DOI:
10.1039/D0EE03659E
(Analysis)
Energy Environ. Sci., 2021,
14, 3679-3685
Is direct seawater splitting economically meaningful?
Received
19th November 2020
, Accepted 8th June 2021
First published on 9th June 2021
Abstract
Electrocatalytic water splitting is the key process for the formation of green fuels for energy transport and storage in a sustainable energy economy. Besides electricity, it requires water, an aspect that seldomly has been considered until recently. As freshwater is a limited resource (<1% of earth's water), lately, plentiful reports were published on direct seawater (around 96.5% of earth's water) splitting without or with additives (buffers or bases). Alternatively, the seawater can be split in two steps, where it is first purified by reverse osmosis and then split in a conventional water electrolyser. This quantitative analysis discusses the challenges of the direct usage of non-purified seawater. Further, herein, we compare the energy requirements and costs of seawater purification with those of conventional water splitting. We find that direct seawater splitting has substantial drawbacks compared to conventional water splitting and bears almost no advantage. In short, it is less promising than the two-step scenario, as the capital and operating costs of water purification are insignificant compared to those of electrolysis of pure water.
Broader context
Due to the large fluctuation of wind and solar power plants, highly scalable energy storage technologies are required to meet the constant energy demand of society. In this regard, the conversion of electricity to chemical energy in form of fuels is suitable due to the easy storability of fuels in tanks compared to resource and cost intensive production of batteries. The key process for chemical energy conversion is water splitting during which hydrogen and oxygen is formed. Hydrogen can directly be stored, transported, and reconverted into electricity in a fuel cell or used to produce other fuels such as methanol, ammonia, or liquid organic hydrogen carriers. On the other hand, molecular oxygen is a useful source of ‘breathable’ oxygen for air exchange systems. Electrolysis of water requires water and electricity. As freshwater is a limited resource, for the hydrogen and oxygen production, several reports on the direct use of seawater with or without additives have recently been published. In this quantitative analysis, we investigate the economic implications of direct seawater splitting and find that they are less promising than previously discussed.
|
For the implementation of a sustainable energy economy, the greatest challenge is the weather-depending, fluctuating electricity production of wind and solar power plants.1,2 To meet this challenge and to satisfy the constant energy demand of society, electricity must be stored in times of overproduction to provide energy when little sunshine and wind is available.1–4 To store the green electricity in a highly scalable way, it must be converted into chemical energy.1–4 The central process for this conversion is electrocatalytic water splitting in which hydrogen and oxygen are formed.1 Hydrogen can directly be stored, transported, and reconverted into electricity in a fuel cell.1,4,5 Further, hydrogen is the starting point for the formation of other fuels such as methanol, ammonia, or liquid organic hydrogen carriers.1,4 Due to the central role of water splitting in a sustainable energy economy, the cost efficiency of this process is crucial and even one percent could save billions of dollars.6,7
More than half of the costs of electrolytic hydrogen production are caused by the required electricity, and, besides that, the capital cost of the electrolyser is another major part.6,8 Additionally, H2O is needed for water splitting. However, so far, this aspect has seldom been considered. As 96.5% of the global water is seawater and less than 1% is nonfrozen freshwater,9 direct seawater splitting (DSS, in this report DSS includes the usage of non-purified seawater with or without the addition of additives such as bases or buffers) seems desirable.10,11 In this regard, recently, several reports on DSS have been published and various arguments in favour of it were raised: (i) freshwater is a limited resource and 80% of the world's population faces a high risk concerning water security while seawater is easily available;11,12 (ii) green energy technologies should not compete with basic human needs such as food and drinking water;13 (iii) omitting the water purification units leads to more compact design resulting in fewer system engineering challenges, lower capital costs, less maintenance, and smaller required space;10,14 (iv) energy intensive desalination is avoided.15 These arguments can be claimed to be especially important as the price of renewable electricity varies strongly with the location and particularly dry coastal regions with limited excess to freshwater are often suitable for cheap energy production, followed by chemical energy conversion and transportation of the fuels via the ocean.1,10,16,17 At a first glance, these arguments seem convincing and have led to substantial interest in DSS with several elaborate publications in high quality journals.10,11,14,15,18–29 However, as pointed out in a recent review article on DSS published in the journal Nature Energy,11 “a comprehensive review with up-to-date costs is still needed.” Indeed, so far, all reports rely on the aforementioned qualitative arguments or assume large cell voltages of 4.5 V for DSS in contrast to currently reported seawater electrolysers, and no investigation exists that compares the costs for the purification of seawater with those of splitting it.17,22,30
Herein, we answer the question: can DSS (see Fig. 1 left) be competitive to a two-step scenario where seawater is first purified and subsequently split (see Fig. 1 right)? To do so, we first outline the challenges of DSS and then compare the two scenarios by evaluating the thermodynamic requirements, the energy consumption of real devices, the complexity and size of these devices, their capital costs, and finally the price of freshwater gained from seawater with that of green hydrogen. We uncover that the costs for the purification of seawater are insignificant compared to those needed to split water. Further, the direct use of seawater implies great challenges. Nevertheless, our findings lead to another question which we briefly discuss: which water purity is economically most suitable as feed for electrolysers?
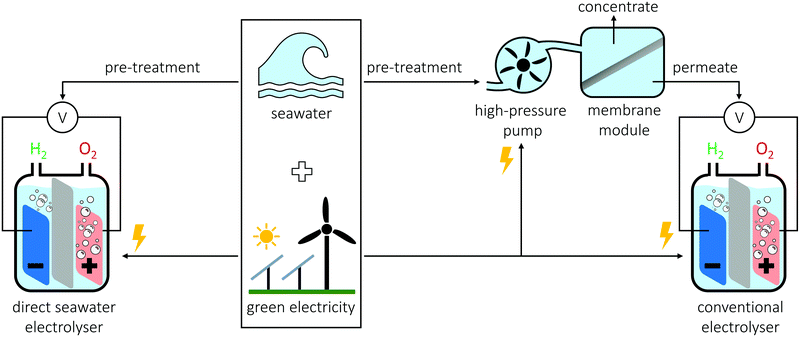 |
| Fig. 1 Two ways to make hydrogen from seawater and green electricity. The pathway on the left shows DSS where only one device is required. In the pathway on the right, the seawater is first desalinated by reverse osmosis and then the water splitting is performed. For this pathway, electricity and a device are required for both, the desalination and the actual water splitting. | |
The challenges of DSS
The composition of seawater
Seawater potentially contains every on earth possible impurity.31 It is not only a mixture of water and dissolved inorganic salts (3.5 weight% on average), but also contains charged and uncharged small organic molecules, polymers (microplastic), living organisms, and dissolved gases (see Table 1).31 Further, the composition of seawater is a function of the location, the weather, the season, and changes over time due to anthropogenic influences such as the arising of microplastic or global warming.31,32 Therefore, an electrolyser that can operate with seawater from the Arabian Gulf might not be compatible with seawater from Taiwan.33
Table 1 Average concentration of the major constituents in surface seawater with a salinity of 3.5% at 20 °C31
Species |
Conc. [ppm] |
Cl− |
19 400 |
Na+ |
10 800 |
SO42− |
2700 |
Mg2+ |
1300 |
Ca2+ |
400 |
K+ |
400 |
HCO3− |
100 |
Br− |
70 |
B(OH)3/B(OH)4− |
30 |
CO32− |
10 |
Sr2+ |
10 |
F− |
1 |
Other inorg. elements |
0.6 |
Organic matter |
1–2 |
Dissolved gases (mainly N2, O2, Ar) |
19 |
Chloride oxidation and gas separator deactivation
As can be seen from Table 1, the most abundant ions in seawater are Na+ and Cl−. While Na+ is usually no harm to water electrolysers without cation exchange membrane, Cl− can be oxidised in a competing reaction to the oxygen evolution reaction (OER) producing toxic, environmentally harmful, and corrosive ClO− or Cl2.34 It should be noted here that the presence of the latter during DSS impairs the purity of dioxygen generated from OER and hence its suitability as ‘breathable’ oxygen in air exchange systems. Even though ClO− and Cl2 are value added chemicals, their demand is orders of magnitude smaller than the projected hydrogen demand in a partially hydrogen based energy economy.29
† Additionally, the transportation costs of chlorine are high and thus in Europe only 5–6% of the Cl2 is transported.29 We also want to note here that for the well-established chlor-alkali process, where NaCl is a substrate, no seawater is used due to the high sensitivity of the electrolyser membranes towards water impurities.35 Many recent studies have focused on the issue of undesired chlorine oxidation in DSS and found that it can be avoided by operating at a pH larger than 7.5, where the thermodynamic overpotential of the OER is 480 mV smaller than that of Cl− oxidation.10,11,21,22,29 A more severe problem is that ions from seawater can deactivate the ion exchange membranes or diaphragms of the electrolysers.10,21,22,35,36 In this regard, recently reported alkaline-exchange-membrane direct-seawater electrolysers show rapid deactivation within a few hundred hours, even when ultra-high purity water with NaCl additives is used and are not meeting industrial requirements with stack lifetimes of >60
000 h.21,22,37 Further, high purity water with NaCl does not represents the complexity of seawater.31
Learning from on-site hypochlorite generators
A more realistic picture of the problems DSS faces can be gained from on-site hypochlorite generators, a technology established since the early 1970s for industrial water cooling systems.33,38 There, low concentrated hypochlorite is used to avoid the growth of marine organisms as they tend to foul equipment and worsen heat transfer.33,34,38 The hypochlorite is formed by direct oxidation of Cl− from the filtered seawater feed. The electrolysers are one compartment cells made of titanium, and the electrodes are comprised of a titanium core with a precious metal oxide coating (Ru, Ir, Pt).33 Regular cleaning with hydrochloric and sulfamic acids and/or large flow rates are needed to withstand Mg/Ca(OH)2 and Ca(CO3) precipitation.33 Other problems are adhesion by F−, deposition of colloids such as alumino-silicate clays, and the deposition of aliphatic organic compounds.38 The original purpose of the hypochlorite generators presents another problem, which is biological fouling. It can occur in electrolysers operating with buffered or pure seawater. In direct seawater electrolysers working at high pH, water purification is unavoidable, as the rise of pH will lead to direct precipitation of the alkaline earth metals of the seawater.30 Further, water splitting electrolysers contain impurity sensitive gas seperators,21,22,36 should work at a minimal overpotential and maximum efficiency,6 and produce high purity gases.39
Seawater requires additives or membranes
Seawater without additives can in principle be used to split water, but it will lead to lower efficiencies, as the minute concentration of H+, OH−, or buffer molecules cannot sufficiently transport the OH− and H+ formed at the cathode and anode, respectively.40,41 The resulting local pH differences unfavourably change the thermodynamics of the hydrogen and oxygen evolution half reactions and might cause precipitation of various species such as earth alkali hydroxides.11,30 Further, the conductivity of pure seawater is low resulting in significant potential losses.19,31 To prevent a pH gradient and to overcome the low conductivity, either a buffer, a base, or an acid can be added.11,19 This will increase the cost of the water feed by several orders of magnitude (e.g., price of deionized water <2 US$ t−1 compared to >800 US$ t−1 KOH and >100 US$ t−1 H2SO4).42–44 In contrast, if high purity water is used, the acid and base can remain for a long time in the electrolyser, and, as only H2O is consumed, it is sufficient to simply add relatively cheap high purity water without additives. Such an operation with seawater is challenging as it will continuously increase the concentration of the seawater impurities in the electrolyser until they precipitate. The usage of a solid electrolyte membrane can potentially avoid additives; however, currently, such membranes are sensitive to impurities that block the ion-exchange sites resulting in membrane deactivation and/or high maintenance costs.11,21,35 Further, even though impurity sensitive proton exchange membrane electrolysers are operated without additives, commercialised alkaline exchange membrane electrolysers work with mild KOH solutions, and the addition of additives was also reported to be beneficial in membrane based cells for DSS.22,45
The outlined problems indicate that, for a direct seawater electrolyser, the water feed-, the maintenance-, and the capital costs will be higher and the efficiency lower when compared to a conventional electrolyser. Nevertheless, as an advantage, no purification of the seawater is needed (see Fig. 1). To find out, whether avoiding water purification justifies to endorse the disadvantages arising from a non-purified seawater feed, we compare the costs of seawater desalination with those of water splitting in the subsequent sections.
The costs of seawater desalination vs. water splitting
To compare seawater purification with water splitting, we evaluated the different energetical and economic aspects to produce 1 kg of purified water from seawater and to split 1 kg of water. The results of this comparison are graphically summarized in Fig. 2.
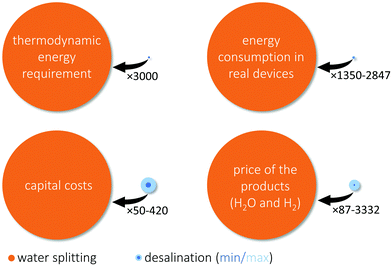 |
| Fig. 2 Comparison of water splitting and water desalination. The areas of the circles represent the required energy or price of water splitting (orange) and for desalination (blue) of the same amount of water. For the H2O and H2 prices, a ratio of 9 : 1 H2O : H2 was used, as 1 kg of water yields 1/9 kg of H2. The figure reveals that the energetic demand and the costs to desalinate seawater are insignificant compared to those required to split water. | |
Thermodynamics
For the thermodynamic estimation, the two processes will be simplified to the following two reaction equations: | 1.035 kg 0.6 M NaCl(aq) → 1 kg H2O(l) + 0.035 kg NaCl(s) | (1) |
| 1 kg H2O(l) → 0.11 kg H2(g) + 0.89 kg O2(g) | (2) |
Both processes are endergonic. Therefore, additional energy input is required to drive them. Process (1) is actually exotherm, but, due to entropic constraints, the standard free Gibbs energy, ΔG0, is 5.4 kJ kgwater−1.46,47
‡ Predominantly, the side product of seawater purification is not solid NaCl but concentrated brine, and then the required free energy is even lower (2.73 kJ kg−1 in the context of reverse osmosis with a vanishing recovery rate).48 Process (2) is endotherm and to accomplish it thermoneutrally 15
888 kJ kgwater−1 are needed (ΔH0 = 286 kJ mol−1).47 These thermodynamic considerations give a lower boundary on the specific energy consumption and the resulting costs of these two processes. They show that thermodynamically it takes around 3000 times more energy to split water than to desalinate seawater (see Fig. 2). This large difference results from the circumstances that, in water desalination, only a salt must be crystallized or a salt free solution together with a higher concentrated one has to be formed, while, in water splitting, strong covalent O–H bonds must be broken. Thus, if there are no technological restrictions for all processes (seawater purification, conventional water splitting, and DSS) one can only save 0.03% (1/3000) of the energy when using seawater directly instead of purifying it which is in stark contrast to the challenges of DSS. However, not only thermodynamics are relevant as real devices are imperfect and their efficiency must be considered.
Energy consumption
Seawater purification can be performed in many ways.49 Herein, we will focus on reverse osmosis (RO), which, in 2016, accounted for around 66% of the global water desalination.50 In reverse osmosis, the seawater is pressed through a water selective membrane, which is impermeable for the salt species. The specific energy consumption for RO has dropped constantly in the last decades,51 and modern plants require around 2.5 to 4 kWh m−3 (9.0–14.4 kJ kgwater−1) for the membrane process, which accounts for approximately 71% of the total energy consumption (the rest of the energy is needed for the water delivery, pre-treatments, and others).49 For acidic and alkaline electrolysers, a voltage efficiency (based on the higher heating value, VHHV = 1.48 V) of 62–82% was previously estimated.37 This efficiency range yields a specific energy consumption of 19
376–25
627 kJ kgwater−1.§ So, considering the efficiencies of real devices, around 1350–2847 times more energy is needed to split water compared to desalinate seawater (see Fig. 2).
Device complexity
An advantage of DSS is that only one device is needed, the electrolyser, instead of two, the water purification unit and the electrolyser (see Fig. 1). In the following, we compare the complexity of these two devices to investigate how big this advantage is. For both direct and indirect seawater splitting, water intake and a pre-treatment (e.g., filtration) units to remove solids are required.51,52 For a RO unit, the key parts are a high-pressure pump and a membrane module (see Fig. 1). The pump feeds the pre-treated seawater to the water selective membrane, where a demineralized water permeate and a concentrate containing the retained salts are produced.49,51 1 m2 of membrane produces around 1000 kg of desalinated water per day.53 In comparison, an electrolyser generally is comprised of a gas collector and two electrodes separated by a gas separator (membrane or diaphragm). Note that alone the gas separator of a proton exchange membrane electrolysers is more than an order of magnitude more expensive than a RO membrane.14 An electrolyser operating at a current density of 1 A m−2 consumes around 8 kg of water per day per 1 m2 of electrochemical cell (gas separator plus two electrodes).¶ Thus, for water splitting, around 125 times more geometrical surface area electrochemical cell is required than surface area membrane for water purification. Considering the higher complexity of the electrochemical cell compared to the water selective membrane, the water purification units are tiny and cheap compared to the electrolysers.
Capital costs
A direct comparison of the capital cost of an electrolyser and a RO device bears some challenges. On the one side, RO is a mature technology and databases with the capital costs of more than 4000 RO plants exist including estimations of learning and scaling effects on the costs;50 on the other side, a vanishingly small number of water electrolysers have been built compared to the amount required for a hydrogen based energy economy. Hence, a realistic estimation of the future capital costs of an electrolyser is more challenging. Therefore, we rely on an expert elicitation study for the estimation of the water electrolyser capital costs.37
The average capital costs of RO plants installed in 2015 were 2.07 US$ for a unit producing 1 kg desalinated water per day.50 As comparatively little water is required for hydrogen production, the required desalination plants might have small capacities, which will increase their capital costs beyond average due to economy of scale.50 To take this into consideration 2–4 US$ (kgwater day−1)−1 capital costs were assumed. For water electrolysers, the expert elicitation yielded capital costs of 912–2850 US$ for units consuming 1 kW of electricity.37 Assuming again a voltage efficiency of 62–82%,37 the electrolyser costs are 203–838 US$ (kgwater day−1)−1.|| Therefore, the capital costs of an electrolyser are around 50 to 420 times higher than those for a water desalination device purifying the required amount of water (see Fig. 2). Furthermore, independently of the water electrolysers, desalination facilities might be required for the workers of the hydrogen production facility with its infrastructure and can also provide fresh water to the surrounding area.
The price of purified seawater and H2
The ultimate criterion of comparison is the price of the substrate, freshwater from seawater, and the product, green hydrogen. As the prices of desalinated water and green hydrogen strongly depend on the local energy costs (46–73% of overall costs for RO water desalination and 59–68% for green hydrogen production)54,55 and the capacity factor,8 only a comparably large price range can be given. In 2019, for the G20 summit, the international energy agency estimated the price of hydrogen from renewables to 2.5–6.0 US$ kg−1.56 The price of desalinated water from seawater was estimated to be 0.2–3.2 US$ m−3, when conventionally produced energy is used.57 This makes the hydrogen 87–3332 times more expensive than the desalinated seawater (see Fig. 2).** The price for water desalination could be higher when renewable sources are used.58 However, the electrolysers should be situated at a location with minimal energy costs to produce affordable hydrogen; therefore, energy costs should be low, but the energy supply might be fluctuating leading to a lower capacity factor. For both technologies, a higher price limit can be given when the costs for a direct coupling to a photovoltaic device is analysed. In such a scenario, the price for seawater desalination was estimated to be 4–11 US$ m−3 and for green hydrogen production 12.1 US$ kg−1.58,59 Thus, under these conditions, the hydrogen is 122–336 times more expensive than the desalinated water. In conclusion, the water desalination step will at most increase the price of the hydrogen by 1%, but most likely the increase will be smaller.
Fresh water consumption
Another point we want to briefly discuss is the consumption of fresh water by water splitting compared to freshwater consumption in general. The global freshwater consumption was approximated to be 4.0 × 1015 kg per year and the global electricity consumption 2.3 × 1013 kWh per year (total global primary energy consumption 1.2 × 1014 kWh per year).60,61 Potentially, around 33 kWh of for electricity can be made from 1 kg hydrogen and 9 kg of water is needed to produce it. Assuming an efficiency of 40% for the applied fuel cells and that all worldwide consumed electricity would be produced from green hydrogen, only 1.6 × 1013 kg per year of freshwater would be required to so, which would be less than 0.4% of the global freshwater consumption (for all primary energy, it would be around 2%).†† Thus, even in a fully established hydrogen economy, the freshwater consumption for water splitting is marginal.
Conclusion
As Fig. 2 shows, the energy requirements, the capital and operating costs of seawater desalination are marginal compared to those of water splitting. Thus, the benefits of direct seawater splitting are insignificant. However, as indicated in this analysis, the disadvantages are considerably large. The electrolyser lifetime is threatened by every possible kind of unavoidable impurity, an always changing feed as seawater changes seasonally and topologically, corrosive Cl− oxidation species, precipitation of solids, blocking of the ion exchange membranes, and biofouling. Further, with current technology, a direct seawater electrolyser must be operated at a high flow velocity and a design that facilitates to wash deposited species away is required, and regular acid cleanings might be required and these aspects lead to increase capital and operating costs. Additionally, the feed of a direct seawater electrolyser might be magnitudes more expensive if additives are used (acids, bases, buffers) or the conductivity and ion transport properties of the electrolyte will be low leading to significant efficiency losses. Considering these aspects, currently, DSS is less promising. Further, if all the challenges are overcome, the potential cost reduction of the seawater feed compared to a freshwater feed is below 1%, as freshwater is relatively cheap (<2 US$ t−1) and readily available in places were seawater and electricity is accessible. This suggests that further studies should focus on the development of the more promissing two-step process including a purification step. In this regard, innovative ideas to combine both processes in one device have recently been reported by Veroneau and Nocera.62 An insightful comparison to DSS is the one to crude oil: the costs for crude oil purification (refinery) are often as high as 16% of the final fuel prices (e.g., for a crack spread of 12 US$ bbl−1 and a crude oil price of 60 US$ bbl−1).63 Nevertheless, even though the relative purification costs for crude oil based fuels (16%) are more than a magnitude larger than those for seawater (below 1% of the hydrogen price), in the last century, no car has been commercialized that directly runs on crude oil.
Is freshwater pure enough?
So far, we discussed the formation of freshwater (<500 ppm dissolved salts) out of seawater (around 35
000 ppm dissolved salts).64 However, conventional electrolysers, especially proton exchange membrane electrolysers, are usually fed with purer water (<10 ppm dissolved salts).11,21 To further purify the freshwater obtained from seawater, again, RO can be used.65 In this regard, it has been demonstrated on the laboratory scale that passing the permeate from seawater RO a second time (two-pass RO) can reduce the salt content to less than 5 ppm.66 The second pass consumes little energy and less than 3 kWh m−3 were required in sum for both passes. The costs of such treated seawater were 0.80 US$ m−3, which is lower than the higher estimate used in this work for freshwater production from seawater. Using RO together with electron deionization and starting from freshwater, it was demonstrated that ultra-high purity water with less than 0.5 ppm salt content could be produced at a cost of only 0.53 US$ m−3.42 These examples show that, even when the seawater is purified to ultra-high purity water, it will probably account for less than 0.3% of the hydrogen price.‡‡ Besides inorganic salts, it might be beneficial to remove organic molecules and dissolved gases from the feed water which can be done with ultraviolet oxidation and a vacuum degasifier, respectively.65 Such additional steps will further increase the water feed costs but might be beneficial for the produced hydrogen purity and the electrolyser lifetime. Thus, the most cost-efficient water purity will depend on the electrolyser type and possibly also on the desired hydrogen purity. So far, alkaline electrolysers seem to tolerate higher impurities than ion exchange membrane ones.10,11 To find the optimal water purity, long term effects of low concentrated species in purified water have to be investigated. In this regard, the plentiful high-quality reports on DSS can be of fundamental importance as they uncovered several issues related to water impurities and found solutions for some of them. Future works can profit from this knowledge when investigating the water feed purity in relation to the electrolyser lifetime, the produced gas purity, and the hydrogen costs.
Author contributions
J. N. H. initiated the idea and developed it together with P. W. M., J. N. H. wrote the first draft. M. D. and P. W. M. supervised the study. All Authors (J. N. H., P. W. M., R. S., M. D.) designed the analysis, discussed the results, and commented on the manuscript.
Conflicts of interest
The authors declare no competing interests.
Acknowledgements
We are grateful to the Einstein Center of Catalysis (EC2) for financial support. This project was also funded by the Deutsche Forschungsgemeinschaft (DFG, German Research Foundation) under Germany's Excellence Strategy – EXC 2008 – 390540038 – UniSysCat.
References
- R. Schlögl, Angew. Chem., Int. Ed., 2019, 58, 343–348 Search PubMed.
- N. S. Lewis and D. G. Nocera, Proc. Natl. Acad. Sci. U. S. A., 2006, 103, 15729–15735 Search PubMed.
- H. B. Gray, Nat. Chem., 2009, 1, 7 Search PubMed.
- Z. W. Seh, J. Kibsgaard, C. F. Dickens, I. Chorkendorff, J. K. Nørskov and T. F. Jaramillo, Science, 2017, 355, eaad4998 Search PubMed.
- Y. Shao-Horn, I. E. L. Stephens, J. Peng, R. R. Rao, M. Risch, C. Wei, Z. J. Xu and B. Huang, Adv. Mater., 2019, 31, 1806296 Search PubMed.
- O. J. Guerra, J. Eichman, J. Kurtz and B. M. Hodge, Joule, 2019, 3, 2425–2443 Search PubMed.
- O. J. Guerra, J. Zhang, J. Eichman, P. Denholm, J. Kurtz and B.-M. Hodge, Energy Environ. Sci., 2020, 13, 1909–1922 Search PubMed.
- D. V. Esposito, Joule, 2017, 1, 651–658 Search PubMed.
- S. Ahmadvand, B. Abbasi, B. Azarfar, M. Elhashimi, X. Zhang and B. Abbasi, Water, 2019, 11, 696 Search PubMed.
- S. Dresp, F. Dionigi, M. Klingenhof and P. Strasser, ACS Energy Lett., 2019, 4, 933–942 Search PubMed.
- W. Tong, M. Forster, F. Dionigi, S. Dresp, R. Sadeghi Erami, P. Strasser, A. J. Cowan and P. Farràs, Nat. Energy, 2020, 5, 367–377 Search PubMed.
- S. Fukuzumi, Y. Lee and W. Nam, ChemSusChem, 2017, 10, 4264–4276 Search PubMed.
- R. C. Forsythe and A. M. Müller, Catal. Today, 2020 DOI:10.1016/j.cattod.2020.06.011.
- L. Shi, R. Rossi, M. Son, D. M. Hall, M. A. Hickner, C. A. Gorski and B. E. Logan, Energy Environ. Sci., 2020, 13, 3138–3148 Search PubMed.
- B. C. M. Martindale and E. Reisner, Adv. Energy Mater., 2016, 6, 1–9 Search PubMed.
- H. Apostoleris, S. Sgouridis, M. Stefancich and M. Chiesa, Nat. Energy, 2018, 3, 1109–1114 Search PubMed.
- R. D’Amore-Domenech and T. J. Leo, ACS Sustainable Chem. Eng., 2019, 7, 8006–8022 Search PubMed.
- A. J. Esswein, Y. Surendranath, S. Y. Reece and D. G. Nocera, Energy Environ. Sci., 2011, 4, 499–504 Search PubMed.
- S. Gao, G.-D. Li, Y. Liu, H. Chen, L.-L. Feng, Y. Wang, M. Yang, D. Wang, S. Wang and X. Zou, Nanoscale, 2015, 7, 2306–2316 Search PubMed.
- W. Xu, F. Lyu, Y. Bai, A. Gao, J. Feng, Z. Cai and Y. Yin, Nano Energy, 2018, 43, 110–116 Search PubMed.
- S. Dresp, F. Dionigi, S. Loos, J. Ferreira de Araujo, C. Spöri, M. Gliech, H. Dau and P. Strasser, Adv. Energy Mater., 2018, 8, 1800338 Search PubMed.
- S. Dresp, T. Ngo Thanh, M. Klingenhof, S. Brückner, P. Hauke and P. Strasser, Energy Environ. Sci., 2020, 13, 1725–1729 Search PubMed.
- Y. Zhao, B. Jin, Y. Zheng, H. Jin, Y. Jiao and S. Qiao, Adv. Energy Mater., 2018, 8, 1801926 Search PubMed.
- X. Lu, J. Pan, E. Lovell, T. H. Tan, Y. H. Ng and R. Amal, Energy Environ. Sci., 2018, 11, 1898–1910 Search PubMed.
- J. G. Vos, T. A. Wezendonk, A. W. Jeremiasse and M. T. M. Koper, J. Am. Chem. Soc., 2018, 140, 10270–10281 Search PubMed.
- S. Hsu, J. Miao, L. Zhang, J. Gao, H. Wang, H. Tao, S. Hung, A. Vasileff, S. Z. Qiao and B. Liu, Adv. Mater., 2018, 30, 1707261 Search PubMed.
- L. Yu, L. Wu, B. McElhenny, S. Song, D. Luo, F. Zhang, Y. Yu, S. Chen and Z. Ren, Energy Environ. Sci., 2020, 11, 12–14 Search PubMed.
- L. Yu, Q. Zhu, S. Song, B. McElhenny, D. Wang, C. Wu, Z. Qin, J. Bao, Y. Yu, S. Chen and Z. Ren, Nat. Commun., 2019, 10, 5106 Search PubMed.
- F. Dionigi, T. Reier, Z. Pawolek, M. Gliech and P. Strasser, ChemSusChem, 2016, 9, 962–972 Search PubMed.
- H. K. Abdel-Aal and I. Hussein, Int. J. Hydrogen Energy, 1993, 18, 553–556 Search PubMed.
-
M. E. Q. Pilson, An Introduction to the Chemistry of the Sea, Cambridge University Press, 2nd edn, 2013 Search PubMed.
- M. Cole, H. Webb, P. K. Lindeque, E. S. Fileman, C. Halsband and T. S. Galloway, Sci. Rep., 2015, 4, 4528 Search PubMed.
-
L. W. Casson and J. W. Bess, Conversion to On-Site Sodium Hypochlorite Generation, CRC Press, 2003 Search PubMed.
- J. E. Bennett, Int. J. Hydrogen Energy, 1980, 5, 401–408 Search PubMed.
-
T. F. O’Brien, T. V. Bommaraju and F. Hine, Handbook of Chlor-Alkali Technology, Springer Science + Business Media, New York, 2005 Search PubMed.
- B. L. Kienitz, H. Baskaran and T. A. Zawodzinski Jr, Electrochim. Acta, 2009, 54, 1671–1679 Search PubMed.
- O. Schmidt, A. Gambhir, I. Staffell, A. Hawkes, J. Nelson and S. Few, Int. J. Hydrogen Energy, 2017, 42, 30470–30492 Search PubMed.
-
A. K. Boal, R. Matousek and W. L. Bradford, On-site Generation of Hypochlorite, American Water Works Association, 1st edn, 2015 Search PubMed.
- Y. Ligen, H. Vrubel and H. Girault, Int. J. Hydrogen Energy, 2020, 45, 10639–10647 Search PubMed.
- I. Katsounaros, J. C. Meier, S. O. Klemm, A. A. Topalov, P. U. Biedermann, M. Auinger and K. J. J. Mayrhofer, Electrochem. Commun., 2011, 13, 634–637 Search PubMed.
- M. Auinger, I. Katsounaros, J. C. Meier, S. O. Klemm, P. U. Biedermann, A. A. Topalov, M. Rohwerder and K. J. J. Mayrhofer, Phys. Chem. Chem. Phys., 2011, 13, 16384 Search PubMed.
- I. G. Wenten, Khoiruddin, F. Arfianto and Zudiharto, Desalination, 2013, 314, 109–114 Search PubMed.
- C. I. Soares Rodrigues, J. J. Jackson and M. D. Montross, Ind. Crops Prod., 2016, 92, 165–173 Search PubMed.
- A. Ghayur, T. V. Verheyen and E. Meuleman, J. Cleaner Prod., 2019, 230, 1165–1175 Search PubMed.
- Enapter, Enapter, https://www.enapter.com/electrolyser, accessed 2 March 2021.
-
J. Barrett, Inorganic Chemistry in Aqueous Solution, RSC Publishing Group, 2003 Search PubMed.
-
J. R. Rumble, CRC Handbook of Chemistry and Physics, CRC Press, 100th edn, 2019 Search PubMed.
- J. M. Gordon and T. C. Hui, Desalination, 2016, 386, 13–18 Search PubMed.
- M. Qasim, M. Badrelzaman, N. N. Darwish, N. A. Darwish and N. Hilal, Desalination, 2019, 459, 59–104 Search PubMed.
- U. Caldera and C. Breyer, Water Resour. Res., 2017, 53, 10523–10538 Search PubMed.
- M. Elimelech and W. A. Phillip, Science, 2011, 333, 712–718 Search PubMed.
- M. Badruzzaman, N. Voutchkov, L. Weinrich and J. G. Jacangelo, Desalination, 2019, 449, 78–91 Search PubMed.
- A. El-gendi, H. Abdallah, A. Amin and S. Kamel, J. Mol. Struct., 2017, 1146, 14–22 Search PubMed.
- A. N. A. Mabrouk, A. S. Nafey and H. E. S. Fath, Desalin. Water Treat., 2010, 22, 56–64 Search PubMed.
- J. I. Levene, M. K. Mann, R. M. Margolis and A. Milbrandt, Sol. Energy, 2007, 81, 773–780 Search PubMed.
- International Energy Agency, The Future of Hydrogen, https://www.iea.org/reports/the-future-of-hydrogen, (accessed 27 August 2019).
- J. R. Ziolkowska, Water Resour. Manage., 2015, 29, 1385–1397 Search PubMed.
- V. G. Gude, N. Nirmalakhandan and S. Deng, Renewable Sustainable Energy Rev., 2010, 14, 2641–2654 Search PubMed.
- M. R. Shaner, H. A. Atwater, N. S. Lewis and E. W. McFarland, Energy Environ. Sci., 2016, 9, 2354–2371 Search PubMed.
- T. Ahmad and D. Zhang, Energy Rep., 2020, 6, 1973–1991 Search PubMed.
- J. Rockström, W. Steffen, K. Noone, Å. Persson, F. S. I. Chapin, E. Lambin, T. M. Lenton, M. Scheffer, C. Folke, H. J. Schellnhuber, B. Nykvist, C. A. de Wit, T. Hughes, S. van der Leeuw, H. Rodhe, S. Sörlin, P. K. Snyder, R. Costanza, U. Svedin, M. Falkenmark, L. Karlberg, R. W. Corell, V. J. Fabry, J. Hansen, B. Walker, D. Liverman, K. Richardson, P. Crutzen and J. Foley, Ecol. Soc., 2009, 14, 32 Search PubMed.
- S. S. Veroneau and D. G. Nocera, Proc. Natl. Acad. Sci. U. S. A., 2021, 118, e2024855118 Search PubMed.
-
C. S. Hsu and P. R. Robinson, Springer Handbook of Petroleum Technology, Springer Nature, Cham, 2017 Search PubMed.
- Y. A. C. Jande, M. B. Minhas and W. S. Kim, Desalin. Water Treat., 2015, 53, 3482–3490 Search PubMed.
- H. Lee, Y. Jin and S. Hong, Desalination, 2016, 399, 185–197 Search PubMed.
- J. Kim and S. Hong, Desalination, 2018, 429, 142–154 Search PubMed.
Footnotes |
† If 10% of the total global primary energy consumption (9,970 Mtoe year−1 which is equivalent to 1.2 × 1014 kWh year−1, see source 60) would be stored in hydrogen (33 kWh kg−1 specific energy calculated based on the free enthalpy), then around 3.6 × 1011 kg of hydrogen would be required ((10/100) × 1.2 × 1014 kWh year−1/ (33 kWh kgH2−1)) which would lead to the anodic production of 9.2 × 1012 kg ClO− or 1.2 × 1013 kg Cl2. |
‡ ΔG0 for the desalination of 1 kg 1 M NaCl(aq) was calculated using ΔG0 = ΔH0 − T × ΔS0 = −3.9 kJ mol−1 + 298.15 K × 43 J (K mol)−1 = 9 kJ mol−1, where ΔH0 is the reaction enthalpy, T the temperature in K, and ΔS0 the reaction entropy. Multiplying with 0.6 gives 5.4 kJ mol−1 for 0.6 M NaCl(aq). |
§ The energy consumption based on the higher heating value, ΔH0HHV, was calculated using H0HHV = VHHV × n × F = 1.48 V × 2 × 96 485 s A mol−1 = 286 kJ mol−1, where n is the number of transferred electrons per H2O from OII− to HI+, and F the Faraday constant. ΔH0HHV can be converted to 15 888 kJ kgwater−1 by multiplying it with 55.5 mol kgwater−1. Considering the efficiency range of 62–82% yields 19 376–25 627 kJ kgwater−1. |
¶ 1 A cm−2 is equivalent to 86 400 000 C (m2 day)−1. Using the Faraday constant, F, this converts to 895 mol (m2 day)−1 which is equivalent to 8 kg (m2 day)−1 of water consumption when divided by 55.5 mol kgwater−1 and considering that two electrons per water molecule are transferred. |
|| 1 kW is equivalent to 86 400 kJ day−1 and considering that 15 888 kJ are required to split 1 kg of H2O (see footnote §), 3.4 to 4.5 kgwater (day kW)−1 are consumed when the efficiency is 62–82%. Dividing 912–2850 US$ kW−1 by 3.4–4.5 kgwater (day kW)−1 yields 203–838 US$ (kgwater day−1)−1. |
** 1 kg of H2O produces 1/9 kg of H2. Thus, the water price was multiplied by nine. |
†† Freshwater needed for water splitting if all electricity is produced from hydrogen: . |
‡‡ Calculated using 0.80 US$ m−3 as water purification costs and 2.5 US$ kg−1 as hydrogen prize. |
|
This journal is © The Royal Society of Chemistry 2021 |
Click here to see how this site uses Cookies. View our privacy policy here.