DOI:
10.1039/D1RA06479G
(Paper)
RSC Adv., 2021,
11, 33646-33652
Nitrogen doped carbon for Pd-catalyzed hydropurification of crude terephthalic acid: roles of nitrogen species†
Received
27th August 2021
, Accepted 28th September 2021
First published on 14th October 2021
Abstract
The purification of crude terephthalic acid was performed by the hydrogenation of 4-carboxybenzaldehyde (4-CBA) over activated carbon (AC) supported Pd catalysts in industry. However, traditional Pd/AC catalysts usually suffer from low hydrogenation activity and poor thermal stability. Herein, nitrogen was incorporated into AC via a simple hydrothermal treatment of AC with urea as the nitrogen resource. The N doped AC contained pyridinic N, pyrrolic N, graphitic N and oxidized N. Wide characterizations revealed that N doping not only effectively improved the dispersion of Pd NPs but also increased the proportion of Pd0. In addition, N doping also enhanced the dissociative adsorption capacity of molecular hydrogen. More importantly, the resistance to sintering of Pd NPs was efficiently suppressed after N doping. As a result, N doped AC supported Pd showed both higher activity and better thermal stability than the N-free one.
1. Introduction
Purified terephthalic acid (PTA) is an important intermediate used for the production of polyesters. Industrially, the crude terephthalic acid (CTA) is produced by the oxidation of p-xylene (PX) over a homogeneous catalyst, containing a small amount of by-product 4-carboxybenzaldehyde (4-CBA). The removal of 4-CBA is generally carried out over Pd catalysts in a trickle reactor under a hydrogen atmosphere. Among the catalyst supports used (TiO2, SiC, SiO2 etc.),1–4 activated carbon (AC) supported Pd catalysts are still considered as one of the most efficient catalysts for the hydrogenation of 4-CBA.5,6 However, there are some drawbacks of traditional Pd/AC. Firstly, Pd nanoparticles (NPs) tend to aggregate due to the weak interaction of Pd and AC under reaction conditions, resulting in limited stability and life time of Pd/AC.7,8 Secondly, Pd is a noble metal and has high cost. Pd/AC needs to be optimized in order to maximize hydrogenation activity with the viewpoint of maximum atom efficiency of noble metal catalysts as well as sustainable development. Studies have shown that surface chemical and structural properties of a catalyst support can modulate catalytic performance of heterogeneous catalysts by changing the morphology or electronic structure of the deposited metal nanoparticles.9–11 For instance, CNTs oxidized with HNO3/H2SO4 can functionalize CNTs with surface oxygen groups and strengthen the coordination of Pt with surface oxygen groups, resulting in highly dispersed Pt NPs.12 Hence, surface modification of AC was one effective approach to modify Pd catalysts with improved catalytic activity and good stability.
Recent studies indicated that N doping of carbon materials can reinforce the interaction between metal and the carbon support.13–16 N doping into carbon materials as supports had profound impact on electronic structures of metal NPs, such as Ni,17 Pt,18 Pd,19 Ru20 and Co21 based catalysts, which was beneficial for their catalytic activity and stability. However, the relations of metallic NPs and nitrogen species resulting in excellent catalytic behavior were complicated. The electronegative property of N atoms may increase the electron density of metal NPs, resulting in the electron transfer from N to metal NPs. Ning et al. demonstrated that the binding energy of Pt0 of Pt/NCNTs shifted to the low binding energy side compared with Pt/CNTs.22 In addition, N doping can greatly improve metal NPs dispersion and in turn contributed to better catalytic activity.23–25 N doping was also helpful for the stabilization of metal NPs and further improve the stability of supported metal catalysts.26–28 Until now, N doped carbon materials supported metal catalysts for the hydrogenation of 4-CBA remained less exploration and large challenge.
Here, nitrogen was doped into AC via the hydrothermal method with urea as nitrogen resource. Then, the obtained N doped AC was used as a support for the loading of Pd NPs by a wetness impregnation method. After N doping, Pd catalyst exhibited higher catalytic activity and better thermal stability for the hydrogenation of 4-CBA compared with un-doped one. Furthermore, the influence of N species on structure properties of Pd catalysts and their effects on catalytic performance were discussed in detail.
2. Experimental section
2.1 Materials
Palladium chloride was purchased from Sigma-Aldrich. 4-CBA were purchased from Aladdin Chemical Reagent (Shanghai, China). Activated carbon was supplied by Sinopec Shanghai Petrochemical Company Limited. Phosphoric acid (H3PO4, 85 wt% in H2O), and ammonia solution (NH3·H2O, 25 wt% in H2O) were purchased from Sinopharm Chemical Reagent Co., Ltd. All other chemicals were analytical grade and used without further purification.
2.2 Preparation of N doped AC
The N doped activated carbon was synthesized by a hydrothermal process using urea as the nitrogen resource. Typically, 0.6 g activated carbon was dispersed in 5 M urea solution. Then, the mixture solution was transferred to a 200 ml Teflon-lined autoclave and heated at 180 °C for 4 h. After reaction, the autoclave was cooled down to room temperature. Then, the product was collected by filtration and washed using de-ionized water. After dried at 120 °C, the sample was calcined at 500 °C for 3 h in nitrogen atmosphere. The final sample was abbreviated as N_AC.
2.3 Preparation of Pd supported N doped AC
The Pd supported N doped AC were prepared by impregnating N doped AC with H2PdCl4 aqueous solution and sodium citrate as the stabilizing agent. After impregnation, 10 ml of 0.1 M NaBH4 aqueous as reductive agent was added dropwise to the above solution under vigorous stirring for 1 h. Finally the Pd catalyst was obtained by filtration, washing with water and dried at 120 °C. The obtained samples were denoted as Pd/N_AC. For comparison, Pd supported on N-free AC was also prepared by the same above method, and denoted as Pd/AC. The loading amount of Pd was 0.5 wt% for all Pd catalysts.
2.4 Catalyst characterization
Powder X-ray diffraction (XRD) measurement was performed using Bruker D8 Advance diffractometer, with Cu Kα radiation (g = 0.15406 nm) at step scan 0.02° from 5° to 80°. The nitrogen adsorption/desorption isotherms were measured at 77 K on a Micromeritics ASAP 2020 analyzer. The total porous volume (Vtotal) was estimated from the adsorbed capacity of nitrogen at a relative pressure P/P0 of 0.98 whereas the microporous volume (Vmicro) was determined using the t-plot method. The morphology and microstructure were measured by scanning electron microscopy (FE-SEM, Hitachi S-4800). X-ray photoelectron spectroscopy (XPS) was carried out with an AXIS Ultra DLD photoelectron spectrometer (Kratos Analytical, UK) using monochromatic Al Kα radiation. The C 1s with the binding energy of 284.6 eV was applied as reference to calibrate the position of the other peaks. The hydrogen temperature programmed desorption (H2-TPD) experiments was conducted using a Micromeritics Autochem II 2920 instrument equipped with a thermal conductivity detector (TCD). Prior to the tests, the samples are pretreated under hydrogen atmosphere at 200 °C for 60 min. H2 desorption in Ar flow was started with temperature ramping from 50 °C to 800 °C. Palladium dispersion on xx was determined by hydrogen titration of chemisorbed oxygen (H2–O2 titration) in a Micromeritics Autochem II 2920 instrument with a thermal conductivity detector (TCD). Prior to the tests, 400 mg Pd catalysts were first reduced at 200 °C under a hydrogen atmosphere for 120 min; hydrogen absorbed on the surface of catalyst was titrated by 15 pulses of oxygen until full saturation; then the resulting monolayer of adsorbed oxygen was titrated using 15 pulses of hydrogen until constant TCD signal detected. In addition, TEM images of Pd catalysts were performed on a Tecnai 20 S-TWIN electron microscope operated at 200 kV. The content of Pd loading was determined by an inductively coupled plasma emission spectrometer (ICP-OES, Varian 725 ES). The bulk elemental composition (C, H, N) was determined by using an elemental analyzer (SDCHN435, Hunan Sundy, China).
2.5 Catalytic activity tests
The catalytic hydrogenation of 4-CBA was carried out in a 100 ml stainless-steel autoclave. In a typical test, 0.15 g of 4-CBA, 50 mg catalyst with 20–40 mesh and 50 ml of de-ionized water were placed in the autoclave and mixed together. After sealed, the autoclave was pressured with 0.8 MPa hydrogen, then heated to 80 °C in a water bath. After reaction, the obtained liquid samples were treated with 14% NH3·H2O and 17% H3PO4 aqueous solutions respectively. Finally, the liquid products were analyzed using high-performance liquid chromatography (HPLC, Agilent 1200) equipped with a UV detector and a C-18 column (4.6 × 250 mm, 5 µm) (Scheme 1).
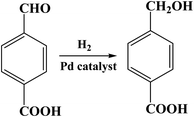 |
| Scheme 1 Hydrogenation pathway of 4-CBA over Pd catalysts. | |
3. Results and discussion
3.1 The textural properties of Pd catalysts
The influence of N doping and Pd loading on the porous structure of AC has been investigated by N2 physical adsorption–desorption at 77 K. The type I isotherm curves indicated the nature of microstructure of activated carbon materials (Fig. S1†). The porosity parameters were summarized in Table 1. Compared with AC, N_AC showed a slight increase in BET area and pore volume after N doping. The hydrothermal treatment of activated carbon at high temperature of water facilitated the production of porous structure.29,30 Compared with supports, the slight decrease of surface area of Pd/AC and Pd/N_AC indicated that part of surface sites of supports were occupied by dispersed Pd NPs after Pd loading.
Table 1 Summary of porosity parameters of supports and Pd catalysts
Sample |
SBET (m2 g−1) |
Smic (m2 g−1) |
Vtotal (cm3 g−1) |
Vmic (cm3 g−1) |
AC |
991.7 |
836.8 |
0.482 |
0.383 |
Pd/AC |
910.4 |
770.9 |
0.439 |
0.352 |
N_AC |
1023.8 |
844.7 |
0.497 |
0.385 |
Pd/N_AC |
925.0 |
765.4 |
0.445 |
0.348 |
3.2 The electronic structures of N and Pd
The direct evidence of N doping was provided by XPS, and the N 1s spectra of N_AC and Pd/N_AC were shown in Fig. S2.† The high resolution C 1s spectra of N_AC and Pd/N_AC can be deconvoluted into three peaks, corresponding to C
C (284.6 eV), C–N (285.5 eV) and O–C
O (288.9 eV) respectively.31–33 These results indicated the incorporation of N atoms into carbon skeleton. The high resolution N 1s XPS spectra of AC and Pd/N_AC (Fig. 1c and d) further indicated the four forms of heteroatom N in the carbon. The four kinds of nitrogen species appeared at different binding energies, corresponding to pyridinic N, pyrrolic N, graphitic N and oxidized N, respectively. After Pd loading, the total nitrogen content decreased from 1.34 at% to 1.12 at% (Fig. S3†). Furthermore, the content of four different nitrogen species before and after Pd loading were summarized in Fig. 2. The relative percentages of pyridinic N, pyrrolic N, graphitic N have no obvious changes except of the slight decreasing of oxidized N. Moreover, the elemental analysis results further revealed that the total N content was similar before (0.58 wt%) and after (0.53 wt%) Pd loading (Table S1†).
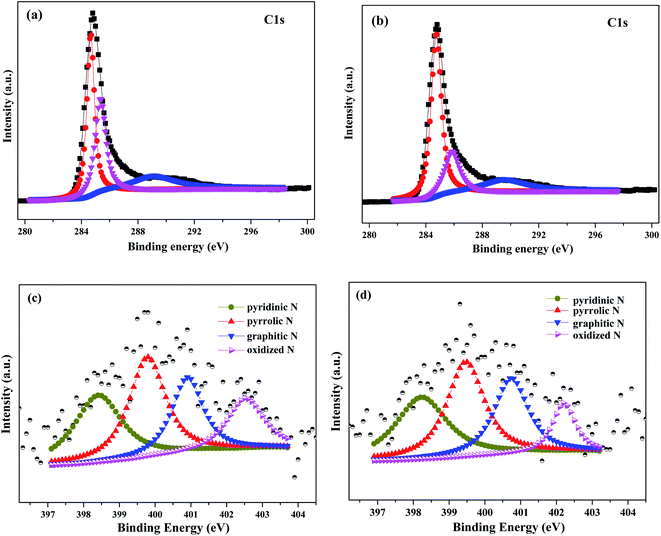 |
| Fig. 1 C 1s and N 1s XPS spectra of (a and c) N_AC and (b and d) Pd/N_AC. | |
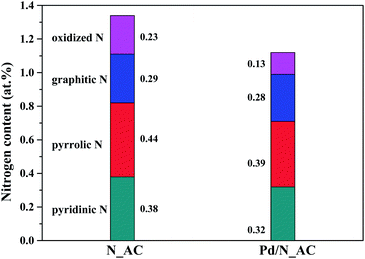 |
| Fig. 2 Different N species distribution of N_AC and Pd/N_AC. | |
To further understand the important influence of N doping on electronic structure of Pd catalysts, XPS was carried out to investigate chemical state of Pd. As shown in Fig. 3, the surface chemical state of Pd species consisted of oxidation state Pd (Pd2+) and metallic state Pd (Pd0). According to XPS analysis, the ratio of Pd0/Pd2+ in Pd/AC and Pd/N_AC was 1.04 and 1.32, respectively. These results clearly indicated that N doping favored the formation of Pd0. Since pyridinic N and pyrrolic N possessed lone pair of electrons, N species can provide an electron-enriched microenvironment and finally can increase the content of Pd0 by donating its electron to Pd.34 Therefore, N dopants can serve as metal coordination sites for anchoring Pd. Wang et al. also revealed that N in carbon texture was beneficial for stabilizing Pd0 and preventing the reoxidation of metallic Pd.35
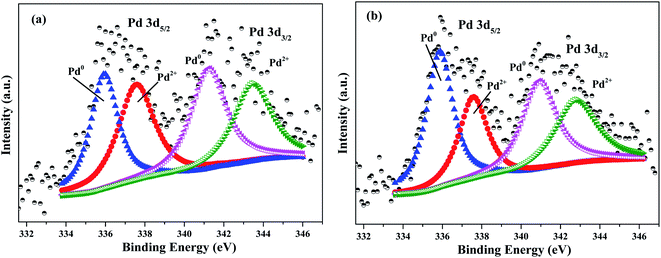 |
| Fig. 3 Pd 3d XPS spectra of (a) Pd/AC and (b) Pd/N_AC. | |
3.3 The dispersion of Pd nanoparticles
The typical HRTEM images of Pd catalysts without and with N doping were shown in Fig. 4. The Pd particle size distribution showed that the N-doped Pd catalyst had narrow diameter distribution with smaller size of Pd NPs than that of the N-free catalyst. This result indicated that N_AC was an ideal support for stabilizing Pd NPs. Pd dispersion before and after N doping have been further tested by hydrogen-oxidation titration and the results were summarized in Table 2. The actual Pd loading were also tested by ICP analysis, which was close to the theoretical value. After N doping, Pd dispersion increased to 35.7% compared with that of the N-free sample (22.4%). Surface nitrogen-containing groups such as pyridinic N and pyrrolic N have been confirmed to increase metal dispersion (e.g. Pt, Ni) via strong metal–N bond at the interface.26,27,36 In recent years, atomically dispersed metal catalysts in N doped graphene matrix were also successfully synthesized with wide applications.37–39 Therefore, nitrogen doping in carbon materials held promising potential for stabilizing highly dispersed metal nanoparticles.40,41
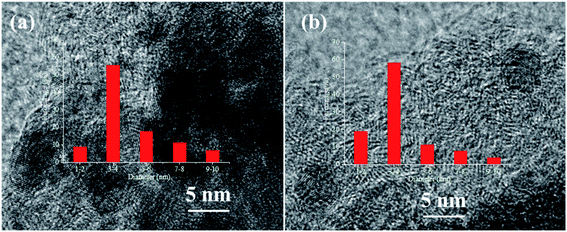 |
| Fig. 4 HRTEM images and size distribution of (a) Pd/AC and (b) Pd/N_AC. | |
Table 2 Physical–chemical properties of Pd catalysts before and after N doping
Entry |
Catalyst |
Pd loadinga (wt%) |
Metal dispersionb (%) |
Determined by ICP-AES. Determined by H2–O2 titration. |
1 |
Pd/AC |
0.47 |
22.4 |
2 |
Pd/N_AC |
0.48 |
35.7 |
3.4 Activation of hydrogen molecular
As reported, the dissociatively adsorption ability of hydrogen molecular were closely associated with catalytic activities of Pd catalysts. Here, hydrogen activation ability over Pd catalysts were detected by H2-TPD. As shown in Fig. 5, Pd catalysts before and after N doping showed a low temperature desorption peak below 100 °C, which was attributed to the desorption of weak adsorbed hydrogen molecular. The large desorption peaks at high temperature (275 °C for Pd/AC and 301 °C for Pd/N_AC) were ascribed to the desorption of strongly adsorbed hydrogen species. The higher desorption temperature in Pd/N_AC indicated the strengthening Pd–support interactions due to N doping. In addition, the intensity of desorption peak in Pd/N_AC was obviously stronger than that in Pd/AC, suggesting the doping of N atoms into AC facilitated the adsorption and activation of molecular hydrogen. Rossi et al. illustrated the crucial role of nitrogen atoms over Au@N-doped carbon catalysts in promoting the heterolytic activation of molecular hydrogen.42
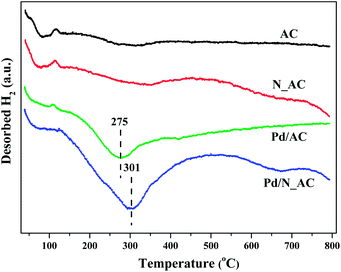 |
| Fig. 5 H2-TPD profiles of AC, N_AC, Pd/AC and Pd/N_AC. | |
3.5 Stability of Pd catalysts
To better understand the crucial role of N species, the sintering resistance of Pd catalysts was investigated by XRD (Fig. 6). The catalysts were calcined in N2 at 500 °C. Compared with fresh Pd catalysts (Fig. S5†), the intensity of Pd (111) diffraction peaks obviously increased after heat treatment at 500 °C. The particle sizes of Pd NPs were calculated through Scherrer equation. The average size of Pd NPs in Pd/N_AC was 14.8 nm which was smaller than that of Pd/C (16.7 nm). This results indicated that N doping can secure Pd NPs on their original position and inhibit the growth of Pd NPs.43,44 In addition, the surface area of Pd/AC-500 and Pd/N_AC-500 was 921.2 and 940.6 m2 g−1, and the corresponding pore volume was 0.488 and 0.489 cm3 g−1 respectively. The surface area and pore volume of aged samples slightly increased compared with the fresh ones.
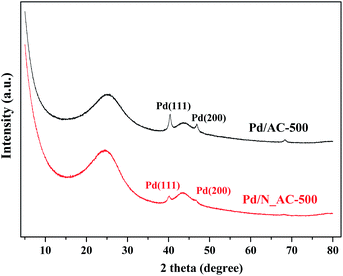 |
| Fig. 6 XRD patterns of Pd catalysts after calcined at 500 °C. | |
3.6 Influence of nitrogen species on catalytic performance of Pd catalysts
The activities of Pd catalysts before and after N doping were tested for the hydrogenation of 4-CBA. When N_AC without Pd used as the catalyst, the conversion of 4-CAB was extremely low, suggesting the N_AC was inactive due to its poor ability for hydrogen molecular activation. Generally, metal state Pd0 was catalytic active center of hydrogenation reaction.45,46 As shown in Fig. 7, Pd loaded on N_AC exhibited higher catalytic activity than that on N-free AC. After reaction for 3 h, the conversion of 4-CBA reached 91.5% while the conversion of Pd/AC was only 83.4%. After reaction for 3 h, the contents of Pd over Pd/AC and Pd/N_AC catalysts were analyzed via ICP, and they were 0.47% and 0.48% respectively. Therefore, Pd leaching was negligible. The above structure characterizations indicated N-functionalization of AC played important roles in the hydrogenation of 4-CBA. Firstly, N species as electron donors in support could affect the chemical state of Pd NPs. N doping increased the content of Pd0 due to the strong electron donating effect of N species. In addition, nitrogen species promoted activation capacity of hydrogen molecular, which was beneficial for the hydrogenation reaction. More importantly, N species enhanced the superior dispersion of Pd NPs with narrow size distribution. Thus, the improved activity of Pd/N_AC could be attributed to the strong coordination of Pd with N species.
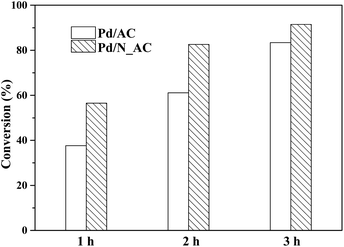 |
| Fig. 7 Catalytic activity of Pd catalysts for 4-CBA hydrogenation. | |
In present work, N doped AC samples were synthesized by a hydrothermal method with urea as nitrogen resource. Fig. S6† showed the catalytic activity of hydrogenation of 4-CBA over Pd catalysts with different N doped AC as supports. The N doping was indeed beneficial for the hydrogenation of 4-CBA compared with N-free AC supported Pd. Here, N doped AC synthesized at 180 °C for 4 h supported Pd catalyst exhibited the best activity.
4. Conclusions
In summary, nitrogen heteroatoms were incorporated into AC by a simple hydrothermal method with urea as nitrogen resource. Pd supported on different N doped AC were prepared by a wetness impregnation method and their catalytic performances were evaluated in the hydrogenation of 4-CBA under mild reaction conditions. After N doping, Pd catalysts exhibited enhanced catalytic activity compared with Pd/AC. The critical roles of N dopant in influencing the electronic structures of Pd on Pd/N_AC were investigated. Firstly, the XPS spectra verified that N species as electron donor can increase the electron density of Pd NPs, thus keeping the high percentage of Pd0 in Pd/N_AC. Secondly, H2-TPD tests revealed that N doping enhanced the activation ability of hydrogen molecular over Pd/N_AC, and thereby facilitated the hydrogenation activity of 4-CBA. Thirdly, Pd dispersion increased to 35.7% after N doping, and facilitated catalytic hydrogenation reaction performance. More importantly, N doping promoted the effective immobilization of Pd NPs by strong metal–support interaction through the large electron affinity of N. As a result, Pd/N_AC showed a better sintering resistance of Pd NPs than Pd/AC. The present work may offer a feasible strategy to synthesize other metal catalysts with high dispersion and well thermal stability.
Conflicts of interest
There are no conflicts to declare.
Acknowledgements
We gratefully acknowledged the financial support from the National Natural Science Foundation of China (U1663221).
Notes and references
- S. H. Jhung, A. V. Romanenko, K. H. Lee, Y. S. Park, E. M. Moroz and V. A. Likholobov, Appl. Catal., A, 2002, 225, 131–139 CrossRef CAS.
- K. T. Li, M. H. Hsu and I. Wang, Catal. Commun., 2008, 9, 2257–2260 CrossRef CAS.
- Y. H. Zhou, X. Y. Li, X. L. Pan and X. H. Bao, J. Mater. Chem., 2012, 22, 14155–14159 RSC.
- Z. Li, C. Wang, X. Chen, X. Wang, X. Li, Y. Yamauchi, X. Xu, J. Wang, C. Lin, D. Luo, X. Wang and X. S. Zhao, Chem. Eng. J., 2020, 381, 122588 CrossRef CAS.
- F. Menegazzo, T. Fantinel, M. Signoretto and F. Pinna, Catal. Commun., 2007, 8, 876–879 CrossRef CAS.
- X. Li, K. Tie, Z. Li, Y. Guo, Z. Liu, X. Liu, X. Liu, H. Feng and X. S. Zhao, Appl. Surf. Sci., 2018, 447, 57–62 CrossRef CAS.
- R. Pellegrini, G. Agostini, E. Groppo, A. Piovano, G. Leofanti and C. Lamberti, J. Catal., 2011, 280, 150–160 CrossRef CAS.
- S. Tourani, F. Khorasheh, A. M. Rashidi and A. A. Safekordi, J. Ind. Eng. Chem., 2015, 28, 202–210 CrossRef CAS.
- S. S. Rich, J. J. Burk, C. S. Kong, C. D. Cooper, D. E. Morse and S. K. Buratto, Carbon, 2015, 81, 115–123 CrossRef CAS.
- Y. X. Tuo, L. J. Shi, H. Y. Cheng, Y. A. Zhu, M. L. Yang, J. Xu, Y. F. Han, P. Li and W. K. Yuan, Insight into the support effect on the particle size effect of Pt/C catalysts in dehydrogenation, J. Catal., 2018, 360, 175–186 CrossRef CAS.
- S. Kattel, W. Yu, X. Yang, B. Yan, Y. Huang, W. Wan, P. Liu and J. G. Chen, Angew. Chem., Int. Ed., 2016, 55, 7968–7973 CrossRef CAS PubMed.
- R. V. Hull, L. Li, Y. Xing and C. C. Chusuei, Chem. Mater., 2006, 18, 1780–1788 CrossRef CAS.
- H. Wang, T. Maiyalagan and X. Wang, ACS Catal., 2012, 2, 781–794 CrossRef CAS.
- M. Li, F. Xu, H. Li and Y. Wang, Catal. Sci. Technol., 2016, 6, 3670–3693 RSC.
- Y. Cao, S. Mao, M. Li, Y. Chen and Y. Wang, ACS Catal., 2017, 7, 8090–8112 CrossRef CAS.
- X. Y. Li, X. L. Pan, Y. H. Zhou and X. H. Bao, Carbon, 2013, 57, 34–41 CrossRef CAS.
- R. Nie, H. Yang, H. Zhang, X. Yu, X. Lu, D. Zhou and Q. Xia, Green Chem., 2017, 19, 3126–3134 RSC.
- G. Wu, D. Li, C. Dai, D. Wang and N. Li, Langmuir, 2008, 24, 3566–3575 CrossRef CAS PubMed.
- R. Nie, H. Jiang, X. Lu, D. Zhou and Q. Xia, Catal. Sci. Technol., 2016, 6, 1913–1920 RSC.
- Y. Cao, L. Ding, Z. Qiu and H. Zhang, Catal. Commun., 2020, 143, 106048 CrossRef CAS.
- F. A. Westerhaus, R. V. Jagadeesh, G. Wienhofer, M. M. Pohl, J. Radnik, A. E. Surkus, J. Rabeah, K. Junge, H. Junge, M. Nielsen, A. Bruckner and M. Beller, Nat. Chem., 2013, 5, 537–543 CrossRef CAS PubMed.
- X. Ning, H. Yu, F. Peng and H. Wang, J. Catal., 2015, 325, 136–144 CrossRef CAS.
- W. Qian, L. Lin, Y. Qiao, X. Zhao, Z. Xu, H. Gong, D. Li, M. Chen, R. Huang and Z. Hou, Appl. Catal., A, 2019, 585, 117183 CrossRef CAS.
- Y. Dai, C. Jiang, M. Xu, B. Bian, D. Lu and Y. Yang, Appl. Catal., A, 2019, 580, 158–166 CrossRef CAS.
- C. Pu, J. Zhang, G. Chang, Y. Xiao, X. Ma, J. Wu, T. Luo, K. Huang, S. Ke, J. Li and X. Yang, Carbon, 2020, 159, 451–460 CrossRef CAS.
- T. Wang, Z. Dong, T. Fu, Y. Zhao, T. Wang, Y. Wang, Y. Chen, B. Han and W. Ding, Chem. Commun., 2015, 51, 17712–17715 RSC.
- L. Perini, C. Durante, M. Favaro, V. Perazzolo, S. Agnoli, O. Schneider, G. Granozzi and A. Gennaro, ACS Appl. Mater. Interfaces, 2015, 7, 1170–1179 CrossRef CAS PubMed.
- S. Li, Y. Shi, J. Zhang, Y. Wang, H. Wang and J. Lu, ChemSusChem, 2021, 14, 2050–2055 CrossRef CAS PubMed.
- L. Sun, L. Wang, C. Tian, T. Tan, Y. Xie, K. Shi, M. Li and H. Fu, RSC Adv., 2012, 2, 4498 RSC.
- R. Shi, J. Zhao, S. Liu, W. Sun, H. Li, P. Hao, Z. Li and J. Ren, Carbon, 2018, 130, 185–195 CrossRef CAS.
- C. Zhang, L. Fu, N. Liu, M. Liu, Y. Wang and Z. Liu, Adv. Mater., 2011, 23, 1020–1024 CrossRef CAS PubMed.
- W. Ding, L. Li, K. Xiong, Y. Wang, W. Li, Y. Nie, S. Chen, X. Qi and Z. Wei, J. Am. Chem. Soc., 2015, 137, 5414–5420 CrossRef CAS PubMed.
- H. Sun, Y. Zhu, B. Yang, Y. Wang, Y. Wu and J. Du, J. Mater. Chem. A, 2016, 4, 12088–12097 RSC.
- Y. Wang, J. Yao, H. Li, D. Su and M. Antonietti, J. Am. Chem. Soc., 2011, 133, 2362–2365 CrossRef CAS PubMed.
- X. Xu, Y. Li, Y. Gong, P. Zhang, H. Li and Y. Wang, J. Am. Chem. Soc., 2012, 134, 16987–16990 CrossRef CAS PubMed.
- D. He, Y. Jiang, H. Lv, M. Pan and S. Mu, Appl. Catal., B, 2013, 132–133, 379–388 CrossRef CAS.
- H. Fei, J. Dong, M. J. Arellano-Jimenez, G. Ye, N. Dong Kim, E. L. Samuel, Z. Peng, Z. Zhu, F. Qin, J. Bao, M. J. Yacaman, P. M. Ajayan, D. Chen and J. M. Tour, Nat. Commun., 2015, 6, 8668 CrossRef CAS PubMed.
- H. B. Yang, S. F. Hung, S. Liu, K. Yuan, S. Miao, L. Zhang, X. Huang, H. Y. Wang, W. Cai, R. Chen, J. Gao, X. Yang, W. Chen, Y. Huang, H. M. Chen, C. M. Li, T. Zhang and B. Liu, Nat. Energy, 2018, 3, 140–147 CrossRef CAS.
- T. Zhang, X. Han, A. Han, Y. Li, J. Liu, T. Zhang, H. Yang, B. Liu, E. Hu, X. Q. Yang and L. Wang, Angew. Chem., Int. Ed., 2020, 59, 12055–12061 CrossRef CAS PubMed.
- G. Sun, Z. J. Zhao, R. Mu, S. Zha, L. Li, S. Chen, K. Zang, J. Luo, Z. Li, S. C. Purdy, A. J. Kropf, J. T. Miller, L. Zeng and J. Gong, Nat. Commun., 2018, 9, 4454 CrossRef PubMed.
- H. Yu, L. Zhang, S. Gao, H. Wang, Z. He, Y. Xu and K. Huang, J. Catal., 2021, 396, 342–350 CrossRef CAS.
- J. L. Fiorio, R. V. Gonçalves, E. Teixeira-Neto, M. A. Ortuño, N. López and L. M. Rossi, ACS Catal., 2018, 8, 3516–3524 CrossRef CAS.
- Z. Li, J. Liu, C. Xia and F. Li, ACS Catal., 2013, 3, 2440–2448 CrossRef CAS.
- K. Zhang, Q. Meng, H. Wu, T. Yuan, S. Han, J. Zhai, B. Zheng, C. Xu, W. Wu, M. He and B. Han, Green Chem., 2021, 23, 1621–1627 RSC.
- Z. Z. Wei, Y. T. Gong, T. Y. Xiong, P. F. Zhang, H. R. Li and Y. Wang, Catal. Sci. Technol., 2015, 5, 397–404 RSC.
- A. Nagendiran, V. Pascanu, A. Bermejo Gomez, G. Gonzalez Miera, C. W. Tai, O. Verho, B. Martin-Matute and J. E. Backvall, Chem.–Eur. J., 2016, 22, 7184–7189 CrossRef CAS PubMed.
Footnote |
† Electronic supplementary information (ESI) available. See DOI: 10.1039/d1ra06479g |
|
This journal is © The Royal Society of Chemistry 2021 |
Click here to see how this site uses Cookies. View our privacy policy here.