Identification of C2–C5 products from CO2 hydrogenation over PdZn/TiO2–ZSM-5 hybrid catalysts†
Received
13th December 2020
, Accepted 10th February 2021
First published on 16th February 2021
Introduction
The sustainable production of energy is one of the major challenges of modern society.1,2 Several technologies have been developed to harvest renewable energy (e.g., solar panels, wind farms) in the form of electricity.2 However, due to the intermittent nature of renewables, surplus produced electricity must be stored as chemical bonds to ensure a steady production of energy when electricity production is low.3 The production of H2via water splitting is a route with a high renewable electricity storage capacity,4 and is a possible energy vector for future technology.5,6 However, energy decarbonisation is likely to occur in a subtle way.7 Therefore, it is important to develop transitory routes that allow the use of current technology, but approach CO2 neutrality.8 This can be achieved by storing H2 produced via water electrolysis through renewable electricity in the form of hydrocarbons, by its reaction with CO2.9–11
The production of CH3OH from syngas (CO/CO2/H2) over a CuO/ZnO/Al2O3 catalyst is a mature process (250–300 °C, 50–100 bar), with an annual CH3OH production of 57 Mt,10 and increasing. Hence, renewable H2 could be easily incorporated in the CH3OH production cycle, however for the process to be CO2 neutral, CH3OH must be obtained from recycled CO2 and sustainably produced H2. Thermodynamically, CH3OH formation from CO2 and H2 is favoured at high pressure and low temperature. Nevertheless, a high temperature (>200 °C) is needed to activate CO2, which in turn results in the deactivation of Cu-based catalysts due to Cu sintering9–13 and coke deposition.14 Pd-based catalysts are employed in CO2 hydrogenation to CH3OH as a stable alternative to Cu-based catalysts.15–19
Research on Pd/ZnO catalysts confirmed the β-PdZn alloy as the active phase for CH3OH synthesis.20–23 Commercially sourced ZnO usually has a low surface area which results in large PdZn particles, and hence, to improve PdZn dispersion, supports with a higher surface area (e.g., CeO2,18 carbon nanofibers,22 carbon nanotubes,24 Al2O3,25 or TiO2 (ref. 25 and 26)) are commonly used. The higher stability of PdZn alloy catalysts allows for higher reaction temperatures, however, then CH3OH productivity is limited by the thermodynamic equilibrium whilst CO formation is favoured through the reverse water gas shift (RWGS) reaction. To increase oxygenate productivity above the limited CO2 hydrogenation to CH3OH dictated by the equilibrium, CH3OH can be simultaneously dehydrated to dimethyl ether (DME) by physically mixing a methanol synthesis catalyst with a solid acid catalyst.27–30 ZSM-5 zeolites are commonly employed as solid acid catalysts to dehydrate CH3OH to DME due to their high resistance to water, high stability and the presence of Lewis and Brønsted acid sites.31 The conversion of methanol or dimethyl ether to hydrocarbons (MTH or DMTH respectively) is a mature process that also employs ZSM-5 zeolites as catalysts (300–500 °C, 1 bar).32–34 More importantly, it has been reported that using H2 or H2O in the feed for the MTH process decreased the deactivation of several zeolites (HSAPO, HSSZ, HFER, HBEA, ZSM-5) by limiting coke deposition within structural pores, without significantly affecting the hydrocarbon chain distribution or the olefin-to-paraffin selectivity.35–37 Water is produced as a by-product in CO2 hydrogenation to CH3OH, moreover H2 is present in the feed. Hence, the synthesis of hydrocarbons from CO2 over a methanol synthesis catalyst combined with an acid catalyst with reduced coke deposition is achievable. Bonura et al.29 studied different reactor bed configurations for the direct synthesis of DME from CO2 by combining a methanol synthesis catalyst and a solid acid catalyst, and found that a physical mixture (also known as a hybrid catalyst) of Cu–ZnO–ZrO2 and H-ZSM-5 gave the highest oxygenate (CH3OH + DME) productivity. Higher oxygenate productivity was also observed for a Pd/ZnO–ZSM-5 hybrid catalyst compared to a PdZn on ZSM-5 catalyst.38 Ihm et al.39 reported the direct synthesis of hydrocarbons from CO2 + H2 on CuO/ZnO/ZrO2–ZSM-5 (Si/Al = 22) hybrid catalysts. At 400 °C and 30 bar the selectivity towards CO, oxygenates and hydrocarbons observed was 93.4, 1.8 and 4.8% respectively. C5+ products were detected, although C1 and C2 products accounted for 95.4% of the hydrocarbon product distribution. Over a ZnZrO2/SAPO catalyst at 380 °C and 20 bar (∼18% CO2 conversion), the CO selectivity was reduced to 47%, whilst C2–C4 olefins accounted for 80% of the total hydrocarbon distribution, and the remaining hydrocarbons were assigned to C2–C4 alkanes (14%), C1 (3%) and C5+ (3%).40 Light olefins synthesised on hybrid catalysts from CO2 can also undergo further reduction to their corresponding alkanes on the methanol synthesis catalyst, which effectively acts as a hydrogenation catalyst. Park et al.41 reported ethane (76.4%) as the main hydrocarbon product over a CuZnOZrO2–ZSM-5 catalyst (28 bar, 400 °C), with little formation of C3 (4.5%), C4 (0.8%) and C5+ (0.2%) products. However, as reported by Giordano, Frusteri and co-workers42,43 for CO2 conversion to DME over CuZnZr/ferrierite hybrid catalysts, Cu remains prone to severe sintering under the reaction conditions (260 °C, 30 bar). This makes catalyst stability the bottle neck of this process.
To the best of our knowledge, reports on PdZn hybrid catalysts for CO2 hydrogenation focus on DME,27,38 but no detailed attention has been paid to the produced hydrocarbons. We therefore assessed the activity and stability of diverse PdZn/TiO2–ZSM-5 hybrid catalysts under CO2 hydrogenation conditions (20 bar, <360 °C) and identified produced hydrocarbons derived from MTH and DMTH.
Experimental section
Materials
All ZSM-5 zeolites used in this work were purchased from Alfa Aesar (NH4+-form of ZSM-5, Si/Al = 23, 50 and 80); Pd acetylacetonate (Pd(acac)2, 99%) and Zn acetylacetonate (Zn(acac)2, 99%) were supplied by Sigma-Aldrich; titanium oxide (TiO2-P25) was ordered from Aeroxide.
PdZn/TiO2 catalyst synthesis
The synthesis of PdZn/TiO2 by chemical vapour impregnation (CVI) was reported previously.25–27 For the synthesis of 3 g of PdZn/TiO2 catalyst with a 5 wt% Pd loading and a 1
:
5 palladium to zinc molar ratio, Pd(acac)2 (0.43 g, 1.40 mmol), Zn(acac)2 (2.06 g, 6.93 mmol) and TiO2 (2.39 g) were physically mixed in a glass vial until homogeneous. The mixture was then transferred into a Schlenk flask, evacuated (10−3 bar) and heated (145 °C, 1 h). The as prepared materials were recovered and annealed in static air (10 °C min−1, 500 °C, 16 h). PdZn/TiO2 characterisation was performed on a portion of catalyst reduced in flowing 5% H2/Ar (400 °C, 5 °C min−1, 1 h).
PdZn/TiO2–ZSM-5 hybrid catalyst preparation
The as received (NH4)–ZSM-5 zeolites were annealed in static air (550 °C, 10 °C min−1, 6 h) to obtain the H-ZSM-5 form prior to reaction. 0.5 g of PdZn/TiO2 and 0.5 g of treated ZSM-5 were physically mixed in a vial until homogeneous. The mixture was pelleted (10 ton) and crushed (425–600 μm) to obtain the hybrid catalyst. Zeolites are named in the text according to their Si/Al ratio, for instance ZSM-5 with a Si/Al ratio of 23
:
1 will be referred to as ZSM-5(23).
CO2 hydrogenation and consecutive MTH/DMTH catalyst testing
Catalytic activity for CO2 hydrogenation to CH3OH, DME, olefins and hydrocarbons was achieved in a stainless steel fixed-bed (50 cm length, 0.5 cm internal diameter) continuous flow reactor. 0.5 g of hybrid catalyst without diluent (or 0.25 g of pelleted PdZn/TiO2 with 0.25 g of SiC as diluent) were secured in the reactor tube using quartz wool. Prior to reaction, the hybrid catalysts were pre-reduced in 5% H2/He (400 °C, 5 °C min−1, 1 h). Subsequently, the reactor was cooled down to 50 °C, the 5% H2/He flow was switched to the reaction mixture (CO2/N2/H2 = 1
:
1
:
3, 30 ml min−1), and the reactor was pressurised to 20 bar and heated to the desired reaction temperature (240, 270, 300, 320, 340 and 360 °C, 5 °C min−1, 6 h dwell). To avoid product condensation, post reactor lines and valves were heated to 130 °C. Products were analysed via online gas chromatography (Agilent 7890, fitted with FID and TCD detectors). Details of how CO2 conversion, product selectivity and productivities were calculated can be found in the ESI (eqn (S1–S11†)).
Catalyst characterisation
X-ray absorption spectroscopy (XAS) was carried out in transmission mode at the Pd K-edge, at the B18 beamline of the Diamond Light Source, Harwell, UK, and a Pd foil was examined simultaneously with the sample and used as a reference. Three spectra were averaged to minimise the noise signal. The X-ray absorption fine structure (EXAFS) was analysed with the Demeter software package (Athena and Artemis).44 X-ray photoelectron spectroscopy (XPS) was carried out on a Kratos Axis Ultra-DLD fitted with a monochromatic Al Kα (75–150 W) source and analyser, using a pass energy of 40 eV. The XPS data were analysed using Casa XPS software. Powder X-ray diffraction (XRD) patterns were obtained on a (θ–θ) PANalytical X’pert Pro powder diffractometer fitted with a hemispherical analyser using a Cu Kα radiation source (40 keV, 40 mA). The pore sizes and BET surface areas of the ZSM-5 zeolites were obtained through N2 adsorption isotherms using a 3-flex Micromeritics instrument. Samples were degassed in situ at 250 °C for 10 h prior to analysis. Coke deposition during CO2 hydrogenation was measured through thermogravimetric analysis on a PerkinElmer TL9000 with a TG-IR-MS interface.
Results and discussion
PdZn/TiO2–ZSM-5 hybrid catalysts for direct CO2 conversion to hydrocarbons
In addition to PdZn/TiO2 employed as a CH3OH synthesis catalyst,20–23 commercial ZSM-5 zeolites with various Si/Al ratios (23, 50 and 80) were used as solid acid catalysts to promote consecutive CH3OH dehydration to DME27–30 and further MTH/DMTH.32–34 XRD patterns, pore sizes and BET surface areas for the commercial ZSM-5 zeolites after annealing (static air, 550 °C, 10 °C min−1, 6 h) can be found in the ESI (Fig. S1 and Table S1,† respectively). Thorough characterisation of PdZn/TiO2 synthesised by chemical vapour impregnation (CVI) with 5 wt% Pd and a Pd/Zn molar ratio of 1
:
5 was previously reported.25–27
Firstly, the catalytic activity of PdZn/TiO2 (0.25 g catalyst diluted with 0.25 g of SiC) for CO2 hydrogenation was assessed (20 bar, CO2/N2/H2 = 1
:
1
:
3, 240–360 °C). As observed in Table S2,† raising the reaction temperature from 240 to 360 °C resulted in an increase in the CO2 conversion from 6.8 to 31.2%, accompanied by an increase in the CO selectivity (from 74.6 to 97.9%) at the expense of CH3OH selectivity (from 24.3 to 1.3%), in accordance with the reaction thermodynamics.45 Below 300 °C, CH3OH synthesis proceeded in the kinetic regime (Fig. 1a), as shown by the increase in the CH3OH productivity with temperature up to 518 mmol kgcat−1 h−1. At 300 °C, the CH3OH yield reached equilibrium (1.45% CH3OH yield),45 and hence, above 300 °C CH3OH synthesis is controlled by the thermodynamic equilibrium (Fig. 1b), as shown by the sharp decrease in CH3OH productivity. Low selectivity toward CH4 (<0.8%) and DME (<1.0%), produced by CH3OH decomposition on TiO2 (ref. 46 and 47) and CH3OH dehydration,27 respectively, was observed. Nevertheless, in the absence of ZSM-5 solid acid catalysts, no other hydrocarbons were detected.
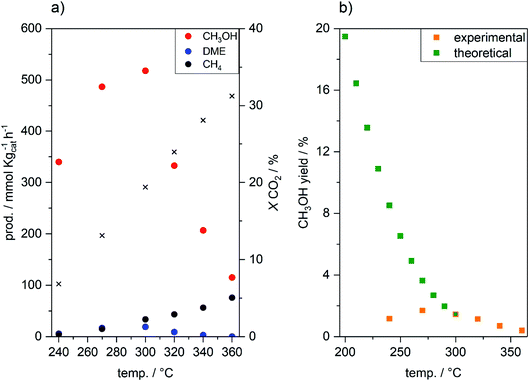 |
| Fig. 1 (a) CH3OH, DME and CH4 productivities and CO2 conversion for CO2 hydrogenation (20 bar, 30 ml min−1, CO2/H2/N2 = 1 : 3 : 1, 240–360 °C, 6 h dwell) over PdZn/TiO2. (b) Theoretical CH3OH yield obtained from Shen et al.45 compared to experimental CH3OH yield with temperature over PdZn/TiO2. | |
Comparable CO2 conversion and CO productivity to PdZn/TiO2 were observed for all PdZn/TiO2–ZSM-5 hybrid catalysts (Fig. 2), indicating that the activity of the methanol synthesis catalyst is not altered by the proximity of solid acid zeolites, and that ZSM-5 zeolites are not active towards the RWGS. To ensure that ZSM-5 zeolites do not act as RWGS or as CH3OH synthesis catalysts, blank ZSM-5(23) was employed for the CO2 hydrogenation reaction (Table S3†), and negligible CO2 conversion was observed at 270 °C. The efficient dehydration of CH3OH to DME occurred over all PdZn/TiO2–ZSM-5 hybrid catalysts. The highest oxygenate productivity (CH3OH + DME) was obtained at 270 °C. At this temperature almost no methanol to olefins (MTH) or dimethyl ether to olefins (DMTH) conversion takes place, with only small traces of ethane detected over hybrid catalysts with ZSM-5(50 and 80), and small amounts of higher hydrocarbons observed for PdZn/TiO2–ZSM-5(23). DME is the major oxygenate product with a selectivity close to 20%. Moreover, the total methanol productivity (CH3OH(tot)), considering that all hydrocarbons originate from CH3OH by either dehydration to DME or through the MTH/DMTH process, was higher for all hybrid catalysts compared to PdZn/TiO2 (Fig. 3).
 |
| Fig. 2 CO2 conversion and CO productivity over PdZn/TiO2 and PdZn/TiO2–ZSM-5 hybrid catalysts during CO2 hydrogenation (20 bar, 30 ml min−1, CO2/H2/N2 = 1 : 3 : 1, 240–360 °C, 6 h dwell). | |
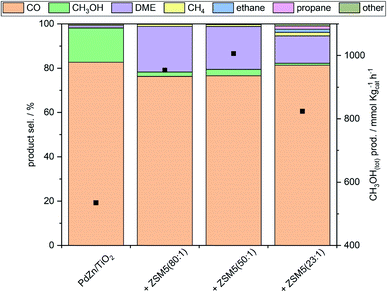 |
| Fig. 3 CO, oxygenate and hydrocarbon selectivity and total CH3OH productivity for CO2 hydrogenation (20 bar, 270 °C, CO2/H2/N2 = 1 : 3 : 1) over PdZn/TiO2 and PdZn/TiO2–ZSM-5 hybrid catalysts. | |
The hydrocarbon productivities and CH3OH(tot) over PdZn/TiO2–ZSM-5 hybrid catalysts can be found in Table S4.† At 300 °C, the hybrid catalysts showed higher CH3OH(tot) compared to PdZn/TiO2, thus overcoming the theoretical CH3OH yield dictated by the equilibrium. Increasing the alumina ratio in the zeolite promoted the formation of longer hydrocarbons. The presence of aluminium sites is related to Brønsted acid sites with mild acidity, and hence, a higher concentration of Brønsted acid sites promotes chain growth via the hydrocarbon pool mechanism.33,48 Light olefins produced as intermediates in MTH49 undergo further hydrogenation over PdZn/TiO2, yielding the corresponding alkanes (ethane and propane); a mixture of n-butane and 2-butene was observed, whilst only olefins were detected in the C5 fraction (1-pentene and 2-cis/trans-pentene). Thus, when PdZn alloys are used for the synthesis of hydrocarbons from CO2via a methanol mediated route over hybrid catalysts, they behave as methanol synthesis catalysts but also as olefin hydrogenation catalysts, limiting hydrocarbon chain growth as also reported for Cu-based catalysts.49–51 CH3OH(tot) over hybrid catalysts is higher compared to PdZn/TiO2 at any temperature, with total CH3OH productivity surpassing the equilibrium yield above 300 °C. The highest total CH3OH productivity for hybrid catalysts was observed in the 270–300 °C range; hybrid catalysts with ZSM-5(80 and 50) gave the highest oxygenate productivity (CH3OH and DME), while ZSM-5(23) led to higher hydrocarbon productivity (Fig. 4) via faster MTH/DMTH. Although the total CH3OH productivity was higher than the equilibrium yield, above 300 °C, the hydrocarbon productivity is limited by CH3OH availability which leads to a decrease in the total CH3OH productivity at higher temperatures. The hydrocarbon selectivity based on MTH/DMTH showed that increasing the aluminium concentration in ZSM-5 in the hybrid catalyst resulted in improved selectivity towards higher hydrocarbons (Table S5†). In the 320–340 °C temperature range ethane and propane accounted for 50% of MTH/DMTH product selectivity for all hybrid catalysts. Note that the real CH4 selectivity via the MTH and DMTH process is lower than the reported values, since CH4 is also produced as a by-product in CH3OH decomposition on PdZn/TiO2.47
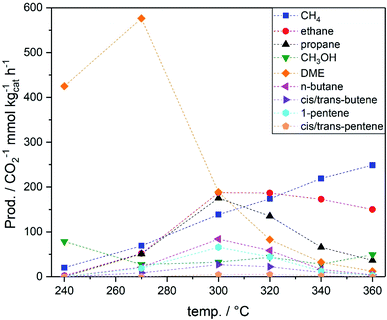 |
| Fig. 4 Productivities based on carbon (e.g., two molecules of CO2 converted per ethane molecule and three molecules of CO2 converted per propane molecule) during CO2 hydrogenation (20 bar, 30 ml min−1, CO2/H2/N2 = 1 : 3 : 1) over the PdZn/TiO2–ZSM-5(23) hybrid catalyst. | |
Catalytic stability of PdZn/TiO2 under the reaction conditions
The higher stability of PdZn alloy catalysts compared to their Cu-based counterparts was proven under methanol reforming conditions,15,52–54 which is the opposite reaction to the intended CO2 hydrogenation to CH3OH. Copper sinters in the presence of water at elevated temperatures, and hence, due to the higher water content when the feed is CO2 instead of CO, PdZn alloys are employed as stable alternatives to Cu-based catalysts for the synthesis of CH3OH from CO2.15–19 According to the Pd–Zn phase diagram developed by Massalski55 and Vizdal et al.,56 the β-PdZn alloy is thermally stable up to 1200 °C. However, in the presence of oxygen at 300 °C, the surface of the PdZn alloy segregates into ZnO and metallic Pd,53 whilst under H2, the β-PdZn alloy was experimentally proven to be stable up to 600 °C.57 Chen et al.,58 based on DFT calculations, suggested that Zn segregates from the PdZn alloy when the alloy is supported on ZnO. Nevertheless, Ahoba-Sam et al.38 reported no changes in the PdZn phase and no formation of extra Pd-phases through operando XAS during CO2 hydrogenation to CH3OH (8 bar, 350 °C).
The stability of the PdZn phase in the PdZn/TiO2 methanol synthesis catalyst was assessed through XAS, XRD and XPS characterisation pre- and post-reaction (20 bar, CO2/H2/N2 = 1
:
3
:
1, 30 ml min−1, 240–360 °C, 6 h dwell, 36 h reaction). Extended X-ray absorption fine-structure spectroscopy (EXAFS) at the Pd K-edge was employed to detect structural and electronic changes in the PdZn phase after reaction. No noticeable differences were observed between the EXAFS spectra up to 3.5 Å of PdZn/TiO2 after pre-reduction (5% H2, 400 °C, 1 h) and after CO2 hydrogenation at up to 360 °C (Fig. 5a). Bulk Pd has a cubic structure with a Pd–Pd bond distance of 1.75 Å, whilst the β-PdZn alloy has a tetragonal structure. As expected for the intercalation of a Zn atom between two Pd atoms, on average shorter bond distances for the first coordination shell compared to bulk Pd were observed (shorter Pd–Zn bond distance compared to the Pd–Pd distance in Pd foil).59 Moreover, comparison with a PdO standard could suggest the presence of a Pd–O bond at 2.02 Å, with the concomitant but lower intensity Pd–O–Pd bond at 3.41 Å in the second coordination shell.60 This could be attributed to oxidation of the first atomic layer of the PdZn alloy in contact with air.53 Peak fitting using Artemis44 allowed us to obtain the Pd–Pd and Pd–Zn bond distances and the Pd coordination environment (Table 1). Details of the fitting can be obtained from Table S6.† Based on previous reports, PdZn alloy formation begins at the surface of Pd nanoparticles via hydrogen spillover to adjacent ZnO, and the alloy grows inwards, generating a PdZn layer over a Pd core.53,57 Therefore, the incorporation of bulk Pd–Pd bond distances was necessary to obtain a good fit. No differences in the Pd–Zn or Pd–Pd bond distances or coordination number were observed, suggesting high bulk structural stability of the PdZn alloy under reaction conditions, as also reported by Olsbye and co-workers.38 Despite the apparent bond distance at 2.02 Å, no good fit was obtained after the introduction of the Pd–O scattering path, indicating that this contribution can be attributed to noise or to marginal PdO content.
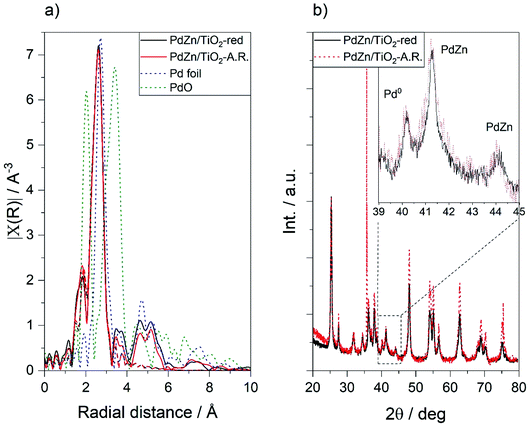 |
| Fig. 5 (a) EXAFS spectra of PdZn/TiO2 after reduction and PdZn/TiO2 after reaction (240–360 °C). Recorded spectra and fits (window 1.8–3.5 Å) are represented by solid and dashed lines, respectively. Spectra of Pd foil and PdO are included for comparison; (b) XRD patterns recorded for PdZn/TiO2 after reduction and PdZn/TiO2 after reaction. | |
Table 1 Bond distances and coordination numbers for PdZn/TiO2 after reduction and PdZn/TiO2 after reaction obtained from EXAFS fitting
PdZn/TiO2 |
Bond |
Distance |
CN |
σ
2
|
R
f
|
Reduced |
Pd–Zn(alloy) |
2.59 |
2.62–0.21 |
0.0047–0.0014 |
0.019 |
Pd–Pd1(alloy) |
3.06 |
7.58 |
0.0217–0.0055 |
Pd–Pd2(alloy) |
3.35 |
3.79 |
0.0215–0.0111 |
Pd–Pd(metal) |
2.75 |
12 (fixed) |
0.0238–0.0030 |
A.R. |
Pd–Zn(alloy) |
2.60 |
2.71 |
0.0050–0.0015 |
0.020 |
Pd–Pd1(alloy) |
3.03 |
7.52 |
0.0216–0.0068 |
Pd–Pd2(alloy) |
3.31 |
3.76–0.2 |
0.0218–0.0115 |
Pd–Pd(metal) |
2.74 |
12 (fixed) |
0.0220–0.0030 |
Pd foil |
Pd–Pd1 |
2.75 |
12 (fixed) |
0.0055–0.0002 |
0.016 |
Pd–Pd2 |
3.89 |
6 (fixed) |
0.0097–0.0022 |
Phase changes in the β-PdZn alloy during reaction were investigated by recording the XRD pattern of PdZn/TiO2 after reduction (400 °C, 1 h) and after reaction (240–360 °C, 20 bar, 36 h). In agreement with the EXAFS analysis, no changes were observed in the (111) and (200) β-PdZn reflections at 41.2° and 44.1° respectively,15,19,27 showing the high thermal stability of bulk PdZn under the reaction conditions (Fig. 5b). Moreover, no significant changes were observed in the XRD peak at 40.1° assigned to metallic Pd (PDF 00-046-1043), which presumably is protected underneath a PdZn layer.53,57 Unincorporated Zn in the PdZn alloy is observed as ZnO at 31.7°, 34.4° and 36.3° (PDF 00-036-1451). In line with PdZn and Pd, no changes in the ZnO reflections were observed after reaction. Nevertheless, the TiO2-related reflections become more intense after reaction, suggesting an increase in the particle size of the support (Fig. S2†).
EXAFS and XRD are averaging techniques sensitive to bulk changes. Catalysis, however, is a surface process, and hence small changes at the surface greatly affect the catalytic activity. To follow surface changes in the PdZn alloy composition, the Pd(3d) and Zn(LM2) orbitals of the PdZn/TiO2 catalyst before and after reaction were analysed by X-ray photoelectron spectroscopy (XPS). The Zn(2p) orbital is not sensitive towards chemical changes (e.g. the binding energies for Zn0 and Zn2+ are reported at 1021.7 and 1022 eV, respectively),61 and as observed by XRD, the unalloyed zinc remained as ZnO, hence the Pd(3d) and Zn(LM2) orbitals were calibrated against the Zn(2p) orbital at 1022 eV. The Pd(3d) peak for PdZn/TiO2 after reduction and after reaction was centred at 335.6 eV (Fig. 6), between the binding energy values reported for metallic Pd (334.8–335.4 eV)62–64 and the PdZn alloy (335.6–336.7 eV).64–66 Peak fitting using finite Lorentzian line shapes for the Pd and PdZn peaks (including satellites) and Gaussian line shapes for the PdO peaks and satellites with a Shirley background as described previously47 indicated the presence of Pd, PdZn and PdO at 335.0, 335.9 and 337.2 eV, respectively (Fig. S3a†).54,64 The presence of Pd and PdZn was confirmed by the XRD and EXAFS bulk characterisation techniques, however bulk PdO was not observed. The broadening of the Pd(3d) peak after reaction indicated an increase in the proportion of surface PdO, suggesting that surface PdZn phase separation into ZnO and Pd occurred, with concomitant palladium passivation when in contact with air.53 No significant changes were observed in the Zn(LM2) Auger electron spectra before and after reaction (Fig. S3b†); the main peak at 998 eV with a minor satellite contribution at 991 eV was attributed to the presence of ZnO.67
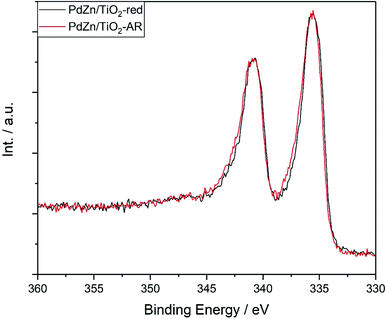 |
| Fig. 6 Pd(3d) XPS analysis for PdZn/TiO2 after reduction (5% H2, 400 °C, 1 h) and after reaction (20 bar, 240–360 °C, 36 h, CO2 : H2 : N2 = 1 : 3 : 1). | |
No significant changes in the PdZn phase were detected by EXAFS or XRD, confirming the bulk thermal stability of PdZn under reaction conditions (20 bar, 240–340 °C, CO2/H2/N2 = 1
:
3
:
1, 36 h). However some surface PdZn phase separation into Pd and ZnO was suggested by the XPS characterisation. Coke deposition is often reported as the main deactivation mechanism for MTH over acid zeolite catalysts. Coke inhibits CH3OH diffusion to the acid active sites by either filling zeolite cavities or blocking pores.34 Zeolites can be regenerated at high temperature (500–600 °C) by oxidising deposited coke to CO2 with oxygen.68 To assess the extent of coke deposition during CO2 hydrogenation (20 bar, 240–340 °C, CO2/H2/N2 = 1
:
3
:
1, 36 h) over PdZn/TiO2–ZSM-5 hybrid catalysts, TGA-MS was performed on fresh and spent catalysts (Fig. S4†). The mass loss observed below 200 °C can be assigned to physi/chemisorbed water. Just above 200 °C, an extra 1 wt% mass loss compared to the fresh samples was observed for the PdZn/TiO2–ZSM-5(80 and 50) hybrid catalysts with a corresponding release of CO2, which could be assigned to coke deposits with high oxygen content as reported for CH3OH conversion to olefins over ZSM-5.69 No additional mass loss at higher temperature, which would be assigned to coke deposits with low oxygen and hydrogen content (e.g. aromatics), was detected.69 No coke deposition was detected for PdZn/TiO2–ZSM-5(23). This should not be interpreted as ZSM-5(23) being less sensitive to coke deposition, since a higher concentration of acid sites generally leads to faster deactivation,70 but instead the initial rate of coke formation might be slower in this system. This might be attributed to the presence of H2O and H2 in the feed35–37 as well as the low concentration of CH3OH throughout the catalyst bed.69
Conclusions
The combination of a PdZn/TiO2 methanol synthesis catalyst with solid acid ZSM-5 zeolites in the form of a hybrid catalyst allowed for consecutive CO2 hydrogenation to CH3OH, CH3OH dehydration to DME, and MTH/DMTH in a one-pass single bed reactor. Thus, the total CH3OH productivity from CO2 hydrogenation over PdZn/TiO2–ZSM-5 hybrid catalysts was higher compared to PdZn/TiO2. The synthesised light olefins undergo further hydrogenation to the corresponding alkanes (ethane, propane and butane) as also reported for Cu-based catalysts, which limit hydrocarbon chain growth. Hence, future research using PdZn alloys for the synthesis of hydrocarbons via the methanol route should focus on limiting the activity towards olefin hydrogenation whilst maintaining good selectivity for CH3OH. Increasing the concentration of aluminium sites in ZSM-5, correlated with mild Brønsted acid sites, resulted in the production of higher hydrocarbons. The bulk stability of the PdZn/TiO2 catalyst up to 360 °C under the reaction conditions (20 bar, CO2/H2/N2 = 1
:
3
:
1, 30 ml min−1, 36 h) was confirmed by XAS and XRD. However XPS suggests that some surface PdZn separation into Pd and ZnO occurred during the reaction.
Dataset available
Data information can be found at http://doi.org/10.17035/d.2021.0129194354.
Conflicts of interest
There are no conflicts to declare.
Acknowledgements
The authors would like to acknowledge the UK Catalysis Hub and the EPSRC for funding (EP/N010531/1) the presented research. We would like to thank Dr Greg Shaw for helping us with TGA-MS measurements.
References
- J. Rockström, W. Steffen, K. Noone, Å. Persson, F. S. Chapin III, E. F. Lambin, T. M. Lenton, M. Scheffer, C. Folke, H. J. Schellnhuber, B. Nykvist, C. A. de Wit, T. Hughes, S. van der Leeuw, H. Rodhe, S. Sörlin, P. K. Snyder, R. Costanza, U. Svedin, M. Falkenmark, L. Karlberg, R. W. Corell, V. J. Fabry, J. Hansen, B. Walker, D. Liverman, K. Richardson, P. Crutzen and J. A. Foley, A Safe Operating Space for Humanity, Nature, 2009, 461, 472 Search PubMed.
-
J. Twidel, Renewable Energy Sources, Routledge, 2015 Search PubMed.
- R. Schlögl, The Role of Chemistry in the Energy Challenge, ChemSusChem, 2010, 3(2), 209–222 Search PubMed.
- M. Carmo, D. L. Fritz, J. Mergel and D. Stolten, A Comprehensive Review on PEM Water Electrolysis, Int. J. Hydrogen Energy, 2013, 38(12), 4901–4934 Search PubMed.
- P. C. Ghosh, B. Emonts, H. Janßen, J. Mergel and D. Stolten, Ten Years of Operational Experience with a Hydrogen-Based Renewable Energy Supply System, Sol. Energy, 2003, 75(6), 469–478 Search PubMed.
- A. Ursua, L. M. Gandia and P. Sanchis, Hydrogen Production From Water Electrolysis: Current Status and Future Trends, Proc. IEEE, 2012, 100(2), 410–426 Search PubMed.
-
DECHEMA Technology Roadmap, Energy and GHG Reductions in the Chemical Industry via Catalytic Processes, International Energy Agency, 2018 Search PubMed.
- M. Bowker, Methanol Synthesis from CO2 Hydrogenation, ChemCatChem, 2019, 11, 4238–4246 Search PubMed.
- E. V. Kondratenko, G. Mul, J. Baltrusaitis, G. O. Larrazábal and J. Pérez-Ramírez, Status and Perspectives of CO2 Conversion into Fuels and Chemicals by Catalytic, Photocatalytic and Electrocatalytic Processes, Energy Environ. Sci., 2013, 6(11), 3112–3135 Search PubMed.
- S. G. Jadhav, P. D. Vaidya, B. M. Bhanage and J. B. Joshi, Catalytic Carbon Dioxide Hydrogenation to Methanol: A Review of Recent Studies, Chem. Eng. Res. Des., 2014, 92(11), 2557–2567 Search PubMed.
- H. Yang, C. Zhang, P. Gao, H. Wang, X. Li, L. Zhong, W. Wei and Y. Sun, A Review of the Catalytic Hydrogenation of Carbon Dioxide into Value-Added Hydrocarbons, Catal. Sci. Technol., 2017, 7(20), 4580–4598 Search PubMed.
- J. Ma, N. Sun, X. Zhang, N. Zhao, F. Xiao, W. Wei and Y. Sun, A Short Review of Catalysis for CO2 Conversion, Catal. Today, 2009, 148(3–4), 221–231 Search PubMed.
- M. B. Fichtl, D. Schlereth, N. Jacobsen, I. Kasatkin, J. Schumann, M. Behrens, R. Schlögl and O. Hinrichsen, Kinetics of Deactivation on Cu/ZnO/Al2O3 Methanol Synthesis Catalysts, Appl. Catal., A, 2015, 502, 262–270 Search PubMed.
- J. Ereña, I. Sierra, M. Olazar, A. G. Gayubo and A. T. Aguayo, Deactivation of a CuO–ZnO–Al2O3/γ-Al2O3 Catalyst in the Synthesis of Dimethyl Ether, Ind. Eng. Chem. Res., 2008, 47(7), 2238–2247 Search PubMed.
- T. Conant, A. M. Karim, V. Lebarbier, Y. Wang, F. Girgsdies, R. Schlögl and A. Datye, Stability of Bimetallic Pd–Zn Catalysts for the Steam Reforming of Methanol, J. Catal., 2008, 257(1), 64–70 Search PubMed.
- C.-H. Kim, J. S. Lee and D. L. Trimm, The Preparation and Characterisation of Pd–ZnO Catalysts for Methanol Synthesis, Top. Catal., 2003, 22(3), 319–324 Search PubMed.
- L. Fan and K. Fujimoto, Promotive SMSI Effect for Hydrogenation of Carbon Dioxide to Methanol on a Pd/CeO2 Catalyst, J. Catal., 1994, 150(1), 217–220 Search PubMed.
- A. S. Malik, S. F. Zaman, A. A. Al-Zahrani, M. A. Daous, H. Driss and L. A. Petrov, Development of Highly Selective PdZn/CeO2 and Ca-Doped PdZn/CeO2 Catalysts for Methanol Synthesis from CO2 Hydrogenation, Appl. Catal., A, 2018, 560, 42–53 Search PubMed.
- J. Xu, X. Su, X. Liu, X. Pan, G. Pei, Y. Huang, X. Wang, T. Zhang and H. Geng, Methanol Synthesis from CO2 and H2 over Pd/ZnO/Al2O3: Catalyst Structure Dependence of Methanol Selectivity, Appl. Catal., A, 2016, 514, 51–59 Search PubMed.
- N. Iwasa, H. Suzuki, M. Terashita, M. Arai and N. Takezawa, Methanol Synthesis from CO2 Under Atmospheric Pressure over Supported Pd Catalysts, Catal. Lett., 2004, 96(1), 75–78 Search PubMed.
- H. Bahruji, M. Bowker, G. Hutchings, N. Dimitratos, P. Wells, E. Gibson, W. Jones, C. Brookes, D. Morgan and G. Lalev, Pd/ZnO Catalysts for Direct CO2 Hydrogenation to Methanol, J. Catal., 2016, 343, 133–146 Search PubMed.
- J. Díez-Ramírez, P. Sánchez, A. Rodríguez-Gómez, J. L. Valverde and F. Dorado, Carbon Nanofiber-Based Palladium/Zinc Catalysts for the Hydrogenation of Carbon Dioxide to Methanol at Atmospheric Pressure, Ind. Eng. Chem. Res., 2016, 55(12), 3556–3567 Search PubMed.
- J. Díez-Ramírez, F. Dorado, A. R. de la Osa, J. L. Valverde and P. Sánchez, Hydrogenation of CO2 to Methanol at Atmospheric Pressure over Cu/ZnO Catalysts: Influence of the Calcination, Reduction, and Metal Loading, Ind. Eng. Chem. Res., 2017, 56(8), 1979–1987 Search PubMed.
- X.-L. Liang, X. Dong, G.-D. Lin and H.-B. Zhang, Carbon Nanotube-Supported Pd–ZnO Catalyst for Hydrogenation of CO2 to Methanol, Appl. Catal., B, 2009, 88(3–4), 315–322 Search PubMed.
- H. Bahruji, M. Bowker, W. Jones, J. Hayward, J. Ruiz Esquius, D. J. Morgan and G. J. Hutchings, PdZn Catalysts for CO2 Hydrogenation to Methanol Using Chemical Vapour Impregnation (CVI), Faraday Discuss., 2017, 197, 309–324 Search PubMed.
- H. Bahruji, J. R. Esquius, M. Bowker, G. Hutchings, R. D. Armstrong and W. Jones, Solvent Free Synthesis of PdZn/TiO2 Catalysts for the Hydrogenation of CO2 to Methanol, Top. Catal., 2018, 61(3), 144–153 Search PubMed.
- H. Bahruji, R. D. Armstrong, J. R. Esquius, W. Jones, M. Bowker and G. J. Hutchings, Hydrogenation of CO2 to Dimethyl Ether over Brønsted Acidic PdZn Catalysts, Ind. Eng. Chem. Res., 2018, 57(20), 6821–6829 Search PubMed.
- A. Álvarez, A. Bansode, A. Urakawa, A. V. Bavykina, T. A. Wezendonk, M. Makkee, J. Gascon and F. Kapteijn, Challenges in the Greener Production of Formates/Formic Acid, Methanol, and DME by Heterogeneously Catalyzed CO2 Hydrogenation Processes, Chem. Rev., 2017, 117(14), 9804–9838 Search PubMed.
- G. Bonura, M. Cordaro, L. Spadaro, C. Cannilla, F. Arena and F. Frusteri, Hybrid Cu–ZnO–ZrO2/H-ZSM5 System for the Direct Synthesis of DME by CO2 Hydrogenation, Appl. Catal., B, 2013, 140–141, 16–24 Search PubMed.
-
S.-K. Ihm, S.-W. Baek, Y.-K. Park and J.-K. Jeon, CO2 Hydrogenation over Copper-Based Hybrid Catalysts for the Synthesis of Oxygenates, in Utilization of Greenhouse Gases;ACS
Symposium Series, American Chemical Society, 2003, vol. 852, pp. 183–194 Search PubMed.
- M. Xu, J. H. Lunsford, D. W. Goodman and A. Bhattacharyya, Synthesis of Dimethyl Ether (DME) from Methanol over Solid-Acid Catalysts, Appl. Catal., A, 1997, 149(2), 289–301 Search PubMed.
- P. Tian, Y. Wei, M. Ye and Z. Liu, Methanol to Olefins (MTO): From Fundamentals to Commercialization, ACS Catal., 2015, 5(3), 1922–1938 Search PubMed.
- C. D. Chang, C. T.-W. Chu and R. F. Socha, Methanol Conversion to Olefins over ZSM-5: I. Effect of Temperature and Zeolite SiO2Al2O3, J. Catal., 1984, 86(2), 289–296 Search PubMed.
- M. Stöcker, Methanol-to-Hydrocarbons: Catalytic Materials and Their Behavior, Microporous Mesoporous Mater., 1999, 29(1–2), 3–48 Search PubMed.
- S. S. Arora, Z. Shi and A. Bhan, Mechanistic Basis for Effects of High-Pressure H2 Cofeeds on Methanol-to-Hydrocarbons Catalysis over Zeolites, ACS Catal., 2019, 9(7), 6407–6414 Search PubMed.
- S. S. Arora, D. L. S. Nieskens, A. Malek and A. Bhan, Lifetime Improvement in Methanol-to-Olefins Catalysis over Chabazite Materials by High-Pressure H2 Co-Feeds, Nat. Catal., 2018, 1(9), 666–672 Search PubMed.
- X. Wu and R. G. Anthony, Effect of Feed Composition on Methanol Conversion to Light Olefins over SAPO-34, Appl. Catal., A, 2001, 218(1–2), 241–250 Search PubMed.
- C. Ahoba-Sam, E. Borfecchia, A. Lazzarini, A. Bugaev, A. A. Isah, M. Taoufik, S. Bordiga and U. Olsbye, On the Conversion of CO2 to Value Added Products over Composite PdZn and H-ZSM-5 Catalysts: Excess Zn over Pd, a Compromise or a Penalty?, Catal. Sci. Technol., 2020, 10, 4373–4385 Search PubMed.
-
S.-K. Ihm, S.-W. Baek, Y.-K. Park and K.-C. Park, 24-P-26-The Nature of Medium Acidity in [CuO/ZnO/ZrO2]SAPO-34 Hybrid Catalyst for CO2 Hydrogenation: Study of the Interactions between Metal Oxides and Acid Sites in Zeolite, in Studies in Surface Science and Catalysis, ed. A. Galarneau, F. Fajula, F. Di Renzo and J. Vedrine, Elsevier, 2001, vol. 135, p. 277 Search PubMed.
- Z. Li, J. Wang, Y. Qu, H. Liu, C. Tang, S. Miao, Z. Feng, H. An and C. Li, Highly Selective Conversion of Carbon Dioxide to Lower Olefins, ACS Catal., 2017, 7(12), 8544–8548 Search PubMed.
- Y.-K. Park, K.-C. Park and S.-K. Ihm, Hydrocarbon Synthesis through CO2 Hydrogenation over CuZnOZrO2/Zeolite Hybrid Catalysts, Catal. Today, 1998, 44(1–4), 165–173 Search PubMed.
- G. Bonura, M. Migliori, L. Frusteri, C. Cannilla, E. Catizzone, G. Giordano and F. Frusteri, Acidity Control of Zeolite Functionality on Activity and Stability of Hybrid Catalysts during DME Production via CO2 Hydrogenation, J. CO2 Util., 2018, 24, 398–406 Search PubMed.
- I. Miletto, E. Catizzone, G. Bonura, C. Ivaldi, M. Migliori, E. Gianotti, L. Marchese, F. Frusteri and G. Giordano, In Situ FT-IR Characterization of CuZnZr/Ferrierite Hybrid Catalysts for One-Pot CO2-to-DME Conversion, Materials, 2018, 11, 2275–2289 Search PubMed.
- B. Ravel and M. Newville, ATHENA, ARTEMIS, HEPHAESTUS: Data Analysis for X-Ray Absorption Spectroscopy Using IFEFFIT, J. Synchrotron Radiat., 2005, 12(4), 537–541 Search PubMed.
- W.-J. Shen, K.-W. Jun, H.-S. Choi and K.-W. Lee, Thermodynamic Investigation of Methanol and Dimethyl Ether Synthesis from CO2 Hydrogenation, Korean J. Chem. Eng., 2000, 17(2), 210–216 Search PubMed.
- H. Bahruji, M. Bowker, C. Brookes, P. R. Davies and I. Wawata, The Adsorption and Reaction of Alcohols on TiO2 and Pd/TiO2 Catalysts, Appl. Catal., A, 2013, 454, 66–73 Search PubMed.
- J. Ruiz Esquius, H. Bahruji, S. H. Taylor, M. Bowker and G. J. Hutchings, CO2 Hydrogenation to CH3OH over PdZn Catalysts, with Reduced CH4 Production, ChemCatChem, 2020, 12, 6024–6032 Search PubMed.
- I. Yarulina, K. De Wispelaere, S. Bailleul, J. Goetze, M. Radersma, E. Abou-Hamad, I. Vollmer, M. Goesten, B. Mezari, E. J. M. Hensen, J. S. Martínez-Espín, M. Morten, S. Mitchell, J. Perez-Ramirez, U. Olsbye, B. M. Weckhuysen, V. Van Speybroeck, F. Kapteijn and J. Gascon, Structure–Performance Descriptors and the Role of Lewis Acidity in the Methanol-to-Propylene Process, Nat. Chem., 2018, 10(8), 804–812 Search PubMed.
- M. Fujiwara, R. Kieffer, H. Ando and Y. Souma, Development of Composite Catalysts Made of Cu-Zn-Cr Oxide/Zeolite for the Hydrogenation of Carbon Dioxide, Appl. Catal., A, 1995, 121(1), 113–124 Search PubMed.
- M. Fujiwara, H. Ando, M. Tanaka and Y. Souma, Hydrogenation of Carbon Dioxide over Cu-Zn-Chromate/Zeolite Composite Catalyst: The Effects of Reaction Behavior of Alkenes on Hydrocarbon Synthesis, Appl. Catal., A, 1995, 130(1), 105–116 Search PubMed.
-
Y. Tan, M. Fujiwara, H. Ando, Q. Xu and Y. Souma, Selective Formation of Iso-Butane from Carbon Dioxide and Hydrogen over Composite Catalysts, in Studies in Surface Science and Catalysis, ed. T. Inui, M. Anpo, K. Izui, S. Yanagida and T. Yamaguchi, Elsevier, 1998, vol. 114, pp. 435–438 Search PubMed.
- R. A. Dagle, A. Platon, D. R. Palo, A. K. Datye, J. M. Vohs and Y. Wang, PdZnAl Catalysts for the Reactions of Water-Gas-Shift, Methanol Steam Reforming, and Reverse-Water-Gas-Shift, Appl. Catal., A, 2008, 342(1–2), 63–68 Search PubMed.
- K. Föttinger, J. A. van Bokhoven, M. Nachtegaal and G. Rupprechter, Dynamic Structure of a Working Methanol Steam Reforming Catalyst: In Situ Quick-EXAFS on Pd/ZnO Nanoparticles, J. Phys. Chem. Lett., 2011, 2(5), 428–433 Search PubMed.
- N. Iwasa, S. Masuda, N. Ogawa and N. Takezawa, Steam Reforming of Methanol over Pd/ZnO: Effect of the Formation of PdZn Alloys upon the Reaction, Appl. Catal., A, 1995, 125(1), 145–157 Search PubMed.
-
T. B. Massalski, Binary Alloy Phase Diagrams, ASM International, Ohio, USA 1996 Search PubMed.
- J. Vizdal, A. Kroupa, J. Popovic and A. Zemanova, The Experimental and Theoretical Study of Phase Equilibria in the Pd–Zn (-Sn) System, Adv. Eng. Mater., 2006, 8(3), 164–176 Search PubMed.
- S. Penner, B. Jenewein, H. Gabasch, B. Klötzer, D. Wang, A. Knop-Gericke, R. Schlögl and K. Hayek, Growth and Structural Stability of Well-Ordered PdZn Alloy Nanoparticles, J. Catal., 2006, 241(1), 14–19 Search PubMed.
- Z.-X. Chen, K. M. Neyman and N. Rösch, Theoretical Study of Segregation of Zn and Pd in Pd–Zn Alloys, Surf. Sci., 2004, 548(1–3), 291–300 Search PubMed.
- Z.-X. Chen, K. M. Neyman, A. B. Gordienko and N. Rösch, Surface Structure and Stability of PdZn and PtZn Alloys: Density-Functional Slab Model Studies, Phys. Rev. B, 2003, 68(7), 075417 Search PubMed.
- D. Cheng, K. Okumura, Y. Xie and C. Liu, Stability Test and EXAFS Characterization of Plasma Prepared Pd/HZSM-5 Catalyst for Methane Combustion, Appl. Surf. Sci., 2007, 254(5), 1506–1510 Search PubMed.
-
https://xpssimplified.com/
.
- M. Brun, A. Berthet and J. C. Bertolini, XPS, AES and Auger Parameter of Pd and PdO, J. Electron Spectrosc. Relat. Phenom., 1999, 104(1–3), 55–60 Search PubMed.
- Y. Zhang, Y. Cai, Y. Guo, H. Wang, L. Wang, Y. Lou, Y. Guo, G. Lu and Y. Wang, The Effects of the Pd Chemical State on the Activity of Pd/Al2O3 Catalystsin CO Oxidation, Catal. Sci. Technol., 2014, 4(11), 3973–3980 Search PubMed.
- P. Kast, M. Friedrich, F. Girgsdies, J. Kröhnert, D. Teschner, T. Lunkenbein, M. Behrens and R. Schlögl, Strong Metal–Support Interaction and Alloying in Pd/ZnO Catalysts for CO Oxidation, Catal. Today, 2016, 260, 21–31 Search PubMed.
- K. M. Eblagon, P. H. Concepción, H. Silva and A. Mendes, Ultraselective Low Temperature Steam Reforming of Methanol over PdZn/ZnO Catalysts—Influence of Induced Support Defects on Catalytic Performance, Appl. Catal., B, 2014, 154–155, 316–328 Search PubMed.
- M. Friedrich, D. Teschner, A. Knop-Gericke and M. Armbrüster, Influence of Bulk Composition of the Intermetallic Compound ZnPd on Surface Composition and Methanol Steam Reforming Properties, J. Catal., 2012, 285(1), 41–47 Search PubMed.
- G. Deroubaix and P. Marcus, X-Ray Photoelectron Spectroscopy Analysis of Copper and Zinc Oxides and Sulphides, Surf. Interface Anal., 1992, 18(1), 39–46 Search PubMed.
- T. V. W. A. Janssens, New Approach to the Modeling of Deactivation in the Conversion of Methanol on Zeolite Catalysts, J. Catal., 2009, 264(2), 130–137 Search PubMed.
- S. Müller, Y. Liu, M. Vishnuvarthan, X. Sun, A. C. van Veen, G. L. Haller, M. Sanchez-Sanchez and J. A. Lercher, Coke Formation and Deactivation Pathways on H-ZSM-5 in the Conversion of Methanol to Olefins, J. Catal., 2015, 325, 48–59 Search PubMed.
- I. Yarulina, A. D. Chowdhury, F. Meirer, B. M. Weckhuysen and J. Gascon, Recent Trends and Fundamental Insights in the Methanol-to-Hydrocarbons Process, Nat. Catal., 2018, 1(6), 398–411 Search PubMed.
Footnote |
† Electronic supplementary information (ESI) available: XRD, pore size and surface area for commercial ZSM-5 after activation (550 °C, 6 h). CO2 reaction metrics. CO2 hydrogenation activity over PdZn/TiO2 at different temperatures, CO2 hydrogenation over ZSM-5 (23 : 1). Productivities and hydrocarbon selectivity based on MTH/DMTH over PdZn/TiO2–ZSM-5 hybrid catalysts. EXAFS fitting parameters. XRD and XPS post reaction PdZn/TiO2 characterisation. Coke determination by TG-MS. See DOI: 10.1039/d0fd00135j |
|
This journal is © The Royal Society of Chemistry 2021 |
Click here to see how this site uses Cookies. View our privacy policy here.