DOI:
10.1039/D1MA00355K
(Review Article)
Mater. Adv., 2021,
2, 6125-6135
Pb in halide perovskites for photovoltaics: reasons for optimism
Received
17th April 2021
, Accepted 14th July 2021
First published on 14th July 2021
Abstract
Following the achievement of impressive power conversion efficiencies of perovskite solar cells (PSCs), the current challenges of this technology include long-term stability, upscaling for industrial processing, and its environmental effect. One of the significant concerns of the latter is accidental Pb leaching from PSCs and modules, due to the well-documented Pb toxicity. Such concerns may cause deceleration in PSC commercialization. However, this threat is found to be comparable to that posed by currently used Pb-containing products, and a plethora of measures are available to mitigate the environmental impact of Pb, as we present in this review. We show that the amount of Pb is estimated to be comparable to that in currently used electricity generation technologies, including fossil fuels, electronic solder wires, and lead–acid batteries. Analysis of accidental (worst-case) scenarios shows that the released quantities are within the orders-of-magnitude typical of currently used Pb-containing technologies. By comparison, PSC processing is found to have larger environmental impacts than Pb release, and the currently available Pb substituents, such as Sn, also have significant negative environmental impacts. Pb contamination can effectively be reduced and controlled using Pb adsorbing materials implemented into the encapsulation layers or integrated into the PSC. Recycling and reusing Pb-containing materials will also reduce the environmental impact, increase the material availability and decrease the devices’ energy payback time. We, therefore, suggest that Pb in PSCs and its effect on the environment are not as concerning as they seem to be.
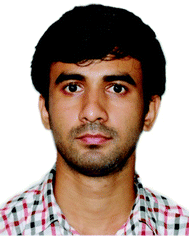
Arindam Mallick
| Dr Arindam Mallick is currently an Israel's Planning and Budgeting Committee postdoctoral fellow at the Swiss Institute for Dryland Environmental and Energy Research, Blaustein Institutes for Desert Research, Ben-Gurion University of the Negev. He received his PhD from the Indian Association for the Cultivation of Science, Kolkata, India in 2018 after completing his BSc and MSc degree in Physics in 2010 and 2012, respectively, from Jadavpur University, Kolkata, India. His research interests include perovskite solar cells, Pb leaching in soil, Pb transport mechanisms, chalcogenide nanoparticles and transparent conducting films. He has published 10 peer-reviewed papers. |
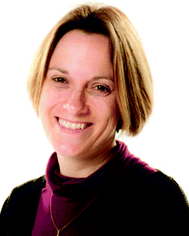
Iris Visoly-Fisher
| Prof. Iris Visoly-Fisher received her BSc and MSc in materials engineering and BA in physics from the Technion – Israel Institute of Technology. She completed her PhD in materials and interfaces at the Weizmann Institute of Science in 2004, studying single grain boundaries in polycrystalline CdTe solar cells. She then moved to Arizona State University as a Fulbright and Rothschild postdoctoral fellow, where she worked on electrochemical potential-dependent current transport in single biomolecules. In 2008 she joined Ben-Gurion University of the Negev as faculty. Her research interests include materials for solar energy conversion and storage, optoelectronics and surface science. |
Introduction
Since their introduction as the absorbing material in solar cells,1 organic–inorganic lead (Pb) halide perovskites have reshaped the prospect of photovoltaic (PV) technologies as a source of green energy. Within a decade, they have attracted tremendous global attention with single-junction solar cell power conversion efficiency (PCE) reaching up to 25.5%.2,3 These materials also show great promise in several other applications such as light-emitting diodes, lasers, batteries, and photodetectors, due to their unique properties, including ambipolarity, high charge-carrier mobility, high carrier diffusion length, high absorption coefficient, and an easy and cheap preparation method at moderate temperatures.4 Pb is an essential part of commonly used halide perovskite compositions, but it is considered a hazardous chemical with major health concerns affirmed by the World Health Organization (WHO).5,6 The prospective effects on the environment associated with the large-scale implementation of this technology are therefore of high interest.7–10 While the toxicity of Pb is of significant concern, several aspects have demonstrated that Pb quantities in perovskite solar cells (PSCs) are comparable to those in currently used technologies, and can safely be handled within acceptable limits, to utilize its benefits. Indeed, severe measures should be taken for safe handling and disposal of Pb-containing perovskites, however, it may not be necessary to eliminate them entirely from PSCs and other halide perovskite-based devices. The present review focuses on such reasons for optimism, showing why and how Pb-containing halide perovskites can be used in a sustainable manner.
The first presence of Pb in human history is tentatively dated back to 6500 B.C.11 Since its discovery, Pb has become an indispensable metal for our civilization due to properties such as high density, low melting point, malleability, ductility, high resistance to corrosion, etc.7 Current applications of Pb are schematically described in Fig. 1 and indicate mostly its utilization in Pb–acid batteries.12 Pb is a cumulative toxicant that affects multiple body systems, distributed to the brain, kidney, liver, and stored in bones and teeth; carcinogenic and neurological effects were also noted.10 It is particularly harmful to young children and during pregnancy, as Pb stored in bone is released into the blood and becomes a source of exposure to the developing fetus. The presence of heavy metals, especially Pb, creates reactive radicals, which damage cell components, including DNA and membranes.13–15 Organic-bound Pb is considered to be the most toxic because of its lipid-soluble nature.16 Indeed, several works have demonstrated the high bioavailability and toxicity of Pb released from halide perovskites.10,17–20
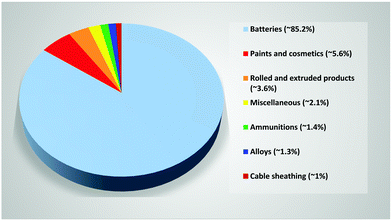 |
| Fig. 1 Usage of Pb in different worldwide applications until 2012; data from ref. 12. | |
Most importantly, there is no minimum level of Pb exposure that is known to have no harmful effects.21 The maximum permissible levels of Pb in drinking water and air has been set to 10 μg L−1 and 0.5 μg m−3, respectively, by the Joint Food and Agriculture Organization of the United Nations (FAO)/WHO Expert Committee on Food Additives (JECFA).22 In 2003, a maximum Pb level of 50 μg per liter of blood has been imposed by the WHO.23 In the next sections, we review Pb quantities in PSCs compared to those found in currently used technologies and indicate its compatibility with the relevant legislation. We then compare the environmental impact of Pb in PSCs to that of its alternatives, which surprisingly do not show clear advantages in that sense. We conclude by reviewing a plethora of measures suggested to mitigate the environmental effects of Pb release from PSCs.
Pb in PSCs and its effect on the environment
The crystalline structure of Pb-based perovskites can be described by the chemical formula ABX3, where the A-site comprises large organic cations like CH3NH3+ (MA), [(NH2)2CH]+ (FA), or inorganic Cs+; B is either lead (Pb2+) or Sn2+ or other divalent metal cations; and X is a halide anion such as I−, Br−, or Cl−. Pb and organic A cations are currently used in PSCs of the highest efficiency.24 Decomposition of Pb-based PSCs occurs in the presence of moisture, UV light, oxygen, temperature, or a combination of these factors. The decomposition results in the production of PbI2 or PbBr2, a small amount of metallic Pb and carbonated moieties that ultimately convert to hydroiodic acid (HI) and methylamine or formamidinium.25 PbI2 and PbBr2 are moderately soluble in water with a solubility product in the order of 10−8, much higher than other heavy metal compounds (e.g. CdTe <10−34).26,27
What are the relevant PSC-related Pb quantities? The typical Pb content in a 300 nm thick methylammonium lead iodide (MAPI) film is estimated to be ∼0.4 g m−2.28 Hailegnaw et al.28 showed that a planar 400 nm thick (non-encapsulated) MAPI layer with an area of 3.6 cm2 would release ∼0.5 mg of Pb when washed with 1 hour of simulated rain (5 mL h−1). In a detailed study, Babayigit et al.7 discussed the fire issue associated with PSCs and, considering 0.4 g Pb per m2 of the module and 50 m2 PSCs installation per house, they estimated ∼15 tons of Pb can be released in one year due to structure fires worldwide, assuming that every home is equipped with a PSC-based photovoltaic installation. For comparison, they calculated the release of 17.8 tons of Pb from batteries in vehicle fires in the USA alone in 2015 considering only 10% of the car batteries involved in car fires.7 Pb quantities per area in PSCs based on thick meso-porous electrodes infiltrated with the perovskite29–32 are naturally larger and more difficult to estimate, requiring further studies.
MAPI-based PSCs with an efficiency of 25% would require ∼160 tons of Pb to provide the USA's yearly electricity demand, reflecting an energy intensity of 38 μg kW−1 h−1.8,33 For comparison, Pb emissions in 2011 from leaded aviation fuel, processing of metals, and electricity generation from fossil fuels in the USA were reported to be 440, 120, and 35 t per year, respectively.34 The Pb content of electronic solder produced in the USA (including commercial PV panels) was reported to be 6200 t per year in 2012.33,35 These numbers indicate that the Pb content of the new perovskite-based PV technology is comparable to that in currently used other technologies that consume or release Pb and can therefore be similarly treated and tolerated.
Life cycle assessment (LCA) is a study of the environmental impact of a given product at different stages of its life. Fig. 2 shows the suggested stages of the life cycle of perovskite solar cells. The initial stages (raw material extraction and material processing) are not unique to PSCs, therefore will not be discussed herein. The manufacturing stage involves heavy metal toxicity from the precursor salts, especially as Pb salts are soluble in fat and organo-Pb compounds demonstrated increased bioavailability compared to inorganic Pb compounds. Proper safety protocols for the workplace and use of personal protective equipment should therefore be used to restrict Pb hazards.10 According to the LCA of the PSC manufacture stage (cradle to gate) by Zhang et al.36 the perovskite absorber is indeed the primary source of environmental impact, associated with 64.77% of the energy consumption and 31.38% of materials consumption. However, Pb only contributes to about 1.14% of the human toxicity potential of the PSC manufacture. Similar conclusions were also drawn by other studies37–40 for different perovskite deposition procedures, where water-soluble Pb(II) halides had relatively little impact. Zhang et al.36 found that the most significant environmental impact in the manufacturing process comes from the solvents used in perovskite synthesis and TiO2 layer deposition, as well as from the energy consuming processes. Gong et al.41 also concluded that most of the environmental impact was related to gold, TCO layer, organic solvents, and the energy-consuming thermal evaporation. Celik et al.37 found that the inorganic HTL layer induced significant environmental impacts, and significant eutrophication can be caused by organic perovskite precursors. Compared with commercial Si and CdTe solar cells, perovskite solar cell manufacturing consumes less energy, shows lower energy payback time, and produces comparable greenhouse gas emissions.36,37,41
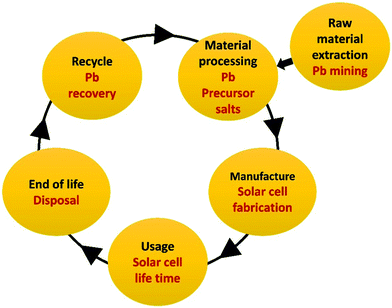 |
| Fig. 2 Schematic presentation of the suggested stages of the life cycle of perovskite solar cells (based on the analysis in ref. 10 and 40). | |
The environmental impacts per unit of electricity generated (the usage stage) depend on the PSC's lifetime and can be low in stable PSCs.37 Billen et al.42 found that the Pb intensity in PSC life cycles can be 4 times lower, and potentially toxic emissions can be 20 times lower, than those in representative USA electricity generation mixes, considering that PSC operational lifetimes are around 20 years. They determined that the toxicity potential is dominated by the manufacturing energy rather than by the use of the PV system, therefore low-energy manufacturing processes and long PSC lifetime would reduce Pb emission by 2 to 4 times with respect to currently used PV technologies.42 Krebs-Moberg et al.43 performed cradle-to-grave LCA comparison of multi-crystalline Si, organic thin-film (OPV), and PSC panels which revealed that the production and use of Si panels resulted in the worst impacts, OPV panels produced significantly lower impacts, and impacts from PSCs fell at mid-range. As Si panels are the most widespread, replacing them with PSCs of comparable PCE (and similar long-term stability,40 yet to be achieved) would indicate improvement in PV environmental impacts. PSC usage and end-of-life disposal can cause local intoxication upon cell damage and in landfill. These stages, as well as mitigation of the Pb release in these stages and the effect of the recycle stage, are discussed in detail in the following sections.
Environmental effects of Pb alternatives in PSCs
Pb toxicity triggered attempts at Pb substitution in perovskite PV, by partial or full replacement of Pb using Sn,44–48 Ge,49–52 Sb,53–55 Bi,56–58 Cu,59,60 and others.61–65 Among all alternatives, Sn-based perovskites receive the most attention with materials such as methylammonium tin iodide (MASnI3), formamidinium tin iodide (FASnI3), and cesium tin iodide (CsSnI3).66,67 However, PCEs of Sn-based PSCs are typically lower than that of Pb-based ones (Fig. 3), and once these materials are exposed to ambient, they degrade much faster mostly due to oxidation from Sn2+ to Sn4+ which causes loss in VOC.68 It has also been reported that Sn-based perovskites crystallize faster than the Pb-based ones and hence grain size is smaller and recombination losses are larger.69,70 Several attempts were made to suppress such limitations.71 Chen et al.72 demonstrated the use of CsSn0.5Ge0.5I3 perovskite as the light absorber in PSCs with 7.11% PCE and less than 10% reduction in efficiency after 500 h of continuous operation in a N2 atmosphere. Improved stability, optoelectronic properties, and PSC performance were achieved through the incorporation of a bulky divalent organic cation, 4-(aminomethyl)-piperidinium (4AMP), in FASnI3.73
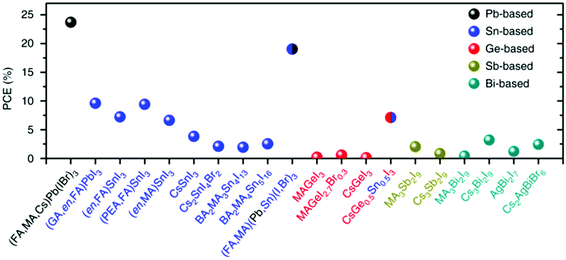 |
| Fig. 3 Highest efficiencies reported for PSCs using different ‘B’ cation-based absorbers such as Pb, Sn, Ge, Sb, and Bi. Reproduced without modifications from Ke et al.65 under a Creative Commons Attribution 4.0 International License http://creativecommons.org/licenses/by/4.0/. | |
Double perovskites with the general formula of either A2B(I)B(III)X6 or A2B(IV)X6 were also suggested. Cs2SnX6 (X = I, Br) was found to be the most stable of the Sn-based perovskites. Despite its narrow direct bandgap of 1.3 to 1.6 eV, unfavorable carrier transport properties limit its efficiency in PV devices.74 A stable cell with a PCE of 1.44% was made of Cs2AgBiBr6.75 Over 28 million AA′BB′X3X′3 double-perovskite-like compositions were screened by Kanno et al.,76 considering their semiconducting properties, the feasibility of their synthesis, toxicity, and cost, where 24 very promising candidates were found, among which 5 were well-known organic–inorganic tin-halide perovskites. The use of trivalent (3+) substitution was also suggested for Pb alternatives where the structure will change from ABX3 to A3B2X9 and will take the form of 0-D or 2-D structures,63,77,78 although less favorable for PV devices due to their strongly bound excitons and low carrier mobility. For example, PSCs based on non-toxic methyl-acetate solution-processed (CH3NH3)3Bi2I9 films with a band-gap of 2.1 eV were fabricated by Jain et al.79 with a low PCE of <2%.
In their perspective, Schileo et al.80 mentioned that Sn-based perovskites or other Pb-free perovskites not only fail to provide substantial advantages in terms of cost, toxicity or environmental safety, but also possess intrinsic limitations that hinder better stability and efficiency compared to Pb-based PSCs. A comparative analysis of the impact on the environment due to the use of Sn- and Pb-based PSCs was done by Serreno-Lujan et al.38 where operational and disposal phases were identified as key device life stages. Sn is found to be more hazardous than Pb complexes in an acidic environment. Sn-based PSCs were found to have a larger impact than Pb-based ones, due to the greater impact of Sn on terrestrial ecotoxicity (rather than human toxicity) and global warming, mainly caused by its low efficiency.38 Babayigit et al.17 compared the environmental impact of PbI2 and SnI2, which are the main degradation products of PSCs. Using zebrafish (Danio rerio) modeling, they showed that for similar concentrations of both compounds, a higher lethal response was found in embryos exposed to SnI2 than for PbI2. It is important to note that the lethality rates and morphological defects in embryos induced by SnI2 are not just due to the presence of Sn, but also due to reduced pH value than the PbI2 case. PSC-released Sn uptake in mint plants was reported to be lower than Pb uptake, yet it similarly inhibited seed germination and early seedling.18 A thorough review of human toxicity effects of Sn from PSCs indicated that Sn poisoning from inorganic compounds causes short-term effects such as ataxia, muscle weakness and irritation of gastrointestinal mucosa, and chronic exposure causes effects similar to Pb exposure, though such effects are less well documented and some are still debated.10 Altogether, currently, Sn does not present clear advantages in terms of environmental effects over the use of Pb in PSCs.
Legislation for restricting Pb usage in PV
Hazardous trash related to electrical and electronic equipment accumulates on landfills, especially in developed countries, which makes the enforcement of various legislations, aimed at limiting the environmental impact of hazardous materials, particularly important.81–83 More than 12 million tons of e-waste has been estimated just in the European Union (EU) by 2020.84 According to Zeng et al.,83 China is the world's leading producer of e-waste and will generate 15.5 and 28.4 million tons of electronic equipment waste between 2020 and 2030, respectively. The global move towards sustainable and renewable energy resources results in a large number of solar modules being installed, which may produce a significant amount of waste at the end of the solar module life cycle.85
To address these global issues, the Restriction of Hazardous Substances (RoHS)-(2002/95/EC) directive was adopted by the EU in 2003, which applies the use of 6 hazardous materials in electrical and electronic equipment, among which Pb and Cd are frequently used in PV systems.86 RoHS 3, which came into effect on July 22, 2019, extended the restrictions to 10 substances.87 A related directive is the EU's Waste from Electrical and Electronic Equipment (WEEE) directive,84 aimed at the collection, recovery, and recycling of electric and electronic equipment, to improve environmental management and recover scarce and costly resources. As of today, all consumable products marketed or manufactured in the EU must pass WEEE compliance and carry the “Wheelie Bin” sticker.84 Manufacturers outside of the EU who wish to import their products to the EU must also comply with the RoHS directive. The Chinese government has its legislation entitled Administrative Measures on the Control of Pollution Caused by Electronic Information Products.88 Pb is identified as one of 6 hazardous substances and its content level in listed products is limited. In the US, the Californian Electronic Waste Recycling Act restricts the content of heavy metals identified in the RoHS and establishes a funding system for the collection and recycling of a limited number of products.89 Many other states in the USA have either effective or pending regulations inspired by the EU RoHS directive. Extensive reviews of Pb-related legislation were presented by Babyigit et al.7 and Kadro et al.85
According to the RoHS directives, “A maximum concentration value of 0.1% by weight in homogeneous materials for Pb (<1000 ppm)… shall be tolerated”.7,86 ‘Homogeneous’ material means a unit that cannot be mechanically dismantled into separate materials, i.e., separated by mechanical actions such as unscrewing, cutting, crushing, grinding, and abrasive processes. In the case of planar PSCs, if the absorber layer is considered uniform and homogeneous, MAPI would contain ∼33 wt% of Pb, which clearly violates the present RoHS limit. However, the ‘homogeneous’ definition becomes somewhat ambiguous with respect to the absorber layer for the commonly used mesoscopic device structure, and an estimated 0.4–0.5 wt% Pb content was calculated for MAPI embedded in mesostructured TiO2 with infiltrated Spiro-MeOTAD,90,91 which still exceeds the permitted limit but is within the same order of magnitude.
Referring specifically to PV panels, permanently installed photovoltaic panels were excluded from the EU's RoHS directive in its RoHS 2 update,92,93 hence large-scale commercialization of Pb-containing PSCs is still possible, as is the case for CdTe PV systems. Naturally, this exclusion would be void if Pb substitutions can be found to provide comparable performance, but until then, the RoHS permits the use of Pb-containing PSCs.86 Similarly, the USA legislation related to hazardous materials in electronic waste does not refer to PV modules.89 In Japan, no restrictions on Pb usage in electronic products are imposed, other than recycling requirements.94 It is further noted that the RoHS and related regulation refer only to Pb in electronic products, which constitutes about 10% of the global Pb consumption, while most of this consumption is attributed to lead–acid batteries, in which Pb usage is not restricted (other than its recycling requirements).95
Mitigating environmental effects of Pb release
PSC exposure to water (in rain, hail, dew, or humidity) or fire will cause its release into the environment. Several studies quantified the release of Pb in the case of PSC failure. Hailegnaw et al.28 simulated the effect of rainfall and found that with time, most or all of the PSC's Pb content can be solubilized. However, the authors predicted an increase by ∼70 ppm in the Pb concentration in the first one cm of soil under the damaged device, assuming an average soil density of 1.5 g mL−1, comparable to the 50–200 ppm of Pb found naturally in the soil in urban areas.96 Standard leaching tests showed concentrations of 3–6 mg L−1 in water, only slightly higher than the hazardous waste limit of 5 mg L−1 set by USA's and China's regulations.20 They also confirmed the slow solubility of Pb by repeated leaching cycles, which may set a time window following the PSC damage that allows limiting the released Pb content. Leached quantities of the same order of magnitude (up to 28.3 mg L−1) were recorded by Jiang et al.97 for unencapsulated modules subjected to simulated hail damages and subsequent water dripping test. Babayigit et al.7 calculated a maximum release of 20 g of Pb from a single domestic PSC-based PV system involved in a structure fire, excluding Pb in soldering material. Further detailed analysis by the same group showed that domestic fires damaging a Si/PSC tandem-based PV system should not cause an immediate health hazard in terms of Pb release quantities to the air, but only treatable long-term effects.98 Analysis of perovskite-originated airborne deposits showed that at locations immediately adjacent to the heated zone a discernible Pb signal was detected, which vanished with increasing distance. “Worst case” atmospheric dispersion modeling, assuming full evaporation of the perovskite, was used to determine the danger from inhaled Pb-containing species. It showed a maximum concentration of 41 μg m−3 of PbO2 in the air downwind of a burning residential installation, within the European Commission's safe limit of 50 μg m−3 for a one-day exposure, or 15 mg m−3 within 30 min suggested by the National Institute for Occupational Safety and Health. The authors therefore concluded that the “health hazard from exposure of perovskite PV fumes from a burning residential installation… would not be alarming”.98 Such accidental (worst-case) release estimates are therefore within the orders-of-magnitude typical of currently used Pb-containing technologies. It should be noted that other airborne toxins (such as CO) may also be released by fire.
While eliminating Pb from PSCs is currently impractical, reducing the Pb content in PSCs will reduce its content in the related waste. Zhu et al.99 theoretically demonstrated that through introduction of an optical spacer layer, the device efficiency can be retained by up to 96% of its original value while reducing the perovskite film thickness to one-third of its previous value. Using this method, the Pb content can be reduced by 70% in PSCs or modules. Partial replacement of Pb by other metal cations was also proposed for the same purpose, with improved PCE compared to complete Pb replacement.44 However, it is not clear whether partial Pb substitution by Sn is beneficial for the PSC's environmental impact or not (see above). Another aspect of reducing the Pb waste from PSCs stems from material loss during perovskite deposition; in that sense, deposition techniques limiting material loss should be preferred (e.g. slot die coating is preferred over spin coating).85
In cases where accidental Pb release has already occurred, remedies are readily available, as extensively reviewed by Dedecker et al.9 These include physical and biological techniques to reduce or eliminate Pb contamination of soil, by soil replacement, isolation, thermal treatment, and the use of Pb-capturing bio-organisms. Various physical and chemical techniques can be used for the water purification of Pb. Chelation therapy is used in cases of human Pb poisoning, with partial success.100 Such concepts were demonstrated to efficiently treat water contaminated by Pb released from damaged PSCs using metal–organic framework (MOF)–polymer composites.101 While the availability of these possible remediation paths is reassuring, the best strategy is to prevent or reduce accidental Pb release. Some methodologies for such prevention in PSCs are described in the following sections.
Encapsulation to prevent Pb release
Poor stability due to environmental factors like moisture and oxygen can be addressed by encapsulation, which would enhance device lifetime102–105 as well as prevent or restrict accidental Pb release into the environment in the case of device breakage.8,9,97 The optimal encapsulation material should possess low water absorptivity, high light transmission, good adhesion, high mechanical strength as well as resistance to ultraviolet (UV) degradation and thermal oxidation.106 Additionally, it should be low cost and its processing needs to be effortless and compatible with the PSC requirements, such as low temperature.107 An in-depth review of the existing PSC encapsulation techniques was published by Corsini et al.108 where details of the currently available encapsulation materials and their role in blocking external influences such as UV light, moisture, and oxygen were discussed. Herein we focus on encapsulation properties relevant to preventing Pb release.
Devices fabricated on rigid substrates such as glass can be sealed with a full glass encapsulation method or glass/adhesive/glass or glass/adhesive/metal plate,109 in which the device is sandwiched between two plates whose edges are sealed. Another frequently used technique is the lamination technique, where the device is kept in between two barrier materials and sealed using an adhesive film adhering to the top glass plate. For example, a five-layer laminated structure: glass front side/EVA (ethylene vinyl acetate)/photovoltaic module/second EVA sealing film/back face protection, has been used to encapsulate Si solar modules.110
Quantitative measurements of Pb leakage due to damage of encapsulated modules by simulated hail impact followed by water dripping and other simulated weather conditions were performed by Jiang et al.97 They found that the leakage rate was significantly dependent on the encapsulation method. 375 times less Pb leakage was reported in glass/adhesive/glass encapsulated modules compared to unencapsulated ones, when the epoxy resin-based polymer adhesive was sandwiched between the FTO/glass substrate and a glass cover, with the addition of another glass plate covering the Au electrode and edge sealing using UV-cured resin. The highest released Pb content measured in water dripped on these damaged modules was 1.8 mg L−1, below the required threshold (see above). They concluded that the key factor in limiting Pb leakage was the ability of the epoxy resin-based polymer to self-repair when heated to temperatures above its Tg, for example, by the sun on a sunny day, combined with its increased mechanical strength.
Conings et al.111 exposed Si/PSC tandem modules, encapsulated by glass/polymer laminate on either side, to simulated fire damage that produced temperatures up to 760 °C and studied the Pb remains on the samples. The glass-covered regions in the damaged samples were found to be void of Pb traces, while the exposed cell areas still indicated significant amounts of Pb. Pb remains were also found on damaged non-encapsulated cells. The authors deduced that during a fire the organic moiety leaves the perovskite first, thereby forming PbI2, which either evaporates or is oxidized into PbO and PbO2, which are less volatile. Significant Pb quantities were found within the encapsulating glass in covered parts of the damaged sample, indicating that nearly all Pb from the perovskite layer dissolved into the glass cover on top of it. The authors concluded that high melting-temperature glass would be resistant to fire damage, improving the Pb leakage protection. Both works demonstrate that Pb leakage from damaged PSCs can be minimized by proper encapsulation.
Pb sequestration by PSC-integrated components
Several attempts were made to integrate Pb-trapping materials into PSCs, as active PSC layers or as added protection layers on the outer electrode surfaces.112 Wu and his co-workers103 used a 2-D conjugated MOF (ZrL3) with n-type electrical behavior at the electron extraction layer (bis-C60)/cathode interface in the PSC. A dense array of thiol groups in the ZrL3-MOF possess the capability of trapping heavy metal ions (Pb2+ in this case), in addition to stabilizing the MOF structure. The resulting PSC showed high PCE, due to improved electron extraction and hole blocking, and good operational stability under N2, probably due to prevention of the interaction between the perovskite and the cathode metal (Ag) by the MOF layer. In the degraded PSCs, Pb2+ ion leakage was shown to be prevented by the MOF layer by SIMS depth profiling. Submerging the degraded PSCs in deionized water with a pH value of ∼5.6 (simulating acidic rain) has shown that the Pb2+ concentration decreased over 80% for MOF-containing PSCs compared to control devices. This indicates that Pb2+ ions from the degraded perovskite can be confined in the thiol-functionalized MOF layer and form water-insoluble complexes. Chen et al.113 utilized a cation exchange polymeric resin that can strongly and selectively adsorb Pb2+via sulfonate groups from aqueous solution, and is water-insoluble, to prevent or reduce Pb leakage from damaged PSCs. Integrating the cation exchange resin into carbon electrodes on top of C60/SnO2 electron extraction layers or directly on the perovskite in hole conductor free PSCs, by mixing with the carbon paste, hardly affected the PCE, while the Pb leakage from broken mini-modules to flowing or soaked water was reduced by up to 98%. The same group have reported a Pb-adsorbing sulfonic acid-based resin incorporated as an insulating mesoporous scaffold into the perovskite layer, that can effectively immobilize Pb ions while not decreasing the PCE.114 Lee et al.115 fabricated high PCE PSCs with a novel hole transporting layer made of a donor–acceptor polymer containing benzo[1,2-b:4,5:b′]dithiophene and tetraethylene glycol (TEG)-substituted 2,1,3-benzothiadiazole capable of chelating Pb2+ ions. The interaction with Pb2+ was demonstrated in solution, and significant Pb content was found in the hole transporting layer in aged devices using SIMS depth profiling, however, no leakage tests were performed. Recently, Mokhtar et al.116 used hydroxyapatite nanoparticles as a Pb-sequestering agent blended into the mesoporous TiO2 layer in high PCE PSCs, which substantially decreased Pb release into water from the PSC (Fig. 4).
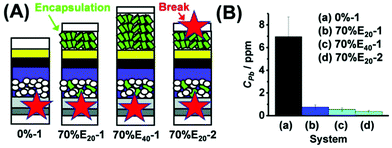 |
| Fig. 4 (A) Device architectures (glass/FTO/bl-TiO2/perovskite/Spiro/Au) used for failure tests. Green indicates the hydroxyapatite nanoparticle's location, and red stars show the breakage points. (B) Pb release from damaged devices of different architectures after 24 h immersion in water. Reproduced from ref. 116 with permission from the Royal Society of Chemistry. | |
Outer-cell protection layers were also used by Chen et al.,113 who coated the cation exchange resin on the metal electrode and the outer face of the glass substrate. The resin was found to reduce Pb leakage from damaged PSCs soaked in water (neutral or acidic) or by water dripping by ∼one order of magnitude in terms of the concentration in water. Li et al.117 used a transparent micron-thick molecular layer on the outer glass surface, which contains phosphonic acid groups known to bind to Pb2+, and is insoluble but highly permeable to water. They also utilized an opaque polymer film blended with chelating agents such as EDTMP (ethylene diamine tetrakis methylene phosphonic acid) on the metal electrode without any negative impact on the PSC performance. Damaged EVA-coated PSCs were soaked in water for Pb leakage tests. Compared to PSCs without the sequestration layers, Pb leakage to water was reduced by over 97%, and significant Pb content was found in both sequestration layers.117 The use of other PSC additives to form stable and insoluble compounds such as phosphates, hydroxides, and sulfates, or adsorbents combined with chelating agents such as EDTA (ethylene diamine tetracetic acid), was also suggested9,28 but are yet to be tested. These studies suggest that although PSCs present similar Pb leakage hazards as frequently used in other technologies, strategies are already available to significantly reduce such leakage without adversely affecting PSC performance.
PSC recycling
Most PV technologies use valuable and hazardous materials, some of which have potential for recycling and reuse, which can reduce their environmental impact, increase their availability and decrease the device's energy payback time.85 Similar to recycling protocols of other PV technologies,118–120 once the operational lifetime is over, PSCs recycling procedure should be robust and aimed to reduce exposure of the hazardous substances to the environment and humans. It typically comprises of mechanical separation of encapsulation materials from the PV device, followed by chemical extraction of the scarce and/or polluting device components. Several methodologies for recycling and re-use of PSCs were examined at the lab scale, although not tested on a commercial scale.121,122 Kadro et al.123 and Binek et al.124 have demonstrated methodologies for selective dismantling processes that can recuperate each key component of the PSCs separately for potential future use (Fig. 5). Several works showed that expensive transparent conductive electrode substrates (typically FTO or ITO, with or without a charge selective metal oxide layer, such as the electron transporting TiO2) can be used several times for efficient device preparation after stripping of the device layers at the end of its life.123–128 It is noted that the heavy use of solvents for such processes will also have a significant environmental impact. Retrieving and re-using Pb from PSCs can significantly reduce Pb waste. Recycling of the active perovskite layer starts by selective stripping of the layers covering it. Binek et al.124 showed that, following such stripping, short immersion of the half-device with an MAPI absorber layer in distilled water resulted in almost fully dissolved MAI and a small amount of dissolved Pb (4 mg L−1), while most of the PbI2 was left on the substrate and could be subsequently dissolved (in dimethylformamide, DMF) and re-used for perovskite deposition (Fig. 5). It is noted that Pb retrieval from water can be done in several ways,9 though not applied therein. In situ recycling of PbI2 from PSCs has been reported by Xu et al.129 by thermal decomposition of MAPI that resulted in evaporation of MAI leaving a PbI2 layer on the substrate/electrode, that can be re-converted to perovskite in a “two-step” deposition method.
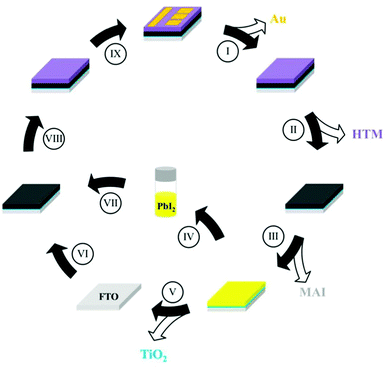 |
| Fig. 5 Schematic illustration of the recycling procedure for PSCs, as suggested by Binek et al.124 (I) Removal of Au electrode with adhesive tape. (II) Removal of the hole transfer material (HTM) by immersing in chlorobenzene. (III) Transformation of MAPI into MAI and PbI2 and extraction of MAI in water. (IV and V) Removal of PbI2 and TiO2 using DMF. (VI) Preparation of a new TiO2 film. (VII) Formation of the perovskite film on recycled FTO from recycled PbI2. (VIII) Preparation of the HTM layer. (IX) Evaporation of the Au top electrode. Reprinted with permission from ref. 124. Copyright (2016) American Chemical Society. | |
The advantage of this method is its compatibility with mesoporous substrates. However, while almost similar device efficiency has been observed after the first cycle, ∼40% reduction in device performance occurred in devices recycled a second time. A similar approach of regenerating MAPI from PbI2 films was applied to MAPI films naturally degraded in ambient.130 The authors noted that enhanced crystallization of the degraded PbI2 films hampered their consecutive conversion back to MAPI. Feng et al.131 recycled the entire MAPI layer by its dissolution in butylamine together with other organic materials in the PSC, followed by butylamine evaporation and selective dissolution of the organic materials from the remaining powder. The recovered MAPI was then used again for PSC fabrication with equivalent performance to that of fresh devices.
Poll et al.132 dissolved the active perovskite layer in an ionic solvent that was subsequently used for electrochemical deposition of metallic Pb from the dissolved material, which can be re-used in various products. At the end-of-life cycle of the PSCs, incineration and recovery of Pb have been suggested to be beneficial as compared to the landfill treatment in terms of environmental impact.38 Though metal recovery from ashes following PV panel incineration is widely accepted by acid leaching and electrolysis,133 we could not find evidence that this is done for Pb recycling. Pb recycling at any stage of the PSC life cycle is certain to reduce its content in waste and its environmental impact.
Summary
Utilizing Pb in PSCs is considered one of the major obstacles to the commercialization of this promising PV technology, due to its negative environmental and health impacts. However, our review demonstrates that this threat is comparable to that posed by currently used Pb-containing products, that the related legislation is supportive of developing PV technologies regardless of their Pb usage, and that a plethora of measures is available to mitigate the environmental impact of Pb. Specifically, we show that the Pb content in PSCs is comparable to that in currently used electricity generation technologies. LCAs show that the impact of Pb in PSCs is significantly lower than that of the energy used in PSC manufacture and that utilization of less wasteful fabrication methods will reduce the Pb consumption of this technology. LCA comparison shows that replacing the currently used Si PV panels by PSCs of similar performance would yield an improvement in their environmental impacts. Examining the environmental impacts of replacing Pb in PV perovskites with other metal cations results in significant PCE losses unless Sn is used, however, Sn demonstrates severely negative impacts by itself.
Analysis of accidental (worst-case) release scenarios shows that the released quantities are within the orders-of-magnitude typical of currently used Pb-containing technologies. As the dissolution of Pb salts in water was found to be relatively slow, frequent inspection and fast response to failure can limit Pb release. Furthermore, methodologies are available to readily mitigate such release. These include the use of optics to reduce the perovskite content in PSCs without reducing its light absorption; soil, water, and human remedies in the case of Pb release; PSC encapsulation to prevent Pb release; Pb trapping by PSC-integrated components, preventing its release in the case of device failure; and recycling of the PSC active/absorber layer to reduce Pb release as waste. Altogether, we suggest that the Pb-associated barrier to PSC commercialization is significantly smaller than currently considered.
Conflicts of interest
The authors have no conflicts of interest to declare.
Acknowledgements
This work was supported by the ISRAEL SCIENCE FOUNDATION (grant no. 1728/18). A. M. gratefully acknowledges the Israeli Planning and Budgeting Committee Fellowship for Outstanding Post-doctoral Researchers from China and India.
References
- A. Kojima, K. Teshima, Y. Shirai and T. Miyasaka, J. Am. Chem. Soc., 2009, 131, 6050–6051 CrossRef CAS PubMed.
- National Renewable Energy Lab: Best Research-Cell Efficiency Chart, https://www.nrel.gov/pv/cell-efficiency.html Search PubMed.
- J. Jeong, M. Kim, J. Seo, H. Lu, P. Ahlawat, A. Mishra, Y. Yang, M. A. Hope, F. T. Eickemeyer, M. Kim, Y. J. Yoon, I. W. Choi, B. P. Darwich, S. J. Choi, Y. Jo, J. H. Lee, B. Walker, S. M. Zakeeruddin, L. Emsley, U. Rothlisberger, A. Hagfeldt, D. S. Kim, M. Grätzel and J. Y. Kim, Nature, 2021, 592, 381–385 CrossRef CAS PubMed.
- S. D. Stranks and H. J. Snaith, Nat. Nanotechnol., 2015, 10, 391–402 CrossRef CAS PubMed.
- World Health Orgnization: Exposure to lead: A major public health concern, https://apps.who.int/iris/bitstream/handle/10665/329953/WHO-CED-PHE-EPE-19.4.7-eng.pdf?ua=1.
- World Health Organization: Lead poisoning and health, https://www.who.int/news-room/fact-sheets/detail/lead-poisoning-and-health#:~:text=Lead%20is%20a%20cumulative%20toxicant,where%20it%20accumulates%20over%20time.
- A. Babayigit, H. G. Boyen and B. Conings, MRS Energy Sustain., 2018, 5, 1–15 CrossRef.
- V. K. Ravi, B. Mondal, V. V. Nawale and A. Nag, ACS Omega, 2020, 5, 29631–29641 CrossRef CAS PubMed.
- K. Dedecker and G. Grancini, Adv. Energy Mater., 2020, 10, 2001471 CrossRef CAS.
- A. Babayigit, A. Ethirajan, M. Muller and B. Conings, Nat. Mater., 2016, 15, 247–251 CrossRef CAS PubMed.
- N. H. Gale and Z. Stosgale, Sci. Am., 1981, 244, 176–193 CrossRef CAS.
- UNEP's activities on lead and cadmium, https://www.unep.org/es/node/1192.
-
M. J. Kosnett, in Poisoning & Drug Overdose, ed. K. R. Olson, McGraw-Hill, New York, 2012 Search PubMed.
- D. Beyersmann and A. Hartwig, Arch. Toxicol., 2008, 82, 493–512 CrossRef CAS PubMed.
-
K. Olson, I. B. Anderson, N. L. Benowitz and P. D. Blanc, Poisoning & Drug Overdose, McGraw-Hill, 5th edn, 2006 Search PubMed.
-
J. A. Timbrell, Principles of Biochemical Toxicology, Taylor & Francis, 4th edn, 2008 Search PubMed.
- A. Babayigit, D. D. Thanh, A. Ethirajan, J. Manca, M. Muller, H. G. Boyen and B. Conings, Sci. Rep., 2016, 6, 18721 CrossRef CAS PubMed.
- J. M. Li, H. L. Cao, W. B. Jiao, Q. Wang, M. D. Wei, I. Cantone, J. Lu and A. Abate, Nat. Commun., 2020, 11, 310 CrossRef CAS PubMed.
- S.-Y. Bae, S. Y. Lee, J.-W. Kim, H. N. Umh, J. Jeong, S. Bae, J. Yi, Y. Kim and J. Choi, Sci. Rep., 2019, 9, 4242 CrossRef.
- P. D. Su, Y. Liu, J. K. Zhang, C. Chen, B. Yang, C. H. Zhang and X. Zhao, J. Phys. Chem. Lett., 2020, 11, 2812–2817 CrossRef CAS PubMed.
- H. L. Needleman, A. Schell, D. Bellinger, A. Leviton and E. N. Allred, N. Engl. J. Med., 1990, 322, 83–88 CrossRef CAS PubMed.
- World Health Orgnization: Exposure to lead: A major public health concern, https://apps.who.int/iris/bitstream/handle/10665/329953/WHO-CED-PHE-EPE-19.4.7-eng.pdf?ua=1.
-
L. Fewtrell, R. Kaufmann and A. Prüss-Üstün, Lead: Assessing the Environmental Burden of Disease at National and Local Levels, World Health Organization, 2003 Search PubMed.
- J. Y. Kim, J.-W. Lee, H. S. Jung, H. Shin and N.-G. Park, Chem. Rev., 2020, 120, 7867–7918 CrossRef CAS PubMed.
- B. Conings, J. Drijkoningen, N. Gauquelin, A. Babayigit, J. D'Haen, L. D'Olieslaeger, A. Ethirajan, J. Verbeeck, J. Manca, E. Mosconi, F. D. Angelis and H.-G. Boyen, Adv. Energy Mater., 2015, 5, 1500477 CrossRef.
- C. Zeng, A. Ramos-Ruiz, J. A. Field and R. Sierra-Alvarez, J. Environ. Manage., 2015, 154, 78–85 CrossRef CAS PubMed.
-
A. J. Bard, R. Parsons and J. Jordan, Standard Potentials in Aqueous Solution, Taylor & Francis, 1985 Search PubMed.
- B. Hailegnaw, S. Kirmayer, E. Edri, G. Hodes and D. Cahen, J. Phys. Chem. Lett., 2015, 6, 1543–1547 CrossRef CAS PubMed.
- Z. Ku, Y. Rong, M. Xu, T. Liu and H. Han, Sci. Rep., 2013, 3, 3132 CrossRef PubMed.
- Z. Liu, M. Zhang, X. Xu, L. Bu, W. Zhang, W. Li, Z. Zhao, M. Wang, Y.-B. Cheng and H. He, Dalton Trans., 2015, 44, 3967–3973 RSC.
- S. Alon, M. Sohmer, C. S. Pathak, I. Visoly-Fisher and L. Etgar, Sol. RRL, 2021, 5, 2100028 CrossRef CAS.
- S. G. Hashmi, A. Tiihonen, D. Martineau, M. Ozkan, P. Vivo, K. Kaunisto, V. Ulla, S. M. Zakeeruddin and M. Grätzel, J. Mater. Chem. A, 2017, 5, 4797–4802 RSC.
- D. Fabini, J. Phys. Chem. Lett., 2015, 6, 3546–3548 CrossRef CAS PubMed.
- 2011 National Emissions Inventory, U.S. Environmental Protection Agency: Washington, DC, 2015, https://www.epa.gov/air-emissions-inventories/2011-national-emissions-inventory-nei-data.
- U. S. G. Survey, 2012 minerals Yearbook: Lead; U.S. Geological Survey, Washington, DC, 2015.
- J. Y. Zhang, X. F. Gao, Y. L. Deng, B. B. Li and C. Yuan, ChemSusChem, 2015, 8, 3882–3891 CrossRef CAS PubMed.
- I. Celik, Z. N. Song, A. J. Cimaroli, Y. F. Yan, M. J. Heben and D. Apul, Sol. Energy Mater. Sol. Cells, 2016, 156, 157–169 CrossRef CAS.
- L. Serrano-Lujan, N. Espinosa, T. T. Larsen-Olsen, J. Abad, A. Urbina and F. C. Krebs, Adv. Energy Mater., 2015, 5, 1501119 CrossRef.
- N. Espinosa, L. Serrano-Lujan, A. Urbina and F. C. Krebs, Sol. Energy Mater. Sol. Cells, 2015, 137, 303–310 CrossRef CAS.
- A. Urbina, J. Phys.: Energy, 2020, 2, 022001 CAS.
- J. Gong, S. B. Darling and F. Q. You, Energy Environ. Sci., 2015, 8, 1953–1968 RSC.
- P. Billen, E. Leccisi, S. Dastidar, S. M. Li, L. Lobaton, S. Spatari, A. T. Fafarman, V. M. Fthenakis and J. B. Baxter, Energy, 2019, 166, 1089–1096 CrossRef CAS.
- M. Krebs-Moberg, M. Pitz, T. L. Dorsette and S. H. Gheewala, Renewable Energy, 2021, 164, 556–565 CrossRef CAS.
- W. Ke, C. C. Stoumpos and M. G. Kanatzidis, Adv. Mater., 2019, 31, 1803230 CrossRef CAS PubMed.
- A. Bernasconi, A. Rizzo, A. Listorti, A. Mahata, E. Mosconi, F. De Angelis and L. Malavasi, Chem. Mater., 2019, 31, 3527–3533 CrossRef CAS.
- S. Y. Shao, J. Liu, G. Portale, H. H. Fang, G. R. Blake, G. H. ten Brink, L. J. A. Koster and M. A. Loi, Adv. Energy Mater., 2018, 8, 1702019 CrossRef.
- T. Nakamura, T. Handa, R. Murdey, Y. Kanemitsu and A. Wakamiya, ACS Appl. Electron. Mater., 2020, 2, 3794–3804 CrossRef CAS.
- T. Handa, A. Wakamiya and Y. Kanemitsu, APL Mater., 2019, 7, 080903 CrossRef.
- B. Saparov and D. B. Mitzi, Chem. Rev., 2016, 116, 4558–4596 CrossRef CAS PubMed.
- T. Krishnamoorthy, H. Ding, C. Yan, W. L. Leong, T. Baikie, Z. Y. Zhang, M. Sherburne, S. Li, M. Asta, N. Mathews and S. G. Mhaisalkar, J. Mater. Chem. A, 2015, 3, 23829–23832 RSC.
- I. Kopacic, B. Friesenbichler, S. F. Hoefler, B. Kunert, H. Plank, T. Rath and G. Trimmel, ACS Appl. Energy Mater., 2018, 1, 343–347 CrossRef CAS.
- N. Ito, M. A. Kamarudin, D. Hirotani, Y. Zhang, Q. Shen, Y. Ogomi, S. Iikubo, T. Minemoto, K. Yoshino and S. Hayase, J. Phys. Chem. Lett., 2018, 9, 1682–1688 CrossRef CAS.
- R. Nie, A. Mehta, B. W. Park, H. W. Kwon, J. Im and S. I. Seok, J. Am. Chem. Soc., 2018, 140, 872–875 CrossRef CAS.
- F. Y. Jiang, D. W. Yang, Y. Y. Jiang, T. F. Liu, X. G. Zhao, Y. Ming, B. W. Luo, F. Qin, J. C. Fan, H. W. Han, L. J. Zhang and Y. H. Zhou, J. Am. Chem. Soc., 2018, 140, 1019–1027 CrossRef CAS PubMed.
- J. C. Hebig, I. Kuhn, J. Flohre and T. Kirchartz, ACS Energy Lett., 2016, 1, 309–314 CrossRef CAS.
- K. W. Jung, M. R. Sohn, H. M. Lee, I. S. Yang, S. D. Sung, J. Kim, E. W. G. Diau and W. I. Lee, Sustainable Energy Fuels, 2018, 2, 294–302 RSC.
- B. W. Park, B. Philippe, X. L. Zhang, H. Rensmo, G. Boschloo and E. M. J. Johansson, Adv. Mater., 2015, 27, 6806 CrossRef CAS PubMed.
- R. L. Z. Hoye, R. E. Brandt, A. Osherov, V. Stevanovic, S. D. Stranks, M. W. B. Wilson, H. Kim, A. J. Akey, J. D. Perkins, R. C. Kurchin, J. R. Poindexter, E. N. Wang, M. G. Bawendi, V. Bulovic and T. Buonassisi, Chem. – Eur. J., 2016, 22, 2605–2610 CrossRef CAS PubMed.
- X. L. Li, X. L. Zhong, Y. Hu, B. C. Li, Y. S. Sheng, Y. Zhang, C. Weng, M. Feng, H. W. Han and J. B. Wang, J. Phys. Chem. Lett., 2017, 8, 1804–1809 CrossRef CAS PubMed.
- D. Cortecchia, H. A. Dewi, J. Yin, A. Bruno, S. Chen, T. Baikie, P. P. Boix, M. Grätzel, S. Mhaisalkar, C. Soci and N. Mathews, Inorg. Chem., 2016, 55, 1044–1052 CrossRef CAS PubMed.
- H. Y. Fu, Sol. Energy Mater. Sol. Cells, 2019, 193, 107–132 CrossRef CAS.
- Q. Zhang, F. Hao, J. B. Li, Y. Y. Zhou, Y. X. Wei and H. Lin, Sci. Technol. Adv. Mater., 2018, 19, 425–442 CrossRef CAS PubMed.
- R. M. Nie, R. R. Sumukam, S. H. Reddy, M. Banavoth and S. I. Seok, Energy Environ. Sci., 2020, 13, 2363–2385 RSC.
- R. Kour, S. Arya, S. Verma, J. Gupta, P. Bandhoria, V. Bharti, R. Datt and V. Gupta, Glob. Chall., 2019, 3, 1900050 CrossRef.
- W. J. Ke and M. G. Kanatzidis, Nat. Commun., 2019, 10, 965 CrossRef.
- C. C. Stoumpos, C. D. Malliakas and M. G. Kanatzidis, Inorg. Chem., 2013, 52, 9019–9038 CrossRef CAS PubMed.
- M. Llanos, R. Yekani, G. P. Demopoulos and N. Basu, Renewable Sustainable Energy Rev., 2020, 133, 110207 CrossRef CAS.
- T. Leijtens, R. Prasanna, A. Gold-Parker, M. F. Toney and M. D. McGehee, ACS Energy Lett., 2017, 2, 2159–2165 CrossRef CAS.
- F. Hao, C. C. Stoumpos, P. J. Guo, N. J. Zhou, T. J. Marks, R. P. H. Chang and M. G. Kanatzidis, J. Am. Chem. Soc., 2015, 137, 11445–11452 CrossRef CAS.
- T. Yokoyama, D. Y. H. Cao, C. C. Stoumpos, T. B. Song, Y. Sato, S. Aramaki and M. G. Kanatzidis, J. Phys. Chem. Lett., 2016, 7, 776–782 CrossRef CAS PubMed.
- K. Nishimura, M. A. Kamarudin, D. Hirotani, K. Hamada, Q. Shen, S. Iikubo, T. Minemoto, K. Yoshino and S. Hayase, Nano Energy, 2020, 74, 104858 CrossRef CAS.
- M. Chen, M. G. Ju, H. F. Garces, A. D. Carl, L. K. Ono, Z. Hawash, Y. Zhang, T. Y. Shen, Y. B. Qi, R. L. Grimm, D. Pacifici, X. C. Zeng, Y. Y. Zhou and N. P. Padture, Nat. Commun., 2019, 10, 16 CrossRef CAS PubMed.
- M. Chen, Q. S. Dong, F. T. Eickemeyer, Y. H. Liu, Z. H. Dai, A. D. Carl, B. Bahrami, A. H. Chowdhury, R. L. Grimm, Y. T. Shi, Q. Q. Qiao, S. M. Zakeeruddin, M. Gratzel and N. P. Padture, ACS Energy Lett., 2020, 5, 2223–2230 CrossRef CAS.
- B. Lee, C. C. Stoumpos, N. Zhou, F. Hao, C. Malliakas, C.-Y. Yeh, T. J. Marks, M. G. Kanatzidis and R. P. H. Chang, J. Am. Chem. Soc., 2014, 136, 15379–15385 CrossRef CAS PubMed.
- C. C. Wu, Q. H. Zhang, Y. Liu, W. Luo, X. Guo, Z. R. Huang, H. Ting, W. H. Sun, X. R. Zhong, S. Y. Wei, S. F. Wang, Z. J. Chen and L. X. Xiao, Adv. Sci., 2018, 5, 1700759 CrossRef PubMed.
- S. Kanno, Y. Imamura and M. Hada, Phys. Rev. Mater., 2019, 3, 075403 CrossRef CAS.
- H. H. Tsai, W. Y. Nie, J. C. Blancon, C. C. S. Toumpos, R. Asadpour, B. Harutyunyan, A. J. Neukirch, R. Verduzco, J. J. Crochet, S. Tretiak, L. Pedesseau, J. Even, M. A. Alam, G. Gupta, J. Lou, P. M. Ajayan, M. J. Bedzyk, M. G. Kanatzidis and A. D. Mohite, Nature, 2016, 536, 312–316 CrossRef CAS PubMed.
- L. L. Mao, C. C. Stoumpos and M. G. Kanatzidis, J. Am. Chem. Soc., 2019, 141, 1171–1190 CrossRef CAS PubMed.
- S. M. Jain, T. Edvinsson and J. R. Durrant, Commun. Chem., 2019, 2, 91 CrossRef.
- G. Schileo and G. Grancini, J. Mater. Chem. C, 2021, 9, 67–76 RSC.
- H. Belevi and P. Baccini, Waste Manage. Res., 1989, 7, 43–56 CrossRef CAS.
- A. O. W. Leung, N. S. Duzgoren-Aydin, K. C. Cheung and M. H. Wong, Environ. Sci. Technol., 2008, 42, 2674–2680 CrossRef CAS PubMed.
- X. L. Zeng, R. Y. Gong, W. Q. Chen and J. H. Li, Environ. Sci. Technol., 2016, 50, 1347–1358 CrossRef CAS PubMed.
- The European Parliament and The Council Of The European Union Directive 2002/96/EC on waste electrical and electronic equipment (WEEE), https://eur-lex.europa.eu/resource.html?uri=cellar:ac89e64f-a4a5-4c13-8d96-1fd1d6bcaa49.0004.02/DOC_1&format=PDF.
- J. M. Kadro and A. Hagfeldt, Joule, 2017, 1, 29–46 CrossRef.
- Annex to Directive 2002/95/EC, https://eur-lex.europa.eu/legal-content/EN/TXT/?uri=CELEX:32009D0443.
- RoHS 3 (EU 2015/863), https://www.rohsguide.com/rohs3.htm.
- W. Yang, Rev. Eur. Comp. Int. Environ. Law, 2008, 17, 335–344 Search PubMed.
- State of California: Electronic Waste Recycling Act of 2003, https://www.calrecycle.ca.gov/electronics/act2003/.
- J. H. Im, C. R. Lee, J. W. Lee, S. W. Park and N. G. Park, Nanoscale, 2011, 3, 4088–4093 RSC.
- M. A. Green, A. Ho-Baillie and H. J. Snaith, Nat. Photonics, 2014, 8, 506–514 CrossRef CAS.
- European Commision RoHS 2 FAQ, https://www.rohsguide.com/rohs-faq.htm.
- DIRECTIVE 2011/65/EU OF THE EUROPEAN PARLIAMENT AND OF THE COUNCIL of 8 June 2011 on the restriction of the use of certain hazardous substances in electrical and electronic equipment, https://eur-lex.europa.eu/legal-content/EN/TXT/PDF/?uri=CELEX:32011L0065&from=en.
- H. Aizawa, H. Yoshida and S.-I. Sakai, Resour., Conserv. Recycl., 2008, 52, 1399–1410 CrossRef.
- DIRECTIVE 2006/66/EC OF THE EUROPEAN PARLIAMENT AND OF THE COUNCIL of 6 September 2006 on batteries and accumulators and waste batteries and accumulators and repealing Directive 91/157/EEC, https://eur-lex.europa.eu/legal-content/EN/ALL/?uri=CELEX%3A32006L0066.
-
R. Stehouwer, Lead in Residential Soils: Sources, Testing, and Reducing Exposure, https://extension.psu.edu/lead-in-residential-soils-sources-testing-and-reducing-exposure.
- Y. Jiang, L. B. Qiu, E. J. Juarez-Perez, L. K. Ono, Z. H. Hu, Z. H. Liu, Z. F. Wu, L. Q. Meng, Q. J. Wang and Y. B. Qi, Nat. Energy, 2019, 4, 585–593 CrossRef CAS.
- B. Conings, A. Babayigit and H.-G. Boyen, ACS Energy Lett., 2019, 4, 873–878 CrossRef CAS.
- Y. F. Zheng, R. Su, Z. J. Xu, D. Y. Luo, H. Dong, B. Jiao, Z. X. Wu, Q. H. Gong and R. Zhu, Sci. Bull., 2019, 64, 1255–1261 CrossRef CAS.
- H. C. Kim, T. W. Jang, H. J. Chae, W. J. Choi, M. N. Ha, B. J. Ye, B. G. Kim, M. J. Jeon, S. Y. Kim and Y. S. Hong, Ann. Occup. Environ. Med., 2015, 27, 9 CrossRef PubMed.
- A. J. Huckaba, D. T. Sun, A. A. Sutanto, M. Mensi, Y. Zhang, W. L. Queen and M. K. Nazeeruddin, Energy Technol., 2020, 8, 2000239 CrossRef CAS.
- R. Cheacharoen, N. Rolston, D. Harwood, K. A. Bush, R. H. Dauskardt and M. D. McGehee, Energy Environ. Sci., 2018, 11, 144–150 RSC.
- S. F. Wu, Z. Li, M. Q. Li, Y. X. Diao, F. Lin, T. T. Liu, J. Zhang, P. Tieu, W. P. Gao, F. Qi, X. Q. Pan, Z. T. Xu, Z. L. Zhu and A. K. Y. Jen, Nat. Nanotechnol., 2020, 15, 934–940 CrossRef CAS PubMed.
- Z. P. Wang, D. P. McMeekin, N. Sakai, S. van Reenen, K. Wojciechowski, J. B. Patel, M. B. Johnston and H. J. Snaith, Adv. Mater., 2017, 29, 1604186 CrossRef PubMed.
- A. A. Said, J. Xie and Q. Zhang, Small, 2019, 15, 1900854 CrossRef PubMed.
- A. Uddin, M. B. Upama, H. M. Yi and L. P. Duan, Coatings, 2019, 9, 65 CrossRef.
- J. Ahmad, K. Bazaka, L. J. Anderson, R. D. White and M. V. Jacob, Renewable Sustainable Energy Rev., 2013, 27, 104–117 CrossRef CAS.
- F. Corsini and G. Griffini, J. Phys.: Energy, 2020, 2, 031002 CAS.
- D. M. Tanenbaum, H. F. Dam, R. Rosch, M. Jorgensen, H. Hoppe and F. C. Krebs, Sol. Energy Mater. Sol. Cells, 2012, 97, 157–163 CrossRef CAS.
- A. El Amrani, A. Mahrane, F. Y. Moussa and Y. Boukennous, Int. J. Photoenergy, 2007, 2007, 027610 CrossRef.
- B. Conings, A. Babayigit and H. G. Boyen, ACS Energy Lett., 2019, 4, 873–878 CrossRef CAS.
- V. K. Ravi, B. Mondal, V. V. Nawale and A. Nag, ACS Omega, 2020, 5, 29631–29641 CrossRef CAS PubMed.
- S. Chen, Y. Deng, H. Gu, S. Xu, S. Wang, Z. Yu, V. Blum and J. Huang, Nat. Energy, 2020, 5, 1003–1011 CrossRef.
- S. Chen, Y. Deng, X. Xiao, S. Xu, P. N. Rudd and J. Huang, Nat. Sustainable, 2021, 4, 636–643 CrossRef.
- J. Lee, G.-W. Kim, M. Kim, S. A. Park and T. Park, Adv. Energy Mater., 2020, 10, 1902662 CrossRef CAS.
- M. Z. Mokhtar, J. He, M. Li, Q. Chen, J. C. R. Ke, D. J. Lewis, A. G. Thomas, B. F. Spencer, S. A. Haque and B. R. Saunders, Chem. Commun., 2021, 57, 994–997 RSC.
- X. Li, F. Zhang, H. Y. He, J. J. Berry, K. Zhu and T. Xu, Nature, 2020, 578, 555 CrossRef CAS PubMed.
- V. M. Fthenakis, Energy Policy, 2000, 28, 1051–1058 CrossRef.
- J. Tao and S. R. Yu, Sol. Energy Mater. Sol. Cells, 2015, 141, 108–124 CrossRef CAS.
- T. Y. Wang, Y. C. Lin, C. Y. Tai, R. Sivakumar, D. K. Rai and C. W. Lan, J. Cryst. Growth, 2008, 310, 3403–3406 CrossRef CAS.
- F. Yang, S. Wang, P. Dai, L. Chen, A. Wakamiya and K. Matsuda, J. Mater. Chem. A, 2021, 9, 2612–2627 RSC.
- F.-W. Liu, G. Biesold, M. Zhang, R. Lawless, J.-P. Correa-Baena, Y.-L. Chueh and Z. Lin, Mater. Today, 2021, 43, 185–197 CrossRef CAS.
- J. M. Kadro, N. Pellet, F. Giordano, A. Ulianov, O. Muntener, J. Maier, M. Gratzel and A. Hagfeldt, Energy Environ. Sci., 2016, 9, 3172–3179 RSC.
- A. Binek, M. L. Petrus, N. Huber, H. Bristow, Y. H. Hu, T. Bein and P. Docampo, ACS Appl. Mater. Interfaces, 2016, 8, 12881–12886 CrossRef CAS PubMed.
- B. Augustine, K. Remes, G. S. Lorite, J. Varghese and T. Fabritius, Sol. Energy Mater. Sol. Cells, 2019, 194, 74–82 CrossRef CAS.
- B. J. Kim, D. H. Kim, S. L. Kwon, S. Y. Park, Z. Li, K. Zhu and H. S. Jung, Nat. Commun., 2016, 7, 11735 CrossRef CAS PubMed.
- L. Huang, Z. Hu, J. Xu, X. Sun, Y. Du, J. Ni, H. Cai, J. Li and J. Zhang, Sol. Energy Mater. Sol. Cells, 2016, 152, 118–124 CrossRef CAS.
- L. Huang, J. Xu, X. Sun, R. Xu, Y. Du, J. Ni, H. Cai, J. Li, Z. Hu and J. Zhang, ACS Sustainable Chem. Eng., 2017, 5, 3261–3269 CrossRef CAS.
- J. Xu, Z. Y. Hu, L. K. Huang, X. K. Huang, X. Y. Jia, J. Zhang, J. J. Zhang and Y. J. Zhu, Prog. Photovoltaics, 2017, 25, 1022–1033 CAS.
- P. Chhillar, B. P. Dhamaniya, V. Dutta and S. K. Pathak, ACS Omega, 2019, 4, 11880–11887 CrossRef CAS.
- X. Feng, Q. Guo, J. Xiu, Z. Ying, K. W. Ng, L. Huang, S. Wang, H. Pan, Z. Tang and Z. He, Cell Rep. Phys. Sci., 2021, 2, 100341 CrossRef CAS.
- C. G. Poll, G. W. Nelson, D. M. Pickup, A. V. Chadwick, D. J. Riley and D. J. Payne, Green Chem., 2016, 18, 2946–2955 RSC.
- F. Ardente, C. E. L. Latunussa and G. A. Blengini, Waste Manage., 2019, 91, 156–167 CrossRef CAS PubMed.
|
This journal is © The Royal Society of Chemistry 2021 |
Click here to see how this site uses Cookies. View our privacy policy here.