DOI:
10.1039/D1RA02335G
(Paper)
RSC Adv., 2021,
11, 16841-16848
Hydrodynamic synthesis of Fe2O3@MoS2 0D/2D-nanocomposite material and its application as a catalyst in the glycolysis of polyethylene terephthalate†
Received
24th March 2021
, Accepted 24th April 2021
First published on 7th May 2021
Abstract
We report a fast and simple synthesis of Fe2O3@MoS2 0D/2D-nanocomposite material using a Taylor–Couette flow reactor. A Taylor–Couette flow with high shear stress and mixing characteristics was used for fluid dynamic exfoliation of MoS2 and deposition of uniform Fe2O3 nanoparticles, resulting in a Fe2O3@MoS2 in the form of 0D/2D-nanocomposite material. Using Taylor–Couette flow reactor, we could synthesize Fe2O3@MoS2 0D/2D-nanocomposite material at a rate higher than 1000 mg h−1 which is much higher than previously reported production rate of 0.2–116.7 mg h−1. The synthesis of Fe2O3@MoS2 nanocomposite was achieved in an aqueous solution without thermal or organic solvent treatment. Exfoliated MoS2 nanosheets show an average thickness of 2.6 ± 2.3 nm (<6 layers) and a lateral size of 490 ± 494 nm. Fe2O3 nanoparticles have an average size of 7.4 ± 3.0 nm. Fe2O3 nanoparticles on chemically and thermally stable MoS2 nanosheets show catalytic activity in the glycolysis of polyethylene terephthalate (PET). High conversion of PET (97%) and a high yield (90%) for bis(hydroxyethyl) terephthalate (BHET) were achieved in a reaction time of 3 h at the reaction temperature of 225 °C.
Introduction
Two-dimensional (2D) nanosheets such as graphene, transition metal dichalcogenides (TMD), and hexagonal boron nitride (hBN) may be promising for heterogeneous catalyst supports1–3 because of their outstanding mechanical strength4 and high surface area.5 Among 2D layered materials, MoS2 nanosheets exhibit thermal and chemical stability,6–8 and antioxidation properties9 and thus were used as 2D substrates for the 0D/2D-nanocomposite material with noble metal10,11 and metal oxide.12 Among these, the combination of MoS2 nanosheets with iron oxide nanoparticles enhanced electrochemical, optical, and catalytic properties by chemical bonding-induced synergistic effect such as heterojunction on the 0D/2D-nanomaterial platform.13–15 To synthesize iron oxide nanoparticles and MoS2 nanosheets composites, various methods have been reported.13–21 Hydrothermal method is the most common method to synthesize either iron oxide nanoparticles or their composite with MoS2 nanosheets.13–17 It can synthesize uniform iron oxide nanoparticles on the MoS2 nanosheets but it requires high temperature and pressure with long reaction time and has limited scale-up capacity due to energy inefficiency. Organic phase synthesis is similar to hydrothermal method, and it needs heating under inert gas conditions with organic solvents.18–20 Most of previous methods have needed heat treatment, organic solvents, or specific conditions such as inert gas in the synthesis of iron oxide nanoparticles on the MoS2 nanosheets which hinder mass production and further applications.
Fluid dynamic system is one of the promising alternatives for mass-production of 0D/2D nanocomposite. Thus, synthesis of nanoparticles,22 growth of polymers,23 and exfoliation of 2D materials24,25 were achieved using fluid dynamic system. Among the fluid dynamic systems, Taylor–Couette flow reactor with high shear stress and mass transfer characteristics was used for the exfoliation of 2D materials such as graphite, hBN, and MoS2.24–26 Our group reported deposition of noble metal (Pt, Ag, and Pd) nanoparticles on exfoliated hBN nanosheets in a Taylor–Couette flow reactor.27 High shear stress and mixing characteristics of Taylor–Couette flow reactor allowed the operation under mild reaction conditions in short reaction time.
Polyethylene terephthalate, commonly called PET, is one of the most consumed polymers in more than 300 million tons annually due to its mechanical strength and thermoplastic-based property.28,29 Enormous consumption of PET in a daily life causes serious environmental problems due to poor biodegradability of PET.30,31 To solve the problem, the chemical recycling methods such as alcoholysis,32 aminolysis,33 hydrolysis,34 and glycolysis35 were investigated. Among these, glycolysis of PET decomposes PET using ethylene glycol (EG) to produce bis(2-hydroxyethyl) terephthalate (BHET) monomers which can be used to synthesize polymers again providing the sustainability in the polymer ecosystem. The major drawback of PET glycolysis is slow reaction despite high temperature.36 Heavy metal salts, known as trans-esterification catalysts, were used as catalysts for PET glycolysis to solve the problem.37,38 Although the reaction temperature was lowered to around 200 °C, there was still an environmental problem due to the presence of heavy metals in recycled BHET monomers. To replace heavy metal salts, eco-friendly ionic liquids were used in PET glycolysis but their high cost was a concern.39,40 Because of environmentally abundant and eco-friendly characteristics,35,41,42 the use of cobalt oxide,43 iron oxide,44 and manganese oxide45 was reported in the glycolysis of PET. However, needs for organic solvent-based processes and calcination make the synthetic processes of oxide material still formidable. Therefore, large-scale manufacturing of an effective catalyst material for PET recycling should be practiced in a more economical and eco-friendly routes.
Here, we report a fast and simple hydrodynamic synthesis method without heating for the synthesis of Fe2O3 nanoparticles on exfoliated MoS2 nanosheets in the form of 0D/2D-nanocomposites in a Taylor–Couette flow reactor. To the best of our knowledge, synthesis of Fe2O3@MoS2 0D/2D nanocomposites without heating or organic solvents has not been reported. The synthesis of Fe2O3@MoS2 nanocomposite was achieved in an hour without organic solvents. Fe2O3 nanoparticle is preferable for a catalyst because it is the most stable among iron oxides. However, it usually needs additional treatment such as calcination to convert Fe2O3 from Fe3O4. Fluid dynamic process enabled the direct synthesis of Fe2O3 nanoparticles on MoS2 nanosheets. The synthetic Fe2O3@MoS2 nanocomposite was used to validate its catalytic activity in PET glycolysis.
Experimental procedure
Materials and chemicals
Iron(III) chloride hexahydrate powder (FeCl3·6H2O, 99%), molybdenum disulfide powder (MoS2, <2 μm), sodium hydroxide (NaOH) powder, ethylene glycol (EG, 99.8%), and bis(2-hydroxyethyl) terephthalate (BHET) powder were purchased from Sigma-Aldrich Corporation (USA). Polyethylene terephthalate powder (PET, <200 μm, weight average molecular weight: 56 780 g mol−1) was obtained from Goodfellow Corporation (UK).
Preparation of Fe2O3@MoS2 nanocomposite
The schematic for the synthesis of Fe2O3@MoS2 nanocomposite using the Taylor–Couette flow reactor is illustrated in Fig. 1a. Pristine MoS2 powder (1000 mg) was initially dispersed in deionized (DI) water at a concentration of 2 mg mL−1 in a 500 mL volume. Next, FeCl3 powder (181 mg–3940 mg) was dispersed in MoS2 aqueous mixture at various Fe
:
Mo molar ratio from 1
:
9 to 7
:
3. The MoS2/FeCl3 mixtures were reacted for 1 h in the Taylor–Couette flow reactor with 2000 rotations per minute (rpm) of inner cylinder under room temperature. At the end of the reaction, 10 mL of 1 M NaOH aqueous solution was added to the Taylor–Couette flow reactor and reacted for 5 more minutes to convert FeCl3 to Fe2O3 nanoparticles. To compare the effect of mass transfer in the size distribution of Fe2O3 nanoparticles, 3 different Fe2O3@MoS2 nanocomposites with Fe
:
Mo molar ratio of 3
:
7 were synthesized at 3 different rotation speeds (500, 1500 and 2000 rpm) of inner cylinder in the Taylor–Couette flow reactor. Fe2O3@MoS2 nanocomposite dispersed in the solution is shown in Fig. 1b. Synthetic Fe2O3@MoS2 nanocomposite was centrifuged at 3200g for 1 h and separated from un-exfoliated MoS2 followed by vacuum filtration using a cellulose nitrate filter (pore size: 100 nm) to extract extra ions (Na+ and Cl−) from the supernatant. The filtered Fe2O3@MoS2 nanocomposite was re-dispersed in 200 mL DI water and freeze-dried at −50 °C with 20 Pa to obtain Fe2O3@MoS2 nanocomposite powder at a rate higher than 1000 mg h−1 as shown in Fig. 1c. Detailed specification of the Taylor–Couette reactor was denoted in Fig. S1.†
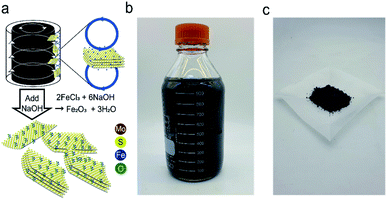 |
| Fig. 1 (a) Schematic illustrations of the synthesis process of Fe2O3@MoS2 nanocomposite by fluid dynamic exfoliation and deposition, (b) produced Fe2O3@MoS2 nanocomposite in solution, (c) Fe2O3@MoS2 nanocomposite powder. | |
Characterization
The spherical aberration transmission electron microscopy (Cs-TEM) images were obtained by Titan3™ G2 60-300 (FEI). Transmission electron microscopy (TEM), scanning transmission electron microscopy (STEM), fast Fourier transform (FFT) diffraction pattern, and energy-dispersive X-ray spectroscopy (EDS) analysis were carried out by Tecnai G2 F30 S-TWIN (FEI) operating at 300 kV. Raman spectroscopy data were obtained using LabRAM HR Evolution Visible_NIR (HORIBA Co). Atomic force microscopy (AFM) data were obtained with INNOVA-LABRAM HR800 (Bruker Daltonik Co). X-ray photoelectron spectroscopy (XPS) data were acquired with a Kα (Thermo VG Scientific Co). Inductively coupled plasma-optical emission spectrometry (ICP-OES) analysis was carried out by Agilent ICP-OES 720 (Agilent Technologies). High performance liquid chromatography (HPLC) data were obtained by micrOTOF-QII (Bruker Daltonik Co) at 200–1000 parts per million (ppm) concentration in tetra hydro furan (THF). The thermogravimetric analysis (TGA)-differential scanning calorimetry (DSC) curves were obtained by LABSYS Evo (Setaram Co). Brunauer–Emmett–Teller (BET) analysis was carried out with Tristar II 3020 (Micromeritics Company). The 1H and 13C nuclear magnetic resonance (NMR) spectra analyses were carried out with Agilent 400 MHz 54 mm NMR DD2 (Agilent Technologies) at room temperature. The chemical shifts were denoted in ppm using dimethyl sulfoxide-d6 (DMSO-d6) signal as a standard.
Glycolysis of PET
The condition for the glycolysis of PET was based on a previous report using iron oxide as a catalyst.44 Prepared Fe2O3@MoS2 nanocomposite (20 mg) was dispersed in 8 g of EG, and the mixture was placed in a Teflon reactor along with 2 g of PET powder (Goodfellow, <200 μm). The reactants in the Teflon reactor were heated in a furnace between 200 and 300 °C for 3 to 5 h to examine the effect of temperature and time on glycolysis. Reacted solution was cooled to 70 °C in an oven. Vacuum filtration was performed to separate unreacted PET and catalyst from the product. The filtered solution was cooled in a refrigerator at 4 °C for 24 h. BHET was filtered by vacuum filtration followed by washing with cool DI water 3 times to remove extra EG. Mass of BHET was calculated by conventional HPLC method with a calibration curve in the range of 200 to 1000 ppm.
Conversion of PET and the yield of BHET were calculated using eqn (1) and (2):27
|
 | (1) |
|
 | (2) |
In the equations above, WPET represents the initial weight of PET, and W is the weight of PET after reaction. MPET is the molecular weight of the repeated unit of PET. WBHET is the weight of BHET based on the HPLC calibration curve, and MBHET is the molecular weight of BHET. Fe2O3@MoS2 nanocomposite was recovered by vacuum filtration method. Due to more than 97% conversion of PET, the filtered precipitate was used for recycling as a recovered catalyst.
Results and discussion
Morphology of Fe2O3@MoS2 nanocomposite
Morphology and crystalline structure of MoS2 nanosheets were investigated using AFM and TEM. AFM image of MoS2 nanosheets is presented in Fig. 2a. AFM data of 70 samples of Fe2O3@MoS2 nanocomposite were used to determine the average thickness and average lateral size (Fig. S2†). MoS2 nanosheets had an average lateral size of 493.19 ± 494.50 nm and an average thickness of 2.65 ± 2.38 nm, indicating successful exfoliation of MoS2 (Fig. 2b and c). Cs-TEM and EDS analysis were performed to confirm the deposition of Fe2O3 nanoparticles on MoS2 nanosheets. Fig. 2d is the Cs-TEM image of Fe2O3@MoS2 nanocomposite. Specific lattice structures of iron oxide(III), denoted by red lines, were distinguished from the hexagonal lattice of the surrounding MoS2. The characteristic lattice lengths of Fe2O3 and MoS2 were 2.5 Å for (110) and 2.7 Å for (100), respectively.14 EDS analysis of the same sample was performed to confirm the deposition of Fe2O3 nanoparticles on the MoS2 nanosheet (Fig. 2e). The yellow signal of sulfur and the purple signal of molybdenum indicate MoS2 in the STEM image. The blue signal of Fe on the MoS2 indicates successful synthesis of Fe2O3@MoS2 nanocomposite.
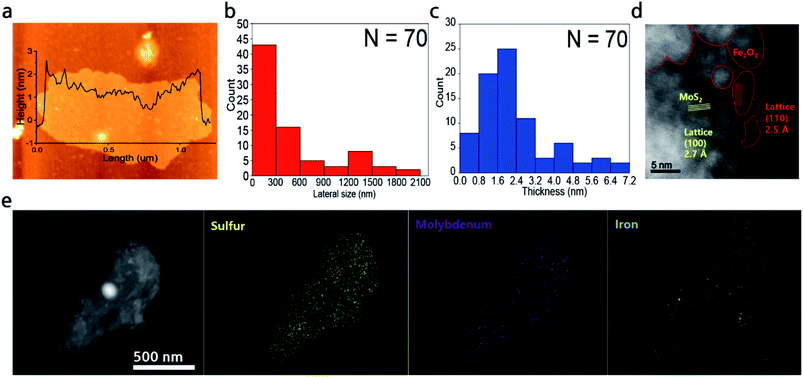 |
| Fig. 2 (a) AFM image of Fe2O3@MoS2 nanocomposite. (b) Lateral size and (c) thickness distribution of Fe2O3@MoS2 nanocomposite. (d) Cs-TEM image of Fe2O3@MoS2 nanocomposite. (e) STEM image and elemental mapping images of sulfur, molybdenum, and iron of Fe2O3@MoS2 nanocomposite. | |
BET surface area analysis was performed to further investigate the surface area of Fe2O3@MoS2 nanocomposite. Fig. S3† shows the BET surface area data of pristine MoS2, MoS2 nanosheets, and Fe2O3@MoS2 nanocomposite. In Fig. S3a, c and e,† BET surface area data show typical isotherm for 2D materials. The surface area of pristine MoS2 and MoS2 nanosheets was 3.18 m2 g−1 and 9.33 m2 g−1, respectively in Fig. S3b and d.† Fe2O3@MoS2 nanocomposite had a surface area of 47.95 m2 g−1 and a higher slope isotherm due to Fe2O3 nanoparticles (Fig. S3f†) which are consistent with previous reports despite being a top-down method.44 Since it is a 0D/2D hybrid material, the surface area per unit mass is smaller than that of Fe2O3 nanoparticles. Even with a less surface area, MoS2 nanosheets represent a stable substrate to prevent aggregation of Fe2O3 nanoparticles and its lateral size facilitates the recovery of Fe2O3@MoS2 nanocomposite after reaction.
Size distribution of Fe2O3 nanoparticles depending on flow regime in the Taylor–Couette flow reactor
TEM analysis was used to compare the distribution of Fe2O3 nanoparticles in Fe2O3@MoS2 nanocomposite synthesized at various Fe
:
Mo ratios from 1
:
9 to 7
:
3. Fig. S4a and b† show Fe2O3@MoS2 nanocomposite synthesized with Fe
:
Mo ratio of 1
:
9. Fe2O3 nanoparticles are rare on MoS2 nanosheets in high resolution image. Fe2O3@MoS2 nanocomposite synthesized with Fe
:
Mo ratio of 3
:
7 shows relatively more Fe2O3 nanoparticles on MoS2 nanosheets in Fig. S4c and d.† The Fe2O3@MoS2 nanocomposite with Fe
:
Mo ratio of 5
:
5 shows fairly dense Fe2O3 nanoparticles on MoS2 nanosheets (Fig. S4e and f†). For Fe2O3@MoS2 nanocomposite with Fe
:
Mo ratio of 7
:
3, Fe2O3 nanoparticles are distributed more densely on MoS2 nanosheets than that with Fe
:
Mo ratio of 5
:
5 (Fig. S4g and h†). As expected, amount of Fe2O3 nanoparticles on MoS2 nanosheets increased as ratio of Fe increased.
TEM images and FFT diffraction patterns of Fe2O3@MoS2 nanocomposite synthesized at different rotation speeds of inner cylinder in the Taylor–Couette flow reactor are shown in Fig. 3. Fe2O3 nanoparticles are distributed well on MoS2 nanosheets with the characteristic hexagonal FFT diffraction patterns marked with yellow circles. Flow regimes in the Taylor–Couette flow reactor varied depending on rotation speed of inner cylinder as laminar, wavy, and turbulent regimes in the order of increasing rotation speed. Previously, our group reported efficiency of exfoliation for 2D materials in various flow regimes of Taylor–Couette flow and found about 2000 rpm corresponding to wavy regime is optimum for the exfoliation of 2D materials.24,25 In order to compare the synthesis of Fe2O3 nanoparticles at different rpm, Fe2O3@MoS2 nanocomposite was synthesized in the Taylor–Couette flow reactor at various rotation speeds of inner cylinder. Fig. 3a and b show Fe2O3@MoS2 nanocomposite synthesized at 500 rpm in the Taylor–Couette flow reactor. According to the TEM image and size distribution data, Fe2O3 nanoparticles showed an average size of about 13.73 ± 3.82 nm. As rpm increased, the average size of Fe2O3 nanoparticles decreased to 11.79 ± 4.21 nm at 1500 rpm of rotation speed (Fig. 3c and d). Uniformity of the Fe2O3 nanoparticles was improved at 2000 rpm of rotation speed, and the average size of Fe2O3 nanoparticles was also reduced to 7.41 ± 2.95 nm (Fig. 3e and f).
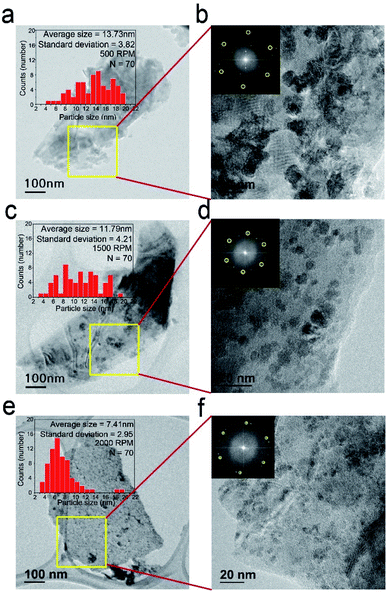 |
| Fig. 3 Size distributions of Fe2O3 nanoparticles and TEM images of Fe2O3@MoS2 nanocomposite synthesized at (a) 500 rpm, (c) 1500 rpm, and (e) 2000 rpm in the Taylor–Couette flow reactor, and their magnified TEM images with FFT diffraction patterns of Fe2O3@MoS2 nanocomposite synthesized at (b) 500 rpm, (d) 1500 rpm, and (f) 2000 rpm. | |
Even in the top down method without heating, Fe2O3 nanoparticles were distributed well on MoS2 nanosheets. Based on the TEM image, the size distribution of Fe2O3 nanoparticles on MoS2 nanosheets was obtained, showing average size of the nanoparticles as 7.41 nm and mostly less than 10 nm at 2000 rpm of rotation speed. Fe2O3 nanoparticles usually require thermal treatment for their synthesis.13–15,17 However, in our study, no thermal treatment was conducted. Increased mixing characteristics with increasing rpm of Taylor–Couette flow reactor46 made Fe2O3 nanoparticles synthesized on MoS2 nanosheets in a nanometer scale without thermal treatment. In addition, TEM grid was observed below the transparent MoS2 nanosheets, indicating adequate exfoliation of MoS2.
Chemical composition and synthetic mechanism of Fe2O3@MoS2 nanocomposite
Raman spectroscopy and XPS were used to examine the chemical state of Fe2O3@MoS2 nanocomposite by measuring its response to photons. E12g mode reflects the in-plane vibration, and the A1g mode reflects the out-plane vibration of MoS2.48 Fig. 4a shows the Raman spectroscopy data of Fe2O3@MoS2 nanocomposite and pristine MoS2, and peaks for MoS2 and Fe2O3 were observed. In Fig. 4b, the E12g mode of Fe2O3@MoS2 nanocomposite was located at 375.7 cm−1, while the E12g mode of pristine MoS2 was located at 379.9 cm−1. Also the A1g mode of Fe2O3@MoS2 nanocomposite was located at 401.4 cm−1, and A1g mode of pristine MoS2 was located at 404.2 cm−1. A1g mode of Fe2O3@MoS2 nanocomposite were shifted less than E12g mode. According to previous study, it means that out-plane of MoS2 was affected by the external factor,47 presumably Fe2O3 nanoparticles, which are bonded to the basal plane (out-plane) of MoS2.
 |
| Fig. 4 (a) Raman spectroscopy data of pristine MoS2 and Fe2O3@MoS2 nanocomposite, (b) and its magnified data from 340 to 500 cm−1. | |
XPS analysis was performed to confirm the interaction, and chemical composition of Fe2O3 nanoparticles and MoS2 nanosheets.20,25,42 Survey scan data show that both iron oxide and molybdenum disulfide exist in Fe2O3@MoS2 nanocomposite (Fig. 5a). In Fig. 5b and c, Fe2p and O1s scan were used to compare the synthesis of Fe2O3 nanoparticles on MoS2 and other 2D substrates. Since FeCl3 with Fe3+ was used as the precursor, the Fe2p scan of all experimental groups shows the typical Fe3+ and its satellite peaks at 710.7 eV, and 719.2 eV, respectively, which are similar to pristine Fe2O3.44 O–Fe bond and O–H bond in O1s scan represent Fe2O3 and Fe(OH)3, respectively, and the ratio between O–H bond and O–Fe bond depends on the kind of substrates. The ratio of O–Fe bond to O–H bond was 70
:
30 in Fe2O3@MoS2 nanocomposite. On the other hand, the ratios of O–Fe bond to O–H bond were 46
:
54 and 37
:
63 in graphite and hBN, respectively, with the Fe3+ precursor. The ratio of O–Fe bond to O–H bond was highest in Fe2O3@MoS2 nanocomposite, and these results signify that, Fe2O3 is converted successfully from FeCl3 with NaOH on MoS2 substrate better than on graphite or hBN in the Taylor–Couette flow reactor. Previous research has reported that the interface between Fe2O3, and MoS2 has a lower formation energy of −1.76 eV for chemical bonding.49,50 To further confirm the chemical bonding between MoS2 and Fe2O3, the binding energy of Fe2O3@MoS2 nanocomposite was compared with the pristine Fe2O3 and pristine MoS2. Fe2p scan data of Fe2O3@MoS2 nanocomposite reveal the peak for Fe3+ at 711.7 eV, red shifted by 1 eV compared to pristine Fe2O3. On the other hand, Mo3d and S2p scans of the Fe2O3@MoS2 nanocomposite show 0.7 eV and 0.2 eV blue shifted binding energies, respectively, compared to pristine MoS2 in Fig. 5d and e. The shifts of binding energy in Fe2O3@MoS2 nanocomposite indicate a chemical interaction between Fe2O3 nanoparticles and MoS2 nanosheets as shown by Raman spectroscopy data. XPS and Raman spectroscopy data of Fe2O3@MoS2 nanocomposite show that even in a fluid dynamic-based production method without heating, Fe2O3 nanoparticles were bound to MoS2 nanosheets by chemical bonds, and MoS2 nanosheet is effective 2D substrates to incorporate Fe2O3 nanoparticles.
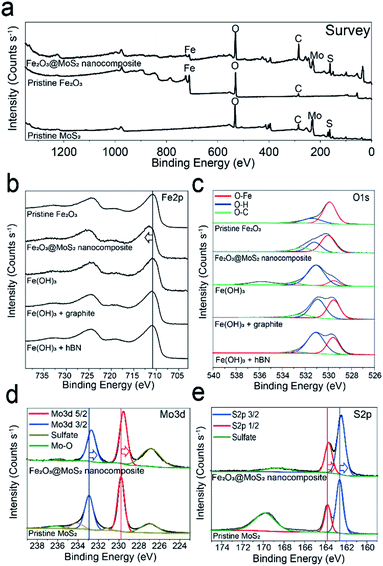 |
| Fig. 5 XPS (a) survey scan of Fe2O3@MoS2 nanocomposite, pristine Fe2O3, and pristine MoS2, (b) Fe2p and (c) O1s scan of pristine Fe2O3, Fe2O3@MoS2 nanocomposite, and Fe(OH)3 with various substrate reacted in the Taylor–Couette flow reactor, (d) Mo3d and (e) S2p scan of Fe2O3@MoS2 nanocomposite and pristine MoS2. | |
In XPS analysis, atomic ratio of Fe and Mo was 3
:
6.6, which is similar to that of the precursor ratio of 3
:
7. Further compositional analysis was conducted by ICP-OES, which confirmed successful conversion of FeCl3 to Fe2O3 nanoparticles. The ICP-OES data show atomic ratio of 3
:
6.3, which is almost identical to the atomic ratio between Fe and Mo in the XPS data (Table S1†).
Glycolysis of PET by Fe2O3@MoS2 nanocomposite
Because glycolysis reaction occurs at the temperature above 175 °C, it is necessary to confirm the thermal stability of Fe2O3@MoS2 nanocomposite. Fig. S5a and b† present the TGA data and derivative thermogravimetry (DTG) data, which showed no reduction below 400 °C. There was small increase of mass at 400 °C because of nitrogen adsorption followed by the reduction at high temperature. Since the glycolysis reaction was performed below 300 °C, Fe2O3@MoS2 nanocomposite will be thermally stable during the reaction.
Previously suggested mechanism of PET glycolysis using Fe2O3 is shown in Fig. 6a.44,51 The yield of BHET in PET glycolysis was measured by conventional method using HPLC,27 and the comparison with previous reports is presented in Table S2.† Fig. 6b shows the conversion of PET with Fe2O3@MoS2 nanocomposite having various Fe
:
Mo ratios. MoS2 nanosheets show only 7% conversion in the glycolysis of PET, and the conversion of PET using Fe2O3@MoS2 nanocomposite was found to be saturated in the Fe
:
Mo ratio of 3
:
7. Fig. 6c shows the conversion of PET with the varying ratio between PET and Fe2O3@MoS2 nanocomposite. A 98% conversion of PET was reached at the ratio higher than 1/100. In Fig. 6d, the yield of BHET was maintained at around 90% up to 250 °C. However, the yield of BHET suddenly decreased at 275 °C and continued to decrease to almost 50% at 300 °C. To analyze the decrease in yield, the process was carried out at 300 °C for 3 to 5 h (Fig. 6e) and showed further decrease in yield to 38%. Previous studies have reported that decreased yield of BHET in glycolysis of PET is caused by chemical equilibrium, and HPLC data of glycolysis product at 300 °C show by-product peaks in HPLC data different from HPLC data of commercial BHET and produced BHET at 225 °C (Fig. S6a–c†). There would be side reactions between BHET and EG or oligomer of PET, reducing the yield of BHET from 50% to less than 40% as reaction time increased.35
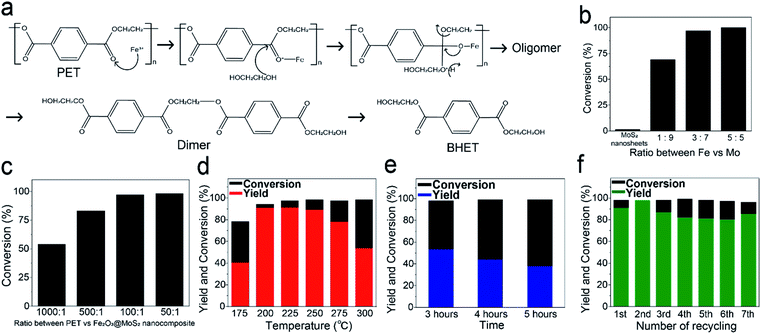 |
| Fig. 6 (a) Suggested mechanism for glycolysis of PET using Fe2O3 nanoparticles as a catalyst,44,51 (b) conversion of PET with MoS2 nanosheets and various Fe : Mo ratio of Fe2O3@MoS2 nanocomposite, (c) conversion of PET with various ratio of PET and Fe2O3@MoS2 nanocomposite, yield and conversion (d) with 3 h reaction at different reaction temperature using Fe2O3@MoS2 nanocomposite, (e) at 300 °C with 3 different reaction time, and (f) with repeated recycling of catalyst at 225 °C for 3 h. | |
In Fig. S7a,† Fe2O3@MoS2 nanocomposite catalyst was recovered by simple filtration, and the recycling reaction with recycled catalyst was carried out at 225 °C for 3 h. During 7 recycles, the yield of BHET remained around 85% (Fig. 6f). TEM and ICP-OES were used to characterize the recovered Fe2O3@MoS2 nanocomposite. Fig. S7b and c† show the morphology of recovered Fe2O3@MoS2 nanocomposite. Even though Fe2O3@MoS2 nanocomposite was recycled repeatedly during PET glycolysis, Fe2O3 nanoparticles are clearly distributed on MoS2 nanosheets in the recovered Fe2O3@MoS2 nanocomposite as fresh Fe2O3@MoS2 nanocomposite. ICP-OES data in Table S3† also show that the composition of Mo and Fe in recycled Fe2O3@MoS2 nanocomposite was maintained after the recycling. Although the catalytic yield and conversion rate are not superior to previous work, the production rate of Fe2O3@MoS2 nanocomposite was 1120 mg h−1, and is much higher than 0.2 mg h−1 to 116.7 mg h−1 of other reports and stable without decomposition or separation (Table S4†).
1H and 13C NMR analyses were performed to confirm the purity of BHET as shown in Fig. 7a. NMR δ values were as follows: white solid, 1H NMR (DMSO-d6, 400 MHz, δ/ppm), δ = 8.09 (s, 4H), δ = 4.95 (t, 2H), δ = 4.28 (t, 4H), δ = 3.69 (q, 4H). 13C NMR (DMSO-d6, 400 MHz, δ/ppm) data were: δ = 165.06, 133.62, 129.42, 66.93, 58.86. Thus, the characteristic peaks of BHET consist of 5 carbons and 4 hydrogens indicated as A to E and 1 to 4 in NMR spectra data. Fig. 7b and c show DSC and TGA data of BHET. DSC curve shows a peak at 107 °C, and the TGA data show double decreases at 240 °C and 420 °C, showing the same thermal properties as reported previously for BHET.35,39 Produced BHET is intended to be used as a monomer to synthesize polymeric material, and fewer impurity in BHET is more desirable. ICP-OES data indicating the residual amounts of Fe and Mo in the extracted BHET are shown in Table S5.† Only small amount of Fe and Mo, 10−4 and 10−5 weight percent, respectively, was detected in the extracted BHET.
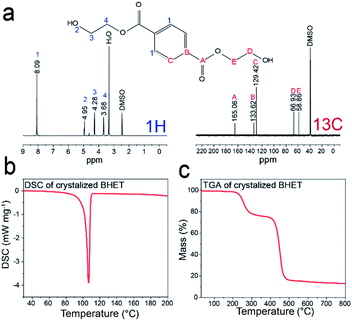 |
| Fig. 7 (a) 1H and 13C NMR spectra data for produced BHET, (b) DSC data of crystalized BHET, (c) TGA data of crystalized BHET. | |
In order to check whether the catalyst works effectively in the scaled-up process, the glycolysis reaction was performed with 100 g of PET. 100 g of PET was dispersed in 400 mL of EG with 1 g of Fe2O3@MoS2 nanocomposite as shown in Fig. S8a.† The reaction was proceeded at 196 °C for 3 h with simple stirring under ambient condition. The product of glycolysis and produced BHET had identical brown and white color, respectively, with the previous product of glycolysis (Fig. S8b and c†), and HPLC data of product showed identical peaks with that of product from the smaller scale glycolysis of PET (Fig. S8d†). However, the peak of retention time at 18.37 is higher than that of commercial BHET (Fig. S6a†) which means higher contents of dimer. The yield and conversion were 87% and 94%, respectively. Therefore, Fe2O3@MoS2 nanocomposite can be used in the increased scale of PET glycolysis and can be considered as an attractive catalyst in the recycling of large amount of PET by glycolysis to produce high quality BHET.
Conclusions
We reported a method for the synthesis of uniform Fe2O3 nanoparticles on exfoliated MoS2 nanosheets due to the high mixing characteristics of the Taylor–Couette flow reactor. Exfoliated MoS2 nanosheets were produced in an aqueous solution with a thickness of few nanometers. Fe2O3 nanoparticles were synthesized with a size below 7 nm without thermal or organic solvent treatment. Fe2O3@MoS2 nanocomposite was synthesized at high production rate (1120 mg h−1) under mild conditions. Synthesized Fe2O3@MoS2 nanocomposite was used for glycolysis of PET and showed an approximately 90% yield of high quality BHET. The aggregation of Fe2O3 nanoparticles during the reaction was prevented by forming Fe2O3 nanoparticles on MoS2 nanosheets. Used Fe2O3@MoS2 nanocomposite was recovered by simple filtration of glycolysis product without decomposition or separation of Fe2O3 nanoparticles and MoS2 nanosheets. Recovered Fe2O3@MoS2 nanocomposite showed 94.4% catalytic activity of fresh Fe2O3@MoS2 nanocomposite. Our method for the synthesis of Fe2O3@MoS2 nanocomposite would be a promising strategy to produce large amount of catalyst necessary for large-scale catalytic processes.
Conflicts of interest
There are no conflicts to declare.
Acknowledgements
This work was supported by the National Research Foundation of Korea (NRF) grant funded by the Korea government (MSIT) (No. 2018R1A2A3075668) and the R&D Center for Valuable Recycling (Global-Top R&BD Program) of the Ministry of Environment (Project No. 2016002240001).
Notes and references
- A. Kumar and Q. Xu, Chem. Nanostruct. Mater., 2018, 4, 28–40 CAS.
- R. I. Jafri, N. Rajalakshmi and S. Ramaprabhu, J. Mater. Chem., 2010, 20, 7114–7117 RSC.
- X. Cai, Y. Luo, B. Liu and H.-M. Cheng, Chem. Soc. Rev., 2018, 47, 6224–6266 RSC.
- Z. Fu, H. Zhang, C. Si, D. Legut, T. C. Germann, Q. Zhang, S. Du, J. S. Francisco and R. Zhang, J. Phys. Chem. C, 2018, 122, 4710–4722 CrossRef CAS.
- H. Long, A. Harley-Trochimczyk, T. Pham, Z. Tang, T. Shi, A. Zettl, C. Carraro, M. A. Worsley and R. Maboudian, Adv. Funct. Mater., 2016, 26, 5158–5165 CrossRef CAS.
- Y.-C. Chen, A.-Y. Lu, P. Lu, X. Yang, C.-M. Jiang, M. Mariano, B. Kaehr, O. Lin, A. Taylor, I. D. Sharp, L.-J. Li, S. S. Chou and V. Tung, Adv. Mater., 2017, 29, 1703863 CrossRef PubMed.
- N. Bandaru, R. S. Kumar, D. Sneed, O. Tschauner, J. Baker, D. Antonio, S.-N. Luo, T. Hartmann, Y. Zhao and R. Venkat, J. Phys. Chem. C, 2014, 118, 3230–3235 CrossRef CAS.
- L. Nurdiwijayanto, R. Ma, N. Sakai and T. Sasaki, Inorg. Chem., 2017, 56, 7620–7623 CrossRef CAS PubMed.
- H. S. Sen, H. Sahin, F. M. Peeters and E. Durgun, J. Appl. Phys., 2014, 116, 083508 CrossRef.
- S. Najmaei, A. Mlayah, A. Arbouet, C. Girard, J. Leotin and J. Lou, ACS Nano, 2014, 8, 12682–12689 CrossRef CAS PubMed.
- Y. Cheng, S. Lu, F. Liao, L. Liu, Y. Li and M. Shao, Adv. Funct. Mater., 2017, 27, 1700359 CrossRef.
- J. Hu, C. Zhang, Y. Zhang, B. Yang, Q. Qi, M. Sun, F. Zi, M. K. H. Leung and B. Huang, Small, 2020, 16, 2002212 CrossRef CAS PubMed.
- M. B. Lejbini and P. Sangpour, Optik, 2019, 177, 112–117 CrossRef.
- X. Yang, H. Sun, L. Zhang, L. Zhao, J. Lian and Q. Jiang, Sci. Rep., 2016, 6, 31591 CrossRef CAS PubMed.
- C.-Y. Wu, W.-E. Chang, Y.-G. Sun, J.-M. Wu and J.-G. Duh, Mater. Chem. Phys., 2018, 219, 311–317 CrossRef CAS.
- Y. Chen, B. Song, X. Tang, L. Lu and J. Xue, Small, 2014, 10, 1536–1543 CrossRef CAS PubMed.
- N. D. Chuong, T. D. Thanh, N. H. Kim and J. H. Lee, ACS Appl. Mater. Interfaces, 2018, 10, 24523–24532 CrossRef CAS PubMed.
- T. Liu, S. Shi, C. Liang, S. Shen, L. Cheng, C. Wang, X. Song, S. Goel, T. E. Barnhart, W. Cai and Z. Liu, ACS Nano, 2015, 9, 950–960 CrossRef CAS PubMed.
- Y. A. Kabachii, A. S. Golub, S. Y. Kochev, N. D. Lenenko, S. S. Abramchuk, M. Y. Antipin, P. M. Valetsky, B. D. Stein, W. E. Mahmoud, A. A. Al-Ghamdi and L. M. Bronstein, Chem. Mater., 2013, 25, 2434–2440 CrossRef CAS.
- V. Nandwana, W. Huang, Y. Li and V. P. Dravid, ACS Appl. Nano Mater., 2018, 1, 1949–1958 CrossRef CAS.
- A. S. K. Kumar, S.-J. Jiang and J. K. Warchol, ACS Omega, 2017, 2, 6187–6200 CrossRef PubMed.
- A. K. Yadav, M. J. Barandiaran and J. C. Cal, Chem. Eng. J., 2012, 198–199, 191–200 CrossRef CAS.
- A. Igder, S. Pye, A. H. M. Al-Antaki, A. Keshavarz, C. L. Raston and A. Nosrati, RSC Adv., 2020, 10, 14761–14767 RSC.
- D. Seo, W.-S. Kim and D. H. Kim, Chem. Eng. J., 2020, 399, 125726 CrossRef CAS.
- J.-M. Jeong, H. G. Kang, H.-J. Kim, S. B. Hong, H. Jeon, S. Y. Hwang, D. Seo, B. E. Kwak, Y.-K. Han, B. G. Choi and D. H. Kim, Adv. Funct. Mater., 2018, 28, 1802952 CrossRef.
- H. Jeon, J.-M. Jeong, H. G. Kang, H.-J. Kim, J. Park, D. H. Kim, Y. M. Jung, S. Y. Hwang, Y.-K. Han and B. G. Choi, Adv. Energy Mater., 2018, 8, 1800227 CrossRef.
- J.-M. Jeong, S. B. Jin, H. J. Park, S. H. Park, H. Jeon, H. Suh, Y.-J. Park, D. Seo, S. Y. Hwang, D. H. Kim and B. G. Choi, Adv. Mater. Interfaces, 2020, 7(16), 2000599 CrossRef CAS.
- X. Zhang, M. Fevre, G. O. Jones and R. M. Waymouth, Chem. Rev., 2018, 118, 839–885 CrossRef CAS PubMed.
- A. Rahimi and J. M. García, Nat. Rev. Chem., 2017, 1, 0046 CrossRef.
- J. Zhang, X. Wang, J. Gong and Z. Gu, J. Appl. Polym. Sci., 2004, 93, 1089–1096 CrossRef CAS.
- F. Awaja and D. Pavel, Eur. Polym. J., 2005, 41, 1453–1477 CrossRef CAS.
- J. Chen, J. Lv, Y. Ji, J. Ding, X. Yang, M. Zou and L. Xing, Polym. Degrad. Stab., 2014, 107, 178–183 CrossRef CAS.
- S. R. Shukla and A. M. Harad, Polym. Degrad. Stab., 2006, 91, 1850–1854 CrossRef CAS.
- E. H. Acero, D. Ribitsch, G. Steinkellner, K. Gruber, K. Greimel, I. Eiteljoerg, E. Trotscha, R. Wei, W. Zimmermann, M. Zinn, A. Cavaco-Paulo, G. Freddi, H. Schwab and G. Guebitz, Macromolecules, 2011, 44, 4632–4640 CrossRef.
- M. Imran, D. H. Kim, W. A. Al-Masry, A. Mahmood, A. Hassan, S. Haider and S. M. Ramay, Polym. Degrad. Stab., 2013, 98, 904–915 CrossRef CAS.
- A. B. Raheem, Z. Z. Noor, A. Hassan, M. K. A. Hamid, S. A. Samsudin and A. H. Sabeen, J. Cleaner Prod., 2019, 225, 1052–1064 CrossRef CAS.
- D. E. Nikles and M. S. Farahat, Macromol. Mater. Eng., 2005, 290, 13–30 CrossRef CAS.
- N. George and T. Kurian, Ind. Eng. Chem. Res., 2014, 53, 14185–14198 CrossRef CAS.
- A. M. Al-Sabagh, F. Z. Yehia, A. M. F. Eissa, M. E. Moustafa, G. Eshaq, A. M. Rabie and A. E. ElMetwally, Polym. Degrad. Stab., 2014, 110, 364–377 CrossRef CAS.
- A. M. Al-Sabagh, F. Z. Yehia, A.-M. M. F. Eissa, M. E. Moustafa, G. Eshaq, A.-R. M. Rabie and A. E. ElMetwally, Ind. Eng. Chem. Res., 2014, 53, 18443–18451 CrossRef CAS.
- M. Imran, K. G. Lee, Q. Imtiaz, B.-K. Kim, M. Han, B. G. Cho and D. H. Kim, J. Nanosci. Nanotechnol., 2011, 11, 824–828 CrossRef CAS PubMed.
- I. Cano, C. Martin, J. A. Fernandes, R. W. Lodge, J. Dupont, F. A. Casado-Carmona, R. Lucena, S. Cardenas, V. Sans and I. Pedro, Appl. Catal., B, 2020, 260, 118110 CrossRef CAS.
- F. R. Veregue, C. T. P. Silva, M. P. Moisés, J. G. Meneguin, M. R. Guilherme, P. A. Arroyo, S. L. Favaro, E. Radovanovic, E. M. Girotto and A. W. Rinaldi, ACS Sustainable Chem. Eng., 2018, 6, 12017–12024 CrossRef CAS.
- L. Bartolome, M. Imran, K. G. Lee, A. Sangalang, J. K. Ahn and D. H. Kim, Green Chem., 2014, 16, 279–286 RSC.
- G. Park, L. Bartolome, K. G. Lee, S. J. Lee, D. H. Kim and T. J. Park, Nanoscale, 2012, 4, 3879–3885 RSC.
- M. Nemri, S. Charton and E. Climent, Chem. Eng. Sci., 2016, 139, 109–124 CrossRef CAS.
- A. S. George, Z. Mutlu, R. Ionescu, R. J. Wu, J. S. Jeong, H. H. Bay, Y. Chai, K. A. Mkhoyan, M. Ozkan and C. S. Ozkan, Adv. Funct. Mater., 2014, 24, 7461–7466 CrossRef CAS.
- S. Wang, X. Wang and J. H. Warner, ACS Nano, 2015, 9, 5246–5254 CrossRef CAS PubMed.
- H. Pan, X. Meng, X. Qi and G. Qin, CrystEngComm, 2017, 19, 6333–6338 RSC.
- Y. Zhao, W. Cai, Y. Shi, J. Tang, Y. Gong, M. Chen and Q. Zhong, ACS Sustainable Chem. Eng., 2020, 8, 12603–12611 CrossRef CAS.
- A. M. Al-Sabagh, F. Z. Yehia, D. R. K. Harding, G. Eshaq and A. E. ElMetwally, Green Chem., 2016, 18, 3997–4003 RSC.
Footnote |
† Electronic supplementary information (ESI) available: Dimension of the Taylor–Couette flow reactor, AFM image of MoS2 nanosheets, BET surface area of pristine MoS2, MoS2 nanosheets, and Fe2O3@MoS2 nanocomposite, TEM image of Fe2O3@MoS2 nanocomposite with different initial Fe : Mo ratio, TGA for Fe2O3@MoS2 nanocomposite, HPLC data for glycolysis of PET, recovered Fe2O3@MoS2 nanocomposite, comparison table for production of Fe2O3@MoS2 nanocomposite and previous reports, ICP-OES for Fe2O3@MoS2 nanocomposite, and BHET, comparison table for glycolysis reaction using Fe2O3@MoS2 nanocomposite and previous reports. See DOI: 10.1039/d1ra02335g |
|
This journal is © The Royal Society of Chemistry 2021 |
Click here to see how this site uses Cookies. View our privacy policy here.