DOI:
10.1039/D0RA05334A
(Paper)
RSC Adv., 2020,
10, 29296-29305
Kenaf fibre treatment and its impact on the static, dynamic, hydrophobicity and barrier properties of sustainable polystyrene biocomposites
Received
17th June 2020
, Accepted 28th July 2020
First published on 7th August 2020
Abstract
Natural fibre-polymer adhesion can be improved by treating the fibre surface or polymer. In this study, resorcinol-hexamethylenetetramine mixture (R-HMT) is used as a chemical treatment for kenaf fibre waste to extend the interfacial adhesion between the fibre-polystyrene matrices. The effect of the untreated and treated kenaf fibre (designated as UK and TK fibre) on the thermal (DSC), viscoelastic, mechanical, hydrophobicity, and barrier properties of polystyrene (PS) was studied. Four different percentages of each type of fibre (10, 20, 30, and 40 wt%) were used. The chemical structure of the TK fibre was confirmed by Fourier-transform infrared spectroscopy (FT-IR) analysis. The compatibility of the fibre-polymer was investigated by scanning electron microscopy (SEM). The results showed that the use of the treated fibre at 30 wt%, enhanced the tensile strength by 148% and 212% compared to neat PS and PS/UK-30, respectively, indicating a good fibre bond adhesion. The DMA data demonstrated that the storage modulus increased significantly, especially for the PS/TK-30 composite. Meanwhile, the glass transition temperature (Tg) shifted to a lower temperature for both types of fibre. Also, the hydrophobicity of the PS composites, which was determined by thickness swelling measurements, was improved when the TK fibre was inserted. Furthermore, water vapor and oxygen transmission rates were determined. A good correlation between most of the properties for the PS composite-based treated fibre was observed, which revealed the possibility of using these materials for sustainable automotive components and gas sensitive packaging applications.
1. Introduction
Early research showed that plastics, including thermoplastics and thermosets, have been used to replace more conventional materials and metals in several engineering applications because of easier processing as well as cost reduction. Among them, polystyrene (PS) is the simplest thermoplastic, based on a styrene monomer, and named atactic PS as it is an amorphous material. In 1930, it was developed and industrially produced on a large-scale by the BASF Company in Germany and Dow in USA.1 After a few years, and because of the achievements made using Ziegler-Natta catalysts in the field of polymer synthesis, both isotactic and syndiotactic polystyrene were also successfully prepared and then after characterization were found to be semi-crystalline materials.2–5 Thus, PS has become one of the most promising thermoplastics in a variety of engineering applications because of its excellent properties compared with other petroleum-based plastics.
Because of its stereoregular structure, high transparency, inexpensive cost, good electrical properties and ability to be foamed, as well as its recycling capability, the PS polymer could be used in a wide range of applications such as the fabrication of CDs, medical equipment, toys and Styrofoam products that are widely used for food containers. However, the brittleness, low heat distortion temperature, poor barrier to water vapor and gases, non-biodegradability, in addition to the absence of polar groups in its backbone restrict the applications of PS. To overcome these deficiencies, hybrid PS polymer are produced by grafting or blending with other polar polymers to enhance the mechanical and viscoelastic properties and to expand its uses in industrial sectors.6–10
In the literature, numerous studies11–15 are found on the incorporation of PS with natural fibres to offer a proper option for enhancing these properties or to create new biocomposites with high performance for end use products. Among these fibres, kenaf fibres are a lignocellulosic material which is extracted from Hibiscus cannabinus plants and are available in tropical countries such as Egypt, India, Malaysia, Indonesia and Thailand.16 Kenaf fibre was known to ancient Egyptians and was the only material used by the Pharaohs to fabricate their clothes rather than leather.17
Natural fibres or agro-wastes such as jute, sisal, hemp, kenaf, and so on, mainly contain cellulose, hemicelluloses, lignin, and in addition, proteins and a non-negligible amount of mineral oxides.18,19 As a consequence, they have been attracting the attention of many scientists as “biomass or cleaner materials” with several potential uses in various fields such as biofuels20–22 and bioenergy.23–25 Over the last ten years, sisal or kenaf fibre used as a bio-reinforcement for polymers has become a highly preferable alternative to classical petroleum-based fibres because of its abundance, price, lightweight, renewability and its 100% biodegradability. Furthermore, they consume less energy during their processing. Currently, kenaf fibre waste is used in the construction, automotive, ceiling gypsum board, textiles, and paper industries.26,27 However, the main problem associated with the use of kenaf fibre as reinforcement in hydrophobic matrices is incompatibility because of its hydrophilicity, and tendency to form aggregates during processing, which has been viewed as problematic in industrial applications. Because of these problems, this study has focused on a simple treatment of kenaf fibre with a R-HMT mixture in order to improve its hydrophobicity for its use as biomass or reinforcing material.
There are many studies that have been carried out to achieve the miscibility and interfacial bonding between the agro-waste materials and polymers. Among these studies, some have focused on coupling agents or compatibilizer insertion into the polymer matrix, others on grafting or coating of the fibre with convenient chemical reagents with the aim of obtaining a hydrophobic material.28–31 Sanjay and Yogesha32 have studied the effect of treatments for jute and kenaf on the morphology and mechanical properties of epoxy composite laminates. Maldas et al.33 have reported that the grafting and chemical treatments for sawdust wood residue had a positive effect on the mechanical performance of PS. Joseph et al.34 have reported that a remarkable enhancement in physical and mechanical properties of PS/sisal fibre could be achieved when the fibres were pre-treated with cardanol derivatives of isocyanates.
The influence of water uptake on dynamic mechanical and barrier properties of kenaf/polyester composites were investigated by Mazuki et al.35 However, it was also reported previously36 that after a torrefaction thermal treatment, agriculture wastes could be used as a reinforcing agent for biodegradable poly(butylene adipate-co-terephthalate) without requiring a compatibilizer. Currently, Youssef et al. are investigating the use of biocomposites as a potential alternative for automotive and aircraft component manufacturing because they are low density and save fuel, leading to a reduction in CO2 emissions.37
In the present study, we try to overcome the lack of compatibility by treating the fibres with a bonding agent, i.e., using an R-HMT mixture as a new bonding agent for kenaf fibres, in order to make the fibre more hydrophobic, and thereby enhancing the interfacial adhesion between fibre-PS matrices. The main aim of this work is to develop sustainable cleaner composites from PS based TK fibre as a bio-reinforcing material to produce eco-friendly applications. The effect of UK and TK fibre loading on the static and dynamic mechanical properties of PS biocomposites is reported. The hydrophobicity of fibre-reinforced PS composites was assessed by measuring thickness swelling. The morphological characteristics of the investigated samples were also clarified.
2. Materials and experimental techniques
2.1. Materials
The PS with a mass density of 1.04 g cm−3, a MW of 97 × 103 g mol−1 and a melt flow index (200 °C, 5 kg) of 8.50 g 10 min−1 was purchased in the form of pellets from the Chi Mei Corporation, Taiwan. Natural kenaf fibre was cultivated in Egypt and obtained from the Agriculture Research Center, Cairo, Egypt. Resorcinol with a purity > 99% was purchased from Sigma-Aldrich, Egypt. High purity HMT (≥99%, used to produce formaldehyde in the preparation of the fibre), and obtained from Sigma-Aldrich, Egypt. Citric acid was obtained from El Nasr Pharmaceutical Chemicals, Cairo, Egypt.
2.2. Preparation and chemical treatment of kenaf fibre
The kenaf fibre was initially cut into short pieces and pre-dried in an oven (W. C. Heraeus GmbH, Germany) at 60 °C for 24 h in order to remove the moisture and to facilitate the tearing of the fibre. The dried fibre was then transferred into the crushing mill to obtain short fibres. The chemical treatment of the kenaf fibre was carried out as follows: HMT (∼0.903 g) was added into 50 mL of deionized water and stirred at 60 rpm at 70 °C for 30 min to produce formaldehyde and aqueous ammonia. Next, resorcinol (∼1.70 g) was added into the solution, followed by drop-wise addition of 1.90% citric acid with continuous stirring for an additional 30 min. The resultant brown solution was placed in a heating system equipped with a condenser. Then, the kenaf fibre was dispersed in the solution and the temperature was raised to 120 °C with stirring at 400 rpm for 48 h. After the reaction, the treated kenaf (TK) fibre was purified by filtration to remove the excess citric acid and unreacted resorcinol, and this was followed by washing three times with a large excess of deionized water. The TK fibre was dried in an oven at 65 °C for 12 h (see Fig. 1). The TK fibre was kept in a laboratory desiccator prior to the characterization and the compounding.
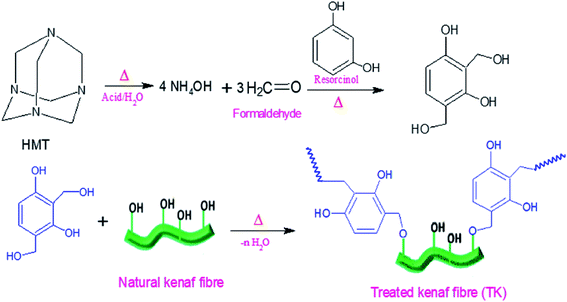 |
| Fig. 1 Schematic representation illustrating the treatment of natural kenaf fibre with a R-HMT mixture. | |
2.3. Fabrication of kenaf-PS biocomposites
Prior to the compounding, untreated kenaf (UK) fibre and PS resin were dried in an oven at 65 °C for 24 h. The PS polymer was pre-mixed at 185 °C for 3 min using a closed Brabender Plasti-Corder Lab Station (Brabender, USA), before introducing the UK or TK fibre. The UK or TK fibres were added with different ratios for a total mixing time of 8 min at 80 rpm and according to the mixing conditions as given in (Table 1). The obtained blends were then molded by placing them in a molding set consisting of a 150 × 150 × 2 mm thick steel spacer placed between two Teflon papers and two steel sheets using a EuroPress men laboratory hydraulic press (Mackey Bowley, UK) under a pressure of 160 kg cm−2 at 185 °C for 5 min. The mold set was removed from the press, followed by air cooling under a certain load until the mold reached a temperature of about 50–60 °C. The extruded sheets were coded according to the type and ratio of fibre in the composite, as shown in Table 1.
Table 1 Composition, mixing protocol and labeling of prepared formulations for kenaf-PS biocomposites containing various proportions of fibre
Ingredients, wt% |
Neat PS |
PS/UK-10 |
PS/UK-20 |
PS/UK-30 |
PS/UK-40 |
PS/TK-10 |
PS/TK-20 |
PS/TK-30 |
PS/TK-40 |
PS |
100 |
100 |
100 |
100 |
100 |
100 |
100 |
100 |
100 |
UK fibre |
— |
10 |
20 |
30 |
40 |
— |
— |
— |
— |
TK fibre |
— |
— |
— |
— |
— |
10 |
20 |
30 |
40 |
Mixing time, min |
8 |
3 + 5 |
3 + 5 |
3 + 5 |
3 + 5 |
3 + 5 |
3 + 5 |
3 + 5 |
3 + 5 |
Screw speed, rpm |
80 |
80 |
80 |
80 |
80 |
80 |
80 |
80 |
80 |
Temperature, °C |
185 |
185 |
185 |
185 |
185 |
185 |
185 |
185 |
185 |
2.4. Fourier-transform infrared spectroscopy (FT-IR)
The FT-IR spectroscopy, in transmission mode, was used to characterize the chemical structure of the kenaf fibre before and after chemical treatment with R-HMT. The FT-IR spectra were acquired by using a Nicolet 380 FT-IR spectrometer (ThermoFisher Scientific, USA), over the wavenumber range of 4000 cm−1 to 600 cm−1 with a resolution of 4 cm−1 and 32 scans. The samples were prepared by pressing ∼150 mg of dried KBr with ∼2 mg of specimen to obtain a thin disk. A pristine KBr disk was used as a reference.
2.5. Scanning electron microscopy (SEM)
The compatibility of UK or TK of fibre in PS was investigated using a high resolution Quanta 250 FEG SEM, (Brno, Czech Republic). The SEM images were obtained at an acceleration voltage of 5–10 kV and the electron beam spot size of 3–3.5 in order to optimize the quality of the images. The fractured surfaces after the tensile test were coated with a thin gold layer and at low vacuum.
2.6. Differential scanning calorimetry (DSC)
The thermal analysis of neat PS and its filled composites with different contents of UK or TK fibres was carried out using a DSC131 evo differential scanning calorimeter (Setaram Instrumentation, Caluire, France), equipped with a liquid nitrogen cooling (LN2) unit. The sample mass was chosen between 10 to 15 mg and investigated using a heating ramp rate from 75 °C to 120 °C at a heating rate of 5 K min−1 and nitrogen flow rate of 50 mL min−1. During the heating cycle, the Tg and its shift with or without TK were evaluated. Duplicate tests were performed for each composite.
2.7. Dynamic mechanical analysis (DMA)
The DMA analysis was conducted on a DMA Q800 (TA Instruments, Newcastle DE, USA) from 30 °C to 150 °C at a heating rate of 3 K min−1, and at a fixed frequency of 1 Hz in the tension mode and with a % strain of 0.02. Sample dimensions of 35 × 6 × 2 mm3 were used for the test. At least three specimens were measured for each sample.
2.8. Mechanical properties
The stress–strain properties of the investigated samples were determined using a Z010 tensile testing machine (Zwick, Germany), with a load cell of 10 kN and a crosshead speed of 5 mm min−1, and in general the results complied with the specification given in ASTM D638-14.38 Type IV dumbbell specimens were die-cut from the extruded sheets. Because environmental conditions have a significant effect on the tensile properties, all the specimens investigated were conditioned in a climate room at 23 ± 2 °C and 50 ± 5% relative humidity (RH) for at least 40 h before the testing, and the conditions were monitored using a Hygrometer (Testo, UK). Five specimens from each composite were tested and the average result was taken.
2.9. Thickness swelling evaluation
The resistance of water absorption for fibre-reinforced PS biocomposites was determined using a thickness swelling test method according to ASTM D570-98.39 The test specimens were cut into strips of size 60 × 60 × 1 mm3 and the initial thickness (T0) was measured, followed by complete immersion in a water bath containing distilled water. The swollen thickness (Tt) for all the specimens were recorded at different times (0, 24, 48, and 96 h) and at normal environmental conditions. The thickness swelling percentage (TS) was calculated according to the following equation:40
The average was calculated from three parallel measurements for each type of composite.
2.10. Barrier properties
Barrier properties in terms of water vapor (WVTR) and gas transmission rates (GTR) for neat PS and its filled composites with untreated and treated fibres were conducted using a W303-B Water Vapor Permeability Analyzer (Lab Geni), according to ASTM D1653-16 (ref. 41) and ASTM D3985-17,42 respectively. This equipment is based on a cup method to measure smooth and uniform plastic sheets. Each sample was cut from the sheet in ring shape of 50 mm and of 90 mm in diameter in case of WVTR and GTR, respectively, with a 200 μm thickness for both. The test was repeated three times and the average values were recorded.
3. Results and discussion
3.1. FT-IR spectroscopy
The FT-IR spectra were used to ascertain the results of the chemical treatment of kenaf fibre by the R-HMT mixture. The results of the fibre treatment are shown in Fig. 2. The spectrum corresponding to raw fibre was also conducted for comparison. In Fig. 2, both spectra show characteristic absorption peaks at ∼2930 and 2850 cm−1 (corresponding to the asymmetric C–H stretching vibration of CH3 and the C–H stretching vibration of CH2, respectively) and a broad peak at ∼3420 cm−1 (hydroxyl groups).43 After chemical treatment, a large peak for the TK fibre appeared at 1060 cm−1 attributed to the ether –C–O–C– groups.31 In addition, new characteristic peaks corresponding to the aromatic ring (ph-ring) and its double bond (C
C) were detected at about 780 cm−1 and 1610 cm−1, respectively. The intensity of the peak which was attributed to hydroxyl groups was reduced in the case of TK fibre as shown in Fig. 2. These results confirmed that the chemical treatment of kenaf fibre by R-HMT had been achieved, as shown in the schematic representation in Fig. 2.
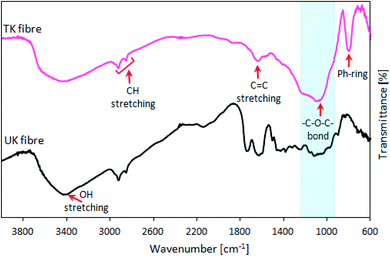 |
| Fig. 2 The results of the FT-IR spectroscopy for UK and TK fibre in the transmission mode. | |
3.2. Differential scanning colorimetry (DSC)
In the DSC, for neat PS and its bio-reinforced composites, a heating ramp was applied to study the effect of UK and TK fibre on the Tg of PS composites containing various ratios of fibre, and the results are shown in Fig. 3. As shown in Fig. 3, the heating ramp rate for neat PS shows a thermal transition centered at around 109.20 °C. This was ascribed to the Tg of the PS polymer, and was probably a semi-crystalline syndiotactic PS type. This finding agrees with that obtained by using a round robin test.44 However, with the addition of the fibre, whether treated kenaf fibre or not, to the matrix, the Tg values shifted to ∼105.40 °C towards a lower temperature and more flexible properties. As reported in previous research,45,46 the kenaf fibres generally have a positive effect on reducing the Tg of the material. In this research, this result was supported by the DMA analysis.
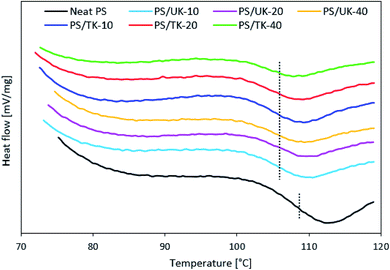 |
| Fig. 3 The DSC thermograms for neat PS and its reinforced composites with different untreated and treated kenaf fibre ratios during the heating ramp. | |
3.3. Dynamic mechanical analysis (DMA)
Neat PS and its filled biocomposites were analyzed with DMA to explore the influence of TK fibre loadings on the viscoelastic properties of the PS polymer in comparison with untreated fibres. As mentioned in previous reports in the literature,43,47 DMA parameters such as dynamic storage modulus (E′) and the damping property (tan
δ) are critical to the molecular motions, reinforcing agent, and relaxation of the material. Fig. 4 and 5 show the DMA curves of the evaluation of E′ and tan
δ as a function of temperature from 30 °C to 150 °C. The curves in Fig. 4(a) show that the storage modulus of all the untreated samples in the glass transition region improved when compared to the neat PS. However, the E′ values are similar with increasing UK content within the experimental errors.
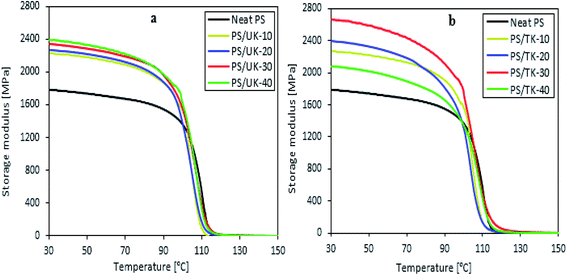 |
| Fig. 4 Storage modulus for neat PS and its filled biocomposites with different ratios of untreated (a) and treated (b) kenaf fibre obtained using DMA in tension mode at a frequency of 1 Hz. | |
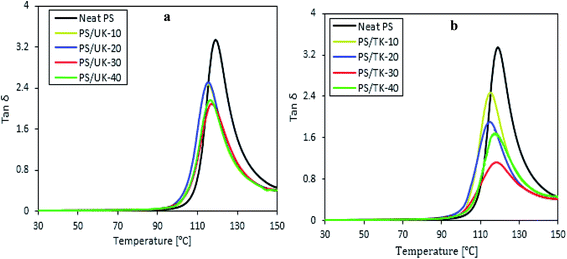 |
| Fig. 5 Damping factor (tan δ) for neat PS and its filled biocomposites with different ratios of untreated (a) and treated (b) kenaf fibre obtained using DMA in tension mode at a frequency of 1 Hz. | |
This was probably attributed to the stiffness of the kenaf fibre, on the other hand, it may be said that UK fibre loadings in the matrix had no positive effect on the dynamic storage modulus. However, a significant increase in storage modulus was regularly was observed after adding TK fibre, ranging from ∼2260 MPa and 2670 MPa in the case of PS/TK-10 and PS/TK-30 samples, respectively, as compared to neat polymer (∼1780 MPa). This improvement was apparently due to the addition of the TK fibre which enhanced the compatibility and the interfacial adhesion within the PS matrix, and which in turn, promoted the chemical linkages between the fibre and the matrix. Hence, E′ values for composites based on TK were found to be higher than the composites based on UK and neat PS. Similar results were explained by Ghasemi et al.48 when hybrid kenaf fibre and wood flour was used as a reinforcing agent for polypropylene. It can also be observed from Fig. 5(a) and (b) that tan
δ was strongly affected by hybridization and the loading of the kenaf fibre. From the figure, it seems that neat PS polymer had a fairly high tan
δ peak at Tg ∼ 119.40 °C.
These results agree with those verified elsewhere for PS/sisal hybrid composites.13 However, the intensity of the tan
δ peaks decreases dramatically with the increasing fibre content, especially in case of composite-based TK when compared to neat PS. Meanwhile, the Tg values shifted to a lower temperature when the fibre was added to the PS matrix. The decrease in the damping peak height mainly depended on the fibre volume fraction in the composite. As the fibre volume fraction increased in the matrix, the movement of little groups and the chains of molecules within the polymer matrix may be hindered because of the lower volume fraction of the polymer. These data agree with those reported in other works.45–49
3.4. Mechanical properties
The static mechanical properties were determined to discover the impact of UK and TK fibres on the tensile properties of the PS polymer at ambient temperature. Typical stress–strain curves for PS/kenaf composites are shown in Fig. 6(a) and (b) and the average stress at maximum for all the samples as a function of fibre volume fraction are plotted in Fig. 6(c). From the figure, it appears that neat PS was a viscoelastic polymer with a tensile stress of ∼22.95 MPa and a low strain at break of 9.50%. With the addition of 10 wt% UK fibre, the stress and strain at break clearly reduced to ∼17.10 MPa and ∼4.40%, respectively, as shown in Fig. 6(a). When the UK fibre ratio was increased to 40 wt%, and a remarkable decrease in both parameters was noticed and declined to 11.7 MPa and 3.20%, respectively. The reason for this might be due to the hydrophilic nature of the kenaf fibre which induced poor compatibility with the PS polymer, and the presence of moisture boosted the void formation, resulting in premature breaks in the polymer chains during the test.49 These results were confirmed by the SEM observations. Similar results have been reported by Moustafa et al.36 when lignocellulosic coffee wastes were used as a reinforcing agent for biodegradable poly(butylene adipate-co-terephthalate) (PBAT). In contrast, a significant increase in tensile stress value (∼21.80 MPa) was observed when introducing 10 wt% TK fibre compared to composites based on UK and neat PS.50 On further increase of the TK fibre content to 30 wt%, the tensile stress improved significantly to ∼33.80 MPa as shown in Fig. 6(b). These increases in tensile stress value were about 212% and 148% when compared with PS/UK-30 and neat PS samples, respectively. The enhancement was because compatibility and the interfacial bonding between the TK fibre and PS polymer was achieved, and the TK fibre was embedded in the PS matrix which is shown in the SEM images.
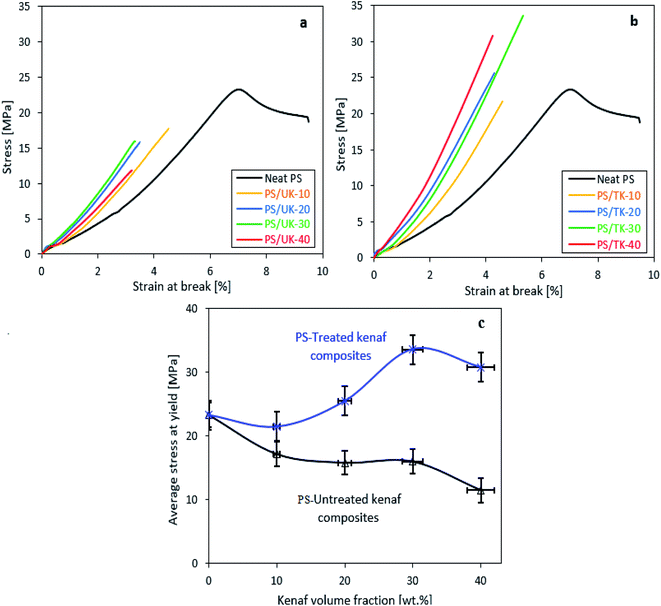 |
| Fig. 6 Stress–strain curves for neat PS, and its filled composites with UK and TK fibre (a and b), and their average stress values at maximum with fiber content (c). | |
Beyond 30 wt%, the tensile stress for the PS/TK-40 composite was clearly reduced but its value remained much higher compared to neat polymer and its composites based on UK fibre. These results show that the modification process for lignocellulosic kenaf fibre is needed for the hybrid kenaf-PS composites to keep their excellent mechanical properties and the optimum fibre ratio was found to be 30 wt% for the TK fibre, as shown in Fig. 6(c). This result was also consistent with that reported by Srebrenkoska et al.51 Nevertheless, the stain at break of the kenaf-PS composites was found to be lower with the insertion of the fibres.
3.5. Morphological analysis
Fig. 7 displays SEM images of fractured surfaces for neat PS polymer and its filled composites containing 30 wt% of UK or TK kenaf fibre. The SEM observations revealed interesting information about the compatibility of the fibre and the fibre-matrix adhesion level when the tensile tests were applied. The SEM micrograph for neat PS shows that it has a uniform surface. When 30 wt% of unmodified fibre was added into the PS matrix, there was incompatibility and large voids and phase-separation of the fibre in the matrix was observed. This was associated with the hydrophilicity of kenaf inducing interfacial debonding between the UK fibre and the matrix. Similar results have been reported by Alias et al.52 when they found that the lowering of impact strength of a kenaf fibre/PLA composite was due to poor interfacial adhesion between the matrix and fibre causing a crack in the matrix. However, for composites containing 30 wt% of TK fibre, better compatibility in the whole of PS matrix was observed and is shown in (Fig. 7). The treatment of the fibre could result in enhanced embedding of the fibre with high intertwining of the fibres within the matrix. This finding was agreement with the results obtained from viscoelastic, mechanical and thickness swelling tests.
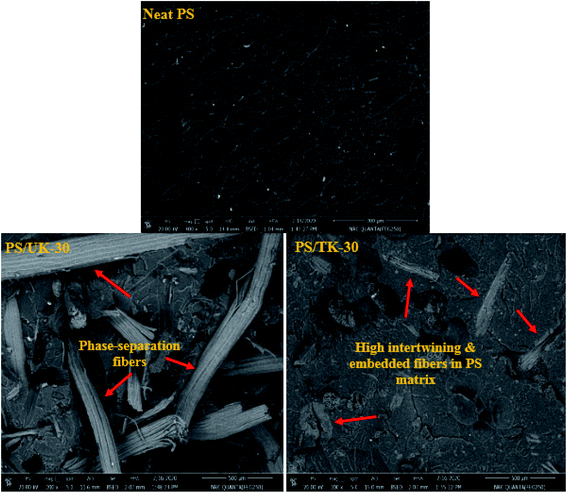 |
| Fig. 7 SEM images of the fractured surfaces for neat PS and its filled composites containing 30 wt% of UK or TK fibre. | |
3.6. Hydrophobicity of PS biocomposites determined by a thickness swelling assessment
Thickness swelling of neat PS and its filled composites with UK or TK fibre was evaluated in terms of water absorption. This property is very closely related to the composite properties and can be largely impacted by some parameters such as the type and loading of the reinforcement, polarity of material, as well as compatibility. In Fig. 8, neat PS shows a significantly lower thickness swelling value with the increase of immersion time, attesting to the hydrophobic nature of the polymer. However, the composite-based UK fibre had a higher thickness swelling result and the increase occurred with both increased fibre loadings and immersion time. This was related to the hydrophilic character of the composite because of the hydrophilic –OH groups of the fibre, thereby leading to phase segregation with voids that could create a preferential pathway for water molecules in the matrix, thereby increasing the thickness swelling. This result agrees with the SEM observations.
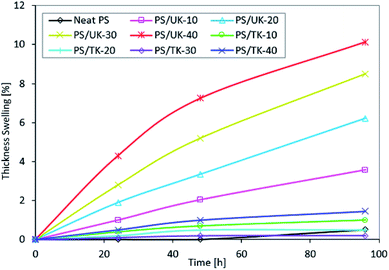 |
| Fig. 8 Thickness swelling (%) of neat PS and its filled biocomposites as a function of immersion time. | |
Correspondingly, the composites containing TK fibres exhibited the lowest thickness swelling values, as demonstrated in Fig. 8, and this effect was amplified when treated fibre was added. This implied that the hydrophobicity of the fibre-reinforced polymer composites strongly depended upon the chemical treatment of the fibre, which led to good compatibility and interfacial adhesion between the fibre and the polymer, which prevented the absorbed water from sneaking into the matrix. In other words, the cellulose components can lose more hydroxyl groups in kenaf fibre during the chemical modification process, which leads to them becoming a more hydrophobic material, as seen in Fig. 1. The results obtained in this work agreed with similar results that were reported in the literature.53,54
3.7. Barrier properties
Barrier properties are considered to be of major importance for packaging materials to keep them safer in severe conditions such as transport, handling and storage. However, the barrier performance can be influenced by some parameters such as the type and the shape of the reinforcement, polarity, miscibility, and filler dispersion state.55,56 The WVTR and GTR values for all the investigated composites are summarized in Table 2. It can be seen that the WVTP and GTR of neat PS were ∼7.67 g per m2 per day and ∼0.02 cm3 per m2 per day, respectively, which indicated there was quite a good barrier property. Nevertheless, after blending with UK fibre to 40 wt%, the values of both properties were dramatically increased up to ∼64.60 g per m2 per day and ∼0.40 cm3 per m2 per day, respectively, for WVTP and GTR for the PS/UK-40 sample. The reason for this is due to the incompatibility of the kenaf fibre with the polymer. Compared with the modified kenaf fibre, the WVTR value was reduced to ∼27.24 g per m2 per day for the PS/TK-40 sample.
Table 2 WVTR and GTR values for neat PS and its composites filled with UK or TK fibre at 23 ± 1 °C/50 ± 5% RH
Sample code |
WVTR, g per m2 per day |
GTR, cm3 per m2 per day |
Neat PS |
7.67 ± 0.5 |
0.02 ± 0.3 |
PS/UK-10 |
49.80 ± 1.7 |
0.12 ± 0.7 |
PS/UK-20 |
51.68 ± 1.3 |
0.15 ± 0.9 |
PK/UK-30 |
58.55 ± 0.9 |
0.22 ± 0.6 |
PK/UK-40 |
64.60 ± 1.6 |
0.40 ± 0.5 |
PS/TK-10 |
12.64 ± 0.8 |
0.03 ± 0.2 |
PS/TK-20 |
21.70 ± 0.5 |
0.01 ± 0.4 |
PS/TK-30 |
24.89 ± 0.3 |
0.00 ± 0.0 |
PS/TK-40 |
27.24 ± 0.7 |
0.00 ± 0.0 |
On the contrary, the GTR for the treated films provided a high oxygen barrier property, especially for the PS/TK-30 and PS/TK-40 samples when compared to neat PS and its composite-based UK fibre. This was because of the good wettability between the TK fibre and PS matrix, as well as anisotropicity of the fiber (i.e., the orientation of fiber), leading to the increase of a tortuous diffusion path in the matrix. Chowdhury et al.56 have reported that anisotropic cellulose nano-crystal films showed the highest gas barrier properties when compared to isotropic films.
4. Conclusions
In the current work, the chemical treatment of natural kenaf fibre waste with an R-HMT mixture was successful and it could be used as a hydrophobic reinforcing material for the PS polymer. Its compatibility in the matrix was found to be good when compared to the untreated fibre. The chemical mechanism of the bonding agent (R-HMT) and the kenaf fibre was confirmed by the results of FT-IR analysis. The renewable kenaf-PS composites based on UK or TK fibre were prepared by melt blending. The effect of UK or TK fibre loadings was studied using the thermal, dynamic, static, thickness swelling, and barrier properties. The results obtained showed that the Tg measured by either DSC or DMA was affected by the insertion of UK or TK fibres, and shifted towards lower temperatures. The DMA experiments illustrated a significant enhancement in the dynamic storage modulus in the glass region, particularly with 30 wt% TK fibre in the matrix, whereas the intensity of the damping peak decreased compared to other samples. There was a large increase in tensile stress values for the PS biocomposites when the TK fibre was used. Nevertheless, the mechanical results for composites reinforced with UK fibre revealed inferior tensile stress values. These results were confirmed by the SEM observations. Furthermore, the composite-based TK fibre had better results for thickness swelling because of the fibre-polymer adhesion that prevented the absorbed water from sneaking into the matrix, resulting in highly hydrophobic materials which could be used in sustainable automotive and packaging applications. However, high thickness swelling values were obtained as the immersion time was increased for the composite-based UK. Also, enhancements in water vapor and oxygen permeability were observed when the TK fibre was used compared to the composites based on the UK fibre.
Conflicts of interest
There are no conflicts to declare.
References
- M. Jaymand, Recent progress in the chemical modification of syndiotactic polystyrene, Polym. Chem., 2014, 5(8), 2663–2690 RSC.
- J. Boor Jr, Ziegler - Natta Catalysts and Polymerization, Academic Press, New York, 1979 Search PubMed.
- G. Natta, P. Pino, E. Mantica, F. Danusso, G. Mazzanti and M. Peraldo, Stereospecific polymerization of α-olefins, Chim. Ind., 1956, 38, 124–127 Search PubMed.
- H. Sinn and W. Kaminsky, Ziegler-Natta catalysis, in Advances in Organometallic Chemistry, Academic Press, 1980, vol. 18, pp. 99–149 Search PubMed.
- N. Ishihara, T. Seimiya, M. Kuramoto and M. Uoi, Crystalline syndiotactic polystyrene, Macromolecules, 1986, 19(9), 2464–2465 CrossRef.
- T. Wang, D. Liu and D. Cui, Highly Syndioselective Coordination (Co) Polymerization of ortho-Fluorostyrene, Macromolecules, 2019, 52(24), 9555–9560 CrossRef.
- N. Ishihara, M. Kuramoto and M. Uoi, Stereospecific polymerization of styrene giving the syndiotactic polymer, Macromolecules, 1988, 21(12), 3356–3360 CrossRef.
- C. Pellecchia, P. Longo, A. Grassi, P. Ammendola and A. Zambelli, Synthesis of highly syndiotactic polystyrene with organometallic catalysts and monomer insertion, Makromol. Chem., Rapid Commun., 1987, 8(6), 277–279 CrossRef.
- W. N. He and J. T. Xu, Crystallization assisted self-assembly of semicrystalline block copolymers, Prog. Polym. Sci., 2012, 37(10), 1350–1400 CrossRef.
- N. Galdi, A. Buonerba, P. Oliva and L. Oliva, Nanostructured ethylene–styrene copolymers, Polym. Chem., 2014, 5(8), 3045–3052 RSC.
- E. M. Woo, Y. S. Sun and C. P. Yang, Polymorphism, thermal behavior, and crystal stability in syndiotactic polystyrene vs. its miscible blends, Prog. Polym. Sci., 2001, 26(6), 945–983 CrossRef.
- H. Moustafa, A. M. Youssef, N. A. Darwish and A. I. Abou-Kandil, Eco-friendly polymer composites for green packaging: Future vision and challenges, Composites, Part B, 2019, 172, 16–25 CrossRef.
- K. M. Nair, S. Thomas and G. Groeninckx, Thermal and dynamic mechanical analysis of polystyrene composites reinforced with short sisal fibres, Compos. Sci. Technol., 2001, 61(16), 2519–2529 CrossRef.
- A. M. Youssef, F. M. Malhat and A. F. Abd El-Hakim, Preparation and utilization of polystyrene nanocomposites based on TiO2 nanowires, Polym.-Plast. Technol. Eng., 2013, 52(3), 228–235 CrossRef.
- K. M. Nair, S. M. Diwan and S. Thomas, Tensile properties of short sisal fiber reinforced polystyrene composites, J. Appl. Polym. Sci., 1996, 60(9), 1483–1497 CrossRef.
- K. I. Kuroda, A. Izumi, B. B. Mazumder, Y. Ohtani and K. Sameshima, Characterization of kenaf (Hibiscus cannabinus) lignin by pyrolysis-gas chromatography-mass spectrometry in the presence of tetramethylammonium hydroxide, J. Anal. Appl. Pyrolysis, 2002, 64(2), 453–463 CrossRef.
- https://aawsat.com/english/home/article/2010611/pharaohs-mastered-linen-cultivation-weaving-million-years-ago.
- H. Moustafa, C. Guizani, C. Dupont, V. Martin, M. Jeguirim and A. Dufresne, Utilization of torrefied coffee grounds as reinforcing agent to produce high-quality biodegradable PBAT composites for food packaging applications, ACS Sustainable Chem. Eng., 2017, 5(2), 1906–1916 CrossRef.
- S. I. Mussatto, M. Fernandes, A. M. Milagres and I. C. Roberto, Effect of hemicellulose and lignin on enzymatic hydrolysis of cellulose from brewer's spent grain, Enzyme Microb. Technol., 2008, 43(2), 124–129 CrossRef CAS.
- C. H. Biradar, K. A. Subramanian and M. G. Dastidar, Production and fuel quality upgradation of pyrolytic bio-oil from Jatropha curcas de-oiled seed cake, Fuel, 2014, 119, 81–89 CrossRef CAS.
- M. A. Silva, S. A. Nebra, M. M. Silva and C. G. Sanchez, The use of biomass residues in the Brazilian soluble coffee industry, Biomass Bioenergy, 1998, 14(5–6), 457–467 CrossRef CAS.
- H. M. El Sharkawi, S. Tojo, T. Chosa, F. M. Malhat and A. M. Youssef, Biochar-ammonium phosphate as an uncoated-slow release fertilizer in sandy soil, Biomass Bioenergy, 2018, 117, 154–160 CrossRef CAS.
- D. R. Vardon, B. R. Moser, W. Zheng, K. Witkin, R. L. Evangelista, T. J. Strathmann, K. Rajagopalan and B. K. Sharma, Complete utilization of spent coffee grounds to produce biodiesel, bio-oil, and biochar, ACS Sustainable Chem. Eng., 2013, 1(10), 1286–1294 CrossRef CAS.
- L. Limousy, M. Jeguirim, S. Labbe, F. Balay and E. Fossard, Performance and emissions characteristics of compressed spent coffee ground/wood chip logs in a residential stove, Energy Sustainable Dev., 2015, 28, 52–59 CrossRef CAS.
- M. A. Silva, S. A. Nebra, M. M. Silva and C. G. Sanchez, The use of biomass residues in the Brazilian soluble coffee industry, Biomass Bioenergy, 1998, 14(5–6), 457–467 CrossRef CAS.
- N. Saba, M. T. Paridah and M. Jawaid, Mechanical properties of kenaf fibre reinforced polymer composite: A review, Constr. Build. Mater., 2015, 76, 87–96 CrossRef.
- M. R. Sanjay, G. R. Arpitha, L. L. Naik, K. Gopalakrishna and B. Yogesha, Applications of natural fibers and its composites: An overview, Nat. Resour., 2016, 7(3), 108–114 Search PubMed.
- H. Moustafa, C. Guizani and A. Dufresne, Sustainable biodegradable coffee grounds filler and its effect on the hydrophobicity, mechanical and thermal properties of biodegradable PBAT composites, J. Appl. Polym. Sci., 2017, 134(8), 44498 CrossRef.
- M. M. Ibrahim, H. Moustafa, E. N. Abd EL Rahman, S. Mehanny, M. H. Hemida and E. El-Kashif, Reinforcement of starch based biodegradable composite using Nile rose residues, J. Mater. Res. Technol., 2020, 9(3), 6160–6171, DOI:10.1016/j.jmrt.2020.04.018.
- H. Moustafa, A. M. Youssef, S. Duquesne and N. A. Darwish, Characterization of bio-filler derived from seashell wastes and its effect on the mechanical, thermal, and flame retardant properties of ABS composites, Polym. Compos., 2017, 38(12), 2788–2797 CrossRef CAS.
- A. M. Youssef, M. S. Hasanin, M. A. El-Aziz and O. M. Darwesh, Green, economic, and partially biodegradable wood plastic composites via enzymatic surface modification of lignocellulosic fibers, Heliyon, 2019, 5(3), e01332 CrossRef CAS PubMed.
- M. R. Sanjay and B. Yogesha, Studies on hybridization effect of jute/kenaf/E-glass woven fabric epoxy composites for potential applications: Effect of laminate stacking sequences, J. Ind. Text., 2018, 47(7), 1830–1848 CrossRef CAS.
- D. Maldas, B. V. Kokta, R. G. Raj and C. Daneault, Improvement of the mechanical properties of sawdust wood fibre—polystyrene composites by chemical treatment, Polymer, 1988, 29(7), 1255–1265 CrossRef CAS.
- K. Joseph, S. Thomas and C. Pavithran, Effect of ageing on the physical and mechanical properties of sisal-fiber-reinforced polyethylene composites, Compos. Sci. Technol., 1995, 53(1), 99–110 CrossRef CAS.
- A. A. Mazuki, H. M. Akil, S. Safiee, Z. A. Ishak and A. A. Bakar, Degradation of dynamic mechanical properties of pultruded kenaf fiber reinforced composites after immersion in various solutions, Composites, Part B, 2011, 42(1), 71–76 CrossRef.
- H. Moustafa, C. Guizani, C. Dupont, V. Martin, M. Jeguirim and A. Dufresne, Utilization of torrefied coffee grounds as reinforcing agent to produce high-quality biodegradable PBAT composites for food packaging applications, ACS Sustainable Chem. Eng., 2017, 5(2), 1906–1916 CrossRef CAS.
- A. M. Youssef, T. Bujdosó, V. Hornok, S. Papp, A. E. Hakim and I. Dékány, Structural and thermal properties of polystyrene nanocomposites containing hydrophilic and hydrophobic layered double hydroxides, Appl. Clay Sci., 2013, 77, 46–51 CrossRef.
- ASTM D638-14, Standard Test Method for Tensile Properties of Plastics Search PubMed.
- ASTM D570-98(2018), Standard Test Method for Water Absorption of Plastics Search PubMed.
- A. N. Azammi, S. M. Sapuan, M. R. Ishak and M. T. Sultan, Physical and damping properties of kenaf fibre filled natural rubber/thermoplastic polyurethane composites, Def. Technol., 2019, 16, 29–34 CrossRef.
- ASTM D1653-16, Standard Test Methods for Water Vapor Transmission of Organic Coating Films Search PubMed.
- ASTM D3985-17, Standard Test Method for Oxygen Gas Transmission Rate Through Plastic Film and Sheeting Using a Coulometric Sensor Search PubMed.
- H. Moustafa, N. A. Darwish, M. A. Nour and A. M. Youssef, Biodegradable date stones filler for enhancing mechanical, dynamic, and flame retardant properties of polyamide-6 biocomposites, Polym. Compos., 2018, 39(6), 1978–1987 CrossRef CAS.
- J. Rieger, The glass transition temperature of polystyrene, J. Therm. Anal., 1996, 46(3–4), 965–972 CrossRef CAS.
- C. H. Lee, S. M. Sapuan and M. R. Hassan, Thermal analysis of kenaf fiber reinforced floreon biocomposites with magnesium hydroxide flame retardant filler, Polym. Compos., 2018, 39(3), 869–875 CrossRef CAS.
- S. H. Aziz and M. P. Ansell, The effect of alkalization and fibre alignment on the mechanical and thermal properties of kenaf and hemp bast fibre composites: Part 1–polyester resin matrix, Compos. Sci. Technol., 2004, 64(9), 1219–1230 CrossRef CAS.
- T. Murayama, Dynamic mechanical analysis of polymeric material, Elsevier Scientific Pub. Co., 1978 Search PubMed.
- E. Ghasemi, H. Azizi and N. Naeimian, Rheological behaviour of polypropylene/kenaf fibre/wood flour hybrid composite, Iran. Polym. J., 2009, 17, 191–198 Search PubMed.
- A. K. Saha, S. Das, D. Bhatta and B. C. Mitra, Study of jute fiber reinforced polyester composites by dynamic mechanical analysis, J. Appl. Polym. Sci., 1999, 71(9), 1505–1513 CrossRef CAS.
- H. Anuar and A. Zuraida, Improvement in mechanical properties of reinforced thermoplastic elastomer composite with kenaf bast fibre, Composites, Part B, 2011, 42(3), 462–465, DOI:10.1016/j.compositesb.2010.12.013.
- V. Srebrenkoska, G. B. Gaceva, M. Avella, M. E. Errico and G. Gentile, Recycling of polypropylene-based eco-composites, Polym. Int., 2008, 57(11), 1252–1257, DOI:10.1002/pi.2470.
- N. F. Alias, H. Ismail and K. M. Ku Ishak, The Effect of Kenaf Loading on Water Absorption and Impact Properties of Polylactic Acid/Natural Rubber/Kenaf Core Powder Biocomposite, Mater. Today: Proc., 2019, 17, 584–589, DOI:10.1016/j.matpr.2019.06.338.
- M. Jacob, S. Thomas and K. T. Varughese, Mechanical properties of sisal/oil palm hybrid fiber reinforced natural rubber composites, Compos. Sci. Technol., 2004, 64(7–8), 955–965 CrossRef CAS.
- A. Atiqah, M. Jawaid, M. R. Ishak and S. M. Sapuan, Moisture absorption and thickness swelling behaviour of sugar palm fibre reinforced thermoplastic polyurethane, Procedia Eng., 2017, 184, 581–586 CrossRef CAS.
- H. Moustafa, H. Galliard, L. Vidal and A. Dufresne, Facile modification of organoclay and its effect on the compatibility and properties of novel biodegradable PBE/PBAT nanocomposites, Eur. Polym. J., 2017, 87, 188–199 CrossRef CAS.
- R. A. Chowdhury, M. Nuruddin, C. Clarkson, F. Montes, J. Howarter and J. P. Youngblood, Cellulose nanocrystal (CNC) coatings with controlled anisotropy as high-performance gas barrier films, ACS Appl. Mater. Interfaces, 2018, 11(1), 1376–1383 CrossRef.
|
This journal is © The Royal Society of Chemistry 2020 |
Click here to see how this site uses Cookies. View our privacy policy here.