DOI:
10.1039/D1RA06287E
(Paper)
RSC Adv., 2021,
11, 38537-38546
Effect of hydrogen-rich gas from char gasification on rapid pyrolysis products of low rank coal in a downer pyrolyzer
Received
19th August 2021
, Accepted 25th November 2021
First published on 30th November 2021
Abstract
For guiding a novel integrated process of low-rank coal pyrolysis and gasification with char gasification gas as a heat carrier, this study investigated the effect of simulated coal gas from char gasification (SCGG) on rapid pyrolysis products of low rank coal from 550 to 700 °C in a downer pyrolyzer. Results indicated that the component of SCGG directly affected the distribution and composition of pyrolysis products. Compared with N2, SCGG facilitated the formation of tar below 600 °C. H2 in SCGG and that from water gas shift reaction (WGS: CO + H2O → CO2 + H2) increased the tar yield by reacting with solid-phase free radicals in coal and inhibiting the secondary reaction of gas-phase volatile radicals. Also, CO2 in SCGG raised the tar yield due to its promotion to coal cracking. When the pyrolysis temperature exceeded 600 °C, the reforming reactions of nascent tar with steam occurred, resulting in a reduced tar yield. SCGG could distinctly reduce the coke yield (coke-S) and pitch content in tar due to the inhibiting effect of H2 from SCGG and WGS on the polycondensation reactions of volatile radicals and reforming reactions of nascent tar. The chemical composition analysis of tar by GC × GC-MS demonstrated that compared with under N2, the contents of phenols, oxygenated compounds, and heterocyclic compounds in tar under SCGG were decreased while the content of aromatics was the opposite mainly due to hydrogenation and reforming reactions of nascent tar. Also, the H/C and O/C ratios of char under the action of SCGG were higher than those under N2 at the same temperature.
1. Introduction
Low-rank coal, including lignite and sub-bituminous coals, is rich globally, accounting for about half of the coal reserves.1 They are relatively low heat value with high amounts of moisture and volatiles. Direct combustion or gasification of these coals would result in low energy efficiency, high pollutant emissions, and the waste of high-value components in volatiles.2,3 Special interest has been taken in coal conversion technology that can extract high-value components in volatiles ahead of gasification or combustion. Poly-generation technologies combining low-and-mid temperature pyrolysis with combustion or gasification have been developed to implement the pre-extraction of volatiles from coal.4–7 In most of these processes, coal is first fed to a pyrolyzer to extract volatiles, and then the resulting char is sent to a combustor or gasifier for heat/power or syngas production. Between the two reactors, hot ash from the combustor or gasifier supplies heat for coal pyrolysis. These processes can generally produce multiple products such as tar, coal gas, and power with high energy efficiency and low emissions of pollutants, and realize the hierarchical utilization of low-rank coal.8–10 However, the tar generated from the processes usually contains higher pitch content due to the low hydrogen–carbon molar ratio of coal and uncontrolled secondary reaction of volatiles on heat carrier particles.11 Also, the intense mixing between cold coal and hot solid heat carrier in the reactor generates a great deal of dust.12 The high-viscosity pitch in tar is likely to condensate and mix with coke and dust in tar, leading to frequent clogging of volatile product lines and devices and affecting the long-term stable operation of the system.13,14 Besides, the pitch in tar is also difficult to be treated, which against the subsequent tar upgrading.15,16 To overcome these problems, the authors' previous study proposed a novel poly-generation process, which integrated low-rank coal pyrolysis and gasification with char gasification gas as heat carrier,17 as is shown in Fig. 1. In this process, coal is first pyrolyzed in a downer pyrolyzer, the hot char from the pyrolyzer is directly fed to a fluidized bed gasifier, and the gas from char gasification is used as the heat carrier and reaction atmosphere for coal pyrolysis after it is cooled to a suitable temperature. The process can reduce dust generation from the intense mixing between cold coal and hot solid heat carrier. Meanwhile, the hydrogen-rich gas from char gasification may positively affect coal pyrolysis.18 Besides, in the process, the high-grade sensible heat of coal gas from char gasification is efficiently used by the pyrolyzer, avoiding the outer energy supply for coal pyrolysis and reducing CO2 emissions to a certain extent. However, the effect of hydrogen-rich gas from char gasification on coal pyrolysis needs to be further investigated in the process.
 |
| Fig. 1 Principle of the novel poly-generation process. | |
There exist some studies on the effect of hydrogen-rich gas on coal pyrolysis. Braekman-Danheux et al.19,20 studied the influences of simulated coke oven gas (55% H2, 30% CH4, 15% N2) on product yields. They reported that the overall conversion and oil yield were lower than in pure hydrogen, but higher than in helium. Jin et al.18 studied the effects of simulated coal gases (SCG) (25% H2, 25% CH4, 25% CO2, 12.5% CO, 12.5% N2) on coal pyrolysis. They found that small molecular radicals (H˙,
radicals) generated from SCG stabilized free radicals from coal pyrolysis, resulting in high tar yield and quality. Xiong et al.21 investigated the tar yields and tar composition characteristics in N2 and simulated pyrolysis gas (SPG) (20% H2, 20% CO, 15% CO2, and 45% CH4). The results showed that the SPG promoted tar formation and the tar contained fewer aliphatic C–H bonds and more aromatic compounds comparing with N2 atmosphere. Zhong et al.22 investigated the pyrolysis characteristics of a sub-bituminous coal in a fluidized bed reactor in N2-base atmospheres containing O2, H2, CO, CH4, and CO2. The result indicated that the effects of adding H2, CO, CH4, or CO2 into the atmosphere on the tar yield were related to the O2 content in the atmosphere. Liu et al.23,24 reported that the integrated process of CO2 reforming methane and coal pyrolysis could improve the tar yield and quality due to the combination of H˙ and
radicals produced from CO2 reforming methane with radicals from coal pyrolysis.
Although many researchers evaluated the effects of different hydrogen-rich gases, such as coke oven gas, pyrolysis gas, and gas from CO2 reforming methane, on coal pyrolysis, reports on the effect of coal gas from char gasification on coal pyrolysis were rare. Especially, the coal gas from char gasification (35% CO, 35% H2, 15% CO2, 15% steam) in this process (in Fig. 1) contain a certain amount of steam. In addition, the effect of hydrogen-rich gas on coke deposition during coal pyrolysis has not been reported. The purpose of this study was to investigate how simulated coal gas from char gasification affects the rapid pyrolysis process of low rank coal at low-and-mid temperature (550–700 °C), and the distribution and composition of pyrolysis products. The experimental results are expected to guide the process design and operation optimization of the novel poly-generation process that we proposed. Meanwhile, the study was expected to deepen the understanding of the effects of different atmospheres on coal pyrolysis.
2. Experimental
2.1 Coal sample
A high volatile Naomaohu bituminous coal from Xinjiang of China is used in this study. The main characteristics of the coal sample are listed in Table 1. The sample was ground and sieved to the sizes of 0.250–0.425 mm for experimental tests. The coal sample was dried in a vacuum oven at 105 °C for 12 h before the experiment.
Table 1 Main characteristics of the coal sample used in experimentsa
Proximate analysis (wt%) |
Ultimate analysis (wt%, daf) |
Mad |
Ad |
Vdaf |
C |
H |
N |
S |
Oa |
M, moisture; A, ash; V, volatile matter; ad: air-dry basis; daf: dry-and-ash-free basis; a: by difference. |
19.50 |
5.60 |
48.85 |
73.38 |
5.04 |
0.89 |
0.29 |
20.40 |
2.2 Apparatus and procedure
Coal pyrolysis experiments were conducted in a laboratory-scale downer pyrolyzer. Fig. 2 shows the schematic diagram of the experimental equipment. The experimental apparatus mainly contains the following parts: gas supplying system, feeder, downer reactor, electric furnace, condensation system, and gas analysis system. The downer reactor is made of quartz glass. It consists of a pyrolysis reaction section (PRS) in the upper part, a char collection section (CCS) in the lower part and a product export section (PES) in the middle part. The pyrolysis reaction section is 167 cm in length and 2.0 cm in inner diameter, the char collection section is 48 cm in length and 4.6 cm in inner diameter, and the product export section is 69 cm in length and 2.5 cm in inner diameter. In the experiment, the pyrolysis reaction section was set at 550, 600, 650, 700 °C with 850 mL min−1 flow rate of pyrolysis atmospheres, the char collection section was controlled at 300 °C with 1200 mL min−1 N2 to avoid condensation of volatiles, and the product export section was set at 500 °C to ensure volatiles output. The tested pyrolysis atmospheres are N2, and simulated coal gas from char gasification (expressed as SCGG). The SCGG comprises 35% CO, 35% H2, 15% CO2, 15% steam by volume. For understanding the role of each component of SCGG in coal pyrolysis, the individual gas (H2, CO, CO2, steam) in SCGG was also used as tested pyrolysis atmospheres. The flow of the investigated gas was set at the same as in SCGG, and N2 replaced the remaining compositions to ensure the total gas flow rate was 850 mL min−1. For each experiment, the coal sample used was 100 g. When the reactor was heated to the desired temperature, coal sample was injected continuously into the reactor with about 1.0 g min−1 from the screw feeder. The residence time of coal particles in the reactor was about 2–3 s according to literatures' method.25 The generated char particles fell into the char collection section during the pyrolysis process, and the gaseous pyrolysis products outflowed through the product export section and then were further cooled down into tar and water. At the same time, the pyrolysis gases were analyzed by a Raman laser gas analyzer (RLGA-174b) after filtration.
 |
| Fig. 2 Diagram of experimental equipment. | |
After the experiment finished, the collection bottle, connecting lines and reactor outlet were washed repeatedly with the tetrahydrofuran (THF) solvent to recover the tar. Then, the tar was filtrated with the organic membrane of 0.45 μm pore size and the filtered residue was named as THF insoluble substances (coke-S). The organic membrane is made of nylon 66, and provided by Xinya purification device factory of Shanghai in China. The coke-S on the organic membrane were dried at 45 °C under a vacuum oven for 2 h. The mass was determined by the mass difference between the organic membrane loaded with and without coke-S. During the volatiles reaction, some carbon formed and deposited on the inner surface of the reactor. This carbon was named as coke-D. It was difficult to recover the carbon to obtain an accurate mass. Therefore, oxygen was introduced to combust the carbon. The mass was calculated based on the integration of the measured CO2 and CO after combustion. To reduce experimental errors and avoid outlier data, the above experiments were repeated three times under the same conditions.
2.3 Product analysis
The moisture in tar was measured by a water titrator (KEM MKV-710B) employing the Karl-Fischer method. The fraction of tar was detected by a simulated distillation GC (Agilent 7890A) according to ASTM 2887. The fraction with a boiling point below 360 °C was defined as the light tar and the fraction with a boiling point above 360 °C was referred to the pitch. The chemical composition of tar was conducted by a GC × GC-MS equipped with an Agilent 7890B gas chromatograph, an Agilent 5977B mass spectrometer and a Zoxe-2 LN2 cooled-loop thermal module. The GC oven was heated from 70 °C to 290 °C at a heating rate of 3 °C min−1, and the modulator was heated from 280 °C to 300 °C at a heating rate of 15 °C min−1. The detector can analyze m/z signals of tar from 45 to 330 amu. The composition of char was analyzed by Chinese standards of GB/T212-2008 and GB/T476-2001.
3. Results and discussion
3.1 Influence of simulated coal gas on the distribution of pyrolysis products
Fig. 3 shows the yields of pyrolysis products under N2 and SCGG at different temperatures. It can be seen that the yields of pyrolysis products under N2 and SCGG exhibited the same trend with increasing temperature from 500 to 700 °C. The tar yield under N2 and SCGG increased from 550 to 600 °C and then decreased. The char yield decreased from 550 to 700 °C while the gas, water, and coke yields (including coke-S and coke-D) increased gradually. This could be attributed to increasing pyrolysis temperature promoting the release of volatiles, resulting in the decrease of char yield and increase of tar, pyrolysis gases, and water yields at 550 to 600 °C. When the pyrolysis temperature exceeded 600 °C, the secondary reaction of volatiles was intensified. Tar precursors tended to crack into pyrolysis gases or polycondensate into coke, leading to the decrease of tar yield.
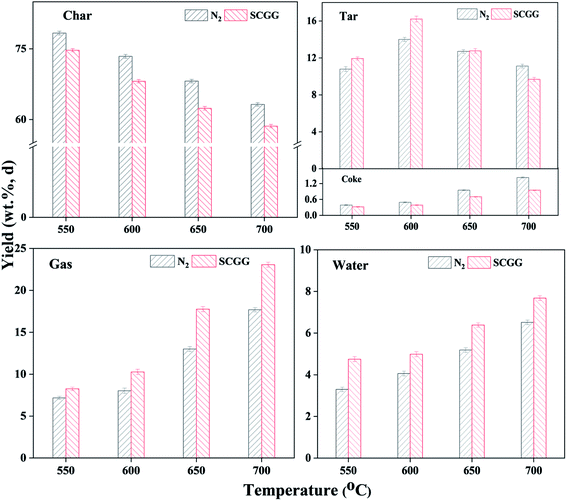 |
| Fig. 3 Yields of pyrolysis products under N2 and SCGG at different temperatures. | |
Further comparing the yields of pyrolysis products of tar under N2 and SCGG, they were significantly different at the same temperature, suggesting SCGG participated in the coal pyrolysis. The tar yields under SCGG at 550 and 600 °C were 11.94 wt% and 16.22 wt%, which were 9.63% and 15.70% higher than that under N2, respectively. Combined with the yields of pyrolysis products under individual gas at 600 °C in Fig. 4, it can be seen that compared with N2, H2, CO, and CO2 promoted tar yield at 600 °C while steam had little impact on tar yield, and the action of H2 was relatively obvious. Meanwhile, the char yields under H2, CO, and CO2 were lower than that under N2. During coal pyrolysis, H2 can diffuse into the coal particles and react with solid-phase free radicals in coal to promote the release of volatile matter;26 for another, it can inhibit the secondary reaction of gas-phase volatile radicals from coal pyrolysis via combining with them, blocking the formation of char and coke.27 This was also consistent with the char and coke yields under H2 and SCGG were lower than those under N2 at the same temperature. The action of CO could be similar to that of H2 because the existence of water gas shift reaction (WGS: CO + H2O → CO2 + H2) between CO and H2O from coal pyrolysis. The water yield under CO was lower than that under N2, suggesting the occurrence of WGS reaction. In addition, SCGG included 15% steam, which could promote the WGS reaction. By thermodynamic calculation, the WGS reaction could occur under SCGG at 550 to 700 °C. However, the water yield under SCGG was higher than that under N2 at the same temperature. Some oxygen-containing radicals in volatiles could react with H2 to form water, increasing the water yield,27,28 so it is suggested that the increase of water yield under SCGG depended on the comprehensive effect of H2 and WGS. The promotion of CO2 on tar formation was attributed to its inductive effect on the decomposition of chemical bonds in coal/char.29,30 Under CO2 atmosphere, adsorbed active C(O) and C can be generated due to the dissociative adsorption of CO2 on coal/char during pyrolysis, which can inductive the cracking of organic groups on the coal/nascent char and further increase the tar yield.30
 |
| Fig. 4 Yields of pyrolysis products under individual gas at 600 °C. | |
Further, comparing the tar yields under different atmospheres, the tar yield under SCGG, H2, CO and CO2 were 2.21 wt%, 1.70 wt%, 0.90 wt% and 0.94 wt% higher than that under N2, respectively. The increment of tar yield under SCGG was lower than the sum of the increments of that under H2, CO and CO2. It is because during pyrolysis, the interactions between different gases and coal are mutually affected. For example, CO2 could occupy a certain number of active centers of coal hydrogenation reaction, which reduces the chance of contact between H2 and with solid-phase free radicals in coal.31 In a similar way, H2 could also take up adsorption sites of CO2 on coal/char during pyrolysis, weakening the promotion of CO2 to coal cracking. In addition, compared with coal pyrolysis at 550 °C, the difference of tar yield at 600 °C under N2 and SCGG was more obvious, showing that SCGG was more likely to be activated and participate in the coal pyrolysis system at relatively high temperature. With the further increase of pyrolysis temperature, the tar yield under SCGG and N2 presented different regularities. The tar yield under SCGG was relatively close to that under N2 at 650 °C, while it was distinctly lower than the latter at 700 °C. It is inferred that increasing temperature promotes the reforming reactions of nascent tar with steam in SCGG to cause tar loss.32 The steam in the atmosphere can react with the evolved tar leading to larger yields of non-condensable components at higher temperature. It is also observed that the differences of the yield of pyrolysis gases under SCGG and N2 were more obvious at 650 and 700 °C.
Fig. 5(a) shows the coke suspended in tar (coke-S) and the coke deposited on reactor wall (coke-D) yields under N2 and SCGG at different temperature. Their formations are attributed to the volatiles reactions. It can be seen that compared with under N2, the coke-S and coke-D yields under SCGG were lower at the same temperature. In conjunction with Fig. 5(b), the coke-S and coke-D yields under H2 and CO were obviously lower than that under N2 at 600 °C, while those under CO2 and steam had little change. This demonstrates that the decrease of coke-S and coke-D yields under SCGG was mainly due to the effect of H2 and CO in SCGG. The macromolecular volatile radicals were generally the precursor of coke and they were prone to recombine to form coke in the absence of H source.33 When introduction of hydrogen source into the volatile system, it could provide active H to hinder the polycondensation reactions of macromolecule volatile radicals, reducing the formation of coke-S and coke-D. It is also noted that the differences of the coke-S and coke-D yields under N2 and SCGG were more obvious with increasing temperature. Compared with under N2, the coke-S and coke-D yields under SCGG at 550 °C reduced by 13.68% and 21.25%, respectively, while that under SCGG at 700 °C reduced by 29.64% and 37.10%. This validated that H2 was easier to be activated and participate in the coal pyrolysis system with increasing temperature.
 |
| Fig. 5 Yields of coke-S and coke-D under N2 and SCGG at different temperatures (a) and under individual gas at 600 °C (b). | |
3.2 Influence of simulated coal gas on the fraction distribution of tar
The effect of simulated coal gas on the fraction distribution of tar is presented in Fig. 6(a). Overall, under both N2 and SCGG, light tar content decreased gradually while the pitch content increased with increasing temperature between 550 and 700 °C. With the increase of pyrolysis temperature, the macromolecular network in coal began to break down except for the cleavage of some bridged bonds and side chains, generating larger free radical fragments; for another, the polycondensation reactions of the volatile radicals were promoted with increased temperature.34 However, compared with N2, SCGG increased the content of light tar and decreased the content of pitch at the same temperature, and the action of SCGG was more significant at higher temperature. The content of pitch under SCGG under 550, 600, 650 and 700 °C was 9.52%, 15.89%, 19.77% and 20.55% lower than those under N2 at the same temperature, respectively. From Fig. 6(b), it can be seen that light tar contents under H2 and CO atmosphere were obviously higher than that under N2 at 600 °C while the pitch contents under H2 and CO were lower. The distribution of tar fraction under CO2 and steam was basically the same as that under N2. This result proved that the effects of H2 and CO in SCGG were responsible for the change of tar fraction. As mentioned above, these pyrolysis gas atmospheres not only react with coal, but also participate in the volatiles' reactions. H2 could timely stabilize free radicals, restraining the secondary reaction of volatile radicals, and its action was more obvious at a higher temperature. CO had similar action with H2 because of the occurrence of WGS. The polycondensation reactions of volatiles radicals were prevented by H2 in SCGG and from WGS, reducing the transformation from light tar to pitch. In addition, the reforming reactions of volatile radicals with steam in SCGG were also beneficial to the formation of light tar at 650 and 700 °C. With increasing pyrolysis temperature, the steam became more active and could react with volatile radicals. The heavy tar in volatile radicals, such as pitch, has larger aromatics, which is more likely to develop complicated molecular structures in three dimensions,35 providing more contacting points with steam; furthermore, the average bond energy of larger aromatics is low partially due to the stereo-hindrance effect.35 Therefore, the pitch in volatile radicals was more prone to react with steam, transforming into light tar or gas, resulting in the increase of light tar. The studies of Chen et al.36 and Wang et al.37 also showed steam could promote the cracking of heavy tar (larger aromatic rings) to form light tar (smaller aromatic rings) by steam reforming reactions at above 600 °C.
 |
| Fig. 6 Fraction distribution of tar under N2 and SCGG at different temperatures (a) and under individual gas at 600 °C (b). | |
3.3 Influence of simulated coal gas on the chemical composition of tar
Fig. 7(A) shows the chemical composition of tar under N2 and SCGG at different temperature. The contents of aliphatics, oxygenated compounds, and heterocyclic compounds in tar decreased while the content of aromatics increased from 550 to 700 °C. The content of phenolics in tar increased from 550 to 600 °C and then decreased with a further increase in the temperature. This was mainly resulted from the competition between volatiles' release and secondary reactions, as discussed in Section 3.1.
 |
| Fig. 7 Chemical composition of tar under N2 and SCGG at different temperatures (A) and under individual gas at 600 °C (B) ((a) aliphatics, (b) phenols, (c) oxygenated compounds. (d) aromatics, (e) heterocyclic compounds). | |
Comparing the chemical composition of tar under N2 and SCGG, it can be seen that the contents of phenols, oxygenated compounds, and heterocyclic compounds in tar under SCGG were lower than those under N2 at the same temperature. In contrast, the content of aromatics was the opposite. In combination with Fig. 7(B), the changes of the chemical composition of tar under H2, CO and SCGG were similar in comparison with under N2 at 600 °C, showing that the effects of H2 and CO in SCGG on the chemical composition of tar were dominant. The phenols, oxygenated compounds, and heterocyclic compounds contain polar Cal–O (Car–O), Cal–S (Car–S), or Cal–N (Car–N) bonds, which are relatively unstable tar components.38 They are easier to participate in chemical reactions including hydrodeoxygenation, hydrodesulfurization, or hydrodenitrogenation under action of H2.25 Thus, a part of phenols, oxygenated compounds, and heterocyclic compounds converted into aromatics in the effect of H2 from SCGG and WSG. Also, they may react with steam under SCGG at a relatively high temperature, translating into non-condensable gases, resulting in the decrease of oxygenated compounds in tar.39,40 Besides, the increasing aromatics content in tar was also ascribed to the more release of volatile matter with aromatic structure in coal under SCGG.
The contents of aliphatics and oxygenated compounds in tar under CO2 atmosphere were higher than those under N2, while the content of aromatics was lower. This may be due to that the organic groups containing some weak bonds on coal/char, such as ester, ether, aliphatic linkages, were easier to be induced by the generated active sites (active O, C, C(O)) under CO2, and further decomposed to oxygenated and aliphatic radicals. They combined with other radicals in volatiles, generating aliphatics and oxygenated compounds.
Furthermore, the more obvious difference of the tar's composition under N2 and SCGG at 650 and 700 °C can be attributed to the increasingly intensive hydrogenation and reforming reactions of nascent tar. It is also noted that the content of aliphatics in tar under SCGG was higher than that under N2 at 550 and 600 °C, whereas it was lower at 650 and 700 °C. This resulted from the comprehensive action of hydrogenation and reforming reactions. At 550 and 600 °C, some oxygenated compounds, such as aliphatic acids, aliphatic ethers, and aliphatic ketones, decomposed into aliphatics through hydrogenation reactions. With the increase of temperature, the reforming reactions of nascent tar with steam existed except for the hydrogenation reactions. Some aliphatics in tar could react with steam, transforming into non-condensable gases.
3.4 Influence of simulated coal gas on the composition of char
Table 2 illustrates the composition of char under N2 and SCGG at different temperature. The ash and fixed carbon contents of char under N2 and SCGG were increased from 550 to 700 °C. In contrast, the volatile content of char was decreased due to the increasing decomposition of organic matter in coal with increasing temperature. At the same time, the carbon content of char was increased while the hydrogen and oxygen contents of char were decreased, leading to the decrease of H/C and O/C ratios in char.
Table 2 Composition of char under N2 and SCGG at different temperaturea
Pyrolysis condition |
Proximate analysis (wt%) |
Ultimate analysis (wt%, daf) |
H/C |
O/C |
Ad |
Vdaf |
FCdaf |
C |
H |
N |
S |
Ob |
ad: air-dry basis, daf: dry-and-ash-free basis. By difference. |
550 °C/N2 |
6.71 |
40.51 |
59.49 |
76.20 |
4.27 |
0.95 |
0.29 |
18.28 |
0.672 |
0.180 |
600 °C/N2 |
7.23 |
37.89 |
62.11 |
77.54 |
3.82 |
1.00 |
0.24 |
17.40 |
0.591 |
0.168 |
650 °C/N2 |
7.59 |
33.70 |
66.30 |
79.20 |
3.24 |
1.03 |
0.25 |
16.27 |
0.491 |
0.154 |
700 °C/N2 |
8.02 |
28.23 |
71.77 |
80.69 |
3.06 |
0.97 |
0.29 |
14.98 |
0.455 |
0.139 |
550 °C/SCGG |
6.94 |
36.21 |
63.79 |
77.65 |
3.62 |
1.00 |
0.28 |
17.44 |
0.559 |
0.168 |
600 °C/SCGG |
7.66 |
32.59 |
67.41 |
78.61 |
3.33 |
1.05 |
0.33 |
16.68 |
0.508 |
0.159 |
650 °C/SCGG |
8.30 |
29.37 |
70.63 |
79.92 |
3.14 |
1.03 |
0.28 |
15.62 |
0.471 |
0.147 |
700 °C/SCGG |
8.86 |
25.93 |
74.07 |
81.71 |
2.89 |
1.07 |
0.27 |
14.05 |
0.424 |
0.129 |
Furthermore, the ash and fixed carbon contents of char under SCGG were higher than those under N2, while the volatile content of char was the opposite at the same temperature. And the H/C and O/C ratios of char under SCGG were also lower than under N2 at the same temperature. Combining with Table 3, the change of the composition of char under H2, CO, and CO2 atmospheres was inconsistent with that under SCGG at 600 °C. This showed that H2, CO, and CO2 in SCGG facilitated the release of volatiles, resulting in decreased H/C and O/C ratios in char from coal pyrolysis. This was agreed with the char yield under those atmospheres, as shown in Fig. 3 and 4. H2 from SCGG and WSG could react with solid-phase free radicals in coal to promote the release of volatile matter, getting more volatiles in coal/char into the gas phase. CO2 in SCGG could promote the cracking of coal/nascent char, increasing the release of volatiles in coal/char. It is also noted that the composition of char under SCGG at 600 °C was close to that under H2, indicating that H2 in SCGG played a more critical role.
Table 3 Composition of char under individual gas at 600 °Ca
Pyrolysis condition |
Proximate analysis (wt%) |
Ultimate analysis (wt%, daf) |
H/C |
O/C |
Ad |
Vdaf |
FCdaf |
C |
H |
N |
S |
Ob |
ad: air-dry basis; daf: dry-and-ash-free basis. By difference. |
N2 |
7.23 |
37.89 |
62.11 |
77.54 |
3.82 |
1.00 |
0.24 |
17.40 |
0.591 |
0.168 |
H2 |
7.69 |
33.15 |
66.85 |
78.40 |
3.38 |
0.95 |
0.28 |
16.79 |
0.517 |
0.161 |
CO |
7.40 |
34.42 |
65.58 |
78.10 |
3.56 |
0.94 |
0.26 |
17.14 |
0.546 |
0.164 |
CO2 |
7.46 |
34.58 |
65.42 |
77.97 |
3.67 |
0.97 |
0.21 |
17.18 |
0.565 |
0.165 |
H2O |
7.26 |
37.53 |
62.47 |
77.38 |
3.90 |
1.03 |
0.20 |
17.49 |
0.605 |
0.169 |
3.5 Influence of simulated coal gas from char gasification on the novel poly-generation process
Based on the above analysis, SCGG played a different role at different temperature (550–700 °C) during coal pyrolysis, resulting in the change of distribution and composition of pyrolysis products. In particular, the changes of high value-added tar yield and quality (coke yield (coke-S), pitch content, oxygenated compounds content) would affect the stable operation and economic efficiency of the process and subsequent processing of tar.13,15,41,42 SCGG had a positive effect on tar yield and quality at 500 and 600 °C, especially at 600 °C. Compared with under N2, the tar yield under SCGG increased by 15.70% at 600 °C while coke-S yield under SCGG decreased by 16.47%. Meanwhile, the pitch content and oxygenated compounds content in tar under SCGG was 15.89% and 16.72% lower than that under N2 at 600 °C, respectively. The increase of tar yield was beneficial to the economic feasibility of the process, and the decrease of coke-S yield, pitch content and oxygenated compounds content in tar were helpful for the stable operation of the process and the tar subsequent utilization. When the pyrolysis temperature exceeded 600 °C, SCGG decreased tar yield despite improving tar quality, which lead to the weakening of economic efficiency of the process. Compared with under N2, the tar yield under SCGG dropped by 12.86% at 700 °C. Therefore, the effect of SCGG on coal pyrolysis at different temperature should be taken into account comprehensively in the design and operation optimization of the process.
4. Conclusions
The rapid pyrolysis behavior of low rank coal under N2 and simulated coal gas from char gasification (SCGG) from 550 to 700 °C was investigated in a downer pyrolyzer. Compared with pyrolysis under N2, SCGG was beneficial to tar formation below 600 °C due to the reactions of H2 in SCGG and those from WGS (CO + H2O → CO2 + H2) with solid-phase free radicals in coal and their inhibiting effect on the secondary reaction of gas-phase volatile radicals, and promotion of CO2 on coal cracking. Above 600 °C, the reforming reactions of nascent tar with steam reduced the tar yield. The highest tar yield (16.22 wt%) was obtained under SCGG at 600 °C, 15.70% higher than that under N2. Also, the inhibition of H2 from SCGG and WGS on the secondary reaction of volatile radicals and the reforming reactions of nascent tar reduced the coke yield (coke-S) and pitch content in tar. The contents of phenols, oxygenated compounds, and heterocyclic compounds in tar under SCGG were lower than those under N2 at the same temperature, while the content of aromatics was the opposite due to hydrogenation and reforming reactions of nascent tar. These differences were more evident at higher temperature, which could be attributed to that increasing temperature activated the SCGG more easily. The effects of SCGG on the distribution and composition of pyrolysis products are closely related to the stable operation and economic efficiency of the process and subsequent processing of tar. Thus, these results will guide the industrialization of the proposed novel poly-generation process and other similar processes.
Conflicts of interest
The authors declare that there are no conflicts of interest.
Acknowledgements
The work was financially by the National Key Research and Development Plan Project of China (No. 2016YFB0600302) and the National Natural Science Foundation of China (No. 22078224, 21706173).
Notes and references
- Z. Rao, Y. Zhao, C. Huang, C. Duan and J. He, Recent developments in drying and dewatering for low rank coals, Prog. Energy Combust. Sci., 2015, 46, 1–11 CrossRef.
- H. Osman, S. Jangam, J. Lease and A. Mujumdar, Drying of low-rank coal-A review of recent patents and innovations, Drying Technol., 2011, 29, 1763–1783 CrossRef CAS.
- Y. Zhang, Y. Wang, L. Cai, C. Yao, S. Gao, C. Li and G. Xu, Dual bed pyrolysis gasification of coal: process analysis and pilot test, Fuel, 2013, 112, 624–634 CrossRef CAS.
- Z. Guo, Q. Wang, M. Fang, Z. Luo and K. Cen, Thermodynamic and economic analysis of polygeneration system integrating atmospheric pressure coal pyrolysis technology with circulating fluidized bed power plant, Appl. Energy, 2014, 113, 1301–1314 CrossRef CAS.
- D. Pan, X. Qu and J. Bi, Effect of gasified semi-coke on coal pyrolysis in the poly-generation of CFB gasification combined with coal pyrolysis, J. Anal. Appl. Pyrolysis, 2017, 127, 461–467 CrossRef CAS.
- Y. Li, C. Fan and W. Song, Pyrolysis-bridged hybrid power systems and their application for thermal power plants, Energy Fuels, 2014, 28, 6531–6539 CrossRef CAS.
- R. Zhang, Thermodynamic and economic analysis of a coal staged conversion utilization polygeneration system, Energy Technol., 2015, 3, 646–657 CrossRef CAS.
- R. Zhang, Y. Chen, K. Lei, B. Ye, J. Cao and D. Liu, Thermodynamic and economic analyses of a novel coal pyrolysis-gasification-combustion staged conversion utilization polygeneration system, Asia-Pac. J. Chem. Eng., 2018, 13, 1932–2135 CrossRef PubMed.
- T. Lv, M. Fang, H. Li, J. Yan, J. Cen, Z. Xia, J. Tian and Q. Wang, Pyrolysis of a typical low-rank coal: application and modification of the chemical percolation devolatilization model, RSC Adv., 2021, 11, 17993 RSC.
- R. Liu, M. Liu, P. Fan, Y. Zhao and J. Yan, Thermodynamic study on a novel lignite poly-generation system of electricity-gas-tar integrated with pre-drying and pyrolysis, Energy, 2018, 165, 140–152 CrossRef CAS.
- Z. Liu, X. Guo, L. Shi, W. He, J. Wu, Q. Liu and J. Liu, Reaction of volatiles-a crucial step in pyrolysis of coals, Fuel, 2015, 154, 361–369 CrossRef CAS.
- Y. Zhang, P. Liang, J. Yu, J. Zhu and X. Qin, Studies of granular bed filter for dust removal in the process of coal pyrolysis by solid heat carrier, RSC Adv., 2017, 7, 20266 RSC.
- Q. Zhou, Q. Liu, L. Shi, Y. Yan and Z. Liu, Behaviors of coking and radicals during reaction of volatiles generated from fixed-bed pyrolysis of a lignite and a subbituminous coal, Fuel Process. Technol., 2017, 161, 304–310 CrossRef CAS.
- W. He, Z. Liu, Q. Liu, M. Liu, X. Guo, L. Shi, J. Wu, X. Guo and D. Ci, Analysis of tars produced in pyrolysis of four coals under various conditions in a viewpoint of radicals, Energy Fuels, 2015, 29, 3658–3663 CrossRef CAS.
- J. Wu, Q. Liu, R. Wang, W. He, L. Shi, X. Guo, Z. Chen, L. Ji and Z. Liu, Coke formation during thermal reaction of tar from pyrolysis of a subbituminous coal, Fuel Process. Technol., 2017, 155, 68–73 CrossRef CAS.
- J. Edwards, K. Schluter and R. Tyler, Upgrading of flash pyrolysis tars to synthetic crude oil: 1. first stage hydrotreatment using a disposable catalyst, Fuel, 1985, 64, 594–599 CrossRef CAS.
- J. Kong, M. Wang, Y. Yu, T. Li, L. Chang and W. Bao, A device for coupling pyrolysis and gasification to produce oil and gas and its use, China Patent, CN 108048140 A, 2017 Search PubMed.
- L. Jin, H. Zhao, M. Wang, B. Wei and H. Hu, Effect of temperature and simulated coal gas composition on tar production during pyrolysis of a subbituminous coal, Fuel, 2019, 241, 1129–1137 CrossRef CAS.
- C. Braekman-Danheux, R. Cyprès, A. Fontana and M. Van Hoegaerden, Coal hydromethanolysis with coke-oven gas. 2: influence of the coke-oven gas components on pyrolysis yields, Fuel, 1995, 74, 17–19 CrossRef CAS.
- C. Braekman-Danheux, A. Fontana, A. Labani and P. Laurent, Coal hydromethanolysis with coke-oven gas. 3: influence of the coke-oven gas components on the char characteristics, Fuel, 1996, 75, 1274–1278 CrossRef.
- R. Xiong, L. Dong, J. Yu, X. Zhang, L. Jin and G. Xu, Fundamentals of coal topping gasification: Characterization of pyrolysis topping in a fluidized bed reactor, Fuel Process. Technol., 2010, 91, 810–817 CrossRef CAS.
- M. Zhong, Z. Zhang, Q. Zhou, J. Yue, S. Gao and G. Xu, Continuous high-temperature fluidized bed pyrolysis of coal in complex atmospheres: Product distribution and pyrolysis gas, J. Anal. Appl. Pyrolysis, 2012, 97, 123–129 CrossRef CAS.
- J. Liu, H. Hu, L. Jin, P. Wang and S. Zhu, Integrated coal pyrolysis with CO2 reforming of methane over Ni/MgO catalyst for improving tar yield, Fuel Process. Technol., 2009, 91, 419–423 CrossRef.
- J. Liu, H. Hu, L. Jin, P. Wang and S. Zhu, Effects of the catalyst and reaction conditions on the integrated process of coal pyrolysis with CO2 reforming of methane, Energy Fuels, 2009, 23, 4782–4786 CrossRef CAS.
- C. Fushimi, S. Okuyama, M. Kobayashi, M. Koyama, H. Tanimura, H. Fukushima, S. Thangavel and K. Matsuoka, Pyrolysis of low-rank coal with heat-carrying particles in a downer reactor, Fuel Process. Technol., 2017, 167, 136–145 CrossRef CAS.
- Y. Tang, Y. Wang and P. Cui, Research progress and prospect in hydropyrolysis of coals, Anhui Chem. Ind., 2018, 5, 4–7 Search PubMed.
- H. Jüntgen, Review of the kinetics of pyrolysis and hydropyrolysis in relation to the chemical constitution of coal, Fuel, 1984, 63, 731–737 CrossRef.
- J. Ibarra, R. Moliner, J. Miranda and R. Cypres, Pyrolysis under H2 and He of Utrillas coal, Fuel, 1988, 67, 464–468 CrossRef CAS.
- S. Niu, Y. Zhou, S. Zhu, L. Ren, L. Yan, F. Li and Y. Bai, Investigation into the yields and characteristics of products from lignite low-temperature pyrolysis under CO2 and N2 atmospheres, J. Anal. Appl. Pyrolysis, 2019, 138, 161–169 CrossRef CAS.
- S. Gao, L. Zhai, Y. Qin, Z. Wang, J. Zhao and Y. Fang, Investigation into the cleavage of chemical bonds induced by CO2 and its mechanism during the pressurized pyrolysis of coal, Energy Fuels, 2018, 32, 3243–3253 CrossRef CAS.
- H. Liao, C. Sun and B. Li, Coal pyrolysis with hydrogen-rich gases. Coal pyrolysis with coke-oven gas, J. Fuel Chem. Technol., 1997, 2, 114–118 Search PubMed.
- J. Hayashi, H. Takahashi, M. Iwatsuki, K. Essaki and A. Tsutsumi, Rapid conversion of tar and char from pyrolysis of a brown coal by reactions with steam in a drop tube reactor, Fuel, 2000, 79, 439–447 CrossRef CAS.
- Z. Liu, Advancement in coal chemistry: structure and reactivity, Sci. Sin.: Chim., 2014, 44, 1431–1435 CAS.
- Q. Zhou, Q. Liu, L. Shi, Y. Yan, J. Wu, C. Xiang, T. Wang and Z. Liu, Effect of volatiles’ reaction on composition of tars derived from pyrolysis of a lignite and a bituminous coal, Fuel, 2019, 242, 140–148 CrossRef CAS.
- S. Zhang, Z. Chen, H. Zhang, Y. Wang, X. Xu, L. Cheng and Y. Zhang, The catalytic reforming of tar from pyrolysis and gasification of brown coal: Effects of parental carbon materials on the performance of char catalysts, Fuel Process. Technol., 2018, 174, 142–148 CrossRef CAS.
- Z. Chen, Y. Shi, D. Lai, S. Gao, Z. Shi, Y. Tian and G. Xu, Coal rapid pyrolysis in a transport bed under steam-containing syngas atmosphere relevant to the integrated fluidized bed gasification, Fuel, 2016, 176, 200–208 CrossRef CAS.
- F. Wang, H. Ren, Y. Wang and L. Cui, Formation and transformation law of tar during pyrolysis and gasification of Shengli Brown, Coal Sci. Technol., 2016, 44, 189–193 Search PubMed.
- L. Shi, Q. Liu, X. Guo, W. Wu and Z. Liu, Pyrolysis behavior and bonding information of coal- A TGA study, Fuel Process. Technol., 2013, 108, 125–132 CrossRef CAS.
- X. Zeng, Y. Wang, J. Yu, S. Wu, M. Zhong, S. Xu and G. Xu, Coal pyrolysis in a fluidized bed for adapting to a two-stage gasification process, Energy Fuels, 2011, 25, 1092–1098 CrossRef CAS.
- Y. Tursun, S. Xu, G. Wang, W. Chao and Y. Xiao, Tar formation during co-gasification of biomass and coal under different gasification condition, J. Anal. Appl. Pyrolysis, 2015, 111, 191–199 CrossRef CAS.
- Y. Huang, W. Li, G. Wu, J. Feng and Q. Yi, Comparative analysis of typical low rank coal pyrolysis technology based on a Nonlinear Programming Model, Energy Fuels, 2017, 31, 12977–12987 CrossRef CAS.
- X. Jin, X. Li, J. Kong, W. Xie, M. Wang, J. Wang, W. Bao and L. Chang, Insights into coke formation during thermal reaction of six different distillates from the same coal tar, Fuel Process. Technol., 2021, 211, 106592 CrossRef CAS.
|
This journal is © The Royal Society of Chemistry 2021 |
Click here to see how this site uses Cookies. View our privacy policy here.