DOI:
10.1039/D0QI01021A
(Research Article)
Inorg. Chem. Front., 2021,
8, 127-140
Insights into the chemical and structural evolution of Li-rich layered oxide cathode materials
Received
22nd August 2020
, Accepted 21st October 2020
First published on 22nd October 2020
Abstract
Lithium-rich layered oxide cathodes have an advantage of high energy density. However, continuous capacity fading and voltage hysteresis have largely restricted their practical application. In this work, we investigated in depth the voltage-fading mechanism of Li-rich materials by in situ Raman spectroscopy, X-ray absorption near edge structure (XANES) spectroscopy, and high-resolution transmission electron microscopy (HRTEM). It has been found that the chemical and structural evolution of a Li1.2Ni0.15Co0.1Mn0.55O2 cathode is quasi-reversible in a whole charge–discharge cycle. The structural evolution is evidently irreversible upon long-term cycling, resulting in the dissolution of cations from the lattices and structural collapse, which in turn leads to undesirable voltage fading. This finding is important for a better understanding of the redox reaction mechanisms of high-capacity Li-rich cathodes.
1. Introduction
Li-Rich layered oxides, represented by the chemical formula xLiMO2·(1 − x)Li2MnO3 (0 < x < 1.0, M = Mn, Ni, Co, etc.), have recently attracted significant research interest due to their extraordinarily high energy density, being considered as cathode materials for lithium ion batteries.1,2 The ultra-high capacity of Li-rich compounds originates from the simultaneous cationic and anionic redox processes.3,4
However, Tarascon and his co-workers5 have shown that the oxygen redox process is strongly associated with the structural evolution in Li-rich materials. In addition, redox-mediated oxygen vacancies can be induced by the formation and escape of oxygen gas at a high charge cutoff voltage, typically above 4.5 V for most Li-rich or Na-deficient materials.5,6 Therefore, the oxygenic redox-mediated irreversible structural evolution is theoretically inevitable if we want to activate and take advantage of the anionic redox activity.7,8 Therefore, the anionic redox activity endows Li-rich layered oxides with a satisfactory high capacity but unsatisfactory long-term cycling stability.9,10 Ultimately, these restrictions still hinder the practical application of Li-rich layered oxides.
Nonetheless, various characterization methods have been previously developed to study the electrochemical degradation mechanisms of Li-rich materials.11–13 However, the previous studies lack a comprehensive consideration of the evolution of cations and the local structure of Li-rich cathodes after short- and long-term charge/discharge cycles, which have been a long-standing hurdle for the understanding of the mechanistic link between the chemical/structural evolution and the voltage and capacity degradation of Li-rich materials. Therefore, it is of great importance to clarify the impact of cation evolution and the local structure on the electrochemical stability of Li-rich layered cathode materials.
Herein, to better understand the mechanistic link between the chemical/structural evolution and the voltage degradation of Li-rich materials, we employed different characterization techniques to investigate the structural characteristics of a representative layer-structured Li-rich cathode material Li1.2Ni0.15Co0.1Mn0.55O2 before and after cycling. The results clearly revealed that the cation dissolution and the irreversible local structural evolution are mainly responsible for the degradation mechanism of Li-rich materials.
2. Experimental section
2.1. Chemicals
Commercially available chemical reagents were used as received without any further purification. Nickel(II) sulfate hexahydrate (NiSO4·6H2O), cobalt(II) sulfate heptahydrate (CoSO4·7H2O), manganese(II) sulfate monohydrate (MnSO4·H2O), sodium carbonate (Na2CO3), ammonium hydroxide (NH3·H2O), lithium carbonate (Li2CO3), poly(vinylidene fluoride) (PVDF), Super P, and 1-methyl-2-pyrrolidinone (NMP) were provided by Sinopharm Chemical Reagent Co. Ltd (Shanghai, China). Commercially available battery-grade chemicals, diethyl carbonate (DEC), dimethyl carbonate (DMC), ethylene carbonate (EC), and lithium hexafluorophosphate (LiPF6) were obtained from Sigma-Aldrich Co. Ltd (Shanghai, China).
2.2. Preparation of the Li1.2Ni0.15Co0.1Mn0.55O2 material
Firstly, a Ni0.15Co0.1Mn0.55(CO3)0.8 precursor material was synthesized via co-precipitation by the modified Jean-Marie Tarascon's method.14 In detail, the desired stoichiometric amounts of MnSO4·H2O, CoSO4·7H2O and NiSO4·6H2O were dissolved in an aqueous solution (cation concentration of 2.0 M in total, Ni2+
:
Co2+
:
Mn2+ = 1.5
:
0.5
:
5.5 in molar ratio). An appropriate amount of Na2CO3 aqueous solution (2.0 M, CO32−
:
M2+ = 1.1 in molar ratio) was used as the precipitant and added dropwise into the above-mentioned aqueous sulfate solution under continuous stirring. Ammonia solution (20 wt%) was fed into the reaction as a chelating agent. Then the mixed solution was kept at 80 °C and a pH of 8 for 12 h. The greyish yellow Ni0.15Co0.1Mn0.55(CO3)0.8 precipitate obtained was centrifuged, collected, thoroughly washed with deionized water, and vacuum-dried at 120 °C for 12 h. Then the as-prepared Ni0.15Co0.1Mn0.55(CO3)0.8 precursor was grind-mixed with Li2CO3 (Li
:
M = 1.6 in molar ratio). Then the obtained mixed powders were pre-calcined at 500 °C for 6 h, followed by sintering at 900 °C for 15 h under air atmosphere to afford the grayish black Li1.2Ni0.15Co0.1Mn0.55O2 material.
2.3. Electrochemical measurements
Firstly, the cathode electrode material slurry was fabricated with 80 wt% of Li1.2Ni0.15Co0.1Mn0.55O2 active material, 10 wt% of PVDF binder, and 10 wt% of conductive Super P additive in NMP. Then the slurry was pasted onto aluminium foil. The cathode electrode laminates were pressed down for an active material loading of 4–5 mg cm−2 with a scraper blade and a calender. Once calendered, the electrodes were thoroughly dried for 12 h at 120 °C under vacuum. The obtained electrode material was cut into disks with a diameter of 12 mm. Then CR2016 coin-type cells were assembled in an argon-filled glove box with the as-prepared Li1.2Ni0.15Co0.1Mn0.55O2 electrode as the cathode, metallic lithium foil as the anode, a polypropylene micro-porous film (Cellgard 2400) as the separator, and 1 M LiPF6 (EC/DMC/DEC, 1
:
1
:
1 volume ratio) as the electrolyte. The galvanostatic discharge–charge measurements were performed with the as-assembled CR2016 coin-type cells on a battery test system with a potential range of 2.25 to 4.75 V (vs. Li/Li+) at 25 °C.
2.4. Characterization
XRD (powder X-ray diffraction) characterization of the Li1.2Ni0.15Co0.1Mn0.55O2 material was performed on a Bruker D8 XRD instrument (Bruker Corporation, German) for Rietveld refinement and a Rigaku Smartlab 9KW XRD instrument for general measurements on the electrodes. The morphologies of the Li1.2Ni0.15Co0.1Mn0.55O2 sample were observed on a FEI Tecnai F30 high resolution transmission electron microscope (HRTEM, FEI Corporation, America) and a TESCAN Mira 3 scanning electron microscope (SEM, TESCAN Corporation, Czech Republic). In situ Raman spectroscopic characterization was carried out on a Renishaw inVia microscopic Raman spectrometer (Renishaw Corporation, UK) with a 532 nm wavelength laser, a laser beam of ≈1 μm diameter, a 50 mW power, a CCD camera, and an optical Leica microscope. A 50× objective lens and a 1800 lines per mm grating were used to focus the incident beam. The N2 adsorption–desorption isotherms were measured using a Micromeritics ASAP 2020 analyzer at 77 K (liquid nitrogen temperature). The specific surface area of the cathode sample was determined using the Brunauer–Emmett–Teller (BET) model, and pore size distribution was calculated using the Barrett–Joyner–Halenda (BJH) method. Electrochemical impedance spectroscopy (EIS) measurements on the Li1.2Ni0.15Co0.1Mn0.55O2 cathode were carried out using a Bio-Logic VMP3 electrochemical workstation (Bio-Logic Science Instruments Inc., France) with a 5 mV perturbation and a frequency range of 105–10−2 Hz. XANES and nano-CT experiments were performed at the Shanghai Synchrotron Radiation Facility (SSRF) BL08U1A and the Beijing Synchrotron Radiation Facility (BSRF) 4W1A, respectively.
3. Results and discussion
3.1. Physicochemical properties of as-prepared Li1.2Ni0.15Co0.1Mn0.55O2 cathode material
The as-prepared pristine Li1.2Ni0.15Co0.1Mn0.55O2 material was characterized using scanning electron microscopy (SEM), transmission electron microscopy (TEM), powder X-ray diffusion (XRD) and N2 adsorption–desorption isotherms. The SEM image (Fig. 1A) and TEM image (Fig. 1B) show that the Li1.2Ni0.15Co0.1Mn0.55O2 sample is composed of secondary particles of ∼2 μm. The Rietveld refinement of the XRD pattern of the pristine Li1.2Ni0.15Co0.1Mn0.55O2 is presented in Fig. 1C. The XRD pattern displays relatively sharp peaks, implying high crystallinity. The obtained XRD reflections are in line with a rhombohedral structure (R
m, LiMO2) and a monoclinic structure (C2/m, Li2MnO3), indicating that the fine layered structure of the Li1.2Ni0.15Co0.1Mn0.55O2 material is crystallized with rhombohedral symmetry with an R
m space group and monoclinic symmetry with a C2/m space group. The N2 adsorption–desorption isotherm and the BJH pore-size distribution are shown in Fig. 1D. The N2 adsorption–desorption isotherm shows a hysteresis loop due to the capillary condensation of N2 gas in the pores of the Li1.2Ni0.15Co0.1Mn0.55O2 sample.15 The BJH average pore diameter is 5.76 nm, and the BET specific surface area is 20.61 m2 g−1, suggesting that the Li1.2Ni0.15Co0.1Mn0.55O2 sample exhibits typical characteristics of mesoporous materials.
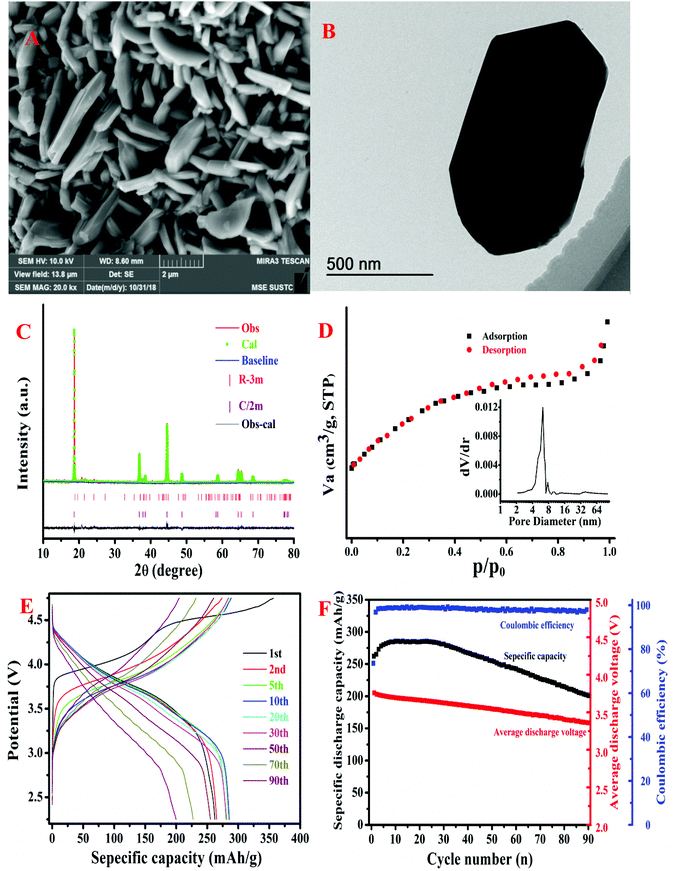 |
| Fig. 1 Characterization and electrochemical performance of Li1.2Ni0.15Co0.1Mn0.55O2: (A) SEM image, (B) TEM image, (C) XRD and Rietveld refinements, and (D) N2 adsorption–desorption isotherm (inset: BJH pore-size distribution); (E) charge–discharge profiles at different cycle numbers; (F) specific capacity, coulombic efficiency, and average discharge voltage as a function of cycle number. | |
The electrochemical properties of the Li1.2Ni0.15Co0.1Mn0.55O2 cathode material were investigated in a half cell configuration. Galvanostatic discharge–charge cycling was performed under a current density of 20 mA g−1 between 2.25 V and 4.75 V. The results are shown in Fig. 1E. As shown in Fig. 1E, two plateaus with charge voltages around 4.0 V and 4.5 V can be observed during the first charging process, which are typical characteristics of Li-rich layered materials.16,17 In addition, the plateau (at 4.5 V) disappears in the following charging processes, revealing a structural variation in the first charging process, which may be ascribed to the oxygen redox process.18 The Li1.2Ni0.15Co0.1Mn0.55O2 cathode material exhibits good cycling performance as it exhibits high coulombic efficiencies (close to 100%) in the following cycles. However, as shown in Fig. 1F, the Li1.2Ni0.15Co0.1Mn0.55O2 cathode material suffers from capacity fading and voltage decay during cycling, which are common problems encountered in Li-rich layered cathode materials.19,20
3.2. Characterization and analysis of the Li1.2Ni0.15Co0.1Mn0.55O2 cathode material during its first charge–discharge cycle
3.2.1.
In situ Raman.
In situ Raman spectra of the Li1.2Ni0.15Co0.1Mn0.55O2 electrode at different voltage states during its first charging and discharging cycle can be seen in Fig. 2. The Raman peak at 518 cm−1 belongs to the A1g bond (δO–M–O), shifts to 480 cm−1 (A1g′) during de-lithiation and re-lithiation processes, and eventually returns to 518 cm−1. This indicates the reversible variation of the lattice parameters during the Li+ extraction and re-insertion processes, which is, however, more drastic during the anionic redox process.21 Meanwhile, the broad Raman peak at 618 cm−1 can be attributed to Eg vibrations (υMO6). The intensity of this peak is not obviously decreased until Li1.2Ni0.15Co0.1Mn0.55O2 reaches the second charge plateau, reflecting a layered-to-spinel phase transition during the anionic redox process.22,23 Then this Raman peak regains its intensity during the discharge process of the Li1.2Ni0.15Co0.1Mn0.55O2 cathode, a fact that can be related to the reversible structural variation during the whole charge–discharge process. Therefore, the cationic redox process can activate the variation of the lattice parameters without any variation of the crystal phases, whereas the anionic redox process can induce variations both on the lattice parameters and crystal phase. The Raman peaks at 700, 716, 742, 891, 905, 936, and 974 cm−1 can be ascribed to LiPF6, EC, solvated EC with Li+ (EC-Li+), DEC, solvated DEC with Li+ (DEC-Li+), DMC, and solvated DMC with Li+ (DMC-Li+), respectively.24 We can conclude that the electrolyte undergoes an oxidation decomposition during the charging process and a reversible reduction resurrection during the discharging process. Notably, an intense Raman peak at ∼850 cm−1 is observed for a charging voltage above 4.4 V, increasing gradually until the end of charging, and then decreasing until the discharging voltage falls below 3.95 V. These peaks can be attributed to the typical peroxo O–O (O22−) bond stretching, caused by the oxygen redox process in Li1.2Ni0.15Co0.1Mn0.55O2.25,26 Interestingly, the Raman peak corresponding to peroxo O–O (O22−) slightly shifts to higher wavenumbers during charging, and then gradually returns to its original position during discharging. This indicates that the bond length is shortened when the O2− in Li1.2Ni0.15Co0.1Mn0.55O2 is partially oxidized to O22−, whereas the O2−/O− redox process is reversible during charging/discharging.27,28 The in situ Raman spectra provide definite evidence that reversible oxygen evolution and structural variation are involved in the whole charging/discharging process of Li1.2Ni0.15Co0.1Mn0.55O2.
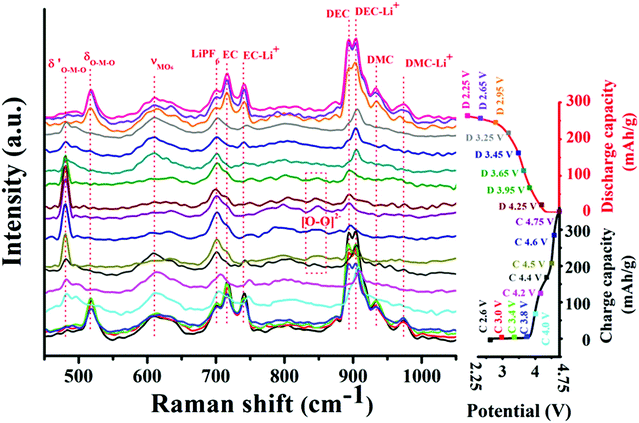 |
| Fig. 2
In situ Raman spectra of Li1.2Ni0.15Co0.1Mn0.55O2 throughout the first galvanostatic cycle. The corresponding voltage profiles are shown for clarity. | |
3.2.2.
Ex situ XANES.
Ex situ X-ray absorption near-edge structure (XANES) spectra of the Li1.2Ni0.15Co0.1Mn0.55O2 electrodes were obtained at various designated voltages, providing valuable information about the valence state and the redox chemistry of Li1.2Ni0.15Co0.1Mn0.55O2 upon its first charge–discharge process. As shown in Fig. 3, the shape of the spectrum of the O K edge peak in the pristine state is distinctly different from those of other states, whereas the spectra of other elements show a similar shape throughout all states of the charge/discharge process. This is probably due to the presence of oxygen vacancies in the pristine material, which is in accordance with previous reports.29,30 Upon charging from the pristine open-circuit voltage (OCV) → C 4.35 V, the spectra of Ni L3, Mn L3, and Co L3 edge peaks shift rightward to higher energy levels, without any significant shift of the O K edge peak, suggesting the oxidation of the transition metal (TM) ions during this charging process. In contrast, when charging through C 4.35 V → C 4.75 V, a significant change of the shape (broaden) and position (rightward shift) of the O K peak can be observed, whereas the position of TM L3-edge peaks changes negligibly, indicating that the oxygen redox instead of cationic redox process is mainly involved in this charging plateau.31 It is also worth noting that the increase in the pre-edge intensities may be assigned to the influence of the anionic redox reaction and the stronger hybridization of the higher-valent transition metal and oxygen.32 When discharging through C 4.75 V → D 3.75 V, all the TM L3 and O K edge peaks shift to lower energy levels, which is related to the simultaneous reduction of oxygen and TM ions, reflecting the appearance of a hybridized “TM-O redox” process.33 Upon further discharging through D 3.75 V → D 2.25 V, a continuous leftward shift of the XAS peaks can be observed. The TM L3 edge peaks reach their initial positions with a decrease in their intensity, indicating the weakening of the hybridization strength between the transition metal and oxygen during this process.20 The evolution of the XAS spectra indicates that both the transition metal cations and oxygen ions participate in the charge compensation reactions during the reversible redox cycles. The redox reactions of the transition metal cations proceed at a lower voltage, whereas in the high-voltage region between 4.35 V and 4.75 V, electron transfer occurs mainly at the oxygen sites. Then, the simultaneous reduction of oxygen and transition metal ions can be achieved by the hybridized “TM-O redox” process. As for one whole charge/discharge process, the chemical evolution of the Li1.2Ni0.15Co0.1Mn0.55O2 cathode is quasi-reversible.
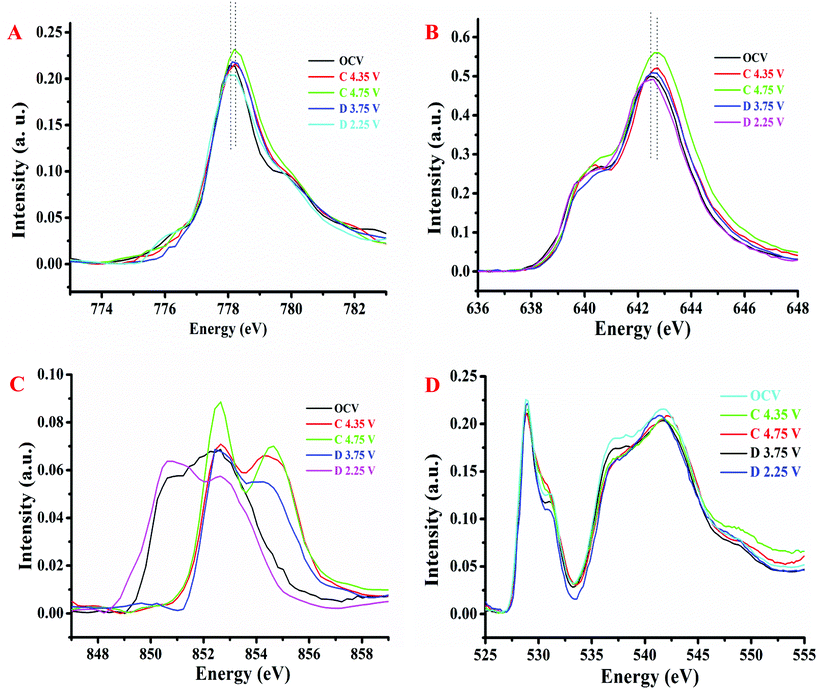 |
| Fig. 3
Ex situ XANES of Li1.2Ni0.15Co0.1Mn0.55O2 during the first cycle: Co L3 (A), Mn L3 (B), Ni L3 (C), and O K (D) edges. | |
3.3. Characterization and analysis of the Li1.2Ni0.15Co0.1Mn0.55O2 cathode material during long-term cycle-aging
3.3.1. HR-TEM and SAED.
The HR-TEM images of the Li1.2Ni0.15Co0.1Mn0.55O2 electrodes before and after cycle-aging revealed that the cycling deterioration of Li1.2Ni0.15Co0.1Mn0.55O2 is mainly associated with its phase transformation during electrochemical cycling. Detailed lattice fringes of the pristine Li1.2Ni0.15Co0.1Mn0.55O2 material can be observed in Fig. 4A, revealing the typical (111) crystal planes of the Li2MnO3 phase and the typical (003) crystal plane of the LiMO2 phase, respectively.34,35 The high crystallinity of the pristine Li1.2Ni0.15Co0.1Mn0.55O2 material is further verified using selected-area electron diffraction (SAED) (Fig. 4B). However, the HR-TEM image of the cycled material shows regions with highly degraded and randomly distributed lattice fringes, verifying the phase transformation from the original highly crystallized layered structure into a spinel-like structure. The phase transformation might have resulted from the Li and oxygen vacancies formed during the charging processes. These vacancies facilitate the migration of the transition metal ions from their original sites into the lithium layer, resulting in the structural rearrangement and irreversible local structural changes.36 The bulk degradation and electrochemical performance deterioration of the Li-rich cathode are probably associated with this phase transformation.37
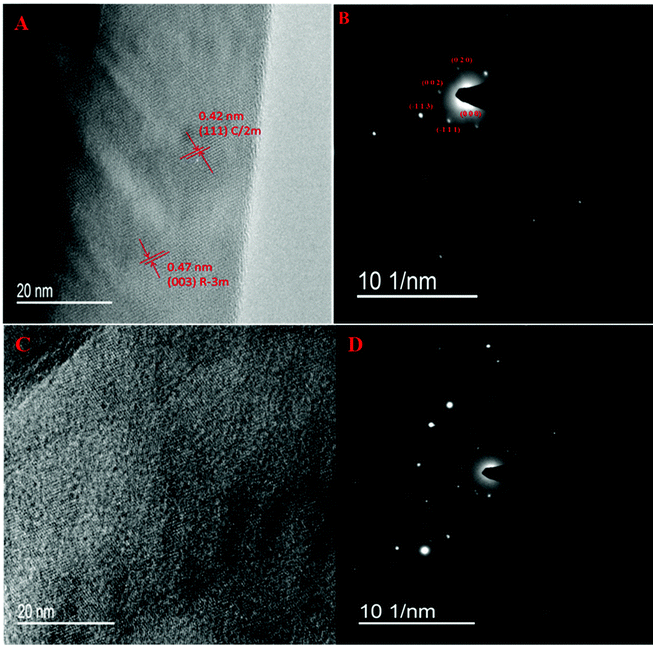 |
| Fig. 4 HRTEM images of Li1.2Ni0.15Co0.1Mn0.55O2 before (A) and after 90 cycles (C); and (B) and (D) the corresponding SAED patterns. | |
3.3.2. TEM-EDS.
Normalized using the C peak intensity, Fig. 5 shows the spectra of the TEM-energy dispersive spectroscopy (EDS) of the Li1.2Ni0.15Co0.1Mn0.55O2 cathode and the corresponding elemental analysis (in molar ratio) before and after 90 times charge–discharge. Before cycling, the pristine Li1.2Ni0.15Co0.1Mn0.55O2 material possesses almost the same molar ratio of O
:
Mn
:
Ni
:
Co = 71.8
:
19.3
:
5.37
:
3.53 as the nominal one. As shown in Fig. 5B, after cycling, the retention rate of O, Mn, Ni, and Co is 90.4%, 89.5%, 67.3%, and 95.1%, respectively. Therefore, we can draw the conclusion that the electrochemical cycling is responsible for the observed change in the chemical composition in Li1.2Ni0.15Co0.1Mn0.55O2. This finding is consistent with the phase transformation from the layered structure (Li[LixM1−x]O2, where x ≥ 0) to the defective spinel structure (LixM2O4) as extended cycling occurs,38 which is also further corroborated by the HR-TEM observation. In fact, the oxygen loss and dissolution of transition metals, especially for Ni, cause a deterioration of the structural stability, which contributes to cell capacity fading.39
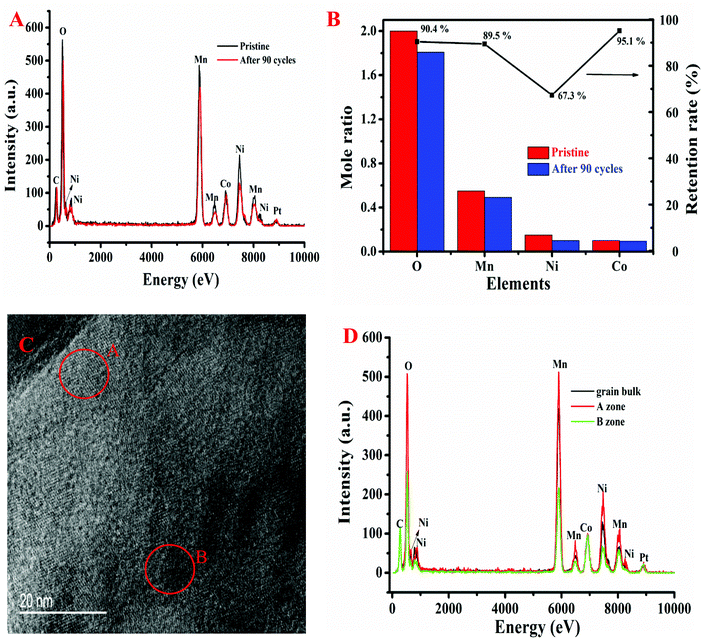 |
| Fig. 5 TEM-EDS profiles (A) and chemical composition (B) of the Li1.2Ni0.15Co0.1Mn0.55O2 cathode before and after cycling; (C): typical TEM image of a cycled Li1.2Ni0.15Co0.1Mn0.55O2 cathode for two-spot EDS analysis; and (D) EDS profile of a cycled Li1.2Ni0.15Co0.1Mn0.55O2 cathode. | |
EDS analysis was also conducted at two different locations of the aged Li1.2Ni0.15Co0.1Mn0.55O2 cathode with a spot size of 10 nm (Fig. 5C). The two selected areas display distinctly different crystal structures, as the A zone possesses better crystallinity than the B zone. Normalized using the C peak intensity, the obtained EDS spectra are shown in Fig. 5D. Apparently, the content of each element in the A zone is higher than that in the B zone, signifying the irreversible structural and chemical evolution during cycling. The loss of elements is differentiated within the entire area, resulting in distortion of crystal periodicity. It can be conclusively stated that the lattice transformation and chemical evolution are the main degradation mechanisms for the Li-rich cathodes. Interestingly, the variation of the molar ratio of Co content is relatively negligible at different zones or after cycling, suggesting the good stability of the Co element in the lattice. Therefore, appropriate doping with the Co element may be an effective method to improve the structural stability of Li-rich materials.
3.3.3. EIS studies.
The EIS characterization of a cycle-aged cell was performed at a state of charge of 100% at 25 °C. Fig. 6A displays the specific equivalent circuit model,40 and the obtained Nyquist plots and detailed resulting electrochemical impedance values are given in Fig. 6B and Table 1, respectively. The inset of Fig. 6B displays the magnified regions at high frequencies in the Nyquist plots. The intersection with the x-axis, which can be attributed to the ohmic resistance (Rs) of the battery, increases monotonically with the increasing cycling number, reflecting the continuously increasing internal resistance of the battery during cycle-aging. Two semicircles can be observed in a frequency range of 25 Hz to 200 kHz. The left one can be assigned to the cumulative solid–electrolyte interfaces (SEI) of both the electrodes, whereas the right semicircle can be ascribed to the solid diffusion in the electrode materials. A widening of the semicircles can be observed in Fig. 6B, indicating the general trend of impedance increase upon increasing the number of cycles, which is related to the aging of the cell.41
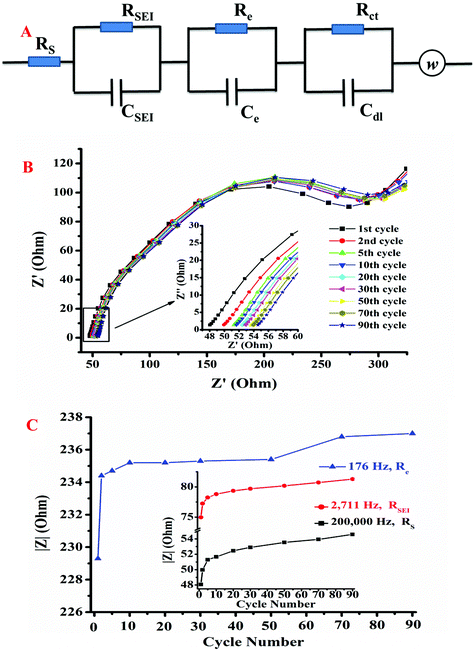 |
| Fig. 6 EIS analysis of pristine and cycling-aged Li1.2Ni0.15Co0.1Mn0.55O2: a specific equivalent circuit model (A), Nyquist curves (B) and evolution of Re, RSEI, and RS (C) as a function of cycle numbers. | |
Table 1 Simulated electrochemical impedance parameters of Li1.2Ni0.15Co0.1Mn0.55O2
Number of cycles |
R
s (Ω) |
R
SEI (Ω) |
R
e (Ω) |
R
ct (Ω) |
Fitting coefficient |
1 |
48.07 |
74.96 |
229.3 |
2760 |
97.79 |
2 |
49.97 |
77.25 |
234.4 |
2661 |
97.14 |
5 |
51.29 |
78.24 |
234.7 |
2058 |
96.63 |
10 |
51.66 |
78.8 |
235.2 |
2018 |
96.89 |
20 |
52.46 |
79.35 |
235.2 |
1981 |
96.70 |
30 |
52.9 |
79.69 |
235.3 |
1586 |
96.98 |
50 |
53.54 |
80.19 |
235.4 |
1495 |
96.45 |
70 |
53.94 |
80.72 |
236.8 |
1356 |
97.24 |
90 |
54.59 |
81.29 |
237 |
1251 |
96.06 |
Fig. 6C shows the absolute values of impedances at characteristic frequencies upon increasing the number of cycles. The green curve shows the resistance of solid diffusion in the cathode electrode material (Re), whereas the inset displays the ohmic resistance (Rs) of the cell and the resistance of the SEI (RSEI). A distinct increase during the initial several cycles and a slow increase in the following cycles can be observed in each impedance curve due to the progressive aging of the cell. It can be conclusively stated that the increase of the Rs, RSEI, and Re values reflects the increase of the internal ohmic resistance, thickness of the SEI, and resistance of solid diffusion in the electrode material during cyclic aging, respectively. It should be clarified that the rise of Re is not solely caused by the structural variations of the cathode material; the identified isolated area in the surfaces of the electrodes (SEI/electrode interfaces) is also crucial.42 The formation and growth of the SEI contribute significantly to the increase of the impedance parameters of the aging cell, and a robust SEI on the electrodes can be established after 10 charge–discharge cycles. However, as suggested in Fig. 6B, the degree of Re increase is larger than that of RSEI, revealing the existence of cathode degradation during cycling.43
3.3.4. XANES.
The X-ray absorption near-edge structure (XANES) spectra at the O K edge and L3-edges of Mn, Co and Ni were collected at the pristine and 90 charge–discharge cycling-aged Li1.2Ni0.15Co0.1Mn0.55O2 electrode (Fig. 7). An obvious leftward shift toward lower energy levels accompanied by a decreased intensity of the pre-edge peaks can be observed after long-term cycling. This suggests that the average content and valence state of Mn, Co, and Ni cations in Li1.2Ni0.15Co0.1Mn0.55O2 are continuously reduced upon increasing the number of cycles.44 As previously reported, the dissolution of cations in the electrolyte is more severe for the cations of lower valence states.45,46 This transition metal cation dissolution is a common detrimental factor towards voltage decrease and capacity decay.47,48 Moreover, the peak at 534 eV, shown in the O K-edge XAS spectra in Fig. 7D, can be associated with Li2CO3, which is a major constituent of the SEI layer, indicating the growth of the CEI layer during cycling.49,50 The decreased pre-edge peaks and similar-shaped O K-edge spectrum before and after cycling can be explained by taking into account the surface reconstruction due to the formation of oxygen vacancies and rock-salt/spinel phases.20 The evolution of the XANES spectra in the cycling-aged Li1.2Ni0.15Co0.1Mn0.55O2 electrode reveals its structural degradation during cycling.
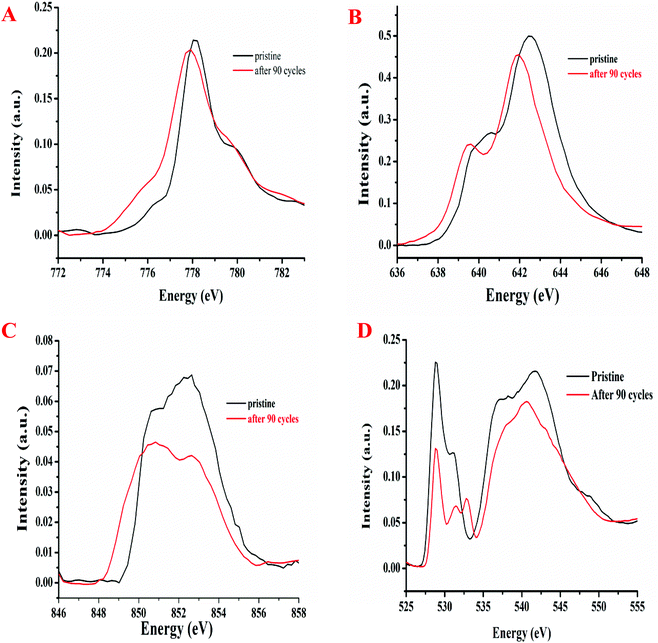 |
| Fig. 7 XANES of pristine and cycling-aged Li1.2Ni0.15Co0.1Mn0.55O2: Co L3 (A), Mn L3 (B), Ni L3 (C), and O K (D) edges. | |
3.3.5. XRD.
Fig. 8 displays the XRD patterns of the pristine and cycling-aged Li1.2Ni0.15Co0.1Mn0.55O2 cathode materials. As shown in Fig. 8A, the diffraction peaks of pristine Li1.2Ni0.15Co0.1Mn0.55O2 cathode electrodes at 36.62°, 36.69°, 36.76°, 36.85°, and 36.94° can be attributed to the (1 0 1) plane of C/2m, (2 0 −1) plane of R
m, (1 3 −1) plane of R
m, (0 0 6) plane of C/2m, and (1 1 −2) plane of R
m, respectively. During the initial several cycles, the obtained XRD patterns of cycling-aged Li1.2Ni0.15Co0.1Mn0.55O2 electrodes are similar to those observed over fresh cells. However, the diffraction peaks of the cycled samples that slightly shifted to a lower diffraction angle greatly gained in intensity, as previously reported by Debasish Mohanty et al.51 This evolution of the XRD patterns can be ascribed to the increased lattice parameters along with increased atom disorder in the local lattice of the cycling-aged Li-rich material.52 Interestingly, a new main peak emerges at 36.50°, which is characteristic of the (3 1 1) lattice plane of the Li4Mn5O12 spinel phase (JCPDS 46-0810). The latter suggests that the high cut-off voltage cycling induces an inevitable complex phase transition of the cycling-aged Li1.2Ni0.15Co0.1Mn0.55O2 electrodes.53 The atom loss in the lattice and layered-to-spinel phase conversion resulted in an increase in the lattice parameters. The overall structure of the cycling-aged Li1.2Ni0.15Co0.1Mn0.55O2 cathode material still remains layered, but spinel domains of small size can be gradually generated and then locally integrated into the layered framework.
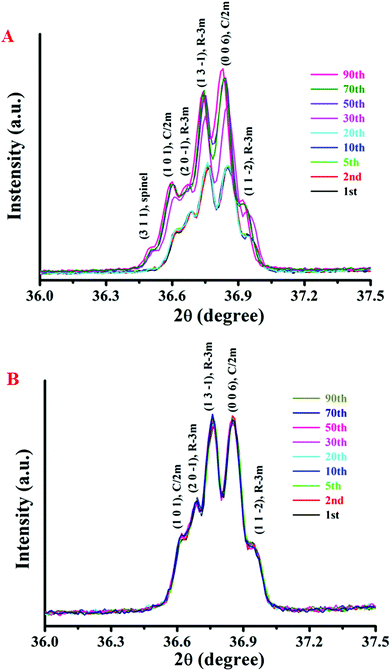 |
| Fig. 8 The evolution of XRD patterns in a range of 36–37.5 as a function of cycling numbers for Li1.2Ni0.15Co0.1Mn0.55O2: (A) galvanostatically cycled in voltage ranges of 2.25–4.75 V and (B) 2.25–4.35 V. | |
For better comparison, the Li1.2Ni0.15Co0.1Mn0.55O2 cathode electrodes were galvanostatically tested in a potential window of 2.25–4.35 V (vs. Li+/Li). The XRD patterns of the cycling-aged electrodes are shown in Fig. 8B. The XRD patterns remain essentially the same in all cases, indicating that atom loss from the lattice and layered-to-spinel phase conversion can hardly be induced by a low cut-off voltage. As explained above, the chemical and structural evolution in the Li1.2Ni0.15Co0.1Mn0.55O2 material has an important effect on the lithium deintercalation/intercalation process. Compared with the first cycle, lithium extraction/intercalation can occur at a lower voltage in the subsequent cycles, probably due to the migration of the lithium/transition metal cations in Li/M slabs from their original crystallographic sites to other available sites during the charge/discharge process. The latter can lead to re-ordering or even loss of transition metal cations and the formation of a spinel phase in some regions.54 The present XRD results provide insight into the structural transformation of the cycling-aged Li1.2Ni0.15Co0.1Mn0.55O2 illuminating the voltage-fading mechanism.
3.3.6. 3D CT.
The structural information about the internal structure and spatial distribution of the grain bulk of Li1.2Ni0.15Co0.1Mn0.55O2 is confirmed by three-dimensional (3D) tomographic imaging. To illustrate this, virtual 3D cross-sectional slices of the grain bulk of Li1.2Ni0.15Co0.1Mn0.55O2 particles are shown as yellow-coloured solid blocks in Fig. 9. In Fig. 9A, some cracks can be observed in the large secondary particles of the pristine Li1.2Ni0.15Co0.1Mn0.55O2 sample. These particle fractures of the pristine Li1.2Ni0.15Co0.1Mn0.55O2 sample resulted from the applied high pressure on the cathode during the fabrication process.55
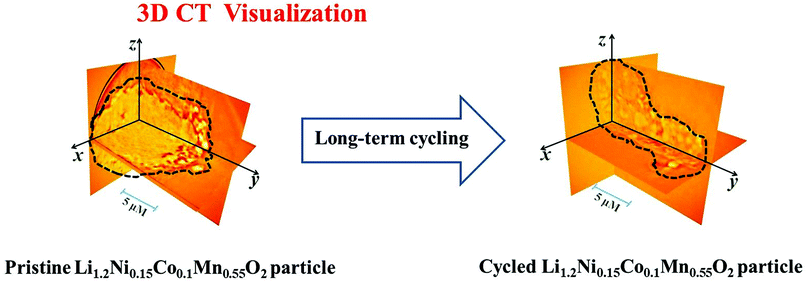 |
| Fig. 9 Virtual 3D cross-sectional slices of the grain bulk of the Li1.2Ni0.15Co0.1Mn0.55O2 particles before (A) and after 90 cycles (B). | |
It is noticeable, as shown in Fig. 9B, that fragmented pieces have been peeled off from the initial bulk particles, and thus the morphology of the secondary particles of Li1.2Ni0.15Co0.1Mn0.55O2 changes significantly to small and irregular shaped sub-micron pieces with many voids after 90 charging–discharging cycles. It is worth noting that the progressive erosion on the electrode is not uniform with the depth and shape, which has been reported consistently by Chongmin Wang et al.56 The intrinsic mechanism that causes such structural fragmentation of Li1.2Ni0.15Co0.1Mn0.55O2 is related to the variation of the strain and stress due to the volume expansion and contraction during cycling.57 In particular, the primary particles of Li1.2Ni0.15Co0.1Mn0.55O2 undergo a lattice expansion/contraction strain caused by delithiation/lithiation during electrochemical cycling, resulting in numerous randomly distributed small voids due to the anisotropy and inhomogeneity of the primary particles. Upon deep electrochemical cycling, the discontinuous voids grow across forming cracks, and then the cracks propagate and link up to cause the fragmentation of the secondary particles of Li1.2Ni0.15Co0.1Mn0.55O2. Eventually, the structural collapse of the grain bulk of Li1.2Ni0.15Co0.1Mn0.55O2 is caused by the removal of the fragmented pieces of the secondary particles.
4. Conclusion
In this work, we investigated the capacity degradation and voltage fading mechanisms of a Li1.2Ni0.15Co0.1Mn0.55O2 cathode as a representative Li-rich layered oxide cathode material for lithium ion batteries. Based on the in situ Raman and ex situ XANES characterization, the chemical evolution and structural transformation of the Li1.2Ni0.15Co0.1Mn0.55O2 cathode are found to be quasi-reversible during a whole charge/discharge cycle. However, according to the results of the electrochemical measurements, HRTEM, SAED, TEM-EDS, EIS, XRD, XANES, and 3D CT of the pristine and cycling-aged Li1.2Ni0.15Co0.1Mn0.55O2 cathode material, the activation of the anionic redox reaction could be an effective route to develop a high-capacity cathode. However, the anionic redox activity could also have various serious undesirable consequences, including irreversible layered-to-spinel structural transformation, atom disorder in the local lattice, oxygen vacancies, and cation dissolution, which eventually result in the lattice instability or even structural collapse of the grain bulk, and finally to voltage and capacity degradation. Our research findings also indicate that the promotion of the structural compatibility and stability, especially the stabilization of the oxygen lattice and reversible oxygen redox process, is the most critical factor towards constructing Li-rich materials with high capacity and good cycling stability.
Conflicts of interest
The authors declare no conflict of interest
Acknowledgements
This work was financially supported by the Basic Research Project of the Science and Technology Innovation Commission of Shenzhen (no. JCYJ20170412153139454), the National Natural Science Foundation of China (no. 21875097), Natural Science Foundation of Guangdong Province (no. 2018A030313725 and 2018B030322001), and the Professorial and Doctoral Scientific Research Foundation of Huizhou University (no. 2020JB025). In this work, XANES and Nano CT experiments were completed at the Shanghai Synchrotron Radiation Facility (SSRF) BL08U1A and the Beijing Synchrotron Radiation Facility (BSRF) 4 W1A, respectively. We thank Dr Zhenhua Chen, Dr Lijuan Zhang and Dr Xiangzhi Zhang from the SSRF for their help in XANES experiments and data analysis. We appreciate the support of the BSRF and the great help from Dr Kai Zhang and Dr Wanxia Huang.
References
- P. K. Nayak, E. M. Erickson, F. Schipper, T. R. Penki, N. Munichandraiah, P. Adelhelm, H. Sclar, F. Amalraj, B. Markovsky and D. Aurbach, Review on challenges and recent advances in the electrochemical performance of high capacity Li- and Mn-rich cathode materials for Li-ion batteries, Adv. Energy Mater., 2018, 8, 1702397 CrossRef.
- H. Yu and H. Zhou, High-energy cathode materials (Li2MnO3-LiMO2) for lithium-ion batteries, J. Phys. Chem. Lett., 2013, 4, 1268–1280 CrossRef CAS.
- P. E. Pearce, A. J. Perez, G. Rousse, M. Saubanère, D. Batuk, D. Foix, E. McCalla, A. M. Abakumov, G. Van Tendeloo and M.-L. Doublet, Evidence for anionic redox activity in a tridimensional-ordered Li-rich positive electrode β-Li2IrO3, Nat. Mater., 2017, 16, 580 CrossRef CAS.
- M. Saubanère, E. McCalla, J.-M. Tarascon and M.-L. Doublet, The intriguing question of anionic redox in high-energy density cathodes for Li-ion batteries, Energy Environ. Sci., 2016, 9, 984–991 RSC.
- A. Grimaud, W. Hong, Y. Shao-Horn and J.-M. Tarascon, Anionic redox processes for electrochemical devices, Nat. Mater., 2016, 15, 121 CrossRef CAS.
- W. Zheng, Q. Liu, Z. Y. Wang, Z. L. Wu, S. Gu, L. J. Cao, K. L. Zhang, J. Fransaer and Z. G. Lu, Oxygen redox activity with small voltage hysteresis in Na0.67Cu0.28Mn0.72O2 for sodium-ion batteries, Energy Storage Mater., 2020, 28, 300–306 CrossRef.
- W. Zheng, Q. Liu, Z. Y. Wang, Z. B. Yi, Y. Z. Li, L. J. Cao, K. L. Zhang and Z. G. Lu, Stabilizing the oxygen lattice and reversible oxygen redox in Na-deficient cathode oxides, J. Power Sources, 2019, 439, 227086 CrossRef CAS.
- W. Zheng, Q. Liu, Z. Wang, Z. Yi, Y. Li, L. Cao, K. Zhang and Z. Lu, Stabilizing the oxygen lattice and reversible oxygen redox in Na-deficient cathode oxides, J. Power Sources, 2019, 439, 227086 CrossRef CAS.
- D. Ye, B. Wang, Y. Chen, G. Han, Z. Zhang, D. Hulicova-Jurcakova, J. Zou and L. Wang, Understanding the stepwise capacity increase of high energy low-Co Li-rich cathode materials for lithium ion batteries, J. Mater. Chem. A, 2014, 2, 18767–18774 RSC.
- D. Luo, P. Shi, S. Fang, W. Guo, L. Yang and S. Hirano, Li1.17Mn0.50Ni0.16Co0.17O2 assembled microspheres as a high-rate and long-life cathode of Li-ion batteries, Inorg. Chem. Front., 2017, 4, 650–658 RSC.
- A. Boulineau, L. Simonin, J.-F. Colin, C. Bourbon and S. Patoux, First evidence of manganese-nickel segregation and densification upon cycling in Li-rich layered oxides for lithium batteries, Nano Lett., 2013, 13, 3857–3863 CrossRef CAS.
- Z. Ding, M. Xu, J. Liu, Q. Huang, L. Chen, P. Wang, D. G. Ivey and W. Wei, Understanding the enhanced kinetics of gradient-chemical-doped lithium-rich cathode material, ACS Appl. Mater. Interfaces, 2017, 9, 20519–20526 CrossRef CAS.
- Q. Li, Y. Wang, X. J. Wang, X. Sun, J. Zhang, X. Yu and H. Li, Investigations on the fundamental process of cathode electrolyte interphase formation and evolution of high-voltage cathodes, ACS Appl. Mater. Interfaces, 2020, 12, 2319–2326 CrossRef CAS.
- V. Pimenta, M. Sathiya, D. Batuk, A. M. Abakumov, D. Giaume, S. Cassaignon, D. Larcher and J.-M. Tarascon, Synthesis of Li-rich NMC: A comprehensive study, Chem. Mater., 2017, 29, 9923–9936 CrossRef CAS.
- M. Xu, Z. Chen, H. Zhu, X. Yan, L. Li and Q. Zhao, Mitigating capacity fade by constructing highly ordered mesoporous Al2O3/polyacene double-shelled architecture in Li-rich cathode materials, J. Mater. Chem. A, 2015, 3, 13933–13945 RSC.
- Y. Cai, L. Ku, L. Wang, Y. Ma, H. Zheng, W. Xu, J. Han, B. Qu, Y. Chen, Q. Xie and D.-L. Peng, Engineering oxygen vacancies in hierarchically Li-rich layered oxide porous microspheres for high-rate lithium ion battery cathode, Sci. China Mater., 2019, 62, 1374–1384 CrossRef CAS.
- Y. Kang, Z. Liang, Y. Zhao, H. Xu, K. Qian, X. He, T. Li and J. Li, Large-scale synthesis of lithium- and manganese-rich materials with uniform thin-film Al2O3 coating for stable cathode cycling, Sci. China Mater., 2020, 63, 1683–1692 CrossRef CAS.
- J. Zheng, M. Gu, A. Genc, J. Xiao, P. Xu, X. Chen, Z. Zhu, W. Zhao, L. Pullan and C. Wang, Mitigating voltage fade in cathode materials by improving the atomic level uniformity of elemental distribution, Nano Lett., 2014, 14, 2628–2635 CrossRef CAS.
- W. Li, B. Song and A. Manthiram, High-voltage positive electrode materials for lithium-ion batteries, Chem. Soc. Rev., 2017, 46, 3006–3059 RSC.
- E. Hu, X. Yu, R. Lin, X. Bi, J. Lu, S. Bak, K.-W. Nam, H. L. Xin, C. Jaye and D. A. Fischer, Evolution of redox couples in Li-and Mn-rich cathode materials and mitigation of voltage fade by reducing oxygen release, Nat. Energy, 2018, 3, 690 CrossRef CAS.
- E. Flores, N. Vonrüti, P. Novák, U. Aschauer and E. J. Berg, Elucidation of LixNi0.8Co0.15Al0.05O2 redox chemistry by operando Raman spectroscopy, Chem. Mater., 2018, 30, 4694–4703 CrossRef CAS.
- Y.-P. Deng, F. Fu, Z.-G. Wu, Z.-W. Yin, T. Zhang, J.-T. Li, L. Huang and S.-G. Sun, Layered/spinel heterostructured Li-rich materials synthesized by a one-step solvothermal strategy with enhanced electrochemical performance for Li-ion batteries, J. Mater. Chem. A, 2016, 4, 257–263 RSC.
- H. Cui, H. Li, J. Liu, Y. Zhang, F. Cheng and J. Chen, Surface modification of Li-rich manganese-based cathode materials by chemical etching, Inorg. Chem. Front., 2019, 6, 1694–1700 RSC.
- G. Yang, I. N. Ivanov, R. E. Ruther, R. L. Sacci, V. Subjakova, D. T. Hallinan and J. Nanda, Electrolyte solvation structure at solid-liquid interface probed by nanogap surface-enhanced Raman spectroscopy, ACS Nano, 2018, 12, 10159–10170 CrossRef CAS.
- S. Hy, F. Felix, J. Rick, W.-N. Su and B. J. Hwang, Direct In situ observation of Li2O evolution on Li-Rich high-capacity cathode material, Li[NixLi(1-2x)/3Mn(2-x)/3]O2 (0 ≤ x ≤ 0.5), J. Am. Chem. Soc., 2014, 136, 999–1007 CrossRef CAS.
- X. Li, Y. Qiao, S. H. Guo, Z. Xu, H. Zhu, X. Y. Zhang, Y. Yuan, P. He, M. Ishida and H. S. Zhou, Direct visualization of the reversible O2−/O− redox process in Li-rich cathode materials, Adv. Mater., 2018, 30, 1705197 CrossRef.
- X. Li, Y. Qiao, S. Guo, K. Jiang, M. Ishida and H. Zhou, A new type of Li-rich rock-salt oxide Li2Ni1/3Ru2/3O3 with reversible anionic redox chemistry, Adv. Mater., 2019, 31, 1807825 CrossRef.
- E. McCalla, A. M. Abakumov, M. Saubanère, D. Foix, E. J. Berg, G. Rousse, M.-L. Doublet, D. Gonbeau, P. Novák and G. Van Tendeloo, Visualization of OO peroxo-like dimers in high-capacity layered oxides for Li-ion batteries, Science, 2015, 350, 1516–1521 CrossRef CAS.
- N. Palina, A. Annadi, T. C. Asmara, C. Diao, X. Yu, M. B. Breese, T. Venkatesan and A. Rusydi, Electronic defect states at the LaAlO3/SrTiO3 heterointerface revealed by O K-edge X-ray absorption spectroscopy, Phys. Chem. Chem. Phys., 2016, 18, 13844–13851 RSC.
- D. N. Mueller, M. L. Machala, H. Bluhm and W. C. Chueh, Redox activity of surface oxygen anions in oxygen-deficient perovskite oxides during electrochemical reactions, Nat. Commun., 2015, 6, 6097 CrossRef CAS.
- M. Oishi, K. Yamanaka, I. Watanabe, K. Shimoda, T. Matsunaga, H. Arai, Y. Ukyo, Y. Uchimoto, Z. Ogumi and T. Ohta, Direct observation of reversible oxygen anion redox reaction in Li-rich manganese oxide, Li2MnO3, studied by soft X-ray absorption spectroscopy, J. Mater. Chem. A, 2016, 4, 9293–9302 RSC.
- J. Hong, W. E. Gent, P. Xiao, K. Lim, D.-H. Seo, J. Wu, P. M. Csernica, C. J. Takacs, D. Nordlund, C.-J. Sun, K. H. Stone, D. Passarello, W. Yang, D. Prendergast, G. Ceder, M. F. Toney and W. C. Chueh, Metal-oxygen decoordination stabilizes anion redox in Li-rich oxides, Nat. Mater., 2019, 18, 256–265 CrossRef CAS.
- Z.-L. Wu, H. Xie, F. Zhang, Z. Wang, W. Zheng, M. Yang, Y. Li, Z. Xu and Z. Lu, Li1.2Ni0.25Mn0.55O2: A new type high-capacity cathode material with a homogeneous monoclinic Li2MnO3-like Superstructure [J], J. Alloys Compd., 2020, 827, 154202 CrossRef CAS.
- X. Liu, Z. Wang, W. Zhuang, Z. Li, W. Li, L. Ban, M. Gao and S. Lu, Reinforcing the surface conductivity and stability of primary particles for high-performance Li-rich layered Li1.18Mn0.52Co0.15Ni0.15O2 via an integrated strategy, Inorg. Chem. Front., 2020, 7, 3154–3164 RSC.
- X. Yu, Y. Lyu, L. Gu, H. Wu, S. M. Bak, Y. Zhou, K. Amine, S. N. Ehrlich, H. Li and K. W. Nam, Understanding the rate capability of high-energy-density Li-rich layered Li1.2Ni0.15Co0.1Mn0.55O2 cathode materials, Adv. Energy Mater., 2014, 4, 1300950 CrossRef.
- C.-H. Shen, Q. Wang, F. Fu, L. Huang, Z. Lin, S.-Y. Shen, H. Su, X.-M. Zheng, B.-B. Xu and J.-T. Li, Facile synthesis of the Li-rich layered oxide Li1.23Ni0.09Co0.12Mn0.56O2 with superior lithium storage performance and new insights into structural transformation of the layered oxide material during charge-discharge cycle: In situ XRD characterization, ACS Appl. Mater. Interfaces, 2014, 6, 5516–5524 CrossRef CAS.
- Y. Xie, M. Saubanère and M.-L. Doublet, Requirements for reversible extra-capacity in Li-rich layered oxides for Li-ion batteries, Energy Environ. Sci., 2017, 10, 266–274 RSC.
- J. Zheng, P. Xu, M. Gu, J. Xiao, N. D. Browning, P. Yan, C. Wang and J.-G. Zhang, Structural and chemical evolution of Li-and Mn-rich layered cathode material, Chem. Mater., 2015, 27, 1381–1390 CrossRef CAS.
- Y.-R. Ji, S.-T. Weng, X.-Y. Li, Q.-H. Zhang and L. Gu, Atomic-scale structural evolution of electrode materials in Li-ion batteries: a review, Rare Met., 2020, 39, 205–217 CrossRef CAS.
- X.-Y. Qiu, Q.-C. Zhuang, Q.-Q. Zhang, R. Cao, P.-Z. Ying, Y.-H. Qiang and S.-G. Sun, Electrochemical and electronic properties of LiCoO2 cathode investigated by galvanostatic cycling and EIS, Phys. Chem. Chem. Phys., 2012, 14, 2617–2630 RSC.
- Y. Xie, J. Li and C. Yuan, Mathematical modeling of the electrochemical impedance spectroscopy in lithium ion battery cycling, Electrochim. Acta, 2014, 127, 266–275 CrossRef CAS.
- M. Heinrich, N. Wolff, N. Harting, V. Laue, F. Röder, S. Seitz and U. Krewer, Physico-chemical modeling of a lithium-ion battery: An ageing study with electrochemical impedance spectroscopy, Batter. Supercaps, 2019, 2, 530–540 CrossRef CAS.
- X. Li, K. Zhang, K. Zhang, D. Mitlin, Z. Yang, M. Wang, Y. Tang, F. Jiang, Y. Du and J. Zheng, Fundamental insight into Zr modification of Li- and Mn-rich cathodes: combined transmission electron microscopy and electrochemical impedance spectroscopy study, Chem. Mater., 2018, 30, 2566–2573 CrossRef CAS.
- S. Wu, W. Wang, M. Li, L. Cao, F. Lyu, M. Yang, Z. Wang, Y. Shi, B. Nan and S. Yu, Highly durable organic electrode for sodium-ion batteries via a stabilized α-C radical intermediate, Nat. Commun., 2016, 7, 13318 CrossRef CAS.
- J. Song, D. W. Shin, Y. Lu, C. D. Amos, A. Manthiram and J. B. Goodenough, Role of Oxygen Vacancies on the Performance of Li[Ni0.5-xMn1.5+x]O4 (x=0, 0.05, and 0.08) Spinel Cathodes for Lithium-Ion Batteries, Chem. Mater., 2012, 24, 3101–3109 CrossRef CAS.
- Y. Huo, N. Qin, C. Liao, H. Feng, Y. Gu and H. Cheng, Hydrothermal synthesis and energy storage performance of ultrafine Ce2Sn2O7 nanocubes, J. Cent. South Univ., 2019, 26, 1416–1425 CrossRef CAS.
- G.-L. Xu, Q. Liu, K. K. S. Lau, Y. Liu, X. Liu, H. Gao, X. Zhou, M. Zhuang, Y. Ren, J. Li, M. Shao, M. Ouyang, F. Pan, Z. Chen, K. Amine and G. Chen, Building ultraconformal protective layers on both secondary and primary particles of layered lithium transition metal oxide cathodes, Nat. Energy, 2019, 4, 484–494 CrossRef CAS.
- J. Zhang, F. Cheng, S. Chou, J. Wang, L. Gu, H. Wang, H. Yoshikawa, Y. Lu and J. Chen, Tuning oxygen redox chemistry in Li-rich Mn-based layered oxide cathodes by modulating cation arrangement, Adv. Mater., 2019, 31, 1901808 CrossRef CAS.
- M. Gauthier, T. J. Carney, A. Grimaud, L. Giordano, N. Pour, H.-H. Chang, D. P. Fenning, S. F. Lux, O. Paschos, C. Bauer, F. Maglia, S. Lupart, P. Lamp and Y. Shao-Horn, Electrode-electrolyte interface in Li-ion batteries: current understanding and new insights, J. Phys. Chem. Lett., 2015, 6, 4653–4672 CrossRef CAS.
- W. E. Gent, K. Lim, Y. Liang, Q. Li, T. Barnes, S.-J. Ahn, K. H. Stone, M. McIntire, J. Hong and J. H. Song, Coupling between oxygen redox and cation migration explains unusual electrochemistry in lithium-rich layered oxides, Nat. Commun., 2017, 8, 2091 CrossRef.
- D. Mohanty, S. Kalnaus, R. A. Meisner, K. J. Rhodes, J. Li, E. A. Payzant, D. L. Wood III and C. Daniel, Structural transformation of a lithium-rich Li1.2Co0.1Mn0.55Ni0.15O2 cathode during high voltage cycling resolved by in situ X-ray diffraction, J. Power Sources, 2013, 229, 239–248 CrossRef CAS.
- B. Song, Z. Liu, M. O. Lai and L. Lu, Structural evolution and the capacity fade mechanism upon long-term cycling in Li-rich cathode material, Phys. Chem. Chem. Phys., 2012, 14, 12875–12883 RSC.
- P. Yan, J. Zheng, M. Gu, J. Xiao, J.-G. Zhang and C.-M. Wang, Intragranular cracking as a critical barrier for high-voltage usage of layer-structured cathode for lithium-ion batteries, Nat. Commun., 2017, 8, 14101 CrossRef CAS.
- J. Hu, Z. Wang, Y. Fu, L. Lyu, Z. Lu and L. Zhou, In situ assembly of MnO2 nanosheets on sulfur-embedded multichannel carbon nanofiber composites as cathodes for lithium-sulfur batteries, Sci. China Mater., 2020, 63, 728–738 CrossRef CAS.
- H. Liu, J. M. Foster, A. Gully, S. Krachkovskiy, M. Jiang, Y. Wu, X. Yang, B. Protas, G. R. Goward and G. A. Botton, Three-dimensional investigation of cycling-induced microstructural changes in lithium-ion battery cathodes using focused ion beam/scanning electron microscopy, J. Power Sources, 2016, 306, 300–308 CrossRef CAS.
- P. Yan, J. Zheng, Z.-K. Tang, A. Devaraj, G. Chen, K. Amine, J.-G. Zhang, L.-M. Liu and C. Wang, Injection of oxygen vacancies in the bulk lattice of layered cathodes, Nat. Nanotechnol., 2019, 14, 602–608 CrossRef CAS.
- B. Song, T. Sui, S. Ying, L. Li, L. Lu and A. M. Korsunsky, Nano-structural changes in Li-ion battery cathodes during cycling revealed by FIB-SEM serial sectioning tomography, J. Mater. Chem. A, 2015, 3, 18171–18179 RSC.
|
This journal is © the Partner Organisations 2021 |
Click here to see how this site uses Cookies. View our privacy policy here.