DOI:
10.1039/D0RA05824F
(Paper)
RSC Adv., 2020,
10, 32532-32547
A novel highly selective electrochemical chlorobenzene sensor based on ternary oxide RuO2/ZnO/TiO2 nanocomposites
Received
3rd July 2020
, Accepted 10th August 2020
First published on 1st September 2020
Abstract
A novel electrochemical (EC) chlorobenzene (CBZ) sensor was fabricated using a ternary oxide RuO2/ZnO/TiO2 nanocomposite (NC)-decorated glassy carbon electrode (GCE). The nanoparticles (NPs) were synthesized by a wet-chemical method and characterized by X-ray photoelectron spectroscopy (XPS), powder X-ray diffraction (XRD), field emission scanning electron microscopy (FESEM), energy-dispersive X-ray spectroscopy (EDS), and ultraviolet-visible (UV-vis) spectroscopy. The synthesized RuO2/ZnO/TiO2 NC was layered as thin film on a GCE with Nafion (5% suspension in ethanol) adhesive, and the as-prepared sensor was subjected to CBZ analysis using an electrochemical approach. The calibration of the proposed CBZ sensor was executed with a linear relation of current versus concentration of CBZs known as the calibration curve. The sensitivity (32.02 μA μM−1 cm−2) of the CBZ sensor was calculated from the slope of the calibration curve by considering the active surface area of the GCE (0.0316 cm2). The lower detection limit (LD; 98.70 ± 4.90 pM) was also calculated at a signal-to-noise ratio of 3. Besides these, the response current followed a linear relationship with the concentration of chlorobenzene and the linear dynamic range (LDR) was denoted in the range of 0.1 nM to 1.0 μM. Moreover, the CBZ sensor was found to exhibit good reproducibility, reliability, stability, and fast response time. Finally, the sensing mechanism was also discussed with the energy-band theory of ternary doped semiconductor materials. The sensing activity of the proposed sensor was significantly enhanced due to the combined result of depletion layer formation at the heterojunction of RuO2/ZnO/TiO2 NCs as well as the activity of RuO2 NPs as oxidation catalysts. The proposed CBZ sensor probe based on ternary oxide RuO2/ZnO/TiO2 NCs was developed with significant analytical parameters for practical application in monitoring the environmental pollutants of CBZs for the safety of environmental fields on a large scale.
1. Introduction
Aromatic chlorobenzene (CBZ) compounds are commonly used as raw materials, intermediates and solvents in insecticides, pesticides, pharmaceuticals, printing, dyeing, leather, and electronics industries.1 All the chlorobenzenes used in pesticides and insecticides are directly released into soil during their application, and they enter the food chain via leaching of soil by rainwater. Therefore, the use of agrochemicals formulated with chlorobenzenes (pesticides and insecticides) is responsible for direct contamination of the environment. Besides this, the incomplete incineration of municipal, industrial and medical wastes is another important source of the release of CBZs into the environment.2,3 As a result, the chlorinated volatile organic compounds from various stationary sources have great impact on environment due to its high toxicity.4 Therefore, CBZs are considered the hazardous environmental pollutants.5,6 As a result, there is a potential risk of accumulation of CBZs in human beings via the food chain. Consequently, this may cause teratogenesis, cancer, and mutagenesis and can badly affect the central nervous system and cause damage as reported previously.7 In addition, it may also cause copious symptoms such as headache, numbness, sleepiness, vomiting, liver and kidney damage.8 Therefore, the United States Environmental Protection Agency (EPA) has ranked CBZs as priority toxic pollutants.9 Therefore, a reliable analytical method to determine CBZs in the environment is obviously very important.
Up to date, chlorobenzenes are determined quantitatively applying different conventional techniques such as gas chromatography,8 mass spectrometry,10 HPLC,11 ion mobility spectrometry,12 and other integrated methods. However, these techniques face different critical limitations including complicated fabrication, high cost, time consumption in sample pretreatment including separation and the prolonged data analysis. Over the past decades, electrochemical (EC) methods have received excessive attention in various diagnoses including clinical,13–15 environmental,16,17 biological,18 pharmaceutical, and quality control during food processing.19 Among the EC methods, the electrochemical approach has drawn significant attention of researchers due to its high sensitivity, good selectivity, inexpensive instruments, ease of operation, simple pretreatment of samples, and faster analysis. To improve the sensitivity and avoid the multi-selectivity, the electrodes have been modified with various semi-conductive metal oxides such as ZnO,20–22 Cr2O3,23 SnO2,24 WO3,25 and Co3O4 to detect numerous toxic chemicals and biochemicals.26 In the recent years, few research studies based on semi-conductive metal oxides have been reported for the reliable detection of CBZs. As reported previously, Pt-decorated ZnO NCs,27 Au-decorated ZnFe2O4 yolk–shell spheres,28 In2O3 nano-rods,29 Pd NPs on porous ZnO nano-plates,30 and coral-like SnO2 nanostructures31 have been reported as efficient sensing mediators for the reliable detection of CBZs. Besides this, FeO/CdO nanocubes and MCM-41 material-decorated GCEs have performed potentially to detect CBZs in an electrochemical approach.32,33
Among semiconductor metal oxides, zinc oxide (ZnO) has attracted great attention as a promising sensing material owing to its outstanding stability, non-toxicity, electrical properties, photosensitivity, EC activities, high electron communicating features, and so on.34–37 Therefore, as an effectual sensing material, ZnO has been used previously to detect xanthine,38 hydrazine,39 3-methoxyphenol,40 4-aminophenol,41 and 4-nitrophenol.42 However, most of these research works have been executed to detect toxic chemicals in the gaseous phase. Furthermore, the sensitivity and selectivity of these modified electrodes are not satisfactory enough for real-time applications. In this context, the modification of electrodes utilizing two or multiple semi-conductive metal oxide nanocomposites could be an effective way to enhance the selectivity as well as sensitivity of the EC sensors. In addition, any change in interfacial resistance due to the formation of a heterojunction results in improved performance of sensors.43
Composite metal oxides have already been utilized for the reliable and selective detection of numerous toxicants in the gaseous phase, such as ZnO/SnO2 nanofibers for ethanol,44 ZnO/Cr2O3 nanorods and ZnO/In2O3 nanofibers for trimethylamine,45,46 V2O5 doped ZnO NCs for phenylhydrazine,17 MgO/ZnO composite for H2O2,47 and RuO2/ZnO NCs for 2-nitrophenol16 as reported earlier. Similarly, TiO2 is another n-type semiconductor with a wide optical band gap, and it has good stability and opto-electro-chemical properties.48 TiO2, due to its multiple properties, has already been tested as an excellent sensor material to sense tetracycline,49 hydrogen,50 glucose,51 formaldehyde,52 uric acid53 and hydrogen peroxide.54,55 Besides this, RuO2 exhibits brilliant electronic and electro-catalytic properties.56 As a result, RuO2-based nanomaterials have been applied as supercapacitors,57 electrodes for oxygen and chlorine production, water splitting,58,59 CO oxidation60 and HCl oxidation61,62 as testified previously. Here, the incorporation of RuO2 into a ZnO/TiO2 nanostructured material was employed as a great deal of consideration due to its chemical, structural, physical, and optical properties in terms of large active surface area, high stability, and high porosity.63 These properties are directly dependent on the structural morphology of the reactant precursors for making the ternary RuO2/ZnO/TiO2 materials a basic medium at low temperatures. This RuO2/ZnO/TiO2 material was synthesized by a facile solution method using reducing agents. This technique has several advantages including facile preparation, accurate control of reactant temperature, ease of handling, and one-step reaction. Optical, morphological, electrical, and chemical properties of the ternary RuO2/ZnO/TiO2 nanomaterial are of huge significance from the scientific aspect, compared to the counterpart ZnO, TiO2, and RuO2 nanomaterials. Non-stoichiometry, mostly oxygen vacancies, renders it the conducting nature in heterostructure materials.64,65 The formation energy of oxygen vacancies in the semiconductor is very low and thus this defect forms eagerly, resulting in the increased conductivity of RuO2/ZnO/TiO2 materials compared to other pure materials. Ternary materials have also attracted considerable interest due to their potential applications including, optoelectronics, electro-analyses, selective detection assays, chemical sensor devices, hybrid-composites, electron field emission sources, biochemical detection, and surface-enhanced Raman scattering.66,67 RuO2/ZnO/TiO2 materials offer improved performance due to the large active surface area, which increased the conductivity and current responses of the RuO2/ZnO/TiO2 NCs/Nafion/GCE assembly during the electrochemical investigation. It has been stated that ZnO, TiO2 and RuO2 have been applied as sensing mediators for the development of various toxic chemical sensors. In this context, combining ZnO, TiO2 and RuO2 metal oxides to form composite semiconductors would have a synergetic effect, which might improve the sensing performance of EC sensors. Thus, the investigation of the potentiality of RuO2/ZnO/TiO2 NCs as sensor materials would be of great scientific and technical interest. Furthermore, as far as we know, no EC sensor based on ternary oxide RuO2/ZnO/TiO2 NCs is yet reported for the detection of CBZs in a buffer medium.
In this approach, a novel EC sensor based on a wet-chemically prepared RuO2/ZnO/TiO2 NC-modified GCE was developed. Subsequently, the sensing performance of the projected sensor was investigated for the selective detection of chlorobenzenes. The I–V technique was employed to conduct all the experiments. To execute the analytical performances such as linear dynamic range (LDR), sensitivity and detection limit (DL) of the fabricated chlorobenzene sensor, a calibration curve was prepared by plotting current against chlorobenzene concentration. Then, the performance of the chlorobenzene sensor was investigated in detail.
2. Materials and methods
2.1. Chemicals and reagents
The TiO2, ZnO and RuO2 nanoparticles were synthesized using analytical grade titanium(IV) butoxide (Ti(OCH2CH2CH2CH3)4), acetoxyzinc dihydrate (Zn(Ac)2·2H2O), and ruthenium trichloride trihydrate (RuCl3·3H2O) respectively, and these chemicals were obtained from Sigma Aldrich (Germany). To accomplish this study, the environmental toxins such as 1,4-dioxane, 3-chlorophenol, 2,4-dinitrophenol (2,4-DNP), chlorobenzene (CBZ), p-nitrophenol (p-NP), 4-nitrophenyl hydrazine (4-NPHyd), phenylhydrazine (PHyd), m-xylene, zimataldehyde, and pyridine were procured from Sigma-Aldrich and used as purchased. Besides this, Nafion (5% suspension in ethanol), and mono- and disodium phosphate were similarly acquired from Sigma Aldrich (Germany).
2.2. Synthesis of nanoparticles
2.2.1. Synthesis of TiO2 NPs. An efficient sol–gel technique was applied to prepare titanium oxide (TiO2) NPs using titanium butoxide as a precursor following the procedure described elsewhere.68 Following this typical method, 4 mL titanium butoxide was added into a 50 mL beaker containing a mixture of 2.6 mL acetic acid and 4.3 mL butanol. Then, 4 mL water was slowly added into the beaker and kept under continuous stirring to yield TiO2 as a colloid form. After that, the resulting colloidal solution was kept under similar conditions for another 5 h. Finally, the obtained colloid was dried at 110 °C overnight and followed by calcination at 500 °C for 2 h. At the end, the calcined powder was ground and stored in an air-tight container.
2.2.2. Synthesis of ZnO NPs. ZnO nanoparticles were prepared by a homogeneous precipitation technique using Zn(Ac)2·2H2O precursor and urea as a precipitating agent. In this wet-chemical method, a solution of 12.0 g urea and 3.12 g Zn(Ac)2·2H2O in 200.0 mL deionized water was taken in a 250.0 mL beaker and placed on a hot plate at 90 °C for 4 h with continuous stirring. A white precipitate of ZnO was obtained under vigorous mixing. Then, the mixture was kept under ambient conditions in the laboratory to settle down, and the a precipitate of ZnO was obtained. After that, the ZnO precipitate was separated from the aqueous medium and washed successively with deionized water. Then, it was kept inside an oven at 110 °C overnight to dry. The as-prepared dried particles were then ground into fine particles and annealed at 500 °C for 2 h. Finally, the annealed powder was further ground and stored in an air-tight container.
2.2.3. Synthesis of RuO2/ZnO/TiO2 ternary nanocomposites. The RuO2/ZnO/TiO2 NCs containing different percentages of RuO2 were prepared by an impregnation technique described previously,69 keeping the weight ratio of TiO2 and ZnO constant. According to the described impregnation method, a predetermined amount of RuCl3·H2O was dissolved in 50.0 mL deionized water in a 100 mL beaker. Then, 0.15 g of the prepared TiO2 NPs and 0.15 g of ZnO NPs were dispersed into the RuCl3·H2O solution with continuous stirring for 4 h. At the same time, water was removed by evaporation to result in nanoparticles. Finally, the obtained nanoparticles were calcined in a muffle furnace at 500 °C for 2 h in the presence of atmospheric oxygen to result in the desired RuO2/ZnO/TiO2 NCs.
2.3. Characterizations of NPs
The phase crystallinity of the prepared NPs was investigated using a X-ray diffractometer (model 3040XPert PRO, Philips) at 2θ degree in the range of 10–80°. The mean size of the crystallite was calculated applying Scherrer's formula. X-ray photoelectron spectra (XPS) were recorded using a Thermo-Scientific spectrophotometer (Thermo Scientific K-Alpha KA1066 spectrometer) equipped with an Al-Kα X-ray excitation radiation source with a beam-spot size of 300.0 μm. Besides this, field emission scanning electron microscopy (FESEM; JSM-7600F, JEOL, Japan) equipped with an EDS was used to investigate the elemental analysis and surface morphology of RuO2/ZnO/TiO2 NCs. Moreover, a Keithley electrometer (6517A, USA) was applied as the central dominating equipment to supply constant potential for the exploration of the electrochemical behavior of the proposed sensor. The band gap energy of the prepared NPs was determined by measuring the UV-vis diffuse reflectance spectra (UV-vis DRS) of the NPs under ambient conditions. The UV-vis DRS was recorded by scanning the samples from 200 to 800 nm using a UV-vis-NIR spectrometer (LAMDA 750, PerkinElmer, Inc, USA). Furthermore, Sintered PTFE was used as the standard reference.
2.4. Fabrication RuO2/ZnO/TiO2 NC-based sensor
The working electrode that is the key element of an EC sensor was produced by modifying a conventional GCE (surface area of 0.0316 cm2) with a slurry of RuO2/ZnO/TiO2 NCs. To execute this modification task, the slurry was formulated by adding a suitable quantity of RuO2/ZnO/TiO2 NCs to ethanol. A thin film of RuO2/ZnO/TiO2 NCs was subsequently obtained by dropwise addition of the slurry on the active area of the GCE followed by drying under ambient conditions. A suspension containing 5% Nafion in ethanol was added to the RuO2/ZnO/TiO2 NC thin film in order to enhance the binding strength of the film. After adding Nafion binder, the film was kept in an oven at 35 °C to dry it again entirely. Finally, the desired electrochemical cell known as the sensor was assembled using a Keithley electrometer, where the modified GCE as RuO2/ZnO/TiO2 NCs/GCE and a Pt wire were connected using a Keithley electrometer in a series. It is noted that the assembled sensor was based on a two-electrode (working and counter) system. The performance of the recently developed EC sensor towards the analyte chlorobenzene was determined in a phosphate buffer solution. A number of chlorobenzene solutions of concentrations ranging from 0.1 mM to 0.1 nM were produced by diluting the 0.1 mM stock solution of chlorobenzene and used as the target analyte for the electrochemical characterization of the CBZ sensor. The response current was estimated applying a potential from 0.0 to +1.5 V. The pH and the volume of solution were kept fixed to 7 and 10 mL, respectively. A linear relation of current versus concentration of CBZs was executed to form the calibration curve of CBZ sensor. The slope of calibration curve and surface area of GCE (0.0316 cm2) were used to calculate the sensitivity of the CBZ sensor. Considering the maximum linear segment on the calibration curve, the linear dynamic range for CBZ detection was identified. Applying a signal-to-noise ratio of 3, the lower limit of the CBZ sensor was estimated. Equimolar concentrations of mono- and disodium phosphate were used to prepare a buffer medium of pH 7.0.
3. Results and discussions
3.1. Characterization of NPs
3.1.1. XRD analysis. The powder X-ray diffraction (XRD) analysis was performed on the synthesized NPs to identify the phase crystallinity and average crystal size of RuO2/ZnO/TiO2 NCs, as illustrated in Fig. 1. As perceived in Fig. 1(a), the diffracted peaks of pure TiO2 at 2θ of 25.4°, 37.7°, 48°, 53.8°, 55.1° and 62.36° were ascribed to the crystallographic structure anatase phase TiO2 and could be indexed as the (101), (004), (200), (105), (211), (204) and (103) planes, respectively. The observed diffraction peaks of TiO2 were well matched with the values cited in the literature70,71 and JCPDS no. 0078-2486. Besides this, the diffraction peaks for ZnO at 2θ = 31.8°, 34.5°, 36.38°, 47.6°, 56.6° and 62.85° are exhibited in Fig. 1(c) and indexed as the (100), (002), (101), (102), (110), (103), and (112) planes, respectively, which were identified by JCPDS no. 0036-1451 and previously reported articles on ZnO.72,73 Moreover, Fig. 1(b) shows the characteristic XRD pattern of RuO2/ZnO/TiO2 NCs and all the reflected lines were similar to the diffraction peaks of TiO2, as shown in Fig. 1(a), and ZnO, as shown in Fig. 1(c). However, the peaks diffracted from the planes of RuO2 in Fig. 1(b) did not appear clearly owing to the overlap of a more intense peak of ZnO. As anonymous XRD peaks were not perceived in Fig. 1(b), it can be confirmed that RuO2/ZnO/TiO2 NCs was prepared without any contamination. The mean crystallite size (D) of the prepared samples was estimated using Debye–Scherrer's formula74 as follows: |
D = (0.9λ)/(β cos θ)
| (1) |
where λ is the wavelength of Cu Kα radiation (λ = 1.5405 Å), β is the full width at half maximum (FWHM) for the diffraction line under the consideration (radian) and θ is the diffraction angle (°). The value of θ for the ZnO (101) peak was 18.19° and the TiO2 (101) peak was 12.7°. The corresponding β values were estimated to be 0.30 and 0.43 for ZnO and TiO2, respectively. From the XRD pattern of RuO2/ZnO/TiO2 NCs, as shown in Fig. 1(b), the crystallite sizes of the ZnO NPs at the (101) plane and TiO2 NPs at the (101) plane were found as 27.86 and 18.93 nm, respectively, which were very close to pure ZnO (26.1 nm), as shown in Fig. 1(c), and TiO2 (15.47 nm), as shown in Fig. 1(a) respectively.
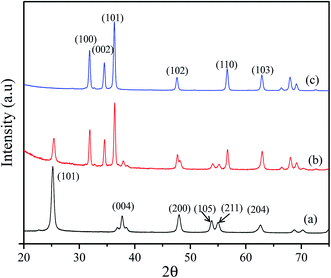 |
| Fig. 1 Comparison of X-ray diffraction pattern of synthesized NPs. (a) XRD patterns of TiO2 NPs, (b) the X-ray diffracted peaks of RuO2/ZnO/TiO2 NCs, and (c) resulted X-ray lines of ZnO NPs. | |
3.1.2. XPS analysis. The XPS studies were executed on RuO2/ZnO/TiO2 NCs to explore the chemical compositions and oxidation states of the elements existing in the synthesized RuO2/ZnO/TiO2 NCs. The XPS survey spectra of RuO2/ZnO/TiO2 NCs shown in Fig. 2 demonstrated that the emissions of only Zn, O, Ti, Ru and C were detected. The detected signal originated from the adsorbed carbon on the surface during the exposure of the NPs to the ambient atmosphere, which commonly exists for XPS. Any peak associated with the presence of impurity was not identified. Thus, the XPS study confirmed that the RuO2/ZnO/TiO2 samples were composed of only ZnO, TiO2 and RuO2 NPs.
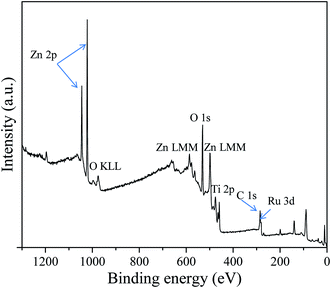 |
| Fig. 2 XPS survey spectrum of RuO2/ZnO/TiO2 NCs. | |
The XPS high-resolution spectra of Ti 2p (Fig. 3(A)) displayed two peaks in the Ti 2p region: the first peak at 458.85 eV was assigned to Ti 2p3/2 and the second peak at 464.50 eV was ascribed to Ti 2p1/2. The distance between Ti 2p1/2 and Ti 2p3/2 peaks was 5.65 eV, which was a characteristic value of the Ti4+ ionization state as reported previously.75,76 The distances between splitting Ti 2p1/2 and Ti 2p3/2 peaks have been stated as 5.73, 5.60, 5.66, and 6.13 eV for Ti2+, Ti3+, Ti4+ and metallic Ti0, respectively.76 This evidenced no contribution of reduced Ti3+ in the spectrum. The XPS spectra of Zn 2p (Fig. 3(B)) demonstrated two peaks at 1021.88 and 1044.98 eV, respectively, which were symmetric and originated from the spin-orbital splitting of the Zn 2p3/2–Zn 2p1/2 core level states of Zn assigned to the lattice ZnO.77 The distance (23.1 eV) between Zn 2p3/2 and Zn 2p1/2 peaks was similar to the standard reference value of ZnO.78 These estimated values of the Zn 2p spectra confirmed the Zn2+ oxidation state of Zn in RuO2/ZnO/TiO2 NCs.78,79
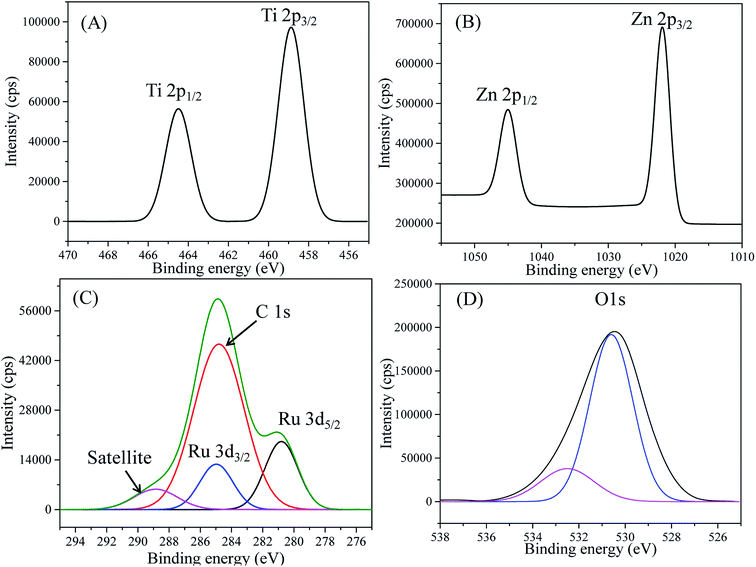 |
| Fig. 3 (A) High-resolution XPS spectra of Ti 2p, (B) Zn 2p level orbital, (C) C 1s + Ru 3d, and (D) O 1s orbit of RuO2/ZnO/TiO2 NCs. | |
Moreover, Fig. 3(C) revealed emission lines of the core-level Ru 3d orbit, which was the overlapped C 1s orbit as perceived. However, the deconvolution of the obtained Ru 3d level as in Fig. 3(C) resulted in three peaks for Ru 3d5/2, Ru 3d3/2 and C 1s. As illustrated in Fig. 3(C), the spin orbitals of Ru 3d5/2 and Ru 3d3/2 were located at 280.8 and 284.97 eV, respectively, and identified for Ru4+ cation existing in the synthesized NPs, as reported previously.78,80 Furthermore, Fig. 3(D) displayed the O 1s orbital of RuO2/ZnO/TiO2 NCs, which was asymmetric indicating the several chemical states existing in the NCs. The deconvolution of the O 1s peak confirmed the two surface compositions of synthesized NCs. The most intense peak as shown in Fig. 3(D) was located at 530.5 eV and could be ascribed to lattice oxygen as Zn–O, Ti–O and Ru–O bonds in the prepared NCs.81–84 However, the weaker peak at 532.5 eV was associated with oxygen in hydroxyl groups on the surface of NPs, i.e., Ti–OH, Ru–OH and Zn–OH bonds.84–86
3.1.3. SEM and EDX analysis. The morphology of the surface of prepared nanomaterials is one of the key parameters that affect the sensing activity of the NPs as a sensing mediator. The RuO2/ZnO/TiO2 nanomaterials were investigated by FESEM, as presented in Fig. 4. The low- and high-magnification images of FESEM analysis shown in Fig. 4(A and B) revealed that the RuO2/ZnO/TiO2 nanomaterials were nanoparticles in shape with irregular size and aggregation. This similar evidence was found from the observation of EDS image, as revealed in Fig. 4(C). The elemental analysis as demonstrated in Fig. 4(D) confirmed the presence of Zn, Ti, Ru, and O only in the synthesized NCs and any peak was not identified for impurity. As perceived in Fig. 4(D), the elemental compositions of RuO2/ZnO/TiO2 NCs were 26.23% O, 3.32% Ti, 62.26% Zn, and 8.19% Ru as weight. The average size of NPs was calculated as 32.5 nm in the range of 20.0–40.0 nm. The size distribution of NPs was calculated from the SEM image and presented in Fig. 4(E).
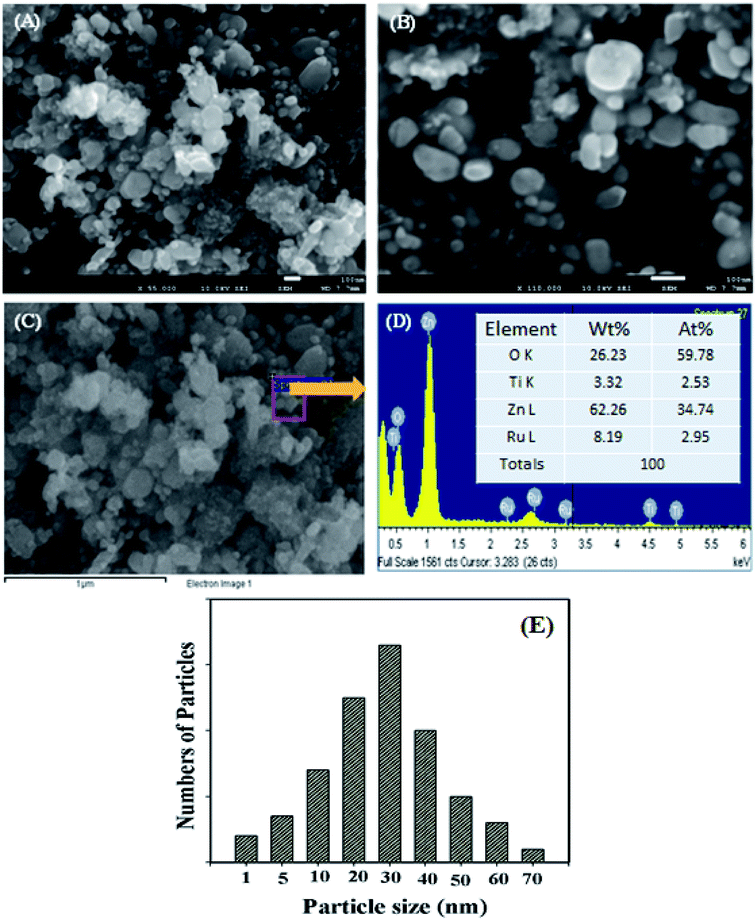 |
| Fig. 4 (A and B) Low- and high-magnification FESEM images of RuO2/ZnO/TiO2 NPs, (C) image of EDS, (D) the elemental compositions of RuO2/ZnO/TiO2 NCs as weight and atomic percentages, and (E) size distribution of NPs. | |
3.1.4. UV-vis DRS analysis. The UV-vis DRS was employed to inspect the optical property of the as-synthesized NPs. The UV-vis DRS spectra of NPs are displayed in Fig. 5(A). As illustrated in Fig. 5(A), the TiO2 NPs and ZnO NPs exhibited the characteristic spectra with fundamental sharp absorption edges at 382 and 370 nm, respectively. The direct optical band gap energy (Eg) of the semiconductor is generally determined following the equation α(hν) = A(hν − Eg)1/2, where α,ν, and A are denoted as the absorption coefficient, light frequency, and constant, respectively.87 The value of Eg is obtained by extrapolating a straight line to the abscissa axis, where α = 0.88 The Kubelka–Munk theory gives a relation between αand remission function F(R), which is defined as α/s = F(R) = (1R)2/(2R), where s is the scattering coefficient and R is the diffused reflectance.89 Thus, the values of Eg of the prepared samples were obtained from intercepts of the tangents of the plot of (F(R)hν)2 versus (hν). The values of Eg of TiO2, ZnO and RuO2/ZnO/TiO2 were estimated to be 3.22, 3.32 and 3.25 eV, respectively, as shown in Fig. 5(B).
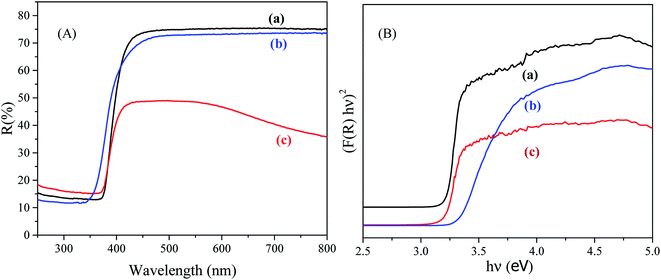 |
| Fig. 5 (A) UV-vis DRS and (B) (F(R)hν)2 versus hν plot of (a) TiO2, (b) ZnO and (c) 1 wt% ternary RuO2/ZnO/TiO2 NCs. | |
3.2. Analytical performance of RuO2/ZnO/TiO2 NC-based sensors
The sensing characterization of the proposed ternary RuO2/ZnO/TiO2 NC-based EC sensor was investigated by applying the current–voltage (I–V) technique. The EC sensor was developed by modifying a GCE with RuO2/ZnO/TiO2 NCs as a thin layer of film that served as the working electrode, while a Pt wire functioned as the counter electrode to assemble the sensor. One of the requirements of this study was the stability of NPs on the GCE. Therefore, few drops of Nafion adhesive were added on the surface of the modified GCE, which enhanced the stability of NPs layer on the GCE during electrochemical investigation and increased the conductance of the assembled working electrode due to the conductive nature of the Nafion co-polymer. As a result, the assembled sensor experienced intense electrochemical responses as the comparable statement has been reported previously in the detection of various chemicals and bio-chemicals in an electrochemical approach.16,90,91 In electrochemical detection, the observed current was assessed on the surface of a thin layer of NCs on the GCE and the delay time in electrometer was constantly set as 1 s throughout the investigation. To explore the selectivity of the assembled sensor, the different analytes with a concentration of 0.1 μM in a phosphate buffer of pH 7.0 were analyzed at a potential ranging from 0 to +1.5 V, as illustrated in Fig. 6(A). As demonstrated in Fig. 6(A), the chlorobenzene (CBZ) exhibited superior electrochemical response to 1,4-dioxane, 2,4-dinitrophenol, 3-chlorophenol, 4-nitrophenylhydrazine, m-xylol, phenylhydrazine, p-nitrophenol, pyridine, zimtaldehyde. Therefore, considering the highest electrochemical reactivity of CBZs toward the sensor assembly, it was denoted as the selective chemical to RuO2/ZnO/TiO2 NCs on the GCE. The consequence of the compositions of RuO2/ZnO/TiO2 NCs in electrochemical sensing of CBZs was studied to explore the optimum composition of NCs as shown in Fig. 6(B). As observed in Fig. 6(B), the ternary nanoparticles of 1% RuO2/ZnO/TiO2 showed high electrochemical sensing performance among the other compositions in analysis of CBZs at 0.1 μM and a potential of 0 to +1.5 V in a buffer phase of pH 7.0. This higher electrochemical response could be ascribed to the combined effects of RuO2, ZnO and TiO2 NPs. The mechanism of improved response of the proposed sensor based on 1% RuO2/ZnO/TiO2/GCE would be discussed in detail in the subsequent section.
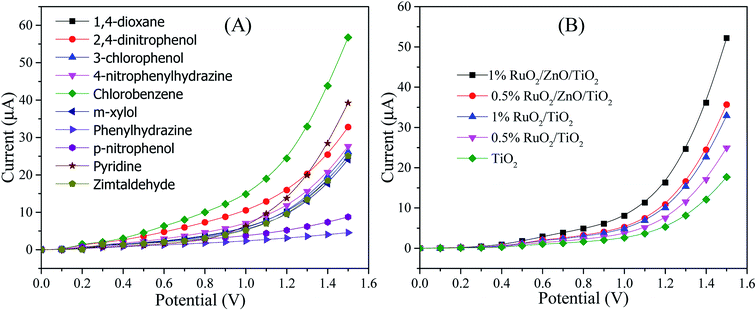 |
| Fig. 6 Performance optimization of the RuO2/ZnO/TiO2/GCE-based chlorobenzene sensor. (A) Electrochemical investigation of toxic chemicals to execute the selectivity of the sensor at 0.1 μM in a buffer phase of pH 7.0, and (B) the control experiments to optimize the composition of ternary RuO2/ZnO/TiO2 NCs as CBZ sensing mediators. | |
Then, the RuO2/ZnO/TiO2 NPs/GCE sensor was subjected to analysis of CBZ solution based on the concentration ranging from 0.1 nM to 0.1 mM in a buffer phase as explored in Fig. 7(A). As presented in Fig. 7(A), the electrochemical responses of CBZs with the assembled sensor were enriched with the increase in chlorobenzene concentrations and distinguishable over the concentration range. The distinguishable responses of the proposed sensor towards different concentrations of CBZs were further confirmed by presenting an enlarged view of Fig. 7(A), as shown in Fig. 7(B). Similar tendencies of electrochemical responses to detect different toxicants have been reported earlier.16,92–94 This result reflected that the conductivity of the fabricated RuO2/ZnO/TiO2 NC-modified electrode increased with the enrichment of CBZ concentration, as excess free electrons were provided to the conduction bands of ZnO and TiO2 NPs in the synthesized RuO2/ZnO/TiO2 NCs.
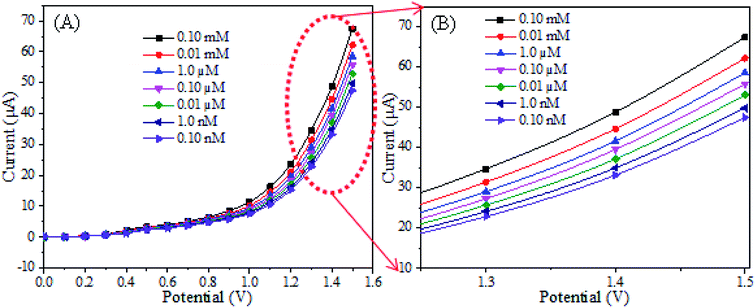 |
| Fig. 7 (A) Typical current–voltage responses of the fabricated sensor at different concentrations of CBZs, and (B) magnified electrochemical responses of the sensor at different CBZ concentrations in the range from 1.2 to 1.5 V. | |
The sensing performance parameters such as sensitivity, LDR and DL of the RuO2/ZnO/TiO2 NC-based chlorobenzene sensor were estimated from the calibration curve of chlorobenzene concentrations versus response currents. To draw the calibration curve of CBZ sensor, the observed current density at different CBZ concentrations were isolated from Fig. 7(B) at a potential of +1.5 V and a new plot of current versus CBZ concentration was constructed, as illustrated in Fig. 8(A), known as the calibration curve of the CBZ sensor. As represented in Fig. 8(A), the current data were linear on the straight line over the concentration range of 0.1 nM to 1 μM, which was denoted as the linear dynamic range (LDR) of the CBZ sensor. Obviously, the obtained LDR was very wider from 0.1 nM to 1.0 μM. To calculate the linearity (r2) of LDR, current versus log(CBZ concentration) was plotted and presented in Fig. 8(B). The regression co-efficient r2 was found to be 0.998, which demonstrated the good linearity of LDR. The CBZ sensor sensitivity was determined from the slope of the calibration curve by considering the area of the GCE (0.0316 cm2). The obtained sensitivity result was calculated as 32.02 μA μM−1 cm−2, which was the highest value compared to the reported articles on the CBZ sensor. The DL of CBZ sensor was calculated at a signal-to-noise ratio of 3 and the determined value was 98.7 ± 4.9 pM, which might be sufficiently low.
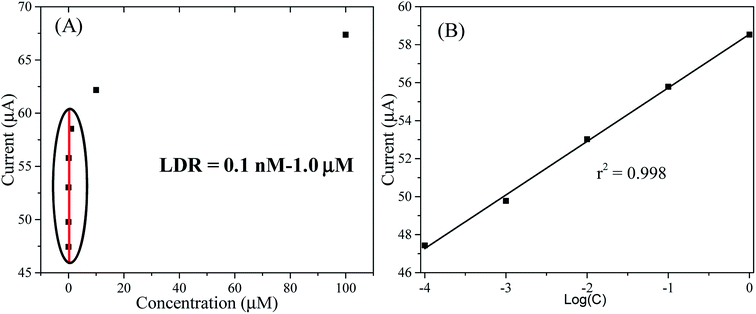 |
| Fig. 8 (A) The calibration of the CBZ sensor based on the ternary RuO2/ZnO/TiO2 NCs/GCE, and (B) the linearity of LDR based on current versus log(CBZ concentration). | |
3.2.1. Optimization of the sensor. The reproducibility test of the CBZ sensor probe with RuO2/ZnO/TiO2 NCs/GCE was accomplished in 0.1 μM CBZ at an applied potential ranging from 0 to +1.5 V in a buffer medium of pH 7.0, as presented in Fig. 9(A). As represented in Fig. 9(A), there were no significant changes in the electrochemical responses of CBZs at successive seven replicated runs. The obtained electrochemical responses were not altered on washing of the electrode after each run. Therefore, it can be predicted that the proposed sensor probe was stable-enough to generate similar electrochemical responses in the detection of CBZs under identical conditions. The response time is another key performance to measure the efficiency of the sensor and defined as the time required to achieve 90% of its steady stated signal.95 To measure the response time, the electrodes of the proposed sensor were applied to analyze the CBZs at 0.1 μM at a pH of 7.0, as perceived in Fig. 9(B). As shown in Fig. 9(B), the current versus time plot becomes steady after 10 s. Therefore, the proposed CBZ sensor based on RuO2/ZnO/TiO2 NCs/GCE needed 10 s to complete the electrochemical response of CBZs and the response time was 9 s, which evidenced the high efficiency of the CBZ sensor.
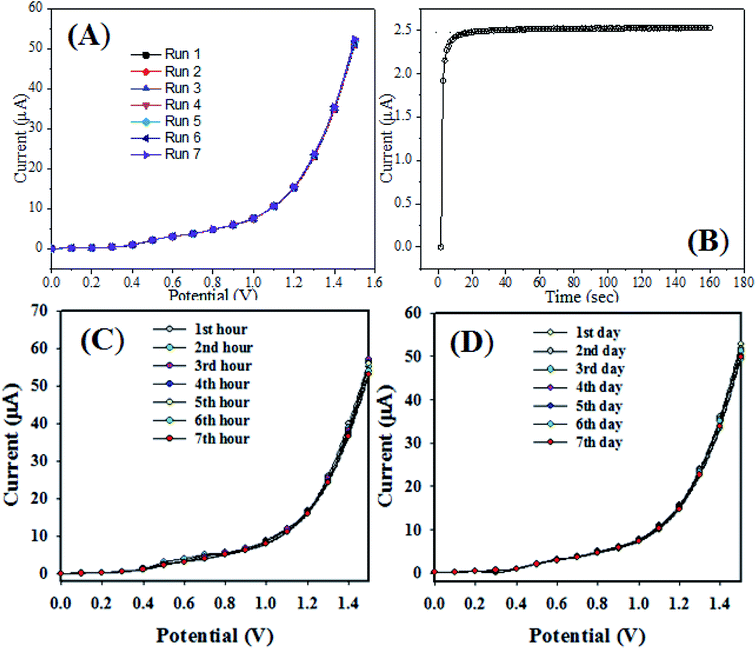 |
| Fig. 9 Performance of reliability test: (A) reliability test of the CBZ sensor at 0.1 μM, (B) response time estimation, (C) intra-day reproducibility performances, and (D) inter-day reproducibility performances. | |
Besides that, we analyzed the intra-day and inter-day electrochemical responses with the RuO2/ZnO/TiO2 NCs/GCE sensor probe by an electrochemical method under identical conditions, as presented in Fig. 9(C and D). Seven readings were taken at 1 hour interval with the sensor probe for the detection of CBZs under identical conditions. However, the sensor reading was taken after one-day interval with the same electrode. The RuO2/ZnO/TiO2 NCs/GCE sensor probe was very stable and almost reproducible, and stable responses were observed from these investigations.
As revealed in Fig. 10(A), the toxic chemicals such as CBZs, 2,4-dinitrophenol, 4-phenylhydrazine, and zimtaldehyde exhibited distinct electrochemical responses at 0.1 μM concentration in a buffer phase of pH 7.0. However, as shown in Fig. 10(B), the electrochemical responses of chlorobenzenes in the presence of 2,4-dinitrophenol, 4-phenylhydrazine, and zimtaldehyde were completely undistinguished and not possible to separate each other. Therefore, these investigations confirm that the projected sensor based on the ternary metal oxide RuO2/ZnO/TiO2 NCs/GCE was selective to chlorobenzenes, and the other co-existing toxic chemicals did not alter its electrochemical response.
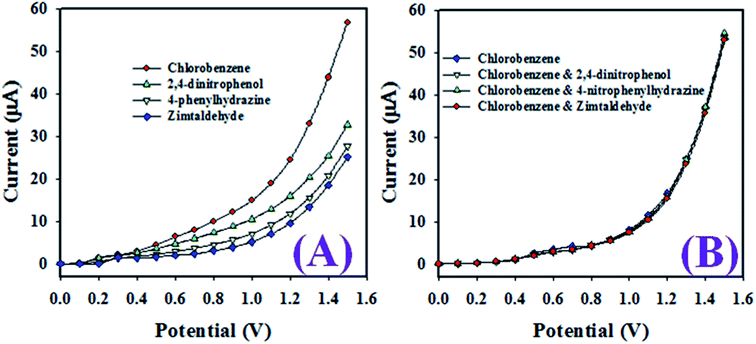 |
| Fig. 10 (A) Electrochemical responses of various toxic chemicals at 0.1 μM concentration in a buffer phase of pH 7.0, and (B) interference effect of other co-existing toxins in the chlorobenzene sensor. | |
3.2.2. Sensing mechanism. The experimental results revealed that all the TiO2, RuO2/TiO2 and ternary oxide RuO2/ZnO/TiO2 NC-based sensors were sensitive to CBZs. The response value of the sensor based on RuO2/TiO2 NPs was higher than the response value of TiO2. Accordingly, the RuO2/ZnO/TiO2 NC-based electrochemical (EC) sensor demonstrated higher response current than TiO2, RuO2/TiO2-based sensors. The possible sensing mechanism of the proposed sensor to detect CBZs is schematically shown in Scheme 1. The proposed mechanism could be explained with the following equations: |
O2 (air/liquid interface) → O2 ads(RuO2/ZnO/TiO2)
| (2) |
|
O2 ads(RuO2/ZnO/TiO2) + 2e− (RuO2/ZnO/TiO2) → 2O− ads(O−/O2−)
| (3) |
|
2C6H5Cl + 29O− → 12CO2 + 5H2O + 2Cl− + 27e−
| (4) |
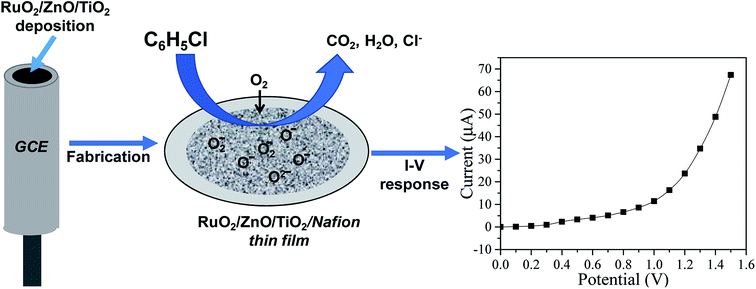 |
| Scheme 1 Mechanism of CBZ detection with ternary oxide RuO2/ZnO/TiO2 NCs by an electrochemical approach in an aqueous medium. | |
First of all, bulk oxygen molecules available at the liquid/air interface tended to adsorb and react with electrons from ternary RuO2/ZnO/TiO2 NC conduction bands, and subsequently, the adsorbed oxygen was ionized (eqn (2) and (3)) and converted into negative oxygen species (O2−, O−, O2−) around the surface of ternary RuO2/ZnO/TiO2 NCs leading to an increase in the sensing material resistance. When CBZs reacted with the adsorbed oxygen species, they were oxidized as explained in eqn (4), liberating free electrons that were sent back to the semiconductor conduction band. It is obvious from the above reactions that some of the chemisorbed O− oxygen ions were removed for oxidizing CBZs, releasing electrons back to the semiconductor conduction band and increasing the electronic conductivity of the NP surface. The oxygen adsorption and the electrochemical CBZ oxidation were further confirmed by the preceding authors.30,96,97
The enhanced sensing mechanism of the ternary RuO2/ZnO/TiO2 NC-based EC sensor could be explained using the band theory of semiconductor metal oxides. First of all, the capture of electrons in the conduction band of both TiO2 and ZnO by adsorbed oxygen led to the development of an electron-depleted, space-charge layer at the interface of ternary RuO2/ZnO/TiO2 NCs. Therefore, a potential barrier was built, which hindered the movement of the conduction band electron and increased the resistance of the sensing materials. Second, it is reported in our previous studies that the RuO2 work function (6.2 eV) was larger than TiO2 (3.8 eV) and ZnO (4.2 eV) work function.69,98 Thus, the Fermi energy levels of both TiO2 and ZnO were more negative than RuO2. As a result, when RuO2 came into contact with ZnO and TiO2 NPs, the electrons migrated from TiO2 and ZnO to RuO2 for equalizing the Fermi levels at a thermal equilibrium, resulting in the development of an electron depletion region and surface upward bent band in the semiconductor (Fig. 11(A) and (D)).
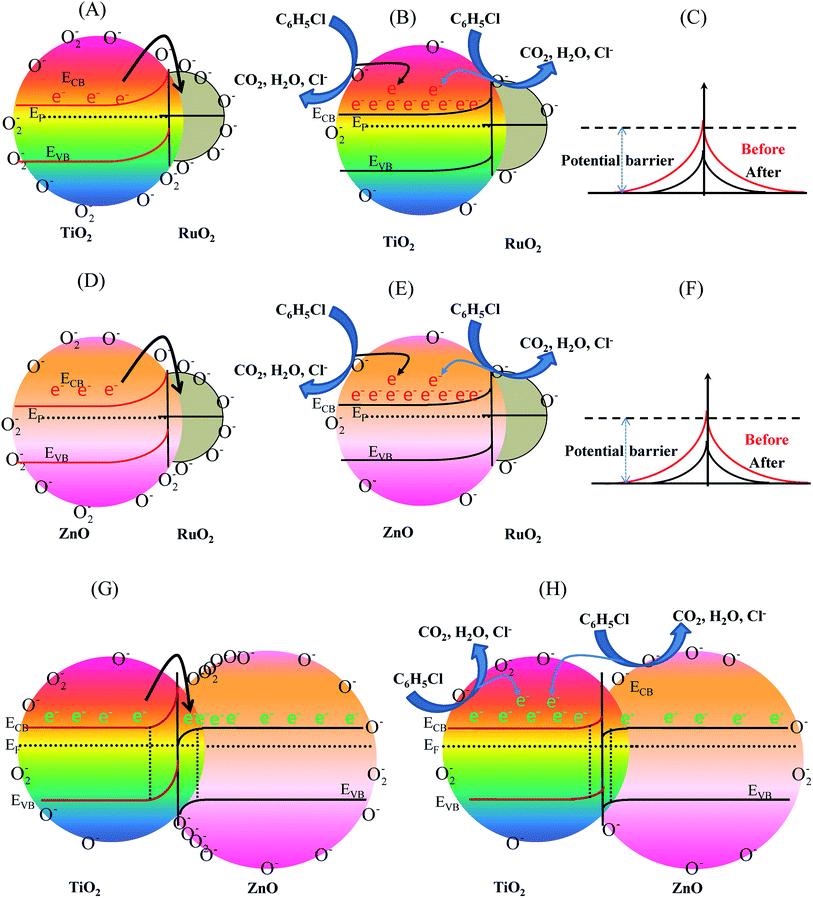 |
| Fig. 11 Energy band diagram of nanocomposite systems when exposed to the CBZ solution; before (A) RuO2/TiO2, (D) RuO2/ZnO, and (G) ZnO/TiO2 and after: (B and C) RuO2/TiO2 (E and F) RuO2/ZnO, and (H) ZnO/TiO2. | |
The electron depletion region formed led to an internal electric field, resulting in increased resistance at the heterojunction. Third, the Fermi energy level (EF) of TiO2 was more negative than the Fermi energy level of ZnO;69,98 electrons migrated from TiO2 to ZnO until the Fermi level of the n–n heterojunction of ZnO/TiO2 came to equilibrium. The migration of electrons to the ZnO side created an electron depletion layer on the side of TiO2 and further bent the band and led to a higher resistance of sensing materials than the pure TiO2 and ZnO sensors, as revealed in Fig. 11(G). Thus, at thermal equilibrium, the oxygen adsorption was enhanced on the ZnO surface because of the formation of an electron-enriched zone at the ZnO side. Furthermore, it led to a more substantial depletion of TiO2 grains and the formation of contact potential at the interface of ZnO/TiO2. According to the reaction mechanism as described above, when RuO2/ZnO/TiO2 NC-based sensors were exposed to chlorobenzenes, the interaction of CBZ molecules with pre-adsorbed oxygen ions released electrons back to the conduction bands of the sensing RuO2/ZnO/TiO2 NCs. This significantly reduced the width of the depletion layer at the heterojunction of RuO2/TiO2 (Fig. 11(B and C)) and RuO2/ZnO (Fig. 11(E and F)), and between TiO2 and ZnO (Fig. 11(H)), resulting in a great decrease in sensor resistance, hence increasing the response current. In summary, the formation of heterojunctions in ternary RuO2/ZnO/TiO2 NCs greatly increased the resistance in the absence of CBZs and decreased the resistance in the presence of CBZs in comparison with the TiO2 sensors. Furthermore, it is reported that nano-sized RuO2 could act as a catalyst for the oxidation reaction.99,100 As a catalyst for the oxidation reaction, RuO2 activated the CBZ molecules when CBZs were adsorbed onto the RuO2 surface. Subsequently, the activated CBZ molecules were migrated to react with oxygen species on the ZnO and TiO2 metal oxide NP surface, thus releasing electrons and increasing the conductivity of the sensing materials. Consequently, the improved sensing activity of composite RuO2/ZnO/TiO2 NCs was ascribed to the combined effects of depleted layer formation at the surface of individual TiO2 and ZnO and the formation of a hetero-junction between ZnO and TiO2 grains and between RuO2 and ZnO or TiO2 grains.
To establish the reliability of this study, a comparison based on the analytical parameters of the CBZ sensor such as sensitivity, LDR and DL is illustrated in Table 1. It was found that the CBZ sensor based on RuO2/ZnO/TiO2 NCs/GCE exhibited better performances. As stated in Fig. 1, ternary oxide RuO2/ZnO/TiO2 NCs possessed high crystallinity with very small grain size at nano-levels. Besides this, the FESEM investigation confirmed that the synthesized nanomaterials consisted of nanoparticles with a spherical-like shape. Therefore, the reactive surface area of the synthesized NPs was very high. As a result, the prepared NPs on the GCE were able to provide a nano-environment, which was favorable for high electrochemical sensing performance. For these reasons, the assembled CBZ sensor exhibited better sensitivity, LDR and DL among the tested material, as illustrated in Table 1. Moreover, the projected CBZ sensor exhibited good reproducibility and efficiency in analyzing real environmental samples.
Table 1 Performance of the CBZ detection with various nanocomposite sensors by an electrochemical methoda
Modified electrode |
DL |
LDR |
Sensitivity |
Ref. |
DL (detection limit), LDR (linear dynamic range). |
FeO/CdO NCs/GCE |
72.73 pM |
0.089 nM to 0.89 mM |
1.3054 μA μM−1 cm−2 |
32 |
MCM-41/GCE |
13.0 pM |
0.089 nM to 8.9 mM |
0.7468 μA μM−1 cm−2 |
33 |
PPY/CZO/AgE |
0.34 nM |
0.35 nM to 3.5 mM |
2.702 × 10−3 μA μM−1 cm−2 |
101 |
RuO2/ZnO/TiO2 NCs/GCE |
98.7 pM |
0.1 nM to 1.0 μM |
32.02 μA μM−1 cm−2 |
This work |
3.3. Analysis of real samples
To satisfy the real-time application of the proposed sensor, the presented CBZ sensor with RuO2/ZnO/TiO2 NCs/GCE was used to detect CBZs in environmental samples applying a recovery method via an electrochemical approach. We used extracts of PC-baby bottle, industrial waste effluents, PC-water bottles, and PVC-food packaging bags (PVC-FPB) to measure CBZs in environmental samples. Based on the performance of the CBZ sensor, as indicated in Table 2, it was possible to detect the targeted analyte (CBZ) in the real environmental samples with acceptable and satisfactory results.
Table 2 Measured concentrations of the CBZ analytes in real environmental samples
Sample |
Added CBZ concentration (μM) |
Determined CBZ concentrationa by RuO2/ZnO/TiO2 NPs/GCE (μM) |
Average recoveryb (%) |
RSDc (%) (n = 3) |
R1 |
R2 |
R3 |
Mean of three repeated determination (signal to noise ratio 3) with by RuO2/ZnO/TiO2 NPs/GCE. Concentration of CBZs determined/concentration taken (unit: μM). Relative standard deviation value indicates precision among three repeated measurements (R1, R2, R3). |
Industrial effluent |
0.0100 |
0.0096 |
0.0095 |
0.0095 |
95.33 |
0.61 |
PC-baby bottle |
0.0100 |
0.0098 |
0.0098 |
0.0099 |
98.33 |
0.59 |
PC-water bottle |
0.0100 |
0.0103 |
0.0101 |
0.0098 |
100.66 |
2.50 |
PVC-FPB |
0.0100 |
0.0101 |
0.0099 |
0.0102 |
100.67 |
1.52 |
4. Conclusion
In conclusion, a highly sensitive CBZ sensor was developed based on ternary metal oxides such as RuO2/ZnO/TiO2 NCs on a GCE by an electrochemical approach. The RuO2/ZnO/TiO2 NC was prepared by an impregnation technique, while ZnO and TiO2 NPs were synthesized by precipitation and sol–gel techniques, respectively. The sensor was assembled with a GCE modified with RuO2/ZnO/TiO2 NCs as a thin film with conducting Nafion binder, which served as the working electrode. The fabricated sensor showed good selectivity towards CBZ detection in a buffer medium compared to other chemicals. The response time was about 9 s, which was faster enough for real-time monitoring of sensor probes. The prepared NP sensor probe displays higher sensitivity, large LDR, lower DL, excellent reproducibility, good reliability and stability. At the end, the sensing mechanism of the ternary oxide RuO2/ZnO/TiO2-based electrochemical sensor was discussed and analyzed by the semiconductor energy-band theory in this report. This work provided a new strategy to utilize ternary metal oxide RuO2/ZnO/TiO2 NCs as efficient electron mediators to develop highly selective sensors toward CBZ detection for the safety of environmental and healthcare fields on large scales.
Conflicts of interest
On behalf of all authors, the corresponding author declares that there is no conflict of interest.
Acknowledgements
This work was financially supported by Bangladesh Bureau of Educational Information and Statistics (BANBEIS), Ministry of Education, Government of the People's Republic of Bangladesh (Grant No. SD2019841).
References
- N. Kometani, S. Inata, A. Shimokawa and Y. Yonezawa, Int. J. Photoenergy, 2008, 512170, DOI:10.1155/2008/512170.
- K. Poplawski, J. Lichtenberger, F. J. Keil, K. Schnitzlein and M. D. Amiridis, Catal. Today, 2000, 62(4), 329–336, DOI:10.1016/S0920-5861(00)00434-X.
- S. Krishnamoorthy, J. A. Rivas and M. D. Amiridis, J. Catal., 2000, 193(2), 264–272, DOI:10.1006/jcat.2000.2895.
- X. Ma, Q. Sun, X. Feng, X. He, J. Guo, H. Sun and H. Cao, Appl. Catal., A, 2013, 450(15), 143–151, DOI:10.1016/j.apcata.2012.10.019.
- D. Calamari, S. Galassi, F. Setti and M. Vighi, Chemosphere, 1983, 12(2), 253–262, DOI:10.1016/0045-6535(83)90168-6.
- Y. He, Y. Wang and H. K. Lee, J. Chromatogr. A, 2000, 874, 149–154 CrossRef CAS.
- D. Djohan, J. Yu, D. Connell and E. Christensen, J. Toxicol. Environ. Health, Part A, 2007, 70(19), 1594–1603, DOI:10.1080/15287390701432384.
- R. R. Kozani, Y. Assadi, F. Shemirani, M. R. M. Hosseini and M. R. Jamali, Talanta, 2007, 72(2), 387–393, DOI:10.1016/j.talanta.2006.10.039.
- R. Nazari, L. Rajić, A. Ciblak, S. Hernández, I. E. Mousa, W. Zhou, D. Bhattacharyya and A. N. Alshawabkeh, Chemosphere, 2019, 226, 556–563, DOI:10.1016/j.chemosphere.2018.10.143.
- L. S. Riter, L. Charles, M. Turowski and R. G. Cooks, Rapid Commun. Mass Spectrom., 2001, 15(23), 2290–2295, DOI:10.1002/rcm.489.
- P. Jandera, J. Fischer and B. Prokeš, Chromatographia, 2001, 54, 581–587, DOI:10.1007/BF02492182.
- H. Borsdorf, A. Rämmler, D. Schulze, K. O. Boadu, B. Feist and H. Weiß, Anal. Chim. Acta, 2001, 440, 63–70 CrossRef CAS.
- M. M. Alam, A. M. Asiri, M. M. Rahman and M. A. Islam, Mater. Chem. Phys., 2020, 244, 22740, DOI:10.1016/j.matchemphys.2020.122740.
- S. Vinoth, R. Ramaraj and A. Pandikumar, Mater. Chem. Phys., 2020, 245, 122743, DOI:10.1016/j.matchemphys.2020.122743.
- C. I. L. Justino, T. A. P. Rocha-Santos and A. C. Duarte, TrAC, Trends Anal. Chem., 2013, 47, 27–36, DOI:10.1016/j.trac.2013.02.004.
- M. T. Uddin, M. M. Alam, A. M. Asiri, M. M. Rahman, T. Toupance and M. A. Islam, RSC Adv., 2020, 10, 122–132, 10.1039/c9ra08669b.
- M. M. Alam, A. M. Asiri and M. M. Rahman, Mater. Chem. Phys., 2020, 243, 122658, DOI:10.1016/j.matchemphys.2020.122658.
- P. Bollella, G. Fusco, C. Tortolini, G. Sanzò, G. Favero, L. Gorton and R. Antiochia, Biosens. Bioelectron., 2017, 89, 152–166, DOI:10.1016/j.bios.2016.03.068.
- Y. Song, Y. Luo, C. Zhu, H. Li, D. Du and Y. Lin, Biosens. Bioelectron., 2016, 76, 195–212, DOI:10.1016/j.bios.2015.07.002.
- R. C. Singh, O. Singh, M. P. Singh and P. S. Chandi, Sens. Actuators, B, 2008, 135, 352–357, DOI:10.1016/j.snb.2008.09.004.
- M. K. Hossain, S. C. Ghosh, Y. Boontongkong, C. Thanachayanont and J. Dutta, J. Metastable Nanocryst. Mater., 2005, 23, 27–30, DOI:10.4028/www.scientific.net/JMNM.23.27.
- R. Jagadish, S. Yellappa, M. Mahanthappa and K. B. Chandrasekhar, J. Chin. Chem. Soc., 2017, 64, 813–821, DOI:10.1002/jccs.201600817.
- H. Ma, Y. Xu, Z. Rong, X. Cheng, S. Gao, X. Zhang, H. Zhao and L. Huo, Sens. Actuators, B, 2012, 174, 325–331, DOI:10.1016/j.snb.2012.08.073.
- J. Huang, X. Xu, C. Gu, W. Wang, B. Geng, Y. Sun and J. Liu, Sens. Actuators, B, 2012, 173, 599–606, DOI:10.1016/j.snb.2012.07.068.
- Z. Li, J. Li, L. Song, H. Gong and Q. Niu, J. Mater. Chem. A, 2013, 1, 15377–15382, 10.1039/c3ta13500d.
- C. Zhao, B. Huang, J. Zhou and E. Xie, Phys. Chem. Chem. Phys., 2014, 16, 19327–19332, 10.1039/c4cp02961e.
- C. Gu, H. Huang, J. Huang, Z. Jin, H. Zheng, N. Liu, M. Li, J. Liu and F. Meng, Sens. Actuators, A, 2016, 252, 96–103, DOI:10.1016/j.sna.2016.11.004.
- K. Li, Y. Luo, L. Gao, T. Li and G. Duan, ACS Appl. Mater. Interfaces, 2020, 12, 16792–16804, DOI:10.1021/acsami.0c00525.
- Y. Tang and J. Ma, RSC Adv., 2014, 4, 25692–25697, 10.1039/c3ra46554c.
- Z. Feng, C. Gao, X. Ma and J. Zhan, RSC Adv., 2019, 9, 42351–42359, 10.1039/c9ra09705h.
- Y. Wan, J. Liu, W. Li, F. Meng, Z. Jin, X. Yu, X. Huang and J. Liu, Nanotechnology, 2011, 22, 315501, DOI:10.1088/0957-4484/22/31/315501.
- M. M. Rahman, M. M. Alam and A. M. Asiri, J. Ind. Eng. Chem., 2018, 62, 392–400, DOI:10.1016/j.jiec.2018.01.019.
- B. M. Abu-Zied, M. M. Alam, A. M. Asiri, W. Schwieger and M. M. Rahman, Colloids Surf., A, 2019, 562, 161–169, DOI:10.1016/j.colsurfa.2018.11.024.
- E. Comini, G. Faglia, G. Sberveglieri, Z. Pan and Z. L. Wang, Appl. Phys. Lett., 2002, 81, 1869–1871 CrossRef CAS.
- Ü. Özgür, Y. I. Alivov, C. Liu, A. Teke, M. A. Reshchikov, S. Doğan and V. Avrutin, J. Appl. Phys., 2005, 98, 041301 CrossRef.
- M. Chakraborty, P. Mahapatra and R. Thangavel, Thin Solid Films, 2016, 612, 49–54 CrossRef CAS.
- K. S. Lee, C. W. Park and J. D. Kim, Colloids Surf., A, 2017, 512, 87–92 CrossRef CAS.
- R. Devi, M. Thakur and C. S. Pundir, Biosens. Bioelectron., 2011, 26, 3420–3426 CrossRef CAS PubMed.
- A. Umar, M. M. Rahman and Y.-B. Hahn, J. Nanosci. Nanotechnol., 2009, 9, 4686–4691 CrossRef CAS PubMed.
- H. B. Balkhoyor, M. M. Rahman and A. M. Asiri, RSC Adv., 2016, 6, 58236–58246, 10.1039/c6ra10863f.
- H. Koga and T. Kitaoka, Chem. Eng. J., 2011, 168, 420–425 CrossRef CAS.
- K. Singh, A. A. Ibrahim, A. Umar, A. Kumar, G. R. Chaudhary, S. Singh and S. K. Mehta, Sens. Actuators, B, 2014, 202, 1044–1050 CrossRef CAS.
- D. X. Ju, H. Y. Xu, Z. W. Qiu, Z. C. Zhang, Q. Xu, J. Zhang, J. Q. Wang and B. Q. Cao, ACS Appl. Mater. Interfaces, 215, 7, 19163–19171, DOI:10.1021/acsami.5b04904.
- X. Song, Z. Wang, Y. Liu, C. Wang and L. Li, Nanotechnology, 2009, 20, 075501, DOI:10.1088/0957-4484/20/7/075501.
- H. S. Woo, C. W. Na, I. D. Kim and J. H. Lee, Nanotechnology, 2012, 23, 245501, DOI:10.1088/0957-4484/23/24/245501.
- C. S. Lee, I. D. Kim and J. H. Lee, Sens. Actuators, B, 2013, 181, 463–470, DOI:10.1016/j.snb.2013.02.008.
- J. Zhao, F. Mu, L. Qin, X. Jia and C. Yang, Mater. Chem. Phys., 2015, 166, 176–181, DOI:10.1016/j.matchemphys.2015.09.044.
- X. Chen and S. S. Mao, Chem. Rev., 2007, 107(7), 2891–2959, DOI:10.1021/cr0500535.
- Y. Tang, P. Liu, J. Xu, L. Le Li, L. Yang, X. Liu, S. Liu and Y. Zhou, Sens. Actuators, B, 2018, 258, 906–912, DOI:10.1016/j.snb.2017.11.071.
- E. Şennik, Z. Çolak, N. Kilinç and Z. Z. Öztürk, Int. J. Hydrogen Energy, 2010, 35, 4420–4427, DOI:10.1016/j.ijhydene.2010.01.100.
- S. J. Bao, C. M. Li, J. F. Zang, X. Q. Cui, Y. Qiao and J. Guo, Adv. Funct. Mater., 2008, 18, 591–599, DOI:10.1002/adfm.200700728.
- S. Lin, D. Li, J. Wu, X. Li and S. A. Akbar, Sens. Actuators, B, 2011, 156, 505–509, DOI:10.1016/j.snb.2011.02.046.
- H. C. Lee, L. F. Zhang, J. L. Lin, Y. L. Chin and T. P. Sun, Sensors, 2013, 13, 14161–14174, DOI:10.3390/s131014161.
- J. Yu and H. Ju, Anal. Chem., 2002, 74, 3579–3583, DOI:10.1021/ac011290k.
- J. Yu and H. Ju, Anal. Chim. Acta, 2003, 486, 209–216, DOI:10.1016/S0003-2670(03)00508-7.
- J. Riga, C. Tenret-Noel, J. J. Pireaux, R. Caudano and J. J. Verbist, Phys. Scr., 1977, 16, 351–354 CrossRef CAS.
- V. Subramanian, S. C. Hall, P. H. Smith and B. Rambabu, Solid State Ionics, 2004, 175, 511–515, DOI:10.1016/j.ssi.2004.01.070.
- E. R. Kötz and S. Stucki, J. Appl. Electrochem., 1987, 17, 1190–1197 CrossRef.
- A. Mills, P. A. Duckmanton and J. Reglinski, Chem. Commun., 2010, 46, 2397 RSC.
- K. Reuter and M. Scheffler, Phys. Rev. B: Condens. Matter Mater. Phys., 2006, 73, 045433 CrossRef.
- N. López, J. Gómez-Segura, R. P. Marín and J. Pérez-Ramírez, J. Catal., 2008, 255, 29–39 CrossRef.
- C. Mondelli, A. P. Amrute, F. Krumeich, T. Schmidt, J. Perez-Ramirez and J. Pérez-Ramírez, ChemCatChem, 2011, 3, 657–660 CrossRef CAS.
- M. M. Rahman, J. Ahmed and A. M. Asiri, Biosens. Bioelectron., 2018, 99, 586–592, DOI:10.1016/j.bios.2017.08.039.
- M. M. Alam, A. M. Asiri, M. M. Rahman and M. A. Islam, Surf. Interfaces, 2020, 19, 100540, DOI:10.1016/j.surfin.2020.100540.
- J. Ahmed, M. M. Rahman, I. A. Siddiquey, A. M. Asiri and M. A. Hasnat, Sens. Actuators, B, 2018, 256, 383–392, DOI:10.1016/j.snb.2017.10.076.
- M. M. Alam, M. M. Rahman, M. T. Uddin, A. M. Asiri, Inamuddin, M. T. Saeed Chani and M. A. Islam, J. Lumin., 2020, 227, 117528, DOI:10.1016/j.jlumin.2020.117528.
- M. M. Rahman and J. Ahmed, Biosens. Bioelectron., 2018, 102, 631–636 CrossRef CAS PubMed.
- M. T. Uddin, Y. Nicolas, C. Olivier, W. Jaegermann, N. Rockstroh, H. Junge and T. Toupance, Phys. Chem. Chem. Phys., 2017, 19, 19279–19288, 10.1039/c7cp01300k.
- M. T. Uddin, Y. Nicolas, C. Olivier, T. Toupance, M. M. Müller, H. J. Kleebe, K. Rachut, J. Ziegler, A. Klein and W. Jaegermann, J. Phys. Chem. C, 2013, 117, 22098–22110, DOI:10.1021/jp407539c.
- T. Sreethawong, Y. Yamada, T. Kobayashi and S. Yoshikawa, J. Mol. Catal. A: Chem., 2005, 241, 23–32, DOI:10.1016/j.molcata.2005.07.009.
- M. T. Uddin, Y. Nicolas, C. Olivier, W. Jaegermann, N. Rockstroh, H. Junge and T. Toupance, Phys. Chem. Chem. Phys., 2017, 19, 19279–19288, 10.1039/c7cp01300k.
- Y. Zhang, F. Zhu, J. Zhang and L. Xia, Nanoscale Res. Lett., 2008, 3, 201–204 CrossRef CAS.
- M. T. Uddin, Y. Nicolas, C. Olivier, L. Servant, T. Toupance, S. Li, A. Klein and W. Jaegermann, Phys. Chem. Chem. Phys., 2015, 17, 5090–5102, 10.1039/c4cp04780j.
- A. L. Patterson, Phys. Rev., 1939, 56, 978, DOI:10.1103/PhysRev.56.978.
- V. Bilovol, S. Ferrari, D. Derewnicka and F. D. Saccone, Mater. Chem. Phys., 2014, 146, 269–276, DOI:10.1016/j.matchemphys.2014.03.021.
- M. C. Biesinger, L. W. M. Lau, A. R. Gerson and R. S. C. Smart, Appl. Surf. Sci., 2010, 257, 887–898, DOI:10.1016/j.apsusc.2010.07.086.
- M. Pérez-González and S. A. Tomás, Catal. Today, 2019 DOI:10.1016/j.cattod.2019.08.009.
- D. Briggs, C. D. Wanger, W. M. Riggs, L. E. Davis, J. F. Moulder and G. E. Muilenberg, Handbook of X-ray Photoelectron Spectroscopy: a reference book of standard data for use in x-ray photoelectron spectroscopy, PerkinElmer Corp, 1979 Search PubMed.
- S. Parthasarathy, V. Nandhini and B. G. Jeyaprakash, J. Colloid Interface Sci., 2016, 482, 81–88, DOI:10.1016/j.jcis.2016.07.066.
- Y. Kaga, Y. Abe, H. Yanagisawa, M. Kawamura and K. Sasaki, Surf. Sci. Spectra, 1999, 6, 68–74, DOI:10.1116/1.1247890.
- P. Banerjee, W. J. Lee, K. R. Bae, S. B. Lee and G. W. Rubloff, J. Appl. Phys., 2010, 108, 043504 CrossRef.
- A. Ievtushenko, O. Khyzhun, I. Shtepliuk, V. Tkach, V. Lazorenko and G. Lashkarev, Acta Phys. Pol., A, 2013, 124, 858–861, DOI:10.12693/APhysPolA.124.858.
- M. T. Uddin, O. Babot, L. Thomas, C. Olivier, M. Redaelli, M. D’Arienzo, F. Morazzoni, W. Jaegermann, N. Rockstroh, H. Junge and T. Toupance, J. Phys. Chem. C, 2015, 119, 7006–7015, DOI:10.1021/jp512769u.
- Y. Zhan, M. R. J. Tan, X. Cheng, W. M. A. Tan, G. F. Cai, J. W. Chen, V. Kumar, S. Magdassi and P. S. Lee, J. Mater. Chem. C, 2017, 5, 9995–10000, 10.1039/c7tc02456h.
- G. G. Guillén, M. I. M. Palma, B. Krishnan, D. Avellaneda, G. A. Castillo, T. K. D. Roy and S. Shaji, Mater. Chem. Phys., 2015, 162, 561–570, DOI:10.1016/j.matchemphys.2015.06.030.
- J. P. Zhao, W. Y. Hernández, W. J. Zhou, Y. Yang, E. I. Vovk, M. Capron and V. Ordomsky, ChemCatChem, 2020, 12, 238–247, DOI:10.1002/cctc.201901249.
- E. A. Davis and N. F. Mott, Philos. Mag., 1970, 22, 0903–0922, DOI:10.1080/14786437008221061.
- E. Sanchez and T. Lopez, Mater. Lett., 1995, 25, 271–275, DOI:10.1016/0167-577X(95)00190-5.
- A. B. Murphy, Sol. Energy Mater. Sol. Cells, 2007, 91, 1326–1337, DOI:10.1016/j.solmat.2007.05.005.
- M. M. Alam, M. T. Uddin, A. M. Asiri, M. M. Rahman and M. A. Islam, Measurement, 2020, 163, 107990, DOI:10.1016/j.measurement.2020.107990.
- M. M. Rahman, M. M. Alam, A. M. Asiri and M. A. Islam, Talanta, 2017, 170, 215–223, DOI:10.1016/j.talanta.2017.04.017.
- M. M. Alam, A. M. Asiri, M. T. Uddin, M. A. Islam and M. M. Rahman, ChemistrySelect, 2018, 3, 11460–11468, DOI:10.1002/slct.201802750.
- M. M. Alam, A. M. Asiri, M. T. Uddin, M. A. Islam and M. M. Rahman, RSC Adv., 2018, 8, 12562–12572, 10.1039/c8ra01734d.
- M. M. Alam, A. M. Asiri, M. T. Uddin, M. A. Islam, M. R. Awual and M. M. Rahman, New J. Chem., 2019, 43, 8651–8659, 10.1039/c9nj01287g.
- A. Wei, L. Pan and W. Huang, Mater. Sci. Eng., B, 2011, 176, 1409–1421, DOI:10.1016/j.mseb.2011.09.005.
- G. N. Dar, A. Umar, S. A. Zaidi, S. Baskoutas, S. H. Kim, M. Abaker, A. Al-Hajry and S. A. Al-Sayari, Sci. Adv. Mater., 2011, 3, 901–906, DOI:10.1166/sam.2011.1242.
- M. Abaker, A. Umar, S. Baskoutas, G. N. Dar, S. A. Zaidi, S. A. Al-Sayari, A. Al-Hajry, S. H. Kim and S. W. Hwang, J. Phys. D: Appl. Phys., 2011, 44, 425401, DOI:10.1088/0022-3727/44/42/425401.
- M. T. Uddin, Y. Nicolas, C. Olivier, L. Servant, T. Toupance, S. Li, A. Klein and W. Jaegermann, Phys. Chem. Chem. Phys., 2015, 17, 5090–5102 RSC.
- J. Lim, J. M. Lee, C. Kim, S. J. Hwang, J. Lee and W. Choi, Environ. Sci.: Nano, 2019, 6, 2084–2093, 10.1039/c9en00500e.
- R. He, G. Xu, Y. Wu, K. Shi, H. Tang, P. Ma, J. Zeng, Y. Bai and S. Chen, Int. J. Hydrogen Energy, 2019, 44, 5940–5947, DOI:10.1016/j.ijhydene.2019.01.114.
- A. A. P. Khan, A. Khan, M. M. Rahman, A. M. Asiri and M. Oves, Int. J. Biol. Macromol., 2017, 98, 256–267, DOI:10.1016/j.ijbiomac.2017.02.005.
|
This journal is © The Royal Society of Chemistry 2020 |
Click here to see how this site uses Cookies. View our privacy policy here.