DOI:
10.1039/D1RA06751F
(Paper)
RSC Adv., 2021,
11, 31448-31459
A new phase transfer nanocatalyst NiFe2O4–PEG for removal of dibenzothiophene by an ultrasound assisted oxidative process: kinetics, thermodynamic study and experimental design
Received
8th September 2021
, Accepted 8th September 2021
First published on 22nd September 2021
Abstract
In this study, NiFe2O4–PEG, an effective nanocatalyst was synthesized via a hydrothermal method using different PEG concentrations and synthesis times. The synthesized nanocatalyst was used in the ultrasound assisted oxidative desulfurization (UAOD) of model fuels (e.g. n-hexane and dibenzothiophene (DBT)) for the first time. The nanocatalyst was then characterized by XRD, FTIR, BET, SEM, VSM and TEM analyses. In addition, central composite design was used to evaluate the effective variables on the UAOD process. The optimal values of effective factors such as catalyst dose, oxidant amount, irradiation time and ultrasonic power to maximize of the percentage of sulfur removal were 0.149 g, 15 mL, 11.96 min, and 70 MHz, respectively. Moreover, the kinetic aspects of the oxidation reaction of DBT in the UAOD process were investigated using a pseudo-first-order model. Furthermore, using the Arrhenius equation, an activation energy of 35.86 kJ mol−1 was obtained. Additionally, thermodynamic analysis showed that the oxidation reaction of DBT was endothermic with a positive Gibbs free of energy, indicating the non-spontaneity of oxidation of DBT in the UAOD process. Moreover, the conversion rate of DBT has increased from 57% at 35 °C to 85% at 65 °C.
1. Introduction
Liquid fuels consist of various organosulfur compounds such as sulfides, disulfides, thiophenes and their corresponding derivatives. Sulfur is emitted in the form of sulfur dioxide (SO2) upon burning liquid fuels, which is harmful for human health and the environment as a whole.1 Therefore, reducing the amount of sulfur has become one of the most important activities of refineries. Different methods such as hydrodesulfurization (HDS) have been used to remove sulfur from hydrocarbon fuels. However, this process is not effective in eliminating BT, DBT and 4,6-DMDBT from fossil fuels.2,3 Deep HDS is an alternative method for the production of ultra-low sulfur diesel fuel. However, this method requires over a three-fold increase in the catalyst volume/reactor size and harsh reaction conditions, making it extremely expensive.4–6 Oxidative desulfurization (ODS) is an alternative method for the latter method since it can be performed under mild conditions (low temperature and pressure), is highly selective and does not require the application of expensive hydrogen in the process.7–9 In ODS, sulfur compounds are oxidized into the corresponding sulfoxides and sulfones via the electrophilic addition of oxygen using a catalyst and an oxidizing agent.10,11 A wide range of oxidants such as hydrogen peroxide,12 Fenton reagent,13 ozone14 and molecular oxygen15 have been used to oxidize organosulfur compounds to sulfoxides and/or sulfones. One of the most widely used oxidants for the sulfur removal is hydrogen peroxide because of its cheap price, ease of accessibility, and environmentally benign nature.16,17 However, there are still some drawbacks associated with ODS process including the insolubility of the organosulfur substrate and oxidant, resulting in their reaction merely at the interface. Consequently, the conversion and reaction rates of sulfur compounds are reduced. Therefore, ultrasound technology has been used to increase the efficiency of ODS method.18–20 The advantage of ultrasound assisted oxidative desulfurization (UAOD) method over ODS is the higher desulfurization rate because ultrasound irradiation is an effective method for enhancing the interfacial area between the fuel and oxidant through the generation of cavitation and microstreaming.21 In contrast, phase transfer catalysts (PTC) or phase transfer agents (PTA) possessing exceptional capability of dissolution in both organic and aqueous phases have been used in the ODS process.22 In fact, PTC is used to enhance mass transfer in emulsion systems.23,24 Collins et al.16 employed PTC for oxidation of sulfur compounds in fuels. Jiarong et al.25 reported that the main problem related to PTC was its recovery in the industry. Therefore, in the present work, attempt has been made to solve the problem of PTC recovery by using the magnetic property of metal oxides. In addition, significant types of metal oxides are spinel ferrite (SF) magnetic compounds. In this study, phase transfer nanocatalysts of polyethylene glycol have been synthesized and characterized using magnetic nickel ferrite. NiFe2O4–PEG has also been prepared by hydrothermal method with different concentrations of PEG during various reaction times. In addition, the effects of catalyst amount, irradiation time, amount of oxidant and ultrasound frequency on the DBT oxidation in the UAOD process were investigated. The kinetic and thermodynamic properties of dibenzothiophene oxidation including ΔH°, ΔG° and ΔS° have also been investigated. The model developed by Zhao et al.26 has been used to study the kinetics of the oxidation reaction of DBT in the UAOD process.
2. Experimental section
2.1. Materials
Commercially available chemicals and solvents were used with no further purification. Dibenzothiophene (DBT), n-hexane, hydrogen peroxide (H2O2 30 vol%), nickel nitrate Ni(NO3)2·6H2O, ferric nitrate Fe(NO3)3·9H2O and polyethylene glycol (PEG 4000) were purchased from Sigma Aldrich Chemical Co.
2.2. Synthesis of the phase-transfer-type (NiF2O4–PEG) nanocatlyst
0.2 g of Ni(NO3)2·6H2O, 0.68 g of Fe(NO3)3·9H2O and 0.86 g of carbohydrate (sucrose) were all dissolved in 10 mL of distilled water. The solution (i) obtained was then stirred using a magnetic stirrer to obtain a clear solution. A solution (ii) of PEG was next prepared in two concentrations of (5% and 7%) in distilled water. Afterwards, 10 mL of PEG solution (ii) were added to solution (i). After continuous stirring at 400 rpm for an hour, a homogenous solution was obtained, which was then transferred to a Teflon container and placed in a hydrothermal furnace at 150 °C for different hydrothermal synthesis times (5, 7, and 10 hours). Subsequently, after cooling the sample to room temperature, it was centrifuged and consecutively washed 3 times with distilled water and ethanol, respectively, to remove the impurities. And finally dried in a vacuum oven at 25 °C for 12 h.
2.3. UAOD process of prepared model fuel
The model fuel was obtained by dissolution of dibenzothiophene (DBT) in n-hexane to prepare a 200 ppm concentration of sulfur. Appropriate volumes of model fuel with phase transfer type (NiFe2O4–PEG) nanocatalyst and hydrogen peroxide as oxidizing agent were added into the reaction vessel. The mixture obtained was subjected to ultrasonication (Model HD3400, Bandelin, Germany) for a specific time. The oxidation reaction of DBT was performed in the temperature range of 35° to 65 °C to obtain the activation energy. The ultrasonic probe was immersed in the reaction vessel center at three quarters of the solution depth. Ultrasonic intensities were evaluated at different values of 30, 50 and 70 MHz at different time intervals (5, 10 & 15 min). The mixture was then centrifuged after cooling to separate the organic and aqueous phases. Sulfur concentration was measured using a Petro test X-ray fluorescence sulfur meter (Tanaka scientific Ry-360sH), according to ASTM D-42946. The efficiency of the UAOD was calculated using the following equation: |
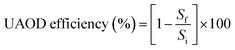 | (1) |
where Sf and Si are the final and initial concentrations (mg L−1) of DBT in the solution, respectively.
2.4. Design of experiment
A multi-variable of the response surface design, central composite design (CCD), was used to evaluate the effects of process variables including the catalyst dose, oxidant amount, irradiation time and ultrasonic power on sulfur removal percentage (response), facilitating the data fitting through the quadratic model. The levels of the independent factors were coded as −1, 0 and 1 for low, central or middle, and high points, respectively. Table 1 shows the ranges and levels of the variables in the coded units based on RSM studies. The experimental data were then evaluated using Minitab 18 (trial version) including ANOVA to determine the responses and interactions between the processed variables. In this work, 25 experiments was carried out to investigate the effects of the four main independent variables including irradiation time (X1), oxidant amount (X2), catalyst dose (X3) and ultrasonic power (X4) on sulfur removal efficiency.
Table 1 Levels of factors in response surface design
Factors |
Levels |
−1 |
0 |
1 |
Irradiation time (min), X1 |
5 |
10 |
15 |
Oxidant amount (mL), X2 |
5 |
10 |
15 |
Catalyst dose (g), X3 |
0.05 |
0.1 |
0.15 |
Ultrasonic power (MHz), X4 |
30 |
50 |
70 |
3. Results and discussion
3.1. Nanocatalyst characteristics
3.1.1. SEM EDS images. SEM was used to determine the microstructure of the synthetic products. The Scanning Electron Microscopy (SEM) images of hybrid nanocatalysts based polyethylene glycol (PEG) with different selected PEG contents are shown in Fig. 1. The SEM images of NiFe2O4–7% PEG (5 h, 7 h, 10 h) nanocatalysts are shown in Fig. 1(a–c), respectively. The SEM images of NiFe2O4–5% PEG (5 h, 7 h, 10 h) nanocatalysts are shown in Fig. 1(d–f), respectively. It is clear that all micrographs show two phases in almost good dispersion and high degree of homogeneity. The magnetic phase is arranged or distributed in a circular manner, forcing the other phase to fellow the same trend. It is also observed that as the PEG wt% ratio increases, its density increases in the nanocatalyst and hence the arrangements or the distribution of PEG become better and clearer. In addition, it is clearly observed in the micrographs that the average grain size of PEG increases as its ratio increases. According to the EDS spectrum the presence of Fe, Ni, O and C can confirm the high purity of products.
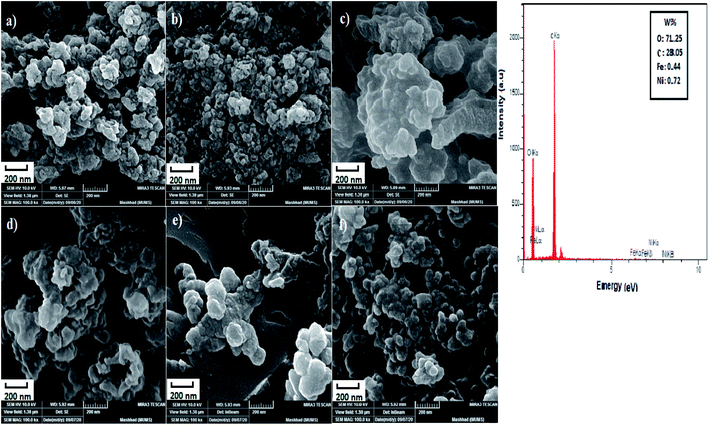 |
| Fig. 1 SEM images of (a–c) NiFe2O4–7% PEG (5 h, 7 h, 10 h), (d–f) NiFe2O4–5% PEG (5 h, 7 h, 10 h) in 200 nm and EDS images of NiFe2O4–7% PEG (10 h). | |
3.1.2. XRD analysis. The XRD patterns of NiFe2O4–PEG nanocatalysts, indicating phase type, crystal structure, product purity and the size of crystalline grains. Fig. 2 show the XRD images of NiFe2O4–7% PEG (10 h). The PEG with a well-defined crystal structure, strong reflection peaks at 19.23° and 23.35° and weak reflection peaks at 26.09°, 35.25° and 38.91° has a high crystalline nature. The crystalline peaks of PEG and nickel ferrite are also observed in the structures of all the related nanocatalysts, which indicates the presence of PEG in the samples. All of the diffraction peaks observed is indexed by the NiFe2O4 cubic structure of (JCPDS no. 19-629). The line profile, which is shown in Fig. 2, corresponds to the eleven peaks with the following miller indices: (111) (220) (311) (400) (422) (511) (440). Using Scherer equation below, the crystal size of NiFe2O4 was found to be 53 nm. |
 | (2) |
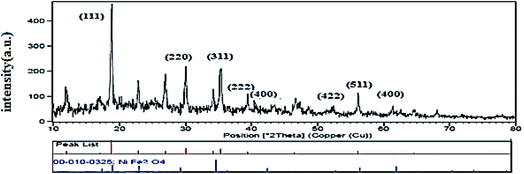 |
| Fig. 2 XRD pattern of NiFe2O4–7% PEG (10 h). | |
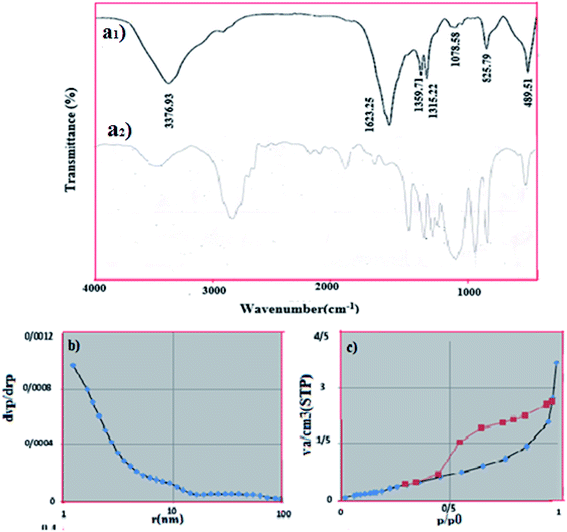 |
| Fig. 3 (a) ((a1) FT-IR spectrum of obtained NiFe2O4–PEG (a2) pure PEG), (b) N2 adsorption–desorption isotherm (c) pore size of NiFe2O4–7% PEG (10 h). | |
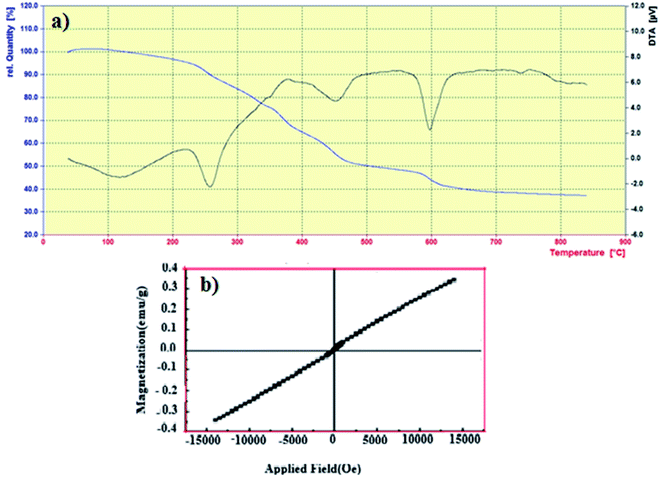 |
| Fig. 4 (a) TGA curve of NiFe2O4–7% PEG (10 h) (b) VSM curve of NiFe2O4–7% PEG (10 h) nanocatalyst. | |
In which D, θ, λ, and FWHM are the size of the crystal, Bragg angle of peaks (°), wavelength (0.154 nm) and full width at half maximum (rad), respectively, and k is a constant equal to 0.89.
3.1.3. FTIR analysis. Fig. 3(a1) shows the FTIR spectra of NiFe2O4–PEG nanocatalyst in the range of 4000–400 cm−1. It is revealing clear that the broad peaks observed at respectively are attributed to the adsorbed water and PEG, respectively, corresponding which are assigned to the vibration of OH and H–O–H groups. The two bands at 825.76 and 489.51 cm−1 are attributed to the stretching vibrations of Fe
O and Ni
O, respectively.27 The intense peak at 3376.93 cm−1 and the less intensive one at 1624 cm−1 are ascribed to the stretching vibration between hydrogen and oxygen atoms.28,29 Fig. 3(a2) shows the FTIR spectra of pure PEG, that shows many characteristic peaks at 3423, 2878, 1965, 1648, 1467,1343, 1281, 1243, 1114, 963, 843 and 530 cm−1 matching with the reported results.30,43
3.1.4. BET results. The specific surface area of NiFe2O4–PEG nanocatalyst was determined using Brunauer–Emmett–Teller (BET). Fig. 3(b) shows the corresponding N2 adsorption/desorption isotherm, which indicates a porous structure (isotherm type IV and H2-type hysteresis) for this compound. H2-Type hysteresis loop is associated with porous compounds, based on the IUPAC classification. BET surface area was 2.5001 m2 g−1. The micropore diameter was found to be 1.21 nm by BJH method (Fig. 3(c)).
3.1.5. TGA analysis. Thermal stability of NiFe2O4–7% PEG (10 h) nanocatalyst was investigated using TGA analysis in Fig. 4(a) In the TG curve, weight loss of about 28% is observed in the temperature range of 25–800 °C, which is related to the relatively strong bonding force between PEG and Fe2O3 nanoparticles, so it can be concluded that PEG is located on the surface of ferrite nickel nanoparticles. It is observed that a small fraction of weight loss from room temperature to 100 °C is related to the evaporation of water absorbed in the sample. In the DTA curve, two weight losses of about 280 and 470 are related to the thermal oxidative decomposition of PEG polymer.31,32
3.1.6. VSM analysis. In order to study the effect of PEG on the magnetic behavior of the nanocatalysts prepared, magnetization measurements were performed. Fig. 4(b) shows the magnetic hysteresis loop. The saturation magnetization (Ms) and coercivity (Hc) of the NiFe2O4 nanoparticles were 0.3428 emu g−1 and 14
000 Oe, respectively. Clear hysteresis loops were shown by the magnetization of the samples under the applied field demonstrated due to their ferromagnetic behavior.30
3.1.7. TEM images. Fig. 5 shows the TEM images in four different scales. The dark field images exhibit the polyethylene glycol catalyst. On the other hand, the presence of nanocrystals between 100, 60, 40 and 20 nm is observed in bright field mode. TEM analysis shows that the use of PEG has increased the crystallization and reduced the agglomeration of nanoparticles as well as controlling their spherical shape.
3.2. UAOD results of prepared model fuel
The NiFe2O4–PEG nanocatalysts were synthesized using different amounts of PEG and hydrothermal reaction times. Fig. 6 displays the comparison of the performances of NiFe2O4–PEG 5% (5 h, 7 h, 10 h) and PEG 7% (5 h, 7 h, 10 h) nanocatalyst in the desulfurization process. Fig. 6 for picted in Fig. 5, NiFe2O4-7% PEG (10 h) nanocatalyst shows the best performance among all nanocatalysts due to the highest PEG wt% with growth of oxidation of DBT. Furthermore, increasing the hydrothermal synthesis time resulted in the better homogeneity of nickel ferrite particles. A comparison of the nanocatalysts in this work with those reported in the literature is given in Table 2. The literature reports mainly deal with high concentrations (>500 ppm) of sulfur while the least concentration of sulfur (200 ppm) was used in this work. Thus, the nanaocatalysts used in this work showed better efficiencies compared with those reported in the literature because desulfurization of fuels with low sulfur concentrations is difficult (Fig. 6).
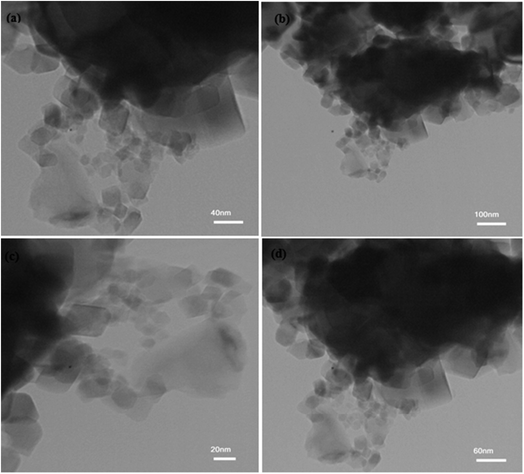 |
| Fig. 5 TEM images of NiFe2O4–7% PEG (10 h) nanocatalyst in four different scales (a) 40 nm (b) 100 nm (c) 20 nm (d) 60 nm. | |
Table 2 Presents a summary of previous literature in oxidative desulfurization with PTAa
Sl. no |
Authors |
Reaction conditions |
PTA |
Oxidation system |
% reduction |
TOAB – tetraocthyl ammonium bromide, TBAB – tetrabuthyl ammonium bromide, TBAB – tetrabutyl ammonium bromide, TOBA – tetraoctyl bromide ammonium MBAH – methyltributyl ammonium hydroxide, TODAB – tetraoctadecyl ammonium bromide, TOAF – tetraoctyl ammonium fluoride, TDAB – tetradecyl ammonium bromide. Tem – temperature, vol – volume, str – stirrer speed, US freq – ultrasound frequency. |
1 |
Sachdeva et al.,45 |
DBT (325 ppm); solv.: octane normal; tem.: 70 °C; str.: 1000 rpm |
TOAB |
H2O2/phosphotungstic acid |
98 |
2 |
Zhao et al.,26 |
DBT (600 ppm); solv.: heptane normal; tem.: 45 °C; str.: 200 rpm |
TBSB |
H2O2/CH3COOH |
86.4 thiophene, 97.5 DBT |
3 |
Mei et al.,38 |
Thiophene (400 ppm); react vol.: 50 mL; US freq.: 20 kHz; tem.: 75 °C |
TOBA |
H2O2/phosphotungstic acid |
98 |
4 |
Chen et al.,47 |
Thiophene + DBT (960); solv. toluene; tem.: 88 °C; US freq.: 20 kHz |
TOAB |
H2O2/phosphotungstic acid |
88.4 |
5 |
Wan et al.,48 |
DBT + BT + thiophene + 2-methyl-T + 4-methyl-DBT |
TOAF TDAB, TOAB, TBAB |
H2O2/phosphotungstic acid |
90.3, 59.9, 43.6, 38.3 |
6 |
Rezvani et al.,39 |
BT + DBT + 4,6-DMDBT + 4-methyl-DBT (500 ppm); solv.: n-heptan; tem; 60 °C; str.: 500 rpm |
(TBA)4PW11Fe@pbo |
H2O2/CH3COOH |
97 |
7 |
Rezvani et al.,49 |
Gasoline + BT + TH + DBT (500 ppm); react vol.: 50 mL; tem.: 35 °C; str.: 600 rpm |
PMOCu–MgCu2O4@PVA |
H2O2/CH3COOH |
Gasoline: 97, DBT: 99, BT: 97, TH: 98 |
9 |
Cuihong Zhou et al.,50 |
Crude oil + gasoline; tem.: 50 °C |
— |
H2O2/HCOOH/PW/acetonitrile/methanol |
Crude oil: 72, gasoline: 81 |
10 |
Najafi et al.,51 |
Diesel (7240 ppm) |
Fe2SO4 |
H3PO4/H2O2 |
69 |
11 |
Present work |
DBT(200 ppm); solv.: n-hexane; tem.: 35 °C; US freq.: 70 MHz; react vol.: 40 mL |
NiFe2O4–PEG |
H2O2 |
85 |
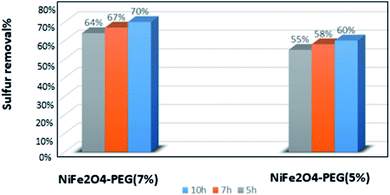 |
| Fig. 6 Comparison between the performance of NiFe2O4–PEG with different cases of PEG and different synthesis times. | |
3.3. Kinetics of the DBT oxidation reaction
To describe the kinetics of the oxidation reaction of DBT, the pseudo-first-order equation was used in the temperatures range of 35 to 65 °C in the UAOD process. The pseudo-first-order kinetic models are described by eqn (3): |
 | (3) |
In which C0 and C (ppm) are the sulfur concentrations at initial and time t (min), respectively. A straight line of ln(C/C0) vs. t was employed to calculate K (L min−1) (Fig. 7(a)). In addition, the correlation coefficients (R2) obtained was close to one. Therefore, according to these result, the experimental data well fit pseudo-first-order model.33–35
 |
| Fig. 7 (a) The plot of ln c/c0 versus time at different temperature, (b) Arrhenius plot (b). | |
3.3.1. Arrhenius (kinetic) and thermodynamic analysis. Arrhenius analysis was carried out using pseudo-first-order kinetic constants at different temperatures. The Arrhenius equation is shown by eqn (4): |
 | (4) |
In which T and R are the reaction temperature and universal gas constant, respectively. Furthermore, Ea represents the activation energy, which can be obtained by plotting the ln
K, vs. 1/T (Fig. 7(b)), leading to Ea of 35.86 kJ mol−1.36 In addition, the presence of metal ions and ultrasound in the reaction system has caused relatively low activation energy.37
Eyring equation could be used to obtain the thermodynamic parameters of the oxidative desulfurization process:
|
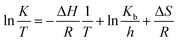 | (5) |
where
h and
Kb are Planck and Boltzmann constants, respectively. Arrhenius analysis results were used to determine Δ
H°, Δ
G° and Δ
S° thermodynamic parameters. The Arrhenius and thermodynamic parameters of the UAOD process at various temperatures are summarized in
Table 3. As observed in the table, the values of
K increase with increasing temperature. Additionally, positive values of Δ
G° indicate that the oxidation reaction of DBT is non-spontaneous. Increasing the Δ
G° values with increasing temperature indicates that higher temperatures improve the reaction. Positive Δ
H° values have been obtained for the oxidation reaction of DBT, indicating that the process is endothermic. Negative values of Δ
S indicate a decrease in stochasticity as a result of the oxidation reaction.
Table 3 Thermodynamic parameters for removal of DBT from model fuel in UAOD process
Temperature (K) |
K (Arrhenius constant) |
ΔH° (kJ mol−1) |
ΔG° (kJ mol−1) |
ΔS° (kJ mol−1 K−1) |
308 |
0.0090 |
33.26 |
85.62 |
−0.170 |
318 |
0.0140 |
33.18 |
88.83 |
−0.175 |
328 |
0.0218 |
33.10 |
90.82 |
−0.176 |
338 |
0.0324 |
33.01 |
92.70 |
−0.177 |
3.4. Proposed mechanism of UAOD oxidation reaction
In the UAOD system containing metal catalysts, PTA and heat, hydrogen peroxide is converted to hydroxyl free radicals. The hydroxyl free radicals then form superoxide. Afterwards, terminal metal atoms (M = Ni or Fe) in the NiFe2O4–PEG accept active oxygen from superoxide and Fe2+ is readily oxidized into Fe3+, which reacts with DBT molecules, leading to sulfones.38 The PEG present in the nanocatalyst acts as the PTA and increases the mass transfer at the interface, thus facilitating the transfer of peroxo-metal anions into the oil phase.39 The transient cavitation, ultrasound, and PTA effective interphase transport of the oxidant were produced synergistically affect influence of fine emulsification, which leads to approximately thorough removal of DBT from the model oil.40 Therefore, the character of cavitation and ultrasound in PTC assisted ultrasonic oxidative desulfurization is the physical process, which enhances DBT oxidation. The mechanism described in Fig. 8 is shown.
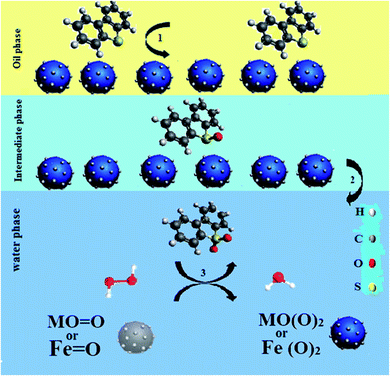 |
| Fig. 8 Schematic illustration of the probable mechanism for the oxidation sulfur containing compounds. | |
3.5. Optimization of UAOD parameters
In order to optimization the UAOD operating conditions, the effect of four parameters (i.e., catalyst dose, oxidant amount, irradiation time and ultrasonic power) on the sulfur removal percentage were studied by employing the CCD method. In Table 4 are presented the runs of the experiments and the response values for each test. Based on the CCD, the regression equation to describe a mathematical correlation between the sulfur removal percentage (Y) and the selected parameters (i.e., X1, X2, X3 and X4) is expressed by the following second-order polynomial equation:41,42 |
DBT removal (%) = 43.3898 + 3.6667X1 + 13.0556X2 + 6.8611X3 + 7.3056X4 − 5.2881X12 + 11.2119X22 − 4.5381X32 − 0.0625X1X2 − 1.0625X1X3 + 0.75X1X4 + 1.25X2X3 + 0.9375X2X4 − 0.3125X3X4
| (8) |
Table 4 The 22 response surface design
Experimental run |
Oxidant amount (mL) |
Irradiation time (min) |
Catalyst dose (mg) |
Ultrasonic power (kHz) |
Desulfurization rate (%) |
1 |
15 |
10 |
0.10 |
50 |
73.5 |
1 |
15 |
10 |
0.10 |
50 |
73.5 |
2 |
15 |
15 |
0.05 |
70 |
65.5 |
3 |
10 |
10 |
0.10 |
50 |
39.5 |
4 |
10 |
5 |
0.10 |
50 |
40.0 |
5 |
5 |
10 |
0.15 |
50 |
50.0 |
6 |
10 |
5 |
0.05 |
70 |
58.5 |
7 |
15 |
15 |
0.05 |
30 |
52.5 |
8 |
5 |
5 |
0.15 |
70 |
72.5 |
9 |
5 |
15 |
0.05 |
70 |
46.5 |
10 |
5 |
5 |
0.05 |
30 |
22.5 |
11 |
10 |
15 |
0.15 |
30 |
66.0 |
12 |
10 |
10 |
0.10 |
50 |
32.0 |
13 |
5 |
15 |
0.05 |
30 |
30.0 |
14 |
5 |
5 |
0.05 |
30 |
42.5 |
15 |
15 |
10 |
0.10 |
70 |
66.5 |
16 |
15 |
5 |
0.05 |
70 |
29.5 |
17 |
15 |
10 |
0.10 |
30 |
35.0 |
18 |
15 |
15 |
0.15 |
30 |
40.0 |
19 |
5 |
15 |
0.10 |
50 |
40.0 |
20 |
5 |
10 |
0.05 |
50 |
31.5 |
21 |
10 |
5 |
0.15 |
70 |
45.0 |
22 |
5 |
5 |
0.15 |
30 |
60.5 |
23 |
15 |
15 |
0.15 |
70 |
82.5 |
24 |
10 |
15 |
0.15 |
70 |
50.0 |
25 |
15 |
5 |
0.15 |
30 |
36.0 |
According to eqn (8), negative signs show antagonistic effects whiles positive ones indicate synergistic effects. Moreover, Table 5 presents the result of analysis of variance (ANOVA) obtained by this study. This table gives linear terms of the four variables (i.e., X1, X2, X3 and X4) are statistically significant (p < 0.05). The results showed the coefficient of determination of R2 = 0.93 represents a favorable value for model validation. Also, from the F-value of the model (29.59) in the ANOVA table, it can be inferred that the model is significant and it is evident that catalyst dose and oxidant amount are the most important factors in the proposed correlation (e.g. eqn (8)). It can be concluded that oxidant amount is the most effective parameter on the removal efficiency of DBT. Furthermore, Fig. 9(a) displays the normal probability plot of residuals used to examine the normal distribution of standard deviations. As shown, the majority of residuals follow a straight line with minimal variations from their directions. In addition, Fig. 9(b) depicts the plot of the predicted responses against residuals. Based on the data, all the points in the experimental runs are randomly distributed around the average of the response variable, indicating that the proposed model is sufficient.
Table 5 Estimated regression coefficient for the model
Source |
Sum of squares |
Degrees of freedom |
Mean square |
F-Value |
P-Value |
Model |
5736.57 |
14 |
409.75 |
29.59 |
0001.0> |
Irradiation time-X1 |
242 |
1 |
242.06 |
5.60 |
0.040 |
X2-Oxidant amount |
3068.06 |
1 |
3068.06 |
70.96 |
0001.0> |
Catalyst dose-X3 |
847.35 |
1 |
847.35 |
19.60 |
0.001 |
Ultrasonic power-X4 |
960.68 |
1 |
960.68 |
3.18 |
0.001 |
X12 |
20.81 |
1 |
71.22 |
1.65 |
0.228 |
X22 |
428.43 |
1 |
320.14 |
7.40 |
0.022 |
X32 |
25.52 |
1 |
52.45 |
1.21 |
0.297 |
X42 |
75.97 |
1 |
75.97 |
0.26 |
0.214 |
X1X2 |
70.06 |
1 |
0.06 |
0 |
0.970 |
X1X3 |
18.06 |
1 |
18.06 |
0.42 |
0.533 |
X1X4 |
9.00 |
1 |
9.00 |
0.21 |
0.658 |
X2X3 |
25.00 |
1 |
25.00 |
0.58 |
0.465 |
X2X4 |
4.06 |
1 |
14.06 |
0.33 |
0.581 |
X3X4 |
1.56 |
1 |
1.25 |
0.04 |
0.853 |
Residual error |
432.37 |
10 |
43.24 |
|
|
Total |
6168.94 |
24 |
|
|
|
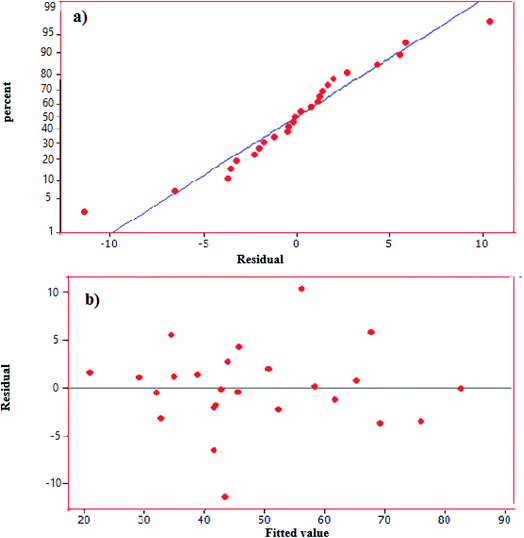 |
| Fig. 9 (a) Normal probability plot of residuals, (b) plot of residual versus predicted values. | |
3.6. Response surface and contour plots
Three dimensional (3D) surface and (2D) contour plots are the graphs, which can be used to investigate the interactive effects of the selected factors on the oxidation reaction of DBT in UAOD process. The resulted surface response 3-D plots of conversion as a function of two independent variables, (a) X4 and X1; (b) X4 and X3; (c) X3 and X1; (d) X3 and X2; (e) X2 and X4; (f) X2 and X1 are shown in Fig. 10(a–f) respectively. Also, the 2-D contour plots are shown in Fig. 11(a–f). According to surface and contour plots, the DBT removal efficiency was set to be maximum while ultrasonic power and oxidant amount dose were set at the maximum value and the other parameters were kept in range. It was also discovered that when ultrasonic power, irradiation time, oxidant amount and catalyst dose were set to 70 MHz, 11.96 min, 15 mL, and 0.14 g respectively, the maximum conversion reached 85.5%.
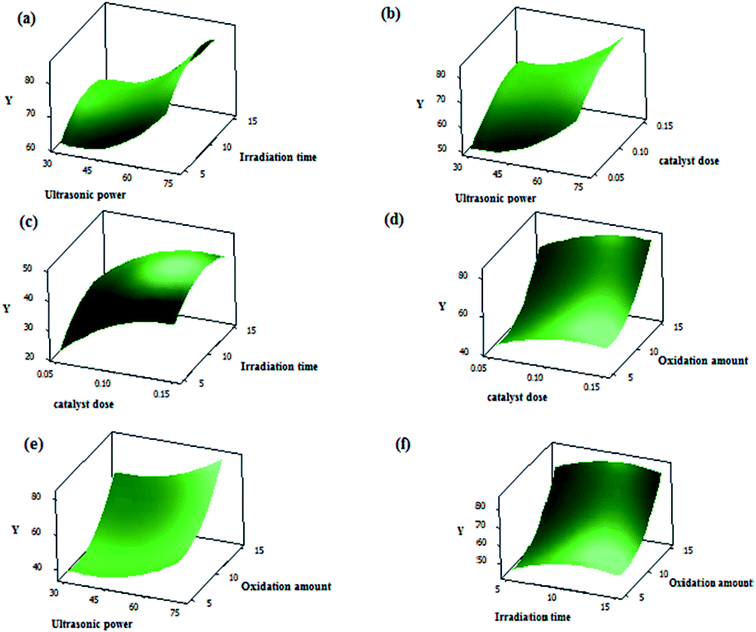 |
| Fig. 10 (a) 3-D plot of conversion vs. ultrasonic power and irradiation time, (b) 3-D plot of conversion vs. ultrasonic power and catalyst dose, (c) 3-D plot of conversion vs. catalyst dose and irradiation time, (d) 3-D plot of conversion vs. catalyst dose and oxidation amount, (e) 3-D plot of conversion vs. oxidant amount and ultrasonic power, (f) 3-D plot of conversion vs. oxidant amount and irradiation time. | |
3.7. Regeneration experiments
Phase transfer catalyst regeneration is a significant parameter for industrial applications. The nanocatalyst selected from Fig. 6 was used in the recovery experiments. 0.15 gr of the nanocatalyst and 15 mL of H2O2 were used per 15 mL of the model fuel (DBT and n-hexane) in the UAOD process. The catalyst was removed from the reaction mixture by filtration, washed with ethanol, and finally dried at 90 °C for 1 hour. As shown in Fig. 12, after three regeneration cycles, the conversion rate of DBT has decreased from 85% to 78%, which could be due to the deposition of the produced sulfone on the nanocatalyst active sites, which results in a decrease in the catalyst activity.43,44,46
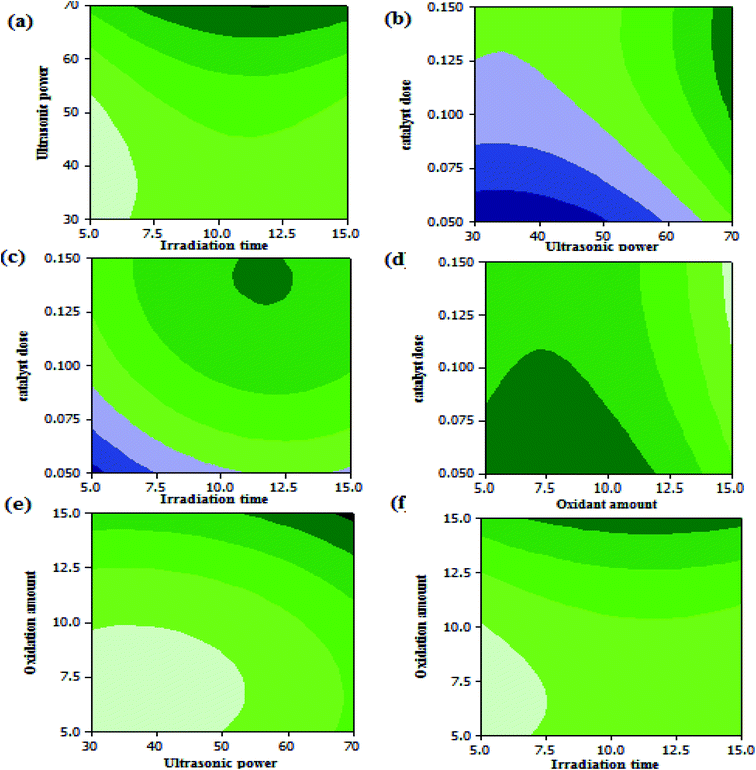 |
| Fig. 11 (a) contour plots of ultrasonic power vs. irradiation time, (b) ultrasonic power and catalyst dose, (c) catalyst dose vs. irradiation time, (d) catalyst dose vs. oxidant amount , (e) oxidation amount vs. ultrasonic power (f) oxidant amount vs. irradiation time. | |
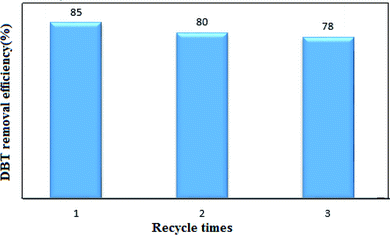 |
| Fig. 12 Recyclability performance of nanocatalyst in UAOD of DBT. | |
4. Conclusions
Efficient AFe2O4–PEG nanocatalysts were synthesized by hydrothermal method and the effect of different concentrations of PEG (5% and 7%) and various synthesis times were investigated. The nanocatalyst was then used in the UAOD process for the removal of DBT from a model fuel. According to the results, NiFe2O4–PEG was prepared with 7 wt% of PEG and 10 hour hydrothermal times demonstrated the best performance in comparison to other nanocatalysts. Furthermore, based on the experimental design, the optimal conditions for the UAOD process were nanocatalyst dose of 0.14 gr, irradiation time of 11.96 min, ultrasonic power of 70 MHz, and oxidant amount of 15 mL. The kinetic data show that the pseudo-first order model best describes the oxidation reaction of DBT in the UAOD process. Moreover, based on the results of the thermodynamic studies for determining the entropy, enthalpy and Gibbs free energy, the oxidation of DBT is an exothermic and non-spontaneous reaction. From Arrhenius analysis, the activation energy was obtained as 35.86 kJ mol−1. In addition, the results confirmed that the increase in temperature led to the considerable improvement of the removal efficiency. However, selecting a suitable PTC is regarded an essential challenge in the UAOD process. The present nanocatalyst can be a good candidate for the removal of other sulfur compounds. The present approach, which is based on the application of mild operating conditions, high DBT conversion, and a simple mechanism, can be further developed for the industrial desulfurization of hydrocarbon fuels.
Conflicts of interest
The authors of this manuscript declare that they have no conflict of interest.
Acknowledgements
The authors acknowledge the University of Kashan by Grant No. (159271/SMT3), Semnan University and Iran National Science Foundation (INSF, 97017837) for supporting this investigation.
References
- C. Malins, E. Dumitrescu, D. Kodjak, R. de Jong, S. Galarza, J. Akumu and B. Fabian, Report, 2016 Search PubMed.
- H. Li, W. Zhu, S. Zhu, J. Xia, Y. Chang, W. Jiang, M. Zhang, Y. Zhou and H. Li, AIChE J., 2016, 62, 2087–2100 CrossRef CAS.
- D. Zhang, H. Tao, C. Yao and Z. Sun, Chem. Eng. Sci., 2017, 174, 203–221 CrossRef CAS.
- L. Dong, G. Miao, X. Ren, N. Liao, A. W. Anjum, Z. Li and J. Xiao, Ind. Eng. Chem. Res., 2020, 59, 10130–10141 CrossRef CAS.
- J. Zou, Y. Lin, S. Wu, M. Wu and C. Yang, Sep. Purif. Technol., 2021, 264, 118434 CrossRef CAS.
- J. Zou, Y. Lin, S. Wu, Y. Zhong and C. Yang, Adv. Funct. Mater., 2021, 31, 2100442 CrossRef CAS.
- W. N. W. Abdullah, W. A. W. A. Bakar, R. Ali, W. N. A. W. Mokhtar and M. F. Omar, J. Cleaner Prod., 2017, 162, 1455–1464 CrossRef CAS.
- M. d. C. Capel-Sanchez, P. Perez-Presas, J. M. Campos-Martin and J. Fierro, Catal. Today, 2010, 157, 390–396 CrossRef CAS.
- J. M. Campos-Martin, M. Capel-Sanchez, P. Perez-Presas and J. Fierro, J. Chem. Technol. Biotechnol., 2010, 85, 879–890 CrossRef CAS.
- C. Song and X. Ma, Appl. Catal., B, 2003, 41, 207–238 CrossRef CAS.
- A. W. Bhutto, R. Abro, S. Gao, T. Abbas, X. Chen and G. Yu, J. Taiwan Inst. Chem. Eng., 2016, 62, 84–97 CrossRef CAS.
- A. M. Dehkordi, M. A. Sobati and M. A. Nazem, Chin. J. Chem. Eng., 2009, 17, 869–874 CrossRef CAS.
- Y. Dai, Y. Qi, D. Zhao and H. Zhang, Fuel Process. Technol., 2008, 89, 927–932 CrossRef CAS.
- J. Behin and N. Farhadian, Ultrason. Sonochem., 2017, 38, 50–61 CrossRef CAS PubMed.
- H. Lü, J. Gao, Z. Jiang, Y. Yang, B. Song and C. Li, Chem. Commun., 2007, 150–152 RSC.
- F. M. Collins, A. R. Lucy and C. Sharp, J. Mol. Catal. A: Chem., 1997, 117, 397–403 CrossRef CAS.
- A. E. S. Choi, S. Roces, N. Dugos, C. M. Futalan, S.-S. Lin and M.-W. Wan, J. Taiwan Inst. Chem. Eng., 2014, 45, 2935–2942 CrossRef CAS.
- L. Thompson, Science and engineering, Ind. Eng. Chem. Res., 1999, 38, 1215–1249 CrossRef CAS.
- J.-L. Luche, Synthetic organic sonochemistry, Springer Science & Business Media, 2013 Search PubMed.
- Y. T. Shah, A. Pandit and V. Moholkar, Cavitation reaction engineering, Springer Science & Business Media, 1999 Search PubMed.
- K. Keynejad, M. Nikazar and B. Dabir, Pet. Sci. Technol., 2018, 36, 718–725 CrossRef CAS.
- L. Doraiswamy, in Organic Synthesis Engineering, Oxford University Press, 2001 Search PubMed.
- T. Sachdeva and K. Pant, Fuel Process. Technol., 2010, 91, 1133–1138 CrossRef CAS.
- J. Qiu, G. Wang, D. Zeng, Y. Tang, M. Wang and Y. Li, Fuel Process. Technol., 2009, 90, 1538–1542 CrossRef CAS.
- J. Li, Z. Yang, S. Li, Q. Jin and J. Zhao, J. Ind. Eng. Chem., 2020, 82, 1–16 CrossRef.
- D. S. Zhao, Z. M. Sun, F. T. Li and H. D. Shan, J. Fuel Chem. Technol., 2009, 37, 194–198 CrossRef CAS.
- Y. Köseoğlu, M. Bay, M. Tan, A. Baykal, H. Sözeri, R. Topkaya and N. Akdoğan, J. Nanopart. Res., 2011, 13, 2235–2244 CrossRef.
- H. A. H. Alshamsi and S. H. Alwan, Res. J. Pharm., Biol. Chem. Sci., 2015, 6, 985–996 CAS.
- N. Hussain, S. Alwan, H. Alshamsi and I. Sahib, Int. J. Chem. Eng., 2020, 2020, 9068358 Search PubMed.
- B. Davodi, M. Jahangiri and M. Ghorbani, Particulate Science and Technology, 2020, 38(3), 325–336 CrossRef CAS.
- Z. J. Zhang, X. Y. Chen, B. N. Wang and C. W. Shi, J. Cryst. Growth, 2008, 310, 5453–5457 CrossRef CAS.
- Y. Xiaotun, X. Lingge, N. S. Choon and C. S. O. Hardy, Nanotechnology, 2003, 14, 624 CrossRef.
- H. Altaee, H. A. H. Alshamsi and B. A. Joda, AIP Conf. Proc., 2020, 2290, 030036 CrossRef CAS.
- H. Altaee and H. A. Alshamsi, J. Phys.: Conf. Ser., 2020, 1664, 012074 CrossRef CAS.
- N. Jose, S. Sengupta and J. Basu, Fuel, 2011, 90, 626–632 CrossRef CAS.
- V. Garshasbi, M. Jahangiri and M. Anbia, Appl. Surf. Sci., 2017, 393, 225–233 CrossRef CAS.
- Y. Dai, D. Zhao and Y. Qi, Ultrason. Sonochem., 2011, 18, 264–268 CrossRef CAS PubMed.
- H. Mei, B. Mei and T. F. Yen, Fuel, 2003, 82, 405–414 CrossRef CAS.
- M. A. Rezvani, S. Khandan and N. Sabahi, Energy Fuels, 2017, 31, 5472–5481 CrossRef CAS.
- J. B. Bhasarkar, M. Singh and V. S. Moholkar, RSC Adv., 2015, 5, 102953–102964 RSC.
- M. Alimohammady, M. Jahangiri, F. Kiani and H. Tahermansouri, Res. Chem. Intermed., 2018, 44(1), 69–92 CrossRef CAS.
- H. A. Alshamsi, M. A. Al Bedairy and S. H. Alwan, IOP Conf. Ser. Earth Environ. Sci., 2021, 722, 012005 CrossRef.
- M. A. Rezvani, Z. Shokri Aghbolagh, H. Hosseini Monfared and S. Khandan, J. Ind. Eng. Chem., 2017, 52, 42–50 CrossRef CAS.
- M. A. Al-Bedairy and H. A. H. Alshamsi, Eurasian J. Anal. Chem., 2018, 13(6), em72 Search PubMed.
- T. O. Sachdeva and K. K. Pant, Fuel Process. Technol., 2010, 91, 1133–1138 CrossRef CAS.
- F. Vafaee, S. Mandizadeh, O. Amiri, M. Jahangiri and M. Salavati-Niasari, RSC Adv., 2021, 11, 22661–22676 RSC.
- T.-C. Chen, Y.-H. Shen, W.-J. Lee, C.-C. Lin and M.-W. Wan, J. Cleaner Prod., 2010, 18, 1850–1858 CrossRef CAS.
- M.-W. Wan and T.-F. Yen, Appl. Catal., A, 2007, 319, 237–245 CrossRef CAS.
- M. A. Rezvani, M. Shaterian, F. Akbarzadeh and S. Khandan, Chem. Eng. J., 2018, 333, 537–544 CrossRef CAS.
- C. Zhou, Y. Wang, X. Huang, Y. Wu and J. Chen, Chem. Eng. Process., 2020, 147, 107789 CrossRef CAS.
- I. Najafi, M. A. Makarem and M. Amani, Adv. Pet. Explor. Dev., 2011, 2, 63–69 Search PubMed.
|
This journal is © The Royal Society of Chemistry 2021 |
Click here to see how this site uses Cookies. View our privacy policy here.