DOI:
10.1039/D1RA03023J
(Review Article)
RSC Adv., 2021,
11, 32917-32941
Long-term durability and ecotoxicity of biocomposites in marine environments: a review
Received
18th April 2021
, Accepted 20th September 2021
First published on 7th October 2021
Abstract
There is a growing interest in replacing fossil-based polymers and composites with more sustainable and renewable fully biobased composite materials in automotive, aerospace and marine applications. There is an effort to develop components with a reduced carbon footprint and environmental impact, and materials based on biocomposites could provide such solutions. Structural components can be subjected to different marine conditions, therefore assessment of their long-term durability according to their marine applications is necessary, highlighting related degradation mechanisms. Through an up-to-date review, this work critically discusses relevant literature on the long-term durability of biocomposites specific for marine environments. Importantly, in this review we report the effects of abiotic parameters, such as the influence of hygrothermal exposures (temperatures and UV radiation) on physical, mechanical and thermal characteristics of biocomposites. Furthermore, we identify and discuss the potential ecotoxicological effects of leaching substances and microplastics derived from biocomposites, as well as the change in mechanical, physical and thermal behaviours correlated to degradation in the fibre matrix interface, surface defects and overall deterioration of the composite's properties. Finally, the combined effects of various environmental exposures on the long-term durability of the biocomposites are critically reviewed.
1. Introduction
Polymers have been a suitable solution to various applications in our society since their origin, whether for household or industrial purposes.1,2 About 8.3 billion tonnes of plastic have been manufactured already since 1950 and the global production of fossil fuel-based polymers is about 360 million tonnes per year.3 Despite many benefits plastics offer to human societies, they also lack proper recovery and recycling procedures, hence representing a significant risk of environmental damage.4 Accidental release or poor waste management can lead to accumulation of plastic debris in marine environments, including in the form of microplastics (MPs, <5 mm), which have the potential to adversely affect organisms and humans.5 For example, currently the Mediterranean and Yellow Seas are considered to be hotspots of MPs accumulation and areas where biota may already be at risk.6 Moreover, the severity of the marine environment due to high salinity, fluctuant temperature, ultraviolet (UV) radiation and moisture uptake, has led to strong interest in materials that are resistant to physical stress and particularly not affected by corrosion.7,8 Efforts to recover or recycle fossil based plastics have been motivated by concerns over maximum fossil-fuel resource dependence, greenhouse gas emission and damage to ecosystems and human health, leading research towards the development of more sustainable polymers.9 To evaluate the durability of biocomposites for marine structures it is important to describe this environment and its interactions with both floating and underwater polymeric structures. Glass and carbon fibre reinforced composites have been used for applications in the aerospace, automotive and marine fields for many years due to their outstanding mechanical properties. However, these composites are made from fossil-based polymers, using an energy intensive process with a large carbon footprint.10 For example, in the last decades material science and research has been directed towards using more sustainable biobased and biodegradable polymers and composites instead of using fossil-based polymers. This shift can provide a more sustainable solution for reducing the dependence on non-renewable fossil-based plastics. The increased use of biocomposites has been addressed in previous reviews,11–14 nevertheless, their mechanistic and ecotoxicological characteristics have often been studied on an ad hoc basis and not specifically referred to marine applications. Seawater applications such as sailing yacht design, water crafting, small submersible boat or craft, offshore structures, and other marine structural components can benefit from biopolymers and composites. The degree of biodegradability and biocompatibility of contemporary biopolymers, as well as the interaction with natural fibres, are addressed hereafter, considering exclusive key factors crucial to the moisture uptake of these materials in marine applications. The goal of this review paper is to highlight benefits for the industry and some key issues of biopolymers and composites materials together with their long-term durability in abiotic conditions; moreover, further recommendations on the type of biocomposites that are more suitable for marine environment will be provided and presented by critically analysing current available literature. Additionally, this work will provide an overview on biobased composites, ecotoxicological effects, related critical issues and important properties (mechanical, long-term durability and environmental) in recent marine applications.
1.1 The marine environments and their effects on service conditions
The marine environment combines a number of factors, general or specific, which induce stress and pressure leading to changes in the mechanical and physical properties of natural fibre reinforced and polymer matrix composites. The most obvious is exposure to liquid water, either through exposure to high relative humidity or complete seawater immersion. The moisture absorption and humidity are common to many composite applications but the seawater immersion is a specific marine feature and requires particular attention. Continuous exposure to UV radiation may also degrade polymers and needs to be considered. Other environmental parameters such as temperature are within commonly accepted ranges, typically from around 5 °C in deep sea to a maximum around 50 °C at the surface. A specific marine factor is marine fouling, which involves the adhesion of marine growth to structures in shallow water. Another specific factor to consider is mechanical loading. Wave action periods are typically around 10 seconds, so marine structures can accumulate large numbers of cyclic loads leading to fatigue. Underwater applications are subjected to hydrostatic pressures, which increase with immersion depth so compression behaviour is important. Lastly, the coupled effects of seawater immersion and mechanical loading require complex interactions to be considered.15–19
Material requirements for marine structures depend on where and how the materials are deployed. Overall, we consider two categories, surface vessels and underwater structures. Surface structures such as boats, buoys, and other floating systems are partly immerged and partly exposed to sunlight. In addition to these two environments an intermediate splash zone can include the worst of both, with parts of the structure continuously drying then re-wetting. This is a critical zone for metallic structures, where corrosion rates are highest20 and thus it is particularly attractive for composite solutions. For all long-term floating applications protective coatings are used, anti-fouling paints in particular and these will affect both durability in service and end-of-life options. Underwater structures include a range of structures from oceanographic equipment to sub-sea offshore equipment and submarines. While composites are less widespread than for surface applications their use is increasing as renewable energy developments advance and deep-sea exploration and oil and gas exploration extend to deeper water. The design environment is more easily defined than for floating structures with pressure due to immersion depth the main parameter to consider. A typical service life for an offshore structure is 20 years so detailed knowledge of material behaviour is needed.16
2. Understanding hygrothermal ageing of biocomposites for extended service life under marine environments
2.1 Effects of seawater immersion on the mechanical properties
Biocomposites are more environmentally sensitive than conventional composites.21–23 To understand the different degradation mechanisms, the effect of water on the mechanical properties of each independent component, i.e., the fibres, the matrix, and the fibre/matrix interphase region, as well as the biocomposite should be studied. Hydroscopic ageing of the polymers involves complex degradation phenomena. Two main degradation processes can be induced; physical ageing (matrix swelling and plasticisation) and chemical ageing (hydrolysis, oxidation).15 The changes in properties can be either reversible or permanent, often resulting in a drop in the mechanical properties: for example, Deroiné et al.24 have performed a one year accelerated ageing study on poly(3-hydroxybutyrate-co-3-hydroxyvalerate) (PHBV) with tensile property characterisation. These authors observed that at a first stage of the immersion the PHBV tends to recover its initial mechanical properties after drying, showing a reversible phenomenon due to plasticisation. But after one year of ageing at 40 and 50 °C the behaviour evolved towards irreversible degradation with a decrease of strain and stress at break, a phenomenon correlated with hydrolysis of the polymeric matrix.24 The mechanical properties of natural fibres show variable responses to environmental stresses, depending on many environmental parameters.25 Controlling these parameters is not possible, so this can lead to uncertainty in fibre performance and their mechanical behaviours. To avoid uncertainty, key design criteria can be defined. For instance, Singh Virk et al.26 have proposed the failure strain criteria. The structure of the fibre is also a key parameter which influences the moisture absorption. The materials that compose the fibres have a distinct hygroscopic nature, that fosters the loss of mechanical properties, further accentuated by their composition (cellulose, hemicellulose, lignin, pectin, wax content).22,27,28 Low humidity content is generally beneficial for the mechanical properties of the fibres; additional humidity plays a key role in their performance, for example, at high humidity level general mechanical properties drop.29 For biocomposites, the loss of mechanical properties due to hygroscopic ageing is mainly due to the resin–matrix interface. Dhakal et al.21 have found that the tensile and flexural properties of hemp/polyester composites drop significantly due to the degradation of the fibre–matrix interface as a consequence of moisture absorption. This phenomenon can pose a serious issue for natural fibre composites to be used in marine applications. In order to get a better understanding of the loss of properties, the interfacial degradation mechanism induced by water has been directly tested by Le Duigou et al.30 who studied the apparent interfacial shear strength of a single flax fibre embedded in epoxy micro droplets. These authors found that for short immersion durations, the loss of mechanical properties was reversible, but that for longer durations the loss was permanent, with the degradation involving the dissolution of fibre constituents and at long immersion times the damage of microstructures. Espert et al.31 have also reported the same loss of adhesion between fibre and matrix on a wood fibre/polypropylene composite. With Scanning Electron Microscopy (SEM) images, the authors showed the appearance of voids and the disappearance of fibre constituents after ageing. Thwe and Liao32 observed similar behaviour with a bamboo polypropylene composite with a reduction of tensile strength and modulus as well as a degradation of both the fibre and the interfacial adhesion. Another reported degradation mechanism of biocomposites inducing loss of mechanical properties with ageing is the swelling of the fibres. Badia et al.33 have shown that the swelling of the sisal fibres in a PHBV matrix caused cracks and fibre debonding. In the literature most of the studies have involved tensile testing. However, in marine applications such as boat hulls the mechanical response to impact is crucial. This mechanical property has been studied by Papa et al. on flax polypropylene composites after ageing.34 The 44 mm thick composite samples were immersed for a week at 70 °C. The authors evaluated the short beam shear strength and the flexural strength, together with the maximal load and the penetration energy from the response of the material to a low velocity impact. This section highlighted the critical role of the interface region in obtaining enhanced mechanical properties. Therefore, there is a need to develop new solutions that are capable of addressing the issues covering different marine conditions.
2.2 Ageing characteristics under different service conditions
Composites can be used in marine environment in various applications. Some of them can be used for several decades, such as canoes or boats for example (see Section 3 of this paper). To simulate the marine conditions, composite samples are subjected to hygroscopic ageing in laboratories. It is well known that polymers and composites absorb water because of the difference in chemical potential between the material and the environment. In the case of biocomposites made with natural fibres, the water absorption is even larger than with classic glass fibre composites.35 In fact, both glass and carbon fibres absorb little water whereas natural fibres such as flax can absorb more than 15% by weight.35 This behaviour can be explained by the fibre composition.36 Weighing of samples to measure water absorption is one of the characterisation techniques used to monitor the moisture gain behaviour during ageing.37,38 The preferred ageing method is to immerse the material in the medium of the application, i.e., seawater; however, this is not always possible in the laboratory environment and in many studies, samples are immersed in distilled water or tap water. The influence of the nature of the water (presence of mineral salts, presence of ions, impurities, etc.) can impact water absorption in biocomposite materials. As an example, Deroiné et al.39 have performed a comparative accelerated ageing study of polylactide (PLA) between distilled and seawater. The PLA samples were immersed in distilled water, renewed every week, at 25, 30, 40 and 50 °C and in naturally filtered and constantly renewed seawater at 25 and 40 °C. The water diffusion was shown to be faster in distilled water due to the presence of mineral salts.
Hygroscopic studies are sometimes preferred to immersion studies. In this case, leaching from the biocomposite into water does not occur. Célino et al.40 studied the water diffusion in 4 different natural fibres (hemp, flax, jute and sisal) when samples were either immersed at room temperature or placed in an environmental chamber at 80% relative humidity and 23 °C. They observed that all fibres have similar water diffusion behaviour in the same environment but their behaviour differs from one environment to the other. Réquilé et al.41 have performed hygroscopic studies on hemp/epoxy with amine hardener composite. Samples were in environmental chambers at 9, 33, 75 and 98% RH at 23 °C. They found that the moisture sorption was mainly controlled by the fibres, despite a non-negligible hydrophilic behaviour of the matrix, and that at high humidity level the large increase of the water uptake in the composite correlates with a similar behaviour in the natural fibres.
Under hydrothermal ageing, the rate of moisture gain, also known as diffusion coefficient, is greatly influenced by the temperature and humidity. In order to get moisture absorption percentage up to the saturation level experimentally at room temperature, it often requires long durations. In order to reduce this time, accelerated ageing conditions are used. Moreover, to estimate the long-term behaviour, accelerated ageing tests are mandatory. The most common way to perform accelerated ageing tests is by increasing the temperature and the relative humidity.15
The effect of the temperature has been studied by Le Duigou et al.42 on flax/poly-L-lactide (PLLA) composite immersed in seawater at 4, 20, 40, 60 and 80 °C. The composting of PLLA has a temperature close to 58 °C. They showed that ageing close to the glass transition temperature leads to a very rapid degradation related to hydrolysis of the matrix, not representative of what happens in the sea. The temperature has a strong influence on the water uptake, as was also confirmed by Badia et al.33 on poly(3-hydroxybutyrate-co-3-hydroxyvalerate) (PHBV)/sisal biocomposites. The choice of the accelerating temperature has to be performed with care depending on the material, the application and the service environment. Natural exposure studies on biocomposite are needed to correlate accelerate ageing in the laboratory with natural ageing in service. For example, Le Duigou et al.,36 performed a 2 year study on injection moulded flax/PLLA composites. Samples were immersed in the sea at 5 m depth and were periodically removed to be characterised. It was found that biocomposites have high water uptake content in both laboratory and sea environments, with similar loss in modulus and strength when plotted as a function of weight gain. The work carried out by Fulco et al.43 on the carbon epoxy laminate aged by hygrothermal exposure. In such exposures either direct to liquid water or marine environments, the interactions causes degradation of polymer matrix and the fibre/matrix interface becomes vulnerable. This phenomenon is further elaborated by the SEM images illustrated in Fig. 1. For the samples exposed to ageing, loss of matrix mass with the exposure of carbon fibres and degradation at the fiber/matrix interface can be observed.
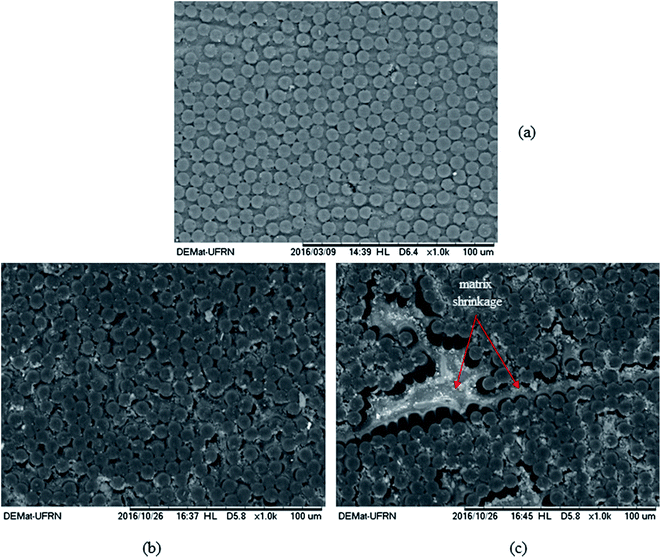 |
| Fig. 1 SEM images of a carbon/epoxy composite (cross-section): (a) before and (b and c) after hygrothermal ageing (source: A. P. P. Fulco, A. M. de Medeiros, M. L. P. Tonatto, S. C. Amico, R. Talreja and J. D. D. Melo, Composites, Part A, 2019, 127, 105628). | |
2.3 Factors influencing ageing and degradation
The marine environment is known to be very aggressive, with both abiotic (i.e., humidity, UV, physical stresses) and biotic degradation processes.44 All polymers and composites absorb water when they are immersed or exposed to various ageing conditions; i.e. high temperature, humidity, and various loads. The effects of single or combined ageing conditions may contribute the degradation of thermal and mechanical properties limiting the overall environmental durability of biobased composites. As noted previously, hydroscopic ageing involves complex phenomena that can lead to two degradation processes; physical changes induced by matrix swelling and plasticisation and chemical changes with hydrolysis of the matrix and fibre degradation.15,45 On glass epoxy composites, Thomason45 has shown that several factors can influence the water absorption such as the void content, the type of matrix system, the interfacial strength and the fibre surface coating. On hemp fibre reinforced unsaturated polyester composites, Dhakal et al.,21 also showed that water uptake increases with increase of voids and cellulose content. Several authors have shown that biocomposites made with natural fibres have a high-water absorption which is controlled by the fibres35,46 due to their hydrophilic character. Le Duigou et al.36 have explained the important water uptake of flax fibres by their chemical constitution (cellulose and lignin) and by the multi-layered structure of the fibre. Most of the polymers proposed as biocomposite matrices are hydrophobic, which can lead to poor fibre/matrix adhesion. Several strategies have been developed by various authors to improve fibre/matrix adhesion. Chemical and physical treatments can improve biocomposite properties. The most common chemical method is the use of coupling agents. Joseph et al.47 have shown that the use of cardanol derivative toluene diisocyanate treatment reduced the hydrophilic nature of the sisal fibre in the sisal-polyethylene composite. Joffe et al.48 have studied several surface treatments on flax fibres, they found that an optimal choice of fibre treatment can improve the adhesion between the fibre and matrix. Concerning physical treatments, Summerscales and Grove49 consider the conditioning of the reinforcement fibres before composite manufacture to be essential. Baley et al.50 have performed an extensive study on the drying of flax fibres and its impact on the composite properties. It appears that excessive drying of the fibres results in a loss of biocomposite properties. Van de Velde et al.51 have shown that boiled flax can improve composite properties. Van den Oever et al.52 show that separating flax fibres into elementary fibres improves properties.
The matrix itself also ages and may be degraded with time. For exemple, Deroiné et al.24 have shown that the main abiotic degradation mechanism of immersed PHBV, a biodegradable biopolymer, is hydrolysis. Water diffusion in polymers is a complex phenomenon and it has been widely studied.53,54 Suitable matrix selection has to include durability considerations, as well as manufacturing and end of life options. Manufacturing adjustments can also provide a way to prevent the degradation. Le Duigou et al.30 have added extra layers of PLLA on the surface of flax/PLLA composites, they showed that these extra coatings can significantly slow down the water absorption. Van de Velde et al.51 have studied the influence of different process parameters on press moulding of flax/polypropylene composites: fibre orientation, pressing temperature and time all affect the final product. The manufacturing parameters such as temperature and pressure should be chosen carefully with respect of the fibre used and the polymeric matrix to avoid degradation. It is well accepted that the fibre orientation has a considerable impact on water absorption. The service conditions will also influence ageing and degradation. Zhang et al.29 have studied the influence of the relative humidity, and found a drop of properties of their flax/polyester composites around 70% RH. Complete immersion with accessible fibres at sample edges is therefore a very aggressive test condition for biocomposite ageing. Biocomposites based on wood have been used successfully in shipbuilding for centuries, and are still employed today but if we limit the definition of biocomposites to continuous natural fibre reinforced polymer composites then the marine applications are more limited. One of the first applications was for surf and paddle boards. For example, the ECOBoard project55 started in 2012 with the aim of making surfboards more sustainable by paying more attention to the materials used and their carbon footprint. In parallel, there have been several prototype boats projects. The NAVECOMAT study (2007–2011), resulted in the manufacture of a flax/PLA canoe demonstrator (Fig. 2).56
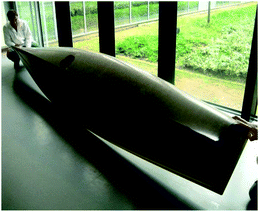 |
| Fig. 2 Flax/PLA canoe manufactured during the NAVECOMAT project. | |
Other flax reinforced canoes have also been proposed in Europe, for example by Flaxland57 and Lake Constance Canoes.58 A prototype 6.5 meters racing yacht Araldite with 50% flax reinforcement and the remainder in carbon fibres was developed and launched in 2010, competing in the 2011 mini-transatlantic race.59 A prototype 7 meters multihull entirely reinforced with flax fibres was designed by Kairos and built by the Tricat boatyard using infusion (Fig. 3).60 It was launched in 2013 after more than 3 years of material studies. Both multiaxial and unidirectional flax fibres are used to reinforce a partially biosourced polyester matrix. Cork and balsa wood are used in the lateral and central hulls respectively.
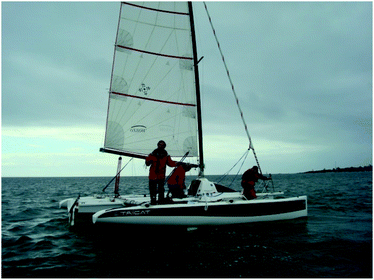 |
| Fig. 3 Gwalaz, flax fibre reinforced trimaran. | |
Tests performed on samples removed after one year of navigation indicated no change or degradation in mechanical properties. Another flax fibre boat project was described by Castegnaro et al.61 This used flax/epoxy in a balsa sandwich. No damage was noted after 4 years of navigation. These results indicate that provided the matrix polymer can protect the fibres from moisture then natural fibre composites can be a good candidate material for marine applications.
2.4 Mechanical properties
The mechanical properties of biobased composites are influenced by various abiotic parameters and conditions. With this in view, there has been a significant amount of research and development work concentrated in achieving comparable mechanical performance of biobased composites with respect to conventional composites reinforced with glass fibres. However, morphological structure, chemical composition and fibre dimension variability can all play a contributing role in lowering mechanical properties for natural fibre reinforced biobased composites. This variability can lead to further issues in sample fabrication and processing parameters. Another key issue faced by biocomposite materials is their long-term durability in harsh environments. For example, natural fibre reinforced composites and biocomposites absorb moisture under various environmental conditions and this can be further accelerated by mechanical stresses, UV radiation and exposure to elevated temperatures. The influence of these conditions is more prominent for natural fibre composites than for glass or carbon fibre composites. The following sections review some of the published work covering these aspects of natural fibre composites and biocomposites.
2.4.1 Effects of moisture absorption on the mechanical properties. The effects of the temperature on the mechanical properties of hemp fibre reinforced unsaturated polyester (UP) composites was investigated at room and elevated temperature.21 The report highlighted first that the presence of hemp fibre reinforcement contributed to an improvement of mechanical properties of the UP matrix. The mechanical properties (tensile and flexural) of hemp/UP composites were significantly influenced by the moisture absorption at room and elevated temperatures. The saturation moisture uptake and moisture diffusion coefficient were reported to increase with the increase in temperature due to the creation of increased micro-cracks at higher temperature. The reduction in mechanical properties was attributed to weak fibre matrix interfaces (deterioration of fibre/matrix bonding) induced by the moisture ingress (Fig. 4). Furthermore, fibre swelling induced by moisture absorption accentuates debonding. There are many reported works suggesting that moisture absorption decreases mechanical strength and modulus but increases ductility due to plasticisation effects. To minimise the water immersion test time, accelerated water absorption measurements at higher temperatures are usually considered. The moisture ingress at elevated temperatures can cause swelling, cracking, and further debonding resulting in a significant loss of structural integrity. Work reported by Chang et al.62 on jute/PLA highlighted that the interfacial shear strength was significantly reduced after immersion in boiling water. This was attributed to the swelling as well as deterioration of the fibre/matrix interface adhesion. The strength reduction evolution has been assigned to three different stages (Fig. 5). It is evident from the above discussion that moisture ingress has a negative effect on mechanical properties. Nevertheless, if available material improvement techniques are applied the negative influence on mechanical properties from moisture attack can be minimised.
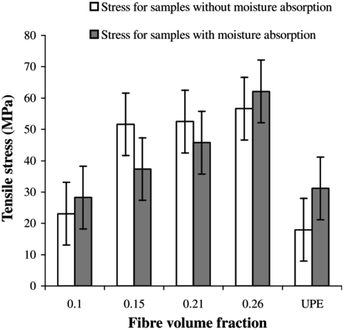 |
| Fig. 4 Effects of moisture absorption on the tensile strength of hemp/UP composites. Reproduced with permission from ref. 21 [license number: 4992421301110]. | |
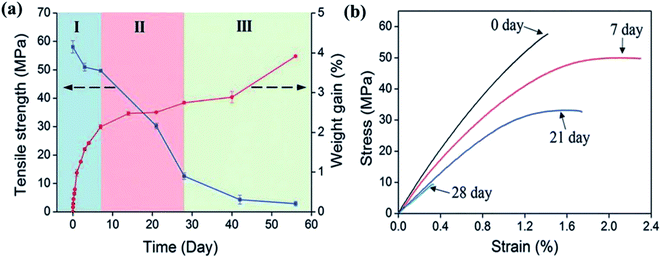 |
| Fig. 5 Reduction of tensile properties of jute/PLA biocomposites after ageing 50 °C (a) tensile strength against weight gain as a function of immersion time (b) effect of ageing degradation duration on stress-curves (source: B. P. Chang, A. K. Mohanty and M. Misra, RSC Adv., 2020, 10, 17955–17999). | |
2.4.2 Techniques to improve mechanical properties and water repellence behaviour of composites. Different fibre surface treatment techniques have been employed to improve the water repellence behaviour and to enhance the fibre–matrix interfacial properties of natural fibre composites to be used in marine applications. These various treatments promote strong interfacial bonding which is critical to achieve optimal mechanical properties. Various treatments remove impurities and hydrophilic components present on fibre surfaces. Additionally, these various treatments improve the wettability of fibres, which in turn provides better interfacial bonding. One of the techniques used to measure the wettability fibres by matrix polymers is contact angle measurement, which provides information on surface energies.In recent years hybrid techniques, based on the synergistic effects of two materials in single composites, has been employed to overcome some of the drawbacks of natural fibre composites, including moisture absorption behaviour. A hybrid approach consists in introducing less hydrophilic reinforcements as filler to the matrix, reducing the effect of the moisture absorption and saturation moisture uptake. Hybridisation of synthetic fibres into natural fibre composites has been shown to be an effective technique to enhance mechanical, thermal and water repellence behaviour of natural fibre composites as illustrated (Fig. 6).62 This technique is one way to address some of the drawbacks of natural fibre composites.
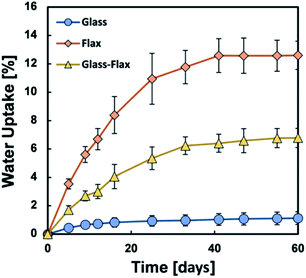 |
| Fig. 6 Enhanced water uptake resistance with the addition of glass fibre into flax biocomposites [source: B. P. Chang, A. K. Mohanty and M. Misra, RSC Adv., 2020, 10, 17955–17999]. | |
Barouni and Dhakal worked on the low velocity impact damage of flax and glass/flax hybridised composites.63 Their results exhibited a significant improvement on the impact damage behaviour of flax fibre reinforced composites with the incorporation of glass fibre as hybrid reinforcement (Fig. 7). Their findings suggest that hybridising synthetic fibres into natural fibres helps to overcome the deficit of mechanical properties and moisture repellence behaviours of natural fibre composites.
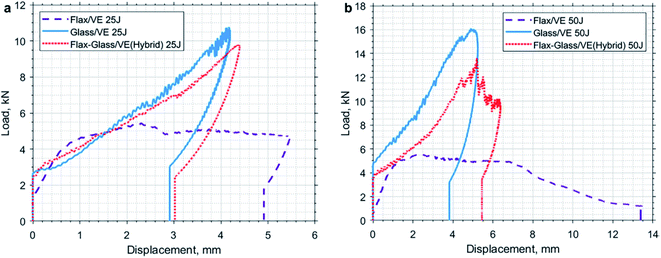 |
| Fig. 7 Load–displacement traces for flax and glass/flax reinforced hybrid composites under (a) 25 Joules and (b) 35 Joules of impact energy. Reproduced with permission from K. Barouni and H. N. Dhakal63 [license number: 4992430539751]. | |
A similar result has been suggested by Almansour et al.64 who investigated the influence of moisture absorption on mode II interlaminar fracture toughness characteristics of flax and basalt fibre reinforced vinyl ester hybrid composites.64
They reported a significant improvement in fracture toughness behaviour of flax/VE composites with basalt fibre hybridisation. Similarly, they were able to reduce the moisture absorption of flax/VE composites with basalt fibre hybridisation as illustrated in (Fig. 8).
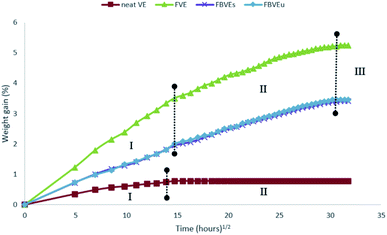 |
| Fig. 8 Weight gain versus function of time 3-point end notched specimens (FVE: neat VE, flax/vinyl ester (FVE), flax/vinyl ester stitched (FBVEs) and flax basalt vinyl ester unstitched (FBVEu)) exposed to distilled water. Reproduced with permission from ref. 64 [license number: 4992430819544]. | |
Dhakal et al.65 carried out an investigation into the effects of carbon fibre hybridisation on the mechanical and moisture resistance behaviours of flax/epoxy biobased composites. They reported noticeable improvements in moisture repellence behaviour and tensile properties of hybrid composites as a result of carbon fibre hybridisation.65
Flax cross-ply samples exhibited a 282% increase in tensile strength. However, the strain of flax cross-ply composites was decreased by a 47%. In this case, the stiffness was increased but the strain to failure was decreased (Fig. 9). The influence of moisture absorption on the properties of flax fibre reinforced epoxy based composites was investigated by Scida et al.66 who showed a large drop in modulus (−55%) but a smaller reduction in strength (−12%) after 38 days ageing at 90% RH (Fig. 10).
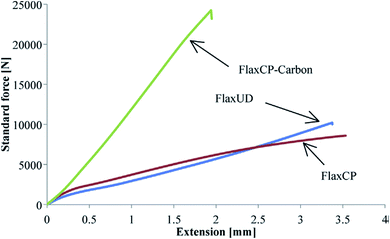 |
| Fig. 9 Load–extension plots for different flax and flax carbon hybrid composite samples in tensile testing. Reproduced with permission from ref. 65 [license number: 4992431067492]. | |
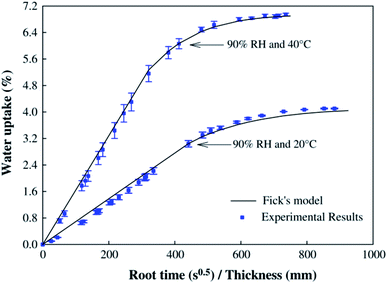 |
| Fig. 10 Moisture diffusion characteristics of flax fibre reinforced composites at two different temperatures at 90% humidity. Reproduced with permission from ref. 66 [license number: 4992431222559]. | |
2.5 Moisture uptake behaviour and mechanisms
Moisture ingress in biocomposites takes place in various ways depending on the environments that they are exposed to. For example, if composites are exposed to elevated temperatures, moisture penetration is more aggressive into the fibre–matrix interface compared to room temperature exposure. Natural fibres include: flax, hemp, jute, sisal, kenaf, date palm, bagasse (fibrous residue after sugarcane stalks are crushed) amongst others. Natural fibres contain cellulose, and hemicellulose, which contain a large number of available hydroxyl groups, which attract water molecules and create hydrogen bonds. This process allows cell walls to swell as the fibrils are pushed out.21 This phenomenon causes natural fibres to weaken, and results in reduced ability to withstand applied load and an inability to transfer load in the interface region of composite. This disruption causes a weak fibre matrix interface. As a result, this whole moisture ingress process leads to significant reduction of strength and stiffness. Understanding moisture ingress mechanisms especially in a marine environment (seawater exposure) is a complex process.67 The different diffusion mechanisms (matrix, fibres and interfaces) and the effects of geometric dimensions and the fibre orientation are illustrated in Fig. 1168 and been described in figure caption.
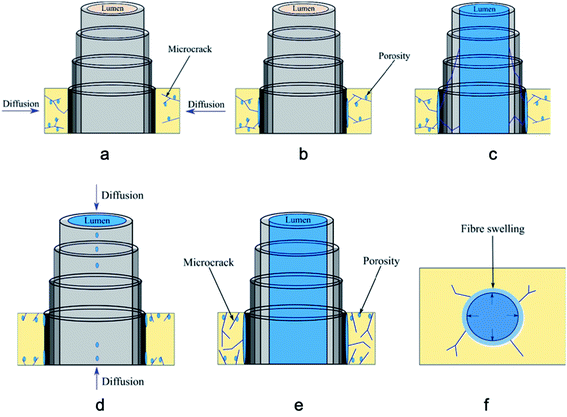 |
| Fig. 11 The diffusion mechanisms are illustrated: (a) micro-cracks present in resin; (b) water molecules reaching in the fibre–matrix interface, and (c) filling the hollow part of the flax fibre lumen. Diffusion phenomenon occurs also through the direction of fibres; (d) water molecules ingress by capillarity through the micro-cracks present at the fibre–matrix interface and through lumen; (e) micro-cracks present in resin and at the fibre matrix interface; (f) fibre swelling and matrix radial cracking. Reproduced with permission from ref. 68 [license number: 4992440237683]. | |
The resulting reduction in strength is accentuated by swelling and debonding of the fibres.65 The key steps leading to changes and degradation of the fibre and composite structure are summarised below:
• Water molecules diffuse through the microscopic gaps (micropores) between polymer chains in the fibre and the composite.
• Voids, defects and gaps lead to capillary transport between the fibres and the matrix.
• Swelling of the fibres, causes expansion of the micro-cracks in the matrix leading to debonding.
• The overall fibre–matrix bond is damaged and this leads to reduction of mechanical properties (strength and stiffness).
It has been shown65 that for flax unidirectional (Flax/UD) and flax cross-ply (Flax/CP) samples immersed in de-ionised water at room temperature (23 °C), the moisture uptake percentages were approximately 13% and 23%, respectively, after 648 hours. The moisture absorption values measured for carbon fibre hybridised specimens, were much lower. The maximum percentage weight gains for FlaxUD/carbon and for FlaxCP/carbon immersed at room temperature for 648 h were approximately 2% and 8%, respectively. It is worthy to note that moisture ingress is equally influenced how the fibres are laid out in the composite; for example, cross-ply samples show higher moisture uptake compared to unidirectional flax fibre composites as highlighted by Dhakal et al.65
2.6 Thermal degradation
One important aspect of the durability of biocomposites is their thermal stability. The stability of the composite components, fibres and matrix polymer, is first critical during manufacturing of components, as many thermoplastic matrix polymers require elevated temperatures to flow and impregnate fibres. The thermal behaviour of the manufactured composite is also one of the factors which can limit final applications performance, though high temperature environments are not a feature of most marine applications. Here we will first consider the base materials, then the resulting composite. First, it should be noted that there a number of factors involved in the thermal stability. A common way to quantify the thermal stability of polymers is through thermo-gravimetric analysis (TGA). This involves heating at a constant rate and measuring weight loss, it can certainly provide useful information on global changes but additional techniques are required to understand the causes of these changes. The polymer microstructure can change during heating (cure, post-cure, crystallinity changes, oxidation) and various other analyses such as differential scanning calorimetry (DSC), Fourier-transform infrared spectroscopy (FTIR), gel permeation chromatography (GPC), can provide valuable information. Most plant fibres are based on cellulose and lignin that are vulnerable at high temperatures. The thermal susceptibility of natural fibres represents the first limitation in biocomposites manufacturing. There have been extensive studies on how temperature affects wood products, but mostly concerned with pyrolysis. For example, Shen and Gu69 analysed products evolving during heating but focussed on high temperatures, above 400 °C. George et al.70 describe a study on untreated (green) and treated (Duralin process, 180 °C treatment) flax fibres. The treatment increases the fibre stability but above 200 °C lignin degradation starts, and at higher temperatures other polysaccharides, mainly cellulose, are oxidised and degraded. They concluded that the maximum processing temperature for flax fibre composites is around 220 °C. Gassan and Bledzki71 studied the thermal degradation of jute and flax fibres at temperatures up to 210 °C for up to 120 minutes. These authors found that temperatures below 170 °C only slightly affect flax and jute fibre properties, while temperatures above 170 °C significantly reduced fibre tenacity and degree of polymerisation. Chaishome et al.72 indicate that the decomposition of hemicelluloses in flax fibres during thermal degradation is a factor, which will have a detrimental effect on the thermal stability of fibres, particularly with slow heating rates. The second limitation on manufacturing temperature is the stability of the matrix polymer. Peelman et al.73 have provided data for several biopolymers based on PLA, polyhydroxyalkanoate (PHA), cellulose and proteins. PLA in particular has low thermal stability, and is particularly sensitive to hydrolysis.74 In a study of biocomposite manufacturing, Khanlou75 have described various degradation mechanisms, and proposed a thermo-kinetic model to account for chain scission of both flax fibres and PLA at different processing temperatures. These models were then employed to predict composite tensile properties after compression moulding. Baley et al.50 examined the influence of drying on single fibre and unidirectional epoxy composite properties. Drying fibres for 24 hours at 105 °C was shown to reduce both failure stress (−44% on average) and failure strain (−39%) significantly, and these reductions were transferred to dried composites. Finally, it is interesting to note that flax fibres have been shown to exhibit anti-oxidant properties when used to reinforce polyethylene.76 It is evidence from the above discussion that biocomposites reinforced with cellulose and lignocellulose fibres undergo to different thermal degradation processes in which temperature plays significant role. The reason being these reinforcements along with their morphological structures that influences the thermal stability.
2.7 UV degradation
The challenge of replacing synthetic materials with natural materials has encouraged major R&D contributions to justify the selection of natural fibres as reinforcement for polymer-based composites. In parallel, the increase in demand for natural fibres such as hemp, flax, kenaf, jute and bamboo manifest a clear interest from the industry to introduce alternatives to traditional synthetic reinforcing materials. Indeed, production and related energy consumption of synthetic fibres can exceed by 60% that required for natural ones, as reported for the case of the glass fibres.77 The degradation of natural reinforcement is also attracting the attention of materials scientists aiming to solve critical issues related to the use of biobased reinforcement and related moisture, thermal, fire, and ultra UV degradation mechanisms. The intrinsic hydrophilicity of natural fibres can lead to inferior interfacial bounding to the polymeric matrices, which are mostly hydrophobic.78–81 Biodegradability is a degradation process that can be particularly influenced by the light-degradation or photo-degradation rate of the material of interest. In general, polymers are destabilised by sunlight or by artificial light, and UV degradation tests are performed to severely damage the materials. The constantly growth of CO2 in the atmosphere is responsible for a major impact of the UV rays that arrive with a mean wave length of 280–320 nm, representing a threat not only for construction materials but even for highly organised biomaterials such as skin.82 Photodegradation of natural composites is mostly promoted by weathering periods, and outdoor exposure.83 The mechanical strength of natural fibre composites can be affected as a result of photodegradation processes that act over several length scales within polymers. Critically, degradation due to oxidation acts first on the surface because of the major exposure of the surface to oxygen. Cracks are activated by mechanical stresses within inhomogeneous regions defined by different molecular weights. Indeed, UV radiation absorbed by the polymer can start molecular chain scissions, followed by crack opening, light penetration and degradation of the global material mechanical behaviour.84–86 The increasing surface area due to the chain scission, encourages further degradation. Moreover, different environments present several factors that promote microbial assimilation of plastics. Water, salty water, soil and landfill are environment in which UV light can activate their degradation mechanisms depending on the penetration level. For example, in landfill conditions there is limited availability of UV light and oxygen given the dark and anaerobic nature of this environment.87 Previous studies addressed the UV degradation as a chain reaction which can be initiated by a prior exposure of the polymer to UV light88 and that can continue even in its absence.89,90 An environment such as water presents elements that accelerate the polymer degradability due to the joint effect of UV light, oxygen and moderate temperatures.91 Nevertheless, the seawater environment has lower concentrations of micro-organisms, therefore slows down the hydrolysis rate of polymers, together with the ability of these microorganisms to colonise the plastic surface.92 Natural fibre polymeric components are vulnerable to UV light degradation. In particular lignin, that is the main polymeric components in natural fibres, absorbs up to 80–90% of incident light. Surface oxidation, matrix crystallinity alteration and interfacial degradation compromise the mechanical properties of natural fibre composites.93 Moreover, further studies addressed how water spray cycles combined with UV radiation foster photodegradation activities leading to mechanical degradation.84,85 Research contributions towards the stabilisation of lignin within the cell wall or extracellular matrix are crucial to improve the overall biocomposite resistance to ultraviolet radiation. Moreover, additives can be included in fibre reinforced polymers, which are subject to colour changes if exposed to UV rays. The colour reflects undergoing chemical changes, beneath the surfaces of composites where the degradation of the fibres is happening. Polymer coatings able to reflect UV radiation can be developed by using cold plasma modification. Biocomposites suffer from oxidative degradation and antioxidants can be used to make them more competitive in terms of durability and mechanical properties. Addition of antioxidants and fire retardants could improve the tensile, flexural and impact strengths but at the expense of the wettability of the biocomposites that absorb more water.94 Most studies are conducted under accelerated conditions in order to monitor the degradation rate. Reproducing boundary conditions similar to nature implies years of experimentation. Therefore, UV lighting can be used in conjunction with incubation at different temperatures to start polymeric chain breakdown and polymer degradation.90,95–98
3. Assessment of leaching substances from biocomposites to the marine environment
3.1 Plastic additives used in biocomposites
Plastic additives are chemical compounds incorporated in the polymer matrix to polymerise, process or modify the properties of polymers.99 Common plastic additives can be categorised as: functional additives (e.g., plasticisers, flame retardants, stabilisers and lubricants), colorants (e.g., pigments), reinforcements (e.g., glass fibres, hemp fibres), and filters.100 To date, 418 substances have been recognised as plastic additives and registered under the REACH (Registration, Evaluation, Authorization and Restriction) regulation of the European Union.101 In addition to their functional or visual role, additives are also applied to improve the performance of final applications during the manufacturing of biocomposites and biopolymers (representative additives summarised in Table 1). For example, biopolymers like PLA and poly(3-hydroxybutyrate) (PHB) can be too hard, brittle or fragile to be used directly in final applications, but the inclusion of plasticisers improves their flexibility.102,103 Additives used for biocomposites are usually natural-based plasticisers like polyols, citrate esters, monosaccharides, fatty acids and vegetable oils.104 These additives are used instead of conventional substances, as they have a lower potential for toxicity to the environment and organisms (Table 1). Similarly, synthetic antioxidants such as butylated hydroxyanisole (BHA) and butylated hydroxytoluene (BHT) are usually alternated by natural-derived substances like gallic acids and α-tocopherol especially in biocomposites for packaging applications.105,106 Apart from organic additives, a group of inorganic compounds are commonly included as flame retardants in biocomposite applications.107–109 The majority of substances used as additives in biocomposites have either been registered or pre-registered in the REACH regulation. Most of these substances are readily biodegradable and are not considered harmful to aquatic organisms, indicating a potential low impact to the environment when leaching (see Section 4.2), if considered as single substances (Table 1). However, the toxicity of leaching substances combined in a mixture is mostly unknown.
Table 1 Summarised information of representative additives used in biopolymers and biocompositesa
Category of additives |
Example substances |
Polymeric applications |
CASb |
Molecular weightb (g mol−1) |
log Kow or log Kpb |
Water solubilityb (mg L−1) |
Registered in REACH?b |
Ready biodegradabilityb |
Aquatic toxicityb |
BIOPP: biobased polypropylene; TPS: thermoplastic starch; BioPET: biobased polyethylene terephthalate; PLA: polylactic acid; PVA: poly vinyl alcohol; PHB: poly(3-hydroxybutyrate). Values are selected from the European Chemical Agency (ECHA)'s REACH registered substance factsheets. Further information can be found at https://echa.europa.eu/information-on-chemicals/registered-substances.127 |
Plasticisers |
Glycerol |
BioPP, TPS, BioPET, PVA composites |
56-81-5 |
92.09 |
−1.75 |
1000 g L−1 |
Yes |
Readily biodegradable (100%) |
LC50 (EC50) values > 885 mg L−1 |
Propylene glycol (PG) |
BioPP, PLA |
57-55-6 |
76.09 |
−1.07 |
100 vol% at 20 °C |
Yes |
Readily biodegradable (100%) |
96 h EC50 is 19100 mg L−1 in Skeletonema costatum |
Sucrose (α-D-Glc-(1→2)-β-D-Fru) |
BioPP |
57-50-1 |
342.3 |
|
|
Pre-registered |
|
|
D-Sorbitol (D-glucitol) |
BioPP |
50-70-4 |
182.17 |
|
|
Pre-registered |
|
|
Tributyrin (glycerol tributyrate) |
PLA, PHB |
60-01-5 |
302.36 |
|
|
Pre-registered |
|
|
Acetyl tributyl citrate (ATBC) |
PLA |
77-90-7 |
402.5 |
4.29–4.92 at 20–40 °C |
4.49 mg L−1 at 20 °C |
Yes |
Readily biodegradable (50%), Inherently biodegradable (50%) |
PNEC aqua marine = 2.2 μg ATBC per L |
Triethyl citrate (TEC) |
PLA |
77-93-0 |
276.28 |
1.17 at 40 °C |
58.1 g L−1 at 20 °C |
Yes |
Readily biodegradable (100%) |
Non-classification |
Polyethylene glycol (peg) |
PLA |
25322-68-3 |
|
−0.698 at 25 °C |
256.084 g L−1 at 25 °C |
Yes |
Readily biodegradable (100%) |
96 h EC50 > 100 mg L−1 in green algae |
1-Butyl-3-methylimidazolium chloride (BMIM-Cl) |
PLA |
79917-90-1 |
174.67 |
— |
— |
Yes |
— |
— |
Tributyl citrate (TBC) |
BioPET |
77-94-1 |
360.4 |
3.5 at 23 °C |
102.7 mg L−1 at 20 °C |
Yes |
Readily biodegradable but failing the 10 day window (100%) |
Non-classification |
Castor oil |
BioPET |
8001-79-4 |
933.4 |
|
|
Pre-registered |
|
|
Triacetin (glyceryl triacetate) |
PLA |
102-76-1 |
218.2 |
0.25–0.36 |
58 g L−1 at 25 °C |
Yes |
Readily biodegradable (100%) |
Non-classification |
Bis(2-ethylhexyl) adipate |
PLA |
103-23-1 |
370.6 |
8.94 at 25 °C |
3.2 μg L−1 at 22 °C |
Yes |
Readily biodegradable (100%) |
NOEC > limit of water solubility |
Biphenyl-2-ol |
BioPET |
90-43-7 |
170.21 |
3.18 at 22.5 °C |
560 μg L−1 at 20 °C |
Yes |
Readily biodegradable (100%) |
Environmental hazard chronic cat. 1 |
Flame retardants |
Ammonium polyphosphate |
BioPP, TPS, wood polymer composites; wood flour-PP composites; PP-bamboo fibre semi-biocomposites |
14728-39-3 |
|
|
|
Pre-registered |
|
|
Expandable graphite |
Wood flour-PP composites |
|
|
|
|
|
|
|
Magnesium hydroxide |
BioPP; natural fibre –PP composites |
1309-42-8 |
58.32 |
1.65 |
9 mg L−1 at 18 °C |
Yes |
|
Not classified as harmful to the aquatic environment |
Aluminum hydroxide |
Natural fibre–PP composites |
21645-51-2 |
78.004 |
|
Practically insoluble in water |
Yes |
|
Soluble aluminium salts are not classified |
Zinc borate |
BioPP; natural fibre–PP composites |
14720-55-9 |
313.8 |
|
|
Pre-registered |
|
|
Boric acid |
Natural fibre–PP composites |
10043-35-3 |
61.84 |
0.175 |
48.8–49.2 g L−1 at 20 °C |
Yes |
|
PNEC = 2.9 mg L−1 in marine water |
Antioxidants |
Gallic acid |
PLA |
149-91-7 |
170.12 |
0.7 |
11.4 g L−1 @ 20 °C |
Yes |
Readily biodegradable (100%) |
EC10 or NOEC = 1 mg L−1 for freshwater algae |
α-Tocopherol |
PLA |
59-02-9 |
430.7 |
12.2 at 25 °C |
1.3 μg L−1 at 20 °C |
Yes |
Inherently biodegradable (100%) |
PNEC = 0.003 mg L−1 in marine water |
3.2 Leaching of additives from biocomposites
Plastic additives are often physically, rather than chemically, bonded to the main polymer matrix, and under stress conditions can be released, i.e., can leach, from the plastic applications to the surrounding aqueous environment and organisms.110,111 The leaching potency of plastic additives is determined by their physical–chemical properties and by environmental conditions.110,112 Hence, leachates, i.e., additives released from the polymer matrix to the environment, with low hydrophobicity or octanol–water partition coefficient (Kow), and low molecular weight are more likely to migrate to the marine environment.113 Besides the inherent physical–chemical properties of additives, environmental conditions, such as radiation and mechanical forces, play a major role in the migration of plastic additives to the aquatic environment. To date, additives of fossil fuel-based polymers (e.g., phthalates, bisphenol A, and brominated flame retardants) have already been reported to leach to the aqueous environment and to induce harmful effects on aquatic organisms.114 Luo et al.115 characterized the number of fluorescent additives leached from new and aged polyurethane (PU). The results showed that more additives were released from the aged PU, suggesting the stimulating effect of weathering on the leaching of additives. In addition, it has been reported that the amount of leachates is positively related with the salinity and turbulence of aqueous media.115–117
A first step to assess the toxicity of leaching substances from fossil fuel-based plastic and biocomposite applications to the marine environment is to prepare environmentally relevant leachate solutions. Kocasoy et al.118 summarised a list of established standard leaching protocols (e.g., DIN 38414-S4 and Minnesota test) recommended by the European Union (EU) and United States Environmental Protection Agency (US EPA). Most of these tests are conducted in distilled water, and for short periods of time (<48 h), making them less representative for the leaching of substances that occurs in the marine environment. More environmentally relevant leaching tests under marine conditions with longer duration (>48 h) have been introduced in recent ecotoxicological studies.119,120 These studies provide a cost-effective way (e.g., not based on industrial bioreactors) of generating a large volume of leachate solution in various saltwater media which suits both ecotoxicological tests and chemical characterisation. Nevertheless, as demonstrated in Gunaalan et al.,112 these studies vary in several parameters like solid to liquid ratio, duration, hindering the comparisons in quantities of leachates (Table 2). Future work is encouraged to establish: (1) relationships between leachate concentrations and procedure parameters including solid to liquid ratios, duration and illumination; (2) guidelines to perform environmentally relevant leaching tests in the marine medium with both fossil fuel-based polymers and biocomposites.
Table 2 A summary of methods of leachate preparation in (natural & artificial) seawater from biocomposites and fossil fuel-based polymersa
Polymer category |
Polymer type |
Solid/liquid ratio (L kg−1) |
Illumination |
Duration |
Temperature (°C) |
References |
BioPET: biobased polyethylene terephthalate; PLA: polylactic acid; HDPE: high density polyethylene; LDPE: low density polyethylene; PVC: polyvinyl chloride; PS: polystyrene; PP: polypropylene; CTR: car tire rubber; PC: polycarbonate. |
Biopolymers |
PLA, BioPET, corn starch/aliphatic esters |
10 |
— |
96 h |
Room temperature |
Bejgarn et al. (2015)119 |
Fossil fuel-based polymers |
HDPE, PVC |
40–125 (HDPE); 200–8000 (PVC) |
Continuous illumination |
5 days |
22 |
Tetu et al. (2019)125 |
PET, PS, PP, PVC, CTR |
12.5 |
No |
14 days |
25 |
Capolupo et al. (2020)120 |
PET, HDPE, PVC, LDPE, PP, PS, PC |
0.5 m2 L−1 |
— |
24 h |
28 |
Li et al. (2016)128 |
PVC |
10 |
No |
24 h |
20 |
Oliviero et al. (2019)129 |
PE |
100 |
Dark |
48 |
25 |
Ke et al. (2019)130 |
PET, PE, PP, PS |
4 |
UV A + B light irradiation |
96 h |
20–30 |
Rummel et al. (2019)131 |
PP, PS, LDPE, HDPE, PVC, PET, PLA, Nylon |
10 |
— |
96 h |
Room temperature |
Bejgarn et al. (2015)119 |
3.3 Chemical characterisation of leaching substances
A wide array of organic and inorganic compounds is added to polymer matrices, and their compositions and amounts in oil- and biobased polymers vary. In most cases, the information on the exact added portions and substances is unknown, especially in commercial products and end-of-life litter items, impeding the hazardous-substance screening in the leachates from plastics and further ecotoxicological studies. Most of the reports on hazardous substances leaching to the marine environment from fossil fuel-based polymers have focused on a single substance or a group of its congeners (e.g., bisphenol A;121 phthalates;122 brominated flame retardants;123 lead chromate pigment124). In addition, few studies have performed systematic chemical-profiling of leachates to the marine environment from fossil fuel-based polymers and especially from biocomposites.119,120,125 Capolupo et al.120 successfully characterised a list of organic additives in the leachate solutions (in filtered natural seawater) of five fossil fuel-based polymers by a combination of non-target and target chemical analyses in gas chromatography-mass spectrometry (GC-MS). Additionally, these authors identified and quantified several metal elements (e.g., Pb, Zn, and Mn) using inductively coupled plasma mass spectrometry (ICP-MS). The use of the ICP-MS technique has also been applied and validated by other studies such as the work of Lithner et al.126 and Tetu et al.125
The work of Bejgarn et al.119 was the only one found to date to have performed a chemical screening of leachates from biopolymers, but no individual substances were identified. As such, there is a need to standardise procedures to systematically extract and characterise the chemical compositions of leachates from plastics to the marine environment, especially from biocomposites. The information on the dissolved leachate composition under realistic scenarios will contribute to an improved environmental risk assessment of biocomposite materials based on high quality data.
4. Ecotoxicology of microplastics and leachates from biobased materials
4.1 Ecotoxicological effects of microplastics in aquatic environments
Microplastics (MPs, <5 mm) result mainly from the degradation and fragmentation of larger units of oil- and biobased plastics, and have the potential to induce toxic effects in marine and other aquatic organisms.132 The high variability and complexity of polymers, shapes, and sizes of particles released in the environment, together with the use of exposure concentrations orders of magnitude higher than environmentally relevant ones, has limited the quality of the data to assess the risk MPs to biota.133 The ingestion of fossil fuel-based MPs can induce inhibition of digestive processes (e.g., amphipods134), cause gut abrasion and lesions (e.g., in fish135), and be retained and give a false sensation of satiation, leading to malnutrition and hunger (e.g., in mussels136). However, an increasing number of studies are reporting no effects of MPs exposure in aquatic organisms, especially at environmentally relevant concentrations. For instance, there have been reports of no impacts of MPs exposure on food consumption or growth of fish larvae,137 nor on the survival of sea urchins larvae.138 In marine amphipods, exposure to environmentally relevant concentrations of polystyrene (PS) microparticles had no effect on food consumption and growth of adult organisms.139
The variety of the reported magnitudes of the ecotoxicological effects of MPs in organisms can be due to the diversity of particle shapes and sizes, which induces differing ingestion and encounter rates by organisms, or gut retention times.140 However it can also be due to unreported experimental artefacts,141 to the lack of use of standardised ecotoxicological assessments (such as the recommended standard operational procedures from the International Organization for Standardization, ISO; The Organisation for Economic Co-operation and Development, OECD; etc.) or to exposures that exceed environmentally relevant concentrations.142 To assess the risk of MPs in the environment, there is a need to both improve the quality of ecotoxicological assessments, as well as to report the effect thresholds to identify the impact of MPs in the biota.133 Only by building up on the current knowledge will it be possible to conduct improved environmental risk assessments, especially in marine areas where MPs accumulate.132,143
The knowledge on the effects of MPs from biobased polymers is more restricted when compared to particles from fossil fuel-based polymers, and mostly limited to the ecotoxicological effects of PHB and PLA (Table 3). Up to now, there is little evidence that biobased MPs will induce significant effects in aquatic organisms, especially at environment relevant concentrations (<1 μg L−1, i.e., 0.001 mg L−1 or 1 × 109 MPs per L (ref. 142)) (Table 3). For example, in a mesocosm scenario, the bioturbation and metabolic activity of lugworms (burrowing invertebrates) in PLA exposures were not different from organisms in control treatments, while lugworms exposed to PVC decreased their activity.144 In the same study, the concentrations of microphytobenthos (diatoms) only decreased by a factor of 1.6 in higher dose exposure (2% MPs w/w sediment), in PLA treatments when compared to PVC (2.5×).144 Similarly, in a freshwater study, Straub et al.145 reported that the assimilation efficiency (digestive process) of amphipods (invertebrates) was not impaired after a 4 week exposure to PHB (32–64 μm, ca. 1 mg L−1) when compared to organisms exposed to polymethylmethacrylate (PMMA), but PHB exposure led to body mass loss in amphipods after 3 weeks. Finally, the reproduction and mortality of water fleas was impaired by PLA, but only at extremely high concentrations (EC50 = 122 mg L−1, median effective concentration, for reproduction and increase in mortality (60%) and decrease in adult body length at 500 mg L−1).146 Even though the evidence seems to point to a low toxicity of MPs derived from biobased polymers, there is, however, a large gap in the knowledge of these MPs' effects in aquatic organisms. As a consequence, this limited number of ecotoxicological reports and data does not yet allow for a valid and reliable risk assessment of biobased MPs to be performed.
Table 3 Summary of ecotoxicological assessments and reported effects of microplastics and leachates originated from biobased polymers
Ecotoxicological assessment |
Biobased polymer |
Organisms |
Exposure medium |
Exposure |
Effects |
Reference |
Microplastics |
Polylactic acid (PLA) |
Lugworms (Arenicola marina) |
Seawater |
Mesocosm: mean 235.7 (±14.8 SE) μm; 0, 0.02, 0.2 and 2% PLA MPs of wet sediment weight; 31 d |
No mortality registered |
Green et al.144 |
Biomass was not significantly different between any treatments |
Metabolic rate (O2 uptake): no difference from control treatments |
Bioturbation (production of surface casts): no difference from control treatments |
Microphytobenthos |
|
|
The biomass (concentration of microalgae at the surface of the sediment) was 1.6× lower than control treatments in exposures of 2% PLA (w/w) |
(Nutrient fluxes) |
|
|
Nutrient fluxes were not affected |
Polyhydroxy-butyrate (PHB) |
Amphipod (Gammarus fossarum) |
Freshwater |
32–64 μm; 1 mg L−1 (100 000 MPP per individual); 28 d |
Feeding rate and assimilation efficiency did not differ between treatments |
Straub et al.145 |
Weight (body mass) loss after 3 and 4 weeks of exposure to PHB: 0.36 mg (±0.52 95% CI, confidence interval) |
PLA |
Water fleas (Daphnia magna) |
Freshwater |
10, 50, 100, 500 mg L−1, <59 μm; 21 d |
Decrease in reproduction rate (EC50 = 122 mg L−1, median effective concentration). Significantly higher mortality than controls at 122 mg L−1 |
Zimmermann et al.147 |
Increase in mortality (60%) and decrease in adult body length at 500 mg L−1 |
Leachates |
PLA |
Copepod (Nitokra spinipes) |
Seawater |
Leachates obtained from materials pre- and post-treated with irradiance at 765 W m−2 for 96 h at 40 °C (weathering). Exposure for 96 h to a dilution series |
No induced toxicity |
Bejgarn et al.119 |
50% corn starch and 50% aliphatic polyester |
|
|
|
Significantly more toxic after irradiation, i.e., lower LC50 (median lethal concentration) for treatments when compared with control exposure |
|
PLA |
Bacterium (Aliivibrio fischeri) |
In vitro exposure |
Leachates obtained from the extraction of 3 g of material in methanol, after evaporation and solved in medium using dimethyl sulfoxide (DMSO). Exposure for 30 min (baseline toxicity) to a dilution series 1 : 2 (corresponding to 0.0027–7.5 mg PLA) |
Leachates from PLA significantly induced baseline toxicity |
Zimmermann et al.148 |
Cell lines (AREc32) |
|
Exposure to leachates obtained as above, for 24 h (oxidative stress) to a dilution series 1 : 2 (corresponding to 0.0027–7.5 mg PLA) |
Leachates from PLA significantly induced oxidative stress |
Yeast Estrogen Screen (YES) and the Yeast Antiandrogen Screen (YAAS) |
|
Exposure to leachates obtained as above, for 20 h (endocrine activity) to a dilution series 1 : 2 (corresponding to 0.0037–7.5 mg PLA) |
Leachates from PLA significantly induced cytotoxicity |
PLA |
Water fleas (Daphnia magna) |
Freshwater |
Leachates extracted from 122 mg L−1 of MPs in methanol (sonication, 1 h), evaporated and solved in DMSO. Exposure for 21 d |
No induced toxicity (mortality, day of first brood and number of offspring) |
Zimmermann et al.147 |
Microplastics have the potential to enhance the bioaccessibility of co-contaminants adsorbed onto the surface of particles,149 inducing extra toxicological effects in the biota. Bioaccessibility is defined as the portion of a compound released in the gastrointestinal tract and accessible for absorption.150 Once ingested, the rate of desorption of metals151 or of organic co-contaminants152 from MPs may increase. Enhanced desorption rates can be induced due to the higher ionic strength of biological fluids in the gut and to low pH conditions, corresponding to an increased bioaccessibility of substances153 and toxicity of contaminants to organisms. A model approach has shown that hydrophobic organic chemicals (HOC), sorbed to MPs, can biomagnify (increased bioaccumulation in higher trophic levels) differently in food webs in the marine environment, with PCBs having a lower potential than PAHs due to their physical–chemical characteristics.154 However, the potential bioaccumulation of HOCs induced by MPs is only relevant for diets of over 3% of MPs,154 a condition rarely met in common aquatic habitats, but that could occur in areas of higher MPs concentrations (MPs hot-spots), or in the future due to increased emissions of MPs.132 Even though there is little evidence that MPs increase the bioaccessibility of co-contaminants to organisms when compared with food items, sediments and aquatic media,153,155,156 the interaction of MPs with other toxicants sources is still not fully understood.157
Biobased MPs can differ in adsorption rates of co-contaminants when compared to fossil fuel-based MPs, but their contribution to the bioaccessability of co-contaminants to organisms is unknown. For example, chlorinated phenols adsorption to biobased MPs (PLA) is similar to PE, but lower than PP, in freshwater scenarios.158 Fipronil, a phenylpyrazole pesticide, has a significantly higher sorption rate for PLA and polybutylene succinate (PBS) when compared with PE, PP, PVC and polystyrene (PS).159 The diversity of the dynamics of sorption–desorption of co-contaminants to MPs derived from biobased polymers may play a significant role in their bioaccessibility and consequent toxicity to organisms. However, there is currently no information on whether the bioaccessibility of co-contaminants adsorbed to biobased MPs will be enhanced or reduced.
The release of leachates from the polymer matrices can be of significant importance (see Section 4) and lead to further meaningful toxicological effects in organisms, which can be chemical-led rather than particle induced. For instance, Boyle et al.160 demonstrated that PVC-MPs release lead (Pb) additives to freshwater media, which were bioavailable [the fraction of an ingested compound that is absorbed by the digestive system150] and toxic to zebrafish. In seawater, leachates from common fossil fuel-based polymers significantly enhanced toxicity to sea urchin embryos (PVC products) and clam larvae (PE plastic bags),130 while inhibiting the settlement of barnacle cyprids [higher toxicity on leachates from PVC, low-density polyethylene (LDPE) and PC].128 In the work of Bejgarn et al.,119 the only in vivo assessment of the effects of leachates from biobased plastics in a marine organism, the authors showed that PLA did not induce any toxic effects in Nitokra spinipes at tested concentrations. However, substances released from a biodegradable plastic bag (50% corn starch and 50% aliphatic polyester) showed increased toxicity after weathering processes,119 indicating that environmental stressors such as the UV irradiation (weathering) on plastic materials can play an important role in the leachates release and toxicity to organisms. In the assessment of ecotoxicological effects of leachates from biobased plastics in freshwater organisms, Zimmermann et al.161 showed that PLA leachates (extracted from a MP concentration of 122 mg L−1) did not induce any toxicity on reproduction nor in the survival of adult water fleas. However, in parallel treatments, water fleas exposed directly to MPs that did not incur any extraction procedure showed a decrease in their reproduction rate (EC50 = 122 mg L−1).161 These results indicate that particles may induce physical effects beyond chemical toxicity, even though at an order of magnitude highly exceeding environmental relevant concentrations. In an in vitro assessment from the same authors,148 leachates from PLA showed a strong baseline toxicity, similar to leachates from PVC and polyurethane (PU), but once more at concentrations exceeding expected ones in the environment. These early assessments on the toxicity of leachates from biobased plastics indicate that even though individual additives may not be considered toxic for aquatic organisms (see Section 4, Table 1), complex mixtures of additives released in the environment may induce toxicity, which may be enhanced by weathering processes of the materials. Currently the effects of leached chemicals from the matrices of biobased products on aquatic organisms are largely unknown, and this topic requires further investigation to provide high quality data for the assessment of the realistic environmental risks of biocomposites.
5. Improvement of the performance of biocomposites used in marine applications
5.1 Composites and biocomposites design and fabrication
The European directive (2008/98/EC) on waste management defines the role of the designer as fundamental to the development of a more eco-sustainable product. The load/degradation scenario of an object needs to be addressed a priori to define the structural design boundary conditions. Preliminary design can be improved by detailed numerical analysis to obtain relevant safety factors during the overall design process.61 After the design stage, the mechanical performance of biocomposite materials is dependent on manufacturing techniques. There is a need to investigate conventional and unconventional manufacturing processes to limit misalignments of the fibres, waviness, formation of voids and interfacial problems that lead to porosities and fibre/matrix debonding. A systematic tuning of the manufacturing parameters should always be considered, knowing that mechanical properties can drop very quickly due to flaws and void content.162 For example, a 1% voids inclusion within conventional composites can reduce tensile, flexural and interlaminar shear strengths by 10 to 20%. The following section aims to highlight the latest advances in the fabrication of biocomposites for marine applications. In particular, some aspects related to design, surface coatings, material treatments, and alternative manufacturing processes are highlighted for future biocomposites development.
5.2 Design considerations
Both engineering and nature are adept at creating functional components, sometimes achieving the same result in terms of mechanical properties, but adopting different design strategies. Biological composites and usual engineering materials can be grouped together under the concept of architectured materials.163 From an engineering point of view an architectured material is an object, made of organised matter that responds to external stimuli to perform certain functions. The way in which material is organised and combined with other materials provides their functions and effectiveness. It is up to scientists, whether they are chemists, mechanical, electrical or process engineers to cooperate to develop new structural designs and improvements of biocomposites through micro- and macro-structures. The majority of so called ‘semi-green’ or ‘green’ composites have maximum tensile strengths and stiffness in the ranges of 100–200 MPa and 1–4 GPa,164 restricting their use for primary, load-bearing components. One way to overcome lower performance is to use designs based on the repetition of a unit cell (or scaffolds) of known geometry and properties. In this way the properties of the resulting materials can be measured according to different boundary conditions, then compared to finite element methods (FEM) and predictive modelling since properties of the unit cell are known a priori.165 In addition, investigation to compare manufactured structures and designed counterparts gives reliable feedback to be included in the iterative process of custom scaffold design. Despite different systematic theoretical and experimental attempts described in the literature, many procedural conflicts remain. In general, geometrical key-features and parameters can be gauged from biology thanks to medical imaging or microscopy, then processed, often modelled and replicated in a Computer Aided Design (CAD) environment (Fig. 12).
 |
| Fig. 12 Workflow approach to manufacturing bioinspired structures. | |
Current manufacturing approaches are lacking in terms of both CAD design and manufacturing strategies needed for hybrid replication. Technology is consequently missing out on many advantages of bioinspiration because of both big data handling and the absence of material manufacturing control at the small scales. The CAD has evolved to generative design (GD),166–168 where specific elements and algorithms are provided to tune geometries that can be oriented to different purposes. The GD can be defined as a form-finding process, meant to produce a wide range of solutions, from a few to thousands, depending on the level of complexity of the object and the controlled parameters that define the geometrical entity. Algorithms can be written starting from an ideal case and formalised in codes. The computed process is able to follow the rules in input and shapes can be visualised by the user. If the output is in accordance with the ideal case, the next step is to choose an appropriate manufacturing process to make the parts. For example, one tool for computer aided industrial design (CAID) called Rhinoceros™ (McNeal, Seattle, WA, USA) is providing means and plugins to widen free form modelling, regardless of any level of shape size and complexity. The GD is a conceptual, dynamic, iterative and fluent way of shaping objects. Object dimensions can be set within the 3D environment in order to design at sub-micron length scales as well as above the meter scale. In this sense, limits related to the adopted manufacturing technology are boundary conditions necessary for the production of a bioinspired functional material. Structure provides the framework for the distribution of materials and is demonstrated here across a range of length scales (Fig. 13).
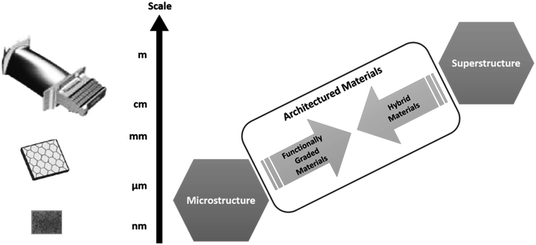 |
| Fig. 13 Schematic showing the relationship between multiple length scales, the potential for functional grading and the use of multiple materials to produce hybrid materials (adapted from Wainwright et al.169). | |
5.3 Manufacturing processes and important parameters
Challenges that need to be addressed in the coming years include making technologies economically viable for production of biobased monomers and biobased polymers from renewable sources. It is very important to develop new manufacturing routes by replacing existing methods to reach high performing composites as well as approaching length scales not accessible to conventional manufacturing techniques. Biocomposite material selection implies a prior study of the mechanical properties of the composite constituents, chemical resistance, dimensional stability and suitable manufacturing process. Moreover, the different nature of constituents decides the end-of-life recycling of the final composites and the ability to be recyclable or biodegradable. Benefits over synthetic fibres such as low manufacturing energy consumption, low carbon footprint and biodegradability are an evidence of natural fibres being much less cost effective due to low energy to production costs when compared to traditional reinforcing fibres such as glass and carbon.170 Technological developments and manufacturing strategies are very case-specific, strictly related to mechanical needs and economic convenience. Among the disadvantages associated with the use of natural fibres within biocomposites, poor moisture resistance, limited processing temperatures, lower durability, variation in quality and price, reduce the chance to use established manufacturing processes.78,171 Moisture is crucial when fabricating biocomposites; the low processability of biocomposites results in poor mechanical performance composites absorbing water depending on processing temperature, fibre volume fraction, orientation of reinforcement, permeability nature of fibre, area of exposed surfaces, diffusivity, reaction between water and matrix and surface protection.46 Among the conventional techniques for the production of biocomposites parts, stratification, hand lay-up and vacuum bagging methods are the most popular.172 Composite materials can be made of layers fabricated with a thickness between 0.1 and 0.5 mm when laminated but even thicker when it comes to low cost applications.173–175 Moreover, laminate composites perform better when fibres are oriented according to a main loading direction. Multidirectional loading conditions require stratification manufacturing techniques that vary the distribution/direction of the reinforcement, layer by layer. Long-fibre laminate composites show superior mechanical performances, but the ease of processability of short and fragmented fibres composites is more convenient thanks to automated workflows that even contemplate material reuse. Of all the fabrication methods, the hand lay-up laminating is probably the earliest technique employed in the production of composite materials, particularly in the marine industry. This technique allows for the production of solid laminates and sandwich composite structures. It is well suited to the production of large parts such as boat hulls. Reinforcement fibres are laid on a mould where a resin is then poured and squeezed with a roller to remove trapped air. A vacuum effect is necessary before the catalyst is activated to harden the resin and reinforcement into the final composite. Lastly, lamination pressurizing and vacuum bagging methods can be applied during the curing stage to further remove the air interlayer, increasing interfacial stress transfer thanks to an optimized fibre-to-resin ratio in the composite part.176 The application of nanotechnology has been introduced in some research areas and has further potential to improve the behaviour of biocomposites. The use of nanoscale fillers such as inorganic pigments,177 minerals,178 ceramics,179 nanocellulose180 and nanoclays181 were recently considered in the production of composite coatings for paper. Moreover, antimicrobial paper,182 and self-healing properties for cotton fabric183 are desirable properties that would be of interest for the case of biocomposite material manufacturing. In the specific case of the manufacturing process of sustainable biocomposites the available technologies are listed as follow: spray-up process, filament winding, pultrusion process, compression moulding, resin transfer moulding, pre-preggers, compounding and extrusion and injection moulding processes. Resin winding and pultrusion are interesting processes that use filaments of uninterrupted fibres. Resin winding blends together the reinforcement thanks to a bath of resin into which fibres are continuously fed at varying speed or twisting angle. The pultrusion method is preferred in the fabrication of continuous, constant cross-section products, especially for the high productive nature of the process. Compression moulding forms composites made of dry fibres and resins applying high pressure in rigid moulds placed in hydraulic presses, whereas resin transfer moulding is a process more related to cold pressing.184 Pre-pregs are compounds made of fibre, resin, fillers and catalyst produced in sheet or dough for sheet moulding and dough moulding compound respectively. The former forms the final product via compression moulding, whereas the dough can also be injected before the catalyst is activated by heat.185 Compounding and extrusion are processes widely used with varieties of materials such as blend fibre composites that can be extruded into pellets for injection moulding. Finally, injection moulding forces the preheated composite into closed moulds to be cooled and removed after solidification of the part.186
Three-dimensional 3DP printing, also known as Additive Manufacturing (AM), is also currently offering a wide range of different materials solutions. Polymers, ceramics, organics and reinforced biobased materials can be extruded, cured, bound and sintered from micro- to meter-scale. Advantages are currently under evaluation aiming at understanding technology drawbacks and possible improvements and developments.187–189 However, virtual 3D geometries with almost arbitrary shape and complexity, can be produced adding material where needed.190 On the biocomposite side, multi-material printers are fostering additive processes for their ability to combine different materials with transfer of interfacial activation mechanisms from biological to engineering composites. Furthermore, advanced manufacturing can rely on Computed Aided Design (CAD) coupled to algorithm modelling and imaging technologies to exploit the complexities enabled by 3DP using multiple materials. Algorithm modelling and 3DP are now providing the possibility to create complex topologies with resolutions approaching several length scales.191–194 Several kinds of 3D printing process exist, but most can be placed into one of three distinct categories.195,196 First, there are printers that form object layers extruding a semi-liquid material from a computer-controlled print head nozzle. Secondly, there are printers that use photo polymerisation to selectively solidify a liquid with a laser beam or light source. And finally, there are devices that 3D print by adhering particles of powder to achieve some form of granular materials binding. Direct tools allow the creation of architectural forms taking advantage of the intuitive interaction between user and 3D modeller. Freedom in designing complex shapes is gained, possibly made of multiple parts leading to the manufacturing of multi-material assemblies. Therefore control can be reached not only on the hierarchical disposition of materials, but also on their chemical and physical functionality.196,197
5.4 Surface treatments and coatings
So far, the use of biobased composites has been restricted to interior and moderate loading applications. The poor outdoor resistance of the natural fibres, especially in wet conditions, implies the need of developing coatings, surface treatments and additives to reduce the tendency of the composite to absorb moisture over time. Moreover, the matrix/reinforcement system is based on a mechanical interplay that, for the case of biobased composites, weakens due to the opposing nature of hydrophilic matrix and hydrophobic reinforcement.198 Therefore, surface treatments can be crucial in the attempt to preserve mechanical properties, especially in a marine environment where major concerns are related to biocomposites long-term durability and life time prediction.199 Within two years, the tensile strength of jute/phenolic composites can be reduced by 50% in outdoor conditions. Fibre/polyester composites suffer less from weathering effects, with a strength loss that can vary between 5-25% and more in water conditions.200,201 Moreover, structural properties of biobased materials can be affected by fungus and bacteria development. Humid conditions facilitate the formation of fungus after a few days of moisture exposure, as observed in the case of flax fibres that improved their environmental durability with the application of Duralin. Duralin flax fibres show reduced moisture uptake thanks to the process that transforms lignin and hemicellulose into lower molecular weight compounds to be cured into water resistant resins.202 In contrast with flax, which falls into the steam fibres category together with hemp and jute, leaf fibres like abaca and sisal demonstrate better suitability in seawater applications. Sisal fibres perform very well in addition to glyoxal phenolic resins to form thermosets that with 30% of reinforcement by weight improved the impact strength of one order of magnitude with respect to the glyoxal-phenolic matrix. Degradation mechanisms must be avoided at different length scales and dedicated surface modifications can be listed depending on the approached scale level. A hierarchical classification of possible surface treatments would help in the selection of appropriate procedural steps to transform raw materials into superior performance composites. On one hand surface treatments can be applied at system level with the help of coatings or barriers against wettability. Inspiration can be taken from the delicate case of paper, an excellent biobased material that requires control over its intrinsic hydrophilicity and porosity in order to preserve shape and mechanical function during the product lifetime. Nowadays, paper coatings are mainly fossil-oil based as in the case of polyolefins (polyethylene), waxes, ethylene vinyl alcohol, polyvinylidene chloride that provide a significant barrier against water and oxygen permeability. Examples of biopolymer films and biobased coating substitutes can be found in the literature such as polysaccharides (starch and cellulose derivatives, chitosan, and alginates), proteins (casein, whey, collagen, soya, and gluten), lipids (bees and carnauba wax, and free fatty acids) and polyesters PHA and PLA.203,204 Bioinspired solutions can be achieved by adopting superhydrophobic PPS/PTFE composite coatings which have attracted research interest for their high interfacial strength, excellent impact resistance and high thermal stability205 However, the surface morphology characterisation by SEM showed that these superhydrophobic coatings have similar macro–nano-structures to that of lotus leaf, hence classifiable as biologically inspired. Another way of approaching this problem is using a melting-blend process to produce biodegradable composite films, commonly used in the packaging engineering field. Hybrid composites made of traditional polymer matrix (PP), biodegradable polymers (PLA) and nanofillers (NANO-TiO2) were manufactured to promote biocomposite resistance to both UV light and water penetration. It has been shown that maleic anhydride (MHA) increases the interfacial compatibility between PP and PLA, showing increased crystallinity and thermal properties. Critically, PP/PLA/MHA film composites show increased tensile strength and elastic modulus by 100% and 140% respectively, when compared to PP/PLA based films. A 1% wt concentration of NANO-TiO2 allowed a UV transmittance that is almost zero in the PP/PLA/MHA composite. Although this approach was intended for packaging engineering, similar solutions can be transferred to other applications such as marine structures.82 At a lower level, modifying the fibre surface for a better compatibility and consequential adhesion with the matrix is preferred. Chemical treatments such as alkalization, bleaching and silanes are promising techniques that would allow improved mechanical transverse strength and stiffness of biocomposites.206–208 Alkali treatments aim to increase the contact area at the interface between fibre surface and polymeric matrix. Chemical treatments such as this rely on the induced interlocking mechanisms due to a rougher, but bondable fibre surface. Surface treatments can act at molecular level developing an intermediate region between fibres and matrix. The intermediate elastic modulus of this third phase gradually varies so that a toughening mechanism takes place on the basis of an improved interplay between matrix and fibres. Limited studies have investigated the chemical bridges formed when using silanes as a compatibiliser. The matrix/fibres bonding of resin-based composites is at risk during the curing process of the resin or when heat is applied while manufacturing the composite. Moisture would eventually reach the surfaces of the fibres leading to the formation of voids when it evaporates.209 However, natural fibres cannot withstand high temperatures, with 180–200 °C a limit above which mechanical properties loss is guaranteed.
6. Conclusions and future perspectives
6.1 Perspectives and foreseen challenges of biocomposites for marine environments
Biobased polymers and composites are new classes of lightweight sustainable materials suitable for use in marine, automotive, aerospace and other lightweight applications. In terms of their specific application in the marine sector, understanding their long-term durability under harsh marine environments needs to be fully analysed and appropriate methods need to be developed to improve their service conditions. Reducing the environmental burden caused by the use of non-sustainable composite materials in marine sector is an emerging issue. The development and use of sustainable biobased composites as a replacement for non-renewable conventional fibres reinforced glass and carbon fibre composites offers a viable materials alternative with low cost, sustainable and recyclability attributes.
However, it is important to recognise that these sustainable biobased composites also present challenges including that of meeting the functional requirements, understanding environmental ageing behaviour relating to long term weathering performance and their ecotoxicology aspects. The real risk of biobased polymers to biota is largely unknown and there is a need to test effects of both leachates and derived MPs according to internationally standardised ecotoxicity protocols.
The properties of biobased sustainable composites can be enhanced to meet the functional requirements by using various techniques and by optimising numerous process parameters. It is expected that using biobased polymers and composite materials in marine applications will reduce environmental impact, including fewer leaching substances to the marine environment, limiting damage to marine life and to the eventual reduction of our overall carbon footprint.
6.2 Perspectives on the ecotoxicology of microplastics and leachates from biobased materials
Microplastics and leachates resulting from the degradation and fragmentation of biobased plastics have the potential to induce toxic effects in aquatic organisms, but currently there is little evidence to establish their toxicity in the environment.
The number of ecotoxicological data points of biobased MPs is substantially lower than for fossil fuel-based polymer materials, and limited to a restricted number of organisms (Table 3). In the case of leachate effects, the number of studies is even lower, and to date there are very few in vivo ecotoxicological assessments (Table 3). Furthermore, there is currently no information on the bioaccessibility and bioavailability to organisms of co-contaminants sorbed to biopolymer MPs. High quality ecotoxicological assessments are needed to evaluate whether biobased materials can provide a sustainable alternative to fossil fuel-based applications. To enable a correct risk assessment of biobased materials in marine and other aquatic environments, there is a need to (1) increase the number of ecotoxicological assessments with a variety of organisms and life stages, for representativity; (2) guarantee that exposures be performed using robust concentration-relationships, to include environmentally relevant scenarios and generate data suitable to calculate effect thresholds, and (3) run exposures using high quality methodologies based on internationally validated standard operating procedures, for comparability and reliability. Only high-quality studies will provide reliable data to inform the public, industry and policymakers on the development and implementation of more sustainable and safe solutions using biobased composites.
Over the past decade, the use of sustainable materials derived from sustainable resources in the marine sector has attracted significant interest. However, despite the many attractive features that sustainable polymers and composites offer, resolving their shortcomings can be a test. For instance, these include low long-term durability subjected to harsh outdoor environments (temperature, seawater ageing, mechanical stresses, UV radiation) and inferior mechanical performance in comparison to established glass fibre composites that are currently widely used in marine applications. Moreover, dealing with the end of their life cycle and establishing a reliable supply chain remain key challenges for these composites before they are more widely used in the marine sector.
The marine sector has shown a growing interest in the use of sustainable biobased composites. The prospect of continued development and the use of biobased polymers and composites with environmental credentials presents a possible solution to replace materials with a high carbon footprint. To realise the full potential of this new class of sustainable materials for marine applications, an understanding of their design, process parameters, material structures and long term-durability relationships is crucial. More importantly, understanding the durability and degradation mechanisms involving moisture ingress and various chemical interactions of biobased polymers and composites exposed to marine environments is crucial.
Abbreviations
UV | Ultraviolet |
PHBV | Poly(3-hydroxybutyrate-co-3-hydroxyvalerate) |
SEM | Scanning electron microscopy |
PLA | Polylactide |
PLLA | Poly-L-lactide |
PHBV | Poly(3-hydroxybutyrate-co-3-hydroxyvalerate) |
RH | Relative humidity |
UP | Unsaturated polyester |
FVE | Flax/vinyl ester |
FBVEs | Flax/vinyl ester stitched |
FBVEu | Flax basalt vinyl ester unstitched |
Flax/UD | Flax unidirectional |
Flax/CP | Flax cross-ply |
TGA | Thermo-gravimetric analysis |
DSC | Differential scanning calorimetry |
FTIR | Fourier-transform infrared spectroscopy |
GPC | Gel permeation chromatography |
REACH | Registration, evaluation, authorization and restriction |
PHB | Poly(3-hydroxybutyrate) |
BHA | Butylated hydroxyanisole |
BHT | Butylated hydroxytoluene |
Kow | Octanol–water partition coefficient |
PU | Polyurethane |
EU | European Union |
US EPA | United States Environmental Protection Agency |
GC-MS | Gas chromatography-mass spectrometry |
ICP-MS | Plasma mass spectrometry |
BIOPP | Biobased polypropylene |
TPS | Thermoplastic starch |
BioPET | Biobased polyethylene terephthalate |
PVA | Poly vinyl alcohol |
HDPE | High density polyethylene |
LDPE | Low density polyethylene |
PVC | Polyvinyl chloride |
PS | Polystyrene |
PP | Polypropylene |
CTR | Car tire rubber |
PC | Polycarbonate |
MPs | Microplastics |
ISO | International Organization for Standardization |
OECD | The Organisation for Economic Co-operation and Development |
PMMA | Polymethylmethacrylate |
EC | Effective concentration |
HOC | Hydrophobic organic chemicals |
PBS | Polybutylene succinate |
LDPE | Low-density polyethylene |
PU | Polyurethane |
FEM | Finite element methods |
CAD | Computer aided design |
GD | Generative design |
CAID | Computer aided industrial design |
3DP | Three-dimensional printing |
AM | Additive manufacturing |
CAD | Computed aided design |
NANO-TiO2 | Nanofillers |
Funding
This work was conducted within the SeaBioComp project, which has received funding from Interreg 2 Seas Mers Zeeën program 2014–2020 co-funded by the European Regional Development Fund under subsidy contract No. 2S06-006.
Conflicts of interest
The authors declare that they have no known competing financial interests or personal relationships that could have appeared to influence the work presented in this review paper.
References
- R. J. Hofmann, M. Vlatkovic and F. Wiesbrock, Polymers, 2017, 9, 534 CrossRef PubMed.
- N. Sazali, H. Ibrahim, A. S. Jamaludin, M. A. Mohamed, W. N. W. Salleh and M. N. Z. Abidin, IOP Conf. Ser.: Mater. Sci. Eng., 2020, 788, 012047 CrossRef CAS.
- S. Walker and R. Rothman, J. Cleaner Prod., 2020, 261, 121158 CrossRef CAS.
- D. M. Whitacre, Occurrence, Degradation, and Effect of Polymer-Based Materials in the Environment, 2014, vol. 227 Search PubMed.
- S. A. for P. by E. A. SAPEA, SAPEA, A Scientific Perspective on Microplastics in Nature and Society, Berlin, 2019 Search PubMed.
- G. Everaert, M. De Rijcke, B. Lonneville, C. R. Janssen, T. Backhaus, J. Mees, E. van Sebille, A. A. Koelmans, A. I. Catarino and M. B. Vandegehuchte, Environ. Pollut., 2020, 267, 115499 CrossRef CAS PubMed.
- L. Zhao and Y. Yin, Proc. Int. Offshore Polar Eng. Conf., 2018, 27–34 Search PubMed.
- A. G. S. Morton, Marine Corrosion, Elsevier Ltd., 1982 Search PubMed.
- T. A. Hottle, M. M. Bilec and A. E. Landis, Resour., Conserv. Recycl., 2017, 122, 295–306 CrossRef.
- H.-y. Cheung, M.-p. Ho, K.-t. Lau, F. Cardona and D. Hui, Composites, Part B, 2009, 40, 655–663 CrossRef.
- T. Gurunathan, S. Mohanty and S. K. Nayak, Composites, Part A, 2015, 77, 1–25 CrossRef CAS.
- S. B. Roy, D. S. C. Shit, D. R. A. Sen Gupta and D. P. R. Shukla, Int. J. Innov. Res. Sci. Eng. Technol., 2014, 03, 16814–16824 CrossRef.
- O. Akampumuza, P. M. Wambua, A. Ahmed, W. Li and X. H. Qin, Polym. Compos., 2017, 38, 2553–2569 CrossRef CAS.
- K. N. Bharath and S. Basavarajappa, Sci. Eng. Compos. Mater., 2016, 23, 123–133 Search PubMed.
- A. Siriruk and D. Penumadu, Effect of Sea Water on Polymeric Marine Composites, Solid Mechanics and Its Applications, in Durability of Composites in a Marine Environment, ed. P. Davies and Y. Rajapakse, Springer, Dordrecht, 2014, vol. 208 Search PubMed.
- P. Davies and Y. D. S. Rajapakse, Solid Mech. Its Appl., 2017, E1 Search PubMed.
- T. Hofstatter, D. B. Pedersen, G. Tosello and H. N. Hansen, Challenges and opportunities of fibre-reinforced polymers in additive manufacturing with focus on industrial applications, in Proceedings of the Joint Special Interest Group meeting between euspen and ASPE: Dimensional Accuracy and Surface Finish in Additive Manufacturing., The European Society for Precision Engineering and Nanotechnology, euspen and ASPE Special Interest Group Meeting: Additive Manufacturing, Leuven, Belgium, 2017 Search PubMed.
- J. Graham-Jones and J. Summerscales, Mar. Appl. Adv. Fibre-Reinforced Compos., 2016, 1–15 CAS.
- R. Pemberton, J. Summerscales and J. Graham-Jones, Mar. Compos., 2019, xvii–xxi Search PubMed.
- E. V. Creamer, Splash Zone Protection of Marine Structures, Paper presented at the, Offshore Technology Conference, April 1970 Search PubMed.
- H. N. Dhakal, Z. Y. Zhang and M. O. W. Richardson, Compos. Sci. Technol., 2007, 67, 1674–1683 CrossRef CAS.
- A. Moudood, A. Rahman, A. Öchsner, M. Islam and G. Francucci, J. Reinf. Plast. Compos., 2018, 38, 323–339 CrossRef.
- ASTM International, Z. N. Azwa, B. F. Yousif, A. C. Manalo, W. Karunasena, H. Lintsen, F. Veraart, J. P. Smits, J. Grin, L. Shen, J. Haufe, M. K. Patel, F. Gironi, V. Piemonte, European Bioplastics, W. F. Spencer, M. M. Cliath, M. van den Oever, K. Molenveld, M. van der Zee, H. Bos, E. T. H. Vink, D. A. Glassner, J. J. Kolstad, R. J. Wooley, R. P. O'Connor, A. Kormut’ák, V. Čamek, M. Branná, M. Čelková, B. Vooková, P. Maňka, M. Galgóci, P. Boleček, D. Gömöry, J. Manyika, M. Chui, J. Bughin, S. Project and P. Number, Folia Oecologica, 2013, 3, 424–442 Search PubMed.
- M. Deroiné, A. Le Duigou, Y.-M. Corre, P.-Y. Le Gac, P. Davies, G. César and S. Bruzaud, Polym. Test., 2014, 39, 70–78 CrossRef.
- C. Baley, M. Gomina, J. Breard, A. Bourmaud and P. Davies, Ind. Crops Prod., 2020, 145, 111984 CrossRef CAS.
- A. S. Virk, W. Hall and J. Summerscales, Compos. Sci. Technol., 2010, 70, 995–999 CrossRef CAS.
- G. Cicala, G. Cristaldi, G. Recca and A. Latteri, Woven Fabr. Eng., 2010, 317–342 Search PubMed.
- Y. Li, Y.-W. Mai and L. Ye, Compos. Sci. Technol., 2000, 60, 2037–2055 CrossRef CAS.
- D. Zhang, N. R. Milanovic, Y. Zhang, F. Su and M. Miao, Composites, Part B, 2014, 60, 186–192 CrossRef CAS.
- A. Le Duigou, P. Davies and C. Baley, Composites, Part A, 2013, 48, 121–128 CrossRef CAS.
- A. Espert, F. Vilaplana and S. Karlsson, Composites, Part A, 2004, 35, 1267–1276 CrossRef.
- M. M. Thwe and K. Liao, J. Mater. Sci., 2003, 38, 363–376 CrossRef CAS.
- J. D. Badia, T. Kittikorn, E. Strömberg, L. Santonja-Blasco, A. Martínez-Felipe, A. Ribes-Greus, M. Ek and S. Karlsson, Polym. Degrad. Stab., 2014, 108, 166–174 CrossRef CAS.
- I. Papa, A. Formisano, V. Lopresto, F. Cimino, L. Vitiello and P. Russo, J. Compos. Mater., 2020, 54, 3481–3489 CrossRef CAS.
- N. Sgriccia, M. C. Hawley and M. Misra, Composites, Part A, 2008, 39, 1632–1637 CrossRef.
- A. Le Duigou, A. Bourmaud, P. Davies and C. Baley, Ocean Eng., 2014, 90, 140–148 CrossRef.
- S. Dixit and P. Verma, Adv. Appl. Sci. Res., 2012, 3(3), 1463–1465 CAS.
- S. Sethi and B. C. Ray, Adv. Colloid Interface Sci., 2015, 217, 43–67 CrossRef CAS PubMed.
- M. Deroiné, A. Le Duigou, Y.-M. Corre, P.-Y. Le Gac, P. Davies, G. César and S. Bruzaud, Polym. Degrad. Stab., 2014, 108, 319–329 CrossRef.
- A. Célino, S. Fréour, F. Jacquemin and P. Casari, J. Appl. Polym. Sci., 2013, 130, 297–306 CrossRef.
- S. Réquilé, A. Le Duigou, A. Bourmaud and C. Baley, Composites, Part A, 2019, 123, 278–285 CrossRef.
- A. Le Duigou, P. Davies and C. Baley, Polym. Degrad. Stab., 2009, 94, 1151–1162 CrossRef CAS.
- A. P. P. Fulco, A. M. de Medeiros, M. L. P. Tonatto, S. C. Amico, R. Talreja and J. D. D. Melo, Composites, Part A, 2019, 127, 105628 CrossRef CAS.
- P. Davies and D. Choqueuse, Ageing Compos., 2008, 326–353 CAS.
- J. L. Thomason, Composites, 1995, 26, 477–485 CrossRef CAS.
- P. V. Joseph, M. S. Rabello, L. H. C. Mattoso, K. Joseph and S. Thomas, Compos. Sci. Technol., 2002, 62, 1357–1372 CrossRef CAS.
- K. Joseph, S. Thomas and C. Pavithran, Polymer, 1996, 37, 5139–5149 CrossRef CAS.
- R. Joffe, J. Andersons and L. Wallström, Composites, Part A, 2003, 34, 603–612 CrossRef.
- J. Summerscales and S. Grove, Nat. Fibre Compos., 2014, 176–215 CAS.
- C. Baley, A. Le Duigou, A. Bourmaud and P. Davies, Composites, Part A, 2012, 43, 1226–1233 CrossRef CAS.
- K. Van de Velde and P. Kiekens, Compos. Struct., 2003, 62, 443–448 CrossRef.
- H. L. Bos, J. Müssig and M. J. A. van den Oever, Composites, Part A, 2006, 37, 1591–1604 CrossRef.
- H. L. Frisch, J. Appl. Polym. Sci., 1970, 14, 1657 CrossRef.
- C. Yang, X. Xing, Z. Li and S. Zhang, Polymers, 2020, 12, 138 CrossRef CAS PubMed.
- H. M. Karandikar, W. J. Ward, C. Kostas and D. P. Tate, Proc. 1998 IEEE Int. Symp. Electron. Environ. ISEE - 1998 (Cat. No. 98CH36145), 1998 Search PubMed.
- Y. Perrot, C. Baley, Y. Grohens and P. Davies, Appl. Compos. Mater., 2007, 14, 67–87 CrossRef CAS.
- T. La May, Flaxland, Gustave-Alexandre, Oxford University Press, 2001 Search PubMed.
- R. de Heer, PsycEXTRA Dataset, 2009 Search PubMed.
- Racing yacht construction part-replaces carbon fibre with flax, 2010, October 1, The Free Library (2010), Retrieved September 23, 2021 from https://www.thefreelibrary.com/Racing yacht construction part-replaces carbon fibre with flax.-a0241962411 Search PubMed.
- Multihullnews.com, OutremerRoland and Jourdain launch a flax fibre catamaran. Retrieved June 14, 2021 from https://www.boatsnews.com/story/37282/outremer-and-roland-jourdain-launch-a-flax-fibre-catamaran.
- S. Castegnaro, C. Gomiero, C. Battisti, M. Poli, M. Basile, P. Barucco, U. Pizzarello, M. Quaresimin and A. Lazzaretto, Ocean Eng., 2017, 133, 142–150 CrossRef.
- B. P. Chang, A. K. Mohanty and M. Misra, RSC Adv., 2020, 10, 17955–17999 RSC.
- A. K. Barouni and H. N. Dhakal, Compos. Struct., 2019, 226, 111224 CrossRef.
- F. A. Almansour, H. N. Dhakal and Z. Y. Zhang, Compos. Sci. Technol., 2018, 154, 117–127 CrossRef CAS.
- H. N. Dhakal, Z. Y. Zhang, R. Guthrie, J. MacMullen and N. Bennett, Carbohydr. Polym., 2013, 96, 1–8 CrossRef CAS PubMed.
- D. Scida, M. Assarar, C. Poilâne and R. Ayad, Composites, Part B, 2013, 48, 51–58 CrossRef CAS.
- A. Paturel and H. N. Dhakal, Molecules, 2020, 25, 1–16 CrossRef PubMed.
- A. Chilali, M. Assarar, W. Zouari, H. Kebir and R. Ayad, Composites, Part A, 2017, 95, 75–86 CrossRef CAS.
- D. K. Shen and S. Gu, Bioresour. Technol., 2010, 101, 6879 CrossRef CAS.
- J. George, E. T. J. Klompen and T. Peijs, Adv. Compos. Lett., 2001, 10, 096369350101000 CrossRef.
- J. Gassan and A. K. Bledzki, J. Appl. Polym. Sci., 2001, 82, 1417–1422 CrossRef CAS.
- J. Chaishome, K. A. Brown, R. Brooks and M. J. Clifford, Adv. Mater. Res., 2014, 894, 32–36 Search PubMed.
- N. Peelman, P. Ragaert, K. Ragaert, B. De Meulenaer, F. Devlieghere and L. Cardon, J. Appl. Polym. Sci., 2015, 132, 42305–42320 CrossRef.
- A. Le Duigou, J. M. Deux, P. Davies and C. Baley, Int. J. Polym. Sci., 2011, 2011, 1–8 CrossRef.
- H. M. Khanlou, P. Woodfield, J. Summerscales, G. Francucci, B. King, S. Talebian, J. Foroughi and W. Hall, Measurement, 2018, 116, 367–372 CrossRef.
- L. Van Schoors, M. Gueguen Minerbe, S. Moscardelli, H. Rabii and P. Davies, Ind. Crops Prod., 2018, 126, 333–339 CrossRef CAS.
- D. Brosius, Compos. Technol., 2006, 12, 32–37 Search PubMed.
- D. B. Dittenber and H. V. S. Gangarao, Composites, Part A, 2012, 43, 1419–1429 CrossRef.
- Y. Xie, C. A. S. Hill, Z. Xiao, H. Militz and C. Mai, Composites, Part A, 2010, 41, 806–819 CrossRef.
- Y. F. Shih, Mater. Sci. Eng., A, 2007, 445–446, 289–295 CrossRef.
- H. Chen, M. Miao and X. Ding, Composites, Part A, 2009, 40, 2013–2019 CrossRef.
- Q. Jiang, X. Pei, L. Wu, T. T. Li and J. H. Lin, Adv. Polym. Technol., 2018, 37, 2971–2980 CrossRef CAS.
- Q. T. H. Shubhra, A. K. M. M. Alam, M. A. Khan, M. Saha, D. Saha and M. A. Gafur, Composites, Part A, 2010, 41, 1587–1596 CrossRef.
- M. D. H. Beg and K. L. Pickering, Polym. Degrad. Stab., 2008, 93, 1939–1946 CrossRef CAS.
- L. M. Matuana, S. Jin and N. M. Stark, Polym. Degrad. Stab., 2011, 96, 97–106 CrossRef CAS.
- J. S. Fabiyi, A. G. McDonald, M. P. Wolcott and P. R. Griffiths, Polym. Degrad. Stab., 2008, 93, 1405–1414 CrossRef CAS.
- E. W. Tollner, P. A. Annis and K. C. Das, J. Environ. Eng., 2011, 137, 291–296 CrossRef CAS.
- B. Tansel and B. S. Yildiz, Environ. Dev. Sustain., 2011, 13, 821–831 CrossRef.
- M. Bläsing and W. Amelung, Sci. Total Environ., 2018, 612, 422–435 CrossRef PubMed.
- N. B. Vogt and E. A. Kleppe, Polym. Degrad. Stab., 2009, 94, 659–663 CrossRef CAS.
- C. L. Chen, Regulation and management of marine litter, 2015 Search PubMed.
- A. L. Andrady, Mar. Pollut. Bull., 2011, 62, 1596–1605 CrossRef CAS PubMed.
- A. Campos, J. M. Marconcini, S. M. Martins-Franchetti and L. H. C. Mattoso, Polym. Degrad. Stab., 2012, 97, 1948–1955 CrossRef CAS.
- M. R. Y. Hamid, M. H. Ab Ghani and S. Ahmad, Ind.
Crops Prod., 2012, 40, 96–102 CrossRef CAS.
- I. Jakubowicz, N. Yarahmadi and V. Arthurson, Polym. Degrad. Stab., 2011, 96, 919–928 CrossRef CAS.
- L. Contat-Rodrigo, Polym. Degrad. Stab., 2013, 98, 2117–2124 CrossRef CAS.
- A. Corti, M. Sudhakar and E. Chiellini, J. Polym. Environ., 2012, 20, 1007–1018 CrossRef CAS.
- O. Yashchuk, F. S. Portillo and E. B. Hermida, Procedia Mater. Sci., 2012, 1, 439–445 CrossRef CAS.
- OECD, OECD Environ. Heal. Saf. Publ. Ser. Emiss. Scenar. Doc. No. 3 Emiss., 2009, pp. 1–141 Search PubMed.
- E. Hansen, N. H. Nilsson, D. Lithner and C. Lassen, Hazard. Subst. Plast. Mater., 2013, 148 Search PubMed.
- ECHA, Plastic additives initiative - Supplementary Information on Scope and Methods, 2019, vol. 20 Search PubMed.
- Z. Kulinski and E. Piorkowska, Polymer, 2005, 46, 10290–10300 CrossRef CAS.
- P. Bordes, E. Pollet, L. Avérous, Prog. Polym. Sci., 2009, 34, 125–155 Search PubMed.
- L. E. A. Vieira, S. K. Solanki, N. A. Krivova and I. Usoskin, Astron. Astrophys., 2011, 531(A6), 20 Search PubMed.
- Y. Byun, Y. T. Kim and S. Whiteside, J. Food Eng., 2010, 100, 239–244 CrossRef CAS.
- P. Kulawik, F. Özogul, R. Glew and Y. Özogul, J. Agric. Food Chem., 2013, 61, 475–491 CrossRef CAS PubMed.
- M. Sain, S. H. Park, F. Suhara and S. Law, Polym. Degrad. Stab., 2004, 83, 363–367 CrossRef CAS.
- E. N. Kalali, L. Zhang, M. E. Shabestari, J. Croyal and D. Y. Wang, Fire Saf. J., 2019, 107, 210–216 CrossRef CAS.
- N. M. Barkoula, B. Alcock, N. O. Cabrera and T. Peijs, Polym. Polym. Compos., 2008, 16, 101–113 CAS.
- E. L. Teuten, J. M. Saquing, D. R. U. Knappe, M. A. Barlaz, S. Jonsson, A. Björn, S. J. Rowland, R. C. Thompson, T. S. Galloway, R. Yamashita, D. Ochi, Y. Watanuki, C. Moore, P. H. Viet, T. S. Tana, M. Prudente, R. Boonyatumanond, M. P. Zakaria, K. Akkhavong, Y. Ogata, H. Hirai, S. Iwasa, K. Mizukawa, Y. Hagino, A. Imamura, M. Saha and H. Takada, Philos. Trans. R. Soc., B, 2009, 364, 2027–2045 CrossRef CAS PubMed.
- A. A. Koelmans, E. Besseling and E. M. Foekema, Environ. Pollut., 2014, 187, 49–54 CrossRef CAS PubMed.
- K. Gunaalan, E. Fabbri and M. Capolupo, Water Res., 2020, 184, 116170 CrossRef CAS PubMed.
- J. S. Kwon, N. J. Everetts, X. Wang, W. Wang, K. Della Croce, J. Xing and G. Yao, Cell Rep., 2017, 20, 3223–3235 CrossRef CAS PubMed.
- J. N. Hahladakis, C. A. Velis, R. Weber, E. Iacovidou and P. Purnell, J. Hazard. Mater., 2018, 344, 179–199 CrossRef CAS PubMed.
- H. Luo, Y. Xiang, D. He, Y. Li, Y. Zhao, S. Wang and X. Pan, Sci. Total Environ., 2019, 678, 1–9 CrossRef CAS PubMed.
- T. J. Suhrhoff and B. M. Scholz-Böttcher, Mar. Pollut. Bull., 2016, 102, 84–94 CrossRef CAS PubMed.
- W. A. Stubbings and S. Harrad, Sci. Total Environ., 2016, 569–570, 1004–1012 CrossRef CAS PubMed.
- G. Kocasoy and Z. M. Murat, J. Environ. Sci. Health, Part A: Toxic/Hazard. Subst. Environ. Eng., 2009, 44, 605–614 CrossRef CAS PubMed.
- S. Bejgarn, M. MacLeod, C. Bogdal and M. Breitholtz, Chemosphere, 2015, 132, 114–119 CrossRef CAS PubMed.
- M. Capolupo, L. Sørensen, K. D. R. Jayasena, A. M. Booth and E. Fabbri, Water Res., 2020, 169, 115270 CrossRef CAS PubMed.
- J. Sajiki and J. Yonekubo, Chemosphere, 2003, 51, 55–62 CrossRef CAS PubMed.
- A. Paluselli, V. Fauvelle, F. Galgani and R. Sempéré, Environ. Sci. Technol., 2019, 53, 166–175 CrossRef CAS PubMed.
- K. Tanaka, H. Takada, R. Yamashita, K. Mizukawa, M. A. Fukuwaka and Y. Watanuki, Environ. Sci. Technol., 2015, 49, 11799–11807 CrossRef CAS PubMed.
- H. Luo, Y. Li, Y. Zhao, Y. Xiang, D. He and X. Pan, Environ. Pollut., 2020, 257, 113475 CrossRef CAS PubMed.
- S. G. Tetu, I. Sarker, V. Schrameyer, R. Pickford, L. D. H. Elbourne, L. R. Moore and I. T. Paulsen, Commun. Biol., 2019, 2, 1–9 CrossRef PubMed.
- D. Lithner, I. Nordensvan and G. Dave, Environ. Sci. Pollut. Res., 2012, 19, 1763–1772 CrossRef CAS PubMed.
- ECHA, REACH registered substance factsheets, updated on August 6, 2021, https://echa.europa.eu/information-on-chemicals/registered-substances.
- H. X. Li, G. J. Getzinger, P. L. Ferguson, B. Orihuela, M. Zhu and D. Rittschof, Environ. Sci. Technol., 2016, 50, 924–931 CrossRef CAS PubMed.
- M. Oliviero, T. Tato, S. Schiavo, V. Fernández, S. Manzo and R. Beiras, Environ. Pollut., 2019, 247, 706–715 CrossRef CAS PubMed.
- A. Y. Ke, J. Chen, J. Zhu, Y. H. Wang, Y. Hu, Z. L. Fan, M. Chen, P. Peng, S. W. Jiang, X. R. Xu and H. X. Li, Mar. Pollut. Bull., 2019, 142, 54–57 CrossRef CAS PubMed.
- C. D. Rummel, B. I. Escher, O. Sandblom, M. M. Plassmann, H. P. H. Arp, M. Macleod and A. Jahnke, Environ. Sci. Technol., 2019, 53, 9214–9223 CrossRef CAS PubMed.
- G. Everaert, M. De Rijcke, B. Lonneville, C. R. Janssen, T. Backhaus, J. Mees, E. van Sebille, A. A. Koelmans, A. I. Catarino and M. B. Vandegehuchte, Environ. Pollut., 2020, 267, 115499 CrossRef CAS PubMed.
- V. N. de Ruijter, P. E. Redondo-Hasselerharm, T. Gouin and A. A. Koelmans, Environ. Sci. Technol., 2020, 1–156 Search PubMed.
- P. Blarer and P. Burkhardt-Holm, Environ. Sci. Pollut. Res., 2016, 23, 23522–23532 CrossRef CAS PubMed.
- C. Ahrendt, D. J. Perez-Venegas, M. Urbina, C. Gonzalez, P. Echeveste, M. Aldana, J. Pulgar and C. Galbán-Malagón, Mar. Pollut. Bull., 2020, 151, 110795 CrossRef CAS PubMed.
- L. Guilhermino, L. R. Vieira, D. Ribeiro, A. S. Tavares, V. Cardoso, A. Alves and J. M. Almeida, Sci. Total Environ., 2018, 622–623, 1131–1142 CrossRef CAS PubMed.
- C. J. Foley, Z. S. Feiner, T. D. Malinich and T. O. Höök, Sci. Total Environ., 2018, 631–632, 550–559 CrossRef CAS PubMed.
- K. L. Kaposi, B. Mos, B. P. Kelaher and S. A. Dworjanyn, Environ. Sci. Technol., 2014, 48, 1638–1645 CrossRef CAS PubMed.
- S. Bruck and A. T. Ford, Environ. Pollut., 2018, 233, 1125–1130 CrossRef CAS PubMed.
- J. E. Ward, M. Rosa and S. E. Shumway, Anthr. Coasts, 2019, 2, 39–49 CrossRef.
- I. Paul-Pont, K. Tallec, C. Gonzalez-Fernandez, C. Lambert, D. Vincent, D. Mazurais, J. L. Zambonino-Infante, G. Brotons, F. Lagarde, C. Fabioux, P. Soudant and A. Huvet, Front. Mar. Sci., 2018, 5, 252 CrossRef.
- R. Lenz, K. Enders and T. G. Nielsen, Proc. Natl. Acad. Sci. U. S. A., 2016, 113, E4121–E4122 CrossRef CAS PubMed.
- G. Everaert, L. Van Cauwenberghe, M. De Rijcke, A. A. Koelmans, J. Mees, M. Vandegehuchte and C. R. Janssen, Environ. Pollut., 2018, 242, 1930–1938 CrossRef CAS PubMed.
- D. S. Green, B. Boots, J. Sigwart, S. Jiang and C. Rocha, Environ. Pollut., 2016, 208, 426–434 CrossRef CAS PubMed.
- S. Straub, P. E. Hirsch and P. Burkhardt-Holm, Int. J. Environ. Res. Public Health, 2017, 14(7), 774 CrossRef PubMed.
- L. Zimmermann, G. Dierkes, T. A. Ternes, C. Völker and M. Wagner, Environ. Sci. Technol., 2019, 53(19), 11467–11477 CrossRef CAS PubMed.
- L. Zimmermann, S. Göttlich, J. Oehlmann, M. Wagner and C. Völker, Environ. Pollut., 2020, 267, 115392 CrossRef CAS PubMed.
- L. Zimmermann, Z. Bartosova, K. Braun, J. Oehlmann, C. Völker and M. Wagner, Environ. Sci. Technol., 2021, 55(17), 11814–11824 CrossRef CAS PubMed.
- C. G. Avio, S. Gorbi, M. Milan, M. Benedetti, D. Fattorini, G. D'Errico, M. Pauletto, L. Bargelloni and F. Regoli, Environ. Pollut., 2015, 198, 211–222 CrossRef CAS PubMed.
- D. I. Santos, J. M. A. Saraiva, A. A. Vicente and M. Moldão-Martins, in Innovative Thermal and Non-Thermal Processing, Bioaccessibility and Bioavailability of Nutrients and Bioactive Compounds, Elsevier, 2019, pp. 23–54 Search PubMed.
- F. R. Khan, D. Boyle, E. Chang and N. R. Bury, Environ. Pollut., 2017, 231, 200–206 CrossRef CAS PubMed.
- A. Bakir, S. J. Rowland and R. C. Thompson, Environ. Pollut., 2014, 185, 16–23 CrossRef CAS PubMed.
- A. Bakir, I. A. O'Connor, S. J. Rowland, A. J. Hendriks and R. C. Thompson, Environ. Pollut., 2016, 219, 56–65 CrossRef CAS PubMed.
- N. J. Diepens and A. A. Koelmans, Environ. Sci. Technol., 2018, 52, 8510–8520 CrossRef CAS PubMed.
- A. A. Koelmans, A. Bakir, G. A. Burton and C. R. Janssen, Environ. Sci. Technol., 2016, 50, 3315–3326 CrossRef CAS PubMed.
- L. G. A. Barboza, A. Dick Vethaak, B. R. B. O. Lavorante, A. K. Lundebye and L. Guilhermino, Mar. Pollut. Bull., 2018, 133, 336–348 CrossRef CAS PubMed.
- N. B. Hartmann, S. Rist, J. Bodin, L. H. S. Jensen, S. N. Schmidt, P. Mayer, A. Meibom and A. Baun, Integr. Environ. Assess. Manage., 2017, 13, 488–493 CrossRef PubMed.
- A. Tubić, M. Lončarski, S. Maletić, J. M. Jazić, M. Watson, J. Tričković and J. Agbaba, Water, 2019, 11, 2358 CrossRef.
- W. Gong, M. Jiang, P. Han, G. Liang, T. Zhang and G. Liu, Environ. Pollut., 2019, 254, 112927 CrossRef CAS PubMed.
- D. Boyle, A. I. Catarino, N. J. Clark and T. B. Henry, Environ. Pollut., 2020, 263, 114422 CrossRef CAS PubMed.
- L. Hildebrandt, N. Voigt, T. Zimmermann, A. Reese and D. Proefrock, Mar. Environ. Res., 2019, 151, 104768 CrossRef CAS PubMed.
- M. Mehdikhani, L. Gorbatikh, I. Verpoest and S. V. Lomov, J. Compos. Mater., 2019, 53, 1579–1669 CrossRef CAS.
- C. M. Lewandowski, N. Co-investigator and C. M. Lewandowski, Eff. Br. mindfulness Interv. acute pain Exp. An Exam. Individ. Differ., 2015, vol. 1, pp. 1689–1699 Search PubMed.
- U. G. K. Wegst and M. F. Ashby, Philos. Mag., 2004, 84(21), 2167–2186 CrossRef CAS.
- F. Barthelat, Bioinspiration Biomimetics, 2010, 5, 1–8 Search PubMed.
- M. Fantini, M. Curto and F. De Crescenzio, Virtual Phys. Prototyping, 2016, 11, 77–90 CrossRef.
- M. Fantini and M. Curto, Int. J. Interact. Des. Manuf., 2017, 1–12 CAS.
- M. Fantini, M. Curto and F. De Crescenzio, Lect. Notes Mech. Eng., 2017, 425–435 Search PubMed.
- S. A. Wainwright, W. D. Biggs, J. D. Currey and J. M. Gosline, Mechanical Design in Organisms, Princeton University Press, 1982 Search PubMed.
- P. Peças, H. Carvalho, H. Salman and M. Leite, J. Compos. Sci., 2018, 2, 66 CrossRef.
- J. R. Araújo, W. R. Waldman and M. A. De Paoli, Polym. Degrad. Stab., 2008, 93, 1770–1775 CrossRef.
- E. Pellicer, D. Nikolic, J. Sort, M. D. Baró, F. Zivic, N. Grujovic, R. Grujic and S. Pelemis, Adv. Appl. Ind. Biomater., 2017, 1–214 Search PubMed.
- D. Ghelli and G. Minak, Composites, Part B, 2011, 42, 2067–2079 CrossRef.
- S. Boria, A. Pavlovic, C. Fragassa and C. Santulli, Procedia Eng, 2016, 167, 223–230 CrossRef CAS.
- E. Poodts, G. Minak, L. Mazzocchetti and L. Giorgini, Composites, Part B, 2014, 56, 673–680 CrossRef CAS.
- M. Savoia, M. Stefanovic and C. Fragassa, Int. J. Qual. Res., 2016, 10, 1–16 Search PubMed.
- A. Hladnik and T. Muck, Dyes Pigm., 2002, 54, 253–263 CrossRef CAS.
- C. Kugge and B. Johnson, Prog. Org. Coat., 2008, 62, 430–435 CrossRef CAS.
- W. A. Daoud, J. H. Xin and X. Tao, J. Am. Ceram. Soc., 2004, 87, 1782–1784 CrossRef CAS.
- A. Dufresne, Mater. Today, 2013, 16, 220–227 CrossRef CAS.
- Z. Yang, H. Peng, W. Wang and T. Liu, J. Appl. Polym. Sci., 2010, 116, 2658–2667 CAS.
- D. S. Cha and M. S. Chinnan, Crit. Rev. Food Sci. Nutr., 2004, 44, 223–237 CrossRef CAS PubMed.
- S. Chen, X. Li, Y. Li and J. Sun, ACS Nano, 2015, 9, 4070–4076 CrossRef CAS PubMed.
- T. G. Kannan, Asian Text. J., 2008, 17, 34–36 Search PubMed.
- A. Mohanty, M. Misra, L. Drzal, S. Selke, B. Harte and G. Hinrichsen, in Soy Protein-based Plastics, Blends, and Composites, 2005, vol. 1, pp. 1–36 Search PubMed.
- K. Pickering, Properties and Performance of Natural-Fibre Composites, 2008 Search PubMed.
- H. Yang, J. C. Lim, Y. Liu, X. Qi, Y. L. Yap, V. Dikshit, W. Y. Yeong and J. Wei, Virtual Phys. Prototyping, 2017, 12, 95–103 CrossRef.
- R. Olszewski, P. Szymor and M. Kozakiewicz, J. Cranio-Maxillofacial Surg., 2014, 42, 1847–1852 CrossRef PubMed.
- E. Huotilainen, R. Jaanimets, J. Valášek, P. Marcián, M. Salmi, J. Tuomi, A. Mäkitie and J. Wolff, J. Cranio-Maxillofacial Surg., 2014, 42, 259–265 CrossRef PubMed.
- V. Le, H. Paris and G. Mandil, 22 ème Congrès Français Mécanique CFM2015, 2015, pp. 1–8 Search PubMed.
- J. Z. Manapat, Q. Chen, P. Ye and R. C. Advincula, Macromol. Mater. Eng., 2017, 302, 1–13 CrossRef.
- J. Z. Manapat, J. D. Mangadlao, B. D. B. Tiu, G. C. Tritchler and R. C. Advincula, ACS Appl. Mater. Interfaces, 2017, 9, 10085–10093 CrossRef CAS PubMed.
- B. G. Compton and J. A. Lewis, Adv. Mater., 2014, 26, 5930–5935 CrossRef CAS PubMed.
- W. Yu, H. Zhou, B. Q. Li and S. Ding, ACS Appl. Mater. Interfaces, 2017, 9, 4597–4604 CrossRef CAS PubMed.
- ASTM International, Rapid Manuf. Assoc., 2013, 10–12 Search PubMed.
- S. Yang and Y. F. Zhao, Int. J. Adv. Des. Manuf. Technol., 2015, 80, 327–342 CrossRef.
- M. Kumke, H. Watschke and T. Vietor, Virtual Phys. Prototyping, 2016, 11, 3–19 CrossRef.
- A. K. Mohanty, M. Misra and L. T. Drzal, Compos. Interfaces, 2001, 8, 313–343 CrossRef CAS.
- K. G. Satyanarayana, G. G. C. Arizaga and F. Wypych, Prog. Polym. Sci., 2009, 34, 982–1021 CrossRef CAS.
- B. Singh and M. Gupta, J. Polym. Environ., 2005, 13, 127–137 CrossRef CAS.
- K. G. Satyanarayana, K. Sukumaran, A. G. Kulkarni, S. G. K. Pillai and P. K. Rohatgi, Composites, 1986, 17, 329–333 CrossRef CAS.
- A. Stamboulis, C. A. Baillie, S. K. Garkhail, H. G. H. Van Melick and T. Peijs, Appl. Compos. Mater., 2000, 7, 273–294 CrossRef CAS.
- K. Khwaldia, E. Arab-Tehrany and S. Desobry, Compr. Rev. Food Sci. Food Saf., 2010, 9, 82–91 CrossRef CAS PubMed.
- C. Andersson, Packag. Technol. Sci., 2008, 21, 339–373 CrossRef CAS.
- N. Sun, S. Qin, J. Wu, C. Cong, Y. Qiao and Q. Zhou, J. Nanosci. Nanotechnol., 2012, 12, 7222–7225 CrossRef CAS PubMed.
- A. Valadez-Gonzalez, J. M. Cervantes-Uc, R. Olayo and P. J. Herrera-Franco, Composites, Part B, 1999, 30, 309–320 CrossRef.
- B. N. Dash, A. K. Rana, H. K. Mishra, S. K. Nayak and S. S. Tripathy, J. Appl. Polym. Sci., 2000, 78, 1671–1679 CrossRef CAS.
- S. Joseph, Z. Oommen and S. Thomas, J. Appl. Polym. Sci., 2006, 100, 2521–2531 CrossRef CAS.
- R. Malkapuram, V. Kumar and Y. Singh Negi, J. Reinf. Plast. Compos., 2009, 28, 1169–1189 CrossRef CAS.
|
This journal is © The Royal Society of Chemistry 2021 |
Click here to see how this site uses Cookies. View our privacy policy here.