DOI:
10.1039/D0RA10039K
(Paper)
RSC Adv., 2021,
11, 3981-3989
Upconversion luminescence and temperature sensing properties of NaGd(WO4)2:Yb3+/Er3+@SiO2 core–shell nanoparticles†
Received
27th November 2020
, Accepted 5th January 2021
First published on 21st January 2021
Abstract
Optical thermometry based on the fluorescence intensity ratio (FIR) of two thermally coupled levels in lanthanide ions has potential application in non-contact optical temperature sensing techniques. In this work, a shell of SiO2 with tunable thickness was uniformly coated on NaGd(WO4)2:Yb3+/Er3+ core upconversion nanoparticles (UCNPs). The effects of the silica shell on UC luminescence and thermal sensing properties of core–shell NaGd(WO4)2:Yb3+/Er3+@SiO2 UCNPs were investigated. Under 980 nm laser excitation, the temperature-dependent UC emission spectra of obtained samples were measured. The FIR was analyzed based on the thermally coupled 2H11/2 and 4S3/2 levels of Er3+ in the biological temperature range of 300–350 K, in which the Boltzmann distribution is applied. The emission from the upper 2H11/2 state within Er3+ was enhanced as temperature increased due to the thermal effect. Absolute sensitivities (SA) and relative sensitivities (SR) of the core and core–shell UCNPs were calculated. It was found that after SiO2 coating, the maximum SA was enhanced by ∼2-fold (1.03% K−1 at 350 K). Especially, SA was as high as 2.14% K−1 at 350 K by analyzing the FIR of the non-thermally coupled 2H11/2 and 4F9/2 levels.
1. Introduction
Lanthanide-doped nanomaterials have been widely investigated in bio-therapies, such as magnetic resonance imaging, photodynamic therapy, photothermal therapy, and X-ray tomography because of their outstanding chemical and optical properties.1–5 In biological environments, temperature is an important parameter. However, it is not easy to get accurate temperature in vivo directly. Recently, upconversion (UC) luminescent materials for optical temperature sensing application have been received considerable attention.6 It is based on the fluorescence intensity ratio (FIR) of two thermally coupled energy levels, which can provide a non-invasive technique to monitoring temperature with a high sensitivity and a fast response. This technique is independent on variations of sample concentration and intensity fluctuation.7,8 The energy difference is required to be in the range of 200–2000 cm−1 to enable a Boltzmann distribution for the population ratio of two neighboring excited states.9 The Yb3+ and Er3+ ions are the most popular ion couple to realize UC luminescence. The 2H11/2 and 4S3/2 levels within Er3+ are thermally coupled with energy gap of ∼800 cm−1. Yb3+ ions are employed as the co-doping ions to sensitize Er3+ due to the large absorption cross-section at 980 nm of Yb3+ and the efficient energy transfer from Yb3+ to Er3+.
Compounds such as oxides, fluorides, and oxysulfides, have been reported with good properties of optical temperature sensing.10,11 However, to enable good control of shape and uniformity, UC nanoparticles (UCNPs) are usually synthesized in non-polar solvents. Then, aqueous dispersibility is absent for the UCNPs. Therefore, post-treatments are usually required.12 In general, rare-earth oxides have better thermal stability and thermal sensitivity than fluorides,13–15 and thus are promising in bio-imaging and bio-sensing. Coating the nanoparticles with shell structures is a common approach to eliminate the surface defects and enhance the luminescence, so the optical thermometry performance of the nanoparticles can be improved.16–18 A versatile shell is silica due to its high chemical stability, optical transparency, and easy control of shell thickness. Especially, for biological applications, the silica is non-toxic and bio-compatible,19,20 and the surface of the silica can be further modified to enable dispersity in a variety of polar solvents.21 The silica can be porous and can realize targeting binding, such as for drug delivering.22–25 Therefore, SiO2 coating on lanthanide doped nanomaterials can not only improve the chemical and physical properties, but expand the application of lanthanide doped luminescent materials in biomedicine fields.
Lanthanide doped double tungstates have been investigated as potential thermometric probes due to their good thermal stability and high thermal sensitivity.26–28 Temperature sensing performance of material can be improved after silica coating. It has been reported that the performing temperature of nanothermometry for the classical up-converting nanoparticles NaYF4:Er3+,Yb3+ was expanded from 600 K to 900 K, which enables the application of the material in high temperature environments.29 The protective effect of silica shell benefits the UCNPs to maintain the morphology and optical properties at high temperatures with good repeatability. In addition, the UC luminescence and the thermal sensitivity can be enhanced by the silica coating, which was demonstrated by the study on LuVO4:Yb3+/Er3+.30
In this work, NaGd(WO4)2:Yb3+/Er3+ (NGW:Yb3+/Er3+) core UCNPs and NaGd(WO4)2:Yb3+/Er3+@SiO2 (NGW:Yb3+/Er3+@SiO2) core–shell UCNPs were successfully synthesized. Silica with different thickness was coated on NGW:Yb3+/Er3+ nanoparticles by Stöber method. The morphology, structure and luminescence properties of the core NGW:Yb3+/Er3+ and core–shell NGW:Yb3+/Er3+@SiO2 UCNPs were characterized. Performance of optical temperature sensing was studied via the FIR analysis on the two thermally coupled energy levels 2H11/2 and 4S3/2 within Er3+. The benefits of silica shell coating were also discussed in detail.
2. Experimental
2.1 Materials
Absolute ethanol (Analytical Reagent, A.R.), ammonium hydroxide (A.R.), gadolinium(III) acetate hydrate (99.9%), ytterbium(III) acetate hydrate (99.9%), erbium(III) acetate hydrate (99.9%), sodium tungstate hydrate (A.R.), ethylene glycol (A.R.), tetraethyl orthosilicate (TEOS, 99.0%) were used as raw materials without further purification.
2.2 Synthesis of NGW:Yb3+/Er3+ UCNPs
NGW:Yb3+/Er3+ core UCNPs were synthesized with ethylene glycol-assistant hydrothermal method. Firstly, solutions of 0.10 mol L−1 Gd(CH3COOH)3, 0.10 mol L−1 Yb(CH3COOH)3, 0.02 mol L−1 Er(CH3COOH)3 and 0.20 mol L−1 Na2WO4 were prepared via dissolving the reactants separately in deionized water. Next, 3.33 mL Na2WO4 was added to the solution containing 2.65 mL Gd(CH3COOH)3, 0.67 mL Yb(CH3COOH)3 and 83 μL Er(CH3COOH)3 under magnetic stirring. After stirring for 5 min, 27 mL ethylene glycol was mixed into the solution with following vigorous stirring for 30 min. Subsequently, the mixture was transferred into a 40 mL Teflon-lined stainless autoclave, which was sealed and maintained at 200 °C for 20 h. The white products were collected by centrifugation and washed three times with distilled water and ethanol, and were obtained in powder after drying at 70 °C for 12 h. Finally, the obtained UCNPs were annealed at 600 °C for 3 h with temperature rise of 2 °C min−1 in a muffle furnace.
2.3 Synthesis of NGW:Yb3+/Er3+@SiO2 UCNPs
In order to coat a SiO2 shell onto the NGW:Yb3+/Er3+ UCNPs, 0.030 g NGW:Yb3+/Er3+ UCNPs were dispersed in mixtures including 50 mL ethanol, 10 mL deionized water, and 2 mL ammonium hydroxide in a 100 mL flask via ultrasonication for 20 min. Then, TEOS dropwise was added with mild stirring. To prepare core–shell UCNPs with various SiO2 shell thickness, a certain amount of TEOS (10 μL, 20 μL, 40 μL, 80 μL, 160 μL and 320 μL) was added into the above mentioned solution with stirring at room temperature for 8 h. The suspensions were washed by deionized water and ethanol for three times, and the NGW:Yb3+/Er3+@SiO2 UCNPs were collected by centrifugation and further dried at 70 °C for 12 h. Finally, the obtained UCNPs were annealed at 600 °C for 3 h with a heating rate of 2 °C min−1 in a muffle furnace.
2.4 Characterization
Crystal phase of the prepared UCNPs was determined by X-ray diffractometer (XRD, RIGAKU, D-MAX 2200 VPC, Cu Kα radiation) at a scanning rate of 10° min−1 with a step of 0.02° and 2θ ranging from 10° to 70°. Fourier transform infrared (FT-IR, Frontier) spectra were measured within the frequency range of 400–4000 cm−1 by using the KBr pellet technique. Morphologies of UCNPs were characterized by scanning electron microscope (SEM, field-emission SEM, Zeiss Gemini 500) with an energy dispersive X-ray spectrometer (EDS, Bruker Flat QUAD). High-Resolution Transmission Electron Microscopies (HRTEM) were analyzed by using spherical aberration corrected transmission electron microscope JEM-ARM200P. UC emission spectra and decay curves at room temperature were obtained using the Edinburgh Instruments FLS1000 spectrometer with a power tunable 980 nm laser as the excitation light source and a detector of photomultiplier tube (Hamamatsu R928P). Temperature-dependent UC emission spectra were measured using the OXFORD instrument with a temperature controlling system under nitrogen cryogenics.
3. Results and discussion
3.1 Crystal structure and morphologies
The synthetic procedures of core NGW:Yb3+/Er3+ and core–shell NGW:Yb3+/Er3+@SiO2 UCNPs are schematically shown in Fig. 1a. The core UCNPs were synthesized initially by the hydrothermal method. Then, the tunable silica layers were coated on the core NGW:Yb3+/Er3+ UCNPs by the Stöber method. Finally, both the core and core–shell UCNPs were sintered in air at 600 °C for 3 h to improve the crystallinity and enhance the luminescence properties.
 |
| Fig. 1 Characterizations for the core NGW:Yb3+/Er3+ and the core–shell NGW:Yb3+/Er3+@SiO2 UCNPs after annealing. (a) Schematic illustration for the synthesis. (b) XRD patterns. (c) FT-IR spectra. | |
The NaGd(WO4)2 crystal is in a scheelite-like tetragonal structure with I41/a space group and cell parameters of a = b = 0.5243 nm, c = 1.1368 nm.31 The phase composition and crystalline nature of the prepared samples at each stage have been characterized by XRD measurements. Fig. 1b shows the XRD patterns of the core and core–shell UCNPs. Referring to the NaGd(WO4)2 standard (JCPDS#25-0829), both the core and core–shell UCNPs are in the tetragonal structure. No second diffraction peak can be observed after the silica coating.
The surface chemistry of the core NGW:Yb3+/Er3+ and core–shell NGW:Yb3+/Er3+@SiO2 UCNPs were analyzed by FT-IR measurements as shown in Fig. 1c. The multiple absorption peaks from 700 cm−1 to 900 cm−1 and weak absorption band around 927 cm−1 are assigned to the asymmetrical stretching vibrations and symmetrical stretching vibrations of W–O in the WO42− group.32,33 The peak around 2342 cm−1 observed in both UCNPs is due to the asymmetrical C–O stretching mode from ambient of CO2.34 In addition, the broad absorption bands near 3405 cm−1 and 1600 cm−1 can be attributed to the O–H stretching and bending vibrations of water molecules, respectively. The water adsorption on the UCNPs can occur during the preparation of the UCNPs, especially because the UCNPs are nanocrystalline. The new peaks at 1095 cm−1 and 472 cm−1 (curve B) belong to the symmetrical stretching vibration of Si–O–Si and the bending vibration of Si–O, which indicates the successful coating of silica shell.
To explore the direct formation of the silica layer around the NGW:Yb3+/Er3+ UCNPs, scanning transmission electron microscopy in scanning electron microscopy (STEM-in-SEM) was used to determine the morphology of the products in different stages as shown in Fig. 2. Core NGW:Yb3+/Er3+ UCNPs are monodisperse in a regular olivary shape with an average size of 300 nm × 150 nm (Fig. 2a). We can observe the distinct contrast between the core and the shell structures. The low contrast contour demonstrates a uniform growth of the silica shell on the core NGW:Yb3+/Er3+ UCNPs. The mean thickness of silicon shell is 25 nm (Fig. 2c). The morphology and monodispersity for the UCNPs are unaltered after the SiO2 coating. Therefore, the STEM images confirm that the NGW:Yb3+/Er3+ UCNPs are coated by silica shell successfully.
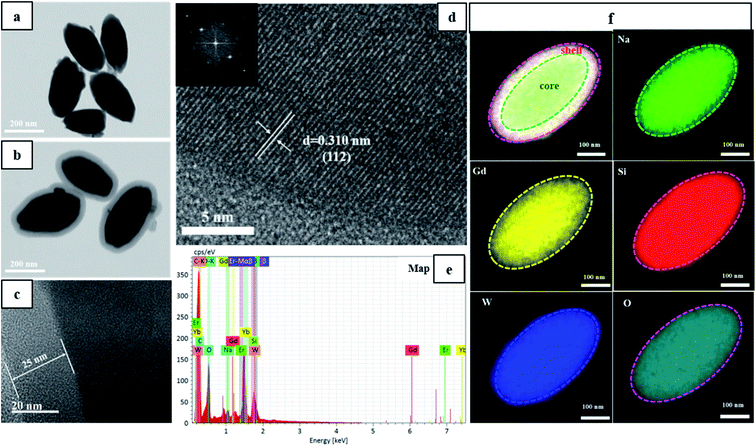 |
| Fig. 2 Electron microscopy characterizations of the core NGW:Yb3+/Er3+ and the core–shell NGW Yb3+/Er3+@SiO2 UCNPs. (a and b) STEM images. (c and d) HR-TEM images. (e) EDS spectrum. (f) Elemental mapping profiles. | |
Lattice fringes can be well-resolved in the HR-TEM image (Fig. 2d) and the distance of lattice fringe is 0.310 nm, which is consistent with the d-spacing between (112) planes of NaGd(WO4)2 (JCPDS#25-0829). The inset in Fig. 2d is the corresponding fast Fourier transform pattern, indicating a single crystalline nature of the inner core NaGd(WO4)2. Moreover, the EDS spectra and elemental mapping profile of the core–shell UCNPs (Fig. 2e and f) were collected through a single core–shell UCNP to qualitatively analyze the chemical compositions. The resulting elemental mapping profile in Fig. 2f reveals the homogeneous distribution of Na, Gd, W, Si, O in the core–shell UCNPs. Notice that the Si and O elements (red and indigo) cover larger area than other elements, which confirms the existence of the silicon outer shell.
For biological nanomaterial, it is imperative to produce UCNPs with good control on morphology, size, and aqueous dispersity. To give an insight into the effects of SiO2 shell on morphology and monodispersity, the obtained core and core–shell UCNPs before and after annealing are characterized by STEM as showed in Fig. S1.† The core NGW:Yb3+/Er3+ UCNPs are well-dispersed in water after the hydrothermal reaction. However, the annealing process, which is used to improve the luminescence properties of the UCNPs, could cause a severe agglomeration (see Fig. S1b†). This problem can be solved mostly by coating SiO2 shell, as shown in Fig. S1c.† Due to the protective effect of the silica, the NGW Yb3+/Er3+@SiO2 core–shell UCNPs after annealing preserve the morphology and the monodispersity. In addition, the thickness of SiO2 layer can be tuned by changing the amount of TEOS that is the silica source during the shell growth. The STEM images of the NGW Yb3+/Er3+@SiO2 core–shell UCNPs with silica layer in different thickness are shown in Fig. S2.† The average thickness of SiO2 layer is calculated to be 15 nm, 25 nm, 40 nm, 60 nm, 90 nm, 120 nm for the UCNPs synthesized with 10 μL, 20 μL, 40 μL, 80 μL, 160 μL, and 320 μL TEOS. If the TEOS is much excess, spherical silica can be formed as a second phase (Fig. S2f†).
3.2 Upconversion luminescence properties and mechanism
To investigate the effect of the silica shell on UC emission, the UC spectra of the core (NGW:Yb3+/Er3+) and core–shell (NGW:Yb3+/Er3+@SiO2) UCNPs were measured under excitation of 980 nm laser (power density of 56 mW cm−2). The optimal doping concentrations for Yb3+/Er3+ ions are 20% Yb3+ and 0.5% Er3+ according to the analysis of concentration quenching (Figure S3†). As shown in Fig. 3a, the UC emission consists of intra-configurational 4f–4f Er3+ transitions at green and red regions. The red emission with maximum intensity at 657 nm derives from the 4F9/2 → 4I15/2 transition. The green emission is attributed to the transitions from the thermally coupled states 2H11/2 and 4S3/2 to the ground state 4I15/2 at 531.5 nm and 553 nm. The silica shell has no influence on the position of emission lines and the relative UC emission intensity. For nanoparticles, on the one hand, UC luminescence can be enhanced by growth of SiO2 shell owning to the passivation effect to reduce the surface defects.35–38 On the other hand, SiO2 layers can quench the UC emission due to O–H vibrations. As our UCNPs before and after silica coating are thermally treated, the above effects of silica coating can be neglected. As a result, the core–shell UCNPs are similar to the core UCNPs on the UC luminescence intensity.
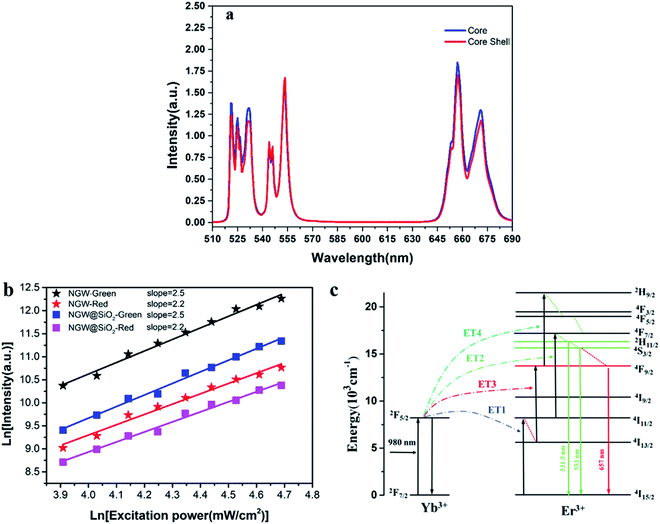 |
| Fig. 3 (a) UC emission spectra for the core NGW:Yb3+/Er3+ and the core–shell NGW Yb3+/Er3+@SiO2 UCNPs under excitation of 980 nm laser (power density of 56 mW cm−2). (b) Double logarithmic plot of green and red UC emission intensity versus excitation power density for the core and core–shell UCNPs. The solid lines are the linear fits of the double logarithmic plots. (c) Energy-level diagram for UC emission. | |
In the Yb3+–Er3+ ion couple, Yb3+ ions can resonantly transfer energy to neighboring Er3+ ions involving a multi-photon process. UC emission spectra were measured under different excitation powder density of laser. The relation of UC emission intensity and pumping power density can be described by eqn (1):
where
I is the UC emission intensity,
P represents the 980 nm laser power density, and value
n is the number of pumped IR photons that are required for UC emission. The logarithm of UC emission intensity is plotted
versus power in
Fig. 3b, indicating a two-photon UC process for the red emission. Both two- and three-photon UC processes contribute to the green emission. The silica shell barely affects the UC processes. The energy level diagram and the proposed energy transfer UC mechanism are schematically shown in
Fig. 3c. Upon excitation of 980 nm laser, the Yb
3+ ions are excited from the ground state
2F
7/2 to the excited state
2F
5/2. Energy could be resonantly transferred from Yb
3+ excited state to Er
3+ 4I
11/2 by ground state absorption. The Er
3+ ion is excited to the
4F
7/2 excited state by subsequent excited state absorption. Fast nonradiative relaxation occurs from
4F
7/2 to
2H
11/2,
4S
3/2 or
4F
9/2 states. An alternative path to populate the red emission state is originated from the nonradiative relaxation from
4I
11/2 to
4I
13/2 and the following excited state absorption. From the red emitting
4F
9/2 level, a third photon can be absorbed and excites Er
3+ to
2H
9/2 state. Finally, the radiative decay from the excited states
2H
11/2,
4S
3/2 and
4F
9/2 to the ground state
4I
15/2 gives rise to green and red emission.
Fig. 4a and b shows the luminescence decay curves of the 2H11/2/4S3/2 and 4F9/2 excited states for both core and core–shell UCNPs. The rise time indicates the energy transfer of Yb3+ to Er3+ ions. Following decay fits to the mono-exponential behavior. The lifetime for the 2H11/2/4S3/2 green UC emission is 40.2 μs (core) and 40.7 μs (core–shell). For the 4F9/2 red emission, the lifetime is 68.4 μs (core) and 66.6 μs (core–shell). Again, the results of decay time confirm that UC emission and UC efficiency is unaltered with the silica coating. The decay time of the green and the red UC emission is 2–3 times longer than those for NaY(WO4)2:Er3+/Yb3+ UCNPs in our previous work.39 Reason is that the UCNPs in this work is relatively large in size and is thermally treated, thus the quenching from defects and surrounding ligands is largely suppressed.
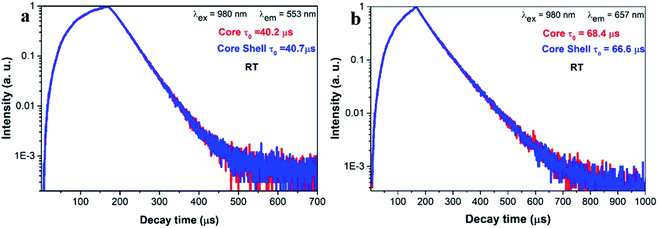 |
| Fig. 4 Luminescence decay of (a) 2H11/2/4S3/2 green emission and (b) 4F9/2 red emission for the core NGW:Yb3+/Er3+ and the core–shell NGW Yb3+/Er3+@SiO2 UCNPs under excitation of 980 nm laser (power density of 56 mW cm−1−2). | |
To further justify the effects of the silica coating on UC luminescence, the NGW:Yb3+/Er3+ core UCNPs were coated with a silica shell in varied thickness. The UC emission spectra for these core–shell UCNPs (Fig. S4†) show that the UC emission intensity decreases gradually upon coating thicker layer of silica. It was speculated that the silica could attenuate the emission. The integrated intensity ratio of green and red emission is plotted in Fig. S4.† With the increased silica shell, the integrated intensity ratio of green/red emission increases. This is contrary to the usual observation of enhanced red emission, thus decreased green/red intensity ratio.35,40 In those cases, the nonradiative decay from Er3+ 4I11/2 to 4I13/2 state is enhanced due to the O–H quenching as the energy gap between 4I11/2 and 4I13/2 states matches the O–H vibration energy (3200–2600 cm−1).41,42 Then, there is a high probability that the second IR photon excites Er3+ from the 4I13/2 state to the red emitting 4F9/2 state. In our case, the core–shell UCNPs with thermal treatment are limited influenced by the O–H quenching. This agrees with the unchanged green and red emitting lifetime after the silica coating because the nonradiative decay rate is unaltered.
3.3 Luminescence thermometry
Temperature sensing properties were measured and compared for the core NGW:Yb3+/Er3+ and core–shell NGW:Yb3+/Er3+@SiO2 UCNPs. Temperature-dependent UC emission spectra of UNCP powders were collected in the temperature range of biological systems (300–350 K in a step of 5 K) under 980 nm laser excitation (power density of 162 mW cm−1−2). Before measuring spectra, each temperature point holds for at least 5 min for stabilization. The thermocouple can measure the real-time temperature and compensate the caused laser heating. Furthermore, the laser power density is relatively low, thus the laser heating effect should be slight. As the population probability in the 2H11/2 and 4S3/2 states follows the Boltzmann's distribution, the relative emission intensity in the two states changes with temperature. The fluorescence intensity ratio (FIR) follows eqn (2) |
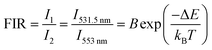 | (2) |
where I531.5 nm and I553 nm are the integrated UC emission intensity of the 2H11/2 and 4S3/2 levels, ΔE is the energy gap between the 2H11/2 and 4S3/2 levels, kB is the Boltzmann's constant, T is the absolute temperature and B is a constant. Fig. 5a shows the temperature (300–350 K) dependent UC emission spectra of the core–shell NGW:Yb3+/Er3+@SiO2 UCNPs with the normalized intensity of 4S3/2 → 4I15/2 emission. The emission intensity of the transition 2H11/2 → 4I15/2 increases with temperature, as expected for the thermal coupling of excited states. Thus the FIR of the 2H11/2 and 4S3/2 green emission increases as shown in Fig. 5b. Fitting the plot with eqn (2), ΔE between the 2H11/2 and 4S3/2 states is calculated to be about 845.8 cm−1 and matches the experimental value of 796.4 cm−1 determined from the emission spectra of the core and core–shell UCNPs (Fig. 3a). For temperature sensors, absolute sensitivities (SA) and relative sensitivities (SR) are key parameters for practical applications to evaluate the temperature sensitivity of FIR technique and are defined as following equations: |
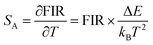 | (3) |
|
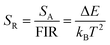 | (4) |
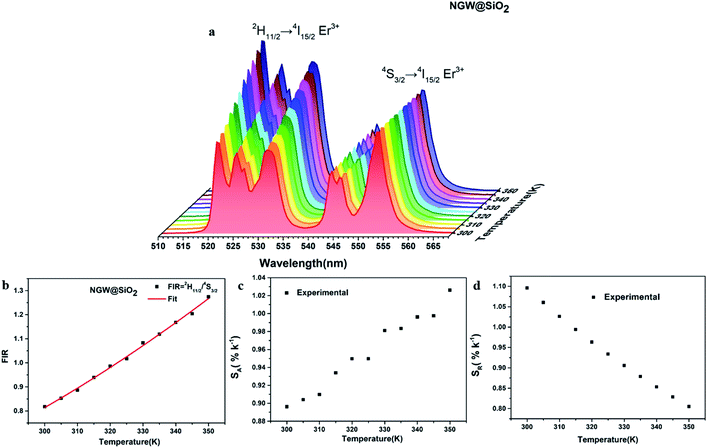 |
| Fig. 5 FIR analysis of the 2H11/2 and 4S3/2 levels for the core–shell NGW:Yb3+/Er3+@SiO2 UCNPs in the temperature range from 300 K to 350 K. (a) UC emission spectra under 980 nm laser excitation (power density of 162 mW cm−1−2). The spectra are normalized to the emission peak at 553 nm. (b) FIR, (c) SA, and (d) SR versus temperature. | |
Fig. 5c and d shows the plots of SA and SR versus temperature, respectively. In the biological temperature range from 300 K to 350 K, SA continuously increases with temperature, whereas SR decreases. The maximum SA is 1.03% K−1 at 350 K and the maximum SR is 1.10% K−1 at 300 K for the core–shell NGW:Yb3+/Er3+@SiO2 UCNPs. As a comparison, the temperature-sensing properties of the core NGW:Yb3+/Er3+ UCNPs were evaluated (Fig. S5†). The SA of the core–shell NGW:Yb3+/Er3+@SiO2 UCNPs is ∼2-fold enhanced compared with the core NGW:Yb3+/Er3+ UCNPs in the biological temperature range. The observation of improved thermal sensitivity after silica coating is in agreement with previous studies on the system of vanadates.30,43 It was observed that an improvement of thermal sensitivity after silica coating, but details in the mechanism for the performance improvements is still not clear. Silica coating can improve the thermal stability for NaYF4:Er3+,Yb3+ UCNPs, which may provide a hint for the enhanced thermal sensitivity with the silica coating. Although enhanced UC emission is not observed after silica coating, the silica shell can somewhat passivate the surface and thus improve the thermal sensitivity. Ultrasmall NaLa(WO4)2:Yb3+/Er3+ UCNPs (sub-10 nm in size) was demonstrated to be thermally stable until ∼600 K.15 In regard of present NaGd(WO4)2:Yb3+/Er3+ UCNPs in a relatively big size, it is reasonable to envisage that the silica coated UCNPs in our work can survive at higher temperatures. Besides the improvement of thermal sensitivity, the silica coating can extend the application of the material to high temperature environments.
Although the most widely used model system in UC nanothermometry is the thermally coupled neighboring states, emission from non-thermally coupled states can be feasible probes of thermal sensing. Therefore, for the core–shell UCNPs, the thermal sensing ability using the FIR of the 2H11/2 (531.5 nm) and 4F9/2 (657 nm) levels was further investigated. The population related to the 2H11/2 and 4F9/2 levels is not following the Boltzmann distribution. For example, in the cases of Nd3+–Yb3+ and Eu3+–Tb3+ ions couples, FIR technique can monitor the emission intensity from two different emitting ions.44,45 The emission from two emitting levels for FIR analysis is not following the Boltzmann law, which is based on energy transfer. Fig. 6a shows the temperature dependent UC emission spectra of the core–shell NGW:Yb3+/Er3+@SiO2 UCNPs with normalized emission intensity at 657 nm. The FIR can be fit well to a second order polynomial relationship with temperature:
|
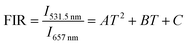 | (5) |
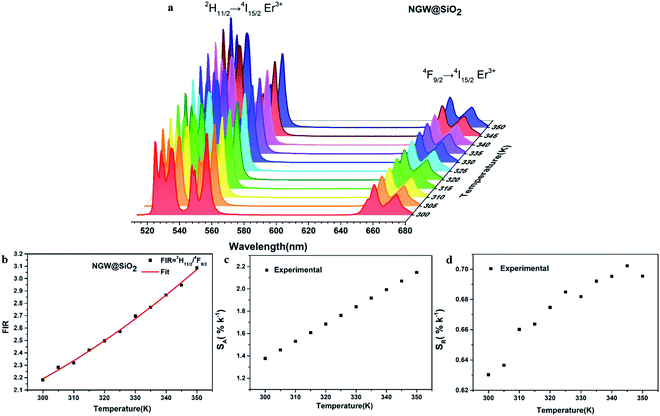 |
| Fig. 6 FIR analysis of the 2H11/2 green emission to the red 4F9/2 emission for the core–shell NGW:Yb3+/Er3+@SiO2 UCNPs in the temperature range from 300 K to 350 K. (a) UC emission spectra under 980 nm laser excitation (power density of 162 mW cm−2). The spectra are normalized to the emission peak at 657 nm. (b) FIR, (c) SA, and (d) SR versus temperature. | |
The FIR increases from 2.18 (300 K) to 3.09 (350 K) as shown in Fig. 6b. The 2H11/2/4F9/2 FIR values are higher than those of 2H11/2/4S3/2 FIR. The corresponding SA and SR are plotted versus temperature in Fig. 6c and d. Similar to the case of 2H11/2/4S3/2 FIR (1.03% K−1 at 350 K), here SA (calculated as the first derivative of FIR respect to each temperature point) increases with temperature, but is higher (2.14% K−1 at 350 K). The red emitting 4F9/2 level is thermally quenched by increasing temperature, similar to the green emitting 4S3/2 level. In contrast, SR also increases with temperature with the highest 0.70% K−1 at 345 K.
Thermal cycling experiments were measured to demonstrate the repeatability and accuracy of our FIR analysis based on the prepared core–shell UCNPs. FIR per cycle step is shown in Fig. 7. During different cycles of heating and cooling, FIR fluctuates slightly, verifying the reliability of ratiometric technique.
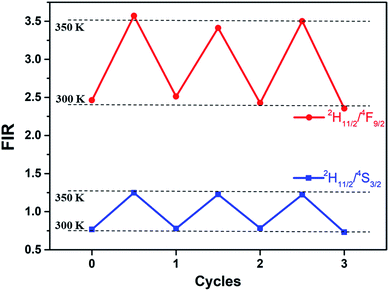 |
| Fig. 7 FIR of Er3+ 2H11/2/4S3/2 and 2H11/2/4F9/2 at 300 and 350 K in three cycles of heating and cooling for the core–shell UCNPs (the dots are experimental data). | |
Finally, thermal sensitivity is compared for the core–shell NGW:Yb3+/Er3+@SiO2 UCNPs and other Yb3+ and Er3+ co-doped materials, as summarized in Table 1. The results of comparison demonstrate that the prepared core–shell NGW:Yb3+/Er3+@SiO2 UCNPs in this work is a good candidate for biological nanothermometry based on the FIR analysis of thermally coupled and non-thermally coupled levels.
Table 1 Comparison of temperature-sensing properties using FIR technique within Er3+
Sensing materials |
Temperature range (K) |
Maximum SA(K−1) |
SR (% K−1) |
λ (nm) |
Ref. |
LuVO4:Yb3+/Er3+@SiO2 NP |
303–353 |
0.57% at 353 K |
1077/T2 |
525/553 |
46 |
NaY(WO4)2:Yb3+/Er3+ NP |
293–503 |
0.9% at 503 K |
1127/T2 |
525/552 |
39 |
LuVO4:Yb3+/Er3+ MP |
303–423 |
0.82% at 423 K |
1030/T2 |
524/553 |
47 |
Er3+/Yb3+:Na0.5Gd0.5MoO4 |
298–778 |
0.86% at 590 K |
1195/T2 |
521/541 |
48 |
β-NaYF4:Yb3+/Er3+@SiO2 NP |
299–337 |
— |
1168/T2 |
525/545 |
49 |
Er3+/Yb3+:K3LuF6 MP |
300–773 |
0.38% at 625 K |
1256/T2 |
521/545 |
50 |
Er3+/Yb3+:GdVO4@SiO2 NP |
297–343 |
1.01% at 343 K |
— |
520/550 |
43 |
SrWO4:Yb3+/Er3+ MP |
300–420 |
1.50% at 403 K |
866/T2 |
525/547 |
51 |
Er3+/Yb3+:GdOF@SiO2 NP |
260–490 |
0.98% at 490 K |
1087/T2 |
534/543 |
52 |
NaGd(WO4)2:Yb3+/Er3+@SiO2 NP |
300–350 |
1.03% at 350 K (2H11/2/4S3/2) |
1217/T2 |
531.5/553 |
This work |
NaGd(WO4)2:Yb3+/Er3+@SiO2 NP |
300–350 |
2.14% at 350 K (2H11/2/4F9/2) |
1217/T2 |
531.5/657 |
This work |
4. Conclusions
In summary, uniformly dispersed NGW:Yb3+/Er3+ core and NGW:Yb3+/Er3+@SiO2 core–shell UCNPs have been successfully synthesized using the ethylene glycol-assistant hydrothermal method and the Stöber method for silica coating. The silica shell is homogeneously coated on the surface of the core NGW:Yb3+/Er3+ UCNPs. Through silica coating, the stability of UCNPs was improved and provides more options in surface functionalization without damaging UC emission. After thermal treatments, the UCNPs can have relatively strong green and red UC emission involving two- and three-photons absorption and energy transfer. Temperature-dependent UC emission spectra were measured in the small biological temperature range and analyzed based on the FIR technique of the 2H11/2 level to the thermally coupled 4S3/2 level and the non-thermally coupled 4F9/2 level. The maximum SA is ∼2-fold enhanced through the silica coating. A high absolute sensitivity of 2.14% K−1 at 350 K can be realized by FIR analysis of the unconventional 2H11/2 and 4F9/2 levels. The study demonstrates that the core–shell NGW:Yb3+/Er3+@SiO2 UCNPs can be promising in nanothermometry for the biological systems with proper size control and surface engineering.
Conflicts of interest
There are no conflicts to declare.
Acknowledgements
This work was financially supported by the National Natural Science Foundation of China (grant no. 21771196).
References
- B. Ding, S. Shao, C. Yu, B. Teng, M. Wang, Z. Cheng, K. Wong, P. Ma and J. Lin, Adv. Mater., 2018, 30, 1802479 CrossRef
. - C. Hsu, S.-L. Lin and C. A. Chang, ACS Appl. Mater. Interfaces, 2018, 10, 7859–7870 CrossRef CAS
. - H. Dong, S. Du, X. Zheng, G. Lyu, L. Sun, L. Li, P. Zhang, C. Zhang and C. Yan, Chem. Rev., 2015, 115, 10725–10815 CrossRef CAS
. - A. Karnkaew, F. Chen, Y. Zhan, R. L. Majewski and W. Cai, ACS Nano, 2016, 10, 3918–3935 CrossRef
. - M. Haase and H. Schafer, Angew. Chem., Int. Ed., 2011, 50, 5808–5829 CrossRef CAS
. - F. Vetrone, R. Naccache, A. Zamarron, A. Juarranz de la Fuente, F. Sanz-Rodriguez, L. Martinez Maestro, E. Martin Rodriguez, D. Jaque, J. Garcia Sole and J. A. Capobianco, ACS Nano, 2010, 4, 3254–3258 CrossRef CAS
. - L. Liu, L. Cheng, B. Chen, J. Shang, X. Qi, Y. Zhu and R. Hua, J. Alloys Compd., 2018, 741, 927–936 CrossRef CAS
. - H. Zheng, B. Chen, H. Yu, J. Zhang, J. Sun, X. Li, M. Sun, B. Tian, S. Fu, H. Zhong, B. Dong, R. Hua and H. Xia, J. Colloid Interface Sci., 2014, 420, 27–34 CrossRef CAS
. - L. Mukhopadhyay and V. K. Rai, New J. Chem., 2017, 41, 7650–7661 RSC
. - X. Zhu, J. Li, X. Qiu, Y. Liu, W. Feng and F. Li, Nat. Commun., 2018, 9, 2176 CrossRef
. - T. Li, C. Guo, S. Zhou, C. Duan, M. Yin and H. Hintzen, J. Am. Ceram. Soc., 2015, 98, 2812–2816 CrossRef CAS
. - A. Dong, X. Ye, J. Chen, Y. Kang, T. Gordon, J. M. Kikkawa and C. B. Murray, J. Am. Chem. Soc., 2011, 133, 998–1006 CrossRef CAS
. - C. Cascales, C. L. Paino, E. Bazan and C. Zaldo, Nanotechnology, 2017, 28, 185101 CrossRef
. - G. Gao, D. Busko, S. Kauffmann-Weiss, A. Turshatov, I. A. Howard and B. S. Richards, J. Mater. Chem. C, 2017, 5, 11010–11017 RSC
. - Z. Wang, J. Christiansen, D. Wezendonk, X. Xie, M. A. van Huis and A. Meijerink, Nanoscale, 2019, 11, 12188–12197 RSC
. - F. Artizzu, D. Loche, D. Mara, L. Malfatti, A. Serpe, R. Van Deun and M. F. Casula, J. Mater. Chem. C, 2018, 6, 7479–7486 RSC
. - X. Xu, W. Li, W. Zhou, G. Tan, Y. Zheng, C. Hu, B. Lei, X. Zhang, Y. Liu and J. Zhuang, J. Mater. Chem. C, 2018, 6, 10360–10366 RSC
. - A. El-Toni, M. Habila, J. Labis, Z. ALOthman, M. Alhoshan, A. Elzatahry and F. Zhang, Nanoscale, 2016, 8, 2510–2531 RSC
. - M. Ocana, E. Cantelar and F. Cusso, Mater. Chem. Phys., 2011, 125, 224–230 CrossRef CAS
. - L. Liu, H. Xiao, X. An, Y. Zhang, R. Qin, L. Liu, D. Zhang, R. Sun and L. Chen, Chem. Phys. Lett., 2015, 619, 169–173 CrossRef CAS
. - D. Yang, C. Cao, W. Feng, C. Huang and F. Li, J. Rare Earths, 2018, 36, 113–118 CrossRef CAS
. - A. Ansari, A. Khan, J. Labis, M. Alam, M. Aslam Manthrammel, M. Ahamed, M. Akhtar, A. Aldalbahi and H. Ghaithan, Mater. Sci. Eng., C, 2019, 96, 365–373 CrossRef CAS
. - F. Chen, C. Yang, X. Liu, N. Zhang, P. Rong, S. Liang and R. Ma, ACS Sustainable Chem. Eng., 2018, 6, 10463–10471 CrossRef CAS
. - T. Zhao, N. Goswami, J. Li, Q. Yao, Y. Zhang, J. Wang, D. Zhao and J. Xie, Small, 2016, 12, 6537–6541 CrossRef CAS
. - M. Gnanasammandhan, N. Idris, A. Bansal, K. Huang and Y. Zhang, Nat. Protoc., 2016, 11, 688–713 CrossRef CAS
. - K. Li, D. Zhu and H. Lian, J. Alloys Compd., 2020, 816, 152554 CrossRef CAS
. - Y. Zhu, Q. Meng, W. Sun and S. Lu, J. Lumin., 2020, 218, 116854 CrossRef CAS
. - Z. Zou, T. Wu, H. Lu, Y. Tu, S. Zhao, S. Xie, F. Han and S. Xu, RSC Adv., 2018, 8, 7679–7686 RSC
. - R. Geitenbeek, P. Prins, W. Albrecht, A. van Blaaderen, B. Weckhuysen and A. Meijerink, J. Phys. Chem. C, 2017, 121, 3503–3510 CrossRef CAS
. - G. Xiang, X. Liu, J. Zhang, Z. Liu, W. Liu, Y. Ma, S. Jiang, X. Tang, X. Zhou, L. Li and Y. Jin, Inorg. Chem., 2019, 58, 8245–8252 CrossRef
. - J. Liao, L. Nie, Q. Wang, S. Liu, H.-R. Wen and J. Wu, RSC Adv., 2016, 6, 35152–35159 RSC
. - J. Gu, Y. Zhu, H. Li, X. Zhang and Y. Qian, J. Solid State Chem., 2010, 183, 497–503 CrossRef CAS
. - A. Kaminskii, H. Eichler, K. Ueda, N. Klassen, B. Redkin, L. Li, J. Findeisen, D. Jaque, J. Garcia-Sole, J. Fernandez and R. Balda, Appl. Opt., 1999, 38, 4533–4547 CrossRef CAS
. - M. Mahata, K. Kumar and V. Rai, Spectrochim. Acta, Part A, 2014, 124, 285–291 CrossRef CAS
. - J. van Hest, G. A. Blab, H. C. Gerritsen, C. D. Donega and A. Meijerink, J. Phys. Chem. C, 2017, 121, 19373–19382 CrossRef CAS
. - X. Ge, L. Sun, B. Ma, D. Jin, L. Dong, L. Shi, N. Li, H. Chen and W. Huang, Nanoscale, 2015, 7, 13877–13887 RSC
. - H. Ding, Y. Zhang, S. Wang, J. Xu, S. Xu and G. Li, Chem. Mater., 2012, 24, 4572–4580 CrossRef CAS
. - R. Calderon-Villajos, C. Zaldo and C. Cascales, Nanotechnology, 2012, 23, 505205 CrossRef
. - M. Lin, L. Xie, Z. Wang, B. S. Richards, G. Gao and J. Zhong, J. Mater. Chem. C, 2019, 7, 2971–2977 RSC
. - J. Boyer, M. Manseau, J. Murray and F. van Veggel, Langmuir, 2010, 26, 1157–1164 CrossRef CAS
. - Z. Wang and A. Meijerink, J. Phys. Chem. C, 2018, 122, 26298–26306 CrossRef CAS
. - F. Rabouw, P. Prins, P. Villanueva-Delgado, M. Castelijns, R. Geitenbeek and A. Meijerink, ACS Nano, 2018, 12, 4812–4823 CrossRef CAS
. - O. A. Savchuk, J. J. Carvajal, C. Cascales, M. Aguilo and F. Diaz, ACS Appl. Mater. Interfaces, 2016, 8, 7266–7273 CrossRef CAS
. - L. Marciniak, K. Prorok, L. Frances-Soriano, J. Perez-Prieto and A. Bednarkiewicz, Nanoscale, 2016, 8, 5037–5042 RSC
. - E. C. Ximendes, W. Q. Santos, U. Rocha, U. K. Kagola, F. Sanz-Rodriguez, N. Fernandez, A. d. S. Gouveia-Neto, D. Bravo, A. M. Domingo, B. del Rosal, C. D. S. Brites, L. D. Carlos, D. Jaque and C. Jacinto, Nano Lett., 2016, 16, 1695–1703 CrossRef CAS
. - G. Xiang, X. Liu, J. Zhang, Z. Liu, W. Liu, Y. Ma, S. Jiang, X. Tang, X. Zhou, L. Li and Y. Jin, Inorg. Chem., 2019, 58, 8245–8252 CrossRef
. - Y. Ma, G. Xiang, J. Zhang, Z. Liu, P. Zhou, W. Liu, X. Tang, S. Jiang, X. Zhou, L. Li, Y. Luo and Y. Jin, J. Alloys Compd., 2018, 769, 325–331 CrossRef CAS
. - P. Du, L. Luo, H.-K. Park and J. S. Yu, Chem. Eng. J., 2016, 306, 840–848 CrossRef CAS
. - M. Runowski, N. Stopikowska, D. Szeremeta, S. Goderski, M. Skwierczynska and S. Lis, ACS Appl. Mater. Interfaces, 2019, 11, 13389–13396 CrossRef CAS
. - J. Cao, F. Hu, L. Chen, H. Guo, C. Duan and M. Yin, J. Am. Ceram. Soc., 2017, 100, 2108–2115 CrossRef CAS
. - A. Pandeya, V. K. Rai, V. Kumar, V. Kumar and H. C. Swart, Sens. Actuators, B, 2015, 209, 352–358 CrossRef
. - H. Suo, X. Zhao, Z. Zhang and C. Guo, ACS Appl. Mater. Interfaces, 2017, 9, 43438–43448 CrossRef CAS
.
Footnote |
† Electronic supplementary information (ESI) available. See DOI: 10.1039/d0ra10039k |
|
This journal is © The Royal Society of Chemistry 2021 |
Click here to see how this site uses Cookies. View our privacy policy here.