DOI:
10.1039/D1RA05034F
(Review Article)
RSC Adv., 2021,
11, 36273-36288
Engineering encapsulated ionic liquids for next-generation applications
Received
29th June 2021
, Accepted 21st October 2021
First published on 12th November 2021
Abstract
Ionic liquids (ILs) have attracted considerable attention in several sectors (from energy storage to catalysis, from drug delivery to separation media) owing to their attractive properties, such as high thermal stability, wide electrochemical window, and high ionic conductivity. However, their high viscosity and surface tension compared to conventional organic solvents can lead to unfavorable transport properties. To circumvent undesired kinetics effects limiting mass transfer, the discretization of ILs into small droplets has been proposed as a method to increase the effective surface area and the rates of mass transfer. In the present review paper, we summarize the different methods developed so far for encapsulating ILs in organic or inorganic shells and highlight characteristic features of each approach, while outlining potential applications. The remarkable tunability of ILs, which derives from the high number of anions and cations currently available as well as their permutations, combines with the possibility of tailoring the composition, size, dispersity, and properties (e.g., mechanical, transport) of the shell to provide a toolbox for rationally designing encapsulated ILs for next-generation applications, including carbon capture, energy storage devices, waste handling, and microreactors. We conclude this review with an outlook on potential applications that could benefit from the possibility of encapsulating ILs in organic and inorganic shells.
1. Introduction
Ionic liquids (ILs) are a class of organic salts that consist of cations and weakly coordinating anions.1–4 The low melting temperature of ILs, which is close to or even below room temperature, is the result of the difference in size of anions and cations, as well as the charge delocalization and geometric asymmetry of (at least) one of the ions. The unique properties of ILs (e.g., high thermal stability, low flammability, wide electrochemical window, low vapor pressure, and high ionic conductivity) have made them candidate materials for several applications, including as electrolytes in energy storage devices,5 additives in lubricants,6 and separation media.7 One particularly attractive feature of ILs is their tunability: owing to the number of permutations of cations and anions, ILs can be designed and synthesized with task-specific properties, which has led to consider ILs as “designer solvents”.2–4
The broad applicability of ILs has resulted in a continuously growing number of published papers related to their investigation (Fig. 1). In the case of studies exploring the potential use of ILs as electrolytes for energy storage devices, adsorbed layers on solid catalysts, or lubricants, significant efforts have been spent in evaluating the structure and dynamical evolution of solid/IL interfaces as they determine the functional behavior (e.g., charge storage of supercapacitors, friction reduction).8–22 The confinement of ILs in nanoscale geometries creates radically different conditions than the ones in the bulk phase, and promotes a strong interaction with the boundaries of the confining matrix, which affects the behavior of ILs (e.g., phase transition, wetting, and ion mobility).19,21,22
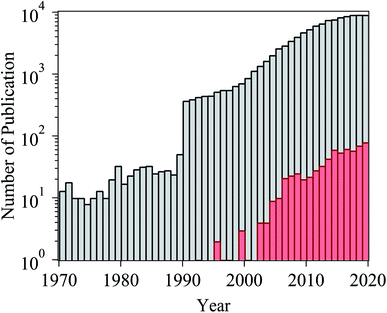 |
| Fig. 1 Number of publications per year that include “ionic liquid” (black bars) or “encapsulated ionic liquid” (red bars) in the title, abstract, or keywords (data obtained from Web of Science in February 2021). | |
In the case of studies aiming to use ILs as separation or reaction media, the high viscosity and surface tension of these fluids compared to conventional organic solvents can lead to unfavorable transport properties. To circumvent undesired kinetics effects limiting mass transfer, ILs have been supported on solids to combine the advantages of using ILs as solvents with the ones of solid-based technologies.23 These early efforts focused on the stabilization of ILs on a variety of solid supports, such as porous silica,24–26 membranes,23,27 and electrolytes.28 Recently, the discretization of ILs into small droplets has been proposed as a method to increase the effective surface area and mass transfer rate.24,29–40 Since the first report demonstrating the possibility of encapsulating ILs within microcapsules, several research groups have developed methodologies for discretizing ILs in microscopic particles with engineered transport properties. In light of the numerous developments reported in the literature, this review article aims to provide an overview on the methodologies developed so far for encapsulating ILs, the criteria for their selection (section 2), and the application of encapsulated ILs (section 3). This contribution ends with a perspective about potential future applications of encapsulated ILs (section 4).
2. Methods of encapsulation
Several methods for encapsulating ILs within a shell made of a second material have been reported in the literature. Table 1 lists the different methods together with details about the encapsulated ILs, the shell material, and the size distribution of the capsules. Fig. 2 displays schematics for each method presented below.
Table 1 Methods for encapsulating ionic liquids (ILs) within an organic or inorganic shell. Details about the encapsulated IL, shell composition, and size distribution of the microcapsules are also provided. The chemical structures of cations and anions constituting the ILs are, respectively, reported in Tables 2 and 3 in the Appendix
Encapsulation method |
Ionic liquid |
Shell type |
Size distribution (μm) |
Ref. |
Cation |
Anion |
Emulsion polymerization |
[BMIM] |
[TFSI] |
Poly(butyl methacrylate-co-ethylene glycol dimethacrylate) |
5–15 |
41 |
[HMIM] |
[TFSI] |
[BMIM] |
[PF6] |
Polyurea |
2–80 (average: 22) |
42 |
[BMIM] |
[PF6] |
Silica |
4–5 |
32 |
[BMIM] |
[PF6] |
2–14 (average: 7) |
43 |
[P6,6,6,14] |
[(C8)2PO2] |
0.3–1 |
44 |
[EMIM] |
[TFSI] |
Poly(thiourethane) and poly(amide-thioether) |
100–250 |
45 |
[HMIM] |
[TFSI] |
60–200 |
Impregnation |
[OMIM] |
[PF6] |
Activated carbon |
0.45 |
37 |
[P6,6,6,14] |
[2-CNPyr] |
0.31–0.53 |
46 |
[BMIM] |
[OAc] |
0.34 |
47 |
[EMIM] |
[NTf2] |
0.9 ± 0.1 |
48 |
[NH2,Me,EtOH] |
[Pe] |
[EtOHmim] |
[BF4] |
0.6 |
49 |
Choline |
[NTf2] |
[(EtOH)3MeN] |
[MeSO4] |
[P6,6,6,14] |
Cl |
Sodium alginate/gelatin |
∼2000 |
31 |
Pickering emulsion |
[BMIM] |
[PF6] |
Reduced graphene oxide |
25–100 |
50 |
[BMIM] |
[PF6] |
Polyurethane/lignin |
From 27 ± 18 to 105 ± 25 |
51 |
[BMIM] |
[PF6] |
Graphene oxide and polyurea |
10–35 |
52 |
[EMIM] |
[TFSI] |
[HMIM] |
[TFSI] |
[Mpp] |
[TFSI] |
[BM2IM] |
[PF6] |
[EMIM] |
[DMP] |
[BMIM] |
[BF4] |
10–25 |
[EMIM] |
[TFSI] |
Alkylated graphene oxide and polyurea |
5–55 |
53 |
[HMIM] |
[TFSI] |
3–38 |
Solvent evaporation |
[BMIM] |
[PF6] |
Polysulfone |
170–300 |
30 |
[EMIM] |
[TFSI] |
50–225 |
54 |
[HMIM] |
[TFSI] |
5–25 |
55 |
[BMIM] |
[PF6] |
44.2 |
35 |
[BMIM] |
[PF6] |
Polyacrylonitrile |
200–350 |
39 |
[BMIM] |
[BF4] |
[HMIM] |
[BF4] |
[BMIM] |
[TFSI] |
Polystyrene |
2 |
56 |
Vapor phase deposition |
[EMIM] |
[BF4] |
Poly(tetrafluoroethylene) + poly(1H,1H,2H,2H-perfluorodecyl acrylate-co-ethylene glycol diacrylate) |
2000 |
38 |
Non-solvent induced phase inversion |
[EMIM] |
[TFSI] |
Poly(vinylidene fluoride-co-hexafluoropropylene) |
1000–2000 |
57 |
Chemical patterning |
[BMIM] |
Cl |
Octadecyltrichlorosilane |
1–1.5 |
58 |
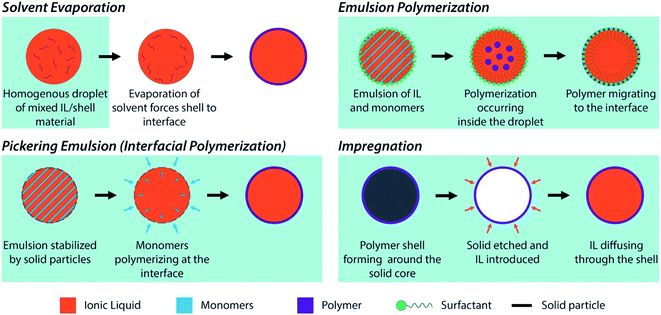 |
| Fig. 2 Schematic representations of the different methods used for the preparation of encapsulated ILs. | |
Specific characteristic of the capsules should be considered when designing and fabricating them, including: (a) capsule size distribution; (b) chemistry of the shell material; (c) shell thickness; and (d) shell properties (e.g., permeability, mechanical properties). The tunability of the capsules' chemistry, size, and properties provided by the synthetic approaches listed above combines with the versatility in combining varied cation–anion moieties (1018 ILs theoretically available)59 to pave the way towards the rational design of encapsulated ILs with task-specific properties for a variety of applications in several sectors (section 3). In the following, the most widely used encapsulation methods are briefly presented and discussed.
2.1 Emulsion polymerization
One of the most common methods of forming microcapsules across all types of materials is based on the process of emulsion polymerization,60–65 in which a polymer shell is formed at the liquid/liquid interface of an emulsion. The fundamental mechanisms of microemulsion polymerization have widely been explored and characterized. As a particular example, Loxley and Vincent66 provided a detailed discussion of the mechanisms and phenomena governing the formation of poly(methylmethacrylate) microcapsules with liquid cores. Compared to simpler solvent evaporation methods of capsule preparation (described in the following section), in emulsion polymerization the shell material is chemically bonded, typically via polymerization or cross-linking, once it is introduced to the emulsion interface. This enables complex formulations of shell materials, as component monomers can be added through both the disperse and continuous phases.42 Because of this, the materials selection process is less restrictive relative to solvent evaporation. Additionally, the plethora of polymeric materials currently available paves the way towards the systematic evaluation of changes in shell chemistry/structure on functional properties (e.g., gas permeability, mechanical properties), while providing opportunities for shell optimization.
As the creation of an IL microemulsion in a continuous phase is the first step in the preparation of polymeric microshells with IL core, particular attention should be paid in the parameters affecting the properties of the microemulsion. Recently, Hejazifar et al.67 exhaustively reviewed the types, mechanisms of formation, and applications of IL microemulsions. One notable feature of IL emulsions that was highlighted is their tunability and possibility of including long alkyl chains in the ions, which make them amphiphilic and allowing them to function as surfactants able to stabilize the microemulsion.
One specific class of encapsulation methods of IL microemulsions was described by the Minami group as an extension of the self-assembly of phase-separated polymer method,41 which is based on the authors' previous work with conventional oil in water microemulsions.68–70 In this method, the majority of the shell is formed by crosslinking ethylene glycol dimethacrylate (EGDM), though addition of polymethacrylates to the emulsion was shown to dramatically improve the internal capsule morphology. Fig. 3 displays an example of scanning electron microscopy (SEM) and transmission electron microscopy (TEM) micrographs of cross-sections of the prepared poly(triethylene glycol dimethacrylate/n-butyl methacrylate)/poly(n-butyl methacrylate)/[HMIM][TFSI] (P(TEGDM-BMA)/P(BMA)/[HMIM][TFSI]) composite particles, which exhibit a smooth surface morphology together with a single hollow inner structure.
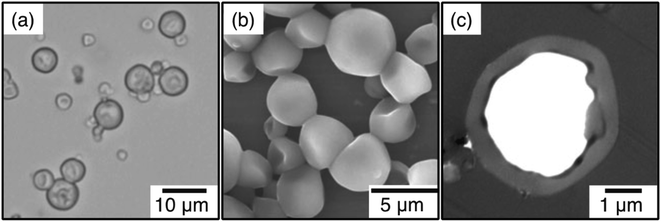 |
| Fig. 3 Optical micrograph (a), SEM (b), and TEM micrograph of ultrathin cross-section (c) of poly(triethylene glycol dimethacrylate/n-butyl methacrylate)/poly(n-butyl methacrylate)/[HMIM][TFSI] (P(TEGDM-BMA)/P(BMA)/[HMIM][TFSI]) composite particles prepared by microemulsion polymerization. [Reprinted with permission from ref. 41. Copyright (2013) Springer]. | |
Though most preparations of IL capsules via emulsion are based on an aqueous continuous phase, IL-in-oil emulsions have also been produced.67 An example of capsules created using an IL-in-oil emulsions was recently reported by Li et al.,45 who used poly(amide-thioether) as surfactant and exploited the IL (1-ethyl-3-methylimidazolium bis(trifluoromethylsulfonyl)imide [EMIM][TFSI], and 1-hexyl-3-methylimidazolium bis(trifluoromethylsulfonyl)imide [HMIM][TFSI]) to catalyze an IL/oil interfacial reaction and create a shell made of polythiourethane and poly(amide-thioether). Weiss et al.42 encapsulated 1-butyl-3-methylimidazolium hexafluorophosphate ([BMIM][PF6]) in polyurea microspheres by emulsification of [BMIM][PF6] in oil and interfacial polymerization of isocyanate and amine polymers, while also highlighting the changes necessary in the surfactant when carrying out the emulsification in oil vs. in water. Even though surfactants were adjusted depending on the continuous phase (oil or water), the capsule morphology and size distributions were mostly similar (Fig. 4).
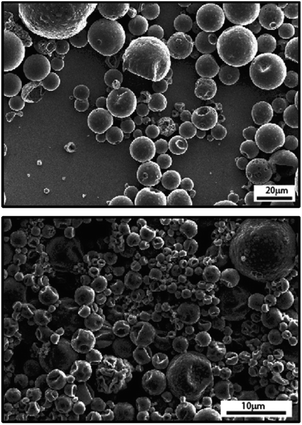 |
| Fig. 4 SEM micrographs of [BMIM][PF6] in polyurea capsules prepared via emulsion polymerization in water (top) and in oil (bottom). [Reprinted from React. Funct. Polym., Weiss, E.; Gertopski, D.; Gupta, M. K.; Abu-Reziq, R. Encapsulation of Ionic Liquid BMIm[PF6] within Polyurea Microspheres. 2015, 96, 32–38, with permission from Elsevier].42 | |
Finally, while microemulsion encapsulation has mostly been used to create polymeric shells, sol–gel condensation methods have also been employed to encapsulate ILs in solid capsules made of silica.32,43,44 This is typically achieved by direct addition of tetraethoxysilane (TEOS) to an IL emulsion prepared using organic surfactants tailored to the IL-water interface32,44 or dissolved gelatin, similar to that used in preparations utilizing solvent evaporation.43
Even though encapsulation via microemulsion polymerization is relatively straightforward and has great potential for further optimization owing to the tunability of the shell material enabled by our detailed knowledge of polymer chemistry, which allows several physico-chemical properties (e.g., permeability) and mechanical properties of the polymeric shell to be tailored for specific applications, a significant drawback observed with this fabrication method is that capsule sizes tend to be highly polydisperse, and none of the permutations of this method performed so far has managed to consistently generate capsule with diameters less than 5 μm. This limitation can greatly affect the potential use of encapsulated ILs due to negative impacts on capsule packing and long-term stability in suspensions.
2.2 Solvent evaporation
Encapsulation via solvent evaporation is one of the simplest and most direct methods of microcapsule preparation, and thus was one of the earliest methods utilized for IL encapsulation. This class of encapsulation methods has remained popular for its simplicity due to the high miscibility of ILs and most organic solvents. The driving mechanism for capsule formation is the evaporation of a volatile solvent containing both the IL and the shell material, resulting in self-organization of the mixture based on relative interfacial energies. The primary shell material selected for IL encapsulation has been polysulfones (PSFs),30,54 due to their solubility in both ILs and volatile solvents such as dichloromethane (DCM), and the ability to form durable, IL-impermeable shells without further polymerization or crosslinking.
A potential major advantage for solvent evaporation is the relative ease of integrating microfluidic fabrication, and its associated advantages. As microfluidics have already been applied in the field of microencapsulation owing to the possibility of achieving monodisperse populations of microparticles of different size and shapes,71–75 several published studies have explored the possibility of encapsulating IL via solvent evaporation using microfluidics devices.30,39,76 Yang et al. used solvent evaporation to create hollow PSF microcapsules containing [BMIM][PF6] IL using a two-stage microfluidic method,30 while Xiang et al. used a microfluidic device to create an emulsion from a mixture of poly(dimethylsiloxane) and n-butyl acetate as continuous phase and a dispersed phase made of polyacrylonitrile and ionic liquids ([BMIM][PF6], [BMIM][BF4], [HMIM][BF4]) dissolved in N,N-dimethylformamide, which was followed by the extraction of N,N-dimethylformamide to create the microcapsules.39 While the microfluidic technology provides the possibility of accurately controlling the size and distribution of the microcapsules, the encapsulation of IL through simple mechanical stirring could also be achieved, as demonstrated by Li et al., who synthesized PSF microcapsules filled with [EMIM][TFSI] IL.54
Among the methods described in this section, the solvent evaporation approach is the most conducive to large scale fabrication of encapsulated ILs, as the simple nature of the process combined with the possibility of precisely controlling the capsule size, which is enabled by the use of microfluidic devices, can allow for the production of relatively large quantities of capsules while minimizing variation within and between batches. However, the range of possible capsule compositions is relatively narrow, as the IL, shell material, and any potential additives must all be miscible (while mutually immiscible) with the carrying fluid.
2.3 Pickering encapsulation
The use of Pickering emulsions (i.e., emulsions stabilized by solid particles) as template for the encapsulation of ILs was pioneered by the group of Pentzer.50,52,53,77,78 This methodology, which employs either graphene oxide (GO) nanosheets or alkylated GO as surfactants, has two main advantages over other encapsulation methods: (a) the drastic reduction in the loading of the surfactant (in Pickering emulsions the surfactant/IL weight ratio is around ∼1/100, while in the case of systems relying on molecular surfactants this ratio is ∼1/10); and (b) the use of GO-based surfactants enables both IL-in-water and IL-in-oil emulsions to be created, thus allowing the selection of the most appropriate continuous phase for the IL under consideration. The latter advantage is particularly important in the case of ILs (most ILs are hygroscopic) as the possibility of performing the encapsulation in a water-free continuous phase enables the water content in the encapsulated IL to be carefully controlled. The selection of the GO-based surfactant strongly depends on the nature of the continuous phase: in the case IL-in-water systems, GO nanosheets stabilize the emulsions, while in the case of IL-in-oil systems the functionalization of GO nanosheets with alkyl amines of varying chain length can be used to stabilize the emulsions (Fig. 5).77
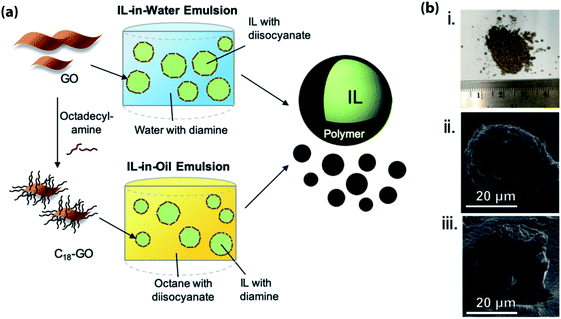 |
| Fig. 5 (a) Schematic representation for the preparation of encapsulated IL using either IL-in-water or IL-in-oil Pickering emulsions stabilized by GO nanosheets or alkylated GO nanosheets followed by interfacial polymerization; (b) photograph (i) and SEM micrographs ((ii) and (iii)) of ILs capsules. [Reprinted with permission from ref. 52. Copyright (2019) American Chemical Society]. | |
The stabilized Pickering emulsions could then be used as template for the formation of polymeric capsules via interfacial polymerization, in which the reaction occurs between reagents present both in the IL and in the continuous phase (water or oil). Most polymerization reactions have been carried out using di-isocyanates and diamines as the monomers are commercially available and the reactions do not result in the formation of byproducts. The resulting capsules incorporate a large amount of IL (65–85 wt%).50,51
2.4 Impregnation
The high affinity of ILs with activated carbon (AC)79 inspired Palomar et al. to encapsulate IL within carbon nanocapsules having a micro/mesoporous shell structure and a hollow core.37,46–48 The spherical capsules, which were synthesized by a template method,80,81 contained a high carbon content (i.e., >94 wt%), exhibited a homogeneous morphology with diameter lower than 1 μm and a high contribution of pores with diameter lower than 8 nm, and could incorporate a large amount of ILs (70–85 wt%). The discretization of the IL fluid into extremely small drops could drastically increase the gas/liquid contact area, thus enhancing the kinetics of adsorption processes, while not affecting the solvent capacity of ILs.37,46–48 An example of SEM and TEM micrographs of empty hollow carbonaceous submicrocapsules is reported in Fig. 6 together with micrographs of the same capsules filled with an IL (i.e., 1-butyl-methylimidazolium acetate, [BMIM][acetate]).47 While this method is capable of synthesizing capsules with sub-micron diameters and narrow size distributions, it is the most involved method described so far, with several steps required to fabricate the low diameter shells, which are described in detail by Alonso-Morales et al.81 Despite the potential of this method, the range of suitable shell materials has not been explored extensively, as only capsules using activated carbon shells have been investigated so far.
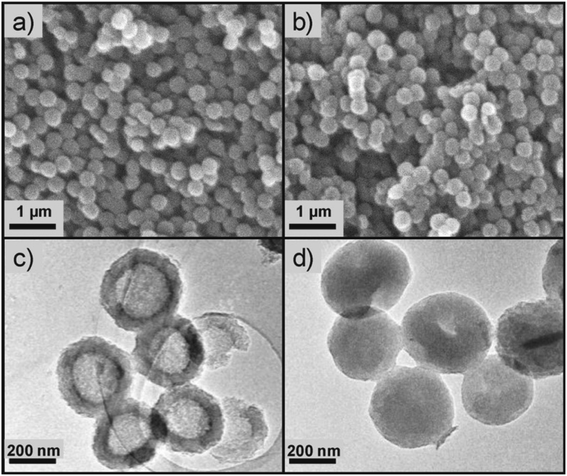 |
| Fig. 6 SEM (a) and TEM (c) micrographs of empty hollow carbonaceous submicrocapsules. SEM (b) and TEM (d) micrographs of hollow carbonaceous submicrocapsules containing 1-butyl-methylimidazolium acetate ([BMIM][OAc]). [Reprinted with permission from ref. 47. Copyright (2019) American Chemical Society]. | |
3. Areas of application
In the following sections, the potential applications of encapsulated ILs in several fields are outlined. Considering the wide range of existing solutions that have been applied to exploit ILs in several technologies, among which it is critical to highlight supported ionic liquids (SILs) given their potential use for the selective separation of chemical species,23,27,82,83 it is imperative to examine any advantages and shortcomings inherent to IL encapsulation as a IL discretization/immobilization method in comparison to more established methods. In general, the main advantages of encapsulated ILs over other IL-based technologies are: (a) greater surface area compared to solid supported ILs, which can increase mass transfer and catalysis rates,84 (b) facile modification and functionalization of the shell material, which opens the path towards greater customizability for specific applications,85,86 and (c) ease of integrating encapsulated IL in engineering systems, such as fixed or fluidized bed reactors and direct injection into fluid streams.
3.1 Carbon capture
Emission of carbon dioxide (CO2) in the atmosphere has for a long time been recognized to have negative environmental effects owing to its drastic effects leading to global warming.87 In addition, the significant amount of CO2 contained in natural gas, syngas, and biogas lowers the heating value of gases, while potentially causing corrosion of components and requiring additional energy for gas conversion.88,89 In the last decade, significant efforts have been spent in developing technologies for CO2 capture and sequestration (CCS). Among them, the use of ILs in CCS has recently shown a rapid growth owing to the attractive properties of ILs together with their high affinity for CO2.90–96 Despite the high CO2 absorption capacity of ILs, a critical limitation in their use lies in their high viscosity, which can also increase upon CO2 capture and limit mass transfer during the absorption process. As absorption rates have been recognized as a limiting factor in CO2 capture systems that rely on ILs,97–99 extensive research has been performed in the development of solutions that consider both thermodynamic and kinetics aspects when selecting ILs. While supported IL phases (SILPs), which rely on infusing an inorganic porous support with IL100,101 to increase the gas/liquid interfacial area, have been proposed as a way to increase the mass transport rate of CO2 in IL, the limited capacity of SILP systems, due to low IL loading ratios of the porous media,102,103 is calling for further improvements.
The development of encapsulated ILs has emerged as an effective way to overcome these limitations by increasing the gas/liquid contact area and incorporating large amounts of IL in the capsules, thus making it attractive for CO2 capture.37,46–48,57,78 As a particular example, Moya et al. encapsulated [BMIM][OAc] in hollow carbon microcapsules and provided evidence that the encapsulation did not affect the IL absorption capacity, but significantly enhanced the mass transfer rate.47 Additionally, the sorption capacity of the encapsulated ILs was shown to remain unchanged upon successive CO2 sorption–desorption cycles. The authors also highlighted that when [BMIM][OAc] IL encapsulated in hollow carbon microcapsules is used in a fixed-bed reactor, the CO2 sorption capacity per bed volume is comparable to that obtained for CO2 carbonaceous absorbents reported in the literature.104 These findings allowed the author to conclude that the large contact surface area of the IL capsules lead to fast and favorable CO2 sorption even in fixed-bed operation. More recently, the same authors reported the encapsulation of an IL with an aprotic heterocyclic anion, namely trihexyl(tetradecyl)phosphonium 2-cyanopyrrolide ([P6,6,6,14][2-CNPyr]), in porous carbon microspheres.46 ILs with aprotic heterocyclic anions are particularly promising for CCS owing to the ability of the anion to bond to CO2 by reversible carboxylation with a N-heterocyclic carbine.105,106 The results reported by Moya et al. indicated an increase in the CO2 absorption rates upon encapsulation compared to those of the neat IL, while maintaining the high absorption capacity characteristic of the IL.46 Inspired by these results, the Pentzer group synthesized capsules using an IL-in-oil Pickering emulsion stabilized by alkylated graphene oxide nanosheets, which was coupled with the polymerization of hexamethylene diisocyanate and ethylene diamine.53 The encapsulated IL ([EMIM][TFSI]) was shown to reach full capacity, while unagitated bulk [EMIM][TFSI] could not reach the same thermodynamic equilibrium due to limitations in mass transfer.
3.2 Microreactors
The high viscosity and surface tension of ILs compared to conventional organic solvents, which result in unfavorable transport properties of these fluids, has constrained their use in additional applications, including biocatalysis107–109 and organic reactions.110–112 The discretization of ILs in microcapsules has been proposed as an effective method for overcoming this mass transport problem and opening the path for the exploitation of ILs as green solvents in catalysis. As a particular example, Weiss et al. reported the encapsulation of [BMIM][PF6] within silica shells.32 The capsules were created by emulsifying [BMIM][PF6] in water using surfactants, which was followed by interfacial polycondensation of tetraethoxysilane. The introduction of palladium acetate into [BMIM][PF6] encapsulated within silica shells (Fig. 7) allowed the authors to form Pd nanoparticles within the capsules. When used for the selective hydrogenation of alkynes, these catalytic capsules demonstrated up to 98% conversion of 1-octyne to octenes, compared to 77% from a chemically identical formulation of Pd/SiO2 catalyst with [BMIM][PF6] as solvent. The capsules also showed negligible degradation in selectivity and conversion after three catalytic cycles. In this case, the confinement of Pd nanoparticles within the capsules was proposed to maintain a higher catalytic stability than more open solid supported catalysts, where particle aggregation during the reaction process reduces the catalytic surface area.
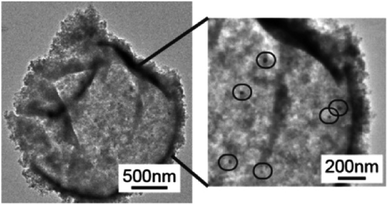 |
| Fig. 7 TEM micrographs of Pd/[BMIM][PF6] in SiO2, with black circles highlighting Pd nanoparticle formation within the capsules. [Reprinted with permission from ref. 32. Copyright (2014) American Chemical Society]. | |
The same authors later reported the encapsulation of [BMIM][PF6] in polyurea shells by emulsification and interfacial polymerization.42,113 The dissolution of platinum acetylacetonate or cinchonine in the pre-emulsified IL enabled the authors to use the capsules as microreactors for hydrosilylation and Michael addition reactions. Due to capsule cracking during the first catalytic cycle,42 the authors subsequently encapsulated the same IL in polyurethane shells, which did not undergo any change in morphology during their use as microreactors for Michael addition reactions.113 Notably, a minimal decrease in activity (∼5%) of the catalyst was also observed after three catalytic cycles, thus indicating the stability of the microreactor under operating conditions.
3.3 Waste handling
IL have attracted considerable attention as potential fluids for removing different kinds of contaminants from mixtures.35,114–118 However, a significant challenge arises from the limited miscibility of IL in oil or water. One attractive solution to this problem lies in the encapsulation of the ILs, which can be used as separation media, extractors, or as extraction media for active materials (e.g., crown ethers),119 within polymer or composite shells. The resulting encapsulated ILs can be used in separation or extraction processes by mixing them with contaminated solutions followed by their isolation by filtration.31,35,120 The encapsulation of ILs has also the additional benefit of overcoming the mass transfer limitation due to the inherent high viscosity of ILs. Recently, Elizarova et al. developed a method for fabricating stable IL-in-water nano-emulsion via a low-energy phase reversal emulsification, which was followed by layer-by-layer polyelectrolyte deposition with the aim of increasing the stability of the emulsion.120 The stabilized, multilayered IL nano-emulsion was shown to extract Cd2+ with nearly 100% efficiency and high selectivity. Notably, the encapsulated IL nano-emulsion exhibited long-term stability, as suggested by the lack of any statistically significant change in zeta-potential values after four months of storage. While other emulsion-based extraction systems have already been reported in the literature with similar extraction efficiency,121–123 the encapsulation process greatly increases the long-term stability and allows for the facile removal of the capsules from aqueous solutions compared to non-encapsulated emulsion droplets. More recently, Luo et al. prepared capsules of [BMIM][BF4] using alkylated graphene oxide nanosheet surfactants in IL-in-oil emulsions followed by interfacial polymerization relying on the reaction between a diamine and diisocyanate.52 The encapsulated IL exhibited superior performance than bulk IL, as they could be used to remove ∼98% of phenol from a contaminated oil (hexane) solution (Fig. 8). This finding does not only demonstrate that the encapsulation of IL is a fully scalable method to prepare column-packing materials with high mass transport rates for the removal of phenol from oils, but also that this method can minimize formation of undesirable emulsions, a major limitation of liquid/liquid extraction processes.
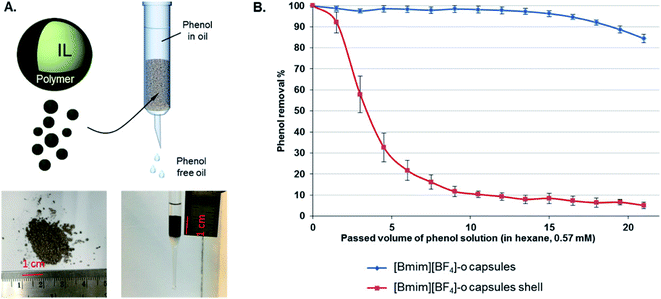 |
| Fig. 8 (A) Schematic of a column containing IL capsules that is employed for extracting phenol from hexane solutions. Photographs of the IL capsules and packed column are also displayed. (B) Phenol removal for the case of [BMIM][BF4] capsules (blue trace) and the capsule shell (red trace, after IL extraction). [Reprinted with permission from ref. 52. Copyright (2019) American Chemical Society]. | |
3.4 Medical materials
Several reviews, books, and book chapters have been dedicated to the biological properties of ILs124–127 as well as their pharmaceutical aspects.128–134 Furthermore, microencapsulation has been extensively explored as a drug delivery method owing to high tissue specificity and therapeutic efficiency provided by surface functionalization and targeted release mechanisms.135,136 Despite this, the encapsulation of ILs for medical applications has been largely unexplored. One notable effort to exploit encapsulated ILs as agents susceptible to microwaves (MWs) and contrast agents to be used in magnetic resonance (MR) imaging for cancer MW thermotherapy was published in 2015 by Du et al.137 The microcapsules, which were composed of [BMIM][BF4] IL and iron oxide (Fe3O4) nanoparticles as the core and gelatin as the shell, exhibited strong MW absorbing property owing to the high susceptibility of IL to MW irradiation.128,138–140 Additionally, the presence of Fe3O4 nanoparticles in the capsules allowed monitoring the tumor response after the MW irradiation, thus enabling the effective assessment of the efficacy of the therapeutic treatment. The results reported by Du et al. thus clearly highlight the potential of using encapsulated IL for tumor therapeutics, while calling for further studies on the topic.
3.5 Energy storage
Supercapacitors have emerged as one of the most promising electrochemical storage devices141 owing to their high power density and good stability upon cycling. Supercapacitors can be classified into two main groups, namely electrochemical double-layer capacitors (EDLCs) that use porous carbon electrodes,141,142 and pseudocapacitors that employ metal oxides.143 In the case of the former, the charge is electrostatically stored at the electrode/electrolyte interface without, ideally, any faradaic reactions.144 The high ionic conductivity, high thermal and chemical stability, together with the wide electrochemical window of ILs have made these fluids candidate electrolytes for EDLCs. However, the high viscosity of ILs together with their rather high surface tension can negatively affect the wetting behavior of IL electrolyte on the electrode. While several efforts have been spent in improving carbon electrodes by, for example, optimizing the pore size or changing their surface chemistry to enhance wettability,145,146 encapsulating ILs in shells made of reduced graphene oxide (rGO)/polyurea was recently proposed by Luo et al. as a method to increase the specific capacitance.50 The rGO-IL capsules were used, together with functionalized cellulose binder, to create disk electrodes, which were subsequently covered by [BMIM][PF6] and employed as both the anode and the cathode in a CR2032 coin cell containing a cellulose separator (which was also wet with [BMIM][PF6]). The specific capacitance at 18 °C was higher across several scan rates (from 10 to 5000 mV s−1) than the one measured using cells fabricated similarly, but having the anode and cathode made of either porous carbon (YP-50) or only the rGO material (Fig. 9). The temperature dependence of the electrochemical performance of the coin cells provided the authors with insights into the impact of the architecture of anode/cathode on the performance: while the capacitance for the rGO-IL capsule cells at 60 °C increases ∼60% compared to its value at 18 °C, the increase in capacitance at 60 °C for the YP-50 cell was much more significant. This finding clearly demonstrated that the low ion mobility across [BMIM][PF6] infused YP-50 due to high viscosity of ILs, especially at low temperature, strongly impacts the electrochemical performance, while highlighting the potential of rGO-IL capsules owing to their less dramatic change in capacitance with temperature.
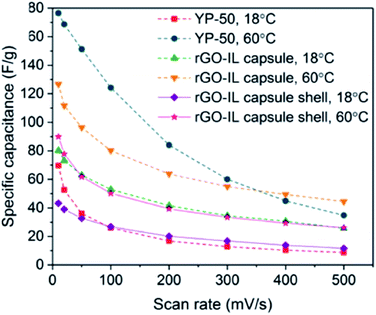 |
| Fig. 9 Specific capacitances for coin-cell supercapacitors made of anode/cathode material containing rGO-IL capsules, rGO-IL capsule shells, and YP-50 as a function of the cyclic voltammetry scan rate (red trace, after IL extraction). [Reprinted with permission from ref. 50. Copyright (2019) American Chemical Society]. | |
Overall, the results presented by Luo et al. provided a clear demonstration of the potential use of ILs encapsulated within a shell made of rGO nanosheets in electrochemical double-layer capacitors. This work has paved the way towards the optimization of the nanoarchitecture to achieve higher specific capacitance values. In particular, research efforts should be devoted to increase the interactions between IL and nanoshells (through, for example, the reduction of the capsule diameter) and decrease the amount of non-conductive polymer that is used to bind the rGO nanosheets, while increasing the amount of active electrode material (rGO).
4. Conclusions and outlook
In this paper we described the rationale for encapsulating ILs in organic or inorganic shells and summarized the different methods for discretizing ILs in microcapsules. The combination of the remarkable tunability of ILs originating from the high number of possible permutations of anions and cations with the possibility of tailoring the size, composition, and properties (e.g., mechanical properties, permeability) of the shells is opening the path for the rational design of encapsulated ILs with task-specific properties for next-generation applications.
While this literature review highlighted the potential of encapsulating ILs in organic or inorganic capsules for several applications, significant work is required to shed light on the factors dictating the size, size distribution, and shape of the capsules for each specific methodology reported in published studies. Though it is generally understood that reducing capsule size increases total surface area, most encapsulation methods cannot produce capsules with radii less than 5 μm (Table 1), restricting their use in several areas, such as biomedical applications. Morphologies beyond spherical core–shell structures, such as helical coils and multilayer structures, can be constructed with relative ease with microfluidic devices,120,147–149 but their performance compared to more conventional IL capsules in comparable tasks has not yet been thoroughly investigated. Finally, the physico-chemical and mechanical properties of the capsule shell should be more extensively evaluated using state-of-the-art characterization techniques. Gaining insights into the structure and composition of the material constituting the capsule shell could provide guidance for tailoring the encapsulation process to achieve specific shell properties (e.g., permeability, stiffness) critical for the final implementation of encapsulated ILs in specific applications.
While published studies have mostly exploited the encapsulation of IL for overcoming kinetics limitations in mass transport, the discretization of IL in shells could also provide additional benefits, such as reducing undesirable IL chemical activity and mediating IL solubility. The prevalence of halogenated ions such as (trifluoromethylsulfonyl)imide (TFSI) and alkyl halides in most IL formulations frequently results in the formation of corrosive hydrogen halides when exposed to air due to the absorption of atmospheric water.150,151 The highly negative and undesirable effects when these ILs are employed in the presence of some engineering materials, including most steels, have called for the synthesis and evaluation of halogen-free ILs. However, these halogen-free ILs, such as those incorporating amino acids or chelated borates, tend to have limited solubility in fluids of importance for engineering applications, such as mineral or synthetic oils used for lubrication purposes.152,153 Following the successes demonstrated in utilizing encapsulated ILs in the lubrication of solid coatings,43,55,154 one ongoing research thrust in the laboratory of the authors is the encapsulation of oil-immiscible ILs to exploit them as friction- or wear-reducing agents in lubricants for engine oils.
Appendix
Tables 2 and 3.
Table 2 List of IL cations with the corresponding chemical structure used for encapsulation experiments
Cation |
Structure |
1-Alkyl-3-methylimidazolium ([{n}MIM], {n} substitutes: E = ethyl, B = butyl, H = hexyl, O = octyl) |
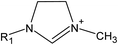 |
Trihexyltetradecylphosphonium ([P6,6,6,14]) |
 |
1-Butyl-2,3-dimethylimidazolium ([BM2IM]) |
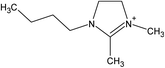 |
1-(2-Hydroxyethyl)-3-methylimidazolium ([EtOHMIM]) |
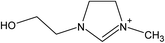 |
N-Methyl-2-hydro-xyethylammonium [NH2,Me,EtOH][Pe] |
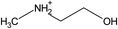 |
Choline |
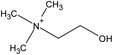 |
Tris(2-hydroxyethyl)methylammonium [(EtOH)3MeN] |
 |
1-Methyl-1-propylpyrrolidinium [Mpp] |
 |
Table 3 List of IL cations with the corresponding chemical structure used for encapsulation experiments
Anion |
Structure |
Bis(trifluoromethylsulfonyl)imide [TFSI] or [NTf2] |
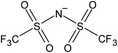 |
Hexafluorophosphate [PF6] |
 |
Tetrafluoroborate [BF4] |
 |
Bis(2,4,4-trimethylpentyl)phosphinate [(C8)2PO2] |
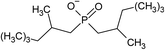 |
2-Cyanopyrrolide [2-CNPyr] |
 |
Acetate [OAc] |
 |
Pentanoate [Pe] |
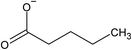 |
Methyl sulfate [MeSO4] |
 |
Dimethylphosphate (DMP) |
 |
Author contributions
Jieming Yan: conceptualization, investigation, writing – original draft, writing – review & editing; Filippo Mangolini: conceptualization, investigation, writing – original draft, writing – review & editing; funding acquisition.
Conflicts of interest
The authors declare no competing financial interests.
Acknowledgements
The material is based upon work supported by the Welch Foundation (Grant No. F-2002-20190330), the National Science Foundation Faculty Early Career Development Program (Grant No. 2042304), and the Taiho Kogyo Tribology Research Foundation (Grant No. 20A03). F. M. acknowledges support from the 2018 Ralph E. Powe Junior Faculty Enhancement Award sponsored by the Oak Ridge Associated Universities (ORAU), and from the Walker Department of Mechanical Engineering and the Texas Materials Institute at the University of Texas at Austin. Finally, the authors would like to thank the reviewers for their constructive criticism, which critically help the authors improve the review article.
References
- D. R. MacFarlane, M. Kar and J. M. Pringle, An Introduction to Ionic Liquids, in Fundamentals of Ionic Liquids, Wiley-VCH Verlag GmbH & Co. KGaA, 2017, pp. 1–25, DOI:10.1002/9783527340033.ch1.
- M. J. Earle and K. R. Seddon, Ionic Liquids. Green Solvents for the Future, Pure Appl. Chem., 2000, 72(7), 1391–1398, DOI:10.1351/pac200072071391.
- N. V. Plechkova and K. R. Seddon, Applications of Ionic Liquids in the Chemical Industry, Chem. Soc. Rev., 2008, 37(1), 123–150, 10.1039/b006677j.
- M. Petkovic, K. R. Seddon, L. P. Rebelo and C. Silva Pereira, Ionic Liquids: A Pathway to Environmental Acceptability, Chem. Soc. Rev., 2011, 40(3), 1383–1403, 10.1039/c004968a.
- A. Matic and B. Scrosati, Ionic Liquids for Energy Applications, MRS Bull., 2013, 38(7), 533–537, DOI:10.1557/mrs.2013.154.
- Y. Zhou and J. Qu, Ionic Liquids as Lubricant Additives: A Review, ACS Appl. Mater. Interfaces, 2017, 9(4), 3209–3222, DOI:10.1021/acsami.6b12489.
- H. Passos, M. G. Freire and J. A. P. Coutinho, Ionic Liquid Solutions as Extractive Solvents for Value-Added Compounds from Biomass, Green Chem., 2014, 16(12), 4786–4815, 10.1039/c4gc00236a.
- R. Hayes, G. G. Warr and R. Atkin, Structure and Nanostructure in Ionic Liquids, Chem. Rev., 2015, 115(13), 6357–6426, DOI:10.1021/cr500411q.
- R. Hayes, N. Borisenko, M. K. Tam, P. C. Howlett, F. Endres and R. Atkin, Double Layer Structure of Ionic Liquids at the Au(111) Electrode Interface: An Atomic Force Microscopy Investigation, J. Phys. Chem. C, 2011, 115(14), 6855–6863, DOI:10.1021/jp200544b.
- M. Han and R. M. Espinosa-Marzal, Molecular Mechanisms Underlying Lubrication by Ionic Liquids: Activated Slip and Flow, Lubricants, 2018, 6(3), 64, DOI:10.3390/lubricants6030064.
- J. M. Black, J. Come, S. Bi, M. Zhu, W. Zhao, A. T. Wong, J. H. Noh, P. R. Pudasaini, P. Zhang and M. B. Okatan, et al., Role of Electrical Double Layer Structure in Ionic Liquid Gated Devices, ACS Appl. Mater. Interfaces, 2017, 9(46), 40949–40958, DOI:10.1021/acsami.7b11044.
- J. M. Black, D. Walters, A. Labuda, G. Feng, P. C. Hillesheim, S. Dai, P. T. Cummings, S. V. Kalinin, R. Proksch and N. Balke, Bias-Dependent Molecular-Level Structure of Electrical Double Layer in Ionic Liquid on Graphite, Nano Lett., 2013, 13(12), 5954–5960, DOI:10.1021/nl4031083.
- J. M. Black, M. Baris Okatan, G. Feng, P. T. Cummings, S. V. Kalinin and N. Balke, Topological Defects in Electric Double Layers of Ionic Liquids at Carbon Interfaces, Nano Energy, 2015, 15, 737–745, DOI:10.1016/j.nanoen.2015.05.037.
- Z. Li and F. Mangolini, Recent Advances in Nanotribology of Ionic Liquids, Exp. Mech., 2021, 61, 1093, DOI:10.1007/s11340-021-00732-7.
- H. Li, M. W. Rutland and R. Atkin, Ionic Liquid Lubrication: Influence of Ion Structure, Surface Potential and Sliding Velocity, Phys. Chem. Chem. Phys., 2013, 15(35), 14616–14623, 10.1039/c3cp52638k.
- F. Endres, N. Borisenko, S. Z. El Abedin, R. Hayes and R. Atkin, The Interface Ionic Liquid(s)/Electrode(s): In Situ STM and AFM Measurements, Faraday Discuss., 2012, 154, 221–233, 10.1039/c1fd00050k.
- R. Hayes, G. G. Warr and R. Atkin, At the Interface: Solvation and Designing Ionic Liquids, Phys. Chem. Chem. Phys., 2010, 12(8), 1709–1723, 10.1039/b920393a.
- S. Perkin, T. Albrecht and J. Klein, Layering and Shear Properties of an Ionic Liquid, 1-Ethyl-3-Methylimidazolium Ethylsulfate, Confined to Nano-Films between Mica Surfaces, Phys. Chem. Chem. Phys., 2010, 12(6), 1243–1247, 10.1039/b920571c.
- C. S. Perez-Martinez and S. Perkin, Interfacial Structure and Boundary Lubrication of a Dicationic Ionic Liquid, Langmuir, 2019, 35(48), 15444–15450, DOI:10.1021/acs.langmuir.9b01415.
- R. Lhermerout, C. Diederichs and S. Perkin, Are Ionic Liquids Good Boundary Lubricants? A Molecular Perspective, Lubricants, 2018, 6(1), 9, DOI:10.3390/lubricants6010009.
- S. Perkin, Ionic Liquids in Confined Geometries, Phys. Chem. Chem. Phys., 2012, 14(15), 5052–5062, 10.1039/c2cp23814d.
- R. M. Espinosa-Marzal, M. Han, A. Arcifa, N. D. Spencer and A. Rossi, Ionic Liquids at Interfaces and Their Tribological Behavior, in Reference Module in ChemistryMolecular Sciences and Chemical Engineering, 2018, pp. 172–194, DOI:10.1016/B978-0-12-409547-2.13857-0.
- L. J. Lozano, C. Godínez, A. P. de los Ríos, F. J. Hernández-Fernández, S. Sánchez-Segado and F. J. Alguacil, Recent Advances in Supported Ionic Liquid Membrane Technology, J. Membr. Sci., 2011, 376(1–2), 1–14, DOI:10.1016/j.memsci.2011.03.036.
- F. Shi, Q. Zhang, D. Li and Y. Deng, Silica-Gel-Confined Ionic Liquids: A New Attempt for the Development of Supported Nanoliquid Catalysis, Chem.–Eur. J., 2005, 11(18), 5279–5288, DOI:10.1002/chem.200500107.
- R. Marcilla, M. Sanchez-Paniagua, B. Lopez-Ruiz, E. Lopez-Cabarcos, E. Ochoteco, H. Grande and D. Mecerreyes, Synthesis and Characterization of New Polymeric Ionic Liquid Microgels, J. Polym. Sci., Part A: Polym. Chem., 2006, 44(13), 3958–3965, DOI:10.1002/pola.21483.
- R. Ciriminna, P. Hesemann, J. J. E. Moreau, M. Carraro, S. Campestrini and M. Pagliaro, Aerobic Oxidation of Alcohols in Carbon Dioxide with Silica-Supported Ionic Liquids Doped with Perruthenate, Chem.–Eur. J., 2006, 12(20), 5220–5224, DOI:10.1002/chem.200501556.
- M. A. Malik, M. A. Hashim and F. Nabi, Ionic Liquids in Supported Liquid Membrane Technology, Chem. Eng. J., 2011, 171(1), 242–254, DOI:10.1016/j.cej.2011.03.041.
- P. Wang, S. M. Zakeeruddin, J. E. Moser and M. Grätzel, A New Ionic Liquid Electrolyte Enhances the Conversion Efficiency of Dye-Sensitized Solar Cells, J. Phys. Chem. B, 2003, 107(48), 13280–13285, DOI:10.1021/jp0355399.
- A. Späth, H. Minami, T. Suzuki and R. H. Fink, Morphology Changes of Ionic Liquid Encapsulating Polymer Microcontainers upon X-Ray Irradiation, RSC Adv., 2014, 4(7), 3272–3277, 10.1039/c3ra45980b.
- W. W. Yang, Y. C. Lu, Z. Y. Xiang and G. S. Luo, Monodispersed Microcapsules Enclosing Ionic Liquid of 1-Butyl-3-Methylimidazolium Hexafluorophosphate, React. Funct. Polym., 2007, 67(1), 81–86, DOI:10.1016/j.reactfunctpolym.2006.10.005.
- T. Vincent, A. Parodi and E. Guibal, Immobilization of Cyphos IL-101 in Biopolymer Capsules for the Synthesis of Pd Sorbents, React. Funct. Polym., 2008, 68(7), 1159–1169, DOI:10.1016/j.reactfunctpolym.2008.04.001.
- E. Weiss, B. Dutta, A. Kirschning and R. Abu-Reziq, BMIm-PF6@SiO2 Microcapsules: Particulated Ionic Liquid as a New Material for the Heterogenization of Catalysts, Chem. Mater., 2014, 26(16), 4781–4787, DOI:10.1021/cm501840d.
- H. Minami, H. Fukaumi, M. Okubo and T. Suzuki, Preparation of Ionic Liquid-Encapsulated Polymer Particles, Colloid Polym. Sci., 2013, 291(1), 45–51, DOI:10.1007/s00396-012-2691-1.
- Z. Du, E. Li, G. Li, F. Cheng and G. Wang, One-Step Strategy for Synthesis of Yolk–Shell Silica Spheres Using Trisiloxane-Tailed Ionic Liquids
as a Template, J. Mater. Sci., 2014, 49(14), 4919–4926, DOI:10.1007/s10853-014-8193-4.
- D.-x. Chen, X.-k. OuYang, Y.-g. Wang, L.-y. Yang, K.-j. Wu and C.-h. He, Adsorption of Caprolactam from Aqueous Solution by Novel Polysulfone Microcapsules Containing [Bmim][PF6], Colloids Surf., A, 2014, 441, 72, DOI:10.1016/j.colsurfa.2013.08.069.
- D. Shanthana Lakshmi, A. Figoli, G. Fiorani, M. Carraro, L. Giorno and E. Drioli, Preparation and Characterization of Ionic Liquid Polymer Microspheres [PEEKWC/DMF/CYPHOS IL 101] Using the Phase-Inversion Technique, Sep. Purif. Technol., 2012, 97, 179–185, DOI:10.1016/j.seppur.2012.01.045.
- J. Palomar, J. Lemus, N. Alonso-Morales, J. Bedia, M. A. Gilarranz and J. J. Rodriguez, Encapsulated Ionic Liquids (ENILs): From Continuous to Discrete Liquid Phase, Chem. Commun., 2012, 48(80), 10046–10048, 10.1039/c2cc35291e.
- L. C. Bradley and M. Gupta, Encapsulation of Ionic Liquids within Polymer Shells via Vapor Phase Deposition, Langmuir, 2012, 28(27), 10276–10280, DOI:10.1021/la301170a.
- Z. Y. Xiang, Y. C. Lu, Y. Zou, X. C. Gong and G. S. Luo, Preparation of Microcapsules Containing Ionic Liquids with a New Solvent Extraction System, React. Funct. Polym., 2008, 68(8), 1260–1265, DOI:10.1016/j.reactfunctpolym.2008.06.006.
- H. Gao, J. Xing, X. Xiong, Y. Li, W. Li, Q. Liu, Y. Wu and H. Liu, Immobilization of Ionic Liquid [BMIM][PF6] by Spraying Suspension Dispersion Method, Ind. Eng. Chem. Res., 2008, 47(13), 4414–4417, DOI:10.1021/ie701702n.
- H. Minami, H. Fukaumi, M. Okubo and T. Suzuki, Preparation of Ionic Liquid-Encapsulated Polymer Particles, Colloid Polym. Sci., 2012, 291(1), 45–51, DOI:10.1007/s00396-012-2691-1.
- E. Weiss, D. Gertopski, M. K. Gupta and R. Abu-Reziq, Encapsulation of Ionic Liquid BMIm[PF6] within Polyurea Microspheres, React. Funct. Polym., 2015, 96, 32, DOI:10.1016/j.reactfunctpolym.2015.09.003.
- M. Yang, X. Zhu, G. Ren, X. Men, F. Guo, P. Li and Z. Zhang, Tribological Behaviors of Polyurethane Composite Coatings Filled with Ionic Liquid Core/Silica Gel Shell Microcapsules, Tribol. Lett., 2015, 58(1), 9, DOI:10.1007/s11249-015-0492-7.
- T. Shi, S. Livi, J. Duchet and J.-F. Gérard, Ionic Liquids-Containing Silica Microcapsules: A Potential Tunable Platform for Shaping-Up Epoxy-Based Composite Materials?, Nanomaterials, 2020, 10(5), 881, DOI:10.3390/nano10050881.
- C. Li, Z. Su, J. Tan, Y. Xue, Y. Yang, H. Yin, G. Zhang and Q. Zhang, Autocatalyzed Interfacial Thiol–Isocyanate Click Reactions for Microencapsulation of Ionic Liquids, J. Mater. Sci., 2020, 55(21), 9119–9128, DOI:10.1007/s10853-020-04670-y.
- C. Moya, N. Alonso-Morales, J. De Riva, O. Morales-Collazo, J. F. Brennecke and J. Palomar, Encapsulation of Ionic Liquids with an Aprotic Heterocyclic Anion (AHA-IL) for CO2 Capture: Preserving the Favorable Thermodynamics and Enhancing the Kinetics of Absorption, J. Phys. Chem. B, 2018, 122(9), 2616–2626, DOI:10.1021/acs.jpcb.7b12137.
- C. Moya, N. Alonso-Morales, M. A. Gilarranz, J. J. Rodriguez and J. Palomar, Encapsulated Ionic Liquids for CO2 Capture: Using 1-Butyl-Methylimidazolium Acetate for Quick and Reversible CO2 Chemical Absorption, ChemPhysChem, 2016, 17(23), 3891–3899, DOI:10.1002/cphc.201600977.
- J. Lemus, F. F. A. Da Silva, J. Palomar, P. J. Carvalho and J. A. P. P. Coutinho, Solubility of Carbon Dioxide in Encapsulated Ionic Liquids, Sep. Purif. Technol., 2018, 196, 41–46, DOI:10.1016/j.seppur.2017.08.032.
- J. Lemus, J. Bedia, C. Moya, N. Alonso-Morales, M. A. Gilarranz, J. Palomar and J. J. Rodriguez, Ammonia Capture from the Gas Phase by Encapsulated Ionic Liquids (ENILs), RSC Adv., 2016, 6(66), 61650, 10.1039/c6ra11685j.
- Q. Luo, P. Wei, Q. Huang, B. Gurkan and E. B. Pentzer, Carbon Capsules of Ionic Liquid for Enhanced Performance of Electrochemical Double-Layer Capacitors, ACS Appl. Mater. Interfaces, 2018, 10(19), 16707–16714, DOI:10.1021/acsami.8b01285.
- Y. Ma, Z. Li, H. Wang and H. Li, Synthesis and Optimization of Polyurethane Microcapsules Containing [BMIm]PF6 Ionic Liquid Lubricant, J. Colloid Interface Sci., 2019, 534, 469–479, DOI:10.1016/j.jcis.2018.09.059.
- Q. Luo, Y. Wang, Z. Chen, P. Wei, E. Yoo and E. Pentzer, Pickering Emulsion-Templated Encapsulation of Ionic Liquids for Contaminant Removal, ACS Appl. Mater. Interfaces, 2019, 11(9), 9612, DOI:10.1021/acsami.8b21881.
- Q. Huang, Q. Luo, Y. Wang, E. Pentzer and B. Gurkan, Hybrid Ionic Liquid Capsules for Rapid CO2 Capture, Ind. Eng. Chem. Res., 2019, 58(24), 10503–10509, DOI:10.1021/acs.iecr.9b00314.
- H. Li, Q. Wang, H. Wang, Y. Cui, Y. Zhu and B. Wang, Fabrication of Thermally Stable Polysulfone Microcapsules Containing [EMIm][NTf2] Ionic Liquid for Enhancement of In Situ Self-Lubrication Effect of Epoxy, Macromol. Mater. Eng., 2016, 301(12), 1473–1481, DOI:10.1002/mame.201600293.
- P. Bandeira, J. Monteiro, A. M. Baptista and F. D. Magalhães, Tribological Performance of PTFE-Based Coating Modified with Microencapsulated [HMIM][NTf2] Ionic Liquid, Tribol. Lett., 2015, 59(1), 1–15, DOI:10.1007/s11249-015-0545-y.
- I. L. Guarnido, A. F. Routh, M. D. Mantle, M. F. Serrano and P. C. Marr, Ionic Liquid Microcapsules: Formation and Application of Polystyrene Microcapsules with Ionic Liquid Cores, ACS Sustainable Chem. Eng., 2019, 7(2), 1870–1874, DOI:10.1021/acssuschemeng.8b05478.
- S. Kaviani, S. Kolahchyan, K. L. Hickenbottom, A. M. Lopez and S. Nejati, Enhanced Solubility of Carbon Dioxide for Encapsulated Ionic Liquids in Polymeric Materials, Chem. Eng. J., 2018, 354, 753–757, DOI:10.1016/j.cej.2018.08.086.
- X. Zhang and Y. Cai, Octadecyltrichlorosilane (OTS)-Coated Ionic Liquid Drops: Micro-Reactors for Homogenous Catalytic Reactions at Designated Interfaces, Beilstein J. Nanotechnol., 2012, 3(1), 33–39, DOI:10.3762/bjnano.3.4.
- H. Niedermeyer, J. P. Hallett, I. J. Villar-Garcia, P. A. Hunt and T. Welton, Mixtures of Ionic Liquids, Chem. Soc. Rev., 2012, 41(23), 7780–7802, 10.1039/c2cs35177c.
- T. Dobashi, F. J. Yeh, Q. Ying, K. Ichikawa and B. Chu, An Experimental Investigation on the Structure of Microcapsules, Langmuir, 1995, 11(11), 4278–4282, DOI:10.1021/la00011a018.
- K. Ichikawa, Dynamic Mechanical Properties of Polyurethane–Urea Microcapsules on Coated Paper, J. Appl. Polym. Sci., 1994, 54(9), 1321–1327, DOI:10.1002/app.1994.070540914.
- H. K. Mahabadi, T. H. Ng and H. S. Tan, Interfacial/Free Radical Polymerization Microencapsulation: Kinetics of Particle Formation, J. Microencapsulation, 1996, 13(5), 559–573, DOI:10.3109/02652049609026041.
- Y. Okahata, H. Noguchi and T. Seki, Functional Capsule Membranes. 26. Permeability Control of Polymer-Grafted Capsule Membranes Responding to Ambient PH Changes, Macromolecules, 1987, 20(1), 15–21, DOI:10.1021/ma00167a004.
- R. Arshady, Albumin Microspheres and Microcapsules: Methodology of Manufacturing Techniques, J. Controlled Release, 1990, 14(2), 111–131, DOI:10.1016/0168-3659(90)90149-n.
- R. Arshady, Microspheres and Microcapsules, a Survey of Manufacturing Techniques Part II: Coacervation, Polym. Eng. Sci., 1990, 30(15), 905–914, DOI:10.1002/pen.760301505.
- A. Loxley and B. Vincent, Preparation of Poly(Methylmethacrylate) Microcapsules with Liquid Cores, J. Colloid Interface Sci., 1998, 62(208), 49–62 CrossRef PubMed.
- M. Hejazifar, O. Lanaridi and K. Bica-Schröder, Ionic Liquid Based Microemulsions: A Review, J. Mol. Liq., 2020, 303, 112264, DOI:10.1016/j.molliq.2019.112264.
- M. Okubo and H. Minami, Formation Mechanism of Micron-Sized Monodispersed Polymer Particles Having a Hollow Structure, Colloid Polym. Sci., 1997, 275(10), 992–997, DOI:10.1007/s003960050177.
- M. Okubo, Y. Konishi, T. Inohara and H. Minami, Size Effect of Monomer Droplets on the Production of Hollow Polymer Particles by Suspension Polymerization, Colloid Polym. Sci., 2003, 281(4), 302–307, DOI:10.1007/s00396-002-0774-0.
- H. Minami, M. Okubo and Y. Oshima, Preparation of Cured Epoxy Resin Particles Having One Hollow by Polyaddition Reaction, Polymer, 2005, 46(4), 1051–1056, DOI:10.1016/j.polymer.2004.11.041.
- Y. Hennequin, N. Pannacci, C. P. De Torres, G. Tetradis-Meris, S. Chapuliot, E. Bouchaud and P. Tabeling, Synthesizing Microcapsules with Controlled Geometrical and Mechanical Properties with Microfluidic Double Emulsion Technology, Langmuir, 2009, 25(14), 7857–7861, DOI:10.1021/la9004449.
- S. Okushima, T. Nisisako, T. Torii and T. Higuchi, Controlled Production of Monodisperse Double Emulsions by Two-Step Droplet Breakup in Microfluidic Devices, Langmuir, 2004, 20(23), 9905–9908, DOI:10.1021/la0480336.
- M. Seo, Z. Nie, S. Xu, M. Mok, P. C. Lewis, R. Graham and E. Kumacheva, Continuous Microfluidic Reactors for Polymer Particles, Langmuir, 2005, 21(25), 11614–11622, DOI:10.1021/la050519e.
- Z. Nie, S. Xu, M. Seo, P. C. Lewis and E. Kumacheva, Polymer Particles with Various Shapes and Morphologies Produced in Continuous Microfluidic Reactors, J. Am. Chem. Soc., 2005, 127(22), 8058–8063, DOI:10.1021/ja042494w.
- H. J. Oh, S. H. Kim, J. Y. Baek, G. H. Seong and S. H. Lee, Hydrodynamic Micro-Encapsulation of Aqueous Fluids and Cells via “on the Fly” Photopolymerization, J. Micromech. Microeng., 2006, 16(2), 285–291, DOI:10.1088/0960-1317/16/2/013.
- J. K. Stolaroff, C. Ye, J. S. Oakdale, S. E. Baker, W. L. Smith, D. T. Nguyen, C. M. Spadaccini and R. D. Aines, Microencapsulation of Advanced Solvents for Carbon Capture, Faraday Discuss., 2016, 192, 271–281, 10.1039/c6fd00049e.
- Q. Luo, Y. Wang, E. Yoo, P. Wei and E. Pentzer, Ionic Liquid-Containing Pickering Emulsions Stabilized by Graphene Oxide-Based Surfactants, Langmuir, 2018, 34, 10114 CrossRef CAS PubMed.
- Q. Luo and E. Pentzer, Encapsulation of Ionic Liquids for Tailored Applications, ACS Appl. Mater. Interfaces, 2020, 12(5), 5169–5176, DOI:10.1021/acsami.9b16546.
- J. Palomar, J. Lemus, M. A. Gilarranz and J. J. Rodriguez, Adsorption of Ionic Liquids from Aqueous Effluents by Activated Carbon, Carbon, 2009, 47(7), 1846–1856, DOI:10.1016/j.carbon.2009.03.028.
- S. B. Yoon, K. Sohn, J. Y. Kim, C. H. Shin, J. S. Yu and T. Hyeon, Fabrication of Carbon Capsules with Hollow Macroporous Core/Mesoporous Shell Structures, Adv. Mater., 2002, 14(1), 19–21, DOI:10.1002/1521-4095(20020104)14:1<19::aid-adma19>3.0.co;2-x.
- N. Alonso-Morales, M. A. Gilarranz, J. Palomar, J. Lemus, F. Heras and J. J. Rodriguez, Preparation of Hollow Submicrocapsules with a Mesoporous Carbon Shell, Carbon, 2013, 59, 430–438, DOI:10.1016/j.carbon.2013.03.036.
- C. P. Mehnert, R. A. Cook, N. C. Dispenziere and M. Afeworki, Supported Ionic Liquid Catalysis-A New Concept for Homogeneous Hydroformylation Catalysis, J. Am. Chem. Soc., 2002, 124(44), 12932–12933, DOI:10.1021/ja0279242.
- C. V. Doorslaer, W. Joos, M. Pascal, B. Koen and D. D. Vos, Immobilization of Molecular Catalysts in Supported Ionic Liquid Phases, Dalton Trans., 2010, 39(36), 8377–8390, 10.1039/c001285h.
- J. K. Stolaroff, C. Ye, D. T. Nguyen, J. Oakdale, J. M. Knipe and S. E. Baker, CO2 Absorption Kinetics of Micro-Encapsulated Ionic Liquids, Energy Procedia, 2017, 114, 860–865, DOI:10.1016/j.egypro.2017.03.1228.
- L.-T. T. Nguyen, X. K. D. Hillewaere, R. F. A. Teixeira, O. v. d. Berg and F. E. D. Prez, Efficient Microencapsulation of a Liquid Isocyanate with in Situ Shell Functionalization, Polym. Chem., 2015, 6(7), 1159–1170, 10.1039/c4py01448k.
- J. Feng, M. Sun, Y. Bu and C. Luo, Hollow Fiber Membrane-Coated Functionalized Polymeric Ionic Liquid Capsules for Direct Analysis of Estrogens in Milk Samples, Anal. Bioanal. Chem., 2016, 408(6), 1679–1685, DOI:10.1007/s00216-015-9279-9.
- E. S. Sanz-Pérez, C. R. Murdock, S. A. Didas and C. W. Jones, Direct Capture of CO2 from Ambient Air, Chem. Rev., 2016, 116(19), 11840–11876, DOI:10.1021/acs.chemrev.6b00173.
- G. George, N. Bhoria, S. Alhallaq, A. Abdala and V. Mittal, Polymer Membranes for Acid Gas Removal from Natural Gas, Sep. Purif. Technol., 2016, 158, 333–356, DOI:10.1016/j.seppur.2015.12.033.
- K. Huang, X. M. Zhang, Y. Xu, Y. T. Wu, X. B. Hu and Y. Xu, Protic Ionic Liquids for the Selective Absorption of H2S from CO2: Thermodynamic Analysis, AIChE J., 2014, 60(12), 4232–4240, DOI:10.1002/aic.14634.
- Y. Zhang, S. Zhang, X. Lu, Q. Zhou, W. Fan and X. P. Zhang, Dual Amino-Functionalised Phosphonium Ionic Liquids for CO2 Capture, Chem.–Eur. J., 2009, 15(12), 3003–3011, DOI:10.1002/chem.200801184.
- B. F. Goodrich, J. C. De La Fuente, B. E. Gurkan, D. J. Zadigian, E. A. Price, Y. Huang and J. F. Brennecke, Experimental Measurements of Amine-Functionalized Anion-Tethered Ionic Liquids with Carbon Dioxide, Ind. Eng. Chem. Res., 2011, 50(1), 111–118, DOI:10.1021/ie101688a.
- I. Niedermaier, M. Bahlmann, C. Papp, C. Kolbeck, W. Wei, S. Krick Calderón, M. Grabau, P. S. Schulz, P. Wasserscheid and H. P. Steinrück, et al., Carbon Dioxide Capture by an Amine Functionalized Ionic Liquid: Fundamental Differences of Surface and Bulk Behavior, J. Am. Chem. Soc., 2014, 136(1), 436–441, DOI:10.1021/ja410745a.
- X. X. Zhang, X. X. Zhang, H. Dong, Z. Zhao, S. Zhang and Y. Huang, Carbon Capture with Ionic Liquids: Overview and Progress, Energy Environ. Sci., 2012, 5(5), 6668, 10.1039/c2ee21152a.
- M. Ramdin, T. W. De Loos and T. J. H. Vlugt, State-of-the-Art of CO2 Capture with Ionic Liquids, Ind. Eng. Chem. Res., 2012, 51(24), 8149–8177, DOI:10.1021/ie3003705.
- S. Babamohammadi, A. Shamiri and M. K. Aroua, A Review of CO2 Capture by Absorption in Ionic Liquid-Based Solvents, Rev. Chem. Eng., 2015, 31(4), 383–412, DOI:10.1515/revce-2014-0032.
- L. C. Tomé and I. M. Marrucho, Ionic Liquid-Based Materials:
A Platform to Design Engineered CO2 Separation Membranes, Chem. Soc. Rev., 2016, 45, 2785–2824, 10.1039/c5cs00510h.
- X. Zhang, D. Bao, Y. Huang, H. Dong, X. Zhang and S. Zhang, Gas-Liquid Mass-Transfer Properties in CO2 Absorption System with Ionic Liquids, AIChE J., 2014, 60(8), 2929–2939, DOI:10.1002/aic.14507.
- M. P. Gimeno, M. C. Mayoral and J. M. Andrés, Influence of Temperature on CO2 Absorption Rate and Capacity in Ionic Liquids, Energy Fuels, 2013, 27(7), 3928–3935, DOI:10.1021/ef401063r.
- R. Krupiczka, A. Rotkegel and Z. Ziobrowski, Comparative Study of CO2 Absorption in Packed Column Using Imidazolium Based Ionic Liquids and MEA Solution, Sep. Purif. Technol., 2015, 149, 228–236, DOI:10.1016/j.seppur.2015.05.026.
- J. Lemus, J. Palomar, M. A. Gilarranz and J. J. Rodriguez, Characterization of Supported Ionic Liquid Phase (SILP) Materials Prepared from Different Supports, Adsorption, 2011, 17(3), 561–571, DOI:10.1007/s10450-011-9327-5.
- K. N. Ruckart, R. A. O'Brien, S. M. Woodard, K. N. West and T. G. Glover, Porous Solids Impregnated with Task-Specific Ionic Liquids as Composite Sorbents, J. Phys. Chem. C, 2015, 119(35), 20681–20697, DOI:10.1021/acs.jpcc.5b04646.
- A. Erto, A. Silvestre-Albero, J. Silvestre-Albero, F. Rodríguez-Reinoso, M. Balsamo, A. Lancia and F. Montagnaro, Carbon-Supported Ionic Liquids as Innovative Adsorbents for CO2 Separation from Synthetic Flue-Gas, J. Colloid Interface Sci., 2015, 448, 41–50, DOI:10.1016/j.jcis.2015.01.089.
- I. H. Arellano, S. H. Madani, J. Huang and P. Pendleton, Carbon Dioxide Adsorption by Zinc-Functionalized Ionic Liquid Impregnated into Bio-Templated Mesoporous Silica Beads, Chem. Eng. J., 2016, 283, 692–702, DOI:10.1016/j.cej.2015.08.006.
- J. Lemus, M. Martin-Martinez, J. Palomar, L. Gomez-Sainero, M. A. Gilarranz and J. J. Rodriguez, Removal of Chlorinated Organic Volatile Compounds by Gas Phase Adsorption with Activated Carbon, Chem. Eng. J., 2012, 211–212, 246–254, DOI:10.1016/j.cej.2012.09.021.
- B. Gurkan, B. F. Goodrich, E. M. Mindrup, L. E. Ficke, M. Massel, S. Seo, T. P. Senftle, H. Wu, M. F. Glaser and J. K. Shah, et al., Molecular Design of High Capacity, Low Viscosity, Chemically Tunable Ionic Liquids for CO2 Capture, J. Phys. Chem. Lett., 2010, 1(24), 3494–3499, DOI:10.1021/jz101533k.
- H. A. Duong, T. N. Tekavec and J. Louie, Reversible Carboxylation of N-Heterocyclic Carbenes, Chem. Commun., 2004, 4(1), 112–113, 10.1039/b311350g.
- R. Patel, M. Kumari and A. B. Khan, Recent Advances in the Applications of Ionic Liquids in Protein Stability and Activity: A Review, Appl. Biochem. Biotechnol., 2014, 172, 3701–3720, DOI:10.1007/s12010-014-0813-6.
- Y. Hu, J. Yang, R. Jia, Y. Ding, S. Li and H. Huang, Chemical Modification with Functionalized Ionic Liquids: A Novel Method to Improve the Enzymatic Properties of Candida Rugosa Lipase, Bioprocess Biosyst. Eng., 2014, 37(8), 1617–1626, DOI:10.1007/s00449-014-1134-4.
- M. Goldfeder and A. Fishman, Modulating Enzyme Activity Using Ionic Liquids or Surfactants, Appl. Microbiol. Biotechnol., 2014, 98, 545–554, DOI:10.1007/s00253-013-5395-7.
- J. P. Hallett and T. Welton, Room-Temperature Ionic Liquids: Solvents for Synthesis and Catalysis. 2, Chem. Rev., 2011, 111(5), 3508–3576, DOI:10.1021/cr1003248.
- T. Welton, Ionic Liquids in Catalysis, Coord. Chem. Rev., 2004, 248(21–24), 2459–2477, DOI:10.1016/j.ccr.2004.04.015.
- T. Welton, Room-Temperature Ionic Liquids. Solvents for Synthesis and Catalysis, Chem. Rev., 1999, 99(8), 2071–2083, DOI:10.1021/cr980032t.
- E. Weiss and R. Abu-Reziq, Ionic Liquid-Based Polymeric Microreactors and Their Applicability, J. Mater. Sci., 2017, 52, 10637, DOI:10.1007/s10853-017-1236-x.
- V. Archana, K. M. Meera and N. Anantharaman, Studies on Removal of Phenol Using Ionic Liquid Immobilized Polymeric Micro-Capsules, Arabian J. Chem., 2016, 9(3), 371, DOI:10.1016/j.arabjc.2013.03.017.
- Y. De Gaetano, J. Hubert, A. Mohamadou, S. Boudesocque, R. Plantier-Royon, J. H. Renault and L. Dupont, Removal of Pesticides from Wastewater by Ion Pair Centrifugal Partition Extraction Using Betaine-Derived Ionic Liquids as Extractants, Chem. Eng. J., 2016, 285, 596 CrossRef CAS.
- M. M. Seitkalieva, A. S. Kashin, K. S. Egorova and V. P. Ananikov, Ionic Liquids As Tunable Toxicity Storage Media for Sustainable Chemical Waste Management, ACS Sustainable Chem. Eng., 2018, 6, 719 CrossRef CAS.
- R. Leyma, S. Platzer, F. Jirsa, W. Kandioller, R. Krachler and B. K. Keppler, Novel Thiosalicylate-Based Ionic Liquids for Heavy Metal Extractions, J. Hazard. Mater., 2016, 314, 164 CrossRef CAS PubMed.
- O. G. Sas, I. Domínguez, B. González and Á. Domínguez, Liquid–Liquid Extraction of Phenolic Compounds from Water Using Ionic Liquids: Literature Review and New Experimental Data Using [C2mim]FSI, J. Environ. Manage., 2018, 228, 475 CrossRef CAS PubMed.
- S. Dai, Y. H. Ju and C. E. Barnes, Solvent Extraction of Strontium Nitrate by a Crown Ether Using Room-Temperature Ionic Liquids, J. Chem. Soc., Dalton Trans., 1999,(8), 1201–1202, 10.1039/a809672d.
- I. S. Elizarova and P. F. Luckham, Layer-by-Layer Encapsulated Nano-Emulsion of Ionic Liquid Loaded with Functional Material for Extraction of Cd2+ Ions from Aqueous Solutions, J. Colloid Interface Sci., 2017, 491, 286, DOI:10.1016/j.jcis.2016.12.054.
- H. Bai, Q. Zhou, G. Xie and J. Xiao, Temperature-Controlled Ionic Liquid-Liquid-Phase Microextraction for the Pre-Concentration of Lead from Environmental Samples Prior to Flame Atomic Absorption Spectrometry, Talanta, 2010, 80(5), 1638–1642, DOI:10.1016/j.talanta.2009.09.059.
- S. Li, S. Cai, W. Hu, H. Chen and H. Liu, Ionic Liquid-Based Ultrasound-Assisted Dispersive Liquid–Liquid Microextraction Combined with Electrothermal Atomic Absorption Spectrometry for a Sensitive Determination of Cadmium in Water Samples, Spectrochim. Acta, Part B, 2009, 64(7), 666–671, DOI:10.1016/j.sab.2009.05.023.
- M. Chamsaz, A. Atarodi, M. Eftekhari, S. Asadpour and M. Adibi, Vortex-Assisted Ionic Liquid Microextraction Coupled to Flame Atomic Absorption Spectrometry for Determination of Trace Levels of Cadmium in Real Samples, J. Adv. Res., 2013, 4(1), 35–41, DOI:10.1016/j.jare.2011.12.002.
- P. D. de María, Ionic Liquids in Biotransformations and Organocatalysis: Solvents and Beyond, John Wiley and Sons, 2012, DOI:10.1002/9781118158753.
- A. Mohammad, Dr. Inamuddin, Green Solvents II: Properties and Applications of Ionic Liquids, Springer, Netherlands, 2012, DOI:10.1007/978-94-007-2891-2.
- Ionic Liquid Applications: Pharmaceuticals, Therapeutics, and Biotechnology, ed. Malhotra S. V., ACS Symposium Series, American Chemical Society, Washington, DC, 2010, vol. 1038, DOI:10.1021/bk-2010-1038.
- Ionic Liquids Completely UnCOILed: Critical Expert Overviews, ed. N. V. Plechkova and K. R. Seddon, Wiley, 2015 Search PubMed.
- D. D. Patel and J. M. Lee, Applications of Ionic Liquids, Chem. Rec., 2012, 12(3), 329–355, DOI:10.1002/tcr.201100036.
- M. Smiglak, J. M. Pringle, X. Lu, L. Han, S. Zhang, H. Gao, D. R. Mac Farlane and R. D. Rogers, Ionic Liquids for Energy, Materials, and Medicine, Chem. Commun., 2014, 50(66), 9228–9250, 10.1039/c4cc02021a.
- W. L. Hough and R. D. Rogers, Ionic Liquids Then and Now: From Solvents to Materials to Active Pharmaceutical Ingredients, Bull. Chem. Soc. Jpn., 2007, 80(12), 2262–2269, DOI:10.1246/bcsj.80.2262.
- R. Ferraz, L. C. Branco, C. Prudêncio, J. P. Noronha and Ž. Petrovski, Ionic Liquids as Active Pharmaceutical Ingredients, ChemMedChem, 2011, 6(6), 975–985, DOI:10.1002/cmdc.201100082.
- M. Moniruzzaman and M. Goto, Ionic Liquids: Future Solvents and Reagents for Pharmaceuticals, J. Chem. Eng. Jpn., 2011, 44(6), 370–381, DOI:10.1252/jcej.11we015.
- J. Stoimenovski, D. R. MacFarlane, K. Bica and R. D. Rogers, Crystalline vs. Ionic Liquid Salt Forms of Active Pharmaceutical Ingredients: A Position Paper, Pharm. Res., 2010, 27, 521–526, DOI:10.1007/s11095-009-0030-0.
- T. Siodmiak, M. Piotr Marszall and A. Proszowska, Ionic Liquids: A New Strategy in Pharmaceutical Synthesis, Mini-Rev. Org. Chem., 2012, 9(2), 203–208, DOI:10.2174/157019312800604698.
- R. Ladj, A. Bitar, M. M. Eissa, H. Fessi, Y. Mugnier, R. Le Dantec and A. Elaissari, Polymer Encapsulation of Inorganic Nanoparticles for Biomedical Applications, Int. J. Pharm., 2013, 458(1), 230–241, DOI:10.1016/j.ijpharm.2013.09.001.
- R. H. Müller, K. Mäder and S. Gohla, Solid Lipid Nanoparticles (SLN) for Controlled Drug Delivery – A Review of the State of the Art, Eur. J. Pharm. Biopharm., 2000, 50(1), 161–177, DOI:10.1016/s0939-6411(00)00087-4.
- Q. Du, T. Ma, C. Fu, T. Liu, Z. Huang, J. Ren, H. Shao, K. Xu, F. Tang and X. Meng, Encapsulating Ionic Liquid and Fe3O4 Nanoparticles in Gelatin Microcapsules as Microwave Susceptible Agent for MR Imaging-Guided Tumor Thermotherapy.Pdf, ACS Appl. Mater. Interfaces, 2015, 7(24), 13612, DOI:10.1021/acsami.5b03230.
- N. Fechler, T. P. Fellinger and M. Antonietti, “salt Templating”: A Simple and Sustainable Pathway toward Highly Porous Functional Carbons from Ionic Liquids, Adv. Mater., 2013, 25(1), 75–79, DOI:10.1002/adma.201203422.
- G. J. Qian, N. Wang, Q. Shen, Y. H. Sheng, J. Q. Zhao, M. Kuang, G. J. Liu and M. C. Wu, Efficacy of Microwave versus Radiofrequency Ablation for Treatment of Small Hepatocellular Carcinoma: Experimental and Clinical Studies, Eur. Radiol., 2012, 22(9), 1983–1990, DOI:10.1007/s00330-012-2442-1.
- H. Ren, Y. Zhou and L. Liu, Selective Conversion of Cellulose to Levulinic Acid via Microwave-Assisted Synthesis in Ionic Liquids, Bioresour. Technol., 2013, 129, 616–619, DOI:10.1016/j.biortech.2012.12.132.
- P. Simon and Y. Gogotsi, Materials for Electrochemical Capacitors, Nat. Mater., 2008, 7, 845–854, DOI:10.1038/nmat2297.
- F. Béguin, V. Presser, A. Balducci and E. Frackowiak, Carbons and Electrolytes for Advanced Supercapacitors, Adv. Mater., 2014, 26(14), 2219–2251, DOI:10.1002/adma.201304137.
- T. Brousse, D. Bélanger and J. W. Long, To Be or Not To Be Pseudocapacitive?, J. Electrochem. Soc., 2015, 162(5), A5185–A5189, DOI:10.1149/2.0201505jes.
- A. Brandt, S. Pohlmann, A. Varzi, A. Balducci and S. Passerini, Ionic Liquids in Supercapacitors, MRS Bull., 2013, 38(7), 554–559, DOI:10.1557/mrs.2013.151.
- Z. She, D. Ghosh and M. A. Pope, Decorating Graphene Oxide with Ionic Liquid Nanodroplets: An Approach Leading to Energy-Dense, High-Voltage Supercapacitors, ACS Nano, 2017, 11, 10077 CrossRef CAS PubMed.
- T. Y. Kim, H. W. Lee, M. Stoller, D. R. Dreyer, C. W. Bielawski, R. S. Ruoff and K. S. Suh, High-Performance Supercapacitors Based on Poly(Ionic Liquid)-Modified Graphene Electrodes, ACS Nano, 2011, 5(1), 436–442, DOI:10.1021/nn101968p.
- Y. Yu, J. Guo, L. Sun, X. Zhang and Y. Zhao, Microfluidic Generation of Microsprings with Ionic Liquid Encapsulation for Flexible Electronics, Research, 2019, 2019, 1–9, DOI:10.34133/2019/6906275.
- A. Y. Gebreyohannes, L. Upadhyaya, L. P. Silva, G. Falca, P. J. Carvalho and S. P. Nunes, Hollow Fibers with Encapsulated Green Amino Acid-Based Ionic Liquids for Dehydration, ACS Sustainable Chem. Eng., 2020, 8(48), 17763–17771, DOI:10.1021/acssuschemeng.0c06001.
- S. Lee, T. Y. Lee, E. Amstad and S.-H. H. Kim, Microfluidic Production of Capsules-in-Capsules for Programed Release of Multiple Ingredients, Adv. Mater. Technol., 2018, 3(5), 1800006, DOI:10.1002/admt.201800006.
- R. P. Swatloski, J. D. Holbrey and R. D. Rogers, Ionic Liquids Are Not Always Green: Hydrolysis of 1-Butyl-3-Methylimidazolium Hexafluorophosphate, Green Chem., 2003, 5(4), 361–363, 10.1039/b304400a.
- M. D. Bermúdez, A. E. Jiménez and G. Martínez-Nicolás, Study of Surface Interactions of Ionic Liquids with Aluminium Alloys in Corrosion and Erosion–Corrosion Processes, Appl. Surf. Sci., 2007, 253(17), 7295–7302, DOI:10.1016/j.apsusc.2007.03.008.
- W. Xu, L. M. Wang, R. A. Nieman and C. A. Angell, Ionic Liquids of Chelated Orthoborates as Model Ionic Glassformers, J. Phys. Chem. B, 2003, 107(42), 11749–11756, DOI:10.1021/jp034548e.
- R. Santiago, J. Lemus, C. Moya, D. Moreno, N. Alonso-Morales and J. Palomar, Encapsulated Ionic Liquids to Enable the Practical Application of Amino Acid-Based Ionic Liquids in CO2 Capture, ACS Sustainable Chem. Eng., 2018, 6(11), 14178–14187, DOI:10.1021/acssuschemeng.8b02797.
- H. Li, Y. Cui, H. Wang, Y. Zhu and B. Wang, Preparation and Application of Polysulfone Microcapsules Containing Tung Oil in Self-Healing and Self-Lubricating Epoxy Coating, Colloids Surf., A, 2017, 518, 181–187, DOI:10.1016/j.colsurfa.2017.01.046.
|
This journal is © The Royal Society of Chemistry 2021 |
Click here to see how this site uses Cookies. View our privacy policy here.