DOI:
10.1039/D0NA01074J
(Paper)
Nanoscale Adv., 2021,
3, 2075-2088
The construction of a dual direct Z-scheme NiAl LDH/g-C3N4/Ag3PO4 nanocomposite for enhanced photocatalytic oxygen and hydrogen evolution†
Received
25th December 2020
, Accepted 3rd February 2021
First published on 26th February 2021
Abstract
Dual direct Z-scheme photocatalysts for overall water decomposition have demonstrated strong redox abilities and the efficient separation of photogenerated electron–hole pairs. Overall water splitting utilizing NiAl-LDH-based binary and ternary nanocomposites has been extensively investigated. The synthesized binary and ternary nanocomposites were characterized via XRD, FTIR, SEM, HRTEM, XPS, UV-DRS, and photoelectrochemical measurements. The surface wettability properties of the prepared nanocomposites were measured via contact angle measurements. The application of the NiAl-LDH/g-C3N4/Ag3PO4 ternary nanocomposite was investigated for photocatalytic overall water splitting under light irradiation. In this work, we found that in the presence of Ag3PO4, the evolution of H2 and O2 is high over LCN30, and 2.8- fold (O2) and 1.4-fold (H2) activity increases can be obtained compared with the use of LCN30 alone. It is proposed that Ag3PO4 is involved in the O2 evolution reaction during water oxidation and g-C3N4 is involved in overall water splitting. Our work not only reports overall water splitting using NiAl-LDH-based nanocomposites but it also provides experimental evidence for understanding the possible reaction process and the mechanism of photocatalytic water splitting. Photoelectrochemical measurements confirmed the better H2 and O2 evolution abilities of NiAl-LDH/g-C3N4/Ag3PO4 in comparison with NiAl LDH, g-C3N4, Ag3PO4, and LCN30. The observed improvement in the gas evolution properties of NiAl LDH in the presence of Ag3PO4 is due to the formation of a dual direct Z-scheme, which allows for the easier and faster separation of charge carriers. More importantly, the LCNAP5 heterostructure shows high levels of H2 and O2 evolution, which are significantly enhanced compared with LCN30 and pure NiAl LDH.
1. Introduction
The photocatalytic production of hydrogen and oxygen is one of the most promising approaches for overcoming both the energy and environmental issues that currently exist worldwide. This is because it is the best avenue for the direct generation of energy carriers that can be easily stored and transformed into electric energy.1,2 The water-splitting process consists of two half-reactions: water reduction with the evolution of H2; and water oxidation to produce O2.3 Oxygen evolution is hard to realize compared to hydrogen evolution due to the higher energy barrier. Moreover, 1 mol of water decomposes into 1 mol of hydrogen and 1/2 mol of oxygen, and 237 kJ is theoretically required for the water-splitting reaction under standard conditions. In general, a photocatalyst with a low (more positive) conduction band bottom or a high (more negative) valence band potential reduces the driving forces of photocatalytic reduction and oxidation reactions.4 Obtaining semiconductor photocatalysts with suitable redox potentials for water splitting is very difficult. At present, Z-scheme photocatalysts have generated much attention for achieving the complete water-splitting reaction. They can simultaneously reduce the recombination of charge carriers and retain strong redox abilities in the form of photo-excited electron–hole pairs.5
To date, 2D layered materials have also attracted extensive attention for photocatalytic water splitting. As a representative of layered materials, layered doubled hydroxides (LDHs) have attracted much attention in the field of catalysis due to their structures. Also, they have large surface-to-volume ratios, excellent chemical stability, low cost, low toxicity, rich redox activity, and appropriate band edges.6,7 LDHs are also known as anionic clays or hydrotalcite-like compounds, and they can be represented by the general formula [M2+1−xM3+x(OH)2]x+[Ax/n]n−·mH2O, where M2+ and M3+ represent divalent and trivalent metal cations, respectively, and An− represents interlayer anions.8 Unfortunately, single photocatalysts show limited performance during simultaneous water oxidation and reduction, and there is a need to develop heterojunction photocatalysts to enhance the redox reaction.9,10 In the available literature there are many examples of LDHs in suitable redox composites, e.g., with g-C3N4,11–13 CeO2,8 rGO,7 Cu2O,14 CdS,15 Ni5P4,16 CoP,17 and carbon black,18 and the water-splitting half-reaction (water reduction and oxidation) activities have been significantly increased. Hence, if suitable water redox composites are formed with LDHs, gaseous hydrogen and oxygen evolution could be achieved through water splitting.18 Polymeric g-C3N4 has recently attracted attention due to its enhanced visible response, tunable band structure, and extraordinary thermal and chemical stability.19,20 Formerly, our group studied the photocatalytic H2 evolution rates of LDH/g-C3N4 (in the presence of TEOA) composites through water splitting, which exhibited remarkable activities.11 Moreover, the excellent photocatalytic performance of LCN30 could be further improved through increasing the lifetimes of electrons and holes. Therefore, constructing an LCN30 ternary composite could not only facilitate charge carrier transfer at the interface of LDH and g-C3N4 but it could also improve the harvesting abilities for visible light.21,22
Several heterostructures have been fabricated to improve water splitting efficiencies in the literature.23–25 It is worth noting that silver orthophosphate (Ag3PO4) is a potential candidate in the field of photocatalytic water splitting due to its superior quantum efficiency under light irradiation.26 Loading Ag3PO4 onto P–g-C3N4 increased the photocatalytic hydrogen evolution activity 1.2-fold compared with pure P–g-C3N4.27 Tian et al. reported that Ag3PO4 coupled with g-C3N4/MOS2 to form a Z-scheme configuration can improve oxygen evolution during water splitting.28 The hybridization of Ag3PO4 with other semiconductors has resulted in superior water splitting performance. An artificial Z-scheme photocatalytic system is a gift for overall water splitting.29 This is because the Z-scheme system exhibits high quantum yields at a given wavelength and operates over a wide range of the solar spectrum.30 Z-scheme-type ternary photocatalytic composite materials have been proven to be more efficient than binary composite photocatalysts with single Z-scheme channels. The recombination of photoinduced electron–hole pairs can be suppressed due to an increased number of transfer channels. Moreover, the traditional charge-transfer process is not favorable for oxidation–reduction reactions.31–33 Herein, we designed a dual direct Z-scheme photocatalyst, in which NiAl-LDH/g-C3N4/Ag3PO4 serves as the H2 and O2 evolution photocatalyst. The synthesized dual direct Z-scheme photocatalyst shows enhanced photocatalytic activity for overall water splitting under light irradiation. Lastly, the enhanced activity of the dual direct Z-scheme photocatalyst can be attributed to Ag3PO4.
2. Experimental section
2.1. Materials
Nickel nitrate hexahydrate, aluminum nitrate nonahydrate, urea, disodium hydrogen phosphate dihydrate, and methylene blue stain were purchased from Merck India. Melamine was purchased from Loba Chemie Pvt. Ltd. Silver nitrate was purchased from Himedia chemical industry. All reagents were of analytical grade and used without further purification. DI water was used throughout the experiments.
2.2. Synthesis of the NiAl-LDH/g-C3N4 composite (LCN)
Pristine g-C3N4 was prepared via the heat treatment of melamine, as reported previously.11 To obtain NiAl-LDH/g-C3N4, as prepared g-C3N4 sheets (30 wt%) were dispersed in 25 ml of DI water through 20 min of sonication. In the meantime, an aqueous solution (60 ml) of Ni(NO3)2·6H2O and Al(NO3)3·9H2O was prepared at a 2
:
1 ratio. This clear green solution was added dropwise into 25 ml of the above g-C3N4 dispersion and vigorous stirring was carried out for 1 h. Then, 0.4 M urea was added into the suspension at room temperature. After being stirred for another 30 min, the NiAl-LDH/g-C3N4 suspension was transferred into a 100 ml Teflon-lined stainless-steel autoclave and heated at 140 °C for 10 h. The precipitate was collected, washed, and dried at 80 °C for 24 h. The obtained NiAl-LDH/g-C3N4 composite was denoted as LCN30.
2.3. Synthesis of NiAl-LDH/g-C3N4/Ag3PO4 (LCNAP)
1 g of NiAl-LDH/g-C3N4 (30 wt%) was dispersed in 80 ml of DI water via ultrasonication for 10 min. Then, 10 ml of Na2HPO4·2H2O solution was added into the above dispersion, followed by stirring for 10 min. Subsequently, 10 ml of AgNO3 solution was dropped into the above suspension, and this was then stirred for 15 min. After that, the resulting nanocomposite suspension was sonicated for 20 min in the dark at room temperature. The obtained final product was filtered and washed (with DI water and ethanol) several times and dried at 60 °C for 24 h. Nanocomposites were prepared via varying the ratio between Ag3PO4 and NiAl-LDH/g-C3N4, and these were designated as NiAl-LDH/g-C3N4/AgPOx (x = 5 and 10 wt%) and labeled as LCNAP5 and LCNAP10, respectively. The fabrication process for the NiAl-LDH/g-C3N4/Ag3PO4 composite is described in Scheme 1.
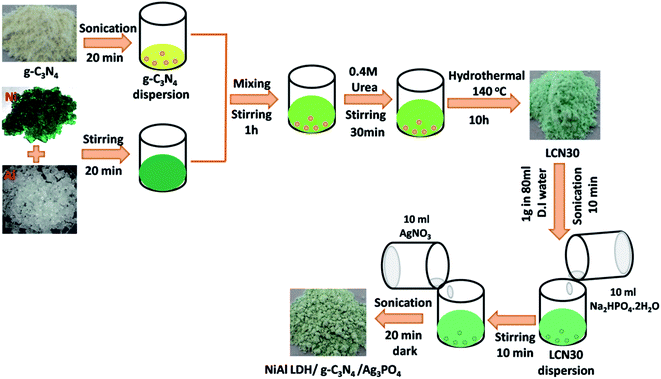 |
| Scheme 1 The fabrication process of the NiAl-LDH/g-C3N4/Ag3PO4 composite. | |
2.4. Characterization
The crystal structures and phase compositions of the synthesized products were identified in the range of 5 to 80° using a Rigaku Miniflex (Cu Kα Radiation) XRD diffractometer (operating at 40 kV and 30 mA). The surface functional groups of the materials were analyzed using a Brucker Tensor 27 Fourier-transform infrared spectrometer. The photoluminescence (PL) spectra were obtained using a JASCO-FP-8200 fluorescence spectrometer with an excitation wavelength of 380 nm. UV-visible diffuse reflectance spectra were obtained using a PerkinElmer Lambda 25 diffuse reflection spectrometer. X-ray photoelectron spectra characterization was carried out using an ESC 3400 photoelectron spectroscope system. FE-SEM and HR-TEM images were obtained using JEOL JSM 7001F and JEOL JEM 2100F electron microscopes. An Oxford EDS system was used to obtain EDS spectra and elemental maps. The water contact angles of the materials were measured with a Holmarch contact angle meter. A conventional three-electrode system using a BioLogic Science electrochemical workstation (France) was used to determine the photoelectrochemical properties of the samples. 20 mg of prepared catalyst and 100 μL of Nafion were ultrasonicated in 500 μL of ethanol for 30 min to get a slurry, which was then evenly spin-coated onto cleaned FTO (1 cm2) conducting glass to serve as the working electrode. Ag/AgCl (in saturated KCl solution) acted as the reference electrode and Pt acted as the counter electrode, and experiments were performed in 0.5 M Na2SO4 solution. A 150 W xenon lamp with a 1.5 AM filter was used for light irradiation for photoelectrochemical measurements. Transient photocurrent (I-t) measurements were performed for 500 s according to the chronoamperometry technique. Nyquist plots were obtained in the range between 1 MHz and 0.1 Hz via the electrochemical impedance spectroscopy (EIS) technique with an AC amplitude of 10 mV at the open circuit potential. Mott–Schottky (M–S) studies were done at a frequency of 1 kHz under dark conditions.
2.5. Measurements of the photocatalytic activity
The photocatalytic efficiencies of the prepared photocatalysts were tested based on the water-splitting reaction in a sealed air-tight quartz reactor under simulated light irradiation. The reactor contained 50 mg of photocatalyst in 50 ml of distilled water with a scavenger. For the H2 evolution reaction, 10% methanol (hole scavenger) solution [45 ml water + 5 ml methanol] was used, whereas 0.05 M AgNO3 (electron scavenger) solution was used for the O2 evolution reaction. The solution was stirred to prevent coagulation and subjected to light irradiation using a 250 W quartz tungsten halogen lamp as a light source. Before the photocatalytic reaction, the solution was purged with N2 gas for 1 h to remove dissolved gases. During the reaction, H2 and O2 gas samples were collected and analyzed using offline gas chromatography (CG-14C, Shimadzu, Japan) equipped with a TCD detector and 5 Å molecular sieve column with nitrogen as the carrier gas. Apparent quantum yields were determined via the following equations:
For H2 evolution:
For O2 evolution:
3. Results and discussion
3.1. Phase composition and morphology analyses
Fig. 1 presents the X-ray diffraction patterns of pure NiAl-LDH, g-C3N4, Ag3PO4, and LCNAP composites with different Ag3PO4 wt% values. From Fig. 1a, the diffraction peaks at 11.54°, 23.14°, 34.86°, 39.36°, 46.7°, 60.9°, and 62.3° match well with the (003), (006), (012), (015), (018), (110), and (113) planes, respectively, of pure NiAl-LDH (JCPDS card no. 15-0087).34,35 The diffraction peak at 27.1° is assigned to the (002) plane of graphitic carbon nitrate (JCPDS card no. 41-1487) (Fig. 1c).36 In LCNAP (Fig. 1e and f), the peaks at 33.18°, 36.53°, and 54.96° could be ascribed to the (210), (211), and (320) planes of the cubic phase of Ag3PO4, and this clearly showed the presence of both g-C3N4 and Ag3PO4 in the composites (JCPDS card no. 06-0505). Loading with Ag3PO4 causes a decrease in the peak intensity of the (003) plane of LCN30, as it steadily covers the surface of LCN30, controlling the growth of that peak. The XRD pattern confirms the presence of multiple phases (g-C3N4 and Ag3PO4) in the LCNAP composite.
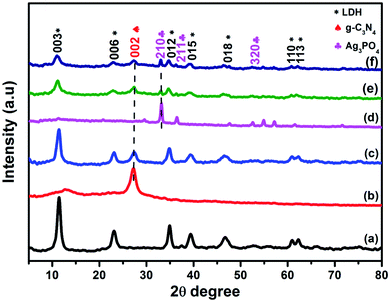 |
| Fig. 1 XRD patterns of (a) NiAl-LDH, (b) g-C3N4, (c) LCN30, (d) Ag3PO4, and (e and f) LCNA (5 and 10 wt%) nanocomposites. | |
The chemical compositions and vibrational modes of the synthesized samples are shown in Fig. 2. The broad bands at around 3580, 1630, and 1381 cm−1 correspond to the stretching and bending vibrations of interlayer and surface (O–H) water molecules. The band at 1370 cm−1 indicates the stretching vibrations of interlayer anionic carbonate groups. The band at 2150 cm−1 shows the presence of CO2 in the NiAl-LDH sample.37,38 Additionally, the peaks below 800 cm−1 represent the M–O (Ni–O and Al–O) and M–O–M (Ni–O–Al) bond stretching of NiAl-LDH.39 g-C3N4 exhibits a characteristic peak at 3200 cm−1 corresponding to the N–H stretching vibration mode, whereas the peak appearing at 1660 cm−1 is related to the aromatic C
N stretching vibration. The peak at 806 cm−1 is related to the stretching mode of the s-triazine unit of g-C3N4.40,41 In the case of pure Ag3PO4, the peaks observed at 1030 and 550 cm−1 can be ascribed to the P–O stretching vibration of PO4.42 As can be seen, all the characteristic peaks of NiAl-LDH, Ag3PO4, and g-C3N4 are observed in the LCNAP samples, confirming the formation of NiAl-LDH/g-C3N4/Ag3PO4 nanocomposites.
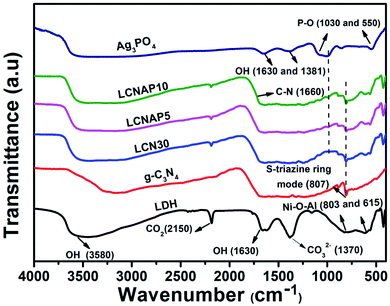 |
| Fig. 2 FTIR spectra of the NiAl-LDH, g-C3N4, LCN30, Ag3PO4, and LCNAP nanocomposites. | |
The surface morphologies and microstructures of the as-fabricated samples were probed via FE-SEM, TEM, and HR-TEM techniques. Fig. 3(a and b) and 4(a and b) show pure LDH and g-C3N4, demonstrating their sheet structures. From the SEM image, it can be observed that pure Ag3PO4 exhibited irregular spheroidal structures with sizes ranging from 200–400 nm, as depicted in Fig. 3c. The synthesis of Ag3PO4 was carried out based on silver–ligand complexes with Na2HPO4 at room temperature. The irregular structure of Ag3PO4 was due to the direct reaction of AgNO3 and Na2HPO4 in water.43Fig. 3f shows an SEM image of LCNAP10; both the g-C3N4 sheets and Ag3PO4 nanoparticles appear to be uniformly distributed on the surfaces of the NiAl-LDH layers. After the formation of the ternary composite, this helps to create better photoexcited electron–hole separation, hence improving the photo-oxidation and -reduction compared with LCN30. To further establish the emergence of g-C3N4 and Ag3PO4 on the surface of NiAl-LDH, TEM analysis of LCNAP5 was carried out (Fig. 4). Fig. 4e reveals that the heterostructure possesses multiple overlapping layers, with g-C3N4 and Ag3PO4 electrostatically assembled on the surfaces of the NiAl-LDH sheets, resulting in the formation of the LCNAP nanocomposite. However, the Ag3PO4 nanoparticles are not easily detected in the LCNAP5 composite (Fig. 3e and 4e) because they are loaded at a very low wt% on the surface of LCN30. Furthermore, HRTEM analysis was used to provide pivotal evidence for the suitable interaction of components and the formation of the LCNAP5 heterostructure. As shown in the insets of Fig. 4a–c, the lattice fringe patterns of NiAl-LDH, g-C3N4, and Ag3PO4 have d-spacing values of 0.76, 0.32, and 0.262 nm, respectively, corresponding to the (003), (002), and (210) planes, respectively, which are consistent with their XRD patterns. In addition, the lattice fringes of Ag3PO4 are not visible in the composite samples (Fig. 4e and f), revealing the existence of heavy-atom formation. The energy-dispersive X-ray spectrum and elemental mapping of the LCNAP5 nanocomposite are shown in Fig. 5a–i, confirming the existence of C, O, N, Ni, Al, Ag, and P elements. These results indicate the successful formation of the NiAl-LDH/g-C3N4/Ag3PO4 nanocomposite.
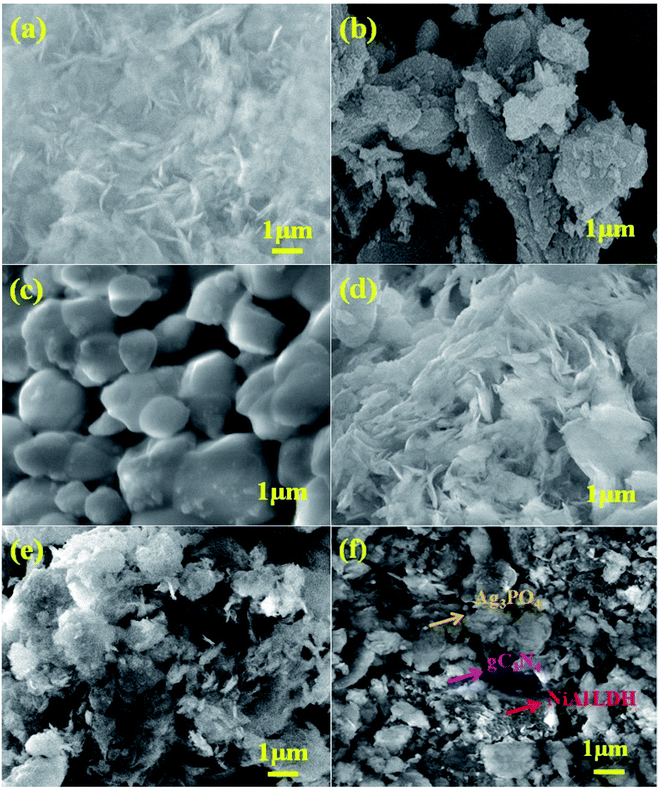 |
| Fig. 3 FE-SEM images of (a) NiAl-LDH, (b) g-C3N4, (c) Ag3PO4, and the (d) LCN30, (e) LCNAP5, and (f) LCNAP10 nanocomposites. | |
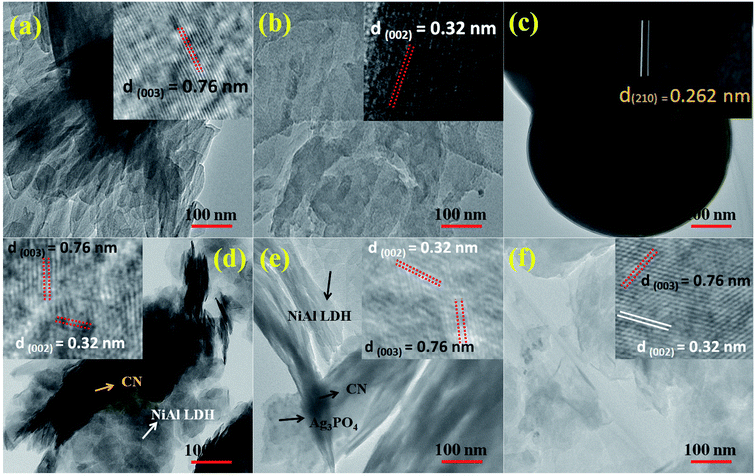 |
| Fig. 4 TEM and HRTEM images of (a) NiAl-LDH, (b) g-C3N4, (c) Ag3PO4, and the (d) LCN30, (e) LCNAP5, and (f) LCNAP10 nanocomposites. | |
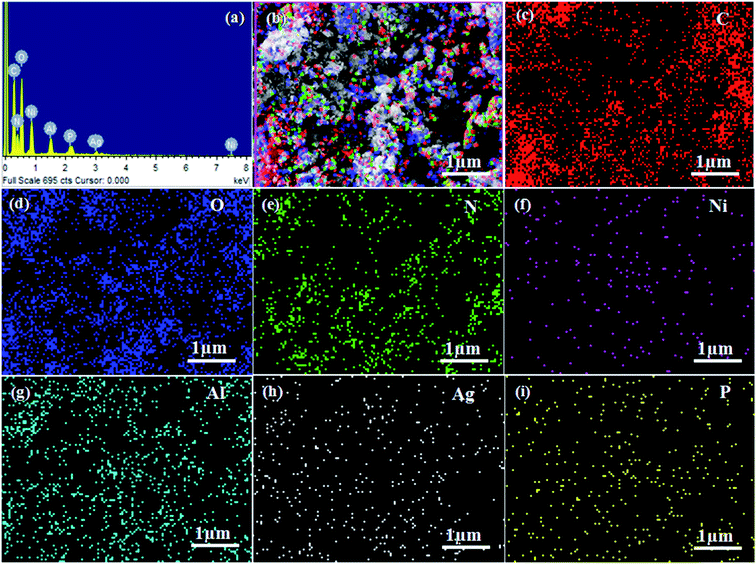 |
| Fig. 5 (a) The energy-dispersive X-ray (EDX) spectrum and (b–i) elemental mapping (EDS) images of the LCNAP5 nanocomposite. | |
3.2. Surface chemical composition
The chemical and electronic structures of the synthesized LCNAP5 nanocomposite were investigated via X-ray photoelectron spectroscopy (XPS) studies. The survey spectrum in Fig. 6a displays the existence of Ag, P, Ni, Al, C, N, and O elements. The high-resolution spectra of pure g-C3N4 and Ag3PO4 are presented in Fig. S1 and S2.† Characteristic C 1s peaks in the spectrum were observed at 282.3, 284.7, and 285.6 eV, relating to the C–OH, C–C, and C–O/C–N bonds of the prepared samples; these also indicated the presence of intercalated carbonate anions in the layer structure of NiAl-LDH.8,44,45 Peaks at 529 and 530.5 eV were also present in the O 1s spectrum: the first peak indicated lattice oxygen (O2−) in the pure and heterogeneous multiphase nanocomposite; and the second peak was attributed to oxygen bonds in the carbonate anions in the LDH interlayers (Fig. 6c). The peak at 531.5 eV indicated the presence of C–OH bonds in pure Ag3PO4 (Fig. S2†).45,46 In the N 1s spectrum (Fig. S1† and 6d), the three peaks located at 395.2, 396.4, and 401.1 eV in the pure g-C3N4 spectrum and at 395.4, 397.1, and 401.3 eV in the LCNAP5 spectrum could be assigned to the nitrogen-bonded species of C–N
C, N–(C)3, and C–N–H, respectively.47 In the Ni 2p spectrum, the 2p3/2 and 2p½ peaks at 854.6 and 871.8 eV, respectively, indicated the existence of Ni2+, whereas the satellite peaks appearing at 860.3 and 873.4 eV signified the presence of high-spin divalent Ni2+ in this hydrotalcite sample (Fig. 6e).48 Moreover, in the Al 2p spectrum (Fig. 6f), trivalent Al3+ can be determined with a binding energy of 67 eV, and a binding energy at 72 eV indicates Al(0).49,50 The observation of Ag and P peaks manifested the presence of Ag3PO4 in the composite, as shown in Fig. 6g and h. The spectra in Fig. 6g and S2† show that the characteristic peaks of Ag 3d were located at 367.65 and 373.72 eV for pure Ag3PO4 and at 365.03 and 371.02 eV for LCNAP5. Compared with pure Ag3PO4, the binding energies of the LCNAP5 composite were decreased, which indicates strong interfacial interactions between Ag3PO4 and LCN30.51 From Fig. 6h and S2,† the peak observed at 133.57 eV indicates the presence of phosphate ions in the P 2p orbital state.52
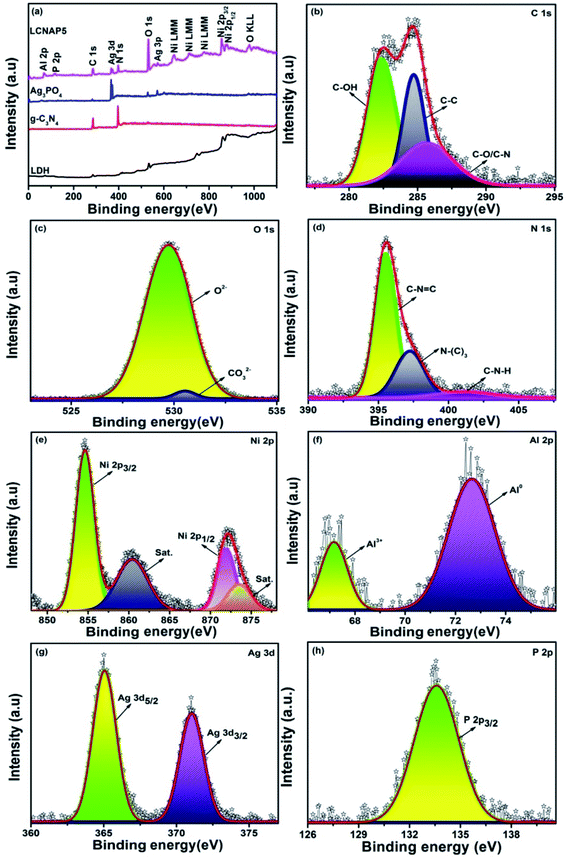 |
| Fig. 6 (a) XPS survey spectra of pure LDH, g-C3N4, Ag3PO4, and the LCNAP5 nanocomposite, and high-resolution (b) C 1s, (c) O 1s, (d) N 1s, (e) Ni 2p, (f) Al 2p, (g) Ag 3d, and (h) P 2p spectra of the LCNAP5 nanocomposite. | |
3.3. Optical properties and energy band structure
The water-splitting activity of a photocatalyst is particularly related to its optical absorption and band-structure characteristics. In this regard, UV-vis DRS and Mott–Schottky measurements were carried out to investigate the optical properties and energy band structures of NiAl-LDH, Ag3PO4, LCN30, and LCNAP photocatalysts, as presented in Fig. 7. NiAl-LDH displays three apparent absorption bands; the one that appears in the UV range (200 to 300 nm) is assigned to ligand–metal charge transfer (LMCT) from a transition occurring between the 2p orbital of O and the 3d orbitals of Ni2+ ions in the LDH layer, and the other two broad absorption bands located in the visible range (300–500 nm and 600–800 nm) correspond to the d–d transitions of Ni2+ ions with MO6 octahedral geometry (Fig. 7a). The 3A2g (F) → 3T1g (P) and 3A2g (F) → 3T1g (F) spin-allowed transitions give rise to bands at 380 and 740 nm and the bands at 420 and 640 nm correspond to the spin-forbidden transitions of 3A2g (F) → 1T2g (D) and 3A2g (F) → 3T2g (D), respectively.37,53,54 Furthermore, the light absorption of NiAl-LDH is enhanced in the visible range upon the addition of g-C3N4, which indicates strong co-ordination between NiAl-LDH and g-C3N4 in the resulting LCN30 heterojunction. Upon the loading of Ag3PO4, the LCNAP composites possess significantly improved absorption in the visible region (470 nm) compared to the other two samples (NiAl-LDH and LCN30) and there is an obvious red shift of the absorption edge. According to the UV-DRS spectra, the bandgap energies estimated from Tauc plots of NiAl-LDH, g-C3N4, Ag3PO4, LCN30, and LCNAP5 are 2.53, 2.69, 2.26, 2.62, and 2.56 eV, respectively (Fig. S3†). Furthermore, it was observed that the bandgap of LCNAP5 was considerably decreased after the loading of Ag3PO4. In addition to a suitable bandgap, determining the position of the valence band and the conduction band of a prepared photocatalyst is also extremely important when constructing a photocatalyst. As shown in Fig. 7b and c, M–S plots of pure NiAl-LDH, g-C3N4, Ag3PO4, and composite LCN30 and LCNAP5 samples were obtained. All samples showed positive slopes in the M–S plots, suggesting that they are n-type semiconductors. Furthermore, the flat-band potential (Vfb) can be determined based on the Mott–Schottky (M–S) plots. The estimated flat-band potentials are −0.43, −0.64, 0.58, −0.54, and −0.47 V vs. Ag/AgCl (at pH = 7) for pure NiAl-LDH, g-C3N4, Ag3PO4, and the LCN30 and LCNAP5 composites, respectively. Moreover, the carrier densities (ND) can be estimated based on the slopes of the Mott–Schottky plots. The calculated carrier density values of pure NiAl-LDH, g-C3N4, Ag3PO4, and the LCN30 and LCNAP5 nanocomposites are reported in Table 1. They show that after the formation of a composite between LCN30 and Ag3PO4, the carrier density was significantly increased compared with pure samples. Therefore, the LCNAP5 composite can improve charge separation and extend the photoresponse of the photocatalyst, resulting in improved photocatalytic water splitting activity. This suggests the creation of superior performance upon the deposition of g-C3N4 and Ag3PO4.
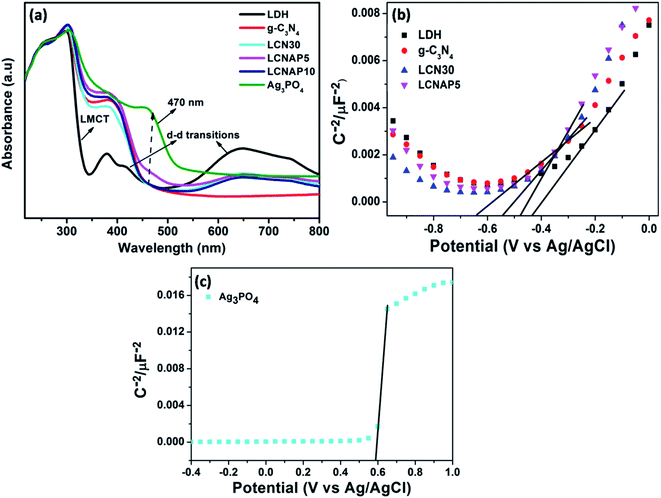 |
| Fig. 7 (a) UV-DRS spectra and (b and c) M–S plots of pure NiAl-LDH, g-C3N4, Ag3PO4, and the LCN30 and LCNAP nanocomposites. | |
Table 1 Flat-band potentials and carrier concentrations (ND) of the studied materials
Catalyst |
Flat-band potential (Vfb; V) |
Carrier concentration (ND; cm−3) |
NiAl LDH |
−0.43 |
3.88 ×1021 |
g-C3N4 |
−0.64 |
6.25 × 1021 |
Ag3PO4 |
0.58 |
1.83 ×1021 |
LCN30 |
−0.54 |
7.30 × 1021 |
LCNAP5 |
−0.47 |
9.39 ×1021 |
3.4. Wettability and water contact angles
The surface wettability is intimately related to the catalytic performance, and it involves the interaction between a liquid and solid in contact. Water contact angles were measured to verify the wetting behaviors of the prepared samples. As shown in Fig. 8a and b, pure NiAl-LDH, gCN, and the LCN30 nanocomposite exhibited contact angles of 26.56°, 52.89°, and 42.01°, respectively.55,56 Moreover, improved hydrophilicity was achieved upon the further modification of LCN30 with Ag3PO4, and the contact angles were found to be 29.31° and 49.06° for LCNAP5 and LCNAP10, respectively (Fig. 8e and f). LCNAP5 is significantly more hydrophilic than LCNAP10 (as indicated by the higher water contact angle value). The water contact angle of a photocatalyst is different when the surface functional groups are different. The excess amount of Ag3PO4 controls the water contact angle of LCNAP10 because it blocks the OH groups of the photocatalyst surface. It is known that when surfaces have hydrophilic properties, the photocatalytic performance is also high.
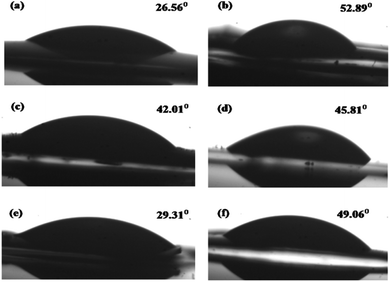 |
| Fig. 8 The water contact angles of (a) NiAl-LDH, (b) g-C3N4, (c) LCN30, (d) Ag3PO4, and the (e) LCNAP5 and (f) LCNAP10 nanocomposites. | |
3.5. Photocatalytic overall water splitting activities
Fig. 9 shows photocatalytic H2 evolution from aqueous methanol solution and O2 evolution from aqueous silver nitrate. The length of H2 and O2 evolution using pure NiAl-LDH, Ag3PO4, and the LCN30 and LCNAP nanocomposites was 4 h, and a 250 Watt QTH lamp was used (Fig. 9a and c). Fig. 9b and d shows that only the composite samples (LCN30 and LCNAP) can evolve H2 and O2, whereas pure NiAl-LDH and Ag3PO4 could not produce H2 gas. Further, the overall water splitting activity was improved upon the addition of Ag3PO4. When forming a ternary composite with the ratio seen in LCNAP5, higher rates of gas evolution were obtained [H2 = 268 μmol g−1 h−1; O2 = 4330 μmol g−1 h−1] compared with the LCN30 composite. The apparent quantum yields with the LCNAP5 nanocomposite are 1.29% (H2) and 41.71% (O2). Comparisons of H2 and O2 evolution performance between relevant reported photocatalytic systems and the LCNAP5 nanocomposite are presented in Tables 2 and 3. The gas evolution rates of pure and composite samples are shown in Fig. 10; the gas evolution performance dropped when 10 wt% Ag3PO4 was used. This concentration dependence is attributed to the overloading of Ag3PO4 on the LCN30 surface. Unfortunately, the large amount of Ag3PO4 that seems to occupy the active centers on the surface of LCN30 may hinder light penetration into the composite material, and it might restrict interfacial charge transfer between NiAl-LDH, g-C3N4, and Ag3PO4, leading to lower H2 and O2 production with the LCNAP10 nanocomposite. The NiAl-LDH/g-C3N4/Ag3PO4 composite with a loading amount of 5 wt% Ag3PO4 revealed the best photocatalytic water reduction and oxidization efficiencies.
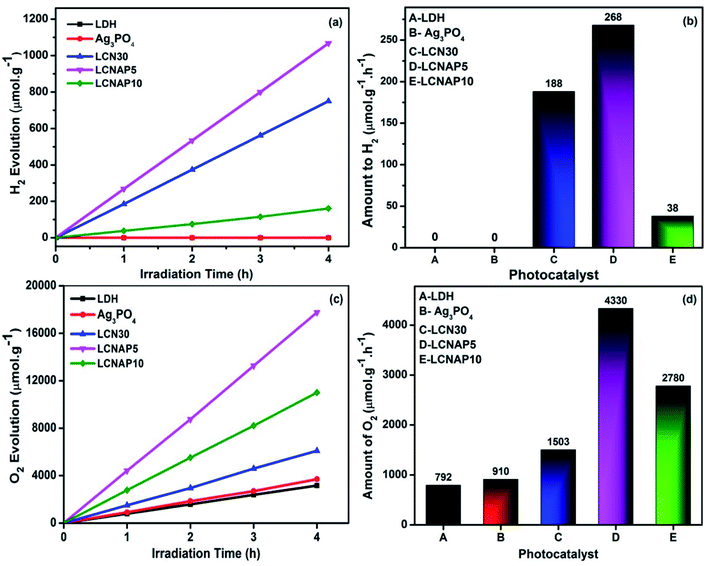 |
| Fig. 9 The time depended and comparative plots of pure NiAl LDH, Ag3PO4 and LCN30, LCNAP nanocomposites (a and b) water reduction and (c and d) water oxidation. | |
Table 2 A comparison of the H2 evolution performances of relevant photocatalysts
Photocatalyst |
Light source |
Sacrificial donor |
H2 production, μmol g−1 h−1 |
Reference |
NiAl-LDH/gC3N4/Ag3PO4 |
250 W quartz tungsten halogen lamp |
Methanol |
268 |
This work |
Co(OH)2/gC3N4 |
300 W Xe lamp |
TEOA |
0 |
57
|
Co3O4/gC3N4 |
Visible light |
TEOA |
50 |
58
|
Pt/NiTi-LDH |
300 W Xe lamp |
Lactic acid |
153 |
59
|
Pt/MgAlTi-LDH |
300 W Xe lamp |
Lactic acid |
49 |
59
|
Au/layered H2SrTa2O7 |
300 W Xe lamp |
— |
17.5 |
60
|
NYF@Ag3PO4@black phosphorus |
Laser light |
Glycerol |
145.9 |
61
|
Ag3PO4/polyoxometalates/GO |
500 W Xe arc lamp |
Methanol |
50.75 |
62
|
Co2P/gC3N4 |
300 W Xe lamp |
TEOA |
53.3 |
63
|
Table 3 A comparison of the O2 evolution performances of relevant photocatalysts
Photocatalyst |
Light source |
Sacrificial donor |
O2 production, μmol g−1 h−1 |
Reference |
NiAl-LDH/gC3N4/Ag3PO4 |
250 W quartz tungsten halogen lamp |
AgNO3 |
4330 |
This work |
ZnCr-LDH/layered TiO2 |
450 W Xe lamp |
AgNO3 |
1180 |
64
|
ZnCr-LDH/RGO |
450 W Xe lamp |
AgNO3 |
1200 |
65
|
gC3N4/NiFe-LDH |
125 W mercury lamp |
AgNO3 |
886 |
66
|
NiFe-LDH/N-rGO/g-C3N4 |
125 W Hg lamp |
AgNO3 |
1280 |
7
|
Ag@Ag3VO4/ZnCr-LDH |
150 W Hg lamp |
AgNO3 |
571 |
67
|
TbZnCr-LDH |
150 W Xe lamp |
AgNO3 |
1022 |
68
|
MoSe2/Ag3PO4 |
25 mW white light LED |
AgNO3 |
182 |
69
|
TiO2@CoAl-LDH |
300 W Xe lamp |
AgNO3 |
2240 |
70
|
Ag3PO4/graphdiyne/g-C3N4 |
300 W Xe lamp |
AgNO3 |
753.1 |
71
|
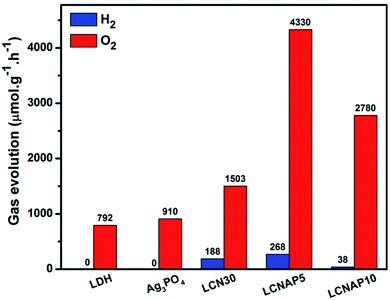 |
| Fig. 10 The photocatalytic overall water splitting performances of the prepared samples under light irradiation. | |
The photocatalytic recyclability and stability of a photocatalyst are very important for its practical application. Therefore, cyclic testing of LCNAP5 was carried out to estimate the H2 and O2 production stability of the catalyst (Fig. 11a and b) under light irradiation for 4 days, with each experiment conducted for 4 h. After the end of the third cycle, the catalytic activity was slightly decreased, although the water reducing activity of LCNAP5 remained at 84% (Fig. 11a). At the same time, the water oxidation activity of LCNAP5 was maintained at 82% (Fig. 11b). Thereafter, upon the addition of the sacrificial reagents methanol (CH3OH) and silver nitrate (AgNO3) to the same reaction mixture, the photocatalyst almost regained its maximum activity. Hence it is clear that a decreased concentration of sacrificial reagents was the main reason for the declining activity. This confirmed that the LCNAP5 nanocomposite is stable for both H2 and O2 production during long-term photocatalytic reactions.
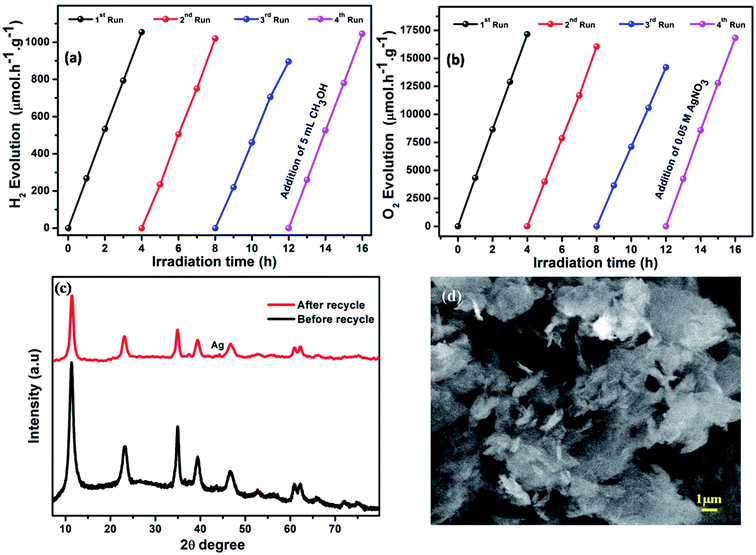 |
| Fig. 11 Cycling study of LCNAP5 during light-driven (a) water reduction and (b) water oxidation reactions. (c) XRD patterns of LCNAP5 before and after 4 cycles of water oxidation. (d) An SEM image of LCNAP5 after 4 cycles of water oxidation. | |
As shown in Fig. 11c and d, X-ray diffraction patterns and SEM images of the LCNAP5 nanocomposite after 4 cycles of water oxidation were obtained. One new peak located at 44.2° was seen in the XRD pattern after the photocatalytic reaction, which indicates that some Ag3PO4 has decomposed to Ag.69 Ag could cover active sites on the surface of LCNAP5, resulting in a decrease in the photocatalytic efficiency. However, only a small amount of Ag was formed during the recycling process, so no obvious differences were observed in the SEM image after 4 cycles of water oxidation.
3.6. Photoelectrochemical and photoluminescence analysis
The charge-carrier generation behavior and their migration abilities in the LCNAP ternary composite were verified based on the transient photocurrent response and electrochemical impedance spectroscopy (EIS) under light irradiation. As shown in Fig. 12a, the photocurrent density of LCNAP5 is much higher than those of NiAl-LDH, g-C3N4, Ag3PO4, LCN30, and LCNAP10, suggesting efficient photogenerated electron–hole-pair separation. A higher photocurrent intensity suggests a slower recombination rate of photoinduced carriers. Furthermore, the charge-carrier lifetime can be obtained from the photocurrent response using the following kinetic equation:47,72,73
where I(t) denotes the current at a certain time, and I is the photoanode current where ‘i’ and ‘f’ represent the initial and final states, respectively. It is found that the lifetimes of NiAl-LDH, g-C3N4, Ag3PO4, LCN30, LCNAP5, and LCNAP10 are 5.10, 4.21, 6.89, 6.39, 11.65, and 7.40 s, respectively. The carrier lifetime of 5 wt% LCNAP indicates a decrease in the recombination rate and an increase in the lifetime of photogenerated excitons. To further verify the efficient charge transfer and electrical conductivity, EIS Nyquist plot measurements were carried out, and the results are shown in Fig. 12b. The inset shows the equivalent circuit model, in which Rs, Rct, and CPE are the internal resistance, charge-transfer resistance, and a parallel constant phase element, respectively. The calculated Rct values for NiAl-LDH, g-C3N4, Ag3PO4, LCN30, LCNAP5, and LCNAP10 are 70.67, 92.5, 40.27, 53.02, 18.03, and 33.76 kΩ,74 respectively. As LCNAP5 has lower charge transfer resistance, it revealed enhanced capacitance behavior and less resistance against charge-carrier diffusion. Generally, a small radius indicates high charge-carrier transfer. Compared with LCN30, the impedance spectrum of the LCNAP5 composite shows a smaller diameter, indicating greatly enhanced charge-carrier transfer due to the superior electrical properties of Ag3PO4.
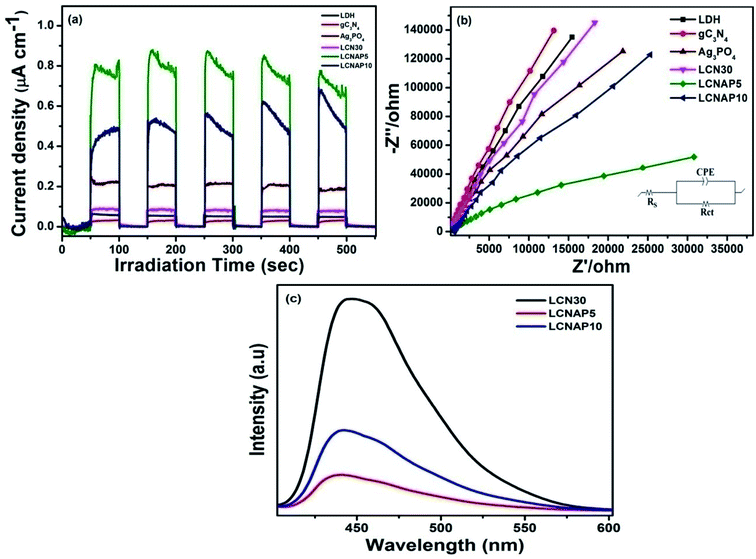 |
| Fig. 12 (a) Photocurrent responses and (b) Nyquist impedance plots of pure and composite samples. (c) PL emission spectra of LCN30, LCNAP5, and LCNAP10 photocatalysts. | |
Subsequently, the photoluminescence (PL) emission was studied to determine the photogenerated electron and hole separation efficiencies of the photocatalysts. Fig. 12c shows the PL spectra of LCN30, LCNAP5, and LCNAP10 using an excitation wavelength of 380 nm. LCNAP5 exhibited a lowered recombination rate of excitons in comparison to LCNAP10, which might be due to the excess loading of Ag3PO4 on the surface of LCN30. The results obtained from the PL measurements of LCNAP5 support the photocurrent measurement results, which indicated that electron–hole-pair separation was improved upon introducing Ag3PO4 on LCN30, which further leads to efficient photocatalytic evolution.
3.7. Mechanism of the dual direct Z-scheme system
The band alignment between NiAl-LDH, g-C3N4, and Ag3PO4 leads to the formation of a Z-scheme system, which plays a crucial role in determining the photocatalytic water splitting activity of the NiAl-LDH/g-C3N4/Ag3PO4 nanocomposite. According to the M–S plots, the estimated ECB values of NiAl-LDH, g-C3N4, and Ag3PO4 were −0.43, −0.64, and 0.58 eV, respectively.75 Moreover, the VB position can be determined using the following relation:31
where ECB is the conduction band position and Eg is the bandgap. The calculated EVB positions of pure NiAl-LDH, g-C3N4, and Ag3PO4 were 2.1, 2.05, and 2.84 eV, respectively. The conduction and valance band positions of NiAl-LDH, g-C3N4, and Ag3PO4 for photocatalytic water splitting are represented in Fig. 13a. The higher VB potential of Ag3PO4 exerts a strong driving force for the separation of photogenerated charge pairs in the space charge region. Based on the above results, the photocatalytic water splitting mechanism of NiAl-LDH/g-C3N4/Ag3PO4 is proposed, as shown in Fig. 13b. The coupling of semiconductors with various band structures can expand the visible light absorption range and enhance the lifetime of charge carriers due to charge separation. The charge transfer mechanism of the Z-scheme system is different from traditional and heterojunction photocatalysts; in this scheme, at least one material should satisfy either oxidation or reduction reaction conditions. Hence, electrons from the lower CB recombine with holes from the higher VB. Moreover, the electrons from the higher CB generate H2 and those from the lower VB generate O2. In this process, only half of the photoexcited electrons and holes are completely used. The introduction of Ag3PO4 into NiAl-LDH and g-C3N4 favors enhanced H2 and O2 evolution from the dual direct Z-scheme system. Under illumination, photoexcited electrons from the CB of Ag3PO4 can directly combine with holes from the VB of NiAl-LDH, while excited electrons migrate to the CB of NiAl-LDH. In the meantime, holes are left in the VB and electrons are stored in the CB of g-C3N4. The holes in the VB of Ag3PO4 and the electrons in the CB of g-C3N4 are used to improve the strong redox abilities for H2 and O2 evolution. In this process of photocatalytic water splitting, the evolution of hydrogen and the evolution of oxygen occur separately at opposite surfaces of the semiconductor photocatalyst due to the half-reaction system in the dual direct Z-scheme. Furthermore, the positive band potential of Ag3PO4 can be used as a hole carrier, providing effective charge transfer.
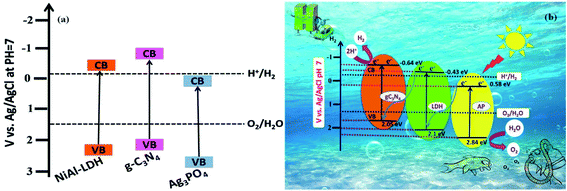 |
| Fig. 13 (a) The band structures of the pure samples. (b) A schematic diagram of the photocatalytic water splitting mechanism over the LCNAP photocatalyst system under light irradiation. | |
4. Conclusions
In summary, the effects of Ag3PO4 on the photocatalytic water splitting activity of NiAl-LDH/g-C3N4 sheets were investigated. The performance was much improved when using the LCNAP5 ternary nanocomposite compared to pure LDH and the LCN30 binary nanocomposite. It was established that LCNAP5 demonstrated enhanced water splitting activity due to promoted charge transfer and suppressed charge recombination. The results strongly suggest that during the water-splitting reaction both the water oxidation (O2 evolution) and reduction (H2 evolution) reactions are enhanced after the addition of Ag3PO4. This work not only develops a NiAl-LDH/g-C3N4/Ag3PO4 ternary nanocomposite with high photocatalytic activity to achieve overall water splitting but it also provides deeper understanding for constructing efficient dual direct Z-scheme systems.
Conflicts of interest
There are no conflicts to declare.
Acknowledgements
The authors would like to acknowledge DST-SERB, India (F. No. EMR/2017/001238), and DIST (Ref No. SR/FST/PS-II/2017/28(C)) for financial support.
References
- D. Li, D. Wang, H. Tang, X. Yang and Q. Liu, ACS Sustainable Chem. Eng., 2019, 7, 8466–8474 CrossRef CAS.
- X. Guan and L. Guo, ACS Catal., 2014, 4, 3020–3026 CrossRef CAS.
- Y. J. Yuan, D. Chen, S. Yang, L. X. Yang, J. J. Wang, D. Cao, W. Tu, Z. T. Yu and Z. G. Zou, J. Mater. Chem. A., 2017, 5, 21205–21213 RSC.
- S. H. Chen, Y. S. Jiang and H. Y. Lin, ACS Omega, 2020, 5, 8927–8933 CrossRef CAS.
- N. Wang, L. Wu, J. Li, J. Mo, Q. Peng and X. Li, Sol. Energy Mater. Sol. Cells, 2020, 215, 110624 CrossRef CAS.
- R. Boppella, C. H. Choi, J. Moon and D. H. Kim, Appl. Catal., B, 2018, 239, 178–186 CrossRef CAS.
- S. Nayak and K. M. Parida, Sci. Rep., 2019, 9, 1–23 CrossRef CAS.
- S. Nayak and K. M. Parida, Int. J. Hydrogen Energy, 2016, 41, 21166–21180 CrossRef CAS.
- S. Bai, C. Gao, J. Low and Y. Xiong, Nano Res., 2019, 1–24 Search PubMed.
- S. Zhong, Y. Xi, Q. Chen, J. Chen and S. Bai, Nanoscale, 2020, 12, 5764–5791 RSC.
- S. Megala, M. Sathish, S. Harish, M. Navaneethan, S. Sohila, B. Liang and R. Ramesh, Appl. Surf. Sci., 2020, 509, 144656 CrossRef CAS.
- C. Prasad, H. Tang, Q. Liu, I. Bahadur, S. Karlapudi and Y. Jiang, Int. J. Hydrogen Energy, 2020, 45, 337–379 CrossRef CAS.
- Q. Liu, J. Huang, L. Wang, X. Yu, J. Sun and H. Tang, Sol. RRL, 2020, 2000504 CrossRef.
- C. Wang, B. Ma, S. Xu, D. Li, S. He, Y. Zhao, J. Han, M. Wei, D. G. Evans and X. Duan, Nano Energy, 2017, 32, 463–469 CrossRef CAS.
- S. Li, L. Wang, Y. Li, L. Zhang, A. Wang, N. Xiao, Y. Gao, N. Li, W. Song, L. Ge and J. Liu, Appl. Catal., B, 2019, 25, 4145–4155 Search PubMed.
- X. Liu, Y. Zhao, X. Yang, Q. Liu, X. Yu, Y. Li and T. Zhang, Appl. Catal., B, 2020, 119144 CrossRef CAS.
- Q. Liu, J. Huang, H. Tang, X. Yu and J. Shen, J. Mater. Sci. Technol., 2020, 56, 196–205 CrossRef.
- T. S. Munonde, H. Zheng and P. N. Nomngongo, Ultrason. Sonochem., 2019, 59, 104716 CrossRef CAS.
- X. Li, K. Pan, Y. Qu and G. Wang, Nano Res., 2018, 11, 1322–1330 CrossRef CAS.
- Y. N. Liu, C. C. Shen, N. Jiang, Z. W. Zhao, X. Zhou, S. J. Zhao and A. W. Xu, ACS Catal., 2017, 7, 8228–8234 CrossRef CAS.
- B. Song, Z. Zeng, G. Zeng, J. Gong, R. Xiao, S. Ye, M. Chen, C. Lai, P. Xu and X. Tang, Adv. Colloid Interface Sci., 2019, 272, 101999 CrossRef CAS.
- R. Kavitha, P. M. Nithya and S. Girish Kumar, Noble metal deposited graphitic carbon nitride based heterojunction photocatalysts, Appl. Surf. Sci., 2020, 508, 145142 CrossRef.
- K. Kaviyarasu, C. M. Magdalane, D. Jayakumar, Y. Samson, A. K. H. Bashir, M. Maaza and J. Kennedy, J. King Saud Univ., Sci., 2020, 32, 1516–1522 CrossRef.
- S. Panimalar, R. Uthrakumar, E. T. Selvi, P. Gomathy, C. Inmozhi, K. Kaviyarasu and J. Kennedy, Surf. Interfaces, 2020, 100512 CrossRef.
- C. M. Magdalane, K. Kaviyarasu, G. M. A. Priyadharsini, A. K. H. Bashir, N. Mayedwa, N. Matinise and M. Maaza, J. Mater. Res. Technol., 2019, 8, 2898–2909 CrossRef CAS.
- H. Zhang, D. Yu, W. Wang, P. Gao, K. Bu, L. Zhang, S. Zhong and B. Liu, Adv. Powder Technol., 2019, 30, 1910–1919 CrossRef CAS.
- P. Chen, L. Chen, S. Ge, W. Zhang, M. Wu, P. Xing, T. B. Rotamond, H. Lin, Y. Wu and Y. He, Int. J. Hydrogen Energy, 2020, 42, 14354–14367 CrossRef.
- L. Tian, X. Yang, X. Cui, Q. Liu and H. Tang, Appl. Surf. Sci., 2019, 463, 9–17 CrossRef CAS.
- M. Han, L. Hu, Y. Zhou, S. Zhao, L. Bai, Y. Sun and Z. Kang, Catal. Sci. Technol., 2018, 8, 840–846 RSC.
- K. Maeda, D. Lu and K. Domen, ACS Catal., 2013, 3, 1026–1033 CrossRef CAS.
- W. Liu, J. Shen, X. Yang, Q. Liu and H. Tang, Appl. Surf. Sci., 2018, 45, 6369–6378 Search PubMed.
- J. Li, H. Hao and Z. Zhu, Mater. Lett., 2016, 168, 180–183 CrossRef CAS.
- Z. Dong, Y. Wu, N. Thirugnanam and G. Li, Appl. Surf. Sci., 2018, 430, 293–300 CrossRef CAS.
- W. Zheng, S. Sun, Y. Xu, R. Yu and H. Li, J. Alloys Compd., 2018, 768, 240–248 CrossRef CAS.
- R. Xie, G. Fan, Q. Ma, L. Yang and F. Li, J. Mater. Chem. A., 2014, 2, 7880–7889 RSC.
- J. Wang, G. Fan, H. Wang and F. Li, Ind. Eng. Chem. Res., 2011, 50, 13717–13726 CrossRef CAS.
- S. Tonda, S. Kumar, M. Bhardwaj, P. Yadav and S. Ogale, ACS Appl. Mater. Interfaces, 2018, 10, 2667–2678 CrossRef CAS.
- D. P. Sahoo, S. Nayak, K. H. Reddy, S. Martha and K. Parida, Inorg. Chem., 2018, 57, 3840–3854 CrossRef CAS.
- J. Ni, J. Xue, L. Xie, J. Shen, G. He and H. Chen, Phys. Chem. Chem. Phys., 2018, 20, 414–421 RSC.
- J. Barzegar, A. Habibi-Yangjeh, A. Akhundi and S. Vadivel, Solid State Sci., 2018, 78, 133–143 CrossRef CAS.
- S. Sun, X. Gou, S. Tao, J. Cui, J. Li, Q. Yang, S. Liang and Z. Yang, Mater. Chem. Front., 2019, 3, 597–605 RSC.
- L. Liu, Y. Qi, J. Lu, S. Lin, W. An, Y. Liang and W. Cui, Appl. Catal., B, 2016, 183, 133–141 CrossRef CAS.
- Y. S. Xu and W. D. Zhang, CrystEngComm, 2013, 15, 5407–5411 RSC.
- X. Du, Z. Zhang, H. Chen and P. Liang, Appl. Surf. Sci., 2020, 499, 143939 CrossRef CAS.
- D. P. Sahoo, S. Patnaik, D. Rath and K. M. Parida, Inorg. Chem. Front., 2018, 5, 879–896 RSC.
- S. Patnaik, D. P. Sahoo, L. Mohapatra, S. Martha and K. Parida, Energy Technol., 2017, 5, 1687–1701 CrossRef CAS.
- Y. Yang, J. Wu, T. Xiao, Z. Tang, J. Shen, H. Li, Y. Zhou and Z. Zou, Appl. Catal., B, 2019, 255, 117771 CrossRef CAS.
- H. Jia, W. Zhu, Z. Xu, X. Nie, T. Liu, L. Gao and J. Zhao, Electrochim. Acta, 2018, 266, 7–16 CrossRef CAS.
- S. Tonda, S. Kumar, M. Bhardwaj, P. Yadav and S. Ogale, ACS Appl. Mater. Interfaces, 2018, 10, 2667–2678 CrossRef CAS.
- N. Krstulović, K. Salamon, O. Budimlija, J. Kovač, J. Dasović, P. Umek and I. Capan, Appl. Surf. Sci., 2018, 440, 916–925 CrossRef.
- N. K. Eswar, V. V. Katkar, P. C. Ramamurthy and G. Madras, Ind. Eng. Chem. Res., 2015, 54, 8031–8042 CrossRef CAS.
- X. Hu, R. Li, S. Zhao and Y. Xing, Appl. Surf. Sci., 2017, 396, 1393–1402 CrossRef CAS.
- G. Salehi, R. Abazari and A. R. Mahjoub, Inorg. Chem., 2018, 57, 8681–8691 CrossRef CAS.
- W. K. Jo and S. Tonda, J. Hazard. Mater., 2019, 368, 778–787 CrossRef CAS.
- X. Wang, L. Li, Z. H. Xie and G. Yu, Electrochim. Acta, 2018, 283, 1845–1857 CrossRef CAS.
- A. Deák, L. Janovák, E. Csapó, D. Ungor, L. Pálinkó, S. Puskás and L. Dékány, Appl. Surf. Sci., 2016, 389, 294–302 CrossRef.
- Z. Lia, Y. Wua and G. Lu, Appl. Catal., B, 2016, 188, 56–64 CrossRef.
- L. Yang, J. Liu, L. Yang, M. Zhang, H. Zhu, F. Wang and J. Yin, Renewable Energy, 2020, 145, 691–698 CrossRef CAS.
- Y. Zhao, P. Chen, B. Zhang, D. S. Su, S. Zhang, L. Tian, J. Lu, Z. Li, X. Cao, B. Wang, M. Wei, D. G. Evans and X. Duan, Chem.–Eur. J., 2012, 18, 11949–11958 CrossRef CAS.
- W. Chen, Y. Wang and W. Shangguan, Int. J. Hydrogen Energy, 2019, 44(8), 4123–4132 CrossRef CAS.
- Y. Zhang, L. Wang, S. H. Park, X. Kong, X. Lan, Z. Song and J. Shi, Chem. Eng. J., 2019, 375, 121967 CrossRef CAS.
- G. Liua, X. Zhaob, J. Zhanga, S. Liuc and J. Shaa, Dalton Trans., 2018, 47, 6225–6232 RSC.
- D. Zeng, W. J. Ong, Y. Chen, S. Y. Tee, C. S. Chua, D. L. Peng and M. Y. Han, Part. Part. Syst. Charact., 2018, 35, 1700251 CrossRef.
- J. L. Gunjakar, T. W. Kim, H. N. Kim, I. Y. Kim and S. Hwang, J. Am. Chem. Soc., 2011, 133, 14998–15007 CrossRef CAS.
- J. L. Gunjakar, I. Y. Kim, J. M. Lee, N. S. Lee and S. J. Hwang, Energy Environ. Sci., 2013, 6, 1008–1017 RSC.
- S. Nayak, L. Mohapatra and K. M. Parida, J. Mater. Chem. A, 2015, 3, 18622–18635 RSC.
- D. P. Sahoo, S. Patnaik, D. Rath and K. M. Parida, Inorg. Chem. Front., 2018, 5, 879–896 RSC.
- Y. Fu, F. Ning, S. Xu, H. An, M. Shao and M. Wei, J. Mater. Chem. A, 2016, 4, 3907–3913 RSC.
- D. Li, H. Wang, H. Tang, X. Yang and Q. Liu, ACS Sustainable Chem. Eng., 2019, 7, 8466–8474 CrossRef CAS.
- Y. Dou, S. Zhang, T. Pan, S. Xu, A. Zhou, M. Pu and X. Duan, Adv. Funct. Mater., 2015, 25, 2243–2249 CrossRef CAS.
- H. Y. Si, C. J. Mao, J. Y. Zhou, X. F. Rong, Q. X. Deng, S. L. Chen and J. Zhang, Carbon, 2018, 132, 598–605 CrossRef CAS.
- M. Radecka, M. Wierzbicka, S. Komornicki and M. Rekas, Phys. B, 2004, 348, 160–168 CrossRef CAS.
- Y. H. Ng, A. Iwase, A. Kudo and R. Amal, J. Phys. Chem. Lett., 2010, 1, 2607–2612 CrossRef CAS.
- J. Chen, C. Wang, Y. Zhang, Z. Guo, Y. Luo and C. J. Mao, Appl. Surf. Sci., 2020, 506, 144999 CrossRef CAS.
- R. Tao, S. Yang, C. Shao, X. Li, X. Li, S. Liu, J. Zhang and Y. Liu, ACS Appl. Nano Mater., 2019, 2, 3081–3090 CrossRef CAS.
Footnote |
† Electronic supplementary information (ESI) available. See DOI: 10.1039/d0na01074j |
|
This journal is © The Royal Society of Chemistry 2021 |
Click here to see how this site uses Cookies. View our privacy policy here.