DOI:
10.1039/D0RA09420J
(Paper)
RSC Adv., 2021,
11, 4339-4355
Retracted Article: Introduction of a trinuclear manganese(III) catalyst on the surface of magnetic cellulose as an eco-benign, efficient and reusable novel heterogeneous catalyst for the multi-component synthesis of new derivatives of xanthene†
Received
5th November 2020
, Accepted 21st December 2020
First published on 21st January 2021
Abstract
In this work, the new trinuclear manganese catalyst defined as Fe3O4@NFC@NNSM-Mn(III) was successfully manufactured and fully characterized by different techniques, including FT-IR, XRD, TEM, SEM, EDX, VSM, and ICP analysis. There have been reports of the use of magnetic catalysts for the synthesis of xanthine derivatives. The critical potential interest in the present method include short reaction time, high yields, recyclability of the catalyst, easy workup, and the ability to sustain a variety of functional groups, which give economical as well as ecological rewards. Also, the synthesized catalyst was used as a recyclable trinuclear catalyst in alcohol oxidation reactions at 40 °C. The magnetic catalyst activity of Fe3O4@NFC@NNSM-Mn(III) could be attributed to the synergistic effects of the catalyst Fe3O4@NFC@NNS-Mn(III) with melamine. Employing a sustainable and safe low temperature, using an eco-friendly solvent, no need to use any additive, and long-term stability and magnetic recyclability of the catalyst for at least six successive runs are the advantages of the current protocol towards green chemistry. This protocol is a benign, environmentally friendly method for heterocycle synthesis.
Introduction
In the last decades, scientists have considered new approaches, including the development of environmentally friendly chemicals in terms of academic and industrial processes. The main criteria for assisting green chemical processes are the use of benign environmental solvents and the prevention of the formation of by-products in the synthesis of reactions using heterogeneous catalysts.1,2 A multi-component reaction (MCR) is a process in which three or more easily accessible components are combined in a single reaction vessel to produce a final product displaying all inputs' features. MCR suggests greater possibilities for molecular variety per step with minimum synthetic time and endeavor.3 Therefore, organic synthesis through multi-component reactions (MCR) is now a research area in organic chemistry. MCR reactions are a powerful tool in drug discovery processes. Multi-component reactions (MCR) play an important role in chemistry because they can synthesize drug molecules with structural diversity. These reactions show significant advantages such as reduced reaction time, high selectivity, reduction of by-products, and high efficiency.4–6 Among the multi-component reactions referred to as biologically active heterocycles is called xanthene. The synthesis of new compounds comprising heterocyclic systems grabs an important position in the scope of synthetic organic chemistry.7–9 xanthene and its derivatives have become an important class of organic chemistry in the last few decades because of their wide range of biological and pharmaceuticals such as anti-inflammatory,10 antibacterial,11 anti-plasmodial,12 antidepressants,13 antimalarial agent14 and antiviral.15 They also have basic applications in biodegradable processes such as photodynamic therapy,16 agrochemicals,17 fluorescent materials,18 laser technologies,19 and luminescent sensors.20 To date, several routes and reagents have been engaged in preparing many of these organic derivatives. Many catalysts are used for preparing various xanthenes, such as PVSA,21 [Et3NSO3H]Cl,22 core/shell Fe3O4@GA@isinglass,14 SbCl3/SiO2,23 amberlyst-15,24 boric acid,25 nano TiO2,26 sulfamic acid,27 acetonitrile28 and etc. However, many of these methods toil from certain drawbacks, including powerful acidic conditions, long reaction times, low yields of products and spicy reaction conditions, toxic solvents, and excessive and costly catalysts. Therefore, it has become important to find another route for an environment-friendly preparation of xanthene derivatives. Heterogeneous catalysis is a significant accost to environmental remediation because it decreases the cost and energy provisions of chemical operations. However, catalyst recycling and recovery from the reaction medium are essential to prevent product contamination and protect the environment. Recently, magnetic nanoparticles (Fe3O4) have received scientific attention due to their extraordinary performance, such as high super magnetic properties in the presence of an external magnetic field, etc.29 The surface of magnetic nanoparticles has been used for biological and medical engineering due to its small size, good compatibility, low toxicity and good physical, and chemical stability such as magnetic resonance imaging, drug delivery, biosensors, cancer treatment with magnetic induced hyperthermia.30 Howbeit magnetic nanoparticles can be separated from the reaction mixture by an external magnet, the removal of nanoparticles from the reaction mixture systems is very challenging. These nanoparticles can easily accumulate oxidized and agglomerate in aqueous solutions due to their petite size.31 These small nanoparticles can be distributed over a large area, making them difficult to be collecting. Therefore, to prevent the oxidation of magnetic nanoparticles, a new approach should be considered, such as modifying the nanoparticles' surface with polymer groups or using a mold to prevent the nanoparticles from oxidizing for a specific structure, which can be useful approaches.32,33 In the recent past, some green plant polymers,34 such as nanofiber cellulose, lignin, and hemicellulose, polylactic acid (PLA),35,36 chitin37,38 and chitosan,39,40 were considered. Among the various materials used as a mold to prevent oxidation of magnetic nanoparticles, cellulose nanofiber can be mentioned because of its many capabilities, including low cost, easy access, biodegradability, low density, excellent mechanical properties, and high level.41–43 Trinuclear catalyst Mn could be better alternatives for greener production of xanthene derivatives because they can provide a large surface terrain as the catalytic patronage for catalyzing organic reactions.44,45 To the best of our knowledge, no such trinuclear catalyst based on magnetic nanofiber cellulose has been used so far to prepare these derivatives making this approach a novel one for such synthesis. In this work, we synthesized a manganese trinuclear catalyst using a mechanical method using nanofiber cellulose as a substrate and a ligand as an anchor.
During our ongoing research into the activity of manganese trinuclear catalysts finally, after a successful study of trinuclear catalysts, their application to the oxidation of primary/secondary alcohols to produce corresponding carbonyl compounds with high conversion and good selectivity has been investigated. Also inspired by these facts as part of our ongoing efforts to develop new catalytic methods for performing xanthene multi-component reactions and alcohol oxidation under more benign environmental conditions, we present here Fe3O4@NFC@NNSM-Mn(III). We have evaluated this magnetic ternary catalyst with various techniques and finally used it in the mentioned reactions.
Result and discussion
Synthesis and characterization of Fe3O4@NFC@NNSM-Mn(III)
Therefore, it is important to use an effective method that provides the xanthene simply and easily. In this research, an effective and efficient synthetic method for preparing several xanthene derivatives using tri-nuclear catalyst manganese is introduced. Fe3O4@NFC@NNSM-Mn(III) was synthesized, as shown in (Fig. 1). The Fe3O4 nanoparticles, obtained by chemical purification protocol, were coated with cellulose to obtain Fe3O4@NFC. The ligand was then placed on a magnetic substrate. In the next step, manganese nanoparticles were immobilized in Fe3O4@NFC@NNSM-Mn(III) by adsorption of Mn(OAC)3 in Fe3O4@NFC@NNS. The catalysts were characterized by FT-IR, XRD, FE-SEM, EDX, TEM, TGA-DTA, VSM, and ICP-OES spectroscopy. FT-IR spectra of Fe3O4, Fe3O4@NFC, Fe3O4@NFC–Cl, Fe3O4@NFC@NN, Fe3O4@NFC@NNS, Fe3O4@NFC@NNSM-Mn(III) are shown in (Fig. 1). The FT-IR spectrum of Fe3O4 (Fig. 1a), exhibited a wide absorption band at about 550–600 cm−1, which is related to the vibration modes of Fe–O bonds in the Fe3O4 crystalline lattice. The characteristic bands that appeared at 1600, and 3400 cm−1 are certified to the bending and stretching vibrations of the surface hydroxyl groups and adsorbed water molecules. In addition to Fe3O4 peaks observed in the spectrum that approves the formation of Fe3O4 nanoparticles, the strong peak at 1097, 2960, 3328 cm−1 shows the (C–O, C–H, O–H stretching vibrations) of cellulose nanofibers (Fig. 1b). The strong absorption bands at about 1097, 1120, 1410–1520, 2990, and 3120 cm−1 could correspond to the stretching vibration frequencies of Si–O, C–N, C
C aromatic, and C–H aliphatic and aromatic bonds.
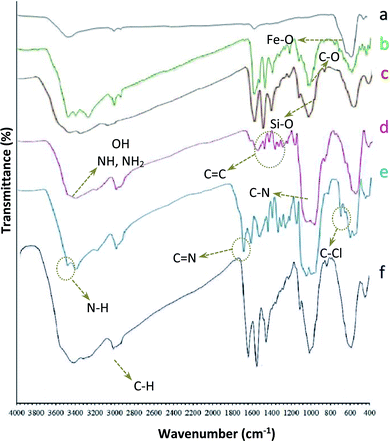 |
| Fig. 1 (a) Fe3O4, (b) Fe3O4@NFC, (c) Fe3O4@NFC–Cl, (d) Fe3O4@NFC-NN, (e) Fe3O4@NFC-NNS-Mn(III), (f) Fe3O4@NFC-NNSM-Mn(III). | |
Also, the observed broadband at around 3000–3450 cm−1 could attribute to the stretching vibration frequency of the NH, NH2, and OH groups (Fig. 1c and d). As shown in (Fig. 1e), The FT-IR spectrum of compound 4 (Fig. 1d), indicates the Schiff base reaction between Fe3O4@NFC@NN and 5-(chloromethyl)-2-hydroxy benzaldehyde, the characteristic peaks at 753 cm−1 (C–Cl stretching), 1670 cm−1 (C
N stretching vibration) confirms the structure of (Fig. 1e). Complexation of manganese and melamine to Fe3O4@NFC@NNS causes the adsorption of chlorine bond to be lost and causes the imine bond (1670 cm−1) absorption to lower wavenumbers by about 20 cm−1 (1650 cm−1), indicating the participation of azomethine nitrogen in bonding with metal ion and confirming the coordination of ν(C
N) stretch to the metal via a nitrogen atom. Also, absorption bands at 1100 and 1600 cm−1 could be assigned to (C–N and C
N) melamine stretching, respectively (Fig. 1e). These absorption bonds support the successful preparation of the catalyst. XRD analysis was carried out for Fe3O4 and Fe3O4@NFC@NNSM-Mn(III) to understand the structural features of the stimulus (Fig. 2). Present tense Fe3O4, Mn2O3 (MnIII), and Fe3O4@NFC@NNSM-Mn(III) X-ray diffraction patterns in the 2θ range between 10°.
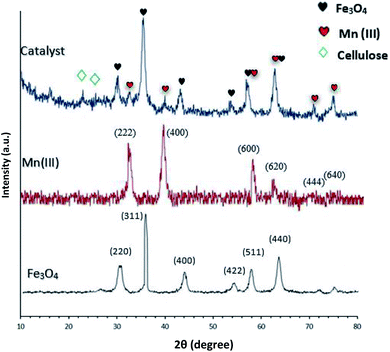 |
| Fig. 2 XRD spectra of (black) Fe3O4, (red) Mn2O3 and (blue) Fe3O4@NFC-NNSMMn(III). | |
The XRD pattern of Fe3O4 shows six characteristic diffraction peaks at 2θ = 30.3°, 35.8°, 43.6°, 54.8°, 57.3°, and 63.2° corresponding to the (220), (311), (400), (422), (511), and (440) crystallographic phases, respectively, that were entirely in agreement with the standard structure and the reported XRD pattern for magnetic (Fig. 2: Fe3O4).46 Besides, diffraction peaks in Fe3O4 nanoparticles, a broader peak was observed in the XRD pattern of the Fe3O4@NFC@NNSM-Mn(III) spheres in the 2θ range of 20–30°, which is the result of the amorphous cellulose. Thus, the XRD curve of the Fe3O4@cellulose nanoparticles composites of the same peaks was also observed in the Fe3O4@NFC XRD pattern, indicating retention of the crystalline spinel ferrite core structure during the cellulose coating process.36 It is the characteristic of diffraction peaks of Mn(III) nanoparticles observed in the XRD pattern in the catalyst. Weak and robust peaks at 2θ = 32.07°, 39.47°, 50.12°, 60.72°, 62.17°, and 71.02° corresponding to the (222), (400), (600), (620), (444), and (640) crystallographic phases in XRD pattern are related to Mn2O3.47
EDX graph confirms the successful connection of Schiff base manganese(III) complex by the presence of all metallic and non-metallic elements involved in the catalyst like carbon, nitrogen, oxygen, silicon, iron, and manganese (Fig. 3). Besides, the best technique for verification of catalyst preparation incredibly problematic half, is inductively coupled plasma optical emission spectroscopy (ICP-OES) analysis. Loading amount of Mn on the catalyst was measured by inductively coupled plasma optical emission spectroscopy (ICP-OES) instruments due to more ensure attainment. The experiment indicated that 1.1 mmol of Mn metal per gram of the catalyst (1.1 mmol 1 g) was loaded on the catalyst framework VII. Also, the analyses give the percentage of the heavy metals as: 45.54 w%, 2.33 w%, 7.10 w% for Fe, Si, Mn respectively.
 |
| Fig. 3 EDX image of Fe3O4@NFC@NNSM-Mn(III). | |
This technique gives the amount of manganese in the fresh and reuse catalyst. The Mn content of the catalyst was measured by ICP analysis, which illustrated the attendance of 0.12 mmol Mn per 1.0 g of the Fe3O4@NFC@NNSM-Mn(III). The surface morphology of Fe3O4@NFC@NNSM-Mn(III) was further determined using SEM and TEM images. A comparison of the FE-SEM images of Fe3O4 with that of Fe3O4@NFC, Fe3O4@NFC@NNSM-Mn(III) clearly showed the presence of other nanoparticles in the SEM images of Fe3O4@NFC@NNSM-Mn(III), which could be referred to as cellulose or ligand and Mn. As it is evident in the TEM images, the mean particle sizes of Fe3O4@NFC@NNSM-Mn(III) were measured to be around 16–29 nm. The particles of Fe3O4 and NFC can also be recognized through their indicative crystal lattice fringes (Fig. 4).
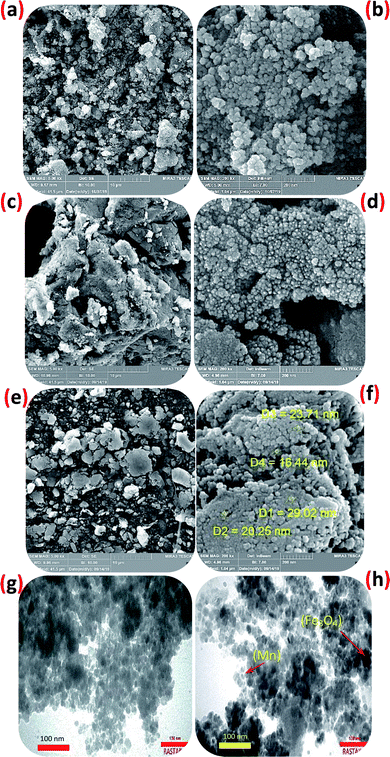 |
| Fig. 4 SEM image of (a and b) Fe3O4, of (c and d) Fe3O4@NFC, of (e and f) Fe3O4@NFC@NNSM-Mn(III) and (g and h) TEM image of the Fe3O4@NFC@NNSM-Mn(III). | |
The TGA analysis was conducted to determine the uncoated Fe3O4 NPs, cellulose (NFC), and NFC-coated Fe3O4 NPs, content in the Fe3O4@NFC@NNSM-Mn(III) nano catalyst. The results are illustrated in Fig. 5. The TGA analysis was performed to confirm the coating of organic content on the surface of the Fe3O4 NPs. TGA spectra of uncoated Fe3O4 NPs show little weight loss, which is about 10% in the range of 25–800 °C. This might be due to the loss of residual water in the uncoated Fe3O4 NPs.48 On the other hand, Fig. 5b shows the TGA spectra of cellulose. The initial step at 125 °C occurs because of the loss of hydrated and constituent water. The second stage involves weight reduction that occurs at approximately 225–425 °C. This is generally associated with the natural carbon of cellulose under oxidizing conditions. Disintegration past 425 °C occurs because of oxidation of the degraded products of cellulose.49 Comparing with the TGA curves, Fig. 5c illustrates the thermal decomposition diagrams for Fe3O4@NFC synthesized by the green method. The first mass reduction phase occurred at 50–120 °C, caused by the water's loss absorbed in the nanocomposite surface. The second phase occurred at 150–425 °C, which could have arisen due to the breakdown of the bonds and destruction of the cellulose structure. The third stage of weight loss occurs at temperatures above 650 °C, which can be due to the rupture of the bond between nanofiber cellulose and Fe3O4 nanoparticles,50,51 which were conducted on thermal and mechanical properties of Fe3O4@NFC.
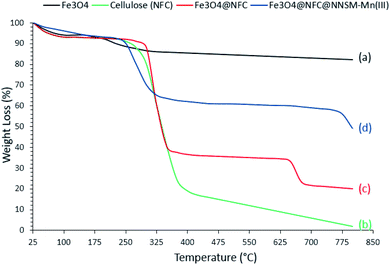 |
| Fig. 5 TGA curves for (a) Fe3O4, (b) cellulose, (c) Fe3O4@NFC, and (d) Fe3O4@NFC@NNSM-Mn(III). | |
Finally, the thermal stabilities of the Fe3O4@NFC@NNSM-Mn(III) were examined by TGA (Fig. 5d). As introduced in Fig. 5, a total weight loss of about 47% was determined from the TGA curve of the Fe3O4@NFC@NNSM-Mn(III). The reduction in mass below 160 °C can be attributed to the loss of embedded water molecules. Subsequently, the main weight loss step in the temperature ranges 160–350 °C (33% reduction) is attributed to the decomposition of cellulose units through the formation of levoglucosan and other volatile compounds or another mass loss, which shows higher thermal stability than Fe3O4@NFC@NNSM-Mn(III) has been modified due to a reasonable reduction in the amount of oxygen-containing functional groups in cellulose.52a
Moreover, the weight loss of about 6% in the temperature range between 300 and 700 °C may be due to the thermal crystal phase alteration from Fe3O4 to γ-Fe2O3.52b Other stages of weight loss up to 800 °C may be due to the decomposition of organic moieties on the surface of the Fe3O4@NFC core–shell nanoparticles. The magnetic behavior of Fe3O4 and Fe3O4@NFC@NNSM-Mn(III) was examined by VSM analysis at room temperature (Fig. 6). As it could be perceived from the resulting magnetization curves, the saturation magnetization amount of Fe3O4 and Fe3O4@NFC@NNSM-Mn(III) were 66.50 and 24.30 emu. g−1, respectively. No discover hysteresis loop in the magnetization curves of both Fe3O4 and Fe3O4@NFC@NNSM-Mn(III) illustrated the superparamagnetic feature of these compounds.
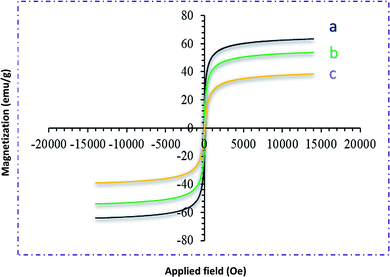 |
| Fig. 6 VSM pattern Fe3O4 (a), Fe3O4@NFC (b) and (c) Fe3O4@NFC@NNSM-Mn(III). | |
The magnetic catalyst activity of Fe3O4@NFC@NNSM-Mn(III) in the xanthene reaction
To optimize the xanthene reaction parameters, we studied the effect of catalyst amount, solvent, temperature, and time were explored towards the reaction progress over the reaction of benzaldehyde with dimedone as a multi-component reaction.
Among the various solvents examined for the xanthine reaction (Table 1, entries 1–8), the ethanol solvent performed best (Table 1, entry 3). After that, the effects of different factors on the reaction progress were perused in EtOH (Table 1, entries 9–13). The result lumpish that the best yield of the product was obtained in the presence of a stimulus (Table 1, entry 3). However, the reaction did not proceed without employing any factors. The effect of the magnetic catalyst amount was next studied (Table 1, entries 9–11). As clearly understood from the results in Table 1, a premier yield of the desired product was achieved by using 0.5 mol% of the magnetic catalyst (Table 1, entry 3). A control experiment lumpish that no product was obtained when the reaction was accomplished in the absence of the catalyst (Table 1, entry 9). The effect of different temperatures was also examined on the model reaction progress (Table 1, entries 12–14) and found that the multi-component reaction proceeded surprisingly at 45 °C (Table 1, entry 3). It is noteworthy that the MCR reaction has a small efficiency without temperature conditions (entry 12). In the next experiment, time differences were separately used to investigate the effect of time on the model reaction's progress (Table 1, entries 15–17). Results indicated that 10 min is the best time for the xanthene reaction (Table 1, entry 3). To obtain better about the efficiency of the Fe3O4@NFC@NNSM-Mn(III) catalyst, the magnetic catalytic activity of Fe3O4, Fe3O4@NFC, Fe3O4@NFC@NNS-Mn(III) (mononuclear), and Fe3O4@NFC@NNSM-Mn(III) (trinuclear) were separately studied in the model reaction (Table 1, entries 18–20). As can be seen in Table 1, no product was gained by using Fe3O4 and Fe3O4@NFC species. However, when the reaction was carried out in the presence of Fe3O4@NFC@NNS-Mn(III), the result was far from satisfactory (Table 1, entry 20). These findings indicated that the enhanced magnetic catalytic activity of Fe3O4@NFC@NNSM-Mn(III) could be attributed to the synergistic effect of melamine and Fe3O4@NFC@NNS-Mn(III) towards the xanthene reaction as a high-efficiency trinuclear catalyst (see the magnetic catalytic mechanism synthesis part for more details). With these interpretations, it can be inferred that the proper reaction of melamine and Fe3O4@NFC@NNS-Mn(III) in the synthesis of magnetic catalyst not only increases the power of the catalyst but also multiplies the activity of the magnetic catalyst. This property expedites and facilitates the reaction process in terms of time and other reaction conditions. These observations well proved the significant influence of the trinuclear catalyst to advance the xanthene MCR reaction.
Table 1 Optimization of reaction conditions for synthesis of 3,3,3,6,6-pentamethyl-9-phenyl-3,4,5,6,7,9-hexahydro -1H-3,5-xanthene-1,8(2H)-dione
The magnetic catalytic activity of Fe3O4@NFC@NNSM-Mn(III) in the alcohol oxidation reaction
Encouraged by the promising results obtained from the xanthene reaction, the magnetic catalytic activity of Fe3O4@NFC@NNSM-Mn(III) was next explored towards the alcohol oxidation reaction under solvent-free conditions (Table 3). As shown in Table 3, this magnetic catalytic method was very efficient for the oxidation reaction of different alcohol. Interestingly, it was found that the oxidation reactions for the readily available and low-cost benzyl alcohol as the highly challenging substrates, with various derivatives, were also companion with satisfactory results (Table 4, entries 1–16). One of the most powerful and useful tools for the production of aldehydes and ketones is the oxidation of alcohols, which are significant mediators in the synthesis of drugs and chemicals. To develop the application of the trinuclear catalysts, Fe3O4@NFC@NNSM-Mn(III) magnetic catalyst was employed for the oxidation of a series of primary and secondary alcohols. To evaluate the reaction conditions of alcohol oxidation and compare the performance of manganese catalyst, benzyl alcohol was selected as a model reaction for alcohol oxidation and the results of this reaction are summarized in Table 3. Firstly, TBHP was chosen as the oxidant, as it introduced the highest oxidative activity among all the oxidants. Noticeably, the additive also has a strong effect. On the catalytic performance in the selective oxidation of alcohols.
Table 2 One-pot three-component synthesis of various xanthene derivatives catalysed by Fe3O4@NFC@NNSM-Mn(III)a
Table 3 Screening reaction conditionsa
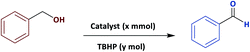
|
Entry |
Solvent |
Catalyst (mol%) |
Temp. (°C) |
TBHP (mmol) |
Yieldb (%) |
Reaction conditions: benzyl alcohol (1 mmol), 20 min. Yields of product isolated. |
1 |
Water |
1 |
40 |
2 |
40 |
2 |
EtOH |
1 |
40 |
2 |
85 |
3 |
CH3CN |
1 |
40 |
2 |
60 |
4 |
Solvent free |
1 |
40 |
2 |
97 |
5 |
Solvent free |
— |
40 |
2 |
25 |
6 |
Solvent free |
0.5 |
40 |
2 |
65 |
7 |
Solvent free |
1.5 |
40 |
2 |
97 |
8 |
Solvent free |
2 |
40 |
2 |
90 |
9 |
Solvent free |
1 |
r.t, |
2 |
50 |
10 |
Solvent free |
1 |
50 |
2 |
97 |
11 |
Solvent free |
1 |
60 |
2 |
75 |
12 |
Solvent free |
1 |
70 |
2 |
65 |
13 |
Solvent free |
1 |
40 |
1 |
75 |
14 |
Solvent free |
1 |
40 |
3 |
85 |
Table 4 Oxidation of alcohols to corresponding aldehydes or ketones in the present of Fe3O4@NFC@NNSM-Mn(III) catalysta
Additive and organic/inorganic mixed solvent can promote the smooth oxidation of alcohol at 40 °C temperature. Low to moderate yields were obtained when using Fe3O4, Fe3O4@NFC, Fe3O4@NFC@NNS-Mn(III), Fe3O4@NFC@NNSM-Mn(III) as an additive (20–97%, Fig. 7 respectively). Fe3O4@NFC@NNSM-Mn(III) (trinuclear) and Fe3O4@NFC@NNS-Mn(III) (mononuclear) catalysts only exhibited 97% and 80% yield of the product. Whereas with the same conditions Fe3O4@NFC@NNSM-Mn(III) catalyst, indicating that the optimization of parameters and active sites can indeed improve the overall catalytic performance of the oxidation reactions (Table 3). Finally, the Fe3O4@NFC@NNSM-Mn(III) catalyst improves the oxidation reaction of alcohol. Finally, the product was obtained with 97% yield at 40 °C in a solvent-free condition for 30 min. Furthermore, in the next step, solvents were optimized, which increased the yield overall. The highest yield (97%) was obtained at solvent-free conditions (Table 3, entries 1–4), which is in line with the green chemistry. Control experiments were also performed in the absence of Mn catalyst in alcohol oxidation. In this case, the product is difficult to identify (Table 3, entries 5). Increasing the amount of the catalyst up to 0.5 mol% led to improved yields, but the more increasing it had no significant effect on the product yield (entries 9–12). Then, the model reaction was carried out under solvent-free conditions at room temperature and also 40–70 °C (entries 9–12). The product yield was increased up to 40 °C and was decreased significantly to 60 °C. The reduction in the product yield could be due to the decomposition of TBHP to molecular water and tert-butanol in the presence of Fe3O4@NFC@NNSM-Mn(III) at evaluated temperatures. As a result, 40 °C was selected as the optimum reaction temperature. Further investigation disclosed that the number of oxidizing agents is crucial to the product yield (entries 13–14). When the oxidation of the model reaction was carried out using 1, 2, and 3 mmol of tert-butyl hydroperoxide, the product's yield increased as the concentration of tert-butyl hydroperoxide increased. However, employing more than three mmol oxidizing agents had the opposite effect on the product yield that it could be due to over-oxidation. When H2O2, oxone, and NaIO4 were used instead of TBHP as the oxidant, the catalyst activity was less than the original, indicating that the choice of oxidant also has a significant impact on the oxidation of alcohol (Fig. 8). The results showed that TBHP is the best oxygen source because of its good oxidation conversion. By contrast, the Fe3O4@NFC@NNS-Mn(III) catalyst with a larger size in the support material exhibited better activity under the same reaction conditions (80%).
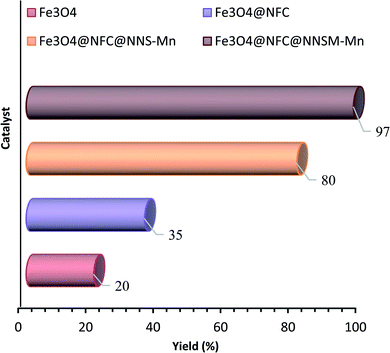 |
| Fig. 7 Comparison of the performance of catalysts with each other. Reaction conditions: alcohols (1 mmol), TBHP (2 mmol), catalyst (0.5 mol%), S. F., 40 °C. | |
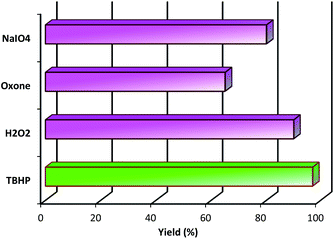 |
| Fig. 8 Reaction conditions: benzyl alcohol (1 mmol), oxidant (2 mmol), catalyst (0.5 mol%), S. F., 40 °C for 20 min. | |
Moreover, the Fe3O4@NFC@NNSM-Mn(III) catalyst as a trinuclear catalyst with a larger surface area exhibited better activity than the Fe3O4@NFC@NNS-Mn(III) catalyst, indicating that the larger surface, the site can contribute to improved catalytic performance. After the optimized conditions were established, this catalytic system was applied to oxidate a wide variety of primary and secondary alcohols to the corresponding carbonyl compounds. As shown in Table 4, good to excellent yields were accomplished in both primary and secondary alcohols. The electron nature of the substituents on the aromatic ring of primary alcohols displayed no apparent effect on this transformation, because the products were obtained in high yields. Secondary alcohols to the corresponding carbonyl compounds. As shown in Table 4, good to excellent results were accomplished in both primary and secondary alcohols.
The stability and reusability of Fe3O4@NFC@NNSM-Mn(III) as a tri-nuclear catalyst manganese in the xanthene and alcohol–oxidation reactions
Recovery and reusability of the catalyst are very substantial factors, exclusively for commercial and industrial applications. These abilities, clearly contend a heterogeneous catalyst as a suitable troth towards more sustainable and green chemical developments. In this line, to investigate the catalyst recyclability, experiments were performed for the model xanthene and alcohol–oxidation reactions, under the optimized reaction conditions. To do this, after each investigation, the catalyst was separated from the reaction mixture with a magnet. Then, the isolated catalyst was washed with water and EtOH, vacuum-dried at 60 °C for 2 h, and directly used in the next run of the reaction. Residual activation was analyzed by ICP for measurement. The amount of manganese that goes from the catalyst to the solution. As shown in Fig. 9, the catalyst was recovered and reused for at least 6 consecutive runs without notable loss of activity. The xanthene and alcohol–oxidation reactions yield reached to 85% and 87% for the 6th run. To show durability and structure of the catalyst, the recovered catalyst after 6th run was subjected to some analyses. Also, metal leaching of the catalyst was measured in each cycle. As shown in Fig. 9, a few leaching was observed for Fe3O4@NFC@NNSM-Mn(III), whereas only 3.6% for xanthene reaction and 3.2% for alcohol oxidation reaction metal leaching was observed after the 6th run. Moreover, ICP analysis of the catalyst for each heavy metal demonstrated an insignificant change in their weight percentage than the corresponding fresh values: Fe 45.58, Si 2.35, Mn 6.9 w%. These results demonstrated insignificant changes in the percentages of the heavy metals and confirm the durability of the catalyst during recycling.
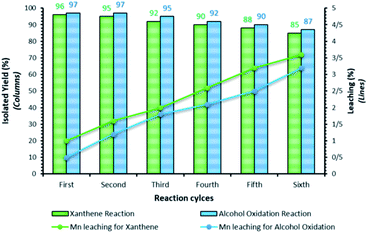 |
| Fig. 9 Recyclability of Fe3O4@NFC@NNSM-Mn(III) in the model alcohol oxidation and xanthene multi-component reaction, under the optimized reaction conditions; Reaction times: 10 min (xanthene multi-component reaction) and 30 min (alcohol oxidation). | |
To show the durability and structure of the catalyst, the recovered catalyst after the 6th run was subjected to some analyses. The FT-IR spectrum of the recovered catalyst after five runs (Fig. 10), revealed the entire preservation of the shape, position, and relative intensity of the characteristic absorption bands. This result proved that no substantial changes occurred in the chemical structure of the present catalyst.
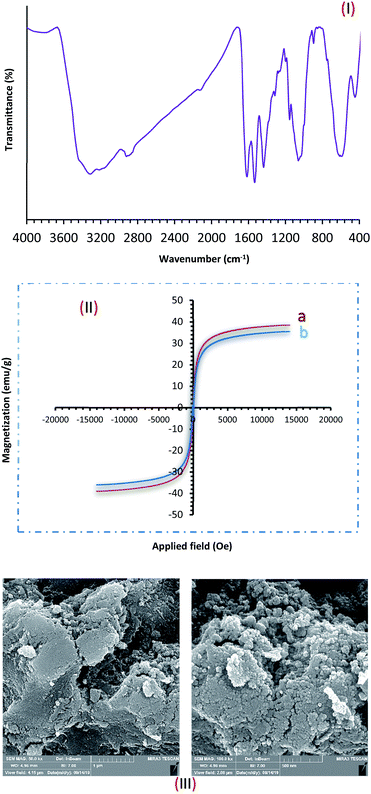 |
| Fig. 10 (I) FT-IR; (II) VSM ((a) before recycling and (b) after recycling); (III) Fe-SEM analysis of Fe3O4@NFC@NNSM-Mn(III) after six times. | |
Furthermore, the VSM and FESEM analysis of the catalyst after six times of reuse showed that the design and morphology of the catalyst maintained unchanged during the recycling process (Fig. 10). These findings well suggested the commendable stability and durability of the tri-nuclear catalyst Mn(III).
Experimental
Materials and measurement
Chemicals and solvents used by Merck company have been prepared. Product identification is made by their physical and spectral properties. The FT-IR spectra are recorded by the Perkin Elmer 780. The 13C NMR and 1H NMR spectra are recorded by the Bruker Avance DPX-250 in CDCl3 solvent at room temperature and the use of TMS as an internal standard. The Electrothermal 9100 was used to measure melting temperature. The transmitting electron microscope (TEM) of the Philips CM10 model and imaging was performed with 100 kV voltage. The elements in the samples were probed by energy-dispersive X-ray (EDX) spectroscopy accessory to the Philips scanning electron microscopy, field emission scanning electron microscopy (FE-SEM) images were obtained on a Tescan MIRA3 Powder X-ray diffraction (PXRD) was conducted using an X'Pert Pro MPD diffractometer equipped with a Cu-Kα (l = 1.54060 Å) radiation source between 2y = 21 and 2y = 50.01. Magnetic isotherms were obtained at room temperature using the VSM magnetic meter, the LakeShore Cryotronics 7407 model.
Synthesis of Fe3O4@NFC–Cl (I–II)
Core–shell (I) Fe3O4@NFC nanospheres were prepared according to the formerly described method (Scheme 1).52 Initially, Fe3O4@NFC (1.5 g) was sonicated in dry toluene (15 ml) for 30 min, and then 3-chloropropyl-trimethoxy silane (1 ml) was added slowly to the mixture. The mixture was then stirred for 24 h under N2 gas at reflux conditions. After completion of the reaction, the reaction mixture was washed with toluene and diethyl ether and separated using an external magnet, and dried at 75 °C for 8 h in an oven under vacuum.
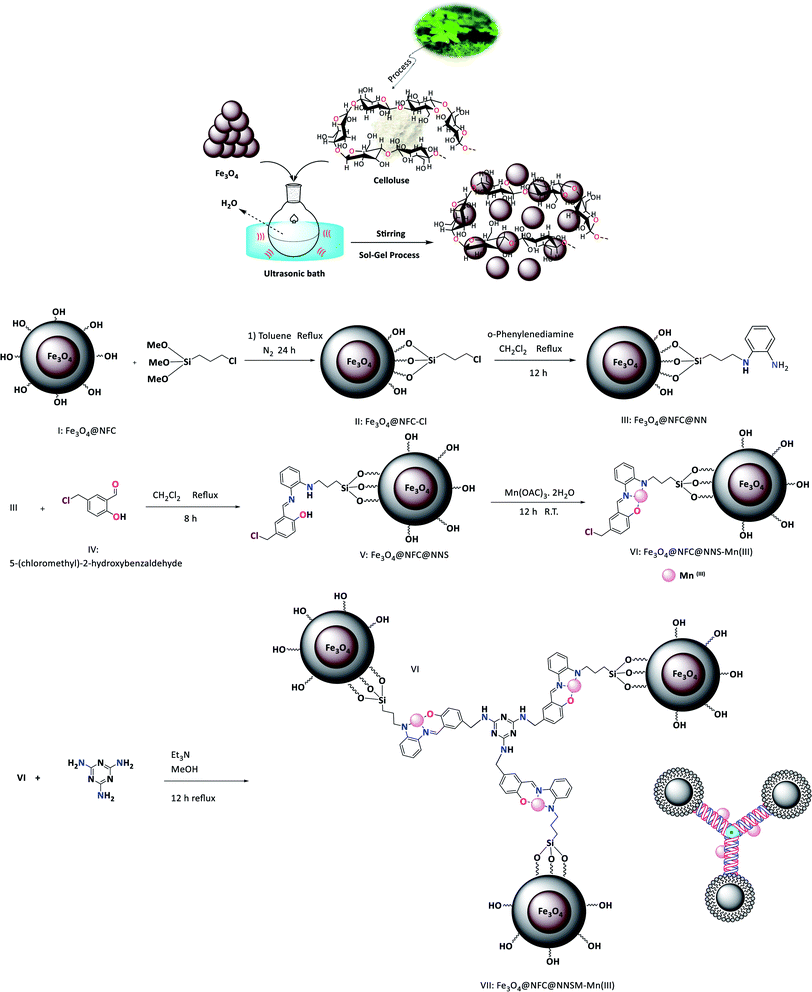 |
| Scheme 1 Overall flowchart for the fabrication of Fe3O4@NFC@NNSM-Mn(III). | |
Synthesis of 5-(chloromethyl)-2-hydroxybenz aldehyde (IV)
We prepared 1 according to a procedure described62,63 that involved addition (0.125 mol) of salicylaldehyde, in small portions with stirring, to 75 ml of concentrated hydrochloric acid containing (0.225 mol) of paraformaldehyde. This reaction mixture was maintained at 70 °C with stirring for 24 h and then water (20 ml) was added to the mix, and the product was extracted into CH2Cl2 (20 ml). Then the reliable product was collected by suction filtration and anhydrous MgSO4 was used for drying the organic phase. The CH2Cl2 was removed with a rotary evaporator and thick yellow oil was set aside overnight. Then a pale purple reliable product III was isolated (Scheme 1). MP 85–87 °C, yield: 95% of pale purple crystals. Its purity was checked using TLC with silica-gel plates.
FT-IR (KBr):
= 3151 (O–H), 3033, 2975, 2865 (C–H aldehyde), 1665 (C
O), 1434 (C
C), 673 (CH2–Cl) cm−1.
1H NMR (DMSO, 300 MHz): δ = 4.80 (s, 2H, CH2), 7.56–7.60 (d,d, 2H, H–Ar), 7.72 (s, 1H, H–Ar), 10.06 (s, 1H, CH of aldehyde), 11.30 (s, 1H, O–H) ppm. 13C NMR (DMSO, 75 MHz): δ = 47.0, 117.8, 124.8, 131.1, 136.1, 136.4, 148.4, 163.2, 197.7 ppm.
Preparation of the Fe3O4@NFC@NN from o-phenylenediamine functionalized Fe3O4@NFC–Cl (III, V)
Fe3O4@NFC–Cl (1.00 g) was refluxed with o-phenylenediamine (1 mmol
:
0.108 g) in CH2Cl2 (10.0 ml) for 12 h to replace the terminal chlorine atoms. Then 5-(chloromethyl)-2-hydroxy benzaldehyde (1 mmol
:
0.17 g) was added and the mixture was refluxed for 8 h. Finally, Fe3O4@NFC@NNS(V) was filtered off, washed three times with ethanol, and dried at 70 °C in the vacuum oven.
Loading with Mn (OAc)3·2H2O (VI)
Fe3O4@NFC@NNS (1.00 g) was mixed with Mn(OAc)3·2H2O (1.2 mmol
:
0.32 g) in ethanol (5 ml). The mixture was stirred for 12 hours at room temperature. After completion of the reaction, then it was filtered, and the solid obtained was washed with ethanol and dried at 70 °C overnight to give Fe3O4@NFC@NNS-Mn. The manganese loading of Fe3O4@NFC@NNS-Mn(III) was determined by the inductively coupled plasma (ICP) technique.
Synthesis of Fe3O4@NFC@ONSM-Mn magnetic catalyst (VII)
Immobilized Fe3O4@NFC@NNS-Mn(III) complex (8) along with a weighted amount of melamine (molar ratio 3
:
1) were transferred to a 25 ml oven-dried round bottom flask equipped with a magnet and a condenser. A solution of triethylamine (3.0 mmol
:
0.39 ml) in MeOH (10.0 ml) was added to the mentioned mixture. The mixture was refluxed in N2 atmosphere for 12 h. The product, Fe3O4@NFC@NNSM-Mn(III) (9) was collected using an external magnetic field, washed with water (2 × 10 ml) and EtOH (2 × 10 ml) and dried into a vacuum oven (5 h, 60 °C). Scheme 1 shows the complete route for the preparation of VII.
Synthesis of bis-aldehyde derivatives
A mixture of 2-hydroxy benzaldehyde (10 mmol) or 3-hydroxy benzaldehyde (10 mmol) or 4-hydroxy benzaldehyde (10 mmol) and 1,4-di-bromobutane (5 mol) or 1,2-di-bromoethane (5 mmol) in NaOH (10 mmol) in ethanol solvent was refluxed for 24 hours. The reaction mixture was cooled to room temperature, and the product precipitate was separated after re-crystallization in ethanol and dried in an oven.
General experimental procedure for the synthesis of xanthene
In a round-bottomed flask, aldehyde (1 mmol), dimedone (2 mmol) and Fe3O4@NFC@NNSM-Mn(III) (0.5 mol%) were mixed thoroughly at EtOH (5 ml). The flask was heated at 45 °C with concomitant stirring. After completing the reaction confirmed by TLC (EtOAc
:
n-hexane), the solid catalyst was separated from the reaction mixture by an ordinary magnet. The solvent was evaporated, and the green products were recrystallized from ethanol, gave the pure products 88–97% yields based on the starting aldehyde (Scheme 2). The products were characterized via a comparison of their melting points with the reported ones. The spectral data for the selected compounds are as follows:
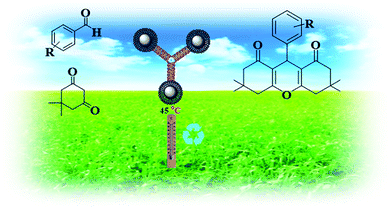 |
| Scheme 2 Catalytic activity of the Fe3O4@NFC@NNSM-Mn(III) xanthene reactions. | |
9-Phenyl-3,4,5,6,7,9-hexahydro-1H-xanthene-1,8(2H)-dione (Table 2, entry 1). 1H NMR (DMSO, 300 MHz): δ = 1.63–1.93 (m, 4H, CH2), 2.01–2.20 (m, 4H, CH2), 2.37–2.48 (m, 4H, CH2), 3.97 (s, 1H, CH), 7.13–7.20 (m, 5H, aromatic) ppm. 13C NMR (DMSO, 75 MHz): δ = 21.0, 29.1, 36.3, 38.7113.1, 124.7, 127.1, 129.4, 143.9, 155.4, 199.8 ppm. Mp (°C): 203–204.
9-(4-Chlorophenyl)-3,4,5,6,7,9-hexahydro-1H-xanthene-1,8(2H)-dione (Table 2, entry 2). 1H NMR (DMSO, 300 MHz): δ = 2.11–2.14 (m, 4H, CH2), 2.45–2.48 (m, 4H, CH2), 2.97–3.04 (m, 4H, CH2), 3.93 (s, 1H, CH), 6.97–7.09 (m, 4H, aromatic) ppm. 13C NMR (DMSO, 75 MHz): δ = 21.5, 29.6, 36.9, 38.9, 113.2, 127.8, 129.7, 131.8, 143.9, 155.6, 199.5 ppm. Mp (°C): 229–230.
9-(4-Methoxyphenyl)-3,4,5,6,7,9-hexahydro-1H-xanthene-1,8(2H)-dione (Table 2, entry 3). 1H NMR (DMSO, 300 MHz): δ = 1.58–1.70 (m, 4H, CH2), 2.63–2.67 (t, 4H, CH2), 2.99–3.04 (t, 4H, CH2), 3.67–3.71 (s, 3H, CH3), 4.05 (s, 1H, CH), 6.70–7.13 (s, s, 4H, aromatic) ppm. 13C NMR (DMSO, 75 MHz): δ = 20.9, 29.8, 35.4, 36.9, 55.3, 113.2, 113.8, 129.7, 134.6, 153.8, 157.3, 199.9 ppm. Mp (°C): 205–206.
9-(2-Nitrophenyl)-3,4,5,6,7,9-hexahydro-1H-xanthene-1,8(2H)-dione (Table 2, entry 4). 1H NMR (DMSO, 300 MHz): δ = 0.85–0.96 (m, 4H, CH2), 2.52–2.56 (t, 4H, CH2), 2.73–2.78 (t, 4H, CH2), 3.99 (s, 1H, CH), 6.68–7.58 (m, 4H, aromatic) ppm. 13C NMR (DMSO, 75 MHz): δ = 22.5, 29.3, 34.2, 36.0, 116.0, 124.5, 127.1, 129.4, 130.4, 134.6, 147.8, 154.5, 199.6 ppm. Mp (°C): 259–261.
9-(2-Hydroxyphenyl)-3,3,6,6-tetramethyl-3,4,5,6,7,9-hexahydro-1H-xanthene-1,8(2H)-dione (Table 2, entry 5). 1H NMR (DMSO, 300 MHz): δ = 1.35–1.49 (m, 4H, 2CH2), 2.01–2.09 (t, 4H, 2CH2), 2.57–2.63 (t, 4H, 2CH2), 4.59 (s, 1H, CH), 7.02–7.21 (m, 4H, aromatic), 10.51 (s, 1H, OH) ppm. 13C NMR (DMSO, 75 MHz): δ = 20.8, 29.8, 32.3, 35.2, 111.0, 115.7, 118.3, 124.5, 127.5, 128.0, 154.7, 156.8, 196.6 ppm. Mp (°C): 259–261.
3,3,6,6-Tetramethyl-9-phenyl-3,4,5,6,7,9-hexahydro-1H-xanthene-1,8(2H)-dione (Table 2, entry 6). 1H NMR (DMSO, 300 MHz): δ = 1.11 (s, 12H, 4CH3), 1.82 (s, 4H, 2CH2), 2.07 (s, 4H, 2CH2), 4.06 (s, 1H, CH), 7.02–7.09 (m, 5H, aromatic) ppm. 13C NMR (DMSO, 75 MHz): δ = 28.3, 33.8, 37.8, 52.4, 110.3, 125.8, 127.8, 128.4, 144.7, 155.7, 197.7 ppm. Mp (°C): 203–204.
9-(4-Chlorophenyl)-3,3,6,6-tetramethyl-3,4,5,6,7,9-hexahydro-1H-xanthene-1,8(2H)-dione (Table 2, entry 7). 1H NMR (DMSO, 300 MHz): δ = 1.25 (s, 6H, 2 × 2CH3), 2.19 (s, 2H, 2 × CH2), 5.51 (s, 1H, CH), 7.11–7.17 (d, 2H, 2 × 2CH aromatic) ppm. 13C NMR (DMSO, 75 MHz): δ = 26.9, 30.1, 36.0, 36.5, 52.4, 114.5, 128.4, 133.1, 141.3, 157.1, 198.7 ppm. Mp (°C): 169–171.
9-(2-Hydroxyphenyl)-3,3,6,6-tetramethyl-3,4,5,6,7,9-hexahydro-1H-xanthene-1,8(2H)-dione (Table 2, entry 8). 1H NMR (DMSO, 300 MHz): δ = 1.07 (s, 12H, 4CH3), 1.71 (s, 4H, 2CH2), 2.26 (s, 4H, 2CH2), 1.98–2.00 (m, 2H, CH2), 2.36 (s, 2H, CH2), 2.40 (s, 2H, CH2), 6.66–7.24 (m, 4H, CH-aromatic) 10.51 (s, 1H, OH) ppm. 13C NMR (DMSO, 75 MHz): δ = 20.8, 27.7, 32.5, 34.2, 37.1, 48.5, 112.4, 115.7, 124.7, 126.2, 127.3, 128.8, 155.5, 157.9, 196.4 ppm. Mp (°C): 200–202.
4-(3,3,6,6-Tetramethyl-1,8-dioxo-2,3,4,5,6,7,8,9-octahydro-1H-xanthene-9-yl) benzaldehyde (Table 2, entry 9). 1H NMR (DMSO, 300 MHz): δ = 1.25 (s, 6H, 2 × 2CH3), 1.88 (s, 2H, 2× CH2), 2.19 (s, 2H, 2× CH2), 5.51 (s, 1H, CH), 7.11–7.17 (d, 2H, 2 × 2CH aromatic), 11.88 (s, 1H, COH) ppm. 13C NMR (DMSO, 75 MHz): δ = 28.3, 31.7, 37.8, 52.4, 115, 127.8, 130.2, 133.1, 149, 157.1, 195.6, 206.4 ppm. Mp (°C): 295–297.
9-(1H-Indol-3-yl)-3,4,5,6,7,9-hexahydro-1H-xanthene-1,8(2H)-dione (Table 2, entry 10). 1H NMR (DMSO, 300 MHz): δ = 1.79–1.84 (m, 4H, 2CH2), 1.92–1.96 (m, 4H, 2CH2), 3.45–3.49 (t, 4H, 2CH2), 4.89 (s, 1H, CH), 6.93–6.98 (m, 2H, aromatic), 6.99 (s, 1H, CH indole), 7.04–7.59 (d of d, 2H, aromatic), 10.80 (s, 1H, NH) ppm. 13C NMR (DMSO, 75 MHz): δ = 22.3, 26.9, 34.1, 36.9, 103.9, 111.8, 118.5, 119.4, 120.9, 124.2, 126.1, 136.6, 164.7, 196.8 ppm. Mp (°C): 267–269.
3,3,6,6-Tetramethyl-9-(5-nitrofuran-2-yl)-3,4,5,6,7,9-hexahydro-1H-xanthene-1,8(2H)-dione (Table 2, entry 11). 1H NMR (DMSO, 300 MHz): δ = 1.14 (s, 12H, 4CH3), 1.85 (s, 4H, 2CH2), 2.32 (s, 4H, 2CH2), 5.47 (s, 1H, CH), 6.25 (s, 1H, furane), 7.28 (s, 1H, furane) ppm. 13C NMR (DMSO, 75 MHz): δ = 26.2, 28.0, 31.9, 35.5, 50.4, 110.3, 111.9, 115.1, 150.7, 161.5, 162.9, 196.1 ppm. Mp (°C): 155–157.
4-(4-(4-(1,8-Dioxo-2,3,4,5,6,7,8,9-octahydro-1H-xanthene-9-yl)phenoxy)butoxy)benzaldehyde (Table 2, entry 12). 1H NMR (DMSO, 300 MHz): δ = 1.93–2.04 (m, 4H, 2CH2), 2.33–2.67 (m, 8H, 4CH2), 3.95–4.13 (m, 4H, 2CH2), 4.78 (s, 1H, CH), 6.75–6.79 (m, 2H, CH aromatic), 4.78 (s, 1H, CH), 6.75–6.79 (m, 2H, Ar), 7.00–7.04 (m, 2H, Ar), 7.20–7.25 (m, 2H, Ar), 7.84–7.88 (m, 2H, Ar), 9.91 (s, 1H, COH) ppm. 13C NMR (DMSO, 75 MHz): δ = 20.3, 25.9, 27.1, 30.8, 37.0, 67.1, 67.9, 114.0, 114.7, 117.0, 117.1, 129.3, 129.8, 132.0, 136.8, 157.4, 163.7, 164.1, 190.9, 196.7 ppm. Mp (°C): 168–170.
4-(2-(4-(3,3,6,6-Tetramethyl-1,8-dioxo-2,3,4,5,6,7,8,9-octahydro-1H-xanthene-9-yl)phenoxy)ethoxy)benzaldehyde (Table 2, entry 13). 1H NMR (DMSO, 300 MHz): δ = 1.12 (s, 12H, 4CH3), 2.21 (s, 4H, 2CH2), 2.29 (s, 4H, 2CH2), 3.97 (s, 1H, CH), 4.29–4.32 (m, 2H, CH2), 4.37–4.40 (m, 2H, CH2), 6.79–6.86 (m, 4H, aromatic), 7.04–7.07 (d, 2H, aromatic), 7.84–7.88 (m, 2H, aromatic), 9.91 (s, 1H, COH) ppm. 13C NMR (DMSO, 75 MHz): δ = 27.3, 32.2, 50.7, 66.0, 66.8, 114.1, 114.9, 115.6, 115.7, 127.8, 129.4, 132.0, 137.2, 156.8, 157.0, 162.1, 163.7, 190.8, 196.5 ppm. Mp (°C): 200–202.
2-(4-(2-(1,8-Dioxo-2,3,4,5,6,7,8,9-octahydro-1H-xanthene-9-yl)phenoxy)butoxy)benzaldehyde (Table 2, entry 14). 1H NMR (DMSO, 300 MHz): δ = 2.01–2.09 (m, 4H, 2CH2), 2.33–2.65 (m, 8H, 4CH2), 3.06–3.11 (m, 4H, 2CH2), 3.80 (s, 1H, CH), 3.97–4.14 (m, 4H, 2CH2), 6.94–7.04 (m, 3H, aromatic), 7.23–7.25 (d, 1H, aromatic), 7.42–7.45 (d, 1H, aromatic), 7.57–7.60 (t, 1H, aromatic), 7.69–7.71 (d, 1H, aromatic), 7.84–7.86 (d, 1H, aromatic), 9.91 (s, 1H, COH) ppm. 13C NMR (DMSO, 75 MHz): δ = 20.4, 25.9, 27.0, 30.3, 36.9, 67.7, 68.5, 112.5, 114.0, 119.8, 121.0, 124.7, 127.9, 131.0, 132.9, 136.9, 157.7, 158.6, 161.5, 189.5, 196.5. Mp (°C): 220–222.
9,9′-((Ethane-1,2-diylbis(oxy))bis(3,1-phenylene))bis(3,3,6,6-tetramethyl-3,4,5,6,7,9-hexahydro-1H-xanthene-1,8(2H)-dione) (Table 2, entry 15). 1H NMR (DMSO, 300 MHz): δ = 1.03 (s, 12H, 2 × 4CH3), 2.23 (s, 4H, 2 × 2CH2), 2.49 (s, 4H, 2 × 2CH2), 4.28 (s, 2H, 2× CH2), 4.77 (s, 1H, 2× CH), 6.70–7.18 (m, 4H, 2× aromatic) ppm. 13C NMR (DMSO, 75 MHz): δ = 27.5, 32.2, 50.7, 112.4, 114.9, 115.5, 121.4, 128.9, 145.7, 158.5, 162.3, 196.4 ppm. Mp (°C): 250–252.
The general procedure of oxidation of alcohols
In a typical experiment, Fe3O4@NFC@NNSM-Mn(III) (0.5 mol%) and TBHP (1 mmol) were placed in a vessel containing benzyl alcohol (1 mmol) without any organic solvents as green conditions were stirred at 40 °C for an appropriate time. Upon reaction completion, monitored by TLC, the catalyst was removed from the mixture of reaction by the magnet. The products were purified on a silica gel plate to give pure products. For the identification of the final products, their physical data were compared with those of reliable samples, because all of them have been studied in the past. Also all of these compounds are already known.
Comparative study
To better clarify the merits of the competency tri-nuclear catalytic system over the reported metal-based other catalytic systems in the xanthene reactions, the comparing efficacy results were tabulated in Table 5. It has been observed that the synthesized catalyst has almost a very good advantage over other reported catalysts which can be due to suitable reaction conditions, short reaction time, high reaction efficiency and lower catalyst load and on the other hand timely recovery of magnetic catalyst. In addition to the reusability of the catalyst, most importantly, the use of a non-toxic, benign green solvent that is environmentally friendly and does not require the use of any additives or toxic solvents supports the green chemistry approach well. Chromium derivatives containing aromatic aldehydes can be synthesized by our catalytic method. These promising results should be attributed to the co-operation of three metal verb positions: Lewis acid in Fe3O4@NFC@NNSM-Mn(III). Finally, a series of green metrics72,73 such as atom economy (AE), atom efficiency (AEF), carbon efficiency (CE), reaction mass efficiency (RME), optimum efficiency (OE), process mass intensity (PMI), E-factor (E), solvent intensity (SI), and water intensity (WI) were calculated to evaluate the greenness of the one-pot three-component reaction of aldehydes, dimedone (Fig. 11–13, see ESI for detailed calculations† for detailed calculations). As it is shown in Fig. 11a and 12a, the high values of the AE, AEF, CE, RME, and OE for the synthesis of three xanthene derivatives of Table 2 (entries 5–7) and also new derivatives Table 2 (entries 11–15), illustrate well the greenness of the process. The lower the PMI, E, and SI, the more favourable is the process because of green chemistry. These values are less than 50 in the synthesis of the xanthene mentioned above's (Fig. 11b and 12b, see ESI†). Minimal amounts of WI were also obtained in these processes (Fig. 11b and 12b, see ESI†). The green organic solvent, which was used in these protocols was EtOH. Hence, it can be concluded that about the high values of RME and low values of PMI, E, SI, and WI, this one-pot three-component process is an efficient and green protocol for synthesizing xanthene. To stable, the more greenness of the current catalyst over the reported catalysts in the one-pot three-component reaction of benzaldehyde, dimedone, the current catalyst's green metrics was compared with those of two previously reported catalysts (Table 5, entries 1 and 8).56,70
Table 5 Comparison of the reaction conditions and results for the synthesis of xanthene
Entry |
Catalyst |
Solvent |
Time (min) |
Temp. (°C) |
Yield (%) |
Ref. |
Trichloroisocyanuric acid. Propyl sulfonic acid functionalized LUS-1 (Laval University silica) (LUS-Pr-SO3H). |
1 |
[SO3H–Pyrazine–SO3H]Cl2 |
Solvent free |
10 |
100 |
93 |
56 |
2 |
Fe3O4 nanoparticles |
Solvent free |
20 |
100 |
90 |
64 |
3 |
TCCAa |
Solvent free |
40 |
110 |
78 |
65 |
4 |
[Et3N–SO3H]Cl |
Solvent free |
60 |
80 |
97 |
22 |
5 |
LUS-Pr-SO3Hb |
Solvent free |
15 |
140 |
90 |
66 |
6 |
[Cmmim][BF4] |
Solvent free |
120 |
80 |
94 |
67 |
7 |
ICl3/SiO2 |
Solvent free |
60 |
75 |
90 |
68 |
8 |
NP |
EtOH |
6.5 h |
Reflux |
90 |
69 |
9 |
Cu(II)/NP |
EtOH |
120 |
Reflux |
98 |
70 |
10 |
— |
EtOH |
24 h |
Reflux |
— |
71 |
11 |
Fe3O4@NFC@NNSM-Mn(III) |
EtOH |
10 |
45 |
96 |
This work |
As can be perceived from the results in Fig. 13a and b (see ESI†), the higher the AEF, CE, and RME factors and the lower the PMI, E, SI, and WI factors of Fe3O4@NFC@NNSM-Mn(III) compared with those of NP and [SO3H–Pyrazine–SO3H]Cl2, acknowledged that the Fe3O4@NFC@NNSM-Mn(III) is a greener and more supportable catalyst for such an Multi-component reaction (see ESI† for detailed calculations).
Mechanism studies
An acceptable mechanism for the synthesis of xanthine using the Fe3O4@NFC@NNSM-Mn(III) catalyst has been reported. Initially, the acid catalyst Fe3O4@NFC@NNSM-Mn(III) activates the carbonyl aldehyde and dimedone groups, and intermediate (I) is formed from the densified Knoevenagel densities of dimedone and aryl aldehyde by the removal of a water molecule. Then, from the increase of Michael Dimedone's next molecule to intermediate (I), intermediate (II) is formed, which is tautomeric with intermediate (III). In the end, by intramolecular looping and removal of a water molecule, product (IV) is obtained (Scheme 3).
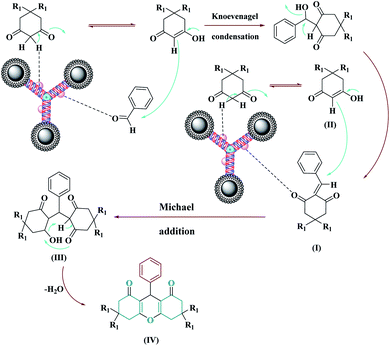 |
| Scheme 3 A plausible mechanism for the synthesis of xanthene while using the Fe3O4@NFC@NNSM-Mn(III) catalyst. | |
The proposed reaction mechanism for the oxidation of benzyl alcohol derivatives using TBHP in the presence of Fe3O4@NFC@NNSM-Mn(III) based on the available literature74 is shown in Scheme 4. Decomposition of t-BuOOH on the surface of Fe3O4@NFC@NNSM-Mn(III) leads to the formation of t-BuOO˙ radical species and also increase of Mn(III) to Mn(IV).
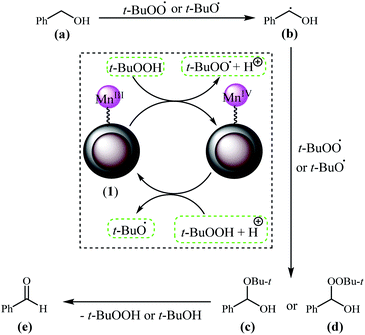 |
| Scheme 4 A plausible mechanism for the synthesis of oxidation alcohols while using the Fe3O4@NFC@NNSM-Mn(III) catalyst. | |
Besides, decomposition of t-BuOOH on the surface of Mn(IV) generates t-BuO˙ species. Next, t-BuOO˙ and t-BuO˙ radical species underwent hydrogen abstraction of the substrate (a) to produce intermediate (b). The reaction of intermediate (b) with t-BuOO˙ and t-BuO˙ results in (c) and (d), which ultimately have corresponding aldehyde (e) through the elimination of t-BuOOH and t-BuOH.
Conclusions
In this work, a novel magnetically trinuclear catalyst denoted as Fe3O4@NFC@NNSM-Mn(III) was successfully fabricated as an efficient trinuclear catalyst. To characterize the tri-nuclear catalyst, various techniques, including FT-IR, XRD, TGA, TEM, FESEM, EDX, VSM, and ICP analysis have been employed. Interestingly, Fe3O4@NFC@NNSM-Mn(III) was an excellent trinuclear catalyst to promote the xanthene and alcohol–oxidation reactions of a broad range of benzaldehyde and most importantly the highly challenging benzyl alcohol, which are far extensively available and cheaper. The presented catalytic system can be magnetically separated and conveniently recycled at least five times without a noticeable decrease in its activity. Moreover, low metal leaching and utilizing an eco-friendly solvent are other advantages that support the going protocol towards green chemistry. The use of the presented new trinuclear catalyst to promote another Multi-component reaction is continuing in our lab.
Conflicts of interest
There are no conflicts to declare.
Acknowledgements
We gratefully acknowledge the financial support of the research Council of the University of Birjand and we also thank University of Ferdowsi.
References
- L. Chao-Jun and B. M. Trost, Proc. Natl. Acad. Sci., 2008, 105, 13197–13202 CrossRef.
- P. Ghamari Kargar, S. Aryanejad and G. Bagherzade, Appl. Organomet. Chem., 2020, e5965 CAS.
- L. Weber, Drug Discovery Today, 2002, 7, 143–147 CrossRef CAS.
- C. C. A. Cariou, G. J. Clarkson and M. Shipman, J. Org. Chem., 2008, 73, 9762–9764 CrossRef CAS.
- C. Mukhopadhyay, P. K. Tapaswi and M. G. B. Drew, Tetrahedron Lett., 2010, 51, 3944–3950 CrossRef CAS.
-
(a) H. Khashei Siuki, G. Bagherzade and P. Ghamari Kargar, ChemistrySelect, 2020, 5, 13537–13544 CrossRef CAS;
(b) G. Brahmachari and S. Das, Tetrahedron Lett., 2012, 53, 1479–1484 CrossRef CAS.
- P. Ghamari Kargar, M. Bakherad, K. Ali and A. H. Amin, Iran. J. Catal., 2018, 8(3), 179–187 Search PubMed.
- W. Miao, P. Ye, M. Bai, Z. Yang, S. Duan, H. Duan and X. Wang, RSC Adv., 2020, 10, 25165–25169 RSC.
- T. Yıldız and H. B. Küçük, RSC Adv., 2017, 7, 16644–16649 RSC.
- A. G. Banerjee, L. P. Kothapalli, P. A. Sharma, A. B. Thomas, R. K. Nanda, S. K. Shrivastava and V. V. Khatanglekar, Arabian J. Chem., 2016, 9, S480–S489 CrossRef CAS.
- A. Barmak, K. Niknam, G. Mohebbi and H. Pournabi, Microb. Pathog., 2019, 130, 95–99 CrossRef CAS.
- A. G. B. Azebaze, M. Meyer, A. Valentin, E. L. Nguemfo, Z. T. Fomum and A. E. Nkengfack, Chem. Pharm. Bull., 2006, 54, 111–113 CrossRef CAS.
- G. Rathee, S. Kohli, N. Singh, A. Awasthi and R. Chandra, ACS Omega, 2020, 5, 15673–15680 CrossRef CAS.
- E. Pourian, S. Javanshir, Z. Dolatkhah, S. Molaei and A. Maleki, ACS Omega, 2018, 3, 5012–5020 CrossRef CAS.
- H. N. Hafez, M. I. Hegab, I. S. Ahmed-Farag and A. B. A. El-Gazzar, Bioorg. Med. Chem. Lett., 2008, 18, 4538–4543 CrossRef CAS.
- P. Bansal, N. Kaur, C. Prakash and G. R. Chaudhary, Vacuum, 2018, 157, 9–16 CrossRef CAS.
- F. M. Abdel-Galil, B. Y. Riad, S. M. Sherif and M. H. Elnagdi, Chem. Lett., 1982, 11, 1123–1126 CrossRef.
- A. Poursattar Marjani, S. Abdollahi, M. Ezzati and E. Nemati-Kande, J. Heterocycl. Chem., 2018, 55, 1324–1330 CrossRef CAS.
- A. Banerjee and A. K. Mukherjee, Stain Technol., 1981, 56, 83–85 CrossRef CAS.
- R. L. Poupelin, J. P. G. Saint Ruf, O. Foussard-Blanpin, G. Narcisse and G. Uchida-Ernouf, Chem. Informations., 1978, 9 Search PubMed.
- A. Rahmatpour, Monatsh. Chem., 2011, 142, 1259–1263 CrossRef CAS.
- A. Zare, A. R. Moosavi-Zare, M. Merajoddin, M. A. Zolfigol, T. Hekmat-Zadeh, A. Hasaninejad, A. Khazaei, M. Mokhlesi, V. Khakyzadeh, F. Derakhshan-Panah, M. H. Beyzavi, E. Rostami, A. Arghoon and R. Roohandeh, J. Mol. Liq., 2012, 167, 69–77 CrossRef CAS.
- X. ZHANG, D. JING, M. LIU and L. GUO, Catal. Commun., 2008, 9, 1720–1724 CrossRef CAS.
- G. Song, B. Wang, H. Luo and L. Yang, Catal. Commun., 2007, 8, 673–676 CrossRef CAS.
- Z. Karimi-Jaberi and M. Keshavarzi, Chin. Chem. Lett., 2010, 21, 547–549 CrossRef CAS.
- B. F. Mirjalili, A. Bamoniri, A. Akbari and N. Taghavinia, J. Iran. Chem. Soc., 2011, 8, S129–S134 CrossRef CAS.
- B. Rajitha, B. Sunil Kumar, Y. Thirupathi Reddy, P. Narsimha Reddy and N. Sreenivasulu, Tetrahedron Lett., 2005, 46, 8691–8693 CrossRef CAS.
- H.-K. Fun, C. W. Ooi, B. P. Reddy, V. Vijayakumar and S. Sarveswari, Acta Crystallogr., Sect. E: Struct. Rep. Online, 2012, 68, o2367–o2368 CrossRef CAS.
- V. Esquivel-Peña, V. Guccini, S. Kumar, G. Salazar-Alvarez, E. Rodríguez de San Miguel and J. de Gyves, RSC Adv., 2020, 10, 12460–12468 RSC.
- N. Amiralian, M. Mustapic, M. S. A. Hossain, C. Wang, M. Konarova, J. Tang, J. Na, A. Khan and A. Rowan, J. Hazard. Mater., 2020, 394, 122571 CrossRef CAS.
- M. Mustapić, M. S. Al Hossain, J. Horvat, P. Wagner, D. R. G. Mitchell, J. H. Kim, G. Alici, Y. Nakayama and B. Martinac, Microporous Mesoporous Mater., 2016, 226, 243–250 CrossRef.
- M. S. Shahriman, N. N. Mohamad Zain, S. Mohamad, N. S. Abdul Manan, S. M. Yaman, S. Asman and M. Raoov, RSC Adv., 2018, 8, 33180–33192 RSC.
- M. H. Haggui, M. Haddar, A. El Mahi, Z. Jendli and A. Akrout, Appl. Acoust., 2019, 147, 100–110 CrossRef.
- D. M. Langhorst, W. P. Amy, B. Shannon, D. Frantz, B. James and A. Kiziltas, Composites, Part B, 2019, 165, 712–724 CrossRef.
- F.-L. Jin, S.-J. Park and R.-R. Hu, Composites, Part B, 2019, 164, 287–296 CrossRef CAS.
- R. Xiong, Y. Wang, X. Zhang and C. Lu, RSC Adv., 2014, 4, 22632–22641 RSC.
- G. Gözaydın, S. Song and N. Yan, Green Chem., 2020, 22, 5096–5104 RSC.
-
(a) S. Azad and B. B. F. Mirjalili, RSC Adv., 2016, 6, 96928–96934 RSC;
(b) P. Li, T. Feng, Z. Song, Y. Tan and W. Luo, RSC Adv., 2020, 10, 30077–30086 RSC.
- K. Manzoor, M. Ahmad, S. Ahmad and S. Ikram, RSC Adv., 2020, 10, 2943 RSC.
- S. Nisar, A. H. Pandit, L.-F. Wang and S. Rattan, RSC Adv., 2020, 10, 14694–14704 RSC.
- E. R. D. Seiler, Y. Takeoka, M. Rikukawa and M. Yoshizawa-Fujita, RSC Adv., 2020, 10, 11475–11480 RSC.
- M. Tominaga, K. Kuwahara, M. Tsushida and K. Shida, RSC Adv., 2020, 10, 22120–22125 RSC.
- R. J. Moon, A. Martini, J. Nairn, J. Simonsen and J. Youngblood, Chem. Soc. Rev., 2011, 40, 3941 RSC.
- Y. Ning, Y. Huo, H. Xue, Y. Du, Y. Yao, A. C. Sedgwick, H. Lin, C. Li, S.-D. Jiang, B.-W. Wang, S. Gao, L. Kang, J. L. Sessler and J.-L. Zhang, J. Am. Chem. Soc., 2020, 142, 10219–10227 CrossRef CAS.
- W. S. Abo El-Yazeed, Y. G. Abou El-Reash, L. A. Elatwy and A. I. Ahmed, RSC Adv., 2020, 10, 9693–9703 RSC.
- B. Z. Tang, Y. Geng, J. W. Y. Lam, B. Li, X. Jing, X. Wang, F. Wang, A. B. Pakhomov and X. X. Zhang, Chem. Mater., 1999, 11, 1581–1589 CrossRef CAS.
- S. Yin, P. Qian Ren, R. Wang, H. Wang, J. Key, J. Dan, L. Brett, b Shan Ji and K. Shen, J. Mater. Chem. A, 2015, 4, 7591–7595 Search PubMed.
- S. Zhou, Y. Li, F. Cui, M. Jia, X. Yang, Y. Wang, L. Xie, Q. Zhang and Z. Hou, Macromol. Res., 2014, 22, 58–66 CrossRef CAS.
- L. K. Kumawat, M. Kumar, P. Bhatt, A. Sharma, M. Asif and V. K. Gupta, Sens. Actuators, B, 2017, 240, 365–375 CrossRef CAS.
- M. Yadav, Compos. Commun., 2018, 10, 1–5 CrossRef.
- L. E. Low, B. T. Tey, B. H. Ong, E. S. Chan and S. Y. Tang, Carbohydr. Polym., 2017, 155, 391–399 CrossRef CAS.
-
(a) N. Safajoo, B. B. F. Mirjalili and A. Bamoniri, RSC Adv., 2019, 9, 1278–1283 RSC;
(b) P. Ghamari Kargar, G. Bagherzade and H. Eshghi, RSC Adv., 2020, 10, 37086–37097 RSC.
- F. Shirini, M. Abedini, M. Seddighi, O. G. Jolodar, M. Safarpoor, N. Langroodi and S. Zamani, RSC Adv., 2014, 4, 63526–63532 RSC.
- F. Shirini, M. Mamaghani and S. V. Atghia, J. Iran. Chem. Soc., 2013, 10, 415–420 CrossRef CAS.
- A. Kishore Kumar, V. Sunitha, B. Shankar, T. Murali Krishna, C. A. Lincoln and P. Jalapathi, Russ. J. Gen. Chem., 2017, 87, 2011–2020 CrossRef CAS.
- S. E. Sadati Sorkhi, M. M. Hashemi and A. Ezabadi, Res. Chem. Intermed., 2020, 46, 2229–2246 CrossRef CAS.
- B. Maleki, A. Davoodi, M. V. Azghandi, M. Baghayeri, E. Akbarzadeh, H. Veisi, S. S. Ashrafi and M. Raei, New J. Chem., 2016, 40, 1278–1286 RSC.
- A. Khazaei, M. Rezaei, A. R. Moosavi-Zare and S. Saednia, J. Chin. Biochem. Soc., 2017, 64, 1088–1095 CrossRef CAS.
- F. Shirini, M. S. N. Langarudi, M. Seddighi and O. G. Jolodar, Res. Chem. Intermed., 2015, 41, 8483–8497 CrossRef CAS.
- R. Ghorbani-Vaghei, Z. Salimi, S. M. Malaekehpoor, F. Eslami and S. Noori, RSC Adv., 2014, 4, 33582 RSC.
- A. M. Abdelghany, A. A. Menazea, M. A. Abd-El-Maksoud and T. K. Khatab, Appl. Organomet. Chem., 2020, 2(34), e5250 Search PubMed.
- P. Ghamari kargar, G. Bagherzade and H. Eshghi, RSC Adv., 2020, 10, 32927–32937 RSC.
- G. Wulff and A. Akelah, Macromol. Chem. Phys., 1978, 179, 2647–2651 CrossRef CAS.
- A. Ghasemzadeh, J. Safaei-Ghomi and S. Zahedi, J. Serb. Chem. Soc., 2013, 78, 769–779 CrossRef.
- B. Maleki, M. Gholizadeh and Z. Sepehr, Bull. Korean Chem. Soc., 2011, 32, 1697–1702 CrossRef CAS.
- M. Rahimifard, G. Mohammadi Ziarani, A. Badiei, S. Asadi and A. Abolhasani Soorki, Res. Chem. Intermed., 2016, 42, 3847–3861 CrossRef CAS.
- A. N. Dadhania, V. K. Patel and D. K. Raval, J. Saudi Chem. Soc., 2017, 21, S163–S169 CrossRef CAS.
- M. H. Mashhadizadeh and Z. Karami, J. Hazard. Mater., 2011, 190, 1023–1029 CrossRef CAS.
- A. Fallah, M. Tajbakhsh, H. Vahedi and A. Bekhradnia, Res. Chem. Intermed., 2017, 43, 29–43 CrossRef CAS.
- A. Amini, A. Fallah, C. Cheng and M. Tajbakhsh, RSC Adv., 2018, 8, 41536–41547 RSC.
- M. R. Taghartapeh, N. Noroozi Pesyan, H. Rashidnejad, H. R. Khavasi and A. Soltani, J. Mol. Struct., 2017, 1149, 862–873 CrossRef CAS.
- F. Roschangar, R. A. Sheldon and C. H. Senanayake, Green Chem., 2015, 17, 752–768 RSC.
- D. J. C. Constable, A. D. Curzons and V. L. Cunningham, Green Chem., 2002, 4, 521–527 RSC.
- M. Kazemnejadi, S. A. Alavi, Z. Rezazadeh, M. A. Nasseri, A. Allahresani and M. Esmaeilpour, J. Mol. Struct., 2019, 1186, 230–249 CrossRef CAS.
Footnote |
† Electronic supplementary information (ESI) available. See DOI: 10.1039/d0ra09420j |
|
This journal is © The Royal Society of Chemistry 2021 |
Click here to see how this site uses Cookies. View our privacy policy here.