DOI:
10.1039/D1RA01185E
(Paper)
RSC Adv., 2021,
11, 12614-12625
An asymmetric Salamo-based Zn complex supported on Fe3O4 MNPs: a novel heterogeneous nanocatalyst for the silyl protection and deprotection of alcohols under mild conditions
Received
12th February 2021
, Accepted 12th March 2021
First published on 31st March 2021
Abstract
In this study, a magnetic asymmetric Salamo-based Zn complex (H2L = salen type di-Schiff bases)-supported on the surface of modified Fe3O4 (Fe3O4@H2L-Zn) as a new catalyst was designed and characterized via numerous analytical techniques such as FT-IR spectroscopy, XRD, EDS, ICP-AES, SEM, TEM, TGA and VSM. An efficient and sustainable synthetic protocol has been presented for the synthesis of silyl ether substructures via the silyl protection of alcohols under mild conditions. The synthetic protocol involves a two-component solvent-free reaction between various hydroxyl-bearing substrates and hexamethyldisilazane (HMDS) as an inexpensive silylating agent using Fe3O4@H2L-Zn MNPs as a magnetically separable, recyclable and reusable heterogeneous catalyst. Fe3O4@H2L-Zn MNPs were also applied for the removal of silyl protecting groups from hydroxyl functions using water in CH2Cl2 under green conditions. The catalyst demonstrated good to excellent catalytic yield efficiency for both the reactions compared to the commercial metal-based catalysts under green conditions for a wide range of substrates.
1. Introduction
In numerous preparation methods of delicate organic compounds, some specific parts of their molecules cannot survive the required reagents or chemical environments. Therefore, these parts, or groups, must be protected.1–4 Regarding the number of protection and deprotection groups, it is highly significant to consider and reconsider the chemistry applied in unnatural structures and also in the building of nature's architecturally beautiful and diverse molecular frameworks. Usually attached to the asymmetrically substituted carbon atom, the hydroxyl group can be regarded as the most fundamental functional group in organic chemistry.5–10 Therefore, it is evident that a wide variety of approaches have been disclosed and also the enantioselective synthesis of alcohols can be regarded as one of the most important steps in total synthesis.11 Although there are important advances in the late-stage functionalization of complex molecules, the protection of hydroxyl groups is highly required during the succeeding steps.12 In order to protect the alcohol group, there are several methods. In this sense, silylation can be regarded as one of the most common and easy methods in order to protect hydroxyl and thiol groups.13 Silyl ethers are the most useful and important protecting groups for the protection of hydroxyl functional groups in organic chemistry from both synthetic and analytical point of views.14
During the recent decades, numerous types of silyl ethers have been developed via the reaction of silyl halides with parent alcohols in the presence of a base, such as triethylamine, pyridine, and n-butyl lithium.15–17 To date, numerous procedures have been introduced for the silylation of alcohols using different silylation reagents in the presence of various catalysts including organo bases (e.g. N-oxides and N-halo reagents), iodine, trihalides, transition metals, Brønsted–Lowry acids as well as catalyst-free conditions.2,18–20 These silylation methods are efficient, but unfortunately, they have serious disadvantages since they require a careful filtration or extraction process to remove the impurities derived from the reaction of by-product acids and co-bases during the silylation reaction.
Besides, R3SiCl, MeSiN = C(Me)OSiMe, Me3SiCl, or Me3SiOTf in the presence of base are the reagents applied in the traditional and conventional processes.12,21–29 Moreover, hexamethyldisilazane (HMDS) is a stable, commercially available and inexpensive reagent that can be used for the protection of hydroxy bearing compounds to trimethylsilyl ethers.30–32 Its handling does not require special precautions, and the workup is not time-consuming because the by-product of the reaction is ammonia, which is easily removed from the reaction medium.33,34
The use of nanostructured heterogeneous catalysts in organic transformations has recently been very exciting owing to their catalytic efficiency and selectivity.35–40 Furthermore, 2D materials have become an important platform to design numerous single-atom catalysts for diverse chemical reactions, such as N2 reduction, CO2 reduction, and CO oxidation.41–52 The ease of isolation and separation of the heterogeneous catalysts from the desired organic product and the recyclability and reusability further enhanced the sustainability of the catalysts.53–60 Moreover, the heterogeneous catalysts not only catalyze the reactions on their own, but also serve as an effective support for the immobilization of active catalysts and facilitate the efficient magnetic separation of the catalysts for their recovery and reusability.61–63 The functionalization and modification of iron oxide nanoparticles with numerous biocompatible and biodegradable materials in many different ways have been demonstrated with efficient and effective catalysts.59,64,65 Salen-based compounds can be considered as excellent candidates for the functionalization of iron oxide nanoparticles due to the presence of four coordination atoms (O, N, N, and O) in the center, which can coordinate with various metal ions to form M–Salen complexes.66 The structure of metal ion coordination with nitrogen and oxygen of salen complexes has attracted considerable attention in the field of catalytic methods in organic syntheses due to their important and interesting variable structures, simple synthesis route, high efficiency with high selectivity and easy recycling of the catalysts.67 Zinc is an inexpensive and readily available metal (zinc is easily extracted from the minerals in high purity). Low toxicity, low cost, abundance and accessibility of zinc make it attractive for application in catalysis chemistry.68–71
In the present study, we are concerned with the high yield synthesis of silyl ether substructures via the silyl protection of alcohols and phenols, followed by their deprotection via removal of silyl protecting groups from the hydroxyl functions under mild conditions using an asymmetric Salamo-based-Zn catalytic complex-functionalized magnetically separable nanocomposite as a recyclable and reusable nanocatalyst.
2. Experimental
2.1. Materials
All the reagents and solvents were purchased from Merck and used without additional purification.
2.2. Preparation of asymmetric Salamo-based-Zn supported on the surface of Fe3O4 MNPs
Fe3O4@APTES MNPs were prepared according to a previously reported method.72 Then, its surface was functionalized by H2L, which was prepared according to the procedure of Bian et al.66 For the synthesis of asymmetric Salamo-based ligand supported on Fe3O4 nanoparticles, 1 g of the as-prepared Fe3O4@APTES was dispersed in 50 ml of toluene via sonication for 45 min, and then H2L (3 mmol) was added to the mixture. The reaction mixture was stirred under nitrogen atmosphere at reflux conditions for 24 h. Then, the obtained Fe3O4@H2L product was separated via magnetic decantation and washed with hot ethanol and acetone to remove the unreacted ligand and dried in an oven at 50 °C for 8 h. The obtained Fe3O4@H2L (0.5 g) was dispersed in 25 ml of ethanol by sonication for 60 min and then zinc nitrate (3 mmol) was added to the reaction mixture. The reaction mixture was stirred under nitrogen atmosphere at 80 °C for 48 h. The final product (Fe3O4@H2L-Zn) was separated via magnetic filtration and washed with ethanol to remove the unattached substrates. The Fe3O4@H2L-Zn nanoparticulate product was dried in an oven at 60 °C for 8 h (Scheme 1).
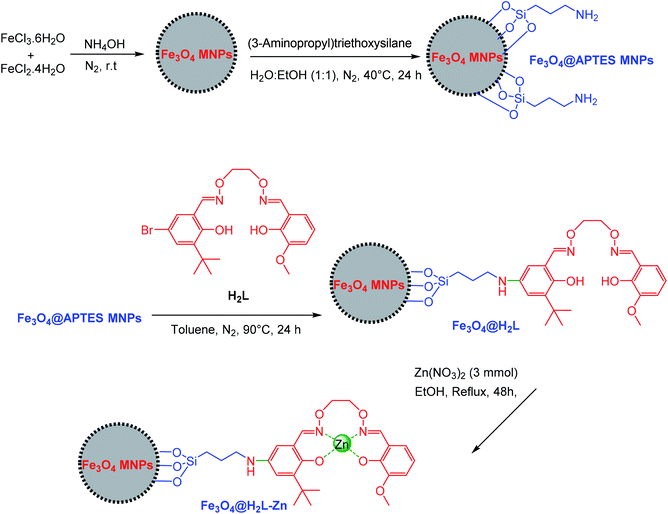 |
| Scheme 1 The stepwise synthesis of Fe3O4@H2L-Zn nanoparticles. | |
2.3. General procedure for the trimethylsilylation of alcohols
A mixture of alcohols (1 mmol), HMDS (0.8 mmol) and Fe3O4@H2L-Zn (6 mg) was stirred at room temperature under solvent-free conditions and the progress of the reaction was monitored by TLC. After the completion of the reaction, the catalyst was separated by an external magnet and the mixture was decanted. Then, the mixture was washed with EtOAc and water to destroy the extra amounts of HMDS and organic layer was dried over anhydrous Na2SO4. The evaporation of the solvent under a reduced pressure obtain the pure product without further purification.
2.4. General procedure for the deprotection of silyl ether derivatives
Fe3O4@H2L-Zn (6 mg) was added to a mixture of TMS ethers (1 mmol) in CH2Cl2 (4 ml) moistened by three drops of water and then the mixture was stirred at room temperature for the specified time and the progress of the reaction was monitored via TLC. After the completion of the reaction, the catalyst was separated by an external magnet and the mixture was decanted. The solvent was evaporated under a reduced pressure to obtain corresponding alcohols.
3. Results and discussion
3.1. Synthesis and characterization of the catalyst
3.1.1. Design of catalyst. The magnetic nano catalyst was prepared based on Scheme 1. First, magnetic nanoparticles (Fe3O4) were synthesized according to the literature using FeCl3·6H2O and FeCl2·4H2O with the addition of NH4OH.72 In order to prevent the agglomeration of the nanoparticles during the synthesis, the Fe3O4 MNPs were dispersed and then (3-aminopropyl)triethoxysilane (APTES) was reacted with it until the amine functional group got attached to it. Next, an H2L linker as the ligand was covalently bonded on the surface of Fe3O4@APTES groups by the intermolecular nucleophilic attack of the primary amine nucleophile to the haloalkane bond of H2L. Finally, for the preparation of zinc-loaded materials, Fe3O4@H2L-Zn particles were treated with Zn(NO3)2 as the Zn source (Scheme 1). The successful synthesis and physical and chemical properties of the as-prepared Fe3O4@H2L-Zn was investigated via FT-IR spectroscopy, XRD, EDX, ICP-OEC, SEM, TGA and VSM techniques.
3.1.2. Chemical composition of the catalyst. The FT-IR spectra of the Fe3O4 (a), Fe3O4@APTES (b), H2L (c), Fe3O4@h2L (d) and Fe3O4@H2L-Zn complex (e) are shown in Fig. 1. The FT-IR patterns in figure (a) and (b) are completely consistent with the previous analyses of Fe3O4 MNPs and Fe3O4@APTES, respectively.72 In the FT-IR curves of H2L and Fe3O4@H2L (Fig. 1c and d), strong C
N stretching vibration band in the region of 1590–1615 cm−1, C–O stretching vibration band around 1256 cm−1 and C
C band around 1456–1496 cm−1 provide evidences for the successful immobilization of the H2L ligand on the surface of the modified support.73 The shift on the C–O, C
N peaks in the Fe3O4@H2L-Zn to more lower wavenumbers in comparison to the Fe3O4@H2L confirm the successful complexion of Zn ions with the oxime nitrogen atoms and phenol oxygen atoms.73
 |
| Fig. 1 FT-IR spectra of (a) Fe3O4, (b) Fe3O4@APTES, (c) H2L, (d) Fe3O4@H2L and (e) Fe3O4@H2L-Zn MNPs. | |
The presence of Fe, O, Si, C, N, and Pd elements on the surface of the catalyst were confirmed by energy dispersive X-ray (EDX) measurements and there were no other elements showing the high purity of the sample (Fig. 2). As shown in this Figure, the presence of N was observed but Br was not observed. This indicated that the covalent adsorption of the H2L ligand successfully occurred on the catalyst surface. It is worth noting that the amount of zinc in Fe3O4@H2L-Zn was 1.17 × 10−3 mol g−1, which was determined by the ICP analysis.
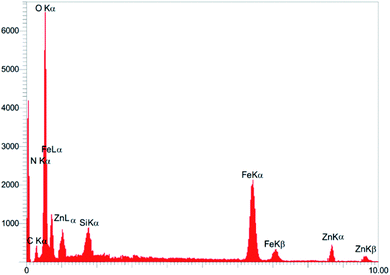 |
| Fig. 2 EDX analysis of Fe3O4@H2L-Zn MNPs. | |
Fig. 3 depicts the XRD patterns of Fe3O4 and Fe3O4@H2L-Zn complex. In the Fe3O4 pattern, six major peaks were observed around 2θ = 30°, 35°, 43°, 53°, 57°, and 62° that corresponded to the (220), (311), (400), (422), (511), and (440) Miller indices, respectively. It can be seen in this figure that the Fe3O4@H2L-Zn pattern is in good agreement with the characteristic peaks of bare Fe3O4, which indicates the retention of the crystalline spinel ferrite core structure during the functionalization of MNPs.74 In the wide angle XRD pattern (Fig. 3b), the diffraction peaks corresponding to Zn ions cannot be observed for Fe3O4@H2L-Zn, which reveals high zinc dispersion. The absence of Zn diffraction peaks indicates the formation of finely dispersed zinc species on the nanocomposite that are not detectable by this technique. However, the angles of the diffraction peaks of Fe3O4@H2L-Zn decreased in comparsion to those of Fe3O4 nanoparticles, which confirm the presence of zinc ions in the final complex with high dispersion.75
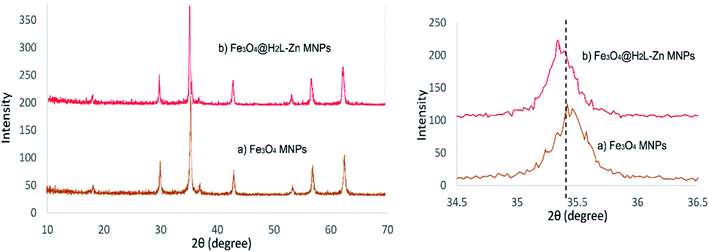 |
| Fig. 3 XRD pattern of (a) Fe3O4 and (b) Fe3O4@H2L-Zn MNPs. | |
3.1.3. Structure of the catalyst. Fig. 7 displays the FE-SEM images of Fe3O4@H2L-Zn. These images illustrated the presence of uniform and regular spherical particles. These type of particles are good candidates for both catalysis and adsorption processes (Fig. 4).
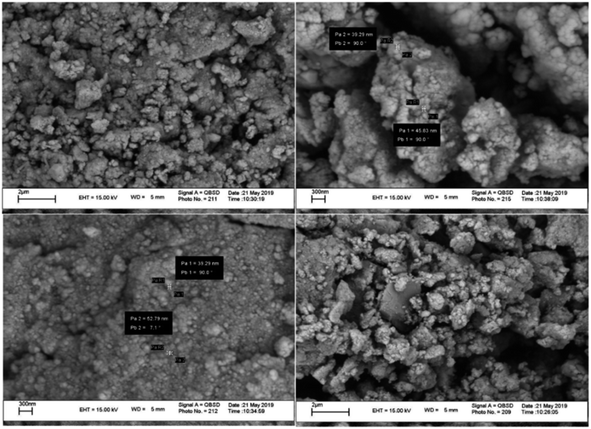 |
| Fig. 4 SEM images of Fe3O4@H2L-Zn MNPs. | |
The morphology and average size of Fe3O4@H2L-Zn were determined via transmission electron microscopy and the corresponding TEM micrographs are shown in Fig. 5. The TEM images show that the as-prepared nanocatalyst has almost a spherical-like shape with monodispersity. The average size of the as-synthesized Fe3O4@H2L-Zn was 22 nm, with the maximum number of particles having size in the range of 18–21 nm.
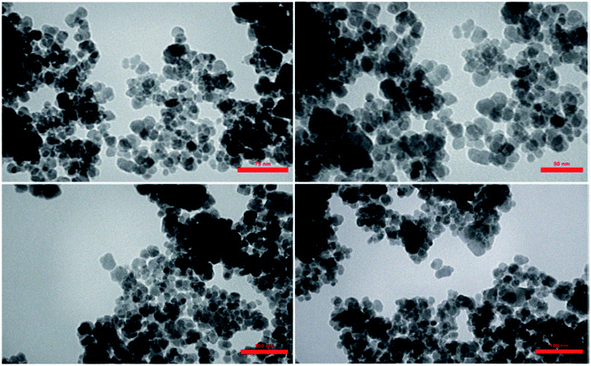 |
| Fig. 5 TEM images of Fe3O4@H2L-Zn MNPs. | |
3.1.4. Physicochemical properties of the catalyst. The thermal stability of Fe3O4, Fe3O4@APTES and Fe3O4@H2L-Zn nanocomposites was examined by thermogravimetric analysis (TGA) (Fig. 6). In all of the TGA curves, the first obvious weight loss was found in the temperature range of 25–200 °C, which was attributed to the release of physically adsorbed moisture and solvent from the sample.76 The other stage of gradual weight loss was found in the temperature range of 300–450 °C, which was caused by the decomposition of the APTES shells on the surface of the support. However, above 450 °C, catalyst decomposition started and the main weight change at 450–650 °C in the TGA curve represents the decomposition of the H2L-Zn hybrid material.77,78 As shown, the weight loss values of Fe3O4 to Fe3O4@H2L-Zn MNPs increased sequentially. The results show that with the increase in temperature, the organic groups of the products are gradually decomposed in the process of pyrolysis, which confirms the successful chemical adsorption of the organic complex layers via chemical bonding on the modified Fe3O4 MNPs.
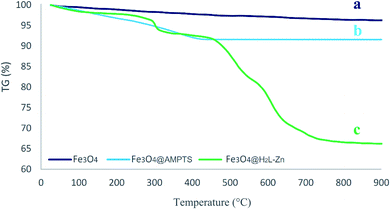 |
| Fig. 6 TGA curve of Fe3O4, Fe3O4@APTES and Fe3O4@H2L-Zn MNPs. | |
The vibrating sample magnetometer (VSM) technique was used to examine the magnetic properties of the Fe3O4@H2L-Zn and its synthons. The saturation magnetization values of Fe3O4, Fe3O4@APTES, Fe3O4@H2L, Fe3O4@H2L-Zn and recovered Fe3O4@H2L-Zn MNPs are shown in Fig. 7. As shown in the figure, the saturation magnetization (Ms) value from Fe3O4 to Fe3O4@H2L-Zn decreased sequentially. This result confirms the successful chemical adsorption of the H2L-Zn complex via chemical bonding with the modified Fe3O4 MNPs. As shown, the saturation magnetization value of Fe3O4@H2L-Zn was 43 emu g−1. Compared with that of Fe3O4 NPs (56 emu g−1), this decrease can be attributed to the presence of H2L-Zn and other functionalized groups on the surface of Fe3O4. The sequential decrease in the Ms value in each step can be a sufficient reason to confirm the successful immobilization of organic functional groups at different stages.
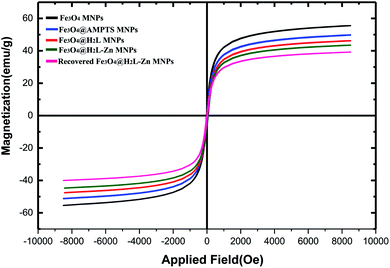 |
| Fig. 7 VSM curves of Fe3O4, Fe3O4@APTES, Fe3O4@H2L, Fe3O4H2L-Zn and recovered Fe3O4@H2L-Zn MNPs. | |
The nitrogen physisorption isotherm of the catalyst is shown in Fig. 8. The results of the BET analysis indicated that the highest surface area of the adsorbent was 121.92 m2 g−1. The large surface may endow the material with stronger catalytic activity. Furthermore, it can also be seen that the H2L-Zn incorporation does not significantly change the BET parameters of the supports. This could indicate that the H2L-Zn species are not incorporated into the framework but they are grafted on its surface.
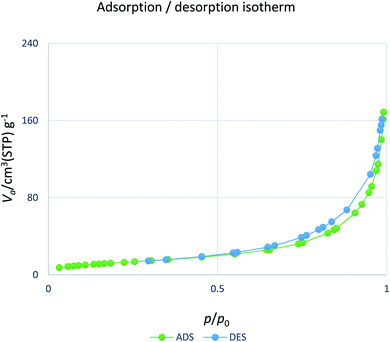 |
| Fig. 8 Nitrogen adsorption/desorption isotherm of Fe3O4@H2L-Zn MNPs. | |
3.2. Catalytic properties of the catalyst
After the successful synthesis and characterization of the Fe3O4@H2L-Zn complex, we focused on its catalytic activity in the selective trimethylsilylation of alcohols as well as its catalytic activity in the deprotection of the as-prepared silyl ethers to parent alcohols.
For the optimization of reaction conditions, we studied the reaction of HMDS as a green silylation agent using benzyl alcohol in different conditions, and the effective reaction parameters including amount of the catalyst, type of solvent and temperature were optimized. The results show that the reaction promotion is highly affected by the catalyst loading and the solvent type. The effects of the catalyst amount in the reaction were examined by varying the catalyst loadings (2, 3, 4, 5, 6 and 7 mg) in the model reaction. It was observed that the yield of the trimethylsilyl ethers product enhanced with the increase in the amount of Fe3O4@H2L-Zn from 2 to 6 mg (Table 1, entries 5–9). The best result in an appropriate time was obtained using 6 mg of the catalyst (Table 1, entry 9). It is worth mentioning that in the presence of 7 mg of Fe3O4@H2L-Zn almost the same result as that in the presence of 6 mg was observed (Table 1, entry 10). Moreover, in the catalyst free conditions, the reaction did not proceed at all even after 12 h (Table 1, entry 1). The efficiency of the catalyst was also considerably affected by the solvent (Table 1). Among the applied solvents such as acetonitrile, ethyl acetate, n-hexane, tetrahydrofuran, dichloromethane and solvent-free conditions, the best result was obtained in excellent yield after 10 min under solvent-free conditions as the reaction media (Table 1, entries 9 and 11–15). However, acetonitrile, ethyl acetate, n-hexane, tetrahydrofuran show good yields, but dichloromethane delivered a low yield of the corresponding product. By increasing the reaction temperature from 25 to 90 °C, the reaction time was reduced but room temperature was selected purely on the basis of green chemistry principle and high yield of the reaction in this condition. Finally, the best conditions for this coupling reaction are the following: Fe3O4@H2L-Zn (6 mg), at room temperature under solvent-free conditions (Table 1, entry 9).
Table 1 Optimization of the reaction conditions for the trimethylsilylation of benzyl alcohol (1 mmol) using HMDS (0.6 mmol) as a model compound

|
Entry |
Catalyst |
Catalyst (mg) |
Solvent |
Temperature |
Time |
Yield (%) |
1 |
— |
— |
Solvent free |
RT |
12 h |
NR |
2 |
Fe3O4 |
6 |
Solvent free |
RT |
2 h |
Trace |
3 |
Fe3O4@APTES |
6 |
Solvent free |
RT |
2 h |
33 |
4 |
Fe3O4@H2L |
6 |
Solvent free |
RT |
2 h |
Trace |
5 |
Fe3O4@H2L-Zn |
2 |
Solvent free |
RT |
10 |
51 |
6 |
Fe3O4@H2L-Zn |
3 |
Solvent free |
RT |
10 |
83 |
7 |
Fe3O4@H2L-Zn |
4 |
Solvent free |
RT |
10 |
89 |
8 |
Fe3O4@H2L-Zn |
5 |
Solvent free |
RT |
10 |
96 |
9 |
Fe3O4@H2L-Zn |
6 |
Solvent free |
RT |
10 |
100 |
10 |
Fe3O4@H2L-Zn |
7 |
Solvent free |
RT |
10 |
100 |
11 |
Fe3O4@H2L-Zn |
6 |
Acetonitrile |
RT |
15 |
94 |
12 |
Fe3O4@H2L-Zn |
6 |
EtOAc |
RT |
20 |
95 |
13 |
Fe3O4@H2L-Zn |
6 |
n-Hexane |
RT |
15 |
92 |
14 |
Fe3O4@H2L-Zn |
6 |
THF |
RT |
10 |
97 |
15 |
Fe3O4@H2L-Zn |
6 |
CH2Cl2 |
RT |
60 |
NR |
16 |
Fe3O4@H2L-Zn |
6 |
Solvent free |
45 |
7 |
100 |
17 |
Fe3O4@H2L-Zn |
6 |
Solvent free |
60 |
5 |
100 |
18 |
Fe3O4@H2L-Zn |
6 |
Solvent free |
90 |
5 |
100 |
After the optimization of reaction conditions, the direct silylation of hydroxyl bearing compounds for the preparation of their corresponding trimethylsilyl ethers was studied under the obtained optimized reaction conditions. The results are presented in Table 2. As shown in Table 2, the Fe3O4@H2L-Zn catalytic complex exhibited high efficiency in the solvent-free trimethylsilylation of numerous alcohols including several functional groups in excellent yields using hexamethyldisilazane under mild conditions at room temperature (25 °C). In this method, 24 different examples of benzylic and aliphatic alcohols including primary, bulky secondary, tertiary hydroxyl functional groups reacted with the HMDS (0.6 mmol) reagent and transformed to the corresponding trimethylsilyl ethers in good to excellent yields (89–100%) in short reaction time (8–60 min).
Table 2 Catalytic trimethylsilylation of various alcohols with HMDS in the presence of 6 mg of Fe3O4@H2L-Zn
As silyl ether can be further converted to the parent alcohols under acidic conditions, the silylation of alcohols can be regarded as an alternative method for hydroxyl protection under ambient reaction conditions. Merging the silyl protection/deprotection of alcohols with modern methodologies, such as green chemistry and nanoscience, has added additional value to these temporary components of synthetic intermediates. Furthermore, in the final part of our studies, we report the use of the resulted nanocomposite (Fe3O4@H2L-Zn) as a highly efficient catalyst for the chemoselective deprotection of some of the obtained trimethylsilyl ethers to their parent hydroxyl groups in wet dichloromethane moistened by 3 drops of water at room temperature. The results of this study are summarized in Table 3. As presented in Table 3, this catalytic system worked very well and the selected trimethylsilyl ethers gave the parent hydroxyl compounds in good to excellent yields in the presence of catalytic amount of (Fe3O4@H2L-Zn) at room temperature.
Table 3 Deprotection of trimethylsilyl ethers (1 mmol) in the presence of the Fe3O4@H2L-Zn catalyst in CH2Cl2 (4 ml) moistened by 3 drops of water at room temperature
3.3. Scale-up production
Developing a strategy for scaling up of the protection and deprotection of alcohols is a challenge for numerous drug and pharmaceutical manufacturers. Attempting larger-scale chemical fabrication with reactions previously optimized at the laboratory scale is a big challenge. To clearly demonstrate the potential of this method for the scaled up protection of benzyl alcohol and deprotection of its corresponding trimethylsilyl ether to its parent hydroxyl compound, the reactions were investigated using 20.0 mmol of substrates under optimized conditions. Desired protected and deprotected products were obtained in 97 and 95% yields, respectively.
4. Recycling ability, hot filtration and leaching tests of the catalyst
Recyclability is one of the most important properties of heterogeneous catalysts. The recyclability of the catalyst Fe3O4@H2L-Zn was studied in a typical trimethylsilylation reaction with benzyl alcohol and HMDS under the optimized reaction conditions. Briefly, after the finalization of each run of the trimethylsilylation reaction, which was monitored by TLC, the heterogeneous catalyst was separated using an external magnet, washed with acetone and water and dried overnight under vacuum at 60 °C to use in the next run. Fig. 9 shows that the Fe3O4@H2L-Zn complex can be reused 10 times and the catalytic activity was not significantly reduced and it was indicated that the catalyst has good recyclability. It was also proved by the hot filtration test that the Fe3O4@H2L-Zn complex played a catalytic role in the reaction rather than the free Zn in the solution. Furthermore, difference in the Zn content for the fresh and reused catalyst, after eight run, was only 0.5%, proving a low rate of leaching.
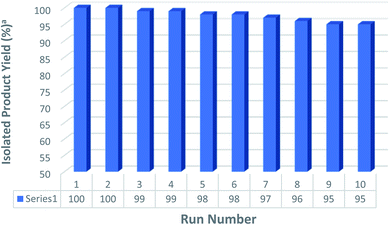 |
| Fig. 9 Recyclability of the catalyst. | |
5. Comparison
In order to investigate the efficiency of this new procedure compared to the reported procedures in the literature, the results for the trimethylsilylation of benzyl alcohol as the representative example was compared to the best of the well-known data from the literature, as outlined in Table 4. The comparison results show that the present catalytic system modified the Heck reaction time, yields and conditions.
Table 4 Comparing catalytic activity of Fe3O4@H2L-Zn with previously reported methods in the trimethylsilylation of benzyl alcohol
Entry |
Catalyst |
Time (min) |
Yielda (%) |
Ref. |
Isolated yield. |
1 |
La(NO3)3·6H2O |
95 |
98 |
79 |
2 |
Au/TiO2 |
60 |
96 |
80 |
3 |
Natural kaolinitic clay |
120 |
91 |
81 |
4 |
Aliquat 336 |
240 |
82 |
82 |
5 |
Fe3O4@H2L-Zn |
10 |
100 |
This work |
6. Conclusion
In summary, a novel catalyst H2L-Zn complex was successfully prepared on the Fe3O4 surface and was characterized by a progressive mode for the preparation. The Fe3O4@H2L-Zn catalysts have an efficient catalytic activity for the silyl protection and deprotection of alcohols by the selective trimethylsilylation of primary, secondary and tertiary aromatic and aliphatic alcohols in high yields in green media at 25 °C in low reaction times. More importantly, Fe3O4@H2L-Zn has several advantages such as simple to synthesize, wide range of carriers, ligand-free protocol and easy to separate the use of commercially available, eco-friendly, inexpensive and chemically stable reagents with operational simplicity, practicability and good to high yields. The separation of products and recycling of catalysts are easier and simpler with the assistance of an external magnet. The catalyst can be reused 10 times with little loss of activity.
7. Data availability
The data that support the findings of this study are available from the corresponding author upon reasonable request.
Conflicts of interest
There are no conflicts to declare.
References
- M. Mohebbi, P. Salehi, M. Bararjanian and S. N. Ebrahimi, J. Iran. Chem. Soc., 2018, 15, 47–53 CrossRef CAS.
- Y. Horino, M. Ishibashi, K. Nakasai and T. Korenaga, Tetrahedron, 2020, 76, 131493 CrossRef CAS.
- Y. Yang, M. Lin, J. Tang, S. Ma and Y. Yu, Anal. Bioanal. Chem., 2020, 412, 6679–6690 CrossRef CAS PubMed.
- J. Grzybek, M. Kubů, W. J. Roth, B. Gil, J. Čejka and V. Kasneryk, Catal. Today, 2020, 354, 133–140 CrossRef CAS.
- E. Indarti, H. Marwan, R. Rohaizu and W. D. Wanrosli, Int. J. Biol. Macromol., 2019, 135, 106–112 CrossRef CAS PubMed.
- J. F. Hartwig and E. A. Romero, Tetrahedron, 2019, 75, 4059–4070 CrossRef CAS PubMed.
- J. Seliger and M. Oestreich, Chem.–Eur. J., 2019, 25, 9358–9365 CrossRef CAS.
- S. Sittihan and T. F. Jamison, J. Am. Chem. Soc., 2019, 141, 11239–11244 CrossRef CAS PubMed.
- Y. Liu, Q. Zhang, M. Xu, H. Yuan, Y. Chen, J. Zhang, K. Luo, J. Zhang and B. You, Appl. Surf. Sci., 2019, 476, 632–640 CrossRef CAS.
- C. Zuo, Q. Chen, L. Tian, L. Waller and A. Asundi, Opt. Lasers Eng., 2015, 71, 20–32 CrossRef.
- R. Das and D. Chakraborty, Appl. Organomet. Chem., 2012, 26, 140–144 CrossRef CAS.
- M. Mittersteiner, M. A. Voigt, P. C. de Jesus and P. B. Brondani, ChemistrySelect, 2018, 3, 10717–10720 CrossRef CAS.
- K. Yoshida and K. I. Takao, Tetrahedron Lett., 2014, 55, 6861–6863 CrossRef CAS.
- J. Seliger, X. Dong and M. Oestreich, Angew. Chem., Int. Ed., 2019, 58, 1970–1974 CrossRef CAS PubMed.
- S. Yoshimatsu and K. Nakata, Adv. Synth. Catal., 2019, 361, 4679–4684 CrossRef CAS.
- K. Hyodo, S. Gandhi, M. Van Gemmeren and B. List, Synlett, 2015, 26, 1093–1095 CrossRef CAS.
- T. Avullala, P. Asgari, Y. Hua, A. Bokka, S. G. Ridlen, K. Yum, H. V. R. Dias and J. Jeon, ACS Catal., 2019, 9, 402–408 CrossRef CAS PubMed.
- M. Marin-Luna, B. Pölloth, F. Zott and H. Zipse, Chem. Sci., 2018, 9, 6509–6515 RSC.
- B. F. Bergel, L. Leite Araujo, A. L. dos Santos da Silva and R. M. Campomanes Santana, Carbohydr. Polym., 2020, 241, 116274 CrossRef CAS PubMed.
- T. Nagy, Á. Kuki, L. Nagy, M. Zsuga and S. Kéki, J. Mass Spectrom., 2018, 53, 240–246 CrossRef CAS PubMed.
- X. Wang, P. Li, Z. Li, W. Chen, H. Zhou, Y. Zhao, X. Wang, L. Zheng, J. Dong, Y. Lin, X. Zheng, W. Yan, J. Yang, Z. Yang, Y. Qu, T. Yuan, Y. Wu and Y. Li, Chem. Commun., 2019, 55, 6563–6566 RSC.
- P. Bunse, C. Schlepphorst, F. Glorius, M. Kitamura and B. Wünsch, J. Org. Chem., 2019, 84, 13744–13754 CrossRef CAS PubMed.
- J. E. Radcliffe, V. Fasano, R. W. Adams, P. You and M. J. Ingleson, Chem. Sci., 2019, 10, 1434–1441 RSC.
- C. Llorente, R. Jimenez, J. Jackie, Y. Brotman, A. R. Fernie and N. Sreenivasulu, Methods Mol. Biol., 2019, 1892, 187–199 CrossRef CAS PubMed.
- R. Hrdina, Synthesis, 2019, 51, 629–642 CrossRef CAS.
- B. Su, T. Lee and J. F. Hartwig, J. Am. Chem. Soc., 2018, 140, 18032–18038 CrossRef CAS PubMed.
- D. I. Zhilyaev, L. G. Voskresensky, N. Y. Polovkov and R. S. Borisov, J. Anal. Chem., 2018, 73, 1323–1326 CrossRef CAS.
- C. Díez-Poza, P. Val, F. Pulido and A. Barbero, Mar. Drugs, 2018, 16, 421 CrossRef PubMed.
- S. De Pooter, S. Latré, F. Desplentere and D. Seveno, J. Non-Cryst. Solids, 2018, 499, 217–226 CrossRef CAS.
- M. Galehassadi and S. Pourreza, J. Inorg. Organomet. Polym. Mater., 2019, 29, 541–549 CrossRef CAS.
- N. Anbu, C. Vijayan and A. Dhakshinamoorthy, Mol. Catal., 2019, 474, 110357 CrossRef CAS.
- A. Azad, M. G. Dekamin, S. Afshar, A. Tadjarodi and A. Mollahosseini, Res. Chem. Intermed., 2018, 44, 2951–2963 CrossRef CAS.
- M. Yadegari, M. Moghadam, S. Tangestaninejad, V. Mirkhani and I. Mohammadpoor-Baltork, Polyhedron, 2012, 31, 332–338 CrossRef CAS.
- S. T. Kadam and S. S. Kim, Green Chem., 2010, 12, 94–98 RSC.
- Z. Zhuang and D. Liu, Nano-Micro Lett., 2020, 12, 132 CrossRef CAS PubMed.
- C. Megías-Sayago, S. Navarro-Jaén, R. Castillo and S. Ivanova, Curr. Opin. Green Sustain. Chem., 2020, 21, 50–55 CrossRef.
- N. Kaur, N. Ahlawat, P. Bhardwaj, Y. Verma, P. Grewal and N. K. Jangid, Synth. Commun., 2020, 50, 137–160 CrossRef CAS.
- X. Wang, J. Wang, X. Sun, S. Wei, L. Cui, W. Yang and J. Liu, Nano Res., 2018, 11, 988–996 CrossRef CAS.
- X. Li, R. Zhang, X. Zhang, P. Zhu and T. Yao, Chem.–Asian J., 2020, 15, 1175–1179 CrossRef CAS PubMed.
- Y. Liu, B. Hu, S. Wu, M. Wang, Z. Zhang, B. Cui, L. He and M. Du, Appl. Catal., B, 2019, 258, 117970 CrossRef CAS.
- C.-X. Huang, G. Li, L.-M. Yang and E. Ganz, ACS Appl. Mater. Interfaces, 2021, 13, 608–621 CrossRef CAS PubMed.
- B. Song, Y. Zhou, H.-M. Yang, J.-H. Liao, L.-M. Yang, X.-B. Yang and E. Ganz, J. Am. Chem. Soc., 2019, 141, 3630–3640 CrossRef CAS PubMed.
- L. Xu, L.-M. Yang and E. Ganz, Theor. Chem. Acc., 2018, 137, 98 Search PubMed.
- Y. Liu, L.-M. Yang and E. Ganz, Condens. Matter, 2019, 4, 65 Search PubMed.
- J. Yang, X. Wang, Y. Qu, X. Wang, H. Huo, Q. Fan, J. Wang, L.-M. Yang and Y. Wu, Adv. Energy Mater., 2020, 10, 2001709 Search PubMed.
- L.-M. Yang, V. Bačić, I. A. Popov, A. I. Boldyrev, T. Heine, T. Frauenheim and E. Ganz, J. Am. Chem. Soc., 2015, 137, 2757–2762 CrossRef CAS.
- J.-H. Liu, L.-M. Yang and E. Ganz, ACS Sustainable Chem. Eng., 2018, 6, 15494–15502 CrossRef CAS.
- J.-H. Liu, L.-M. Yang and E. Ganz, J. Mater. Chem. A, 2019, 7, 3805–3814 RSC.
- J.-H. Liu, L.-M. Yang and E. Ganz, J. Mater. Chem. A, 2019, 7, 11944–11952 RSC.
- J.-H. Liu, L.-M. Yang and E. Ganz, RSC Adv., 2019, 9, 27710–27719 RSC.
- J.-H. Liu, L.-M. Yang and E. Ganz, Energy Environ. Mater., 2019, 2, 193–200 CrossRef CAS.
- R. Tong, Z. Sun, X. Wang, L. Yang, J. Zhai, S. Wang and H. Pan, Int. J. Hydrogen Energy, 2020, 45, 18912–18921 CrossRef CAS.
- S. Kumar, S. Jain, M. Nehra, N. Dilbaghi, G. Marrazza and K.-H. Kim, Coord. Chem. Rev., 2020, 420, 213407 CrossRef CAS.
- M. Ghabdian, M. A. Nasseri, A. Allahresani and A. Motavallizadehkakhky, Appl. Organomet. Chem., 2018, 32, e4545 CrossRef.
- Q. Jia, S. Huang, M. Hu, Y. Song, M. Wang, Z. Zhang and L. He, Sens. Actuators, B, 2020, 323, 128647 CrossRef CAS.
- X. Li, Y. Feng, B. Liu, D. Yi, X. Yang, W. Zhang, G. Chen, Y. Liu and P. Bai, J. Alloys Compd., 2019, 788, 485–494 CrossRef CAS.
- Y. Song, M. Xu, Z. Li, L. He, M. Hu, L. He, Z. Zhang and M. Du, Sens. Actuators, B, 2020, 321, 128527 CrossRef CAS.
- P. Xu, W. Lu, J. Zhang and L. Zhang, ACS Sustainable Chem. Eng., 2020, 8, 12366–12377 CrossRef CAS.
- M. Shi, B. Wang, Y. Shen, J. Jiang, W. Zhu, Y. Su, M. Narayanasamy, S. Angaiah, C. Yan and Q. Peng, Chem. Eng. J., 2020, 399, 125627 CrossRef CAS.
- A. Kazemi and S. Yang, JOM, 2019, 71, 1209–1214 CrossRef CAS.
- M. Wang, M. Hu, Z. Li, L. He, Y. Song, Q. Jia, Z. Zhang and M. Du, Biosens. Bioelectron., 2019, 142, 111536 CrossRef PubMed.
- Z. Lei, S. Hao, J. Yang, L. Zhang, B. Fang, K. Wei, Q. Lingbo, S. Jin and C. Wei, Chemosphere, 2021, 270, 128646 CrossRef CAS PubMed.
- Y.-C. Wang, K. Huang, X. Lai, Z. Shi, J.-B. Liu and G. Qiu, Org. Biomol. Chem., 2021, 19(9), 1940–1944 RSC.
- R. Hudson, Y. Feng, R. S. Varma and A. Moores, Green Chem., 2014, 16, 4493–4505 RSC.
- M. Wang, L. Yang, B. Hu, J. Liu, L. He, Q. Jia, Y. Song and Z. Zhang, Biosens. Bioelectron., 2018, 113, 16–24 CrossRef CAS.
- R.-N. Bian, J.-F. Wang, X. Xu, X.-Y. Dong and Y.-J. Ding, Appl. Organomet. Chem., 2020, e6040 Search PubMed.
- T. Rasheed, A. A. Hassan, M. Bilal, T. Hussain and K. Rizwan, Chemosphere, 2020, 259, 127369 CrossRef CAS PubMed.
- C. J. Rhodes, Sci. Prog., 2010, 93, 223–284 CrossRef CAS PubMed.
- H. J. Yoo and S. W. Youn, Org. Lett., 2019, 21, 3422–3426 CrossRef CAS PubMed.
- M. A. Wani, A. Kumar, M. D. Pandey and R. Pandey, Polyhedron, 2017, 126, 142–149 CrossRef CAS.
- X. Pan, Z. Liu, R. Cheng, X. He and B. Liu, J. Organomet. Chem., 2015, 775, 67–75 CrossRef CAS.
- U. Kurtan and A. Baykal, Mater. Res. Bull., 2014, 60, 79–87 CrossRef CAS.
- M. Asadi, K. Mohammadi, S. Esmaielzadeh, B. Etemadi and H. K. Fun, Polyhedron, 2009, 28, 1409–1418 CrossRef CAS.
- V. A. J. Silva, P. L. Andrade, M. P. C. Silva, D. A. Bustamante, L. De Los Santos Valladares and J. Albino Aguiar, J. Magn. Magn. Mater., 2013, 343, 138–143 CrossRef CAS.
- Z. Lv, Q. Wang, Y. Bin, L. Huang, R. Zhang, P. Zhang and M. Matsuo, J. Phys. Chem. C, 2015, 119, 26128–26142 CrossRef CAS.
- B. Maleki, O. Reiser, E. Esmaeilnezhad and H. J. Choi, Polyhedron, 2019, 162, 129–141 CrossRef CAS.
- L. Moradi and M. Tadayon, J. Saudi Chem. Soc., 2018, 22, 66–75 CrossRef CAS.
- A. Ahmadi, T. Sedaghat, R. Azadi and H. Motamedi, Catal. Lett., 2020, 150, 112–126 CrossRef CAS.
- B. Akhlaghinia, Phosphorus, Sulfur Silicon Relat. Elem., 2009, 184, 2530–2535 CrossRef CAS.
- C. Gryparis and M. Stratakis, Chem. Commun., 2012, 48, 10751 RSC.
- T. T. Upadhya, T. Daniel, A. Sudalai, T. Ravindranathan and K. R. Sabu, Synth. Commun., 1996, 26, 4539–4544 CrossRef CAS.
- M. Lissel and J. Weiffen, Synth. Commun., 1981, 11, 545–549 CrossRef CAS.
|
This journal is © The Royal Society of Chemistry 2021 |
Click here to see how this site uses Cookies. View our privacy policy here.