DOI:
10.1039/D1EE00691F
(Review Article)
Energy Environ. Sci., 2021,
14, 6099-6121
Environmental impacts, pollution sources and pathways of spent lithium-ion batteries
Received
5th March 2021
, Accepted 12th October 2021
First published on 13th October 2021
Abstract
There is a growing demand for lithium-ion batteries (LIBs) for electric transportation and to support the application of renewable energies by auxiliary energy storage systems. This surge in demand requires a concomitant increase in production and, down the line, leads to large numbers of spent LIBs. The ever-increasing battery waste needs to be managed accordingly. Currently, there are no universal or unified standards for waste disposal of LIBs around the globe. Each country uses one or a combination of practices such as landfilling, incineration and full or partial recycling depending on the number of batteries leaving the market, current legislation and infrastructures. Informal disposal or reprocessing is not a rare activity. This review records, identifies and categorises the environmental impacts, sources and pollution pathways of spent LIBs. The drawbacks of the disposal practices are highlighted and the threats associated with them are discussed. The evidence presented here is taken from real-life incidents and it shows that improper or careless processing and disposal of spent batteries leads to contamination of the soil, water and air. The toxicity of the battery material is a direct threat to organisms on various trophic levels as well as direct threats to human health. Identified pollution pathways are via leaching, disintegration and degradation of the batteries, however violent incidents such as fires and explosions are also significant. Finally, the paper discusses some of the main knowledge gaps for future assessments. The current study offers a comprehensive overview of the threats and hazards that need to be managed in order to ensure the design and implementation of safe disposal and processing options for spent LIBs.
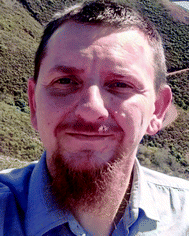
Wojciech Mrozik
| Wojciech Mrozik is a Faraday Institution Research Fellow at Newcastle University, UK. He is part of the “SafeBatt – Science of Battery Safety” and previously “Reuse and Recycling of lithium-ion Batteries” projects funded by Faraday Institution. He is an expert in environmental and analytical chemistry with a particular interest in environmental fate assessment and removal of anthropogenic pollutants. Last few years Wojciech's research focused on the safe application, operation and utilization of lithium-ion batteries. That concerns understanding of battery thermal runaway, fire prevention and mitigation. |
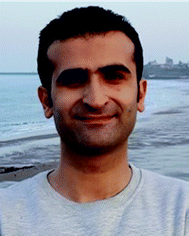
Mohammad Ali Rajaeifar
| Mohammad Ali Rajaeifar is currently a research associate at Newcastle University. He studies technologies and management strategies and provides sustainability analysis of different production systems. He started his MSc in the area of sustainable agriculture and biofuel production in 2013. Then he extended his research to sustainability assessment of biorefineries, low carbon transport systems and waste management systems during his PhD and post-doctoral studies. More recently, he has developed his research area by focusing on the sustainability of EVs and lithium–ion batteries. Mohammad is also an expert in data collection and analysis, compiling data inventories, and assessing the environmental impacts of complicated industrial systems. |
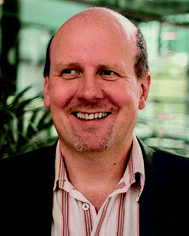
Oliver Heidrich
| Since 1992 Oliver has worked with national and international companies, local authorities and Universities in waste, recycling, environmental, life cycle assessment, stakeholder and corporate management. He was a director of Econoplas, a plastic manufacturing business and SEQM a business consultancy business. He provides detailed understanding of the inter-relationships between resource use and their spatial distribution within and outside cities, in relation to climate change, the built environment, and associated resource requirements. Besides his many expert reports and research papers, Oliver is concerned to see the results of his research disseminated through the wider press and digital media. |
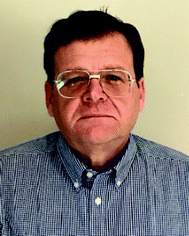
Paul Christensen
| Senior Advisor to the UK National Fire Chiefs Council, member of UK Department of Business, Energy and Industrial Strategy Energy (BEIS) Storage Health and Safety Governance, and BEIS Storage safety – Fire Service Working groups. Working with Fire and Rescue Services across the UK, New Zealand and Australia. Commissioned by UK Office for Product and Safety Standards & BEIS to research the Safety of Second Life Batteries in Domestic Battery Energy Storage Systems. Over 180 papers in international, peer-reviewed journals, H-index of 53. Editorial Board member, Nature Special Reports. |
Broader context
Lithium-ion batteries (LIBs) are permeating ever deeper into our lives – from portable devices and electric cars to grid-scale battery energy storage systems, which raises concerns over the safety and risk associated with their disposal. Spent LIBs are currently landfilled, incinerated, partially/fully recycled, or a combination of these, depending on the existing infrastructure, legislation etc. of the country concerned. Spent LIBs are considered hazardous wastes (especially those from EVs) due to the potential environmental and human health risks. This study provides an up-to-date overview of the environmental impacts and hazards of spent batteries. It categorises the environmental impacts, sources and pollution pathways of spent LIBs. Identified hazards include fire and explosion, toxic gas release (e.g. HF and HCN), leaching of toxic metal nanooxides and the formation of dangerous degradation products from the electrolyte. Ultimately, pollutants can contaminate the soil, water and air and pose a threat to human life and health. In this work, we discuss some of the main knowledge gaps and probe questions on the environmental impacts of spent LIBs that might help to manage these better in the future to design and implement safe disposal and processing options for spent LIBs.
|
1. Introduction
Lithium-ion batteries (LIBs) are found in all aspects of our lives – from small portable electronic devices through electric vehicles (EVs) to battery energy storage systems (BESS). LIBs are perceived as crucial to support the wide adoption of renewable energy sources as these do require BESS to manage the intermittency in their power supply for a reliable operation of the electricity grid. The application of LIBs in electric traction has initiated a revolution in the automotive industry that is motivated to decarbonise the transport sector and reduce local air pollution. In 2009, there were nearly 25.6 GW h (about 134
000 tons) of LIB energy storage capacity placed on the global market, in 2019 it was about 218 GW h (over 1.2 million tons), and it has been estimated that in 2030 more than 2500 GW h (over 12.7 million tons) will be placed on the market, which subsequently results in a vast amount of waste from the spent LIBs.1
Various international and domestic initiatives like the European Green Deal in the EU,2 the UK Government pledge to ban new ICE cars by 2030 (hybrids by 2035)3 or the need to establish zero-emission mobility as an urgent priority,4 require a very large increase in the production of new LIBs. Moreover, transitioning to a low carbon economy5 requires building new, more powerful BESS all around the world. These installations will be used as storage of intermittent solar, wind, or wave electricity, grid support, frequency stabilisation and behind-the-meter-storage, replacing conventional technologies. On one hand, the increased number of LIBs has created concerns over the availability of some critical metals, and their wild short-term price volatility which could affect the sustainable supply of such energy storage devices.6 There are also some ethical and environmental concerns with the extraction of some metals for LIBs.7 On the other hand, this surge in demand for batteries will require a concomitant increase in production and, down the line, large numbers of LIBs reaching end-of-life (EoL). Hence, that will cause an ever-increasing battery waste that needs to be managed accordingly.8 However, many types of batteries currently do end up in landfills or are incinerated, primarily due to the lack of adequate standards; enforcement of regulatory controls, inefficient, or absence of, national battery collection and recycling schemes.9 As a result, human health and environmental quality could be placed at risk as a wide range of pollutants could be released like heavy metals or hydrofluoric acid (HF) when batteries are disposed of inappropriately.
The main aim of this study is to provide an up-to-date overview of the environmental impact and hazards of spent batteries. This paper reports and discusses the fate, disposal routes and potential pollution sources and pathways from spent LIBs. Despite the clear importance of this area, the data on the environmental impact of EoL LIBs is extremely limited, thus, this study identifies the possible environmental impacts associated with battery EoL. There is an urgent need from manufacturers, waste handling companies, recycling firms and public stakeholders to understand this matter as wrong disposal practices, lack of data or improper identification of hazards will drastically increase the number of incidents, fires and potentially fatal accidents. The possible emission routes and pollution pathways e.g. air, water and land, are also evaluated through the course of this study. We have also recognised possible hazards to human health and ecosystem quality due to different battery treatment and disposal practices. Finally, the knowledge gaps are identified that need to be covered if the right disposal practices and management systems are to be implemented.
2. Disposal of spent batteries
The management of spent LIBs incorporates reuse, recycling, landfilling, processing or (unfortunately) illegal disposal (Fig. 1). The local disposal routes depend on national legislation and regulations, recycling capacities, collection systems, consumer behaviours and the battery retail markets.10 Clearly, different approaches are required for small batteries compared to large ones.
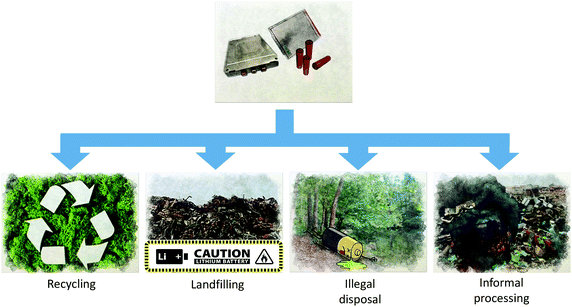 |
| Fig. 1 Disposal routes of LIBs. | |
Small LIBs are returned by the customer either through battery drop-off points (LIBs that can be easily detached from the device) or given to waste electrical and electronic equipment sites (WEEEs) if the user cannot remove them from the electrical device. From these collection points, they are transported to sorting facilities and later to be recycled or landfilled. Through ignorance of the collection system or idleness, small spent LIBs may be put into general waste or into recycle bins by customers, which led to damaging fires during transportation or in material recovery facilities (MRFs). Veolia, one of the global waste handling companies, has noted a 38% increase of incidents since 2017,11 due to the presence of the LIBs in the waste stream. At MRFs, LIBs will be crushed or penetrated during the standard processing, which can also lead to fires or even explosions. The Environmental Services Association estimates that12 there were ca. 250 fires in the UK waste treatment facilities caused by small LIBs between April 2019 and March 2020, compared to ca. 130 in the year to March 2020, a rise of 25% of all fires in these facilities.13,14 The German steel recyclers confederation (BDSV) has claimed that 90% of fires at their associated sites in the last years were caused by LIBs.15 Some specific examples of such fires are the incident at the Great Blakenham scrapyard, UK (15th Sep 2017) where 100 tonnes of metal and a crane were caught up in fire;16 multiple incidents at Tokyo's Musashino Clean Center garbage disposal facility, Japan, in 2017 and 2018;17 and some other regular incidents in the UK, USA, Scotland, and Germany.18
Large LIBs are typically transported by professional services once removed from EVs,19 however, their health status is usually unknown. If internally damaged, they are in slow thermal runaway and hence remain unnoticed for a long time, after which they may either burst into flames or they release gases and droplets of solvent, the “white vapour”, composed of toxic and explosive gases.7,20–24 These events may take place during transportation, storage, recycling or landfilling.
2.1 Recycling
2.1.1 Low recovery rates.
Material recovery from the EoL batteries is the preferred option over the other disposal routes10,25,26 since LIBs are now considered a strategically valuable waste stream containing relatively valuable metals such as cobalt, nickel or lithium.27,28 These are of significant value, especially in light of the shrinking global supply of critical materials.29–32 Material recovery is also the way to be less dependent on raw mining elsewhere or to protect the country's own small reserves. For instance, the lithium demand for LIBs produced in China by 2050 could meet up 60% by recycling.33 Currently, China is the largest consumer and producer of LIBs and recycling of spent LIBs has only started recently.34 Although some 14 pieces of legislation try to manage the emission pathways of all types of batteries waste, effective regulation of controlling spent LIB is still in its infancy.34 In the USA the management and regulation of LIBs is also fragmented, due to its Federal States, with some federal policies guiding battery disposal, specifically the 1996 Mercury-Containing and Rechargeable Battery Management Act to manage certifications and standards of batteries.35 However, overall, it is patchwork of state by state regulations with different levels of maturity and control.36 In the EU, new legislation is coming into force in 2022 to manage and control the raw material sourcing, disposal and recycling of LIBs.1
Clearly, material recovery should avert the environmental burden from ore mining and beneficiation of metals used in LIBs by replacing the recycled ones in the production chain,37 and could also avoid the environmental burdens from the other harmful disposal routes. In 2018, it is estimated that 97
000 tonnes of LIBs were recycled globally,19 including LIBs from portable electronics as well as LIBs from EVs and BESS applications. Small LIBs currently dominate recycling (i.e. more than 80% of the recycled batteries) as the number of batteries reaching actual EoL from EVs is relatively low.38 This is due to the relatively nascent application of LIBs in EVs, and the fact that when EV LIBs have reached EoL they still have potential use in other applications, such as supporting the Grid or renewable energy generation, as they typically retain up to 80% of their original capacity.39 Thus, LIBs from EVs may be finally discarded up to 10 years after their first life.40
A closer look at the recovery of LIBs reveals that compared to the amount of LIBs placed on the global market, the actual recovery rates are quite low. For example, the average collection rate in the EU, one of the well-regulated markets, is nearly 40% while only 12% belongs to LIBs.41 The average recovery rates are also lower for some other less-regulated markets such as Australia and the US.29,42 However, there are still few markets that perform better than the EU. More specifically, South Korea and China together showed better recovery rates. Actually, these countries are the destination of most of the exported batteries (either in a separate battery form or as part of electronic devices) from many parts of the world especially Europe and North America. This is also reflected in the total quantity of LIBs recycled: from 97
000 tonnes treated globally in 2018, 67
000 were processed in China and 18
000 in South Korea.19 However, it is estimated that less than 40% of the total battery materials actually can be recycled under the current materials flow scheme.43 For instance, in 2016, only around 30% of nickel, 33% of cobalt, 23% of lithium and 5% of graphite were recovered in China.44 Such poor management resulted in economic loss due to the free discharge of valuable materials, as well as damage to the environment and human health.45,46 Various national and international initiatives have been implemented to tackle this low recovery problem such as the 2006 EU battery directive47 and the proposed new EU regulation which concerns batteries and waste batteries.48 The key challenge, however, is the lack of recycling infrastructure around the world, there are only a few full-scale recycling facilities (Table 1).49,50 Illustration of this problem is the UK situation. Prior to exiting the EU on the 31st December 2020, the regular practice was to ship batteries to mainland Europe for recycling, e.g. to Umicore in Belgium. However, with the restricted access to the EU market and strict regulations treating large LIBs as hazardous materials, the UK, without proper recycling infrastructure, may either have to landfill its batteries51 or temporarily store them in dedicated facilities until suitable facilities are built or until an appropriate trade deal with the EU is agreed.
Table 1 Current recycling facilities around the world adopted from ref. 49 and 50
Company name |
Location |
Processa |
Capacity (tonne of battery per year) |
P – pyrometallurgy, H – hydrometallurgy, M – physical separation.
|
Accurec Recycling |
Germany |
P, M |
4000 |
Akkuser |
Finland |
M |
1000 |
Aubermacher Redux |
Germany |
M |
1000 |
Bangpu Ni\\& Co High Tech |
China |
H |
3600 |
Batrec |
Switzerland, Wimmis |
P |
200 |
Dowa Eco-System Co. Ltd |
Japan |
P, H |
1000 |
Duesenfeld |
Germany |
M |
3000 |
Envirostream |
Australia |
P |
3000 |
Euro Dieuze |
France |
M, H |
6000 |
GEM |
China |
H |
100 000 |
Glencore |
USA, Canada, Norway |
P |
7000 (Norway) |
High Power International |
China |
P, H |
10 000 |
Huayou Cobalt |
China |
H |
60 000 |
Hunan Brunp Recycling Tech |
China |
H |
30 000 |
Inmetco |
USA |
P |
6000 |
Jiangxi Ganfeng Lithium |
China |
H |
5000 |
JX Nippon Mining & Metals Corp |
Japan, Tsuraga |
P, H |
600 |
KOBAR |
South Korea |
H |
1000 |
LiCycle |
Canada |
H |
2500 |
Nickelhütte Aue |
Germany |
P, H |
1000 |
Nippon Recycle Center Corp |
Japan |
P |
2000 |
Recupyl |
France/Singapore |
H |
110/1200 |
SNAM |
France |
P, M, H |
1500 |
SungEel Hitech |
South Korea |
H |
8000 |
Sungeel Hi-tech |
Hungary |
M, H in South Korea |
3000 |
Taisen Recycling |
China & South Korea |
H |
6000 |
Tele Recycle |
China |
H |
2000 |
TES (Recupyl) |
France |
M, H in Singapore |
1000 |
Umicore |
Belgium |
P, H |
7000 |
Ute Vilomara |
Spain |
H |
>53.32 |
Both landfilling and stockpiling will have a potentially negative effect on the surrounding environment as they can release pollutants, contaminants and cause accidental fires, which are discussed below.
2.1.2 Recycling methods.
Material recovery from the EoL LIBs is currently carried out by one of three major processes: pyrometallurgy, hydrometallurgy, and direct recycling.25,40 Pyrometallurgy employs smelting in a high-temperature process, which usually involves burning and subsequent separation to produce a mixed metal alloy of Co, Cu, Fe and Ni.52 That is an established technology commonly applied to small and large LIBs, especially to cobalt-rich batteries. Usually this method does not require pre-sorting of battery types, however, the resulting alloy requires further processing. Hydrometallurgy recovers the desired metals from cathode material via leaching in an acidic or basic aqueous solution. Additional steps such as subsequent concentration and purification are later required. This process allows the recovery of almost all LIBs components with high purity.53 However, the separation of the metals from each other requires additional purification steps: in addition, unlike pyrometallurgy, sorting is required. Finally, direct recycling involves the direct re-use of the cathode and/or anode material from the electrodes of spent LIBs after reconditioning. Although promising in principle, as it allows the simple recovery and re-use (without further processing) of most of the battery constituents,25,54,55 it is still not fully matured as a technology. There are also alternative technologies under investigation such as plasma smelting technology,37 bioleaching,56 redox targeting-based material recycling,57etc.
Each of the listed technologies has its own limitations in recovering LIB's materials. Therefore, the final process should involve a combination of various techniques with a well-defined material flow chart to assure the highest efficiency of recycling.58 The enormous research and development effort should tackle this issue, however, the gradual but constant change in battery chemistry will require the facilities to shift their operational mode in just a few years. Is the process safe to operate with new chemistry? Are there any hazardous by- and end-products that need to be treated accordingly? These and other questions must be answered to ensure the safety of the workers and mitigate the environmental impact of the process.
2.1.3 Pollution specific to recycling and the potential environmental impacts.
Materials recovery is not a pollution-free activity. For example, pyrometallurgy is a highly energy-demanding process, resulting in GHG emissions and the generation of toxic gases or hazardous slag that may need to be landfilled.31 Moreover, the intermittent product, so-called “black mass” (a sludgy mixture of lithium, manganese and cobalt), may also contain other hazardous substances such as alkylfluorophosphates that are a serious health concern.59 Pyrometallurgical recycling process could impose environmental risks in global warming, photochemical ozone creation, carcinogenic and non-carcinogenic effect, ozone layer depletion and eutrophication impact categories.18 A recent study on plasma smelting recycling showed that the employed energy source (for the smelter), recycling efficiency, the quality of the recycled materials, aluminium recovery and adopting a battery waste improvement process could significantly affect the overall environmental impacts of pyrometallurgy.37
In contrast, hydrometallurgy produces far less GHG emissions but requires supplementary wastewater treatment to ensure that receiving waters do not suffer additional pollution, e.g. from acids. Hydrometallurgical recycling processes were reported to impose environmental risks on freshwater and terrestrial acidification.18 Mohr et al. (2020) compared the environmental impacts of recycling of different battery chemistries (i.e. NMC, NCA, LFP and solid-state) using a conventional pyrometallurgical, a conventional hydrometallurgical process and an advanced hydrometallurgical process (that recovers graphite and electrolyte).60 The results indicated that the advanced hydrometallurgical processes could perform the best (in terms of global warming impact) due to additional recovery of graphite and electrolyte, while the pyrometallurgical process performs the worst due to high energy consumption and lack of Li recovery. The authors also suggested that a cell chemistry specific approach for recycling should be taken into consideration since some recycling processes could lead to unfavourable impact on the environment when treating some specific chemistries, for example, hydrometallurgical recycling of LFP and sodium-ion batteries (SIB) could add more burden in abiotic resource depletion potential; or pyrometallurgical recycling of LFP cells could increase the global warming impact.
As direct recycling is still in its very early stages of development, there are no real-world data on potential pollution. According to Dunn et al. (2015), using a direct recycling process for NMC, LCO, LFP and LMO batteries could significantly reduce the emissions of GHGs and SOx (from the production of batteries) and thus mitigate global warming and acidification potential of the whole battery life cycle.61 It should be noted that when talking about the environmental impacts of a specific recycling process, the net impact on the environment is usually considered which is calculated by subtracting the released emissions from the avoided emissions (recycling benefits). Thus, a recycling process itself may have a negative impact on the environment in a specific environmental impact category while the credits from the recycled materials (environmental impacts avoided due to returning the recovered material to the market) might compensate those negative impacts and make the net environmental impact favourable. Overall, it should be noted that the environmental impacts of different recycling processes could vary based on the processed cell chemistry, the employed emission reduction technology, recycling efficiency and the quality of the materials recovered.
2.1.4 Comparison to non-lithium ion battery recycling methods.
Finally, there is a lesson to be learnt from the already established recycling processes for other battery types. For example, the processing of lead-acid batteries is of major concern especially in developing, countries62 as, in such locations, recycling is often performed without controlling lead emissions.63 In addition, there is also often a lack of appropriate regulation and the consequent existence of informal and polluting recycling industries. Thus, in the absence of adequate standards and/or lack of enforcement of regulatory controls, the lead recycled from batteries results in significant environmental contamination and human exposure even in established, industrial-scale recycling facilities.64 It has been estimated that over 495
000 deaths and more than 9 million disability-adjusted life years (DALYs) occur as a result of the long-term impact of lead exposure on health. Reports also show that low- and middle-income countries have the highest death rates associated with lead exposure.65 Comparative analysis reveals that current environmental and social influence such as consumption of raw material/metal, energy demand, scrap emissions, recycling or disposal cost; of the lead-acid battery system is greater than that of the LIB system.66 However, it should be highlighted that such studies are performed on retrospective data (i.e. for China in 2016) and do not fully reflect the future with much higher numbers of production and recycling/disposal of LIBs. Therefore, it is essential to assess in detail all the gaps in knowledge and technology, as well as socio-economic issues, and apply these to the future LIB recycling industry. This is important not only for developed countries but even more for emerging economies that usually have lax or weak environmental legislation.67
2.2 Landfill
Landfilling is the main method of disposing of solid waste68 – with the rates of deposition of municipal waste ranging from 53% in the USA,69 79% in China70 to 94% in Malaysia.71 Of these, around 4% includes electronic wastes (e-waste), often containing batteries.72 Given the low global recovery rates, it is clear that most e-wastes containing small LIBs are discarded into the landfill sites rather than recovered.73–76 This is the case not only for many emerging economies but also in developed ones due to (as stated above) lax or weak regulations as well as the lack of recycling infrastructure. Therefore, in the short-term at least, it is certain that LIBs (especially those from small portable devices) will be buried. Currently, due to the relatively small number of EVs, large LIBs are usually recovered.44 However, with the rapid growth in volume and still inadequate infrastructure, even high-powered batteries may be either landfilled or temporarily stored. Yet, in the long-term, it is more likely they will follow the recovery route rather than landfilling, as it would be a waste of a significant resource of valuable materials.67
The landfill itself can be both a sink or source of pollution that can have negative impacts on surrounding communities.68 The main sources of emissions from landfills are surface dust, landfill gases (e.g. biogas), leachate and fires.77,78 The extent of pollution from a site depends upon location, waste composition and age, and geo-climatic conditions.51,79–81 However, in the future it's possible that landfills may be a place of valuable resources for urban mining – the sink of the rare and needed metals that can be extracted without actual mining.
2.2.1 Landfill fires.
Landfill fires are clearly undesirable but unfortunately quite frequent.82–86 There are two types of fire, surface and subsurface (cavity): and in most cases, they are due to the spontaneous auto-ignition of methane.87 Surface fire spreads outside the landfill area but is relatively easy to extinguish. Cavity fires are a form of combustion (pyrolysis) where the thermal reaction takes place under anoxic conditions deep below the landfill surface.77,88 These are difficult to detect and may create large voids in the landfill, which can cause the landfill surface to cave in. Buried LIBs, which may be holding a charge and contain flammable electrolytes, may trigger, amplify and prolong landfill fires.
Landfill fires caused by (usually small) LIBs are a major emerging problem. The Environmental Services Association (ESA), the trade body representing the UK's resource and waste management industry, reported that 25% of total landfill fires (>500) in the UK in the period 2017–18, were attributed to LIBs: a significant 20% increase in comparison to the previous year.89 Examples of such fires include that at the Dunbar landfill site on 22nd January 2019, where around 300 tonnes of waste burst into flames in waste sorting building.90 Fires in pre-landfilling facilities may be illustrated by Shoreway MRF, USA. At least 25 fires at this facility were caused by LIBs between April 2013 and September 2017. The most severe fire, on the 9th September 2017, required over 100 firefighters to extinguish it, and the fire shut the facility for 3 months and cost over $8.5M in restoration.91
Accurate prediction of the ignition potential of LIBs is challenging, as spent batteries will have various compositions, States of Health (SoH) and charge (SoC); besides, it is likely that cells, modules and packs will be dumped and landfilled. In landfills, batteries may be damaged during compacting and hence ignite either immediately or after burial: in the latter case, serious fires could result due to surrounding flammable materials and existing methane in the landfill environment. Even if damaged batteries do not ignite, the pyrolysis that accompanies thermal runaway will generate significant heat and toxic and potentially explosive gases.92 It should be noted that fires caused by batteries may occur months or even years after they were buried.
The hazards of damaged LIBs are in addition to conventional landfill fires, which produce a mixture of toxic gases and smoke77,93 consisting of polycyclic aromatic hydrocarbons (PAHs),94–96 dioxins/furans,97–101 volatile organic compounds (VOCs),102,103 heavy metals104,105 polychlorinated biphenyls or organochlorine pesticides104 and finally, particulate matter (PM) with an aerodynamic diameter smaller than 2.5 μm.106,107 Subsurface fires favour the generation of harmful gases such as CO, SO2 or H2S77 – some of these gases are also generated within burning batteries.7,20–24 Landfill fires do not only affect the air around the site as the smoke can carry particulate matter and chemicals to further distances: for example, it has been shown that there may be a short term rise in the concentrations of heavy metals and Chemical Oxygen Demand (COD) or PAHs86 in water bodies next to burning sites. Therefore, avoiding battery landfilling or at least neutralization/immobilization of hazardous content must be seriously considered. That could be for instance (i) complete discharging-no excess of the energy, immobilization of copper on aluminium foil; (ii) removal of the flammable electrolyte from the battery – reduced fire risk, formation of hazardous gasses and vapour cloud explosion; (iii) using additional liners (bentonite clay etc.) capable of binding heavy metals – no transport through landfill layers.
2.3 Illegal disposal and processing
Wherever there is a potential of making profit there are attempts to bypass official routes of making business. As the recycling of LIBs will be profitable at least to some degree, there is a big chance that some illegal processing will occur, as it happened for waste electronic equipment. Such activity will result in pollution surrounding the processing site, poor working conditions of workers and thus worsening their health and quality of life. Illegal disposal will occur if the recycling or official landfilling will be to “too expensive” for some “business”. The dumpsites will be located in very random places, completely not fit for purpose and that will result in severe pollution, unexpected fires and huge additional costs to local residents/councils – utilization and remediation of the area. Unexpected incidents (e.g. fires) may even occur months after the disposal making the process of finding responsible/guilty person very tricky.
It is certain that LIBs will be illegally recycled and disposed of.67,108 Moreover, the burden of illegal processing will be mostly put on emerging economies due to the high costs of labour, lack of recycling facilities and strict environmental laws in developed countries.6 A good example of this exploitation is the export of e-waste facilitated by rich and developed nations to poor and developing ones.109,110 This is also reflected in the statistics: for instance, two-thirds of global e-waste collected in 2014 were exported, but more importantly, half of it was through illegal routes.111 This resulted in over 3 million tonnes of e-waste exported outside of regulated schemes. Data for 2019 show that 82.6% of global e-waste flows were neither formally collected, properly managed nor documented.72 The EU generates ca. 44.3 Mt of e-waste annually, however only 0.6 Mt is known to reach landfills whilst the rest is dumped, traded, informally exported or recycled in a non-environmentally appropriate way.112 Hence there is no guarantee that exported EoL LIBs will be recycled or processed in regulated, safe and environmentally friendly ways.44
2.3.1 E-Waste problem.
Interestingly, even now with a relatively low number of EoL EVs, it is possible to buy used LIB cells, modules on the popular, online, auction portals. This means that they are sold outside official collection/recycling schemes, even though they have reached their first EoL. With the growing demand from individuals, e.g. for behind-the-meter energy storage, some of the batteries may be illegally sold, especially in countries with weak or no regulations, and the obvious question arises: what happens to such self-made systems when they reach real EoL? Will they be passed to accredited recycling centres or dumped? In addition, what would be the impact of the illegal processing of LIBs on human health and the natural environment? These issues can be illustrated by current informal WEEE operations - often the recycling is carried out without any environmental and health protection, and this results in the contamination of soil, air and water and a serious impact on human health.108,113–121 The findings include the fact that heavy metals (i.e. lead or cadmium) and polycyclic aromatic hydrocarbons in the soils or watercourses surrounding such centres are significantly above national safety limits. Cobalt, copper and nickel are also heavy metals included in LIBs that might cause hazards if LIBs are inappropriately treated. Lead-acid battery informal processing can highlight potential issues for LIBs in the future. For instance, estimates have shown that there could be between 10
000 and 30
000 informal lead-acid battery recyclers in 90 low- and middle-income countries that pose a major threat to up to 16 million people.122 Such sites elevate levels of lead in soils and plants123 and have caused higher concentrations of the metal in children's blood in Serbia,124 Australia,125 China126 and India.127,128 Informal sites rarely control their harmful emissions, are subject to weak or no regulation, and are often located within residential areas.124,129,130
2.4 Incidents involving LIBs
Incidents involving LIBs are mostly focused on fires and the release of toxic gases. In addition to the risk of these hazards to first responders and spectators at, for example, a road traffic accident, there is also the broader spectrum of the environmental impact of such fires. Fig. 2131,132 shows typical emission pathways from a burning LIB to the surroundings. In addition to heat, fire or a toxic and potentially explosive vapour cloud there is also a possibility of air transportation of substances and with time, their deposition in other, distant places. The close surroundings are also affected by the fire debris, transportation of pollutants by fire extinguishing agents and release of remaining contamination from burnt carcasses – depending on the type and place of the disposal.
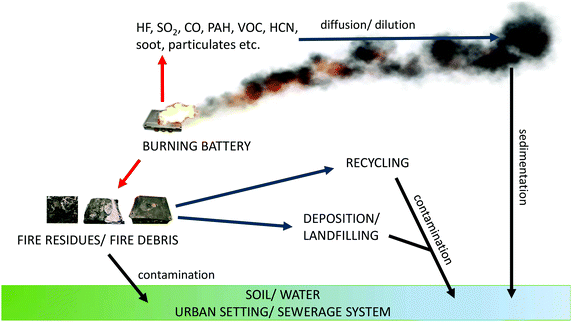 |
| Fig. 2 Emission pathways from fires (adapted from ISO, 2011; Stec et al., 2019). | |
The sometimes explosive failure of LIBs is always due to some form of abuse which can be from heat, penetration, blunt trauma or overcharging, and examples of the results of these can be found in the literature citing examples on the land, sea and in the air.133,134 Spontaneous ignition of LIBs has also been reported, particularly concerning electric vehicles;135 the events leading to this remain essentially unknown, but contamination during production or poor design is often quoted. An increasing and slightly worrying phenomenon is the incidence of fires and explosions in large LIB energy storage systems (LIBESS). The first such incident occurred in Arizona in 2012 in a new 1.5 MW LIBESS owned by Arizona Public Services.136 Several design flaws were identified following the incident including a lack of proper ventilation and inadequate monitoring all of which were supposed to have been addressed137 when a second LIBESS owned by APS exploded in April 2019 injuring four first responders, two of whom badly. The incident is now believed to have been a vapour cloud explosion.138,139 We listed some other examples of LIBESS incidents in Table 2 to illustrate the rising problem.
Table 2 List of some major involving LIBESS and Maritime incidents
Major LIBESS incidents |
Place |
Date |
Comments |
https://www.greentechmedia.com/articles/read/what-we-know-and-dont-know-about-the-fire-at-an-aps-battery-facility.
https://www.fox6now.com/news/damage-may-exceed-3-million-after-lithium-ion-battery-fire-at-sc-electric-in-franklin.
Deign J. In: Media G, editor. Engie investigates source of Belgian battery blaze. Boston, MA, USA: Greentech Media Headquarters; 2017. https://www.greentechmedia.com/articles/read/engie-investigates-source-of-belgian-battery-blaze, (accessed 25th May 2020).
Yoon-seung K. Faulty batteries blamed for ESS fires: panel. South Korea: Yonhap News Agency; 2020.
DNV GL, McMicken Battery Energy Storage System Event Technical Analysis and Recommendations, Arizona Public Service, https://www.aps.com/-/media/APS/APSCOM-PDFs/About/Our-Company/Newsroom/McMickenFinalTechnicalReport.ashx?la=en&hash=50335FB5098D9858BFD276C40FA54FCE, 2020.
Dennien M. Firefighter’ knocked on his back’ in fire blast at Griffith University. Brisbane, Australia: Brisbane Times; 2020.
https://www.energy-storage.news/news/fire-at-20mw-uk-battery-storage-plant-in-liverpool.
https://www.ouest-france.fr/region-occitanie/ariege/ariege-un-incendie-dans-un-container-de-batteries-au-lithium-une-quarantaine-de-pompiers-mobilises-7070012.
https://www.datacenterdynamics.com/en/news/ovh-fire-update-four-halls-sbg1-destroyed-well-all-sbg2/.
https://www.datacenterknowledge.com/industry-perspectives/give-ovh-break-and-use-data-center-fire-teachable-moment.
Fire at Solar Plant in Hongseong Involves EV Batteries from LG Energy Solution – Businesskorea.
https://www.pv-magazine.com/2021/04/21/two-firefighters-killed-and-one-missing-after-beijing-battery-blaze/.
https://www.shawlocal.com/mywebtimes/news/local/2021/07/19/no-evacuations-for-battery-fire-at-energy-storage-facility-east-of-grand-ridge/.
https://www.theage.com.au/national/victoria/blaze-at-tesla-big-battery-extinguished-after-three-day-battle-for-control-20210802-p58f6x.html.
https://www.professionalmariner.com/battery-related-fire-damages-famed-hybrid-tug-puts-it-out-of-service/.
https://112-water.nl/inzetten-verslagen/201-brand-aan-boord-bij-hybride-boot.
https://www.wsws.org/en/articles/2019/07/12/russ-j12.html.
https://gcaptain.com/fire-and-gas-explosion-in-battery-room-of-norwegian-ferry-prompts-lithium-ion-power-warning/.
https://maritime-executive.com/article/newly-built-hybrid-passenger-vessel-suffers-battery-fire-under-way.
|
APS Arizona, USA |
February 2012 |
Testing a new 1.5 MW BESS linked to a solar energy system when it was destroyed by fire. Subsequent investigation concluded that lack of ventilation and inadequate monitoring were the major causes of the incident and recommended improved ventilation, 24/7 monitoring and the ability to send remote alarms.a |
Wisconsin, USA |
August 2016 |
The damage is estimated up to $4M. The fire started in the DC power and control system rather than the lithium ion batteries.b |
Drogenbos, Belgium |
November 2017 |
Fire badly damaged the container of a 1 MW BESS after the fire detection and control system failed to control the blaze.c |
Various places across South Korea |
2018–2019 |
Up to 30 fires involving LG Chem lithium ion BESS. The causes of these fires have not been made public as yet, but defective lithium ion cells were not believed to be a major contributing factor. The concatenation of multiple factors have been postulated.d |
Surprise Arizona |
April 2019 |
Vapour cloud explosion. Four first responders were injured, 2 very badly. 9 first responders contaminated with hydrogen cyanide.e |
Nathan campus of Griffiths University, Brisbane, Australia |
March 2020 |
LFP BESS exploded causing major damage to buildings. The cause of the fire and explosion has been stated as having been an internal short circuit.f |
Carnegie Road, Merseyside, UK |
September 2020 |
One of three containers exploded in the early hours of 15 September, followed by a fire. The ventilation units were blown off the roof of the container by the blast, with debris (including one of the doors) scattered across a wide area. The cause of the explosion remains under investigation.g |
Perles-et-Castelet, Ariège France |
December 2020 |
A BESS containing 60 “batteries” ignited. The container was situated on top of a second container and presented some difficulties to the fire service, which had to pull the burning container down. The cause of the fire is under investigation.h |
SBG-2 OVHcloud data centre in Strasbourg, France |
March 2021 |
One data centre was completely destroyed and 4 of the 12 rooms of a second centre were also destroyed. Unconfirmed reports that fire started in BESS.ij |
Hongseong, South Chungcheong Province, China |
April 2021 |
Fire in the BESS supporting a solar energy facility, supplied by LG Energy Solution (LGES). The fire destroyed the facility causing ca. 440 M Won damagek. |
Shopping mall in Beijing, China |
April 2021 |
Explosion and fire in a 25 MW h LFP BESS situated on the roof of a shopping mall. The BESS supported a solar array. 2 firefighters were killed, 1 injured. The BESS consisted of two sections, North and South: whilst dealing with a fire in the Southern section and explosion occurred in the Northern section, killing the firefighters.l |
Invenergy storage facility, LaSalle County, USA |
July 2021 |
Fire in one of the 18 containers at a LFP BESS near the La Salle Generation Station nuclear power plant.m |
“Victorian Big Battery”, Moorabool, Geelong, Australia |
July/August 2021 |
The Moorabool installation is the largest LiBESS in Australia. The fire started in one container and spread to a second, paired container which was adjacent to the first. The firefighters adopted a defensive strategy due to the challenges of the installation, and allowed the containers to burn out in a controlled manner over 3 days.n |
|
|
|
Maritime incidents |
|
|
Place |
Date |
Comments |
Hybrid tug Campbell Foss, USA |
November 2012 |
Fire in BESS of the vessel after it had finished assisting a second vessel in the port of Long Beach. The fire started in the battery compartment and spread to the engine room via a ventilation duct. The vessel's engineer was hospitalized. The incident has been attributed to long term overcharging of the battery.o |
Boat Carila Sis, Sneek harbour, Netherlands |
May 2019 |
The explosion occurred on board a pleasure craft whilst moored in the harbour. A fireball was observed above the boat by local residents.p |
Russian nuclear submarine Losharik, Barents Sea |
July 2019 |
An electrical short circuit occurred while the nuclear submarine was docking with the Podmoskovye, its mothership. This caused lithium ion cells to go into thermal runaway resulting in explosions and fire, killing 14 high-ranking officers on board.q |
Hybrid electric ferry Ytterøyningen, Norway |
October 2019 |
Coolant leaked from the 1989 kW h BESS on the vessel causing a small fire. This was extinguished by the seawater sprinkler system. However, the seawater then caused short circuits in the battery which exploded on the following day. 12 firefighters were hospitalized due to exposure to hazardous gases.r |
Hybrid passenger vessel Brim, Norway |
March 2021 |
Fire in the 790 kW h battery compartment of the 24-meter hybrid catamaran passenger vessel Brim in Oslofjord.s |
In essence, LIBs in thermal runaway produce gases that are a mixture including hydrogen, carbon monoxide, carbon dioxide, HF, short-chain alkanes and alkenes, HCN, NOx and droplets of solvent,21,23,138,140–142 the last giving the mixture the appearance of a white cloud.143 In broad terms, the composition of the white vapour varies little as a function of cell chemistry, form factor or manufacturer.138 The gas mixture will be vented either when safety valves/blast caps activate or when a pouch cell bursts: at high SOC and in the presence of sufficient oxygen, the white vapour ignites to produce flare-like flames. At low SOC or in the absence of sufficient air (e.g. the air is displaced by the vapour or by fire suppressant) the white vapour does not ignite,144 in which case, in a confined space, there could be a possibility of a flash fire, fireballs developing, or in extreme cases, even a vapour cloud explosion.
LIBs are also more and more used in marine transportation. They can work as a propulsion system, powering ferries or even submarines,145 energy recapture systems or hybrid systems. The advantage is usually lower weight and better efficiency in comparison to i.e. lead-acid systems.146 As in the case of the EVs and BESS, there is a possibility of faults, incidents, fires and thus pollution of water ecosystems. An example of such an incident is a fire and subsequent gas explosion on board a diesel-electric ferry in Norway on the 10th of October 2019147 – the fire was spotted during the crossing, but the ferry returned to the harbour under its power where everyone was safely evacuated. Overnight, however, a serious gas explosion rocked the battery room causing significant damage. It was reported that twelve firefighters were hospitalized due to exposure to hazardous gases associated with the burning batteries. Table 2 also shows some other known up-to-date incidents.
Fire extinguishing agents (water, foam etc.) used to mitigate the incidents will be a carrier to all pollutants released from LIBs. That can broader the area of the impact. For instance, HF released during a fire may form a solution with the fire extinguishing agent and thus, at concentrations as low as 0.01%, could cause injury to the more sensitive areas of human skin following exposures as short as 5 min.148 If we add that between 20 and 200 mg of HF could be released per W h of an EV battery pack,22 such solution or even higher concentrations may be of no surprise. This reaction should be also taken into account when designing and using any extinguishing systems in places dealing with larger amounts of LIBs. The first responders must also be aware of the additional hazards, thus proper personal protective equipment (PPE) and operating procedures should be in place.
When the fire is gone there are left carcasses of burnt batteries. Except probably some steel parts (pack cover, module case etc.) they would not represent any value for recycling thus probably discarded/landfilled. These carcasses may be treated as fire debris according to Fig. 2. Currently, there are no data directly revealing what kind of pollutants may be released from such waste. Given the typical post-fire analysis132,149 and the composition of LIBs, we can suspect these may be remains of nanooxides, metals, PAHs and VOCs.
3. Sources and pollution pathways
Spent LIBs are considered hazardous wastes (especially those from EVs) due to the potential environmental and human health risks associated with heavy metals.74,150–154 The disposal and processing of LIBs, as well as their properties (e.g. chemistries), will have a significant impact on various environmental compartments (Fig. 3). LIBs contain a variety of chemicals including reactive salts, volatile organic electrolytes and additives: the latter are often commercial secrets and hence their toxicity and combustion products are largely unknown.155,156 Moreover, battery fires, in combination with biogas from landfills, may release toxins into the air or leach the harmful contents into the soil, groundwater and surface water.118,157,158 Once released, they pose risks to the surrounding environment alone or in combination with other pollutants.159–165
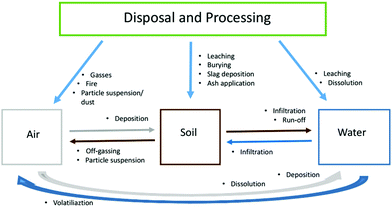 |
| Fig. 3 Possible emission routes of pollutants from LIBs into the environment. | |
Fig. 3 shows likely pollution routes (originated from EoL LIBs disposal/processing) to the environment and possible cross-contamination within different compartments. Pollutants once released from LIBs may enter one compartment first and later be transported to another one. For instance, heavy metals may be collected by dumpsite leachate and transported into the soil or groundwater outside the initial site. On the other hand, if a battery leaches onto open ground, heavy metals may run-off with the rain to a nearby river or lake. However, due to knowledge and data gaps, not all routes could be fully reviewed in this work.
3.1 Emissions to air
3.1.1 Dust.
Fine particles may be released from LIBs to the air during disassembly and recycling processes; from a landfill or dumpsite by degradation or fire/explosion; and are considered as a part of the total dust emissions.166 Generally, dust is a mixture of solid particles and liquid droplets of a wide range of sizes (nanometres to few micrometres) and chemical composition, all together suspended in the atmosphere.167,168 Particulate matter with aerodynamic diameters of less than 10 or 2.5
μm (PM10 and PM2.5) can jeopardize human health, adversely affect climate and reduce visibility at local and regional scales.169–171 Particulates may contain matter-bound metals such as arsenic, cadmium, chromium, cobalt, copper or lead due to the decomposition of recyclable batteries, scrap metals and electronic waste.172–174 Dust can enter the respiratory system causing adverse health effects such as cardiovascular and respiratory diseases, carcinogenicity, or disruption of the endocrine system.175–187
During disassembly and material recovery of LIBs, shredding is the main mechanical processing option25 that could generate dust emissions. These emissions could potentially cause a respiratory hazard to workers in recycling centres as well as those living or working in the vicinity. Moreover, particles and chemicals (e.g. PAHs) released from batteries may aggregate together in the atmosphere, be transported on larger distances and settled down causing for example soil pollution. As LIBs particles may be of different materials and sizes, it is mandatory to assess and investigate their possible toxicity and respiratory hazard.
The potential negative effect of three battery materials: lithium iron phosphate (LFP), lithium titanium oxide (LTO) and lithium cobalt oxide (LCO) was studied utilizing mouse bioassays.188 The mixed metal oxides present in the cathodes of LIBs could release particles small enough to penetrate the lungs and induce inflammation. The extent of the impact varies depending on the chemistry of the LIB. From the materials tested by Sironval et al. (2018), LTO was the least harmful, whereas LCO induced the strongest inflammation. As a result, the fibrotic responses were observed in cells with higher inflammation rates.188
Another generator of dust and particles are explosions and fires. During thermal runaway the particles are first ejected from the safety vent together with other gases, resulting in heavy smoke with black colour.189,190 After cooling down, they settled as surface dust. The composition of these powders from lithium nickel cobalt manganese (NMC) cells was mainly C, O, Al, Mn, and F. This result suggests that it is mostly the negative carbon particles of the battery, as well as the oxidized positive substances of the electrode, that are ejected during gas venting.190 Another study191 found that thermally abused prismatic automotive NMC cells released PM that contained heavy metals. The authors found that nickel and copper were detected in all collected fractions (1.45 to 500 μm) whereas zinc and chromium settled with bigger fractions (50 to 500 μm). Ni had the largest mass percentage followed by Cu, Zn and Cr. In terms of the total emitted quantity, PM accounted for 1.7% of the cell mass. Once settled, such particulates may interact with surrounding waters and soil and ultimately be of threat to crops.
3.1.2 Hydrofluoric acid.
Out of various hazardous gases released from LIBs to air, HF is of the highest concern and must be treated with high caution. It can enter the human body via the skin or respiratory systems and causes severe corrosive effects and systemic toxicity.192 Inhalation of just a few ppm of HF can result in serious toxic effects. HF readily penetrates the skin and moves quickly to the deeper tissue layers where it releases the freely dissociable fluoride ion. This ion is extremely toxic, due to its strong reactivity.193 Moreover, HF gas is hygroscopic and readily soluble in water.158,194,195 Concentrated solutions of HF are highly corrosive to the skin and underlying tissues and accidental dermal exposure has been reported to cause death in humans.148,196
HF is generated in LIBs during the first charge and by subsequent cycling, a phenomenon known as gassing.197–200 The acid can also be produced due to accidental spillage and hence the exposure of the LiPF6 in the electrolyte to humid air158 according to:
| LiPF6 + H2O → LiF + 2HF + POF3 | (1) |
although this is disputed.
201
As well as the direct reaction of LiPF6 with water, at ambient temperature in the organic carbonate solvents employed, LiPF6 exists in equilibrium with its decomposition products according to:
PF
5 is prone to degradation upon exposure to traces of water, moisture or alcohols
202 to form HF which is also highly toxic:
158 | PF5 + H2O ↔ POF3 + 2HF | (3) |
To mitigate the effect of reaction (3), commercial LIB electrolytes often contain additives, up to 5% by mass or volume, some of which suppress PF5 formation. Others are added to protect against overcharge, provide fire-retarding protection or improve Solid Electrolyte Interphase (SEI) formation or quality.203 It is not clear what effect these may have on reaction (2) or other decomposition reactions, or their toxicity or the identity of the products from their combustion.
The second likely source of HF from LIBs is a thermal runaway and fire. The amount of HF produced during an incident depends on the size of the cell and its chemistry21,23,142,204–206 and may incorporate endothermal decomposition of the binder – polyvinylidene fluoride (PVDF).159
Sturk et al. (2015) detected significant quantities of HF from burning NMC and LFP type pouch cells.141 Surprisingly, LFP cells produced the highest levels of hydrofluoric acid fumes. So far this type of chemistry was regarded as one of the safest as having the highest cathode decomposition temperature;135 however, the cells employed in the LIBESS that exploded at Griffiths University in March 2020 were LFP cells.207
Larsson et al. (2017) have estimated that between 20 and 200 mg of HF could be released per W h of an EV battery pack.22 Thus, the amount of HF could be greater than 80–800 times the US National Institute for Occupational Safety and Health Immediate Danger to Life or Health (IDLH) level.208
3.1.3 Vapours and gases.
It is now apparent that thermal runaway generates a white vapour during venting the cells, essentially independent of chemistry, form factor and manufacturer.139 This white vapour contains H2, SO2, NO2, HF, HCl, CO, CO2, droplets of organic solvent (giving the white colour) and a large range of small chain alkanes and alkenes.7,20–24 The exact composition of the white vapour appears to depend on the State of Charge (SoC) and battery chemistry.20,142,209,210 The white vapour is produced when cell is venting as a result of various chemical processes, triggered at successively higher temperatures.135 There is insufficient oxygen produced when the cathode structure collapses to sustain fire, but when the white vapour vents from the cells it may or may not ignite: at SoC > 50% and if sufficient oxygen is present, the vapour can ignite to produce jet-like flames.144 However, if there is insufficient oxygen, e.g. inside a LIBESS with air displaced by the vapour and/or a suppressant,138 the vapour represents a wholly novel hazard concerning LIBs; if the white vapour contacts an ignition source, there could be a possibility of a flash fire, fireballs developing, or in extreme cases even a vapour cloud explosion.211
3.2 Emissions to soil and water
Once physically disposed of, LIBs will leach their contents into the surrounding soils, infiltrate to deeper layers, pollute groundwater and can run-off into surface waters. As water is very often a carrier of pollutants in the soil, it is challenging to ascertain the individual impact of LIBs on these two spheres alone, and hence we discuss the impact on them jointly.
3.2.1 Landfill/dump leachate.
One of the most important hazards associated with landfilling and illegal processing is the generation of leachate: it is formed as a result of various biological and chemical degradation processes, and rain percolating through waste. Non-LIB related leachates are a complex mixture of substantial amounts of dissolved organics, inorganic salts, ammonia, heavy metals and xenobiotic organic compounds that are remains of personal care products, pharmaceuticals, industrial, household chemicals, their transformation and degradation products, especially from landfills.212–214 Leachate could impose a serious environmental impact as it can act as a transportation medium for hazardous species. It may pollute soils or groundwater and transport contaminates over considerable distances, often many kilometres from the site215–219 potentially contaminating groundwater.212
LIB leachates will potentially carry various pollutants such as heavy metals, additives, electrolyte degradation products but also dissolved gases. The latter, such as HF, HCl or SO2 (in form of sulphuric acid) not only have a straightforward toxic effect but also alter the properties of receiving waters and solutions in soil. The acidification caused by these corrosive species may have the same effect as “acid rain”, lowering the pH and thus strongly impacting plants and animals.220 They would also enhance the release of soil-bound heavy metals. Under more acidic conditions the actual toxicity of heavy metals is higher than it would be predicted from the metal concentration alone.221
3.2.2 Heavy metals.
The content of metals in batteries depends upon their design and size (i.e. cylindrical, prismatic or pouch cells), as well as their chemistry (i.e. NMC, LCO etc.). Typically they are in the range of 0.05–0.37 kg Co per kW h, 0.25–0.86 kg Ni per kW h and 0.46–0.9 kg Li per kW h.222–225 These figures translate to tens of kilograms of such materials in EV packs that potentially may be released to the environment if improperly disposed of, representing a series of threats to human health and the environment.
The toxicity of heavy metals from LIBs includes attaching, blocking and disturbing the conformational structure of carbohydrates, lipids, proteins or enzymes.226–228 Heavy metals polluting crops, fruits or dust are known to induce genetic damage in children229,230 and cause lower academic performance.231
Nickel released into the environment binds strongly to small solid particles, especially containing iron or manganese. Ni has a low tendency to accumulate in fish and small animals. With respect to human health, nickel is the most common allergic metal. It may also cause respiratory disorders and even cancer at higher concentrations.232 Lithium has relatively low toxicity and small dosages are beneficial for various trophic levels of organisms.233 Nevertheless, it is quite an active element and, in higher concentrations, may cause digestive and neurologic systems disorders.234,235 Small dosages of cobalt are beneficial to humans (synthesis of vitamin B12) but larger dosages cause respiratory problems and skin rashes.236 In general, adverse reactions to Co exposure depend primarily on its chemical form.237
The leachate from LIBs penetrating through landfill or illegal dumpsites will collect and carry various metals, including lithium, cobalt, nickel, manganese, iron, chromium and copper.155 A few studies have reviewed various leaching scenarios to assess the correlation of typical mass compositions in different types of LIBs to their contamination potential.238–241 Metals found in leachates (both real and artificial) that exceeded toxicity limits were lead, mercury, cobalt, copper, nickel, chromium and thallium – depending on the type of test used. One of the studies242 analysed the leachate from a landfill containing NMC batteries: the authors found that less than 4% of the total cobalt, nickel, aluminium, copper, and iron from the battery were in solution, whilst 11.45% of the manganese and 42.50% of the lithium were present.
It is unlikely that metals will be released only in metallic or ionic form from buried LIBs: they will likely be mobilized as nanoparticles (NPs) as well. Such nanomaterials (mostly of cathode origin) and their ecotoxicological potential towards various organisms were assessed by several studies. Thus Hang et al. (2017) studied the impact of NMC on the soil bacteria Shewanella oneidensis MR-1 and found that exposure to 5 mg L−1 NMC significantly impaired bacterial population growth and respiration.243 The authors showed that these effects were due to the release of metal ions from the NMC, with the largest effects arising from Ni2+ and Co2+ species. Gunsolus et al. (2017) also investigated the toxicity of NMC towards the same bacteria, varying the relative composition of the metals in the mixed metal oxide.244 The authors found that lowering the Ni and Co content and increasing the Mn content, lowered the biological impact significantly. In fact, reducing the cobalt content and increasing Ni has been a key aspect of NMC battery development over the last few years, driven by safety considerations245,246 and global supply chain issues.247,248 Another study assessed the biological impact of NMC on a Gram-positive model bacterium, Bacillus subtilis.249 Growth and cellular respiration of the bacteria were inhibited significantly by free Ni2+ and Co2+ ions released from the incongruent dissolution of the NMC. DNA damage tests at the single-cell level confirmed that the toxicity caused by the redesigned NMC (enriched in Mn) was lower in comparison to solutions containing either free Ni and Co or original NMC material. A recent paper250 reported a study on the influence of multiphase lithiated cobalt phosphate (mLCP) nanomaterial on Shewanella oneidensis MR-1 and Bacillus subtilis. The authors found that mLCP was toxic to both species due to the release of cobalt ions.
The toxicity of NMC and LCO materials towards eukaryotic organisms was studied using Daphnia magna.251 The work showed that there is negligible acute toxicity to daphnid at the highest concentrations of 25 mg L−1, whereas there is a significant impact on daphnid reproduction and survival during chronic exposure (21 days) at concentrations of 0.25 mg L−1 for LCO and 1.0 mg L−1 for NMC. They confirmed that toxicity depends on chemical composition – the replacement of Co by Ni and Mn resulted in better daphnid survival, reproduction, and body size. Finally, the authors highlighted there was a strong nanomaterial-specific impact – probably due to adhesion.252 Although, the effect could not be fully confirmed by experiments with just free Li, Ni, Mn, and Co ions dissolved in suspension metal.
LCO and NMC have been shown to have adverse effects on the benthic invertebrate Chironomus riparius253 by inhibiting growth and development. The increased toxicity of these materials was associated with quick sedimentation of nanoparticles and thus faster interaction with benthic organisms. As in previous studies, a reduction in the biological impact of NMC versus LCO was observed.
On the higher trophic level, the fish class, there is an evident impact of LCO on rainbow trout gill epithelial cells.254 It was found that exposure to Li+ and Co2+ alone, did not reduce cell viability, however strong toxic effects were observed for LCO nanoparticles and these were found to increase the concentration of reactive oxygen species (ROS). Overproduction of ROS may cause biochemical damage, overstress to cells and ultimately, their damage.255 These negative effects were measured at sub-toxic concentrations of LCO which are close to predicted environmental levels. Finally, it was found that the nanomaterials were internalized in cellular organelles, which was not the case for bacteria.243 A subsequent paper256 reported studies on the response of the same type of cells to LCO-induced oxidative stress. The authors postulated a “two-hit” model for LCO toxicity. Initially, the intact LCO material induces high levels of ROS leading to gradual engagement of stress response genes (“first hit”). In the next step, the gradual release of metal ions from NPs starts to suppress the expression of these genes, disrupting the cell response to elevated ROS levels (“second hit”). This mode of action ultimately confuses the cell response to stress and may lead to severe damage.
The take-home message from all ecotoxicity studies is that the replacement of toxic metals (Co and Ni) with less toxic ones (Mn) may increase the environmental compatibility and sustainability of the next generation of LIB materials.
Heavy metals from LIBs may also enter the natural environment due to materials recovery processes, as well as legal and illegal disposal routes. Due to the lack of valid data concerning the recycling of LIBs, for analytical purposes, we can consider other well-established processing of automotive batteries. Critical analysis of the lead-acid batteries recovery reveals that large quantities of potentially toxic slag have to be dealt with. In most countries, such wastes are often disposed of in waste dumps that may lack properly designed engineered landfills, especially in emerging economies. Analysis of slag revealed that apart from high pH (12.22) it contained also high concentrations (g kg−1) of Pb (>101), Cu (>2.5), Cr (>1.2), Zn (0.5), Cd (>0.5) and Ni (0.1), indicating a poor metal recovery in the recycling processes.257 The authors suggested that there was a greater risk of release of these heavy metals over the long-term following disposal into the environment. Fujimori et al. (2016) found elevated levels of Pb in some China soils located next to recycling plants.258 In the case of LIB recycling, we also have to deal with the slag resulting from the pyrometallurgical route, mainly containing Mn, Li, and Al.259
3.2.3 Battery degradation products.
The study undertaken by Grützke et al. (2015) may give indications of the fate of processed battery material when kept in storage (i.e. prior to recycling) or landfilled.59 The authors shredded NMC LIBs from EVs and enclosed them in sealed tinplate and plastic cans. Their main goal was to assess which compounds are released from spent, processed material, and if there is any further degradation of original compounds, and the possible emergence of hazardous transformation products. The so-called “black mass” was monitored for over 20 months with regular analyses of gases, liquids and remaining salts. Their results showed that the tinplate cans underwent fast corrosion – first spots were visible after a few days, and after five months some of the cans were already perforated by rusting. Plastic cans did not show any visual signs of degradation. In addition to HF, the authors found traces of phosphoric acids, LiPF6, other additives (i.e. cyclohexylbenzene) and solvents – DMC, EC, EMC and their degradation products. More importantly, they identified several alkylfluorophosphates, including dimethyl fluorophosphate (DMFP) and diethylfluorophosphate (DEFP). Alkylfluorophosphates are of concern as they have similar structures to the chemical warfare agents such as sarin.260 DMFP and DEFP were also detected by Kraft et al. (2015 and 2016) who investigated the thermal degradation of LIB electrolytes.160,261 Although present in manageable low concentrations, they still may have toxic potential both to humans and the environment.
These studies highlight the important issue of storing spent and processed battery materials. If real-life scenarios are envisaged, such as temporary storage in the canister or landfilling, certainly, the corrosion of containers or battery metal case (module or pack) will be speeded up by external environmental factors such as leachate or humid air. It also indicates that spent degraded battery already contains harmful content – these products may enter the air or be transported with the solution to other compartments.
3.2.4 Additives.
Finally, LIBs may also leach the remains of electrolyte and its additives.262,263 The most common additives are polymers, Lewis acids, sulphur-containing and phosphorous containing additives, polyfluoroalkyl substituted ethylene carbonates or ionic liquids (ILs). The latter, ILs, are particularly interesting as they can play many roles in the battery system: as a pure electrolyte; in mixture with conventional solvents; as a gel polymer electrolyte or as a binder.264,265 ILs are non-volatile and a non-flammable class of organic salts consisting of an organic cation and an organic or inorganic anion and there is a broad spectrum of cations (i.e. imidazolium, pyridinium, choline etc.) and anions (organic and inorganic).266 Therefore, there is a very broad spectrum of the environmental impact of these compounds depending on their structure. However, due to their properties, the routes of exposure and potential hazards are limited to interactions with solutions. The distribution of ionic liquids in the environment is governed by their structure e.g. ILs with longer alkyl chains absorb more easily on the soil surface. Therefore, some ionic liquids may be quite mobile in water or soil columns whereas others may bind strongly to various environmental compartments and may become persistent pollutants. Additionally, the properties of soil such as high cation exchange capacity and/or abundance of organic matter will greatly increase the uptake of ILs.267–275 Although their use is usually restricted to small quantities, ILs could still have considerable negative effects on wildlife and human health. For instance, most of the ionic liquids in battery systems are considered toxic and poorly biodegradable compounds.276,277 As in the case of the mobility and transport in environmental media, the toxicity of ILs depends on the lipophilicity and alkyl chain length, the direct interaction with the biological system (membrane, cell or organism) and trophic levels (bacteria, plants, invertebrates or human cells). Usually, the longer the derivative the more toxic it is but there is also a strong impact of the counter-ion, especially fluorinated ones.278–287
4. Recommendations for future studies
Table 3 illustrates the possible routes of emission and pollutants released from LIBs. Although partially supported by the existing literature (see Sections 2 and 3), this is more of an indicative list. There are lots of unknowns, incomplete data, not yet researched specific topics or even contradictory results that need to be clarified to mitigate any negative impact of spent batteries.
Table 3 Possible pollutants and routes of their emission released from LiBs
Battery component |
Source of pollutant |
Specific pollutant |
Route |
Affected environment |
Hazard |
Pack casing |
– Steel |
i.e. Fe, Al, Ni, Cr other |
Leaching |
Land |
– In excess toxic to wildlife |
Natural waters |
– Accumulation in plants and crops |
Module casing |
– Steel |
– Fe, Ni, Cr other |
Leaching |
Land |
– In excess toxic to wildlife |
– Aluminium |
– Al |
Natural waters |
– Accumulation in plants and crops |
Cell packing |
– Aluminium foil |
– Al, Ni |
Leaching |
Natural waters |
– In excess toxic to wildlife |
– Polymers |
– PET, PP |
Fire |
Land |
– Accumulation in plants and crops |
– Ni-Coated steel |
|
|
Air |
|
Cathode |
– Metal |
– Al |
Leaching |
Land |
– Toxic to the various organism |
– Metal oxides |
– LMO – Li/Mn/O |
Dust |
Natural waters |
– Toxic to humans if breathed |
|
– LFP – Li/Fe/P/O |
|
Air |
– In excess toxic to wildlife |
|
– NMC – Li/Ni/Mn/Co/O |
|
|
– Accumulation in plants and crops |
|
– LCO – Li/Co/O |
|
|
|
|
– NCA – Li/Ni/Co/Al/O |
|
|
|
Anode |
– Copper |
– Cu |
Leaching |
Land |
– In excess toxic to wildlife |
– Graphite |
– C (nanomaterial) |
Natural waters |
– Accumulation in plants and crops |
|
– LTO – Li/Ti/O |
|
– Toxic to humans if breathed |
Separator |
– Polymers |
– Polyethylene (PE) |
Leaching |
Land |
– Microplastics accumulation |
– Polypropylene (PP) |
Fire |
Natural waters |
|
Dust |
Air |
Binder |
– PDVF |
– HF |
Fire |
Air |
– Toxic to humans if breathed |
– Toxic to humans if in contact |
Electrolyte |
– Ethylene carbonate |
– HF |
Fire |
Air |
– Toxic to humans if breathed |
– Propylene carbonate |
– SOx |
Vapours/gases |
Land |
– Toxic to humans if in contact |
– Dimethyl carbonate |
– HCN |
Leaching |
Natural waters |
– Toxic to wildlife |
– Diethyl carbonate |
– H2 |
|
|
– Accumulation in soils |
– Salts: LiPF6 |
– CO |
|
|
|
– Additives |
– CO2 |
|
|
|
|
– NOx |
|
|
|
|
– COS |
|
|
|
|
– HCl |
|
|
|
|
– Degradation products of electrolyte (i.e. C2H4; CH3COCHO etc.) |
|
|
|
|
– Ionic liquids |
|
|
|
|
– Unknown additives/degradation products |
|
|
|
Therefore, we identified some of the main knowledge gaps and probe the following questions on the environmental impacts of spent LIBs that might help to manage these better in the future:
(1) What are the current and prospective volumes of spent LIBs?
(2) How much spent batteries reach the relevant disposal stream?
(3) Where spent batteries will be processed/disposed of/abandoned?
(4) In what form: as a whole, partitioned, shredded etc. LIBs will be processed/disposed of/abandoned?
(5) What is the impact of changing chemistries on the waste streams in terms of needed technology but also in terms of the life span?
(6) What, how, where and in which volumes are hazards released from the spent batteries?
(7) What is the prevalence and distribution of battery pollutants once being released into the natural environment?
(8) What is the circulation and interactions of battery pollutants among the land–water–air-emission pathways and the wildlife nexus?
(9) What is the (eco)toxicity and (bio)accumulation of LIBs materials to various organisms and humans?
(10) How should or would environmental studies support the design and disposal of spent LIBs?
Although, some of these questions could be partially answered already based on approximations i.e. prospective volumes are estimated on sales number; but there is an urgent need for reliable and verified data. Obtaining reliable and accurate data will have serious implications for the safety of the recycling and disposal facilities and helps to shape, implement and regulate appropriate practices and legislations. The real data should be supported by various Life Cycle Assessments methodology, cost-benefit studies and the use of more modelling in the prediction of i.e. life cycle of the specific battery in a given application.
As the growing demand for new LIBs will result in increased numbers of spent batteries, we recommend that this quantity must be appropriately managed and controlled across the various disposal routes. The best-case scenario assumes high collection rates of spent batteries with an almost full recovery of materials that can be reused (boosting the circular economy). It is evident that domestic i.e. decentralised recycling will be more profitable than centralised recycling, however, it will take time for the industry to scale up collection, processes and infrastructures.6 It is also argued that latecomers will be threatened by the existing industry that may benefit more quickly from the larger economies of scale. Decentralised systems do require a substantial amount of spent LIBs (especially large EV) to reach economy of scale as it was estimated that recycling costs will decrease if between 1000 and 15
000 tonnes per year are recycled at one plant.6 Collection of spent and “second-life” large batteries, might be linked with some business model e.g. sale of the car but the lease of battery – then the responsibility is on dealer/seller or can be governed by local councils with i.e. specialized collection centre – responsibility on the user. To improve the collection and later decision on the re-use, recycling or landfilling knowing the usage history of “first life” of EV/BESS batteries would be of great use – the battery's condition can be determined much faster and more economically. That will speed up the streamlining of LIBs to an accurate route of processing. However, we must bear in mind that modules in the pack can age differently288 – so possible that the selection will be on the modules not pack level. Nevertheless, improving the reuse of the materials could reduce the environmental, economic and social burden of the existing battery supply chain including disposal practices is inevitable. However, the challenges in the collection, dismantling and recycling of LIBs must be overcome. It is of crucial importance to develop innovative technologies to lower the cost of material recovery and reduce the environmental impacts of this industry.6 Furthermore, illegal disposal and informal processing that leads to serious pollution must be prevented. This could be achieved through better collection schemes, expansions, and improvements in the current recycling infrastructure and posing legal obstacles for exporting second-hand EVs or LIBs. The last anybody wants is that LIBs to become, for instance, a source of soil pollution by heavy metals. Moreover, there should be a constant drive to produce LiBs containing less hazardous and more “green” materials289 that not only improve the capacity and efficiency of the battery but also prevent destructive behaviour and have minimal negative impact on the environment if improperly disposed of.290 New LIBs should be designed for recycling meaning the materials can be easy separate from each other and able to be re-used in new batteries (direct recycling). That links to new technologies of material recovery that are less energy intensive, cheaper and produce less or no secondary pollution.
The improvements must be guided by appropriate legislation, regulations and management structures. These must encourage customers and manufacturers to properly handle spent batteries, highlighting the benefits of recycling (in light of the obligations for economic operators as regards the sourcing of raw materials) and promote the circular economy model and finally, must also clearly ensure where each liability lays.48
Finally, we must address the problem of penetration of large “2nd life” LIBs into society. There is a general perception, particularly in Europe, that the re-use (using an EV battery without change in an EV), remanufacture (using an EV battery after replacing defective modules in an EV) and repurposing (using modules from an EV at end-of-life to assemble a battery for a purpose other than traction, e.g. stationary storage) of LIBs can make a positive contribution to the decarbonization of the planet.48 The safety of new cells, modules and battery packs can be assessed using the “type tests” that form the basis of all codes, standards and regulations governing, for example, domestic and industrial battery energy storage systems. Type testing relies on testing a sample of cells from a batch, usually to destruction, and accepting the result as representative of the batch. The use of type testing on new cells is valid due to the extremely tight quality control of their manufacture, however, such type testing is now accepted as inappropriate to assess the safety of second life LIBs due to the wide variation in SoH across an EV pack during its life and possible exposure to extremes of temperature, overcharging and/or charging at high currents,291–293 all of which can increase the potential for thermal runaway.294,295 The draft standards IEC63330296 (Requirements for reuse of secondary batteries) and IEC63338297 (General guidance for reuse of secondary cells and batteries) fully acknowledge the fact that type tests cannot be employed to assess the safety of second life LiBs. The key challenge is determining the SoH, or more correctly, the State-of-Safety of second life LIBs.298 A part of the latter must be full knowledge of the first life of the LIB in the EV, including full details of any abuse (e.g. overcharging) maximum charge and discharge currents & operational temperatures. The draft standards IEC63330 and IEC63338 were intended to address this problem and hence facilitate the safe application of second life LiBs, but have failed to do so, as they do not require any testing and rely completely on the original manufacturers of the EVs passing on full BMS data (and hence potentially valuable intellectual property) to remanufacturers & repurposers, which is perceived as highly unlikely. The draft EU Batteries Regulation also sidesteps the safety issue of second-life batteries by requiring only that BMS data is made fully available.
It is generally accepted that the re-use, remanufacturing and repurposing of complete packs where the original EV manufacturer is retained in the supply chain is of low risk.299 However, second life cells, modules and even full battery packs are freely available from online retailers, such that inexperienced organisations and even the general public can repurpose LIBs. Thus, a major concern is the use of these suppliers by homeowners to build do-it-yourself domestic BESS: domestic battery energy storage systems are currently completely unregulated in the UK with respect to the application of lithium-ion batteries. Concerns over the hazards posed by such systems in the home environment have been addressed in other countries: thus the US NFPA 855 standard300 and the draft DR2 AS/NZS 5139
:
2019 Australian and New Zealand standard301 do not permit domestic lithium-ion BESS inside the home, and NFPA 855 does not permit do-it-yourself lithium-ion BESS at all.
The online trade-in 2nd life LIBs is completely unregulated, and delivery of these devices is often offered by means illegal under UN 38.3302 as they are classified as dangerous goods and hence require transportation in accordance with the European agreement “Accord européen relatif au transport international des marchandises dangereuses par route” (ADR) requirements.303
5. Conclusion
There is no doubt that the urgent need to decarbonise transportation puts LIBs at the forefront of the action. However, the growing stream of spent LIBs would impose an enormous threat to the natural environment and human health, as batteries contain hazardous materials. In this review, the current, possible and likely waste management practices of LIBs were identified – from collection and recycling to landfilling, through the EoL incidents up to illegal disposal. Currently, landfilling is the most common practice but there is a growing share of recycling. The current review also assessed the most likely hazards and incidents during each EoL practice. The fire and explosion incidents are currently the most common events that have been evidenced by real-life incidents. Leaching is another pollution pathway that will co-dominate in the future. Identified hazards released from LIBs contain vapours and gases (i.e. HF, CO or HCN), metal nanooxides (i.e. LMO, NMC), degradation products of the electrolyte (alkylfluorophosphates) and possible traces of additives. These pollutants may be released to soil, water (groundwater) and air, depending on recycling, disposal method or abuse incident. Released pollutants may pose a serious threat to wildlife and humans with often immediate effects like in the case of contact with HF during EV fire. Degradation of the battery content (especially electrolyte) in some cases may lead to the emergence of chemicals structurally similar to chemical warfare agents. The initial studies on the (eco)toxicity of the cathode nanomaterials showed that LIBs may pose a threat to living organisms and human health. But the replacement of toxic metals (Co and Ni) with less toxic ones (Mn) may increase the environmental compatibility and sustainability of the next generation of lithium battery materials. Finally, we identified several urgent knowledge gaps that need to be covered to mitigate the negative impact on the environment of LIBs, and recommended some actions to tackle these issues.
Author contributions
Wojciech Mrozik: writing – original draft, writing – review & editing, conceptualization, visualization, investigation; methodology; Mohammad Ali Rajaeifar: writing – original draft, writing – review & editing; Oliver Heidrich: writing – original draft, writing – review & editing, conceptualization, funding; Paul Christensen: writing – original draft, writing – review & editing, funding.
Abbreviations
Aging | The loss of capacity due to, e.g. loss of lithium ions or spallation of the anodes. This can be due to use (charging and discharging) and/or sitting at open circuit (calendar aging) |
Anode | The negative electrode. In lithium-ion batteries this is most typically small particles of graphite |
Battery (pack) | The complete energy storage unit consisting of a number of modules |
BESS | Battery energy storage system |
Cathode | The positive electrode. These typically comprise lithium plus metal oxides: e.g. lithium nickel manganese cobalt oxide (LiNi0.33Mn0.33Co0.33O2) |
Cell | The smallest unit of a battery |
Electrolyte | In electrochemistry, this term is ambiguous as it can refer to the inorganic salt (e.g. LiPF6) or to the salt + organic solvent |
End of Life (EoL) | The point at which a battery ceases to be suitable for its current application. For automotive batteries this is typically 75–80% State-of-Health |
GHG | Greenhouse gases, gases that cause the greenhouse effect e.g. CO2 and CH4 |
Landfill | A site for the disposal of waste materials |
LCO cathode | Lithium cobalt oxide, LiCoO2 |
LIB | Lithium-ion battery |
LIBESS | Lithium-ion battery energy storage system |
LFP cathode | Lithium iron (ferrous) phosphate, LiFePO4 |
LMO cathode | Lithium manganese oxide LiMnO2 |
LTO anode | Lithium titanium oxide Li4Ti5O12 |
MRF | Material recovery facilities; solid-waste management plant that processes recyclable materials to sell to manufacturers as raw materials for new products |
NCA cathode | (lithium) Nickel cobalt aluminium oxide, e.g. LiNi0.8Co0.15Al0.05O2 |
NMC cathode | (lithium) Nickel manganese cobalt oxide, e.g. LiNi0.33Mn0.33Co0.33O2 (NMC 111), LiNi0.6Mn0.2Co0.2O2 (NMC 622) |
PAHs | Polycyclic aromatic hydrocarbons; made up of fused aromatic rings molecules |
Recycling | The process of converting waste materials into new materials and objects |
Separator | A plastic film permeable to lithium and hexafluorophosphate ions that prevents the anode and cathode from touching and causing a short-circuit |
Solid Electrolyte Interphase (SEI) | The protective layer that forms on the anode during the first charge from reduction of the LiPF6 and solvent which prevents further, explosive degradation of the electrolyte and thermal runaway |
Solvent | Mixture of organic carbonates, containing ethylene carbonate, as this is essential for the formation of the SEI. Ethylene carbonate is a solid at room temperature and other carbonates are essential to reduce viscosity |
State of Charge (SoC) | The amount of charge stored compared to that equivalent to full charge, expressed as % |
State of Health (SoH) | The amount of charge stored currently when fully charged compared to that stored (when fully charged) at the beginning of the cell or battery life, expressed as % |
VOCs | Volatile organic compounds; compounds that have a high vapour pressure and low water solubility |
Conflicts of interest
There are no conflicts to declare.
Acknowledgements
This work was supported by the UK's Engineering and Physical Sciences Research Council (EPSRC) and the Faraday Institution (EP/S003053/1) as part of its “Recycling of Li-Ion Batteries (ReLIB)” project (FIRG005) “SafeBatt – Science of Battery Safety” (FIRG028). The funders had no input or role to play in the conceptualization, design, literature collection, analysis, decision to publish or preparation of the study of this manuscript.
References
- H. E. Melin, M. A. Rajaeifar, A. Y. Ku, A. Kendall, G. Harper and O. Heidrich, Science, 2021, 373, 384–387 CrossRef CAS PubMed.
- European_Commission, 2019, COM/2019/640 final.
-
R. Harrabin, Ban on new petrol and diesel cars in UK from 2030 under PM's green plan, 2020, accessed 20.11.2020 Search PubMed.
-
UKRI, Industrial Strategy Challenge Fund: Future of mobility, 2020, accessed 20.09.2020 Search PubMed.
- UKRI, Industrial Strategy Challenge Fund, 2020, accessed 20.09.2020 Search PubMed.
- L. Lander, T. Cleaver, M. A. Rajaeifar, V. Nguyen-Tien, R. J. R. Elliott, O. Heidrich, E. Kendrick, J. S. Edge and G. Offer, iScience, 2021, 24, 102787 CrossRef PubMed.
- G. Lombardo, B. Ebin, M. R. S. J. Foreman, B.-M. Steenari and M. Petranikova, ACS Sustainable Chem. Eng., 2019, 7, 13668–13679 CrossRef CAS.
- M. A. Rajaeifar, O. Heidrich, P. Ghadimi, M. Raugei and Y. Wu, Resour., Conserv. Recycl., 2020, 161, 104905 CrossRef.
-
M. J. Smith and F. M. Gray, in Alternative Energy and Shale Gas Encyclopedia, ed. J. H. Lehr, J. Keeley and T. B. Kingery, 2016, pp. 566–577 Search PubMed.
- J.-P. Skeete, P. Wells, X. Dong, O. Heidrich and G. Harper, Energy Res. Soc. Sci., 2020, 69, 101581 CrossRef.
-
Veolia, 2020, https://www.veolia.co.uk/press-releases/preventing-battery-fires.
-
B. Morris, 2020, https://www.bbc.co.uk/news/business-54634802, accessed 01.10.2021.
- D. Lisbona and T. Snee, Process Saf. Environ. Prot., 2011, 89, 434–442 CrossRef CAS.
-
FAA, An Introduction to Lithium Batteries and the Challenges that they pose to the Waste and Recycling Industry, https://www.youtube.com/watch?v=OjFHYpI7GrM&feature=youtu.be, accessed 15.11.2020 Search PubMed.
-
M. Reintjes, https://recyclinginternational.com/business/at-least-one-scrap-fire-every-week-in-germany/28831/, 2020, accessed 05.03.2021.
-
BBC, https://www.bbc.co.uk/news/uk-england-nottinghamshire-47976224, 2019, accessed 20.09.2021.
-
K. Akemi, 2020, http://www.asahi.com/ajw/articles/AJ202001100077.html, accessed 18.09.2021.
- P. A. Christensen, P. A. Anderson, G. D. J. Harper, S. M. Lambert, W. Mrozik, M. A. Rajaeifar, M. S. Wise and O. Heidrich, Renewable Sustainable Energy Rev., 2021, 148, 111240 CrossRef.
-
H. E. Mellin, State-of-the-art in reuse and recycling of lithium-ion batteries – A research review, The Swedish Energy Agency, Circular Energy Storage, 2019 Search PubMed.
- A. Lecocq, G. G. Eshetu, S. Grugeon, N. Martin, S. Laruelle and G. Marlair, J. Power Sources, 2016, 316, 197–206 CrossRef CAS.
- F. Larsson, S. Bertilsson, M. Furlani, I. Albinsson and B.-E. Mellander, J. Power Sources, 2018, 373, 220–231 CrossRef CAS.
- F. Larsson, P. Andersson, P. Blomqvist and B.-E. Mellander, Sci. Rep., 2017, 7, 10018 CrossRef PubMed.
- S. Chen, Z. Wang, J. Wang, X. Tong and W. Yan, J. Loss Prev. Process Ind., 2020, 63, 103992 CrossRef CAS.
- G. Lombardo, B. Ebin, M. R. S. J. Foreman, B.-M. Steenari and M. Petranikova, J. Hazard. Mater., 2020, 393, 122372 CrossRef CAS PubMed.
- G. Harper, R. Sommerville, E. Kendrick, L. Driscoll, P. Slater, R. Stolkin, A. Walton, P. Christensen, O. Heidrich, S. Lambert, A. Abbott, K. Ryder, L. Gaines and P. Anderson, Nature, 2019, 575, 75–86 CrossRef CAS PubMed.
- C. M. Costa, J. C. Barbosa, R. Gonçalves, H. Castro, F. J. D. Campo and S. Lanceros-Méndez, Energy Storage Mater., 2021, 37, 433–465 CrossRef.
- C. J. Rydh and B. Svärd, Sci. Total Environ., 2003, 302, 167–184 CrossRef CAS PubMed.
- Y. Hua, S. Zhou, Y. Huang, X. Liu, H. Ling, X. Zhou, C. Zhang and S. Yang, J. Power Sources, 2020, 478, 228753 CrossRef CAS.
- S. King and N. J. Boxall, J. Cleaner Prod., 2019, 215, 1279–1287 CrossRef.
- F. O. Ongondo, I. D. Williams and G. Whitlock, Waste Manage., 2015, 45, 4–9 CrossRef CAS PubMed.
- X. Zeng, J. Li and N. Singh, Crit. Rev. Environ. Sci. Technol., 2014, 44, 1129–1165 CrossRef CAS.
- European_Commission, 2020, COM(2020) 474 final.
- D. Qiao, G. Wang, T. Gao, B. Wen and T. Dai, Sci. Total Environ., 2021, 764, 142835 CrossRef CAS PubMed.
- S. Sun, C. Jin, W. He, G. Li, H. Zhu and J. Huang, Sci. Total Environ., 2021, 776, 145913 CrossRef CAS PubMed.
-
T. L. Curtis, L. Smith, H. Buchanan and G. Heath, A Circular Economy for Lithium-Ion Batteries Used in Mobile and Stationary Energy Storage: Drivers, Barriers, Enablers, and U.S. Policy Considerations, Report NREL/TP-6A20-77035, National Renewable Energy Laboratory (NREL), 2021.
- Call2Recycle, Recycling Laws By State, https://www.call2recycle.org/recycling-laws-by-state/, accessed 25 Mar 2021.
- M. A. Rajaeifar, M. Raugei, B. Steubing, A. Hartwell, P. Anderson and O. Heidrich, J. Ind. Ecol., 2021, 1–12 Search PubMed.
- J. Heelan, E. Gratz, Z. Zheng, Q. Wang, M. Chen, D. Apelian and Y. Wang, JOM, 2016, 68, 2632–2638 CrossRef CAS.
- Y. Bai, N. Muralidharan, Y.-K. Sun, S. Passerini, M. S. Whittingham and I. Belharouak, Mater. Today, 2020, 41, 304–315 CrossRef CAS.
- M. Chen, X. Ma, B. Chen, R. Arsenault, P. Karlson, N. Simon and Y. Wang, Joule, 2019, 3, 2622–2646 CrossRef CAS.
-
H. E. Melin, The lithium-ion battery end-of-life market 2018-2025, Circular Energy Storage, United Kingdom, 2018 Search PubMed.
-
EBRA, Noticeable Growth of the Quantity of Batteries Recycled, European Battery Recycling Association, Brussels, Belgium, 2012 Search PubMed.
- J. Song, W. Yan, H. Cao, Q. Song, H. Ding, Z. Lv, Y. Zhang and J. Sun, J. Cleaner Prod., 2019, 215, 570–581 CrossRef CAS.
-
R. Danino-Perraud, The Recycling of Lithium-ion Batteries: A Strategic Pillar for the European Battery Alliance, Etudes de l'Ifri, Ifri, 2020 Search PubMed.
- A. Akcil, C. Erust, S. Ozdemiroglu, V. Fonti and F. Beolchini, J. Cleaner Prod., 2015, 86, 24–36 CrossRef CAS.
- A. P. Das, L. B. Sukla, N. Pradhan and S. Nayak, Bioresour. Technol., 2011, 102, 7381–7387 CrossRef CAS PubMed.
-
European_Commission, 2014 Directive 2006/66/EC.
- European_Commission,
2020, COM(2020) 798/3.
- J. Baars, T. Domenech, R. Bleischwitz, H. E. Melin and O. Heidrich, Nat. Sustainability, 2021, 4, 71–79 CrossRef.
- R. Sommerville, P. Zhu, M. A. Rajaeifar, O. Heidrich, V. Goodship and E. Kendrick, Resour., Conserv. Recycl., 2021, 165, 105219 CrossRef.
- X. Zeng and J. Li, Front. Environ. Sci. Eng., 2014, 8, 792–796 CrossRef CAS.
-
C. Ekberg and M. Petranikova, in Lithium Process Chemistry, ed. A. Chagnes and J. Światowska, Elsevier, Amsterdam, 2015, pp. 233–267 Search PubMed.
- D. L. Thompson, J. M. Hartley, S. M. Lambert, M. Shiref, G. D. J. Harper, E. Kendrick, P. Anderson, K. S. Ryder, L. Gaines and A. P. Abbott, Green Chem., 2020, 22, 7585–7603 RSC.
- L. Gaines, Sustainable Mater. Technol., 2014, 1-2, 2–7 CrossRef.
- M. Fan, X. Chang, Y.-J. Guo, W.-P. Chen, Y.-X. Yin, X. Yang, Q. Meng, L.-J. Wan and Y.-G. Guo, Energy Environ. Sci., 2021, 14, 1461–1468 RSC.
- M. Sethurajan and S. Gaydardzhiev, Resour., Conserv. Recycl., 2021, 165, 105225 CrossRef.
- J. Yu, X. Wang, M. Zhou and Q. Wang, Energy Environ. Sci., 2019, 12, 2672–2677 RSC.
- Y. He, X. Yuan, G. Zhang, H. Wang, T. Zhang, W. Xie and L. Li, Sci. Total Environ., 2020, 142382 Search PubMed.
- M. Grützke, S. Krüger, V. Kraft, B. Vortmann, S. Rothermel, M. Winter and S. Nowak, ChemSusChem, 2015, 8, 3433–3438 CrossRef PubMed.
- M. Mohr, J. F. Peters, M. Baumann and M. Weil, J. Ind. Ecol., 2020, 24, 1310–1322 CrossRef CAS.
- J. B. Dunn, L. Gaines, J. C. Kelly, C. James and K. G. Gallagher, Energy Environ. Sci., 2015, 8, 158–168 RSC.
- T. J. van der Kuijp, L. Huang and C. R. Cherry, Environ. Health, 2013, 12, 61 CrossRef CAS PubMed.
-
A. Manhart, T. Amera, G. Kuepouo, D. Mathai, S. Mng’anya and T. Schleicher, The deadly business – Findings from the Lead Recycling Africa Project, Oeko-Institut EV, Freiburg, Germany, 2016 Search PubMed.
-
WHO, Recycling used lead-acid batteries: health considerations, World Health Organization, Geneva, 2017.
-
WHO, 2017, https://www.who.int/publications/i/item/recycling-used-lead-acid-batteries-health-considerations.
- Y. Yu, J. Mao and X. Chen, Sci. Total Environ., 2020, 746, 140763 CrossRef CAS PubMed.
-
F. Cerdas, R. Gerbers, S. Andrew, J. Schmitt, F. Dietrich, S. Thiede, K. Dröder and C. Herrmann, Recycling of Lithium-Ion Batteries, Springer, 2018, pp. 83–97 Search PubMed.
- M. D. Vaverková, Geosciences, 2019, 9, 431 CrossRef.
- W. Sun, X. Wang, J. F. DeCarolis and M. A. Barlaz, Waste Manage., 2019, 91, 120–127 CrossRef CAS PubMed.
- J. Havukainen, M. Zhan, J. Dong, M. Liikanen, I. Deviatkin, X. Li and M. Horttanainen, J. Cleaner Prod., 2017, 141, 453–461 CrossRef CAS.
- S. T. Tan, C. T. Lee, H. Hashim, W. S. Ho and J. S. Lim, J. Cleaner Prod., 2014, 71, 48–58 CrossRef.
-
V. Forti, C. P. Baldé, R. Kuehr and G. Bel, The Global E-waste Monitor 2020: Quantities, flows and the circular economy potential, United Nations University (UNU), United Nations Institute for Training and Research (UNITAR), SCYCLE Programme, International Telecommunication Union (ITU) & International Solid Waste Association (ISWA), Bonn/Geneva/Rotterda, 2020 Search PubMed.
- S. Karnchanawong and P. Limpiteeprakan, Waste Manage., 2009, 29, 550–558 CrossRef CAS PubMed.
- A. D. Zand and M. A. Abduli, Waste Manage., 2008, 28, 2085–2090 CrossRef PubMed.
- I. C. Nnorom and O. Osibanjo, Int. J. Environ. Sci. Technol., 2009, 6, 641–650 CrossRef CAS.
- N. Ferronato and V. Torretta, Int. J. Environ. Res. Public Health, 2019, 16, 1060 CrossRef CAS PubMed.
-
FEMA, Landfill fires their magnitude, characteristics, and mitigation, Federal Emergency Management Agency, United States Fire Administration, National Fire Data Center, Arlington, 2002 Search PubMed.
- J. M. Torrente-Velásquez, M. Giampietro, M. Ripa and R. Chifari, Sci. Total Environ., 2020, 706, 135988 CrossRef PubMed.
- P. Kjeldsen, M. A. Barlaz, A. P. Rooker, A. Baun, A. Ledin and T. H. Christensen, Crit. Rev. Environ. Sci. Technol., 2002, 32, 297–336 CrossRef CAS.
- K. Szymański, B. Janowska, A. Iżewska, R. Sidełko and I. Siebielska, Environ. Monit. Assess., 2018, 190, 415 CrossRef PubMed.
- O. Bridges, J. W. Bridges and J. F. Potter, Environmentalist, 2000, 20, 325–334 CrossRef.
- A. E. Peter, S. M. Shiva Nagendra and I. M. Nambi, Waste Manage., 2019, 85, 151–163 CrossRef CAS PubMed.
- P. Ruokojärvi, M. Ettala, P. Rahkonen, J. Tarhanen and J. Ruuskanen, Chemosphere, 1995, 30, 1697–1708 CrossRef.
- P. M. Lemieux, C. C. Lutes and D. A. Santoianni, Prog. Energy Combust. Sci., 2004, 30, 1–32 CrossRef CAS.
- J. Downard, A. Singh, R. Bullard, T. Jayarathne, C. M. Rathnayake, D. L. Simmons, B. R. Wels, S. N. Spak, T. Peters, D. Beardsley, C. O. Stanier and E. A. Stone, Atmos. Environ., 2015, 104, 195–204 CrossRef CAS PubMed.
- J. K. Øygard, A. Måge, E. Gjengedal and T. Svane, Waste Manage., 2005, 25, 712–718 CrossRef PubMed.
- S. Moqbel, D. Reinhart and R. H. Chen, Waste Manage., 2010, 30, 1600–1607 CrossRef CAS PubMed.
- D. Chavan, P. Lakshmikanthan, P. Mondal, S. Kumar and R. Kumar, Waste Manage., 2019, 97, 123–130 CrossRef CAS PubMed.
- ESA, 2020, http://www.esauk.org/application/files/2615/9783/3646/PRESS_RELEASE_Take_Charge_Campaign_v1.pdf.
-
Viridor, 2019, https://www.viridor.co.uk/who-we-are/latest-news/2019-news/lithium-ion-battery-warning-issued-after-landfill-site-fire/, accessed 29.09.2021.
-
H. Gans, Shoreway Fire Hazard Mitigation Plan, Rethink Waste South Bayside Waste Management Authority, https://rethinkwaste.org/wp-content/uploads/legacy_media/022317-shoreway-operations.original.pdf, 2017.
- W. Liu, X. Zhong, J. Han, W. Qin, T. Liu, C. Zhao and Z. Chang, ACS Sustainable Chem. Eng., 2019, 7, 1289–1299 CrossRef CAS.
- S. Morales, G. E. Raúl, A. Toro, R. Morales, L. Leiva and A. Manuel, Air Qual., Atmos. Health, 2018, 11, 111–121 CrossRef.
- D. R. Nammari, W. Hogland, M. Marques, S. Nimmermark and V. Moutavtchi, Waste Manage., 2004, 24, 9–18 CrossRef CAS PubMed.
- A. D. St-Amand, P. M. Mayer and J. M. Blais, Atmos. Environ., 2008, 42, 2948–2958 CrossRef CAS.
- E. D. Vicente, A. M. Vicente, B. A. Musa Bandowe and C. A. Alves, Air Qual., Atmos. Health, 2016, 9, 653–668 CrossRef CAS.
- I. Vassiliadou, A. Papadopoulos, D. Costopoulou, S. Vasiliadou, S. Christoforou and L. Leondiadis, Chemosphere, 2009, 74, 879–884 CrossRef CAS PubMed.
- Y.-H. Shih, S. J. e. Kasaon, C.-H. Tseng, H.-C. Wang, L.-L. Chen and Y.-M. Chang, Air Qual., Atmos. Health, 2016, 9, 201–211 CrossRef CAS.
- L. Bastian, J. Yano, Y. Hirai and S.-I. Sakai, J. Mater. Cycles Waste Manage., 2013, 15, 229–241 CrossRef CAS.
- B. K. Gullett, B. Wyrzykowska, E. Grandesso, A. Touati, D. G. Tabor and G. S. Ochoa, Environ. Sci. Technol., 2010, 44, 394–399 CrossRef CAS PubMed.
- B. Gworek, A. Hajduk, E. Koda, A. Grochowalski and A. Jeske, Chemosphere, 2013, 92, 753–759 CrossRef CAS PubMed.
- S. Weichenthal, D. Van Rijswijk, R. Kulka, H. You, K. Van Ryswyk, J. Willey, R. Dugandzic, R. Sutcliffe, J. Moulton, M. Baike, L. White, J.-P. Charland and B. Jessiman, Environ. Res., 2015, 142, 46–50 CrossRef CAS PubMed.
- A. T. Nair, J. Senthilnathan and S. M. S. Nagendra, Process Saf. Environ. Prot., 2019, 121, 143–154 CrossRef CAS.
- L. Chrysikou, P. Gemenetzis, A. Kouras, E. Manoli, E. Terzi and C. Samara, Environ. Int., 2008, 34, 210–225 CrossRef CAS PubMed.
- B. Sahariah, L. Goswami, I. U. Farooqui, P. Raul, P. Bhattacharyya and S. Bhattacharya, J. Geochem. Explor., 2015, 157, 100–109 CrossRef CAS.
- S. Kumar, S. G. Aggarwal, P. K. Gupta and K. Kawamura, Atmos. Environ., 2015, 108, 49–58 CrossRef CAS.
- R. Agarwal, K. Shukla, S. Kumar, S. G. Aggarwal and K. Kawamura, Atmos. Pollut. Res., 2020, 11, 554–565 CrossRef CAS.
- D. Perkins, M.-N. Brune Drisse, T. Nxele and D. Sly, Ann. Global Health, 2014, 80, 286–295 CrossRef PubMed.
- M. Iqbal, K. Breivik, J. H. Syed, R. N. Malik, J. Li, G. Zhang and K. C. Jones, Environm. Pollut., 2015, 207, 308–318 CrossRef CAS PubMed.
- M. Ackah, Environ. Sci. Pollut. Res., 2017, 24, 24092–24101 CrossRef PubMed.
-
J. Huisman, I. Botezatu, L. Herreras, M. Liddane, J. Hintsa, V. Luda di Cor temiglia, P. Leroy, E. Vermeersch, S. Mohanty, S. van den Brink, B. Ghenciu, D. Dimitrova, E. Nash, T. Shryane, M. Wieting, J. Kehoe, C. P. Baldé, F. Magalini, A. Zanasi, F. Ruini and A. Bonzio, Countering WEEE Illegal Trade (CWIT) Summary Repor t, Market Assessment, Legal Analysis, Crime Analysis and Recommendations Roadma, Lyon, France, 2015 Search PubMed.
-
V. Rotter, P. Maehlitz, N. Korf, P. Chancerel, J. Huisman, H. Habib, L. Herreras, S. Ljunggren and A. Hallberg, Prospecting Secondary raw materials in the Urban mine and Mining waste – Deliverable 4.1 – Waste Flow Studies, http://www.prosumproject.eu/sites/default/files/160324%20ProSUM%20Deliverable%20Report%20%204%201%20FINAL%20Submitted.pdf, 2016.
- S.-X. Quan, B. Yan, F. Yang, N. Li, X.-M. Xiao and J.-M. Fu, Environ. Sci. Pollut. Res., 2015, 22, 1290–1298 CrossRef CAS PubMed.
- Y. Liu, X. Huo, L. Xu, X. Wei, W. Wu, X. Wu and X. Xu, Sci. Total Environ., 2018, 624, 621–627 CrossRef CAS PubMed.
- Y. Wang, J. Hu, W. Lin, N. Wang, C. Li, P. Luo, M. Z. Hashmi, W. Wang, X. Su, C. Chen, Y. Liu, R. Huang and C. Shen, Environ. Int., 2016, 87, 33–41 CrossRef CAS PubMed.
- Y. Lin, X. Xu, Y. Dai, Y. Zhang, W. Li and X. Huo, Sci. Total Environ., 2016, 573, 760–766 CrossRef CAS PubMed.
- X. Tang, C. Shen, D. Shi, S. A. Cheema, M. I. Khan, C. Zhang and Y. Chen, J. Hazard. Mater., 2010, 173, 653–660 CrossRef CAS PubMed.
- Z. Wu, G. Gao and Y. Wang, Ecotoxicol. Environ. Saf., 2019, 180, 705–714 CrossRef CAS PubMed.
- A. K. Awasthi, M. Wang, M. K. Awasthi, Z. Wang and J. Li, Environ. Pollut., 2018, 243, 1310–1316 CrossRef CAS PubMed.
- M. Vaccari, G. Vinti, A. Cesaro, V. Belgiorno, S. Salhofer, M. I. Dias and A. Jandric, Int. J. Environ. Res. Public Health, 2019, 16, 1595 CrossRef CAS PubMed.
- B. H. Robinson, Sci. Total Environ., 2009, 408, 183–191 CrossRef CAS PubMed.
- B. Ericson, P. Landrigan, M. P. Taylor, J. Frostad and J. Caravanos, Ann. Global Health, 2017, 82, 686–689 CrossRef PubMed.
- P. Gottesfeld, F. H. Were, L. Adogame, S. Gharbi, D. San, M. M. Nota and G. Kuepouo, Environ. Res., 2018, 161, 609–614 CrossRef CAS PubMed.
- S. Mandić-Rajčević, Z. Bulat, V. Matović, M. Popević, M. Lepić, B. Mandić, M. Jovanović, V. Haufroid, M. Žarković and P. Bulat, Environ. Res., 2018, 167, 725–734 CrossRef PubMed.
- M. P. Taylor, C. F. Isley and J. Glover, Environ. Int., 2019, 127, 340–352 CrossRef CAS PubMed.
- Y. Yan, S. Yang, Y. Zhou, Y. Song, J. Huang, Z. Liu, Y. Wang and S. Wei, Environ. Int., 2020, 137, 105553 CrossRef CAS PubMed.
- K. Varshney, P. K. Varshney, K. Gautam, M. Tanwar and M. Chaudhary, Mater. Today: Proc., 2020, 26(2), 592–602 CAS.
- M. Singh, P. S. Thind and S. John, Chemosphere, 2018, 203, 426–433 CrossRef CAS PubMed.
- L. Carrizales, I. Razo, J. I. Téllez-Hernández, R. Torres-Nerio, A. Torres, L. E. Batres, A. C. Cubillas and F. Díaz-Barriga, Environ. Res., 2006, 101, 1–10 CrossRef CAS PubMed.
- M. P. Taylor, D. Camenzuli, L. J. Kristensen, M. Forbes and S. Zahran, Environ. Pollut., 2013, 178, 447–454 CrossRef CAS PubMed.
- ISO 26367-1:2011, Guidelines for assessing the adverse environmental impact of fire effluents – Part 1, General, 2011.
- A. A. Stec, K. Dickens, J. L. J. Barnes and C. Bedford, Chemosphere, 2019, 226, 576–586 CrossRef CAS PubMed.
- L. Bravo Diaz, H. He, Z. Hu, F. Restuccia, M. Marinescu, J. Varela Barreras, Y. Patel, G. Offer and G. Rein, J. Electrochem. Soc., 2020, 167, 090559 CrossRef.
-
J. Hemmerdinger, 2020, https://www.flightglobal.com/airframers/eviation-alice-fire-involved-lithium-ion-batteries-which-ignited-after-hours-of-powerplant-tests/141228.article, accessed 27.08.2021.
- X. Feng, M. Ouyang, X. Liu, L. Lu, Y. Xia and X. He, Energy Storage Mater., 2018, 10, 246–267 CrossRef.
-
H. Mai, 2019, https://www.utilitydive.com/news/aps-storage-facility-explosion-raises-questions-about-battery-safety/553540/, accessed 01.09.2021.
-
G. Hering, 2019, https://www.spglobal.com/marketintelligence/en/news-insights/latest-news-headlines/51900636, accessed 01.09.2021.
- DNV GL, McMicken Battery Energy Storage System Event Technical Analysis and Recommendations, Arizona Public Service, https://www.aps.com/-/media/APS/APSCOM-PDFs/About/Our-Company/Newsroom/McMickenFinalTechnicalReport.ashx?la=en&hash=50335FB5098D9858BFD276C40FA54FCE, 2020.
-
I. Exponent, Progress Report, APS McMicken, https://docket.images.azcc.gov/E000007939.pdf, 2020.
- Q. Wang, B. Mao, S. I. Stoliarov and J. Sun, Prog. Energy Combust. Sci., 2019, 73, 95–131 CrossRef.
- D. Sturk, L. Hoffmann and A. Ahlberg Tidblad, Traffic Inj. Prev., 2015, 16, S159–S164 CrossRef PubMed.
- J. Sun, J. Li, T. Zhou, K. Yang, S. Wei, N. Tang, N. Dang, H. Li, X. Qiu and L. Chen, Nano Energy, 2016, 27, 313–319 CrossRef CAS.
- P. A. Christensen, Z. Milojevic, M. S. Wise, M. Ahmeid, P. S. Attidekou, W. Mrozik, N. A. Dickman, F. Restuccia, S. M. Lambert and P. K. Das Methology, Appl. Therm. Eng., 2021, 116623 CrossRef CAS.
-
P. A. Christensen, Z. Milojevic, M. S. Wise, M. Ahmeid, P. S. Attidekou, W. Mrozik, N. A. Dickman, F. Restuccia, S. M. Lambert and P. K. Das, Appl. Therm. Eng., under review.
-
X. Vavasseur, 2020, https://www.navalnews.com/naval-news/2020/03/jmsdf-commissioned-its-1st-li-ion-battery-submarine-ss-511-js-oryu-%E3%81%8A%E3%81%86%E3%82%8A%E3%82%85%E3%81%86/, accessed 17.08.2021.
- Z. Zhou, M. Benbouzid, J. Frédéric Charpentier, F. Scuiller and T. Tang, Renewable Sustainable Energy Rev., 2013, 18, 390–400 CrossRef CAS.
-
M. Schuler, 2019, https://gcaptain.com/fire-and-gas-explosion-in-battery-room-of-norwegian-ferry-prompts-lithium-ion-power-warning, accessed 24.08.2021.
- M. J. Derewku, S. C. Gad, F. Gavigan and B. J. Dunn, J. Toxicol., Cutaneous Ocul. Toxicol., 1985, 4, 73–85 CrossRef.
- A. A. Stec, Fire Saf. J., 2017, 91, 79–90 CrossRef CAS.
- A. M. Bernardes, D. C. R. Espinosa and J. A. S. Tenório, J. Power Sources, 2004, 130, 291–298 CrossRef CAS.
- J. A. Guevara-García and V. Montiel-Corona, J. Environ. Manage., 2012, 95, S154–S157 CrossRef PubMed.
- M. Sun, X. Yang, D. Huisingh, R. Wang and Y. Wang, J. Cleaner Prod., 2015, 107, 775–785 CrossRef.
- Y. Yu, X. Wang, D. Wang, K. Huang, L. Wang, L. Bao and F. Wu, J. Hazard. Mater., 2012, 229–230, 455–460 CrossRef CAS PubMed.
- Y. Choi, K.-J. Chen and T. L. Marsh, J. Consum. Behav., 2020, 19, 382–396 CrossRef.
- K. M. Winslow, S. J. Laux and T. G. Townsend, Resour., Conserv. Recycl., 2018, 129, 263–277 CrossRef.
- F. Rodrigues dos Santos, E. de Almeida, P. D. da Cunha Kemerich and F. L. Melquiades, X-Ray Spectrom., 2017, 46, 512–521 CrossRef CAS.
- H. Omar and S. Rohani, Front. Chem. Sci. Eng., 2015, 9, 15–32 CrossRef CAS.
- N. P. Lebedeva and L. Boon-Brett, J. Electrochem. Soc., 2016, 163, A821–A830 CrossRef CAS.
-
J. Diekmann, M. Grützke, T. Loellhoeffel, M. Petermann, S. Rothermel, M. Winter, S. Nowak and A. Kwade, in Recycling of Lithium-Ion Batteries: The LithoRec Way, ed. A. Kwade and J. Diekmann, Springer International Publishing, Cham, 2018, pp. 39–51 Search PubMed.
- V. Kraft, W. Weber, B. Streipert, R. Wagner, C. Schultz, M. Winter and S. Nowak, RSC Adv., 2016, 6, 8–17 RSC.
- L. Terborg, S. Weber, F. Blaske, S. Passerini, M. Winter, U. Karst and S. Nowak, J. Power Sources, 2013, 242, 832–837 CrossRef CAS.
- M. Grützke, V. Kraft, B. Hoffmann, S. Klamor, J. Diekmann, A. Kwade, M. Winter and S. Nowak, J. Power Sources, 2015, 273, 83–88 CrossRef.
- U. Heider, R. Oesten and M. Jungnitz, J. Power Sources, 1999, 81-82, 119–122 CrossRef CAS.
- A. V. Plakhotnyk, L. Ernst and R. Schmutzler, J. Fluorine Chem., 2005, 126, 27–31 CrossRef CAS.
- T. Kawamura, S. Okada and J.-I. Yamaki, J. Power Sources, 2006, 156, 547–554 CrossRef CAS.
- E. Chalvatzaki, V. Aleksandropoulou and M. Lazaridis, Water, Air, Soil Pollut., 2013, 225, 1782 CrossRef.
- E. Chalvatzaki, V. Aleksandropoulou, T. Glytsos and M. Lazaridis, Waste Manage., 2012, 32, 2456–2468 CrossRef CAS PubMed.
- K. H. Lui, T. Jones, K. BéruBé, S. S. H. Ho, S. H. L. Yim, J.-J. Cao, S. C. Lee, L. Tian, D. W. Min and K. F. Ho, Chemosphere, 2019, 230, 578–586 CrossRef CAS PubMed.
- E. Chalvatzaki, I. Kopanakis, M. Kontaksakis, T. Glytsos, N. Kalogerakis and M. Lazaridis, Waste Manage., 2010, 30, 2058–2064 CrossRef CAS PubMed.
- L. Guan, Y. Liang, Y. Tian, Z. Yang, Y. Sun and Y. Feng, Sci. Total Environ., 2019, 659, 764–772 CrossRef CAS PubMed.
- S. Madhwal, V. Prabhu, S. Sundriyal and V. Shridhar, Atmos. Pollut. Res., 2020, 11, 156–169 CrossRef.
- A. E. Peter, S. M. Shiva Nagendra and I. M. Nambi, Atmos. Pollut. Res., 2018, 9, 1021–1031 CrossRef CAS.
- G. Feuyit, S. Nzali, J. N. Lambi and S. Laminsi, J. Chem., 2019, 2019, 3021894 Search PubMed.
- Y. Wang, K. Cheng, W. Wu, H. Tian, P. Yi, G. Zhi, J. Fan and S. Liu, Atmos. Environ., 2017, 152, 6–15 CrossRef CAS.
- D. W. Dockery, Ann. Epidemiol., 2009, 19, 257–263 CrossRef PubMed.
- S. K. Guttikunda and R. Goel, Environ. Dev., 2013, 6, 8–20 CrossRef.
- L. Koshy, T. Jones and K. BéruBé, Biomarkers, 2009, 14, 49–53 Search PubMed.
- A. D. Kappos, P. Bruckmann, T. Eikmann, N. Englert, U. Heinrich, P. Höppe, E. Koch, G. H. M. Krause, W. G. Kreyling, K. Rauchfuss, P. Rombout, V. Schulz-Klemp, W. R. Thiel and H. E. Wichmann, Int. J. Hyg. Environ. Health, 2004, 207, 399–407 CrossRef CAS PubMed.
- N. Englert, Toxicol. Lett., 2004, 149, 235–242 CrossRef CAS PubMed.
- N. Li, G. Chen, F. Liu, S. Mao, Y. Liu, S. Liu, Z. Mao, Y. Lu, C. Wang, Y. Guo, H. Xiang and S. Li, Environ. Res., 2020, 182, 109109 CrossRef CAS PubMed.
- S. Lee, W. Lee, D. Kim, E. Kim, W. Myung, S. Y. Kim and H. Kim, Environ. Res., 2019, 171, 313–320 CrossRef CAS PubMed.
- X. Chen, X. Li, X. Yuan, G. Zeng, J. Liang, X. Li, W. Xu, Y. Luo and G. Chen, Environ. Int., 2018, 116, 92–100 CrossRef PubMed.
- C. Chen, P. Zhu, L. Lan, L. Zhou, R. Liu, Q. Sun, J. Ban, W. Wang, D. Xu and T. Li, Environ. Res., 2018, 161, 188–194 CrossRef CAS PubMed.
- M. Kermani, M. Aghaei, M. Gholami, F. B. Asl, S. Karimzadeh, S. F. Jokandan and M. Dowlati, Iran Occup. Health, 2016, 13, 49–61 Search PubMed.
- G. R. Zosky, C. E. Boylen, R. S. Wong, M. N. Smirk, L. Gutiérrez, R. C. Woodward, W. S. Siah, B. Devine, F. Maley and A. Cook, Respirology, 2014, 19, 58–66 CrossRef PubMed.
- M. Gualtieri, E. Longhin, M. Mattioli, P. Mantecca, V. Tinaglia, E. Mangano, M. C. Proverbio, G. Bestetti, M. Camatini and C. Battaglia, Toxicol. Lett., 2012, 209, 136–145 CrossRef CAS PubMed.
- T. Maudgalya, A. Genaidy, G. Weckman, R. Shell, W. Karwowski and S. Wallace, Hum. Factors Ergon. Manuf., 2008, 18, 358–373 CrossRef.
- V. Sironval, L. Reylandt, P. Chaurand, S. Ibouraadaten, M. Palmai-Pallag, Y. Yakoub, B. Ucakar, J. Rose, C. Poleunis, R. Vanbever, E. Marbaix, D. Lison and S. van den Brule, Arch. Toxicol., 2018, 92, 1673–1684 CrossRef CAS PubMed.
- X. Feng, S. Zheng, X. He, L. Wang, Y. Wang, D. Ren and M. Ouyang, Front. Energy Res., 2018, 6 Search PubMed.
- Z. Liao, S. Zhang, K. Li, M. Zhao, Z. Qiu, D. Han, G. Zhang and T. G. Habetler, J. Energy Storage, 2020, 27, 101065 CrossRef.
- H. Wang, Y. Zhang, W. Li, C. Li and M. Ouyang, WSEAS Trans. Syst. Control, 2020, 15, 30–38 Search PubMed.
- J. C. Bertolini, J. Emerg. Med., 1992, 10, 163–168 CrossRef CAS.
- J. J. R. Kirkpatrick, D. S. Enion and D. A. R. Burd, Burns, 1995, 21, 483–493 CrossRef CAS PubMed.
-
R. A. Smith and K. Othmer, Encyclopedia of Chemical Technology, 2003, DOI:10.1002/0471238961.0825041819130920.a01.pub2.
- S. E. Sloop, J. K. Pugh, S. Wang, J. B. Kerr and K. Kinoshita, Electrochem. Solid-State Lett., 2001, 4, A42 CrossRef CAS.
- K. Dennerlein, F. Kiesewetter, S. Kilo, T. Jäger, T. Göen, G. Korinth and H. Drexler, Toxicol. Lett., 2016, 248, 25–33 CrossRef CAS PubMed.
- C. R. Fell, L. Sun, P. B. Hallac, B. Metz and B. Sisk, J. Electrochem. Soc., 2015, 162, A1916–A1920 CrossRef CAS.
- J. Self, C. P. Aiken, R. Petibon and J. R. Dahn, J. Electrochem. Soc., 2015, 162, A796–A802 CrossRef CAS.
- Z. Mao, M. Farkhondeh, M. Pritzker, M. Fowler and Z. Chen, J. Electrochem. Soc., 2017, 164, A3469–A3483 CrossRef CAS.
- D. J. Xiong, L. D. Ellis, R. Petibon, T. Hynes, Q. Q. Liu and J. R. Dahn, J. Electrochem. Soc., 2016, 164, A340–A347 CrossRef.
- H. Yang, G. V. Zhuang and P. N. Ross, J. Power Sources, 2006, 161, 573–579 CrossRef CAS.
- K. Tasaki, K. Kanda, S. Nakamura and M. Ue, J. Electrochem. Soc., 2003, 150, A1628–A1636 CrossRef CAS.
- S. S. Zhang, J. Power Sources, 2006, 162, 1379–1394 CrossRef CAS.
- A. R. Baird, E. J. Archibald, K. C. Marr and O. A. Ezekoye, J. Power Sources, 2020, 446, 227257 CrossRef CAS.
- R. Spotnitz and J. Franklin, J. Power Sources, 2003, 113, 81–100 CrossRef CAS.
- F. Diaz, Y. Wang, R. Weyhe and B. Friedrich, Waste Manage., 2019, 84, 102–111 CrossRef CAS PubMed.
-
M. Dennien, 2020, https://www.brisbanetimes.com.au/national/queensland/firefighter-injured-in-overnight-blaze-at-griffith-university-campus-20200316-p54aet.html, accessed 12.08.2021.
- CDC, Immediately Dangerous To Life or Health (IDLH) Values, https://www.cdc.gov/niosh/idlh/default.html.
- P. Ribière, S. Grugeon, M. Morcrette, S. Boyanov, S. Laruelle and G. Marlair, Energy Environ. Sci., 2012, 5, 5271–5280 RSC.
- A. Nedjalkov, J. Meyer, M. Köhring, A. Doering, M. Angelmahr, S. Dahle, A. Sander, A. Fischer and W. Schade, Batteries, 2016, 2, 5 CrossRef.
-
G. Atkinson, J. Hall and A. McGillivray, Review of Vapour Cloud Explosion Incidents, HSE Research Report RR1113, 2017.
- S. R. Samadder, R. Prabhakar, D. Khan, D. Kishan and M. S. Chauhan, Sci. Total Environ., 2017, 580, 593–601 CrossRef CAS PubMed.
- T. H. Christensen, P. Kjeldsen, P. L. Bjerg, D. L. Jensen, J. B. Christensen, A. Baun, H. J. Albrechtsen and G. Heron, Appl. Geochem., 2001, 16, 659–718 CrossRef CAS.
- P. Ghosh, I. S. Thakur and A. Kaushik, Ecotoxicol. Environ. Saf., 2017, 141, 259–270 CrossRef CAS PubMed.
-
K. Szymański and B. Janowska, - Archives of Environmental Protection L1 - http://journals.pan.pl/Content/102408/PDF/aep-2016-0026.pdf L2 - http://journals.pan.pl/Content/102408, 2016 DOI:10.1515/aep-2016-0026.
- Y. Xu, X. Xue, L. Dong, C. Nai, Y. Liu and Q. Huang, Waste Manage., 2018, 82, 156–166 CrossRef CAS PubMed.
- I. A. Talalaj, J. Water Chem. Technol., 2014, 36, 144–151 CrossRef.
- Y. Li, J. Li, S. Chen and W. Diao, Environ. Pollut., 2012, 165, 77–90 CrossRef CAS PubMed.
- J. Kapelewska, U. Kotowska, J. Karpińska, A. Astel, P. Zieliński, J. Suchta and K. Algrzym, Chem. Eng. J., 2019, 359, 790–800 CrossRef CAS.
- E. Bååth, Water, Air, Soil Pollut., 1989, 47, 335–379 CrossRef.
- T. Pennanen, J. Perkiömäki, O. Kiikkilä, P. Vanhala, S. Neuvonen and H. Fritze, FEMS Microbiol. Ecol., 1998, 27, 291–300 CrossRef CAS.
-
P. Nelson, S. Ahmed, K. Gallagher and D. Dees, Modeling the Performance and Cost of Lithium-Ion Batteries for Electric-Drive Vehicles, Argonne National Laboratory, USA, 2019 Search PubMed.
-
IEA, Global EV Outlook 2018, International Energy Agency, Paris, 2018 Search PubMed.
- M. Wentker, M. Greenwood and J. Leker, Energies, 2019, 12, 504 CrossRef CAS.
- M. A. Cusenza, S. Bobba, F. Ardente, M. Cellura and F. Di Persio, J. Cleaner Prod., 2019, 215, 634–649 CrossRef CAS PubMed.
- A. Prabhakar, S. Mishra and A. P. Das, Geomicrobiol. J., 2019, 36, 894–903 CrossRef CAS.
- K. Chatham-Stephens, J. Caravanos, B. Ericson, J. Sunga-Amparo, B. Susilorini, P. Sharma, P. J. Landrigan and R. Fuller, Environ. Health Perspect., 2013, 121, 791–796 CrossRef PubMed.
- S. Mishra, C. c. Rath and A. P. Das, Mar. Pollut. Bull., 2019, 140, 188–197 CrossRef CAS PubMed.
- X. Zeng, X. Xu, H. M. Boezen and X. Huo, Chemosphere, 2016, 148, 408–415 CrossRef CAS PubMed.
- Y. Yu, X. Zhu, L. Li, B. Lin, M. Xiang, X. Zhang, X. Chen, Z. Yu, Z. Wang and Y. Wan, Ecotoxicol. Environ. Saf., 2019, 169, 178–184 CrossRef CAS PubMed.
- F. N. Soetrisno and J. M. Delgado-Saborit, Sci. Total Environ., 2020, 717, 137099 CrossRef CAS PubMed.
- ATSDRHealth Public Statement for Nickel, 2005, https://www.atsdr.cdc.gov/ToxProfiles/tp15-c1-b.pdf, accessed 15.01.2021.
- H. Aral and A. Vecchio-Sadus, Ecotoxicol. Environ. Saf., 2008, 70, 349–356 CrossRef CAS PubMed.
- A. Chen, K. N. Dietrich, X. Huo and S.-M. Ho, Environ. Health Perspect., 2011, 119, 431–438 CrossRef PubMed.
- D. Pant, D. Joshi, M. K. Upreti and R. K. Kotnala, Waste Manage., 2012, 32, 979–990 CrossRef CAS PubMed.
- ATSDRHealth Public Statement for Cobalt, 2004, https://www.atsdr.cdc.gov/ToxProfiles/tp33-c1-b.pdf, accessed 15.01.2021.
- L. Leyssens, B. Vinck, C. Van Der Straeten, F. Wuyts and L. Maes, Toxicology, 2017, 387, 43–56 CrossRef CAS PubMed.
- D. H. P. Kang, M. Chen and O. A. Ogunseitan, Environ. Sci. Technol., 2013, 47, 5495–5503 CrossRef CAS PubMed.
- Y. Li, J. B. Richardson, R. Mark Bricka, X. Niu, H. Yang, L. Li and A. Jimenez, Waste Manage., 2009, 29, 2147–2150 CrossRef CAS PubMed.
- S. Yadav and S. Yadav, J. Environ. Manage., 2014, 144, 101–107 CrossRef CAS PubMed.
- S. Yadav, S. Yadav and P. Kumar, Waste Manage., 2014, 34, 1274–1278 CrossRef CAS PubMed.
- K. Richa, C. W. Babbitt and G. Gaustad, J. Ind. Ecol., 2017, 21, 715–730 CrossRef.
- M. N. Hang, I. L. Gunsolus, H. Wayland, E. S. Melby, A. C. Mensch, K. R. Hurley, J. A. Pedersen, C. L. Haynes and R. J. Hamers, Chem. Mater., 2016, 28, 1092–1100 CrossRef CAS.
- I. L. Gunsolus, M. N. Hang, N. V. Hudson-Smith, J. T. Buchman, J. W. Bennett, D. Conroy, S. E. Mason, R. J. Hamers and C. L. Haynes, Environ. Sci.: Nano, 2017, 4, 636–646 RSC.
- W. Yan, S. Yang, Y. Huang, Y. Yang and Y. Guohui, J. Alloys Compd., 2020, 819, 153048 CrossRef CAS.
- Q. Wang, L. Jiang, Y. Yu and J. Sun, Nano Energy, 2019, 55, 93–114 CrossRef CAS.
- S. W. D. Gourley, T. Or and Z. Chen, iScience, 2020, 23, 101505 CrossRef CAS PubMed.
- I. Overland, Energy Res. Soc. Sci., 2019, 49, 36–40 CrossRef.
- Z. V. Feng, B. R. Miller, T. G. Linn, T. Pho, K. N. L. Hoang, M. N. Hang, S. L. Mitchell, R. T. Hernandez, E. E. Carlson and R. J. Hamers, Environ. Sci.: Nano, 2019, 6, 305–314 RSC.
- P. L. Clement, J. E. Kuether, J. R. Borgatta, J. T. Buchman, M. S. Cahill, T. A. Qiu, R. J. Hamers, Z. V. Feng and C. L. Haynes, Chem. Res. Toxicol., 2020, 33, 806–816 Search PubMed.
- J. Bozich, M. Hang, R. Hamers and R. Klaper, Environ. Toxicol. Chem., 2017, 36, 2493–2502 CrossRef CAS PubMed.
- J. Chen, Z. Xiu, G. V. Lowry and P. J. J. Alvarez, Water Res., 2011, 45, 1995–2001 CrossRef CAS PubMed.
- N. J. Niemuth, B. J. Curtis, M. N. Hang, M. J. Gallagher, D. H. Fairbrother, R. J. Hamers and R. D. Klaper, Environ. Sci. Technol., 2019, 53, 3860–3870 CrossRef CAS PubMed.
- E. S. Melby, Y. Cui, J. Borgatta, A. C. Mensch, M. N. Hang, W. B. Chrisler, A. Dohnalkova, J. M. Van Gilder, C. M. Alvarez, J. N. Smith, R. J. Hamers and G. Orr, Nanotoxicology, 2018, 12, 1166–1181 CrossRef CAS PubMed.
- C. Mihai, W. B. Chrisler, Y. Xie, D. Hu, C. J. Szymanski, A. Tolic, J. A. Klein, J. N. Smith, B. J. Tarasevich and G. Orr, Nanotoxicology, 2015, 9, 9–22 CrossRef CAS PubMed.
- Y. Cui, E. S. Melby, A. C. Mensch, E. D. Laudadio, M. N. Hang, A. Dohnalkova, D. Hu, R. J. Hamers and G. Orr, Nano Lett., 2019, 19, 1990–1997 CrossRef CAS PubMed.
- W. Gwenzi, G. T. Kosta and N. Chaukura, Environ. Processes, 2018, 5, 611–629 CrossRef CAS.
- T. Fujimori, A. Eguchi, T. Agusa, N. M. Tue, G. Suzuki, S. Takahashi, P. H. Viet, S. Tanabe and H. Takigami, J. Mater. Cycles Waste Manage, 2016, 18, 599–607 CrossRef CAS.
- W. Lv, Z. Wang, H. Cao, Y. Sun, Y. Zhang and Z. Sun, ACS Sustainable Chem. Eng., 2018, 6, 1504–1521 CrossRef CAS.
- R. T. Delfino, T. S. Ribeiro and J. D. Figueroa-Villar, J. Braz. Chem. Soc., 2009, 20, 407–428 CrossRef CAS.
- V. Kraft, W. Weber, M. Grützke, M. Winter and S. Nowak, RSC Adv., 2015, 5, 80150–80157 RSC.
- D. C. Agourakis, I. M. C. De Camargo, M. B. Cotrim and M. Flues, Quim. Nova, 2006, 29, 960–964 CrossRef.
- A. M. Haregewoin, A. S. Wotango and B.-J. Hwang, Energy Environ. Sci., 2016, 9, 1955–1988 RSC.
- A. Eftekhari, Y. Liu and P. Chen, J. Power Sources, 2016, 334, 221–239 CrossRef CAS.
- H. Qi, Y. Ren, S. Guo, Y. Wang, S. Li, Y. Hu and F. Yan, ACS Appl. Mater. Interfaces, 2020, 12, 591–600 CrossRef CAS PubMed.
- N. V. Plechkova and K. R. Seddon, Chem. Soc. Rev., 2008, 37, 123–150 RSC.
-
P. Stepnowski, Sorption, Lipophiilicity and Partitioning phenomena of ionic liquids in environmental systems, Elsevier BV, 2007 Search PubMed.
- P. Stepnowski, W. Mrozik and J. Nichthauser, Environ. Sci. Technol., 2007, 41, 511–516 CrossRef CAS PubMed.
- W. Mrozik, C. Jungnickel, M. Skup, P. Urbaszek and P. Stepnowski, Environ. Chem., 2008, 5, 299–306 CrossRef CAS.
- W. Mrozik, J. Nichthauser and P. Stepnowski, Pol. J. Environ. Stud., 2008, 17, 383–388 CAS.
- W. Mrozik, A. Kotłowska, W. Kamysz and P. Stepnowski, Chemosphere, 2012, 88, 1202–1207 CrossRef CAS PubMed.
- W. Mrozik, C. Jungnickel, M. Paszkiewicz and P. Stepnowski, Water, Air, Soil Pollut., 2013, 224, 1759 CrossRef PubMed.
- W. Mrozik, J. Nichthauser and P. Stepnowski, Pol. J. Environ. Stud., 2008, 17, 383–388 CAS.
- M. Markiewicz, W. Mrozik, K. Rezwan, J. Thöming, J. Hupka and C. Jungnickel, Chemosphere, 2013, 90, 706–712 CrossRef CAS PubMed.
- Q. Miao and E. Bi, J. Environ. Manage., 2018, 223, 975–983 CrossRef CAS PubMed.
- D. Coleman and N. Gathergood, Chem. Soc. Rev., 2010, 39, 600–637 RSC.
- A. Jordan and N. Gathergood, Chem. Soc. Rev., 2015, 44, 8200–8237 RSC.
- S.-K. Ruokonen, C. Sanwald, M. Sundvik, S. Polnick, K. Vyavaharkar, F. Duša, A. J. Holding, A. W. T. King, I. Kilpeläinen, M. Lämmerhofer, P. Panula and S. K. Wiedmer, Environ. Sci. Technol., 2016, 50, 7116–7125 CrossRef CAS PubMed.
- T. P. Thuy Pham, C.-W. Cho and Y.-S. Yun, Water Res., 2010, 44, 352–372 CrossRef PubMed.
- B. Kudłak, K. Owczarek and J. Namieśnik, Environ. Sci. Pollut. Res., 2015, 22, 11975–11992 CrossRef PubMed.
- C.-W. Cho, S. Stolte and Y.-S. Yun, Sci. Rep., 2016, 6, 33403 CrossRef CAS PubMed.
- A. Latała, P. Stepnowski, M. Nędzi and W. Mrozik, Aquat. Toxicol., 2005, 73, 91–98 CrossRef PubMed.
- M. Amde, J.-F. Liu and L. Pang, Environ. Sci. Technol., 2015, 49, 12611–12627 CrossRef CAS PubMed.
- C. Pretti, C. Chiappe, I. Baldetti, S. Brunini, G. Monni and L. Intorre, Ecotoxicol. Environ. Saf., 2009, 72, 1170–1176 CrossRef CAS PubMed.
- P. Stepnowski, A. C. Skladanowski, A. Ludwiczak and E. Laczyńska, Hum. Exp. Toxicol., 2004, 23, 513–517 CrossRef CAS PubMed.
- X.-D. Hou, Q.-P. Liu, T. J. Smith, N. Li and M.-H. Zong, PLoS One, 2013, 8, e59145 CrossRef CAS PubMed.
- N. S. M. Vieira, S. Stolte, J. M. M. Araújo, L. P. N. Rebelo, A. B. Pereiro and M. Markiewicz, ACS Sustainable Chem. Eng., 2019, 7, 3733–3741 CrossRef CAS.
- Z. Milojevic, P. S. Attidekou, M. Muhammad, M. Ahmeid, S. Lambert and P. K. Das, J. Power Sources, 2021, 506, 230242 CrossRef CAS.
- C. Jin, J. Nai, O. Sheng, H. Yuan, W. Zhang, X. Tao and X. W. Lou, Energy Environ. Sci., 2021, 14, 1326–1379 RSC.
- S. S. Sharma and A. Manthiram, Energy Environ. Sci., 2020, 13, 4087–4097 RSC.
- M. Fleischhammer, T. Waldmann, G. Bisle, B.-I. Hogg and M. Wohlfahrt-Mehrens, J. Power Sources, 2015, 274, 432–439 CrossRef CAS.
- D. Ren, H. Hsu, R. Li, X. Feng, D. Guo, X. Han, L. Lu, X. He, S. Gao, J. Hou, Y. Li, Y. Wang and M. Ouyang, eTransportation, 2019, 2, 100034 CrossRef.
- S. Bertilsson, F. Larsson, M. Furlani, I. Albinsson and B.-E. Mellander, J. Power Sources, 2017, 365, 446–455 CrossRef CAS.
-
A. I. Ilieş, I. Ciascai and D. Pitică, 2019 42nd International Spring Seminar on Electronics Technology (ISSE), 2019 DOI:10.1109/ISSE.2019.8810304.
- J. Liu, Q. Duan, M. Ma, C. Zhao, J. Sun and Q. Wang, J. Power Sources, 2020, 445, 227263 CrossRef CAS.
- BSI_Group, BS EN 63330 Ed.1.0 Requirements for reuse of secondary batteries, 2021, accessed 30.08.2021.
-
BSI_Group, BS EN 63338 Ed.1.0 General guidance for reuse of secondary cells and batteries, 2021, accessed 30.08.2021.
- E. Cabrera-Castillo, F. Niedermeier and A. Jossen, J. Power Sources, 2016, 324, 509–520 CrossRef CAS.
- INERIS, DRA06 – Opération B3, Seconde vie des batteries Li-ion, INERIS, MINISTERE DE LA TRANSITION ECOLOGIQUE ET SOLIDAIRE, 2020.
-
NFPA, 2020, https://www.nfpa.org/codes-and-standards/all-codes-and-standards/list-of-codes-and-standards/detail?code=855.
- Electrical_Regulatory_Authorities_Council_(ERAC), 2021.
-
R. Coombes, Beginners guide: UN3480, UN3481 & IATA regulations, 2021, accessed 30.08.2021.
-
HSE, https://www.hse.gov.uk/cdg/manual/index.htm, 2011, accessed 14.09.2021.
|
This journal is © The Royal Society of Chemistry 2021 |
Click here to see how this site uses Cookies. View our privacy policy here.