DOI:
10.1039/D1RA01588E
(Paper)
RSC Adv., 2021,
11, 13061-13076
Preparation, characterization and application of MgFe2O4/Cu nanocomposite as a new magnetic catalyst for one-pot regioselective synthesis of β-thiol-1,4-disubstituted-1,2,3-triazoles†
Received
27th February 2021
, Accepted 30th March 2021
First published on 7th April 2021
Abstract
Magnesium ferrite magnetic nanoparticles were synthesized by a solid-state reaction of magnesium nitrate, hydrated iron(III) nitrate, NaOH and NaCl salts and then calcined at high temperatures. In order to prevent oxidation and aggregation of magnesium ferrite particles, and also for preparing a new catalyst of supported copper on the magnetic surface, the MgFe2O4 was covered by copper nanoparticles in alkaline medium. Magnetic nanoparticles of MgFe2O4/Cu were successfully obtained. The structure of the synthesized magnetic nanoparticles was identified using XRD, TEM, EDS, FT-IR, FESEM and VSM techniques. The prepared catalyst was used in the three component one-pot regioselective synthesis of 1,2,3-triazoles in water. The various thiiranes bearing alkyl, allyl and aryl groups with terminal alkynes, and sodium azide in the presence of the MgFe2O4/Cu nanocatalyst were converted to the corresponding β-thiolo/benzyl-1,2,3-triazoles as new triazole derivatives. The effects of different factors such as time, temperature, solvent, and catalyst amount were investigated, and performing the reaction using 0.02 g of catalyst in water at 60 °C was chosen as the optimum conditions. The recovered catalyst was used several times without any significant change in catalytic activity or magnetic property.
1. Introduction
In recent decades, 1,2,3-triazoles have attracted considerable attention due to their important biological and pharmacological activities such as analgesic,1 local anaesthetic,2 antimicrobial,3,4 anti HIV,5 anticancer,6 antiallergic,7 anticonvulsant,8 antiproliferative,9 antiviral, antitubercular,10 antifungal,11 antibacterial,12 antioxidants,13 antimalarial,14 and anti-inflammatory activities.15
Huisgen 1,3-dipolar cycloaddition between an azide and alkyne has rapidly gained importance for its potential to manufacture drug targets with different biological significance.6 Recently, one-pot synthesis of β-hydroxy-1,2,3-triazoles has been reported through the click reaction of azides, alkynes and epoxides catalyzed by various copper catalysts.16–31 Although nucleophilic ring opening of strained three-membered heterocycles such as epoxides and aziridines is easily carried out using different nucleophiles such as azides and amines, no cases have been reported yet for 1,3-dipolar cycloaddition between azide, alkyne and thiiranes.
Multi-component reactions (MCRs) are reactions in which three or more reactants react to generate only one product. MCRs present a convenient synthetic procedure for producing complex molecules with structural variety and molecular intricacy.32 These kinds of reactions provide major benefits like environmental compatibility, high efficiency, quick and plain performance, and reducing the reaction time and saving energy. Compared to conventional methods, these reactions require fewer steps to achieve the final product and can be performed in one-pot. Therefore, MCRs play significant roles in different research fields such as biomedical, synthetic organic, generating libraries of bioactive compounds, pharmaceutical and drug discovery research, industrial chemistry etc.33–36 An ideal multicomponent reaction permits the concurrent addition of all reactants, reagents and catalysts under the same reaction conditions. One-pot reactions show an efficient strategy in modern synthetic chemistry.37 Minimizing the number of synthetic steps in obtaining products from starting reactants is highly favorable in organic synthesis. The perfect regioselectivity and high purity of desired products, and excellent yields are among the other remarkable advantages of multicomponent one-pot reactions.
Ferrite nanoparticles due to their magnetic property are easily separable. Recently, they have received great attention in biomedicine,38–40 and organic synthesis.41–44 Nevertheless, the nano-ferrites have hydrophobic surfaces with a large surface to volume ratio and strong magnetic dipole–dipole attractions, and they always suffer from adsorption problems because of their intense tendency of self-aggregation and low quantity of functional groups.45,46 To prevent agglomeration of magnetic nanoparticles (MNPs) and improve their efficiency, surface coating of the MNPs is required.47 Aqueous MNP dispersions can be achieved by surface coating with copper nanoparticles.
In continuation of pioneering works on nano-ferrites,48–54 herein, we wish to report an efficient, three-component click reaction protocol for synthesis of β-thiol-1,4-disubstituted-1,2,3-triazoles as new triazole derivatives from sodium azide, thiiranes, and terminal alkynes in the presence of MgFe2O4/Cu magnetic nanoparticles as a novel and environmentally friendly heterogeneous catalyst in water (Scheme 1).
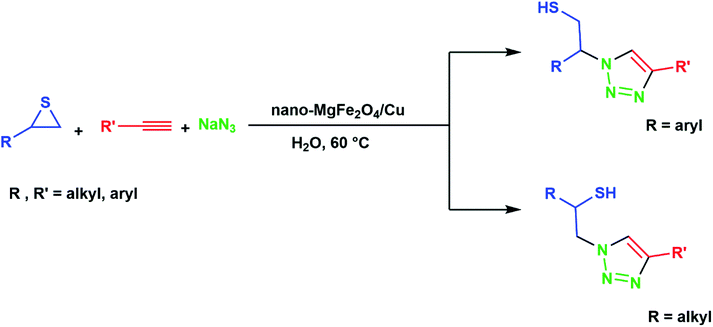 |
| Scheme 1 Synthesis of β-thiol-1,4-disubstituted-1,2,3-triazoles from thiiranes catalyzed by MgFe2O4/Cu. | |
2. Experimental
2.1. Instruments and materials
All materials were purchased from the Merck and Aldrich Chemical Companies with the best quality and they were used without further purification. IR and 1H/13C NMR spectra were recorded on Thermo Nicolet Nexus 670 FT-IR and 500 MHz Bruker Avance spectrometers, respectively. Melting points were measured on an Electrothermal IA9100 microscopic digital melting point apparatus. The synthesized nanocatalyst was characterized by XRD on a Bruker D8-Advanced diffractometer with graphite-monochromatized Cu Kα radiation (λ = 1.54056 Å) at room temperature. TEM image was recorded using an EM10C-100 kV series microscope from the Zeiss Company, Germany. FESEM images were determined using FESEM-TESCAN. The energy dispersive X-ray spectrometer (EDS) analysis was taken on a MIRA3 FE-SEM microscope (TESCAN, Czech Republic) equipped with an EDS detector (Oxford Instruments, UK). Magnetic property of synthesized nanocatalyst was measured using a VSM (Meghnatis Daghigh Kavir Co., Kashan Kavir, Iran) at room temperature. HRMS analyses were also carried out in the electron impact mode (EI) at 70 eV. The Cu content on the catalyst was determined by Perkin Elmer Optima 7300DV ICP-OES analyzer.
2.2. Synthesis of MgFe2O4 nanoparticles
MgFe2O4 nanoparticles were synthesized by a solid-state procedure according to our reported investigation.48 Briefly, in a mortar, Mg(NO3)2·6H2O (0.512 g, 2 mmol), Fe(NO3)3·9H2O (1.61 g, 4 mmol), NaOH (0.64 g, 16 mmol), and NaCl (0.232 g, 4 mmol) were mixed in a molar ratio of 1
:
2
:
8
:
2 and ground together for 55 min. The reaction was carried out with the release of heat. After 5 minutes of grinding, the mixture became pasty and its color changed to dark brown. For removing the additional salts, the obtained mixture was washed with double-distilled water for several times. The produced mixture was dried at 80 °C for 2 h and it was then calcined at 900 °C for 2 h to obtain the MgFe2O4 nanoparticles as a dark brown powder.
2.3. Preparation of MgFe2O4/Cu nanocomposite
In a round-bottom flask, a solution of CuCl2·2H2O (0.68 g, 4 mmol) in distilled water (50 mL) was prepared and then MgFe2O4 (1 g) was added. The mixture was stirred vigorously for 30 min and followed by gradually addition of KBH4 powder (0.1 g) in order to reduce Cu2+ cations to copper nanoparticles. The stirring of mixture was continued at room temperature for 1 h. The black MgFe2O4/Cu nanocomposite was separated using a magnet, washed with distilled water and then dried under air atmosphere.
2.4. Solvent-free synthesis of thiiranes from epoxides: general procedure
The various thiiranes were prepared using a solvent-free method reported in our previous research.55 Briefly, a mixture of epoxide (1 mmol) and alumina immobilized thiourea (0.752 g, 25% w/w) was ground in a mortar for an appropriate time at room temperature. The progress of the reaction was monitored by TLC using n-hexane
:
EtOAc (5
:
2) as an eluent. After completion of the reaction, the mixture was washed with EtOAc (3 × 5 mL). The combined washing solvents were evaporated under reduced pressure to give the crude thiirane for further purification by a short-column chromatography over silica gel.
2.5. One-pot synthesis of β-thiol-1,4-disubstituted-1,2,3-triazoles from thiiranes catalyzed by MgFe2O4/Cu in water: a general procedure
In a round-bottomed flask equipped with a magnetic stirrer and condenser, a solution of the thiirane (1 mmol), alkyne (1 mmol) and sodium azide (0.078 g, 1.2 mmol) in H2O (5 mL) was prepared. MgFe2O4/Cu nanocomposite (0.02 g) was then added to the solution and the resulting mixture was stirred magnetically for 2–4 h at 60 °C. The progress of the reaction was monitored by TLC using n-hexane
:
EtOAc (10
:
2) as an eluent. After completion of the reaction, the magnetic nanocatalyst was separated using an external magnet and collected for the next run. The reaction mixture was extracted with ethyl acetate and then dried over anhydrous Na2SO4. After evaporating the organic solvent, the crude β-thiol-1,4-disubstituted-1,2,3-triazoles were obtained. Removal of the solvent under vacuum, followed by recrystallization with EtOH/H2O (1
:
1) afforded the pure β-thiol-1,4-disubstituted-1,2,3-triazoles derivatives in 80–96% yield (Table 2). All products are new compounds and were characterized by HRMS (EI), FT-IR, 1H NMR and 13C NMR spectra. The spectra of the products are given in the ESI.†
2.5.1. Characterization of β-thiol-1,4-disubstituted-1,2,3-triazoles.
2.5.1.1. 2-Phenyl-2-(4-phenyl-1H-1,2,3-triazol-1-yl)-ethane-1-thiol (1b).
White solid: mp 122–124 °C, FT-IR (KBr): ν/cm−1 3371, 3085, 3026, 2927, 2365, 1584, 1450, 1270, 1029, 762, 695; 1H NMR (500 MHz, CDCl3) δ 7.78–7.71 (m, 2H, Ar-H), 7.44–7.23 (m, 9H, Ar-H) 5.69 (dd, J = 7, 4.5 Hz, 1H, CHN), 4.63 (dd, J = 12.5, 5 Hz, 1H, CH2), 4.23 (dd, J = 15, 5 Hz, 1H, CH2), 3.63 (bs, 1H, SH); 13C NMR (125 MHz, CDCl3) δ 146.7 (
CN), 135.0 (NCH
), 128.1, 127.8, 127.2, 126.1, 124.7, 119.5 (10 × ArC), 66.2 (CHCH2), 28.6 (CH2). HRMS (EI) m/z calcd for C16H15N3S 281.0987, found 281.0985.
2.5.1.2. 1-Phenoxy-3-(4-phenyl-1H-1,2,3-triazol-1-yl)propane-2-thiol (2b).
Milky solid: mp 113–114 °C, FT-IR (KBr): ν/cm−1 3302, 3086, 2919, 2873, 2365, 1587, 1638, 1599, 1497, 1474, 1466, 1303, 1044, 764, 752, 712, 691; 1H NMR (500 MHz, CDCl3) δ 7.86 (s, 1H, NCH
C), 7.67–7.65 (m, 2H, Ar-Ho), 7.35–7.31 (m, 2H, OAr-Hm), 7.29–7.26 (m, 3H, Ar-Hm,p), 7.00–6.87 (m, 3H, OAr-Ho,p), 4.96 (bs, 1H, SH), 4.67 (dd, J = 13, 5 Hz, 1H, CH2O), 4.52 (dd, J = 13, 5 Hz, 1H, CH2O), 4.47 (dd, 1H, J = 12.5, 5 Hz, CH2N), 4.08 (dd, 1H, J = 12.5, 5 Hz, CH2N), 4.05–3.72 (m, 1H, CHS); 13C NMR (125 MHz, CDCl3) δ 157.1 (
CN), 146.53, 129.1 (2 × ArC), 128.6, 128.5, 127.8, 127.1, 124.6, 120.5, 120.4 (10 × ArCH), 113.5 (NCH
), 67.8 (CH2O), 52.2 (CH2N), 28.6 (CHS). HRMS (EI) m/z calcd for C17H17N3OS 311.1092, found 311.1092.
2.5.1.3. 1-Chloro-3-(5-phenyl-1H-1,2,3-triazol-1-yl)propane-2-thiol (3b).
Mint white solid: mp 154–157 °C FT-IR (KBr): ν/cm−1 3690, 3100, 2920, 2363, 2344, 1561, 1441, 1364, 1045, 764, 692, 668. 1H NMR (500 MHz, CDCl3) δ 7.93 (s, 1H, NCH
C), 7.88–7.23 (m, 5H, Ar-H), 4.61–4.41 (m, 2H, CH2N), 4.39–4.31 (m, 1H, CH2Cl), 4.00–3.94 (m, 1H, CH2Cl), 3.90–3.37 (m, 1H, CHS), 2.07 (bs, 1H, SH); 13C NMR (125 MHz, CDCl3) δ 148.0 (
CN), 130.1 (ArC, NCH
), 128.9, 128.4, 125.7, 117.6 (5 × ArCH), 55.9 (CH2N), 34.4 (CH2Cl), 29.6 (CHS). HRMS (EI) m/z calcd for C11H12ClN3S 253.0441, found 253.0442.
2.5.1.4. 1-(4-Phenyl-1H-1,2,3-triazol-1-yl)butane-2-thiol (4b).
White solid: mp 104–106 °C, FT-IR (KBr): ν/cm−1 3692, 3139, 2958, 2873, 2366, 2345, 1585, 1439, 1230, 1072, 765, 694; 1H NMR (500 MHz, CDCl3) δ 7.83 (s, 1H, NCH
C), 7.68–7.23 (m, 5H, Ar-H), 4.49 (dd, J = 14, 5 Hz, 1H, CH2N), 4.24 (dd, J = 14, 8 Hz, 1H, CH2N), 4.09–4.04 (m, 1H, CHS), 3.43 (bs, 1H, SH), 1.61–1.55 (m, 2H, CH2), 1.06 (t, J = 7.5 Hz, 3H, CH3); 13C NMR (125 MHz, CDCl3) δ 147.3 (
CN), 130.3 (NCH
), 128.7, 128.0, 125.5, 121.1 (6 × ArC), 71.7 (CH2N), 55.9 (CHS), 27.4 (CH2), 9.8 (CH3). HRMS (EI) m/z calcd for C12H15N3S 233.0987, found 233.0986.
2.5.1.5. 1-Isopropoxy-3-(4-phenyl-1H-1,2,3-triazol-1-yl)propane-2-thiol (5b).
Yellow solid: mp 74–75 °C, FT-IR (KBr): ν/cm−1 3177, 2968, 2875, 2369, 2345, 1583, 1460, 1444, 1366, 1071, 767, 702; 1H NMR (500 MHz, CDCl3) δ 7.86 (s, 1H, NCH
C), 7.67–7.65 (m, 2H, Ar-H), 7.33–7.23 (m, 3H, Ar-H), 4.53 (dd, J = 14, 4 Hz, 1H, CH2N), 4.34 (dd, J = 14, 7.5 Hz, 1H, CH2N), 4.21–4.16 (m, 2H, OCH2), 3.58–3.51 (m, 1H, CHO), 3.46–3.35 (m, 2H, CHS overlapped with SH), 1.11 (d, J = 5 Hz, 6H, 2CH3); 13C NMR (125 MHz, CDCl3) δ 147.9 (
CN), 130.3 (NCH
), 128.7, 128.0, 125.5, 121.4 (6 × ArC), 72.3 (CHO), 69.2 (OCH2), 69.1 (CH2N), 53.4 (CHS), 21.9 (2 × CH3). HRMS (EI) m/z calcd for C14H19N3OS 277.1249, found 277.1247.
2.5.1.6. 2-(4-Phenyl-1H-1,2,3-triazol-1-yl)cyclohexane-1-thiol (6b).
Pale green solid: mp 156–159 °C, FT-IR (KBr): ν/cm−1 3305, 3094, 2936, 2853, 2364, 1586, 1440, 1236, 1055, 766, 698; 1H NMR (500 MHz, CDCl3) δ 7.83 (s, 1H, NCH
C), 7.63–7.25 (m, 5H, Ar-H), 4.12–4.04 (m, 1H, CHN), 3.57–2.94 (m, 1H, CHS), 2.04–1.22 (m, 4 × CH2 overlapped with 1H, SH); 13C NMR (125 MHz, CDCl3) δ 146.6 (
CN), 132.4 (NCH
), 130.2, 128.6, 127.9, 125.4, 119.8 (6 × ArC), 72.5 (CHN), 67.2 (CHS), 28.6 (CHS), 33.8, 31.5, 24.8, 24.0 (4 × CH2). HRMS (EI) m/z calcd for C14H17N3S 259.1143, found 259.1143.
2.5.1.7. 1-(Allyloxy)-3-(4-phenyl-1H-1,2,3-triazol-1-yl)propane-2-thiol (7b).
Cream solid: mp 70 °C, FT-IR (KBr): ν/cm−1 3233, 3141, 2930, 2872, 2366, 1590, 1438, 1350, 1230, 1000, 767, 696; 1H NMR (500 MHz, CDCl3) δ 7.85 (s, 1H, NCH
C), 7.55–7.23 (m, 5H, Ar-H), 5.80–5.87 (m, 1H,
CH), 5.22 (dt, J = 17, 1.2 Hz, 1H, C
CH2), 5.14 (dt, J = 10, 1.2 Hz, 1H, C
CH2), 4.55–4.50 (m, 2H, CH2O), 4.35 (dd, J = 15, 7 Hz, 1H, CH2N), 4.26–4.23 (m, 1H, CH2N), 4.00–3.88 (m, 2H, OCH2), 348–3.41 (m, 1H, CHS), 2.91 (bs, 1H, SH); 13C NMR (125 MHz, CDCl3) δ 147.1 (
CN), 134.2 (NCH
), 130.2 (
CH), 128.7, 128.0, 125.5, 121.5 (6 × ArC), 117.4 (
CH2), 72.3 (OCH2), 71.2 (CH2O), 69.0 (CH2N), 53.4 (CHS). HRMS (EI) m/z calcd for C14H17N3OS 275.1092, found 275.1094.
2.5.1.8. 2-Mercapto-3-(4-phenyl-1H-1,2,3-triazol-1-yl)propyl methacrylate (8b).
Milky solid: mp 86–92 °C, FT-IR (KBr): ν/cm−1 3000, 2925, 2367, 1719, 1593, 1438, 1294, 1097, 762, 695; 1H NMR (300 MHz, CDCl3): δ 7.86 (s, 1H, NCH
C), 7.66–7.64 (m, 2H, Ar-H), 7.34–7.25 (m, 3H, Ar-H), 6.10 (d, J = 10 Hz, 1H,
CH2), 5.93 (d, J = 10 Hz, 1H,
CH2), 4.48–4.12 (m, 2H, OCH2), 3.57 (m, 2H, CH2N), 3.66 (bs, 1H, SH), 3.33–3.32 (m, 1H, CSH), 2.05 (s, 3H, CH3); 13C NMR (125 MHz, CDCl3): δ = 161.6 (C
O), 147.3 (
CN), 135.7 (C
), 128.9 (NCH
), 128.8, 128.2, 125.5, 121.6 (6 × ArC), 70.6 (OCH2), 63.6 (CH2N), 53.0 (CHS), 18.3 (CH3). HRMS (EI) m/z calcd for C15H17N3O2S 303.1042, found 303.1045.
2.5.1.9. 2-(4-Cyclohexyl-1H-1,2,3-triazol-1-yl)-2-phenylethane-1-thiol (9b).
White solid: mp 125–128 °C, FT-IR (KBr): ν/cm−1 3233, 3117, 3061, 2923, 2849, 1448, 1067, 889, 756, 697; 1H NMR (500 MHz, CDCl3): δ 7.60 (s, 1H, NCH
C), 7.42–7.26 (m, 5H, Ar-H), 5.68 (dd, J = 8.7, 4.8 Hz, 1H, NCHCH2), 4.40–4.28, 4.15–4.03 (2 m, 2H, CH2S), 3.32 (t, J = 5.9 Hz, 1H, SH), 2.76–2.68 (m, 1H, CH2CHCH2), 1.76–1.65 (m, 4H, 2 × CH2CH2CH), 1.43–1.36 (m, 4H, 2 × CH2CH2CH), 1.27–1.18 [m, 2H, (CH2)2CH2(CH2)2]. 13C NMR (125 MHz, CDCl3): δ = 153.9 (NCCH), 138.5 (ArC), 129.7, 129.3, 128.1 (5 × ArCH), 120.9 (NCCH), 64.7 (NCHCH2), 53.3 (CH2S), 36.1 (CH2CHCH2), 33.8, 26.9, 26.8 [(CH2)5]; HRMS (EI) m/z calcd for C16H21N3S 287.1456, found 287.1455.
2.5.1.10. (1-(2-Mercapto-1-phenylethyl)-1H-1,2,3-triazol-4-yl)methanol (10b).
Colorless solid: mp 101–105 °C, FT-IR (KBr): ν/cm−1 3340, 3167, 2932, 2893, 1454, 1234, 1119, 1084, 1011, 849, 795, 702. 1H NMR (500 MHz, CDCl3): δ 7.62 (s, 1H, NCH
C), 7.37–7.28 (m, 5H, Ar-H), 5.68 (dd, J = 8.7, 4.8 Hz, 1H, NCHCH2), 4.52 (s, 2H, CH2O), 4.38–4.30, 4.13–4.02 (2 m, 2H, CH2S), 3.76 (bs, 1H, OH), 3.32 (t, J = 5.9 Hz, 1H, SH), 13C NMR (125 MHz, CDCl3): δ = 147.1 (
CN), 130.1 (ArC), 128.5, 128.0, 125.7 (5 × ArCH), 121.3 (
CHN), 71.8 (CHN), 55.7 (CH2O), 27.3 (CH2S). HRMS (EI) m/z calcd for C11H13N3OS 235.0779, found 235.0781.
2.5.1.11. 2-(4-(4-Methoxyphenyl)-1H-1,2,3-triazol-1-yl)-2-phenylethane-1-thiol (11b).
White solid: mp 130–132 °C, FT-IR (KBr): ν/cm−1 3371, 3085, 3026, 2927, 2365, 1584, 1450, 1270, 1074, 1041, 1029, 762, 695; 1H NMR (500 MHz, CDCl3) δ 7.76–7.71 (m, 3H, Ar-H), 7.44–7.21 (m, 7H, Ar-H) 5.71 (dd, J = 7, 4.5 Hz, 1H, CHN), 4.15 (s, 3H, OCH3), 3.76 (dd, J = 12.5, 5 Hz, 1H, CH2), 3.37 (dd, J = 15, 5 Hz, 1H, CH2), 2.75 (bs, 1H, SH); 13C NMR (125 MHz, CDCl3) δ 146.6 (
CN), 135.0 (NCH
), 128.1, 127.7, 127.2, 126.1, 124.7, 119.1 (10 × ArC), 66.2 (CHN), 58.26 (OCH3), 28.6 (CH2S). HRMS (EI) m/z calcd for C17H17N3OS 311.1092, found 311.1095.
2.6. Recycling of MgFe2O4/Cu nanocatalyst
The MgFe2O4/Cu nanoparticles were recovered with an external magnet, washed several times with ethyl acetate and distilled water, and used for the subsequent cycles after drying under air atmosphere.
3. Results and discussion
3.1. Synthesis and characterization of MgFe2O4/Cu nanocatalyst
Although, MgFe2O4 has a large surface to volume ratio and therefore possesses high catalytic capability due to its wide contact surface, it tends to aggregate so as to minimize the surface energies. Moreover, the naked magnesium ferrite nanoparticles have high chemical activity, and are easily oxidized in air, generally resulting in loss of magnetic property and dispersibility. Therefore, it is significant to provide appropriate surface coating to keep the stability of MgFe2O4 particles. Coating with an inorganic layer, such as silica, metal or nonmetal elementary substance and metal oxide is important because the protecting shells not only reduces the aggregation of the nanoparticles in the solution and stabilize the magnetic nano-ferrite, but can also be used for further functionalization and improves the efficiency of the catalyst.56 Ferrites are highly valuable catalyst supports because they take advantage of magnetic property and can provide unique features such as easy separation, recoverability and reusability for the new synthesized MgFe2O4/Cu nanocatalyst.
The nanoparticles of MgFe2O4/Cu were synthesized in a two-step procedure. MgFe2O4 was prepared using solid-state reaction of Mg(NO3)2·6H2O, Fe(NO3)3·9H2O, NaOH, and NaCl in a mortar (Scheme 2). After calcination of crude powder at 900 °C, the MgFe2O4 nanoparticles were obtained with high crystallinity and phase purity. Then, MgFe2O4 nanoparticles were added to an aqueous solution of CuCl2·2H2O and followed by gradually addition of KBH4 powder under intense stirring. Finally, the black precipitate was collected through magnetic separation, washed with deionized water, and dried at room temperature (Scheme 3). The prepared MgFe2O4/Cu nanocatalyst was characterized by various techniques such as FT-IR, vibration sample magnetometer (VSM), X-ray diffraction (XRD), transmission electron microscopy (TEM), field emission scanning electron microscope (FESEM), energy dispersive X-ray spectrometer (EDS), and inductively coupled plasma optical emission spectrometry (ICP-OES) analyses.
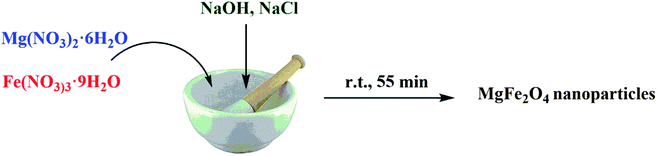 |
| Scheme 2 Synthesis of MgFe2O4 nanoparticles. | |
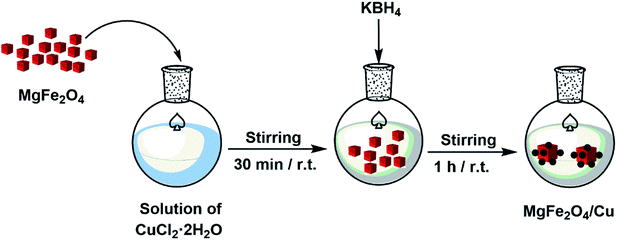 |
| Scheme 3 Synthesis of MgFe2O4/Cu nanocomposite. | |
3.1.1. Vibration sample magnetometer (VSM). The hysteresis loops, saturation magnetization (Ms) and switching field (Hc) of MgFe2O4 and MgFe2O4/Cu nanoparticles are shown in Fig. 1. MgFe2O4/Cu nanoparticles show lower magnetization saturation (27 emu g−1) than the uncoated magnesium ferrite nanoparticles (48 emu g−1). This is owing to the effect of copper shell coating where each ferrite particle was separated from its neighbors by the coated layer leading to diminish the magnetostatic coupling between the particles. The samples exhibit typical ferromagnetic behavior at room temperature. The narrow cycles and the hysteresis loops show the behavior of soft magnetic materials with low coercivity.
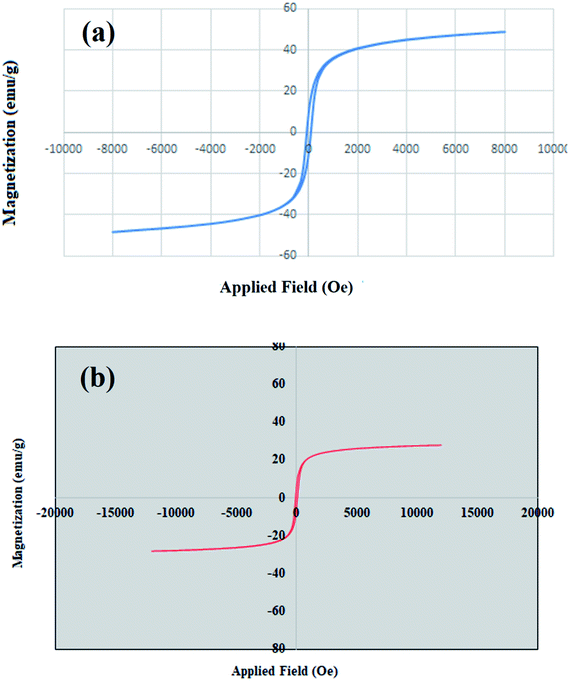 |
| Fig. 1 Magnetization curves of (a) MgFe2O4 (b) MgFe2O4/Cu nanoparticles. | |
3.1.2. Fourier transform infra-red (FT-IR) spectrum. Fig. 2 shows the FT-IR spectrum of MgFe2O4/Cu nanocatalyst. The absorption band at 577 cm−1 is related to the vibration of metal oxide bonds (Fe–O and Mg–O) which confirms the formation of MgFe2O4 nanoparticles. The absorption peaks at 3314 and 3449 cm−1 are assigned to the stretching vibration of H2O molecules and indicates the OH groups on the surface of the magnetic nanoparticles. The band around 1637 cm−1 corresponds to the bending mode of H2O molecules.51
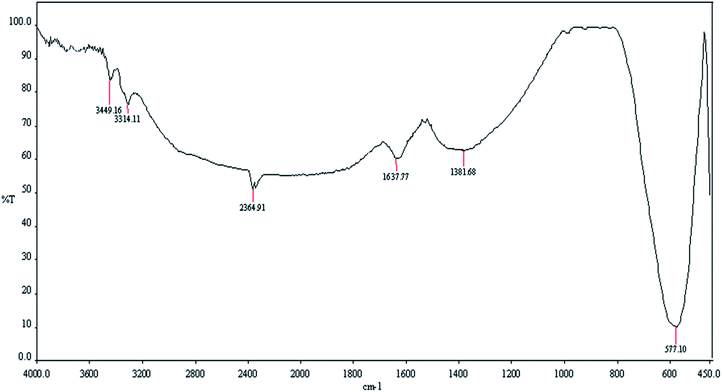 |
| Fig. 2 FT-IR (KBr) spectrum of MgFe2O4/Cu nanoparticles. | |
3.1.3. X-ray diffraction (XRD). Fig. 3 shows the X-ray diffraction (XRD) patterns of MgFe2O4/Cu, MgFe2O4 and copper nanoparticles. In the XRD pattern of MgFe2O4/Cu, all the peaks of MgFe2O4 and Cu nanoparticles are traceable. The lines (220), (311), (400), (422), (511), (440), (620) and (533) related to 2θ = 30.22°, 35.60°, 37.18°, 43.27°, 57.09°, 62.68°, 74.38° and 75.39° respectively, are assigned to the diffraction of MgFe2O4 crystals and indicate that the synthesized MgFe2O4 nanoparticles are pure and high crystalline. These peaks are compatible with the standard data (JCPDS: 01-036-0398).51 The characteristic diffraction peaks of copper located at 2θ = 43.7°, 50.7°, and 74.3° which correspond to the (111), (200), and (220) planes of the fcc structure, respectively and they are in good agreement with copper standard (JCPDS: 04-0836).57 The peaks at 43.7° and 74.3° for copper overlap with the 43.27° and 74.38° peaks of MgFe2O4, respectively. The average crystallite size of MgFe2O4/Cu nanoparticles is calculated using the Scherrer's formula (46 nm).
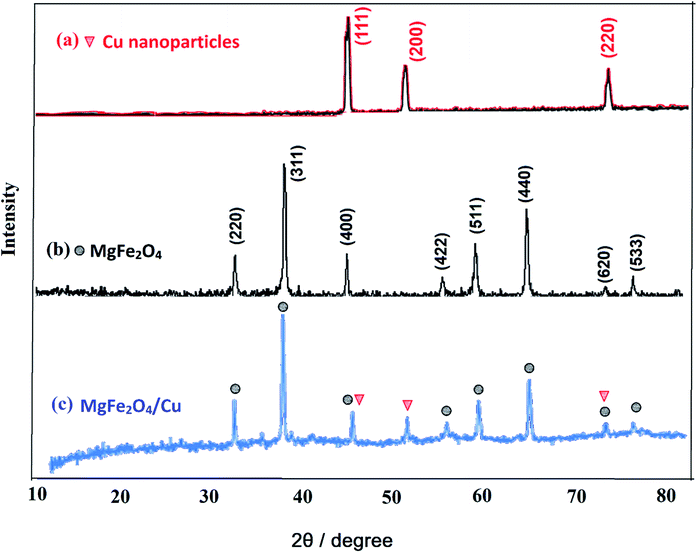 |
| Fig. 3 The X-ray diffraction patterns of (a) nano-Cu, (b) nano-MgFe2O4 and (c) MgFe2O4/Cu nanocomposite. | |
3.1.4. TEM, FESEM and EDS of MgFe2O4/Cu. The morphology and size distribution of the synthesized nanocatalyst have been studied by TEM and FESEM techniques. TEM images of the MgFe2O4/Cu nanocomposite are shown in Fig. 4. As can be seen from the images, two sizes of particles are clearly distinguishable, with differences in their colour and morphology. The larger grey spots with cubic shape were attributed to the MgFe2O4 particles which coated with the small black segments of copper nanoparticles.
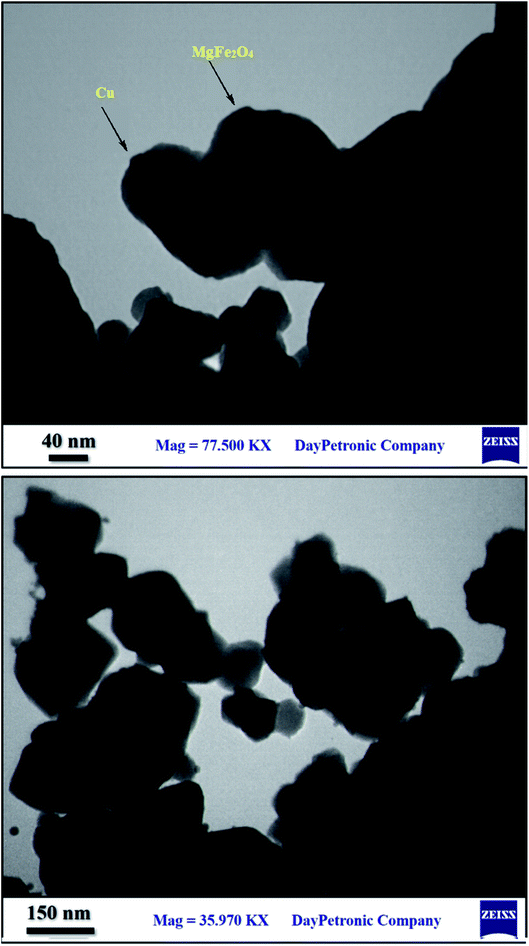 |
| Fig. 4 TEM images of MgFe2O4/Cu. | |
Fig. 5 shows FESEM images of MgFe2O4/Cu nanocomposite that confirm the presence of nanoparticles with diameters ranging from 29 to 43 nm. The obtained results are in good agreement with TEM and XRD data.
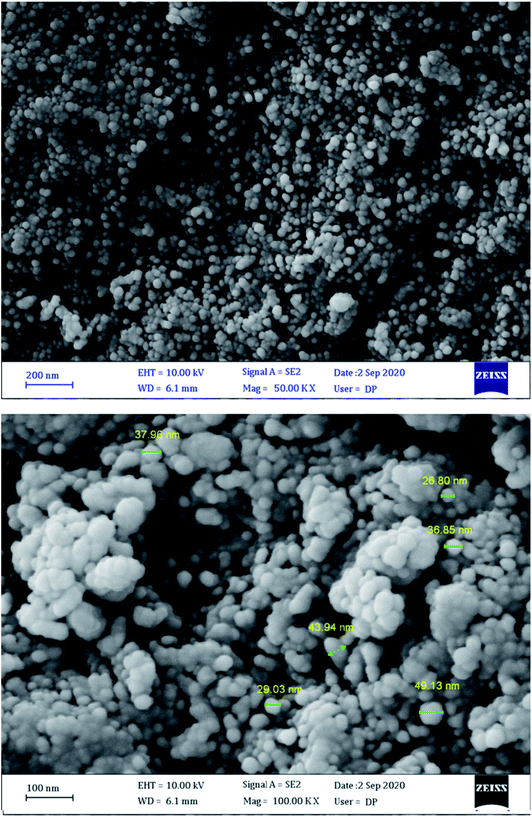 |
| Fig. 5 FESEM images of MgFe2O4/Cu. | |
The chemical composition of MgFe2O4/Cu nanocomposite was confirmed with EDS data. In this analysis, Cu, Mg, Fe, and O signals are observable (Fig. 6). Additionally, the exact concentration of Mg, Fe and Cu was determined by ICP-OES and the obtained values were 10.2, 33.35 and 31.68 wt% respectively, which are in good agreement with EDS data.
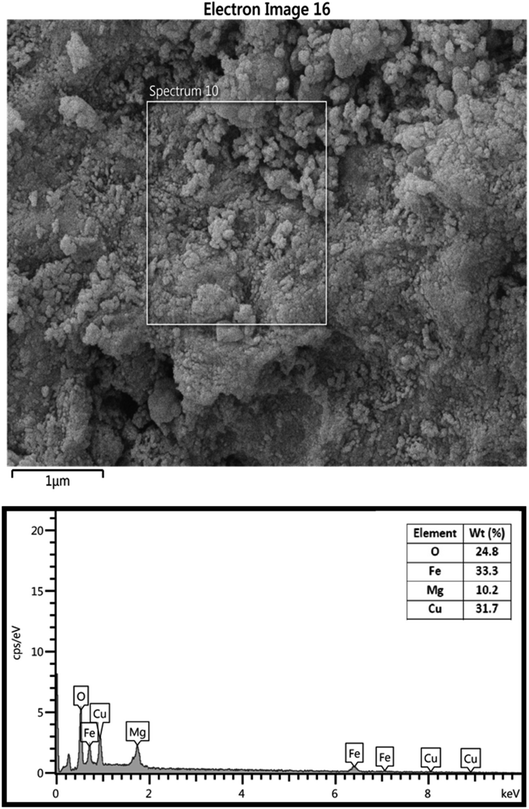 |
| Fig. 6 EDS of MgFe2O4/Cu. | |
3.2. Catalytic activity of MgFe2O4/Cu for the synthesis of β-thiol-1,4-disubstituted-1,2,3-triazoles
In order to optimize the reaction conditions, we investigated the one-pot click synthesis of 2-phenyl-2-(4-phenyl-1H-1,2,3-triazol-1-yl)ethane-1-thiol from styrene episulfide, sodium azide and phenyl acetylene under various reaction conditions. Initially, temperature, solvents, reaction time and the amounts of catalyst and reactants were studied as experimental factors, and then the results were summarized in Table 1. The favorable outcome was obtained using styrene episulfide (1 mmol), sodium azide (1.2 mmol) and phenylacetylene (1 mmol) in the presence of nano-MgFe2O4/Cu (0.02 g) as catalyst in water at 60 °C (Table 1, entry 4). It is noteworthy that the presence of catalyst was necessary to perform the reaction and in the absence of nanocomposite, the reaction did not proceed even after 11 h (entry 1). The quantity of catalyst was optimized using various amounts of nano-MgFe2O4/Cu (0.005, 0.01, 0.02 and 0.03 g), and the best result was obtained with 0.02 g of catalyst. The catalyst concentration plays a significant role in the optimization of the product yield. An increase in the amount of catalyst from 0.01 to 0.02 g not only increased the triazole yield but also accelerated the rate of reaction (entries 2–4). Using the more amounts of nanocatalyst did not improve the product yield (entry 5).
Table 1 Nano-MgFe2O4/Cu-catalysed reaction of styrene episulfide with phenylacetylene and sodium azide under different conditionsa
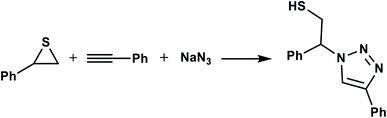
|
Entry |
MgFe2O4/Cu (g) |
Solvent |
Time (h) |
Temperature (°C) |
Yieldb (%) |
All reactions were carried out with styrene episulfide (1 mmol), phenylacetylene (1 mmol) and sodium azide (1.2 mmol). Isolated yields. Catalysed by MgFe2O4. Catalysed by Cu nanoparticles. |
1 |
— |
H2O |
11 |
60 |
0 |
2 |
0.005 |
H2O |
5 |
60 |
40 |
3 |
0.01 |
H2O |
5 |
60 |
75 |
4 |
0.02 |
H2O |
2.5 |
60 |
96 |
5 |
0.03 |
H2O |
2.4 |
60 |
96 |
6 |
0.02 |
CH3CN |
3 |
82 |
50 |
7 |
0.02 |
EtOH |
3 |
78 |
60 |
8 |
0.02 |
MeOH |
3 |
65 |
60 |
9 |
0.02 |
EtOAc |
3 |
77 |
65 |
10 |
0.02 |
DMF |
3 |
100 |
55 |
11 |
0.02 |
THF |
20 |
60 |
0 |
12 |
0.02 |
n-Hexane |
20 |
68 |
0 |
13 |
0.02 |
CCl4 |
20 |
77 |
0 |
14 |
0.02 |
H2O |
10 |
25 |
45 |
15 |
0.02 |
H2O |
6 |
45 |
70 |
16c |
0.02 |
H2O |
4 |
60 |
Trace |
17d |
0.02 |
H2O |
3 |
60 |
92 |
In order to study of solvent effect, the cyclization reaction was tested in the various solvents. The results showed that the polar solvents such as water, acetonitrile, ethanol, methanol, ethyl acetate and dimethylformamide were effective and utilizable whereas non-polar solvents were not suitable for this purpose (entries 6–13). The reaction was carried out successfully in H2O and it was selected as the best option because in comparison with water, the product yields were lower in all other solvents and also water is a green and eco-friendly solvent (entry 4).
The effect of temperature was also investigated and the reaction was tested at different temperatures (25, 45 and 60 °C). The product yield was not satisfactory at room temperature (25 °C) after 10 h (entry 14). Increasing the temperature simultaneously increased the reaction rate and product yield, and the desired triazole was synthesized in 70% yield after 6 h at 45 °C (entry 15). Further increase of temperature up to 60 °C led to produce the product with excellent yield at short reaction time (entry 4). The reaction was tested in the presence of bare MgFe2O4 and Cu nanoparticles separately under the optimized conditions and results showed that although magnesium ferrite nanoparticles improve and enhance the catalytic activity of nanocomposite, copper particles play an essential role for proceeding the reaction and their presence is vital in triazole cyclization (entries 16 and 17).
The generality of the presented procedure was established by reaction of various thiiranes bearing either electron-donating or withdrawing substituents, and cyclic thiiranes with phenylacetylene and sodium azide in the presence of MgFe2O4/Cu nanocomposite under the optimized conditions. The results are summarized in Table 2. In addition, the reaction of other alkynes such as aliphatic terminal alkynes and 4-methoxyphenyl acetylene with styrene episulfide was also considered under mentioned conditions (entries 9–11). All reactions were carried out successfully within 2–4 h to give triazoles in 80–96% yields.
Table 2 One-pot synthesis of β-Thiol-1,4-disubstituted-1,2,3-triazoles from thiiranes catalyzed by nano-MgFe2O4/Cua
Entry |
Thiirane (a) |
Alkyne |
Triazole (b) |
Time (h) |
Yieldb (%) |
All reactions were carried out with 1 mmol of thiirane in the presence of alkyne (1 mmol), sodium azide (1.2 mmol) and nano-MgFe2O4/Cu (0.02 g) in water at 60 °C. Yields refer to isolated pure products. |
1 |
 |
 |
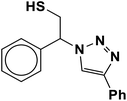 |
2.5 |
96 |
2 |
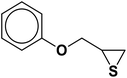 |
 |
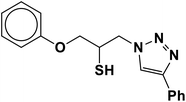 |
2 |
91 |
3 |
 |
 |
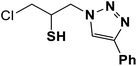 |
2.5 |
80 |
4 |
 |
 |
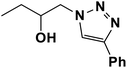 |
4 |
95 |
5 |
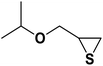 |
 |
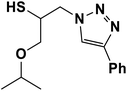 |
3 |
90 |
6 |
 |
 |
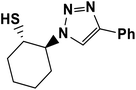 |
2 |
94 |
7 |
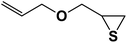 |
 |
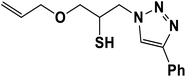 |
2.5 |
90 |
8 |
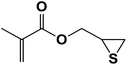 |
 |
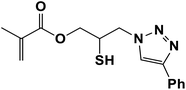 |
2 |
80 |
9 |
 |
 |
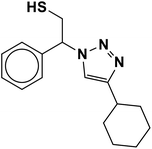 |
3 |
92 |
10 |
 |
 |
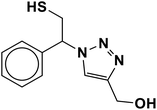 |
3.5 |
90 |
11 |
 |
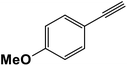 |
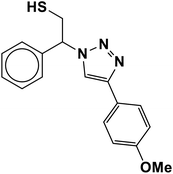 |
2.5 |
95 |
3.3. Recycling of nano-MgFe2O4/Cu
The recycling of the green nanocatalyst was investigated under the optimized reaction conditions (Table 2, entry 1). The nanoparticles were easily accumulated by applying an external magnetic field, washed with ethyl acetate and distilled water and, after drying, reused several times without any significant loss of activity (Fig. 7). The structure of the recovered catalyst was confirmed using VSM, FESEM, XRD and TEM analyses after five runs (Fig. 8).
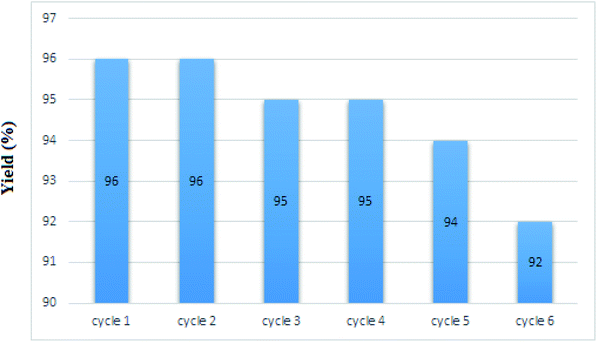 |
| Fig. 7 Recycling of nano-MgFe2O4/Cu in the synthesis of 2-phenyl-2-(4-phenyl-1H-1,2,3-triazol-1-yl)ethane-1-thiol. | |
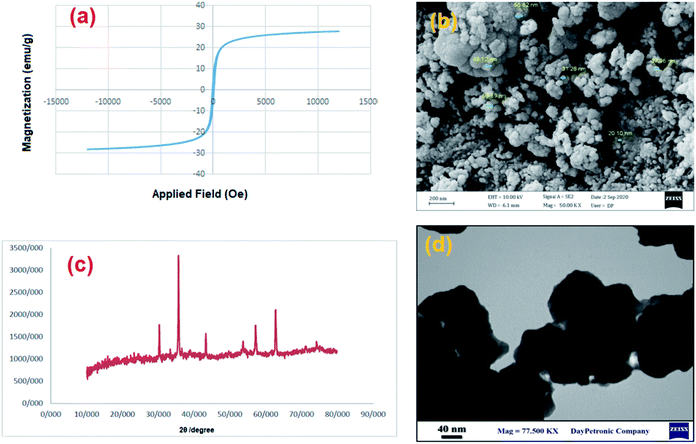 |
| Fig. 8 (a) Magnetization curve, (b) FESEM, (c) XRD pattern and (d) TEM image of MgFe2O4/Cu after five runs in the synthesis of 2-phenyl-2-(4-phenyl-1H-1,2,3-triazol-1-yl)ethane-1-thiol. | |
The extent of Mg, Fe and Cu leaching during catalytic reaction was studied by ICP-OES analysis of the supernatant liquid after removal of catalyst and the result showed no presence of Mg, Fe and Cu in supernatant liquid.
3.4. Mercury poisoning and hot filtration tests
In order to confirm the heterogeneity of the catalyst, both hot filtration and mercury poisoning tests were performed. Accordingly, the filtration of the catalyst was carried out after 30 min at 100 °C and the filtrate was allowed to react for additional 2 hours, but the reaction due to the absence of copper did not take place, and no cyclization reaction was occurred.
The Hg poisoning test was conducted for the model reaction under the optimum conditions as follows: the one-pot reaction of styrene episulfide (1 mmol), phenyl acetylene (1 mmol), sodium azide (1.2 mmol) and MgFe2O4/Cu nanocatalyst (0.02 g) was carried out in the presence of Hg(0) excess (1.89 g, 9.43 mmol, 277 equiv.) under intense stirring conditions at 60 °C for 3 h in water. The suppression of catalysis by mercury is evidence for a heterogeneous catalyst.58 The added Hg(0) poisoned and inactivated MgFe2O4/Cu heterogeneous catalyst through amalgamating the metal catalyst or adsorbing on its surface and no product was obtained after 3 h.
3.5. The proposed mechanism for synthesis of β-thiol-1,4-disubstituted-1,2,3-triazoles catalyzed by MgFe2O4/Cu
The designed mechanism for the synthesis of β-thiol-1,4-disubstituted-1,2,3-triazole may comprise two possible pathways (A and B). MgFe2O4/Cu nanoparticles catalyze both cleavage of the thiirane ring and 1,3-dipolar cycloaddition leading to the formation of triazoles.27,28 First, as a result of non-covalent interaction a bond is formed between metal and azide, followed by activation of thiirane ring with MgFe2O4/Cu catalyst. Then, ring opening of thiirane is accomplished through azide transference from the catalyst which leads to the formation of 2-azido-2-arylethanethiol (pathway A). The thiirane rings carrying aryl groups due to the stability of benzyl carbocation prefer to be opened from the more hindered position via SN1 type of mechanism (α-cleavage); nevertheless, the regioselective ring opening of thiiranes bearing alkyl and allyl substituents by azide is powerfully preferred from less hindered carbon of the thiirane via SN2 type of mechanism (β-cleavage). In order to accredit the catalytic role of MgFe2O4/Cu in the pathway A, the styrene episulfide and sodium azide were reacted in the absence of catalyst, and it was found that, only a trace amount of 2-azido-2-arylethanethiol had been generated. For pathway A, consumption of styrene episulfide and sodium azide and also the generation of 2-azido-2-phenylethanethiol intermediate were monitored by gas chromatography (GC) analysis and thin layer chromatography (TLC) runs of the reaction mixture, and we found that 2-azido-2-arylethanethiol is formed easily (within the first 30 min of the reaction) and the rate determining step (RDS) was found to be the 1,3-dipolar cycloaddition step. 2-Azido-2-arylethanethiol was characterized by FT-IR spectrum and stretching frequency of 2097 cm−1 related to the azide (the FT-IR spectrum of 2-azido-2-phenylethanethiol has been provided in ESI Section†).
The pathway B shows the insertion of copper to the C–H bond of phenylacetylene and generation of the intermediate(I), which accelerates the [3+2] cycloaddition between azide and carbon–carbon triple bond of in situ produced intermediate(II), to afford the Cu–C-triazole(IV). The phenylacetylene consumption and also the disappearance of the 2-azido-2-arylethanethiol intermediate, were monitored by GC analysis and TLC runs of the reaction mixture. Eventually, proteolysis of the Cu–C bond of intermediate(IV) by aqueous media gives the corresponding β-thiol-1,4-disubstituted-1,2,3-triazole(V) (Scheme 4).
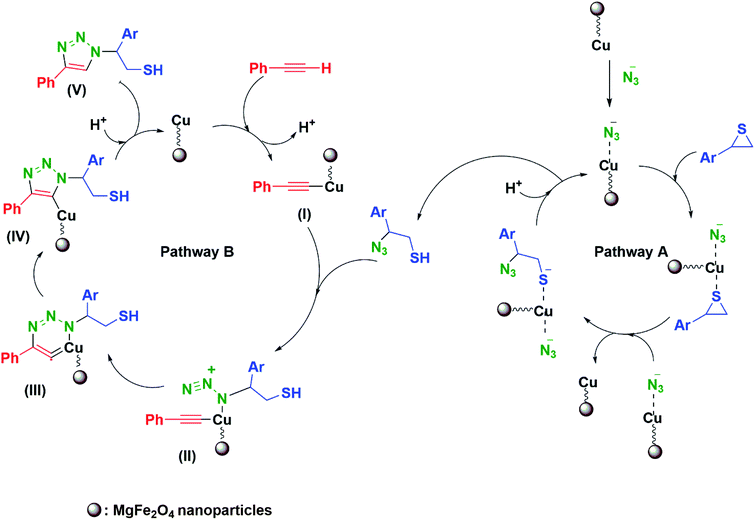 |
| Scheme 4 The mechanism proposed for the one-pot synthesis of β-thiol-1,4-disubstituted-1,2,3-triazole catalyzed by MgFe2O4/Cu. | |
In order to evaluate the accuracy of reaction RDS, 2-azido-2-phenylethanethiol was separately reacted with phenylacetylene in the presence of MgFe2O4/Cu nanocatalyst. The formation of corresponding 1,2,3-triazole was monitored via GC analysis and TLC runs. It was observed that the reaction was carried out within 2 h. This result demonstrated that the pathway B determines the reaction rate.
To confirm the formation of acetylide intermediate(I), phenylacetylene and MgFe2O4/Cu nanocatalyst were mixed in a separate experiment in aqueous media, and pH of water as a solvent was investigated. A 0.6 unit decrease in pH after 20 min was detected, indicative of terminal proton release to the water, due to the initial coordination of phenylacetylene to copper to form acetylide intermediate(I).
4. Conclusions
In summary, in this research, the magnetic nanocomposite of MgFe2O4/Cu has been easily manufactured through a solid-state procedure and it was then characterized by different techniques such as VSM, FESEM, TEM, XRD, EDS and FT-IR. This novel composite has been utilized as an efficient catalyst for one-pot synthesis of β-thiol-1,4-disubstituted-1,2,3-triazoles as new products via three component reactions of sodium azide, terminal alkynes, and various thiiranes in water. The method reported is completely new due to the novelty of both the catalyst and the triazole products. Furthermore, perfect regioselectivity, the simple process, high product yields, short reaction times, the use of eco-friendly solvent, easy separation and recycling of catalyst are significant advantages of this proposed procedure.
Conflicts of interest
There are no conflicts to declare.
Acknowledgements
The financial support of this work by the Research Council of Payame Noor University is gratefully acknowledged.
References
- H. N. Hafez, H. A. Abbas and A. R. El-Gazzar, Acta Pharm., 2008, 58, 359 CAS.
- K. M. Banu, A. Dinaker and C. Ananthnarayan, Indian J. Pharm. Sci., 1999, 61, 202 CAS.
- M. D. Chen, S. J. Lu, G. P. Yuag, S. Y. Yang and X. L. Du, Heterocycl. Commun., 2000, 6, 421 CAS.
- E. A. Sherement, R. I. Tomanov, E. V. Trukhin and V. M. Berestovitskaya, Russ. J. Org. Chem., 2004, 40, 594 CrossRef.
- F. C. Silva, M. C. B. V. de Souza, I. I. P. Frugulhetti, H. C. Castro, S. L. d. O. Souza, T. M. L. de Souza, D. Q. Rodrigues, A. M. T. Souza, P. A. Abreu, F. Passamani, C. R. Rodrigues and V. F. Ferreira, Eur. J. Med. Chem., 2009, 44, 373 CrossRef PubMed.
- A. Kamal, S. Prabhakar, M. J. Ramaiah, P. V. Reddy, C. R. Reddy, A. Mallareddy, N. Shankaraiah, T. L. N. Reddy, S. N. C. V. L. Pushpavalli and M. Pal-Bhadra, Eur. J. Med. Chem., 2011, 46, 3820 CrossRef CAS PubMed.
- S. Palhagen, R. Canger, O. Henriksen, J. A. van Parys, M.-E. Riviere and M. A. Karolchyk, Epilepsy Res., 2001, 43, 115 CrossRef CAS PubMed.
- L. P. Guan, Q. H. Jin, G. R. Tian, K. Y. Chai and Z. S. Quan, J. Pharm. Sci., 2007, 10, 254 CAS.
- S. Manfredini, C. B. Vicentini, M. Manfrini, N. Bianchi, C. Rustigliano, C. Mischiati and R. Gambari, Bioorg. Med. Chem., 2000, 8, 2343 CrossRef CAS PubMed.
- C. Menendez, A. Chollet, F. Rodriguez, C. Inard, M. R. Pasca, C. Lherbet and M. Baltas, Eur. J. Med. Chem., 2012, 52, 275 CrossRef CAS PubMed.
- J. N. Sangshetti, R. R. Nagawade and D. B. Shinde, Bioorg. Med. Chem. Lett., 2009, 19, 3564 CrossRef CAS PubMed.
- G. Ravi, A. R. Nath, A. Nagaraj, S. Damodhar and G. N. Rao, Pharma Chem., 2014, 6, 223 Search PubMed.
- M. F. Mady, G. E. A. Awad and K. B. Jørgensen, Eur. J. Med. Chem., 2014, 84, 433 CrossRef CAS PubMed.
- R. Raj, P. Singh, P. Singh, J. Gut, P. J. Rosenthal and V. Kumar, Eur. J. Med. Chem., 2013, 62, 590 CrossRef CAS PubMed.
- T. W. Kim, Y. Yong, S. Y. Shin, H. Jung, K. H. Park, Y. H. Lee, Y. Lim and K. Y. Jung, Bioorg. Chem., 2015, 59, 1 CrossRef CAS PubMed.
- F. Alonso, Y. Moglie, G. Radivoy and M. Yus, J. Org. Chem., 2011, 76, 8394 CrossRef CAS PubMed.
- F. Alonso, Y. Moglie, G. Radivoy and M. Yus, Adv. Synth. Catal., 2010, 352, 3208 CrossRef CAS.
- H. Sharghi, M. H. Beyzavi, A. Safavi, M. M. Doroodmand and R. Khalifeh, Adv. Synth. Catal., 2009, 351, 2391 CrossRef CAS.
- J. S. Yadav, B. V. S. Reddy, G. M. Reddy and D. N. Chary, Tetrahedron Lett., 2007, 48, 8773 CrossRef CAS.
- T. Boningari, A. Olmos, B. M. Reddy, J. Sommer and P. Pale, Eur. J. Org. Chem., 2010, 2010, 6338 CrossRef.
- H. Sharghi, M. Hosseini-Sarvari, F. Moeini, R. Khalifeh and A. S. Beni, Helv. Chim. Acta, 2010, 93, 435 CrossRef CAS.
- B. S. P. Anil Kumar, K. Harsha Vardhan Reddy, G. Satish, R. Uday Kumar and Y. V. D. Nageswar, RSC Adv., 2014, 4, 60652 RSC.
- H. Naeimi and V. Nejadshafiee, New J. Chem., 2014, 38, 5429 RSC.
- K. Rajender Reddy, C. Uma Maheswari, K. Rajgopal and M. Lakshmi Kantam, Synth. Commun., 2008, 38, 2158 CrossRef.
- H. Esmaeili-Shahri, H. Eshghi, J. Lari and S. A. Rounaghi, Appl. Organomet. Chem., 2018, 32, e3947 CrossRef.
- N. Noshiranzadeh, M. Emami, R. Bikas and A. Kozakiewicz, New J. Chem., 2017, 41, 2658 RSC.
- H. Sharghi and I. Ghaderi, Org. Chem. Res., 2017, 3, 162 Search PubMed.
- H. Sharghi, A. Khoshnood, M. M. Doroodmand and R. Khalifeh, J. Iran. Chem. Soc., 2012, 9, 231 CrossRef CAS.
- H. Sharghi, S. Ebrahimpourmoghaddam, M. M. Doroodmand and A. Purkhosrow, Asian J. Org. Chem., 2012, 1, 377 CrossRef CAS.
- G. Kumaraswamy, K. Ankamma and A. Pitchaiah, J. Org. Chem., 2007, 72, 9822 CrossRef CAS PubMed.
- J. Lu, E. Q. Ma, Y. H. Liu, Y. M. Li, L. P. Mo and Z. H. Zhang, RSC Adv., 2015, 5, 59167 RSC.
- S. Saranya, K. R. Rohit, S. Radhika and G. Anilkumar, Org. Biomol. Chem., 2019, 17, 8048 RSC.
- L. M. Ramos, M. O. Rodrigues and B. A. D. Neto, Org. Biomol. Chem., 2019, 17, 7260 RSC.
- K. K. Das, S. Manna and S. Panda, Chem. Commun., 2021, 57, 441 RSC.
- L. Biesen and T. J. J. Müller, Adv. Synth. Catal., 2021, 363, 980 CrossRef CAS.
- D. Insuasty, J. Castillo, D. Becerra, H. Rojas and R. Abonia, Molecules, 2020, 25, 505 CrossRef PubMed.
- J. F. Allochio Filho, B. C. Lemos, A. S. de Souza, S. Pinheiro and S. J. Greco, Tetrahedron, 2017, 73, 6977 CrossRef CAS.
- A. K. Gptar and M. Gupta, Biomaterials, 2005, 26, 3995 CrossRef PubMed.
- Q. A. Pankhurst, J. Connolly, S. K. Jones and J. Dobson, J. Phys. D: Appl. Phys., 2003, 36, R167 CrossRef CAS.
- T. Neuberger, B. Schöpf, H. Hofmann, M. Hofmann and B. von Rechenberg, J. Magn. Magn. Mater., 2005, 293, 483 CrossRef CAS.
- F. Mou, J. Guan, H. Ma, L. Xu and W. Shi, ACS Appl. Mater. Interfaces, 2012, 4, 3987 CrossRef CAS PubMed.
- D. Toulemon, B. P. Pichon, X. Cattoen, M. W. Man and S. Begin-Colin, Chem. Commun., 2011, 47, 11954 RSC.
- R. Chen, C. Zhi, H. Yang, Y. Bando, Z. Zhang, N. Sugiur and D. Golberg, J. Colloid Interface Sci., 2011, 359, 261 CrossRef CAS PubMed.
- Z. P. Sun, L. Liu, D. Z. Jia and W. Pan, Sens. Actuators, B, 2007, 125, 144 CrossRef CAS.
- T. Wang, L. Zhang, H. Wang, W. Yang, Y. Fu, W. Zhou, W. Yu, K. Xiang, Z. Su, S. Dai and L. Chai, ACS Appl. Mater. Interfaces, 2013, 5, 12449 CrossRef CAS PubMed.
- J. Saiz, E. Bringas and I. Ortiz, J. Chem. Technol. Biotechnol., 2014, 89, 909 CrossRef CAS.
- B. Chen, Z. Zhu, J. Ma, M. Yang, J. Hong, X. Hu, Y. Qiu and J. Chen, J. Colloid Interface Sci., 2014, 434, 9 CrossRef CAS PubMed.
- S. Hassanzadeh, R. Eisavi and M. Abbasian, Appl. Organomet. Chem., 2018, 32, e4520 CrossRef.
- R. Eisavi and S. Alifam, Phosphorus, Sulfur Silicon Relat. Elem., 2017, 193, 211 CrossRef.
- R. Eisavi, S. Ghadernejad, B. Zeynizadeh and F. M. Aminzadeh, J. Sulfur Chem., 2016, 37, 537 CrossRef CAS.
- R. Eisavi, F. Ahmadi, B. Ebadzade and S. Ghadernejad, J. Sulfur Chem., 2017, 38, 614 CrossRef CAS.
- S. Hassanzadeh, R. Eisavi and M. Abbasian, J. Sulfur Chem., 2019, 40, 240 CrossRef CAS.
- M. Mahmoudzadeh, E. Mehdipour and R. Eisavi, J. Coord. Chem., 2019, 72, 841 CrossRef CAS.
- R. Eisavi and A. Karimi, RSC Adv., 2019, 9, 29873 RSC.
- R. Eisavi and B. Zeynizadeh, Phosphorus, Sulfur Silicon Relat. Elem., 2016, 191, 65 CrossRef CAS.
- W. Wu, Q. G. He and C. Z. Jiang, Nanoscale Res. Lett., 2008, 3, 397 CrossRef CAS PubMed.
- R. Betancourt-Galindo, P. Y. Reyes-Rodriguez, B. A. Puente-Urbina, C. A. Avila-Orta, O. S. Rodríguez-Fernández, G. Cadenas-Pliego, R. H. Lira-Saldivar and L. A. García-Cerda, J. Nanomater., 2014, 2014, 5, DOI:10.1155/2014/980545.
- J. A. Widegren, M. A. Bennett and R. G. Finke, J. Am. Chem. Soc., 2003, 125, 10301 CrossRef CAS PubMed.
Footnote |
† Electronic supplementary information (ESI) available: FT-IR, 1H NMR and 13C NMR spectra of β-thiol-1,4-disubstituted-1,2,3-triazoles. See DOI: 10.1039/d1ra01588e |
|
This journal is © The Royal Society of Chemistry 2021 |
Click here to see how this site uses Cookies. View our privacy policy here.