DOI:
10.1039/D1RA01626A
(Paper)
RSC Adv., 2021,
11, 20926-20932
Application of decarboxylation reactions for improvement of dielectric properties of a methacrylic polymer†
Received
2nd March 2021
, Accepted 5th June 2021
First published on 14th June 2021
Abstract
In this work, we present a method based on thermally induced decarboxylation to solve the incompatibility of dielectric properties and the developability in aqueous developer solution of dielectric materials for the application in photodefinable insulating materials. Herein, malonic acid 2-hydroxyethyl methacrylate monoester, a methacrylate monomer with β-keto acid is synthesized via phosphotungstic acid catalyzed esterification of 2-hydroxyethyl methacrylate and malonic acid. Further polymerisation is conducted with the obtained monomer to prepare poly(2-hydroxyethyl methacrylate-co-malonic acid 2-hydroxyethyl acrylate monoester). The thermally induced decarboxylation behaviors of the prepared polymer are confirmed with TGA, pyrolysis-GCMS analysis, and IR analysis. Df/Dk tests and dissolution tests are carried out to investigate the influences of decarboxylation on the dielectric properties and dissolubility in aqueous solution, respectively. The results demonstrate that the significant changes in dielectric properties and dissolubility are due to the thermally induced decarboxylation.
1 Introduction
With the rapid development of wireless technology and the coming of the 5G era, traditional dielectric materials will not be satisfactory anymore for the fabrication of printed circuit boards (PCBs). Particularly for high frequencies, the risk of signal loss, such as signal attenuation and data-integrity lapses, becomes remarkable when using those dielectric materials with a high dielectric constant (Dk) and dielectric loss tangent (Df). As is shown in eqn (1),1 the signal loss coming from dielectric materials (αD) is proportional to the frequency f, Df, and the square root of Dk. |
 | (1) |
Furthermore, the miniaturization, multifunction, and high performance requirements of semiconductor devices have been forcing scientists, mechanical engineers, physicists, as well as chemists to work together to unlock significant values of every inch within the devices. By creating finer lines and spaces, smaller vias/holes, and higher connection pad density, it helps to improve the using efficiency of the space in electronic semiconductor devices. Traditional laser irradiation technologies such as CO2 laser-based build-up process has reached its limitation of Φ30 μm of vias formed from the insulating materials.2 New technologies with photodefinable insulating materials will dominate the market for fabrication of semiconductor devices for they can form fine patterns with small dimensions and patterns with different sizes in one shot by photolithography.
The photodefinable insulating materials for photolithography are usually combined together with other components. Those components contains initiation systems including photoinitiation systems (and thermoinitiation systems), non-photosensitive dielectrics and so on. Researchers focus mainly on photo-initiation system including photoinitiators and photosensitizers, and photodefinable insulating materials including photocurable monomers, oligomers, and macromolecules. For photosensitive insulating materials, there are several types of reported materials3 including photosensitive polyimides, photosensitive polybenzoxazoles, and photosensitive engineering plastics. The addition of non-photosensitive dielectrics with certain properties could improve the performance and processability of the products, for instance decrease of the dielectric constant, improvement of the developability, and so on. There are mountains of reported polymers with favorable dielectric properties,4 such as polyimides, polybenzoxazoles, and polynorbornene, etc., but the interest from researchers in the developability, especially the developability in aqueous developers is much less than that in other properties.
In addition to the photocuring, development, however, also becomes important. The residue from incomplete development will results in the bad connection within devices. As the global warming has a serious impact on the environment and the earth, environmentally friendly aqueous development has become widely used. That means the used dielectric materials for photolithography should exhibit good developability in aqueous developer solutions for the applications. The dielectric materials with low Df/Dk, however, are usually difficult to develop in aqueous developer solution.5 The incompatibility between the environmental issues and the applicability coming from the dielectric property prevents further development of the fabrication of PCBs.
To solve the problem of difficult development of dielectric materials with low solubility in aqueous developer solution, Oyama and his co-workers reported a method named Reaction Development Patterning (RDP) technology.6 The reported RDP is usually performed during development. Although the developer is a mixture of several solvents, organic solvents are still necessary including ethanolamine, N-methylpyrrolidone, and so on. In this work, we proposed a method to regulate both the dielectric properties and solubility based on thermally induced decarboxylation reactions. A polymer containing β-keto acid units was designed and prepared. Before decarboxylation, β-keto acid-based polymers could be developed readily in aqueous developer solution for the highly hydrophilic carboxylic acid groups of β-keto acid provide favourable solubility. With thermal treatment, the carboxylic acid groups can be easily converted to relatively hydrophobic ketone with better dielectric performance.7 This method guarantees both the developability and final dielectric properties of dielectric materials.
2 Experimental
2.1 Materials and instrumentation
Unless otherwise specified, reagents and solvents were purchased from FUJIFLIM Wako and used without further purification. The A53 Purex® films were purchased from Toyobo Film Solutions Ltd.
1H NMR (300 MHz) and 13C NMR (75 MHz) spectroscopy was performed on AVANCE 300 Spectrometer from BRUKER at room temperature using tetramethylsilane as internal standards. Fourier transform infrared spectroscopy (IR) was performed on Excalibur Series FTS 3000 Infrared Spectrometer from Bio-Rad. Thermo-gravimetric differential thermal analysis (TG-DTA) was performed on TG/DTA 6300 from Seiko Instruments Inc. Pyrolysis-GCMS was performed on Frontier Lab EGA/PY-3030D Pyrolysis device/Agilent Technologies GC/MS 5977B. Df/Dk tests were performed on Agilent Technologies Vector Network Analyzer E8364B, CP531 (10 GHz resonator, Kanto Electronic Application and Development) and CPMA-V2 program. The measurements of the film thicknesses were performed on Dektak XT® Stylus Profiler from BRUKER.
2.2 Synthesis of malonic acid 2-hydroxyethyl methacrylate monoester (HEMAMalonate)
Following the modified procedure shown in Scheme 1,8 to a flask equipped with a CaCl2 drying tube, a mixture of malonic acid and 2-hydroxyethyl methacrylate (HEMA) with molar ratio of 1
:
1 was added, followed by addition of phosphotungstic acid as a catalyst with a weight ratio of 0.7% in total, and then the mixture was heated up to 75 °C and kept at this temperature for 4 h. After cooling down, the mixture was dissolved in 10 wt% Na2CO3 aqueous solution and got a phase separation. The organic phase mainly containing a diester byproduct was removed. The aqueous phase was firstly washed with a small amount of ethyl acetate to further remove the remaining diester byproduct after addition of 0.3 wt% of 4-methoxyphenol as an inhibitor, and then neutralized with HCl aqueous solution, and further phase separation took place again. The oil phase was collected as the raw product, and washed with diluted brine once, and saturated brine twice, and then dried with Na2SO4 to get the final product containing 15–25 mol% HEMA and around 7 mol% ethyl acetate with a yield of around 45% as a yellowish to reddish liquid.
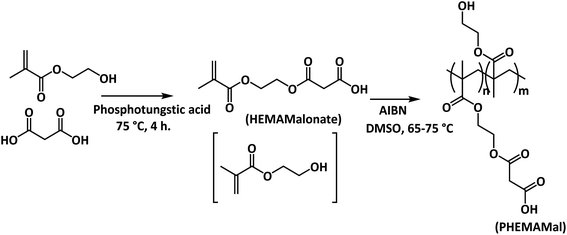 |
| Scheme 1 Synthesis of malonic acid 2-hydroxyethyl methacrylate monoester (HEMAMalonate) and poly(2-hydroxyethyl methacrylate-co-malonic acid 2-hydroxyethyl acrylate monoester) (PHEMAMal). | |
2.3 Synthesis of poly(2-hydroxyethyl methacrylate-co-malonic acid 2-hydroxyethyl acrylate monoester) (PHEMAMal)
AIBN was recrystallized three time from ethanol in prior to use and stored at −20 °C. Following Scheme 1, a solution of HEMAMalonate (36.0 g) in DMSO (140 mL) with 0.568 g of AIBN (3.46 mmol) was bubbled with nitrogen for 1 h at room temperature, and then heated up to 65 °C and kept stirring at 65 °C for 14 h, and then heated up to 75 °C and kept for another 2 h. The raw product was isolated by precipitation from water, and then dissolved in acetone and precipitated twice from water, and once from heptane, and then dried in vacuum oven at 65 °C to get the final product as colorless powder. Yield is 78% (28.20 g). Mw = 349 kDa, Mw/Mn = 1.78 (GPC data, N-methylpyrrolidone as an eluent).
2.4 Preparation of PHEMAMal film
Solution of PHEMAMal in acetone (ca. 30 wt%) was coated onto A53 Purex® films, dried at room temperature for 10 min, and then 60 °C for 15 min, then 80 °C for another 20 min to remove the solvent and get sample films with a thickness of about 80 μm. Then the obtained films were further cut into 7 cm × 5 cm for Df/Dk test.
2.5 Dissolution test
Solution of PHEMAMal in acetone/1-methoxyl-2-propanol (v/v = 3/1, ca. 30 wt% polymer in solvent) was coated onto silicon wafer by bar coating, and dried at 60 °C for 20 min, then 80 °C for 20 min, and then 120 °C for 20 min. Half of the sample was further treated at 150 °C for 2 h. Then the sample was cut into ca. 1 cm × 2 cm for the dissolution tests.
The dissolution tests were conducted using 1 wt% of Na2CO3 aqueous developer solution. Prepared samples were soaked into the developer solution for 30 s, 1 min, 2 min, and 3 min, respectively, and then dried with nitrogen flow. The thicknesses of the samples before and after development were recorded.
3 Results and discussion
3.1 Synthesis
Following the modified literature procedure8 (seen Scheme 1), phosphotungstic acid was used as a catalyst for preparation of malonic acid 2-hydroxyethyl methacrylate monoester (HEMAMalonate). By NMR characterization (Fig. S1 and S2†), the product was confirmed that around 15–25 mol% of starting material, 2-hydroxyethyl methacrylate (HEMA) remained as impurity. For HEMA would not influence the final conclusion, no further purification was performed. The thermal polymerization of the obtained monomer was conducted in DMSO with AIBN as the thermal initiator (Scheme 1), and gave poly(2-hydroxyethyl methacrylate-co-malonic acid 2-hydroxyethyl acrylate monoester) (PHEMAMal) in a yield of 78% with a weight average molecular weight (Mw) of 349 kDa and polydispersity index (PDI = Mw/Mn) of 1.78.
3.2 Preparation of PHEMAMal films for dielectric property tests
Because the polymer was difficult to re-dissolve in organic solvent after workup, it was difficult to prepare a self-standing film from the obtained polymer. Although the polymerization was conducted in DMSO, the obtained dry polymer was difficult to re-dissolve in DMSO, as well as in other organic solvents, such as acetone which was used for workup, toluene, and so on. Moreover, the prepared films were too brittle to keep in one piece when they were peeled off from the substrate. Therefore, the idea was carried out that the preparation of films was conducted before the polymer was dried up. Firstly, during the workup, after precipitation three times from water and once from heptane, a solution with a concentration of around 30 wt% of polymer was made by re-dissolving the precipitated solid in acetone directly. And then, the prepared solution was used for bar coating. The films were finally prepared after removal of the solvent by keeping the films at room temperature for 15 min, then 50 °C for 10 min, and then 80 °C for 10 min, sequentially. The prepared films were ready to be used for dielectric tests.
3.3 Thermally induced decarboxylation behavior of prepared polymer and films
3.3.1 TGA analysis. In this work, we proposed to regulate the dielectric properties and the dissolubility of the materials in developer solution via thermally induced decarboxylation (Scheme 2). Before thermal treatment, the prepared polymer possesses high solubility because of the existence of carboxylic acid groups, while after thermal treatment, the dielectric properties will be improved for the decarboxylation reaction converts carboxylic acid groups into ketones. Firstly, thermo-gravimetric differential thermal analysis (TG-DTA) was employed to study the temperature-dependent behaviors of the prepared polymer and films. The solid polymer powder (PolymPowder) and the film prepared with the obtained polymer (PolymFilm) were characterized with TG-DTA under the air and a nitrogen atmosphere, respectively. The tests ran from 40 °C to 400 °C at a heating rate of 10 K min−1. The results are shown in Fig. 1.
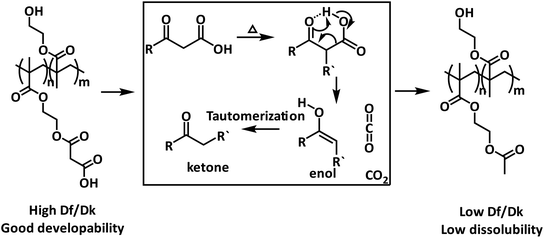 |
| Scheme 2 Schematic proposed mechanism of decarboxylation reaction with PHEMAMal. | |
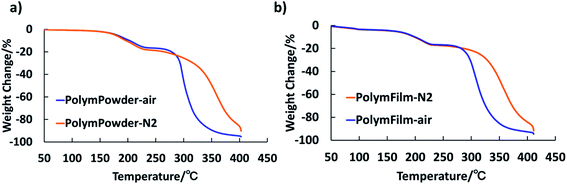 |
| Fig. 1 TG results of (a) the obtained PHEMAMal polymer powder (PolymPowder), (b) the film prepared with PHEMAMal polymer (PolymFilm), from 50 °C to 400 °C with a heating rate of 10 K min−1. | |
As can be seen in Fig. 1a and b, the thermally induced weight loss started slowly at around 130 °C, quickly from around 170 °C, and cut off at around 230 °C for both samples of polymer power and polymer films. It can also be seen that the weight loss at cutoff temperature shifted a bit for PolymPowder at different atmospheres, while it kept almost the same for PolymFilm. Moreover, the weight losses of PolymPowder and PolymFilm at the cutoff temperature matched with each other: around 17.0% for PolymPowder and 16.6% for PolymFilm. The weight losses were also in agreement with theoretical value of 17.3% based on the proposed decarboxylation reaction, suggesting that during thermal treatment, decarboxylation reactions took place. From Fig. 1, it can conclude that below 250 °C, the test atmosphere has little influence on thermal behaviors of the polymer, suggesting that it also has little influence on the proposed decarboxylation reaction in this system within the time range of the tests. Above 250 °C, the polymer decomposes more slowly in nitrogen atmosphere than in air atmosphere, which might be attributed to the oxidation reaction.
3.3.2 Pyrolysis-GCMS. TG-DTA was employed to confirm the decarboxylation reaction from the point of view of mass balance. The pyrolytic products were further characterized with pyrolysis-GCMS from the point of view of reaction—the generated gases during thermal treatment were analysed qualitatively. The results are shown in Fig. S3–S5 in ESI,† respectively. Beside the residual solvent, as DMSO and heptane, there were three more components: CO2, and residual monomers, as HEMA and HEMAMalonate in the MS spectra at retention time of, 1.7 min, 10.7 min, and 12.3 min, respectively. CO2, the typical product generated from decarboxylation reaction, was obviously observed, providing an evidence that the thermal treatment induced decarboxylation reactions. The proposed mechanism of decarboxylation is schematically illustrated in Scheme 2. For decarboxylation, a ketone is produced from a β-keto carboxylic acid, meanwhile a molecule of CO2 is released. The generated CO2 suggested the decarboxylation reaction during thermal treatment.
3.3.3 IR characterization. It was proposed that after thermal treatment, the carboxylic acids would convert to ketones. To provide more concreate evidences, IR spectroscopy was employed to characterize the polymer film before and after thermal treatment from the point of view of the chemical structure. As shown in Fig. 2, the differences are mainly located in the regions of 1200–1300 cm−1, 1700–1800 cm−1, and 2500–2700 cm−1, respectively. In the region of 1200–1300 cm−1, the band at 1263 cm−1 assigned to stretching vibrations of C–O from carboxylic acid disappeared after thermal treatment, suggesting carboxylic acid groups disappeared after thermal treatment. In the region of 1630–1830 cm−1, the carbonyl groups usually have strong absorption, showing a sharp and strong peak. Before decarboxylation, there should be three kinds of carbonyl groups from: (1) HEMA units or the HEMA segment of HEMAMalonate units, (2) the ester segment between HEMA and malonic acid of HEMAMalonate, and (3) the residual acid segment of malonic acid of HEMAMalonate. After decarboxylation, the signal from the residual acid segment will disappear if the decarboxylation completes. In this region, it can be seen that the band at 1762 cm−1 shrank to the extent hardly to be observed. Moreover, in the region of 2500–2700 cm−1, the broad signal also decreases to nearly flat after thermal treatment. This broad signal is from the stretching vibrations of O–H from the residual acid segment. All these three main differences strongly support that the decarboxylation took place during thermal treatment, and after 2 h at 150 °C treatment, the decarboxylation was close to completion.
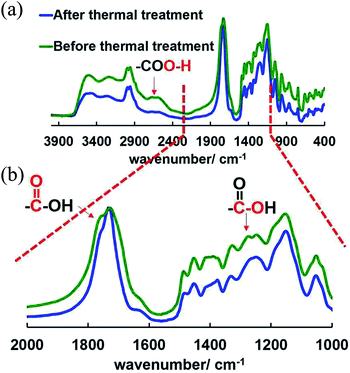 |
| Fig. 2 IR analysis of PHEMAMal polymer film before and after thermal treatment at 150 °C for 2 h (after normalization): (a) full spectra, (b) zoomed-in spectra of the region of 1000–2000 cm−1. | |
3.3.4 Isothermal TG analysis. All the TG-DTA, pyrolysis-GCMS, and IR characterization support the proposed decarboxylation mechanism. Moreover, IR measurements concludes that after thermal treatment at 150 °C for 2 h, the decarboxylation is closed to completion. Further tests with isothermal TG analysis were carried on to support this conclusion. After treatment at 150 °C for 2 h, the weight losses are 13.9% and 15.9% under the air atmosphere and a nitrogen atmosphere, respectively, as can be seen in Fig. 3. The weight loss from isothermal TG under a nitrogen atmosphere suggests that there are only 4 mol% of the carboxylic acid groups left based on the total weight loss of 16.6%. This result is highly in agreement with that observed by IR measurements. The weight loss difference under different atmospheres might result from the oxidation of the generated intermediates of the decarboxylation reactions under the air atmosphere in presence of oxygen. Under a nitrogen atmosphere, only decarboxylation and decomposition takes place while under the air atmosphere, reversal oxidation may also occur simultaneously, as a result, there is a delay under the air atmosphere. Moreover, the weight loss after 1 h thermal treatment reaches to 13.4%, indicating that decarboxylation took place significantly even with the thermal treatment at 150 °C for 1 h. It was reported that the decarboxylation of malonic acid is a first-order reaction,9 here the plot of the time-dependent weight loss versus thermal treatment time also shows the reaction in our system is a pseudo-first-order reaction.
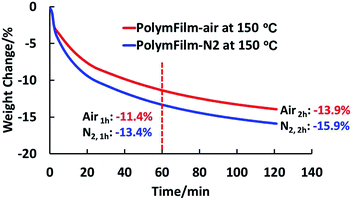 |
| Fig. 3 Time-dependent weight loss of PolymFilm during thermal treatment at 150 °C with TG-DTA. | |
3.4 Dielectric properties of prepared films
The dielectric properties of the dielectric materials in final form, according to eqn (1), contribute significantly to the dielectric loss. In this work, to solve the incompatibility between the dielectric properties and developability in aqueous developer solution, PHEMAMal was designed with a changeable dielectric properties and solubility. The dielectric properties before and after thermal treatment were characterized with the prepared films. For the films prepared with PHEMAMal exhibited brittleness, the Df/Dk measurements were performed together with the substrate A53 Purex® films. The results are summarized in Fig. 4. As can be seen, the Df value of the polymer film with the substrate decreases from 0.117 to 0.059 after thermal treatment for 2 h, and Dk from 4.24 to 3.42. In contrast, the Df value and Dk value of the substrate A53 Purex® film itself almost does not change at all. Based on the previous conclusion that decarboxylation reaction takes place during the thermal treatment, with increasing the thermal treatment time, the carboxylic acid units continuously converts to ketones. The decrease of Df/Dk should be attributed to the conversion of carboxylic acid units to ketones.
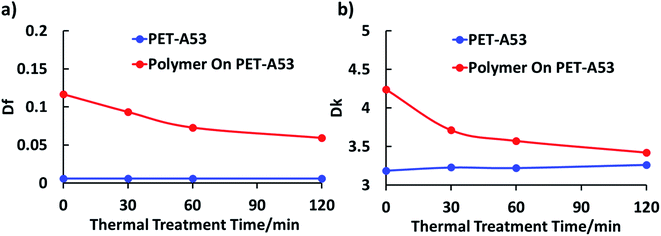 |
| Fig. 4 Df (a) and Dk (b) (at 10 GHz) of PHEMAMal polymer based on the prepared films after thermal treatment at 150 °C. | |
Increasing the amount of polar functionalities (for example hydroxyl groups, carboxylic groups, etc.) in a polymer will increase the dielectric properties significantly. Chung and co-workers10 doubled the value of Dk of isotactic polypropylene dielectrics by addition of –OH functionalities, and Risse and co-workers11 achieved higher Dk by physically addition of fillers with polar cyanide than that with non-polar methylhydrosiloxane to a dielectric elastomer actuator, respectively. On the contrary, the reduction of polar functionalities, such as –OH, will decrease the Dk. Semi-quantitatively, from the Clausius–Mossotti relationship,12 we can get eqn (2):13
|
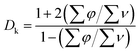 | (2) |
where
φ is the molar polarizability, and
ν is the molar free volume. During thermal treatment, the change of decarboxylation can approximately be regarded as a conversion of a methylene group, a ketone group and a hydroxyl group to a methyl group. Because of high molar polarizability and low molar free volume of hydroxyl group, the elimination of hydroxyl group will result in decrease of
Dk. Usually, a higher
Dk will in turn generate a higher dielectric loss.
12a Therefore, with thermal treatment, the value of
Df decreased. The results are perfectly in agreement with this conclusion.
3.5 Dissolution behaviors in aqueous developer solution
To get the targeted patterns for PCBs fabrication, after photochemical reaction, no matter what kind of photosensitive materials including the negative type and positive type is used, the unnecessary part will be developed. The solubility of the components such as the used resin in the formulation influences the developability significantly as well as the final performance of the devices. If the solubility is low, after development, there is still some resin remained, which will result in the low conductivity of the circuit. As a result, the solubility of the used resin becomes one of the key factors for the final performance of the semiconductor devices. In this work, the developability of the prepared polymer was characterized by dissolution test in a 1 wt% Na2CO3 aqueous developer solution. After soaking the films on silicon wafer into the developer solution for 30 s, 1 min, 2 min, and 3 min, respectively, the thicknesses of the films were then recorded. As can be seen in Fig. 5, the dissolution rates of the prepared films before and after thermal treatment at 150 °C are totally different. Before thermal treatment, it shows the dissolution rate is 0.0525 μm s−1 while after thermal treatment, the dissolution rate is almost 0 μm s−1. And the images of the films for tests are shown in Fig. 6, the film without thermal treatment dissolved into the developer solution during the test and became thinner after development for 3 min while the film after thermal treatment did not change at all after development. The obtained results are in agreement with our proposal. Before thermal treatment, the carboxylic acid units provides a favourable solubility in the aqueous basic developer solution. After thermal treatment, the solubility of polymer will be lowered dramatically. The reason for this change is that the highly hydrophilic β-keto carboxylic acid units in polymer chains are converted into relatively hydrophobic ketones which are not soluble in aqueous solution.
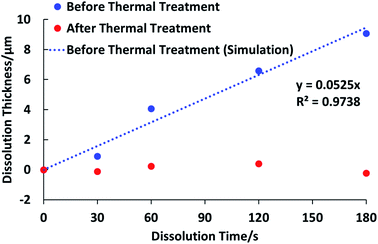 |
| Fig. 5 The dissolution behaviors in 1 wt% Na2CO3 aqueous developer solution of PHEMAMal before and after thermal treatment at 150 °C for 2 h. | |
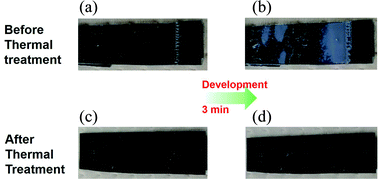 |
| Fig. 6 The images of the films on silicon substrates for dissolution tests: before thermal treatment (a) before development and (b) after development for 3 min, and after thermal treatment at 150 °C for 2 h (c) before development and (d) after development for 3 min. | |
4 Conclusions
In this work, we proposed a novel idea to solve the incompatibility between the dielectric properties and developability in aqueous developer solution of dielectric materials for the application of photosensitive dielectric materials. Based on thermally induced decarboxylation reaction, we could regulate the dielectric properties and dissolubility of the prepared polymer. The proposal was successfully evident with experimental details: the decarboxylation reaction was supported with TG-DTA, IR, and pyrolysis-GCMS analysis, the dielectric properties of the designed polymer before and after thermal treatment were characterized and exhibited significant improvement for practical application, and the different dissolubility before and after thermal treatment in environmentally friendly aqueous developer solution guaranteed the developability. Although the prepared polymer did not show an extremely low Df/Dk behaviors after thermal treatment, this idea for further development of new dielectric materials opens a window to consider both the environmental effects and the dielectric performance in practical applications.
Conflicts of interest
There are no conflicts to declare.
Acknowledgements
The authors would like to thank Mr Noriyuki Nakayama for the support on AFM measurements (seen in ESI†) and Miss Xing Lai for the contribution on the cartoon in the Table of Content.
Notes and references
- T. Okubo, T. Sudo, T. Hosoi, H. Tsuyoshi and F. Kuwako, IEEE Electrical Design of Advanced Packaging and Systems Symposium (EDAPS), Nara, Japan, Dec., 2013 Search PubMed.
- K. Iwashita, T. Katoh, A. Nakamura, Y. Murakami, T. Iwasaki, Y. Sugimasa, J. Nunoshige and H. Nakano, J. Photopolym. Sci. Technol., 2015, 28, 93 CrossRef CAS.
-
(a) M. Fu, T. Higashihara and M. Ueda, Polym. J., 2017, 1–20 Search PubMed;
(b) K. Zoschke, T. Fischer, M. Topper, K. Samulewicz, O. Wunsch, J. Roder, M. Lutz, O. Ehrmann and H. Reichl, IEEE Trans. Adv. Packag., 2010, 33(2), 398–407 CAS.
-
(a) X. Zhao and H. Liu, Polym. Int., 2010, 59, 597–606 CAS;
(b) G. Maier, Prog. Polym. Sci., 2001, 26, 3–65 CrossRef CAS;
(c) Z. Ahmad, Polymer Dielectric Materials, in Dielectric Material, ed. M. A. Silaghi, IntechOpen, London, UK, 2012, ch. 1, DOI:10.5772/50638.
- T. Kakutani, D. Okamoto, Z. Guan, Y. Suzuki, M. Ali, A. Watanabe, M. Kathaperumal and M. Swaminathan, IEEE 70th Electronic Components and Technology Conference (ECTC), Florida, USA, May, 2020 Search PubMed.
-
(a) T. Oyama, A. Kasahara, M. Yasuda and A. Takahashi, J. Photopolym. Sci. Technol., 2016, 29, 273 CrossRef CAS;
(b) S. Sugawara, M. Tomoi and T. Oyama, Polym. J., 2007, 39, 129 CrossRef CAS;
(c) T. Oyama, A. Kitamura, E. Sato and M. Tomoi, J. Polym. Sci., Part A: Polym. Chem., 2006, 44, 2694 CrossRef CAS.
-
(a) M. W. Logue, R. M. Pollack and V. P. Vitullo, J. Am. Chem. Soc., 1975, 97, 6868 CrossRef CAS;
(b) E. J. Corey, J. Am. Chem. Soc., 1953, 75, 1163 CrossRef CAS.
- S. Shanmugam, B. Viswanathan and T. K. Varadarajan, J. Mol. Catal. A: Chem., 2004, 223, 143 CrossRef CAS.
- L. Clark, J. Phys. Chem., 1963, 67, 138 CrossRef CAS.
- X. Yuan, Y. Matsuyama and T. C. Mike Chung, Macromolecules, 2010, 43, 4011–4015 CrossRef CAS.
- S. Risse, B. Kussmaul, H. Krüger and G. Kofod, Adv. Funct. Mater., 2012, 22(18), 1–5 CrossRef.
-
(a) L. Zhu, J. Phys. Chem. Lett., 2014, 5, 3677–3687 CrossRef CAS PubMed;
(b) S. Bonardd, V. Moreno-Serna, G. Kortaberria, D. Díaz, A. Leiva and C. Saldías, Polymers, 2019, 11, 317–326 CrossRef PubMed;
(c) T. M. Levitskaya and B. K. Sternberg, Electrical Spectroscopy of Earth Materials, Elsevier Inc., Amsterdam, NL, 2019, pp. 3–15 Search PubMed.
- I. Ogura, DIC Tech. Rev., 2001, 7, 1–12 Search PubMed.
Footnote |
† Electronic supplementary information (ESI) available. See DOI: 10.1039/d1ra01626a |
|
This journal is © The Royal Society of Chemistry 2021 |
Click here to see how this site uses Cookies. View our privacy policy here.