DOI:
10.1039/D0QM00436G
(Review Article)
Mater. Chem. Front., 2021,
5, 97-128
Rational design of electrospun nanofibrous materials for oil/water emulsion separation
Received
30th June 2020
, Accepted 26th August 2020
First published on 26th August 2020
Abstract
The frequent oil spill accidents and ever-increasing oily wastewater discharged from our daily life and industries greatly threaten the ecological system as well as human health and cause heavy economic loss. To address this problem, developing advanced separation materials towards efficient oil/water emulsion separation is a critical way and has currently risen as a research focus. Electrospun nanofibrous materials with tunable wettability, controllable pore structure, diverse dimensions, and good connectivity hold great promise for meeting the requirements of emulsion separation applications. Herein, we present a comprehensive overview on the recent research regarding the design and fabrication of electrospun nanofibrous materials with special wettability and optimized porous structure for emulsion separation. We firstly introduce the emulsion separation mechanism, followed by the design principles of nanofibrous filtration materials. We subsequently discuss the preparation of electrospun nanofibrous materials beginning with selective wettability tunability (i.e., hydrophobic–oleophilic, hydrophilic–oleophobic, and switchable properties) and porous structure optimization (i.e., 2D and 3D porous structures). Based on the dimensions, nanofibrous materials can be categorized into nanofibrous membranes and nanofibrous aerogels. For each type, representative studies will be highlighted, focusing on the relationship between the synergy of the selective wettability and porous structure and emulsion separation performance. Finally, the existing challenges and future perspectives in the burgeoning field are provided.
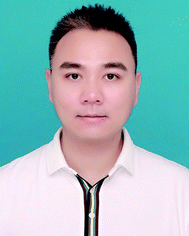
Jichao Zhang
| Jichao Zhang received his MS degree from the College of Textiles in Donghua University in 2015. He is now a PhD candidate in Prof. Bin Ding's group. His current research interests mainly focus on bio-inspired surfaces with special wettability, and nanofibrous oil/water separation materials. |
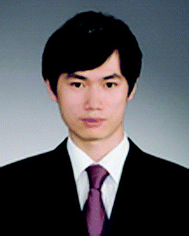
Yang Si
| Yang Si received his BS from Sichuan University, China in 2009. After that he earned his PhD degree from Donghua University, China in 2015. Currently, he is a Full Professor in the Innovation Center for Textile Science and Technology in Donghua University. His research mainly includes antibacterial bioprotective materials, water disinfection materials, and nanofibrous aerogels. |
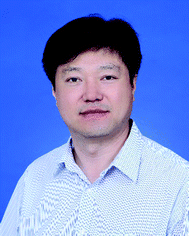
Bin Ding
| Bin Ding received his BS from Northeast Normal University, China, in 1998 and his MS from Chonbuk National University, Korea, in 2003. After that he earned his PhD degree from Keio University, Japan, in 2005. Currently he is a Full Professor in the College of Textiles in Donghua University and awarded as “Changjiang Scholar” by Ministry of Education, China. His research mainly focuses on oil/water separation materials, flexible ceramic nanofibers, waterproof and breathable materials, filtration materials, nanofibrous aerogels, etc. He has already published more than 300 SCI papers and has been authorized more than 50 patents. |
1. Introduction
1.1. Background
Frequent offshore oil production and marine transportation have caused serious leakage of oil into the ocean, which has not only brought about a disastrous impact on the ecosystem but led to enormous economic loss.1–5 For instance, the 2010 Gulf of Mexico oil blowout resulted in 4.9 million barrels of precious oil going into the sea and contaminated an area of 3200 km2.6–8 Besides, the increasing amount of oily wastewater released from our daily life and oil-related industries (e.g., textiles, leather, food, and metal finishing) has already become one kind of major pollutants aggravating the freshwater shortage.9–11 The environmental and economic concerns have emphasized the great need for technologies and materials for oil/water separation. Oil/water mixtures can be classified into three types according to the dispersed phase size: free oil/water mixtures (>150 μm), oil/water dispersions (20–150 μm), and oil/water emulsions (<20 μm).12 Free–floating and dispersed oil can be easily removed by absorbents. In contrast, separating emulsified oil/water mixtures has been confirmed to be the most tough and challenging because of the robust oil/water interface and adsorbed interface-active component.13,14 Traditional techniques including centrifuges, coalescers, sedimentation, and adsorption have limitations of time-consuming and complex operational processes, and are not applicable for oil/water emulsion separation.15 Recently, filtration technology has gained much attention for the separation of oil/water emulsions due to its easy operation, low energy cost, and cost-effectiveness.16–19 Unfortunately, most filtration materials, including phase inversion membranes,20–24 metal sintered materials,25 and porous substrate (metal mesh,26–28 textile,29 and sponge30)-based materials, are often limited by low permeation flux, poor oil/water selectivity or complicated fabrication processes.31–33 Therefore, it is of great importance to create advanced effective materials for oil/water emulsion separation.
1.2. Mechanisms of oil/water emulsion separation
An emulsified oil/water mixture is a colloidal dispersion, in which a tiny quantity (<10%) of liquid (e.g., water or oil) in the form of small droplets is suspended in an immiscible liquid (e.g., oil or water).9,34–36 In this binary mixture system, the droplet is known as the dispersed phase, and the other liquid is the continuous phase.37 Thus, there are two major tasks for filtration materials during separation, i.e., dispersed phase interception and continuous phase permeation.
1.2.1. Dispersed phase interception.
The removal of the dispersed phase from a oil/water emulsion is quite different from the filtration of rigid solid particles because emulsified droplets can deform and squeeze through pores less than their sizes.38 To stop the dispersed phase from passing through a porous material, the size exclusion effect of the porous material should function synergistically with the wettability.39,40 The wettability of a liquid on a porous material can be expressed by the liquid contact angle, which determines the intrusion pressure (Pi) of the liquid, the maximum pressure that the porous material can withstand without letting the liquid flow through.41 The intrusion pressure can be calculated by the Young–Laplace equation: |  | (1) |
where γL represents the surface tension of the liquid, θ is the intrinsic contact angle of the liquid on a flat surface, and rp is the pore radius. A porous material could repel a certain amount of liquid when the intrinsic contact angle of the given liquid is more than 90°. If the intrinsic contact angle is less than 90°, the liquid will permeate the material pores spontaneously. Thus, the separation of oil and water can depend on the intrusion pressure difference between the oil and water. More specifically, removing the oil from an oil/water mixture can be achieved by a filtration material with hydrophobicity and oleophilicity because of its opposite intrusion pressure for oil and water. A hydrophilic–oleophobic filtration material can be employed to remove water from an oil/water mixture.42 For the removal of emulsified droplets, the selectively wettable materials should also be endowed with a pore size (2rp) less than or comparable to the diameter of the emulsified droplets (2rd).39,43 It should be noticed that the pore size distribution also influences the interception capacity. Uniform pores with suitable size should be across the whole porous material. If there is a wide distribution of pore size, most of the droplets will firstly penetrate the larger pores (path of lower resistance), resulting in poor selectivity (Fig. 1e and f).
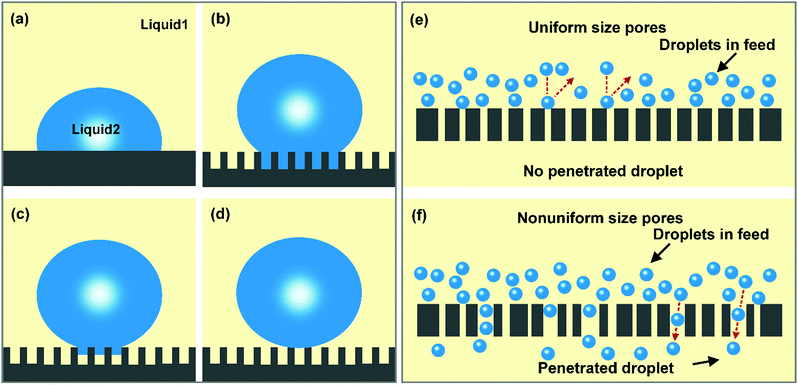 |
| Fig. 1 Schematics showing four underliquid wetting states: (a) underliquid Young's state, (b) underliquid Wenzel's state, (c) underliquid transitional state, and (d) underliquid Cassie's state. (e) With uniform pore size, it is possible to acquire entire interception by a porous material. (f) With nonuniform pores, the largest pore size determines the selectivity. | |
Notably, four wetting states (i.e., Young's state, Wenzel's state, the transitional state, and Cassie's state) describe a liquid on a solid surface, and demonstrate that the wettability is dependent on the chemical composition and surface morphology.44,45 The Young state relates the wettability of a liquid on an ideal smooth surface to the chemical composition. The Wenzel state introduces the effect of roughness into the wettability of a solid surface and puts forward that the rough surface could lead to an amplification of wetting and anti-wetting behaviors. Lyophilic materials will be more lyophilic with an increasing degree of roughness, while lyophobic materials will become more lyophobic when the roughness is enhanced. However, for some porous surfaces, it is difficult for the cavities to be wetted by a liquid and a large amount of air can be entrapped in them, thus giving a composite interface. In this state, the Cassie model is more applicable. Besides, a transitional state exists between the Wenzel state and the Cassie state, in which the liquid may partly intrude into the valleys of the surface rough structure. When separating oil/water emulsions using filtration materials with selective wettability, the separation process will be achieved on an oil–water–solid three-phase interface. For example, if a hydrophobic–oleophilic material is used for separating water-in-oil emulsions, the entire cavity between the microstructures will be wetted by the oil, resulting in a trapped oil layer underneath the water droplet. When treating emulsified oily water using a hydrophilic–oleophobic material, the air in the rough surface will be fully replaced with water. Hence, the underliquid wetting states (i.e., underliquid Young's state, underliquid Wenzel's state, underliquid transitional state, and underliquid Cassie's state) on solid surfaces could be more in line with the oil/water separation situation (Fig. 1a–d).46,47 Due to the different contact areas of the dispersed droplets and solid surface in these four states, the adhesion properties of dispersed droplets to solid surfaces differ sharply and decrease in the order: underliquid Young's state > underliquid Wenzel's state > underliquid transitional state > underliquid Cassie's state. Therefore, the adhesive forces between dispersed droplets and filtration material surfaces can be finely modulated by adjusting the degree of droplet penetration into the surface microstructures, which provides an effective way to improve the antifouling performance of filtration materials.
1.2.2. Continuous phase permeation.
A continuous phase flowing through a porous material can be considered as a viscous flow, which could be expressed by the Hagen–Poiseuille equation:48 |  | (2) |
where J is the permeation flux, ε is the porosity, ΔP is the driving pressure, μ is the liquid viscosity, d is the material thickness, and τ is the tortuosity. Based on the thickness dimension, porous filtration materials can have two basic forms: 2D membranes and 3D blocks. For either of them, an increase in pore size could promote the permeability of the continuous phase, but too large pores may lead to the decline of the separation efficiency. Meanwhile, a well-connected porous structure with high porosity allows the continuous phase to pass through the materials with a low flow resistance. Hence, an ideal emulsion separation material must (i) possess the opposite affinity to water and oil, (ii) possess a suitable pore size to make a good trade-off between selectivity and permeability, and (iii) have as large a porosity as possible.
1.3. Electrospinning and electrospun materials
Electrospinning is considered to be a variant of the electrostatic spraying process, in which a liquid droplet is electrified to form a jet, and then it undergoes vigorous whipping and splitting motion to generate nanoscale continuous fibers. After decades of development, electrospinning technology has been an effective and simple method in fabricating nanofibers with controllable chemical compositions and diverse fibrous structures.49 For example, electrospinning has been utilized to synthesize nanofibers from over 120 kinds of polymers with various surface energy.50–53 Organic/inorganic hybrid nanofibers can be obtained by loading additives into the polymeric spinning solution or combining with post-treatment. By combination with sol–gel chemistry, a wide variety of inorganic nanofibers have also been prepared. Besides, electrospinning holds powerful structure tunability that could tailor the nanofibrous structures from nanotexture on a single nanofiber, to porous structure among fibers, to macroscopic bulk structure (e.g., 1D yarn, 2D membranes, and 3D aerogels).54 Additionally, nanofibrous materials usually combine other outstanding advantages of excellent pore connectivity and high porosity.55 Therefore, the past several years have witnessed a booming expansion of research on the preparation of nanofibrous materials with selectively wettable surfaces (trending from fixed wettability to switchable/responsive wettability) and diverse pore structures (trending from 2D porous structure to 3D porous structure) for effective oil/water emulsion separation. Fig. 2 summarizes some important milestones that have been achieved in nanofibrous emulsion separation material systems.56–66
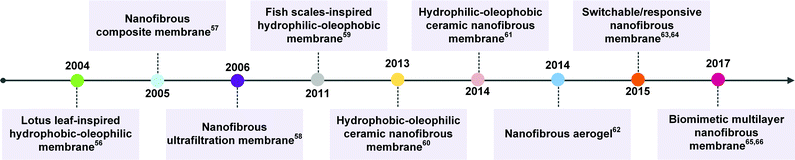 |
| Fig. 2 Timeline of some important milestones in the development of nanofibrous emulsion separation materials.56–66 | |
This review aims to present a systematic overview of the current developments of electrospun nanofibrous materials with selective wettability and optimized porous structure for oil/water emulsion separation (Fig. 3). First, we focus on the design and fabrication of selectively wettable nanofibrous materials, which mainly include the introduction of basic raw materials with appropriate surface energy and generic strategies to roughen the nanofiber surfaces. Then, we highlight some representative methods for regulating 2D and 3D porous structures by electrospinning. Based on the dimension, nanofibers can be assembled into separation materials with two basic forms: 2D membranes and 3D aerogels. The application of these two types of nanofibrous materials for emulsified oil purification and oily wastewater remediation is subsequently summarized with the associated advantages and disadvantages. To conclude, the existing challenges and future perspectives facing nanofibrous emulsion separation materials are also discussed.
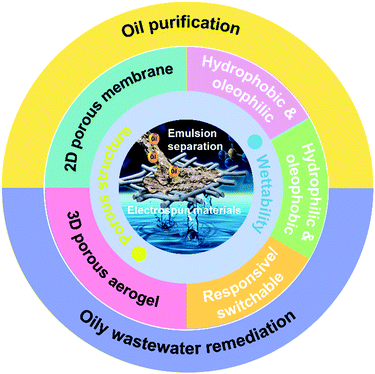 |
| Fig. 3 Electrospun nanofibrous materials for oil/water emulsion separation. The nanofibers could be of special wettabilities, such as hydrophobic and oleophilic, hydrophilic and oleophobic, and responsive/switchable, and could be well-tailored with 2D and 3D porous structures. | |
2. Fabricating nanofibrous materials with selective wettability surfaces
As is well-known, the combination of an appropriate chemical composition and surface roughness is crucial to the preparation of selectively wettable materials. Therefore, two steps, i.e., the selection of materials (electrospinnable polymers, additive agents and so on) with suitable surface energy for electrospinning, and the generation of hierarchical roughness on nanofibers, are involved. This section focuses on the summary and discussion of recently used raw materials for selectively wettable nanofibers, along with strategies to roughen the nanofiber surfaces.
2.1. Electrospinnable polymer materials
Polymers with appropriate surface energy and good spinnability can be used to fabricate selectively wettable nanofibrous materials by a simple direct electrospinning technique. The spinnable polymer requires a suitable molecular weight and can be completely dissolved in some solvents. Generally, the electrospinning of a solution of spinnable low-surface-energy polymers could achieve nanofibrous materials with a hydrophobic–oleophilic property. Also, polymers with high surface energy are selected for fabricating hydrophilic–oleophobic nanofibrous materials.
2.1.1. Hydrophobic–oleophilic polymers.
Polymers with low-surface-energy groups, such as –CH2, –CH3, –CF2, –CF2H, and –CF3, are the preferential materials in the fabrication of hydrophobic–oleophilic nanofibers by direct electrospinning. Hence, the polymers can be categorized into two classes: non-fluorinated and fluorinated polymers.
Polystyrene (PS), a synthetic aromatic polymer with low-surface-energy owing to its phenyl group, has been widely used for the preparation of hydrophobic–oleophilic nanofibers by direct electrospinning.67–76 However, the major problem associated with PS nanofibrous materials is their weak mechanical strength and poor integrity due to the brittle nature of the fibers. To overcome this issue, some rubber-like polymer monomers (e.g., butyl acrylate and dimethylsiloxane) were incorporated into PS systems, and the nanofibers derived from synthesized copolymer poly(styrene-co-butyl acrylate) (PS-co-PBA) and poly(styrene-co-dimethylsiloxane) (PS-co-PDMS) showed good hydrophobicity (water contact angles (WCAs) >130° and oil contact angles (OCAs) of about 0°) and excellent flexibility as well as good mechanical integrity.77–79 Aromatic polyimide (PI) is a step ladder polymer with good hydrophobicity–oleophilicity, and it has been widely used in the filtration field due to the good chemical resistance, superior thermo-oxidative stability, and excellent mechanical properties. However, the insoluble nature in most organic solvents hinders its direct electrospinning. An effective way is the introduction of flexible linkages (e.g., siloxane) into the PI macromolecules to improve its solubility.80 For example, Tian et al. copolymerized a flexible linkage, 1,3-bis(3-aminopropyl)tetramethyldisiloxane, into the PI skeletal chain, and then they used dimethylformamide (DMF) as a solvent for direct electrospinning.81 The resultant PI nanofibers demonstrated hydrophobic and superoleophilic properties with an OCA of 0.9°. The intriguing wettability of PI nanofibers can remain under harsh conditions, such as sodium chloride (NaCl), hydrochloric acid (HCl), sodium hydroxide (NaOH), methylene blue, and sodium dodecylbenzenesulfonate solutions.82 Notably, the combination of electrospinning of a poly(amic acid) (PI precursor) solution and thermal imidization provides an indirect pathway to prepare PI nanofibers.83 Besides, aromatic polymers for the fabrication of hydrophobic–oleophilic nanofibers by direct electrospinning also include polysulfone (PSF),84,85 polyetherimide,86 poly(butylene terephthalate) (PBT),87 polyurethane (PU),88 and polyetherimide poly(disperse orange 3) (PDO 3).66 Some aliphatic polymers, such as syndiotactic polypropylene (SPP),89,90 poly(methyl methacrylate) (PMMA),91,92 poly(vinyl chloride) (PVC),73 and poly(vinyl butyral) (PVB),93 can also be directly electrospun into hydrophobic–oleophilic nanofibers with WCAs of above 100°.
Recently, some low-surface energy biodegradable polymers, including biodegradable polyesters (e.g., polylactide (PLA), poly(glycolic acid) (PGA), poly(ε-caprolactone) (PCL), poly(lactic acid-co-glycolic acid) (PLGA), and poly(hydroxybutyrate) (PHB)) and cellulose derivatives (e.g., cellulose acetate (CA) and ethylcellulose), have attracted a great deal of attention for fabricating hydrophobic–oleophilic surfaces because of their sustainability and environmental friendliness.94–104 For example, Zhang et al. fabricated PLA nanofibers by electrospinning a solution of PLA in a DMF/dichloromethane mixture, and the resultant electrospun PLA products showed a good hydrophobic–oleophilic property with a WCA of 133° and an OCA of 0°.100 As another example, Ma et al. electrospun nanofibers of CA from a mixed solvent of dimethylacetamide (DMAc) and acetone.105 Due to the acetyl groups on the glucose rings, the resultant CA nanofibrous membrane showed a hydrophobic property with a WCA of 124°.
Apart from non-fluorinated polymers, fluorocarbon-based polymers with multiple carbon–fluorine bonds have also been explored to fabricate hydrophobic nanofibrous materials. Derived from the high electronegativity of fluorine atoms and the high bond dissociation energy of the C–F bond, fluoropolymers usually possess excellent physicochemical stability. Polyvinylidene fluoride (PVDF)106–109 and poly(vinylidene fluoride-co-hexafluoropropylene) (PVDF–HFP)110 are the most often used fluoropolymers for the preparation of hydrophobic–oleophilic nanofibers. The obtained electrospun products feature remarkable properties such as excellent chemical resistance, high mechanical strength, and good thermal stability. Notably, polytetrafluoroethylene (PTFE) as an extremely chemically stable polymer is attracting vigorous attention in the preparation of porous filtration membranes, and the PTFE membrane can maintain its surface morphology and chemical composition in harsh conditions. However, the outstanding chemical stability of PTFE also presents a major challenge in its direct electrospinning. Fortunately, Qing and co-workers reported a robust method for the fabrication of PTFE nanofibers.111 Briefly, PTFE nanoparticles (NPs) were dispersed in a carrier polymer poly(vinyl alcohol) (PVA) aqueous solution for direct electrospinning. Then the resultant PVA/PTFE NP nanofibers were sintered in air under a proper temperature to decompose PVA and weld PTFE NPs into continuous nanofibers. The resultant electrospun PTFE nanofibers exhibited hydrophobicity and oleophilicity with a WCA about 150° and an OCA of 0°.
2.1.2. Hydrophilic–oleophobic polymers.
To fabricate nanofibrous filtration materials for only allowing water to flow through freely, a simple method is to directly electrospin polymers with a hydrophilic–oleophobic property. However, few researchers have successfully prepared hydrophilic–oleophobic nanofibers; in theory, oil-repellent surfaces combining extremely low surface energy usually repel water, because the water surface tension is always higher than that of oils.112 Inspired by fish scales that enable the fish to live in oil-contaminated water,46 researchers have recently proposed a biomimetic way to achieve nanofibrous membranes with hydrophilicity–oleophobicity, i.e., hydrophilicity–underwater oleophobicity, by utilization of high-surface-energy polymers.40,113,114 Generally, these polymers possess plenty of polar groups, such as hydroxyl, carboxyl, amino, acylamino, and nitrile.
To date, lots of synthetic polymers have been successfully electrospun for the preparation of hydrophilic–underwater oleophobic nanofibers. Polyamide (PA) and polyacrylonitrile (PAN) are the two most attractive polymers for the preparation of hydrophilic–underwater oleophobic nanofibrous materials because of their high-surface-energy and water insolubility. For instance, Lin et al. electrospun nanofibers of a semi-aromatic PA, poly(trimethyl hexamethylene terephthalamide) (PA6(3)T).115 Because of the numerous amide groups, the resultant PA6(3)T nanofibers were hydrophilic in air with a WCA of 63.9° and underwater oleophobic with an underwater oil contact angle (UWOCA) of 115.4°. The powerful hydrogen bonds between polymer macromolecules endowed the PA6(3)T nanofibers with excellent structure stability in water. In another study, Liang et al. fabricated hydrophilic PAN nanofibers with a WCA of about 18° by electrospinning.116 The abundant hydrogen bonds and dipole–dipole interactions between polymer molecules rendered the PAN nanofibers good structural stability in an aquatic environment. In other work, researchers further improved the hydrophilicity of the PAN nanofibers to superhydrophilicity by post-treatment, such as hydrolysis treatment and heat treatment. For example, Zhang et al. increased the hydrophilicity of PAN nanofibers by basic hydrolysis treatment after electrospinning.117 Because plentiful amounts of hydrophilic groups (hydroxyl, carbonyl, and amine groups) were generated on the fiber surfaces after nitrile reacted with NaOH, the PAN nanofibers changed from hydrophilic to superhydrophilic. Lim et al. demonstrated the thermally-induced hydrophilic enhancement of PAN nanofibers.118 The PAN nanofibers were heated in air at 200 °C to convert the abundant nitrile groups into amide and carboxyl groups, leading to highly hydrophilic PAN nanofibers with a WCA of 0°.
From a practical point of view, the nanofibers derived from water-soluble polymers, including PVA, poly(vinyl pyrrolidone) (PVP), poly(acrylic acid) (PAA), poly(methacrylic acid) (PMAA), poly(ethylene oxide) (PEO), polyacrylamide (PAM), poly(ethylene glycol) (PEG), poly(ethylene imine), and zwitterionic polymers, could not be used for oil/water separation. An effective method to overcome this issue is to crosslink the water-soluble polymers after electrospinning. For example, Zhu and co-workers electrospun PVA/PAA aqueous solution, followed by thermal crosslinking of the composite nanofibers.119 Because a significant number of ester linkages were formed between hydroxyl groups of PVA and carboxyl groups of PAA, the obtained PVA/PAA nanofibers possessed hydrophilicity and good underwater durability. Based on the same principle, Fan et al. used glutaraldehyde as a crosslinker to stabilize the hydrophilic PVA layer, and the resultant membrane showed a promising hydrophilic—underwater oleophobic property in a complex environment (e.g., acids, alkalis, and salts).120
2.1.3. Switchable wettability polymers.
Recently, polymers with switchable wettability that are able to oscillate between two extreme wetting states (i.e., hydrophobic–oleophilic and hydrophilic–oleophobic) have drawn a great deal of attention owing to their great potential of realizing on-demand oil/water separation in response to external stimuli, such as heat,121–126 pH,63,92,127 gas,64 light,128,129 and even multiple stimuli.130,131 It is worth mentioning that the wettability varies in a small range on a polymer flat membrane, and the inherent roughness of electrospun materials can greatly enlarge the transition range of surface wettability, which is beneficial for oil/water separation.
Poly(N-isopropylacrylamide) (PNIPAAm) is an extensively studied thermo-responsive polymer, but suffers from easy solubility in water (Fig. 4a). Recently, a PNIPAAm segment has been often introduced into a hydrophobic polymer system (e.g., PMMA and PS) to improve the underwater durability.132 For instance, Li and co-workers fabricated temperature-sensitive nanofibers by the direct electrospinning of copolymer PMMA-b-PNIPAAm solution.125 The PMMA in the glassy state could endow the resultant nanofibers with good stability underwater, and PNIPAM rendered the nanofibers thermo-responsive wettability. Briefly, PNIPAM will be swollen in water below the lower critical solution temperature (LCST), endowing PMMA-b-PNIPAAM nanofibers with hydrophilicity with a WCA of 0° and underwater superoleophobicity with an OCA of 153°, while the PNIPAAm could collapse above the LCST, resulting in hydrophobicity with a WCA of 130° and underwater oleophilicity with an OCA of 37° (Fig. 4b and c). Besides, the synthesized PMMA-b-PNIPAAM nanofibers could reversibly switch between opposite wetting states by heating and cooling.
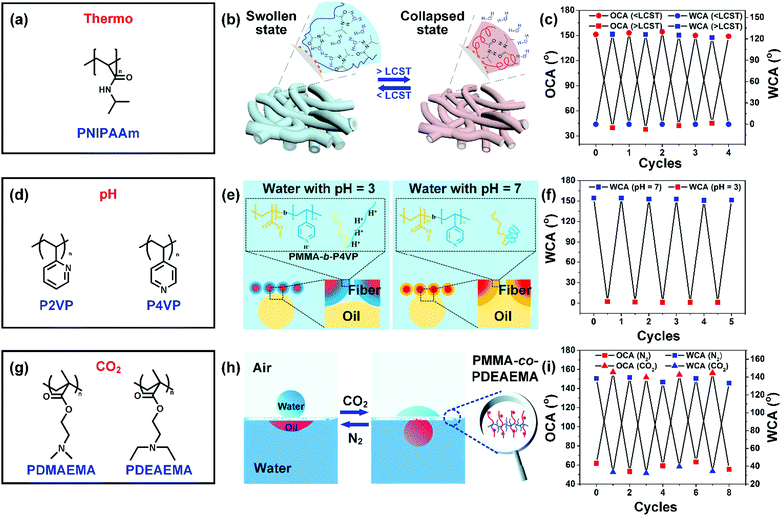 |
| Fig. 4 (a) Polymer with thermo-responsiveness. (b) Diagram showing its thermo-responsive mechanism. Reproduced with permission from ref. 126. Copyright 2018, American Chemical Society. (c) The PMMA-b-PNIPAAm nanofibers showing hydrophilicity and underwater oleophobicity below the LCST, and showing hydrophobicity and underwater oleophilicity above the LCST. Reproduced with permission from ref. 125. Copyright 2015, Royal Society of Chemistry. (d) A summary of common molecules with a pH-responsive property. (e) Schematic explanation about the pH-responsiveness of PMMA-b-P4VP nanofibers. (f) pH-triggered reversible water wettability transition of PMMA-b-P4VP nanofibers. Reproduced with permission from ref. 63. Copyright 2015, American Chemical Society. (g) Some common polymers that are sensitive to CO2. (h) Schematic showing the CO2-responsiveness of PMMA-co-PDEAEMA nanofibers. (i) The PMMA-co-PDEAEMA nanofibers exhibiting gas-switchable wettability. Reproduced with permission from ref. 64. Copyright 2015, Wiley-VCH. | |
Polymers with carboxyl or pyridine groups, such as poly(2-vinylpyridine) (P2VP), and poly(4-vinylpyridine) (P4VP), generally show a pH-responsive switchable wetting property because of the pH-triggered configurational changes of molecules (Fig. 4d). Li and co-workers synthesized a PMMA-b-P4VP copolymer, followed by electrospinning of it into nanofibers.63 The protonation and deprotonation of pyridine groups induced by the solution pH values (e.g., 3 or 7) could regulate the chain conformation (e.g. extended or collapsed) of the P4VP segments. The electrostatic repulsion derived from protonated pyridyl groups could make the P4VP segment extend to water, leading to hydrophilic–underwater oleophobic wetting behavior. The collapsed conformation of the P4VP segment enables the PMMA segments to control the access of water, resulting in a hydrophobic–oleophilic property (Fig. 4e). The intriguing switchable wettability can be reversible for 5 cycles in response to the solution pH values (Fig. 4f).
Gas triggers featuring easy addition or removal in large scale operation have evoked much attention in industrial applications. The gas can be CO2, NH3, O2, and H2. CO2 as an inexpensive, non-toxic, and non-flammable gas has become the most widely used gas trigger. CO2-switchable polymers usually contain tertiary amine groups, and poly(N,N-dimethylaminoethyl methacrylate) (PDMAEMA) and poly(N,N-diethylaminoethyl methacrylate) (PDEAEMA) are the most utilized polymers due to their commercial availability. For example, Che and co-workers synthesized a PMMA-co-PDEAEMA copolymer by a radical copolymerization reaction, and then it was electrospun into continuous nanofibers (Fig. 4g).64 The resultant PMMA-co-PDEAEMA nanofibers could switch the oil/water wettability by utilizing CO2 as the trigger because of the protonation and deprotonation effects of amine groups with CO2 and N2 (Fig. 4h). The protonated macromolecular chains derived from the interaction of tertiary amine groups and CO2 in water displayed a stretched conformation, leading to hydrophilicity–underwater oleophobicity for the nanofibers. Once the CO2 was completely removed, the PMMA-co-PDEAEMA molecules recovered to their hydrophobic–oleophilic aggregate state. The nanofibers could reversibly switch between the two opposite wetting states by alternating CO2 and N2 stimulation (Fig. 4i).
2.2. Surface modification agents
As mentioned above, nanofibrous materials with oil/water selective wettability can be obtained by the selection of appropriate spinnable polymers for direct electrospinning. However, the limited types of these polymers would seriously restrict the diversity of chemical compositions and hinder further wettability improvement. Electrospinning of a blend of a spinnable host polymer and non-spinnable additives with desirable surface energy or loading additives on host polymer fiber surfaces by post-treatment will greatly widen the selection range of materials, representing an effective way to address this issue. In this section, we will summarize the commonly utilized non-spinnable agents for wettability tunability.
2.2.1. Hydrophobic–oleophilic agents.
(1) Organosilicons.
The common organosilicons for hydrophobic–oleophilic surfaces mainly contain polysiloxanes and organosilanes. Polydimethylsiloxane (PDMS) is a commonly used polysiloxanes with low-surface-energy to fabricate hydrophobic surfaces because of its outstanding chemical stability and good anti-abrasive property.133 For example, Mi et al. deposited a layer of PDMS on cobalt-doped SiO2 nanofibers.134 Compared with the pristine hydrophilic SiO2 nanofibers, the resultant SiO2/PDMS nanofibers showed robust hydrophobicity with a WCA of about 150°. Interestingly, the hydrophobic property can be well maintained even in liquid nitrogen and a hot environment of 200 °C (Fig. 5a). As another example, a layer of PDMS was well anchored on the PAN nanofiber surface by blade coating and a subsequent polymerization process. The resultant PAN/PDMS nanofibers showed hydrophobic surfaces with a WCA of 141°. Besides PDMS coatings, several other kinds of polysiloxanes have also been employed to develop hydrophobic nanofibers, such as amino-silicone oil (ASO) and polymethylhydrosiloxane (PMHS). For example, Sheng et al. prepared hydrophobic electrospun PAN nanofibers by blade coating with ASO.135 The wettability of the PAN nanofibers was transformed from hydrophilicity to hydrophobicity with a WCA of 140°. In another study, Zhu et al. directly anchored PMHS onto PU nanofibers, and the WCA significantly increased from 108.8° to 130.2°.136
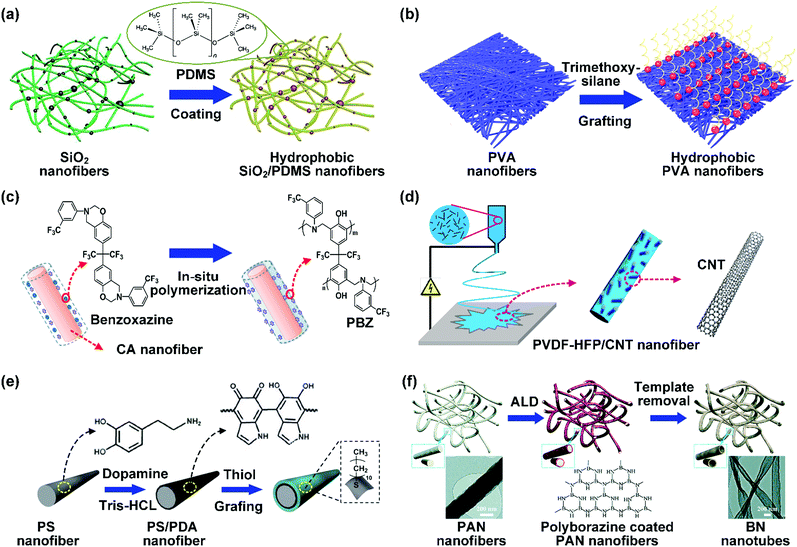 |
| Fig. 5 (a) SiO2 nanofibrous materials modified with PDMS. Reproduced with permission from ref. 134. Copyright 2018, Elsevier. (b) Hydrophobization of PVA nanofibers by silane grafting. Reproduced with permission from ref. 137. Copyright 2015, American Chemical Society. (c) CA nanofiber modified with F-PBZ by in situ polymerization. Reproduced with permission from ref. 138. Copyright 2012, Royal Society of Chemistry. (d) Tailoring the wettability of PVDF–HFP nanofibers by CNTs. Reproduced with permission from ref. 139. Copyright 2016, Elsevier. (e) Schematic showing the modification of PS nanofibers by PDA and thiol. Reproduced with permission from ref. 140. Copyright 2012, Royal Society of Chemistry. (f) Synthetic procedures for the preparation of BN nanotube nanofibers. Reproduced with permission from ref. 141. Copyright 2017, Royal Society of Chemistry. | |
Polysiloxanes could be partly filled into the pores among nanofibers other than only enwrapping the fiber surface during the modification process, resulting in the deterioration of the pore connectivity. Organosilanes as small molecules are grafted on the fiber surface to generate a hydrophobic–oleopilic functional layer, thereby having no effect on the porous structure, but changing the wetting behaviors. Up to now, a series of organosilanes (e.g., methoxysilane, ethoxysilane, and chlorosilane) has been utilized for improving the surface hydrophobic–oleophilic property of nanofibers. The most commonly used organosilanes for hydrophobic–oleophilic modification are summarized in Table 1. It is worth mentioning that the increase of the length of the aliphatic chain could enhance the surface hydrophobicity. For example, Wang et al. prepared hydrophobic–oleophilic TiO2 nanofibers by grafting hexyltrichlorosilane (C6) and trichlorooctadecylsilane (C18) monolayers respectively.142 The morphology of the treated TiO2 nanofibers was not changed, and the wettability changed from hydrophilicity to hydrophobicity–oleophilicity. Due to the longer aliphatic chain of trichlorooctadecylsilane, the C18–TiO2 nanofibers showed a WCA of 105° higher than that of the C6–TiO2 nanofibers (95°). Besides, the replacement of the hydrogen atoms by fluorine atoms in the aliphatic chain could also enhance the hydrophobicity, but the excessive density of fluoroalkylsilanes on the fiber surfaces may lead to oleophobicity. For instance, 1H,1H,2H,2H-perfluorododecyltrichlorosilane (C12F21)-grafted TiO2 nanofibers showed a higher WCA than that of TiO2 nanofibers with a dodecyltrichlorosilane (C12) monolayer.142 Interestingly, Xu et al. improved the hydrophobicity of crosslinked PVA nanofibers by assembling a layer of 1H,1H,2H,2H-perfluorodecyltrimethoxysilane (C10F17) through a condensation reaction between hydroxyl groups of PVA and Si–O alkyl groups of organosilanes (Fig. 5b).137 The WCA of the modified PVA nanofibers increased by 30°, achieving a promising superhydrophobic–oleophilic property. However, the C10F17–TiO2 nanofibers prepared by Wang and co-workers were lyophobic to both water and oil.131 The reason may be the higher areal density of –CF3 groups on TiO2 nanofibers than that of the crosslinked PVA nanofibers.
Table 1 Common organosilanes used to improve the hydrophobicity–oleophilicity of nanofibrous surfaces
Organosilanes |
WCA |
OCA |
Chemical structures |
Ref. |
1H,1H,2H,2H-Perfluorodecyltrimethoxysilane |
148–160° |
0–8° |
|
137 and 143
|
Hexadecyltrimethoxysilane |
>140° |
— |
|
144
|
1H,1H,2H,2H-Perfluorooctyltriethoxysilane |
139–153° |
0° |
|
145–150
|
Vinyltrimethoxysilane |
>145° |
— |
|
151
|
Methyltriethoxysilane |
>150° |
0° |
|
152
|
Octyltriethoxysilane |
>150° |
— |
|
151
|
Vinyltriethoxysilane |
>135° |
— |
|
151
|
Methyltrichlorosilane |
150.4° |
0° |
|
153
|
Hexyltrichlorosilane |
∼140° |
0° |
|
142
|
Dodecyltrichlorosilane |
∼141° |
0° |
|
142
|
Hexadecyltrichorosilane |
∼143° |
0° |
|
142
|
Octadecyltrichlorosilane |
144.7–163.1° |
0° |
|
142, 154 and 155
|
(2) Polymers.
Commonly used polymers for hydrophobic–oleophilic modification mainly include polymers with long alkyl chains and fluorinated polymers. For example, Kaplan et al. synthesized novel poly(lactic acid-co-glycerol monostearate) (PLA–PGC18) copolymers with long aliphatic side chains (i.e., stearic acid), and then added them into PLA solution for electrospinning.156 During the fiber formation process, the low-surface-energy polymer PLA–PGC18 held more mobility to migrate to the surface, while PLA tends to remain at the core. As a result, the synthesized PLA/PLA–PGC18 nanofibers exhibited a significant increase in hydrophobicity with a WCA of about 150° higher than pure PLGA nanofibers with a WCA of 110°. Polymers with active groups can be used as coating agents to improve the hydrophobicity of nanofibers. For example, Zhao et al. produced highly hydrophobic CA electrospun nanofibers by grafting a layer of ECO, a hyperbranched polymer with long chains of hydrocarbons, on fiber surfaces.157 The blocked isocyanate crosslinkers were firstly anchored onto the CA nanofiber surface as an interlayer, and then ECO covalently reacted with them by heat treatment. Benefiting from the hydrocarbon chains of ECO, the pristine hydrophilic CA nanofibers exhibited high hydrophobicity with a WCA of 132.2°.
Thermosetting polymers with 3D crosslinked networks are also efficient for switching the wettability of nanofibers to hydrophobicity–oleophilicity by in situ polymerization. For example, fluorinated polybenzoxazine (PBZ) with low surface energy and good chemical resistance has been widely used to render nanofibers stable hydrophobic–oleophilicity.158 Shang et al. prepared a crosslinked PBZ functional layer on CA nanofibers by in situ polymerization (Fig. 5c).138 Briefly, they firstly dipped the CA nanofibers into an acetone solution of a trifunctional benzoxazine monomer. After subsequent heat treatment, benzoxazine was polymerized into PBZ and formed a Mannich bridge crosslinked structure. The as-prepared CA nanofibers showed a remarkable transition from hydrophilicity to hydrophobicity with a WCA of 136°.
(3) Carbon materials.
Carbon materials have drawn tremendous attention in the fabrication of hydrophobic–oleophilic surfaces due to their low surface energy, good chemical inertness, and excellent mechanical stability. In the past decades, carbon has been extended from conventional charcoal and graphite to nanostructured forms (e.g., carbon nanotubes (CNTs),139,159,160 graphene nanoplatelets (GNPs),161 carbon black (CB),162 and carbon soot163,164). CNTs are a typical 1D carbon material with a hollow cylindrical structure. Shon and co-workers demonstrated the preparation of PVDF–HFP/CNT composite nanofibers by blend electrospinning (Fig. 5d).139 The CNTs were dispersed in a well-aligned fashion on/inside the PVDF–HFP nanofibers and the WCA of the resultant nanofibers increased from 149° to 158.5° as the CNT concentration increased to 5 wt%. GNPs as a 2D nanomaterial possess nanoscale thickness and diameter ranging from submicron to micron. Tijing et al. utilized GNPs to modify PVDF–HFP nanofibers by blend electrospinning.161 Due to the hydrophobic nature of GNPs, the WCA of the PVDF–HFP/GNP nanofibers exhibited a value of 163°, which was higher than that of pristine PVDF–HFP nanofibers (142°). Carbon soot is a product from the combustion of carbon-based materials and possesses extremely high hydrophobicity. It was found that the WCA was about 166° on the surface of carbon soot film. Compared with other nanostructured carbon, carbon soot is a cheap and easily gained material. Recently, it has been widely used as a hydrophobic additive for the wettability regulation of nanofibers. For example, Lei et al. incorporated candle soot into PVDF nanofibers by electrospinning PVDF solution dispersed with soot particles.164 The obtained PVDF/candle soot nanofibers achieved an improved hydrophobic property with a high WCA of 162°.
(4) Others.
The recently reported low-surface-energy agents also involve some organic small molecule compounds (thiols, aliphatic acids, and surfactants) which consist of a long hydrophobic chain ending with active groups, as summarized in Table 2. For example, Li et al. uniformly deposited a polydopamine (PDA) active layer on PS nanofibers, and then the resultant PDA-coated PS nanofibers were directly used as a platform to be firmly grafted with undecanethiol by a Michael reaction.140 Consequently, the resultant nanofibers showed promising hydrophobicity with a WCA of 136° (Fig. 5e). Similarly, Almasian et al. firstly functionalized PAN nanofibers by coating with PDA, and then a layer of nonylphenol ethoxylate nonionic surfactant was grafted onto the nanofiber surfaces.165 The resultant nanofibers exhibited a superhydrophobic property with a WCA of above 150°.
Table 2 Common surfactants, thiols, and aliphatic acids used to produce hydrophobic–oleophilic nanofibrous surfaces
Types |
Agents |
WCA |
OCA |
Ref. |
Thiols |
Undecanethiol |
136° |
0° |
140
|
Hexadecylthiol |
>146° |
0° |
166 and 167
|
1H,1H,2H,2H-Perfluorodecanethiol |
∼155° |
∼0° |
168
|
Surfactants |
Nonylphenol ethoxylate |
>150° |
0° |
165
|
Aliphatic acids |
Cyclohexanecarboxylic acid |
>150° |
0° |
169
|
Boron nitride (BN) is an important hydrophobic nitride ceramic and possesses four crystal structures. Hexagonal BN, analogous to graphite with a layered structure, has been a promising candidate for hydrophobicity tunability due to the good thermal and chemical stability. For example, Hao et al. used PAN nanofibers as templates to create a thin layer of hexagonal BN on them by atomic layer deposition (ALD) of pre-ceramic polyborazine. The resultant PAN/polyborazine nanofibers were annealed under an Ar flow to transform the precursors into dense BN nanotubes forming into PAN/BN hybrid nanofibers, and then heated under NH3 to remove PAN, leading to formation of BN nanotube nanofibers (Fig. 5f).141 The authors demonstrated that the obtained BN nanofibers exhibited a superior water repellent property with a WCA of about 150° and high oleophilicity with an OCA of 0°. The PAN/BN hybrid nanofibrous membrane would be expected to be hydrophobic–oleophilic.
2.2.2. Hydrophilic–oleophobic agents.
(1) Amphiphilic copolymers.
Amphiphilic copolymers consisting of hydrophilic polymer segments (e.g., zwitterionic polymers, PEO, poly((2-methacryloyloxy)ethylphosphorylcholine), and poly(methoxy poly(ethylene oxide)methacrylate)) and hydrophobic segments (e.g., PMMA, PLA, PCL, and PS) have been extensively used to increase the hydrophilicity of nanofiber surfaces. Because of their amphiphilic characteristic, these polymers are usually used to hydrophilize hydrophobic host polymers (e.g., PVDF, PHB, SEBS, PLA, and PCL) by blend electrospinning.98,170–173 The idea is that the low-surface-energy hydrophobic segments could drive the small-molecule copolymer out-migration to the fiber–air interface and then act as anchors to fix on the host polymers, while the hydrophilic segments are useful for improving the hydrophilicity.174–177
For example, Govinna et al. introduced two kinds of zwitterionic polymer-based copolymers, i.e., poly((methyl methacrylate)-ran-sulfobetaine methacrylate) (P(MMA-ran-SBMA)) and poly((methyl methacrylate)-ran-sulfobetaine-2-vinylpyridine) (P(MMA-ran-SB2VP)), into PVDF nanofibers by blend electrospinning.170 During the fiber formation process, the smaller molecular weight and amphiphilic character of the copolymers made them easily accumulate on the fiber surface. Meanwhile, the zwitterionic polymer segments extended upon contact with the aqueous medium, while the PMMA segments anchored in the PVDF matrix to prevent the copolymer from leaching out in water. As a result, the as-prepared PVDF/PMMA-r-SBMA and PVDF/PMMA-r-SB2VP nanofibers both showed significantly enhanced surface hydrophilicity. Triblock copolymers were also investigated to increase the hydrophilicity of the nanofibers. For example, Kurusu et al. incorporated a triblock copolymer PEO–PPO–PEO (F127) into hydrophobic styrene-b-ethylenebutylene-b-styrene (SEBS) nanofibers to regulate the hydrophilicity by blend electrospinning.171 During the electrospinning process, F127 molecules could migrate and aggregate onto the nanofiber surface for its incompatible property with the SEBS matrix. As a result, PPO segments anchored the F127 molecular chain on the hydrophobic SEBS matrix and brush-like PEO segments extended to contact with water. This ternary copolymer changed the wettability of SEBS nanofibers from hydrophobicity with a WCA of 139° to superhydrophilicity with fast water spreading as well as a WCA below 5° (Fig. 6a).
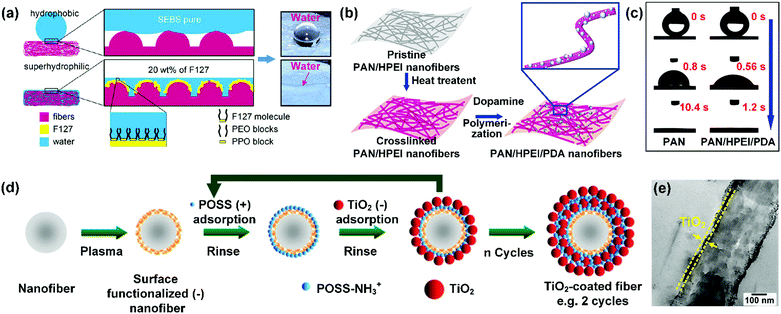 |
| Fig. 6 (a) The hydrophilization of hydrophobic SEBS nanofibers by modification with F127. Reproduced with permission from ref. 171. Copyright 2015, American Chemical Society. (b) PAN/HPEI nanofibers modified with PDA. (c) The enhanced hydrophilicity of PAN/HPEI nanofibers by coating with PDA. Reproduced with permission from ref. 178. Copyright 2018, Elsevier. (d) Electrospun nanofibers modified by TiO2 through the LBL assembly method. (e) TEM image showing a layer of TiO2 deposited on the PSEI fiber surface. Reproduced with permission from ref. 179. Copyright 2009, Wiley-VCH. | |
(2) Natural polymers.
Natural polymers obtained from living organisms (wood, crustacean shells and so on) usually possess lots of oxygen-rich hydrocarbon hydrophilic groups and intrinsic underwater durability. Besides, these polymers also feature promising biocompatibility and non-toxicity. However, the direct electrospinning of natural polymers is seriously limited by low productivity and poor fiberizability.
Natural polymers have been blended with synthetic polymers for electrospinning, leading to the development of natural polymer-based hydrophilic nanofibers. Chitosan is a deacetylated form of chitin with amino and hydroxyl groups. Blend electrospinning of chitosan has been used to improve the hydrophilicity of many synthetic polymer nanofibers, such as PA66,180 PLA,181 and PLGA182 nanofibers. Silk is a protein polymer with amino or hydroxyl groups at the side chains. Guo et al. utilized silk to hydrophilize PBT nanofibers by blend electrospinning.87 In comparison to pristine PBT nanofibers with a WCA of about 125°, the introduction of silk significantly increased the hydrophilicity, leading to a WCA of 18° for the PBT/silk nanofibers.
Another way of using natural polymers to promote nanofiber hydrophilicity is to introduce natural polymers on the fiber surface by a coating strategy. Dopamine is a neurotransmitter released by the human brain for carrying signals between cells. It contains lots of polar groups (e.g., catechol and ethylamino groups), and possesses a similar molecular structure to dihydroxyphenylalanine derived from mussel foot proteins, which provides robust adhesion ability of mussels on marine substrates. Inspired by the phenomena, a growing number of researchers have developed PDA coating layers for promoting the hydrophilicity of nanofibers. For instance, Wang and co-workers used dopamine as the monomer to fabricate PDA-coated nanofibers. By simple immersion of PAN/hyperbranched polyethyleneimine (HPEI) nanofibers into an aqueous solution of dopamine hydrochloride and Tris-buffer, thin PDA shells were synthesized on the fibers. The as-prepared PAN/HPEI/PDA nanofibers showed superhydrophilicity with a water spreading time of less than 1.2 s (Fig. 6b and c).178 Based on the same principle, Mosinger et al. prepared hydrophilic electrospun PS nanofibers. After they coated a layer of PDA on the PS nanofibers through in situ polymerization, the hydrophobic PS nanofiber surfaces (a WCA of about 130°) were changed into highly hydrophilic surfaces with a WCA below 5°.183 Polysaccharides are the most abundant polymers in nature, which have gained lots of attention in filtration and biomedical applications. Recently, polysaccharide nanocrystals have been incorporated onto electrospun nanofiber surfaces to tailor the surface energy. Here, the electrospun nanofibers employed can be PVDF–HFP,184 CA,185 and PAN186 nanofibers. By virtue of the polysaccharide modification, the pristine nanofibers demonstrated a great improvement of hydrophilicity with a fast water spreading time.
(3) Oxide ceramics.
Oxide ceramics are materials that consist of metal or nonmetal elements and exist as compounds of oxides. The strong ionic and covalent bonding render oxide ceramics excellent resistance to high temperatures and various chemicals. Recently, they have been widely used to hydrophilize nanofibers.
Direct utilization of nanostructured oxide ceramics by blend electrospinning is a common method to promote the hydrophilicity of nanofibers. For example, tourmaline as a hydrophilic crystalline material possesses lots of silanol groups. Tijing et al. hydrophilized PU nanofibers by incorporation of tourmaline by blend electrospinning.187 In comparison to the pristine PU nanofibers with a WCA of 125.2°, the PU/tourmaline nanofibers showed a WCA of 13° as the concentration of tourmaline increased to 5 wt%. Similar results were reported for electrospun nanocomposites of PAN with SiO2. The hydroxyl groups on SiO2 effectively influence the interactions between the PAN/SiO2 nanofibers and water, leading a faster spreading rate than PAN nanofibers.188 Other oxide ceramics, such as TiO2, ZnO, ZrO2, and hydroxyapatite have also been electrospun in nanofibers to improve the hydrophilicity. However, the blend electrospinning method showed a limited influence on improving the hydrophobicity of highly hydrophobic nanofibers because most of the introduced oxide ceramics could agglomerate in the interior of the fiber matrix. In view of this, many researchers have applied a surface coating treatment to anchor oxide ceramics on fiber surfaces. For example, the group of Rutledge reported a layer-by-layer (LBL) assembly method for enhancing the hydrophilic property of electrospun polymer nanofibers, such as PS, PMMA, and poly(dimethylsiloxane-b-etherimide) (PSEI) nanofibers (Fig. 6d).179 The polymeric nanofibers were firstly treated with low-pressure air plasma to generate negatively charged groups on their surface. Then they were alternately dipped in polyhedral oligosilsesquioxane (POSS-NH3+) and TiO2 aqueous dispersions to adsorb positively charged POSS-NH3+ molecules and negatively charged TiO2 to enhance the hydrophilicity (Fig. 6e).
Another attractive method to incorporate oxide ceramics into nanofibers is based on an inorganic precursor, involving two key procedures: (i) fabrication of hybrid nanofibers by electrospinning a solution of the polymer carrier and the inorganic precursor, and (ii) calcination of the hybrid nanofibers under a gas flow. When an inert gas (e.g., Ar and N2) was selected as the gas flow, the carbon chain polymer carrier could be carbonized, leading to the formation of carbon/oxide ceramic hybrid nanofibers. For example, Lu et al. firstly electrospun a mixture of preceramic precursor polyureasilazane and carbon precursor PAN into nanofibers.189 During the subsequent calcination process, polyureasilazane was transformed into silicon oxycarbide (SiCO) together with the carbonization of PAN. Thanks to the abundant surface silanol groups of SiCO, the synthesized C/SiCO nanofibers exhibited good superhydrophilicity. When the hybrid nanofibers were calcined in air, the polymeric carrier will decompose, leading to the formation of hydrophilic oxide ceramic nanofibers. For example, Yang et al. fabricated SiO2 nanofibers by calcining PVA/tetraethyl orthosilicate (TEOS) hybrid nanofibers in air.61 The as-prepared SiO2 nanofibers displayed superamphiphilicity in air with both a WCA and OCA of about 0°. Notably, due to the large aspect ratio of the fibers (larger than 1000), the SiO2 nanofibers can be easily bent and folded without any cracks, which is significant for oil/water separation. In addition to SiO2, a variety of other oxide ceramics have also been successfully prepared as hydrophilic nanofibers by this method, including TiO2, ZrO2, ZnO, BaTiO3, LiCoO2, NiFe2O4, and LiFePO4.190–196
2.2.3. Approaches to roughen smooth surfaces.
The theoretical background has revealed that a sufficient hierarchical micro/nano-structure is needed for a superwettable surface. However, the intrinsic roughness on electrospun nanofibrous materials is not enough to bring about superwettability due to its single scale. Therefore, a common strategy is to construct nanoscale rough topography on fiber surfaces, and many important methods involving particle-decoration, in situ growth, etching, and phase separation are used.
(1) Particle-decoration method.
This method involves the introduction of additional nanoparticles onto nanofiber surfaces for creating nanotextures, which includes two major routes: fabrication of polymer/particle composite nanofibers during electrospinning (i.e., colloid electrospinning), and incorporation of nanoparticles after electrospinning by post-treatment (dip coating, surface self-assembly and so on).
Colloid electrospinning is the simplest strategy to prepare composite nanofibers with hierarchical rough surfaces. For example, Li and co-workers prepared hierarchical organic/inorganic hybrid nanofibers by electrospinning of PVDF/octadecyltrichlorosilane-capped SiO2 NP/DMF colloid solution.154 The SiO2 NPs contributed to a multiscale hierarchical structure on the PVDF nanofibers, making the wettability change from hydrophobic to superhydrophobic with a WCA of 163.1°. By adjusting the number of particles in the spinning solution, the density of nano-protrusions on the fibers can be easily controlled, and thus the wettability of the nanofibers can be regulated. For example, Ge et al. controlled the surface morphology of electrospun PAN/SiO2 NP products by the content of SiO2 NPs.65 When the concentration of SiO2 NPs increased from 1 to 4 wt%, the surfaces of the PAN/SiO2 NP products exhibited increased nanoscale roughness, leading to a significant improvement of the UWOCA from 155° to 162°. Because colloid electrospinning could incorporate nanoparticles in both the surface and interior of the fiber matrix, nanoparticles with poor dispersity may deteriorate the fiber mechanical property. Besides, the encapsulation of nanoparticles within polymer fibers limits their application in roughness construction. Surface treatment of the nanofibers is an effective route to overcome this issue, which refers to immersion of the pristine fibers into a nanoparticle suspension, and then the particles could be adsorbed on the fiber surfaces by electrostatic forces, hydrogen bonding or other interactions. For example, Wang et al. prepared hierarchical nanofibers through electrostatic surface assembly (Fig. 7a).197 After grafting of positively charged polyethyleneimine (PEI) on the hydrolyzed PAN (HPAN) nanofibers, the negatively charged SiO2 NPs homogeneously wrapped around the obtained HPAN/PEI nanofibers by electrostatic forces. The resultant hybrid nanofibers exhibited nanoscale protrusions on the fiber surfaces (Fig. 7b and c). Similar work was reported by Lee et al.,198 who firstly introduced a cationic surfactant into PVDF–HFP solution, followed by electrospinning of it into PVDF–HFP nanofibers with positive charge. After immersion of them into a dispersion of negatively charged SiO2 NPs, a layer of SiO2 NPs was firmly absorbed on the PVDF–HFP nanofiber surfaces by strong electrostatic attraction, leading to a hierarchical rough structure on the fiber surfaces. Song et al. introduced Fe3O4 NPs with an electropositive property on the PAA surface by electrostatic attraction, resulting a magnetic hierarchical rough surface.199
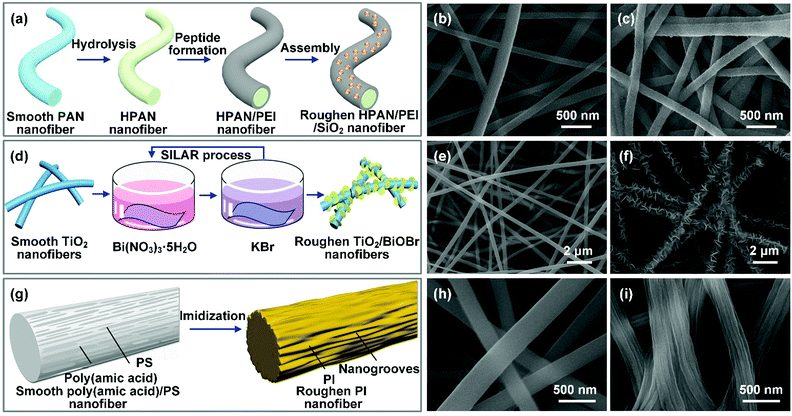 |
| Fig. 7 (a) Preparation of hierarchical nanofibers by the particle-decoration method. SEM images of the PAN nanofibers before (b) and after (c) modification by SiO2 NPs. Reproduced with permission from ref. 197. Copyright 2018, Elsevier. (d) Schematic of in situ growth of BiOBr NPs on TiO2 nanofibers. SEM images of TiO2 nanofibers (e) and a dense coating of BiOBr NPs homogeneously wrapping around TiO2 nanofibers (f). Reproduced with permission from ref. 200. Copyright 2018, Royal Society of Chemistry. (g) Schematic diagram of the formation of nanogrooves on PI nanofibers by the etching method. SEM images of (h) PAA/PS nanofibers with a smooth surface and (i) PI nanofibers with nanogrooves. Reproduced with permission from ref. 201. Copyright 2014, American Chemical Society. | |
(2)
In situ growth method.
The in situ growth method encompasses various construction routes, such as hydrothermal treatment, chemical vapor deposition (CVD), electroless plating, and successive ionic layer adsorption and reaction (SILAR). It allows for the gradual growth of nanocrystals with controllable morphology and uniform dispersity on smooth nanofiber surfaces. The chemical bonding energy between the created nanoscale coatings and nanofibers ensures a robust rough surface, which is conducive to practical applications.
Hydrothermal treatment is a commonly used route to synthesize nanomaterials, including crystal growth and transformation, phase equilibrium, and nanocrystal formation. When the hydrothermal process is combined with nanofibers, various metal oxides with different morphologies (e.g., sphere, sheet, and rods) can be constructed on fiber surfaces. For example, Chang et al. demonstrated a hydrothermal treatment to grow a layer of ZnO nanorods on PI nanofibers.202 The ZnO NPs as seeds were first deposited on PI nanofibers by dip coating, and then the resultant nanofibers were immersed in an aqueous solution of zinc nitrate hexahydrate and hexamethylenetetramine under high temperature for hydrothermal growth. As a result, the PI nanofibers showed a rough surface with a dense layer of ZnO nanorods, which was beneficial for superwettability. The CVD method is another advanced synthetic route for the growth of nanocrystals onto a fibrous substrate through chemical interactions of precursors at high temperature. Compared with the hydrothermal method, CVD avoids the solvent removal process and consequently forms a more uniform coating on nanofiber surfaces. For instance, Park et al. uniformly anchored CNT arrays on the surface of carbon nanofibers by CVD.159 Briefly, carbon/Fe3O4 NP hybrid nanofibers were fabricated by electrospinning of PAN/Fe(Acc)3 solution and a subsequent heat treatment process. Then the metal oxides acted as the catalyst for the formation of CNTs on the carbon nanofiber surfaces by a CVD process under a gas mixture (Ar/H2/C2H2). The fabricated fibers exhibited increased surface roughness, displaying a superhydrophobic property with a WCA of 155°, much higher than that of the smooth carbon nanofibers. As another example, Zeng et al. reported a thermal CVD method to make graphene sheets grow homogeneously and densely along every carbon nanofiber, thereby resulting in an obvious difference in WCA between pristine carbon nanofibers and graphene nanofibers (130° for the former one, but 173° for the latter rougher one).203
The above two routes require the growth of nanocrystals under harsh operational conditions (high temperature and high pressure), thus putting a limit on scalable application. Very recently, the SILAR technique, which relies on ionic reaction under normal temperature and pressure conditions to generate nanocrystals on nanofiber surfaces, has triggered much attention. For example, Cai et al. anchored a layer of BiOBr NPs onto TiO2 nanofibers by SILAR (Fig. 7d).200 Briefly, TiO2 fibers were firstly submerged into Bi(NO3)3 aqueous solution to absorb Bi3+, and then the treated nanofibers were soaked into KBr aqueous solution to form insoluble BiOBr on the TiO2 surface through the chemical interaction between Bi3+ and Br−. After multiple cycles of alternately dipping the TiO2 nanofibers into the two ionic liquids, BiOBr NPs uniformly adhered to the TiO2 nanofibers, leading to nanoscale roughness on the fiber surfaces (Fig. 7e and f). Similar work was reported by Ma et al., who anchored Fe3+/phytic acid coordination complex nanoparticles on PI nanofibers.204 As to the electroless plating process, the metal ions are first suspended in a chemical bath, and when a reducing agent is added, the chemical reaction begins to yield metal nanoparticles on the fiber surfaces. For example, Li et al. demonstrated an electroless plating process to construct nanoscale roughness on PAN nanofibers.166 PAN nanofibers were firstly aminated to generate amine and imine groups for full adsorption of [Ag(NH3)2]+. Then glucose as a reducing agent was added in the solution to synthesize Ag NPs on the PAN nanofiber surfaces. Usually, the created roughness can be adjusted by tuning the electroless plating time.
(3) Etching method.
The etching method means the removal of an unprotected component from the pristine multicomponent fibers by a chemical or physical process, such as decomposition, dissolution, and sublimation. If the aforementioned two roughening methods are designed based on the concept of “addition”, the etching method can be considered as the opposed design philosophy of “subtraction”.
For example, Guo and co-workers introduced nanogroove structure onto PI nanofibers by the etching method (Fig. 7g).201 During the electrospinning of PAA/PS solution, the PS molecular chains were well extended, and aggregated with each other, and then distributed in the PAA/PS fibers along the axial direction. After subsequent thermal imidization, the PS was decomposed, leaving numerous nanogrooves on the PI fiber surfaces (Fig. 7h and i). The resultant PI nanofibers showed a WCA of 134°. In contrast, PI smooth nanofibers only had a WCA of 129°. As another example, Zhang et al. successfully synthesized hierarchical PAN nanofibers by the selection of PVP as a sacrificial template through a dissolution-based etching route.205 The PAN/PVP composite nanofibers were firstly electrospun, and then the fibers were washed with water to dissolve the PVP, enabling the formation of a porous skin on the PAN nanofibers. In another study, Liu et al. used terephthalic acid (PTA) as the sublimating agent to decorate electrospun carbon nanofibers with macropores.206 The PAN/PTA hybrid nanofibers were firstly electrospun. Then PAN was converted into carbon and PTA sublimed by a calcination process under an argon gas flow. The resultant carbon nanofibers exhibited uniformly distributed tiny pores on their surfaces.
(4) Phase separation method.
In this method, a pristine homogenous phase loses its original equilibrium and turns into a new multiphase system that consists of a polymer phase and a liquid phase by the differences of polarity and intermolecular forces. After the liquid phase is removed, roughened polymer fibers could be obtained. This method is also based on the concept of “subtraction”, in which no further post-treatment is needed.
For instance, Lin et al. demonstrated a phase separation method to construct various microstructures (protrusions, grooves, and pits) on PS nanofibers (Fig. 8b–d).207 During the fiber formation process, the water vapor in the air as a non-solvent diffused into the fluid jet and mixed with the solvent, and the solution in the jet then became an unstable thermodynamic system. Combining it with the rapidly decreased temperature of the fluid jet, phase separation could be triggered, leading to the generation of a polymer-rich phase and a solvent-rich phase in the solution jet. After solvent evaporation, the polymer-rich region solidified and formed into the polymeric matrix, while the solvent-rich region evolved into nanopores, resulting in roughed nanofiber surfaces (Fig. 8a). Notably, the microstructures of PS fibers could be finely tuned by the polymer molecular weight, solvent composition, and solution concentration. Based on the same principle, Zhu et al. incorporated submicron pores onto PMMA/CdTe quantum dot nanofibers. During the electrospinning of PMMA/CdTe/chloroform, the evaporation of chloroform significantly lowered the ambient temperature, leading to the condensation of water vapor onto the jet. After water evaporation, rough porous surfaces were successfully gained on the nanofibers, resulting in an increased WCA of 151.2°.208
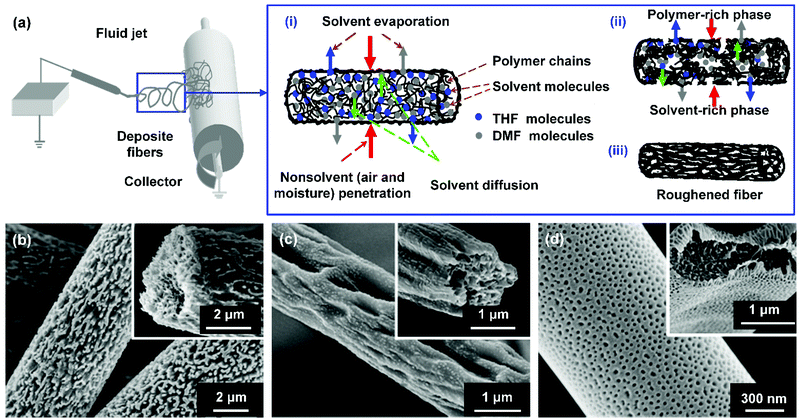 |
| Fig. 8 (a) Schematic showing the formation process of roughened electrospun nanofibers by phase separation. SEM images of the roughened PS fibers formed from various weight ratios of tetrahydrofuran : DMF in solvent: (b) 1 : 4, (c) 3 : 2, and (d) 5 : 0. Reproduced with permission from ref. 207. Copyright 2012, Royal Society of Chemistry. | |
3. Fabricating nanofibrous materials with optimized 2D and 3D porous structures
The porous structure of nanofibrous materials greatly influences the transport behaviors of emulsified droplets and the continuous phase during separation. The most common nanofibrous materials are single-component nanofibers with randomly arranged 2D nonwoven morphology, of which the simple porous structure is very limited in obtaining high separation performance. Through years of endless efforts, tremendous developments have been achieved in finely tailoring the arrangement structure of nanofibers by electrospinning system design and post-processing treatment, which endows nanofibrous materials (i.e., nanofibrous membranes and aerogels) with rational 2D and 3D porous structures, thereby providing a promising approach for achieving a maximum permeability/selectivity trade-off in filtration applications. In this section, we will introduce recently developed methods of regulating 2D and 3D porous structures.
3.1. Methods for regulating 2D porous structure
3.1.1. Multi-spinneret electrospinning.
Multi-spinneret electrospinning exploits an electrospinning system with multiple spinnerets to fabricate membranes with bi-component and multi-component nanofibers. By virtue of the structure characteristics (e.g., diameter and shape) of different component fibers, the membrane porosity and pore size can be synergistically regulated (Fig. 9a). For example, Zhang et al. utilized a multi-spinneret electrospinning system to cause thin PAN nanofibers (with a diameter of ∼270 nm) and thick PSU microfibers (with a diameter of ∼1.3 μm) to uniformly assemble into an integrated membrane.209 Because the thin nanofibers facilitated the formation of small pore size and microfibers were beneficial for reducing the packing density, the PAN/PSU composite nanofibrous membrane could possess a fascinating structure with both a small pore size and high porosity through tuning the jet ratio of PAN/PSU. Another study was demonstrated by Gao et al., in which they fabricated a membrane composed of PAN nanofibers and PAN microspheres by multi-spinneret electrospinning.215 The interwoven PAN nanofibers constituted a robust nanofibrous skeletal framework, in which the microspheres were uniformly inserted, thus enlarging the space among PAN fibers. Compared with the PAN nanofibrous membrane, the PAN nanofiber/microsphere membrane showed a higher porosity without increased pore size, suggesting its potential for rapid matter transfer under similar interception capacity. As a common and facile method for tuning the membrane structure, multi-spinneret electrospinning has been applied in industry. Yet there are still challenges of homogeneous assembly among different fibrous components. Further optimization of the electrospinning equipment (e.g., needle configuration, needle numbers, and interneedle spacing) and spinning parameters is a promising method to enhance the structural uniformity.
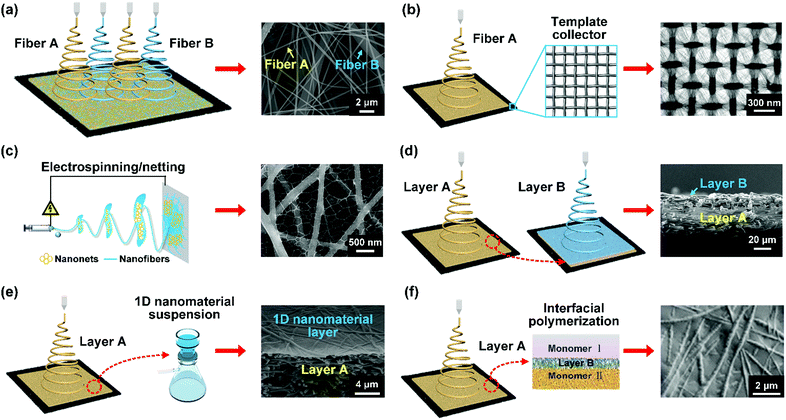 |
| Fig. 9 Schematic showing the method for regulating the 2D porous structure of nanofibrous membranes. (a) Multi-spinneret electrospinning method. Reproduced with permission from ref. 209. Copyright 2016, American Chemical Society. (b) Template-assisted electrospinning method. Reproduced with permission from ref. 210. Copyright 2007, Wiley-VCH. (c) Electrospinning/netting method. Reproduced with permission from ref. 211. Copyright 2017, Wiley-VCH. (d) Sequential electrospinning method. Reproduced with permission from ref. 212. Copyright 2018, Wiley-VCH. (e) Filtration deposition method. Reproduced with permission from ref. 213. Copyright 2011, American Chemical Society. (f) Interfacial polymerization method. Reproduced with permission from ref. 214. Copyright 2015, Elsevier. | |
3.1.2. Template-assisted electrospinning.
Different from the conventional electrospinning process, which relies on a flat collector, template-guided electrospinning with a patterned collector offers a means of externally controlling the nanofiber deposition. The macroscopic organization of nanofibers can be tuned by the design of the collector, thereby consequently leading to tailoring the membrane porous structure (e.g., pore size and shape) (Fig. 9b).210,216–218 For instance, Song et al. fabricated PVB nanofibrous membranes with different pore sizes by electrospinning nanofibers on metal meshes with various mesh numbers.93 During the fiber collection, the nanofibers preferentially deposited on the electroconductive metal wires rather than in the interspaces among the wires, leading to a patterned structure similar to the template collector. As the mesh number increased, the pore size of the resultant nanofibrous membrane could be enlarged. In another study, by virtue of metal ring collectors with metal needles, Li et al. prepared a biomimetic nanofibrous membrane with radially aligned nanofibers and small pore size. This intriguing structure allowed emulsified droplets to directionally move to the intersection of nanofibers under a wettability gradient and gravity.219 Besides, uniaxially aligned arrays of nanofibers could also be obtained under certain conditions such as the utilization of a collector pattened with a linear air gap.220 However, template-assisted electrospinning is not able to fabricate highly patterned nanofibers with a large membrane thickness because of the electrostatic repulsion between the deposited fibers and the incoming fibers. As a result, the ability to fabricate patterned nanofibrous membranes with submicron pore size is still a challenge.
3.1.3. Electrospinning/netting.
Electrospinning/netting is considered to be a variation of the electrospinning process. By virtue of phase separation of tiny charged solution droplets in an electric field, it enables one-step preparation of a 2D “nanonet” with nanoscale diameters (20–50 nm) and a topological Steiner-tree (Fig. 9c).211 This unique product can significantly decrease the membrane pore size without increasing the membrane thickness, which is beneficial for enhancing the membrane permeability. The formation of a nanonet requires the spinning solution parameters (e.g., electrical conductivity, viscoelastic property, and surface energy) to be within a certain range. Besides, the ambient parameters (e.g., temperature and relative humidity) also have a great influence on the formation of the nanonet. Until now, lots of polymers have succeeded in fabricating a nanonet, including hydrophobic polymers (e.g., PVDF and PU) and hydrophilic polymers (e.g., PAN, PVDF-g-PAA, PA6, PA66, PA56, PVA, PAA, CS, and cellulose).221 For instance, Zuo et al. fabricated a PU nanofiber/net membrane by using an ionic liquid (DMAc/LiCl) as a solvent through electrospinning/netting. The complexing action of Li+ and DMAc molecules could effectively mobilize Cl−, which then functioned as charge carriers to improve the charge capacity of the solution, thus increasing the formation probability of nanonets. The resultant PU nanonets endowed the PU membrane with a pore size of only 0.4 μm, which is much smaller than that of common PU nanofibrous membranes (6–12 μm).211 Besides hydrophobic polymer systems, Wang et al. fabricated a hydrophilic PA6 nanofiber/net membrane by finely tailoring the ratio of polymer and solvent.222 Due to the small pore size (∼83 nm) of the PA6 nanonet, the resultant PA6 membrane exhibited a small pore size (<0.2 μm) within a thin thickness (∼10 μm). In another report, Liu et al. investigated the formation of PAN nanonets at different relative humidity. They found that the PAN charged droplets can fully phase-separate at a slower speed during the electrospinning/netting process under a relative humidity of 35%. Higher relative humidity could rapidly dissipate the charge, and thus the formation of the nanonet was severely suppressed. The resultant PAN nanofiber/net membranes formed under 35% relative humidity possessed the integrated characteristics of a small pore size (<0.3 μm) and high porosity (∼93.9%).223 Also, Cheng et al. reported a PVDF-g-PAA nanofiber/net membrane by electrospinning/netting, and the membrane pore size was about 0.32 μm.224 Up to now, the 2D “nanonets” derived by electrospinning/netting are all polymer-based materials, and it is still challenging to prepare inorganic nanonets, which are potentially important in liquid filtration under harsh conditions (high temperature, acids, alkalis, and salts).
3.1.4. Sequential electrospinning.
This method refers to the direct electrospinning of nanofibers onto a porous nanofibrous substrate, providing the capacity to fabricate multilayer nanofibrous membranes with asymmetrical porous structure (pore size, porosity and so on) on each surface (Fig. 9d). Thus, the synthesized multilayer membranes show great potential in the simultaneous optimization of permeability, selectivity, and mechanical strength.225 For example, Wang and co-workers fabricated a bilayer nanofibrous membrane consisting of a thin hydrophilic PVA nanofibrous coating layer and PAN nanofibrous bottom layer by sequential electrospinning.226 Then the PVA nanofiber layer was melted through exposure to water vapor and crosslinked in glutaraldehyde water/acetone solution to form a dense film on the support layer. The resultant PVA/PAN membranes demonstrated bottom-up hierarchical networks. It should be noted that the porous structure of the PVA coating layer can be easily controlled by tuning the deposition time and the crosslinking degree of PVA nanofibers. Similarly, a fascinating report by Raza et al. presented a sequential electrospinning method to deposit PEO/PEGDA nanofibers onto a PAN/PEG nanofibrous membrane. Then they utilized UV-irradiation to in situ crosslink the PEGDA to decrease the pore size of the PEO/PEGDA layer, thereby forming a nanofibrous membrane with asymmetrical pore size.227 Sequential electrospinning is the most simple and effective approach to tune the 2D porous structure in multilayer membranes. However, the porosity among nanofibers may be deteriorated in the following cross-linking process, which is not beneficial for liquid permeation during oil/water separation.
3.1.5. Filtration deposition.
This method means to filtrate a suspension of 1D nanomaterials (with a diameter of several nanometers) onto an electrospun membrane, leaving a layer of 1D nanomaterials with nanoscale thickness on the electrospun substrate (Fig. 9e). This method as a complement of sequential electrospinning significantly increases the physicochemical diversity of coating layers in multilayer membranes. Currently, a variety of ultrafine nanofibers, including biomass fibers (e.g., cellulose nanocrystals and chitin nanofibers), and inorganic fibers (e.g., CNTs and metal nanowires), are employed as the building blocks of coating layers.213,228,229 For instance, Cao et al. prepared a bilayer membrane with a PAN nanofibrous membrane as a substrate and jute cellulose nanocrystals (with fiber diameter ranging from 3 to 10 nm) as the building blocks of the coating layer by the filtration deposition method.229 The synthesized PAN/cellulose nanocrystal membrane demonstrated nanoscale pore size and a thin thickness in the coating layer. A similar process was also realized by depositing ultrafine chitin nanofibers with diameters ranging from 15 to 20 nm on an electrospun PAN nanofibrous membrane.213 The resultant membrane possessed an average pore size of ∼20 nm and main pore size distribution below 50 nm. As another example, Tian and co-workers fabricated a multilayer structured membrane by utilization of an electrospun PAN membrane as the support layer and CNTs as the coating layer.230 The resultant PAN/CNT membrane possessed a narrow pore size distribution and a small average pore size of 0.25 μm, which was more uniform and smaller than the PAN nanofibrous substrate with an average pore size of 0.8 μm. However, it should be noted that 1D nanomaterials with length in the sub-micron range could infuse into the nanofibrous substrate, leading to a discontinuous coating layer and partly blocked pore channels.
3.1.6. Interfacial polymerization.
Interfacial polymerization refers to two highly reactive polyfunctional monomers reacting at the interface between two immiscible liquids, resulting in a polymeric film with a thin thickness (from 10 nm to several micrometers) and small pore size at the interface of the two phases. When the two-phase interface is close to the nanofibrous membrane surface, the synthesized polymeric film could act as a coating layer to adhere to the nanofibrous support, leading to a multilayer membrane (Fig. 9f).231 The porous structure and surface morphology of the coating layer can be well controlled by adjustment of the concentration of monomers, reaction time, and solvent type. Notably, the top layer nanofibers in the nanofibrous substrate can be embedded into the coating layer to create transmission channels between the fiber and polymer matrix, thus facilitating liquid transportation.232 As a typical example, Obaid et al. developed a thin PA film on a PSF nanofibrous membrane by the interfacial polymerization of m-phenylenediamine and 1,3,5-benzenetricarbonyl chloride, thereby optimizing the membrane structure.214,233 Notably, when utilizing electrospun nanomaterials as a platform for interfacial polymerization, the high porosity of the nanofibrous membrane could provide more adhesion points for the formation of the polymeric film, which made it more uniform. However, the considerable porous structure may also lead to defects of the polymerized film, which means that the active layer tends to be damaged under filtration and decreases the selective performance.
3.2. Methods for regulating 3D porous structure
The above methods could flexibly regulate the 2D porous structure in nanofibrous membranes. Despite their outstanding potential in filtration and separation, the major problem associated with membranes still exist, such as easy pore blockage. More recently, strategies of tailoring the 3D porous structure of nanofibrous materials have come into sight, leading to the formation of 3D nanofibrous aerogels. Compared with nanofibrous membranes, nanofibrous aerogels can offer much stereo storage room for droplet retention, thereby effectively avoiding sharp blocking of transport channels by emulsified droplets and greatly prolonging the service life. Meanwhile, nanofibrous aerogels possess ultrahigh porosity (>90%), which is beneficial for continuous phase permeation. Generally, there are two methods for tuning the 3D porous structure of nanofibrous aerogels, i.e., physical template assembly and bottom-up self-assembly.
3.2.1. Physical template assembly.
Template assembly of 3D nanofibrous networks refers to the employment of an existing 3D block substrate as a template, followed by the introduction of nanofibers to tailor its interior frame (Fig. 10a). Commercially available sponges have been extensively utilized as a 3D physical template. For instance, Lv et al. recently reported a physical template assembly process to fabricate an elastic 3D aerogel by the insertion of SiO2 nanofibers into a poly(melamine formaldehyde) sponge.234 Numerous minor pores derived from interwoven SiO2 fibers were created in the sponge, so the intrinsic large pores in the pristine sponge decreased quickly from about 110 to 23 μm. Meanwhile, the aerogel maintained a high porosity (>97.8%) (Fig. 10b–e). Because the structure features of the sponge played a key role in the arrangement of the nanofibers, the porous structure of nanofibrous aerogels would not be flexibly tuned for fixed main frameworks (most sponges with a pore size of 100–500 μm). Therefore, the nanofibrous aerogels synthetized by this method may show a great challenge for removal of submicron or nanoscale emulsified droplets.
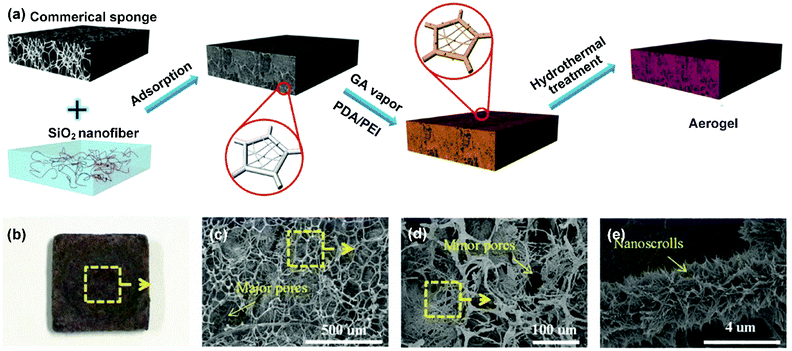 |
| Fig. 10 (a) The regulation of the 3D porous structure of a nanofibrous aerogel by physical template assembly. (b) An optical photograph and (c–e) SEM photographs of the as-prepared nanofibrous aerogel. Reproduced with permission from ref. 234. Copyright 2017, Wiley-VCH. | |
3.2.2. Bottom-up self-assembly.
Bottom-up self-assembly is an economical and efficient method to regulate the 3D porous structure of nanofibrous materials through homogenizing nanofiber dispersions, freeze drying to remove the solvent, and crosslinking the fibrous framework. By carefully controlling the dispersion concentration, fiber dispersity, freezing conditions, and the character of the solvent and fiber, the 3D porous structure (pore size, pore volume, and pore morphology) can be readily regulated, thus overcoming the limitations of the previous method.62 Meanwhile, the nanofibrous aerogels fabricated by this method usually possess hierarchical pore morphologies, thus making them perfect candidates for separation applications, even for separation of oil/water microemulsions. Besides, various shapes (e.g., cubes, cones, cylinders, and tubes) could be easily obtained by designing molds, which is significant for the fabrication of filter modules. For example, Si et al. fabricated a cellular structured nanofibrous aerogel by self-assembly of PAN and SiO2 nanofibers.62 Benzoxazine was employed as a crosslinking agent to stabilize the 3D fibrous scaffold (Fig. 11a). The major cellular pores in the aerogels originated from the non-planar solvent crystals and the minor cellular pores were derived from the bonding of the tangled PAN and SiO2 fibers (Fig. 11c–e). Such a unique hierarchical cellular structure provided numerous microchannels, enabling liquid to pass through easily (Fig. 11f). Moreover, the simplicity and good controllability of the bottom-up self-assembly method ensured that nanofibrous aerogels with various sizes and shapes could be facilely designed and fabricated without second processing (Fig. 11b). Notably, in order to ensure the mechanical integrity of the fibrous aerogel during the filtration process, the crosslinking process in this method should be optimized according to the application environment (such as acids, alkalis, and salts) to avoid aerogel disintegration into suspensions of short fibers upon contact with filtrates.
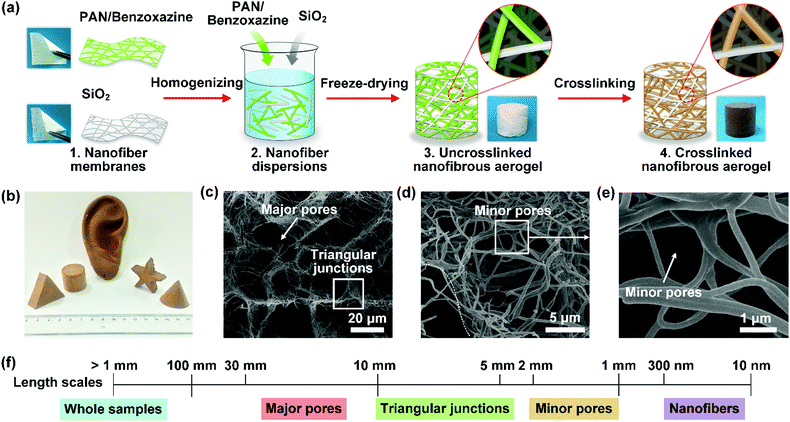 |
| Fig. 11 (a) The regulation of a 3D porous structure nanofibrous aerogel by bottom-up self-assembly. (b) A digital image showing the moldability of nanofibrous aerogels. (c–e) SEM images with different magnifications of the obtained nanofibrous aerogel. (f) Schematic of the levels of hierarchy in three dimensions. Reproduced with permission from ref. 62. Copyright 2014, Nature Publishing Group. | |
4. Applications of electrospun nanofibrous materials in emulsion separation
As discussed in the previous sections, electrospun nanofibrous materials as one of the hottest nanomaterials possess remarkable features, such as controllable chemical compositions, tunable porous structure, diverse dimensions, and good pore connectivity, which make them a promising candidate for emulsified oil purification and oily wastewater remediation. In this section, we will focus on new and typical nanofibrous materials applied in these fields.
4.1. Oil purification
Oil purification is a process that removes emulsified water droplets from oily matter, which requires the electrospun nanofibrous materials to have hydrophobic–oleophilic chemical compositions and appropriate pore size. Generally, these nanofibrous materials can be classified into two types.
4.1.1. Hydrophobic–oleophilic nanofibrous membranes.
Since the fabrication of hydrophobic–oleophilic nanofibrous membranes for oil purification through the direct electrospinning of low-surface-energy polymers (PP,89,90 PVAc,235 PVP,235 and PVDF–HFP110) was reported by Chase et al., considerable efforts have been devoted to the synthesis of filtration membranes in such a way. However, these membranes generally have quite a few drawbacks like poor antifouling performance and unsatisfactory separation performance due to the insufficient roughness and large pore size.
Over the past few years, taking inspiration from the lotus leaf, a variety of biomimetic superwettable nanofibrous materials have been developed by the introduction of nanoscale roughness structure. According to wettability theory, hierarchical roughness structure can transfer the Wenzel state of the pristine nanofibrous membrane to the Cassie state, thus leading to an outstanding anti-water-adhesion property.236 For example, Huang et al. reported a superhydrophobic–superoleophilic nanofibrous membrane by construction of a fluorinated polybenzoxazine (F-PBZ)/Al2O3 NP functional layer on silica nanofiber surfaces through in situ polymerization (Fig. 12a and b).60 The introduction of Al2O3 NPs created a hierarchical rough structure on the membrane, which remarkably enhanced the selective wettability and rendered the membrane superhydrophobic–superoleophilic with a WCA larger than 160° and an OCA approaching 0° (Fig. 12c). When a water-in-petroleum ether emulsion was poured onto the SiO2/F-PBZ/Al2O3 NPs membrane, only oil could permeate through the membrane, while the water droplets were intercepted by the membrane, yielding a permeation flux of 892 L m−2 h−1 (Fig. 12d and e). The trapped oil layer in the hierarchical rough structure effectively prevented contact between the underoil water droplet and membrane surface, leading to an outstanding reusability without flux decline upon 10 cycles (Fig. 12g). Besides, the membrane showed prominent thermal stability (Fig. 12f), which is crucial to practical applications.
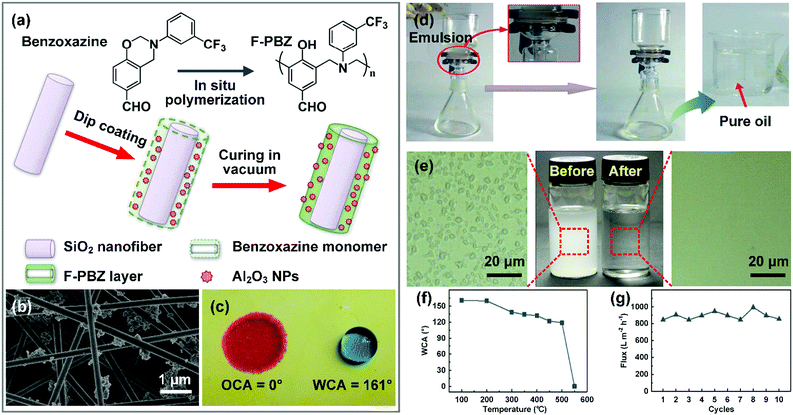 |
| Fig. 12 (a) Schematic of the preparation of and (b) SEM image of the SiO2/F-PBZ/Al2O3 NP nanofibrous membrane. The inset shows a water droplet on the membrane. (c) Digital photograph showing the selective wetting behavior for oil (red) and water (blue). (d) Schematic illustration of the separation of a water-in-oil emulsion by the SiO2/F-PBZ/Al2O3 NP membrane. (e) Digital images and optical micrographs of the feed and filtrate. (f) WCAs of the SiO2/F-PBZ/Al2O3 NPs under various temperatures. (g) Permeation flux of the F-PBZ/Al2O3 membrane for a water-in-oil emulsion within 10 cycles. Reproduced with permission from ref. 60. Copyright 2013, Royal Society of Chemistry. | |
The aforementioned membranes are ineffective for nanoscale emulsions (with a droplet size below 1 μm) because of their micron pore size. To address this problem, Kang et al. demonstrated a sequential electrospinning method to fabricate a thin layer of PDO 3 nanofibers on a highly porous PLC nanofibrous membrane.66 After subsequent light irradiation, the PDO 3 nanofibers were partly fused together to reduce the pore size of the coating layer, while the PCL nanofiber layer remained intact. Thus, this membrane exhibited a bilayer architecture with nanopores in the PDO 3 coating layer and micron pores in the PCL substrate (Fig. 13a–c). Meanwhile, by virtue of the low-surface-energy composition of PDO 3, the obtained PDO 3/PCL membrane possessed highly hydrophobic and superoleophilic properties with a WCA of 141° and an OCA of 0° (Fig. 13d). Utilizing this membrane, the author demonstrated the removal of nanoscale water droplets (with a diameter ranging from 3 to 300 nm) from a series of emulsions (i.e., water-in-isooctane, water-in-petroleum ether, and water-in-hexane), exhibiting high separation efficiencies (>99.96%) and satisfactory oil fluxes (14
165 ± 354 L m−2 h−1 bar−1 for surfactant-free emulsions and 912 ± 79 L m−2 h−1 bar−1 for surfactant-stabilized emulsions). Notably, although the PDO 3/PCL membrane possessed a small pore size, it also demonstrated high permeation fluxes. The reason was that this membrane possessed a thin coating layer and a porous bottom layer, and such a unique structure could effectively decrease the transport distance for oil.
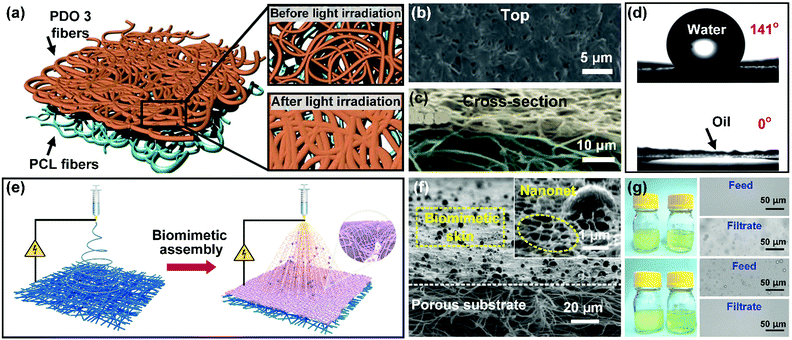 |
| Fig. 13 (a) Schematic of PDO 3 nanofibers, tailoring the membrane pore size by light irradiation. (b and c) Microscopic structure of the PDO 3/PCL membrane after exposure to light. (d) Wettability of the membrane toward water and oil. (e) Procedure for the synthesis of a biomimetic PVDF multilayer nanofibrous membrane by sequential electrospinning. (f) SEM images showing the section morphology of the PVDF multilayer membrane. (g) Separating water-in-oil emulsions without (up) and with (down) a surfactant. Reproduced with permission from ref. 66. Copyright 2017, Royal Society of Chemistry. Reproduced with permission from ref. 237. Copyright 2019, Royal Society of Chemistry. | |
More recently, growing attention has been paid to synchronous regulation of the wettability and porous structure. For instance, Jiang and co-workers presented a filtration coating strategy to form a thin layer of hydrophobic CNTs on a PAN nanofibrous substrate.228 The introduction of CNTs not only created nanotexture on PAN fiber surfaces but endowed the PAN/CNT multilayer membrane with nanoscale pore size. Thus, the PAN/CNT membrane was endowed with Cassie wetting behavior for oil droplets at the solid/water/oil interface, which is significant for enhancing the antifouling performance. The nanopores of the coating layer significantly increased the size sieving capacity of the membrane. In consequence, the developed PAN/CNT membrane was used to treat a nanosized water-in-chloroform emulsion (with a diameter ranging from 0.3 to 1 μm), achieving a high separation efficiency up to 99.2% and an oil flux of 12
000 L m−2 h−1. However, this membrane usually suffers from poor interlayer integrity between the inorganic and organic layers due to the incompatibility, so the inorganic layer tends to detach from the polymeric substrate after a long period of use. To overcome this issue, Zhang and co-workers constructed an all-polymer multilayer membrane consisting of a taro leaf-like hierarchical PVDF thin layer on a porous PVDF nanofibrous membrane through regulating the jet mode of sequential electrospinning (Fig. 13e).237 The obtained polymeric membrane displayed an asymmetrical cross-sectional structure with submicron pores on the top layer and micron pores on the substrate layer as well as good structure integrity (Fig. 13f). Besides, benefiting from the synergy of the biomimetic hierarchical surface and the oleophilic fluorinated polymeric matrix, the PVDF membrane demonstrated a superwettable property with a WCA above 150° and an OCA of 0°. Thanks to the synergy of oil/water selectivity and submicron pores, the PVDF multilayer membrane can be used for separating micrometer- and nanometer-size oil droplets from multiple surfactant-free and surfactant-stabilized water-in-oil emulsions, including water-in-diesel, water-in-isooctane, water-in-petroleum ether, and water-in-cyclohexane emulsions (Fig. 13g).
4.1.2. Hydrophobic–oleophilic nanofibrous aerogels.
Benefiting from the surface chemical composition control and porous structure construction, the separation performance of 2D nanofibrous membranes has been remarkably improved. However, this high performance can only keep stable in the initial stage of the separation process, because water is denser than most oils, and thus water will settle below the oil and form a water layer that prevents oil from penetrating the porous material surface. Although some filtration units can reduce droplet accumulation and enhance the separation stability, they have some limitations such as complex assembly processes.238 Recently, 3D porous nanofibrous aerogels have drawn much attention owing to their unique characteristics, such as ultrahigh porosity, high inter surface area, and stereo sieving manner, which endow them with great potential for droplet storage, thereby leading to a continuous separation process for a long time. As a typical example, Si and co-workers prepared a hierarchical cellular structured nanofibrous aerogel with a superhydrophobic–superoleophilic property by bottom-up self-assembly (Fig. 14a).239 The electrospun PAN nanofibers and SiO2 nanofibers were applied to construct a 3D macroporous skeleton, while SiO2 NPs were introduced to build nanoscale roughness (Fig. 14b–e). Fluoric benzoxazine with low surface energy was used as a hydrophobizing agent and crosslinking agent to increase the stability of the 3D fibrous skeleton. The resultant nanofibrous aerogel demonstrated integrated properties of selective superwettability with a WCA of 162° and OCA of 0° and stable 3D porous structure with ultrahigh porosity (>98%) (Fig. 14f). When treating water-in-oil emulsions (i.e., water-in-petroleum ether, water-in-gasoline, and water-in-diesel), the emulsified water droplets were easily intercepted in these long channels, resulting in high separation efficiency. Its outstanding pore connectivity with high porosity ensured that the oil searched for substitute routes penetrating the aerogel even when some channels were blocked by water droplets, resulting in high permeability for long term service. As a result, the as-prepared nanofibrous aerogel could achieve an intriguing oil flux of 8140 L m−2 h−1 and a high separation efficiency (Fig. 14g). Meanwhile, the nanofibrous aerogel showed excellent antifouling performance, indicating a robust performance for real emulsion separation (Fig. 14h). For 3D nanofibrous aerogels, a simple in situ pumping method could realize continuous oil purification (Fig. 14i).
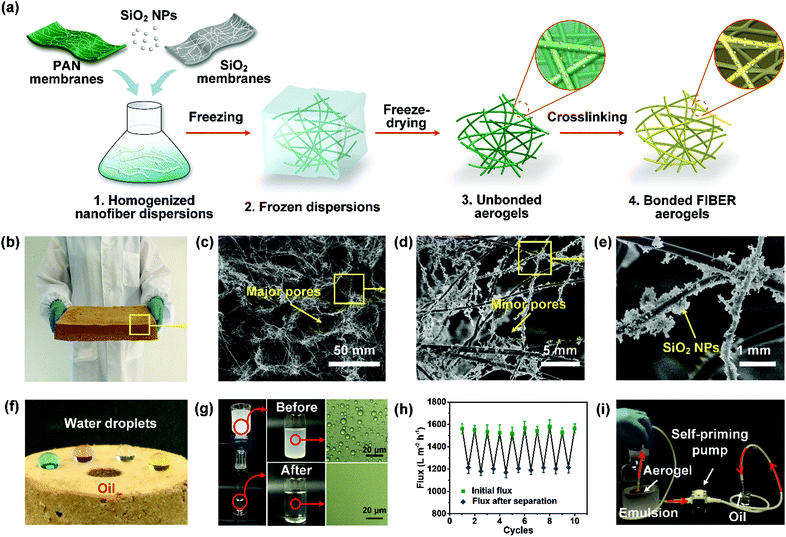 |
| Fig. 14 (a) Schematic of the preparation of the hydrophobic–oleophilic nanofibrous aerogel. (b) A digital photograph of the nanofibrous aerogel on a massive scale of 2.5 L. (c–e) SEM images showing the microscopic structure of the nanofibrous aerogel. (f) Digital photo of the selective permeability of water and oil on the surface of the nanofibrous aerogel. (g) Separation of water-in-oil emulsions using the aerogel, and the corresponding optical microscopy photographs of the emulsions and filtrates. (h) Variation of the oil flux and flux recovery during filtration cycles. (i) Photograph showing a device for continuous oil collection from water-in-oil emulsions. Reproduced with permission from ref. 239. Copyright 2015, American Chemical Society. | |
4.2. Oily wastewater remediation
When treating emulsified oily wastewater, it is reasonable for filtration materials to let water pass through freely and repel oil completely. Recently, researchers have successfully developed a variety of nanofibrous materials with a hydrophilic–oleophobic (i.e., hydrophilic–underwater oleophobic) property and suitable porous structure for treating oily wastewater.
4.2.1. Hydrophilic–oleophobic nanofibrous membranes.
The prevailing strategy for the preparation of hydrophilic–underwater oleophobic nanofibrous membranes is the direct electrospinning of high-surface-energy materials. For instance, Zang and co-workers prepared core–shell structured nanofibers by electrospinning of CA/PMAA solution. During the fiber formation process, phase separation induced PMAA as a hydrophilic shell and CA as a supporting core.240 The subsequent heat treatment induced ester linkages between PMAA and CA, thus increasing the underwater durability of the PMAA shell. Due to the strong affinity of PMAA to water, the resultant CA/PMAA nanofibrous membrane possessed superhydrophilicity–underwater superoleophobicity with a WCA of 0° and UWOCA of 155°. Attributed to the synergistic effect of the promising wettability and small pore size (∼2 μm), the membrane could selectively separate micron oil droplets (n-hexane, petroleum ether, hexadecane, and diesel) from emulsified oily water, exhibiting a high separation efficiency. The pore size of the CA/PMAA membrane could be tuned by the pH value of the emulsions. The enlarged membrane pore size could greatly improve the water flux. Note that the CA/PMAA membrane demonstrated a high underwater oil-adhesion property despite its superwettability, which may lead to poor antifouling performance and a short lifetime. Besides, this membrane exhibited a large pore size above 1 μm, which limited its applications in treating nanoscale emulsions.
Currently, impressive progress has been made on the design and development of high-performance separation membranes to overcome the aforementioned problems, which are usually designed based on two criteria: (i) construction of a roughness structure on fiber surfaces to endow the membrane with an underwater Cassie state, and (ii) regulating the pore size in a suitable range to intercept nanosized droplets. For example, Zhang et al. fabricated a hierarchical TiO2 nanofibrous membrane through the combination of electrospinning and hydrothermal treatment.241 Briefly, a PVP/TiO2 hybrid nanofibrous membrane was first prepared by electrospinning, and then it was converted into a pure TiO2 nanofibrous membrane by calcination in air (Fig. 15a). After a subsequent hydrothermal process, TiO2 nanorods densely grew on the nanofiber surfaces, resulting in pine-branch structured hierarchical fibers and a small pore size (Fig. 15b). The resultant hierarchical TiO2 nanofibrous membrane possessed a superhydrophilic–underwater superoleophobic property with a WCA of 0° and a UWOCA of about 160° (Fig. 15c). Because the entrapped water in the hierarchical roughness structure significantly decreased the contact area between the oil droplet and the membrane surface, the synthesized TiO2 membrane showed an ultralow oil adhesive force of nearly 0 μN (Fig. 15d), which was beneficial for the antifouling performance. Consequently, the as-prepared hierarchical TiO2 membrane could allow treating nanoscale oil (petroleum ether, toluene, hexadecane, isooctane, gasoline, and diesel)-in-water emulsions (with an oil droplet diameter ranging from 41.1 to 313.5 nm) with water fluxes above 35 L m−2 h−1. More than 99% of oil droplets were removed from the water (Fig. 15e). Also, this membrane showed an excellent recyclable property, which may meet the requirements for practical applications. Interestingly, the TiO2 membrane showed higher water fluxes under UV illumination, which suggested that UV-induced hydroxyl groups on the TiO2 nanofiber surface could make the TiO2 membrane more superhydrophilic. It should be noted that once oil permeated through the membrane, it would be contaminated and must be rinsed with organic solvents (e.g., ethanol) to recover the wettability. To avoid oil contamination completely, zwitterionic polymers were employed to be incorporated on the membrane surface for emulsion separation due to their superior electrostatic binding with water molecules. For example, Zhang et al. developed a zwitterionic nanohydrogel (ZN)-grafted PVDF-g-PAA nanofibrous membrane by the combination of electrospinning of PVDF-g-PAA dilute solution and inverse microemulsion polymerization.242 The resultant PVDF-g-PAA/ZN membrane was composed of interpenetrated nanofibers and microspheres, demonstrating a lotus-leaf like hierarchical surface. Thanks to the hierarchical roughness and hydrophilic polymeric matrix, the PVDF-g-PAA/ZN membrane showed superhydrophilic and underwater oleophobic properties with a WCA of 0° and a UWOCA greater than 150° for various oils. Because the zwitterionic polymer exhibited outstanding binding affinity to water, even when the PVDF-g-PAA/ZN nanofibrous membranes were fouled by oils in air, the spread oils can shrink into a droplet and then detach from the membrane surface once immersed in water. By virtue of these integrated features and small pore size, the synthesized PVDF-g-PAA/ZN nanofibrous membrane could remove lots of nanoscale emulsified oil from oily wastewater. This membrane was believed to show stable separation performance after long term use.
 |
| Fig. 15 (a) Formation procedures and (b) SEM image of the hierarchical TiO2 nanofibrous membrane. (c) WCA and UWOCA of the hierarchical TiO2 membrane. (d) Adhesive force–distance curves between diesel droplets and the TiO2 membrane underwater. (e) A separation device and images of the emulsion before and after separation. Reproduced with permission from ref. 241. Copyright 2017, Royal Society of Chemistry. | |
4.2.2. Hydrophilic–oleophobic nanofibrous aerogels.
The integrated features of large specific surface areas, ultrahigh porosity, 3D interconnected channels, and easy access to large thicknesses (>1 cm) have made nanofibrous aerogels favorable candidates for oil purification. More recently, nanofibrous aerogels with a hydrophilic–underwater oleophobic property have also gained tremendous interest in emulsified oily wastewater remediation. Xiao et al. developed a GO sheet/CA nanofiber nanofibrous aerogel with ultrahigh porosity (>99%) by bottom-up self-assembly.243 The GO sheets adhered to CA nanofibers while the CA nanofibers acted as bridges to connect several GO sheets in turn, forming an open-cell geometry structure. Aiming to endow the nanofibrous aerogel with hydrophilicity–underwater oleophobicity and small pore size, the GO/CA nanofibrous aerogel was compressed at a certain strain and then modified with PDA and PEI. The resultant GO/CA/PDA/PEI nanofibrous aerogel demonstrated excellent capability for the separation of emulsified oily water (n-hexane-in-water emulsion), exhibiting a high separation efficiency (>99%) and a superb water flux of more than 19
580 L m−2 h−1 bar−1 (several times higher than commercial membranes).
5. Conclusions and perspectives
In this review, we focus on an overview of the recent progress on electrospun nanofibrous materials for emulsion separation by summarizing the interface wettability tunability from hydrophobic–oleophilic to hydrophilic–oleophobic, architecture regulation from 2D porous structure in membranes to 3D porous structure in aerogels, and their promising applications in emulsified oil purification and oily wastewater remediation. Although tremendous advances have been achieved, several challenging problems still exist.
First, more quantitative research is needed to guide scientists to design nanofibrous filtration materials. For example, it is still less well known how emulsified droplets dynamically interact with the pore channel during separation. Second, the surface physicochemical structure of nanofibers can be readily destroyed by external mechanical forces and chemical contamination, which makes the nanofibrous materials lose selectivity. Future trends in this field may see an expansion towards self-healing nanofibrous materials for their easy and automatic restoration of selective wettability after damage. Third, most nanofibrous materials reported to date are effective to treat oil/water emulsions derived from oils (e.g., petroleum ether, toluene, hexane, chloroform, hexadecane, cyclohexane, isooctane, gasoline, and diesel) with low viscosity (<10 mPa s−1), but cannot work well in treating highly viscous oil and oily wastewater. Therefore, it is highly desired to develop nanofibrous materials for separating emulsified high viscosity oil/water mixtures with high efficiency. Fourth, in the real world, an oil/water emulsion is a highly complicated system due to the inevitable introduced contaminants, such as microorganisms, inorganic salts, and dyes. Therefore, scientists are required to develop multifunctional nanofibrous materials. Finally, from an environmentally friendly and sustainable perspective, researchers need to consider the reclamation of industrial and daily waste, for example, food packaging, cigarette ends, and food residue, as raw materials for designing nanofibrous separation materials.
Despite the many challenges involved, despite many challenges are involved. Future development of electrospun nanofibrous materials will be achieved by multidisciplinary cooperation of materials science, surface chemistry, and engineering. We believe that with additional efforts, an exciting future in the design and fabrication of nanofibrous emulsion separation materials will emerge.
Conflicts of interest
The authors declare no conflicts of interest.
Acknowledgements
This work was supported by the Fundamental Research Funds for the Central Universities (no. 223201900081 and 17D310107), the National Natural Science Foundation of China (no. 51773033, 2191101289, and 51925302), and the Shanghai Municipal Science and Technology Committee of Shanghai Outstanding Academic Leaders Plan (18XD1400200).
Notes and references
- C. H. Peterson, S. D. Rice, J. W. Short, D. Esler, J. L. Bodkin, B. E. Ballachey and D. B. Irons, Long-term ecosystem response to the Exxon Valdez oil spill, Science, 2003, 302, 2082–2086 CrossRef CAS.
- M. Schrope, A Scientist at the centre of the spill, Nature, 2010, 466, 680–684 CrossRef.
- M. Schrope, Oil spill deep wounds, Nature, 2011, 472, 152–154 CrossRef CAS.
- J. Ge, L. A. Shi, Y. C. Wang, H. Y. Zhao, H. B. Yao, Y. B. Zhu, Y. Zhang, H. W. Zhu, H. A. Wu and S. H. Yu, Joule-heated graphene-wrapped sponge enables fast clean-up of viscous crude-oil spill, Nat. Nanotechnol., 2017, 12, 434–440 CrossRef CAS.
- N. Bhardwaj and A. N. Bhaskarwar, A review on sorbent devices for oil-spill control, Environ. Pollut., 2018, 243, 1758–1771 CrossRef CAS.
- S. Gao, J. Sun, P. Liu, F. Zhang, W. Zhang, S. Yuan, J. Li and J. Jin, A robust polyionized hydrogel with an unprecedented underwater anti-crude-oil-adhesion property, Adv. Mater., 2016, 28, 5307–5314 CrossRef CAS.
- H. H. Al-Kayiem and J. A. Khan, Evaluation of alkali/surfactant/polymer flooding on separation and stabilization of water/oil emulsion by statistical modeling, Energy Fuels, 2017, 31, 9290–9301 CrossRef CAS.
- D. Pradilla, J. Ramirez, F. Zanetti and O. Alvarez, Demulsifier performance and dehydration mechanisms in colombian heavy crude oil emulsions, Energy Fuels, 2017, 31, 10369–10377 CrossRef CAS.
- S. J. Gao, Y. Z. Zhu, J. L. Wang, F. Zhang, J. Y. Li and J. Jin, Layer-by-layer construction of Cu2+/alginate multilayer modified ultrafiltration membrane with bioinspired superwetting property for high-efficient crude-oil-in-water emulsion separation, Adv. Funct. Mater., 2018, 28, 1801944 CrossRef.
- Y. Zhu, J. Wang, F. Zhang, S. Gao, A. Wang, W. Fang and J. Jin, Zwitterionic nanohydrogel grafted pvdf membranes with comprehensive antifouling property and superior cycle stability for oil-in-water emulsion separation, Adv. Funct. Mater., 2018, 28, 1804121 CrossRef.
- W. Zhang, Y. Zhu, X. Liu, D. Wang, J. Li, L. Jiang and J. Jin, Salt-induced fabrication of superhydrophilic and underwater superoleophobic PAA-g-PVDF membranes for effective separation of oil-in-water emulsions, Angew. Chem., Int. Ed., 2014, 53, 856–860 CrossRef CAS.
- A. K. Kota, G. Kwon, W. Choi, J. M. Mabry and A. Tuteja, Hygro-responsive membranes for effective oil-water separation, Nat. Commun., 2012, 3, 1025 CrossRef.
- Z. Bao, D. Y. Chen, N. J. Li, Q. F. Xu, H. Li, J. H. He and J. M. Lu, Superamphiphilic and underwater superoleophobic membrane for oil/water emulsion separation and organic dye degradation, J. Membr. Sci., 2020, 598, 117804 CrossRef CAS.
- R. Zolfaghari, A. Fakhru’l-Razi, L. C. Abdullah, S. S. E. H. Elnashaie and A. Pendashteh, Demulsification techniques of water-in-oil and oil-in-water emulsions in petroleum industry, Sep. Purif. Technol., 2016, 170, 377–407 CrossRef CAS.
- L. J. Wang, J. Y. Zhang, S. Wang, J. G. Yu, W. J. H. Hu and F. P. Jiao, Preparation of a polystyrene-based super-hydrophilic mesh and evaluation of its oil/water separation performance, J. Membr. Sci., 2020, 597, 117747 CrossRef CAS.
- G. Kwon, A. K. Kota, Y. X. Li, A. Sohani, J. M. Mabry and A. Tuteja, On-demand separation of oil-water mixtures, Adv. Mater., 2012, 24, 3666–3671 CrossRef CAS.
- X. Gao, J. Zhou, R. Du, Z. Xie, S. Deng, R. Liu, Z. Liu and J. Zhang, Robust superhydrophobic foam: a graphdiyne-based hierarchical architecture for oil/water separation, Adv. Mater., 2016, 28, 168–173 CrossRef CAS.
- H. Huang, Z. Song, N. Wei, L. Shi, Y. Mao, Y. Ying, L. Sun, Z. Xu and X. Peng, Ultrafast viscous water flow through nanostrand-channelled graphene oxide membranes, Nat. Commun., 2013, 4, 2979 CrossRef.
- J. R. Wang, X. F. Wang, S. Zhao, B. Sun, Z. Wang and J. X. Wang, Robust superhydrophobic mesh coated by PANI/TiO2 nanoclusters for oil/water separation with high flux, self-cleaning, photodegradation and anti-corrosion, Sep. Purif. Technol., 2020, 235, 116166 CrossRef CAS.
- D. V. Bhalani, A. K. S. Chandel, J. S. Trivedi, S. Roy and S. K. Jewrajka, High molecular weight poly(vinyl pyrrolidone) induces hierarchical surface morphology in poly(vinylidene fluoride) membrane and facilitates separation of oil-water emulsions, J. Membr. Sci., 2018, 566, 415–427 CrossRef CAS.
- Y. Deng, G. W. Zhang, R. B. Bai, S. S. Shen, X. J. Zhou and I. Wyman, Fabrication of superhydrophilic and underwater superoleophobic membranes via an in situ crosslinking blend strategy for highly efficient oil/water emulsion separation, J. Membr. Sci., 2019, 569, 60–70 CrossRef CAS.
- F. Zhang, S. J. Gao, Y. Z. Zhu and J. Jin, Alkaline-induced superhydrophilic/underwater superoleophobic polyacrylonitrile membranes with ultralow oil-adhesion for high-efficient oil/water separation, J. Membr. Sci., 2016, 513, 67–73 CrossRef CAS.
- F. Zhang, W. B. Zhang, Y. Yu, B. Deng, J. Y. Li and J. Jin, Sol–gel preparation of PAA-g-PVDF/TiO2 nanocomposite hollow fiber membranes with extremely high water flux and improved antifouling property, J. Membr. Sci., 2013, 432, 25–32 CrossRef CAS.
- T. Mimi, X. Lixin, L. Fu and J. Lei, An intelligent superwetting PVDF membrane showing switchable transport performance for oil/water separation, Adv. Mater., 2014, 26, 2943–2948 CrossRef.
- Y. Liao, C. H. Loh, M. Tian, R. Wang and A. G. Fane, Progress in electrospun polymeric nanofibrous membranes for water treatment: Fabrication, modification and applications, Prog. Polym. Sci., 2018, 77, 69–94 CrossRef CAS.
- F. Zhang, W. B. Zhang, Z. Shi, D. Wang, J. Jin and L. Jiang, Nanowire-haired inorganic membranes with superhydrophilicity and underwater ultralow adhesive superoleophobicity for high-efficiency oil/water separation, Adv. Mater., 2013, 25, 4192–4198 CrossRef CAS.
- B. Zhan, Y. Liu, S. Y. Li, C. Kaya, T. Stegmaier, M. Aliabadi, Z. W. Han and L. Q. Ren, Fabrication of superwetting Cu@Cu2O cubic film for oil/water emulsion separation and photocatalytic degradation, Appl. Surf. Sci., 2019, 496, 143580 CrossRef CAS.
- C. C. Ma, Y. J. Li, P. Nian, H. O. Liu, J. S. Qiu and X. F. Zhang, Fabrication of oriented metal-organic framework nanosheet membrane coated stainless steel meshes for highly efficient oil/water separation, Sep. Purif. Technol., 2019, 229, 115835 CrossRef CAS.
- Z. J. Wang, Y. Wang and G. J. Liu, Rapid and efficient separation of oil from oil-in-water emulsions using a janus cotton fabric, Angew. Chem., Int. Ed., 2016, 55, 1291–1294 CrossRef CAS.
- J. Ge, F. Wang, X. Yin, J. Yu and B. Ding, Polybenzoxazine-functionalized melamine sponges with enhanced selective capillarity for efficient oil spill cleanup, ACS Appl. Mater. Interfaces, 2018, 10, 40274–40285 CrossRef CAS.
- L. W. Chen, Y. F. Si, H. Zhu, T. Jiang and Z. G. Guo, A study on the fabrication of porous PVDF membranes by in-situ elimination and their applications in separating oil/water mixtures and nano-emulsions, J. Membr. Sci., 2016, 520, 760–768 CrossRef CAS.
- F. Tian, Y. Yang, X. L. Wang, W. L. An, X. Zhao, S. M. Xu and Y. Z. Wang, From waste epoxy resins to efficient oil/water separation materials via a microwave assisted pore-forming strategy, Mater. Horiz., 2019, 6, 1733–1739 RSC.
- Z. L. Chu, Y. J. Feng and S. Seeger, Oil/water separation with selective superantiwetting/superwetting surface materials, Angew. Chem., Int. Ed., 2015, 54, 2328–2338 CrossRef CAS.
- B. Wang, W. X. Liang, Z. G. Guo and W. M. Liu, Biomimetic super-lyophobic and super-lyophilic materials applied for oil/water separation: a new strategy beyond nature, Chem. Soc. Rev., 2015, 44, 336–361 RSC.
- Z. Zhu, W. Wang, D. Qi, Y. Luo, Y. Liu, Y. Xu, F. Cui, C. Wang and X. Chen, Calcinable polymer membrane with revivability for efficient oily-water remediation, Adv. Mater., 2018, 30, 1801870 CrossRef.
- J. Ge, D. Zong, Q. Jin, J. Yu and B. Ding, Biomimetic and superwettable nanofibrous skins for highly efficient separation of oil-in-water emulsions, Adv. Funct. Mater., 2018, 28, 1705051 CrossRef.
- Y. Chen and C. S. Dutcher, Size dependent droplet interfacial tension and surfactant transport in liquid-liquid systems, with applications in shipboard oily bilgewater emulsions, Soft Matter, 2020, 16, 2994–3004 RSC.
- B. R. Solomon, M. N. Hyder and K. K. Varanasi, Separating oil-water nanoemulsions using flux-enhanced hierarchical membranes, Sci. Rep., 2014, 4, 5504 CrossRef CAS.
- M. Z. Ge, C. Y. Cao, J. Y. Huang, X. N. Zhang, Y. X. Tang, X. R. Zhou, K. Q. Zhang, Z. Chen and Y. K. Lai, Rational design of materials interface at nanoscale towards intelligent oil–water separation, Nanoscale Horiz., 2018, 3, 235–260 RSC.
- W. F. Zhang, N. Liu, Y. Z. Cao, X. Lin, Y. N. Liu and L. Feng, Superwetting porous materials for wastewater treatment: from immiscible oil/water mixture to emulsion separation, Adv. Mater. Interfaces, 2017, 4, 1600029 CrossRef.
- Z. X. Wang, X. B. Yang, Z. J. Cheng, Y. Y. Liu, L. Shao and L. Jiang, Simply realizing “water diode” Janus membranes for multifunctional smart applications, Mater. Horiz., 2017, 4, 701–708 RSC.
- X. Gao, L. P. Xu, Z. Xue, L. Feng, J. Peng, Y. Wen, S. Wang and X. Zhang, Dual-scaled porous nitrocellulose membranes with underwater superoleophobicity for highly efficient oil/water separation, Adv. Mater., 2014, 26, 1771–1775 CrossRef CAS.
- V. Carpintero-Tepole, E. Brito-de la Fuente and B. Torrestiana-Sánchez, Microfiltration of oil in water (O/W) emulsions: effect of membrane microstructure and surface properties, Chem. Eng. Res. Des., 2017, 126, 286–296 CrossRef CAS.
- K. Liu, X. Yao and L. Jiang, Recent developments in bio-inspired special wettability, Chem. Soc. Rev., 2010, 39, 3240–3255 RSC.
- J. L. Yong, F. Chen, Q. Yang, J. L. Huo and X. Hou, Superoleophobic surfaces, Chem. Soc. Rev., 2017, 46, 4168–4217 RSC.
- M. Liu, S. Wang, Z. Wei, Y. Song and L. Jiang, Bioinspired design of a superoleophobic and low adhesive water/solid interface, Adv. Mater., 2009, 21, 665–669 CrossRef CAS.
- Q. F. Wang, Y. Wang, B. X. Wang, Z. Q. Liang, J. C. Di and J. H. Yu, Under-liquid dual superlyophobic nanofibrous polymer membranes achieved by coating thin-film composites: a design principle, Chem. Sci., 2019, 10, 6382–6389 RSC.
- L. Hu, S. Gao, X. Ding, D. Wang, J. Jiang, J. Jin and L. Jiang, Photothermal-responsive single-walled carbon nanotube-based ultrathin membranes for on/off switchable separation of oil-in-water nanoemulsions, ACS Nano, 2015, 9, 4835–4842 CrossRef CAS.
- C. L. Zhang and S. H. Yu, Spraying functional fibres by electrospinning, Mater. Horiz., 2016, 3, 266–269 RSC.
- R. J. Wade and J. A. Burdick, Advances in nanofibrous scaffolds for biomedical applications: From electrospinning to self-assembly, Nano Today, 2014, 9, 722–742 CrossRef CAS.
- Kenry and C. T. Lim, Nanofiber technology: current status and emerging developments, Prog. Polym. Sci., 2017, 70, 1–17 CrossRef CAS.
- S. K. Nataraj, K. S. Yang and T. M. Aminabhavi, Polyacrylonitrile-based nanofibers—A state-of-the-art review, Prog. Polym. Sci., 2012, 37, 487–513 CrossRef CAS.
- G. L. Wang, D. M. Yu, A. D. Kelkar and L. F. Zhang, Electrospun nanofiber: Emerging reinforcing filler in polymer matrix composite materials, Prog. Polym. Sci., 2017, 75, 73–107 CrossRef CAS.
- L. L. Hou, N. Wang, J. Wu, Z. M. Cui, L. Jiang and Y. Zhao, Bioinspired superwettability electrospun micro/nanofibers and their applications, Adv. Funct. Mater., 2018, 28, 1801114 CrossRef.
- X. Wang, J. Yu, G. Sun and B. Ding, Electrospun nanofibrous materials: a versatile medium for effective oil/water separation, Mater. Today, 2016, 19, 403–414 CrossRef CAS.
- L. Feng, Z. Zhang, Z. Mai, Y. Ma, B. Liu, L. Jiang and D. Zhu, A super-hydrophobic and super-oleophilic coating mesh film for the separation of oil and water, Angew. Chem., Int. Ed., 2004, 116, 2046–2048 CrossRef.
- C. Shin, G. G. Chase and D. H. Reneker, Recycled expanded polystyrene nanofibers applied in filter media, Colloids Surf., A, 2005, 262, 211–215 CrossRef CAS.
- X. Wang, D. Fang, K. Yoon, B. S. Hsiao and B. Chu, High performance ultrafiltration composite membranes based on poly(vinyl alcohol) hydrogel coating on crosslinked nanofibrous poly(vinyl alcohol) scaffold, J. Membr. Sci., 2006, 278, 261–268 CrossRef CAS.
- Z. Xue, S. Wang, L. Lin, L. Chen, M. Liu, L. Feng and L. Jiang, A novel superhydrophilic and underwater superoleophobic hydrogel-coated mesh for oil/water separation, Adv. Mater., 2011, 23, 4270–4273 CrossRef CAS.
- M. Huang, Y. Si, X. Tang, Z. Zhu, B. Ding, L. Liu, G. Zheng, W. Luo and J. Yu, Gravity driven separation of emulsified oil-water mixtures utilizing in situ polymerized superhydrophobic and superoleophilic nanofibrous membranes, J. Mater. Chem. A, 2013, 1, 14071–14074 RSC.
- S. Yang, Y. Si, Q. Fu, F. Hong, J. Yu, S. S. Al-Deyab, M. El-Newehy and B. Ding, Superwetting hierarchical porous silica nanofibrous membranes for oil/water microemulsion separation, Nanoscale, 2014, 6, 12445–12449 RSC.
- Y. Si, J. Yu, X. Tang, J. Ge and B. Ding, Ultralight nanofibre-assembled cellular aerogels with superelasticity and multifunctionality, Nat. Commun., 2014, 5, 5802 CrossRef.
- J. J. Li, Y. N. Zhou and Z. H. Luo, Smart fiber membrane for ph-induced oil/water separation, ACS Appl. Mater. Interfaces, 2015, 7, 19643–19650 CrossRef CAS.
- H. L. Che, M. Huo, L. Peng, T. Fang, N. Liu, L. Feng, Y. Wei and J. Y. Yuan, CO2-responsive nanofibrous membranes with switchable oil/water wettability, Angew. Chem., Int. Ed., 2015, 54, 8934–8938 CrossRef CAS.
- J. L. Ge, J. C. Zhang, F. Wang, Z. L. Li, J. Y. Yu and B. Ding, Superhydrophilic and
underwater superoleophobic nanofibrous membrane with hierarchical structured skin for effective oil-in-water emulsion separation, J. Mater. Chem. A, 2017, 5, 497–502 RSC.
- H. S. Kang, H. Cho, W. Panatdasirisuk and S. Yang, Hierarchical membranes with size-controlled nanopores from photofluidization of electrospun azobenzene polymer fibers, J. Mater. Chem. A, 2017, 5, 18762–18769 RSC.
- L. Jiang, Y. Zhao and J. Zhai, A lotus-leaf-like superhydrophobic surface: A porous microsphere/nanofiber composite film prepared by electrohydrodynamics, Angew. Chem., Int. Ed., 2004, 43, 4338–4341 CrossRef CAS.
- J. Y. Lin, Y. Cai, X. F. Wang, B. Ding, J. Y. Yu and M. R. Wang, Fabrication of biomimetic superhydrophobic surfaces inspired by lotus leaf and silver ragwort leaf, Nanoscale, 2011, 3, 1258–1262 RSC.
- M. W. Lee, S. An, S. S. Latthe, C. Lee, S. Hong and S. S. Yoon, Electrospun polystyrene nanofiber membrane with superhydrophobicity and superoleophilicity for selective separation of water and low viscous oil, ACS Appl. Mater. Interfaces, 2013, 5, 10597–10604 CrossRef CAS.
- X. Li, C. Wang, Y. Yang, X. F. Wang, M. F. Zhu and B. S. Hsiao, Dual-biomimetic superhydrophobic electrospun polystyrene nanofibrous membranes for membrane distillation, ACS Appl. Mater. Interfaces, 2014, 6, 2431–2438 CrossRef.
- J. Wu, N. Wang, L. Wang, H. Dong, Y. Zhao and L. Jiang, Electrospun porous structure fibrous film with high oil adsorption capacity, ACS Appl. Mater. Interfaces, 2012, 4, 3207–3212 CrossRef CAS.
- W. S. Y. Wong, N. Nasiri, G. Y. Liu, N. Rumsey-Hill, V. S. J. Craig, D. R. Nisbet and A. Tricoli, Flexible transparent hierarchical nanomesh for rose petal-like droplet manipulation and lossless transfer, Adv. Mater. Interfaces, 2015, 2, 1500071 CrossRef.
- R. Asmatulu, M. Ceylan and N. Nuraje, Study of superhydrophobic electrospun nanocomposite fibers for energy systems, Langmuir, 2011, 27, 504–507 CrossRef CAS.
- B. T. Song, J. Zhu and H. M. Fan, Magnetic fibrous sorbent for remote and efficient oil adsorption, Mar. Pollut. Bull., 2017, 120, 159–164 CrossRef CAS.
- J. Li, P. Guan, M. J. Li, Y. Zhang, P. P. Cheng and R. A. Jia, Anticorrosive superhydrophobic polystyrene-coated mesh for continuous oil spill clean-up, New J. Chem., 2017, 41, 4862–4868 RSC.
- P. Y. Chen and S. H. Tung, One-step electrospinning to produce nonsolvent-induced macroporous fibers with ultrahigh oil adsorption capability, Macromolecules, 2017, 50, 2528–2534 CrossRef CAS.
- N. Xu, J. Cao and Y. Lu, The electrospinning P(Sty-co-BuA) of the copolymer of styrene and butyl acrylate for its application as oil absorbent, SpringerPlus, 2016, 5, 1383 CrossRef.
- M. L. Ma, R. M. Hill, J. L. Lowery, S. V. Fridrikh and G. C. Rutledge, Electrospun poly(styrene-block-dimethylsiloxane) block copolymer fibers exhibiting superhydrophobicity, Langmuir, 2005, 21, 5549–5554 CrossRef CAS.
- N. Xu, J. Cao and Y. Lu, The structure and property evaluation of electrospun porous fibrous membrane based on the copolymer of styrene and butyl acrylate, J. Porous Mater., 2015, 22, 1539–1548 CrossRef CAS.
- P. Yao, J. Gu, X. Lei, W. Sun, Y. Chen and Q. Zhang, Highly soluble and thermally stable copolyimides modified with trifluoromethyl and siloxane, J. Appl. Polym. Sci., 2015, 132, 41713 CrossRef.
- L. Tian, C. Zhang, X. He, Y. Guo, M. Qiao, J. Gu and Q. Zhang, Novel reusable porous polyimide fibers for hot-oil adsorption, J. Hazard. Mater., 2017, 340, 67–76 CrossRef CAS.
- Z. G. Zhu, Y. R. Liu, H. Q. Hou, W. X. Shi, F. S. Qu, F. Y. Cui and W. Wang, Dual-bioinspired design for constructing membranes with superhydrophobicity for direct contact membrane distillation, Environ. Sci. Technol., 2018, 52, 3027–3036 CrossRef CAS.
- Y. Ding, H. Hou, Y. Zhao, Z. Zhu and H. Fong, Electrospun polyimide nanofibers and their applications, Prog. Polym. Sci., 2016, 61, 67–103 CrossRef CAS.
- C. Cojocaru, P. P. Dorneanu, A. Airinei, N. Olaru, P. Samoila and A. Rotaru, Design and evaluation of electrospun polysulfone fibers and polysulfone/NiFe204 nanostructured composite as sorbents for oil spill cleanup, J. Taiwan Inst. Chem. Eng., 2017, 70, 267–281 CrossRef CAS.
- S. Lee, B. Kim, S. H. Kim, E. Kim and J. H. Jang, Superhydrophobic, reversibly elastic, moldable, and electrospun (SupREME) fibers with multimodal functions: from oil absorbents to local drug delivery adjuvants, Adv. Funct. Mater., 2017, 27, 1702310 CrossRef.
- X. Li, N. Wang, G. Fan, J. Yu, J. Gao, G. Sun and B. Ding, Electreted polyetherimide-silica fibrous membranes for enhanced filtration of fine particles, J. Colloid Interface Sci., 2015, 439, 12–20 CrossRef CAS.
- S. Guo, Q. Ke, C. Huang, X. Jin and Y. Cao, Wettability improvement of poly(butylene terephthalate) nanofibrous mats prepared via electrospinning by blending with regenerated silk fibroin, J. Macromol. Sci., Part B: Phys., 2014, 53, 1629–1641 CrossRef CAS.
- J. Zhao, Y. Li, J. Sheng, X. Wang, L. Liu, J. Yu and B. Ding, Environmentally friendly and breathable fluorinated polyurethane fibrous membranes exhibiting robust waterproof performance, ACS Appl. Mater. Interfaces, 2017, 9, 29302–29310 CrossRef CAS.
- G. Viswanadam and G. G. Chase, Water-diesel secondary dispersion separation using superhydrophobic tubes of nanofibers, Sep. Purif. Technol., 2013, 104, 81–88 CrossRef CAS.
- S. U. Patel and G. G. Chase, Separation of water droplets from water-in-diesel dispersion using superhydrophobic polypropylene fibrous membranes, Sep. Purif. Technol., 2014, 126, 62–68 CrossRef CAS.
- W. Yuan, P. Y. Gu, C. J. Lu, K. Q. Zhang, Q. F. Xu and J. M. Lu, Switchable fluorescent AIE-active nanoporous fibers for cyclic oil adsorption, RSC Adv., 2014, 4, 17255–17261 RSC.
- C. T. Liu and Y. L. Liu, pH-Induced switches of the oil- and water-selectivity of crosslinked polymeric membranes for gravity-driven oil-water separation, J. Mater. Chem. A, 2016, 4, 13543–13548 RSC.
- B. T. Song and Q. Xu, Highly hydrophobic and superoleophilic nanofibrous mats with controllable pore sizes for efficient oil/water separation, Langmuir, 2016, 32, 9960–9966 CrossRef CAS.
- C. R. Reshmi, S. P. Sundaran, A. Juraij and S. Athiyanathil, Fabrication of superhydrophobic polycaprolactone/beeswax electrospun membranes for high-efficiency oil/water separation, RSC Adv., 2017, 7, 2092–2102 RSC.
- J. S. Hersey, S. T. Yohe and M. W. Grinstaff, Poly(epsilon-caprolactone) microfiber meshes for repeated oil retrieval, Environ. Sci.: Water Res. Technol., 2015, 1, 779–786 RSC.
- P. Zhang, R. P. Tian, R. H. Lv, B. Na and Q. X. Liu, Water-permeable polylactide blend membranes for hydrophilicity-based separation, Chem. Eng. J., 2015, 269, 180–185 CrossRef CAS.
- X. H. Li, K. Y. Teng, J. Shi, W. Wang, Z. W. Xu, H. Deng, H. M. Lv and F. Y. Li, Electrospun preparation of polylactic acid nanoporous fiber membranes via thermal-nonsolvent induced phase separation, J. Taiwan Inst. Chem. Eng., 2016, 60, 636–642 CrossRef CAS.
- A. Bhattacharjee, K. Kumar, A. Arora and D. S. Katti, Fabrication and characterization of Pluronic modified poly(hydroxybutyrate) fibers for potential wound dressing applications, Mater. Sci. Eng., C, 2016, 63, 266–273 CrossRef CAS.
- Y. Yan, V. Sencadas, J. S. Zhang, D. B. Wei and Z. Y. Jiang, Superomniphilic poly(glycerol sebacate)-poly(l-lactic acid) electrospun membranes for oil spill remediation, Adv. Mater. Interfaces, 2017, 4, 1700484 CrossRef.
- D. Zhang, X. Z. Jin, T. Huang, N. Zhang, X. D. Qi, J. H. Yang, Z. W. Zhou and Y. Wang, Electrospun fibrous membranes with dual-scaled porous structure: super hydrophobicity, super lipophilicity, excellent water adhesion, and anti-icing for highly efficient oil adsorption/separation, ACS Appl. Mater. Interfaces, 2019, 11, 5073–5083 CrossRef CAS.
- M. Klicova, A. Klapstova, J. Chvojka, B. Koprivova, V. Jencova and J. Horakova, Novel double-layered planar scaffold combining electrospun PCL fibers and PVA hydrogels with high shape integrity and water stability, Mater. Lett., 2020, 263, 127281 CrossRef CAS.
- W. Liu, G. Xi, X. Yang, X. Hao, M. Wang, Y. Feng, H. Chen and C. Shi, Poly(lactide-co-glycolide) grafted hyaluronic acid-based electrospun fibrous hemostatic fragments as a sustainable anti-infection and immunoregulation material, J. Mater. Chem. B, 2019, 7, 4997–5010 RSC.
- A. A. Babar, D. Miao, N. Ali, J. Zhao, X. Wang, J. Yu and B. Ding, Breathable and colorful cellulose acetate-based nanofibrous membranes for directional moisture transport, ACS Appl. Mater. Interfaces, 2018, 10, 22866–22875 CrossRef CAS.
- P. Wang, Y. Li, C. Zhang, F. Feng and H. Zhang, Sequential electrospinning of multilayer ethylcellulose/gelatin/ethylcellulose nanofibrous film for sustained release of curcumin, Food Chem., 2020, 308, 125599 CrossRef CAS.
- J. Ma, X. Wang, Q. Fu, Y. Si, J. Yu and B. Ding, Highly carbonylated cellulose nanofibrous membranes utilizing maleic anhydride grafting for efficient lysozyme adsorption, ACS Appl. Mater. Interfaces, 2015, 7, 15658–15666 CrossRef CAS.
- J. Wu, Y. Ding, J. Wang, T. Li, H. Lin, J. Wang and F. Liu, Facile fabrication of nanofiber- and micro/nanosphere-coordinated PVDF membrane with ultrahigh permeability of viscous water-in-oil emulsions, J. Mater. Chem. A, 2018, 6, 7014–7020 RSC.
- C. L. Su, Y. P. Li, Y. Z. Dai, F. Gao, K. X. Tang and H. B. Cao, Fabrication of three-dimensional superhydrophobic membranes with high porosity via simultaneous electrospraying and electrospinning, Mater. Lett., 2016, 170, 67–71 CrossRef CAS.
- Z. P. Zhou and X. F. Wu, Electrospinning superhydrophobic-superoleophilic fibrous PVDF membranes for high-efficiency water-oil separation, Mater. Lett., 2015, 160, 423–427 CrossRef CAS.
- Z. J. Liu, H. Y. Wang, E. Q. Wang, X. G. Zhang, R. X. Yuan and Y. J. Zhu, Superhydrophobic poly(vinylidene fluoride) membranes with controllable structure and tunable wettability prepared by one-step electrospinning, Polymer, 2016, 82, 105–113 CrossRef CAS.
- S. U. Patel, S. U. Patel and G. G. Chase, Electrospun superhydrophobic poly(vinylidene fluoride-co-hexafluoropropylene) fibrous membranes for the separation of dispersed water from ultralow sulfur diesel, Energy Fuels, 2013, 27, 2458–2464 CrossRef CAS.
- W. Qing, X. Shi, Y. Deng, W. Zhang, J. Wang and C. Y. Tang, Robust superhydrophobic-superoleophilic polytetrafluoroethylene nanofibrous membrane for oil/water separation, J. Membr. Sci., 2017, 540, 354–361 CrossRef CAS.
- Q. L. Ma, H. F. Cheng, A. G. Fane, R. Wang and H. Zhang, Recent development of advanced materials with special wettability for selective oil/water separation, Small, 2016, 12, 2186–2202 CrossRef CAS.
- S. Zarghami, T. Mohammadi, M. Sadrzadeh and B. Van der Bruggen, Superhydrophilic and underwater superoleophobic membranes – review of synthesis methods, Prog. Polym. Sci., 2019, 98, 101166 CrossRef CAS.
- N. H. Ismail, W. N. W. Salleh, A. F. Ismail, H. Hasbullah, N. Yusof, F. Aziz and J. Jaafar, Hydrophilic polymer-based membrane for oily wastewater treatment: A review, Sep. Purif. Technol., 2020, 233, 116007 CrossRef CAS.
- Y. M. Lin, C. Song and G. C. Rutledge, Direct three-dimensional visualization of membrane fouling by confocal laser scanning microscopy, ACS Appl. Mater. Interfaces, 2019, 11, 17001–17008 CrossRef CAS.
- Y. Liang, S. Kim, P. Kallem and H. Choi, Capillary effect in Janus electrospun nanofiber membrane for oil/water emulsion separation, Chemosphere, 2019, 221, 479–485 CrossRef CAS.
- J. Zhang, X. Pan, Q. Xue, D. He, L. Zhu and Q. Guo, Antifouling hydrolyzed polyacrylonitrile/graphene oxide membrane with spindle-knotted structure for highly effective separation of oil-water emulsion, J. Membr. Sci., 2017, 532, 38–46 CrossRef CAS.
- H. S. Lim, S. H. Park, S. H. Koo, Y. J. Kwark, E. L. Thomas, Y. Jeong and J. H. Cho, Superamphiphilic Janus Fabric, Langmuir, 2010, 26, 19159–19162 CrossRef CAS.
- M. M. Zhu, D. W. Hua, H. Pan, F. Wang, B. Manshian, S. J. Soenen, R. H. Xiong and C. B. Huang, Green electrospun and crosslinked poly(vinyl alcohol)/poly(acrylic acid) composite membranes for antibacterial effective air filtration, J. Colloid Interface Sci., 2018, 511, 411–423 CrossRef CAS.
- J. Fan, Y. Song, S. Wang, J. Meng, G. Yang, X. Guo, L. Feng and L. Jiang, Directly coating hydrogel on filter paper for effective oil-water separation in highly acidic, alkaline, and salty environment, Adv. Funct. Mater., 2015, 25, 5368–5375 CrossRef CAS.
- P. Muthiah, T. J. Boyle and W. Sigmund, Thermally Induced, Rapid Wettability Switching of Electrospun Blended Polystyrene/Poly(N-Isopropylacrylamide) Nanofiber Mats, Macromol. Mater. Eng., 2013, 298, 1251–1258 CrossRef CAS.
- P. Muthiah, S. M. Hoppe, T. J. Boyle and W. Sigmund, Thermally tunable surface wettability of electrospun fiber mats: polystyrene/poly(N-isopropylacrylamide) blended versus crosslinked poly(N-isopropylacrylamide)-co-(methacrylic acid), Macromol. Rapid Commun., 2011, 32, 1716–1721 CrossRef CAS.
- S. Y. Gu, Z. M. Wang, J. B. Li and J. Ren, Switchable wettability of thermo-responsive biocompatible nanofibrous films created by electrospinning, Macromol. Mater. Eng., 2010, 295, 32–36 CrossRef CAS.
- N. Wang, Y. Zhao and L. Jiang, Low-cost, thermoresponsive wettability of surfaces: Poly(N-isopropylacrylamide)/polystyrene composite films prepared by electrospinning, Macromol. Rapid Commun., 2008, 29, 485–489 CrossRef CAS.
- J. J. Li, L. T. Zhu and Z. H. Luo, Electrospun fibrous membrane with enhanced swithchable oil/water wettability for oily water separation, Chem. Eng. J., 2016, 287, 474–481 CrossRef CAS.
- Y. Liu, S. Tas, K. H. Zhang, W. M. de Vos, J. H. Ma and G. J. Vancso, Thermoresponsive Membranes from Electrospun Mats with Switchable Wettability for Efficient Oil/Water Separations, Macromolecules, 2018, 51, 8435–8442 CrossRef CAS.
- J. J. Li, Y. N. Zhou, Z. D. Jiang and Z. H. Luo, Electrospun fibrous mat with ph-switchable superwettability that can separate layered oil/water mixtures, Langmuir, 2016, 32, 13358–13366 CrossRef CAS.
- M. W. Lee, S. An, B. Joshi, S. S. Latthe and S. S. Yoon, Highly efficient wettability control via three-dimensional (3D) suspension of titania nanoparticles in polystyrene nanofibers, ACS Appl. Mater. Interfaces, 2013, 5, 1232–1239 CrossRef CAS.
- M. Chen and F. Besenbacher, Light-driven wettability changes on a photoresponsive electrospun mat, ACS Nano, 2011, 5, 1549–1555 CrossRef CAS.
- W. J. Ma, S. K. Samal, Z. C. Liu, R. H. Xiong, S. C. De Smedt, B. Bhushan, Q. L. Zhang and C. B. Huang, Dual pH- and ammonia-vapor-responsive electrospun nanofibrous membranes for oil-water separations, J. Membr. Sci., 2017, 537, 128–139 CrossRef CAS.
- H. Chen and Y. L. Hsieh, Ultrafine hydrogel fibers with dual temperature- and pH-responsive swelling behaviors, J. Polym. Sci., Part A: Polym. Chem., 2004, 42, 6331–6339 CrossRef CAS.
- L. Chen, S. Wang, Q. Yu, P. D. Topham, C. Chen and L. Wang, A comprehensive review of electrospinning block copolymers, Soft Matter, 2019, 15, 2490–2510 RSC.
- T. Bharathidasan, T. N. Narayanan, S. Sathyanaryanan and S. S. Sreejakumari, Above 170° water contact angle and oleophobicity of fluorinated graphene oxide based transparent polymeric films, Carbon, 2015, 84, 207–213 CrossRef CAS.
- H. Y. Mi, X. Jing, H. Xie, H. X. Huang and L. S. Turng, Magnetically driven superhydrophobic silica sponge decorated with hierarchical cobalt nanoparticles for selective oil absorption and oil/water separation, Chem. Eng. J., 2018, 337, 541–551 CrossRef CAS.
- J. L. Sheng, Y. Xu, J. Y. Yu and B. Ding, Robust fluorine-free superhydrophobic amino-silicone oil/SiO2 modification of electrospun polyacrylonitrile membranes for waterproof-breathable application, ACS Appl. Mater. Interfaces, 2017, 9, 15139–15147 CrossRef CAS.
- W. Zhu, J. Zhao, X. Wang, X. Liu, J. Yu and B. Ding, Facile fabrication of fluorine-free breathable poly(methylhydrosiloxane)/polyurethane fibrous membranes with enhanced water-resistant capability, J. Colloid Interface Sci., 2019, 556, 541–548 CrossRef CAS.
- Z. Q. Dong, B. J. Wang, X. H. Ma, Y. M. Wei and Z. L. Xu, FAS grafted electrospun poly(vinyl alcohol) nanofiber membranes with robust superhydrophobicity for membrane distillation, ACS Appl. Mater. Interfaces, 2015, 7, 22652–22659 CrossRef CAS.
- Y. W. Shang, Y. Si, A. Raza, L. P. Yang, X. Mao, B. Ding and J. Y. Yu, An in situ polymerization approach for the synthesis of superhydrophobic and superoleophilic nanofibrous membranes for oil-water separation, Nanoscale, 2012, 4, 7847–7854 RSC.
- L. D. Tijing, Y. C. Woo, W. G. Shim, T. He, J. S. Choi, S. H. Kim and H. K. Shon, Superhydrophobic nanofiber membrane containing carbon nanotubes for high-performance direct contact membrane distillation, J. Membr. Sci., 2016, 502, 158–170 CrossRef CAS.
- H. W. Yang, Y. Lan, W. Zhu, W. N. Li, D. Xu, J. C. Cui, D. Z. Shen and G. T. Li, Polydopamine-coated nanofibrous mats as a versatile platform for producing porous functional membranes, J. Mater. Chem., 2012, 22, 16994–17001 RSC.
- W. Hao, C. Marichy and A. Brioude, Promising properties of ALD boron nitride nanotube mats for water purification, Environ. Sci.: Nano, 2017, 4, 2311–2320 RSC.
- L. Wang, Y. Zhao, Y. Tian and L. Jiang, A general strategy for the separation of immiscible organic liquids by manipulating the surface tensions of nanofibrous membranes, Angew. Chem., Int. Ed., 2015, 54, 14732–14737 CrossRef CAS.
- K. Zhang, Q. Li, J. Wu and W. Hong, Preparation of PVDF-HFP@FAS electrospun fibrous film with special wettability and the research of its oil-water separation performance, Integr. Ferroelectr., 2017, 182, 218–227 CrossRef CAS.
- L. F. Wang, S. Y. Yang, J. Wang, C. F. Wang and L. Chen, Fabrication of superhydrophobic TPU film for oil-water separation based on electrospinning route, Mater. Lett., 2011, 65, 869–872 CrossRef CAS.
- J. Wu, A. K. An, J. Guo, E.-J. Lee, M. U. Farid and S. Jeong, CNTs reinforced super-hydrophobic-oleophilic electrospun polystyrene oil sorbent for enhanced sorption capacity and reusability, Chem. Eng. J., 2017, 314, 526–536 CrossRef CAS.
- S. Wang, Q. W. Liu, Y. Zhang, S. D. Wang, Y. X. Li, Q. B. Yang and Y. Song, Preparation of a multifunctional material with superhydrophobicity, superparamagnetism, mechanical stability and acids-bases resistance by electrospinning, Appl. Surf. Sci., 2013, 279, 150–158 CrossRef CAS.
- O. Arslan, Z. Aytac and T. Uyar, Superhydrophobic, hybrid, electrospun cellulose acetate nanofibrous mats for oil/water separation by tailored surface modification, ACS Appl. Mater. Interfaces, 2016, 8, 19747–19754 CrossRef CAS.
- Z. J. Liu, H. Y. Wang, X. G. Zhang, C. J. Wang, C. J. Lv and Y. J. Zhu, Durable and self-healing superhydrophobic surface with bistratal gas layers prepared by electrospinning and hydrothermal processes, Chem. Eng. J., 2017, 326, 578–586 CrossRef CAS.
- S. M. S. Shahabadi, H. Rabiee, S. M. Seyedi, A. Mokhtare and J. A. Brant, Superhydrophobic dual layer functionalized titanium dioxide/polyvinylidene fluoride-co-hexafluoropropylene (TiO2/PH) nanofibrous membrane for high flux membrane distillation, J. Membr. Sci., 2017, 537, 140–150 CrossRef.
- H. Z. Tang, H. Wang and J. H. He, Superhydrophobic Titania Membranes of Different Adhesive Forces Fabricated by Electrospinning, J. Phys. Chem. C, 2009, 113, 14220–14224 CrossRef CAS.
- H. X. Sun, Y. Y. Xu, Y. Y. Zhou, W. Gao, H. R. Zhao and W. G. Wang, Preparation of superhydrophobic nanocomposite fiber membranes by electrospinning poly(vinylidene fluoride)/silane coupling agent modified SiO2 nanoparticles, J. Appl. Polym. Sci., 2017, 134, 44501 Search PubMed.
- H. S. Lim, J. H. Baek, K. Park, H. S. Shin, J. Kim and J. H. Cho, Multifunctional Hybrid Fabrics with Thermally Stable Superhydrophobicity, Adv. Mater., 2010, 22, 2138–2141 CrossRef CAS.
- S. S. Ouyang, T. Wang, X. Y. Jia, Y. Chen, J. M. Yao and S. Wang, Self-indicating and recyclable superhydrophobic membranes for effective oil/water separation in harsh conditions, Mater. Des., 2016, 96, 357–363 CrossRef CAS.
- X. Li, X. F. Yu, C. Cheng, L. Deng, M. Wang and X. F. Wang, Electrospun superhydrophobic organic/inorganic composite nanofibrous membranes for membrane distillation, ACS Appl. Mater. Interfaces, 2015, 7, 21919–21930 CrossRef CAS.
- S. J. Cao, F. Qiu, C. Xiong, X. J. Wang, G. Zhang, S. R. Long and J. Yang, Superhydrophobic PES/PDA/ODTS fibrous mat prepared by electrospinning and silanization modification for oil/water separation, J. Appl. Polym. Sci., 2018, 135, 45923 CrossRef.
- J. A. Kaplan, H. Y. Lei, R. Liu, R. Padera, Y. L. Colson and M. W. Grinstaff, Imparting (PLA-PGC18) superhydrophobicity to biodegradable poly(lactide-co-glycolide) electrospun meshes, Biomacromolecules, 2014, 15, 2548–2554 CrossRef CAS.
- J. Zhao, W. Zhu, X. Wang, L. Liu, J. Yu and B. Ding, Fluorine-free waterborne coating for environmentally friendly, robustly water-resistant, and highly breathable fibrous textiles, ACS Nano, 2020, 14, 1045–1054 CrossRef CAS.
- L. P. Yang, A. Raza, Y. Si, X. Mao, Y. W. Shang, B. Ding, J. Y. Yu and S. S. Al-Deyab, Synthesis of superhydrophobic silica nanofibrous membranes with robust thermal stability and flexibility via in situ polymerization, Nanoscale, 2012, 4, 6581–6587 RSC.
- K. M. Park, B. S. Lee, J. H. Youk, J. Lee and W. R. Yu, Moisture condensation behavior of hierarchically carbon nanotube-grafted carbon nanofibers, ACS Appl. Mater. Interfaces, 2013, 5, 11115–11122 CrossRef CAS.
- L. J. Ye, J. P. Guan, Z. X. Li, J. X. Zhao, C. C. Ye, J. C. You and Y. J. Li, Fabrication of Superhydrophobic Surfaces with Controllable Electrical Conductivity and Water Adhesion, Langmuir, 2017, 33, 1368–1374 CrossRef CAS.
- Y. C. Woo, L. D. Tijing, W. G. Shim, J. S. Choi, S. H. Kim, T. He, E. Drioli and H. K. Shon, Water desalination using graphene-enhanced electrospun nanofiber membrane via air gap membrane distillation, J. Membr. Sci., 2016, 520, 99–110 CrossRef CAS.
- A. Asthana, T. Maitra, R. Buchel, M. K. Tiwari and D. Poulikakos, Multifunctional superhydrophobic polymer/carbon nanocomposites: graphene, carbon nanotubes, or carbon black?, ACS Appl. Mater. Interfaces, 2014, 6, 8859–8867 CrossRef CAS.
- X. Deng, L. Mammen, H. J. Butt and D. Vollmer, Candle soot as a template for a transparent robust superamphiphobic coating, Science, 2012, 335, 67–70 CrossRef CAS.
- T. P. Lei, J. Y. Xiong, J. J. Huang, T. Zheng and X. M. Cai, Facile transformation of soot nanoparticles into nanoporous fibers via single-step electrospinning, AIP Adv., 2017, 7, 085212 CrossRef.
- A. Almasian, M. L. Jalali, G. C. Fard and L. Maleknia, Surfactant grafted PDA-PAN nanofiber: optimization of synthesis, characterization and oil absorption property, Chem. Eng. J., 2017, 326, 1232–1241 CrossRef CAS.
- X. Li, M. Wang, C. Wang, C. Cheng and X. F. Wang, Facile immobilization of Ag nanocluster on nanofibrous membrane for oil/water separation, ACS Appl. Mater. Interfaces, 2014, 6, 15272–15282 CrossRef CAS.
- H. Ji, R. Zhao, Y. M. Li, B. L. Sun, Y. Z. Li, N. Zhang, J. Qiu, X. Li and C. Wang, Robust and durable superhydrophobic electrospun nanofibrous mats via a simple Cu nanocluster immobilization for oil-water contamination, Colloids Surf., A, 2018, 538, 173–183 CrossRef CAS.
- J. Wu, N. Wang, Y. Zhao and L. Jiang, Simple synthesis of smart magnetically driven fibrous films for remote controllable oil removal, Nanoscale, 2015, 7, 2625–2632 RSC.
- Z. Shami, S. M. Amininasab and P. Shakeri, Structure-property relationships of nanosheeted 3D hierarchical roughness mgal-layered double hydroxide branched to an electrospun porous nanomembrane: a superior oil-removing nanofabric, ACS Appl. Mater. Interfaces, 2016, 8, 28964–28973 CrossRef CAS.
- N. Govinna, P. Kaner, D. Ceasar, A. Dhungana, C. Moers, K. Son, A. Asatekin and P. Cebe, Electrospun fiber membranes from blends of poly(vinylidene fluoride) with fouling-resistant zwitterionic copolymers, Polym. Int., 2019, 68, 231–239 CrossRef CAS.
- R. S. Kurusu and N. R. Demarquette, Blending and morphology control to turn hydrophobic SEBS electrospun mats superhydrophilic, Langmuir, 2015, 31, 5495–5503 CrossRef CAS.
- L. M. Buttaro, E. Drufva and M. W. Frey, Phase separation to create hydrophilic yet non-water soluble PLA/PLA-b-PEG fibers via electrospinning, J. Appl. Polym. Sci., 2014, 131, 41030 CrossRef.
- D. Vaikkath, R. Anitha, B. Sumathy and P. D. Nair, A simple and effective method for making multipotent/multilineage scaffolds with hydrophilic nature without any postmodification/treatment, Colloids Surf., B, 2016, 141, 112–119 CrossRef CAS.
- A. Asatekin, S. Kang, M. Elimelech and A. M. Mayes, Anti-fouling ultrafiltration membranes containing polyacrylonitrile-graft-poly(ethylene oxide) comb copolymer additives, J. Membr. Sci., 2007, 298, 136–146 CrossRef CAS.
- J. F. Hester and A. M. Mayes, Design and performance of foul-resistant poly(vinylidene fluoride) membranes prepared in a single-step by surface segregation, J. Membr. Sci., 2002, 202, 119–135 CrossRef CAS.
- A. Akthakul, R. F. Salinaro and A. Mayes, Antifouling polymer membranes with subnanometer size selectivity, Macromolecules, 2004, 37, 7663–7668 CrossRef CAS.
- R. S. Kurusu and N. R. Demarquette, Surface modification to control the water wettability of electrospun mats, Int. Mater. Rev., 2019, 64, 249–287 CrossRef CAS.
- J. Wang, L. A. Hou, K. K. Yan, L. Zhang and Q. L. Yu, Polydopamine nanocluster decorated electrospun nanofibrous membrane for separation of oil/water emulsions, J. Membr. Sci., 2018, 547, 156–162 CrossRef CAS.
- J. A. Lee, K. C. Krogman, M. L. Ma, R. M. Hill, P. T. Hammond and G. C. Rutledge, Highly reactive multilayer-assembled TiO2 coating on electrospun polymer nanofibers, Adv. Mater., 2009, 21, 1252–1256 CrossRef CAS.
- B. K. Shrestha, H. M. Mousa, A. P. Tiwari, S. W. Ko, C. H. Park and C. S. Kim, Development of polyamide-6,6/chitosan electrospun hybrid nanofibrous scaffolds for tissue engineering application, Carbohydr. Polym., 2016, 148, 107–114 CrossRef CAS.
- X. Shan, F. Li, C. Liu and Q. Gao, Electrospinning of chitosan/poly(lactic acid) nanofibers: The favorable effect of nonionic surfactant, J. Appl. Polym. Sci., 2014, 131, 41098 CrossRef.
- Z. X. Meng, W. Zheng, L. Li and Y. F. Zheng, Fabrication, characterization and in vitro drug release behavior of electrospun PLGA/chitosan nanofibrous scaffold, Mater. Chem. Phys., 2011, 125, 606–611 CrossRef CAS.
- P. Henke, H. Kozak, A. Artemenko, P. Kubat, J. Forstova and J. Mosinger, Superhydrophilic polystyrene nanofiber materials generating O-2((1)Delta(g)): postprocessing surface modifications toward efficient antibacterial effect, ACS Appl. Mater. Interfaces, 2014, 6, 13007–13014 CrossRef CAS.
- F. E. Ahmed, B. S. Lalia, N. Hilal and R. Hashaikeh, Underwater superoleophobic cellulose/electrospun PVDF-HFP membranes for efficient oil/water separation, Desalination, 2014, 344, 48–54 CrossRef.
- L. A. Goetz, B. Jalvo, R. Rosal and A. P. Mathew, Superhydrophilic anti-fouling electrospun cellulose acetate membranes coated with chitin nanocrystals for water filtration, J. Membr. Sci., 2016, 510, 238–248 CrossRef CAS.
- N. Tang, S. Zhang, Y. Si, J. Yu and B. Ding, An ultrathin bacterial cellulose membrane with a Voronoi-net structure for low pressure and high flux microfiltration, Nanoscale, 2019, 11, 17851–17859 RSC.
- L. D. Tijing, M. T. G. Ruelo, A. Amarjargal, H. R. Pant, C. H. Park, D. W. Kim and C. S. Kim, Antibacterial and superhydrophilic electrospun polyurethane nanocomposite fibers containing tourmaline nanoparticles, Chem. Eng. J., 2012, 197, 41–48 CrossRef CAS.
- M. K. Dufficy, M. T. Geiger, C. A. Bonino and S. A. Khan, Electrospun ultrafine fiber composites containing fumed silica: from solution rheology to materials with tunable wetting, Langmuir, 2015, 31, 12455–12463 CrossRef CAS.
- P. Lu, Q. Huang, A. Mukherjee and Y. L. Hsieh, SiCO-doped carbon fibers with unique dual superhydrophilicity/superoleophilicity and ductile and capacitance properties, ACS Appl. Mater. Interfaces, 2010, 2, 3738–3744 CrossRef CAS.
- J. Song, X. Wu, M. Zhang, C. Liu, J. Yu, G. Sun, Y. Si and B. Ding, Highly flexible, core-shell heterostructured, and visible-light-driven titania-based nanofibrous membranes for antibiotic removal and E. coli inactivation, Chem. Eng. J., 2020, 379, 122269 CrossRef CAS.
- X. Mao, Y. Bai, J. Yu, B. Ding and J. Ferreira, Flexible and highly temperature resistant polynanocrystalline zirconia nanofibrous membranes designed for air filtration, J. Am. Ceram. Soc., 2016, 99, 2760–2768 CrossRef CAS.
- D. D. Lin, H. Wu and W. Pan, Photoswitches and memories assembled by electrospinning aluminum-doped zinc oxide single nanowires, Adv. Mater., 2007, 19, 3968–3972 CrossRef CAS.
- J. Yan, Y. Han, S. Xia, X. Wang, Y. Zhang, J. Yu and B. Ding, Polymer template synthesis of flexible BaTIO3 crystal nanofiber, Adv. Funct. Mater., 2019, 29, 1907919 CrossRef CAS.
- C. Shao, N. Yu, Y. Liu and R. Mu, Preparation of LiCoO2 nanofibers
by electrospinning technique, J. Phys. Chem. Solids, 2006, 67, 1423–1426 CrossRef CAS.
- D. Li, T. Herricks and Y. Xia, Magnetic nanofibers of nickel ferrite prepared by electrospinning, Appl. Phys. Lett., 2003, 83, 4586–4588 CrossRef CAS.
- S. H. Lee, M. J. Jung, J. S. Im, K. Y. Sheem and Y. S. Lee, Preparation and characterization of electrospun LiFePO4/carbon complex improving rate performance at high C-rate, Res. Chem. Intermed., 2010, 36, 591–602 CrossRef CAS.
- N. Wang, Y. Y. Zhai, Y. Y. Yang, X. Yang and Z. G. Zhu, Electrostatic assembly of superwetting porous nanofibrous membrane toward oil-in-water microemulsion separation, Chem. Eng. J., 2018, 354, 463–472 CrossRef CAS.
- J. Lee, C. Boo, W. H. Ryu, A. D. Taylor and M. Elimelech, Development of omniphobic desalination membranes using a charged electrospun nanofiber scaffold, ACS Appl. Mater. Interfaces, 2016, 8, 11154–11161 CrossRef CAS.
- Y. Song, J. Zhou, J. Fan, W. Zhai, J. Meng and S. Wang, Hydrophilic/oleophilic magnetic janus particles for the rapid and efficient oil-water separation, Adv. Funct. Mater., 2018, 28, 1802493 CrossRef.
- Y. T. Cai, J. Song, X. Y. Liu, X. Yin, X. R. Li, J. Y. Yu and B. Ding, Soft BiOBr@TiO2 nanofibrous membranes with hierarchical heterostructures as efficient and recyclable visible-light photocatalysts, Environ. Sci.: Nano, 2018, 5, 2631–2640 RSC.
- F. Bai, J. T. Wu, G. M. Gong and L. Guo, Biomimetic “water strider leg” with highly refined nanogroove structure and remarkable water-repellent performance, ACS Appl. Mater. Interfaces, 2014, 6, 16237–16242 CrossRef CAS.
- Z. Chang, “Firecracker-shaped” ZnO/polyimide hybrid nanofibers via electrospinning and hydrothermal process, Chem. Commun., 2011, 47, 4427–4429 RSC.
- J. Zeng, X. X. Ji, Y. H. Ma, Z. X. Zhang, S. G. Wang, Z. H. Ren, C. Y. Zhi and J. Yu, 3D Graphene Fibers Grown by Thermal Chemical Vapor Deposition, Adv. Mater., 2018, 30, 1705380 CrossRef.
- W. J. Ma, M. J. Zhang, Z. C. Liu, C. B. Huang and G. D. Fu, Nature-inspired creation of a robust free-standing electrospun nanofibrous membrane for efficient oil-water separation, Environ. Sci.: Nano, 2018, 5, 2909–2920 RSC.
- Y. Zhang, J. Guan, X. Wang, J. Yu and B. Ding, Balsam-pear-skin-like porous polyacrylonitrile nanofibrous membranes grafted with polyethyleneimine for postcombustion CO2 capture, ACS Appl. Mater. Interfaces, 2017, 9, 41087–41098 CrossRef CAS.
- H. Liu, C. Y. Cao, F. F. Wei, P. P. Huang, Y. B. Sun, L. Jiang and W. G. Song, Flexible macroporous carbon nanofiber film with high oil adsorption capacity, J. Mater. Chem. A, 2014, 2, 3557–3562 RSC.
- J. Lin, B. Ding, J. Yang, J. Yu and G. Sun, Subtle regulation of the micro- and nanostructures of electrospun polystyrene fibers and their application in oil absorption, Nanoscale, 2012, 4, 176–182 RSC.
- L. Zhu, S. Y. Yang, J. Wang, C. F. Wang, L. Chen and S. Chen, Quantum-dot-embedded polymeric fiber films with photoluminescence and superhydrophobicity, Mater. Lett., 2013, 99, 54–56 CrossRef CAS.
- S. Zhang, H. Liu, X. Yin, J. Yu and B. Ding, Anti-deformed Polyacrylonitrile/Polysulfone Composite Membrane with Binary Structures for Effective Air Filtration, ACS Appl. Mater. Interfaces, 2016, 8, 8086–8095 CrossRef CAS.
- D. Zhang and J. Chang, Patterning of electrospun fibers using electroconductive templates, Adv. Mater., 2007, 19, 3664–3667 CrossRef CAS.
- F. Zuo, S. Zhang, H. Liu, H. Fong, X. Yin, J. Yu and B. Ding, Free-standing polyurethane nanofiber/nets air filters for effective PM Capture, Small, 2017, 13, 1702139 CrossRef.
- D. Y. Miao, Z. Huang, X. F. Wang, J. Y. Yu and B. Ding, Continuous, spontaneous, and directional water transport in the trilayered fibrous membranes for functional moisture wicking textiles, Small, 2018, 14, 1801527 CrossRef.
- H. Ma, C. Burger, B. S. Hsiao and B. Chu, Ultrafine polysaccharide nanofibrous membranes for water purification, Biomacromolecules, 2011, 12, 970–976 CrossRef CAS.
- M. Obaid, N. A. M. Barakat, O. A. Fadali, M. Motlak, A. A. Almajid and K. A. Khalil, Effective and reusable oil/water separation membranes based on modified polysulfone electrospun nanofiber mats, Chem. Eng. J., 2015, 259, 449–456 CrossRef CAS.
- H. Gao, Y. Yang, O. Akampumuza, J. Hou, H. Zhang and X. Qin, A low filtration resistance three-dimensional composite membrane fabricated via free surface electrospinning for effective PM2.5 capture, Environ. Sci.: Nano, 2017, 4, 864–875 RSC.
- D. Zhang and J. Chang, Electrospinning of three-dimensional nanofibrous tubes with controllable architectures, Nano Lett., 2008, 8, 3283–3287 CrossRef CAS.
- S. Zhang, H. Liu, J. Yu, W. Luo and B. Ding, Microwave structured polyamide-6 nanofiber/net membrane with embedded poly(m-phenylene isophthalamide) staple fibers for effective ultrafine particle filtration, J. Mater. Chem. A, 2016, 4, 6149–6157 RSC.
- S. Zhang, H. Liu, F. Zuo, X. Yin, J. Yu and B. Ding, A controlled design of ripple-like polyamide-6 nanofiber/nets membrane for high-efficiency air filter, Small, 2017, 13, 1603151 CrossRef.
- Z. T. Li, C. M. Tan, W. Tio, J. Ang and D. D. Sun, Manta ray gill inspired radially distributed nanofibrous membrane for efficient and continuous oil-water separation, Environ. Sci.: Nano, 2018, 5, 1466–1472 RSC.
- H. Wu, R. Zhang, Y. Sun, D. Lin, Z. Sun, W. Pan and P. Downs, Biomimetic nanofiber patterns with controlled wettability, Soft Matter, 2008, 4, 2429–2433 RSC.
- X. Wang, B. Ding, G. Sun, M. Wang and J. Yu, Electro-spinning/netting: A strategy for the fabrication of three-dimensional polymer nano-fiber/nets, Prog. Mater. Sci., 2013, 58, 1173–1243 CrossRef CAS.
- N. Wang, Y. Yang, S. S. Al-Deyab, M. El-Newehy, J. Yu and B. Ding, Ultra-light 3D nanofibre-nets binary structured nylon 6–polyacrylonitrile membranes for efficient filtration of fine particulate matter, J. Mater. Chem. A, 2015, 3, 23946–23954 RSC.
- H. Liu, S. Zhang, L. Liu, J. Yu and B. Ding, A fluffy dual-network structured nanofiber/net filter enables high-efficiency air filtration, Adv. Funct. Mater., 2019, 29, 1904108 CrossRef.
- B. W. Cheng, Z. J. Li, Q. X. Li, J. G. Ju, W. M. Kang and M. Naebe, Development of smart poly(vinylidene fluoride)-graft-poly(acrylic acid) tree-like nanofiber membrane for pH-responsive oil/water separation, J. Membr. Sci., 2017, 534, 1–8 CrossRef CAS.
- J. Zhang, L. Liu, Y. Si, J. Yu and B. Ding, Electrospun Nanofibrous Membranes: An Effective Arsenal for the Purification of Emulsified Oily Wastewater, Adv. Funct. Mater., 2020, 2002192, DOI:10.1002/adfm.202002192.
- X. Wang, K. Zhang, Y. Yang, L. Wang, Z. Zhou, M. Zhu, B. S. Hsiao and B. Chu, Development of hydrophilic barrier layer on nanofibrous substrate as composite membrane via a facile route, J. Membr. Sci., 2010, 356, 110–116 CrossRef CAS.
- A. Raza, B. Ding, G. Zainab, M. El-Newehy, S. S. Al-Deyab and J. Y. Yu, In situ cross-linked superwetting nanofibrous membranes for ultrafast oil-water separation, J. Mater. Chem. A, 2014, 2, 10137–10145 RSC.
- Y. S. Jiang, J. W. Hou, J. Xu and B. T. Shan, Switchable oil/water separation with efficient and robust Janus nanofiber membranes, Carbon, 2017, 115, 477–485 CrossRef CAS.
- X. W. Cao, M. L. Huang, B. Ding, J. Y. Yu and G. Sun, Robust polyacrylonitrile nanofibrous membrane reinforced with jute cellulose nanowhiskers for water purification, Desalination, 2013, 316, 120–126 CrossRef CAS.
- M. Tian, Y. Liao and R. Wang, Engineering a superwetting thin film nanofibrous composite membrane with excellent antifouling and self-cleaning properties to separate surfactant-stabilized oil-in-water emulsions, J. Membr. Sci., 2020, 596, 117721 CrossRef CAS.
- Z. Tan, S. Chen, X. Peng, L. Zhang and C. Gao, Polyamide membranes with nanoscale Turing structures for water purification, Science, 2018, 360, 518–521 CrossRef CAS.
- H. Ma, C. Burger, B. S. Hsiao and B. Chu, Highly Permeable Polymer Membranes Containing Directed Channels for Water Purification, ACS Macro Lett., 2012, 1, 723–726 CrossRef CAS.
- M. Obaid, N. A. M. Barakat, O. A. Fadali, S. Al-Meer, K. Elsaid and K. A. Khalil, Stable and effective super-hydrophilic polysulfone nanofiber mats for oil/water separation, Polymer, 2015, 72, 125–133 CrossRef CAS.
- W. Lv, Q. Mei, J. Xiao, M. Du and Q. Zheng, 3D multiscale superhydrophilic sponges with delicately designed pore size for ultrafast oil/water separation, Adv. Funct. Mater., 2017, 27, 1704293 CrossRef.
- S. S. Rajgarhia, S. C. Jana and G. G. Chase, Separation of water from ultralow sulfur diesel using novel polymer nanofiber-coated glass fiber media, ACS Appl. Mater. Interfaces, 2016, 8, 21683–21690 CrossRef CAS.
- A. Tuteja, W. Choi, M. L. Ma, J. M. Mabry, S. A. Mazzella, G. C. Rutledge, G. H. McKinley and R. E. Cohen, Designing superoleophobic surfaces, Science, 2007, 318, 1618–1622 CrossRef CAS.
- J. Zhang, J. Ge, Y. Si, F. Zhang, J. Yu, L. Liu and B. Ding, Taro leaf-inspired and superwettable nanonet-covered nanofibrous membranes for high-efficiency oil purification, Nanoscale Horiz., 2019, 4, 1174–1184 RSC.
- J. Zhang, F. Zhang, J. Song, L. Liu, Y. Si, J. Yu and B. Ding, Electrospun flexible nanofibrous membranes for oil/water separation, J. Mater. Chem. A, 2019, 7, 20075–20102 RSC.
- Y. Si, Q. Fu, X. Wang, J. Zhu, J. Yu, G. Sun and B. Ding, Superelastic and superhydrophobic nanofiber-assembled cellular aerogels for effective separation of oil/water emulsions, ACS Nano, 2015, 9, 3791–3799 CrossRef CAS.
- L. L. Zang, J. Ma, D. W. Lv, Q. L. Liu, W. L. Jiao and P. P. Wang, A core-shell fiber-constructed pH-responsive nanofibrous hydrogel membrane for efficient oil/water separation, J. Mater. Chem. A, 2017, 5, 19398–19405 RSC.
- Y. Y. Zhang, Y. Chen, L. L. Hou, F. Y. Guo, J. C. Liu, S. S. Qiu, Y. Xu, N. Wang and Y. Zhao, Pine-branch-like TiO2 nanofibrous membrane for high efficiency strong corrosive emulsion separation, J. Mater. Chem. A, 2017, 5, 16134–16138 RSC.
- J. Y. Zhang, F. Zhang, A. Q. Wang, Y. Lu, J. Y. Li, Y. Z. Zhu and J. Jin, Zwitterionic nanofibrous membranes with a superior antifouling
property for gravity-driven crude oil-in-water emulsion separation, Langmuir, 2019, 35, 1682–1689 CrossRef CAS.
- J. Xiao, W. Lv, Y. Song and Q. Zheng, Graphene/nanofiber aerogels: Performance regulation towards multiple applications in dye adsorption and oil/water separation, Chem. Eng. J., 2018, 338, 202–210 CrossRef CAS.
|
This journal is © the Partner Organisations 2021 |
Click here to see how this site uses Cookies. View our privacy policy here.