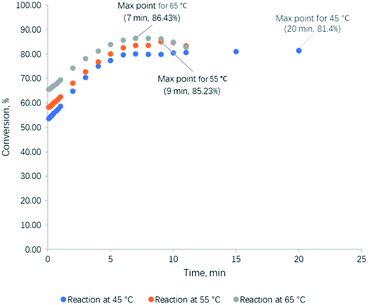 |
| Fig. 4 Conversion of glycerol achieved experimentally at different times and temperatures. | |
3.4 Irreversible second-order kinetic model
The reaction kinetics was tested with the irreversible second-order model according to eqn (11) and the results are shown in Fig. 5. The slope and the intercept of the trend lines in the figure give the forward reaction constant and the model integration constant, respectively. In addition, the R2 values of the trend lines presented gave the confidence levels of the reaction conformity with the relevant kinetic model. MAT of crude glycerol gave 99.6–99.9% confidence level in conformity with irreversible second-order Kinetic model. The reaction at 45 °C has the lowest confidence of 99.6% while the reaction at 55 °C has the highest confidence of 99.9%
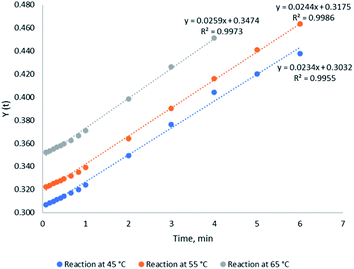 |
| Fig. 5 Conversion of glycerol to GC at different times and temperatures achieved from the irreversible second-order kinetic model. | |
3.5 Rate constants and activation energy
The rate constants of different reaction temperature for irreversible second-order kinetic model are listed in Table 6, which were calculated from the slope of the trendlines as shown in Fig. 5. The rate constant at 45 °C has the lowest value of 0.0234 L mol−1 min−1 while 65 °C has the highest rate constant of 0.0259 L mol−1 min−1. This indicates that an elevation in the temperature accelerated the MAT reaction and reduced the reaction duration in achieving maximum production. This observation is in agreement with the equilibrium times of the reaction at different temperatures as previously discussed. The activation energy of the reaction can be calculated using Arrhenius equation as shown in eqn (12). | 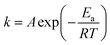 | (12) |
where Ea is the activation energy and A is the frequency factor. In the plot of ln
k versus 1/T, the slope and the intercept of the trend line denotes the value of −Ea/R and A, respectively.
Table 6 Rate constants for the irreversible second order of MAT
Reaction temperature (°C) |
Rate constant (L mol−1 min−1) |
45 |
0.0234 |
55 |
0.0244 |
65 |
0.0259 |
Based on eqn (12) and Fig. 6, the activation energy of the MAT of glycerol was 4.53 kJ mol−1, which is 6 to 12 times lower than the activation energy required for conventional heating. As shown in Table 7, the activation energy reported for conventional heating glycerol carbonate production was in the range of 28.4 to 52.55 kJ mol−1. The comparatively low activation energy achieved in this work might be attributed to both thermal and non-thermal effects of microwave heating on the transesterification reaction. The thermal effect (referred to rapid heating) is caused by dielectric heating of microwave energy. The temperature of the reaction mixtures increases rapidly and therefore the reaction rate is enhanced in accordance to the Arrhenius fundamental. Besides, the non-thermal effect is very much dependent on the interaction between the reactants and microwave irradiation.29 In view of methanol and glycerol being very polar substances, their high microwave absorption capacity22,30 increased dipolar polarization phenomenon and created more localized rotations via dipolar rotation and ionic reduction. The localized rotations facilitate the localized superheating22 and the polarity of a polar substance could be increased under microwave irradiation from a ground state to the transition state31 This eventually lead to a reduction in activation energy. Hence, the OH-group32 (methanol and glycerol) in crude glycerol played a vital role in expediting the microwave-assisted transesterification reaction as confirmed by the literature.33
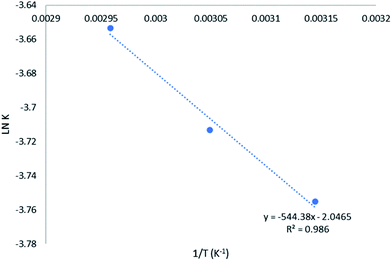 |
| Fig. 6 Arrhenius plot for irreversible second-order kinetic model for MAT of crude glycerol. | |
Table 7 Kinetic study of transesterification of glycerol with DMC
Conventional or microwave heating |
Catalyst type and concentration (wt%) |
Reaction order |
Reaction rate constant, k |
Activation energy (kJ mol−1) |
References |
Conventional |
Ti-SBA-15 catalysts, 5.5 wt% |
N.A. |
N.A. |
39.2 |
36
|
Conventional |
Waste red mud (NaAlO2 and Ca2SiO4), 12.5 wt% |
Pseudo-first order |
75 °C, k = 0.1364 s−1 |
N.A. |
37
|
Conventional |
Hydrotalcite, 15 wt% |
Second order irreversible |
150 °C, k = 1.77 × 10−3 L mol−1 min−1 |
52.55 |
38
|
160 °C, k = 2.90 × 1−3 L mol−1 min−1 |
170 °C, k = 3.73 × 10−3 L mol−1 min−1 |
180 °C, k = 4.44 × 10−3 L mol−1 min−1 |
Conventional |
DBU based ionic liquid, 4 wt% |
Second order irreversible |
30 °C, k = 3.25 × 10−3 L mol−1 min−1 |
30.95 |
39
|
40 °C, k = 4.61 × 10−3 L mol−1 min−1 |
50 °C, k = 6.60 × 10−3 L mol−1 min−1 |
60 °C, k = 9.88 × 10−3 L mol−1 min−1 |
Conventional |
Potassium methoxide, 0.1–0.12 wt% |
Second order irreversible |
50 °C, k = 3.33 × 10−3 L2 mol−2 min−1 |
28.4 ± 1.5 |
40
|
60 °C, k = 4.56 × 10−3 L2 mol−2 min−1 |
70 °C, k = 6.15 × 10−3 L2 mol−2 min−1 |
Microwave |
CaO, 1 wt% |
Second order irreversible |
45 °C, k = 2.34 × 10−2 L mol−1 min−1 |
4.53 |
This work |
55 °C, k = 2.44 × 10−2 L mol−1 min−1 |
65 °C, k = 2.59 × 10−2 L mol−1 min−1 |
The reaction rate constant obtained from this work is of one order magnitude higher. It is due to the high heating rate of microwave method and the limitations encountered in the conventional heating. In general, rapid microwave heating attributes to direct heating of reaction mixture and thus it creates volumetric and uniform heating. Microwave energy heats the reactants directly by eliminating the wall effects that would have occurred in the conventional heating. Owing to their strong microwave absorption ability, methanol and glycerol absorb microwave energy more readily. This triggered localized molecular superheating above the reaction mixture's bulk temperature34,35 to elevate the chemical reaction. Conversely, the heat which was transferred to the sample volume in the conventional heating was used to increase the temperature of the reaction vessel before it reached its internal reaction mixtures.22 Thus, part of the energy supplied through high temperature heating could have been lost to the environment through conduction of materials and convection currents. Furthermore, in conventional heating, higher thermal gradient and non-uniform heating could have taken place while the reaction mixture in contact with the vessel wall was first heated. Thus, conventional heating is relatively slow and less efficient in transferring energy into the system. As a comparison, the reaction rate constant obtained (2.34–2.59 × 10−2) from microwave heating is one order of magnitude higher than the value reported in the process using conventional heating (1.77–6.15 × 10−3) as listed in Table 7. This has proven that the activation energy required for the microwave irradiation transesterification of crude glycerol can be greatly reduced while producing a high reaction rate.
4. Conclusions
The effect of reaction parameters optimized by Box–Behnken design and RSM on MAT of crude glycerol was adequately investigated. The findings enabling the development of a reduced cubic model with good conformity between the actual experimental conversion rates and the values predicted by the model. The DMC/Gly molar ratio is the most influential parameter on the conversion of glycerol. It is worth noting that at low DMC/Gly molar ratio the interaction with temperature and reaction time cannot be neglected. An optimum yield of 99.5% of GC was predicted using the quadratic model at condition of 65 °C, 3 min, DMC/Gly molar ratio of 2.5 and 1 wt% CaO. An average yield of 97.1% of GC obtained is consistent with the predicted yield. The conversion of GC via MAT of crude glycerol yielded 84.0 ± 2.5% in the temperature range of 45 to 65 °C. The reaction duration is inversely proportional to the reaction temperature. The MAT of crude glycerol fit well to an irreversible second-order kinetic model from 45 to 65 °C. In this study, the microwave assisted transesterification of crude glycerol is energy-efficient, with activation energy being 12 times lower and one order of magnitude higher in the reaction rate than that of the conventional heating system.
Conflicts of interest
There are no conflicts to declare.
Acknowledgements
The authors thank University of Malaya for supporting this research under University of Malaya Research Grant (UMRG) RP002B-13AET
References
-
The Future of the Global Glycerin Market 2019-2022, https://www.businesswire.com/news/home/20190206005393/en/Glycerin---2019-Market-Analysis-Trends-Forecasts Search PubMed.
- M. S. Ardi, M. K. Aroua and N. A. Hashim, Renewable Sustainable Energy Rev., 2015, 42, 1164–1173 CrossRef CAS.
- J. Kaur, A. K. Sarma, M. K. Jha and P. Gera, Biotechnol. Rep., 2020, 27, e00487 CrossRef.
- W. K. Teng, G. C. Ngoh, R. Yusoff and M. K. Aroua, Energy Convers. Manage., 2014, 88, 484–497 CrossRef CAS.
- P. S. Kong, M. K. Aroua and W. M. A. W. Daud, Renewable Sustainable Energy Rev., 2016, 63, 533–555 CrossRef CAS.
- M. Szőri, B. R. Giri, Z. Wang, A. E. Dawood, B. Viskolcz and A. Farooq, Sustainable Energy Fuels, 2018, 2, 2171–2178 RSC.
- M. O. Sonnati, S. Amigoni, E. P. Taffin de Givenchy, T. Darmanin, O. Choulet and F. Guittard, Green Chem., 2013, 15, 283–306 RSC.
- T. W. Turney, A. Patti, W. Gates, U. Shaheen and S. Kulasegaram, Green Chem., 2013, 15, 1925–1931 RSC.
- J. R. Ochoa-Gómez, O. Gómez-Jiménez-Aberasturi, C. Ramírez-López and M. Belsué, Org. Process Res. Dev., 2012, 16, 389–399 CrossRef.
- G. Pradhan and Y. Chandra Sharma, J. Cleaner Prod., 2020, 264, 121258 CrossRef CAS.
- R. R. Pawar, S. V. Jadhav and H. C. Bajaj, Chem. Eng. J., 2014, 235, 61–66 CrossRef CAS.
- S. Nomanbhay, M. Y. Ong, K. W. Chew, P.-L. Show, M. K. Lam and W.-H. Chen, Energies, 2020, 13, 1483 CrossRef CAS.
- W. K. Teng, G. C. Ngoh, R. Yusoff and M. K. Aroua, Chem. Eng. J., 2016, 284, 469–477 CrossRef CAS.
- S. Wang, L. Xu, P. U. Okoye, S. Li and C. Tian, Energy Convers. Manage., 2018, 164, 543–551 CrossRef CAS.
- B. Changmai, I. B. Laskar and L. Rokhum, J. Taiwan Inst. Chem. Eng., 2019, 102, 276–282 CrossRef CAS.
- H. R. Prakruthi, B. S. Jai Prakash and Y. S. Bhat, J. Mol. Catal. A: Chem., 2015, 408, 214–220 CrossRef CAS.
- J. Granados-Reyes, P. Salagre and Y. Cesteros, Appl. Clay Sci., 2018, 156, 110–115 CrossRef CAS.
- A. A. Arpia, W.-H. Chen, S. S. Lam, P. Rousset and M. D. G. de Luna, Chem. Eng. J., 2021, 403, 126233 CrossRef CAS.
- P. D. Rocha, L. S. Oliveira and A. S. Franca, Renewable Energy, 2019, 143, 1710–1716 CrossRef CAS.
- A. Guldhe, B. Singh, I. Rawat and F. Bux, Chem. Eng. Res. Des., 2014, 92, 1503–1511 CrossRef CAS.
- J. Esteban, M. Ladero, L. Molinero and F. García-Ochoa, Chem. Eng. Res. Des., 2014, 92, 2797–2805 CrossRef CAS.
- V. Gude, P. Patil, E. Martinez-Guerra, S. Deng and N. Nirmalakhandan, Sustainable Chem. Processes, 2013, 1, 5–36 CrossRef.
-
B. Kaewsubdejsiri, T. Mueansichai and W. Appamana, Suttichai and Assabumrungrat, presented in part at the The 8th International TIChE Conference (ITIChE 2018), Designing Tomorrow Towards Sustainable Engineering
and Technology, A-ONE The Royal Cruise Hotel Pattaya, Thailand, November 8-9, 2018 Search PubMed.
- Y. M. Kurle, M. R. Islam and T. J. Benson, Fuel Process. Technol., 2013, 114, 49–57 CrossRef CAS.
- L. Zhang, B. Sheng, Z. Xin, Q. Liu and S. Sun, Bioresour. Technol., 2010, 101, 8144–8150 CrossRef CAS.
- J. Y. Min and E. Y. Lee, Biotechnol. Lett., 2011, 33, 1789–1796 CrossRef CAS.
- L. Alsaadi, V. Eze and A. Harvey, Front. Chem., 2018, 6, 625 CrossRef CAS.
- Y. Lee, J. H. Lee, H. J. Yang, M. Jang, J. R. Kim, E.-H. Byun, J. Lee, J.-G. Na, S. W. Kim and C. Park, J. Ind. Eng. Chem., 2017, 51, 49–53 CrossRef CAS.
- G. B. Dudley, R. Richert and A. E. Stiegman, Chem. Sci., 2015, 6, 2144–2152 RSC.
- P. Cintas, S. Tagliapietra, E. Calcio Gaudino, G. Palmisano and G. Cravotto, Green Chem., 2014, 16, 1056–1065 RSC.
- W. Xu, J. Zhou, Z. Su, Y. Ou and Z. You, Catal. Sci. Technol., 2016, 6, 698–702 RSC.
- P. Lidström, J. Tierney, B. Wathey and J. Westman, Tetrahedron, 2001, 57, 9225–9283 CrossRef.
- S. Nomanbhay and M. Y. Ong, Bioengineering, 2017, 4, 57 CrossRef.
- P.-K. Chen, M. R. Rosana, G. B. Dudley and A. E. Stiegman, J. Org. Chem., 2014, 79, 7425–7436 CrossRef CAS.
- N. Sweygers, N. Alewaters, R. Dewil and L. Appels, Sci. Rep., 2018, 8, 7719 CrossRef.
- P. Devi, U. Das and A. K. Dalai, Chem. Eng. J., 2018, 346, 477–488 CrossRef CAS.
- B. Das and K. Mohanty, J. Environ. Chem. Eng., 2019, 7, 102888 CrossRef.
- G. D. Yadav and P. A. Chandan, Catal. Today, 2014, 237, 47–53 CrossRef CAS.
- Y. Qing, H. Lu, Y. Liu, C. Liu, B. Liang and W. Jiang, Chin. J. Chem. Eng., 2018, 26, 1912–1919 CrossRef CAS.
- J. Esteban, E. Domínguez, M. Ladero and F. Garcia-Ochoa, Fuel Process. Technol., 2015, 138, 243–251 CrossRef CAS.
Footnote |
† Electronic supplementary information (ESI) available. See DOI: 10.1039/d0se01383h |
|
This journal is © The Royal Society of Chemistry 2021 |
Click here to see how this site uses Cookies. View our privacy policy here.