DOI:
10.1039/D0RA06561G
(Paper)
RSC Adv., 2020,
10, 32156-32161
Anti-flammability, mechanical and thermal properties of bio-based rigid polyurethane foams with the addition of flame retardants
Received
29th July 2020
, Accepted 21st August 2020
First published on 28th August 2020
Abstract
Adding efficient and environmentally friendly flame retardants to polyurethane foams is the preferable way to improve their flame resistance ability. In this work, bio-based rigid polyurethane foams (RPUFs) were prepared with the addition of dicyclohexyl aluminium hypophosphate (DAH) or aluminium diethyl phosphinate (ADP) as the flame retardant. The mechanical properties, thermal degradation and flammability behavior of the obtained RPUFs were evaluated by means of compressive strength tests, thermogravimetry analysis, vertical burning test and scanning electron microscopes. The characterization results indicate that, with the same content of flame retardant, the compressive strength at the deformation of 10% for each RPUF prepared with the addition of DAH is higher than that of the foams with ADP addition, which fully meets the specifications for building insulation materials. Moreover, the average flame height of each RPUF with the addition of flame retardants is less than 250 mm, whereas the average burning time of RPUF with 15 wt% addition of DAH is only 4.4 s, far less than that (12.5 s) of the foam with the same addition amount of ADP. The RPUFs with DAH addition have the potential advantages for thermal insulation applications in various fields.
Introduction
Rigid polyurethane foam (RPUF) is one of the main polyurethane products with typical characteristics of porosity, low density and high strength.1,2 The density and mechanical strength of RPUF can be adjusted by changing the type of raw material and reaction formula to meet the application requirements.3,4 With the rapid development of urban facilities, polyurethane foam as the low-cost engineering material has been widely used in furniture, transportation, building insulation, refrigeration and other fields.5
Actually, RPUF is an organic polymer with flammable characteristics because of the high content of carbon and hydrogen.6,7 Despite many advantages of RPUF, the release of highly flammable and toxic smoke during burning is a serious threat to human lives and the environment.8,9 When the external heat source invades, the heat in RPUF accumulates immediately due to its thermal insulation behavior, leading to the run-up in temperature. When it rises to the decomposition temperature, the RPUF begins to depolymerize into oligomer and generates a large amount of flammable gas, which can react with oxygen to further intensively combust. The combustion heat sequentially flows into the adjacent area, resulting in a wider range of flame diffusion and burning. Furthermore, the toxic gases and high temperature hamper humans and animals from escaping to safe place.10–12 At present, numerous polyurethane foams in practical applications barely have property of flame resistance. In view of flammability control and environmental protection, the RPUFs with improved flame resistance needs to be further developed.
The addition of flame retardants into RPUFs is the effective way to improve their flame resistance. Flame retardants can be classified into organic and inorganic categories. Organic flame retardants mainly include halogen or phosphorous compounds.13 Halogen flame retardants have been widely used in the early stage because of their positive anti-flammability at low addition content. However, their application is restricted due to the release of toxic and harmful hydrogen halide gases from the combustion, resulting in a severe impact on the environment.14 The phosphorus-based flame retardants generally exhibit many advantages than the halogen-based ones, and they are used jointly with other additives to achieve the substantial promotion in controlling flammability. For instance, Maude Jimenez et al. developed a novel flame retardant to promote RPUF carbonization and natural quenching by plasma-induced graft polymerization of phosphate esters with ethylene phosphate diethyl ester as the precursor.6 It is also reported that RPUF has been prepared with melamine polyphosphate and melamine cyanurate as flame retardants, where the carbonaceous char layer was formed on the sample surface and the phosphorus–nitrogen synergistic effect was realized to generate an intumescent film for retarding further combustion.15 The expanded graphite and triethyl phosphate can be also added into the polyurethane foams to restrain their flammability and promote an increase in the ultimate oxygen index.16 On the other hand, the inorganic flame retardants including aluminium, magnesium, silicon and their hydroxides or oxides still act as the important roles in flame retardation.17–20 Typically, aluminium hydroxide is the most commonly utilized for retarding flame, suppressing smoke and enhancing mechanical strength.21 Therefore, the development of the environmentally friendly polyurethane foams with superior flame resistance characteristics will expend their practical application.
Except for flame resistance of RPUFs, the biodegradability is also the critical characteristic for environmental protection and sustainable development. The transformation of the biomass resources into the bio-based polyols can address the above issue. Because of the enrichment in the activated hydroxyl groups, the bio-based polyols can react with isocyanate to prepare polyurethane materials. Vegetable oils, such as castor oil, canola oil and soybean oil, have been successfully converted into polyols to prepare polyurethane foam materials.22–24 Moreover, plant fibers, such as woods, crop straws and shells, were also successfully transformed into polyols through liquefaction by alcohol solvents.25–28 Therefore, the RPUF prepared with bio-based polyols and novel flame retardants is necessary to be investigated for meeting the application requirements of the flame-retardant materials.
The aim of this work was to synthesize RPUFs with bio-based polyols as the soft segment and lab-made dicyclohexyl aluminium hypophosphate (DAH) as the flame retardant, followed by the investigation of their density, compressive strength, combustion performance, thermal behavior and morphology. Furthermore, a comparative study on the DAH and commercial aluminium diethyl hypophosphate (ADP) was also carried out.
Experimental section
Materials
Cyclohexene, sodium hypophosphite, and ADP were purchased from Sinopharm Chemical Reagent Co., Ltd (Shanghai, China) and used without further purification. The DAH was prepared according to the method as previously reported.29 Polymeric methylene-4,4-diphenyl diisocyanate (PMDI, 32.0 wt% of isocyanate group) was obtained from Wanhua Chemical Group Co., Ltd, Yantai, China. Stannous octoate (T-9) was purchased from Air Products and Chemicals, Inc., USA. Triethylene diamine (A-33) and silicone-based surfactant (L-580) were obtained from Momentive Performance Materials Inc., USA. The bio-based polyols were derived from the liquefaction of peanut shells as reported in our previous work.28
Synthesis of flame-resistant RPUFs
The RPUFs with DAH or ADP were prepared by a one-step method, where the addition amount of each raw material was measured based on the weight percentage of bio-based polyols. The preweighted bio-based polyols, catalyst (T-9 and A-33), surfactant (L-580), blowing agent (deionized water) and flame retardant (DAH or ADP) were firstly added to the 250 ml beaker with continuous stirring. Then, the PMDI was added to the blends and continually stirred for 2 min. Finally, the as-synthesized RPUFs were allowed to freely foam in a mould of 200 × 80 × 80 mm and cured for 72 h at room temperature before further analysis. The obtained RPUFs prepared with DAH (RPUF-D) were denoted as RPUF0, RPUF-D5, RPUF-D10, RPUF-D15, and the samples prepared with ADP (RPUF-A) were denoted as RPUF-A5, RPUF-A10, RPUF-A15, respectively, where the number represents the weight percentage of DAH or ADP in final RPUFs.
Characterizations
The apparent densities of RPUFs were measured according to GB T 6343-2009. Before the test, the samples were placed at the temperature of (23 ± 2) °C and relative humidity of (50 ± 5)% for 16 h. According to GB T 8813-2008, the compressive strength was tested on the H10KS electronic universal testing machine with a deformation rate of 5 mm min−1. The vertical burning test was conducted according to GB T 8333-2008 using six samples of (254 ± 1) mm × (19 ± 1) mm × (19 ± 1) mm with uniform density. Before the measurement, the samples were pretreated at (23 ± 2) °C and (50 ± 5)% relative humidity for 24 h. The thermogravimetric (TG) analysis was conducted on A NETZSCH STA 409 PC/PG thermogravimetric analyzer under the nitrogen atmosphere at the temperature range of 30–800 °C with the heating rate of 10 °C min−1. The morphology of gold-coated RPUF samples was observed on the Hitachi S-4800 field emission scanning electron microscope (SEM).
Results and discussion
Apparent density
Fig. 1 shows the effect of flame retardants on the apparent density of the obtained RPUFs. Obviously, the density of RPUF-D samples first increases and then decreases with the increase of DAH content. As an additive-type flame retardant, DAH is regarded as a nucleating agent, which can reduce the surface tension of the foaming mixture, thus resulting in the obtained foams with smaller and more uniform cell size.30,31 Therefore, the apparent density of RPUF-D15 is still higher than that of RPUF0, indicating the potential application as the thermal insulation materials. However, the ADP exhibits a slight effect on the foam density of the corresponding RPUFs due to its weak nucleation ability.
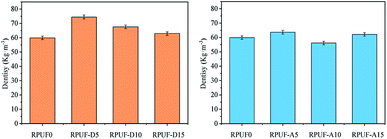 |
| Fig. 1 Apparent density changes of RPUFs after the addition of DAH or ADP. | |
Compressive strength
The compressive strength was measured to investigate the effect of the flame retardants on the mechanical property of RPUFs. The stress–strain curves of RPUFs with different content of DAH or ADP are shown in Fig. 2 and the compressive strength data of RPUFs at 10% deformation are listed in Table 1. The compressive strength of RPUF-D5 exhibits the significantly decrease after the addition of 5 wt% DAH during the synthesis process of the RPUF, and this value continues to decline with further addition of the DAH. However, the RPUF-D15 sample possesses almost the same compressive strength in comparison with the parent RPUF0. According to GB T 21558-2008, the compressive strength value of each RPUF-D sample meets the specifications (>120 kPa) for building insulation materials with effective load carrying capability, indicating the potential application of those bio-based RPUFs in the thermal insulation field. In the case of the addition of ADP, although the compressive strength of the RPUF-A samples increases with the elevated addition amount of ADP, however, this value is still much less than that of the parent RPUF0, even the addition amount of ADP is as high as 15 wt%. For instance, when the deformation is 10%, the compressive strength of RUPF-A5, RUPF-A10, and RUPF-A15 was reduced by 48.65%, 44.75% and 25.12% in comparison with RPUF0, respectively. The decline in compressive strength can be attributed to the cell expansion in foams with the addition of flame retardant, as observed in SEM images (Fig. 5). Moreover, with the same content of flame retardant, the compressive strength at the deformation of 10% for each RPUF-D sample is much higher than that of the RPUF-A sample (Table 1).
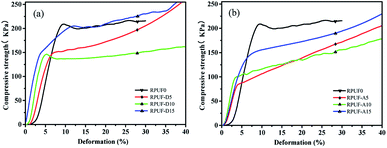 |
| Fig. 2 Stress–strain curves of RPUFs prepared with DAH (a) or ADP (b). | |
Table 1 Compressive strength of RPUFs at 10% deformation
Samples |
RPUF0 |
RPUF-D5 |
RPUF-D10 |
RPUF-D15 |
RPUF-A5 |
RPUF-A10 |
RPUF-A15 |
Compressive strength (kPa) |
207.8 |
154.2 |
136.8 |
197.2 |
106.7 |
114.8 |
155.6 |
Vertical burning tests
The vertical burning test is an important method to measure the flame-retardant property of materials, the corresponding results are listed in Table 2. The burning time of obtained foams progressively reduced with the increasing addition amount of the DAH or ADP. And the RPUF-D15 exhibits the superior flame retardant characteristic with the burning time of 4.4 s as compared to the RPUF-A15. Furthermore, six droplets were generated from the combustion of RPUF0, which implies the acceleration of flame diffusion. However, the RPUF-D and RPUF-A samples did not generate any droplets, indicating the high flame-retardant efficiency of DAH and ADP.
Table 2 The results of the vertical burning tests of RPUFs
Samples |
Density (kg m−3) |
Burning time (s) |
Number of combustion droplets |
Residual mass fraction (wt%) |
Flame height (mm) |
RPUF0 |
59.86 |
56.6 |
6 |
33.35 |
>250 |
RPUF-D5 |
74.45 |
49.6 |
0 |
56.25 |
<250 |
RPUF-D10 |
67.61 |
16.1 |
0 |
85.21 |
<250 |
RPUF-D15 |
62.92 |
4.4 |
0 |
85.61 |
<250 |
RPUF-A5 |
63.69 |
16.8 |
0 |
90.23 |
<250 |
RPUF-A10 |
56.02 |
17.1 |
0 |
85.23 |
<250 |
RPUF-A15 |
62.08 |
12.5 |
0 |
90.89 |
<250 |
The residual mass fraction (RMF) of the sample is also a substantial parameter for evaluating the degree of combustion. The average RMF of RPUFs with the addition of flame retardants is much higher than that (33.35 wt%) of RPUF0. With the addition of flame retardant, the RMF goes up rapidly and finally reaches a plateau at about 85 wt% for the RPUF-D samples, while it displays the smooth value of 85–90 wt% for RPUF-A samples. Moreover, the average flame height of all RPUFs with the addition of flame retardants is <250 mm, which is lower than that of RPUF0. After the comprehensive consideration for these results, the DAH exhibits the superior flame-retardant characteristic for the synthesis of corresponding RPUFs, especially the RPUF-D15.
Thermogravimetric analysis
TG and the corresponding differential thermogravimetry (DTG) provide the significant information about the thermal degradation behavior of the RPUFs, thus the thermal stability at elevated temperatures. Fig. 3 and Fig. 4 show the TG and DTG curves of RPUF-D and RPUF-A samples under N2 atmosphere, respectively, and the related analysis results are listed in Table 3. The weight loss of the RPUFs during the TG tests mainly occurs at the temperature range of 230–550 °C, as verified by the two obvious DTG peaks. The slight weight loss at the temperature of <230 °C may arise from the water evaporation from these foams. The maximum weight loss stage (230–380 °C, stage 1 in the TG curve) is ascribed to the decomposition of urethane bond through the breakdown of isocyanate and polyols, which is in accordance with our previous reports.32 And the decomposition of flame retardants can be responsible for the subsequent weight loss (380–550 °C, stage 2 in the TG curve).33,34 In the final stage of TG tests (>550 °C), the TG and DTG curves reach a plateau due to the formation of char.
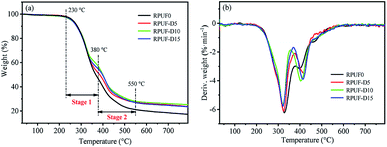 |
| Fig. 3 TG (a) and DTG (b) curves of RPUF-D samples. | |
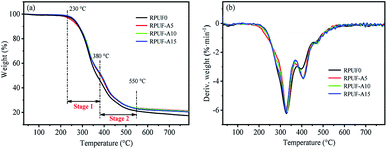 |
| Fig. 4 TG (a) and DTG (b) curves of RPUF-A samples. | |
Table 3 TG analysis of RPUF-D and RPUF-A samplesa
Samples |
T5% (°C) |
T50% (°C) |
Tmax (°C) |
Residue (%) |
T5%: temperature at weight loss of 5%, T50%: temperature at weight loss of 50%, Tmax: temperature at the maximum thermal mass loss rate. |
RPUF0 |
260.4 |
367.6 |
328.2 |
17.28 |
RPUF-D5 |
260.7 |
385.7 |
325.2 |
23.56 |
RPUF-D10 |
254.7 |
399.6 |
321.5 |
25.24 |
RPUF-D15 |
256.6 |
398.6 |
321.9 |
23.39 |
RPUF-A5 |
251.7 |
383.7 |
329.9 |
21.18 |
RPUF-A10 |
260.7 |
386.6 |
328.5 |
20.81 |
RPUF-A15 |
265.7 |
387.6 |
325.6 |
20.43 |
Moreover, the TG curves of RPUF-D samples are located above that of RPUF0 as well as the RPUF-A samples, implying that the relatively high thermal stability RPUF-D samples. As presented in Table 3, the T50% of RPUF-D samples shifts to the high temperature, which further indicates that DAH can enhance the thermal stability of RPUF-D samples. The RPUF-D samples also possess the high content of the final residue in comparison with the RPUF0 and the RPUF-A samples. The DAH can be converted into phosphonates in the combustion process, which can reduce the flame height and restrain combustion.8 Moreover, phosphorus compounds can break up into small fragments, which can catalyse the recombination of hydrogen atoms into hydrogen molecules, leading to the reduction in flame energy.35 And the DAH has multiple cyclohexane structures and long carbon chains than ADP, producing more coke for inhibiting combustion.36
Morphology investigation
The morphology changes of RPUF-D and RPUF-A samples before and after combustion are shown in Fig. 5 and 6. It can be observed that all RPUFs exhibit the closed-cell structure with some connected windows, which could benefit for the application of thermal and sound insulation. After the combustion of these RPUFs, the residue is attached to the surface with a carbon layer, where the flame retardant can prevent the emission of combustible gas and hinder the further combustion of the interior foam. When the flame retardant content is as low as 5%, the carbonization layer on the surface of combustion residue is continuous “worm-like”.37 However, with the increase in the content of flame retardant, the skeleton of the foam cell appears, indicating the progressive decline in the burning degree of foams.38 Furthermore, the phosphorus was turned into a liquid form at high temperature and apt to attach to the foam surface, which is responsible for porous areas in SEM images.39,40
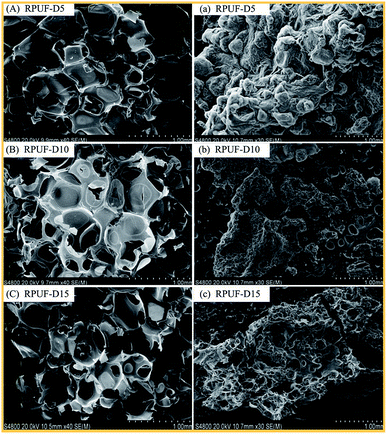 |
| Fig. 5 SEM images of RPUF-D samples before (A–C) and after (a–c) combustion. | |
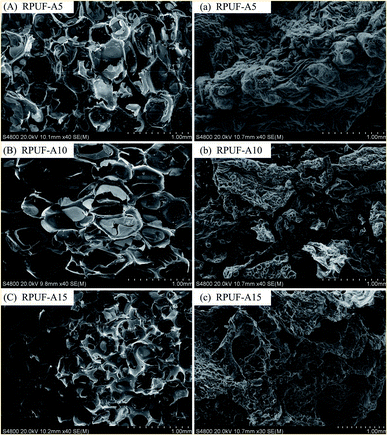 |
| Fig. 6 SEM images of RPUF-A samples before (A–C) and after (a–c) combustion. | |
Conclusions
The bio-based rigid polyurethane foams (RPUFs) have been synthesized with the addition of the lab-made DAH or commercial ADP as the flame retardant. The flammability, mechanical and thermal properties were intensively characterized to investigate the effects of the flame retardants on the physicochemical changes of these foams. The characterization results indicate that the compressive strength of all RPUF-D samples meets the specifications for building insulation materials. And the burning time of RPUF with the DAH addition of 15 wt% was only 4.4 s in comparison with that (12.5 s) of RPUF with same addition amount of ADP. Furthermore, the RPUFs with the addition of DAH also exhibit the better thermal stability in comparison with the parent RPUF0 and the RPUFs with the addition of ADP. This research would enlighten us to further investigate the flame-retardant mechanism for developing novel bio-based RPUFs with superior flame-retardant property.
Conflicts of interest
The authors declare no conflict of interest.
Acknowledgements
This work was supported by the National Natural Science Foundation of China (Grant No. 51803107), and Opening Fund of State Key Laboratory of Heavy Oil Processing (SKLOP202002002).
References
- D. K. Chattopadhyay and K. V. S. N. Raju, Prog. Polym. Sci., 2007, 32, 352–418 CrossRef CAS.
- Z. Rafiee and V. Keshavarz, Prog. Org. Coat., 2015, 86, 190–193 CrossRef CAS.
- N. Mahmood, Z. Yuan, J. Schmidt and C. Xu, Renewable Sustainable Energy Rev., 2016, 60, 317–329 CrossRef CAS.
- E. Ciecierska, M. Jurczyk-Kowalska, P. Bazarnik, M. Gloc, M. Kulesza, M. Kowalski, S. Krauze and M. Lewandowska, Compos. Struct., 2016, 140, 67–76 CrossRef.
- X. Luo, Y. Xiao, Q. Wu and J. Zeng, Int. J. Biol. Macromol., 2018, 115, 786–791 CrossRef CAS PubMed.
- M. Jimenez, N. Lesaffre, S. Bellayer, R. Dupretz, M. Vandenbossche, S. Duquesne and S. Bourbigot, RSC Adv., 2015, 5, 63853–63865 RSC.
- B. P. Jelle, Energy Build., 2011, 43, 2549–2563 CrossRef.
- H. Singh and A. K. Jain, J. Appl. Polym. Sci., 2008, 111, 115–1143 Search PubMed.
- K. T. Joseph and R. F. Browner, Anal. Chem., 2002, 52, 1083–1085 CrossRef.
- K. A. Salmeia, S. Gaan and G. Malucelli, Polymers, 2016, 8, 319 CrossRef PubMed.
- A. R. Horrocks, B. K. Kandola, P. J. Davies, S. Zhang and S. A. Padbury, Polym. Degrad. Stabil., 2005, 88, 3–12 CrossRef CAS.
- Y. Pan, J. Zhan, H. Pan, W. Wang, H. Ge, L. Song and Y. Hu, RSC Adv., 2015, 5, 67878–67885 RSC.
- S.-Y. Lu and I. Hamerton, Prog. Polym. Sci., 2002, 27, 1661–1712 CrossRef CAS.
- M. Modesti and A. Lorenzetti, Polym. Degrad. Stab., 2002, 78, 167–173 CrossRef CAS.
- M. Thirumal, D. Khastgir, G. B. Nando, Y. P. Naik and N. K. Singha, Polym. Degrad. Stab., 2010, 95, 1138–1145 CrossRef CAS.
- M. Modesti, A. Lorenzetti, F. Simioni and G. Camino, Polym. Degrad. Stab., 2002, 77, 195–202 CrossRef CAS.
- P. Zhao, C. Guo and L. Li, Constr. Build. Mater., 2018, 170, 193–199 CrossRef CAS.
- Z. Fanglong, X. Qun, F. Qianqian, L. Rangtong and L. Kejing, Surf. Coat. Technol., 2016, 294, 90–94 CrossRef.
- F. Gholamian, M. Salavati-Niasari, D. Ghanbari and M. Sabet, J. Cluster Sci., 2012, 24, 73–84 CrossRef.
- L. Chen and Y.-Z. Wang, Polym. Adv. Technol., 2010, 21, 1–26 CrossRef.
- M. Baskaran, R. Hashim, J. Y. Leong, Y. N. Ong, M. F. Yhaya and O. Sulaiman, Bull. Mater. Sci., 2019, 42, 138 CrossRef.
- Y. Ji, S. Chen and W. Zhu, Appl. Acoust., 2020, 157, 107010 CrossRef.
- M. Kurańska and A. Prociak, Ind. Crops Prod., 2016, 89, 182–187 CrossRef.
- M. Ionescu, D. Radojčić, X. Wan, M. L. Shrestha, Z. S. Petrović and T. A. Upshaw, Eur. Polym. J., 2016, 84, 736–749 CrossRef CAS.
- D. Yue, O. Oribayo, G. L. Rempel and Q. Pan, RSC Adv., 2017, 7, 30334–30344 RSC.
- J. Zhang, N. Hori and A. Takemura, Polym. Degrad. Stab., 2019, 166, 31–39 CrossRef CAS.
- G. Huang and P. Wang, Polym. Test., 2017, 60, 266–273 CrossRef CAS.
- Q. Zhang, G. Zhang, D. Han and Y. Wu, J. Appl. Polym. Sci., 2016, 133, 44162 Search PubMed.
- H. Zhang, J. Lu, H. Yang, H. Yang, J. Lang and Q. Zhang, Polymers, 2019, 11, 1211 CrossRef CAS PubMed.
- A. A. Septevani, D. A. C. Evans, P. K. Annamalai and D. J. Martin, Ind. Crops Prod., 2017, 107, 114–121 CrossRef CAS.
- Y. Lee, M. Geun Jang, K. Hyung Choi, C. Han and W. Nyon Kim, J. Appl. Polym. Sci., 2016, 133, 43557 Search PubMed.
- Q. Zhang, X. Lin, W. Chen, H. Zhang and D. Han, Polymers, 2020, 12, 107 CrossRef CAS PubMed.
- H. Zhang, J. Lu, H. Yang, J. Lang and H. Yang, Polymers, 2019, 11, 1956 CrossRef CAS.
- L. Zhong, K.-X. Zhang, X. Wang, M.-J. Chen, F. Xin and Z.-G. Liu, J. Therm. Anal. Calorim., 2018, 134, 1637–1646 CrossRef CAS.
- A. Granzow, Acc. Chem. Res., 2002, 11, 177–183 CrossRef.
- L. Chen and Y. Z. Wang, Materials, 2010, 3, 4746–4760 CrossRef CAS PubMed.
- F. Qi, M. Tang, N. Wang, N. Liu, X. Chen, Z. Zhang, K. Zhang and X. Lu, RSC Adv., 2017, 7, 31696–31706 RSC.
- G. Turgut, E. Işıksel, G. Kahraman, T. Eren and G. Özkoç, J. Appl. Polym. Sci., 2018, 135, 45998 CrossRef.
- D.-H. Wu, P.-H. Zhao, Y.-Q. Liu, X.-Y. Liu and X.-f. Wang, J. Appl. Polym. Sci., 2014, 131, 39581 Search PubMed.
- S. Nie, Y. Hu, L. Song, Q. He, D. Yang and H. Chen, Polym. Adv. Technol., 2008, 19, 1077–1083 CrossRef CAS.
Footnote |
† These authors contributed equally to this work. |
|
This journal is © The Royal Society of Chemistry 2020 |
Click here to see how this site uses Cookies. View our privacy policy here.