Fabrication of ultrathin single-layer 2D metal–organic framework nanosheets with excellent adsorption performance via a facile exfoliation approach†
Received
13th August 2020
, Accepted 1st December 2020
First published on 8th December 2020
Abstract
Achieving ultrathin two-dimensional (2D) metal–organic framework (MOF) nanosheets is an extremely meaningful topic and still remains a great challenge. Herein, for the first time, a single-layer 2D Zn-MOF nanosheet was obtained by a facile top-down strategy based on 3D layered Zn-MOF crystals. It involves two steps: firstly, weakening the van de Waals interactions between layers by the protonation of the Zn-MOF under acidic conditions; secondly, further destroying the weakened van der Waals interactions through electrostatic interactions using negatively charged tape molecules, congo red (CR) or methyl orange (MO). Transmission electron microscopy and atomic force microscopy studies demonstrated that ultrathin single-layer (3.4 nm) 2D Zn-MOF nanosheets were obtained, with an ultra-large lateral size (ca. 6 μm), and showed unprecedented adsorption performance toward CR. For CR, the 2D Zn-MOF nanosheets could not only achieve record high uptake capacity (6639.55 mg g−1), but also present efficient and rapid removal. It is worth noting that the adsorption of CR could prevent restacking of the exfoliated 2D Zn-MOF nanosheets and facilitate further exfoliation, which in turn provided more 2D Zn-MOF nanosheets for CR adsorption. Moreover, CR can be selectively and efficiently removed even from the mixed dye solution with different charges. It is anticipated that this methodology could provide a concept to integrate exfoliation and pollutant removal into one process, fulfilling the facile synthesis of ultrathin functionalized 2D nanosheets, with high performance for pollutant removal.
Introduction
Metal–organic frameworks (MOFs) are porous crystalline materials, consisting of metal ions or clusters linked by organic ligands.1 With the unique features of high surface areas, fine-tunable pore structures and adjustable chemical functionalities,2,3 MOFs have been regarded as promising candidates for application in adsorption, catalysis, sensing and electronic materials.4–11 However, the large volume of three-dimensional (3D) bulk MOFs resulted in a slow diffusion velocity and limited accessibility to the active sites inside MOFs that showed a low efficiency and unsatisfactory performance.12,13 Therefore, increasing effort has been focused on developing materials with more efficient applications.
In recent years, two-dimensional (2D) nanomaterials have received immense interest due to their exclusive physical, chemical and optical properties that originate from their ultrathin thickness and 2D morphology.14–17 As an emerging class of functionalized 2D nanomaterials, 2D MOF nanosheets exhibit a range of fascinating attributes and interest to numerous fields.18,19 It could be an effective strategy to acquire MOF-based high-performance, by reducing one dimension of 3D bulk MOFs to a single-layer or few-layers.20,21 The obtained 2D MOF nanosheets not only inherit the advantages of 3D MOFs, such as exhibiting a high level of structural tailorability (including the pore size, shape, morphology and functional group) through suitably selecting bridging ligands and metal ions for specific applications,22,23 but also overcome the drawbacks of 3D MOFs. Firstly, with an ultrathin thickness and large lateral size, 2D MOF nanosheets have shown great potential in surface-active applications owing to their ultrahigh specific surface area.24–27 Secondly, the highly accessible active sites on the surface of 2D MOF nanosheets would facilitate the interactions with substrate molecules, yielding an improved performance.28–33 As a consequence, 2D MOF nanosheets provide an ideal model system to explore precise structure–performance relationships for rational design at atomic/molecular levels.34,35
So far, it is still a great challenge to synthesize 2D MOF nanosheets with varied structures and tailored properties at an atomic or molecular thickness.29,36,37 Like other 2D materials, 2D MOF nanosheets tend to stack along the vertical direction because of the van der Waals forces, π⋯π interactions, and/or hydrogen bonding.38,39 Conventionally, by the top-down exfoliation of physical, chemical, or liquid phase methods, 3D bulk MOFs can be exfoliated into ultrathin 2D MOF nanosheets.40–42 These methods were simple, but their further applications were limited based on the following reasons: (1) the yields of the single-layer nanosheets are relatively low and the lateral sizes are quite small;43 (2) the exfoliated 2D MOF nanosheets often suffer from structural deterioration, originating from the strong mechanical force and harsh solvents required to overcome the interlayer interactions;44–46 (3) the as-prepared 2D MOF nanosheets are liable to restack, owing to the strong interlayer interactions.39 For the bottom-up approach, the formed 2D MOF nanosheets are relatively thick (5–50 nm),47,48 and the synthesis mainly depends on the exploration of surfactants or substrates, which severely restrict their large-scale production and further applications.49,50 Thus, a more reliable exfoliation route to achieve ultrathin 2D nanosheets is highly desired.
Herein, for the first time, a new strategy was developed for the preparation of ultrathin single-layer 2D MOF nanosheets. By elaborate ligand design (Scheme S1†), a novel 3D layered MOF was constructed. The extensively weaker and generally neutral binding groups hydroxyl, ester, ether, and diazene in the layers of the framework are utilized as free-standing groups to interact with hydrogen ions (H+), facilitating the protonation of the as-synthesized MOF. The interlayer van de Waals forces can be weakened by inserting H+ ions into the interlayer space of the bulk crystals. Subsequently, the negatively charged dye congo red (CR) works as the tape to adhere onto the surface of the protonated MOF through electrostatic interactions, and further breaks the weakened van der Waals interactions between the layers to afford 2D nanosheets. The synthetic process is schematically illustrated in Scheme 1. In this study, a 3D layered MOF {[Zn2(5-OH-BDC)2L2]·1.5H2O}n (Zn-MOF; 5-OH-H2BDC = 5-hydroxy-1,3-benzenedicarboxylic acid; L = (pyridin-4-yl)methyl 3-(2-(4-((pyridin-4-yl)methoxy)phenyl)diazenyl)benzoate) is synthesized, and it has a sheet-like morphology and features of 2D layered structures that are held together through weak H-bonding interactions. In the presence of anionic dyes CR or methyl orange (MO) at a pH of 3.5, the 3D layered Zn-MOF can be readily exfoliated into an ultrathin single-layer (3.4 nm) of 2D nanosheets, with an ultra-large lateral size (ca. 6 μm). Meanwhile, CR molecules can be adsorbed onto the surface of the in situ exfoliated 2D Zn-MOF nanosheets, achieving a record high uptake capacity (6639.55 mg g−1). It is noteworthy that the exfoliation and CR adsorption can be processed at the same time, and CR adsorption could prevent restacking of the exfoliated 2D Zn-MOF nanosheets, which facilitate further exfoliation. The two processes promoted each other and were completed in a short time. To the best of our knowledge, we are the first to use in situ exfoliated 2D MOF nanosheets as an adsorbent to remove CR, affording an excellent adsorption performance.
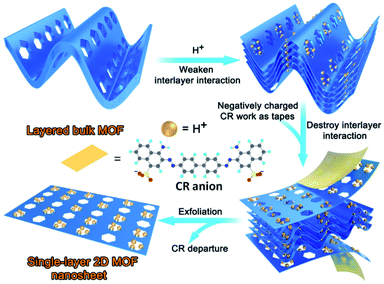 |
| Scheme 1 Schematic illustration of the synthetic process for 2D Zn-MOF nanosheets. | |
Experimental
Synthesis of (pyridin-4-yl)methyl 3-(2-(4-((pyridin-4-yl)methoxy)phenyl)diazenyl)benzoate (L)
3-[(4-Hydroxyphenyl)diazenyl]benzoic acid (4.13 mmol, 1.00 g) and K2CO3 (41.30 mmol, 5.71 g) were added into N,N-dimethylformamide (DMF, 12 mL), and then reacted with a mixture of KI (1.62 mmol, 0.27 g), 4-(chloromethyl)pyridine hydrochloride (9.09 mmol, 1.49 g) and DMF (3 mL) under stirring at room temperature. After reaction for 72 h, the solution was added into deionized water (ca. 20 mL), and a reddish solid of L was afforded. By filtering, the target product was obtained. Then it was washed thoroughly with deionized water, and dried by vacuum. Yield: 0.91 g (52%). 1H NMR (400 MHz, CDCl3, ppm): δ 8.654 (d, 4H), 8.584 (t, 1H), 8.178 (d, 1H), 9.107 (d, 1H), 7.968 (d, 2H), 7.619 (t, 1H), 7.386 (t, 4H), 7.093 (d, 2H), 5.435 (s, 2H, CH2), 5.199 (s, 2H, CH2). 13C NMR (100 MHz, CDCl3, ppm): δ 165.643, 160.907, 152.782, 150.082, 150.056, 147.297, 145.608, 144.958, 131.341, 130.645, 129.358, 126.964, 125.136, 124.185, 121.972, 121.474, 115.151, 68.416, 64.938.
Synthesis of {[Zn2(5-OH-BDC)2L2]·1.5H2O}n (Zn-MOF)
L (0.05 mmol, 21.2 mg), 5-OH-H2BDC (0.05 mmol, 9.1 mg), Zn(NO3)2·6H2O (0.1 mmol, 29.7 mg) and 9 mL H2O/DMF (7
:
2 v/v) were placed in a 20 mL vial. After stirring for 30 min, the mixture was kept in an oven for 24 h (100 °C). Orange block crystals of the Zn-MOF were obtained by cooling down to room temperature at 5 °C h−1. Then, the products were washed with deionized water, and dried at ambient temperature. Yield: 18.4 mg (54%, based on L).
Preparation of nano-Zn-MOF
The bulk Zn-MOF was activated by heating at 180 °C (8 h) under vacuum to remove the encapsulated H2O guests. After this, 100 mg of the ground activated-Zn-MOF was added into 500 mL HCl aqueous solution (pH = 3.5) and stirred for 24 h with a speed of 1500 rpm. Then, the resulting orange suspension was filtered and dried at room temperature, yielding the nano-Zn-MOF.
Preparation of 2D Zn-MOF nanosheets
In a typical experiment, 10 mg of the nano-Zn-MOF was added into 60 mL CR solution (200 ppm) under continuous stirring (2000 rpm) at a pH of 3.5. After the color of CR solution almost disappeared, the solution was filtered and thoroughly washed with DMF to remove the absorbed CR molecules for the obtainment of the 2D Zn-MOF nanosheets. The exfoliated 2D Zn-MOF nanosheets were re-dispersed in 5 mL of DMF before characterization.
Results and discussion
Characterization of the Zn-MOF
Single-crystal X-ray crystallography reveals that the Zn-MOF has the monoclinic space group P21/c. As illustrated in Fig. 1a, Zn1 and Zn2 atoms both adopt tetrahedral geometry and coordinate with two O atoms of carboxylate groups from the 5-OH-BDC ligand and two N atoms of the L ligand. Each Zn atom is connected by bridging 5-OH-BDC ligands to form a 1D [Zn(5-OH-BDC)]n chain. The chain is interlinked to its adjacent ones via L ligands to produce a wrinkled 2D (4,4) layer (Fig. 1b). These 2D layers packed together through H-bonding interactions between H atoms of the hydroxyl groups and O atoms from carboxylate groups in the adjacent layers (O5–H5A⋯O3, 2.697 Å; O10–H10⋯O6, 2.646 Å), resulting in a 3D layered MOF (Fig. 1c and S1†). As shown in Fig. 1e and f, the Zn-MOF has an obvious layered stacked structure, which was further confirmed by scanning electron microscopy (SEM) (Fig. S2†). This structure would facilitate the exfoliation of the 3D MOF into 2D nanosheets with a large lateral area. The weak interactions between the layers are critical for the layers to be delaminated by the simple exfoliation method.51 Because of the long organic backbone of the dipyridyl L ligand, large channels with opening windows of 10.24 × 25.44 Å2 (without taking the van der Waals radius into consideration) along the b axis were formed in the Zn-MOF (Fig. 1c), and it provided facile access for the interaction between H+ and the free-standing groups in 2D layers. As expected, the introduction of ester, diazene, ether and hydroxyl groups endowed the 2D layers of the Zn-MOF with a large number of oxygen and nitrogen sites decorated on the surface, which could be readily protonated under acidic conditions. These protonated functionalized layers with exposed active sites will certainly be conducive to the interaction with the negatively charged species and further destroy the weak van der Waals interactions between the layers for the exfoliation into 2D nanosheets.52 Furthermore, the good thermal stability and water stability (pH 3.0–11.0) provide a guarantee for the exfoliation of the Zn-MOF, which has been evidenced by thermogravimetric analysis (TGA) and powder X-ray diffraction (PXRD) measurements (Fig. S3 and S4†).
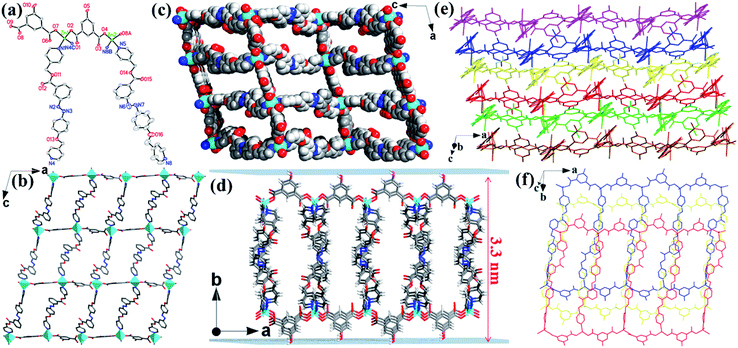 |
| Fig. 1 (a) View of the coordination environment of Zn centers in the Zn-MOF with labeling schemes. Symmetry codes: (A) x − 1, y, z; (B) x, −y + 1/2, z + 1/2; (C) x, −y + 1/2, z − 1/2. (b) View of the wrinkled 2D layer in the Zn-MOF extending along the ac plane. (c) View of the 3D framework with 1D channels in the Zn-MOF looking down the b axis. (d) The 2D layered structure in the Zn-MOF with a single-layer height of 3.3 nm. (e and f) View of the 3D layered structure in the Zn-MOF. Atom color codes: Zn, cyan; O, red; N, blue; C, gray. | |
 |
| Fig. 2 (a) Representative SEM image of nano-Zn-MOF crystals. (b and c) Representative SEM images of 2D CR@Zn-MOF naonosheets. (d) Representative AFM image of a 2D CR@Zn-MOF nanosheet. (e) The height profile, colour-coded blue, is measured along the corresponding track shown in (d). (f) Representative TEM image of a 2D CR@Zn-MOF nanosheet. | |
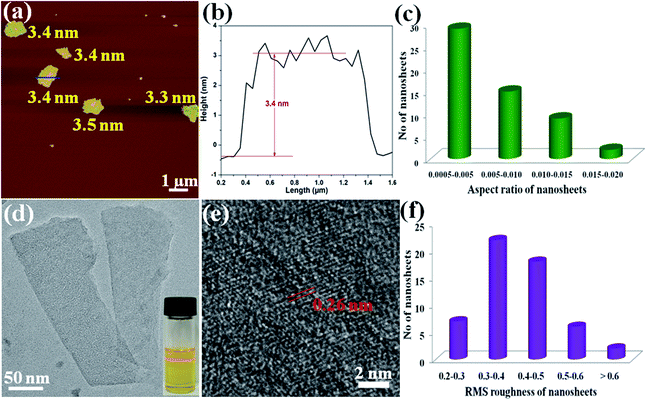 |
| Fig. 3 (a) Representative AFM image of 2D Zn-MOF nanosheets. (b) The height profile, color-coded blue, is measured along the corresponding track shown in (a). (c) Histogram plot of the aspect ratio (H/L) distribution. Most of the nanosheets' aspect ratio ranges between 0.0005 and 0.005. (d) Representative TEM image of a 2D Zn-MOF nanosheet. Inset: Photograph of the Tyndall effect of the 2D Zn-MOF nanosheet suspension. (e) HRTEM image of a typical 2D Zn-MOF nanosheet. (f) Histogram plot of the RMS roughness distribution. Most of the nanosheets' RMS roughness ranges between 0.3 and 0.5 nm. | |
Exfoliation studies
Based on the unique layered structure of the 3D Zn-MOF, we tried to develop a new top-down approach to achieve ultrathin 2D MOF nanosheets. Firstly, by stirring in HCl aqueous solution (pH = 3.5) for 24 h, the 3D bulk Zn-MOF was broken into nanoparticles. The acquired nano-Zn-MOF particles possess rod-shaped morphology with an average size of 150 nm (Fig. 2a), and still have the same layered structure of the 3D bulk Zn-MOF as evidenced by the PXRD studies (Fig. S5†). After treatment with HCl aqueous solution (pH = 3.5), the interactions between the extensively weaker and generally neutral binding groups in the layers and hydrogen ions (H+) would facilitate the protonation of the as-synthesized MOF, and the interlayer van de Waals forces can be weakened by inserting H+ ions into the interlayer space. Fourier transform infrared (FT-IR), UV-vis spectroscopy and solid state 13C NMR measurements were performed to gain insight into the protonation of the MOF. By comparison with the pristine Zn-MOF, some changes were clearly observed in the FT-IR spectrum of the sample after acid treatment (Fig. S6†). Specifically for the peaks at 3060, 1723, 1622 and 1251 cm−1, which are assigned to the vibrations of O–H, C
O, N
N and C–O–C groups, their obviously changed absorption wavenumbers and intensities evidenced the protonation of the Zn-MOF. After treatment with HCl aqueous solution, the changes of the chemical shift for the groups of C
O and C–O–C in 13C NMR spectra (Fig. S7†) and the distinct shift of the wavelength together with its noticeable colour change for the sample in the solid UV-vis spectroscopy (Fig. S8†) further supported the protonation of the Zn-MOF. Secondly, the anionic molecule CR was selected as the tape and its molecular structure is predominantly negative at a pH of 3.5 (Scheme S2†), owing to the fact that the isoelectric point of CR is near pH 3.53,54 As schematically illustrated in Scheme 1, CR can be attached on the surface of the protonated Zn-MOF at a pH of 3.5 as a result of the electrostatic interactions between the positive charges of the protonated 2D layers and SO3− groups in CR, which has been verified by the study of the zeta potential (Fig. S9†). FT-IR measurement provided more information. As demonstrated in Fig. S10,† the appreciably enlarged bands at 1211 and 1034 cm−1 in the spectrum of CR@Zn-MOF nanosheets are attributed to the antisymmetric and symmetric stretching vibrations of the SO3− groups of CR, which are positioned at 1223 and 1039 cm−1 in the spectrum of pure CR, confirming that CR was adsorbed on the surface of the protonated Zn-MOF.55 After CR adsorption, the characteristic protonated peaks of O–H, C
O, and N
N located at 3365, 1724, and 1623 cm−1 shifted to 3339, 1718 and 1640 cm−1, respectively. The obviously shifted wavenumbers of these characteristic protonated peaks and the SO3− group verified that there are electrostatic attraction and hydrogen bonding in CR adsorption. Besides, the steep decrease of weight loss in the TGA of CR@Zn-MOF nanosheets when the temperature was higher than 225 °C (Fig. S4†), corresponding to the departure of the CR molecule, further confirmed the relatively weaker interaction of electrostatic attraction and hydrogen bonding between CR molecules and Zn-MOF nanosheets. In addition, the electrostatic interaction acts as a driving force in exfoliation, and it further destroys the weakened van der Waals interactions between the layers, yielding 2D CR@Zn-MOF nanosheets. The CR molecules absorbed on the surface of 2D Zn-MOF nanosheets could prevent restacking of the exfoliated 2D Zn-MOF nanosheets and facilitate subsequent exfoliation.
To gain further insights into the exfoliation behavior, the colloidal suspensions after exfoliation were collected and dropped on the substrates for characterization by SEM, transmission electron microscopy (TEM), atomic force microscopy (AFM) and energy-dispersive X-ray spectroscopy (EDS). The typical SEM image in Fig. 2b shows that the product lies flat on the Si/SiO2 substrate with a lateral size up to several micrometers, which is different from the rod-shaped morphology of the nano-Zn-MOF (Fig. 2a). Even a nanosheet with size up to ca. 10 μm can also be noticed (Fig. S11†), and the thickness of 2D nanosheets is about 17 nm (Fig. 2c). The EDS spectrum proved the existence of S by the corresponding elemental mapping (Fig. S12†), further confirming that CR molecules were attached on 2D Zn-MOF nanosheets. Meanwhile, the peak intensity in PXRD of the Zn-MOF significantly decreased throughout the interaction with CR (Fig. S13†), which demonstrated that the vast majority of the layered architecture had collapsed.56 The presence of an amorphous-like broad diffraction in a 2θ range of 5–15° is likely due to the scattering from an aggregate of the exfoliated 2D nanosheets.28,57 Upon irradiation with a laser beam, the clear Tyndall effect revealed their colloidal properties (Fig. S14†). Firm evidence for the exfoliation into 2D nanosheets comes from the AFM study. As illustrated in Fig. 2d, the exfoliated nanosheet possessed a lateral dimension of up to ca. 7 μm, with a thickness of approximately 17.8 nm (Fig. 2e), which is in agreement with the SEM result (Fig. 2c). The edges of the measured nanosheets were usually slightly higher than the middle part, maybe because of the overlapping of the small broken flexes (one upon each). The TEM images in Fig. 2f and S15† clearly show the sheet-like morphology held by the exfoliated 2D nanosheets. These results demonstrated the successful exfoliation of 3D bulk Zn-MOF into 2D Zn-MOF nanosheets.
To obtain the single-layer of MOF nanosheets, the above acquired 2D CR@Zn-MOF nanosheets were thoroughly washed with DMF to remove the tape molecules of CR. Then AFM measurements were performed to prove the successful synthesis of single-layer 2D nanosheets and obtain further insight into their thickness (Fig. 3a and b). The height of the as-exfoliated nanosheets was measured to be approximately 3.4 ± 0.1 nm (Fig. 3b), in basic agreement with the single-layer thickness of the 2D Zn-MOF nanosheet determined from the crystallographic data (Fig. 1d). With the help of AFM analysis, the thickness and aspect-ratio were calculated for the products. The statistical distribution plots were made from 55 images of each sample (Fig. S16†). Most of the 2D nanosheets have a thickness in the range of 3.0–4.0 nm (Fig. S16b†), and their lateral length ranges from 500 to 1000 nm (Fig. S16d†), yielding an aspect ratio (height/length) of about 0.0005–0.005 (Fig. 3c). Importantly, the RMS roughness of most nanosheets ranges between 0.3 and 0.5 nm (Fig. 3f), indicating that a smooth monolayer was achieved for the 2D nanosheets. The typical Tyndall effect also emerged when a red laser goes through the suspension of the formed 2D Zn-MOF nanosheets (inset in Fig. 3d), verifying the fine dispersion of the ultrathin nanosheets and their successful exfoliation. Moreover, a typical TEM image of single-layer 2D Zn-MOF nanosheets is captured and displayed in Fig. 3d. As known, most 2D MOF materials are unstable under electron beam irradiation by high-resolution TEM (HRTEM), leading to the rapid destruction of their structure.50 Fortunately, we were able to visualize the lattice fringes of the 2D Zn-MOF nanosheets, and they presented a crystalline nature (Fig. 3e). Unlike the bulk sample, the exfoliated nanosheets do not give rise to any diffraction in the SAED pattern (Fig. S17†), owing to the lack of sufficient layers and the inherent higher-angle Bragg reflections having very low relative intensities for these inorganic-organic hybrid monolayers.14 All the aforementioned results confirmed that the single-layer 2D Zn-MOF nanosheets were successfully prepared. Not only that, partially as-exfoliated 2D single-layer nanosheets were also found (Fig. S18†). The TEM image of these large-sized nanosheets (ca. 6 μm) exhibited slightly wrinkled and curled planes (Fig. S19†), originating from the dimensional characteristics of the nanosheets.39
The integrity of the chemical composition of the as-synthesized 2D Zn-MOF nanosheets was explored by X-ray photoelectron spectroscopy (XPS). As demonstrated in Fig. S20,† the good coincidence of the peaks for the 2D Zn-MOF nanosheets with those of the bulk Zn-MOF is indicative of the intact chemical composition preserved for the 2D nanosheets. The structural integrity was further explored by the measurements of PXRD, solid state 13C NMR, FT-IR spectroscopy and TGA. The PXRD patterns of 2D Zn-MOF nanosheets match well with those of the bulk Zn-MOF (Fig. S21†), and the decreased intensity of the PXRD patterns is consistent with that of previously reported 2D materials.58,59 The 13C NMR comparisons further reveal the intact structure maintained by the 2D nanosheets (Fig. S22†). More validation for the structural integrity of the nanosheets comes from the FT-IR spectra (Fig. S23†) and TGA curve of the sample (Fig. S4†), which agree well with those of the pristine Zn-MOF.
Mechanism exploration
In view of the above observation that the 3D layered Zn-MOF can be exfoliated into 2D Zn-MOF nanosheets with anionic CR molecules at a pH of 3.5, we contend that anionic CR molecules and acidic conditions worked together in the exfoliation process. Then a series of experiments were devised to verify this assertion. Under the synthetic conditions similar to the above, but without anionic CR molecules, there were not any 2D Zn-MOF nanosheets obtained. Similarly, the 3D layered Zn-MOF could not be exfoliated into 2D nanosheets using anionic CR molecules in neutral or alkaline solutions. However, the protonated 3D Zn-MOF can be exfoliated into 2D nanosheets by the ultrasound method in ethanol, but with a larger thickness (16.8 nm; Fig. S24†) and obviously lower yield (<8%). These results further confirmed that H+ ions did work in the exfoliation process. Then, does the selection of tape anionic molecules have any effect on the exfoliation? Two compounds MO and Na2SO4, which can be dissociated into an anionic form with different sizes at a pH of 3.5, were chosen to explore this issue. Interestingly, when MO molecules were stirred with the 3D layered Zn-MOF at a pH of 3.5, 2D MO@Zn-MOF nanosheets were formed (Fig. S25†). After washing, the AFM measurement evidenced that the resulting 2D Zn-MOF nanosheets hold the single-layer structural feature (Fig. S26†). Nevertheless, the 3D layered Zn-MOF still keeps its bulk morphology when Na2SO4 was selected as the tape molecule (Fig. S27†). Based on the above results, we were aware that acidic conditions and suitably sized anionic molecules play a joint role in the exfoliation process. The anionic molecules with suitable sizes can be used as tapes to detach the 3D layered Zn-MOF and further prevent restacking of the exfoliated nanosheets.
Adsorption study
Given that CR can be absorbed on the surface of the in situ exfoliated 2D Zn-MOF nanosheets in exfoliation, which is toxic and considered to be a primary pollutant of water resources,60 we thought of investigating their CR adsorption performance. The pH value greatly influences CR adsorption, and the effect of pH on CR removal efficiency was investigated in the range of 3.5–10.5. As shown in Fig. S28,† the removal efficiency reduced dramatically with the increasing pH value, showing a similar trend to the change of zeta potential along with the pH value (Fig. S9a†), which further confirmed that electrostatic interaction acts as a driving force in CR adsorption. At lower pH, the oxygen and nitrogen sites on the surfaces of the Zn-MOF can be readily protonated, which is conductive to CR adsorption and accelerates the exfoliation of the Zn-MOF. More 2D MOF nanosheets can be obtained by the exfoliation of the Zn-MOF, leading to more exposed surface with extensive active sites to interact with CR molecules. So, H+ plays a vital role in the exfoliation and adsorption process. When the pH value is lower than 3.0, the framework of the Zn-MOF may collapse. As a result, the optimum pH value of 3.5 was selected for the subsequent adsorption experiments.
As seen in Table 1, the CR uptake capacity increased with the increasing concentration, and reached the maximum uptake capacity of 6639.55 mg g−1. The equilibrium adsorption data were fitted with Langmuir, Freundlich and Dubinin–Radushkevich (D–R) isotherm models (Fig. 4). The corresponding equations with detailed analysis are given in the ESI.† By comparison of the fitted parameters for the three models (Table S1†), it can be seen that the Langmuir isotherm model (R2 = 0.999) best fits the experimental data, which indicates a monolayer adsorption of CR molecules onto the homogeneous surface of the adsorbent. Although the value of the regression coefficient (R2 = 0.921) calculated using the D–R model is lower than that obtained from the Langmuir model, it also well fits the isotherm adsorption data. Importantly, the equilibrium adsorption energy E value calculated using the D–R model can be used to judge the adsorption mechanism. It is considered that if the value of E lies between 8 and 16 kJ mol−1, then the adsorption reaction occurs by an ion exchange process; if E < 8 kJ mol−1, the adsorption process is mainly a physical adsorption and if E > 16 kJ mol−1, then the adsorption is dominated by a chemical process.61 The value of E for CR calculated in this study is lower than 8 kJ mol−1, suggesting that the physical adsorption mechanism plays an important role in CR adsorption, such as electrostatic attraction. The maximum theoretical uptake capacity of CR calculated from the Langmuir equation was 6713.26 mg g−1, which matched well with the experimental data (6639.55 mg g−1). To our knowledge, this value is the highest among all reported data for CR, far exceeding that of various benchmark materials (Table S2†). It is worth noting that the exfoliated 2D Zn-MOF nanosheets with given dosage can remove more than 99.35% of CR in the concentration range from 40 to 400 ppm (Table 1). Such unprecedented removal performance could stem from the unique structure of the 2D MOF nanosheets, containing large lateral size, high specific surface area, ultimate exposure of the accessible active sites and the positively charged layers.
Table 1 CR removal performances of 2D Zn-MOF nanosheets
C
0 (ppm) |
C
e (ppm) |
q
m (mg g−1) |
Removal efficiency (%) |
40 |
0.12 |
478.60 |
99.71 |
60 |
0.39 |
715.32 |
99.35 |
100 |
0.46 |
1194.52 |
99.54 |
150 |
0.48 |
1794.27 |
99.68 |
200 |
0.52 |
2393.82 |
99.74 |
250 |
0.67 |
2991.93 |
99.73 |
300 |
0.91 |
3589.15 |
99.70 |
400 |
2.15 |
4774.17 |
99.46 |
500 |
21.85 |
5737.76 |
95.63 |
600 |
46.99 |
6636.08 |
92.17 |
700 |
146.71 |
6639.55 |
79.04 |
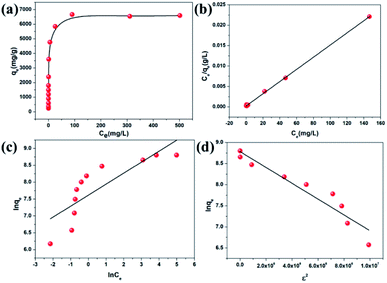 |
| Fig. 4 (a) CR adsorption isotherm for 2D Zn-MOF nanosheets. (b) Langmuir, (c) Freundlich and (d) Dubinin–Radushkevich isotherm model fitting for CR adsorption. | |
Fast adsorption rate, a material can remove most of the target contaminants in a short time, is also a very important parameter to assess the efficiency and practicability of an adsorbent in economical wastewater disposal system. It is a very exciting discovery that more than 99.12% of CR (60 ppm) could be removed within 10 min (Fig. 5a). Further, the kinetics of higher concentrations was also investigated. As shown in Fig. 5b and c, fairly high uptake capacities were accomplished within a short time. The collected experimental data were well fitted by a pseudo-second order kinetic model (Fig. 5d, Table S3†). These results revealed that the in situ exfoliated 2D Zn-MOF nanosheets were fairly efficient in removing CR molecules. On the one hand, the CR molecules adsorbed on the surfaces of the Zn-MOF accelerated the process of exfoliation; on the other hand, the in situ exfoliated 2D Zn-MOF nanosheets provided more exposed active sites for CR adsorption. The two processes promoted each other and were completed in a short time.
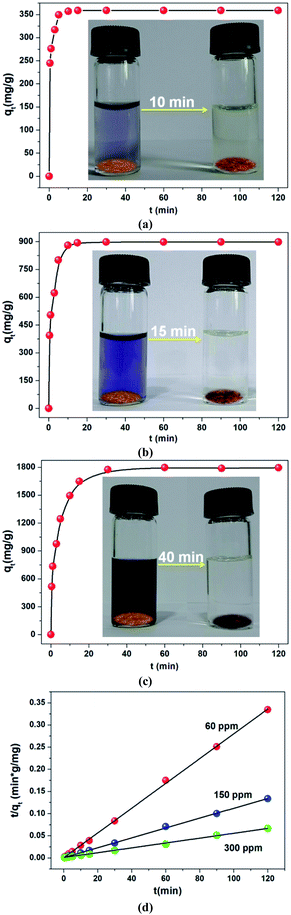 |
| Fig. 5 The adsorption capacity of 2D Zn-MOF nanosheets for CR at different concentrations: 60 ppm (a), 150 ppm (b), and 300 ppm (c), and fitting results from the pseudo-second-order kinetic model for different concentrations (d). The inset photo in (a), (b) and (c) shows that the CR could be removed in a short time. | |
Since electrostatic interaction dominated CR adsorption, the 2D Zn-MOF nanosheets would show high selectivity for CR sorption in the presence of mixed dyes with different charges. Positively charged rhodamine 6G (R6G) and rhodamine B (RhB), and neutral dye fluorescein (FO; Scheme S3†) were chosen as the models for the selective adsorption experiments. By adding the adsorbents into the mixtures of R6G and CR, RhB and CR, and FO and CR, respectively, the concentration changes of the dye mixtures were monitored by UV/Vis spectroscopy. As shown in Fig. 6, all absorption peaks of CR disappeared quickly, leaving the characteristic absorption peaks of R6G, RhB, and FO, respectively. Furthermore, the four dyes R6G, RhB, FO and CR were mixed together and the adsorbents were added into the mixed solution. The result in Fig. 6d clearly shows that CR molecules could be adsorbed with a fast rate, whereas the cationic and neutral dye molecules remained in solution, indicating that the 2D Zn-MOF nanosheets have a strong preference and an ultrahigh selectivity for CR sorption. These observations strongly suggested that CR adsorption was dominated by electrostatic interaction, which was further supported by the adsorption performance for other anionic dyes (Scheme S2†). As expected, the anionic dyes with different sizes can be efficiently adsorbed by 2D Zn-MOF nanosheets, with uptake capacities of 746.52, 790.68 and 819.87 mg g−1 for MO, acid orange G (AO) and acid red 29 (AR), respectively (Fig. S29–S31 and Table S4†). The obviously higher adsorption capacity obtained for CR can be ascribed to its flat molecular structure together with the substantial SO3− groups that locate at the desirable position in CR molecules, which aids the interaction with the 2D adsorbent. Moreover, for the mixed anionic dyes, high adsorption capability can also be achieved for 2D Zn-MOF nanosheets, and the anionic dye mixture can be efficiently removed (Fig. S32†).
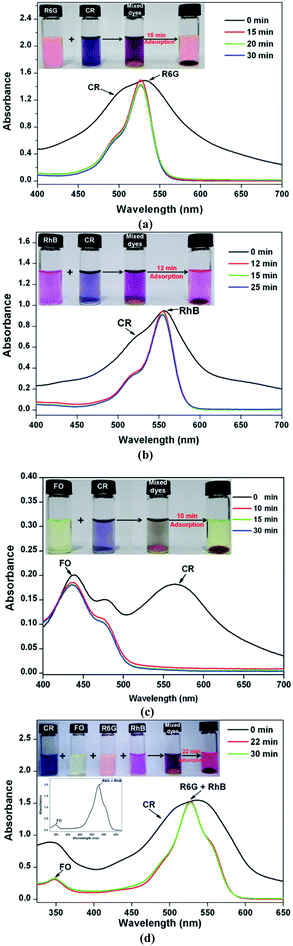 |
| Fig. 6 UV-vis spectra of selective adsorption experiments in the mixed dyes with different charges for 2D Zn-MOF nanosheets: (a) CR&R6G (180/10 ppm); (b) CR&RhB (90/10 ppm); (c) CR&FO (60/20 ppm) and (d) CR&R6G&RhB&FO (180/10/10/20 ppm). The inset photographs show separation of a mixture using 2D Zn-MOF nanosheets. | |
Stability and reusability are two important factors in the application of an adsorbent. And the stability of an adsorbent after dye adsorption is directly related to its regeneration. As shown in Fig. S33,† even after seven cycle experiments, the PXRD patterns of the regenerated 2D Zn-MOF nanosheets matched well with those of the as-synthesized sample, which confirms their good stability and recyclability. Moreover, the 2D Zn-MOF nanosheets presented an appreciable cycle performance, and 86.79% of the initial CR uptake capacity can be retained after seven adsorption–desorption cycles (Fig. S34†). Such fair regeneration ability further confirmed that CR adsorption on 2D Zn-MOF nanosheets was mainly a physical and reversible process, which was dominated by electrostatic interaction. The slight decrease in CR adsorption capacity may originate from the comprehensive factors that combined the adsorbent loss in each cycle during recovery, trace amount of the sample degradation, incomplete CR desorption, etc. In a word, the 2D Zn-MOF nanosheet-based adsorbent establishes an efficient CR adsorption from the aqueous solution, with an ultrahigh uptake capacity.
Conclusions
In conclusion, we have successfully developed a new top-down strategy for the preparation of ultrathin single-layer 2D MOF nanosheets by exfoliation of a novel 3D layered MOF. In the presence of CR or MO at a pH of 3.5, the elaborately constructed 3D layered Zn-MOF, decorated with ester, diazene, ether and hydroxyl groups in the 2D layers, can be readily protonated and exfoliated into 2D Zn-MOF nanosheets, with an ultrathin single-layer (3.4 nm) and ultra-large lateral size (ca. 6 μm). Significantly, the in situ exfoliated 2D Zn-MOF nanosheets can simultaneously adsorb CR through electrostatic interactions. The adsorbed anionic molecules could prevent restacking of the exfoliated 2D Zn-MOF nanosheets and facilitate further exfoliation. The CR uptake capacity achieved a record-high value of 6639.55 mg g−1, surpassing that of all reported adsorbents. The large lateral size, high specific surface area and ultimate exposure of the accessible active sites can be responsible for the impressive results. It is noteworthy that the two processes of exfoliation and CR adsorption promoted each other, and were completed in a short time. Our work provides a new concept for the facile synthesis of ultrathin single-layer 2D MOF nanosheets, which not only has the potential for mass production at low-cost, but could also efficiently remove pollutants.
Conflicts of interest
There are no conflicts to declare.
Acknowledgements
This work was supported by the National Natural Science Foundation of China (21401006, 21771097 and U1304210). We are grateful for the PXRD investigations performed by Fei-Fan Lang (Department of Chemistry, University of Sheffield). We also acknowledge Wei Liu for the single crystal structure analysis (supported by Top Discipline in Materials Science of Shandong Province).
References
- M. Zhao, Y. Huang, Y. Peng, Z. Huang, Q. Ma and H. Zhang, Chem. Soc. Rev., 2018, 47, 6267–6295 RSC.
- X.-L. Lv, S. Yuan, L.-H. Xie, H. F. Darke, Y. Chen, T. He, C. Dong, B. Wang, Y.-Z. Zhang, J.-R. Li and H.-C. Zhou, J. Am. Chem. Soc., 2019, 141, 10283–10293 CrossRef CAS PubMed.
- H. Wang, W. P. Lustig and J. Li, Chem. Soc. Rev., 2018, 47, 4729–4756 RSC.
- P. Ji, X. Feng, P. Oliveres, Z. Li, A. Murakami, C. Wang and W. Lin, J. Am. Chem. Soc., 2019, 141, 14878–14888 CrossRef CAS PubMed.
- C. Yu, Z. Shao and H. Hou, Chem. Sci., 2017, 8, 7611–7619 RSC.
- Z. Shao, C. Huang, J. Dang, Q. Wu, Y. Liu, J. Ding and H. Hou, Chem. Mater., 2018, 30, 7979–7987 CrossRef CAS.
- Z. Shao, C. Huang, Q. Wu, Y. Zhao, W. Xu, Y. Liu, J. Ding and H. Hou, J. Hazard. Mater., 2019, 378, 120719 CrossRef CAS PubMed.
- T. Hashem, A. H. Ibrahim, C. Wöll and M. H. Alkordi, ACS Appl. Nano Mater., 2019, 2, 5804–5808 CrossRef CAS.
- W. P. Lustig, S. Mukherjee, N. D. Rudd, A. V. Desai, J. Li and S. K. Ghosh, Chem. Soc. Rev., 2017, 46, 3242–3285 RSC.
- M. H. Hassan, R. R. Haikal, T. Hashem, J. Rinck, F. Koeniger, P. Thissen, H. Stefan, C. Wöll and M. H. Alkordi, ACS Appl. Mater. Interfaces, 2019, 11, 6442–6447 CrossRef CAS PubMed.
- M. H. Hassan, A. B. Soliman, W. A. Elmehelmey, A. A. Abugable, S. G. Karakalos, M. Elbahri, A. Hassanien and M. H. Alkordi, Chem. Commun., 2019, 55, 31–34 RSC.
- L. Cao, Z. Lin, F. Peng, W. Wang, R. Huang, C. Wang, J. Yan, J. Liang, Z. Zhang, T. Zhang, L. Long, J. Sun and W. Lin, Angew. Chem., Int. Ed., 2016, 55, 4962–4966 CrossRef CAS PubMed.
- Y. Wang, M. Zhao, J. Ping, B. Chen, X. Cao, Y. Huang, C. Tan, Q. Ma, S. Wu, Y. Yu, Q. Lu, J. Chen, W. Zhao, Y. Ying and H. Zhang, Adv. Mater., 2016, 28, 4149–4155 CrossRef CAS PubMed.
- G. A. Bhat, S. Haldar, S. Verma, D. Chakraborty, R. Vaidhyanathan and R. Murugavel, Angew. Chem., Int. Ed., 2019, 58, 16844–16849 CrossRef CAS PubMed.
- W. Zheng, J. Lee, Z.-W. Gao, Y. Li, S. Lin, S. P. Lau and L. Y. S. Lee, Adv. Energy Mater., 2020, 10, 1903490 CrossRef CAS.
- S. Haldar, K. Roy, R. Kushwaha, S. Ogale and R. Vaidhyanathan, Adv. Energy Mater., 2019, 9, 1902428 CrossRef CAS.
- S. Haldar, K. Roy, S. Nandi, D. Chakraborty, D. Puthusseri, Y. Gawli, S. Ogale and R. Vaidhyanathan, Adv. Energy Mater., 2018, 8, 1702170 CrossRef.
- R. Dong, T. Zhang and X. Feng, Chem. Rev., 2018, 118, 6189–6235 CrossRef CAS PubMed.
- C.-X. Yu, F.-L. Hu, J.-G. Song, J.-L. Zhang, S.-S. Liu, B.-X. Wang, H. Meng, L.-L. Liu and L.-F. Ma, Sens. Actuators, B, 2020, 310, 127819 CrossRef CAS.
- C.-X. Yu, K.-Z. Wang, X.-J. Li, D. Liu, L.-F. Ma and L.-L. Liu, Cryst. Growth Des., 2020, 20, 5251–5260 CrossRef CAS.
- J. Huang, Y. Li, R.-K. Huang, C.-T. He, L. Gong, Q. Hu, L. Wang, Y.-T. Xu, X.-Y. Tian, S.-Y. Liu, Z.-M. Ye, F. Wang, D.-D. Zhou, W.-X. Zhang and J.-P. Zhang, Angew. Chem., Int. Ed., 2018, 57, 4632–4636 CrossRef CAS PubMed.
- H.-S. Wang, J. Li, J.-Y. Li, K. Wang, Y. Ding and X.-H. Xia, NPG Asia Mater., 2017, 9, e354 CrossRef CAS.
- R. Xu, Q. Ji, C. Hu, C. Tang, R. Liu, X. Zhang and J. Qu, Chem. Eng. J., 2019, 382, 122658 CrossRef.
- C. Tan, K. Yang, J. Dong, Y. Liu, Y. Liu, J. Jiang and Y. Cui, J. Am. Chem. Soc., 2019, 141, 17685–17695 CrossRef CAS PubMed.
- J. Duan, Y. Li, Y. Pan, N. Behera and W. Jin, Coord. Chem. Rev., 2019, 395, 25–45 CrossRef CAS.
- M. Cai, Q. Liu, Z. Xue, Y. Li, Y. Fan, A. Huang, M.-R. Li, M. Croft, T. A. Tyson, Z. Ke and G. Li, J. Mater. Chem. A, 2020, 8, 190–195 RSC.
- L. Cong, H. Xie and J. Li, Adv. Energy Mater., 2017, 7, 1601906 CrossRef.
- J. Dong, X. Li, K. Zhang, Y. Di Yuan, Y. Wang, L. Zhai, G. Liu, D. Yuan, J. Jiang and D. Zhao, J. Am. Chem. Soc., 2018, 140, 4035–4046 CrossRef CAS PubMed.
- Y. Ding, Y.-P. Chen, X. Zhang, L. Chen, Z. Dong, H.-L. Jiang, H. Xu and H.-C. Zhou, J. Am. Chem. Soc., 2017, 139, 9136–9139 CrossRef CAS PubMed.
- G. Lan, Z. Li, S. S. Veroneau, Y.-Y. Zhu, Z. Xu, C. Wang and W. Lin, J. Am. Chem. Soc., 2018, 140, 12369–12373 CrossRef CAS PubMed.
- S. Duan, L. Wu, J. Li, Y. Huang, X. Tan, T. Wen, T. Hayat, A. Alsaedi and X. Wang, J. Hazard. Mater., 2019, 373, 580–590 CrossRef CAS PubMed.
- X. H. Xiong, Y. Tao, Z. W. Yu, L. X. Yang, L. J. Sun, Y. L. Fan and F. Luo, Chem. Eng. J., 2020, 384, 123240 CrossRef CAS.
- C. Wang, C. He, Y.-H. Luo, S. Su, J.-Y. Wang, D.-L. Hong, X.-T. He, C. Chen and B.-W. Sun, Chem. Eng. J., 2020, 379, 122337 CrossRef CAS.
- S. Zhao, Y. Wang, J. Dong, C.-T. He, H. Yin, P. An, K. Zhao, X. Zhang, C. Gao, L. Zhang, J. Lv, J. Wang, J. Zhang, A. M. Khattak, N. A. Khan, Z. Wei, J. Zhang, S. Liu, H. Zhao and Z. Tang, Nat. Energy, 2016, 1, 16184 CrossRef CAS.
- J. Li, Q. Duan, Z. Wu, X. Li, K. Chen, G. Song, A. Alsaedi, T. Hayat and C. Chen, Chem. Eng. J., 2020, 383, 123189 CrossRef CAS.
- J. Liu, W. Shi and X. Wang, J. Am. Chem. Soc., 2019, 141, 18754–18758 CrossRef CAS PubMed.
- L. Zhuang, L. Ge, H. Liu, Z. Jiang, Y. Jia, Z. Li, D. Yang, R. K. Hocking, M. Li, L. Zhang, X. Wang, X. Yao and Z. Zhu, Angew. Chem., Int. Ed., 2019, 58, 13565–13572 CrossRef CAS PubMed.
- V. Nicolosi, M. Chhowalla, M. G. Kanatzidis, M. S. Strano and J. N. Coleman, Science, 2013, 340, 1226419 CrossRef.
- Y. Wang, L. Li, L. Yan, X. Gu, P. Dai, D. Liu, J. G. Bell, G. Zhao, X. Zhao and K. M. Thomas, Chem. Mater., 2018, 30, 3048–3059 CrossRef CAS.
- C. Tan, X. Cao, X.-J. Wu, Q. He, J. Yang, X. Zhang, J. Chen, W. Zhao, S. Han, G.-H. Nam, M. Sindoro and H. Zhang, Chem. Rev., 2017, 117, 6225–6331 CrossRef CAS PubMed.
- P.-Z. Li, Y. Maeda and Q. Xu, Chem. Commun., 2011, 47, 8436–8438 RSC.
- V. K.-M. Au, K. Nakayashiki, H. Huang, S. Suginome, H. Sato and T. Aida, J. Am. Chem. Soc., 2019, 141, 53–57 CrossRef CAS PubMed.
- H. Zhang, ACS Nano, 2015, 9, 9451–9469 CrossRef CAS PubMed.
- F. Xue, P. Kumar, W. Xu, K. A. Mkhoyan and M. Tsapatsis, Chem. Mater., 2018, 30, 69–73 CrossRef CAS.
- S. Jeong, D. Yoo, M. Ahn, P. Miró, T. Heine and J. Cheon, Nat. Commun., 2015, 6, 5763 CrossRef CAS PubMed.
- Y. Peng, Y. Li, Y. Ban, H. Jin, W. Jiao, X. Liu and W. Yang, Science, 2014, 346, 1356–1359 CrossRef CAS PubMed.
- T. Rodenas, I. Luz, G. Prieto, B. Seoane, H. Miro, A. Corma, F. Kapteijn, F. X. Llabrés i Xamena and J. Gascon, Nat. Mater.c, 2015, 14, 48–55 CrossRef CAS PubMed.
- F.-L. Li, P. Wang, X. Huang, D. J. Young, H.-F. Wang, P. Braunstein and J.-P. Lang, Angew. Chem., Int. Ed., 2019, 58, 7051–7056 CrossRef CAS PubMed.
- J. Duan, S. Chen and C. Zhao, Nat. Commun., 2017, 8, 15341 CrossRef CAS PubMed.
- M. Zhao, Y. Wang, Q. Ma, Y. Huang, X. Zhang, J. Ping, Z. Zhang, Q. Lu, Y. Yu, H. Xu, Y. Zhao and H. Zhang, Adv. Mater., 2015, 27, 7372–7378 CrossRef CAS PubMed.
- W.-M. Liao, J.-H. Zhang, S.-Y. Yin, H. Lin, X. Zhang, J. Wang, H.-P. Wang, K. Wu, Z. Wang, Y.-N. Fan, M. Pan and C.-Y. Su, Nat. Commun., 2018, 9, 2401 CrossRef PubMed.
- J. Wu, J. Peng, Z. Yu, Y. Zhou, Y. Guo, Z. Li, Y. Lin, K. Ruan, C. Wu and Y. Xie, J. Am. Chem. Soc., 2018, 140, 493–498 CrossRef CAS PubMed.
- A. Waheed, M. Mansha, I. W. Kazi and N. Ullah, J. Hazard. Mater., 2019, 369, 528–538 CrossRef CAS PubMed.
- K. Litefti, M. S. Freire, M. Stitou and J. González-Álvarez, Sci. Rep., 2019, 9, 16530 CrossRef PubMed.
- C. Aoopngan, J. Nonkumwong, S. Phumying, W. Promjantuek, S. Maensiri, P. Noisa, S. Pinitsoontorn, S. Ananta and L. Srisombat, ACS Appl. Nano Mater., 2019, 2, 5329–5341 CrossRef CAS.
- H. Yang and H. Fei, Chem. Commun., 2017, 53, 7064–7067 RSC.
- D. Sheberla, L. Sun, M. A. Blood-Forsythe, S. Er, C. R. Wade, C. K. Brozek, A. Aspuru-Guzik and M. Dincă, J. Am. Chem. Soc., 2014, 136, 8859–8862 CrossRef CAS PubMed.
- Y. Peng, Y. Huang, Y. Zhu, B. Chen, L. Wang, Z. Lai, Z. Zhang, M. Zhao, C. Tan, N. Yang, F. Shao, Y. Han and H. Zhang, J. Am. Chem. Soc., 2017, 139, 8698–8704 CrossRef CAS PubMed.
- H. Xu, J. Gao, X. Qian, J. Wang, H. He, Y. Cui, Y. Yang, Z. Wang and G. Qian, J. Mater. Chem. A, 2016, 4, 10900–10905 RSC.
- D. Shetty, I. Jahovic, J. Raya, F. Ravaux, M. Jouiad, J.-C. Olsen and A. Trabolsi, J. Mater. Chem. A, 2017, 5, 62–66 RSC.
- K. Saltalı, A. Sarı and M. Aydın, J. Hazard. Mater., 2007, 141, 258–263 CrossRef PubMed.
Footnote |
† Electronic supplementary information (ESI) available: Materials and physical measurements, X-ray data collection and structure determination, adsorption experiments, PXRD patterns, TGA curves, EDX spectra, SEM images, TEM images, SAED patterns, solid state 13C NMR spectra, FT-IR spectra, XPS survey spectra, AFM images, UV-vis spectra, additional figures, tables and X-ray data. CCDC 1888890. For ESI and crystallographic data in CIF or other electronic format see DOI: 10.1039/d0ta07959f |
|
This journal is © The Royal Society of Chemistry 2021 |
Click here to see how this site uses Cookies. View our privacy policy here.