DOI:
10.1039/D0RA07866B
(Paper)
RSC Adv., 2020,
10, 39146-39159
Influence of lattice strain on Fe3O4@carbon catalyst for the destruction of organic dye in polluted water using a combined adsorption and Fenton process†
Received
14th September 2020
, Accepted 16th October 2020
First published on 26th October 2020
Abstract
In this study, 8, 25 and 50 wt% Fe3O4@activated carbon (AC) catalysts were prepared by simple coprecipitation method. The efficiency of the catalysts for the advanced Fenton's oxidation process using methylene blue (MB) as a model substrate was tested. Both modified and unmodified activated carbon catalysts exhibited similar activity towards the Fenton's oxidation process. Therefore, it is difficult to identify the role of the catalyst in this dye removal process. Hence, we proposed a new methodology to remove the MB by adopting the adsorption process initially, followed by the Fenton's oxidation process. The proposed process significantly improved the methylene blue decomposition reaction over the 25 wt% Fe3O4@AC catalyst. However, this trend was not seen in pure activated carbon and Fe3O4@AC (8 and 50 wt%) catalysts due to the instability of the material in the oxidizing medium. The possible reason for the deactivation of the catalysts was evaluated from lattice strain calculations, as derived from the modified W–H models (Uniform Deformational Model (UDM), Uniform Stress Deformation Model (USDM) and Uniform Deformation Energy Density Model (UDEDM)). These results provided a quantitative relationship between the experimentally calculated lattice strain values and Fenton's catalytic activity. Furthermore, the optimized strain value and crystalite size of Fe3O4 on the activated carbon matrix are responsible for the high catalytic activity.
Introduction
In recent years, uncontrolled natural and synthetic pollutants have increased greatly and lead to the decline of natural water sources. This created a huge demand for efficient technology to recycle the wastewater by a more economical route. Most commonly, the river bodies are being highly polluted by industrial and domestic organic chemicals such as textile dyes and other kitchen waste.1 As a result, many efforts have been taken to clean the organically polluted water by using simple and cost-effective technologies with less energy consumption. A detailed literature survey clearly shows that the advanced oxidation process can significantly improve the water quality either by photochemical or non-photochemical routes.2–10 Recent literature reports strongly suggest that photocatalysis is the best alternative method for removing organic pollutants by using various modified TiO2 materials and their related catalysts in the presence of harmful UV radiation sources. Hence, in order to avoid the UV induced photo reaction, the band gap energy of the photo catalyst has been tuned by several methods to work in the visible region.
Nevertheless, the visible light degradation methodology is not yet completely commercialized for cleaning the industrial wastewater due to the high permissible limit of organic contents and the lack of turn over frequency of the catalyst in the visible region.11 In general, advanced oxidation processes are eco-friendly and as well as more selective towards the complete oxidation reaction due to the formation of transitory radicals in the aqueous medium. In this context, the Fenton's oxidation reaction playing an indispensable role in the treatment of highly contaminated polluted water with powerful OH radicals, which have been generated directly from the decomposition of hydrogen peroxide over the Fe2+ ion sites at pH = 3.12 In recent years, the extensive research works have been focused for the development of heterogeneous photo-Fenton oxidation catalysts to operate at neutral pH medium. The major drawback of photo Fenton oxidation reaction is that it requires a transparent solution to UV or visible light radiation for an interfacial reaction; however, in most of the cases, the industrially polluted waters are not transparent to the light radiation and hence affects the degradation efficiency.13 Therefore, heterogeneous Fenton's oxidation reactions are still considered as a promising route for cleaning the organically polluted water even in the presence of dark environment. Notably, the iron-based catalysts such as Fe3O4, FeS2 and zero-valent-iron (ZVI),14,15 have been widely used for Fenton oxidation reaction. Among these series, iron oxide-based catalysts were extensively studied due to non-toxicity, simple preparation, and low cost. However, these materials are suffering to reach high efficiency due to the low surface area or bulk phase oxide formation. Recently, a variety of high surface area magnetic iron oxide materials were successfully employed for heterogeneous Fenton oxidation reaction including iron oxide supported on high surface CNTs and activated carbon materials.16–18 According to the literature, the common unavoidable problem in the Fenton oxidation reaction is that deactivation of catalyst and complicated regeneration technology was required. For instance, many studies are confirming that the catalyst deactivation was mainly occurred due to extended leaching of iron into the solution.19 In another study, Lejin Xu and Jianlong Wang concluded that the causes of deactivation was mainly due to surface oxidation of Fe2+ to Fe3+ by generated OH radicals during the course of reaction. Therefore, preserving the catalytic activity and stability is continue to be a challenging towards the Fenton oxidation reaction.20 Recently, hydroxylamine (HA) was used to prevent the oxidation of Fe2+ to Fe3+ in the surface bounded species, and they observed significant improvement for oxidative benzoic acid degradation in the presence of hydrogen peroxide.21 Despite these advantages, the use of HA may have a chance to pollute the water further, and hence the supplementary process is required to clean the wastewater. The simple adsorption method is an alternative route for the removal of dye molecules from the wastewater by using a variety of activated carbon material; however, this kind of adsorptive method is just transferring the pollutant from one phase to another, which is not desirable from the environmental point of view. Hence, in the present investigation, we proposed a combined strategy (adsorption and Fenton's oxidation reaction) using the inexpensive catalyst for continuous production of clean water from the dye polluted wastewater without involving any hazardous chemical regeneration treatment. To investigate the reaction pathway and possible reason for the catalytic deactivation, we have chosen MB as a model dye compound and studied in detail with the help of strain confinement effect.
Results and discussion
Determination of particle size and lattice strain
The crystallite size and phase formation of as-prepared (8, 25 and 50 wt% Fe3O4@AC) catalysts were verified by the powder XRD technique (Fig. 1). The peak positions at 2θ values of 30.7, 36.2 43.8, 54.1, 57.7, and 63.3 corresponds to the diffraction planes of (220), (311), (222), (400), (422), (511), and (440), respectively.22 These patterns were found to be in good agreement with previously reported diffraction values corresponding to the cubic spinel structure of Fe3O4 with a space group of Fd3m (227) according to the JCPDS card number 19-0629.20 Whereas, in the case of 8 wt% Fe3O4@AC, it displayed a weak diffraction pattern as compared to 25 wt% Fe3O4@AC catalyst indicating that the concentration of iron oxide was relatively lower than the 25 wt% Fe3O4 loaded catalyst. However, the phase formation on all the catalysts were still the same, demonstrating that the iron oxide loading does not affect the final crystal structure of the material. To further confirm any additional phase formation in the materials, the diffraction patterns are compared with the most stable phase crystalline structure (α-Fe2O3 JCPDS No. 13-534).23 The results from the XRD analysis showed that there was no evidence for the formation of α-Fe2O3 in the parent material representing that the materials exhibited good crystallinity structure. However, it is hard to ascertain from Fe3O4 material to γ-Fe2O3 by just comparing their diffraction patterns alone. Therefore, a special consideration is not required to distinguish both phases separately, since the gamma formation is unfavorable at low-temperature synthesis. Henceforth, we did not consider that particular gamma formation into the account for the Fenton's oxidation reaction. In addition to that, a small broad peak feature was also observed in the range 20–30° owing to the graphitic nature of activated carbon material as evidence from the unmodified XRD pattern (Fig. 1), which means that the structure of the activated carbon materials were not destroyed even after the modification. The average particle size of Fe3O4 loaded on the activated carbon matrix was calculated by plotting a graph between 1/β vs. cos(θ) from their respective FWHM of all the diffraction patterns, according to the Scherrer equation and the size of the particle is found to be 44, 99 and 232 nm, respectively. We observed that the size of the particle was nearly five times lower than that of pure Fe3O4 powder, which proves that the activated carbon matrix helps to decrease the particle size by their unique textural properties. Further, the accurate estimation of lattice constant derived from using Nelson–Riley (NR) extrapolation method in which both systematic and random errors can be minimized.24 The values of the lattice parameter obtained from each diffraction plane was plotted against the NR function (see Fig. S4†). |
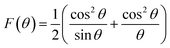 | (1) |
The extrapolation of the linear fit line to F(θ) = 0 or θ = 90° yields the accurate lattice constant, and the values are summarized in the Table 1. The unit cell parameter estimated for 25 and 50 wt% Fe3O4@AC, and Fe3O4 is found to be 8.449 Å, 8.343 Å and 8.659 Å, respectively. The reducing tendency of the unit cell parameter is observed mainly due to the decrease in the size of the particles, resulting in lattice contraction. Similar behaviour was also reported earlier.25 In general, the Scherrer formula will be adopted to measure the spherical shape size of the particle from the XRD peak broadening; however, it doesn't provide any information about the intrinsic lattice strain and stress within the crystal lattice. Usually, these kinds of stress and strain are mainly developed due to the existence of various types of defects present within the crystal lattice, as reported elsewhere.26–28
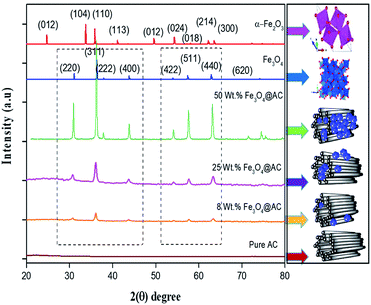 |
| Fig. 1 X-ray diffraction patterns of as-synthesized samples. | |
Table 1 Textural properties of the catalyst
Samples |
Iron contenta wt% |
Particle size (nm) (Scherrer method) |
Unit cell parameter (Å) |
BET surface area (m2 g−1) |
Pore size distribution (nm) |
Micro pore volume (cm3 g−1) |
Meso pore volume (cm3 g−1) |
Total pore volume (cm3 g−1) |
Determined from ICP-OES analysis. |
Pure AC |
— |
— |
— |
960 |
2.02 |
0.201 |
0.616 |
0.900 |
8 wt% Fe3O4@AC |
7.2 |
44 |
8.434 |
858 |
1.85 |
0.241 |
0.452 |
0.651 |
25 wt% Fe3O4@AC |
24.2 |
99 |
8.449 |
669 |
1.53 |
0.22 |
0.301 |
0.513 |
50 wt% Fe3O4@AC |
45.3 |
232 |
8.362 |
358 |
1.12 |
0.18 |
0.214 |
0.321 |
Pure Fe3O4 |
— |
462 |
8.659 |
95 |
— |
— |
— |
— |
Many methods have been successfully developed to study the intrinsic strain in the crystal system but the W–H method is considered as the most appropriate and simple method for doing the calculations. In this connection, the strain as a function of support and non-support effect on Fe3O4 lattice deformation was calculated by W–H method, the obtained average particle size was compared with Scherrer's method. The observed results were summarized in Table 1. According to W–H method, the XRD line broadening was developed mainly due to the size effect of the particles or micro strain within the nano crystal. The XRD line broadening is given by the following eqn (2) as,
|
βtotal = βparticle size + βstrain
| (2) |
To fit into the uniform deformation model (UDM), modified W–H method, corresponding theta values are used as input values in eqn (3).
|
 | (3) |
The above equation was used to determine the particle size and as well as the uniform strain in the crystalline structure and it is commonly known as uniform deformation model (UDM). According to this model, the crystal system considered to be isotropic nature, where the direction of measurement is completely independent. Fig. 2 shows the plot of β
cos(θ) against 4
sin(θ) corresponding to each diffraction patterns of iron oxide loaded on activated carbon and pure iron oxide catalysts. The slope and the intercept of the straight line provides the intrinsic strain and the average particle size of the catalysts, respectively. The plot showed a positive strain for both catalysts indicating that an increase in crystallite size might be due to lattice expansion. The calculated strain for 25 and 50 wt% Fe3O4@AC and Fe3O4 catalysts were found to be 3.50 × 10−3, 2.20 × 10−3 and 9.0 × 10−4, respectively. These values were compared as a function of support effect, interestingly the value of strain obtained from 25 wt% Fe3O4@AC catalyst was significantly larger than the pure Fe3O4 catalysts, it showed that as the particle size decreased, the lattice strain was dramatically increased. In the previous report, iron oxide nano particles were prepared by using with and without capping agents, and the particle size and lattice strain was calculated using W–H method. As summarized in Table 2, the comparison results are showing that although the particle size of 25 wt% Fe3O4@AC catalyst was relatively higher than the reported value, the strain ε value has unusually increased. It indicates that the development of strain owing to the confinement of iron oxide particle inside the porous architecture. The particle size and strain values predicted from the UDM model based on the assumption we made that the crystal has homogeneous and isotropic nature. Nevertheless, it does not actually fit into the real crystal. In general, most of the crystals are anisotropic, and hence, the modified W–H model (USDM) is required for calculating the stress and strain in the crystal lattice.29
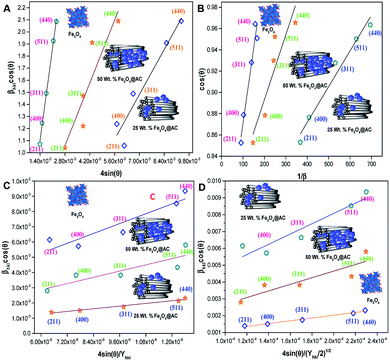 |
| Fig. 2 (A) Debye–Scherer equation plot, (B) βhkl cos θ vs. 4sinθ (UDM) plots, (C) βhkl cos θ vs. 4 sin θ/Yhkl (USDM) plots and (D) βhkl cos θ vs. 4 sin θ (2/Yhkl)1/2 (UDEDM) plots for pure Fe3O4, 25 and 50 wt% Fe3O4@AC. | |
Table 2 Geometrical parameters of the catalysts
Samples |
Scherrer method |
Williamson–Hall method |
UDM |
USDM |
UDEDM |
Size D (nm) |
Size D (nm) |
Strain ε (10−3) |
Size D (nm) |
Strain ε (10−3) |
Stress σ (MPa) |
Size D (nm) |
Strain ε (10−3) |
Stress σ (MPa) |
Energy density (kJ m−3) |
25 wt% Fe3O4@AC |
99 |
72.3 |
3.50 |
69.3 |
3.35 |
537 |
72.9 |
3.43 |
549 |
941.5 |
50 wt% Fe3O4@AC |
231 |
198 |
2.20 |
174 |
2.13 |
341 |
198.2 |
2.19 |
351 |
384.6 |
Fe3O4 |
462 |
346 |
0.90 |
345 |
0.908 |
145 |
346.6 |
0.92 |
147 |
67.8 |
FcP NPs |
9.10 |
11.10 |
2.88 |
N/D |
N/D |
N/D |
11.10 |
2.88 |
350 |
503.7 (ref. 26) |
FC-NPs |
10.00 |
11.25 |
1.53 |
N/D |
N/D |
N/D |
11.25 |
1.53 |
273 |
208.5 (ref. 26) |
According to the Hooke's law the stress and strain can be expressed as follows
|
 | (5) |
According to USDM, the broadening of XRD patterns are mainly transpired due to the development of stress in the crystal structure and the anisotropic nature of Young's modulus.30 On substituting the value of ε in eqn (3) and the model equation is given by below:
|
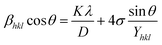 | (6) |
For a cubic crystal, Young's modulus is expressed by the following relation as,31
|
 | (7) |
where
S11,
S12,
S44 are known as elastic compliances of cubic Fe
3O
4 particles, and it can be derived from the elastic stiffness constants
C11,
C12 and
C44, respectively, which are as follows:
|
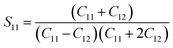 | (8) |
|
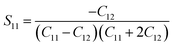 | (9) |
|
 | (10) |
The value of elastic constants (Gpa) at ambient pressure for C11, C12, C44 (cubic Fe3O4) is 260.6, 148.3 and 63.3, respectively.32 By substituting these stiffness constant values in eqn (8)–(10), the elastic compliances values have been calculated as 0.00655, −0.00238 and 0.01580, respectively. From the above values, Young's modulus has been calculated from (220), (311), (400), (511) and (440) diffraction peaks as 165.6, 160.5, 152.6, 156.0 and 165.6 Gpa, respectively. Fig. 2 shows a plot of βhkl
cos
θ against 4
sin
θ/Yhkl. The value of stress and particle size calculated from the slope and the intercept of the equation. The results are summarized in Table 2. According to the Hooke's law, the USDM model is assumed as a linear relationship between stress and strain; however, in many real crystal systems, a linear proportionality between stress/strain and isotropic nature alone cannot be considered for understanding the structural deformation. Since, it exhibits different types of defects, dislocation, and agglomerates; it may create the imperfection in most of the crystal systems. To decipher the uniform anisotropic lattice strain in all directions of the crystal and their respective lattice strain in the crystal, the UDEDM model will be employed. According to Hooke's law, the energy density (u) is directly proportional to strain, and it can be expressed as follows:
|
 | (11) |
where
Yhkl is the anisotropic Young's modulus. Then
eqn (3) can be rewritten according to strain and energy,
|
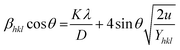 | (12) |
The straight-line equation is popularly known as uniform deformation energy density mode (Fig. 2). From the linear fit model, the uniform deformation energy density of the crystal can be calculated by plotting the value of βhkl
cos
θ in x-axis and 4
sin
θ/(Yhkl/2)1/2 in the y-axis. The intercept of the line provides the average size of the particles, whereas the slope of the equation gives the energy density value in terms of kilojoules per unit volume. As compared to pure iron oxide particle, the calculated density energy was significantly higher for iron-oxide loaded activated carbon catalyst than pure iron oxide catalyst indicating that iron was embed in the more strain environment. These results are in good agreement with our lattice parameter calculation (Table 1). In fact, the values were relatively larger than the reported value confirming that the materials possess more defective sites, which can be achieved by simple precipitation method. The overall detail particle size and crystalline study data concluded that most of the iron oxide was mainly located inside the pores of activated carbon material, and it might be responsible for the higher uniform deformation energy density in the overall crystal system. Moreover, it is noted that there is a significant difference between the value of particle size predicted by the Debye–Scherrer method and from the three W–H models such as UDM, USDM, and UDEDM, respectively. In the Debye–Scherrer model, the particle size was determined from the XRD line broadening, which mainly contributed from the dependencies angle, whereas in the case of the modified W–H method, the particle size determination was accountable by both strain and size induced width to the total broadening. Further, the textural properties of the pure Fe3O4 and Fe3O4 supported activated carbon catalysts were characterized by using N2 adsorption–desorption measurements (Fig. 3), and their values are summarized in Table 1. The pristine Fe3O4 exhibits type I isotherm, while iron oxide loaded catalysts displayed a combination of type I and IV according to IUPAC classifications.33 The obtained results were compared with commercially available pure activated carbon.34 As summarized in Table 1, the textural properties such as surface area, pore diameter, and pore volume was dramatically decreased after the loading of Fe3O4 in the activated carbon matrix; however, the microporous region has not been affected significantly. The decreasing tendency clearly explains that most of the iron oxide is located in the mesoporous region rather than in the microporous architecture structure.
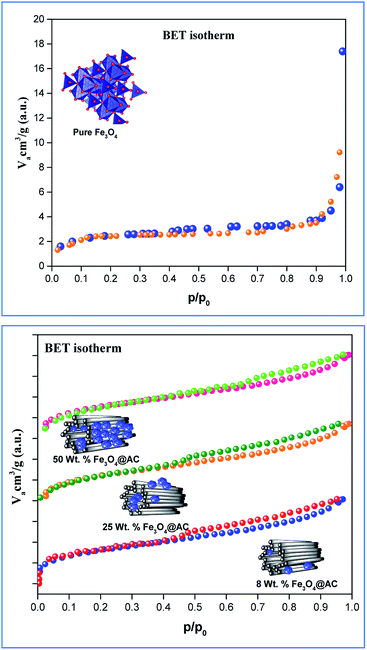 |
| Fig. 3 Nitrogen adsorption/desorption isotherms of catalysts. | |
The scanning electron microscope images are clearly showing that pure activated carbon surface has irregular morphology. The agglomerated spherical shape of Fe3O4 particles are clearly visible on 25 wt% @AC catalyst, and the location was highlighted in the image (Fig. 4b). This situation was dramatically improved on 50 wt% @AC catalyst of the catalyst where the activated carbon surface was completely covered with iron oxide particles. As shown in Fig. 5, the pure and modified Fe3O4 on carbon materials exhibit specific Raman bands at the range from 250 to 800 cm−1, which are the characteristic feature of Fe3O4 particles.35,36 Interestingly, a significant shift in the Raman signals was observed for all iron oxide modified catalysts as compared to pure Fe3O4, in particular, its influence was more on 25% Wt. Fe3O4 catalyst. The shift in peak position is caused mainly due to the lattice strain of the materials. This argument was further well supported with our XRD results. Also, it can be seen in Fig. 5 as the iron oxide concentration increases the amorphous carbon signal was suppressed due to the coverage of iron oxide particles on the surface.
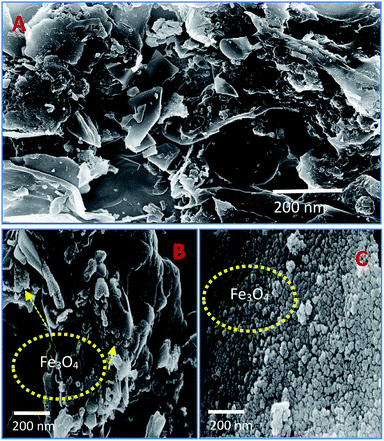 |
| Fig. 4 SEM images of (A) pure Fe3O4, (B) 25 wt% @Fe3O4 and (C) 50 wt%@Fe3O4 catalysts. | |
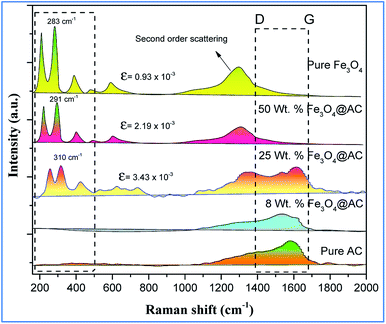 |
| Fig. 5 Raman spectra of pure and modified Fe3O4 catalysts. | |
Catalytic activity
Role of activated carbon on adsorption/Fenton process. The Fenton oxidation reaction of methylene blue (4.48 × 10−4 M) was carried out over 8, 25 and 50 wt% of Fe3O4 loaded on activated carbon catalysts using diluted hydrogen peroxide solution at ambient reaction conditions, as shown in Fig. 6. All the reactions were performed in a batch reactor at the neutral pH medium. For comparison purposes, the Fenton's oxidation reaction was also performed with the help of pure Fe3O4 catalyst and the blank experiment (without any catalyst). The results are confirmed that the complete MB degradation was achieved on all the catalysts except pure Fe3O4. Unambiguously indicating that there was no significant difference between the pure and Fe3O4 decorated on activated carbon catalysts, it also clearly shows that the role of iron oxide was not clearly understood. This unusual trend is the most crucial part of the present investigation, and hence, the study was mainly focused on to understand the reaction pathway with a lot more physical significance. Unfortunately, this reaction involves many complicated steps (adsorption and radical/non-radical pathways), and hence it was difficult to conclude that reaction mainly proceeded either by Fenton's oxidation reaction or simple adsorption process. Hence, it is essential to minimize the many complicated steps at the early stage itself for better understanding of the role of catalyst. Initially, a blank test was performed with and without the addition of hydrogen peroxide solution, and we observed that Fenton's oxidation rate was almost negligible even after two weeks of induction time under identical experimental conditions (Fig. 6). These results are strongly emphasizing that the powerful OH radicals required for a complete MB oxidation reaction.37 The next experiment has performed with the help of pure Fe3O4 catalyst in the presence of hydrogen peroxide solution, and the obtained results are showing that the catalyst exhibited low catalytic activity, as compared to carbon-based catalysts. It specifies that the catalyst may possess a low surface area, or the catalyst might be deactivated quickly owing to extended leaching of either Fe2+ or Fe3+ ions to the reaction mixture and subsequently suppress the reaction rate at the initial stage itself.38 To investigate further the possible reason for low activity of pure Fe3O4, and execution of similar activity on all activated carbon-based catalysts, a time on stream study was studied, and the results were depicted in Fig. 7A and B. A blank experiment was also performed (without hydrogen peroxide) on all the catalysts to differentiate from physical adsorption (Langmuir adsorption isotherm) and Fenton's oxidation reaction. Predictably, the results are concluded that without hydrogen peroxide, the adsorption of methylene was found to be nearly 100% after 5 minutes of stirring time on carbon-based catalysts (the amount of adsorbed MB Conc. was provided in the Fig. 7B). This trend undoubtedly indicates that it follows the simple Langmuir adsorption isotherm rather than Fenton's oxidation reaction; however, this behaviour was not seen in the case of pure Fe3O4 catalyst due to the lack of high surface area of the material as compared to the activated carbon catalyst. It was interesting to find that, except pure Fe3O4 catalyst, all other catalysts are exhibited excellent adsorption capacity. Despite this adsorption phenomenon, the role of hydrogen peroxide and iron oxide active sites are not clear, and hence, we performed the additional test in the presence of added hydrogen peroxide to evaluate any significant improvement in the reaction rate for all the catalysts. Notably, the reaction profile clearly shows that there was no significant difference between these two experiments except Fe3O4 catalyst. This opposite trend on pure Fe3O4 catalyst unanimously confirms that it is well responded to the Fenton's oxidation reaction rather than by a simple adsorption process.
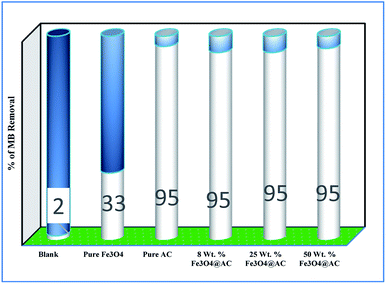 |
| Fig. 6 Effect of catalyst on adsorption and Fenton oxidation reaction of MB. Reaction conditions: initial concentration of MB: 4.48 × 10−4 M: H2O2 concentration 1.6 × 10−3 M: amount of catalyst: 7 mg medium: neutral pH: reaction time: 10 m; reaction temperature: 298 K. Stirring speed: 150 rpm. | |
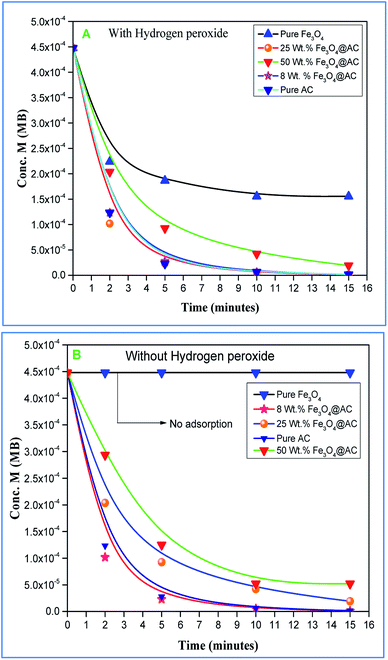 |
| Fig. 7 (A) (with H2O2) and (B) (without H2O2) adsorption study on synthesised catalysts. Reaction conditions: initial concentration of MB: 4.48 × 10−4 M: H2O2 concentration 1.6 × 10−3 M: amount of catalyst: 7 mg medium: neutral pH: reaction time: 10 m; reaction temperature: 298 K. Stirring speed: 150 rpm. | |
As mentioned above, the combined experimental results have proved that the adsorption rate was much faster than the oxidation reaction rate on all the catalysts (i.e., 8, 25 and 50 wt% Fe3O4@AC). Hence, it was difficult to distinguish from adsorption reaction to oxidation reaction. Therefore, it is essential to investigate the role of hydrogen peroxide on iron oxide loaded on activated carbon catalysts for advanced Fenton oxidation reaction system. In fact, the main objective of the present investigation is to remove the organic pollutant from the industrially polluted water by a complete oxidation reaction pathway, but not merely by simple adsorption of methylene blue. Hence a systematic separate reaction study is required for better understanding of the Fenton oxidation reaction, which is a crucial part of the present investigation. Based on our preliminary analysis, the influence of hydrogen peroxide on MB degradation reaction was performed separately over iron oxide loaded on carbon catalysts, and the hydrogen peroxide concentration was kept as 1.6 × 10−3 M. The reaction conditions were shown in Fig. 8A and B. Initially, the methylene blue was allowed to adsorb on a 25 wt% Fe3O4@AC catalyst (optimized wt%) and forced to attain the complete equilibrium under the identical experimental conditions. The maximum up taken of methylene blue was found to be 359.9 mg g−1 at 30 °C in just 5 minutes of reaction time, which is very close to the maximum adsorptivity value (373.9 mg g−1), as reported by Aoumria Ouldmoumna et al.39 The adsorbed methylene blue on the carbon catalyst was further treated with hydrogen peroxide solution, and the reaction continued for another four hours to completely oxidize the adsorbed methylene blue by Fenton's oxidation process. After the oxidation treatment, the methylene blue concentration was increased to the initial value, and the adsorption study was continued on the same catalyst in the same solution, this trend shows that the adsorption behaviour was very similar to the initial run (Fig. 8A). It is a clear indication of all the adsorbed methylene blue can be effectively oxidized by hydrogen peroxide and subsequently clean the surface of activated carbon materials and further help to reabsorb the methylene blue molecule. Further, we spike the methylene blue concentration to initial concentration, and we allowed to attain the adsorption equilibrium and continued the Fenton oxidation reaction. The same methodology was adopted for three consecutive cycles, and we observed that there was no significant difference from the first cycle to the fourth cycle. This cyclization process is very much similar to that of an activation step as used in water purification technology. Surprisingly, the above-mentioned trend was not seen on 8 wt% Fe3O4 loaded on activated carbon catalyst, in fact, the activity was stopped even in the second cycle of the reaction itself (Fig. 8B). It demonstrates that the optimum amount of Fe3O4 species is required on the surface of the catalyst to produce the powerful OH radicals to further attack the adsorbed MB molecule on the catalyst sites. For comparison purpose the same methodology was employed on pure activated carbon catalyst, and it was observed that there was no oxidation ability seen even in the presence of high concentrated hydrogen peroxide solution on adsorbed MB activated carbon material (Fig. 8B). Hence, the study proved that either Fe3+ or Fe2+ ions are required for advance Fenton oxidation process. Also, we observed that the adsorption rate is very much similar to all the catalysts, including the pure activated carbon material. The results clearly explain that iron oxide particles did not play any significant role in improving the adsorption capacity. Additionally, the pure Fe3O4 activity was also investigated by using a similar strategy for meaningful comparison, and the results were depicted in Fig. 9. As we noted that the MB concentration did not drop even after 100 minutes of reaction time, manifesting that there was no physical adsorption of MB taking place over the catalyst, possibly it might be due to the low surface area nature of the material. On the other hand, it shows better activity in the presence of hydrogen peroxide due to the formation of hydroxyl radicals through the Fenton process, but the activity was not retained in the second cycle of reaction due to deactivation of the catalyst either by strong adsorption of MB or complete oxidation of Fe2+ ions into Fe3+.38 Based on the information we gained from the above experimental results, the possible reaction mechanism can be exploited; however, this reaction was believed to proceed via several complicated radical reaction pathways, and hence, few more additional experiments are required to propose the meaningful reaction mechanism for methylene blue degradation reaction. Most importantly, the identification of the real role of iron oxide species for the methylene blue Fenton oxidation reaction on the surface of the activated carbon catalyst is a crucial part of this work and hence, a systematic analysis was carried out with the help of several homogeneous Fenton oxidation reactions with and without added radical scavengers. Initially, the ferrous sulphate solution (0.005 M) was treated with the known concentration of hydrogen peroxide solution (1.6 × 10−3 M), as optimized from the above experimental results, and the results proved that as soon as the addition of Fe2+ in peroxide solution, it would interact with hydrogen peroxide molecule and produce the powerful OH radicals. The resultant OH radicals may subsequently combine with different types of hydroxy/hyrodxyperoxo radicals and produced the oxygen gas with the evolution rate of 1.6 mL min−1 gcat−1 along with the formation of orange-yellow colour precipitation at the end of the reaction.
 |
| Fig. 8 Effect of hydrogen peroxide on methylene adsorption study: (A) 25 wt% Fe3O4/activated carbon catalyst and (B) pure activated carbon and 8 wt% Fe3O4/activated carbon catalysts. Reaction conditions: H2O2 concentration 1.6 × 10 −3 M: amount of catalyst: 7 mg; neutral pH: reaction temperature: 298 K; stirring speed: 150 rpm. | |
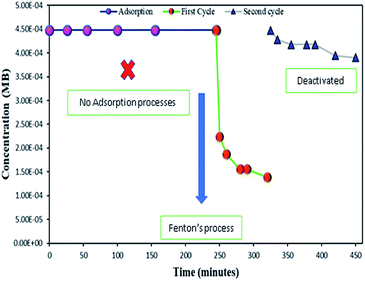 |
| Fig. 9 Effect of hydrogen peroxide on adsorbed methylene blue on activated carbon. Reaction conditions: H2O2 concentration 1.6 × 10−3 M: amount of catalyst: 7 mg; catalyst: pure Fe3O4; neutral pH: reaction temperature: 298 K; stirring speed: 150 rpm. | |
This also confirms that the OH anions would be produced and it reacts with Fe3+ ion to form an insoluble Fe(OH)3 species. Thus, it proves the reaction mainly occurred based on the classical Fenton equation, as shown in Scheme 1.
|
Fe2+ + H2O2 → Fe3+ + OH˙ + OH−
| (i) |
|
 | (ii) |
|
 | (iii) |
|
 | (iv) |
Overall reaction;
|
Fe2+ + H2O2 → Fe(OH)3 ppt + O2
| (13) |
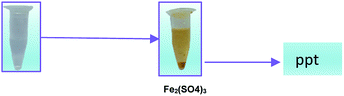 |
| Scheme 1 The formation of Fe(OH)3 precipitate from Fe2+ ion solution. | |
To further confirm the formation of OH radicals, the powerful radical scavenger (acetone) was added in the solution,40 and we observed that there was no oxygen gas was evolved, but it forms the iron hydroxide precipitate in the solution indicates that the all radicals completely were trapped by radical scavengers (as shown in eqn (14)). This analytical method proves that the reaction mainly occurred only by the OH radical formation pathway, as reported by many researchers.
|
Fe2+ + H2O2 + acetone (radical scavanger) → Fe(OH)3 ppt + No O2
| (14) |
A similar reaction was performed with Fe3+ solution (ferric chloride) to infer any significant difference between Fe2+ and Fe3+ ions. Since the catalyst, we prepared eventually contains both the oxidation states, as evident from XRD analysis. It can be seen from Fig. 10 that the rate of production of oxygen was significantly higher than the previous experiment, and remarkably there was no evidence for the formation of Fe(OH)3 species (Scheme 2, according to eqn (15) and (16)), indicating that the reaction was mainly initiated via OOH radical pathway, according to eqn (V)–(XI). Due to the absence of iron hydroxide precipitate formation, the reaction did not proceed via the elementary step of (VII) and (IX) and hence, the rate constant values have not been included in the overall rate consideration. After the addition of radical scavenger, the oxygen evolution reaction rate decreased from 5 mL min−1 to 0.2 mL min−1, it confirms that the reaction mainly executed via the OOH pathway without the formation of OH anions, also, it proves that the reaction not proceeded by barely OH radicals alone. In addition to that, we observed the acetone could act as a good scavenging activity to trap both OH and OOH radicals, respectively.
|
 | (V) |
|
 | (VI) |
|
Fe2+ + OH˙ → Fe3+ + OH−
| (VII) |
|
 | (VIII) |
|
 | (X) |
|
 | (XI) |
|
Fe3+ + H2O2 → No Fe(OH)3 ppt + oxygen was evolved
| (15) |
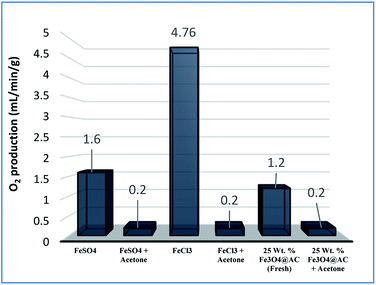 |
| Fig. 10 Effect of radical scavengers on various hetero and homogenous catalyst. Reaction conditions: Conc. of FeSO4 – 0.05 M; Conc. of FeCl3 – 0.05 M; ratio of radical scavenger to catalyst (1 : 4); Conc. of H2O2; 0.125 M; amount of solid catalyst: 7 mg; reaction time: 30 m; stirring speed; 150 rpm. | |
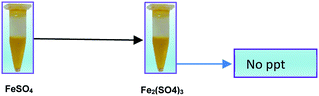 |
| Scheme 2 The absence of Fe(OH)3 precipitate from Fe3+ ion solution. | |
Overall reaction;
|
Fe3+ + H2O2 + acetone (radical scavanger) → No Fe(OH)3 ppt + No O2
| (16) |
For comparison, the MB degradation reaction was also performed in the presence of MB solution and, it was found that in both the experiments the decolorization activity was observed; however, their reaction rates were not the same. The difference in activity was mainly attributed due to the formation of two different types of radicals with two different rate constants, as depicted in eqn (13). In general, OH radicals are more reactive than the OOH radicals, which are directly formed due to the interaction of peroxide molecule with Fe2+ and Fe3+ sites, respectively. However, many researchers did not account for the OOH radicals into degradation efficiency because the rate of formation of hydroperoxide radicals is relatively lower than the hydroxyl radical formation rate. Nevertheless, this tendency was contrary to the oxygen evolution reaction there we observed that the oxygen production rate from Fe2+ sites was significantly larger than one which arises from the Fe2+ ion sites. The difference in rate might be due to dominating the recombination effect of hydroperoxyl radicals, which subsequently enhances the rate of oxygen production and thereby decreases the MB degradation rate. Hence, the overall homogenous Fenton's study concluded that both types of radicals are effectively participating in the MB degradation under identical experimental conditions, but the rate of degradation was not similar due to variable types of radicals are produced in the solution.
In the Recent past, Rachmilovich-Calis et al.41 proposed the degradation reaction mechanism for various types of dye molecules and, they concluded that the reaction mainly occurred not only due to the formation of OH radicals but also due to the involvement of Fe–OOH species in the reaction mixture. These results are inconsistent with our homogenous catalytic study. Based on the experimental results, the complete degradation reaction was mainly occurred due to the involvement of both Fe2+ and Fe3+ ions in the interface reactions. The same methodology was employed over 25 wt% Fe3O4@AC catalyst to estimate the real active sites for MB degradation reaction. Initially, the Fenton's oxidation reaction was performed in the presence of only hydrogen peroxide solution, and the oxygen production rate was calculated. The obtained results are illustrated in Fig. 10. In the first cycle of reaction, the rate of formation of oxygen was found to be 1.2 mL min−1; however, the oxygen production rate has diminished in the next consecutive cycles.
A possible reason can be arrived based on the existence of loosely bounded Fe3+ ion species in the activated carbon matrix, and that could be responsible for oxygen evolution reaction. In the second cycle of reaction, the catalyst was separated from the reaction mixture and washed with distilled water several times, and the reaction was continued with freshly prepared dilute hydrogen peroxide. The observed results are showing that there was no evidence for the oxygen evolution reaction, as we expected from the initial run. These results are inconsistent with our recyclable experiment, as shown in Fig. 12.
Furthermore, the adsorption efficiency of MB on the washed catalyst completely diminished after the addition of radical scavenger in the solution, rationalize that radicals are mainly generated on the surface rather than from the solution containing Fe2+/Fe3+ ions. Hence, the overall study proves that the Fenton's oxidation reaction is facilitated by both Fe2+ and Fe3+ ions with a lesser amount of oxygen evolution reaction (Fig. 11).
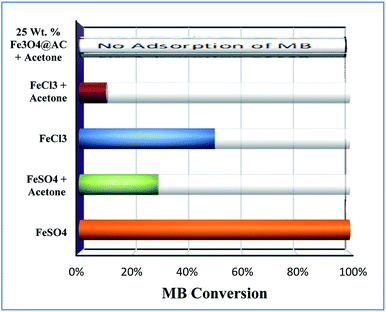 |
| Fig. 11 Effect of radical scavengers on MB degradation. Reaction conditions: Conc. of FeSO4 – 0.005 M; Conc. of FeCl3 – 0.005 M; ratio of radical scavenger to catalyst (1 : 4); Conc. of H2O2; 1.6 × 10−3 M; Conc. of MB 2.0 × 10−4 M; amount of catalyst: 7 mg; reaction time: 30 m; stirring speed: 150 rpm. | |
Deactivation study
To study the sustainability and reusability of the catalyst, the spent catalyst was used for the second set of a cycle without any additional treatment (Fig. 12). The 25 wt% loaded on the catalyst retained almost 85% of their initial activity and the results are completely in contrast to the pure Fe3O4 catalyst. The initial high catalytic activity was mainly due to the extended leaching of Fe2+/Fe3+ species during the course of reaction. However, in the second cycle, the reaction rate completely diminished due to the total oxidation of Fe2+ ion into Fe3+ on the catalyst matrix. The leached iron species was identified by treating the reaction mixture in aqueous ammonia solution, and it produced brown iron hydroxide precipitate at the bottom of the reaction mixture. The overall observation was concluded that 25 wt% Fe3O4@AC catalyst is a promising catalyst for cleaning the dye contaminated water in an inexpensive route.
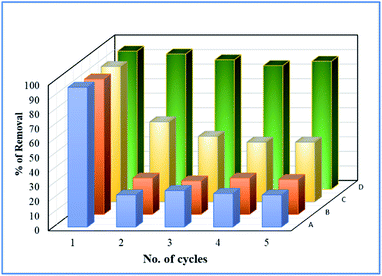 |
| Fig. 12 Deactivation study. Reaction conditions: Initial concentration of MB: 4.48 × 10−4 M: H2O2 concentration 1.6 × 10−3 M: amount of catalyst: 7 mg medium: neutral pH: reaction time: 10 m; reaction temperature: 298 K. Stirring speed: 150 rpm. Catalysts (A) pure Fe3O4; (B) 8 wt% Fe3O4@AC; (C) 50 wt% Fe3O4@AC; (D) 25 wt% Fe3O4@AC. | |
Effect of strain on catalytic activity
In general, the function of a catalyst is describing that the change of rate (and correspondingly, selectivity) reaction without affecting the catalyst structure. Most commonly, the reaction has proceeded with several elementary steps. During each elementary step in a heterogeneous catalyst system, the initial state (IS) transferred to the transition state (TS) on the surface of the catalyst. However, the catalyst does not control the competitive adsorption from one adsorbate relative to another, since the adsorption strength was differing from one intermediate to another is known as scaling relations.42 A more reactive catalyst surface is expected to bind all adsorbates (initial state, transition state, and final state) strongly than the non-reactive surface. Despite the scaling relation provide much information about the sites, but it has its limitations due to the marginal changes in the IS and TS as reported elsewhere. Due to its limitation in the catalyst field, the attempts have been (theoretically and experimentally) made to break the scaling relations (For instance creating second active sites, and creating co-ordination unsaturated sites, etc.).43,44 In another way, the reactivity of catalyst surface can be increased by creating a more straining environment, consult ref,45–47 and citations therein. A surface strain can be created either by applying mechanical loading or creating more defects (dislocations/imperfections) on the catalyst.48
Based on the information gained from the literature, we are trying to correlate the geometrical effect of the catalyst with catalytic activity. To optimize the geometrical factor of the catalyst which directly influence the Fenton oxidation reaction, the pure Fe3O4 was physically mixed with activated carbon to achieve the 25 wt% composition and results were compared with the 25 wt% Fe3O4@AC catalyst. The physically mixed catalyst activity was dropped significantly in the second cycle of reaction proves that the iron oxide material does not tolerate in the aqueous solution. The difference in activity was directly compared with our W–H derived model. For comparison, the anisotropic nature of the crystal was considered on both the catalysts to evaluate the strain effect influencing the catalytic activity. From the W–H model calculations, we confirmed that the 25 wt% Fe3O4@AC catalyst possesses higher lattice strain (along the y and z-axis), which facilitates to reduce the energy barrier between the initial state and final state, respectively. On the other hand, a surface strain creates many defective sites on the chemically mixed catalyst, and it helps to break the MB bonds easily by OH radicals on the surface. As shown in Fig. 13, unlike chemically mixed catalyst, the physically mixed was deactivated quickly either due to extended leaching of Fe2+ ion in the solution or the oxidation of Fe2+ to Fe3+. In order to investigate the extent of meal ion leaching from the catalyst after the third cycle of experiment, the ICP-OES analysis was performed. The detected amount of iron present in the solution was summarized in Table 3. In the previous report concluded that the deformation energy was broadly classified into two types based on the eV per atom variations (>100 meV is stronger; < 50 meV is weak deformation energy) as predicted from the DFT calculations.49 These results are in good agreement with our calculated model. The chemically interacted (25 wt% Fe3O4@AC) catalyst possesses high deformation energy (9.76 eV per mol per unitcell) than the other catalysts. As a result, the bond arrangements are relatively stronger on 25 wt% Fe3O4@AC material than weakly deformed catalysts; consequently, the metal ion has not been easily leached out from the lattice sites (Table 3). Further, the deactivation profile proves that the iron oxide particle in the chemically mixed catalyst was in more confinement environment, therefore, the strain, and deformation energy dramatically increased. The resultant steric confinement effect may prevent the iron oxide leaching as well as the surface oxidation of Fe2+ into Fe3+ ion. The results are concluding that the use of activated carbon support creates a large number of coordinatively unsaturated sites in a more strain environment and to maintain the heterogeneity of catalyst for the continuous Fenton's oxidation reaction.
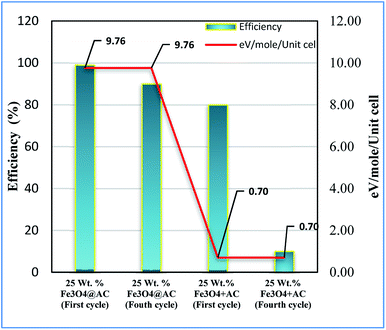 |
| Fig. 13 Influence of strain energy on Fenton's oxidation reaction; Reaction conditions: initial concentration of MB: 4.48 × 10−4 M: H2O2 concentration 1.6 × 10−3 M: amount of catalyst: 7 mg medium: neutral pH: reaction time: 10 m; reaction temperature: 298 K. Stirring speed: 150 rpm (physically mixed catalyst designated as 25 wt% Fe3O4 + AC). | |
Table 3 Correlation of activity vs. lattice strain
Catalysts |
Lattice strain ε (10−3) |
Deformation energy eV per mol per unitcell |
MB Conv. (%) |
The amount of leached irona (mg L−1) |
Determined from ICP-OES analysis. |
Pure Fe3O4 |
0.92 |
0.70 |
22 |
35 |
25 wt% Fe3O4@AC |
3.43 |
9.76 |
88 |
7.3 |
50 wt% Fe3O4@AC |
2.19 |
3.98 |
41 |
35 |
Possible reaction pathway for adsorption/Fenton process
Based on the reaction trend, a possible reaction mechanism for the oxidation of methylene blue on the surface was proposed in Fig. 14. In the first step, the methylene blue was allowed to occupy the sites completely according to Langmuir adsorption isotherm and then treated with hydrogen peroxide to generate the hydroxyl radicals via a dissociative pathway on the surface of defective iron oxide sites.
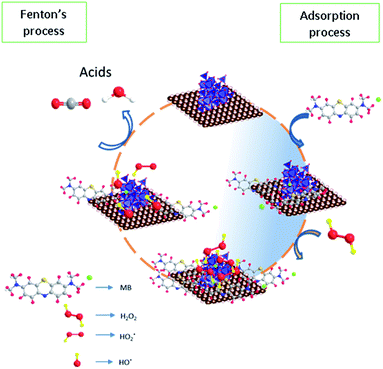 |
| Fig. 14 Proposed reaction mechanism for adsorption and Fenton's oxidation reaction. | |
The electron transfer reaction was initiated by Fe2+/Fe3+ ions and subsequently activated the hydrogen peroxide molecule. The resultant
radicals attack the Methylene blue molecule on the adsorbed surface, which subsequently converted into carbon dioxide and water. A detail process flow diagram was shown in Fig. 15.
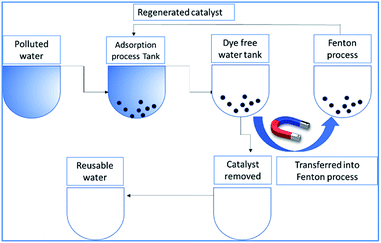 |
| Fig. 15 Process flow diagram of the proposed technology. | |
Conclusions
The Fe3O4 particles are embedded on activated carbon catalyst with different weight percentages (8, 25 and 50 wt%@AC) prepared by co-precipitation method. The embedded iron oxide particles were investigated by XRD, Raman and SEM analysis. The XRD and Raman analysis is supporting that iron oxide particle has located in a 25 wt% catalyst with a more strain environment. The lattice strain was developed due to the interaction of iron oxide in the carbon matrix, as investigated by using a modified W–H model. The results are confirmed that most of the iron oxide mainly located inside the pores of carbon material, and it is responsible for the higher uniform deformation energy density in the overall crystal system. The synthesized materials are evaluated for advanced Fenton's oxidation reaction. Among the catalysts, the 25 wt% loaded on carbon catalyst exhibited both excellent adsorption and Fenton's oxidation ability in the peroxide medium. The reusability tests carried out on all the catalysts, and we observed that 25 wt% Fe3O4@AC catalyst exhibited similar catalytic activity up to 4 consecutive cycles than the physically mixed catalyst. The study concluded that anisotropic strain effect of modified Fe3O4 (eV per mol per unitcell) was played an important role to maintain the heterogeneity of the catalyst. The given experimental results under the strain relations can provide a new possible pathway for the future design of heterogeneous catalysts for longtime durability for many reactions. Further, the combined adsorption/Fenton's strategy provided a new insight for the removal of dye stuff from the industrially polluted wastewater.
Experimental
The synthesis procedure and characterization techniques used in this study were provided in the ESI (Section 2.2 and 2.3).†
Catalytic activity (adsorption/Fenton's process)
The adsorption study was performed in a 5 mL micro-glass reactor containing 2.5 mL of water contaminated with a known concentration of MB. Typically, 7 mg of catalyst was dispersed uniformly in the solution and the pH of the solution was found to be around 5 in the reaction mixture. After the adsorption period, a required concentration of H2O2 added under constant stirring rate. The concentration of MB during the reaction was monitored with the help of the colour analyser application (version 2.0) using the iPhone 6 s smartphone, as shown in Fig. 16.
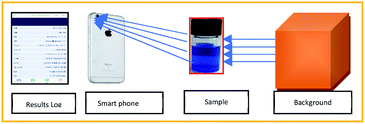 |
| Fig. 16 Method of analysis of Conc. of MB using smart phone technology. | |
The exact concentration was predicted from the constructed calibration curve, as shown in Fig. S1.† The absorbance was calculated from the Beer's law equation (A = −log(Io/I). The curve exhibited perfect linearity without any significant deviation from the regression coefficient value. The use of smartphone technology will be enabled to identify the unknown concentration of methylene blue rapidly; in fact, it does not require any expensive spectrophotometer analysis. The results were perfectly correlated with the UV analysis within 10% of experimental errors. To confirm the decolorization efficiency, the reaction mixture was further analyzed by both UV and HPLC instruments (see Fig. S3†).
Conflicts of interest
There are no conflicts to declare.
Acknowledgements
This research work has been funded by Loyola Research Park Scheme (Project Code No: 5UGRP19CH005).
Notes and references
- C. Jones and C. E. Henninger, Removing the Dye Kitchen from the Textile Supply Chain, in Technology-Driven Sustainability, ed. G. Vignali, L. Reid, D. Ryding and C. Henninger, Palgrave Macmillan, Cham, 2020, pp. 81–92 Search PubMed.
- Y. Yang, J. J. Pignatello, J. Ma and W. A. Mitch, Environ. Sci. Technol., 2014, 48, 2344–2351 CrossRef CAS.
- S. N. Guo, Y. Zhu, Y. Y. Yan, Y. L. Min, J. C. Fan and Q. J. Xu, Appl. Catal., B, 2016, 185, 315–321 CrossRef CAS.
- M. Xing, W. Xu, C. Dong, Y. C. Bai, J. B. Zeng, Y. Zhou, J. L. Zhang and Y. D. Yin, Chem, 2018, 4, 1359–1372 CAS.
- Y. Yuan, L. Feng, N. Xie, L. Zhang and J. Gong, J. Hazard. Mater., 2020, 388, 121730–121739 CrossRef CAS.
- P. Drzewicz, L. P. Estrada, A. . Alpatova, J. W. Martin and M. G. E. Din, Environ. Sci. Technol., 2012, 46, 8984–8991 CrossRef CAS.
- L. Varanasi, E. Coscarelli, M. Khaksari, L. R. Mazzoleni and D. Minakata, Water Res., 2018, 135, 22–30 CrossRef CAS.
- Y. Y. Xiang, J. Y. Fang and C. Shang, Water Res., 2016, 90, 301–308 CrossRef CAS.
- Y. Q. Liu, X. X. He, Y. S. Fu and D. D. Dionysiou, Chem. Eng. J., 2016, 284, 1317–1327 CrossRef CAS.
- F. Laghrib, M. Bakasse, S. Lahrich, M. Abderrahim and E. L. Mhammedi, Int. J. Environ. Anal. Chem., 2020, 1–16 CrossRef.
- Y. Yu, W. Wen, X. Y. Qian, J. B. Liu and J. M. Wu, Sci. Rep., 2017, 41253, 1–13 Search PubMed.
- H. J. H. Fenton, J. Chem. Soc. Trans., 1894, 65, 899–910 RSC.
- G. Iervolino, I. Zammit, V. Vaiano and L. Rizzo, Top. Curr. Chem., 2020, 378, 7 CrossRef CAS.
- E. Petala, K. Dimos, A. Douvalis, T. Bakas, J. Tucek, R. Zboril and M. A. Karakassides, J. Hazard. Mater., 2013, 261, 295–306 CrossRef CAS.
- R. Yamaguchi, S. Kurosu and M. Suzuki, Chem. Eng. J., 2018, 334, 1537–1549 CrossRef CAS.
- S. Amelia, W. B. Sediawan, I. Prasetyo, M. Munoz and T. Ariyanto, J. Environ. Chem. Eng., 2020, 1, 102921–102926 CrossRef.
- S. Su, Y. Liu, X. Liu, W. Jin and Y. Zhao, Chemosphere, 2019, 218, 83–92 CrossRef CAS.
- A. Tolba, M. G. Alalm, M. Elsamadony, A. Mostafa, H. Afify and D. D. Dionysiou, Process Saf. Environ. Protect., 2019, 128, 273–283 CrossRef CAS.
- C. A. Akinremi, S. Rashid, P. D. Upreti, G. T. Chi and K. Huddersman, RSC Adv., 2020, 10, 12941–12952 RSC.
- L. Xu and J. Wang, Environ. Sci. Technol., 2012, 46, 10145–10153 CrossRef CAS.
- X. Hou, X. Huang, F. Jia, Z. Ai, J. Zhao and L. Zhang, Environ. Sci. Technol., 2017, 51, 5118–5126 CrossRef CAS.
- R. Huang, Z. Fang, X. Yan and W. Cheng, Chem. Eng., 2012, 197, 242–249 CrossRef CAS.
- R. Reveendran and M. A. Khadar, Mater. Chem. Phys., 2018, 219, 142–154 CrossRef CAS.
- J. B. Nelson and D. P. Riley, Proc. Phys. Soc., B., 1945, 57, 3 Search PubMed.
- A. Gholizadeh, J. Am. Ceram. Soc., 2017, 100, 3577–3588 CrossRef CAS.
- R. Das and S. Sarkar, Curr. Sci., 2015, 109, 775–778 CrossRef.
- B. E. Warren and B. L. Averbach, J. Appl. Phys., 1952, 23, 497 CrossRef CAS.
- D. Balzar and H. Ledbetter, J. Appl. Crystallogr., 1993, 26, 97–103 CrossRef.
- S. Sarkar and R. Das, Indian J. Pure Appl. Phys., 2018, 56, 765–772 Search PubMed.
- E. Deligoz, K. Colakoglu and Y. Ciftci, Physica B, 2006, 373, 124–130 CrossRef CAS.
- S. Sarkar and R. Das, Nano Lett., 2018, 13, 312–315 CrossRef CAS.
- H. J. Reichmann and S. D. Jacoben, Am. Mineral., 2004, 89, 1061–1066 CrossRef CAS.
- M. Thommes, K. Kaneko, A. V. Neimark, J. P. Olivier, F. Rodriguez-Reinoso, J. Rouquerol and K. S. W. Sing, Pure Appl. Chem., 2015, 87, 1051–1069 CAS.
- Z. Xie, W. Guan, F. Ji, Z. Song and Y. Zhao, Materials Chemistry for Sustainability and Energy, 2014, 491912, 1–9 Search PubMed.
- L. Yang, X. Cui, J. Zhang, K. Wang, M. Shen, S. Zeng, S. A. Dayeh, L. Feng and B. Xiang, Sci. Rep., 2014, 4, 5649 CrossRef CAS.
- O. N. Shebanova and P. Lazor, J. Solid State Chem., 2003, 174, 424–430 CrossRef CAS.
- J. He, X. F. Yang, B. Men, Z. Bi, Y. Pu and D. Wang, Chem. Eng., 2014, 258, 433–441 CrossRef CAS.
- S. V. Niveditha and R. Gandhimathi, Chemosphere, 2020, 242, 125189 CrossRef CAS.
- A. Ouldmoumna, L. Reinert, N. Benderdouche, B. Bestani and L. Duclaux, Desalin. Water Treat., 2013, 51, 3527–3538 CrossRef CAS.
- H. Liu, P. Zhou, X. Wu, J. Sun and S. Chen, Molecules, 2015, 11, 19907–19913 CrossRef.
- S. R. Calis, A. Masarwa, N. Meyerstein, D. Meyerstein and R. V. Eldik, Chem.–Eur. J., 2019, 15, 8303–8309 CrossRef.
- J. E. Sutton and D. G. Vlachos, ACS Catal., 2012, 2, 1624–1634 CrossRef CAS.
- T. Z. H. Gani and H. J. Kulik, ACS Catal., 2018, 8, 975–986 CrossRef CAS.
- F. C. Vallejo, A. Krabbe and J. M. L. Garcia, Chem. Sci., 2017, 8, 124–130 RSC.
- M. M. Montemore and J. W. Medlin, Catal. Sci. Technol., 2014, 4, 3748–3761 RSC.
- J. Greeley, Annu. Rev. Chem. Biomol. Eng., 2016, 7, 605–635 CrossRef.
- Y. Li and Q. Sun, Adv. Energy Mater., 2016, 6, 1600463 CrossRef.
- A. Khorshidi, J. Violet, J. Hashemi and A. A. Peterson, Nat. Catal., 2018, 1, 263–268 CrossRef.
- L. Adamska and S. Sharifzadeh, ACS Omega, 2017, 11, 8290–8299 CrossRef.
Footnote |
† Electronic supplementary information (ESI) available. See DOI: 10.1039/d0ra07866b |
|
This journal is © The Royal Society of Chemistry 2020 |
Click here to see how this site uses Cookies. View our privacy policy here.