DOI:
10.1039/D0RA08329A
(Review Article)
RSC Adv., 2021,
11, 6163-6172
Research progress of catalysts for synthesis of low-carbon alcohols from synthesis gas
Received
29th September 2020
, Accepted 7th January 2021
First published on 3rd February 2021
Abstract
In recent years, the application value of low-carbon alcohols (C1–C6 alcohols) in the fuel, chemical, environmental protection and other fields has become increasingly prominent. Catalytic conversion of synthesis gas to low-carbon alcohol is one of the important ways to realize the industrial production of low-carbon alcohol. Lack of high-performance catalysts is the main reason that restricts the industrial development of producing low-carbon alcohols from synthesis gas. The construction of a dual active-center catalyst with high activity and stability, and the study of its function and catalytic mechanism have become significantly important. In this paper, the characteristics of the reaction process of syngas to low-carbon alcohols, and the catalytic mechanism and preparation methods of different catalyst systems were reviewed, which provide the basis for further research on high performance catalysts.
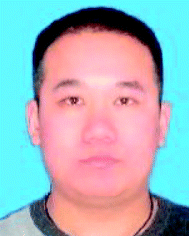 Xiaoxiao Xue | Xiaoxiao Xue joined the research group of Professor Zhang Yulong at the College of Chemistry and Chemical Engineering, Henan Polytechnic University in 2017 as a doctoral student. His research centres on the development of heterogeneous catalysts for the direct conversion of CO-containing syngas into higher alcohols. |
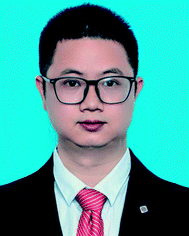 Yujing Weng | Yujing Weng completed his Bachelor's degree in Chemical Engineering at the Taiyuan University of Technology. He earned his PhD in Chemical Engineering from the Guangzhou Institute of Energy Conversion, Chinese Academy of Sciences. He is currently an associate professor at the College of Chemistry and Chemical Engineering, Henan Polytechnic University and joined Zhang Yulong's research group. His main research direction is industrial catalysis, using coal chemical synthesis gas as a raw material, exploring the clean and efficient chemical conversion path for the utilization of synthetic gas resources. |
 Shicheng Yang | Shicheng Yang joined the research group of Professor Zhang Yulong at the College of Chemistry and Chemical Engineering, Henan Polytechnic University in 2017 as a doctoral student. His research mainly focuses on the conversion of CO-containing syngas into aromatics. |
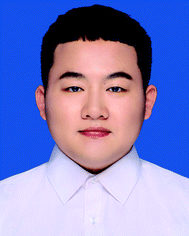 Shihang Meng | Shihang Meng completed his Bachelor's degree in Applied Chemistry at the College of Chemistry and Chemical Engineering, Henan Polytechnic University. He joined the research group of Professor Zhang Yulong at same school in 2019 as a graduate student. Currently, his research mainly focuses on the development of heterogeneous catalysts for the direct conversion of CO-containing syngas into higher alcohols. |
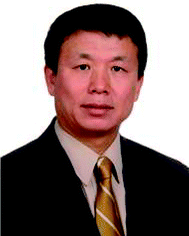 Qi Sun | Sun Qi is currently a professor and doctoral supervisor at the School of Chemistry and Chemical Engineering, Henan Polytechnic University. He is the director of Henan Provincial Key Laboratory of Coal Green Conversion. He has long been engaged in basic and applied research in the coal chemical, petrochemical and environmental chemical fields and has made outstanding contributions in the field of industrial catalysis. |
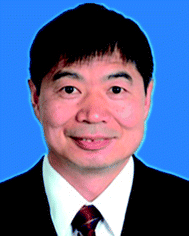 Yulong Zhang | Yulong Zhang is currently a professor and doctoral supervisor at the School of College of Chemistry and Chemical Engineering, Henan Polytechnic University. He is Deputy Director of Henan Provincial Key Laboratory of Coal Green Conversion. He is engaged in the research and development of coal conversion catalytic materials and process technologies, and mastering many key technologies of the coal conversion process. |
1. Introduction
Since entering the 21st century, global energy consumption still mainly depends on primary energy sources such as coal, oil and natural gas. A shift from fossil to renewable carbon resources can decouple chemical production from fossil resources and alleviate CO2 emissions. However, to be cost-effective and environmentally competitive with fossil-based processes, it is imperative to maximize feedstock utilization efficiency. With the continuous consumption of fossil energy and the increasingly serious environmental problems, the development and utilization of new and environmentally friendly energy has become urgent.1,2
As a type of renewable clean energy, low-carbon alcohol has gradually been used in the field of fuels and the chemical industry, and related research has become increasingly popular.3 Low-carbon mixed alcohols (alcohol mixtures of C1∼C6) can firstly be used as high-quality power fuels. Although their calorific value is lower than that of gasoline and diesel, due to the presence of oxygen atoms in alcohols, their combustion is more complete than that of gasoline and diesel. Meanwhile, there are fewer harmful substances in the released gas, which is an environmentally friendly fuel; secondly, low-carbon alcohol has a higher octane number, better explosion-proof and shock-resistant performance, and can replace the carcinogenic methyl tert-butyl ether as a fuel additive; finally, low-carbon alcohols can be used directly as bulk\fine chemical products, which can also be separated to obtain individual alcohols with high economic value such as ethanol, propanol, butanol, and pentanol.4–6 The current methods for preparing low-carbon alcohols have major drawbacks. Take ethanol as an example. The industrial production of ethanol mainly includes two methods: fermentation and chemical synthesis. Fermentation not only brings serious environmental pollution but also consumes a lot of food crops. The calculation shows that 1 ton C2H5OH consumes about 4 to 7 tons of crops. Fermentation of food crops to ethanol seriously violate China's development strategy; chemical synthesis requires a large amount of sulfuric acid, and the equipment is corroded seriously, which leads to high production costs. It is a method worth considering to prepare low-carbon alcohols through catalytic conversion of synthesis gas (CO and H2 mixed gas) with abundant sources and low prices. Synthesis gas can be obtained by coal gasification, natural gas steam reforming and biomass gasification.7,8 If the production of low-carbon alcohols through the catalytic conversion of synthesis gas achieves industrial production, it will, to a certain extent, alleviate the oil shortage and serious environmental pollution problems.
After decades of research, low-carbon alcohol synthesis technology is still in the laboratory stage, although companies or research institutions, such as Dow, IFP and the Shanxi Institute of Coal and Chemical Industry, Chinese Academy of Sciences, have conducted pilot tests. On the recent reported catalysts, C2+ alcohols (alcohols with 2 or more carbon atoms) are not high enough, while the price of C2+ alcohols is often higher. Among them, the price of propanol and butanol is about twice that of ethanol. Therefore, the main reason for the synthesis process of low-carbon alcohols failed to achieve industrialization is that the performance of the catalyst cannot meet the needs of industrialization.9,10 In other words, after decades of research, the design and development of catalysts with higher activity and selectivity is still the focus and difficulty of research in the field of low-carbon alcohol synthesis. Based on recent research, this article summarizes the reaction characteristics and synthesis process of synthesis gas to low-carbon alcohols, and focuses on the analysis of the catalytic reaction mechanism, design ideas and preparation methods of promising catalysts.
2. Reaction mechanisms of lowe-carbon alcohol synthesis reactions
In the process of catalyst research and development, strengthening the exploration of the synthesis mechanism of low-carbon alcohols is conducive to the targeted improvement of the catalytic structure and performance, and provides a solid theoretical basis for improving the activity, alcohol selectivity and long-term stability of the catalyst.
The synthesis of low-carbon mixed alcohols is similar to Fischer–Tropsch (F–T) synthesis and methanol synthesis, with some of the same surface reactions, but the reaction process or catalytic nature of the three is different. The F–T catalyst requires surface dissociative adsorption where the C–O bond is broken, while the methanol catalyst requires non-dissociative adsorption on the surface where the C–O bond remains. Due to the different electronic and physicochemical characteristics of the active sites of the catalyst, the former leads to the growth of hydrocarbon chains and the latter leads to the formation of oxygenated compounds. The design idea of the low-carbon alcohol catalyst is to optimize the combination of these two types of active components. The catalytic conversion of synthesis gas into low-carbon alcohol technology (some literature refer to higher alcohol synthesis, HAS) requires the catalyst to have dual functions, that is, the active sites of dissociative adsorption and non-dissociative adsorption.10,11 The CO insertion mechanism of syngas synthesis of low-carbon alcohols is shown in Fig. 1.12 Part of CO dissociates and adsorbs to form adsorbed C* and adsorbed O*. The adsorbed C* is hydrogenated to form adsorbed *CHx; the adsorbed *CHx reacts with the adsorbed *CHx to achieve carbon chain growth, forming an alkyl species *CnHz. Undissociated CO* is inserted into the *CnHz alkyl species to form an acyl species Cn+1H2n+3CO*, and the acyl species undergoes further hydrogenation to form a lower alcohol.
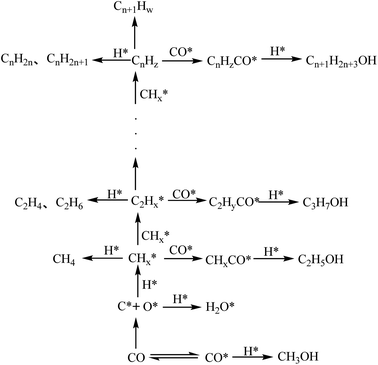 |
| Fig. 1 The reaction process of CO hydrogenation catalyzed synthesis of lower alcohols.12 | |
The reactions involved in the production of low-carbon alcohols from synthesis gas as follows. Reaction eqn (1) and (2) are the basic reactions for preparing low-carbon alcohols from synthesis gas. The reaction is an exothermic and reversible reaction with reduced volume. Increasing pressure or reducing the reaction temperature is beneficial to the synthesis of low-carbon alcohols. In the synthesis process of low-carbon alcohols, there are many types of parallel side reactions at the same time, such as the reaction to generate various alkanes and alkenes, and the water gas shift reaction, such as reaction eqn (3) and (4). In addition, there are secondary reactions to produce aldehydes and esters (5) and (6).
|
nCO + 2nH2 = CnH2n+1OH + (n − 1)H2O
| (1) |
|
(2n − 1)CO + (n + 1)H2 = CnH2n+1OH + (n − 1)CO2
| (2) |
|
nCO + (2n + 1)H2 = CnH2n+2 + nH2O
| (3) |
|
CnH2n+1OH = Cn−1H2n−1CHO + H2
| (5) |
|
C2H5OH + CH3OH = CH3COOCH3 + 2H2
| (6) |
The reaction mechanism of synthesis gas to low-carbon alcohols shows that the formation of C2+ alcohols competes with the formation of C2+ hydrocarbons. Only on a catalyst that has strong chain growth ability and high non-dissociative adsorption CO* insertion activity, can it be possible to improve the selectivity of low-carbon alcohols. Therefore, to improve catalyst activity and lower alcohol selectivity, the key is to increase the number of dual active centers on the catalyst, and to achieve a certain balance between the content of the two types of active centers. The dissociation of the dual active centers, or the imbalance in the number of the two types of active centers will cause the catalyst performance to decrease. How to construct dual active centers with high activity and stability at the nanometer or even atomic scale, and to study its function and transient mechanism, has become a research hotspot that attracts many scientific researchers.
3. Synthesis gas to low-carbon alcohol technology
After decades of research, there are currently four main categories of processes for producing low-carbon alcohols from syngas: MAS process, IFP process, Sygmol process and Octamix process.13–17
3.1. MAS process.
Italy's SNAM Company and Danish Topsoe Company have modified methanol-based catalysts and corresponding process conditions, which can produce other alcohol products while producing methanol.18 In the alcohol products of this process, methanol is the main product, followed by isobutanol. The selectivity of low-carbon alcohols in the alcohol products of this process is poor, and the requirements for operating temperature and operating pressure are relatively high.
3.2. IFP process.
The French Petroleum Institute began to study Cu–Co-based catalysts in 1976, and initially proposed the IFP process, which is the earliest process for the synthesis of low-carbon alcohols.14 It uses two-stage partial reaction equipment to produce low-carbon alcohol with methanol as the main component. Although the temperature and pressure requirements for operating this process are not high, its catalytic activity and selectivity are not ideal. In the end, the French Petroleum Institute built a 7000 barrel/year pilot plant in Japan in 1984, and did not conduct the next step of industrialization experiment.
3.3. Sygmol process.
The process was jointly developed by the Dow Chemical Company and United Carbon Corporation (UCC). It uses an isothermal reactor to fill with molybdenum sulfide catalysts. It is characterized by high selectivity of low-carbon alcohols. The catalyst has excellent resistance to carbon formation and sulfur resistance.1 In China, Peking University and East China University of Science and Technology have improved the Sygmol process, obtained a catalyst with better catalytic performance, and completed a pilot study.
3.4. Octamix process.
The process was developed by the German Lurgi company, using an isothermal reactor (winding tube type or tube type), and the heat generated during the reaction is taken away by the superheated water and steam.19 Although the process achieves high alcohol selectivity, the catalyst is prone to lose activity at high temperature, which limits its industrialization.
Among the above four types of processes, the MAS process is the most mature compared to other process routes. The more advanced ones are the Sygmol process and the Octamix process. Both processes have the advantages of mild reaction conditions, higher alcohol selectivity, and low water content. The Octamix process is much more suitable in China since a number of methanol plants similar to the Octamix process have been built in China. However, the Sygmol process has is still in the pilot stage, and the process technology is relatively difficult. However, the hydrocarbon yield of the Sygmol process is much higher than that of the Octamix process, which is of great significance for improving the thermal efficiency of the process. The catalyst used in the Sygmol process can tolerate 100 times more of the sulfur content in the feed gas than that of the Octamix process, which is beneficial to lower the cost of desulfurization. The process can effectively reduce costs. Therefore, considering the maturity of the process and the operation cost, the development cycle of the Octamix process may be shorter; considering the hydrocarbon yield and the sulfur resistance of the catalyst, the Sygmol process should also be further developed.
4. Catalyst system
The catalyst for production of low-carbon alcohol from synthesis gas mainly includes four major systems, namely, modified methanol catalysts, modified F-T catalysts, molybdenum-based catalysts and precious metal catalysts.
4.1. Modified methanol catalyst
The modified methanol catalysts are represented by the Zn–Cr catalyst developed by Snam Company in Italy and the Cu–Zn catalyst developed by Lurgi in Germany. The products are mainly methanol and isobutanol. The modified Zn–Cr catalyst has harsh operating conditions and needs to be carried out under high pressure and high temperature, and the selectivity of isobutanol is relatively high while the modified Cu–Zn catalyst has mild reaction conditions and can be operated at lower temperature and low pressure. There are many reports on the synthesis mechanism of low-carbon alcohols with modified low-temperature Cu–Zn catalysts. The chain growth rules and alcohol distribution equations proposed by the Smith team based on the Graves chain growth mechanism have been generally recognized by the public, as shown in Fig. 2.20,21 The mechanism believes that: (1) low-carbon alcohols are produced the addition of single carbon or double carbon to a growing chain so for these two intermediates, at least one of the them must be a single-carbon or two-carbon intermediate. (2) The addition reaction only occurs at the α carbon position or β carbon position of the intermediate, and the addition reaction cannot occur on –CH. At the same time, double-carbon addition does not occur at the α-carbon position, and the single-carbon addition at the β-carbon position is faster than the α-carbon addition and also faster than the double-carbon addition and desorption at the β-carbon position. (3) From the perspective of the surface concentration of the intermediates, all catalytic reactions including the desorption of the intermediate are first-order irreversible reactions, and the addition rate is independent of the number of carbon atoms of the intermediate. This mechanism well explains the reason for there are more methanol and isobutanol in the reaction products on the Cu–Zn catalyst. According to the above chain growth mechanism, the insertion of CO is necessary during the formation of low-carbon alcohols, and the insertion center of CO must meet the following conditions: non-dissociatively adsorbed carbon monoxide, and dissociatively adsorbed hydrogen. At the same time, it has a mild hydrogenation activity to prevent the formation of hydrocarbons by over hydrogenation. The insertion of CO and hydrogenation to produce alcohols are completed in the same active center. In order to make CO and hydrocarbon groups better for bonding, the distance to the center of the chain extension should be as short as possible. Adding additives to Cu–Zn-based catalysts can significantly promote the performance of lower-carbon alcohols synthesis. It is found that the promoter Cs can obviously promote the performance of the catalyst Cu/ZnO/Al2O3 to synthesize low-carbon alcohols. Adding a small amount of Cr can significantly increase the surface area of the catalyst, thereby inhibiting the agglomeration of active metals, which in turn makes the catalyst have better activity and stability.22,23
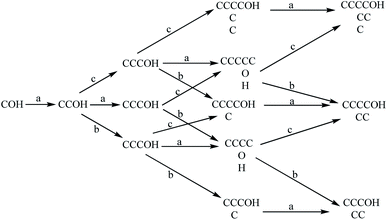 |
| Fig. 2 The carbon chain growth mechanism of the synthesis of lower carbon alcohols and the schematic diagram of the formation of C2+ alcohols.20 | |
4.2. Modified F–T catalyst
In the F–T synthesis reaction, there are usually other side reactions to obtain oxygen-containing compounds such as alcohols. The production of oxygen-containing compounds such as alcohols, acids, ketones, vinegars, etc, is varied with the F–T synthesis catalyst. Therefore, the modification of F–T synthesis catalysts to synthesize low-carbon alcohols has received extensive attention for research, among which Cu–Co and Cu–Fe are the two types of catalysts widely studied.24–27 The modified Fischer–Tropsch Cu–Co catalyst was developed by the French Petroleum Institute, and the synthesis products are mainly C1–C6 linear primary alcohols, whose product distribution is in line with the Anderson–Schulz–Flory (ASF) distribution of F–T. As to the catalytic mechanism, it is generally believed that Cu–Co catalysts for the synthesis of low-carbon alcohols have two types of active centers. Among them, Co is used for dissociative adsorption of CO to generate alkyl chains, and Cu is used for non-dissociative adsorption of CO to oxidize alkyl chains. To produce alcohol, the two type of active centers work together to form a dual-active center required for the synthesis of low-carbon alcohols.2 In recent years, most research on the catalyst development mainly includes two aspects: (1) the ratio of active components Cu and Co; (2) the distribution of the two active centers. To make the active components Cu and Co close to the atomic scale, and distribute them as evenly as possible to increase the number of interfaces will significantly improve the synergistic effect of Cu and Co, leading to increase the selectivity of low-carbon alcohols. The reaction mechanism of Cu–Fe-based catalysts is shown in Fig. 3. The active center Cu of the catalyst can improve the non-dissociative adsorption of CO, thereby improving the ability of the catalyst to synthesize alcohols. The addition of Fe can improve the dissociative adsorption of CO. The ability to generate CHx and promote the growth of carbon chain is conducive to the synthesis of low-carbon alcohols.28,29 In addition, additives such as alkali metal promoters and supports have a great influence on the activity and selectivity of such catalysts.30 Cu–Co catalysts must have alkali metals, otherwise the selectivity of alcohols will be very low. The role of the carrier is also obvious. The catalysts with the active phase supported on different carriers often get different products distribution. For example, catalyst supported on MgO mainly produces methanol, supported on TiO2, CeO2 or La2O3 mainly produce hydrocarbons, while supported on ZrO2, SiO2 and Al2O3 has higher C2+ alcohol selectivity. It is reported that low-carbon alcohols could be synthesized with a cobalt metal–carbide (Co–Co2C) catalyst.31 Density functional theory calculations show that Co2C is highly effective for non-dissociative adsorption of CO for CO insertion, while Co metal is highly active for CO dissociative adsorption for chain growth. The interface between the Co and Co2C worked as the dual sites for formation of low-carbon alcohols.
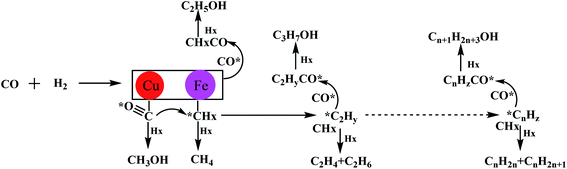 |
| Fig. 3 Cu–Fe-based catalyst for the catalytic synthesis of low-carbon alcohols.30 | |
4.3. Molybdenum-based catalyst
The Dow Chemical Company in the United States first proposed molybdenum-based catalysts with high sulfur resistance and low carbon deposition, so it can be used under the conditions of higher sulfur content and lower H2/CO molar ratio (0.7–1),32,33 respectively, including molybdenum sulfide, molybdenum oxide and molybdenum carbide based catalysts.
The catalytic mechanism of the molybdenum carbide-based catalyst is shown in Fig. 4. The low-valence molybdenum species and the high-valence molybdenum species constitute dual active centers. While, the low-valence molybdenum species is the chain growth center, where CO dissociatively adsorbs and forms surface alkyl groups. To be specific, high-valence molybdenum species undergo non-dissociative adsorption of CO, which is the active center for alcohol formation. The selectivity of low-carbon alcohols is related to the relative content of the two active centers.1
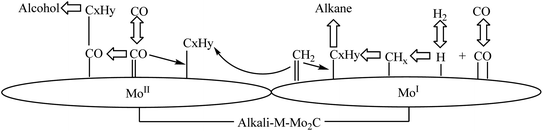 |
| Fig. 4 Molybdenum carbide-based catalyst for the catalytic synthesis of low-carbon alcohols.1 | |
The synthesis mechanism of low-carbon alcohols on K/MoS2 catalysts is shown in Fig. 5. The catalysts of this series also have dual active centers, and the chain growth process is basically the same as that of molybdenum carbide-based catalysts.34 Zhao Lu et al.35 reported that high-performance nano-MoS2-based catalysts for low-carbon alcohols through CO hydrogenation were synthesized using non-thermal plasma under ambient conditions. This flexible and facile approach can give the thinner and shorter MoS2 slabs, expose more coordinatively unsaturated sites, and increase the number of active centers for alcohols formation. This kind of catalyst shows good catalytic performance. Wang Na et al.36 reported a series of catalysts prepared by using molybdenum sulfide clusters as precursors, which provided good dispersion of MoS2 particles with many coordination unsaturated Mo sites, which was conducive to the formation of intermediate active phase and improve the catalytic performance.
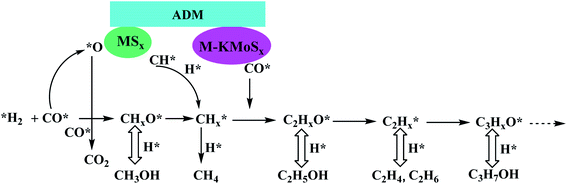 |
| Fig. 5 Catalytic synthesis of lower carbon alcohols by molybdenum sulfide based catalyst.34 | |
Catalytic mechanism of molybdenum oxide-based catalysts: studies have shown that there are both oxidized molybdenum (MoO2−x) and metallic molybdenum (Mo) on the surface of such catalysts. Among them, MoO2−x is conducive to the formation of alcohols. The reaction mechanism is shown in Fig. 6.37 The synthesis gas undergoes dissociative adsorption on the Mo surface to form metal carbene, which is inserted into the metal–alkyl bond to achieve chain growth. On the MoO2−x phase, CO undergoes non-dissociative adsorption, and the alkyl group migrates to the oxidized molybdenum. It reacts with the non-dissociatively adsorbed CO to form acyl groups. Finally, the hydrogenation reaction of alkyl and acyl groups forms hydrocarbons and mixed alcohols on molybdenum sites of different valences. Li et al.38 prepared new MoO2 by RF induced thermal plasma method. The core–shell catalyst has small particle sizes, an amorphous shell, and a crystalline core with strong core–shell interaction and abundant surface species in the shell, so as to improve its catalytic performance.
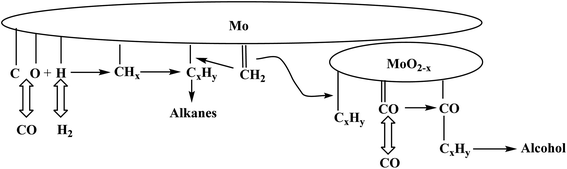 |
| Fig. 6 Catalytic synthesis of low-carbon alcohols by alkali metal modified molybdenum oxide-based catalysts.37 | |
Although this type of catalyst has the advantages of sulfur and carbon deposition resistance, it still has the disadvantages of low activity and selectivity. Researchers have found that the total alcohol yield and C2+ alcohol selectivity of molybdenum sulfide-based catalysts can be improved by adding additives and changing the support.39,40 Alkali metals and alkaline earth metals, such as Na, K, Cs, Sr, Ba, etc., are widely used as promoters for the synthesis of alcohol catalysts, which have a significant impact on the activity, selectivity and life of the catalyst. The most obvious effect of alkali metal additives is to inhibit the formation of hydrocarbons and improve the selectivity of alcohols. In terms of reaction mechanism in the CO hydrogenation reaction, the synthesis of methanol only requires the adsorption of CO in the molecular state; the synthesis of liquid hydrocarbons requires the dissociative adsorption of CO, which is conducive to the growth of the C–C chain, and the progress of the hydrogenation reaction; in the process of low-carbon alcohol synthesis, the molecular state adsorption and dissociative adsorption of CO work together. Only when the two reach an appropriate ratio, can the growth reaction of the C–C chain and the insertion reaction of CO be facilitated to obtain the final higher alcohol product. Alkali metals can prevent the dissociative adsorption of CO at the active site, and facilitate its non-dissociative adsorption to produce alcohols. Some alkaline earth metals such as Sr and Ba also have the above effects. The addition of a small amount of alkali metal promoter can generally increase the reaction rate, while excessive alkali metal will block the active sites on the catalysts surface to reduce the effective surface area and deactivate the catalyst. Most studies have shown that after adding alkali metal compounds to molybdenum-based catalysts, the total activity of the catalyst is reduced, but the selectivity and the space–time yield of alcohols are significantly improved.41 Transition metal promoters of Fe, Co and Ni are studied on catalytic performance. Fig. 7 shows the reaction process of CO hydrogenation on molybdenum sulfide catalysts with transition metals as promoters.46 The CO* adsorbed on the surface of MSx (M = Fe, Co or Ni) is partially dissociated into
and
is further hydrogenated to form CH4; on the M-KMoS2 surface, the non-dissociatively adsorbed CO* is inserted into the metal–methyl groupto form the precursor of an alcohol. The precursor can be further hydrogenated to form an alcohol, or dehydrated to form a hydrocarbon. In this process, the concentration of C1 intermediate compound on the catalyst surface has an important influence on the formation of methanol and branched alcohols (Table 1). For example, Wang et al.42 studied the mechanism of potassium and nickel in MOS based catalysts. In addition, noble metals (Rh, Pd), Mn, rare earth elements La, etc. can also be added to the molybdenum-based catalyst as additives, and their addition can increase the output of higher alcohols in the product.
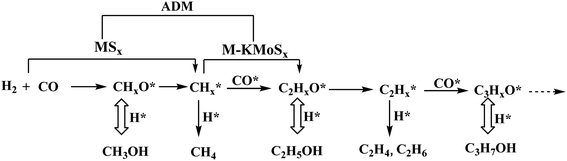 |
| Fig. 7 CO hydrogenation reaction mechanism on K–MoS2 catalyst modified by transition metal (M is Fe, Co or Ni).46 | |
Table 1 Performance of CO hydrogenation over catalysts
Catalyst |
CO con. V(%) |
Selectivity (wt%) |
ROH distribution (we%) |
Ref. |
CHx |
ROH |
MeOH |
C2 + OH |
K0.5-(Ni1Mo0.25)Si-PS |
6.6 |
25.2 |
43.7 |
34.6 |
65.4 |
43 |
Mn–O–Rhδ+ |
42.4 |
59.7 |
40.3 |
11.7 |
88.3 |
44 |
Fe/K/β-Mo2C |
86.92 |
58.53 |
41.47 |
20.96 |
79.04 |
45 |
MoS2-DN |
27.3 |
31.4 |
68.6 |
40.7 |
59.3 |
35 |
K–Mo3Sx-NiL |
46.14 |
34.07 |
65.93 |
23.99 |
76.01 |
42 |
K–NiMo3Sx |
41.41 |
16.76 |
83.24 |
40.29 |
59.71 |
36 |
4.4. Precious metal catalyst
Noble metal catalysts are represented by rhodium-based (Rh) catalysts, with ethanol as the main target product.46 Rhodium-based catalysts are one of the most promising catalyst systems for syngas conversion to synthesize ethanol. However, considering the high price of noble metal rhodium, reducing the amount of rhodium loading and improving the utilization efficiency of metal rhodium have become the research focus. There are many opinions on the synthesis mechanism of low-carbon alcohols and active center structure of rhodium-based catalysts, among which CO insertion has been recognized by many researchers.47 The mechanism is as follows: the first step is the adsorption of CO, in which C is adsorbed on rhodium, and O is adsorbed on the metal promoter; the second step is the hydrogenation of adsorbed CO to form an intermediate species -CHx due to the interaction between the metal rhodium and the promoter. In the third step, CO is inserted into the intermediate species –CHx to form –CHxCO; in the fourth step, hydrogen is added to form alcohol. The preparation of rhodium-based catalysts with high dispersion has a positive effect on the hydrogenation of CO, and rhodium-based catalysts with different supports or with different additives will also have a profound impact on the catalytic effect during the reaction. Jiang et al.48 used a template synthesis method to prepare two-dimensional ordered mesoporous carbon nanomaterials (MCNs) as the carrier of rhodium-based catalysts for synthesis of low-carbon alcohols. The catalytic activity test was carried out on a fixed bed reactor, and the results showed that the nano-sized MCNs supported catalyst has higher alcohol selectivity and C2+ alcohol selectivity than the micron-sized ordered mesoporous carbon supported catalyst. The total alcohol yield of the Rh/CMK-5-MCNs catalyst with a hollow framework structure is quite high, which indicates that there is an interaction between Rh metal particles and the support MCNs, which promotes the catalytic activity.
Based on the above analysis, it can be found that the current synthesis of low-carbon alcohol catalysts mainly has the following problems: (1) the activity is low with the CO conversion rate is relatively low, which is not conducive to the production of alcohols. (2) The reaction conditions are harsh, and the existing catalysts generally require high reaction temperatures and pressures, which undoubtedly increases the cost of industrial production. (3) The selectivity of C2+ alcohol is low, which is the common deficiencies of the existing catalyst. Since the value of methanol in the low-carbon alcohol system is far behind the C2+ alcohol, it will lead to low product economy. Therefore, how to further increase the proportion of C2+ alcohols in low-carbon alcohols and prepare catalysts with high activity and stability is the direction of catalyst development in the future.
5. Catalyst preparation method
The preparation method of catalysts49 influences the catalytic performance of low carbon alcohol synthesis catalysts. The preparation process of a catalyst is influenced by the temperature, the mixing method of active ingredients, drying conditions, calcination conditions, etc, which directly affect the active metal components of the crystal structure of catalyst, the dispersion degree, and the REDOX performance, etc. Therefore, the preparation method of a catalyst directly affects the catalytic performance. The preparation methods of synthesis gas to lower alcohol catalysts are different in many literature reports, mainly including co-precipitation method and impregnation method.50–52
The co-precipitation method involves the interaction of salt solutions of two or more metal ions with the precipitation agent to form a precipitate containing several active metal components.53 The co-precipitation method has the advantages of simple process, short preparation period, low calcination temperature, and stable catalyst performance. However, the addition of precipitating agent may cause excessive local concentration of the solution during the preparation process, resulting in agglomeration or uneven dispersion of metal components, reducing the catalytic performance of the catalyst.
The impregnation method loads one or several metal components on the carrier in the form of a salt solution. It has the advantages of simple operation and high metal utilization. The disadvantage is that the metal is not easy to disperse uniformly and is prone to agglomeration.54 The traditional impregnation method can generally be divided into the excessive impregnation method and the equal volume impregnation method (also called incipient wetness impregnation). Excessive impregnation method can disperse the active metal better, and can maximize the adsorption capacity, but it is hard to exactly control the loading of the active component. To get higher activity, generally speaking, the larger the loading, the better. However, too much active metal lading will lead to agglomeration. The equal volume impregnation method can better control the loading of active components, but it will produce a nonuniform dispersion of active components with uneven metal particle sizes. In order to overcome the shortcomings of the traditional impregnation method, numerous studies have been conducted to promote the full contact of the active metal with the surface of the carrier. One example is through the ultrasonic cavitation effect of ultrasound, in which the active metal can be dispersed evenly on the surface of the catalyst, thereby affecting the dispersion of the active metal, the crystal structure, and the pore diameter of the catalyst distribution and so on.
6. Conclusions
In the reaction process of synthesis gas to lower alcohol, the dissociative adsorption and non-dissociative adsorption of CO are the key to the synthesis of lower alcohol. Too much dissociative adsorption will result in the production of more alkanes in the product, while too much non-dissociative adsorption will result in less C2+ alcohols (with higher economic value) in the synthesized low-carbon alcohols. Only when the catalyst has both strong chain growth ability and high non-dissociative adsorption CO* insertion activity, can it be possible to improve the selectivity of low-carbon alcohols. At present, the most researched catalysts are Cu–M (M is Zn, Co and Fe), Zn–Cr and other bimetallic catalysts, molybdenum-based catalysts and rhodium-based catalysts, etc. These catalysts have the synergistic effects of additives and supports to show higher activity and selectivity for the synthesis of low-carbon alcohols. Therefore, in order to improve the activity and the selectivity of the catalyst for low-carbon alcohols, the key is to research and design a catalyst with a large number of dual active centers and the ratio of the two types of active centers reaches a certain balance.
Author contributions
This manuscript was contributed by all authors. All the authors have ratified the manuscript.
Conflicts of interest
The authors confirm no competitive economic interest.
Acknowledgements
This work was supported by grants from the Outstanding Foreign Scientists Studio of Coal Green Conversion of Henan Province (GZS2020012), the Fundamental Research Funds for the Universities of Henan Province (NSFRFI180327), and Henan Polytechnic University (19A530002).
References
- K. Fang, D. Li and M. Lin, et al., A short review of heterogeneous catalytic process for mixed alcohols synthesis via syngas, Catal. Today, 2009, 147(2), 133–138 CrossRef CAS.
- M. Ao, G. H. Pham and J. Sunarso, et al., Active centers of catalysts for higher alcohol synthesis from syngas: a review, ACS Catal., 2018, 8(8), 7025–7050 CrossRef CAS.
- V. R. Surisetty, A. K. Dalai and J. Kozinski, Alcohols as alternative fuels: an overview, Appl. Catal., A, 2011, 404(1–2), 1–11 CAS.
- Y. Liu, Z. Zuo and C. Li, et al., Effect of preparation method on CuZnAl catalysts for ethanol synthesis from syngas, Appl. Surf. Sci., 2015, 356, 124–127 CrossRef CAS.
- J. Sun, S. Wan and J. Lin, et al., Advances in Catalytic Conversion of Syngas to Ethanol and Higher Alcohols, Petrochemical Catalyst Materials, Processes, and Emerging Technologies, 2016 Search PubMed.
- M. Driess, P. Preikschas and J. Bauer, et al., From a Molecular Single-Source Precursor to a Selective High-Performance RhMnOx Catalyst for the Conversion of Syngas to Ethanol, ChemCatChem, 2018, 11(2) DOI:10.1002/cctc.201801978.
- Y. Chen, H. Zhang and H. Ma, et al., Direct Conversion of Syngas to Ethanol over Rh–Fe/γ-Al2O3 Catalyst: Promotion Effect of Li, Catal. Lett., 2018, 148(2), 691–698 CrossRef CAS.
- G. Zhang, Y. Dong and M. Feng, et al., CO2 reforming of CH4 in coke oven gas to syngas over coal char catalyst, Chem. Eng. J., 2010, 156(3), 519–523 CrossRef CAS.
- A. J. Medford, A. C. Lausche and F. Abild-Pedersen, et al., Activity and selectivity trends in synthesis gas conversion to higher alcohols, Top. Catal., 2014, 57(1–4), 135–142 CrossRef CAS.
- V. Subramani and S. K. Gangwal, A review of recent literature to search for an efficient catalytic process for the conversion of syngas to ethanol, Energy Fuels, 2008, 22(2), 814–839 CrossRef CAS.
- J. Schumann, A. J. Medford and J. S. Yoo, et al., Selectivity of Synthesis Gas Conversion to C2+Oxygenates on fcc (111) Transition-Metal Surfaces, ACS Catal., 2018, 8(4), 3447–3453 CrossRef CAS.
- X. Xiaoding, E. Doesburg and J. Scholten, Synthesis of higher alcohols from syngas-recently patented catalysts and tentative ideas on the mechanism, Catal. Today, 1987, 2(1), 125–170 CrossRef.
- R. Xu, S. Zhang and C. B. Roberts, Mixed alcohol synthesis over a K promoted Cu/ZnO/Al2O3 catalyst in supercritical hexanes, Ind. Eng. Chem. Res., 2013, 52(41), 14514–14524 CrossRef CAS.
- A. Sugier and E. Freund, Process for manufacturing alcohols, particularly linear saturated primary alcohols, from synthesis gas, US Pat., 4122110, 1978 Search PubMed.
- J. Anton, H. Ruland and S. Kaluza, et al., Fast and Reproducible Testing of Cu–Co-Based Catalysts Applied in the Conversion of Synthesis Gas to Ethanol and Higher Alcohols, Catal. Lett., 2015, 145(7), 1374–1381 CrossRef CAS.
- B. Ren, X. Dong and Y. Yu, et al., A density functional theory study on the carbon chain growth of ethanol formation on Cu–Co (111) and (211) surfaces, Appl. Surf. Sci., 2017, 412, 374–384 CrossRef CAS.
- Y. Ding, X. Song and W. Chen, et al., Phosphide catalyst for syngas conversion and the production method and use thereof, US Pat., Application 20140018455, 2015 Search PubMed.
- T. Jiang, Y. Niu and B. Zhong, Synthesis of higher alcohols from syngas over Zn–Cr–K catalyst in supercritical fluids, Fuel Process. Technol., 2001, 73(3), 175–183 CrossRef CAS.
- L. Nowicki, Kinetics of CO hydrogenation on modified Cu/ZnO catalyst in a slurry reactor, Chem. Eng. Process., 2005, 44(3), 383–391 CrossRef CAS.
- G. D. Graves, Higher Alcohols Formed from Carbon Monoxide and Hydrogen1, 2, Ind. Eng. Chem., 1931, 23(12), 1381–1385 CrossRef CAS.
- K. J. Smith and R. B. Anderson, The higher alcohol synthesis over promoted Cu/ZnO catalysts, Can. J. Chem. Eng., 1983, 61(1), 40–45 CrossRef CAS.
- J. Sun, Q. Cai and Y. Wan, et al., Promotional effects of cesium promoter on higher alcohol synthesis from syngas over cesium-promoted Cu/ZnO/Al2O3 catalysts, ACS Catal., 2016, 6(9), 5771–5785 CrossRef CAS.
- K. M. Walter, M. Schubert and W. Kleist, et al., Effect of the Addition of Ethanol to Synthesis Gas on the Production of Higher Alcohols over Cs and Ru Modified Cu/ZnO Catalysts, Ind. Eng. Chem. Res., 2015, 54(5), 1452–1463 CrossRef CAS.
- A. Bordoloi, J. Anton and H. Ruland, et al., Metal–support interactions in surface-modified Cu–Co catalysts applied in higher alcohol synthesis, Catal. Sci. Technol., 2015, 5(7), 3603–3612 RSC.
- G. Liu, T. Niu and A. Cao, et al., The deactivation of Cu–Co alloy nanoparticles supported on ZrO2 for higher alcohols synthesis from syngas, Fuel, 2016, 176, 1–10 CrossRef CAS.
- A. Cao, J. Schumann and T. Wang, et al., Mechanistic Insights into the Synthesis of Higher Alcohols from Syngas on CuCo Alloys, ACS Catal., 2018, 8(11), 10148–10155 CrossRef CAS.
- C. Huang, M. Zhang and C. Zhu, et al., Fabrication of Highly Stable SiO2 Encapsulated Multiple CuFe Nanoparticles for Higher Alcohols Synthesis via CO Hydrogenation, Catal. Lett., 2018, 148(4), 1080–1092 CrossRef CAS.
- H. Guo, H. Zhang and F. Peng, et al., Effects of Cu/Fe ratio on structure and performance of attapulgite supported CuFeCo-based catalyst for mixed alcohols synthesis from syngas, Appl. Catal., A, 2015, 503, 51–61 CrossRef CAS.
- X. Shi, H. Yu and S. Gao, et al., Synergistic effect of nitrogen-doped carbon-nanotube-supported Cu–Fe catalyst for the synthesis of higher alcohols from syngas, Fuel, 2017, 210, 241–248 CrossRef CAS.
- S. Schmidt, C. Göbel and J. Nebel, et al., Recent Developments in the Conversion of Synthesis Gas to Short-Chain Alcohols over Cu-Co-Based Catalysts, Chem. Ing. Tech., 2018, 90(10), 1465–1475 CrossRef CAS.
- Y.-P. Pei, J.-X. Liu and Y.-jie Ding, et al., High Alcohols Synthesis via Fischer–Tropsch Reaction at Cobalt Metal/Carbide Interface, ACS Catal., 2015, 5, 3620–3624 CrossRef CAS.
- B. D. Molina, B. Torres, M. Zarei-chaleshtori, et al., Hydrothermal synthesis of alkali promoted mos2-based catalyst, US Pat., Application 20170335201, 2017 Search PubMed.
- V. Subramani and S. K. Gangwal, A review of recent literature to search for an efficient catalytic process for the conversion of syngas to ethanol, Energy Fuels, 2008, 22(2), 814–839 CrossRef CAS.
- J. K. Hasty, S. Ponnurangam and S. Turn, et al., Catalytic synthesis of mixed alcohols mediated with nano-MoS2 microemulsions, Fuel, 2016, 164, 339–346 CrossRef CAS.
- Z. Lu, Ying Lia and X. Liu, et al., Low-temperature synthesis of high-performance nano-MoS2-based catalyst via non-thermal plasma for higher alcohol synthesis from syngas, Catal. Today, 2020, 355, 17–25 CrossRef.
- Na Wang, J. Li and R. Hu, et al., Enhanced catalytic performance and promotional effect of molybdenum sulfide cluster-derived catalysts for higher alcohols synthesis from syngas, Catal. Today, 2018, 316, 177–184 CrossRef CAS.
- X. Shi, X. Yang and F. Bai, et al., Research progress of molybdenum based catalyst promoters for synthesis of low-carbon alcohols from syngas, Prog. Chem. Chem. Ind., 2010, 29(12), 2291–2297 CAS.
- J. Li, R. Hu and H. Qu, et al., Radio-frequency thermal plasma-induced novel chainmail-like core–shell MoO2 as highly stable catalyst for converting syngas to higher alcohols, Appl. Catal., B, 2019, 249, 63–71 CrossRef CAS.
- S. Liu, H. Zhou and Q. Song, et al., Synthesis of higher alcohols from CO2 hydrogenation over Mo–Co–K sulfide-based catalysts, J. Taiwan Inst. Chem. Eng., 2017, 76, 18–26 CrossRef CAS.
- R. Andersson Catalytic conversion of syngas to higher alcohols over MoS2-based catalysts. KTH Royal Institute of Technology, 2015 Search PubMed.
- P. E. Boahene and A. K. Dalai, Higher Alcohols Synthesis over Carbon Nanohorn-Supported KCoRhMo Catalyst: Pelletization and Kinetic Modeling, Ind. Eng. Chem. Res., 2018, 57(16), 5517–5528 CrossRef CAS.
- Na Wang, R. Hu and L. Jianli, et al., Insight into the promotion mechanism of K and Ni in sulfide molybdenum-based catalysts for higher alcohols synthesis from syngas, Catal. Commun., 2017, 91, 57–61 CrossRef CAS.
- Zhang, Y. Li and S. Gao, et al., Synthesis of higher alcohols by CO hydrogenation on a K-promoted Ni-Mo catalyst derived from Ni-Mo phyllosilicate, Catal. Sci. Technol., 2018, 8(16) 10.1039/C8CY01095A.
- C. T. Wang, J. Zhang and G. Q. Qin, et al., Direct Conversion of Syngas to Ethanol within Zeolite Crystals, Chem, 2019, 6(3), 646–657 CAS.
- N. Wang, K. Fang and D. Jiang, et al., Iron carbide promoted K/β-Mo2C for higher alcohols synthesis, Catalysis Today, 2010, 158, 241–245 CrossRef CAS.
- J. Hu, Y. Wang and C. Cao, et al., Conversion of biomass-derived syngas to alcohols and C2 oxygenates using supported Rh catalysts in a microchannel reactor, Catal. Today, 2007, 120(1), 90–95 CrossRef CAS.
- J. Hu, Y. Wang and C. Cao, et al., Conversion of biomass-derived syngas to alcohols and C2 oxygenates using supported Rh catalysts in a microchannel reactor, Catal. Today, 2007, 120(1), 90–95 CrossRef CAS.
- D. Jiang, Y. Ding and Z. Pan, et al., CO Hydrogenation to C2-oxygenates over Rh–Mn–Li/SiO2 Catalyst: Effects of Support Pretreatment with nC1–C5 Alcohols, Catal. Lett., 2008, 121(3–4), 241–246 CrossRef CAS.
- G. R. Jackson and D. Mahajan, Method for production of mixed alcohols from synthesis gas, US Pat., 6753353, 2001 Search PubMed.
- C. W. Jones, P. K. Agrawal and T. T. Nguyen, Catalyst compositions for converting syngas to produce higher alcohols, US Pat., Application 20130245328, 2017 Search PubMed.
- P. Liao, C. Zhang and L. Zhang, et al., Higher alcohol synthesis via syngas over CoMn catalysts derived from hydrotalcite-like precursors, Catal. Today, 2018, 311, 56–64 CrossRef CAS.
- T. Fu and Z. Li, Review of recent development in Co-based catalysts supported on carbon materials for Fischer–Tropsch synthesis, Chem. Eng. Sci., 2015, 135, 3–20 CrossRef CAS.
- J. Sun, L. Zhang and C. Ge, et al., Comparative study on the catalytic CO oxidation properties of CuO/CeO2 catalysts prepared by solid state and wet impregnation, Chin. J. Catal., 2014, 35(8), 1347–1358 CrossRef CAS.
- B. Da Won, M. H. Jeong and M. H. Kim, et al., Rh–Mn/tungsten carbides for direct synthesis of mixed alcohols from syngas: effects of tungsten carbide phases, Microporous Mesoporous Mater., 2018, 255, 44–52 CrossRef.
|
This journal is © The Royal Society of Chemistry 2021 |
Click here to see how this site uses Cookies. View our privacy policy here.