Shape-memory poly(arylene ether ketone)s with tunable transition temperatures and their composite actuators capable of electric-triggered deformation†
Received
7th October 2019
, Accepted 15th November 2019
First published on 17th November 2019
Abstract
In this paper, a series of shape-memory poly(arylene ether ketone)s (PAKEs) with various flexible groups (i.e., carbolic bonds, ether, and ketone linkages) and entangled crystalline polymeric structures were synthesized by combining different bisphenol monomer (bisphenol A monomer and methyl hydroquinone monomer) proportions with a 4,4′-difluorobenzophenone monomer. The flexible parts and the entangled parts acted as a reversible phase and permanent phase, respectively. The prepared PAEK films exhibited excellent heat-triggered shape-memory behaviors with tunable glass transition temperatures (Tg) from 116 °C to 140.5 °C including an extremely high fixity ratio (over 98%), high recovery ratio (over 92%), and fast recovery rate (within 7.0 s). As increasing the content of the methyl hydroquinone monomer in the structural unit, the recovery ratio showed a downward trend, whereas the recovery time increased gradually. In addition, the electric-triggered shape-memory effect of the PAEK films was achieved via the introduction of carbon nanotubes (CNTs). Upon applying a voltage of 25 V, the recovery ratios of the composite films containing 10 wt% and 15 wt% CNTs were all over 80% (of 83.0% and 87.6%, respectively), indicating a great electric-triggered shape-memory behavior. The recovery ratio increased and the triggered voltage decreased as increasing the content of CNTs. The heat and electric dual-triggered shape-memory PAEK composites could be important smart materials possessing wide application prospects.
Introduction
Shape-memory polymers (SMPs), as a kind of stimuli-responsive smart materials, are capable of memorizing a temporary shape after deformation and recovering back to their permanent shape upon external stimulation, including heat, electric, light, magnetic field, moisture, and pH value.1–5 Due to the robust elasticity of polymer chains, many polymers exhibit shape-memory capabilities that allow programmable actuation in response to external stimuli.6 SMPs have gained increasing attention due to their excellent deformation and shape-changing properties in addition to their light weight, easy processing, and low cost.7 Therefore, SMPs are of tremendous potential for applications in various fields, like medical technology and biomedical applications, space applications as deployable structures and morphing wings, and in textile technology.8–13
SMPs have enjoyed a long history of interest and academic development due to the expectation that they can impart structural responsiveness and ultimately autonomous deployment in most universal places.14,15 To achieve the shape-memory effect (SME), most SMPs consist of reversible and fixed domains. The former is responsible for holding the temporary deformation and responses to an external thermal stimulus, which is usually related to a glass-rubber transition, crystallization/melting transition, and reversible molecule cross-linking structure. The latter provides the recovery force during the shape-recovery process, concerned with the molecular entanglement and chemical cross-linking structure.16,17 Despite their potential wide applications, SMPs also have some drawbacks, such as poor mechanical properties, low recovery stress, slow recovery speed, and short cycle life, strongly restricting their applications in many fields.18 Hence, the issue of how to obtain new types of SMPs with excellent properties urgently needs to be solved. In general, SMPs have been obtained in two main ways: physical blending or chemical synthesis.19 Physical blending is an easy method for preparing SMPs but lacks novelty. Chemical synthesis, despite the preparation being relatively complicated, can endow polymers with designable shape-memory behaviors and has become an effective technique to prepare new types of SMPs.
Poly(aryl ether ketone) (PAEK) is a highly aromatic semi-crystalline thermoplastic with great mechanical properties and thermal stability; it is ranked as one of the most promising matrix polymers for high-performance composite materials.20–24 Besides, its flexibility and thermostability could be regulated and controlled through molecular design.25,26 Furthermore, amorphous PAEKs have received considerable research attention due to their good solubility in ordinary organic solvents, which is beneficial for applications as matrix resins for inorganic compounds.27–29 In the previous literature, only poly(ether ether ketone) (PEEK) has been reported to possess shape-memory behaviours.30 Neat PEEK exhibits shape-memory behavior where a crystalline phase provides the “permanent” network and the glass transition provides the reversible, thermally actuated temporary network. However, the strains within the main chain of PEEK are rather small, and the shape-memory behavior is relatively poor due to creep of either the “permanent” crystalline network or the glassy temporary network.31 To increase the flexibility of main chains, side groups or flexible backbone groups need to be incorporated into the system. So far, to the best of our knowledge, no investigation has been done on the SME of PAEKs or reported in the literature. However, there should be great research value and large application potential in developing PAEKs with a combination of the excellent mechanical and physicochemical performances of traditional PAEKs and their unique shape-memory behaviors.
At present, most SMPs are thermo-activated, and therefore could not be actuated when outer heating sources are not available. Hence, researchers have attempted to expand the actuation routes of SMPs, from thermal to non-thermal triggering (such as electric, magnetism, light, solvent, and microwave).32 Among these triggerings, electrical-actuation has attracted much more attention due to it offering convenient manipulation, remote controllability, and so on.33 To achieve electrical-actuated SMEs, an electricity conductive path must be constructed. Carbon nanotubes (CNTs) are the most extensively investigated type of material for achieving this because of their extremely high intrinsic conductivity, high aspect ratio, and excellent self-entanglement ability, which facilitate the formation of a conductive path in the polymer composites.34,35 CNTs are thin cylinders of carbon that are bonded together in a unique honeycomb nanostructure, and these are believed to be ideal candidates for multi-functional materials.36,37 In addition, due to their high strength, high modulus, and similar chain-like structure to polymer molecular chains,38,39 much research has focused on using CNTs as inorganic enhancing fillers in polymer nanocomposites.40–44
In this paper, we propose a facile method for the synthesis of shape-memory PAEKs with tunable shape-memory effects. The proportion of two bisphenol monomers (bisphenol A monomer and methyl hydroquinone monomer) was adjusted to improve the SME of our prepared PAEKs. Besides, in order to fulfill the electrical-actuation of PAEK, CNTs were added into the polymer matrix to prepare PAEK/CNTs composite films. The shape-recovery behaviors of the composite films possessing great conductivity were actuated by electrical stimulation. Due to the heat and electric-dual-triggered shape-memory performances, the prepared PAEK composites possess wide application prospects in smart devices.
Experimental
Materials
Bisphenol A, methyl hydroquinone, 4,4′-difluorobenzophenone, potassium carbonate (K2CO3), and tetramethylene sulfone (TMSF) were all supplied from Aladdin Industrial. Toluene and N-methyl kelopyrrolidide (NMP) were all obtained from Tianjin Damao Chemical Reagent Factory. CNTs were bought from Chinese Academy of Sciences, Chengdu Organic Chemistry Co., Ltd. Unless otherwise stated, all the materials were of analytical grade and were used without further purification.
Synthesis of PAEKs
PAEKs were synthesized via a stepwise polymerization procedure: a certain amount of bisphenol A, methyl hydroquinone, 4,4′-difluorobenzophenone, and K2CO3 were carefully added into a three-neck round-bottom flask. Then a certain volume of TMSF and toluene were poured into the flask; in addition, a Dean–Stark trap and a condenser under a nitrogen atmosphere were installed. The mixture, with vigorous stirring, was heated at 140 °C for 2.5 h to remove the formed water, via an azeotropic solvent of toluene. Subsequently, the temperature was increased to 170 °C for 5 h to distil the added toluene and to carry out the polymerization. Afterwards, the viscous mixture was slowly poured into a beaker containing a large amount of distilled water to precipitate the polymer and remove the organic solvent. Finally, the precipitate was filtered and rinsed with deionized water and ethanol to remove residual organic solvent, inorganic salts, and small molecules. The obtained PAEKs were triturated and dried at 120 °C under vacuum for 24 h (yield: 92%). The prepared PAEKs were assigned to P1, P2, P3, P4, and P5, corresponding to the proportions of bisphenol A to methyl hydroquinone monomer of 1
:
0, 0.75
:
0.25, 0.5
:
0.5, 0.25
:
0.75, and 0
:
1, respectively. The synthesis pathway and images of the prepared PAEKs are illustrated in Fig. 1.
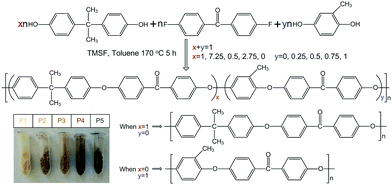 |
| Fig. 1 Synthesis pathway and images of the various types of PAEKs. | |
Preparation of PAEK and PAEK/CNTs composite films
Various proportions of the prepared PAEKs were dissolved into NMP and stirred to obtain homogeneous solutions (10 wt%). P1 was employed as the PAEK matrix, and fixed amounts of CNTs were added into the PAEK matrix, with the content of CNTs as 0% w/w, 5% w/w, 10% w/w, and 15% w/w, named P1C1, P1C2, P1C3, and P1C4, respectively. The mixtures were dissolved into NMP and stirred to obtain homogeneous solutions (10 wt%). All the above solutions were dried at 80 °C for 48 h to obtain PAEK and PAEK/CNTs composite films. It was noteworthy that during the film-forming process, the vacuum environment was equipped only for the last 12 h, avoiding the flowing of solutions.
Characterization
Sample analysis.
The chemical structures of the prepared PAEKs were confirmed through 1H NMR measurements performed with an ADVANCE III 400 MHz 010601 spectrometer (Bruker) while using CDCl3 as the solvent and tetramethylsilane (TMS) as the internal reference. Fourier transform infrared (FT-IR) spectroscopy was used to determine the chemical functional groups. This method was performed using a Spectrum Two instrument (PerkinElmer). The spectral range was 4000–400 cm−1 with a resolution of 4 cm−1. The prepared PAEKs were dissolved into NMP with vigorous stirring to prepare the homogeneous solutions (0.5 g L−1), and the viscosity of the solutions was measured through an Ubbelohde viscometer at the temperature of 25 ± 0.1 °C.
Characterization of the prepared PAEKs.
X-ray diffraction (XRD) analysis was used to determine the crystal structures of the prepared PAEKs through an X’pert XRD analyzer (Panalytical B.V.). The scanning rate was 10° min−1 over a 2θ range of 5°–55°. Differential scanning calorimetric (DSC) data were recorded on a DSC 1 STAR system (Mettler-Toledo) at a heating rate of 10 °C min−1 under a nitrogen atmosphere, and a temperature range of 25–300 °C. Thermal gravimetric analysis (TGA) was carried out on a TGA/DSC 1 STAR system (Mettler-Toledo) at a heating rate of 10 °C min−1 under a nitrogen atmosphere, and a temperature range of 25–800 °C. The dispersion of CNTs in the PAEK matrix was observed using an S-4300 scanning electron microscope (Hitachi). The samples were sputtercoated with gold for better conductivity before imaging. The fresh fracture surface was obtained by freezing the samples in liquid nitrogen and then cracking. The conductivity of the PAEK/CNTs composite films was assessed via a RT-70 V/RG-7C four-point probe (Napson Corp). Ten independent measurements were used to characterize each film sample. Infrared thermographic images were recorded via a JENOPTIK infrared camera (InfraTec) to investigate the temperature distributions of the samples during the electric-triggered shape-recovery process.
Shape-memory test.
Here, “U”-shape film samples were employed to illustrate the shape-memory behaviors of the PAEK and PAEK/CNTs composite films more directly. The film samples were cut into a rectangle with sizes of 5 × 25 mm2. Afterwards, they were bent into a “U” shape at Tg of each sample and then cooled down quickly to the shape-fixity temperature (room temperature). The shape recovery behaviors were actuated through heating the films up to the temperature of Tg + 10 °C. The whole recovery process was recorded using a digital video camera, and snapshots were then analyzed with Digimizer software to obtain the deformation angle θ(t) at time t. The recovery ratio (R) was defined as follows: | 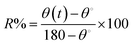 | (1) |
where θ° is the deformation angle at the time of 0 s.
The test for the electric-triggered shape-memory behaviors of the composite films followed similar steps to those described above, except for the actuation of the recovery behaviors. The electric-triggered shape recovery of the samples was actuated using a DC electrical power source at constant applied voltages.
Results and discussion
Synthesis and characterization of the prepared PAEKs
The chemical structures of the prepared PAEKs were determined via1H NMR spectroscopy, as shown in Fig. 2a. For P1, the chemical shifts at 7.77, 7.26, and 7.01 ppm were attributable to protons 7,8,2,4, and 1,5,6,9, indicating that the sample contained a PAEK backbone. The chemical shift at 1.71 ppm was related to the protons of primary methyl groups (3). For P2, P3, and P4, due to the addition of methyl hydroquinone monomer, the new peaks appeared at around 6.95 and 2.20 ppm, corresponding to protons 10,11,12, and 13, respectively. With the increasing content of methyl hydroquinone monomer, the peak strength of 10,11,12 clearly increased. Besides, it was noteworthy that the proportions of bisphenol A monomer and methyl hydroquinone monomer were 1.23
:
0.42, 1.03
:
1.32, and 0.82
:
2 (approximately of 3
:
1, 1
:
1.3, and 1
:
2.5), which almost correspond to the monomer feeding ratios of 0.75
:
0.25, 0.5
:
0.5, and 0.25
:
0.75, respectively. It could be obtained that the resulting polymer was consistent with the monomer feeding ratio. For P5, the structural characteristic peaks of the PAEK backbone were presented at 7.77, 7.01, and 6.95 ppm, and the chemical shift at 2.20 ppm was related to the protons of the primary methyl groups on the phenyl ring. All of these characteristic proton resonances confirmed that PAEKs of various flexible groups and backbones had been synthesized successfully. The FTIR spectra of PAEKs with various proportions of ingredients are shown in Fig. 2b. The peaks at 2924 and 2850 cm−1 could be concerned with alkyl methylene, which were shifted slightly after the introduction of aryl methylene in the methyl hydroquinone monomer. The peak at 1687 cm−1 was attributed to the stretching vibration of aryl carbonyl groups and its symmetric stretching was at 930 cm−1.45 The characteristic stretching vibration peaks of aryl ether groups were at 1547 and 1264 cm−1. The reduced viscosity of PAEK solutions is shown in Fig. S1 (ESI†). It could be observed that the reduced viscosity for all the solutions was over 1.0 L g−1, indicative of the high molecular weight for all PAEKs.46 Besides, it could be found that the molecule weights of P1 and P5 were relatively larger, and that of P3 was the minimum.
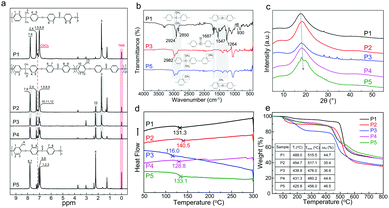 |
| Fig. 2 Synthesis and characterization of the prepared PAEKs (P1, P2, P3, P4, and P5): (a) 1H NMR spectroscopy; (b) FTIR spectra; (c) XRD patterns; (d) DSC curves; (e) TGA analysis. | |
XRD patterns of the PAEKs were obtained and are presented in Fig. 2c. All the prepared PAEKs possessed a semi-crystalline structure, and the crystallinity of P1, P3, and P5 was relatively higher. Intriguingly, with the increase in methyl hydroquinone monomer content, the diffraction peak was shifted slightly to higher degrees. DSC curves of the prepared PAEKs are shown in Fig. 2d. The glass transition temperature (Tg) ranged from 110–140 °C, much lower than the Tg of commercial PEEK at around 155 °C.47 Compared with the regular and rigid chain structure of commercial PEEK, the introduction of carbolic bonds of the main chains and side methyl groups decreased the regularity of the chains, weakened the rigidity, and made the chains more flexible. The Tg of P2, of 140.5 °C, was higher than the Tg of P1 of 131.3 °C, indicating that the induction of side methyl groups increased the stiffness of the whole chains, compared with the P1 backbone. Meanwhile, the induction of carbolic bonds of the main chains decreased the stiffness of the whole chains, as the Tg of P4 was lower than Tg of P5 of 133.1 °C. The Tg of P3, of 116.0 °C, was the lowest among the prepared PAEKs, which indicated that the whole chains of P3 were the most flexible. In addition, a high or low molecular weight contributed to the resulting Tg of the prepared PAEKs. The thermal stability of the prepared PAEKs was measured through thermal gravimetric analysis, as shown in Fig. 2e. As for P2, P3, P4, and P5, there was a slight decrease at around 100 °C, which could be concerned with the loss of free water in the PAEKs. For P1, a significant mass loss occurred at about 486 °C, indicative of the beginning of degradation of the polymer chains. The residual mass was about 44.7% when the temperature was up to 800 °C. With the increasing content of methyl hydroquinone monomer in the structural unit, the initial degradation temperature (Ti) decreased (from 489.0 °C to 454.7 °C, 439.8 °C, 431.3 °C, and 425.8 °C, corresponding to the contents of methyl hydroquinone monomer of 0, 25%, 50%, 75%, and 100%). This might be attributed to the existence of methyl groups on the phenyl ring decreasing the regularity and crystallinity of the whole chain, thus promoting the degradation of polymer chains. The decreased temperature of the maximum degradation rate (Tmax) could be due to the same cause. Nevertheless, when the temperature was up to 800 °C, the residual mass (ωm) of P2, P3, P4, and P5 increased from 35.4% to 36.6%, 44.6%, and 46.5%, corresponding to the contents of methyl hydroquinone monomer of 25%, 50%, 75%, and 100%. This could be due to the increasing content of phenyl ring, induced by the increasing content of methyl hydroquinone monomer. The residual mass of P5 (46.5%) was more than P1 (44.7%), which indicated that the regularity and crystallinity of P1 was the best among the prepared PAEKs. This was because the phenyl ring in the main chain determined the thermal stability directly when the temperature was up to 800 °C.
Heat-triggered shape-memory behaviors
The heat-triggered shape-memory behaviors of the PAEK films were characterized via heat-triggered shape-memory tests, as shown in Fig. 3. Fig. 3a (Video S1, ESI†) shows the whole shape-recovery behavior of the P3 film at the temperature of 126 °C (Tg + 10 °C). The shape-recovery time was less than 4 s in the macroscopic view. In Fig. 3b, the recovery ratios of various PAEKs films were all over 92%, indicative of the excellent SME of the prepared PAEK films. Meanwhile, with the increasing content of methyl hydroquinone monomer in the structural unit, the recovery ratio exhibited a downward trend, which could be due to the decreased flexibility of the main chain. The induction of carbonic bonds on bisphenol A molecules in the polymer main chain improved the flexibility of the main chain, enhancing the shape-recovery ability of the films. Nevertheless, the induction of phenyl rings on methyl hydroquinone molecules in the main chain increased the rigidity and stiffness of the main chain, promoting the shape fixity of the films. In Fig. 3c, the fixity ratios of the prepared PAEK films increased slightly from P1 to P5, due to the same cause. Meanwhile, it was noteworthy that all the PAEK films showed a high fixity ratio, over 98%. Fig. 3d shows that all the PAEK films could finish the recovery process within 7.0 s, indicative of the excellent shape-recovery ability. With the increasing content of methyl hydroquinone monomer in the structural unit, the shape-recovery time of PAEK films exhibited an upward trend, from 4.0 s to 3.1 s, 4.0 s, 5.0 s, and 7.0 s, which corresponded to P1, P2, P3, P4, and P5, respectively. This phenomenon might be related to the enhanced rigidity and the weakened flexibility. Fig. 3e shows the recovery ratio of the P3 film in five consecutive shape-recovery memory processes. In the first three cycles, the recovery ratio decreased gradually, from 97.5% to 94.5%, and then to 90.7%. In the last two cycles, the recovery ratio maintained a relatively stable rate, of 90.3% and 90.4%, respectively. This confirmed that the shape-memory PAEK films possessed great reproducibility at consecutive cycling processes. Fig. 3f shows the effect of bisphenol A and methyl hydroquinone monomers on the flexibility of the main chain and on the shape-memory properties of the prepared PAEK films. The poorer flexibility weakened the shape-memory behaviors of the PAEKs, resulting in a longer recovery time.
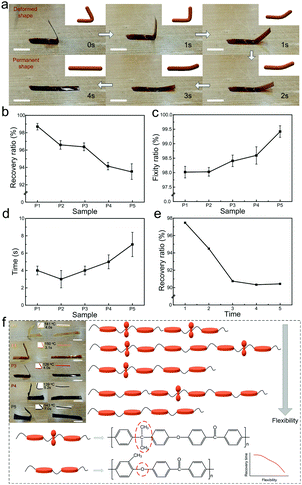 |
| Fig. 3 Heat-triggered shape-memory behaviors of the prepared PAEK films (P1, P2, P3, P4, and P5): (a) the whole shape-recovery process of the P3 film at 126 °C (Tg + 10 °C); (b) shape-recovery ratio; (c) shape-fixity ratio; (d) shape-recovery time; (e). recovery ratio of the P3 film after five times undergoing consecutive shape-recovery processes; (f) shape-recovery behaviors of the prepared PAEK films (scale bars: 1 cm). | |
Electric-triggered shape-memory behaviors
The electric-triggered SME of the PAEK/CNTs composite films was characterized via the electric-triggered shape-memory test. Fig. 4a (Video S2, ESI†) shows the whole shape-recovery behavior of the P1C3 film at a voltage of 25 V. It could be observed that the whole shape-recovery process could be finished in 27 s, indicating a great electric-triggered SME. Thermal infrared images were captured during the recovery process, as shown in Fig. 4b. The color map charted the distribution of temperature. It could be found that the temperature distribution in the sample was relatively uniform. The temperature increased along with the applied voltage, and when the temperature of the sample was raised up to 219.6 °C, it did not increase further and was maintained as stable. Due to the electrothermal effect of the CNTs, the shape-recovery behavior of the sample could be triggered by electricity. Nevertheless, if the content of CNTs was relatively low (0% w/w and 5% w/w), the sample could not recover its permanent shape no matter how high the applied voltage was. A low amount of conductive CNTs could not significantly improve the conductivity of the PAEK matrix, and the limited electrothermal energy could not heat the sample to the transition temperature for shape recovery. Fig. 4c shows the shape-recovery ratios and fixity ratios of the P1C3 and P1C4 films. It could be obtained that the recovery ratios were over 80% (of 83.0% and 87.6%, respectively). In common, introducing CNTs into the composites affected the mobility of the composites, which might decrease the recovery ratio of the composites. Nevertheless, when increasing the content of CNTs, the electrothermal effect was enhanced and the recovery ratio might be increased. As shown in the results, the recovery ratio increased when the content of CNTs increased. This could indicate that the electrothermal effect of CNTs on the recovery ratio was larger than the decreasing flexibility from the addition of CNTs into the PAEK matrix, when the content of CNTs was 15% w/w. The fixity ratio of the two samples were both more than 99%, indicative of the excellent shape-fixity ability. Fig. 4d shows the shape-recovery behavior of the P1C4 film upon an applied voltage of 20 V, whereby the sample could recover its original shape in 60 s. In addition, the heat-triggered shape-recovery behavior of the P1C3 film was characterized, as shown in Fig. 4e. The recovery process could finish within 10 s at a triggered temperature of Tg + 10 °C, 141 °C. Fig. 4f shows the SEM images of the PAEK/CNTs composite films, showing the PAEK films with a low amount of CNTs had a smooth fracture surface. With the increasing content of CNTs, the micro tubular protuberance as well as interlacing overlap and accumulation phenomenon appeared on the fracture surface. It could also be observed from the images that the CNTs were well dispersed in the PAEK matrix. The conductivity of the composite films increased with the increasing content of CNTs, from 0.029 S cm−1 to 0.589 S cm−1 and 1.016 S cm−1, corresponding to the P1C2, P1C3, and P1C4 samples, respectively. The enhanced conductivity endowed the composite films with a great electric-triggered SME, and extends their potential applications in electro-smart device fields.
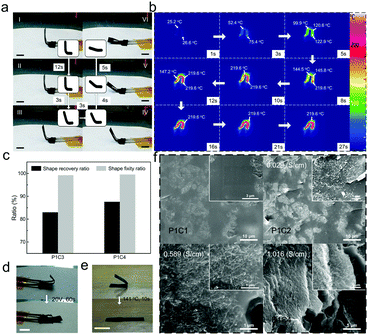 |
| Fig. 4 Electric-triggered shape-memory behaviors of the prepared PAEK/CNTs composite films (P1C1, P1C2, P1C3, and P1C4): (a) the whole shape-recovery process of the P1C3 film at an applied voltage of 25 V; (b) thermal infrared images of the whole shape-recovery process of the P1C3 film; (c) shape-recovery ratio and shape-fixity ratio of the P1C3 and P1C4 films; (d) shape-recovery behavior of the P1C4 film upon an applied voltage of 20 V; (e) heat-triggered shape-recovery behavior of the P1C3 film at 141 °C (Tg + 10 °C); (f) SEM images of PAEK/CNTs composite films (Untagged scale bars: 1 cm). | |
Mechanism of the shape-memory behaviors
The mechanism of the heat-triggered and electric-triggered shape-memory behaviors of the prepared PAEK films is schematically illustrated in Fig. 5. In general, the SME of shape-memory polymers could be attributed to a “dual-state mechanism”, in which the flexible molecular chains are regarded as the reversible phase and the nodes of the macromolecule segments attributed to physical entanglement or the crystalline phase are regarded as the permanent phase.48 In the prepared PAEKs, the carbonic bonds, ether, and ketone linkages offer high flexibility, endow the main chain with the reversible phase, while the crystalline phase and chain entanglement within the polymeric matrix act as the permanent phase.49 Initially, the film sample exhibited a permanent shape, which was related to a certain state of the molecular chains, the crystallinity, and the chain entanglement of PAEK that was determined during the process of the preparation of the films. Subsequently, when the temperature was increased to Tg, the “frozen” molecular chains were “melted”. Upon an applied external force, the shape of the films was deformed and a temporary shape was obtained. When the temperature was cooled, the temporary shape was fixed. Additionally, when the temperature was heated above Tg (Tg + 10 °C), the flexible molecular chains began to move, the internal stress was released, and the permanent shape was recovered. As for the electric-triggered SME, after shape fixation, the temperature was raised by applying an appropriate voltage, because of the electrothermal effect of the CNTs. The thermal power, originating from the electrical power of the applied voltage, improved the flexibility of the molecular chains, and promoted the occurrence of shape recovery.
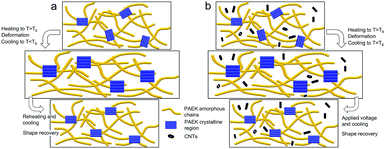 |
| Fig. 5 Schematic representation of the programming process: (a) heat-triggered shape-recovery process of PAEK films; (b) electric-triggered shape-recovery process of PAEK/CNTs composite films. | |
Conclusions
In summary, a series of novel PAEK SMPs with various proportions of bisphenol A and methyl hydroquinone monomer were synthesized via the step polymerization method. The flexible units in the backbone acted as the reversible phase, and the chain entanglement and crystalline phase in the polymeric matrix were employed as the permanent phase. The prepared PAEKs had an excellent shape-memory ability with tuning Tg, from 116 °C to 140.5 °C, and great thermal stability due to existence of phenyl rings in the main chains. All of the PAEK films showed an excellent fixity ratio (over 98%), high recovery ratio (over 92%), and fast recovery rate (within 7.0 s). With the increasing content of methyl hydroquinone monomer in the structural unit, the recovery ratio exhibited a downward trend and the recovery time increased gradually, which were concerned with the decreased flexibility of the main chain. Besides, the prepared PAEK films possessed great reproducibility of their shape-memory behaviors, showing recovery ratios above 90% during five times undergoing consecutive shape-memory processes. In addition, the electric-triggered SME of the PAEK films was obtained via the introduction of CNTs. Upon applying a voltage of 25 V, the recovery ratios of the composite films with over 10% w/w CNTs were all over 80%. As the content of CNTs increased, the recovery ratio increased and the triggered voltage decreased. Such heat- and electric dual-triggered PAEK SMPs would have promising application prospects in the fields of biomedical technology and smart devices, especially in electro-active smart devices.
Conflicts of interest
The authors declare that they have no conflict of interest.
Acknowledgements
This work is supported by the National Natural Science Foundation of China (Grant No. 11632005, 11672086, and 11802077) and the Foundation for Innovative Research Groups of the National Natural Science Foundation of China (Grant No. 11421091).
References
- Y. T. Yao, T. Y. Zhou, J. J. Wang, Z. H. Li, H. B. Lu, Y. J. Liu and J. S. Leng, Composites, Part A, 2016, 90, 502–509 CrossRef CAS.
- H. Yang, W. R. Leow, T. Wang, J. Wang, J. C. Yu, K. He, D. P. Qi, C. J. Wang and X. D. Chen, Adv. Mater., 2017, 29, 1701627 CrossRef PubMed.
- G. G. Zhang, W. J. Peng, J. J. Wu, Q. Zhao and T. Xie, Nat. Commun., 2018, 9, 4002 CrossRef PubMed.
- A. Toncheva, F. Khelifa, Y. Paint, M. Voue, P. Lambert, P. Dubois and J. M. Raquez, ACS Appl. Mater. Interfaces, 2018, 10, 29933–29942 CrossRef CAS PubMed.
- Y. C. Zhang, Y. Li, Y. L. Hu, X. L. Zhu, Y. W. Huang, Z. Zhang, S. L. Rao, Z. J. Hu, W. X. Qiu, Y. L. Wang, G. Q. Li, L. Yang, J. W. Li, D. Wu, W. B. Huang, C. W. Qiu and J. R. Chu, Adv. Mater., 2018, 30, 1803072 CrossRef PubMed.
- X. B. Hu, D. X. Zhang and S. S. Sheiko, Adv. Mater., 2018, 30, 1707461 CrossRef.
- F. H. Zhang, Y. L. Xia, L. L. Wang, L. W. Liu, Y. J. Liu and J. S. Leng, ACS Appl. Mater. Interfaces, 2018, 10(41), 35526–35532 CrossRef CAS.
- H. Q. Wei, Q. W. Zhang, Y. T. Yao, L. W. Liu, Y. J. Liu and J. S. Leng, ACS Appl. Mater. Interfaces, 2017, 9(1), 876–883 CrossRef CAS.
- M. Bao, X. X. Lou, Q. H. Zhou, W. Dong, H. H. Yuan and Y. Z. Zhang, ACS Appl. Mater. Interfaces, 2014, 6(4), 2611–2621 CrossRef CAS PubMed.
- S. Y. Zhuo, Y. X. Liu, L. L. Zhou and X. Q. Feng, J. Mater. Sci., 2018, 53, 13936–13948 CrossRef CAS.
- J. D. Erndt-Marino, D. J. Munoz-Pinto, S. Samavedi, A. C. Jimenez-Vergara, P. Diaz-Rodriguez, L. Woodard, D. W. Zhang, M. A. Grunlan and M. S. Hahn, ACS Biomater. Sci. Eng., 2015, 1(12), 1220–1230 CrossRef CAS.
- Y. T. Yao, H. Q. Wei, J. J. Wang, H. B. Lv, J. S. Leng and D. Hui, Composites, Part B, 2015, 83, 264–269 CrossRef CAS.
- H. Lützen, T. M. Gesing, B. K. Kim and A. Hartwig, Polymer, 2012, 53(26), 6089–6095 CrossRef.
- M. Zarek, M. Layani, I. Cooperstein, E. Sachyani, D. Cohn and S. Magdassi, Adv. Mater., 2016, 28(22), 4449–4454 CrossRef CAS.
- T. L. Landsman, T. Touchet, S. M. Hasan, C. Smith, B. Russell, J. Rivera, D. J. Maitland and E. Cosgriff-Hernandez, Acta Biomater., 2016, 47, 91–99 CrossRef.
- Z. X. Zhang, J. X. Dou, J. H. He, C. X. Xiao, L. Y. Shen, J. H. Yang, Y. Wang and Z. W. Zhou, J. Mater. Chem. C, 2017, 5, 4145–4158 RSC.
- M. Bao, X. L. Wang, H. H. Yuan, X. X. Lou, Q. H. Zhao and Y. Z. Zhang, J. Mater. Chem. B, 2016, 4(31), 5308–5320 RSC.
- J. J. Lai, X. J. Li, R. Q. Wu, J. N. Deng, Y. Pan, Z. H. Zheng and X. B. Deng, Soft Matter, 2018, 14, 7302–7309 RSC.
- D. W. Zhang, S. Yang, K. K. Zhang, G. L. Zhou, Z. X. Jiang and J. Y. Gu, J. Appl. Polym. Sci., 2019, 136, 47037 CrossRef.
- R. Q. Na, G. Z. Huo, S. L. Zhang, P. F. Huo, Y. L. Du, J. S. Luan, K. Zhu and G. B. Wang, J. Mater. Chem. A, 2016, 4, 18116–18127 RSC.
- J. N. Panda, J. Bijwe and R. K. Pandey, Compos. Sci. Technol., 2017, 144, 139–150 CrossRef CAS.
- C. Y. Ru, Z. H. Li, C. J. Zhao, Y. T. Duan, Z. Zhuang, F. Z. Bu and H. Na, ACS Appl. Mater. Interfaces, 2018, 10, 7963–7973 CrossRef CAS.
- B. L. Chen, Y. Wang, S. Berretta and O. Ghita, Mater. Sci., 2017, 52, 6004–6019 CrossRef CAS.
- S. Yang, Y. Ahn and D. Kim, J. Mater. Chem. A, 2017, 5, 2261–2270 RSC.
- M. D. T. Nguyen, S. Yang and D. Kim, J. Power Sources, 2016, 328, 355–363 CrossRef CAS.
- M. Xie, M. Y. Yin, G. D. Nie, J. Wang, C. Wang, D. M. Chao and X. C. Liu, J. Polym. Sci., Part A: Polym. Chem., 2016, 54, 2714–2721 CrossRef CAS.
- F. F. Wang, Z. P. Wang, H. H. Wang and G. Y. Zhou, Polym. Int., 2015, 64(7), 858–866 CrossRef CAS.
- J. H. Pang, X. Jin, Y. Wang, S. N. Feng, K. Z. Shen and G. B. Wang, J. Membr. Sci., 2015, 492, 67–76 CrossRef CAS.
- M. M. He, Y. Hou, Y. L. Jiang, Y. B. Li, Q. Zou, C. Chen, L. Zhang and W. Z. Yang, Mater. Lett., 2019, 235, 242–245 CrossRef CAS.
- Y. Shi and R. A. Weiss, Macromolecules, 2014, 47, 1732–1740 CrossRef CAS.
- Y. Shi, M. Yoonessi and R. A. Weiss, Macromolecules, 2013, 46, 4160–4167 CrossRef CAS.
- L. Chen, W. Li, X. P. Liu, C. Zhang, H. Zhou and S. W. Song, J. Appl. Polym. Sci., 2019, 136(21), 47563 CrossRef.
- J. Zhou, H. Li, W. W. Liu, R. Dugnani, R. Tian, W. C. Xue, Y. J. Chen, Y. P. Guo, H. N. Duan and H. Z. Liu, Composites, Part A, 2016, 91, 292–300 CrossRef CAS.
- H. Nurly, Q. Yan, B. Song and Y. S. Shi, Eur. Polym. J., 2019, 110, 114–122 CrossRef CAS.
- Z. X. Zhang, W. Y. Wang, J. H. Yang, N. Zhang, T. Huang and Y. Wang, J. Phys. Chem. C, 2016, 120, 22793–22802 CrossRef CAS.
- X. X. Liu, M. M. Chang, B. He, L. Meng, X. H. Wang, R. C. Sun, J. L. Ren and F. G. Kong, J. Colloid Interface Sci., 2019, 538, 507–518 CrossRef CAS.
- J. Chen, Z. X. Zhang, W. B. Huang, J. L. Li, J. H. Yang, Y. Wang, Z. W. Zhou and J. H. Zhang, Mater. Des., 2015, 69, 105–113 CrossRef CAS.
- Z. D. Han and A. Fina, Prog. Polym. Sci., 2011, 36, 914–944 CrossRef CAS.
- Z. Spitalsky, D. Tasis, K. Papagelis and C. Galiotis, Prog. Polym. Sci., 2010, 35, 357–401 CrossRef CAS.
- Y. B. Dong, H. Xia, Y. F. Zhu, Q. Q. Ni and Y. Q. Fu, Compos. Sci. Technol., 2015, 120, 17–25 CrossRef CAS.
- M. H. Moghim, S. M. Zebarjad and R. Eqra, Polym. Adv. Technol., 2018, 29, 2496–2504 CrossRef CAS.
- F. Grillard, P. Poulin, A. Korzhenko, P. Gaillard and C. Zakri, ACS Macro Lett., 2014, 3, 224–228 CrossRef CAS.
- J. Bai and Z. X. Shi, ACS Appl. Mater. Interfaces, 2017, 9, 27213–27222 CrossRef CAS.
- Z. X. Deng, T. L. Hu, Q. Lei, J. K. He, P. X. Ma and B. L. Guo, ACS Appl. Mater. Interfaces, 2019, 11, 6796–6808 CrossRef CAS PubMed.
- P. Roy and R. R. N. Sailaja, J. Mech. Behav. Biomed. Mater., 2015, 49, 1–11 CrossRef CAS.
- B. L. Wang, Z. Z. Cai, N. Zhang, B. Zhang, D. Qi, C. J. Zhao and H. Na, RSC Adv., 2015, 5, 536 RSC.
- X. L. Wu, W. M. Huang, Z. Ding, H. X. Tan, W. G. Yang and K. Y. Sun, J. Appl. Polym. Sci., 2014, 131, 39844 Search PubMed.
- P. D. Warren, D. V. McGrath and J. P. V. Geest, Macromol. Mater. Eng., 2010, 295, 386–396 CrossRef CAS.
- X. L. Xiao, D. Y. Kong, X. Y. Qiu, W. B. Zhang, F. H. Zhang, L. W. Liu, Y. J. Liu, S. Zhang, Y. Hu and J. S. Leng, Macromolecules, 2015, 48, 3582–3589 CrossRef CAS.
Footnote |
† Electronic supplementary information (ESI) available: Fig. S1 showed the reduced viscosity of prepared PAEK solutions. Video S1 showed the whole shape recovery behavior of P3 film at the temperature of 126 °C (Tg + 10 °C). Video S2 showed the whole shape recovery behavior of P1C3 film at the voltage of 25 V. See DOI: 10.1039/c9tc05475h |
|
This journal is © The Royal Society of Chemistry 2020 |
Click here to see how this site uses Cookies. View our privacy policy here.